生产线布局培训课件
生产线布局培训共108页
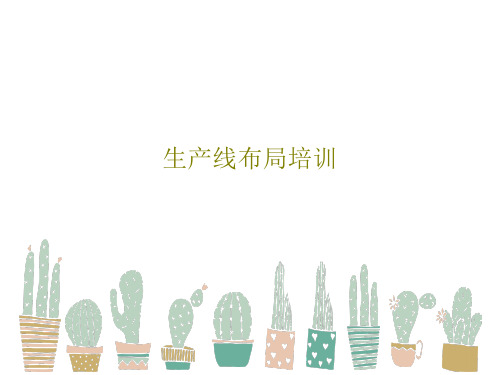
43、重复别人所说的话,只需要教育; 而要挑战别人所说的话,则需要头脑。—— 玛丽·佩蒂博恩·普尔
44、卓越的人一大优点是:在不利与艰 难的遭遇里百折不饶。——贝多芬
45、自己的饭量自己知道。——苏联
Hale Waihona Puke 生产线布局培训46、法律有权打破平静。——马·格林 47、在一千磅法律里,没有一盎司仁 爱。— —英国
48、法律一多,公正就少。——托·富 勒 49、犯罪总是以惩罚相补偿;只有处 罚才能 使犯罪 得到偿 还。— —达雷 尔
50、弱者比强者更能得到法律的保护 。—— 威·厄尔
41、学问是异常珍贵的东西,从任何源泉吸 收都不可耻。——阿卜·日·法拉兹
生产线规划课件

生产顺 序表
间口8奥行4*6 间口8奥行4*7 间口8奥行4*7
1.01日 1.38日 1.48日
顺序货 店高 3*4排
顺序货 店高 3*3排
间口8奥行4*6
间口8奥行4*7 间口8奥行4*7
—— —— ——
—— —— ——
0.25日 0.34日 1.48日
顺序货 店高 3*3排
当的。
▪ 1.公司展望及工厂建设 ▪ 2.丰田生产方式的思考 ▪ 3.生产线布置
工厂布置规划的目标
▪ 有效编排设备与工作区域的整合,使制程是直线流动, 生产一贯化。
▪ 使物料运搬的距离最短,避免有交叉重复现象发生。 ▪ 维持生产作业与制程编排的弹性化,以利必要性之改
善调整。 ▪ 使原物料在制程中能快速流动,避免堆积存放,造成
•加工工时之浪费及需配置人员 •刀具等消耗品(副资材)之浪费 •电气、水、压气等之浪费 •在库空间的浪费(增设仓库) •保管期间品质劣化(例:生锈) •取出工时之增加浪费
•努力之浪费 •作业工时增加之浪费 •加工时间,修整时间之浪费 •材料的浪费 •副资材、电力、水、压气等的浪费
2.丰田生产方式的思考
资金积压。 ▪ 以合理有效的制程规划,减少对设备投资之重复。 ▪ 建筑空间的有效利用规划。 ▪ 人、设备、物流、放置方式考虑原则,并充分提升人
力绩效。
设施布置的方向与目的
布置原则
▪ 设施布置需要作长期规划。 ▪ 设施布置对产品生产成本有重大的影响、要
周详规划。 ▪ 设施布置需要由日常生产活动中不断的改善,
2 等待的浪费 3 运搬的浪费
4 加工的浪费
5 库存的浪费
6 动作的浪费
7
不良品、修 整的浪费
生产线及其平衡培训教材(PPT 116页).ppt

12
流水生产线
分类:
皮带输送机
第4讲
矿用型带式输送机
13
悬挂输送机
流水生产线 第4讲
分类:• 按工作方式(对于传送带)
• 分配式传送带:各工作地排列在流水线体的一 边或两边,流水线体传送制品经过工作地时, 工人从传送带取下制品在工作地加工;加工完 毕再送回流水线体;
移动流水线 多品种流水线
混合流水线 间断流水线 自由节拍流水线
机械化程度
自动线
机械化流水线
手工流水线
运 输 设 备 无专用设备 无动力专用设备 机械化运输设备
工作方式 分配式
工作式
16
流水生产线—— 相关技术术语 第4讲
