精馏塔设备CAD图
精馏塔内部结构原来是这样子啊!
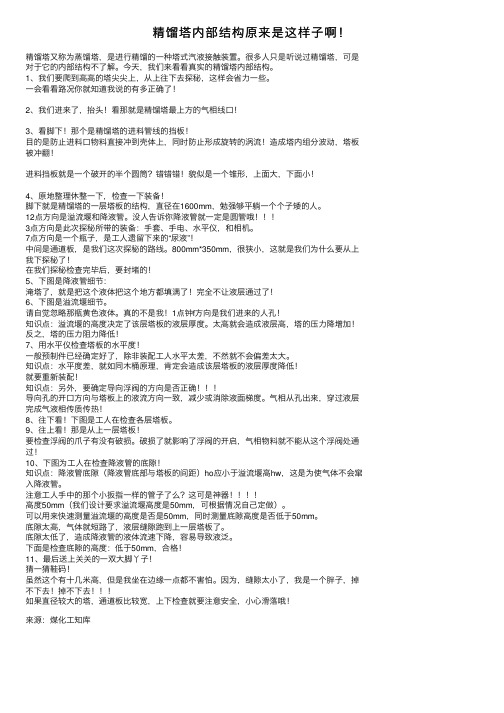
精馏塔内部结构原来是这样⼦啊!精馏塔⼜称为蒸馏塔,是进⾏精馏的⼀种塔式汽液接触装置。
很多⼈只是听说过精馏塔,可是对于它的内部结构不了解。
今天,我们来看看真实的精馏塔内部结构。
1、我们要爬到⾼⾼的塔尖尖上,从上往下去探秘,这样会省⼒⼀些。
⼀会看看路况你就知道我说的有多正确了!2、我们进来了,抬头!看那就是精馏塔最上⽅的⽓相线⼝!3、看脚下!那个是精馏塔的进料管线的挡板!⽬的是防⽌进料⼝物料直接冲到壳体上,同时防⽌形成旋转的涡流!造成塔内组分波动,塔板被冲翻!进料挡板就是⼀个破开的半个圆筒?错错错!貌似是⼀个锥形,上⾯⼤,下⾯⼩!4、原地整理休整⼀下,检查⼀下装备!脚下就是精馏塔的⼀层塔板的结构,直径在1600mm,勉强够平躺⼀个个⼦矮的⼈。
12点⽅向是溢流堰和降液管。
没⼈告诉你降液管就⼀定是圆管哦3点⽅向是此次探秘所带的装备:⼿套、⼿电、⽔平仪,和相机。
7点⽅向是⼀个瓶⼦,是⼯⼈遗留下来的“尿液”!中间是通道板,是我们这次探秘的路线。
800mm*350mm,很狭⼩,这就是我们为什么要从上我下探秘了!在我们探秘检查完毕后,要封堵的!5、下图是降液管细节:淹塔了,就是把这个液体把这个地⽅都填满了!完全不让液层通过了!6、下图是溢流堰细节。
请⾃觉忽略那瓶黄⾊液体。
真的不是我!1点钟f⽅向是我们进来的⼈孔!知识点:溢流堰的⾼度决定了该层塔板的液层厚度。
太⾼就会造成液层⾼,塔的压⼒降增加!反之,塔的压⼒阻⼒降低!7、⽤⽔平仪检查塔板的⽔平度!⼀般预制件已经确定好了,除⾮装配⼯⼈⽔平太差,不然就不会偏差太⼤。
知识点:⽔平度差,就如同⽊桶原理,肯定会造成该层塔板的液层厚度降低!就要重新装配!知识点:另外,要确定导向浮阀的⽅向是否正确导向孔的开⼝⽅向与塔板上的液流⽅向⼀致,减少或消除液⾯梯度。
⽓相从孔出来,穿过液层完成⽓液相传质传热!8、往下看!下图是⼯⼈在检查各层塔板。
9、往上看!那是从上⼀层塔板!要检查浮阀的⽖⼦有没有破损。
板式精馏塔装配图
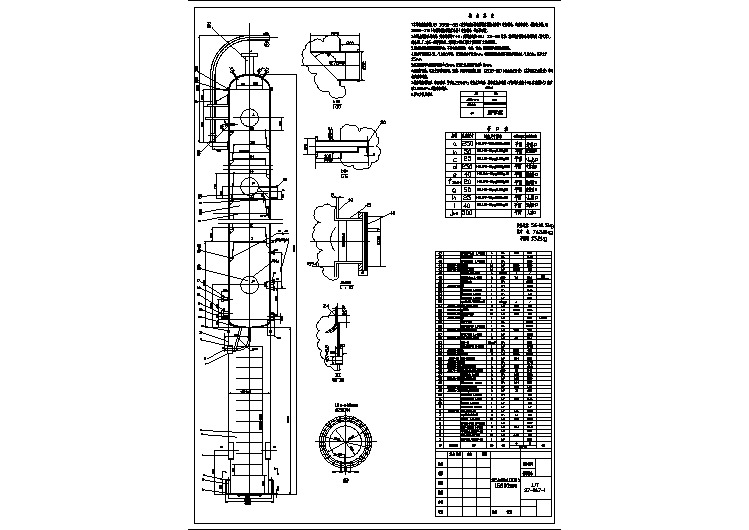
塔板式精馏塔设计(图文表)
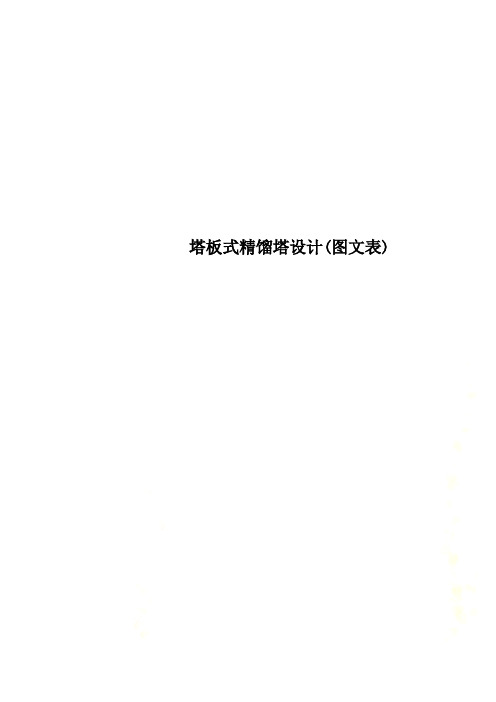
塔板式精馏塔设计(图文表)(一)设计方案的确定本设计任务为乙醇-水混合物。
设计条件为塔顶常压操作,对于二元混合物的分离,应采用连续精馏流程。
酒精精馏与化工精馏过程不同点就在于它不仅是一个将酒精浓缩的过程,而且还担负着把粗酒精中50多种挥发性杂质除去的任务,所以浓缩酒精和除去杂质的过程在酒精工业中称为精馏。
物料中的杂质基本上是在发酵过程中生成的,只是很少数的杂质是在蒸煮和蒸馏过程中生成的。
本次设计的精馏塔用板式塔,内部装有塔板、降液管、各种物料的进出口及附属结构(如全凝器等)。
此外,在塔板上有时还焊有保温材料的支撑圈,为了方便检修,在塔顶还装有可转动的吊柱。
