述机械加工中振动原因及控制措施
机械加工过程中机械振动的成因及解决措施

机械加工过程中机械振动的成因及解决措施摘要:在我国机械加工行业发展日益加快的背景下,机械管理工作迎来更高的挑战。
虽然在一定程度上提高了我国机械加工的效率和精确度,但由于在加工过程中,刀具和被加工机械做周期性往复运动,因此加工过程中产生机械振动是难以避免的。
而一旦发生机械振动不仅会影响到机械加工质量,甚至也会导致加工机械出现损坏。
因此,研究机械加工振动的解决措施,对于促进我国机械加工行业的发展具有重要的意义。
关键词:机械加工;机械振动;成因;解决措施引言在以往的机械加工过程中,经常会出现振动现象,使加工的精准度和精细度受到严重影响。
引起机械振动的原因是多样的,本文分析了机械加工过程中机械振动的不同成因,并针对成因提出了解决措施。
一、机械加工过程中机械振动形成的原因(一)强迫振动形成的原因在整个机械加工过程中,设备加工生产会受到各类外界因素的影响,强迫振动作为主要出现的振动类型,是受到外界因素影响最多的一种振动。
强迫振动就是指在周期性外力的影响之下形成的受破振动,他主要代表的是一种驱动力,由外力影响而诞生的一种额外的驱动性力量。
[1]关于强迫振动,有以下几个特征。
首先是强迫振动本身不会影响到干扰力,因此在加工生产的工程中,强迫振动的体现并不直接,在生产加工阶段我们无法对强迫振动进行额外的干扰,只有后续技术工艺阶段加入进来之后,强迫振动的现象才会停止。
其次是强迫振动受到的外部影响很深,因此其发生频率与外界干扰的周期频率是非常相似的,大部分的强迫振动频率都保持在干扰周期频率的整倍数上。
最后是强迫振动还具有一定的辐射性,它很可能会引起机械的共振现象,进一步的影响到机械设备的作业情况,影响设备生产的精度。
因此总的来看,在思考强迫振动形成原因的时候,更多的是需要关注外部影响和干扰因素对强迫振动的影响,外部的干扰因素越多那么强迫振动的振幅也就越高。
(二)自激振动形成的原因自激振动同其他振动之间有明显的区别,也就是说,在开展自激振动的过程中,外力的影响没有相对应的周期性。
机械加工过程中机械振动的原因及对策分析
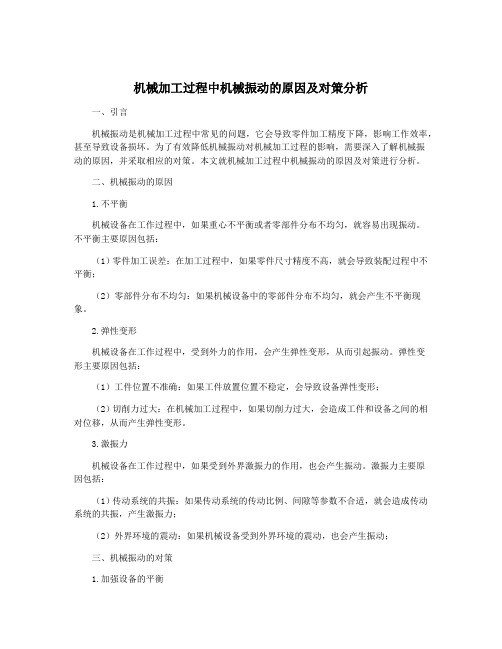
机械加工过程中机械振动的原因及对策分析一、引言机械振动是机械加工过程中常见的问题,它会导致零件加工精度下降,影响工作效率,甚至导致设备损坏。
为了有效降低机械振动对机械加工过程的影响,需要深入了解机械振动的原因,并采取相应的对策。
本文就机械加工过程中机械振动的原因及对策进行分析。
二、机械振动的原因1.不平衡机械设备在工作过程中,如果重心不平衡或者零部件分布不均匀,就容易出现振动。
不平衡主要原因包括:(1)零件加工误差:在加工过程中,如果零件尺寸精度不高,就会导致装配过程中不平衡;(2)零部件分布不均匀:如果机械设备中的零部件分布不均匀,就会产生不平衡现象。
2.弹性变形机械设备在工作过程中,受到外力的作用,会产生弹性变形,从而引起振动。
弹性变形主要原因包括:(1)工件位置不准确:如果工件放置位置不稳定,会导致设备弹性变形;(2)切削力过大:在机械加工过程中,如果切削力过大,会造成工件和设备之间的相对位移,从而产生弹性变形。
3.激振力机械设备在工作过程中,如果受到外界激振力的作用,也会产生振动。
激振力主要原因包括:(1)传动系统的共振:如果传动系统的传动比例、间隙等参数不合适,就会造成传动系统的共振,产生激振力;(2)外界环境的震动:如果机械设备受到外界环境的震动,也会产生振动;三、机械振动的对策1.加强设备的平衡对于不平衡造成的振动,可以采取以下对策:(1)提高零件加工精度:在零件加工过程中,应严格控制尺寸精度,避免误差导致的不平衡;(2)调整零部件分布:改变零部件的位置,使得机械设备的重心分布更加均匀。
2.增加刚度对于弹性变形引起的振动,可以采取以下对策:(1)稳定工件位置:通过改进夹具结构,提高工件的抓紧力,稳定工件的位置,减少弹性变形;(2)优化切削参数:通过调整切削速度、切削深度等参数,降低切削力,减少工件和设备之间的相对位移,减小弹性变形。
3.减少激振力对于激振力引起的振动,可以采取以下对策:(1)改善传动系统的设计:优化传动系统的传动比例、间隙等参数,避免传动系统的共振;(2)加强设备的隔振措施:通过在机械设备底部安装隔振装置,降低设备受外界环境震动的影响。
机械加工中振动的产生机理以及防治措施

机械加工中振动的产生机理以及防治措施一、机械加工过程中振动的危害振动会在工件加工表面出现振纹,降低了工件的加工精度和表面质量,低频振动时会产生波度;振动会引起刀具崩刃打刀现象并加速刀具或砂轮的磨损;振动使机床夹具连接部分松动,影响运动副的工作性能,并导致机床丧失精度;产生噪声污染,危害操作者健康;影响生产效率;二、机械加工过程中振动的类型机械加工过程中振动的类型:自由振动、强迫振动、自激振动。
1.自由振动工艺系统受到初始干扰力而破坏了其平衡状态后,系统仅靠弹性恢复力来维持的振动称为自由振动。
由于系统中存在阻尼,自由振动将逐渐衰弱,对加工影响不大。
2.强迫振动由稳定的外界周期性的干扰力(激振力)作用引起;除了力之外,凡是随时间变化的位移、速度和加速度,也可以激起系统的振动;强迫振动振源:机外+机内。