作业站:指在一个工作位置上给定的生产作业,又称为作业 工序或工位; 总作业量:一个制品的全部加工或装配作业量,即总作业量;
ProductionandOperati onsManagement
第四讲 生产线及其平衡 第4讲 • 流水生产线 • 生产线平衡 • 单件生产与成批生产规划
2
企业经营战略
生
生产运作战略
时间、质量、成本 、服务、柔性
产
与
生产运作系统设计
运
作
产品与服务的选择
生产系统运行与控制
年度计划与主生产计划
需求管理与预测
18
流水生产线—— 组织条件 第4讲
• 产品的结构和工艺应相对稳定 良好工艺性和互换性,工艺规程稳定,以保证加工时间的 稳定和产品质量;
• 制品产量足够大 以保证流水生产线各工作地有充分的负荷;
生产线布局(超详细)【精品课件】.ppt
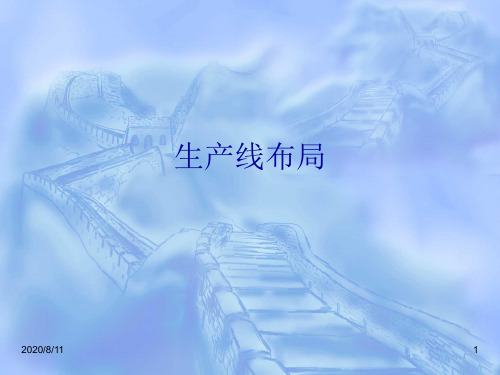
2020/8/11
12
鉴别七大浪费
六、来自工序不当的浪费
工作本身产生的浪费,当机器不正常运作而使操作人员 需要花额外时间,或当操作人员出于习惯或花了过多的 时间使清洁工作超过了规格的要求。
多余的检查也是过程浪费的另一个表现形式。
2020/8/11
13
鉴别七大浪费
七、不需要的动作的浪费
人们在工作设置中经常将工作中的动作搞混乱,实际做的动 作和工作要求的动作往往是不同的。
生产线布局
2020/8/11
1
精益生产五项基本原则
• 价值 (VALUE) : 决定于客户是否愿意为了它而付钱。
• 价值流 (VALUE STREAM) : 从产品设计到客户服务的所有
活动的描述和鉴别,都需要消除非增值活动。
• 流畅 (FLOW) : 消除所有工序的阻滞使价值流“流畅”而没有
中断。
作为一个确定的目的,工作是要作为一组精确的动作来考虑 的,哪些是增值的,那些是不增值的。
一个人在每天的恒定的工作中(例如一个很忙的人)可能实 际上只是很少一部分是增值工作。
工作中的不需要的动作被认为是浪费的,不增值的。
2020/8/11
14
生产布局前的准备工作
▪ 产能评估 ▪ 生产线顺流 ▪ 库存周转评估
1. 采用了看板管理,拉动生产方式 2. 车间布局U型布局; 3. 不同类型的机器摆放在一块; 4. 实现了单件流的生产; 5. 机器小型化 ; 6. 工序中间很少甚至没有库存; 7. 实现了作业标准化; 8. 对工人实行了多技能培训; 9. 具有完善的作业改善活动制度
2020/8/11
3
看谁摘的果子最多!
6
产生更严重的成本连锁反应……
精益生产之LAYOUT--ppt课件
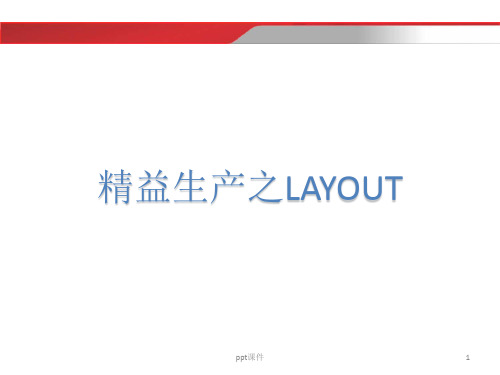
A.Leadtime的定义 从客户下订单到工厂交货,这个过程所花费的时间就是 leadtime,即完成某项目标所花费的流程时间
B.科特尔法则 Leadtime=存货数量X生产节拍或存货数量X生产能力
C.生产节拍 生产节拍是指每生产一个产品所需的间隔时间
例如:一台设备的生产能力是每小时生产120个产品,也就是说这台设
多人分割式U型生产线
ppt课件
25
c.诼兔式
诼兔式式U型生产线
ppt课件
26
B.I字型布局
ppt课件
27
B.Y字型布局
ppt课件
28
3.Cell布局五步法
1).通过产品分类确定生产类型
