解决铸件缩松的方法
铸件缩孔、缩松有何区别?如何解决?

铸件缩孔、缩松有何区别?如何解决?在铸造⽣产中,铸件⽓孔和铸件缩孔有时是伴⽣的,有时是独⽴存在。
当出现⽓孔和缩孔时,我们要快速的判断出缺陷是⽓孔还是缩孔对于解决问题⼗分必要。
⽓孔类缺陷与防治⽅法在铸造⽣产中,孔洞类缺陷是常见缺陷,也是给铸造⼚造成损失⽐较⼤的缺陷之⼀。
孔洞类缺陷分为⽓孔和缩孔。
⽓孔多为由于⾦属液中侵⼊、裹⼊、卷⼊⽓体所⾄。
铸件⽓孔出现在铸件上的位置不同,其产⽣的原因也不同。
这就要求我们的铸造技术员在判断⽓孔缺陷病因时,要掌握各类⽓孔发⽣的原理,具有什么样的特征。
只有如此才能对症下药,将出现的⽓孔缺陷解决掉。
⽓孔特征:(1)卷⼊⽓孔:⾦属液在充型过程中因卷⼊⽓体⽽在铸件内形成⽓孔,多呈孤⽴存在的圆形或椭圆形⼤⽓孔,位置不固定,⼀般偏铸件中上部。
(2)侵⼊⽓孔:由型、芯、涂料、芯撑、冷铁产⽣的⽓孔侵⼊铸件表层⽽形成⽓孔,多呈梨形或椭圆形,尺⼨较⼤,孔壁光滑,表⾯多呈氧化⾊。
(3)反应⽓孔:由⾦属液内部某些成分之间或⾦属液与型、芯在界⾯上发⽣化学反应⽽形成群分布的⽓孔。
位于铸件表层的针头形或腰圆形反应⽓孔称为表⾯针孔与⽪下⽓孔,由⾦属液与型、芯涂料发⽣界⾯反应所⾄;分散或成群分布在铸件整个断⾯上或某个局部区域的针头反应⽓孔。
形成原因:(1)由于炉料潮湿、锈蚀、油污、⽓候的潮湿,熔练⼯具和浇包未烘⼲,⾦属液成分不当,合⾦液为精炼与精炼不⾜,使⾦属液中含有⼤量⽓体或⽓体物质,导致在铸件中析出⽓孔或反应⽓孔。
(2)型、芯未充分烘⼲,透⽓性差,通⽓不良,含⽔分和发⽓物质过多,涂料未烘⼲或含发⽓成分过多,冷铁、芯撑有锈斑、油污或未烘⼲,⾦属型排⽓不良,在铸件中形成侵⼊⽓孔。
(3)浇注系统不合理,浇注和充型速度过快,⾦属型排⽓不良,使⾦属液在浇注和充型过程中产⽣紊流、涡流或断流⽽卷⼊⽓体,在铸件中形成卷⼊性⽓孔。
(4)合⾦液易可吸⽓,在熔炼和浇注过程中未采取有效的精炼、保护和净化措施,使⾦属液中含有⼤量⽓体、夹渣和夹⽓成分,在充型和凝固过程中形成析出⽓孔和反应⽓孔。
球墨铸铁铸件缩松缺陷怎样防治?

球墨铸铁铸件缩松缺陷怎样防治?球墨铸铁铸造生产中经常遇到缩松方面的质量问题,于是就学习,就在实际工作中去想办法解决。
很多时候,通过学习解决了一些问题,也有难以解决的缩松现象。
最近看见了周启明老师的文章和陈子华的报告,结合之前实际工作,汇总以下。
一.影响球铁缩松的一般规律:1.球墨铸铁铸件的模数。
铸件模数大于2.5,容易实现无冒口铸造,但有专家对此规定限制值,有疑问。
一般来讲,比较厚大铸件,由于石墨化膨胀,容易铸造无缩松铸件。
此时,碳当量控制不要大于4.5%,避免石墨漂浮。
而热节分散的薄小铸件,容易产生缩松,通过冷铁,铬矿砂或局部内冒口设置解决。
特别要注意浇冒口系统的补缩,一般来讲,冒口尽可能使用热冒口,避免冷冒口使用。
2.要充分注意砂箱的刚度和砂型的硬度。
在砂箱刚度和砂型紧实度方面,设置再充分都不为过。
3.浇冒口工艺设计的合理性。
尽可能使用热冒口加冷铁,冷冒口补缩效果很差。
4.铸型的冷却速度。
5.浇注温度和浇注速度的合理选择。
一些比较厚的铸件,可以考虑适当调高浇注温度,同时延长浇注速度来解决缩松。
同时利于二次氧化渣浮出铸件内部,增加探伤检测的合格。
6.化学成分的合理选择和适当的残余镁,稀土含量。
7.在砂型冷却条件下,争取较多的石墨球数对减少缩松有利,对提高力学性能有利。
8.比较好的原材料和好的铁水冶金质量,要特别注意铁水不要在出炉前高温下保持时间过久,同时出炉前做好增加铁水石墨结晶核心的预处理,这样可以提高石墨球数,减少缩松。
二.新的减少缩松的观点:1.埃肯陈子华总监最近报告指出:球墨铸铁因为铁水含有镁,促使状态图上共晶点右移,镁含量在0.035-0.045%时,其实际共晶点大约在4.4-4.5%。
2.球铁成分选择在共晶点附近,铁水流动性最好,则凝固时铁水容易补充收缩。
3.球铁球化前后的硫含量不要变化太大。
即原铁水硫含量不要太高。
硫含量高,石墨容易析出过早。
容易产生缩松。
4.锡柴周启明老师今年文章“防止球墨铸铁缩松缩孔方法的新进展”中指出:在不发生石墨漂浮和没有初生石墨析出前提下,尽量提高碳含量。
铸件缩孔缩松产生的原因

铸件缩孔缩松产生的原因
一、金属铸件缩孔缩松的原因
1、模具质量不合格:模具的表面没有经过预处理,工作表面毛糙度不够,加工精度不高,导致熔模渗入的位置不正确,从而影响铸件缩孔的精度。