机外:其他机床、锻锤、火车、卡车等通过地基把振动传给机床机内:1)回转零部件质量的不平衡(旋转零件的质量偏心)2)机床传动件的制造误差和缺陷(如齿轮啮合时的冲击、皮带轮圆度误差及皮带厚度不均引起的张力变化,滚动轴承的套圈和滚子尺寸及形状误差)3)切削过程中的冲击(如往复部件的冲击;液压传动系统的压力脉动;断续切削时的冲击振动)强迫振动的特征:频率特征:与干扰力的频率相同,或是干扰力频率整倍数幅值特征:与干扰力幅值、工艺系统动态特性有关。
当干扰力频率接近或等于工艺系统某一固有频率时,产生共振相角特征:强迫振动位移的变化在相位上滞后干扰力一个φ角,其值与系统的动态特性及干扰力频率有关强迫振动的运动方程:图示:内圆磨削振动系统a) 模型示意图b)动力学模型c)受力图3.自激振动在没有周期性外力(相对于切削过程)作用下,由系统内部激发反馈产生的周期性振动;自激振动过程可用传递函数概念说明;切削过程本身能引起某种交变切削力,而振动系统能通过这种力的变化,从不具备交变特性的能源中周期性的获得补充能量,从而维持住这个振动。
机械加工中机械振动的原因解析与应对

机械加工中机械振动的原因解析与应对随着工业技术的不断发展,机械加工已成为现代生产中不可或缺的重要环节。
然而在机械加工过程中,经常会遇到机械振动的问题,这不仅会影响加工质量,还有可能引发安全事故。
了解机械振动的原因和有效应对是非常重要的。
一、机械振动的原因解析1.不稳定的加工条件在机械加工过程中,如果加工条件不稳定,比如切削速度、切削深度、进给速度等参数没有得到合理控制,就会引起机床工作状态的不稳定,从而产生振动。
2.机床结构设计不合理机床是机械加工的主要设备,如果机床的结构设计不合理,会导致刚性不足、固定件松动等问题,使得在加工过程中产生振动。
3.切削刀具磨损切削刀具是机械加工中常用的工具,如果刀具磨损严重或者安装不良,就会引起加工过程中的振动。
4.工件材料变形在加工过程中,由于工件材料自身性能的变化,也有可能引起机械振动。
5.进给系统问题进给系统的性能不稳定、传动链条出现松动等问题,会导致机床在工作时的振动。
刀具在加工时,间歇切削会引起刀具的振动,影响加工质量。
二、机械振动的应对措施1.合理选择切削工艺参数在机床的结构设计上,要注重刚性的设计和加强工装的固定,确保机床在加工过程中稳定性。
加强机床的维护保养工作,及时发现并解决机床结构问题。
3.切削刀具的选择和维护合理选择切削刀具,并确保刀具的安装正确、刃磨合适,定期进行刀具的维护和更换工作。
选择质量稳定的工件材料,对材料性能进行精密测试和处理,以减少因材料变形引起的机械振动。
对进给系统进行定期的检查和维护工作,确保传动链条、导轨等部件的稳定性和耐磨性。
6.刀具间歇切削的解决方法对于刀具间歇切削引起的问题,可以采用提高刀具速度、增加刀具的刚度等方法来减少刀具的振动。
三、结语在机械加工中,机械振动是一个常见问题,如果不能得到及时合理的处理,会对加工质量和安全性造成很大影响。
加强对机械振动原因的分析和应对措施的研究非常重要。
通过合理选择加工条件、加强机床结构设计和维护、切削刀具的选择和维护、工件材料处理、进给系统的维护以及解决刀具间歇切削等措施,可以有效减少机械振动的发生,提高机械加工的质量和效率。
机械加工中的振动问题分析及其控制措施探讨

制造 企业 在进行 零件的机械加 工中往往会遇到不 同程度 的振动 问题 , 振动 问题对机械加工的影响程度大小不一,但 是都会对加工生产的产品及 生产效率产生不 良影响,制造企业一般将机械 加工 定义为有害于加工质量 的现象 。 假 如机械加工 中出现了振动问题 , 加工工件与刀具都会发 生不 同程 度 的位移 , 位 移导致零件表 面的划 痕, 大大降低了产品 的生产质 量和性能; 机械加工 中出现的振动也会使 刀具受到振动带来的附加压力 ,导致刀具磨 损程度加深, 严重时则会 出现崩刃现象; 机械加 工中出现的振动也会使生产 加工 的夹具、 机床 等工具发生结构松动 , 增 加工具构件之 间的空隙, 一定程 度上减轻生产精度和刚度 , 减少工具的应用生命 , 严重情况下的振动 问题会 导致切削加工停止;机械加工 中出现的振动还会对技术人员造成不 同程度 的身体伤害 为了避免机械加工 中振动 问题的 出现, 制造企业很多情况下选 择减轻切削量, 延长 了加工生产的工期, 降低 了零件的生产效率。针对上述 问题 , 机械加 工中的振动 问题分析及其控 制措施探 讨显得十分必要。 机械 加工振动类型 常见的机械加工振动有三种, 即 自由振动、 受迫振动、 自激振动。 自由振 动 比较容易理解 , 一般是 由于外界干扰力发生的振动, 外界干扰力将 系统 的 平衡力破坏, 就会 出现不 同程度的弹性造 成的振动 。 制造企业 的机械加工系 统 自身具有一定阻尼 , 因此 , 自由振动会相对减弱 , 不会 对机械加工产 生过
2 . 2受 迫 振 动 的特 性
系学说 。 但 因为振动原理及振动缘 由说法不一, 自激振动产生的原 因至今为 止未能有一个统一说法 。 3 . 2自激振动的特性 首先 , 自激振动 不属于衰减类型的振动 , 这是 自激振动不 同于上述受迫 振动 的明显标志 , 当切削工作进行时 自激振动产生 , 切 削停 止, 自激振动也
机械加工振动产生的原因及消除方法

