setm0002 石油化工厂蒸汽系统设计技术规定
2024年蒸汽系统安全操作规(2篇)
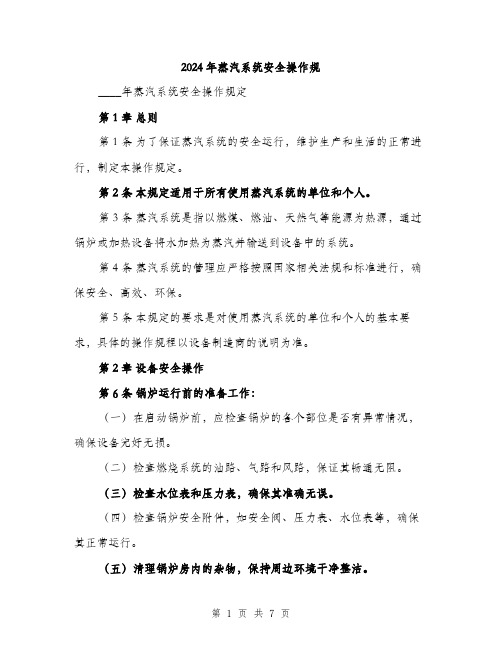
2024年蒸汽系统安全操作规____年蒸汽系统安全操作规定第1章总则第1条为了保证蒸汽系统的安全运行,维护生产和生活的正常进行,制定本操作规定。
第2条本规定适用于所有使用蒸汽系统的单位和个人。
第3条蒸汽系统是指以燃煤、燃油、天然气等能源为热源,通过锅炉或加热设备将水加热为蒸汽并输送到设备中的系统。
第4条蒸汽系统的管理应严格按照国家相关法规和标准进行,确保安全、高效、环保。
第5条本规定的要求是对使用蒸汽系统的单位和个人的基本要求,具体的操作规程以设备制造商的说明为准。
第2章设备安全操作第6条锅炉运行前的准备工作:(一)在启动锅炉前,应检查锅炉的各个部位是否有异常情况,确保设备完好无损。
(二)检查燃烧系统的油路、气路和风路,保证其畅通无阻。
(三)检查水位表和压力表,确保其准确无误。
(四)检查锅炉安全附件,如安全阀、压力表、水位表等,确保其正常运行。
(五)清理锅炉房内的杂物,保持周边环境干净整洁。
第7条锅炉运行中的操作控制:(一)密切关注锅炉的运行情况,特别是水位和压力变化,如发现异常及时进行处理。
(二)严禁擅自调整锅炉的参数,如需调整应由专业人员进行。
(三)定期检查锅炉的燃烧情况及烟气排放情况,如发现异常应及时调整。
(四)严禁在锅炉周围进行乱堆乱放,防止堵塞燃烧系统。
(五)锅炉在运行中如出现异常应立即停机进行检查,排除故障后方可重新运行。
第8条锅炉停止运行及维护:(一)锅炉停止运行后,应先关闭燃料供给,并停止给锅炉供水。
(二)待锅炉冷却后,进行清理和维护工作,如换烟罩、清理烟道等。
(三)定期进行锅炉的检修工作,如清理燃烧器、检查安全附件等。
(四)定期检测锅炉的运行状态,如水质、排放指标等,确保其正常运行。
第3章蒸汽系统安全操作第9条蒸汽系统在运行前应进行如下操作:(一)检查系统的运行状态,如排放系统、输送管道等。
(二)检查蒸汽系统的安全附件,如安全阀、防爆盖等,确保其正常运行。
(三)排查系统中的杂物和堵塞物,并进行清理。
石油化工装置蒸汽管道设计要点与注意事项-化工论文-化学论文
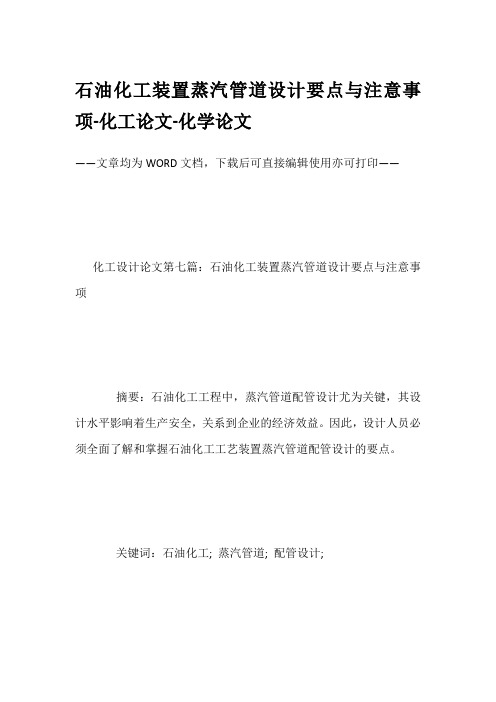
石油化工装置蒸汽管道设计要点与注意事项-化工论文-化学论文——文章均为WORD文档,下载后可直接编辑使用亦可打印——化工设计论文第七篇:石油化工装置蒸汽管道设计要点与注意事项摘要:石油化工工程中,蒸汽管道配管设计尤为关键,其设计水平影响着生产安全,关系到企业的经济效益。
因此,设计人员必须全面了解和掌握石油化工工艺装置蒸汽管道配管设计的要点。
关键词:石油化工; 蒸汽管道; 配管设计;0 引言蒸汽管道在工艺装置中发挥着重要作用,蒸汽管道主要分为蒸汽凝结水管道和蒸汽管道,应用蒸汽管道能够节约能源,减少环境污染,提高石油化工生产的经济效益。
1 蒸汽管道概述蒸汽管道主要由蒸汽凝液管道和蒸汽管道两部分组成,蒸汽管道属热力管道,热力管道也被人们称为热力管网。
热力管网主要指锅炉所在地提供热量形成热管道的热力管网。
热力管网分为两种,一种是蒸汽管网,一种是热水热网。
蒸汽管网主要可分为高压、中压和低压三种不同的类型。
2 石油化工工艺装置蒸汽管道配管设计要点2.1 管廊蒸汽管道布置管廊蒸汽管道布置中,应将蒸汽管道布置在管廊一侧,其能够为型补偿器的设置提供诸多的便利。
同时,波纹管膨胀节需要投入较高的成本,使用寿命较短,因此在蒸汽管上通常不设置膨胀节,而是以其他方式吸收管道热量。
在设计管道型补偿器位置时,规定高压蒸汽管道的间隔为50m,中压蒸汽管道的间距为80m,低压和低低压蒸汽管道间距为100m。
建设项目的不同,用气量也会存在一定差异,蒸汽管道的直径也会发生较大改变,故而应根据应力要求,准确计算所需的蒸汽管道直径。
以集中统一的形式布置型补偿器,大补偿储量管道应设置在外侧,小补偿储量的管道设置在内侧。
两个固定点中间的位置设置型补偿器效果最为理想。
若无法在中间设置,则需尽量缩短其与固定点的间距。
其数值要在两个固定点距离的1/3以内,同时,在形补偿器的两端应设置应力导向架,以管道应力计算所获得的最终数值来明确补偿器固定点推力。
化工厂蒸汽系统设计规范
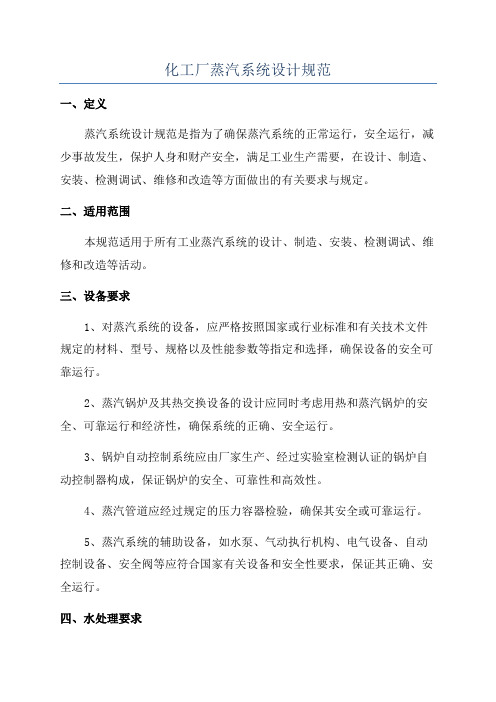
化工厂蒸汽系统设计规范
一、定义
蒸汽系统设计规范是指为了确保蒸汽系统的正常运行,安全运行,减少事故发生,保护人身和财产安全,满足工业生产需要,在设计、制造、安装、检测调试、维修和改造等方面做出的有关要求与规定。
二、适用范围
本规范适用于所有工业蒸汽系统的设计、制造、安装、检测调试、维修和改造等活动。
三、设备要求
1、对蒸汽系统的设备,应严格按照国家或行业标准和有关技术文件规定的材料、型号、规格以及性能参数等指定和选择,确保设备的安全可靠运行。
2、蒸汽锅炉及其热交换设备的设计应同时考虑用热和蒸汽锅炉的安全、可靠运行和经济性,确保系统的正确、安全运行。
3、锅炉自动控制系统应由厂家生产、经过实验室检测认证的锅炉自动控制器构成,保证锅炉的安全、可靠性和高效性。
4、蒸汽管道应经过规定的压力容器检验,确保其安全或可靠运行。
5、蒸汽系统的辅助设备,如水泵、气动执行机构、电气设备、自动控制设备、安全阀等应符合国家有关设备和安全性要求,保证其正确、安全运行。
四、水处理要求
1、蒸汽系统的水质入口应达到相应的水质标准。
浅谈石油化工工艺装置的蒸汽管道设置
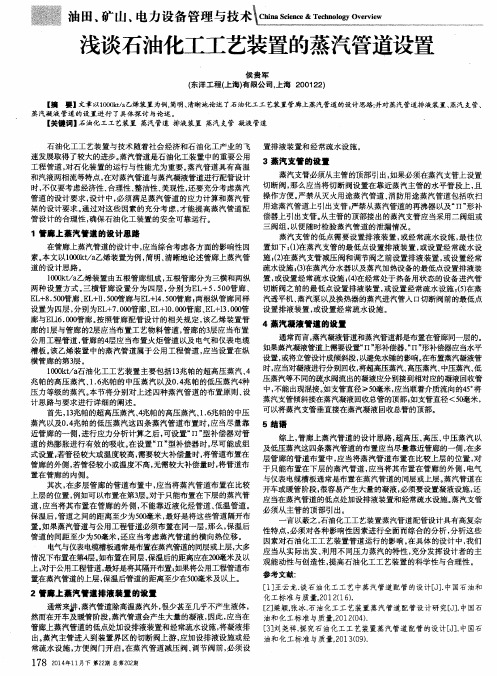
浅谈石油化工工艺装置的蒸汽管道设置
侯 贵 军 ( 东洋工程( 上海) 有 限公司, 上海 2 0 0 1 2 2 ) 【 摘 要】文章  ̄ X 1 0 0 0 k t / a 乙烯装 置为例, 简明、 清晰 地论述 了石油化工工 艺装 置管廊上 蒸汽管道的设计 思路; 并对蒸汽 管i 鲋 液装 置、 蒸汽支管 、 蒸汽凝 液 管道 的设置进 行 了具体 探讨 与论 述 。 【 关键 词 】 石 油化 工 工艺装置 蒸汽 管道 排液装 置 蒸 汽支管 凝 液管道 ’