2、砂芯质量不合格没有经过预处理或抛光处理,表面毛糙度不均,加工精度低,砂芯内部出现裂纹,导致不同部位的造型不稳定,从而影响铸件缩孔的精度。
3、工艺条件不合理:模具配套不当,熔模温度过高或过低,模具保温不足,充型压力不足,熔模渗入缓慢,从而影响铸件缩孔的精度。
4、冷却不当:铸件出模后,冷却时间过长或过短,容易出现开裂现象,从而影响铸件缩孔的精度。
二、金属铸件缩孔缩松的改善措施
1、严格模具质量:采用高强度的整体钢,并且经过精密加工,表面经过研磨抛光,以保证熔模渗入的位置准确,从而提高铸件缩孔的精度。
2、严格砂芯质量:采用高质量的砂芯,经过彻底的预处理,能够保证砂芯表面毛糙度均匀,加工精度高,避免出现裂纹,从而确保缩孔的精度。
3、调整熔模温度:严格控制熔模的温度,熔模温度过高可以导致金属分子值过大,熔态液体容易流失。
分析铸造缩松缺陷形成原因及对策

分析铸造缩松缺陷形成原因及对策铸造缩孔缺陷是在铸造过程中常见的一种问题,它会给制造业带来很多麻烦和损失。
本文将分析铸造缩孔缺陷的形成原因,并提出相应的对策,以期为相关行业提供帮助和指导。
一、铸造缩孔缺陷的形成原因分析1.1 完全凝固不均匀在铸造过程中,铸件凝固是逐渐进行的,如果凝固速度不均匀,就会导致缩孔缺陷的形成。
常见的原因包括铸件的凝固时间过短、冷却速度不均匀、局部温度过高等。
1.2 金属液收缩过大铸造过程中,金属液在凝固过程中会收缩,如果收缩过大,就容易形成缩孔。
这主要是由于铸件材料的物理性质不合理,或者是铸型的设计不合理所导致的。
1.3 铸造材料含有气体铸造材料中含有气体会在凝固过程中释放出来,如果释放过快,就会形成孔洞。
常见的原因是铸造材料中含有气体的含量过高,或者是在铸造过程中没有采取有效的排气措施。
1.4 基材与液态金属的相容性差如果铸件的基材与液态金属的相容性差,就容易在凝固过程中产生裂纹和缩孔。
一般来说,基材与液态金属的相容性差会导致界面张力增大,从而影响凝固过程。
二、对策提出2.1 优化铸造工艺参数通过优化铸造工艺参数,可以降低缩孔缺陷的发生概率。
具体来说,可以调整金属液的浇注温度和速度,控制铸件的凝固时间,改进冷却系统等措施。
2.2 优化铸造材料选择合适的铸造材料也是减少缩孔缺陷的关键。
应选择具有较低的收缩率和较好的流动性的材料,以确保凝固过程中的收缩程度可控。
2.3 采取有效的排气措施在铸造过程中,采取有效的排气措施可以减少气体对铸件凝固过程的干扰,从而降低缩孔缺陷的风险。
排气措施可以包括加入剂、提高浇注温度、采取适当的连续浇注等。
2.4 提高基材与液态金属的相容性为了减少缩孔缺陷的形成,可以通过提高基材与液态金属的相容性来增加界面的稳定性。
可以通过改变基材化学成分、调整金属液的配方等方式来实现。
三、结语以上是对铸造缩孔缺陷形成原因及对策的分析。
通过优化铸造工艺、材料选择、排气措施以及提高基材与液态金属的相容性等方法,可以有效降低缩孔缺陷的发生概率,提高铸件的质量和产能。
铸铁件缩松、缩孔、凹陷缺陷的原因分析与防止方法
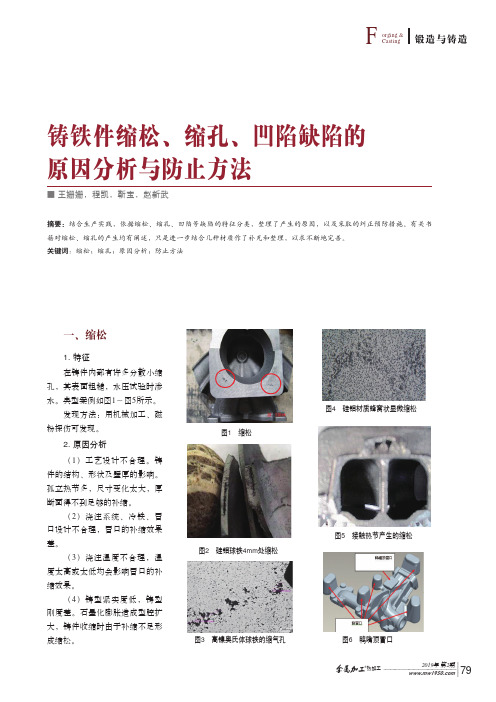
2019年第2期热加工79F锻造与铸造orging &Casting铸铁件缩松、缩孔、凹陷缺陷的原因分析与防止方法■王姗姗,程凯,靳宝,赵新武摘要:结合生产实践,依据缩松、缩孔、凹陷等缺陷的特征分类,整理了产生的原因,以及采取的纠正预防措施。
有关书籍对缩松、缩孔的产生均有阐述,只是进一步结合几种材质作了补充和整理,以求不断地完善。
关键词:缩松;缩孔;原因分析;防止方法一、缩松1. 特征在铸件内部有许多分散小缩孔,其表面粗糙,水压试验时渗水。
典型案例如图1~图5所示。
发现方法:用机械加工、磁粉探伤可发现。
2. 原因分析(1)工艺设计不合理。
铸件的结构、形状及壁厚的影响。
孤立热节多,尺寸变化太大,厚断面得不到足够的补缩。
(2)浇注系统、冷铁、冒口设计不合理,冒口的补缩效果差。
(3)浇注温度不合理,温度太高或太低均会影响冒口的补缩效果。
(4)铸型紧实度低,铸型刚度差。
石墨化膨胀造成型腔扩大,铸件收缩时由于补缩不足形成缩松。
图1 缩松图2 硅钼球铁4mm处缩松图4 硅钼材质蜂窝状显微缩松图3 高镍奥氏体球铁的缩气孔图5 接触热节产生的缩松图6 鸭嘴顶冒口2019年 第2期 热加工80F锻造与铸造orging &Casting(5)碳、硅含量低,磷含量较高;凝固区间大。
