冲孔复合模具设计5226
落料冲孔复合模具设计说明

落料冲孔复合模具设计说明一、模具结构设计1.模具类型:落料冲孔复合模具由上模、下模和导向列组成。
根据工件的要求和形状,模具可以分为单向落料冲孔模、双向落料冲孔模和多向落料冲孔模等类型。
2.上模设计:上模一般由模座、上模板、射针等部分组成。
上模板与下模具配合使用,冲击力传递到工件上。
上模板应尽可能减小重量,提高模具寿命。
3.下模设计:下模由模座、下模板、导柱等部分组成。
下模板与上模具配合使用,负责支撑工件并传递冲压力。
下模板应具备足够的强度和刚度,以保证冲孔过程中不变形。
4.导向列设计:导向列用于保证上模与下模的定位精度。
导向柱是最常见的导向结构,其作用是使上模和下模在冲孔过程中保持相对位置的稳定性和精确性。
二、材料选择1.模具材料:常用于落料冲孔复合模具的材料有Cr12MoV、SKD11、SKH-9等。
这些材料具备良好的硬度、抗磨性和耐冲击性能,能够满足加工要求,并延长模具使用寿命。
2.工作板材:根据冲孔工件的特点和材料选择不同的板材,如不锈钢板、铝合金板、冷轧板等。
工作板材的选择应考虑其刚度、强度和耐磨性能,以提高冲孔质量和效率。
三、加工工艺1.毛坯选择:根据工件要求,选择适合的板材作为冲孔模具的毛坯。
在选择毛坯时,要注意其尺寸和平整度,以便后续的加工和使用。
2.模具加工:模具的加工过程包括车削、铣削、铣孔、磨削、钳工和装配等工序。
在加工过程中要注意控制尺寸精度和表面质量,确保模具在使用中的稳定性和寿命。
3.表面处理:模具的表面处理可以采用镀铬、硬质合金喷涂、表面渗碳等技术。
表面处理能够提高模具的耐磨性和抗腐蚀性,延长模具的使用寿命。
4.模具调试:模具制造完成后,需要进行调试和试模。
通过调试,可以检查模具的定位精度、冲孔质量和加工效率,确保模具满足设计要求。
综上所述,落料冲孔复合模具设计需要考虑模具结构、材料选择和加工工艺等方面。
通过合理的设计和加工,可以提高模具的使用寿命和冲孔质量,满足金属加工的需求。
落料冲孔复合模具设计
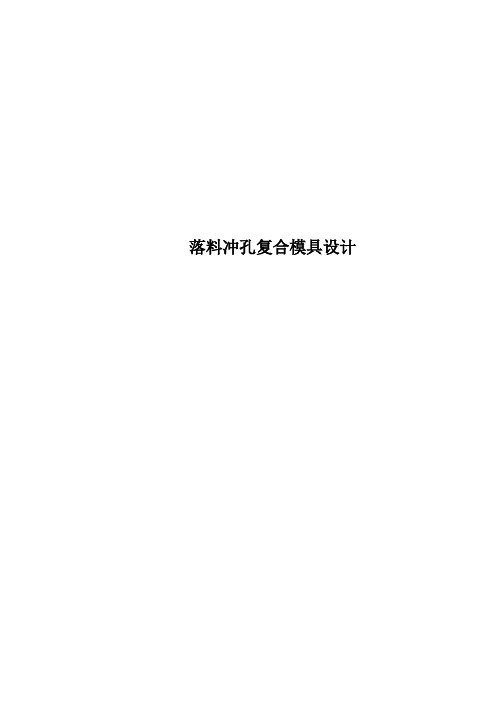
落料冲孔复合模具设计落料冲孔复合模具设计绪论模具主要类型有:冲模,锻模,塑料模,压铸模,粉末冶金模,玻璃模,橡胶模,陶瓷模等。
除部分冲模以外的的上述各种模具都属于腔型模,因为他们一般都是依靠三维的模具形腔是材料成型。
(1)冲模:冲模是对金属板材进行冲压加工获得合格产品的工具。
冲模占模具总数的50%以上。
按工艺性质的不同,冲模可分为落料模,冲孔模,切口模,切边模,弯曲模,卷边模,拉深模,校平模,翻孔模,翻边模,缩口模,压印模,胀形模。
按组合工序不同,冲模分为单工序模,复合模,连续模。
(2)锻模:锻模是金属在热态或冷态下进行体积成型是所用模具的总称。
按锻压设备不同,锻模分为锤用锻模,螺旋压力机锻模,热模锻压力锻模,平锻机用锻模,水压机用锻模,高速锤用锻模,摆动碾压机用锻模,辊锻机用锻模,楔横轧机用锻模等。
按工艺用途不同,锻模可分为预锻模具,挤压模具,精锻模具,等温模具,超塑性模具等。
(3)塑料模:塑料模是塑料成型的工艺装备。
塑料模约占模具总数的35%,而且有继续上升的趋势。
塑料模主要包括压塑模,挤塑模,注射模,此外还有挤出成型模,泡沫塑料的发泡成型模,低发泡注射成型模,吹塑模等。
(4)压铸模:压铸模是压力铸造工艺装备,压力铸造是使液态金属在高温和高速下充填铸型,在高压下成型和结晶的一种特殊制造方法。
压铸模约占模具总数的6%。
(5)粉末冶金模:粉末冶金模用于粉末成型,按成型工艺分类粉末冶金模有:压模,精整模,复压模,热压模,粉浆浇注模,松装烧结模等。
目前,我国17000多个模具生产厂点,从业人数五十多万。
除了国有的专业模具厂外,其他所有制形式的模具厂家,包括集体企业,合资企业,独资企业和私营企业等,都得到了快速发展。
研究和发展模具技术,对于促进国民经济的发展具有特别重要的意义,模具技术已成为衡量一个国家产品制造技术的重要标志之一,随着工业生产的迅速发展,模具工业在国民经济中的地位日益提高,并在国民经济发展过程中发挥越来越大的作用。
毕业设计——垫片落料冲孔复合模设计
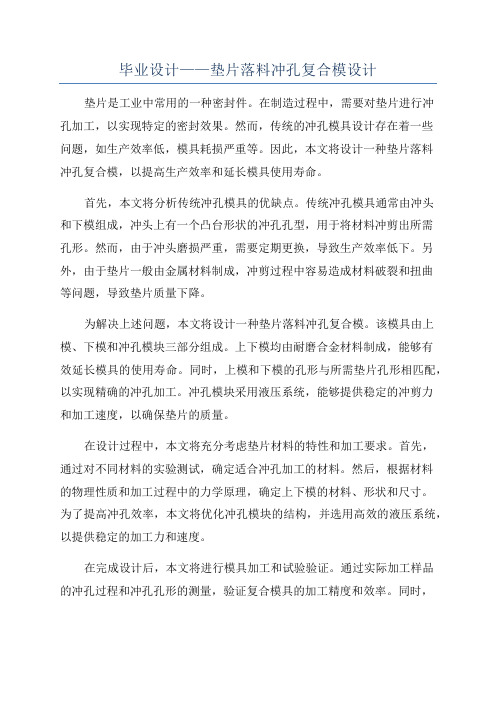
毕业设计——垫片落料冲孔复合模设计垫片是工业中常用的一种密封件。
在制造过程中,需要对垫片进行冲孔加工,以实现特定的密封效果。
然而,传统的冲孔模具设计存在着一些问题,如生产效率低,模具耗损严重等。
因此,本文将设计一种垫片落料冲孔复合模,以提高生产效率和延长模具使用寿命。
首先,本文将分析传统冲孔模具的优缺点。
传统冲孔模具通常由冲头和下模组成,冲头上有一个凸台形状的冲孔孔型,用于将材料冲剪出所需孔形。
然而,由于冲头磨损严重,需要定期更换,导致生产效率低下。
另外,由于垫片一般由金属材料制成,冲剪过程中容易造成材料破裂和扭曲等问题,导致垫片质量下降。
为解决上述问题,本文将设计一种垫片落料冲孔复合模。
该模具由上模、下模和冲孔模块三部分组成。
上下模均由耐磨合金材料制成,能够有效延长模具的使用寿命。
同时,上模和下模的孔形与所需垫片孔形相匹配,以实现精确的冲孔加工。
冲孔模块采用液压系统,能够提供稳定的冲剪力和加工速度,以确保垫片的质量。
在设计过程中,本文将充分考虑垫片材料的特性和加工要求。
首先,通过对不同材料的实验测试,确定适合冲孔加工的材料。
然后,根据材料的物理性质和加工过程中的力学原理,确定上下模的材料、形状和尺寸。
