熟料煅烧液相量与温度
熟料在烧成系统中的形成过程

1、干燥带温度范围:生料温度~450℃。
主要任务:①物料升温至450℃②物理水蒸发(生料进入窑系统后,大约在超过烟气的露点后75~150℃其间水分蒸发)。
该反应在C2-C1上升烟道及C1筒和C3-C2上升烟道完成。
2、预热带温度范围450℃~700℃。
主要任务:①物料升温至700℃②化合水脱水(粘土质原料)。
脱水反应在C3-C2、C2、C4-C3内进行,温度继续上升至700℃。
3、碳酸盐分解带主要承担MgCO3和CaCO3的分解任务,是吸热反应。
碳酸盐在C4已有少量分解,主要分解反应发生在分解炉中,在C5也有少量分解反应发生,出C5筒的物料碳酸盐表观分解率达90%以上,其余部分的分解反应在回转窑内进行,入窑物料温度升至850℃左右。
4、放热反应带(亦称过渡带)主要承担固相反应,生成C2S、C3A、C4AF,以上三种反应生成的热量可使物料温度上升200℃,放热反应在分解炉内、C5筒就有少量发生,大量反应是在进入回转窑内进行的。
5、烧成带主要承担熟料中最主要的矿物C3S的形成和f-CaO的吸收,完成熟料的最后烧成任务。
该带在回转窑内温度最高的部位,在正常的配料范围内,物料在1280℃时就开始出现液相,在1350~1450℃时液相量可达20%多(与配料有关)C2S和CaO先是溶于液相中,在液相中反应结合为C3S结晶析出,倒出地方使其他的C2S和CaO溶于液相,再结晶析出,这样使C3S大量形成,使f-CaO逐渐被C2S吸收。
窑内温度越高,液相粘度越低,C3S形成越快,f-CaO被吸收的越彻底,直至f-CaO逐渐被C2S吸收。
由此可见,影响f-CaO的因素:⑴窑内煅烧温度越高,f-CaO吸收越快,f-CaO被吸收的越彻底,直至f-CaO最后被基本吸收(﹤1.5%)⑵配料中液相量越高(L)液相粘度越低,石灰石吸收越快;饱和比越低,石灰石吸收越快,但对熟料质量有影响,因此要兼顾熟料质量和煅烧能力达到最佳平衡点。
第四讲 熟料煅烧
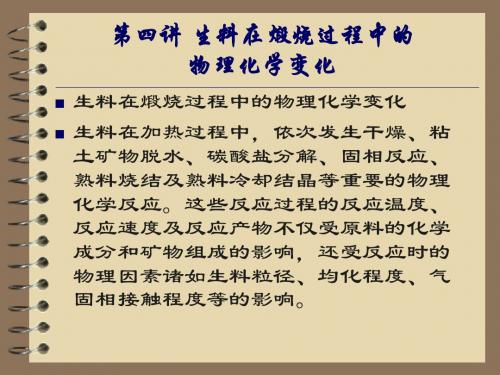
高岭土
生料在煅烧过程中的物理化学变化
3 碳酸盐分解
生料中的碳酸钙和夹杂的少量碳酸镁在煅烧过程中分 解并放出CO2的过程称碳酸盐分解。碳酸镁的分解温度 始于402~480℃左右,最高分解温度700℃左右;碳酸 钙在600℃时就有微弱分解发生,但快速分解温度在 812~928℃之间变化。MgCO3在590 ℃、CaCO3在890℃ 时的分解反应式如下: MgCO3 MgO + CO2↑-(1047~1 214)J/g CaC03 CaO + CO2↑-1645 J/g 其中,碳酸钙在水泥生料中所占比例80%左右,其 分解过程需要吸收大量的热,是熟料煅烧过程中消耗 热量最多的一个过程,因此,它是水泥熟料煅烧过程 重要的一环。
生料在煅烧过程中的物理化学变化
2.液相量 熟料的烧结必须要有一定数量的液相。液 相是硅酸三钙形成的必要条件,适宜的液相量 有利于C3S形成,并保证熟料的质量。液相量 太少,不利于C3S形成,反之,过多的液相易 使熟料结大块,给煅烧操作带来困难。 液相量与组分的性质、含量及熟料烧结温 度等有关。因此,不同的生料成分与煅烧温度 等对液相量有很大影响。一般水泥熟料烧成阶 段的液相量大约为20%~30%。
生料在煅烧过程中的物理化学变化
(2)液相量随熟料中铝率而变化,一般硅酸 盐水泥在煅烧阶段的液相量随铝率和温度的变 化情况见表6-3所示。
表6-3 熟料中液相量随铝率和温度的变化情况 IM=AI2O3/Fe2O3 2.0 1.25 0.64
温度(℃)
Байду номын сангаас1338
1400 1450
18.3
24.3 24.8
液 相
生料在煅烧过程中的物理化学变化
水泥熟料烧成的变化过程

水泥熟料烧成的变化过程一、干燥与脱水1.干燥入窑物料当温度升高到100~150℃时,生料中的自由水全部被排除,特别是湿法生产,料浆中含水量为32~40%,此过程较为重要。
而干法生产中生料的含水率一般不超过1.0%。
2.脱水当入窑物料的温度升高到450℃,粘土中的主要组成高岭土(Al2O3·2SiO2·2H2O )发生脱水反应,脱去其中的化学结合水。
此过程是吸热过程。
Al2O3·2SiO2·2H2O== Al2O3 (无定形) + 2SiO2 (无定形) + 2H2O脱水后变成无定形的三氧化三铝和二氧化硅,这些无定形物具有较高的活性。
二、碳酸盐分解当物料温度升高到600℃时,石灰石中的碳酸钙和原料中夹杂的碳酸镁进行分解,在CO2分压为一个大气压下,碳酸镁和碳酸钙的剧烈分解温度分别是750℃和900℃。
MgCO3=MgO+CO2CaCO3=CaO+CO2碳酸钙分解反应的特点碳酸钙的分解过程是一个强吸热过程(1645 kJ/kg ),是熟料形成过程中消耗热量最多的一个工艺过程;该过程的烧失量大,在分解过程中放出大量的CO2气体,使CaO疏松多孔,强化固相反应。