机械加工振动产生的原因及消除方法摘要:众所周知,在机械加工的过程中,存在着一个普遍的现象那就是机械振动,其实,机械振动是由多方面的因素造成的。
本文主要对机械加工过程中,机械振动的分类和特点进行了阐述,对机械振动的成因和影响展开了分析,同时对如何更好的解决机械振动产生的不利影响进行了深入的研究。
关键词:机械加工;振动产生;原因;消除方法引言机械加工是一项长期、循环往复的过程,由于长时间的运行,刀具和工件往往会受到很大的影响,因而不可避免的出现机械振动的情况。
在振动现象的影响下,加工部件的精度大大被降低,这对生产率的提高是非常不利的。
所以,应根据机械加工中出现的振动类型和产生的原因加以分析,采取有效的手段来降低或消除振动,从而提高机械生产的效率和质量。
1 机械加工振动类型在长时间的分析和实践中,按照机械振动产生的原因来分可以分为三类:自由振动、强迫振动和自激振动。
在机械运转时如果振动系统受到激振力的作用时会破坏机械的平衡状态,把能约束激振力的方式叫做自由振动,制造企业的机械加工系统自身具有一定阻尼,因此,自由振动会相对减弱,不会对机械加工产生过多的负面影响,属于机械加工振动中影响最小的一种振动。
而不同于自由振动,受迫振动和自激振动本身不能靠系统自身减弱振动,相反会对机械加工产生严重影响,本文接下来将对受迫振动及减振措施和自激振动及减振措施进行详细的分析和探讨。
2 振动产生的原因分析2.1自由振动产生的原因发生自动振动形式的主要原因是由于机械系统自身的弹力、重力作用下形成的,而没有任何外力参与。
因为组你和内耗都是振动系统中的一部分,比如简谐振动等,因此产生自由振动的原因是由于弹性元件或者惯性元件引发的。
2.2强迫振动产生的原因2.2.1高速回转出现不平衡状态,机械机床中高速回转的零件非常多,其中包括主轴、电机、皮带、磨床中的砂轮等等,就是由于出现不平衡状态导致出现离心惯性作用。
2.2.2机床传动零件缺陷所引起的周期性变化的传动力。
机械加工过程中振动产生的原因

机械加工过程中振动产生的原因2.1自然振动由于机械的构造非常复杂,在通电之后,机械会受到电力驱使进行运作。
由于机械内部的机械零部件非常多,在使用过程中机械零件急速运转,不同零件受空气阻力,进而产生振动。
可以说,自然振动是机械运转中不可避免的.振动问题,也是最常见、原理最为简单的振动类型。
同时,自然振动还包括外部因素影响,生产地不平、风力因素等影响。
通常情况下,机械各个运作零件都有一个磨合期,在刚刚接通电流时会产生明显振动,随着不同零件正常运转,起振动力机会逐渐削弱。
总之,自然振动是受技术、环境的影响,是不可避免的振动问题,对机械整体运作不会产生明显影响。
2.2自激振动有关调查研究显示,自然振动虽然是一种不可控问题,但如果不加以限制即会产生自激振动。
自激振动相比自然振动来说,就会对机械主体产生一定的伤害,轻则运作零部件松动、重则造成机械短路烧毁电线以及零件破损。
自激振动即是机械主体颤振,机械在正常加工中出现高频率振动,严重影响工业生产。
机械加工产生颤动的原因主要表现在以下几点:(1)机械在加工过程中,由于加工主体硬度突然变化,刀具运作频率突然改变,进而发生刀崩问题后,即会因为内部零件运作不协调而产生自激振动。
(2)机械中的各个零部件在生产中,由于刀具与零件之间契合度不足或生产规格不规范,而产生运作冲突,进而产生自激振动。
(3)机械刀具质量不过关,刚性较差,在生产过程中刀杆振动,进而带动机械整体振动。
(4)在机械生产过程中,由于生产刀具与产品生产规格相冲突,导致切削量无法满足标准,进而出现自激振动。
总体来说自激振动主要是由机械内部因素所引起的问题,主要是机械刀具或零部件之间的问题而产生的自激振动。
但是在自激振动中,振动周期会出现一定变化。
2.3强迫振动强迫振动与自激振动不同,强迫振动通常受外界因素与内部因素所产生的振动问题。
其内部因素主要是指:机械加工生产中,会由于机械各个部门零件所产生的离心振动,继而导致机械整体振动。
车床的震动及预防措施
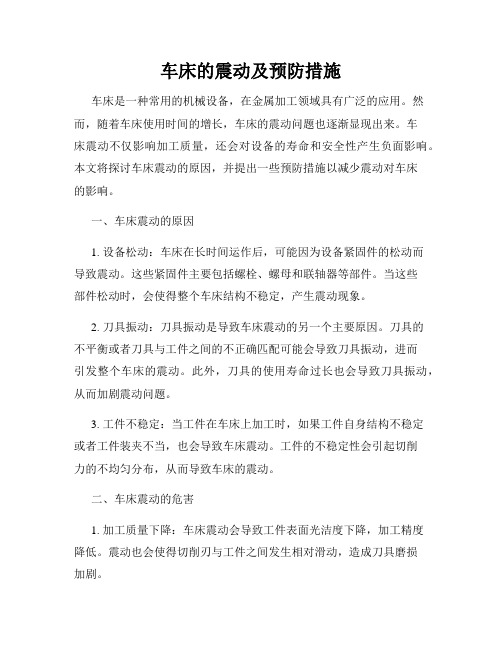
车床的震动及预防措施车床是一种常用的机械设备,在金属加工领域具有广泛的应用。
然而,随着车床使用时间的增长,车床的震动问题也逐渐显现出来。
车床震动不仅影响加工质量,还会对设备的寿命和安全性产生负面影响。
本文将探讨车床震动的原因,并提出一些预防措施以减少震动对车床的影响。
一、车床震动的原因1. 设备松动:车床在长时间运作后,可能因为设备紧固件的松动而导致震动。
这些紧固件主要包括螺栓、螺母和联轴器等部件。
当这些部件松动时,会使得整个车床结构不稳定,产生震动现象。
2. 刀具振动:刀具振动是导致车床震动的另一个主要原因。
刀具的不平衡或者刀具与工件之间的不正确匹配可能会导致刀具振动,进而引发整个车床的震动。
此外,刀具的使用寿命过长也会导致刀具振动,从而加剧震动问题。
3. 工件不稳定:当工件在车床上加工时,如果工件自身结构不稳定或者工件装夹不当,也会导致车床震动。
工件的不稳定性会引起切削力的不均匀分布,从而导致车床的震动。
二、车床震动的危害1. 加工质量下降:车床震动会导致工件表面光洁度下降,加工精度降低。
震动也会使得切削刃与工件之间发生相对滑动,造成刀具磨损加剧。
2. 设备寿命缩短:震动会给车床的零部件带来冲击载荷,加速设备的磨损和老化。
长期以来,震动还可能导致设备的损坏,影响车床的使用寿命。