硅钼和高镍球墨铸铁对碳、硅含量和氧化铁液的敏感性特大,铁液严重氧化或碳、硅量低时,易出现显微缩松。
即便在薄壁处也容易出现缩松(见图2、图3、图4)。
(6)孕育不充分,石墨化效果差。
(7)残余镁量和稀土量过高。
钼含量较高时也会增加显微缩松。
(8)浇注速度太快。
(9)炉料锈蚀,氧化铁多。
(10)铁液在电炉内高温停放时间太长,俗称“死铁水”,造成严重氧化。
(11)冲天炉熔炼时底焦太底,风量太大,元素烧损大,铁液严重氧化。
(12)冒口径处形成接触热节产生缩松(见图5)。
(13)压箱铁不够(或箱卡未锁紧,箱带断裂等),浇注后由于涨箱造成缩松。
球墨铸铁铸件的补缩工艺[1]
![球墨铸铁铸件的补缩工艺[1]](https://img.taocdn.com/s3/m/95563257ad02de80d4d84021.png)
收稿日期:2010-09-19; 修订日期:2010-10-20作者简介:牟行辉(1974- ),四川射洪人,工程师.从事铸铁件铸造工艺设计和质量控制工作.Email:m u_xinghu i@V ol.32N o.1Jan.2011铸造技术F OU N DRY T ECH NO LO GY工艺技术 Technology球墨铸铁铸件的补缩工艺牟行辉(陕西秦川机床工具集团有限公司,陕西宝鸡721009)摘要:通过分析和总结在生产实践过程中球墨铸铁铸件产生缩孔缩松缺陷以及成功解决办法,对球铁铸件凝固收缩理论提出理解和看法:铸件的补缩及缺陷产生取决于压力,由于球铁的凝固特性使石墨化膨胀和凝固收缩分离,薄壁件截面凝固差异不明显,石墨化膨胀压力无法有效利用,厚大件的截面凝固的差异大,容易实现石墨化膨胀压力的利用。
铸造补缩工艺的设计原则就是提供并保持这样的压力,对薄壁要强调外部压力补缩,厚壁则充分利用石墨化膨胀压力自补缩。
关键词:球墨铸铁;缩孔缩松;补缩;凝固压力中图分类号:TG255 文献标识码:A 文章编号:1000-8365(2011)01-0007-04Feeding Process of the Ductile Iron CastingsMU Xing -hui(Qinchuan Machine Tool Group C orp.,Baoji 721009,C hina)Abstract:By analyzing and summ arizin g the process of practice in the production of du ctile iron castings produ ced Shrinkage Defects an d successful solution.Make to some un derstand an d view of du ctile iron castings solidification theory:Feeding a castin g depend upon the pressure.For the solidification ch aracteristic of th e sph eroidal graph ite cast iron,th e expan sion of the graphitization are not syn chronized shrin k.In thin wall,no fu nction of the the expansion pressure of the graphitization because fewer division of solidification,and the thick wall,the more division with solidification in section,so th e expan sion and the shrink will be segistration.So the inten tion of the feeding process disign are su pporting and keepin g on pressu re.Th e th in wall,pressu re shall be su pported with others,and the thick wall,th e pressu re maybe exploit th e th e the expansion of the graphitization.Key words:Du ctile C ast Iron;Shrinkage;Feedin g;Solidification Pressure1 球铁凝固收缩工艺理论对球墨铸铁件采用什么样的工艺措施解决和防止缩孔缩松,目前的共识是,铸型必须具有足够的刚性和强度,化学成分接近共晶成分、加强球化和孕育处理以产生足够的石墨化膨胀。