石油化工工艺装置与技术 随着社会 经济和石油化工产业的飞 速发展取得了较大 的进步。 蒸汽管道是石油化工装置 中的重要公用 工程管道 , 对石化装置的运行与性能尤为重要。 蒸汽管道具有高温 和汽液两相流等特点 , 在对蒸汽管道 与蒸汽凝液管道进行配管设计 时, 不仅要考虑经济性 、 合理性、 整洁性、 美观性 , 还要充分考虑蒸汽 管道 的设计要求 , 设计 中, 必须满足蒸汽管道的应力计算和蒸汽管 架 的设计要求 。 通过 对这 些因素的充分考 虑 , 才能提高蒸汽管道配 管设计 的合理性 , 确保石油化工装置的安全可靠运行 。
置如下 : ( 1 ) 在蒸汽支管 的最低点设置排液装置 , 或设置经常疏水设 施; ( 2 ) 在蒸汽支管减压 阀和调节阀之前设置排液装置 , 或设 置经常 疏水设施 , ( 3 ) 在蒸汽分水器以及蒸汽加热设备 的最低点设置排液装
置, 或 设置 经 常 疏水 设 施 ; ( 4 ) 在 经 常 处 于 热 备 用 状 态 的设 备 进 汽管 切断阀之前 的最低点设置排液装置 , 或设置 经常疏水设施 ; ( 5 ) 在蒸 汽透平机、 蒸汽泵以及换热器的蒸汽进汽管入 口切断阀前的最低点 设置排液装置 , 或设置经常疏水设施 。
石油化工企业燃料气系统
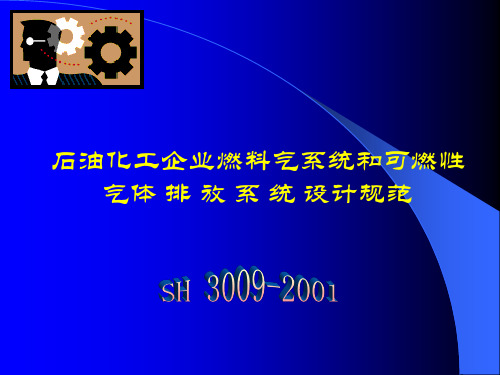
2.0.5 设计燃料气系统和可燃性气体排放系统时 ,装置内外应统一进行流体力学计算及应力计 算。 2.0.6 可燃性气体排放系统宜在下列各处设取样 点: 1 装 置 可然性排放气体进入排放总管前; 2 可 燃 性排放气体进入火炬前; 3 可 燃 性排放气体进入回收设施前。
2.0.7 分液罐、凝结液收集罐、水封罐、气柜等 设备及管网系统,应根据需要采取防冻措施。 2.0.8 燃料气和可燃性气体排放管网的低点应有 密闭排凝措施。
本规 范 共 分4章和4个附录。这次修 订的主要内容有:增加了装置内外应 统一进行热应力计算及对可燃性气 体排放工况进行分析的规定:增加了 避免两相流动冲击力的措施。 在修 订 过 程中,针对原规范中存在 的问题,进行了广泛的调查研究, 总结了近几年来石油化工燃料气系 统和可燃性气体排放系统设计的实 践经验,参照国际先进规范,并征 求了有关设计、施工、生产、科研 等方面的意见,对其中主要问题进 行了多次讨论,最后经审查定稿。
2.0.3 燃料气系统和可燃性气体排放系统的设 计,应考虑下列要求: 1 总 工 艺流程对全厂燃料平衡的要求(包括 分期建设和不同加工方案); 2 装 置 正常生产、开停工、事故处理、维修 吹扫时装置对系统以及系统对装置的要求: 3 燃 料 气中氢、液化烃组分含量较高时,宜 考虑回收利用。
2.0.4 需与外部管网连接的装置,其内部的燃 料气管道和可燃性气体排放管道,应符合下 列要求: 1 装 置 内送出然料气的操作温度不宜高于 400C ,操作压力应与外部管网燃料气系统的 控制压力相适应; 2 装 置 内应有本装置自行吹扫可燃性气体和 排放的措施: 3 高 于 常温并含有碳五以上烃类的可燃性气 体排出装置之前,应经分液罐分液,对于含 有粉尘和固体颗粒物的排放气体还应除尘。
石油化工装置详细工程设计内容规定
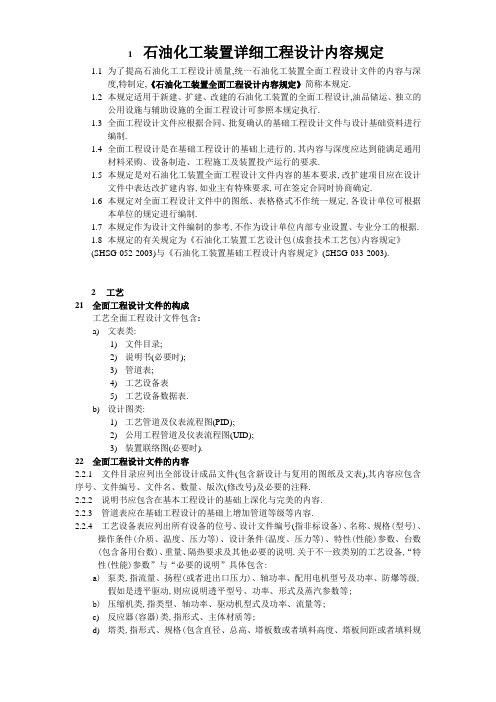
1石油化工装置详细工程设计内容规定1.1为了提高石油化工工程设计质量,统一石油化工装置全面工程设计文件的内容与深度,特制定,《石油化工装置全面工程设计内容规定》简称本规定.1.2本规定适用于新建、扩建、改建的石油化工装置的全面工程设计,油品储运、独立的公用设施与辅助设施的全面工程设计可参照本规定执行.1.3全面工程设计文件应根据合同、批复确认的基础工程设计文件与设计基础资料进行编制.1.4全面工程设计是在基础工程设计的基础上进行的,其内容与深度应达到能满足通用材料采购、设备制造、工程施工及装置投产运行的要求.1.5本规定是对石油化工装置全面工程设计文件内容的基本要求,改扩建项目应在设计文件中表达改扩建内容,如业主有特殊要求,可在签定合同时协商确定.1.6本规定对全面工程设计文件中的图纸、表格格式不作统一规定,各设计单位可根据本单位的规定进行编制.1.7本规定作为设计文件编制的参考,不作为设计单位内部专业设置、专业分工的根据.1.8本规定的有关规定为《石油化工装置工艺设计包(成套技术工艺包)内容规定》(SHSG-052-2003)与《石油化工装置基础工程设计内容规定》(SHSG-033-2003).2工艺21全面工程设计文件的构成工艺全面工程设计文件包含:a)文表类:1)文件目录;2)说明书(必要时);3)管道表;4)工艺设备表5)工艺设备数据表.b)设计图类:1)工艺管道及仪表流程图(PID);2)公用工程管道及仪表流程图(UID);3)装置联络图(必要时).22全面工程设计文件的内容2.2.1 文件目录应列出全部设计成品文件(包含新设计与复用的图纸及文表),其内容应包含序号、文件编号、文件名、数量、版次(修改号)及必要的注释.2.2.2 说明书应包含在基本工程设计的基础上深化与完美的内容.2.2.3 管道表应在基础工程设计的基础上增加管道等级等内容.2.2.4 工艺设备表应列出所有设备的位号、设计文件编号(指非标设备)、名称、规格(型号)、操作条件(介质、温度、压力等)、设计条件(温度、压力等)、特性(性能)参数、台数(包含备用台数)、重量、隔热要求及其他必要的说明.关于不一致类别的工艺设备,“特性(性能)参数”与“必要的说明”具体包含:a)泵类,指流量、扬程(或者进出口压力)、轴功率、配用电机型号及功率、防爆等级,假如是透平驱动,则应说明透平型号、功率、形式及蒸汽参数等;b)压缩机类,指类型、轴功率、驱动机型式及功率、流量等;c)反应器(容器)类,指形式、主体材质等;d)塔类,指形式、规格(包含直径、总高、塔板数或者填料高度、塔板间距或者填料规格)、主体材质等;e)换热器类,指形式、主体材质、设计参数(管、壳程分别填写);f)工业炉类,指形式、热负荷、炉管材质等.