三、固相反应1.反应过程从原料分解开始,物料中便出现了性质活泼的游离氧化钙,它与生料中的SiO2、Al2O3、Fe2O3进行固相反应,形成熟料矿物。
2.影响固相反应的主要因素⑴生料细度及其均匀程度;⑵温度对固相反应的影响;四、熟料烧结水泥熟料主要矿物硅酸三钙的形成需在液相中进行,液相量一般在22~26%。
2 CaO·SiO2 + CaO=3 CaO·SiO2该反应称为烧结反应,它是在1300~1450~1300℃范围进行,故称该温度范围为烧成温度范围;在1450℃时反应迅速,故称该温度为烧成温度。
为使反应完全,还需有一定的时间,一般为15~25分钟。
五、熟料冷却熟料冷却时需急速冷却,其目的和作用是:1、为了防止C3S在1250℃分解出现二次游离氧化钙(对水泥安定性没大影响),降低熟料的强度;2、为了防止C2S在500℃时发生晶型转变,产生“粉化”现象;3、防止C3S晶体长大而强度降低且难以粉磨;4、减少MgO晶体析出,使其凝结于玻璃体中,避免造成水泥安定性不良;5、减少C3A晶体析出,不使水泥出现快凝现象,并提高水泥的抗硫酸盐性能;。
第五章硅酸盐水泥的煅烧

两个传热、一个化学 反应、两个传质
反应条件 悬浮程度 粘土质性质
CA、CF、C2S C12A、C2F C3A、C4AF C3A、C4AF、C2S
生料的细度均匀性 温度和时间 原料性质 矿化剂
C2S+CaO C3S
提高熟料的质量 改善熟料的易磨性 回收余热 易于熟料的输送、 储存和粉磨
最低共熔温度 液相量 液相粘度 液相表面张力 氧化钙溶解速率 反应物存在状态
作用
含氟化合物:常用萤石(CaF2) 硫化物:常用石膏(天然石膏、工业副产石膏) 氯化物:CaCl2 其他:铜矿渣、磷矿渣等 萤石:氟离子破坏晶格;降低液相生成温度;降低液相粘度
硫化物:能降低液相出现温度,降低液相粘度和表面张力 复合矿化剂(萤石-石膏、萤石-重晶石)
晶种:硅酸盐水泥熟料
挥发性组分:碱、氯、硫
4. 入窑物料碳酸钙分解率达30~40%,从而减轻了回转窑 的负荷,使窑的长度缩短。
5. 窑内没有干燥带、预热带,只有其余四个带。
5.5.3 预分解窑内熟料的煅烧
熟料煅烧特点
1. 分解炉中,温度为820~900℃时,分解率可达85~95%, 分解时间 4~10 s,而在窑内分解需30多分钟。
(1)尽可能多地回收熟料的热量,以提高入窑二次空气 温度,降低熟料热耗。 (2)缩短熟料的冷却时间,以提高熟料质量,改善易磨 性。 (3)冷却单位质量熟料的空气消耗量要小,以便提高二 次空气温度,减少粉尘飞扬,降低电耗。 (4)结构简单,操作方便,维修容易,运转率高。
2. 分类:
水泥熟料冷却机
筒式冷却机
5.5.1 回转窑内熟料的煅烧
燃料
低端 窑头 热端
传动大齿轮
高端 窑尾 冷端 生料
煅烧温度和时间对熟料质量的影响

.煅烧温度和时间对熟料质量的影响作者:刘天振纯阅读单位:淮海中联水泥有限公司发布日期:2013-08-15来源:影响熟料质量方面因素很多,但熟料在窑内煅烧是最重要环节之一。
熟料矿物形成实际上是在液相量出现以后进行的。
影响熟料质量方面因素很多,但熟料在窑内煅烧是最重要环节之一。
熟料矿物形成实际上是在液相量出现以后进行的。
液相主要有氧化铁、氧化铝、氧化钙所组成(包括其他次要组分氧化镁、氧化钾、氧化钠等),在高温液相作用下,CS逐渐溶解于液相中与f-cao化合成CS,32随着温度升高和时间延长,CS晶核不断形成,小晶体逐3渐长大,最终形成阿里特晶体。
完成熟料的烧结过程。
实践证明,CS的生成,如果熟料配料时三率值KH、3N、P 适当,生料成分稳定的条件下,主要取决于熟料煅烧温度、液相量、液相性质以及形成晶体反应时间。
本文重点介绍熟料煅烧温度和晶体反应时间对熟料强度的影响。
淮海中联水泥(287.08元/吨,0%)有限公司2#窑是由南京凯盛水泥设计院设计,2005年3月投产的5000t/d资料Word.熟料生产线,2007年8月公司利用现有1条日产5000t/d熟料生产线的窑尾、窑头废气余热,配套建设了1*9MW的纯低温余热发电系统。
该厂3、6、7月份窑系统工艺参数平均台帐(一)6月与3月份工艺参数对比。
CO平均值下降-44.12ppm。
二次风温上升+25.2℃. f-cao合格率上升+5.81%,在同等喂料量情况下窑速降低-0.3rpm,主窑皮长度增加+3.10m;由于窑皮厚度较3月份降低(见表五)。
窑内填充率下降窑功率同比降低-120A。
其它参数无明显变化。
熟料3天、7天、28天强度分别增加+1.38 Mpa、+5.59 Mpa、+4.19Mpa,液相量略有增加+0.1%。