为了提高冲孔效率,本文将优化冲孔模块的结构,并选用高效的液压系统,以提供稳定的加工力和速度。
在完成设计后,本文将进行模具加工和试验验证。
通过实际加工样品的冲孔过程和冲孔孔形的测量,验证复合模具的加工精度和效率。
同时,还将对复合模具和传统模具进行对比试验,评估复合模具的生产效率和模具寿命等性能。
综上所述,本文将设计一种垫片落料冲孔复合模,以提高生产效率和延长模具使用寿命。
通过对材料特性和加工要求的分析,优化模具的结构和液压系统设计,实现精确的冲孔加工。
通过试验验证,评估复合模具的加工精度和效果。
期望该设计能够为垫片冲孔加工提供一种高效、可靠的解决方案。
落料冲孔复合模设计实例

落料冲孔复合模设计实例在此实例中,我们需要设计一个落料冲孔复合模,用于冲压一块厚度为2mm的方形薄板。
薄板的尺寸为100mm × 100mm。
冲孔部分需要在薄板的四个角上冲孔,冲孔直径为10mm。
同时,需要在薄板的一边进行切割,切割长度为80mm。
首先,我们需要确定冲孔的位置和数量。
考虑到薄板的尺寸和形状,我们决定在薄板的四个角上进行冲孔。
冲孔直径为10mm。
为了保证冲孔的准确性和稳定性,我们需要设计一个冲孔模具,包括冲孔钢模和冲孔衬套。
冲孔钢模的尺寸为20mm × 20mm × 10mm。
冲孔衬套的尺寸与冲孔钢模相匹配。
冲孔钢模通过安装在冲床上,固定在冲床的上模座上。
冲孔衬套则通过螺纹固定在冲孔钢模上。
薄板在冲孔时会被钢模和衬套夹住,冲孔钢模通过冲击力将薄板冲孔。
接下来,我们需要设计切割部分的模具。
根据需求,切割长度为80mm。
我们选择使用切割刀具来完成切割操作。
切割刀具的尺寸为80mm × 10mm,其材料为高速钢。
切割刀具通过安装在切割模架上,固定在冲床的下模座上。
切割模架通过滑动导轨与下模座连接,可以准确地控制切割位置和长度。
为了提高生产效率,我们可以选择一次冲孔和切割多个薄板。
这就需要在冲床上设计合适的夹持装置,以固定多个薄板。
夹持装置可以同时夹持多个薄板,使冲孔和切割的连续进行,提高生产效率。
在设计完成后,我们需要进行模具制造和组装。
首先,我们制造冲孔钢模和冲孔衬套,确保其尺寸和形状的准确性。
接着,制造切割刀具和切割模架,保证其切割性能和精度。
最后,将冲孔钢模、冲孔衬套、切割刀具和切割模架组装在冲床上。
当我们需要进行冲孔和切割时,将薄板放入夹持装置中,通过冲床的运动,冲孔钢模将薄板冲孔,切割刀具将薄板切割。
这样,我们就完成了落料冲孔复合模的设计和制造。
总结起来,落料冲孔复合模的设计需要考虑冲孔和切割的几何形状、材料厚度和生产效率等因素。
在此设计实例中,我们根据需求设计了冲孔模具和切割模具,并制造和组装了这些模具。
毕业设计——垫片落料冲孔复合模设计

垫片落料冲孔复合模设计【摘要】复合模具是模具生产的一种,是指通过一定工序将坯料冲裁成形的模具。
按照冲压的工艺性质分类,复合模具是使材料发生变形的冲裁模具。
我的课题包括零件的工艺分析,凸凹模的计算,冲压工序的确定分析的两套模具,正确的选用标准零件和其它的零件,对冲压结构进行了工艺分析已选取压力机。
绘制模具二维装配图和零件图。
此毕业设计需要用到CAD绘图,数控车床的加工打磨。
通过一系列的选择,我最终选择了冲压模零件的设计,主要介绍的是冲压模具的凸凹模计算,工艺顺序,模具的工作原理。
关键词:模具行业发展结构设计目录引言1一、冲裁零件工艺性2(一)零件分析 2(二)工序顺序确定.......................................................... ............................................................ (2)(二)零件工艺分析 2(三)确定冲裁工艺方案2二、确定模具总体结构方案 3(一)模具类型 3(二)选取操作与定位方式 3(三)卸料与出件 3(四)模架的类型选取.......................................................... ............................................................ . (3)三、冲件的工艺与计算3(一)排样方案 3(二)排样图 4(三) 送料冲裁的示意图.......................................................... (4)(四)条料宽度导料板间距计算.......................................................... (4)(五)计算冲压力选取压力机 4四、凸、凹模刃口尺寸计算 6(一)落料凹模刃口尺寸的计算方法 6(二)冲孔凹模的刃口尺寸计算 6五、冲件凸凹模部件的结构与设计 7(一)凹模的设计 8(二)凸模的设计 9(三)凸凹模结构的设计9六、模具总装图11七、冲模的安全措施错误!未定义书签。
拉深冲孔复合模具设计

1绪论1.1冲压的概念、特点及应用冲压成形作为现代工业中一种十分重要的加工方法,用以生产各种板料零件,具有很多独特的优势,其成形件具有自重轻、刚度大、强度高、互换性好、成本低、生产过程便于实现机械自动化及生产效率高等优点,是一种其它加工方法所不能相比和不可替代的先进制造技术,在制造业中具有很强的竞争力,被广泛应用于汽车、能源、机械、信息、航空航天、国防工业和日常生活的生产之中。