3. 安全隐患:车床的震动可能造成设备的不稳定,使操作员在操作过程中发生意外。
同时,震动还可能导致部分设备脱落或者落下,对操作员造成伤害。
三、车床震动的预防措施1. 设备维护:定期检查和维护车床的紧固件,确保其处于良好的工作状态。
对于已松动的紧固件,应该及时加以修复或更换。
另外,车床的润滑系统也需要定期维护,以保证设备正常工作。
2. 刀具选择和装配:使用平衡性好的刀具,并且严格按照刀具制造商的要求进行装配。
切削刃的使用寿命达到上限后,应及时更换,以减少刀具引起的震动。
3. 工件装夹:工件装夹时,要选择稳定的夹具,并且按照正确的方式进行装夹。
机械装配中的振动特性分析与优化方法
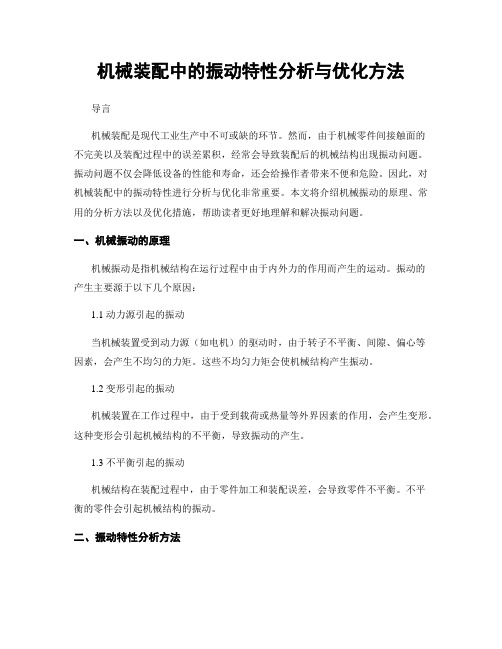
机械装配中的振动特性分析与优化方法导言机械装配是现代工业生产中不可或缺的环节。
然而,由于机械零件间接触面的不完美以及装配过程中的误差累积,经常会导致装配后的机械结构出现振动问题。
振动问题不仅会降低设备的性能和寿命,还会给操作者带来不便和危险。
因此,对机械装配中的振动特性进行分析与优化非常重要。
本文将介绍机械振动的原理、常用的分析方法以及优化措施,帮助读者更好地理解和解决振动问题。
一、机械振动的原理机械振动是指机械结构在运行过程中由于内外力的作用而产生的运动。
振动的产生主要源于以下几个原因:1.1 动力源引起的振动当机械装置受到动力源(如电机)的驱动时,由于转子不平衡、间隙、偏心等因素,会产生不均匀的力矩。
这些不均匀力矩会使机械结构产生振动。
1.2 变形引起的振动机械装置在工作过程中,由于受到载荷或热量等外界因素的作用,会产生变形。
这种变形会引起机械结构的不平衡,导致振动的产生。
1.3 不平衡引起的振动机械结构在装配过程中,由于零件加工和装配误差,会导致零件不平衡。
不平衡的零件会引起机械结构的振动。
二、振动特性分析方法为了更好地了解机械装配中的振动特性,需要进行振动测试和分析。
下面介绍几种常用的振动特性分析方法:2.1 频谱分析频谱分析是一种将时间域信号(振动信号)转换到频率域的方法。
通过频谱分析,可以得到机械结构在不同频率上的振动情况。
常用的频谱分析方法包括傅里叶变换和小波变换。
2.2 模态分析模态分析是一种通过测量机械结构在不同模态下的振动特性,来研究结构的振动行为的方法。
模态分析可以得到机械结构的固有频率、振型和振动模态等信息,有助于判断结构的强度和稳定性。
2.3 有限元分析有限元分析是一种通过将实际结构离散为有限数量的元素,将结构的振动行为转化为运动微分方程组求解的方法。
通过有限元分析,可以计算机械结构在不同工况下的振动响应和应力分布,从而指导结构的优化设计。
三、振动优化方法在进行振动优化时,可以采取以下几种方法:3.1 优化零件加工精度提高零件加工精度可以减小零件间的装配误差,从而减少振动的发生。
机械加工中振动的控制措施及方法
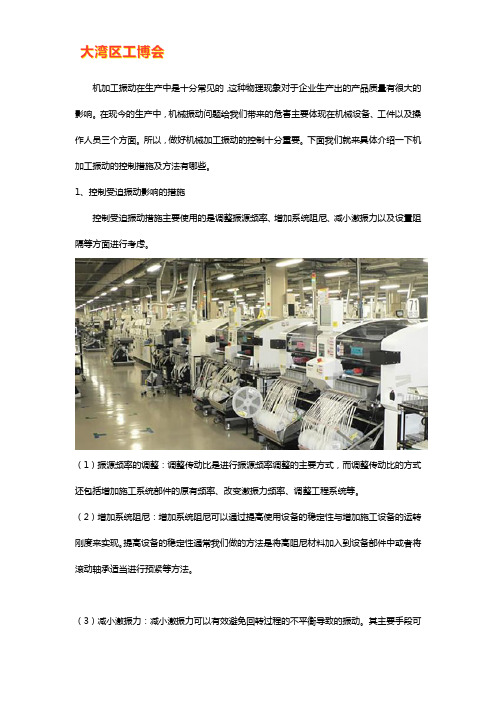
机加工振动在生产中是十分常见的,这种物理现象对于企业生产出的产品质量有很大的影响。
在现今的生产中,机械振动问题给我们带来的危害主要体现在机械设备、工件以及操作人员三个方面。
所以,做好机械加工振动的控制十分重要。
下面我们就来具体介绍一下机加工振动的控制措施及方法有哪些。
1、控制受迫振动影响的措施控制受迫振动措施主要使用的是调整振源频率、增加系统阻尼、减小激振力以及设置阻隔等方面进行考虑。
(1)振源频率的调整:调整传动比是进行振源频率调整的主要方式,而调整传动比的方式还包括增加施工系统部件的原有频率、改变激振力频率、调整工程系统等。
(2)增加系统阻尼:增加系统阻尼可以通过提高使用设备的稳定性与增加施工设备的运转刚度来实现。
提高设备的稳定性通常我们做的方法是将高阻尼材料加入到设备部件中或者将滚动轴承适当进行预紧等方法。
(3)减小激振力:减小激振力可以有效避免回转过程的不平衡导致的振动。
其主要手段可以降低高速运转设备中各元件所受到的离心力的影响,可以通过安装自动平衡装置的方式增加稳定性。
(4)设置阻隔:阻隔在生产中最长见得两种方法是安装吸振装置和安装隔振设备两种。
2、控制自激振动影响的措施与受迫振动相比,自激振动通常会具备更好的频率以及更强的振幅。
所以自激振动会比受迫振动更容易造成设备部件的损坏。
通常控制这种振动的措施主要有四种:改变刀具的几何参数、改变刀具及设备的位置、改变重叠参数以及改变切削用量。
(1)改变刀具的几何参数:对自激振动影响最大的是主偏角的几何参数,因此在施工中可以通过适当改变刀具主偏角来减少自激振幅。
(2)改变刀具及设备的位置:通过选择合理的位置角度以及刚度来提高施工系统的抗振能力。
(3)改变重叠参数:改变刀具的几何参数及改变切削用量是改变重叠参数的主要方式。
(4)改变切削用量:减小自激振动通常可通过减小切削深度以及增加进给量的方式。
机械加工过程中机械振动的原因及对策分析

机械加工过程中机械振动的原因及对策分析机械加工过程中出现机械振动的原因较多,主要包括以下几个方面:1.切削力的不平衡:机械加工过程中,切削力的大小和方向会不断变化,如果切削力不平衡,就会引发机械振动。
这主要是由于工件材料的异质性、表面瑕疵等原因导致的切削力不均匀分布。