通过参数对比分析:CO平均值下降和二次风温以及f-cao合格率上升,都能说明窑系统通风状况较好,二、三次风比例合适,窑内煅烧温度同比较高;在同等喂料量情况下由于窑速降低和主窑皮长度增加,延长了熟料在窑内煅烧时间,使熟料矿物结晶更加完全,熟料强度提高明显。
水泥熟料烧成液相量的计算探讨
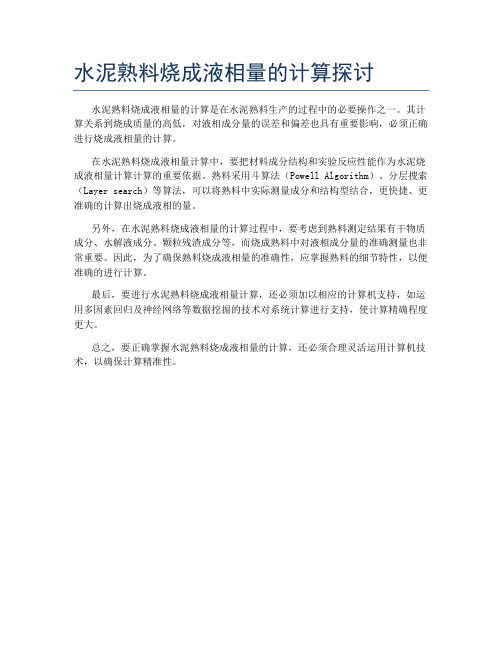
水泥熟料烧成液相量的计算探讨
水泥熟料烧成液相量的计算是在水泥熟料生产的过程中的必要操作之一。
其计算关系到烧成质量的高低,对液相成分量的误差和偏差也具有重要影响,必须正确进行烧成液相量的计算。
在水泥熟料烧成液相量计算中,要把材料成分结构和实验反应性能作为水泥烧成液相量计算计算的重要依据。
熟料采用斗算法(Powell Algorithm)、分层搜索(Layer search)等算法,可以将熟料中实际测量成分和结构型结合,更快捷、更准确的计算出烧成液相的量。
另外,在水泥熟料烧成液相量的计算过程中,要考虑到熟料测定结果有干物质成分、水解液成分、颗粒残渣成分等,而烧成熟料中对液相成分量的准确测量也非常重要。
因此,为了确保熟料烧成液相量的准确性,应掌握熟料的细节特性,以便准确的进行计算。
最后,要进行水泥熟料烧成液相量计算,还必须加以相应的计算机支持,如运用多因素回归及神经网络等数据挖掘的技术对系统计算进行支持,使计算精确程度更大。
总之,要正确掌握水泥熟料烧成液相量的计算,还必须合理灵活运用计算机技术,以确保计算精准性。
水泥熟料的煅烧
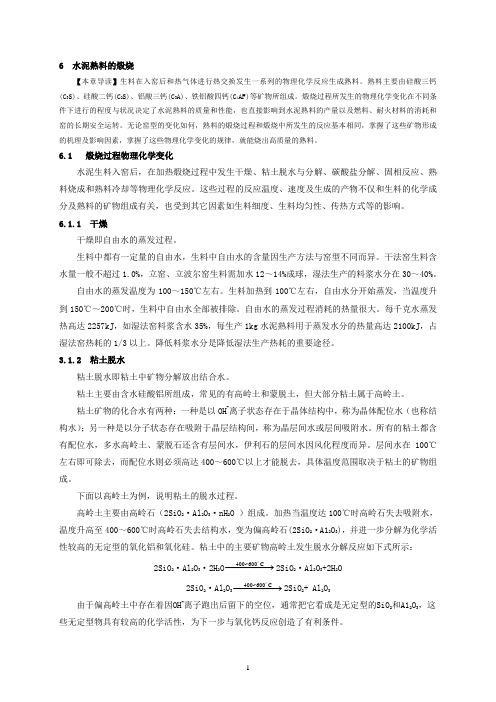
6 水泥熟料的煅烧【本章导读】生料在入窑后和热气体进行热交换发生一系列的物理化学反应生成熟料。
熟料主要由硅酸三钙(C 3S)、硅酸二钙(C 2S)、铝酸三钙(C 3A)、铁铝酸四钙(C 4AF)等矿物所组成。
煅烧过程所发生的物理化学变化在不同条件下进行的程度与状况决定了水泥熟料的质量和性能,也直接影响到水泥熟料的产量以及燃料、耐火材料的消耗和窑的长期安全运转。
无论窑型的变化如何,熟料的煅烧过程和煅烧中所发生的反应基本相同,掌握了这些矿物形成的机理及影响因素,掌握了这些物理化学变化的规律,就能烧出高质量的熟料。
6.1 煅烧过程物理化学变化水泥生料入窑后,在加热煅烧过程中发生干燥、粘土脱水与分解、碳酸盐分解、固相反应、熟料烧成和熟料冷却等物理化学反应。
这些过程的反应温度、速度及生成的产物不仅和生料的化学成分及熟料的矿物组成有关,也受到其它因素如生料细度、生料均匀性、传热方式等的影响。
6.1.1 干燥干燥即自由水的蒸发过程。
生料中都有一定量的自由水,生料中自由水的含量因生产方法与窑型不同而异。
干法窑生料含水量一般不超过1.0%,立窑、立波尔窑生料需加水12~14%成球,湿法生产的料浆水分在30~40%。
自由水的蒸发温度为100~150℃左右。
生料加热到100℃左右,自由水分开始蒸发,当温度升到150℃~200℃时,生料中自由水全部被排除。
自由水的蒸发过程消耗的热量很大。
每千克水蒸发热高达2257kJ ,如湿法窑料浆含水35%,每生产1kg 水泥熟料用于蒸发水分的热量高达2100kJ ,占湿法窑热耗的1/3以上。
降低料浆水分是降低湿法生产热耗的重要途径。
3.1.2 粘土脱水粘土脱水即粘土中矿物分解放出结合水。
粘土主要由含水硅酸铝所组成,常见的有高岭土和蒙脱土,但大部分粘土属于高岭土。
粘土矿物的化合水有两种:一种是以OH -离子状态存在于晶体结构中,称为晶体配位水(也称结构水);另一种是以分子状态存在吸附于晶层结构间,称为晶层间水或层间吸附水。
硅酸盐水泥熟料的煅烧与冷却

熟料的冷却
液相和熟料的烧结
5.1.1 生料的干燥与脱水
干燥 自由水的蒸发。这一过程由于煅烧方式的不同
而有所差异。干法窑生料含水量一般不超过1.0%; 半干法立波尔窑和立窑为便于生料成球,通常含水 12-15%,半湿法立波尔窑过滤水分后的料块通常为 18-22%;湿法为保证料浆的可泵性则通常为30-40%。
(4)分解出的CO2,穿过CaO层面向表面扩散的传质过 程;
(5)表面的CO2向周围介质气流扩散过程
✓影响碳酸盐分解速率的因素
温度 随温度升高,分解速率常数和压力倒数差相)
K(1 — 1 )
p P0
式中: t—分解时间;K—分解常数;
P—CO2的分压;ε—分解率 d—生料等效粒径;
(单个颗粒碳酸盐分解动力学方程)
窑系统的CO2分压 通风良好, CO2分压较低,有利 于碳酸盐分解;
生料细度和颗粒级配 生料细度细,颗粒均匀,粗粒 少,分解速率快;
生料悬浮程度 生料悬浮分散良好,相对减小颗粒 尺寸,增大了传热面积,提高了碳酸盐分解速率;
石灰石的种类和物理性质 结构致密,结晶粗大的 石灰石,分解速率慢;
目的:回收熟料带走的热量,预热二次空气,提高窑 的热效率;改善熟料质量与易磨性;便于熟料 运输、贮存与粉磨。
熟料为何要急冷?