在吸收了力学、数学、金属材料学、机械科学以及控制、计算机技术等方面的知识后,已经形成了冲压学科的成形基本理论。
以冲压产品为龙头,以模具为中心,结合现代先进技术的应用,在产品的巨大市场需求刺激和推动下,冲压成形技术在国民经济发展、实现现代化和提高人民生活水平方面发挥着越来越重要的用。
冲压是利用安装在冲压设备(主要是压力机)上的模具对材料施加压力,使其产生分离或塑性变形,从而获得所需零件(俗称冲压或冲压件)的一种压力加工方法。
冲压通常是在常温下对材料进行冷变形加工,且主要采用板料来加工成所需零件,所以也叫冷冲压或板料冲压。
冲压是材料压力加工或塑性加工的主要方一隶属于材料成型工程术。
冲压所使用的模具称为冲压模具,简称冲模。
冲模是将材料(金属或非金属)批量加工成所需冲件的专用工具。
冲模在冲压中至关重要,没有符合要求的冲模,批量冲压生产就难以进行;没有先进的冲模,先进的冲压工艺就无法实现。
冲压工艺与模具、冲压设备和冲压材料构成冲压加工的三要素,只有它们相互结合才能得出冲压件。
与机械加工及塑性加工的其它方法相比,冲压加工无论在技术方面还是经济方面都具有许多独特的优点。
主要表现如下。
(1)冲压加工的生产效率高,且操作方便,易于实现机械化与自动化。
这是因为冲压是依靠冲模和冲压设备来完成加工,普通压力机的行程次数为每分钟可达几十次,高速压力要每分钟可达数百次甚至千次以上,而且每次冲压行程就可能得到一个冲件。
(2)冲压时由于模具保证了冲压件的尺寸与形状精度,且一般不破坏冲压件的表面质量,而模具的寿命一般较长,所以冲压的质量稳定,互换性好,具有一模一样”的特征。
落料冲孔复合模设计方案实例

落料冲孔复合模设计方案实例一、引言随着工业制造技术的不断发展,冲压工艺在各个领域得到广泛应用。
而在冲压过程中,落料冲孔操作是一个非常重要的环节。
为了提高生产效率和产品质量,设计和制造一套高效可靠的落料冲孔复合模非常关键。
本文将以某企业生产的金属工件为例,介绍一种落料冲孔复合模设计方案。
二、设计目标在设计落料冲孔复合模时,需实现以下目标:1. 提高生产效率:减少生产过程中的冲孔次数和时间。
2. 保证产品质量:减少冲压产生的变形和裂纹,提高工件尺寸和形状的一致性。
3. 提高模具使用寿命:减少因冲压而导致的模具磨损和损坏。
三、设计要素1. 材料选择:选用高硬度和高耐磨性的冷作工具钢作为模具材料,以确保模具的使用寿命和稳定性。
2. 设计结构:根据金属工件的形状和尺寸要求,合理设计落料冲孔复合模的结构和布局。
模具的结构应有利于材料的流动和排气,并能够减小冲压时的变形和应力集中。
3. 润滑系统:在模具设计中,考虑设置润滑系统来减少摩擦和热量的产生,以延长模具寿命。
4. 加工工艺:考虑使用先进的数控加工设备和软件,进行精确的模具制造和调试,以确保模具的准确度和稳定性。
四、具体方案基于以上设计要素,我们提出以下具体方案:1. 模具结构设计:采用分层式复合模设计,将落料和冲孔的功能集成在同一个模具内。
同时,在模具底部设计合适的排气孔和排渣槽,以确保材料的流动性和排气性。
2. 润滑系统设计:在模具的摩擦面和冲孔孔径处设置润滑油槽和喷油装置,以减少热量的产生和模具磨损。
同时,结合自动化控制系统,实现润滑油的定量供给和循环利用,提高润滑效果。
3. 加工工艺设计:采用数控加工设备进行模具的制造和加工,结合CAD和CAM软件进行模具的设计和调试。
优化加工工艺参数,确保模具的精度和稳定性。
五、验证和改进在设计完成后,进行模具的试制和测试。
通过实际生产的验证,对设计方案进行评估和改进。
调整模具的结构和加工工艺参数,优化模具的性能和稳定性,以实现更好的生产效果和质量要求。
复合模具设计说明
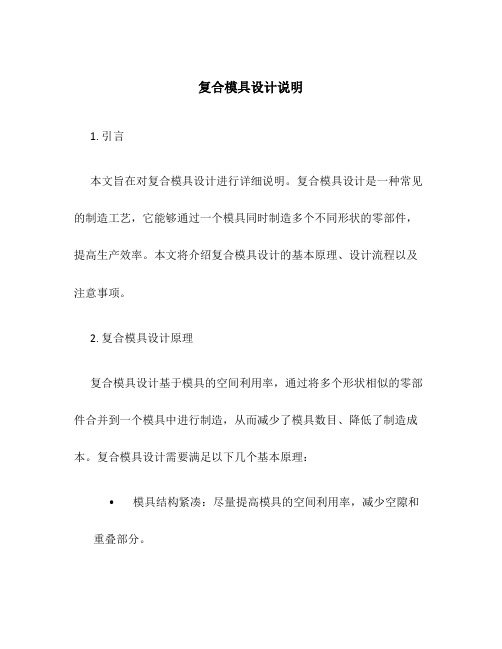
复合模具设计说明1. 引言本文旨在对复合模具设计进行详细说明。
复合模具设计是一种常见的制造工艺,它能够通过一个模具同时制造多个不同形状的零部件,提高生产效率。
本文将介绍复合模具设计的基本原理、设计流程以及注意事项。
2. 复合模具设计原理复合模具设计基于模具的空间利用率,通过将多个形状相似的零部件合并到一个模具中进行制造,从而减少了模具数目、降低了制造成本。
复合模具设计需要满足以下几个基本原理:•模具结构紧凑:尽量提高模具的空间利用率,减少空隙和重叠部分。
•零部件形状相似:复合模具适用于形状相似、尺寸相近的零部件制造。
•制造工艺简化:复合模具能够降低工艺复杂度、提高生产效率。
3. 复合模具设计流程复合模具设计的流程如下:1.需求分析:明确产品的设计要求和制造目标,确定复合模具设计的可行性。
2.零部件分析:对需要制造的零部件进行形状和尺寸的分析,确定它们是否适合应用复合模具设计。
3.模具结构设计:根据零部件的形状和尺寸,设计合适的复合模具结构,确保模具能够容纳所有需要制造的零部件。
4.模具制造与调试:根据模具设计图纸,制造复合模具,并进行调试和优化,确保零部件可以准确无误地制造出来。
5.生产与验收:使用复合模具进行零部件的批量生产,并进行验收和质量检查。
4. 复合模具设计注意事项在进行复合模具设计时,需要注意以下几个方面:•材料选择:选择适合复合模具制造的材料,具备足够的硬度和耐磨性。
•结构稳定性:确保复合模具的结构稳定,不易变形和损坏。
•加工精度:预留足够的加工余量,保证模具加工的精度和一致性。
•模具维护:定期对复合模具进行维护保养,延长使用寿命。
5. 结论复合模具设计是一种提高生产效率的重要工艺,在合适的情况下可以显著降低制造成本。