304不锈钢熔模铸造中缩孔、缩松的几种防止措施

熔模铸造中缩松的几种特有解决方案
缩松是铸造最常见的缺陷之一,是铸件在冷却过程中热节或远浇口部位得不到有效的补缩而产生的细小分散的孔洞。
熔模铸造因为热壳浇注的特点,在浇注系统设计时大大地限制了冒口、冷铁对于缩松的处理,但是却有一系列独特的解决方案。
1、型壳底部淬水
部位:铸件浇注位置底部。
铸件浇注位置底部远离浇冒口,补缩通道过长,如果铸件较高或底部有热节,就容易产生缩松。
原理:通过淬水使型壳底部温度迅速降低,对铸件起到底部激冷的作用。
操作:热壳浇注后,型壳立刻淬水,视铸件薄厚在水中停顿1-3秒,深度为易缩松的位置。
案例1圆环产品,材质304不锈钢,浇注温度1640℃
此产品组树后高度方向尺寸较大,见图1和图2,浇注后于圆环浇注位置的下半圆A处容易出现缩松,如图1,经分析认为补缩通道过长导致下半圆凝固时钢水得不到有效补缩,从而产生缩松。
工艺改进为型壳底部淬水,深度如图2所示,效果良好,基本解决下半圆的缩松问题。
图1 圆环剖面图图2 圆环组树淬水示意图
2、喷水激冷
3、局部补砂泥
4、中空型壳
5、加保温棉
6、工艺散热冷铁
7、冷铁、热贴。
铸件缩孔和缩松缺陷十点分析

铸件缩孔和缩松缺陷十点分析缩孔和缩松都是铸造生产中常见的铸件缺陷。
缩孔是铸件在冷凝过程中收缩,得不到金属溶液的补充而产生的孔洞,形状不规则,孔壁粗糙,一般位于铸件的热节处。
缩孔和气孔在外表上往往极为相似,经常容易混淆。
一般来说,气孔的内壁是平滑的,而缩孔的内壁则呈枝状结晶的末梢状。
缩松是铸件最后凝固的区域没有得到金属溶液的补缩而形成分散和细小的小孔,常出现在铸件的较厚截面以及厚薄截面交接处或热节点上。
缩松的分布面积要比缩孔大得多,往往隐藏于铸件的内部,有时肉眼察觉不到。
缩孔和缩松在铸件废品中占有较大的比例,必须引起足够的重视,以提高铸件合格率。
笔者结合多年的生产实践经验,谈谈铸件缩孔和缩松的产生原因及其防止措施。
1.铸件和模样设计(1)铸件截面尺寸变化过大。
如果在设计中铸件截面尺寸变化过大,薄截面的冷却速度比相邻厚截面的冷凝速度要快得多,这样就很难实现铸件的顺序凝固,同时也难于进行补缩。
设计时要尽量避免这种情况,否则应采用冷铁,以实现铸件的顺序凝固并利于补缩。
(2)铸件断面过厚,如果没有采取相应措施对其进行补缩,会因补缩不良形成缩孔。
(3)圆角太小。
铸件的凹角圆角半径太小,会导致型砂传热能力降低,凝固速度下降,同时由于该处型砂受热作用强,发气压力大,析出的气体可向未凝固的金属液渗入,导致铸件产生气缩孔。
(4)圆角太大。
圆角太大,则圆角部分就成了厚截面,如果相邻的截面较薄,就难以得到有效的补缩,造成补缩不良2.模样(1)模样或芯盒磨损致使铸件截面减薄,导致铸件截面厚度减薄而妨碍补缩。
(2)模样尺寸不当或模样结构不当,导致铸件截面过厚或过薄。
设计时应注意控制模样的厚度,尽量使邻近较厚截面的薄截面保持最大的厚度。
3.砂箱(1)上箱太浅。
生产中为了节省型砂用量或为了降低砂箱和造型成本而使用高度不够的上箱,这是造成缩松缺陷的常见原因。
上箱太浅,会降低金属液的静压力,以致难以进行补缩,补缩压力不够,会导致产生缩松或缩孔,或二者兼有之。
钛合金铸件缩孔(缩松)产生原因及防止方法

钛合金铸件缩孔(缩松)产生原因及防止方法
缩孔(缩松)
特征:缩孔是钛合金铸件表面或内部存在的一种表面粗糙的孔,轻微缩孔是许多分散的小缩孔,即缩松,缩孔或缩松处晶粒粗大。
常发生在钛合金铸件内浇道附近、冒口根部、厚大部位,壁的厚薄转接处及具有大平面的厚薄处。
形成原因:
1、模具工作温度控制未达到定向凝固要求。
2、涂料选择不当,不同部位涂料层厚度控制不好。
3、铸件在模具中的位置设计不当。
4、浇冒口设计未能达到起充分补缩的作用。
5、浇注温度过低或过高。
防治方法:
1、提高磨具温度。
2、调整涂料层厚度,涂料喷洒要均匀,涂料脱落而补涂时不可形成局部涂料堆积现象。