减少C3S分解;防止β-C2S向γ-C2S转化,提高熟料质量; 防止方镁石晶体长大,有利于水泥安定性;急冷熟料晶粒小, 活性高;C3A主要呈玻璃体,抗硫酸盐性能提高;易磨性好 等。
硅酸三钙的形成: C2 S CaO 液相 C3S
物理化学变化过程:随着时间延长和温度升高,液相 量逐渐增加,氧化钙、硅酸二钙 不断溶解、扩散,硅酸三钙晶核 不断形成,小晶体逐渐发育长大, 最终形成几十微米大小、结晶良 好的阿利特晶体。
第五章 熟料的煅烧
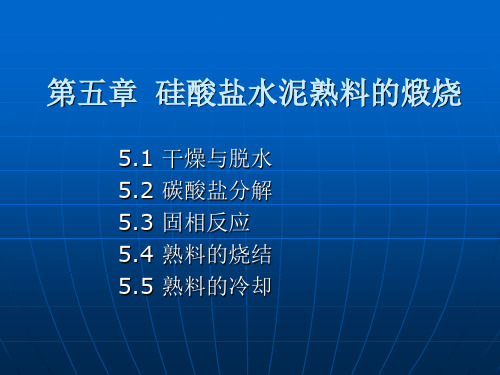
熟料煅烧
二、影响固相反应的主要因素 1. 生料的细度和均匀性
生料愈细,则其颗粒尺寸愈小,比表面积愈 大,各组分之间的接触面积愈大,同时表面的质 点自由能亦大,使反应和扩散能力增强,因此反 应速度愈快。但是,当生料磨细到一定程度后, 如继续再细磨,则对固相反应的速度增加不明显, 而磨机产量却会大大降低,粉磨电耗剧增。因此, 必须综合平衡,优化控制生料细度。生料的均匀 性好,即生料内各组分混合均匀,可以增加各组 分之间的接触,所以能加速固相反应。
由于熟料中还含有氧化镁、氧化钾、氧化钠等其 他成分,可以认为这些成分全部变成液相,因而 计算时还需要加氧化镁含量M与碱含量R,如:
1400℃ P=2.95A+2.2F+M+R 一般熟料在烧成阶段的液相量约为20%~30%, 而白水泥熟料由于Fe2O3含量低,烧成时液相量可 能只有15%左右。
三、液相粘度
其反应式如下:
C2S+CaO C3S
随着温度升高和时间的延长,液相量增加, 液相粘度减小,氧化钙、硅酸二钙不断溶解和扩 散,硅酸三钙不断形成,并使小晶体逐渐发育长 大,最终形成几十微米大小的发育良好的阿利特 晶体,完成熟料的烧结过程。
液相
硅酸盐水泥熟料
一、最低共熔温度
物料在加热过程中,两种或两种以上组分开 始出现液相的温度称为最低共熔温度。表4.1列出 一些系统的最低共熔温度(minimum eutectic temperature)。可知:组分性质与数目都影响系统的 最低共溶温度。硅酸盐水泥熟料由于含有氧化镁、 氧化钾、氧化钠、硫矸、氧化钛、氧化磷等次要 氧化物,因此其最低共熔温度约为1250~1280℃。 矿化剂和其他微量元素对降低共熔温度有一定作 用。
第五章 硅酸盐水泥熟料的煅烧
第五章 熟料的煅烧解读
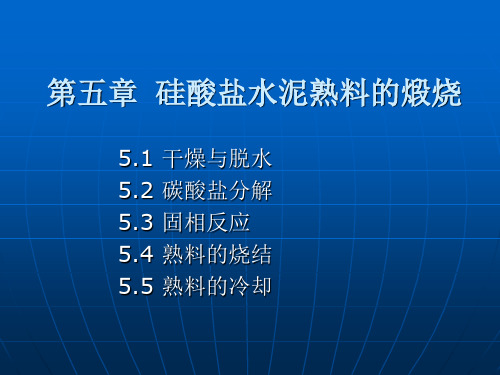
5.4 熟料的烧结
当物料温度升高到1250~1280℃时,即达到其 最低共熔温度后,开始出现以氧化铝、氧化铁和 氧化钙为主体的液相,液相的组分中还有氧化镁 和碱等。在高温液相的作用下,物料逐渐烧结, 并逐渐由疏松状转变为色泽灰黑、结构致密的熟 料,此过程伴随有体积收缩。同时,硅酸二钙和 游离氧化钙都逐步溶解于液相,以Ca2+离子扩散 与硅酸根离子反应,即硅酸二钙吸收氧化钙而形 成硅酸盐水泥熟料的主要矿物硅酸三钙。
(3)反应的起始温度较低,约在600℃时就有 CaCO3进行分解反应,但速度非常缓慢。至894℃ 时,分解放出的CO2分压达0.1MPa,分解速度加 快。1100~1200℃时,分解速度极为迅速。由试 验可知,温度每增加50℃,分解速度常数约增加1 倍,分解时间约缩短50%。
二、碳酸钙的分解过程
2.温度和时间
当温度较低时,固体的化学活性低,质点的扩 散和迁移速度很慢,因此固相反应通常需要在较 高的温度下进行。提高反应温度,可加速固相反 应。由于固相反应时离子的扩散和迁移需要时间, 所以,必须保证一定的时间才能使固相反应进行 完全。 3.原料性质
当原料中含有结晶SiO2(如燧石、石英砂等)和 结晶方解石时,由于破坏其晶格比较困难,所以 使固相反应的速度明显降低,特别是原料中含有 粗粒石英砂时,其影响更大。
熟料矿物C3A和C4AF及C2S的形成是一个复杂的多 级反应,反应过程是交叉进行的。熟料矿物的固 相反应是放热反应,当用普通原料时,固相反应 的放热量约为420~500kJ/kg。 由于固体原子、分子或离子之间具有很大的作用 力,因而,固相反应的反应活性较低,反应速度 较慢。通常,固相反应总是发生在两组分界面上, 为非均相反应。对于粒状物料,反应首先是通过 颗粒间的接触点或面进行,随后是反应物通过产 物层进行扩散迁移,因此,固相反应一般包括界 面上的反应和物质迁移两个过程。
水泥熟料煅烧的液相量以及液相黏度和烧结范围

一、液相量水泥熟料的主要矿物硅酸三钙是通过液相烧结进行的。
在高温液相作用下,硅酸二钙和游离氧化钙都逐步溶解于液相中,以离子的形式发生反应,形成硅酸三钙,水泥熟料逐渐烧结,物料由疏松状态转变为色泽灰黑、结构致密的熟料。
在硅酸盐水泥熟料中,由于含有氧化镁、氧化钠、氧化钾、硫酐、氧化钛等易熔物,其最低共熔温度约为1250℃。
随着温度的升高和时间的延长,液相量会增加,液相黏度会减小,使参与反应的离子更易扩散和结合,也就是说液相在熟料的形成过程中起着非常重要的作用,而且受到水泥熟料化学成分和烧成温度的影响。
既然液相量与化学成分有关,那么在配料上将如何控制呢?根据以往的经验,选定义为1450℃下(比较接近于生产实际)的液相量,液相量按下式计算:L=3.0A+2.25F+M+R式中,L、A、F、M、R分别表示水泥熟料的液相量、氧化铝、氧化铁、氧化镁、氧化钠和氧化钾的合量。