2.进给速度过大:如果在机械加工过程中进给速度过大,刀具与工件之间会发生剧烈的冲击,从而产生振动。
进给速度过大还会引起切屑的断裂不良、刀具严重磨损等问题。
3.机床刚度不足:机床的刚度不足也是引起机械振动的重要原因。
刚度不足会导致机械系统的固有频率过低,与工件切削频率接近,从而引起共振现象。
4.切削液不当:切削液在机械加工过程中起到冷却润滑的作用,如果切削液的流量、温度、质量不合适,则会导致切削液无法有效冷却刀具和工件,增加切削力并引起振动。
针对上述问题,可以采取以下对策来降低机械振动:1.切削力平衡:选择合适的刀具和进给方式,确保切削力均匀分布。
在加工过程中可以采用动态平衡的方法动态调整刀具和工件的重心位置,提高切削力的平衡性。
2.控制进给速度:根据加工材料的性质和切削条件,合理控制进给速度,避免过大的进给速度引起振动。
如果需要加工高硬度材料,可以采用高速切削技术来提高加工效率,减少机械振动。
3.提高机床刚度:加强机床的刚度和稳定性可以有效抑制机械振动。
可以采用增加机床结构重量、增大导轨尺寸、优化机械系统刚度等措施来提高机床刚度。
4.优化切削液:选择合适的切削液,并设置合理的流量、温度和质量控制,确保切削液能够有效冷却刀具和工件,降低切削力。
还可以通过合理的刀具设计、提高工件材料的均匀性、改善切削过程中的冷却条件等方法来减少机械振动的发生,提高加工质量和效率。
对于特殊要求的加工任务,可以采用振动缓冲系统、动态平衡系统等技术手段来抑制机械振动,实现稳定加工。
机械加工过程中的振动和防止方法
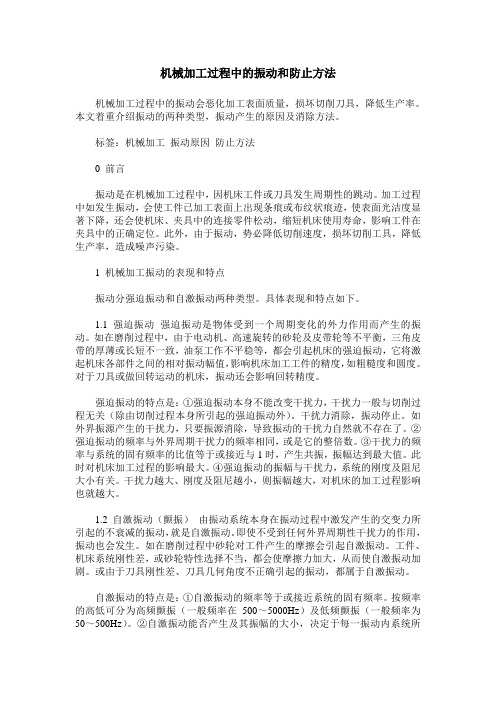
机械加工过程中的振动和防止方法机械加工过程中的振动会恶化加工表面质量,损坏切削刀具,降低生产率。
本文着重介绍振动的两种类型,振动产生的原因及消除方法。
标签:机械加工振动原因防止方法0 前言振动是在机械加工过程中,因机床工件或刀具发生周期性的跳动。
加工过程中如发生振动,会使工件已加工表面上出现条痕或布纹状痕迹,使表面光洁度显著下降,还会使机床、夹具中的连接零件松动,缩短机床使用寿命,影响工件在夹具中的正确定位。
此外,由于振动,势必降低切削速度,损坏切削工具,降低生产率,造成噪声污染。
1 机械加工振动的表现和特点振动分强迫振动和自激振动两种类型。
具体表现和特点如下。
1.1 强迫振动强迫振动是物体受到一个周期变化的外力作用而产生的振动。
如在磨削过程中,由于电动机、高速旋转的砂轮及皮带轮等不平衡,三角皮带的厚薄或长短不一致,油泵工作不平稳等,都会引起机床的强迫振动,它将激起机床各部件之间的相对振动幅值,影响机床加工工件的精度,如粗糙度和圆度。
对于刀具或做回转运动的机床,振动还会影响回转精度。
强迫振动的特点是:①强迫振动本身不能改变干扰力,干扰力一般与切削过程无关(除由切削过程本身所引起的强迫振动外)。
干扰力消除,振动停止。
如外界振源产生的干扰力,只要振源消除,导致振动的干扰力自然就不存在了。
②强迫振动的频率与外界周期干扰力的频率相同,或是它的整倍数。
③干扰力的频率与系统的固有频率的比值等于或接近与1时,产生共振,振幅达到最大值。
此时对机床加工过程的影响最大。
④强迫振动的振幅与干扰力,系统的刚度及阻尼大小有关。
干扰力越大、刚度及阻尼越小,则振幅越大,对机床的加工过程影响也就越大。
1.2 自激振动(颤振)由振动系统本身在振动过程中激发产生的交变力所引起的不衰减的振动,就是自激振动。
即使不受到任何外界周期性干扰力的作用,振动也会发生。
如在磨削过程中砂轮对工件产生的摩擦会引起自激振动。
工件、机床系统刚性差,或砂轮特性选择不当,都会使摩擦力加大,从而使自激振动加剧。
机械加工过程中机械振动的成因及解决措施

随着市场经济的发展,机械加工企业面临着激烈的市场竞争,随着国家产业格局的调整和优化,高科技电子产业快速发展,传统的机械加工行业面临着多方面的压力,市场发展逐渐呈现饱和,市场份额不断减少。在机械制造的过程中,机械加工作为其重要的环节,具有非常高的精度要求。机械加工的过程中机械振动的类型比较多,造成机械振动的原因比较复杂。通过对机械振动进行分析,寻找机械振动的源头,根据机械加工的实际情况,采取相应的改进措施,提高机械加工的效率和质量。
(2)自激振动的改进措施。自激振动的振源找是根据振动频率、范围以及性质等进行综合的判断,使用逐步排查的方式寻找振源。自激振动和系统工艺有着直接的关系,诊断的难度比较低。自激振动中振源在内部的情况下,通过单独驱动机床的各个部分开展相应的空转试验寻找振源。针对有可能发生振动的元器件或者运动部件进行评估,根据相应的参数计算、外力频率分析以及运转试验等进行分析,明确机械自激振动的振源。在改进自激振动中,可以采取下面方式:第一,刀具参数选择应当合理。刀具和工件之间的作用力是自激振动的重要源头,根据刀具参数的要求选择合适的刀具。机械加工的过程中,刀具主偏角和前角的参数是自激振动的主要影响因素,主偏角不断增加,前角就会越大,振幅就会减小。在实际的切削加工中,应当适当的扩大主偏角和前角,在满足条件的情况下,尽量减小后角,有效减小机械振动。第二,选择适当的切削量。切削用量主要有切削速度、进给量以及切削深度,任意一个参数的变化,都会对生产效率产生影响。在机械加工的过程中,根据加工的需求,需要对三个参数进行优化。加工的过程中,进给量选择相对较大的,切削深度应当较小,采用高速切削或者低俗切削的方式,实现减少自激振动的目的。第三,采取相应的减振措施。机械系统自身的抗振性能是自激振动的原因之一,应当注重机械系统刚性的提高,达到降低自激振动的目的。在实际的措施中,可以通过对接触面采取预处理的方式,调整轴承之间的间隙,增加滚动轴承的预紧力等。同时也可以采取相应的减振装置,消耗和吸收振动的能量。