注:“工艺设备”包含泵类、压缩机类、反应器类、塔类、换热器类、容器类、工业炉类及其它类(如过滤器、混合器、消音器、喷射器、干燥机、破碎机、固体物料输送机等).2.2.5 工艺设备数据表应在基础工程设计的基础上根据供货商的资料进行修改与完善.2.2.6 “工艺管道及仪表流程图(PID)”与“公用工程管道及仪表流程图(UID)”应在基础工程设计的基础上增加需要补充与修改的内容,如各专业的要求、管道接点及全部辅助管线、放空、排净及供货商信息等.2.2.7 关于多个装置且由几个设计单位完成的大型工程设计项目应绘制装置联络图,图中应说明各装置之间相互连接的管道(包含管件、阀门、仪表、装置内PID图已有表示的管件、阀门、仪表等除外)及各装置界区线.3设备3.1全面工程设计文件的构成设备全面工程设计文件包含:a)文表类1)文件目录2)强度计算书;3)技术条件.b)设计图类包含全面工程设计图.3.2全面工程设计文件的内容3.2.1 文件目录详见2.2.1条.3.2.2 强度计算书,设备应按规定的标准、规范进行强度与稳固计算,按应力分析法设计时还应提出应力分析报告.(按有关规定,除移动式压力容器,高压容器、第三类中压反应容器与储存容器外,不向使用单位提供强度计算书.)3.2.3 技术条件通常应包含下列内容:a)单体设备制造、检验及验收所遵循的法则、标准、规范及有关规定;b)设备所用材料的标准、供货状态、钢板无损检测、锻件级别、焊接材料等;c)焊接:焊接方法、焊缝表面形状及外观、焊接返修等要求;d)无损检测要求,明确焊接接头无损检测的种类、检测比例、合格级别;e)热处理要求,明确设备是否热处理,热处理的方法、热处理遵循的标准、规范及操纵指标;f)必要时,应有设备安装使用说明书;g)设备的包装与运输的要求.明确设备包装与运输遵循的有关标准;关于大型超限设备,因运输条件的限制,同意分片或者分段交货,但应提出相应的要求;关于可拆卸的内件及其备件应根据各自的特点提出特殊要求;h)其它要求.3.2.4全面工程设计图表示的内容应包含设计条件表、管口表、零部件名细表、设计图样、备注。
石油化工企业设计防火规范(消防)

石油化工企业设计防火规范(七)第七章消防第一节一般规定第7.1.1条石油化工企业应设置与生产、储存、运输的物料相适应的消防设施,供专职消防人员和岗位操作人员使用。
第二节消防站第7.2.1条石油化工企业应设消防站。
消防站的规模,应根据工厂的规模、火灾危险性、固定消防设施的设置情况,以及邻近单位消防协作条件等因素确定。
第7.2.2条消防站的服务范围,应按行车路程计,行车路程不宜大于2.5km;并且接火警后消防车到达火场的时间不宜超过5min。
对丁、戊类的局部场所,消防站的服务范围可加大到4km。
第7.2.3条消防站的位置,应满足下列要求:一、应便于消防车迅速通往工艺装置区和罐区;二、宜避开工厂主要人流道路;三、宜远离噪声场所;四、宜位于生产区全年最小频率风向的下风侧。
第7.2.4条消防站车辆的配置数量,应根据灭火系统设置情况满足扑救最大火灾的要求。
第7.2.5条石油化工企业消防车辆的车型配备,应以大型泡沫消防车为主,且应配备干粉或干粉—泡沫联用车;大型石油化工企业尚宜配备高喷车和通讯指挥车。
第7.2.6条消防站必须设置接受火灾报警的设施和通讯系统,其设置应满足下列要求:一、电话报警系统的受警电话应为录音电话;二、当设有自动报警、手动报警按钮系统时,宜设置报警信号显示盘;三、当企业设有电视安全监视系统时,消防站宜设置显示屏幕;四、当企业设有自动灭火系统时,其反馈信号在消防站宜有显示。
第7.2.7条消防站内储存泡沫液量较多时,宜设置向消防车快速灌装泡沫液的设施。
一级消防站尚宜设置泡沫液罐拖车或运输车,且车上应配备向消防车输送泡沫液的设施。
第7.2.8条消防总站应由车库、通讯室、办公室、值勤宿舍、药剂库、器材库、蓄电池室、干燥室(寒冷或多雨地区)、培训学习室及训练场、训练塔,以及其他必要的生活设施等组成。
消防分站的组成,可根据实际需要确定。
第7.2.9条消防车库的耐火等级不应低于二级;车库室内温度不宜低于12℃。
第二章_蒸汽系统_第一节_蒸汽系统的一般规定

第二章蒸汽系统第一节蒸汽系统的一般规定1)蒸汽、凝水系统是需要送审的系统有时可将舱柜加热系统单独绘设,该加热系统也要送审。
加热管的固定形式要反映上去。
2)大于0.7Mpa蒸汽系统选用II级管;蒸汽压力超过1.63Mpa,DNV超过1.6Mpa或温度超过300℃时,应选用I级管。
在管子材料表中要注明。
3)所有大于0.7Mpa工作压力的阀件及附件应有船级社证书,应在零件表上标明。
4)锅炉安全阀泄压管与安全阀之间应有膨胀节(按制造厂要求)。
5)安全阀的泄压管大小应该厂家推荐,向上引至烟囱的管段弯头也不宜多,否则影响安全阀起跳后的关闭性能。
6)炉体上的泄水管有:安全阀本身设有的泄水管,安全阀泄压管设置的放水管,炉顶放气阀管;水位表下面的冲洗阀管,上述放水管总共5×2共10条,应集中至炉边下部一个安全位置的漏斗上,在原理图上应反映出来。
7)多余蒸汽泄放阀前后连接阀的大小应按照厂家推荐,例如:多余蒸汽泄放阀口径为DN32,而阀前要求连接DN65截止阀,阀后要求连接DN80的截止阀,异径接头应在图中标示,旁通阀可根据进入管径大小来定。
8)多余蒸汽泄放阀组厂家建议放在大气冷凝器附近,但实船该泄放设在锅炉旁未发现有大的问题,主机在100%负荷时,关闭主蒸汽阀出口,多余蒸汽阀自动起跳,15分钟内,炉顶安全阀不起跳。
证明多余蒸汽阀的布置位置没有问题。
但如确实需要按厂家布置在大气冷凝器附近,即应在图上说明,以免引起误工。
9)集气分配筒的个数和尺寸大小视机舱用汽支气管多少的情况而定。
集管可用φ100的管做成,其上除出气管外,还应设置φ100表径的压力表(带根部阀),泄放阀,通岸接头支管阀,蒸汽伴行用总管阀,备用支管阀。
10)蒸汽压力根据规格书要求,一般是0.7Mpa及0.4Mpa,前者用于油柜加热及伴行,后者用于生活杂用或伴行,有蒸汽透平机械的船,还有大一些的蒸汽压力,如1.8Mpa,在蒸汽集气分配筒上分别设置减压站。
化工厂蒸汽系统设计规范