塔板是板式塔的主要构件,本设计所用的塔板为筛板塔板。
筛板塔的突出优点是结构简单造价低,合理的设计和适当的操作能使筛板塔满足要求的操作弹性,而且效率高,并且采用筛板可解决堵塞问题,还能适当控制漏液。
设计中采用泡点进料,将原料液通过预热器加热至泡点后送人精馏塔内。
塔顶上升蒸汽采用全凝器冷凝,冷凝液在泡点下一部分回流至塔内,其余部分经产品冷却器冷却后送至储罐。
该物系属不易分离物系,最小回流比较小,采用其1.5倍。
设计中采用图解法求理论塔板数,在溢流装置选择方面选择单溢流弓形降液管。
塔釜采用间接蒸汽加热,塔顶产品经冷却后送至储罐。
(二)精馏塔的物料衡算1.原料液及塔顶、塔底产品的摩尔分率乙醇的摩尔质量 M 乙醇=46kg/kmol纯水的摩尔质量 M 水 =18kg/kmolx F =18/65.046/35.046/35.0+=0.174x D =18/1.046/9.046/9.0+=0.779x W =46/995.018/005.018/005.0+=0.0022.原料液及塔顶、塔底产品的平均摩尔质量M F =0.174×46+18×(1-0.174)= 22.872 kg/kmol M D =0.779×46+18×(1-0.779)= 39.812 kg/kmol M W =0.002×46+18×(1-0.002)= 18.056 kg/kmol3.物料衡算 D=30024812.3948000000⨯⨯=167.454 kmol/hF=D+WF ·x F =D ·x D +W ·x W解得 F=756.464 kmol/h W=589.01 kmol/h{(三)塔板数的确定1.回流比的选择由任务书提供的乙醇-水物系的气液平衡数据绘出x-y 图;由于设计中选用泡点式进料,q=1,故在图中对角线上自点a(x D,x D)作垂线,与Y轴截距oa=x D/(R min+1)=0.415 即最小回流比R min=x D/oa-1=0.877取比例系数为1.5,故操作回流比R为R=1.5×0.877=1.3162.精馏塔的气液相负荷的计算L=RD=1.316×167.454=220.369 kmol/hV=L+D=(R+1)D=2.316×167.454=387.823 kmol/h L ’=L+qF=220.369+756.464=976.833 kmol/h V ’=V+(q-1)F=V=387.823 kmol/h3.操作线方程精馏段操作线方程为 y=1+R R x+11+R x D =1316.1316.1+x+11.3161+×0.779即:y=0.568x+0.336提馏段操作线方程为y=F q D R qF RD )1()1(--++x-F q D R DF )1()1(--+-x W=1.316*167.454+1*756.464(1.316+1)*167.454x-756.464167.454(1.3161)*167.454-+×0.002 即:y=2.519x-0.0034.