3、对模具进行局部加热或用绝热材料局部保温。
4、热节处镶铜块,对局部进行激冷。
5、模具上设计散热片,或通过水等加速局部地区冷却速度,或在模具外喷水,喷雾。
6、用可拆缷激冷块,轮流安放在型腔内,避免连续生产时激冷块本身冷却不充分。
7、模具冒口上设计加压装置。
8、浇注系统设计要准确,选择适宜的浇注温度。
钛合金铸件缩孔(缩松)产生原因及防止方法。
一种解决垂直线铸件缩松的工艺方法

一种解决垂直线铸件缩松的工艺方法垂直线具有自动化程度高,铸件尺寸精度及表面质量好,无需砂箱等优点,在灰铸铁制动盘生产中得到普遍应用。
采用顺序凝固解决水平造型线灰铸铁件缩松取得良好效果[1]。
要实现顺序凝固,通常需要足够大的冒口,由于垂直线大多采用底注顶部补缩工艺,凝固顺序是铸件→冒口颈→冒口,靠冒口内金属液的重力,将金属液输送到铸件缩松部位,为达到顺序凝固,就需要更大的冒口或冒口颈。
有时为达到补缩效果还需增加补贴,但这样会降低铁液利用率,加工也困难。
即使采用大冒口补缩,有时并不能完全消除缩松现象。
笔者通过模拟分析与试验验证,认为优化工艺,采用无冒口、改变内浇口位置的措施来解决缩松问题效果更好。
1 铸件产品介绍1.1 铸件生产情况在DISA240B垂直无箱造型线生产一种通风制动盘,一箱两件,湿型砂造型,三乙胺冷芯盒制芯,砂芯浸水基涂料。
材质为HT200,铸件重量7 kg,化学成分见表1。
采用中频感应电炉熔化,浇注温度1 360~1 400 ℃。
1.2 铸件结构及缺陷形貌铸件轮廓尺寸ϕ270 mm×38 mm(见图1),在制动盘里属于薄壁中小件。
结构特点是小端根部有凹角,易形成结构热节。
表1 制动盘化学成分(质量分数,%)Tab.1 Chemical composition of brake disc(mass fraction, %)化学成分C Si Mn S含量 3.2~3.5 1.7~2.20.6~0.9≤0.12化学成分P Cr Cu含量≤0.10.1~0.30.1~0.3图1 刹车盘尺寸Fig.1 Brake disc size在工艺试验过程中发现,结构热节附近有孔洞类缺陷,内表面粗糙,形状不规则,缺陷率达100%。
对缺陷部位进行金相与扫描电镜检验(见图2),缩松周围的石墨较其他部位粗大,孔洞内有明显的奥氏体枝晶,产生部位及微观形貌都具有缩松缺陷的典型特征,因此诊断该缺陷为缩松。
解决铸件缩松的方法

解决铸件缩松的方法
摘要:铸件缩松是指铸件在使用过程中产生的尺寸变化,导致铸件尺
寸变大,从而降低它的使用性能。
为了解决这个问题,必须采取有效的措施,以防止铸件缩松或控制缩松程度。
本文综述了常用的解决铸件缩松的
方法,包括熔炼技术、浇铸技术、试验技术、材料强度、热处理和机械处
理等。
关键词:铸件缩松;熔炼技术;浇铸技术;试验技术;材料强度;热
处理;机械处理
1. Introduction
铸件缩松是指铸件在使用过程中产生的尺寸变化,导致铸件尺寸变大,从而降低它的使用性能。
铸件缩松通常会导致连接点的放电问题,损坏表
面外观,降低性能,甚至影响工作精度等问题。
因此,正确理解和控制铸
件的缩松现象对工程结构的质量安全十分重要。
为了解决这个问题,必须采取有效的措施,以防止铸件缩松或控制缩
松程度。
本文将简要介绍一些常用的解决铸件缩松的方法,以提高铸件的
质量与性能。
2.1 Melting Technology
熔炼技术是铸件缩松最重要的解决方法之一、采用熔炼技术可以改变
铸件材料的内部结构,从而降低铸件的体积,减少铸件的体积变化。
铸件产生缩孔和缩松产生的原因及防止措施(音频讲解,实用方便)

铸件产⽣缩孔和缩松产⽣的原因及防⽌措施(⾳频讲解,实⽤⽅便)铸件缩松、缩孔问题防治⽅案来⾃制造⼯业联盟 00:00 10:29
缩孔是集中在铸件上部或最后凝固部位容积较⼤的孔洞
合⾦的液态收缩和凝固收缩愈⼤、浇注温度愈⾼、铸件愈厚,缩孔的容积愈⼤. 缩松是分
散在铸件某区域内的细⼩缩孔
形成原因:铸件最后凝固区域的收缩未能得到补⾜,或因为合⾦呈糊状凝固,被树枝状晶体
分隔开的⼩液体区难以得到补缩所⾄
逐层凝固合⾦,缩松倾向⼩。
糊状凝固合⾦缩松倾向⼤,缩孔倾向⼩。
防⽌缩孔和缩松的措施 1)选择合适的合⾦成分选⽤近共晶成分或结晶温度范围较
窄的合⾦ 2)⼯艺措施顺序凝固原则,获得没有缩孔的致密铸件。
定向凝固就是在铸
件上可能出现缩孔的厚⼤部位通过安放冒⼝等⼯艺措施,使铸件远离冒⼝的部位先凝固,然后