通过合理的设计流程和注意事项,可以设计出高效稳定的复合模具,为企业的生产提供有力支持。
以上就是复合模具设计说明的内容,通过本文的阐述,希望读者可以了解复合模具设计的基本原理、设计流程以及注意事项。
小钣金件冲孔翻边复合模设计

小钣金件冲孔翻边复合模设计摘要:钣金零件上的翻边孔通常首先使用冲底孔后翻边,然后使用两个冲压形模具。
此冲孔程序通常适用于大型板金零件。
对于小型和不规则钣金零件,从冲孔翻边创建复合模具是很有用的,因为定位精度差,输出数量少,并且零件很难获得。
关键词:小钣金件;冲孔;翻边;复合模具随着现代工业技术的迅猛发展,各种模具运用越来越普及,正在汽车、航天、消费电子、仪器和医疗设备等领域得到应用。
冷冲模占行业总产量约40%的模具,,其中模具安装在压机中,并在室温下对材料施加压力,以创建分离、造型或连接,从而得到具有特定形状、大小和特性的零件。
一、冲孔翻孔工序介绍冷冲压工艺有不同的分类方法,可根据不同的分类方法分为离和成形工艺,翻边是其中一个过程。
这是在模具影响下开发的方法。
它将孔的边或工件的外侧边推至垂直边。
但是,如果工件弯曲,则工件的变形仅限于弯曲曲线的圆形部分。
翻边时,工件的圆角部分和边缘必须参与变形。
两者都属于变形带,因此翻边时的变形比弯曲时复杂得多,从而使翻边过程更加有难度。
根据工件边的状态和应力以及各种变形状态,可将翻边分为外缘和内孔翻边,或分为伸长和压缩类。
内孔翻边是冲压过程。
在冲孔过程中,孔边上的直线材料会镜像到先前弯曲的工件上。
根据孔的形状,内孔翻边也可以分为圆孔和异型孔翻边。
二、冲孔翻孔复合模结构五金钣金件通常有一个内孔翻边过程,设计用于攻丝,并从制造零件之间的螺纹连接开始。
大多数常规翻孔方法是冲压一个非常小的预应力孔,然后翻孔两种程序的传统程序可分为三类。
方法1:单工序,如果单工序模具,则必须创建两组模具,冲压一个模具并翻孔以创建另一个模具冲压设备占用两套。
此冲压工艺需要大量人力、较长的交货时间、较低的加工精度、较高的生产成本、较长的生产周期和较低的生产率。
方式2:级进模成形。
这是通过在模具的两个位置形成来实现的,这些需要在两个模具之间进行相对精确的定位,以确保制造精度。
该方法与前者相比具有一定的优势:它提高了零件生产的准确性和效率。
落料冲孔复合模具设计
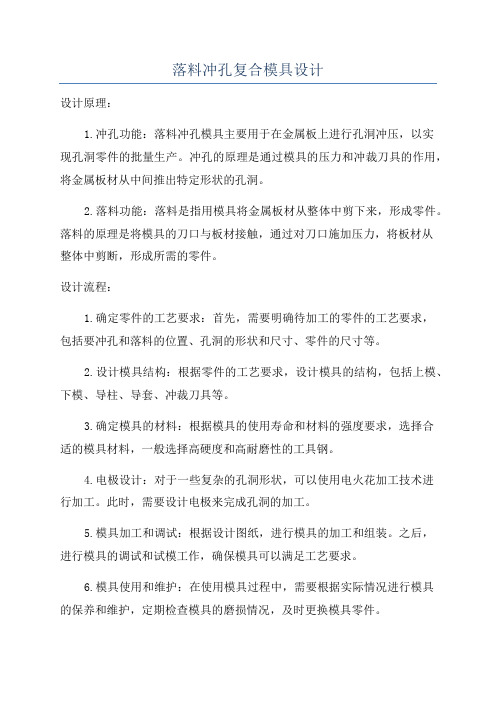
落料冲孔复合模具设计设计原理:1.冲孔功能:落料冲孔模具主要用于在金属板上进行孔洞冲压,以实现孔洞零件的批量生产。
冲孔的原理是通过模具的压力和冲裁刀具的作用,将金属板材从中间推出特定形状的孔洞。
2.落料功能:落料是指用模具将金属板材从整体中剪下来,形成零件。
落料的原理是将模具的刀口与板材接触,通过对刀口施加压力,将板材从整体中剪断,形成所需的零件。
设计流程:1.确定零件的工艺要求:首先,需要明确待加工的零件的工艺要求,包括要冲孔和落料的位置、孔洞的形状和尺寸、零件的尺寸等。
2.设计模具结构:根据零件的工艺要求,设计模具的结构,包括上模、下模、导柱、导套、冲裁刀具等。
3.确定模具的材料:根据模具的使用寿命和材料的强度要求,选择合适的模具材料,一般选择高硬度和高耐磨性的工具钢。
4.电极设计:对于一些复杂的孔洞形状,可以使用电火花加工技术进行加工。
此时,需要设计电极来完成孔洞的加工。
5.模具加工和调试:根据设计图纸,进行模具的加工和组装。
之后,进行模具的调试和试模工作,确保模具可以满足工艺要求。
6.模具使用和维护:在使用模具过程中,需要根据实际情况进行模具的保养和维护,定期检查模具的磨损情况,及时更换模具零件。
设计注意事项:1.强化模具的刚性:落料冲孔复合模具的刚性对于冲孔和落料的质量有很大影响。
因此,设计时需要合理设计模具的结构,提高模具的刚性。
2.合理选择冲裁刀具:根据孔洞的形状和尺寸,选择合适的冲裁刀具。
冲裁刀具应具有足够的硬度和耐磨性,以确保冲裁的质量和寿命。
3.注意冲孔位置的精度:冲孔位置的精度对于零件的质量和装配性能有很大影响。
因此,在设计模具时需要特别注意冲孔位置的精度要求,并通过合理的设计和加工保证冲孔位置的精度。
4.设计合理的导向装置:为了确保模具在使用过程中的精度和稳定性,需要设计合理的导向装置,保证模具在工作时能够准确导向。
总结:落料冲孔复合模具设计需要根据零件的工艺要求和性能要求来设计模具的结构和工艺。
冲孔落料复合模设计
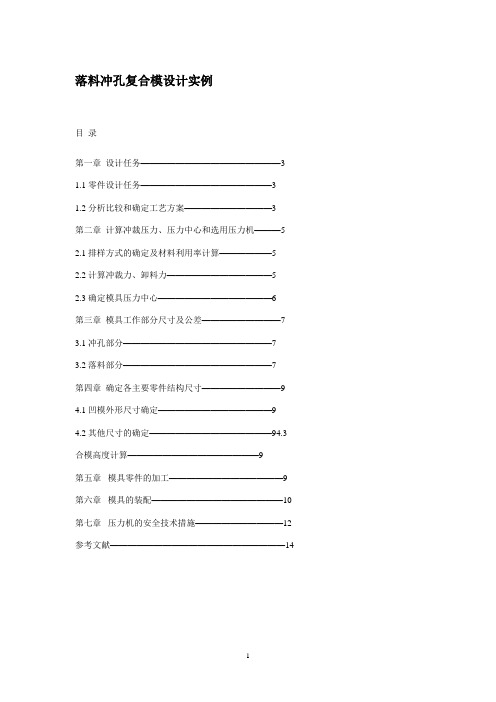
落料冲孔复合模设计实例目录第一章设计任务————————————————3 1.1零件设计任务———————————————31.2分析比较和确定工艺方案——————————3第二章计算冲裁压力、压力中心和选用压力机———5 2.1排样方式的确定及材料利用率计算——————52.2计算冲裁力、卸料力————————————52.3确定模具压力中心—————————————6第三章模具工作部分尺寸及公差—————————7 3.1冲孔部分—————————————————73.2落料部分—————————————————7第四章确定各主要零件结构尺寸—————————9 4.1凹模外形尺寸确定—————————————94.2其他尺寸的确定——————————————94.3 合模高度计算———————————————9第五章模具零件的加工—————————————9 第六章模具的装配———————————————10 第七章压力机的安全技术措施——————————12 参考文献————————————————————14落料冲孔复合模设计实例(一)零件工艺性分析工件为图1所示的落料冲孔件,材料为Q235钢,材料厚度2mm ,生产批量为大批量。