术语....................................................................................................................................................... 2 系统类型及规模................................................................................................................................... 4 4.1 系统类型..................................................................................................................................... 4 4.2 系统规模...................................................................................................................................... 4
3 系统设计基本规定.................................................................................................................................. 3
5 6
系统组成............................................................................................................................................... 5 系统拟定及蒸汽平衡图 ....................................................................................................................... 6 6.1 6.2 6.3 6.4 6.5 6.6 拟定的依据............................................................................................................................... 6 系统拟定................................................................................................................................... 6 纯供热系统拟定....................................................................................................................... 6 热电(功)联产系统拟定 ....................................................................................................... 7 带燃气轮机的系统拟定 ........................................................................................................... 7 蒸汽平衡图............................................................................................................................... 8
石油化工企业可燃性气体排放系统设计规范条文说明
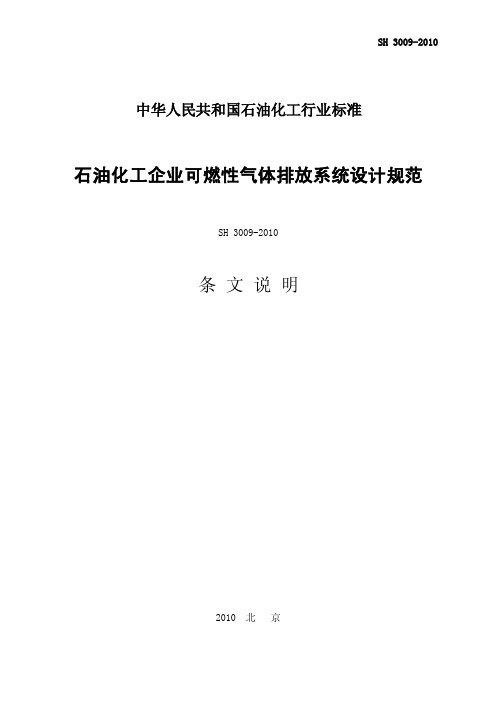
SH 3009-2010中华人民共和国石油化工行业标准石油化工企业可燃性气体排放系统设计规范SH 3009-2010条文说明2010 北京目次3一般规定 (3)4全厂可燃性气体排放系统的设置 (3)5设计排放条件的确定 (4)6全厂可燃性气体排放系统管网 (5)7分液及水封 (6)8高架火炬 (10)8.1允许热辐射强度 (10)9地面火炬 (14)9.1地面火炬的设计原则 (14)9.2封闭式地面火炬 (15)9.3开放式地面火炬 (15)10火炬气回收 (16)石油化工企业可燃性气体排放系统设计规范3 一般规定3.2 为避免全厂可燃性气体排放系统规模过大和工程投资过高,或在为满足环保要求的特定情况下,通常采用自动控制连锁减排系统以减少或消除工艺装置在紧急事故时可燃性气体的排放。
如:由停电引起空冷器风扇停止转动、冷却水中断、塔冷却回流中断等事故时,使用自动控制连锁系统切断热量的输入,可以大大减少或消除可燃性气体的排放。
但自动控制系统不可能百分之百无故障,在确定全厂可燃性气体排放系统时不能不考虑自动控制连锁减排系统发生故障的可能性。
另外,国外某些标准在这方面也有明确的规定。
3.5 理论上讲,高于常温并含有碳五以上烃类或水蒸气的可燃性气体,随着温度的下降会有一部分冷凝液析出。
但通过对放分液罐的使用情况调查发现,重组分装置附近的放空油气管道内存液很多,在装置运行期间,装置边界处分液罐内的凝结液经常处于满负荷。
很多炼厂反应放空油气刚出装置时带油多。
分析其原因,显然大部分的凝结液不是在离开装置这一段裸管因冷却而形成的,而是气流夹带出来的碳5以上的烃类物质。
因此,采用在装置内先进行分液罐分液然后送出装置。