靠近冒⼝部位凝固,最后冒⼝本⾝凝固。
⽬的是铸件各个部位的收缩都能得到补充,⽽将缩孔转移到冒⼝中,最后予以清除措施
1、安放冒⼝
2、在⼯件厚⼤部位增设冷铁。
压铸件缩孔缩松的原因及解决办法
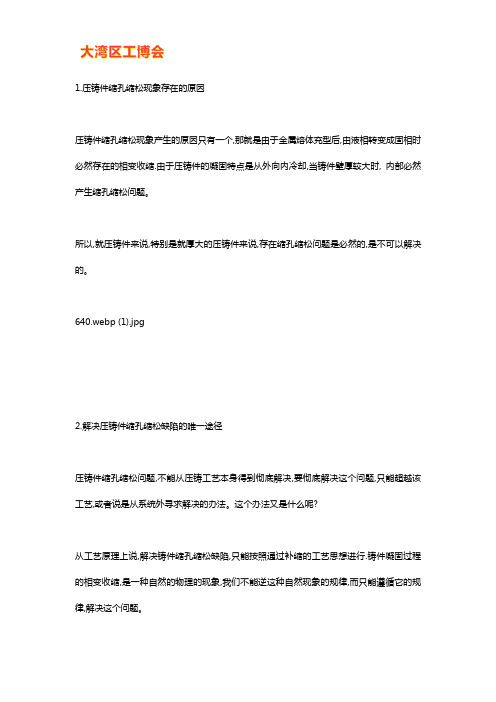
1.压铸件缩孔缩松现象存在的原因压铸件缩孔缩松现象产生的原因只有一个,那就是由于金属熔体充型后,由液相转变成固相时必然存在的相变收缩.由于压铸件的凝固特点是从外向内冷却,当铸件壁厚较大时, 内部必然产生缩孔缩松问题。
所以,就压铸件来说,特别是就厚大的压铸件来说,存在缩孔缩松问题是必然的,是不可以解决的。
640.webp (1).jpg2.解决压铸件缩孔缩松缺陷的唯一途径压铸件缩孔缩松问题,不能从压铸工艺本身得到彻底解决,要彻底解决这个问题,只能超越该工艺,或者说是从系统外寻求解决的办法。
这个办法又是什么呢?从工艺原理上说,解决铸件缩孔缩松缺陷,只能按照通过补缩的工艺思想进行.铸件凝固过程的相变收缩,是一种自然的物理的现象,我们不能逆这种自然现象的规律,而只能遵循它的规律,解决这个问题。
3.补缩的两种途径对铸件的补缩,有两种途径,一是自然的补缩,一是强制的补缩. 要实现自然的补缩,我们的铸造工艺系统中,就要有能实现“顺序凝固”的工艺措施.很多人直觉地以为,采用低压铸造方法就能解决铸件的缩孔缩松缺陷,但事实并不是这么回事.运用低压铸造工艺,并不等于就能解决铸件的缩孔缩松缺陷,如果低压铸造工艺系统没有设有补缩的工艺措施,那么,这种低压铸造手段生产出来的毛坯,也是可能百分之一百存在缩孔缩松缺陷的。
由于压铸工艺本身的特点,要设立自然的“顺序凝固”的工艺措施是比较困难的,也是比较复杂的.最根本的原因还可能是, ”顺序凝固”的工艺措施,总要求铸件有比较长的凝固时间,这一点,与压铸工艺本身有点矛盾。
强制凝固补缩的最大特点是凝固时间短,一般只及”顺序凝固”的四分之一或更短,所以,在压铸工艺系统的基础上,增设强制的补缩工艺措施,是与压铸工艺特点相适应的,能很好解决压铸件的缩孔缩松问题。
4.强制补缩的两种程度挤压补缩和锻压补缩实现铸件的强制补缩可以达到有两种程度.一种是基本的可以消除铸件缩孔缩松缺陷的程度,一种是能使毛坯内部达到破碎晶粒或锻态组织的程度.如果要用不同的词来表述这两种不同程度话,那么,前者我们可以用“挤压补缩”来表达,后者,我们可以用“锻压补缩”来表达。
如何解决压铸件的缩孔缩松问题

如何解决压铸件的缩孔缩松问题压铸件存在缩孔缩松问题是一个普遍的现象,有没有彻底解决这个问题的方法?答案应该是有的,但它会是什么呢?1、压铸件缩孔缩松现象存在的原因:压铸件缩孔缩松现象产生的原因只有一个,那就是由于金属熔体充型后,由液相转变成固相时必然存在的相变收缩。
由于压铸件的凝固特点是从外向内冷却,当铸件壁厚较大时,内部必然产生缩孔缩松问题。
所以,就压铸件来说,特别是就厚大的压铸件来说,存在缩孔缩松问题是必然的,是不可以解决的。
2、解决压铸件缩孔缩松缺陷的唯一途径:压铸件缩孔缩松问题,不能从压铸工艺本身得到彻底解决,要彻底解决这个问题,只能超越该工艺,或者说是从系统外寻求解决的办法。
这个办法又是什么呢?从工艺原理上说,解决铸件缩孔缩松缺陷,只能按照通过补缩的工艺思想进行。
铸件凝固过程的相变收缩,是一种自然的物理的现象,我们不能逆这种自然现象的规律,而只能遵循它的规律,解决这个问题。
3、补缩的两种途径:对铸件的补缩,有两种途径,一是自然的补缩,一是强制的补缩。
要实现自然的补缩,我们的铸造工艺系统中,就要有能实现“顺序凝固”的工艺措施。
很多人以为,采用低压铸造方法就能解决铸件的缩孔缩松缺陷,但事实并不是这么回事.运用低压铸造工艺,并不等于就能解决铸件的缩孔缩松缺陷,如果低压铸造工艺系统没有设有补缩的工艺措施,那么,这种低压铸造手段生产出来的毛坯,也是可能百分之一百存在缩孔缩松缺陷的。
由于压铸工艺本身的特点,要设立自然的“顺序凝固”的工艺措施是比较困难的,也是比较复杂的.最根本的原因还可能是,“顺序凝固”的工艺措施,总要求铸件有比较长的凝固时间,这一点,与压铸工艺本身有点矛盾。
强制凝固补缩的最大特点是凝固时间短,一般只及“顺序凝固”的四分之一或更短,所以,在压铸工艺系统的基础上,增设强制的补缩工艺措施,是与压铸工艺特点相适应的,能很好解决压铸件的缩孔缩松问题。
4、强制补缩的两种程度:挤压补缩和锻压补缩。
铸件缩孔缩松解决方法