采用图解法求理论塔板数塔顶操作压力P D=101.3 KPa单板压降△P=0.7 kPa进料板压力P F=0.7×18+101.3=113.9 kPa塔底操作压力P W=101.3+0.7×26=119.5 kPa精馏段平均压力P m=(101.3+113.9)/2=107.6 kPa 压力P m=(113.9+119.5)/2=116.7 kPa2.操作温度计算计算全塔效率时已知塔顶温度t D=78.43 o C进料板温度 t F=83.75 o C塔底温度t W=99.53 o C精馏段平均温度t m=(t D+t F)/2=(78.43+83.75)/2=81.09 o C提馏段平均温度t m=(t W+t F)/2=(99.53+83.75)/2=91.64 o C3.平均摩尔质量计算塔顶平均摩尔质量计算由x D=y1=0.779 查上图可得x1=0.741M VDm=0.779×46+(1-0.779)×18=39.812 g/molM LDm=0.741×46+(1-0.741)×18=38.748 g/mol进料板平均摩尔质量计算 t f=83.74 o C由y F=0.518 查上图可得x F=0.183M VFm =0.518×46+(1-0.518)×18=32.504 g/mol M LFm =0.183×46+(1-0.183)×18=23.124 g/mol 精馏平均摩尔质量M Vm =( M VDm + M VFm )/2=36.158 g/molM Lm =( M LDm + M LFm )/2=30.936 g/mol4.平均密度计算气相平均密度计算由理想气体状态方程计算,即ρVm =RT PMv =)15.27309.81(314.8158.366.107+⨯⨯=1.321 kg/m 3 液相平均密度计算液相平均密度依1/ρLm =∑αi /ρi 计算 塔顶液相平均密度计算t D =78.43 o C 时 ρ乙醇=740 kg/m 3 ρ水=972.742 kg/m 3ρLDm =)742.972/1.0740/9.0(1+=758.14 kg/m 3进料板液相平均密度计算t F =83.75 o C 时 ρ乙醇=735 kg/m 3 ρ水=969.363 kg/m 3ρLFm =)363.969/636.0735/364.0(1+=868.554 kg/m 3塔底液相平均密度计算t W =99.53 o C 时 ρ乙醇=720 kg/m 3 ρ水=958.724 kg/m 3ρLWm =)724.958/995.0720/005.0(1 =957.137 kg/m 3精馏段液相平均密度计算ρLm =(ρLFm +ρLDm )/2=(758.14+868.554)/2=813.347 kg/m 3提馏段液相平均密度计算ρLm =(ρLFm +ρLWm )/2=(957.137+868.554)/2=912.846 kg/m 35.