这样做有以下优点: a装置操作人员可直接掌握放空油气夹带液滴的情况,有利于操作;b便于对分液罐的管理与操作;c便于分液罐内的轻质馏份回收处理;d有利于系统管网的安全运行。
3.7 大多数石油化工装置可燃性气体的安全泄放压力较低,而通常全厂可燃性气体排放系统管网复杂且管道的路线较长,装置内外统一进行水力计算可以科学优化放空气体管网的规模;统一进行管系的应力计算,有利于避免大直径管道配管的难度。
石油化工工厂基础工程设计内容规定附录A消防设计专篇

石油化工工厂基础工程设计内容规定附录A消防设计专篇附录A:消防设计专篇A.1消防设计专篇的内容消防设计专篇的内容应包括设计依据、概述、火灾危险因素分析、防火安全措施、消防给水及灭火设施设计、灭火救援设施、消防设施专项投资概算和相关附图。
A.2设计依据设计依据部分应列出下列文件的名称和编号:a) 建设项目可行性研究报告、总体设计及其批准文件;b) 设计合同;c) 国家、行业及地方的相关政策、法律和法规;d) 设计执行的相关技术标准、规范;e) 环境影响报告书(表)及其批准文件;f) 安全评价报告及其批准文件。
A.3概述概述部分应简要说明工厂区域位置,工厂组成/主项及设计分工,产品方案,生产规模,建设性质以及主要生产方法和简要工艺过程;工程周边敏感水体环境现状;工厂消防设施和管理机构以及区域联防情况;安全评价报告对策措施落实情况;存在的问题及建议。
对于改扩建项目还应重点描述工厂历年改造情况,消防设施依托情况,消防设施现状及存在的问题,消防安全评估的情况。
A.4火灾危险因素分析火灾危险因素分析应说明各生产装置、公用工程和辅助设施等生产过程中存在的主要火灾危险因素;危险物料应说明危险物料的名称、火灾危险性类别、数量、使用条件、特性和灭火要求(方法)。
A.5防火安全措施防火安全措施部分应包括下列内容:a) 工厂总平面布置、防火间距;b) 各装置和设施的泄压、防爆、防火等安全设施和检测、报警设施:1)正常工况下危险物料的安全控制;2)非正常工况下危险物料的控制(安全泄压、紧急切断、退料、联锁保护等);3)危险物料的泄漏检测和报警。
c) 各罐区储存物料的名称、火灾危险性分类、操作温度和压力以及储罐容积和储罐型式,罐体材质、防火堤和隔堤材质、高度及有效容积等;d) 爆炸危险区划分;e) 供电安全、防雷击、防静电积聚;f) 消防用电及电气防火:包括消防用电负荷等级、消防电源、备用消防电源、应急照明和疏散指示标志、消防配电及回路设计,配电设施及线路敷设、供电线路、用电设施、电气火灾监控;g) 安全疏散设施:包括构筑物安全疏散通道,及建筑物防火分区的安全出口数量、位置、宽度和疏散距离;h) 建、构筑物防火:1)建筑类别和耐火等级(包括建、构筑物面积及位置、防火间距);2)建筑防火构造;3)供暖、通风和空气调节系统防火;4)建筑防爆;5)建筑装修和保温防火;6)构筑物及钢结构的耐火保护。
石油化工安全系统仪表系统设计要求规范内容
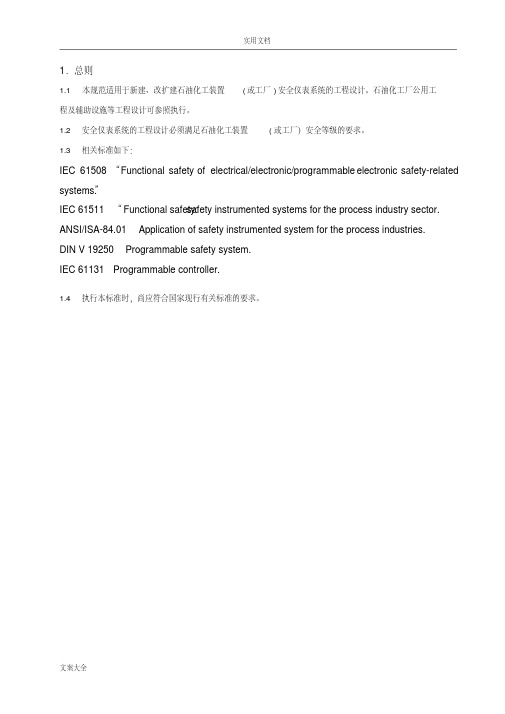
1.总则1.1 本规范适用于新建、改扩建石油化工装置(或工厂)安全仪表系统的工程设计。
石油化工厂公用工程及辅助设施等工程设计可参照执行。
1.2 安全仪表系统的工程设计必须满足石油化工装置(或工厂)安全等级的要求。
1.3 相关标准如下:IEC 61508 “Functional safety of electrical/electronic/programmable electronic safety-related systems.”safety instrumented systems for the process industry sector.IEC 61511 “Functional safety:ANSI/ISA-84.01 Application of safety instrumented system for the process industries.DIN V 19250 Programmable safety system.IEC 61131 Programmable controller.1.4 执行本标准时,尚应符合国家现行有关标准的要求。
2.名词术语下列术语适用于本规范:2.1 危险故障 Dangerous Failure指能够导致安全仪表系统处于危险或失去功能的故障。
2.2 安全仪表系统 Safety Instrumented System (SIS)指能实现一个或多个安全仪表功能的系统。
系统包括传感器,逻辑运算器和最终执行元件。
2.3 安全度等级 Safety Integrity Level(SIL)指用于描述安全仪表系统安全的等级,共4级, 4为最高级, 1为最低级。
2.4 最终执行元件 Final Element指安全仪表系统的一部分,执行必要的动作,使系统达到安全状态。
2.5 逻辑功能 Logic Function指将一个或多个输入信息转换为一个或多个输出信息的功能。
石油化工企业可燃气体和有毒气体检测报警设计规范(GB50493-2009)

石油化工企业可燃气体和有毒气体检测报警设计规范(GB50493-2009)1 总则1.0.1 为预防人身伤害以及火灾与爆炸事故的发生,保障石油化工企业的安全,特制定本规范。
1.0.2 本规范适用于石油化工企业新建、改建、扩建工程中可燃气体和有毒气体检测报警的设计。
1.0.3 石油化工可燃气体和有毒气体检测报警的设计,除执行本规范的规定外,尚应符合现行国家有关标准的规定。
2 术语2.0.1 可燃气体combustible gas指甲类气体或甲、乙A类可燃液体气化后形成的可燃气体。
2.0.2 有毒气体toxic gas指劳动者在职业活动过程中,通过肢体接触可引起急性或慢性健康的气体。
本规范中有毒气体的范围是《高毒物品目录》(卫法监发〔2003〕142号)中所列的有毒蒸汽或有毒气体。
常见的有:二氧化氮、硫化氢、苯、氰化氢、氨、氯气、一氧化碳、丙烯腈、氯乙烯、光气(碳酰氯)等。
2.0.3 释放源 source of release指可释放能形成爆炸性气体混合物或有毒气体的位置或地点。