工艺性分析内容如下:1.材料分析Q235为普通碳素结构钢,具有较好的冲裁成形性能。
2. 结构分析零件结构简单对称,无尖角,对冲裁加工较为有利。
零件中部有一异形孔,孔的最小尺寸为6mm ,满足冲裁最小孔径min d ≥mm 20.1=t 的要求。
另外,经计算异形孔距零件外形之间的最小孔边距为5.5mm ,满足冲裁件最小孔边距min l ≥mm 35.1=t 的要求。
所以,该零件的结构满足冲裁的要求。
3. 精度分析:零件上有4个尺寸标注了公差要求,由公差表查得其公差要求都属IT13,所以普通冲裁可以达到零件的精度要求。
对于未注公差尺寸按IT14精度等级查补。
由以上分析可知,该零件可以用普通冲裁的加工方法制得。
落料冲孔复合模具设计

落料冲孔复合模具设计绪论模具主要类型有:冲模,锻模,塑料模,压铸模,粉末冶金模,玻璃模,橡胶模,瓷模等。
除部分冲模以外的的上述各种模具都属于腔型模,因为他们一般都是依靠三维的模具形腔是材料成型。
(1)冲模:冲模是对金属板材进行冲压加工获得合格产品的工具。
冲模占模具总数的50%以上。
按工艺性质的不同,冲模可分为落料模,冲孔模,切口模,切边模,弯曲模,卷边模,拉深模,校平模,翻孔模,翻边模,缩口模,压印模,胀形模。
按组合工序不同,冲模分为单工序模,复合模,连续模。
(2)锻模:锻模是金属在热态或冷态下进行体积成型是所用模具的总称。
按锻压设备不同,锻模分为锤用锻模,螺旋压力机锻模,热模锻压力锻模,平锻机用锻模,水压机用锻模,高速锤用锻模,摆动碾压机用锻模,辊锻机用锻模,楔横轧机用锻模等。
按工艺用途不同,锻模可分为预锻模具,挤压模具,精锻模具,等温模具,超塑性模具等。
(3)塑料模:塑料模是塑料成型的工艺装备。
塑料模约占模具总数的35%,而且有继续上升的趋势。
塑料模主要包括压塑模,挤塑模,注射模,此外还有挤出成型模,泡沫塑料的发泡成型模,低发泡注射成型模,吹塑模等。
(4)压铸模:压铸模是压力铸造工艺装备,压力铸造是使液态金属在高温和高速下充填铸型,在高压下成型和结晶的一种特殊制造方法。
压铸模约占模具总数的6%。
(5)粉末冶金模:粉末冶金模用于粉末成型,按成型工艺分类粉末冶金模有:压模,精整模,复压模,热压模,粉浆浇注模,松装烧结模等。
目前,我国17000多个模具生产厂点,从业人数五十多万。
除了国有的专业模具厂外,其他所有制形式的模具厂家,包括集体企业,合资企业,独资企业和私营企业等,都得到了快速发展。
研究和发展模具技术,对于促进国民经济的发展具有特别重要的意义,模具技术已成为衡量一个国家产品制造技术的重要标志之一,随着工业生产的迅速发展,模具工业在国民经济中的地位日益提高,并在国民经济发展过程中发挥越来越大的作用。
落料冲孔复合模的设计

落料冲孔复合模的设计
落料冲孔复合模是一种常用的模具,常用于金属成形加工中。
下面介绍落料冲孔复合模的设计步骤。
1. 确定产品设计要求:包括产品尺寸、形状、质量要求等。
2. 确定材料选择:考虑到产品的使用环境及性能要求,选择适
合的材料。
3. 制定加工工艺:根据产品的尺寸、形状进行材料切割、折弯、冲孔等加工工艺的制定。
4. 设计模具结构:根据产品的工艺要求,选择合适的模具结构,包括打孔模、落料模、定位模等。
5. 设计模具的排列和定位:根据产品尺寸和工艺要求,确定模
具的排列和定位。
6. 设计模具的冷却系统:在模具设计中,合理的冷却系统可以
提高加工效率和降低成本。
7. 完成模具设计:根据以上步骤制定的要求,完成模具设计,
注意要对设计进行合理的校核和评估。
8. 制作模具:根据设计图纸和工艺流程制作模具。
9. 检验模具:对制作好的模具进行严格的检验和试模,确保模
具符合要求。
以上是落料冲孔复合模的设计步骤。
冲孔落料复合模具设计

冲孔落料复合模具设计
一、概述
冲孔落料复合模具是一种常见的复杂成型模具。
它通过模具做成空心
的产品,通常用于金属制品和塑料制品的制作,可以实现冲孔、落坯和成
型功能。
本文的主要内容是设计一种新型的冲孔落料复合模具,它具有较
高的体积效率、较高的加工精度,能够有效减少成型周期,并有效提高生
产率和工作效率。
二、复合模具结构
1.冲孔落料复合模具由上模、开口上模、开口下模和下模4部分组成,它们分别由定子构件组成,定子构件上设有冲孔板、落料板和成型板三种
板材。
2.上模包括定子座、凸模、凹模、垫块和支架等组成部分,它们相互
配合,形成复合模具的上表面。
3.定子构件支撑着开口上模和下模,开口上模上设有冲孔孔洞,而开
口下模上设有成型孔洞,它们两者之间隔有一定的距离,能够实现冲孔落
料功能。
4.下模由定子座、支架和支撑构件等组成,它们之间由螺栓和垫圈固定,形成复合模具的下表面。
三、冲孔落料复合模具优点
1.高体积效率:冲孔落料复合模具能够实现冲孔落料一体化,不需要
多种模具,能够有效减少模具组合,提高机械组合效率,节省生产空间,
提高生产效率。
2.高加工精度:冲孔落料复合模。
冲孔落料复合模具设计

冲孔落料复合模具设计一、引言冲孔落料是一种常见的金属板材加工方式,可以通过冲孔和落料来实现对材料上的孔洞和缺口的加工。
为了提高生产效率和产品质量,设计一种冲孔落料复合模具是十分关键的。