液体平均表面张力计算液体平均表面张力依σLm =∑x i σi 计算塔顶液相平均表面张力计算t D =78.43时 σ乙醇=62.866 mN/m σ水=17.8 mN/m σLDm =0.779×17.8+0.221×62.886=84.446 mN/m 进料板液相平均表面张力计算t F =83.75时 σ乙醇=61.889 mN/m σ水=17.3 mN/m σLFm =0.183×17.3+0.817×61.889=53.729 mN/m 塔底液相平均表面张力计算t W =99.53时 σ乙醇=58.947 mN/m σ水=15.9 mN/m σLWm =0.005×15.9+0.995×58.947=58.732 mN/m 精馏段液相平均表面张力计算σLm =(84.446+53.729)/2=69.088 mN/m 提馏段液相平均表面张力计算σLm =(58.732+53.729)/2=56.231 mN/m6.液体平均粘度计算液体平均粘度依lgμLm=∑x i lgμi计算塔顶液相平均粘度计算t D=78.43o C时μ乙醇=0.364mPa·s μ水=0.455 mPa·slgμLDm=0.779lg(0.455)+0.221lg(0.364)=-0.363μLDm =0.436 mPa·s进料液相平均粘度计算t F=83.75 o C时μ乙醇=0.341mPa·s μ水=0.415 mPa·slgμLFm=0.183lg(0.415)+0.817lg(0.341)=-0.452μLFm=0.353 mPa·s塔底液相平均粘度计算t W=99.53 o C时μ乙醇=0.285mPa·s μ水=0.335 mPa·slgμLWm=0.002lg(0.335)+0.998lg(0.285)=-0.544μLWm=0.285 mPa·s精馏段液相平均粘度计算μLm=(0.436+0.353)/2=0.395 mPa·s提馏段液相平均粘度计算μLm=(0.285+0.353)/2=0.319 mPa·s(五)精馏塔的塔体工艺尺寸计算1.塔径的计算精馏段的气液相体积流率为V S =ρ3600VM =2.949 m 3/s L S =ρ3600LM =0.0023 m 3/s 查史密斯关联图,横坐标为Vh Lh (vlρρ)21=949.20023.0(321.1347.813) 1/2=0.0196取板间距H T =0.45m ,板上液层高度h L =0.06m , 则H T -h L =0.39m 查图可得C 20=0.08 由C=C 20(20L σ)0.2=0.08(69.088/20)0.2=0.103u max =C (ρL -ρV )/ ρV =2.554 m/s取安全系数为0.7,则空塔气速为 u=0.7u max =1.788 m/sD=4V s /πu=788.1/14.3/949.2*4=1.39 m 按标准塔径元整后 D=1.4 m 塔截面积A T =(π/4)×1.42=1.539 ㎡ 实际空塔气速为 u=2.717/1.539=1.765 m/s 2.