2.0.4 检(探)测器 detector指由传感器和转换器组成,将可燃气体和有毒气体浓度转换为电信号的电子单元。
2.0.5指示报警设备 indication apparatus指接受检(探)测器的输出信号,发出指示、报警、控制信号的电子部件。
2.0.6 检测范围sensible range指检(探)测器在试验条件下能够检测出被测气体的浓度范围2.0.7报警设定值 alarm set point指报警器预先设定的报警浓度值。
2.0.8 响应时间 response time指在试验条件下,从检(探)测器接触被测气体达到稳定指示值的时间。
通常,达到稳定指示值90%的时间作为响应时间;恢复到稳定指示值10%的时间作为恢复时间。
2.0.9 安装高度vertical height指检(探)测器检测口到制定参照物的垂直距离。
2.0.10爆炸下限 lower explosion limit(LEL)指可燃气体爆炸下限浓度(V%)值。
石油化工企业燃料气系统
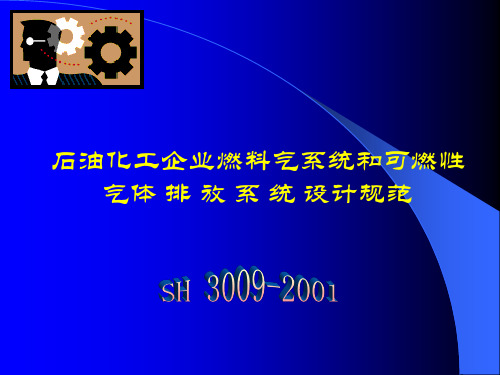
表4.0.22 点火点数
火炬头公称直径(mm) ≤500 500~1000 ≥1000
点火点数量(个) 2 3 4
4.0.23 火炬应有保持正压和防止回火的措施 。 4.0.24 水封罐的设计,应符合下列要求: 1 设 计 流量应按本规范第4.0.6条的要求确定; 2 应 能 分离出排放气体中直径在300um600um 的液滴,当分液罐距水封罐很近时, 液滴密度 可取水的密度; 3 设 计 压力不得小于1.0MPa( g); 4 结 构 尺寸应按附录C计算确定。
2.0.2 在对第2.0. 1条第3, 4款中排放工况数据 进行组合时,应遵循以下原则: A 在 工 艺 装 置 开、停工及发生某一种事故 时,与可燃气体排放管道相连的安全阀或泄 压阀,如 不 同 时 排 放 , 则 其泄放量不应简单叠加: B 应 考 虑 工 艺 自动控制系统中,自动联锁 对排放量的影响: C 不 考 虑 同 时 发生两种事故的工况.对不同 事故发生的排放条件不进行组合; D 不 考 虑 不 可 抗拒因素引起事故对排放系 统的影响。
4.0.21 进入排放系统的可燃性气体,应回收利 用。若采用气柜,宜设一个,其有效容积可按 具体情况确定,但不宜超过30000m3. 4.0.22 火炬应设有可靠的点火设施,确保在不 同气象条件下均能及时点燃火炬。火炬头点火 点的数量和布置应根据火炬头直径及所在地区 风向确定。火炬头点火点数量,宜按表4.0.22确 定:
4.0.6 排放系统的设计排放量,应按本规范第 2.0. 1条及第2.0.2条的规定,选取系统内最大 排放装置的一次最大排放量和同一事故中几 个装置同时泄放的排放量总和中的较大值。 4.0.7 排放系统中各分支段的设计流量,应为 各自通过的最大排放量。 4.0.8 排放系统管道的压力降,可按附录A计 算确定。
化工厂蒸汽系统设计规范

附录 B 典型蒸汽平衡图 ....................................................................................................................... 20 附录 C 热耗数据表及供热系统煤耗 ................................................................................................... 21 本规范用词说明............................................................................................................................... 22 引用标准名录………………………………………………………………………………………22 附:条文说明................................................................................................................................... 23
9 余热利用............................................................................................................................................... 13 10 系统优化........................................................................................................................................... 14 条件表 ..................................................................................................................................... 15 附录 A
蒸汽设备设计技术要求
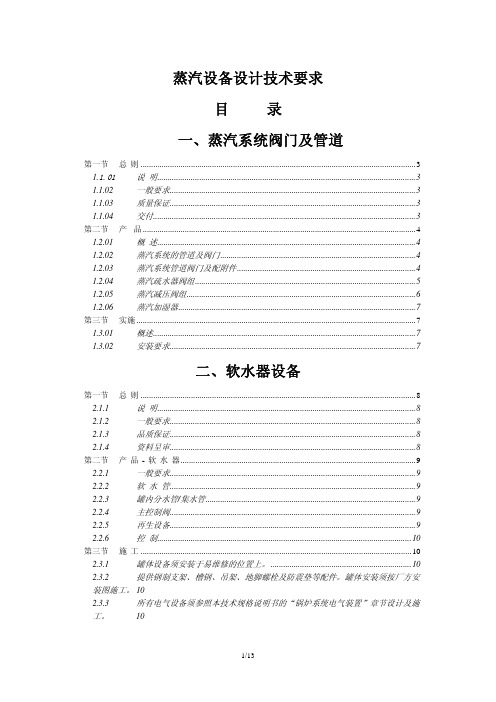
蒸汽设备设计技术要求目 录一、蒸汽系统阀门及管道第一节总则 (3)1.1.01说 明 (3)1.1.02 一般要求 (3)1.1.03 质量保证 (3)1.1.04 交付 (3)第二节产品 (4)1.2.01 概述 (4)1.2.02 蒸汽系统的管道及阀门 (4)1.2.03 蒸汽系统管道阀门及配附件 (4)1.2.04 蒸汽疏水器阀组 (5)1.2.05 蒸汽减压阀组 (6)1.2.06 蒸汽加湿器 (7)第三节实施 (7)1.3.01 概述 (7)1.3.02 安装要求 (7)二、软水器设备第一节总则 (8)2.1.1 说明 (8)2.1.2 一般要求 (8)2.1.3 品质保证 (8)2.1.4 资料呈审 (8)第二节产品-软水器 (9)2.2.1 一般要求 (9)2.2.2 软水管 (9)2.2.3 罐内分水管/集水管 (9)2.2.4 主控制阀 (9)2.2.5 再生设备 (9)2.2.6 控制 (10)第三节施工 (10)2.3.1 罐体设备须安装于易维修的位置上。