水泥熟料的烧成在现阶段的工艺条件下(预分解窑),液相量一般控制在20%-30%的范围内。
这个范围是对所有水泥厂而言的,就某个厂来讲显然是太宽了,各厂应根据自己的实际情况摸索出适合自己厂情的最佳控制范围。
液相量不仅和组分的性质有关,也与组分的含量、熟料烧结温度有关。
一般铝酸三钙(C3A)和铁铝酸四钙(C4AF)在1300℃左右时,都能熔成液相,所以称C3A与C4AF为熔剂性矿物,而C3A与C4AF的增加必须是Al2O3和Fe2O3的增加,所以熟料中Al2O3和Fe2O3的增加使液相量增加。
熟料中MgO、R2O等成分也能增加液相量,但MgO和R2O在含量较多时为有害成分,只有通过增加Al2O3和Fe2O3的含量增加液相量,才有利于C3S 的生成。
但液相量也不是越多越好,过多的液相量易导致结大块、结圈。
二、液相黏度液相黏度对硅酸三钙的形成影响较大。
黏度小,液相中质点的扩散速度增加,有利于硅酸三钙的形成。
液相黏度与液相组成有关,R2O含量的增加,液相黏度会增加,但MgO、K2SO4、Na2SO4、SO3含量增加,液相黏度会有所下降。
熟料煅烧中的有关问题的解析

有害组分 循环富集 硫碱比 失 调 局部温 度过高 外来物造 成的堵塞
漏
风
外 漏 风
喂 料 量 的 波 动 窑灰不均 匀 掺 入
结 皮 堵 塞
五、防止结皮堵塞的措施
• 1)减少或避免使用高硫和高氯的原料,这是减少 结皮的前提。 • 2)如过量的硫和氯难以避免,建议丢弃一部分窑 灰,以减少有害组分的循环。 • 3)采用旁路放风系统 。 • 4)避免使用高灰分及灰分熔点低的煤。 • 5)采用新型耐火材料,即在容易结皮的部位使用 抗结皮的耐火材料。 a:含ZrO2的耐火材料 ;b: 含石墨的耐火材料 。
重庆小南海水泥厂
水泥制造基础知识
——熟料煅烧中的有关问题的解析
二0一三年十一月
一、预分解窑结蛋机理分析
大 蛋 形 成 的 条 件
生料、燃料有害成 必要条件: 分含量高 煤粉的不完全燃烧 充分条件 :
其它条件:
配料方案不合理
入窑生料成分均匀性差
有害成分的循环:
内循环
液相开始 出现的温 度降低
促进
外循环
2、熟料圈的形成
在熟料煅烧过程中,当物料温度达到1280℃ 时,其液相粘度较大,熟料圈最易形成,冷却后比 较坚固,不易除掉,在正常煅烧情况下,熟料圈体 的内径部分,往往被烧熔而掉落,保持正常的圈 体内径。如果在1250~1280℃温度范围内出现 的液相量偏多,往往形成妨碍生产的熟料圈。熟 料圈一般结在烧成带的边界或更远,开始是烧成 带后边的窑皮逐渐增长,逐渐长厚,发展到一定 程度即形成熟料圈。严重熟料圈的窑皮长度有 的甚至长出正常窑皮长度的几倍。
粉 化
C2S多
生料过粗 固相反应不完全
(四)、放置一段时间后粉化原因:
①硫化亚铁水化 ②石灰的消解
熟料煅烧液相量与温度

熟料煅烧液相量与温度熟料的烧结在很大程度上取决于液相含量及其物理化学性质。
因此,控制液相出现的温度、液相量、液相粘度、液相表面张力和氧化钙、硅酸二钙溶于液相的速率,并努力改善它们的性质至关重要。
1.最低共熔温度系 统最低共熔温度(℃) 系 统最低共熔温度(℃) C 3S-C 2S-C 3A 1455 C 3S-C 2S-C 3A –C 4AF 1338 C 3S-C 2S-C 3A -Na 2O 1430 C 3S-C 2S-C 3A -Na 2O -Fe 2O 3 1315 C 3S-C 2S-C 3A -MgO 1375 C 3S-C 2S-C 3A -Fe 2O 3 -MgO 1300 C 3S-C 2S-C 3A-Na 2O-MgO1365C 3S-C 2S-C 3A-Na 2O-MgO -Fe 2O 31280表1 一些系统的量低共熔温度液相出现的温度决定于物料在加热过程中的最低共熔温度。
而最低共熔温度决定于系统组分的性质与数目。
表1列出了一些系统的最低共熔温度。
由表1可知,系统组分数目越多,其最低共熔温度越低,即液相初始出现的温度越低。
硅酸盐水泥熟料由于含有氧化镁、氧化钠、氧化钾、硫矸、氧化钛、氧化磷等次要氧化物,因此,其最低共熔温度约为1280℃左右,适量的矿化剂与其他微量元素等降低最低共熔温度,使熟料烧结时的液相提前出现。
如参加矿化剂后最低共熔温度约1250℃,即1250℃开始出现液相。
2.液相量如前所述,熟料的烧结必须要有一定数量的液相。
液相是硅酸三钙形成的必要条件,适宜的液相量有利于C 3S 形成,并保证熟料的质量。
液相量太少,不利于C 3S 形成,反之,过多的液相易使熟料结大块,给煅烧操作带来困难。
液相量与组分的性质、含量及熟料烧结温度等有关。
因此,不同的生料成分与煅烧温度等对液相量有很大影响。
一般水泥熟料烧成阶段的液相量大约为20%~30%。