精馏塔有效高度的计算精馏段有效高度为Z 精=(N 精-1)H T =7.65 m 提馏段有效高度为Z 提=(N 提-1)H T =3.15 m在进料板上方开一人孔,其高度为 1m 故精馏塔的有效高度为 Z=Z 精+Z 提+1=7.65+3.15+1=11.8 m(六)塔板主要工艺尺寸的计算1.溢流装置计算因塔径D=1.4 m ,可选用单溢流弓形降液管 堰长l W =0.7×1.4=0.98 m 2.溢流强度i 的校核i=L h /l W =0.0023×3600/0.98=8.449≤100~130m 3/h ·m 故堰长符合标准 3.溢流堰高度h W平直堰堰上液层高度h ow =100084.2E (L h /l W )2/3由于L h 不大,通过液流收缩系数计算图可知E 近似可取E=1h ow =100084.2×1×(L h /l W )2/3=0.0119 mh W =h L -h ow =0.06-0.0119=0.0481 m 4.降液管尺寸计算查弓形降液管参数图,横坐标l W /D=0.7 可查得A f /A T =0.093 W d /D=0.151 故 A f =0.093A T =0.143 ㎡ W d =0.151W d =0.211 ㎡留管时间θ=3600A T H T /L H =27.64 s >5 s 符合设计要求5.降液管底隙高度h oh O =L h /3600l W u 0’=0.0023/0.98×0.08=0.03 m h W -h O =0.0481-0.03=0.0181 m >0.006 m 6.塔板布置塔板的分块 D=1400 mm >800 mm ,故塔板采用分块式。
化工制图CAD教程与开发(6)---塔设备绘制
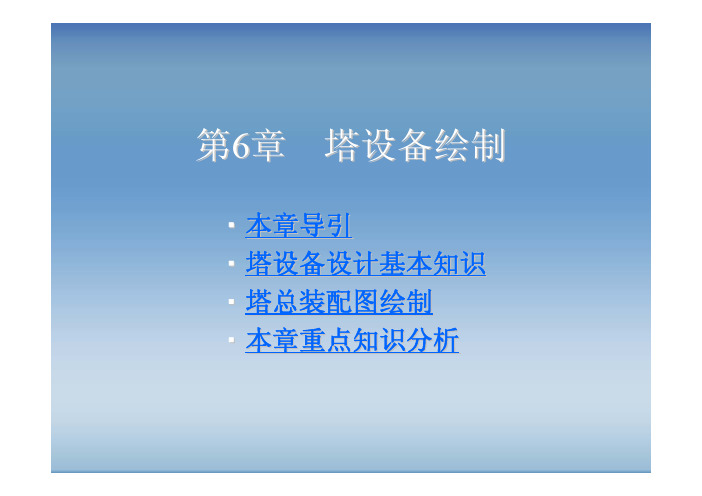
操作时,液体横向流过塔板,靠溢流堰保持塔板上有一定厚度的流动液层, 齿缝浸没于液层之中而形成液封。上升气体通过齿缝进入液层时,被分散成许多 细小的气泡或股流,在板上形成了鼓泡层和泡沫层,为气液两相提供了大量的传 质界面。
尽管泡罩塔有操作弹性大,板效率高,处理量大的优点,但由于其结构复 杂,造价高以及压降大,使用上受到一定的限制.
浮阀塔的突出特点是操作弹性大,由于压降及雾沫夹带均小,故板间距可 缩小。一般浮阀塔在生产能力、塔板效率及结构简单方面优于泡罩而不及筛板。
② 筛板塔 筛板塔的塔板上开有许多均匀分布的筛孔,孔径一般为 3~8mm,筛孔在塔板上作正三角形排列。塔板上设置溢流堰,使板上能维持一 定厚度的液层。操作时,上升气流通过筛孔分散成细小的流股,在板上液层中 鼓泡而出,气液间密切接触而进行传质。在正常的操作气速下,通过筛孔上升 的起来,应能阻止液体经筛孔向下泄漏。
从板间距对塔板效率的影响分析,在一定的气液负荷和塔径的条件下, 增加板间距可使物沫夹带量减小,特别对易起泡的物系,板间距应取大些, 以保证塔板的分离效果。此外,当生产负荷波动大时,也需要增大板间距, 以提高操作弹性。