(10)2.3.2 提供钢制支架、槽钢、吊架、地脚螺栓及防震垫等配件。
罐体安装须按厂方安装图施工。
102.3.3 所有电气设备须参照本技术规格说明书的“锅炉系统电气装置”章节设计及施工。
10三、除 氧 器第一节总则 (11)3.1.1说明 (11)3.1.2一般要求 (11)3.1.3质量保证 (11)3.1.4资料呈审 (11)第二节产品 (12)3.2.1一般说明 (12)3.2.2产品构造 (12)3.2.3配附件 (12)3.2.4安装 (13)一、 蒸 汽 系 统 阀 门 及 管 道第一节 总则1.1.1.说 明本章说明有关阀门与管道配件的规格、安装及试验所需的各项技术要求。
1.1.2.一般要求A.所有送抵工地的阀门均应是全新制成品,并附有明显的标志以便辨别其等级。
B.在运送、储存及安装期间应采取正确的保护设施,以确保阀门及配件在任何情况下不受破损。
- 1、下载文档前请自行甄别文档内容的完整性,平台不提供额外的编辑、内容补充、找答案等附加服务。
- 2、"仅部分预览"的文档,不可在线预览部分如存在完整性等问题,可反馈申请退款(可完整预览的文档不适用该条件!)。
- 3、如文档侵犯您的权益,请联系客服反馈,我们会尽快为您处理(人工客服工作时间:9:00-18:30)。
设计标准SETM 0002-2002实施日期2002年4月11日中国石化工程建设公司石油化工厂蒸汽系统设计技术规定第 1 页共 9 页目次1 总则2 蒸汽系统的类型、组成和蒸汽负荷的统计3 蒸汽系统的拟定4 蒸汽系统的控制5 冷凝水的回收4 全厂蒸汽平衡图(或表)的绘制5 冷凝水的回收6 全厂蒸汽平衡图/表的绘制1 总则1.1 目的蒸汽系石油化工厂的重要二次能源,主要供工艺生产加热及动力用。
其系统是否合理、可靠,是直接影响生产的一个重要环节,因此合理地拟定全厂蒸汽及冷凝水回收系统,是热工专业设计的一项重要内容,也是编制本规定的目的。
1.2 范围适用于大、中型石油化工厂全厂蒸汽系统的设计,小型石化厂可参考执行。
1.3 相关文件、引用标准GB 12241 《安全阀一般要求》HG/T20521 《化工系统蒸汽设计规定》SHJ3 《石油化工厂合理利用能源设计导则》2 蒸汽系统的类型、组成和蒸汽负荷的统计2.1 蒸汽系统的类型蒸汽系统一般可分三种类型。
1)纯供热系统或称集中供热系统本系统的特点是各装置无副产蒸汽,也无其它汽源,均由工厂集中的锅炉房或热电站供汽,所供蒸汽主要供蒸汽加热用,或者只有少数蒸汽供驱动用。
2)热功(电)合产系统此时工厂中有一个主要装置生产过程中产生大量副产蒸汽,因此该装置采取热功合产方式,除供应本装置用汽外,同时可供周围装置或全厂生产用汽,如大、中型乙烯化工厂的蒸汽系统。
3)介于1)、2)两者之间的系统有全厂集中供热系统,又有热功合产系统(在装置内部)相结合的蒸汽系统。
2.2 由于石油化工厂的蒸汽系统已从纯供热系统发展到热功合产系统或联合系统。
因此全厂性蒸汽系统的拟定已不单单是一项装置外部系统的工作,而是一项装置内外相结合的工作,因此本规定同时阐述了装置内部和全厂两部分蒸汽系统的拟定原则。
2.3 蒸汽负荷按使用分类1)动力用户指驱动机、泵用的蒸汽负荷,由于选用的原动机类型不同,其乏汽可以再利用(如背压式汽轮机),或成为冷凝水回收(如凝汽式汽轮机)或无法利用而排空(如往复式汽泵及锻锤用汽)。
2)工艺加热用户指供工艺间接加热用的蒸汽,一般其蒸汽冷凝水均能回收。
3)工艺耗汽户指工艺使用后,冷凝水不能回收的用户,如化学反应过程用汽、直接加热用汽、蒸汽喷射器及物料雾化用汽等。
4)采暖通风及生活用汽户其中部分间接加热的用汽冷凝水可以回收,直接加热的则无法回收。
5)其它用汽户这些用汽户本身不用汽,仅仅改变蒸汽参数,供其它等级的蒸汽用户使用,如蒸汽蓄热器、蒸汽减温减压器等。
严格地说,背压机以及抽汽机的抽汽部分也属于此类,因其取自系统的蒸汽使用后仅改变了参数,仍能以较低参数的蒸汽形态返回系统。
2.4 全厂蒸汽负荷的统计和蒸汽平衡全厂蒸汽负荷的统计和蒸汽平衡应按不同参数列出,并按下列要求进行。
2.4.1 所有用户均应列入输入(即用汽量)、输出(即排汽量)和冷凝水回收量三栏数据,但前述2.3-2)~2.3-4)类负荷无输出,仅第2.3-1)、2.3-5)类负荷有部分或全部输出。
2.4.2 各级蒸汽负荷应达到输入和输出相平衡。
2.4.3 正常用汽量及最大用汽量的定义1)对装置而言,所谓正常用汽量为达到装置额定生产能力时的用汽。
对一个装置而言,所谓正常用汽量为达到装置额定生产能力时的用汽;所谓最大用汽量为该装置在某特定状态(例如,开车或部分开车、间断负荷同时使用)时的用汽量。
2)对于驱动用汽轮机,正常用汽量即为达到其被驱动设备额定出力时的用汽量,而最大用汽量为达到汽轮机额定出力(汽轮机功率一般比其驱动设备大10%)时的用汽量。
对于一般换热设备,所谓正常用汽量为该设备达到额定热负荷时稳定运行的用汽量,所谓最大用汽量为该设备起动时的用汽量(一般比正常大10~20%)。
3)对于全厂而言,正常用汽量为全厂各装置正常用汽量的总和,最大用汽量为各装置正常用汽量之和加上可能同时使用的各装置间断用汽量之和,此间断用汽量应通过分析确定。
2.4.4 对于装置副产蒸汽,也应掌握其正常、最大和最小产汽量。
2.4.5 正常情况的蒸汽平衡一般均应按各用户的正常用汽量和正常产汽量进行平衡。
对于开车或部分停产时需增加用汽的装置,应按正常情况和最不利情况(开车或部分停产时)分别做出蒸汽平衡。
2.4.6 在初步规划阶段未取得汽轮机厂的可靠汽耗资料时,可按常规理论计算方法确定其汽耗,此时应增加10~15%的安全系数以确定其汽耗。