铸件缩孔缩松解决方法铸件缩孔缩松是铸造过程中常见的缺陷问题,会对铸件的强度和密封性能造成影响。
为了解决这一问题,需要采取一系列的措施来减少或消除铸件的缩孔缩松现象。
合理设计铸件的结构是解决缩孔缩松问题的关键。
在铸件设计过程中,应尽量避免出现厚度不均匀、壁厚过大或过小等情况,以免产生应力集中和缩孔缩松的隐患。
同时,应留有足够的浇注系统和冷却系统,以保证铸件在凝固过程中有足够的液态金属供应和冷却条件,从而减少缩孔缩松的产生。
选择合适的铸造材料和工艺参数也是解决缩孔缩松问题的重要措施。
铸造材料的选择应考虑其流动性、凝固收缩率和气孔生成倾向等因素,以减少缩孔缩松的发生。
同时,通过优化浇注温度、浇注速度、浇注压力等工艺参数,可以改善铸件的凝固过程,减少缩孔缩松的产生。
加强铸造过程的控制和监测也是解决缩孔缩松问题的必要手段。
在铸造过程中,应严格控制浇注温度、铸型温度和冷却速度等参数,避免过热或过冷引起的缩孔缩松问题。
同时,通过使用合适的质量监测方法,如X射线探伤、超声波探伤等,及时发现和修复铸件中的缩孔缩松缺陷,确保铸件的质量。
可以采用一些特殊的工艺措施来解决铸件缩孔缩松问题。
例如,可以采用真空铸造、压力铸造或浸渍处理等方法,通过改变铸造环境或材料特性,减少缩孔缩松的发生。
此外,还可以在铸件表面施加压力或采用压力鼓包等方式,增加铸件的实体密度,减少缩孔缩松的存在。
铸件缩孔缩松是铸造过程中常见的缺陷问题,但通过合理的设计、选择合适的材料和工艺参数,加强铸造过程的控制和监测,以及采用特殊的工艺措施,可以有效地解决这一问题。
通过这些措施的综合应用,可以提高铸件的质量和性能,确保产品的可靠性和安全性。
解决铸件缩松的方法

解决铸件缩松的方法李德臣(沈阳鑫浩龙铸造材料公司沈阳110021)Solutions for Casting Shrinkage PorsityLi De-chen(Shenyang Xinhaolong Foundry Materials Co,Ltd.Shenyang · 110021 · China ·)许多铸造厂都普遍存在铸件缩松缺陷。
由此产生的废品率少者15~20%,多者50~70%。
这看似简单的缩松缺陷,却长期极大地影响着企业的成品率和经济效益。
那么,铸件的缩松缺陷是如何产生又如何解决呢?笔者有如下拙见。
一、缩松产生的原因铸件产生缩松的根本原因是“热不平衡”所致。
缩松的位置,产生在铸件的厚大中心部位,几何热节处,不同壁厚的交差处和人为热节处。
这些地方都因热量过高最后凝固又得不到充分补缩而产生了缩松,严重时产生集中性缩孔。
图1中各例分别标示了由铸件结构原因可能产生的缩松。
其次,铸造工艺设计不合理,人为地制造热节而产生缩松缺陷。
如图2中各例。
不少企业,无论铸件多重、多厚、多长,都只设一个内浇口,且设在铸件最厚处。
就是壁厚均匀者,内浇口设的位置与数量也不合理。
这样的工艺设计,落砂时内浇口往往不打自掉,集中性缩孔也是常见的。
第三,浇注温度过高和浇注时间过长。
第四,铸型的造型材料蓄热量小,散热性差,造成铸件凝固时间过长。
第五,一箱多件,件之间距离太近。
第六,球墨铸铁的铸型紧实度低,铸型强度小和表面硬度低,砂箱刚度弱,金属液中共晶团数多,铸件在凝固膨胀时推动着型壁向外移动。
第七,化学成分设计不当,合金化不足。
……二、解决方法解决缩松缺陷,最根本的着眼点就是“热平衡”。
其方法是:第一,在铸件结构形成的厚大处与热节处,实行快速凝固,人为地造成铸件各处温度场的基本平衡。
采用内外冷铁,局部采用蓄热量大的锆英砂、铬铁矿砂或特种涂料(见图3)。
图4是加拿大的QT450-10铸件,重35kg,须超声波探伤(6000m/s)达2级,任何部位都不得有缩松缺陷。
- 1、下载文档前请自行甄别文档内容的完整性,平台不提供额外的编辑、内容补充、找答案等附加服务。
- 2、"仅部分预览"的文档,不可在线预览部分如存在完整性等问题,可反馈申请退款(可完整预览的文档不适用该条件!)。
- 3、如文档侵犯您的权益,请联系客服反馈,我们会尽快为您处理(人工客服工作时间:9:00-18:30)。
解决铸件缩松的方法
李德臣
(沈阳鑫浩龙铸造材料公司沈阳110021)
Solutions for Casting Shrinkage Porsity
Li De-chen
(Shenyang Xinhaolong Foundry Materials Co,Ltd.