在决定板间距时还应考虑安装、检修的需要。例如在塔体人孔处,应留 有足够高的工作空间,其值不应小于600mm。
对于板式塔,应先利用塔效率将理论板层数折算成实际板层数,然后
再由实际板层数和板间距来计算主体塔高,即:
式中
Hz=NT×HT / ET Hz——塔高,m; NT——塔内所需的理论板层数; ET——总板效率; HT——塔板间距,m。
(6-2)
塔板间距HT除直接影响塔高外,板间距还与塔的生产能力、操作弹性即 塔板效率有关。在一定的生产任务下,采用较大的板间距,能允许较高的空 塔气速,因而塔径可小些,但塔高要增加。反之,采用较小的板间距,只能 允许较小的空塔气速,塔径就要增大,但塔高可以降低。对于板数较多的精 馏塔,往往采用较小的板间距,适当地加大塔径以降低塔高。板间距与塔径 之间的关系,应根据实际情况,结合经济权衡,反复调整,以作出最佳选择。 表6-1所列的经验数据可供初选板间距时参考。板间距的数值应按照规定选 取整数,如300mm、350mm、450mm、500mm等。
分离乙醇水精馏塔设计(含经典工艺流程图和塔设备图)
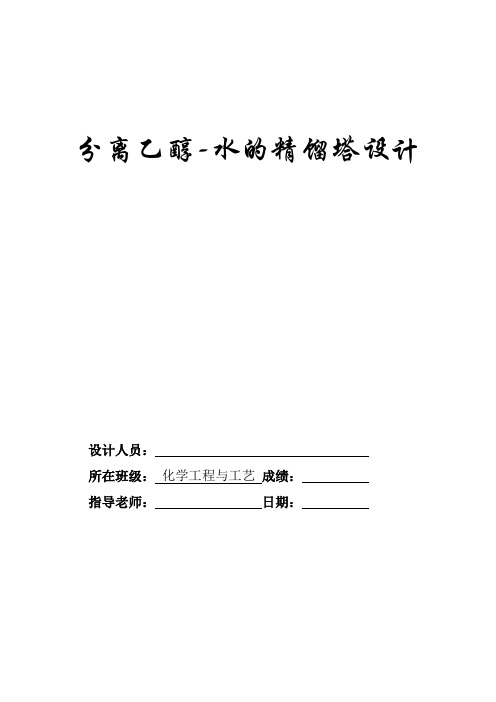
分离乙醇-水的精馏塔设计设计人员:所在班级:化学工程与工艺成绩:指导老师:日期:化工原理课程设计任务书一、设计题目:乙醇---水连续精馏塔的设计二、设计任务及操作条件(1)进精馏塔的料液含乙醇35%(质量分数,下同),其余为水;(2)产品的乙醇含量不得低于90%;(3)塔顶易挥发组分回收率为99%;(4)生产能力为50000吨/年90%的乙醇产品;(5)每年按330天计,每天24小时连续运行。
(6)操作条件a)塔顶压强 4kPa (表压)b)进料热状态自选c)回流比自选d)加热蒸汽压力低压蒸汽(或自选)e)单板压降 kPa。
三、设备形式:筛板塔或浮阀塔四、设计内容:1、设计说明书的内容1)精馏塔的物料衡算;2)塔板数的确定;3)精馏塔的工艺条件及有关物性数据的计算;4)精馏塔的塔体工艺尺寸计算;5)塔板主要工艺尺寸的计算;6)塔板的流体力学验算;7)塔板负荷性能图;8)精馏塔接管尺寸计算;9)对设计过程的评述和有关问题的讨论;2、设计图纸要求;1)绘制生产工艺流程图(A2 号图纸);2)绘制精馏塔设计条件图(A2 号图纸);五、设计基础数据:1.常压下乙醇---水体系的t-x-y 数据;2.乙醇的密度、粘度、表面张力等物性参数。
一、设计题目:乙醇---水连续精馏塔的设计二、设计任务及操作条件:进精馏塔的料液含乙醇35%(质量分数,下同),其余为水;产品的乙醇含量不得低于90%;塔顶易挥发组分回收率为99%,生产能力为50000吨/年90%的乙醇产品;每年按330天计,每天24小时连续运行。
塔顶压强 4kPa (表压)进料热状态自选回流比自选加热蒸汽压力低压蒸汽(或自选)单板压降≤0.7kPa。