2.4.7 全厂热负荷的统计应包括正常用汽量及最大用汽量两部分,全厂热负荷同时应按夏季、冬季进行统计,并结合主要热功合产系统开车等不同工况作出平衡。
3 蒸汽系统的拟定3.1 系统拟定的总原则3.1.1 拟定全厂蒸汽系统的基础是正确统计全厂蒸汽负荷并与各装置共同探讨和确定装置内部的蒸汽系统,使内外蒸汽系统达到协调统一的目的。
蒸汽系统的拟定由工艺系统专业与热工专业按公司分工规定协同完成。
3.1.2 系统中宜配置参数及容量相同的锅炉,余热锅炉参数应与系统相匹配。
3.1.3 对年运行时数在6000小时以上的连续生产的工艺装置供汽时,汽源不宜设置单台燃煤锅炉,可通过技术经济比较,设置两台较小锅炉,增设一台检修用炉或留有发展余地。
3.1.4 全厂的蒸汽冷凝水应充分回收。
对利用蒸汽间接加热的生产设备,冷凝水的回收率不应低于60%,对可能被污染的冷凝水,有回收价值的应设置水质监测及净化装置予以回收,确实不能回收的也应设法利用余热。
3.1.5 对定期检修的化工厂,燃用重油的锅炉及煤粉锅炉均应考虑停炉后继续起动的措施。
例如,设置点火用轻油罐或小型燃烧轻油的开工锅炉等。
3.1.6 拟定系统时应考虑充分利用工厂的中、低温位余热,例如用其加热进除氧器前的补给水等。
3.1.7 全厂蒸汽、给水及冷凝水系统一般均宜采用单母管系统。
对突然停汽会造成一定危害的生产装置,例如PTA及聚酯装置,可考虑双母管或其它保安措施。
3.1.8 系统蒸汽等级不宜过多,一般以二、三级为宜。
新蒸汽为超高压的系统,不宜超过四级。
3.1.9 对全年达5000小时以上的稳定低压用户,宜采用背压式汽轮机供汽。
对负荷有波动或要求稳定发电的,可选用抽汽凝汽式汽轮机供汽。
对较大型自备热电站,较理想的是两者的合理结合。
3.1.10 根据化工厂的蒸汽负荷发展特点,正常情况下汽源的锅炉负荷系数,一般不宜超过90~95%,煤粉锅炉的最低负荷系数不宜小于60~70%。
3.1.11 自备热电站及锅炉房的主机备用系数确定原则1)一般企业自备热电站的汽轮发电机组均不考虑备用,在汽轮机检修时,可通过外来电补充用电需要,锅炉主蒸汽经减温减压后满足各用户的蒸汽需要。
2)为确保工厂安全连续运行,宜设置备用锅炉。
当锅炉全部运行时,可满足最大用汽量的要求;正常时,留有一台作备用。
3.2 纯供热系统的拟定原则3.2.1 应根据全厂最高用汽参数确定最高一级的蒸汽参数,如由集中锅炉房供汽时,此参数也即锅炉的额定运行参数。
当最高用汽参数不高(例如£1.0MPaG)或此最高级用汽参数虽较高,但用汽量不大,而大量用汽参数均较低时,均可考虑建设自备热电站供汽。
此时应通过技术经济比较,论证建设热电站的合理性。
3.2.2 必须了解各装置开、停车过程及生产中对供热的特殊要求,对于间断生产的用户,必须研究其间断生产可能对全厂蒸汽系统的影响,对可能产生蒸汽压力波动的,应采取特殊措施解决,例如,在用户处设置蒸汽蓄热器、单独管道或单独锅炉供应等。
3.2.3 系统中设置的锅炉参数虽由最高一级用汽参数确定,但对其它较低参数用户如何合理供应,应在确定装置内部蒸汽系统时认真研究确定,可能提供的方案有:1)当锅炉房供应的为饱和蒸汽时,对一般低压用户可直接减压供应。
2)当热源供应的为过热蒸汽时,一般应经减温减压后供应;当用量较大且进出口参数差也较大时(例如超过2倍及以上时)可考虑设置小型背压汽轮发电机回收能量,也可通过蒸汽喷射泵回收乏汽以降低能耗如图1(a)、(b)所示。
3.3 热功(电)合产蒸汽系统的拟定3.3.1 热功合产蒸汽系统应根据装置内部及外部条件来确定。
所谓装置内部条件即是根据装置内部最高蒸汽参数来确定最高级的参数,再根据其它用汽户参数确定次级参数。
例如30万吨/年乙烯装置及30万吨/年合成氨装置均根据其废热锅炉所能达到的蒸汽参数确定其最高一级蒸汽参数,然后再根据工艺加热及动力用户要求,确定其它各级参数。
例如:燕山乙烯装置是根据其工艺加热用汽为1.57MPaG(16kgf/cm2G)和0.34MPaG(3.5kgf/cm2G),即做为其第二、三级的蒸汽参数,而功率较小的驱动用汽轮机也采用1.57MPaG一级,以减少蒸汽等级;而扬子、齐鲁乙烯装置则由于要考虑供芳烃抽提用汽,增加了4.17MPaG(42kgf/cm2G),390℃一级的高压(HP)蒸汽,此级同时做为主要传动用汽轮机的进汽参数。
其它等级则和燕山相仿;由于扬子、齐鲁乙烯设计中将小型汽轮机进汽均采用 1.57MPaG 的中压(MP)蒸汽,使排汽温度较低,一般均不必减温,即可排入0.34MPaG的低压(LP)系统。
由于热功合产蒸汽系统不但供应本身用汽,并需供应全厂其它装置用汽,因此对外部条件(即全厂用汽情况)必须完全掌握,才能制定出合理、协调的蒸汽系统。
图 3.3.1 回收低压用户能量的蒸汽系统3.3.2 在逐级利用的蒸汽系统中,特别要注意各级蒸汽参数要符合汽轮机实际膨胀规律,例如:1)抽汽式汽轮机一般经过第一级调节级后压降几达一半,故其最高抽汽压力一般为其进汽压力的0.5~0.6倍。
具有二级以上的抽汽式汽轮机,其上一级最低抽汽和下一级最高抽汽压力之差,一般不小于0.5MPa。
2)汽机的抽汽温度要符合其实际可能达到的温度,一般较大型的抽汽机或背压机其抽汽或排汽温度可定为内效率为70~75%时的汽温(最好应取得制造厂资料后确定),如定得过低则抽汽或排汽出口均需降温,但又不能定得过高,特别是用作化工加热用的蒸汽,一般希望过热度不超过40℃,否则由于传热系数降低而必须加大换热器的加热面积。
3)最低一级蒸汽参数一般可定为0.34~0.5MPaG,并需有10~15℃以上的过热度,此级蒸汽既可作工艺加热用汽,又可用于锅炉的除氧加热用。
一般给水温度低的燃油锅炉均采用0.25~0.5MPaG的中压除氧器,其出水水质完全可以满足高压锅炉的要求。
4)燃煤锅炉给水温度一般较高(国内锅炉一般为150~215℃),此时应与汽轮机厂共同拟定汽机回热级数及热力系统,并使其与全厂蒸汽系统取得协调。
3.3.3 装置蒸汽等级确定后,要据此拟定优化的蒸汽系统,做出蒸汽平衡。
在蒸汽系统优化过程中,主要的原则是:1)驱动用汽轮机尽量采用背压式汽轮机,对少数抽汽式汽轮机则尽量减少冷凝量,使冷凝量达到最少。