二、模具结构设计1.上模上模采用较硬的材料,如合金钢等,以提高其耐磨性和耐腐蚀性。
上模一般设计为多个冲孔模块的集合,可以根据产品的设计要求进行选择。
冲孔孔径的大小和形状需要根据产品的要求进行设计,一般可以通过拉伸槽的装置来调整冲孔的位置和角度。
2.下模下模采用较软的材料,如塑料或橡胶等,以减少对下方的金属板材的损伤。
下模的形状需要与上模的冲孔模块相匹配,以保证冲孔的准确性和质量。
下模可以通过气动或液动装置来实现冲孔和落料的动作,可以根据产品的要求进行调整。
三、模具工作原理当上模和下模合并时,上模的冲孔模块和下模的落料形状之间会形成一个工作腔。
通过施加压力,上模以一定的速度向下冲击,使上模冲孔模块与金属板材接触,将孔洞冲出。
同时,下模的形状会顶住冲孔孔洞,使其成为落料形状。
当冲孔和落料动作完成后,上模和下模分开,取出已经冲孔和落料的金属板材。
四、模具优化设计在冲孔落料复合模具设计过程中,要考虑以下几个方面的优化设计。
1.优化上模的冲孔模块排列方式,使得冲孔过程更加均匀、稳定,并减少模具的使用次数和更换时间。
2.优化下模的形状和结构,通过减小落料形状的尺寸和加工槽口的数量,以提高产品的加工精度和成品率。
3.采用先进的材料和工艺,如表面处理和涂层等,以提高模具的耐用性和寿命。
4.考虑模具的维修和维护问题,设计合理的拆卸和安装装置,以便进行模具的更换和维修。
五、结论冲孔落料复合模具的设计是一项复杂而重要的工作。
通过优化设计模具的结构和工作原理,可以提高产品的加工效率和质量,并减少对模具的使用和更换次数。
因此,在实际设计中,需要综合考虑材料性能、工艺要求和经济效益,以达到最佳的设计效果。
冲压模具设计方案研究以垫片落料冲孔复合模为例

SolidWorks软件概述
SolidWorks是一款由达索系统开发的三维CAD软件,它适用于各种机械设计 领域,包括模具设计。SolidWorks具有强大的图形绘制功能,支持零件建模、装 配体设计、工程图制作等。此外,软件还提供了丰富的材料库、标准件库和渲染 工具,方便设计师进行产品建模、性能分析和效果图制作。
3、设计模具结构:根据工艺分析结果,设计模具的结构,包括垫片的定位、 落料口的尺寸和位置、冲孔的形状和深度等。
4、选用材料和标准件:根据模具的结构和设计要求,选用合适的材料和标 准件,如模架、弹簧、螺栓等。
5、完成细节设计:对模具的细节部分进行设计,如斜楔、导柱、加热元件 等。
6、绘制模具图:完成模具结构设计后,绘制模具装配图和零件图,标注技 术要求和加工信息。
制造质量和生产效率。经过实际生产验证,该模具的定位准确、运行稳定, 能够高效地生产出合格的刹车片产品。与传统的冲压工艺相比,垫片落料冲孔复 合模的使用简化了生产流程,提高了生产效率,降低了生产成本和劳动强度。
因此,垫片落料冲孔复合模在汽车刹车片的生产中取得了良好的应用效果和 经济效果。
结论
本次演示对垫片落料冲孔复合模的设计方案进行了研究,重点探讨了模具的 结构设计、制造工艺和关键技术点。通过案例分析,阐述了垫片落料冲孔复合模 在工业生产中的应用及实际效果。结果表明,合理的模具设计方案对于提高模具 的制造质量和生
冲压工艺与冲压模具设计在制造业中具有重要地位,特别是在汽车、机械制 造等领域。本次演示将从冲压工艺和冲压模具设计的基本概念入手,深入探讨其 原理、特点和未来发展趋势。
一、冲压工艺基本原理及分类
冲压工艺是一种利用压力机将金属板料变形或分离,以获得一定形状、尺寸 和性能的零件的制造方法。冲压工艺按照工艺特点可分为分离工序和成形工序两 大类。分离工序是指将金属板料分割成若干个小部分,如冲裁、剪切等;成形工 序则是指将金属
垫圈落料冲孔复合模具设计

垫圈落料冲孔复合模具设计一、设计原则1.尺寸精确:模具设计的尺寸要精确,以确保最后制作出的垫圈符合规格要求。
2.结构紧凑:模具的结构要简单紧凑,以提高生产效率和质量。
3.制造成本低:要考虑到模具的制造成本,选用合适的材料和加工工艺,以降低生产成本。
4.使用寿命长:模具的设计要考虑到使用寿命,尽可能延长模具的寿命,避免频繁更换。
二、构造设计1.上模和下模:上模和下模是构成模具的主要部分,上模用于冲孔,下模用于落料。
上模和下模的尺寸要与垫圈的规格相匹配,确保加工出符合要求的垫圈。
2.垫圈导向机构:为了确保垫圈在冲压过程中位置准确,需要设计导向机构来限制垫圈的运动方向。
导向机构可以采用导向销、导向板等方式。
3.冲孔机构:冲孔是模具的主要功能之一,冲孔机构需要设计合适的冲头和冲孔座,确保冲出的孔径和位置准确。
4.落料机构:落料机构用于将原料板料送入模具,落料机构需要设计合适的导向和定位装置,确保原料板料的位置准确。
5.排渣机构:在冲孔过程中会产生大量的废料和渣滓,需要设计排渣机构,将废料排出,保持模具的干净。
6.压紧机构:在落料和冲孔过程中需要采用压紧机构,将模具和板料固定在一起,确保加工精度和质量。
三、工艺参数1.材料选择:模具的材料应选择具有较高硬度和韧性的特点,常用的材料有合金工具钢、高速钢等。
2.加工精度:模具加工的精度要求要与垫圈的规格相匹配,冲孔精度要小于垫圈的公差要求。
3.加工表面处理:为了延长模具的使用寿命,可以对模具进行表面处理,如镀硬铬、镀涂层等。
4.模具安装:模具的安装要牢固可靠,确保加工过程中没有松动和位移。
总结:垫圈落料冲孔复合模具设计的关键是尺寸精确、结构紧凑、制造成本低以及使用寿命长等。
通过合理的构造设计和工艺参数,可以实现高效、精确的垫圈制造。