机械振动的原因及其防止措施

机械振动的原因及其防止措施邓显欣 09机电二班【摘要】:机械在其加工产品过程中会产生振动,恶化加工表面质量,损坏切削刀具,降低生产率。
本文围绕振动的类型、产生的原因进行了详细地阐述,并提出了消减强迫振动和自激振动的措施,对于保证加工工件的质量要求,提高生产率,创造良好工作环境具有重要的现实意义。
振动是在机械加工过程中,因机床工件或刀具发生周期性的跳动。
它会使工件已加工表面上出现条痕或布纹状痕迹,使表面光洁度显著下降,还会使机床、夹具中的连接零件松动,缩短机床使用寿命,影响工件在夹具中的正确定位。
一、机械加工振动的特征振动分强迫振动和自激振动两种类型。
具体特征如下。
(一)强迫振动强迫振动是物体受到一个周期变化的外力作用而产生的振动。
如在磨削过程中,由于电动机、高速旋转的砂轮及皮带轮等不平衡,三角皮带的厚薄或长短不一致,油泵工作不平稳等,都会引起机床的强迫振动,它将激起机床各部件之间的相对振动幅值,影响机床加工工件的精度,如粗糙度和圆度。
对于刀具或做回转运动的机床,振动还会影响回转精度。
强迫振动的特点是:1.强迫振动本身不能改变干扰力,干扰力一般与切削过程无关(除由切削过程本身所引起的强迫振动外)。
干扰力消除,振动停止。
如外界振源产生的干扰力,只要振源消除,导致振动的干扰力自然就不存在了。
2.强迫振动的振幅与干扰力,系统的刚度及阻尼大小有关。
干扰力越大、刚度及阻尼越小,则振幅越大,对机床的加工过程影响也就越大。
(二)自激振动(颤振)由振动系统本身在振动过程中激发产生的交变力所引起的不衰减的振动,就是自激振动。
即使不受到任何外界周期性干扰力的作用,振动也会发生。
如在磨削过程中砂轮对工件产生的摩擦会引起自激振动。
工件、机床系统刚性差,或砂轮特性选择不当,都会使摩擦力加大,从而使自激振动加剧。
或由于刀具刚性差、刀具几何角度不正确引起的振动,都属于自激振动。
自激振动的特点是:1.自激振动的频率等于或接近系统的固有频率。
机械加工中振动的产生机理以及防治措施
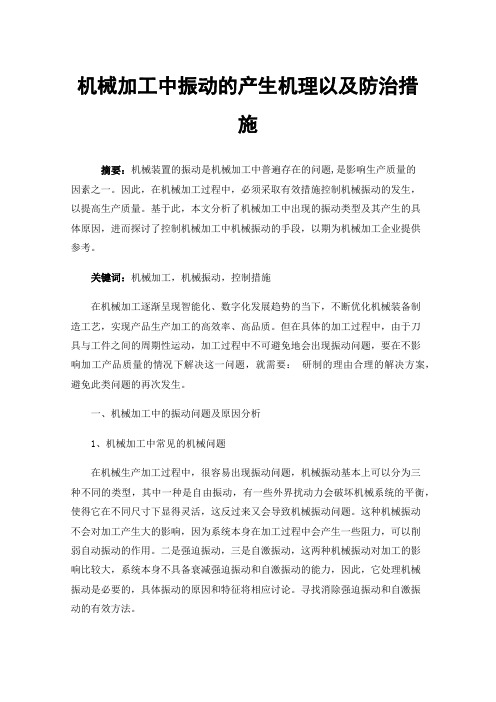
机械加工中振动的产生机理以及防治措施摘要:机械装置的振动是机械加工中普遍存在的问题,是影响生产质量的因素之一。
因此,在机械加工过程中,必须采取有效措施控制机械振动的发生,以提高生产质量。
基于此,本文分析了机械加工中出现的振动类型及其产生的具体原因,进而探讨了控制机械加工中机械振动的手段,以期为机械加工企业提供参考。
关键词:机械加工,机械振动,控制措施在机械加工逐渐呈现智能化、数字化发展趋势的当下,不断优化机械装备制造工艺,实现产品生产加工的高效率、高品质。
但在具体的加工过程中,由于刀具与工件之间的周期性运动,加工过程中不可避免地会出现振动问题,要在不影响加工产品质量的情况下解决这一问题,就需要:研制的理由合理的解决方案,避免此类问题的再次发生。
一、机械加工中的振动问题及原因分析1、机械加工中常见的机械问题在机械生产加工过程中,很容易出现振动问题,机械振动基本上可以分为三种不同的类型,其中一种是自由振动,有一些外界扰动力会破坏机械系统的平衡,使得它在不同尺寸下显得灵活,这反过来又会导致机械振动问题。
这种机械振动不会对加工产生大的影响,因为系统本身在加工过程中会产生一些阻力,可以削弱自动振动的作用。
二是强迫振动,三是自激振动,这两种机械振动对加工的影响比较大,系统本身不具备衰减强迫振动和自激振动的能力,因此,它处理机械振动是必要的,具体振动的原因和特征将相应讨论。
寻找消除强迫振动和自激振动的有效方法。
2、各种机械振动的产生原因(1)自由振动自动振动的原因是由于外界因素的干扰,加工过程中切削力发生变化,产生一定的冲击力,破坏加工系统的平衡。
这类振动的本质是消除限制机械系统振动而引起机械振动问题的力,它是所有机械加工振动中最容易预防和控制的机械振动,具有相对对系统影响不大。
小。
(2)受迫振动受迫振动是在加工系统内外因素的共同作用下发生的。
由于外界的不断干扰,加工系统会引起内部和外部的交替变化,影响加工产品和机械设备的正常运行。
机械加工中机械振动的原因解析与应对

机械加工中机械振动的原因解析与应对
机械加工中的机械振动是指在机械加工过程中产生的机械系统的非均匀运动现象。
机械振动的产生原因很多,主要包括以下几个方面:
1.切削力引起的振动:切削力在机床和工件之间传递,当切削力不平衡时,就会引起机床和工件的振动。
2.零件不平衡引起的振动:在机械加工过程中,如果工件本身不平衡,或者夹具装夹不平衡,都会导致机床的振动。
3.切削过程中的共振现象:机械系统有自然振动频率,当切削过程中的振动频率与机械系统的自然频率相近时,就会发生共振现象,从而引起振动。
4.机床刚度不足引起的振动:机床的刚度直接影响着机床的稳定性和阻尼效果,如果机床刚度不足,就会导致振动加剧。
为了应对机械振动,可以采取以下几种措施:
1.提高机械系统的刚度:通过加强机床的结构设计和制造工艺,增加机床的刚度,从而减少机械振动的发生。
2.使用平衡装置:对工件和夹具进行平衡处理,减小零件的不平衡量,从而减少振动。
3.优化切削参数:合理选择切削速度、进给速度和切削深度等切削参数,避免过大或过小的切削力。
4.选用合适的切削工具:选择合适的切削工具,如刀具的刚度、刀具的几何形状等,从而减小切削力和振动。
5.加强润滑和冷却:合理使用润滑剂和冷却剂,保持切削过程中工件和切削工具的表面温度,减少摩擦和热变形,从而减小振动。
机械振动在机械加工中是一个普遍存在的问题,但通过合理的措施可以减少和控制振动,提高机械加工的质量和效率。
机械加工过程中机械振动的成因分析

机械加工过程中机械振动的成因分析摘要:随着科学技术的飞速发展,机械加工水平也不断提高。
在加工过程中经常出现机械振动就会对机械加工造成不利的影响,因此有必要对机械加工过程中机械振动的成因进行深入研究,以便更好的保证工件的表面质量,并结合具体原因制定解决方案,减少振动的发生,提高加工质量。
关键词:机械加工;机械振动;成因分析1 机械加工中机械振动的分类1.1 强迫振动强迫振动是机械加工过程中较为常见的振动类型之一,产生这一振动的主要原因是由于在机械加工过程中受到外界周期性干扰的影响,进而导致设备系统出现强迫振动现象。
同时由于外界力量所产生的干扰具有周期性的特点,因此可以提供持续的动力机械振动。
也就是说,只要有外力干扰,振动将不会停止。
其中强迫振动的特点主要有:一是干扰力不会受到强迫振动的影响而改变;二是强迫振动的频率与外界周期干扰力的频率具有一定关系,频率相同或者存在整倍数关系;三是当外界干扰力的频率与系统固有频率的比值等于或接近时,机械系统则会产生共振,并且在这种情况下,所产生的振幅将达到最大值。
1.2 自激振动自激振动是在机械加工过程中所出现的交替周期振动,是在一定相互作用下产生的。
其中自激振动表现的特点主要有:一是自激振动的频率与系统固有频率具有一定关第,通常会表现为处于等于或接近的状态;二是自激振动的产生及其振幅受到多种因素影响,通常会取决于系统所获得的能量与阻尼消耗能量的对比情况;三是因为持续自激振动的干扰力是由振动过程本身激发的,所以当外界振动中止,其干扰力及能量补充过程也就会立即消失。
2 产生机械加工振动的原因分析2.1 产生强迫振动的原因在加工过程中容易出现的强迫振动,产生强迫振动有内部因素和外部因素,但主要受到内部因素的影响,主要表现在以下几个方面:一是机床上回转件不平衡影响了机械整体离心力发生周期性变化。
这一状况通常会由电机或卡盘、皮带轮回转不平衡引起。
二是因为机床传动零件的缺陷情况导致周传动力的期性变化。
- 1、下载文档前请自行甄别文档内容的完整性,平台不提供额外的编辑、内容补充、找答案等附加服务。
- 2、"仅部分预览"的文档,不可在线预览部分如存在完整性等问题,可反馈申请退款(可完整预览的文档不适用该条件!)。
- 3、如文档侵犯您的权益,请联系客服反馈,我们会尽快为您处理(人工客服工作时间:9:00-18:30)。
论述机械加工中振动原因及控制措施
摘要:随着我国经济的飞速发展,机械化加工技术在我国得到了前所未有的发展,机械加工中的振动是一种十分有害的物理现象。
通过分析机械加工中各种振动产生的原因和特性,提出了相应的减振措施。
在实际生产中,合理采用这些措施对保证零件表面品质、提高生产率有着积极的意义。
关键词:机械加工;振动;控制措施
中图分类号:th161 文献标识码:a 文章编号:
1、引言
随着机械加工技术的不断广泛的应用,显现的问题也越来越突出,机械加工中的振动对加工表面质量和生产率有很大的影响,是一种十分有害的物理现象。
若加工中产生了振动,刀具与工件间将产生相对位移,会使加工表面产生振痕,严重影响零件的表面质量和性能;振动使刀具受到附加动载荷,加速刀具磨损,有时甚至崩刃;同时振动使机床、夹具等的连接部分松动,从而增大间隙,降低刚度和精度,缩短使用寿命,严重时甚至使切削加工无法继续进行,振动中产生的噪声还将危害操作者的身体健康。
为减小振动,有时不得不降低切削用量,使机床加工的生产效率降低。
因此,研究分析机械加工中的振动原因和特性,寻求控制振动的有效途径是很有必要的。
机械振动的类型分为自由振动、受迫振动和自激振动三类。
自由振动是在初始干扰力的作用下破坏了系统的平衡,仅靠弹性恢复力来维持的振动。
由于系统中总存在阻尼,自由振动会迅
速衰减,所以对机械加工的影响不大。
受迫振动和自激振动都属于不衰减的振动,对机械加工的影响不容忽视。
下面主要分析这两种振动。
2、振动的类型及特征
机械加工中产生的振动主要有受迫振动和自激振动(颤振)两种类型。
2.1受迫振动
由外界周期性干扰力(工艺系统内部或外部振源)所激发的振动。
其主要特征是:
(1)除由切削过程本身不均匀性所引起的受迫振动外,干扰力一般同切削过程无关。
干扰力消除,受迫振动停止。
(2)受迫振动的频率与外界周期性干扰力的频率相同或是它的整数倍。
(3)受迫振动的振幅与干扰力的振幅、工艺系统的刚度及阻尼大小有关。
在干扰力频率不变时,干扰力幅值越大,工艺系统的刚度及阻尼越小,则受迫振动幅越大。
(4)干扰力的频率与工艺系统某一固有频率的比值等于或接近于1时,系统将产生共振,振幅达到最大值。