(1)液相量与煅烧温度、组分含量有关,根据硅酸盐物理化学原理,不同温度下形成的液相量可按下式计算:①煅烧温度为1338℃时:IM(P)>1.38 L=6.1F(6.1)IM(P)<1.38 L=8.2A-5.22F(6.2)②煅烧温度为1400℃和1450℃时:1400℃L=2.95A+2.5F+M+R(6.3)1500℃L=3.0A+2.2F+M+R(6.4)式中L——液相量(%);F——熟料中Fe2O3的含量(%);A——熟料中Al2O3的含量(%);M、R——MgO及(Na2O+K2O)的含量(%)。
如何计算熟料烧成温度下的液相量
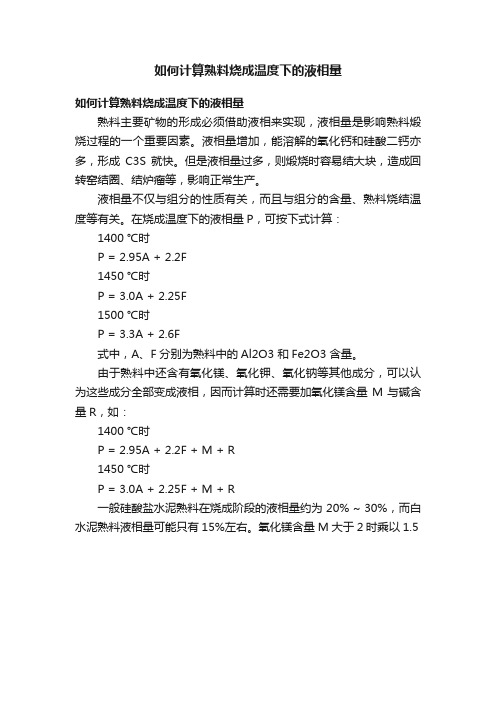
如何计算熟料烧成温度下的液相量
如何计算熟料烧成温度下的液相量
熟料主要矿物的形成必须借助液相来实现,液相量是影响熟料煅烧过程的一个重要因素。
液相量增加,能溶解的氧化钙和硅酸二钙亦多,形成C3S就快。
但是液相量过多,则煅烧时容易结大块,造成回转窑结圈、结炉瘤等,影响正常生产。
液相量不仅与组分的性质有关,而且与组分的含量、熟料烧结温度等有关。
在烧成温度下的液相量P,可按下式计算:
1400 ℃时
P = 2.95A + 2.2F
1450 ℃时
P = 3.0A + 2.25F
1500 ℃时
P = 3.3A + 2.6F
式中,A、F分别为熟料中的Al2O3 和Fe2O3 含量。
由于熟料中还含有氧化镁、氧化钾、氧化钠等其他成分,可以认为这些成分全部变成液相,因而计算时还需要加氧化镁含量M与碱含量R,如:
1400 ℃时
P = 2.95A + 2.2F + M + R
1450 ℃时
P = 3.0A + 2.25F + M + R
一般硅酸盐水泥熟料在烧成阶段的液相量约为20% ~ 30%,而白水泥熟料液相量可能只有15%左右。
氧化镁含量M大于2时乘以1.5。
普通配料的硅酸盐水泥熟料液相出现的温度
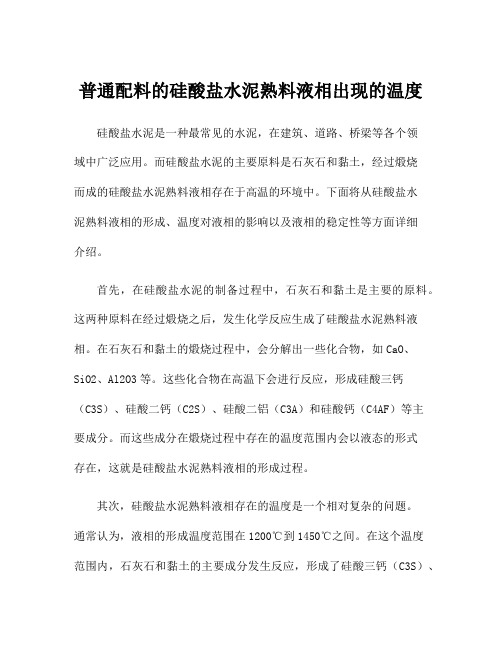
普通配料的硅酸盐水泥熟料液相出现的温度硅酸盐水泥是一种最常见的水泥,在建筑、道路、桥梁等各个领域中广泛应用。
而硅酸盐水泥的主要原料是石灰石和黏土,经过煅烧而成的硅酸盐水泥熟料液相存在于高温的环境中。
下面将从硅酸盐水泥熟料液相的形成、温度对液相的影响以及液相的稳定性等方面详细介绍。
首先,在硅酸盐水泥的制备过程中,石灰石和黏土是主要的原料。
这两种原料在经过煅烧之后,发生化学反应生成了硅酸盐水泥熟料液相。
在石灰石和黏土的煅烧过程中,会分解出一些化合物,如CaO、SiO2、Al2O3等。
这些化合物在高温下会进行反应,形成硅酸三钙(C3S)、硅酸二钙(C2S)、硅酸二铝(C3A)和硅酸钙(C4AF)等主要成分。
而这些成分在煅烧过程中存在的温度范围内会以液态的形式存在,这就是硅酸盐水泥熟料液相的形成过程。
其次,硅酸盐水泥熟料液相存在的温度是一个相对复杂的问题。
通常认为,液相的形成温度范围在1200℃到1450℃之间。
在这个温度范围内,石灰石和黏土的主要成分发生反应,形成了硅酸三钙(C3S)、硅酸二钙(C2S)、硅酸二铝(C3A)和硅酸钙(C4AF)等化合物。
而在这些温度下,这些化合物以液态的形式存在,并随烧结时间的延长而逐渐增多。
液相的形成温度取决于原料的成分和配比,以及烧结温度和时间的控制等因素。
此外,温度对硅酸盐水泥熟料液相的形成和性质也有着重要的影响。
首先,较高的温度有利于液相的形成,因为高温可以促进原料的化学反应。
而在过高的温度下,液相的形成可能过于充分,会导致液相的增加和黏土煅烧不完全。
其次,液相的形成和稳定也受温度的影响。
在较低的温度下,液相的形成可能不充分,导致熟料中存在较多的未反应的石灰石和黏土。
而在过高的温度下,液相的稳定性可能受到影响,使液态的成分变得不稳定,甚至形成异常相。
最后,硅酸盐水泥熟料液相的稳定性也是一个重要的问题。
液相中的主要成分是硅酸三钙(C3S)、硅酸二钙(C2S)、硅酸二铝(C3A)和硅酸钙(C4AF),其中硅酸三钙(C3S)和硅酸二铝(C3A)是最主要的成分。
普通配料的硅酸盐水泥熟料液相出现的温度

普通配料的硅酸盐水泥熟料液相出现的温度摘要:I.引言- 介绍硅酸盐水泥熟料液相的概念II.液相出现的温度- 普通配料的硅酸盐水泥熟料液相出现的温度- 影响液相出现的温度因素III.液相在硅酸盐水泥熟料中的作用- 液相对水泥熟料性能的影响- 液相对水泥生产过程的重要性IV.液相出现温度的控制- 控制液相出现温度的方法- 液相出现温度对水泥质量的影响V.结论- 总结液相出现的温度对硅酸盐水泥熟料的重要性正文:硅酸盐水泥熟料的生产过程中,液相的出现是一个关键环节。
液相是指在高温下,水泥熟料中的一部分矿物质发生熔融形成的液态物质。
液相对水泥熟料的性能有着重要影响,因此,了解液相出现的温度对于控制水泥熟料的质量和性能至关重要。
普通配料的硅酸盐水泥熟料液相出现的温度一般在1300℃左右,但这个温度也会受到配料成分、煅烧过程等因素的影响。
例如,当配料中硅酸盐的含量较高时,液相出现的温度会相应提高。
此外,煅烧过程中温度的变化也会对液相出现的温度产生影响。
液相在硅酸盐水泥熟料中的作用主要体现在对水泥熟料性能的影响。
液相可以填充水泥熟料的微观孔隙,改善其颗粒分布,从而提高水泥的强度和抗渗性能。
此外,液相还可以与水泥熟料中的其他矿物发生反应,进一步提高水泥的性能。
要控制液相出现的温度,需要合理调整配料成分和煅烧工艺。