Shenyang · 110021 · China ·)
许多铸造厂都普遍存在铸件缩松缺陷。
由此产生的废品率少者15~20%,多者50~70%。
这看似简单的缩松缺陷,却长期极大地影响着企业的成品率和经济效益。
那么,铸件的缩松缺陷是如何产生又如何解决呢?笔者有如下拙见。
一、缩松产生的原因
铸件产生缩松的根本原因是“热不平衡”所致。
缩松的位置,产生在铸件的厚大中心部位,几何热节处,不同壁厚的交差处和人为热节处。
这些地方都因热量过高最后凝固又得不到充分补缩而产生了缩松,严重时产生集中性缩孔。
图1中各例分别标示了由铸件结构原因可能产生的缩松。
其次,铸造工艺设计不合理,人为地制造热节而产生缩松缺陷。
如图2中各例。
不少企业,无论铸件多重、多厚、多长,都只设一个内浇口,且设在铸件最厚处。
就是壁厚均匀者,内浇口设的位置与数量也不合理。
这样的工艺设计,落砂时内浇口往往不打自掉,集中性缩孔也是常见的。
第三,浇注温度过高和浇注时间过长。
第四,铸型的造型材料蓄热量小,散热性差,造成铸件凝固时间过长。
第五,一箱多件,件之间距离太近。
第六,球墨铸铁的铸型紧实度低,铸型强度小和表面硬度低,砂箱刚度弱,金属液中共晶团数多,铸件在凝固膨胀时推动着型壁向外移动。
第七,化学成分设计不当,合金化不足。
……
二、解决方法
解决缩松缺陷,最根本的着眼点就是“热平衡”。
其方法是:
第一,在铸件结构形成
的厚大处与热节处,实行快
速凝固,人为地造成铸件各
处温度场的基本平衡。
采用
内外冷铁,局部采用蓄热量大的锆英砂、铬铁矿砂或特种涂料(见图3)。
图4是加拿大的QT450-10铸件,重35kg,须超声波探伤(6000m/s)达2级,任何部位都不得有缩松缺陷。
国内至少有4家企业试制该件,费时数月,耗资几十万元均告失败。
笔者为温州某厂按图5的工艺试制,获得成功。
其技术关键是平做立浇,随形外冷铁,型芯用铬铁矿砂,压边浇冒口和低温浇注。
图4. Fig .4.
第二,科学合理的工艺设计。
内浇口设在铸件相对薄壁处(图6),数量多且分散。
使最早进入厚壁处的金属液率先凝固,薄壁处后凝固,进而使各处基本达到同时凝固。
对于壁厚均匀的铸件,采用多个内浇口和出气孔。
内浇口多、分散与均布,使整体热量均衡。
出气孔细且多,既排气通畅又起散热作用。
第三,改变内浇口的位置
图7.(a)是山西某厂用消失模生产的箱体。
原工艺设计的内浇口在最下面,而底面是考核硬度的地方,结果,硬度值不达标者逾70%。
须知,凡是硬度值偏低的地方,就表明了该处组织必定不致密,近乎缩松。
这是此处“人为过热”的结果。
按笔者的方案,将内浇口向上提高100㎜,让
底面先凝固。
这不但使该件
的硬度值达标,还节省了相
当可观的金属液,一件节省
1公斤,日产5000多件,
其经济效益不言而喻!
图7(b )是山东某厂
的刹车盘,原设计的金属液从厚壁(40㎜)处进入铸型,A处缩松逾50%以上。
经过改进,增加一个型芯,将内浇口设在铸件薄壁(20㎜)处,横浇道的长度大于半个圆周,与直浇道对称地设置多个内浇口。
于是,该铸件热节处的缩松便消除了。
当然,靠近热节处的砂芯采用铬矿砂和底面放置冷铁,效果也很好。
但是,这些措施应当与造型方式相适应,以操作简便、高效和节能节材为实施依据。
第四,选用蓄热量大的造型材料,这对用消失模生产抗磨产品极为重要!铬铁矿砂取代石英砂等蓄热量小的其它砂种,会取得良好的效果,浇毕微震更优!
第五,低温快浇,开放式浇注系统。
使金属液快速、平稳、均衡地充满铸型。
这要因件制宜。
第六,球铁的铸型强度大,表面硬度≥90,砂箱刚性大,对消除缩松有利。
第七,需要冒口时,当首选热冒口,且离开热节。
若将冒口置于热节上,必将加大冒口尺寸,形成“热上加热”。
弄不好,非但缩松难除,还会产生集中性缩孔,又降低了工艺出品率。
第八,铸型倾斜摆放与合金化,都获益(省去叙述)。
※※※※※※
消除铸件缩松缺陷是一个复杂地认识与实施过程。
应以“热平衡”为基本原则,对具体铸件做科学周密地分析,制订合理的工艺方案,选择好适宜的造型材料、工装及正确操作且标准化。
那么,任何铸件的缩松缺陷都不难解决。
写于2010年10月4日。