- 1、下载文档前请自行甄别文档内容的完整性,平台不提供额外的编辑、内容补充、找答案等附加服务。
- 2、"仅部分预览"的文档,不可在线预览部分如存在完整性等问题,可反馈申请退款(可完整预览的文档不适用该条件!)。
- 3、如文档侵犯您的权益,请联系客服反馈,我们会尽快为您处理(人工客服工作时间:9:00-18:30)。
冲孔复合模具设计5226冲孔复合模具设计摘要:垫圈冲孔复合模设计,它的结构的主要特征是有一个既是落料凸模又是冲孔凹模的凹凸模。
这一复合模为倒装式复合模,凹凸模装在下模,落料凹模和冲孔凸模装在上模。
采用刚性推件装置把卡在凹模中的冲件推下,刚性冲件由打杆、推板、连接推杆组成。
冲孔废料直接由冲孔凸模从凸凹模内孔推下,无顶件装置,结构简单,操作方便,主要完成冲孔、落料两道工序。
由打杆顶出制件,橡胶垫驱动的卸料板卸除条料。
由弹性挡料销和导料销定位、导料。
模架为后侧导柱圆形模架,压入式模柄。
由于垫圈的生产为大批量生产,所以在使用模具的前后都应注重模具的保养和修复,防止生产出误差过大的不合格产品。
本次设计使用CATIA绘制零件实体并完成装配,进而生成装配工程图和相关的零件图。
关键词:冲孔复合模具 CATIA 设计1 引言1.1CATIA简介本次设计主要运用了CATIA进行作图设计,下面是关于CATIA的简单介绍。
CATIA具有完备的设计能力和很大的专业覆盖面,它是一套集成的软件应用包,内容覆盖了产品设计的各个方面,包括:计算机辅助设计(CAD),计算机辅助工程分析(CAE)和计算机辅助制造(CAM)。
它既具有各种类型的协同产品设计的必要功能,也可以进行无缝集成完成支持“端到端”的企业流程解决方案,其特有的DMU电子样机模块功能及混合建模技术更使企业竞争力和生产力的提高。
使用CATIA V5版本,可为数字化企业建立一个针对产品整个开发过程的工作环境。
在这个环境中,可以对产品的开发过程进行仿真,实现工人之间的电子通信和产品整个开发过程,包括概念设计、详细设计、工程设计、成品定义和制造乃至成品在整个生命周期中的使用和维护。
总的来说,CATIA具有以下几个方面的特点和应用。
(1)先进的混合建模技术和后期修改性。
设计对象的混合建模:在CATIA V5的设计环境中,无论是实体还是曲面,都做到了真正的互操作。
变量和参数化混合建模:在设计时,用户不必考虑参数化设计目标,CATIA V5提供了变量驱动和后参数化能力。
几何和智能工程混合建模:对于一个企业来说,可以将企业多年的经验积累到CATIA V5的知识库中,用于指导企业新员工,或者指导新产品的开发,以缩短新产品推向市场的时间。
方便的修改性:CATIA V5具有方便的修改能力。
无论是实体建模还是曲面造型,由于CATIA V5提供了智能化的树结构,用户方便快捷的对产品进行重复修改。
在设计的过程中做修改,或者是对方案的更换,都是很简单的事情。
(2)CATIA V5提供了各模块的全相关性和完备的设计能力。
CATIA V5的各个模块以相同的数据裤为前提,因此CATIA V5的各个模块存在着真正的全相关性。
三维模型的修改能完全体现在二维、有限元分析、模具和数控加工的程序中。
这样就使产品就从概念设计到最终产品的形成,从单个零件的设计到最终电子样机的建立,具有统一的数据结构,也将机械设计、工程分析及仿真、数控加工和网络应用解决方案有机的结合在一起,为用户提供完整的解决方案和严密的无纸工作环境。
(3)并行工程的设计环境。
CATIA V5提供了多模型链接的工作环境及混合建模方式,使得并行工程设计模式已不再是概念,总设计部门只要把基本的结构尺寸发放下层部门,各分系统的人员便可以开始工作,即可协同工作又不互相牵连:由于模型之间的相互联结性,使得上游设计结果可作为下游设计的参照,同时,上游设计的修改可直接对下游工作进行刷新,实现真正的并行设计工作环境,从而大大缩短设计周期。
(4)强大电子商务能力。
CATIA V5的基础结构支持即插即用功能的扩展,如OLE;可使用Visual Basic进行高级宏编程。
因此,不管工厂规模如何,使用电子设计和文件资料的二次开发应用,会大大增强企业的竞争力。
(5)与NT和UNIX硬件平台的独立性。
CATIA V5是在Windows NT平台和UNIX平台上开发完成的,并在所有其支持的硬件平台上具有统一的数据、功能、版本发放日期、操作环境和应用支持。
1.2模具工业及其发展1、模具工业在国民经济中的地位模具是制造业的一种基础工艺装备,在机械、电子、轻工、汽车、纺织、航空航天等工业领域里,日益成为使用最广泛的主要工艺装备,它承担了这些工业领域中60%~90%的产品零件、组件和部件的生产加工。
、模具生产出的制件具有较高的精度、复杂度、一致性、生产率和低消耗,是其他加工制造方法所不能比拟的。
模具生产技术水平的高低,已成为衡量一个国家产品制造水平高低的重要标志,在很大程度上决定着产品的质量、效益和新产品的开发能力。
模具工业是国民经济的基础工业,是国际上公认的关键工业。
模具制造的重要性还体现在市场需求上,仅以汽车摩托车行业的模具市场为例。
在发达的国家中,模具的最大市场主要在汽车摩托车这一块,占市场的50%左右。
汽车基本车型不断增加,模具的更新换代也会随之而来。
汽车换型时约有80%的模具需要更换。
中国摩托产量位居世界第一,据统计,我国摩托车共有14种排量、80多个车型,1000多个型号。
单辆摩托车的零部件有过半的零件生产需要模具。
其他的行业,如电子,通信,家电及建筑等,也存在巨大的模具市场。