三、设备形式:筛板塔四、设计内容:1)精馏塔的物料衡算:原料乙醇的组成 xF==0.1740原料乙醇组成 xD0.7788塔顶易挥发组分回收率90%平均摩尔质量 MF =由于生产能力50000吨/年,.则 qn,F所以,qn,D2)塔板数的确定:甲醇—水属非理想体系,但可采用逐板计算求理论板数,本设计中理论塔板数的计算采用图解法。
精馏塔演示图

底产品罐 V13
釜排液前阀
V14 此段管路无 塔底产品冷却器水阀 离心泵 V15直排
回水
原料罐 倒料路径
水表
进水
中控教仪UTS-JL-2J精馏装置图(含减压系统)
产品冷却器
顶冷 V32 顶温
冷凝液温
回流温度
接真空
塔顶放空阀
V26
V50 外 回 流 L1 V52 V40 V49 产品罐
采 出 量 凝液罐
接真空
平衡管
V25 ▲不能以液位高 度判断产品量
凝液罐清空阀 采出泵 齿轮全开 装的高 度不一致 V29 真空缓冲罐 真空泵 A真空管路 蒸 气 量 V2
原料换热后出顶冷↓ 加料口 B接塔顶产品 罐
平衡管接塔顶
原料进顶冷↑
10板 产品罐 清空阀
TIC712 测温点
进料回流L3
蒸气量V1
产品出料 接软管 12板 V03 视镜 鼓泡 预热温 直接回水阀 底产品温度 排釜液流量 V10 V21 接真空
化工制图AutoCAD化工设计第6章---塔设备绘制
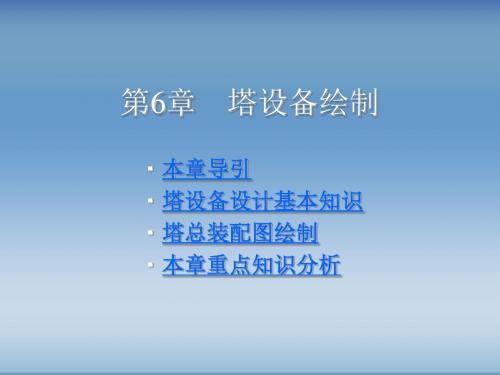
本章目录
塔设备设计基本知识
• 塔设备的分类 • 塔设备关键尺寸的确定 • 计算举例
塔设备的分类
为满足各种生产过程的需要,塔设备经过长期发展,形成了型式繁多的结 构.考虑到便于研究和比较,可以从不同的角度。对塔设备进行分类.例如: 按单元操作分为精馏塔,吸收塔、解吸塔和萃取塔等;按操作压力分为加压塔、 常压塔和减压塔;按塔内件结构分为板式塔和填料塔两大类,但如果将塔内无 任何构件也作为一类,则可以分为三类,见图6-1。 下面将三类塔设备再进行进一步的细分。 ⑴板式塔 板式塔以塔板作为汽(气),液接触的基本构件。气体自塔底向上以鼓泡喷射 的形式穿过塔盘上的液层,塔内气液两相呈逐级逆流操作,在塔板上传质元件 作用下,两相进行接触和分离,同时完成传质(和传热)任务。板式塔构造,除塔 板外,塔的内构件还包括降液管、受液盘、溢流堰、塔板支承件及紧固件等。 塔板选型后,应依次进行塔径、塔板及内构件的设计,然后用负荷性能图进行 结构设计的调整(或优化),直至满足塔内正常操作(或较佳操作)。 除此之外,人们又按板式塔的塔盘结构的不同,将板式塔细分为多种塔。 常见板式塔的类型有:浮阀塔、泡罩塔、筛板塔、斜孔塔及穿流式塔板等。
事实上,我们再在计任何一台塔设备时,很难全部满足上述各项 要求;但我们应该从符合生产的基本要求、满足经济上的合理性、以 及在单位时间内,利用最少的能源和空间,生产加工最多的产品等方 面出发,予以全面考虑,使所设计的塔在满足基本要求的前提下,整 体性能达到最优。 本章将通过对塔设备一些基本知识介绍,具体讲解如何绘制塔设 备,大到绘制整体方案的确定,小到主要零配件的尺寸及绘制方法。 对于前面几章已经详细介绍过的绘制方法,我们将不在讲解,如封头 的绘制、接管的绘制,但我们会提供本章中有关这些零配件的具体尺 寸。