如果液相出现的温度过高,会导致水泥熟料中的矿物质烧结不充分,影响水泥的强度和抗渗性能。
反之,如果液相出现的温度过低,液相的产生量会减少,同样会影响水泥的性能。
总之,液相出现的温度对硅酸盐水泥熟料的质量和性能具有重要影响。
普通配料的硅酸盐水泥熟料液相出现的温度

普通配料的硅酸盐水泥熟料液相出现的温度
摘要:
1.硅酸盐水泥的简介
2.硅酸盐水泥熟料液相出现的温度
3.影响温度的因素
4.结论
正文:
硅酸盐水泥是一种广泛应用于建筑业的基本建材,它是由水泥熟料、石膏和少量混合材料磨制而成的。
在水泥生产过程中,熟料的液相温度是一个非常重要的参数。
那么,普通配料的硅酸盐水泥熟料液相出现的温度是多少呢?
硅酸盐水泥熟料液相出现的温度一般在1300-1500 摄氏度之间。
这个温度范围是根据我国硅酸盐水泥生产工艺和设备水平得出的。
在这个温度范围内,熟料中的矿物成分会发生一系列物理和化学变化,使其具有较高的强度和耐久性。
然而,硅酸盐水泥熟料液相出现的温度受到多种因素的影响,如原料的矿物组成、烧结温度、燃料种类等。
不同的原料矿物组成会影响熟料的矿物相形成和温度分布;烧结温度过高或过低都会使熟料矿物结构发生变化,从而影响液相温度;燃料种类的燃烧特性也会对熟料液相温度产生影响。
综上所述,普通配料的硅酸盐水泥熟料液相出现的温度一般在1300-1500 摄氏度之间,但具体温度会受到原料矿物组成、烧结温度、燃料种类等多种因素的影响。
水泥熟料烧成液相量的计算探讨

水泥熟料烧成液相量的计算探讨
高锦明
【期刊名称】《水泥技术》
【年(卷),期】1993(000)006
【摘要】水泥生料在煅烧过程中,首先进行原料的脱水分解,随着温度不断提高,在1300℃以前,原料中各种氧化物通过固相反应形成C_2S、C_3A、C_4AF等矿物,而熟料中的主要矿物C_3S依靠固相反应形成的量极少,它主要通过液相形成。
熟料烧成过程的主要特征是出现液相,并使C_2S+CaO=C_3S的反应得以顺利进行,因此熟料烧成中液相生成温度、液相量和液相的性质,对C_3S的形成有很大影响。
1 液相量水泥熟料烧成时,当加热温度达到物料中各氧化物所形成的最低共熔点时,就开始出现液相,而液相出现的温度和组成决定于生料的成分。
【总页数】3页(P46-47,51)
【作者】高锦明
【作者单位】无
【正文语种】中文
【中图分类】TQ172.621
【相关文献】
1.微波强化烧成铝酸盐水泥熟料的探讨 [J], 董健苗;龙世宗
2.关于水泥熟料烧成系统操作新技术的探讨 [J], 刘振海
3.水泥熟料烧成系统电耗分析探讨 [J], 殷昭波
4.水泥熟料快速烧成技术(升级)暨水泥熟料快烧矿化剂技术 [J], 杨洪
5.铝率及液相性质对高硅酸三钙含量硅酸盐水泥熟料烧成过程的影响 [J], 郭随华;陈益民;管宗甫;秦守婉;韦江雄;唐润荣;周瑾
因版权原因,仅展示原文概要,查看原文内容请购买。
水泥熟料煅烧
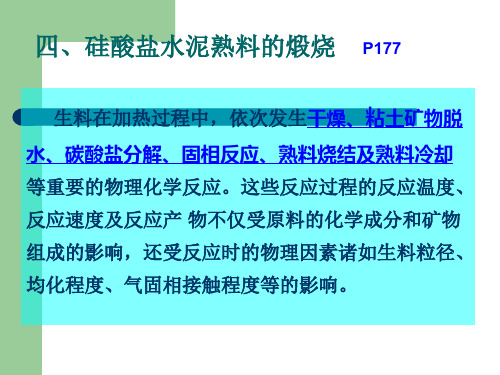
③.原料性质
当原料中含有如燧石、石英砂等结晶SiO2或方解石结 晶粗大时,因破坏其晶格困难,所以固相反应的速率明显降 低,特别是当原料中含有粗粒石英砂时,其影响更大。
5. 熟料烧结
当物料温度升高到1250-1280℃时,即达到其最低共熔 温度,开始出现以氧化铝、氧化铁为主的液相,液相的组分 中还有氧化镁和碱等。
2C+A+S
C2AS
C2AS形成后又分解
C12A7+9C
7C3A
C3A开始形成
C2F+2C+C12A7
7C4AF C4AF开始形成
1100-1200℃:大量形成C3A、C4AF,C2S含量达最大值
4. 固相反应
----放热反应
反应过程
约800℃:开始形成CA、CF与C2S; 800-900℃:开始形成C12A7 、C2F ; 900-1100℃:C2AS形成后又分解、C3A、C4AF开始形 成
----放热反应
反应过程
熟料形成过程的固相反应过程大致如下:
约800℃:开始形成CA、CF与C2S;
C+A
CA
C+F
CF
2C+S
C2S
C2S开始形成
800-900℃:开始形成C12A7、C2F;
7CA+5C
C12A7
4. 固相反应
----放热反应
反应过程
约800℃:开始形成CA、CF与C2S; 800-900℃:开始形成C12A7 、C2F ; 900-1100℃:
生料的均匀性好,即生料内各组分混合均匀,这就可以 增加各组分之间的接触,所以能加速固相反应。
4. 固相反应
----放热反应
影响固相反应的主要因素
①.生料的细度和均匀性
- 1、下载文档前请自行甄别文档内容的完整性,平台不提供额外的编辑、内容补充、找答案等附加服务。
- 2、"仅部分预览"的文档,不可在线预览部分如存在完整性等问题,可反馈申请退款(可完整预览的文档不适用该条件!)。
- 3、如文档侵犯您的权益,请联系客服反馈,我们会尽快为您处理(人工客服工作时间:9:00-18:30)。
熟料煅烧液相量与温度
熟料的烧结在很大程度上取决于液相含量及其物理化学性质。
因此,控制液相出现的温度、液相量、液相粘度、液相表面张力和氧化钙、硅酸二钙溶于液相的速率,并努力改善它们的性质至关重要。