2、我国模具技术的现状及发展趋势我国模具工业从起步到现在,历经了半个多世纪,近几年来,我国模具技术有了很大的发展,模具水平有了较大的提高。
大型、精密、复杂、高效和长寿命的模具有了很好的提升。
我国主要汽车模具企业,已能生产部分轿车覆盖件模具体现高水平制造技术的多工位级进模,已经从电机、电铁芯片模具,扩大到接插件、电子零件、汽车零件、空调器散热片等家电零件模具上。
塑料模热流道技术更趋成熟,气体辅助注射技术已开始采用。
模具质量、寿命显著提高,模具交货期较前缩短。
模具CAD/CAM/CAE 技术在大范围内得到较为广泛的应用。
电加工在制造模具的发展中有着举足轻重的作用。
模具加工机床品种增多,水平明显提高。
模具标准件应用更加广泛,品种有所扩展。
模具材料方面由于对模具寿命的重视,优质模具钢的应用有较大进展。
正由于模具行业的技术进步,模具水平得以提高,模具国产化取得了可喜的成就。
历年来进口模具不断增长的势头得到控制,模具出口量稳步增长。
模具技术有以下发展趋势:(1)模具CAD/CAM/CAE正向集成化、三维化、正能化和网络化方向发展(2)模具制造向高效、精密、复合和多功能方向发展(3)快速经济制模技术得到应用(4)特种加工技术有了进一步发展(5)高速铣削加工得到更广泛的应用(6)模具高速扫描及数字化系统将在逆向工程中发挥更大作用(7)超精加工和复合加工将得到发展(8)模具标准化程度将不断提高(9)模具材料及表面处理技术发展迅速2 工艺分析及模具结构设计2.1设计要求图1 零件图如图1所示零件:垫圈(摘自GB/T97、1-2002)生产批量:大批量材料:08F 优质碳素结构钢 t=2mm设计该零件的冲压工艺与模具 2.2零件的工艺析产品为规则圆形,落料和冲孔也均为圆形。
形状结构对称且简单,无狭槽和尖角;孔与零件边缘之间的最小距离满足c>1.5t 要求。
(75.222544=--=c 1.5t=3) (1)尺寸精度任务书对冲件的尺寸精度没有作要求。
所以根据其他技术要求来确定尺寸精度。
(2)冲裁件断面质量本零件在断面粗糙度上没有要求,所以只要模具精度达到一般要求,在冲裁后加修整工序,冲裁件断面的质量就可以保证。
(3)产品材料分析对于冲压件材料的要求是低强度,高塑性,表面质量和厚度公差符合国家标准。
本设计的产品材料为08钢,属优质碳素结构钢,其力学性能是强度、硬度低而塑性较好,非常适合冲裁加工。
其冲裁出的产品表面质量和厚度公差可以很好的得到保证。
经上述分析,该零件适合冲裁加工。
选用一般模具材料就能够满足该模具对材料强度的要求,又由于零件为大批量生产,选用模具材料时适当提高模具材料的一个档次。
从零件精度方面看,该零件对公差等级没做特别要求,设计精度要求较低,普通冲裁模生产的冲件一般都可以达IT11级,所以选用的冲裁模为一般精度就可以满足此零件的生产要求。
查看参考文献[5]中的表格11-9,比较三种主要冲模,根据零件的实际尺寸情况,决定采用复合模冲裁该零件。
由于冲模的结构简单、制造周期短,价格低,而且通用性好,所以采用复合模冲裁该零件。
2.3排样和压力计算1、排样零件为规则圆形 ,考虑到零件为大批量生产,如果采用交叉双排或多排,则模具尺寸和结构就会相应增大,从而增加模具生产成本,所以本设计决定采用单排结构。
如图2所示。
图2 排样查看参考文献[10],确定搭边当t=2时,a=2.4mm,b=2mm所以条料宽度B=44+2.4*2=48.8mm材料利用率η:%100⨯=SBnA η 式中 n —一个歩距内冲裁件数目; A ——冲裁件面积;S ——歩距长度; B ——板料宽度;取:n=1; A=π*22²=1520.53;S=46;B=48.8η=1520.53/46*48.8=67.73%2、计算冲压力(1)冲裁力冲裁力公式为落孔P P P +=式中 P —冲裁力;孔P —冲孔冲裁力;落P —落料冲裁力。
(2) 冲孔冲裁力孔Pτt nKL P 孔孔=式中 K —系数(取K=1.1);n —孔的个数,n=1。
孔L —冲孔周长,54.78251=⨯==ππd L 孔mmt —材料厚度,mm 2=tτ—材料抗剪强度,查参考文献[10]知,90=τMPa 。
N P 46.777590154.781.1=⨯⨯⨯=孔(3) 落料冲裁力落P 。
τt KL P 落落=mm D L 23.13844=⨯==ππ落所以 N 05 .1866190123.1381.1=⨯⨯⨯=落P(4)卸料力卸P落卸卸P K P =式中 卸K —卸料系数,查参考文献[10]知08.0~05.0=卸K ,取06.0=卸K 。
所以 N P 66.111905.1866106.0=⨯=卸(5)推料力推P孔推推P nK P =式中 推K —推料系数,查参考文献[10]取055.0=推K 。
n —同时卡在凹模洞孔内的件数,1=n 。
所以 N P 65.42746.777555.001=⨯⨯=推(6)顶件力顶P)(落孔顶顶P P K P += 式中 顶K —顶件系数,查参考文献[10]取06.0=顶K 。
所以 ()N P 19.158605.1866146.777506.0=+⨯=顶(7)总冲压力总P冲裁时,压力机的压力值必须大于或等于冲裁各工艺力的总和。
总的冲压力为 KNN P P P P P P P P P P 57.2901.2957019.158665.42766.111905.1866146.7775==++++=++++=+++=顶推卸落孔顶推卸总选定符合压力供给要求的压力机J23-16。