减小受迫振动的措施:受迫振动是由于外界周期性干扰力引起的,因此为了消除受迫振动,应首先找出振源,然后采取相应的措施加
以控制。
(1)减小激振力:对于机床上转速在600r/min以上的零件,如砂
轮、卡盘、电动机转子及刀盘等,必须进行平衡以减小和消除激振力;提高带传动、链传动、齿轮传动及其他传动装置的稳定性,如采用完善的带接头或无接头的胶合平皮带,以斜齿轮或人字齿轮代替直齿轮,采用缓冲装置、降低换向速度等,使动力源与机床本体放在两个分离的基础上。
(2)调整振源频率:在选择转速时,尽可能使引起受迫振动的振源(电机转速)频率远离系统固有频率,避免共振。
(3)提高工艺系统的刚度和阻尼:提高刚度、增大阻尼是增强系统抗振能力的基本措施。
如提高联结部件的接触刚度,预加载荷减小滚动轴承的间隙,采用内阻尼较大的材料制造某些零件能收到较好的效果。
(4)采用隔振措施:隔振就是用弹性隔振装置将需防振的机床或部件与振源之间分开,使大部分振动被吸收,从而达到减小振源危害的目的。
如用橡胶垫将电机与机床隔开,机床下装隔振器,机床四周挖隔振沟,沟内充满锯木屑、纤维、软木、碳渣等。
对于某些动力源,如电机、液压站等,最好与机床分离。
(5)采用减振装置:当采用上述各种措施仍无法控制振动时,可考虑使用消振减振装置。
减振装置通常都是附加在工艺系统中,通过吸收或消耗振动能量,达到减振的目的。
它对抑制自激振动有同样的效果,是提高工艺系统抗振性的一个重要途径。
2.2自激振动(颤振)
机械加工过程中,在没有周期性外力(相对于切削过程而言)作
用下,由系统内部激发反馈产生的周期性振动。
其主要特征如下:(1)由于维持自激振动的干扰力是由振动(切削)过程本身激发的,故振动(切削)一旦中止,干扰力及能量补充过程立即消失。
(2)自激振动能否产生及其振幅的大小,决定于每一振动周期内系统所获得的能量与系统阻尼消耗能量的对比情况。
(3)自激振动的频率等于或接近于系统的固有频率。
目前,国内外对加工过程中振动纹理的控制技术进行了较深入的研究。
提出:利用变速切削加工方法抑制切削颤动;利用非线性颤振理论研究切削振动,并指出切削振动不仅取决于切削力的动态特性,而且也取决于机床机构的动态特性;利用实验方法研究动态切削噪音的“动态切削条件”,提出振动频率主要由机床切削系统的模态固有频率所决定。
控制自激振动的措施:
图1车削时切削速度与振幅的关系曲线图2 前角的影响
(1)合理选择切削用量:图1是车削时切削速度与振幅的关系曲线。
可以看出,在v=20~60m/min时容易产生自振,高于或低于此范围则振动减弱。
若同时考虑提高生产率,则采用高速切削有利。
(2)合理选择刀具几何参数:主要影响参数为主偏角u和前角γ。
当u=90°时振幅最小,此时切削力在y方向上最小、x方向上最大。
由于一般工艺系统的刚度在x方向比y方向上好得多,因此不易起振。
由图2可见,在相同切削速度v时,随前角γ的增大,切削力减小,振幅也减小。
因此通常采用双前角消振刀以减小切削力,可取得
很好的减振效果。
减小后角有利于减振。
一般后角取2°~3°为宜,必要时在后刀面上磨出带负后角的消振棱,形成倒棱减振车刀。
其特点是刀尖不易切入金属,且后角小,有减振作用,切削时稳定性好。
(3)提高工艺系统的抗振性:工艺系统本身的抗振性能是影响颤振的主要因素之一。
首先应设法提高工艺系统的接触刚度,如对接触面进行刮研,减小主轴系统的轴承间隙,对滚动轴承施加一定的预紧力,提高顶尖孔的研磨品质等。
3、实例分析
以某公司一台德国liebherr数控滚齿机lc3000为原型,对加工中出现的振动(蹦刀)问题进行振源诊断:该设备在安装调试完毕后,进行内齿切削时产生严重的振动、蹦刀且噪音大,加工出的齿轮工件齿面有振纹,零件达不到产品的质量要求。
为解决此问题:第一步,降低了切削速度和切削进给量,多次试验后无变化;第二步,对夹具进行了改进,改为由原来的8个m24的螺栓,增加到12个m24的螺栓,同时在工件上端加一个圆环形的压板以提高夹具的稳定性,防止在盘铣刀进给时引起工件振动。
从装夹改进后的实验结果看,只是振动幅度稍有减小,振动还依然存在,没有真正找到振源。
第三步,现场拾振,进行频谱分析。
在现场加工条件下,沿加工部位附近的振动敏感方向,用传感器(加速度计和力传感器等)拾取过程中的振动信号,做频谱分析,画频谱图。
频谱图上较为明显
的峰值点有多少个,机械加工系统中的振动频率成分就有多少个。
从频谱结果分析看,加工工件时的振动频率与机床的固有频率近似相等,使其发生了共振。
解决方案:采用变频方式,修改840d机床参数,在lh90软件系统里添加支程序,让主轴在2rpm速度范围内进行变速切削,解决了振动问题。
结语
通过对切削加工过程中产生振动的原因和特性的分析,采取相应的减振措施,可使切削加工中的振动现象明显减小,大大提高工件表面品质及生产率。
但完全消除振动现象,尚待进一步深入研究振动机理、寻找产生原因及消除措施。
另一方面,近几十年来,通过研究发现,如果科学合理地利用振动,反而可以更好地进行切削,如振动切削和磨削,都是利用振动来提高表面品质和生产率的先进加工技术。
参考文献:
[1]周昌治,等.机械制造工艺学[m].重庆:重庆大学出版
社,2006.
[2]郑修本.机械制造工艺学[m].北京:机械工业出版社,2004.
[3]闻邦椿,等.振动利用工程[m].北京:科学出版社,2005.。