1.最低共熔温度
最低共熔温
系统最低共熔温
系统度(C)度(C)C3S-C2S-C3A1455GS-C2S-C3A - C4AF1338 C3S-C2S-C3A -Na 2O1430C3S-C2S-C3A -Na 2O -Fe 2O31315 C3S-C2S-C3A -MgO1375C3S-C2S-C3A -Fe 2O3 -MgO1300 C3S-C2S-C3A-Na2O-MgO1365C3S-C2S-C3A-Na 2O-MgO -Fe 2O31280
表1 一些系统的量低共熔温度
液相出现的温度决定于物料在加热过程中的最低共熔温度。
而最低共熔温度决定于系统组分的性质与数目。
表1 列出了一些系统的最低共熔温度。
由表1 可知,系统组分数目越多,其最低共熔温度越低,即液相初始出现的温度越低。
硅酸盐水泥熟料由于含有氧化镁、氧化钠、氧化钾、硫矸、氧化钛、氧化磷等次要氧化物,因此,其最低共熔温度约为1280C左右,适量的矿化剂与其他微量元素等降低最低共熔温度,使熟料烧结时的液相提前出现。
如参加矿化剂后最低共熔温度约1250C,即1250C开始出现液相。
2.液相量
如前所述,熟料的烧结必须要有一定数量的液相。
液相是硅酸三钙形成的必要条件,适宜的液相量有利于GS形成,并保证熟料的质量。
液相量太少,不利于C3S形成,反之,过多的液相易使熟料结大
块,给煅烧操作带来困难。
液相量与组分的性质、含量及熟料烧结温度等有关。
因此,不同的生料成分与煅烧温度等对液相量有很大影响。
一般水泥熟料烧成阶段的液相量大约为20%- 30%
(1) 液相量与煅烧温度、组分含量有关,根据硅酸盐物理化学原理,不同温度下形成的液相量可按下式计算:
①煅烧温度为1338 C时:
IM(P) >1.38 L=6.1F(6.1)
IM(P) <1.38 L=8.2A-5.22F(6.2)
②煅烧温度为1400C和1450C时:
1400C L=2.95A+2.5F+M+R(6.3)
1500C L=3.0A+2.2F+M+R(6.4)
式中L――液相量(%);
F――熟料中Fe2O的含量(%);
A――熟料中Al 203的含量(%);
M RMgO及(Na z O+KO)的含量(%)。
(2) 液相量随熟料中铝率而变化,一般硅酸盐水泥在煅烧阶段的液相量随铝率和温度的变化情况见表2所示。
生产中,应合理设计熟料化学成分与率值,控制煅烧温度在一个适当的范围内。
这个范围大体上是出现烧结所必需的最少的液相量时的温度到出
现结大块时的温度之间,即通常所说的烧结范围。
就硅酸盐水泥而言,烧结范围约150C左右。
当系统液相量随温度升高而缓慢增加,其烧结范围就较宽;反之,其烧结范围就窄。
例如,硅酸盐水泥中含铁量较低,该系统的烧结范围就较宽;若含铁量较高,其烧结范围就较窄。
过窄的烧结范围对煅烧操作的控制是不利的。
表2 熟料中液相量随铝率和温度的变化情况
温度(°C)
2.0IM(P)=Al 2Q3/Fe 2Q3
1.250.64
133818.321.10
140024.323.622.4
145024.824.022.9
3.液相粘度
液相粘度对硅酸三钙的形成影响较大。
粘度小,液相中质点的扩散速度增加,有利于硅酸三钙的形成。
而液相的粘度又随温度与组成( 包括少量氧化物) 而变化。
提高温度,液相内部质点动能增加,削弱了相互间作用力,因而降低了液相粘度。
改变液相组成时,随着液相中离子状态和相互作用的变化液相粘
度相应发生改变。
由于Al'+离子半径为0.057卩m Fe3+离子半径为0.067卩m因而Al3+趋向于构成紧密堆积的四面体并与4个0+离子配位,价键较强,粘滞流动中不易断裂,从而粘度高。
Fe3+趋向于构成
疏松的八面体以六配位存在,其价键较弱,粘滞流动中易于断裂,因而粘度较低。
故提高铝率时,液相粘度增大,而降低铝率则液相粘度减少。
MgO SO的存在可使液相粘度降低。
而碱的作用与其形态、性质有关,NaO K2O 使液相粘度增大,而NaSQ或&SQ则使液相粘度降低。
此外,引入适量的
微量组分如氟化物,特别是石膏、萤石这类复合组分可降低液相粘度,但微量组分间的含量配合不当或加入量过多
反而使液相变稠,不利于熟料烧结
4.液相的表面张力
液相的表面张力愈小,愈易润湿固相物质或熟料颗粒,有利于固液反应,促进C3S 的形成。
液相的表面张力与液相温度、组成和结构有关。
液相表面张力随温度的升高而降低。
液相中有镁、碱、硫等物质存在时,可降低液相的表面张力,从而促进熟料烧结。
5.氧化钙和硅酸二钙溶于液相的速率
C 3S的形成过程也可以视为CaO和C2S在液相中的溶解过程。
CaO 和C2S 的溶解速率大,C3S 的成核与发育越快。
因此,要加速C3S 的形成实际上就是提高CaO与GS的溶解速率,而这个速率大小受CaO颗粒大小和液相粘度所控制。
表3为实验室条件下,不同粒径CaO在不同温度下完全溶于液相所需的时间。
表3 CaO 溶于液相所需的时间(min )
温度(c )
0.1粒径(mm)
0.050.0250.001
134011.5592512
1375281464 140015 5.53 1.5
14505 2.310.5 1500 1.8 1.7。