精馏示意图

q值
q>1
q线斜率 q/q1 +
饱和液体
气液混合 物
IF=IL
IL<IF<IV
q=1
0 < q <1
无穷大
–
0
饱和蒸汽
IF=IV
q=0
精馏
5
双组分连续精馏塔的计算
– 不同q值对 操作线的影 响
q值不同改变的 是提馏段的操作线 方程。当进料组成、 回流比及分离要求 一定时,q值的减少 使提馏段操作线越 来越靠近平衡线。
由于提馏段下降 液体量L’不易确定,所 以提馏段操作线的实际 应用价值不大。但提馏 段操作线一定通过C点 (xW,xW)(间接蒸汽 加热方式)
c
d
xW
xD
精馏
4
双组分连续精馏塔的计算 – 不同 q值对应的 q线方 程
f q=1 0 < q <1
q=0 q<0 q>1
e
xF
进料状况
冷液体
进料的焓 IF IF<IL
q<0
q>1
f 0 < q <1
q=0
q=1
e
xW
精馏
xF
xD
6
双组分连续精馏塔的计算
图解法
1
逐板法原理
4 5
2
3
xW
精馏
xF
xD
7
双组分连续精馏塔的计算
图解法(续)
1
实际图解过程
4
2
3
5
xW
精馏
xF
xD
y n1 L D xn xD L D L D
L 令 R ( 回流比) D
AutoCAD绘制化工工艺图纸第6章塔设备绘制
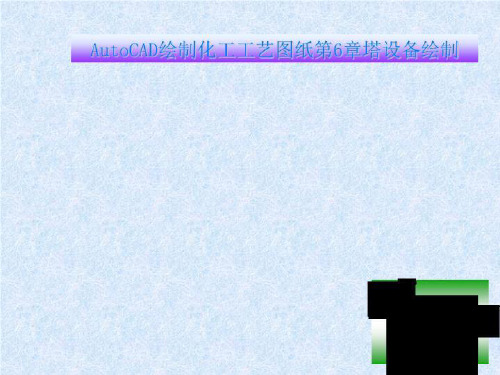
①生产能力大,即气(汽)、液处理量大;
②流体流动阻力小传;
③质效率高;
④结构简单、材料耗用量小、制造和安装容易;
⑤操作弹性大,即在负荷波动较大时,仍能维持较高的效率;
(6-3)
G——气相的空塔质量速度,kg/(m2. h)
D——塔径,m;
Z——填料层高度,m;
——相对挥发度;
L——液相粘度,mPa .s; L——液相密度,kg/m3;
c1、c2、c3——常数,取决于填料类型及尺寸。其部分数据见表6-2。
等板高度的数据或关联结果,一般来自小型实验,故往往不符合工业生产装
④舌型塔板、浮舌塔板和斜孔塔板 三者均为喷射型塔板。在舌型塔板中, 气流经舌孔流出时,促进了液体流动,因而大液量时不会产生大的液面落差,同 时由于汽、液并流,大大减少了雾沫夹带。针对以上缺点,发明了浮舌塔板,它 既有舌形塔板处理量大、压降低、夹带小的优点,又有浮阀弹性大、效率高的优 点。缺点是舌片易损坏。斜孔塔板采用孔口反向交错排列,避免了气、液并流造 成的气流不断加速现象,因而液层低而均匀,雾沫夹带小,塔板效率有所提高, 但由于开孔固定,操作弹性较小。
② 塔的顶部、底部空间及裙座高度的确定
A.塔的顶部空间高度(不包括接管高度) 塔的顶部空间高度是指塔顶第一层塔 盘到塔顶封头切线的距离。为了减少塔顶出口气体中夹带的液体量,顶部空间一般取 1.2~1.5m。有时为了提高产品质量,必须更多地除去气体中夹带的雾沫夹带,则可在 塔顶设置除沫器。如用金属除沫网,则网底到塔盘的距离一般不小于塔板间距。