在进行产品分类时,可以通过P-Q分析法, P-Q分析法是指对企业目前的所有产品按 按加工工艺分类,同时对各类产品的生 产量进行统计分析的一种方法
流程分析的定义
掌握全部生产过程包括工艺加工过程、检查过程、 搬运过程、停滞等的实际状态,发现并消除其过程 中的浪费与不合理
ppt课件
3
1.准确把握工艺流程的整体状态
明确工艺流程的先后顺序 明确工艺工序的整体关系 确定各工序之间的作业时间 发现工艺流程中不合理,不平衡的状态
2.寻找发现工序的问题点
1.检查方法 2.不良率
等待原因
等待地点
等待时间
ppt课件
9
1.流程分析的图示符号
A.产品工艺流程分析符号
工序种类 符号
说明
加工 搬运 检查 停止储存
材料,零部件或新产品在加工过程中发生了外形规格性质 等的变化或为下一工序进行准备的状态
材料,零部件或产品在一定状态下不变,同时转移位置状 态
01第一章-U型生产线布局
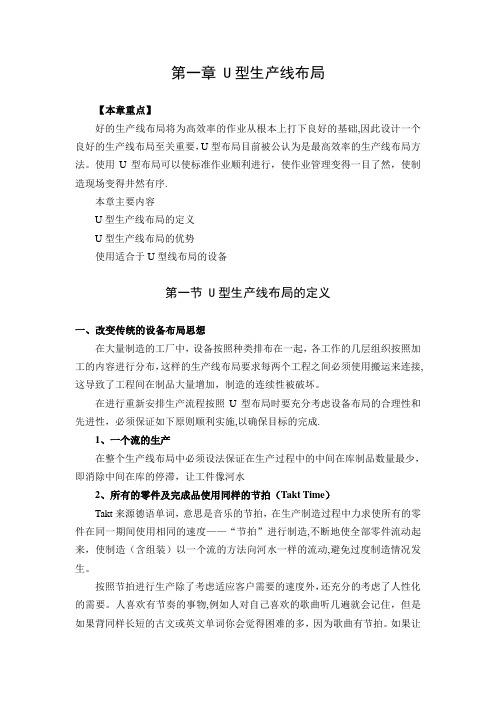
第一章 U型生产线布局【本章重点】好的生产线布局将为高效率的作业从根本上打下良好的基础,因此设计一个良好的生产线布局至关重要,U型布局目前被公认为是最高效率的生产线布局方法。
使用U型布局可以使标准作业顺利进行,使作业管理变得一目了然,使制造现场变得井然有序.本章主要内容U型生产线布局的定义U型生产线布局的优势使用适合于U型线布局的设备第一节U型生产线布局的定义一、改变传统的设备布局思想在大量制造的工厂中,设备按照种类排布在一起,各工作的几层组织按照加工的内容进行分布,这样的生产线布局要求每两个工程之间必须使用搬运来连接,这导致了工程间在制品大量增加,制造的连续性被破坏。
在进行重新安排生产流程按照U型布局时要充分考虑设备布局的合理性和先进性,必须保证如下原则顺利实施,以确保目标的完成.1、一个流的生产在整个生产线布局中必须设法保证在生产过程中的中间在库制品数量最少,即消除中间在库的停滞,让工件像河水2、所有的零件及完成品使用同样的节拍(Takt Time)Takt来源德语单词,意思是音乐的节拍,在生产制造过程中力求使所有的零件在同一期间使用相同的速度——“节拍”进行制造,不断地使全部零件流动起来,使制造(含组装)以一个流的方法向河水一样的流动,避免过度制造情况发生。
按照节拍进行生产除了考虑适应客户需要的速度外,还充分的考虑了人性化的需要。
人喜欢有节奏的事物,例如人对自己喜欢的歌曲听几遍就会记住,但是如果背同样长短的古文或英文单词你会觉得困难的多,因为歌曲有节拍。
如果让人在生产线作业时,和唱歌一样的富有节奏,那么,人的作业将会轻松很多,这也是更多的考虑了人性化管理的内容后所产生的结果。
3、柔性生产系统由于售出的速度会在不同时期发生变化。
因此,必须使生产线布局能够适应不同生产节拍的要求,利用一人多序的方法,调整人的作业范围达到适应不同生产速度之目标。
在作业中,以人的动作为中心,不考虑设备的能力,使人的作业达在这里,需要充分理解一人多机和一人多序的不同二、建立流程型生产线布局将设备布局的形式从集群式改造为流程式之后,随着生产制造过程中的物流距离快速缩短,连续流制造已经可以成为现实。
layout(工厂布局)ppt课件
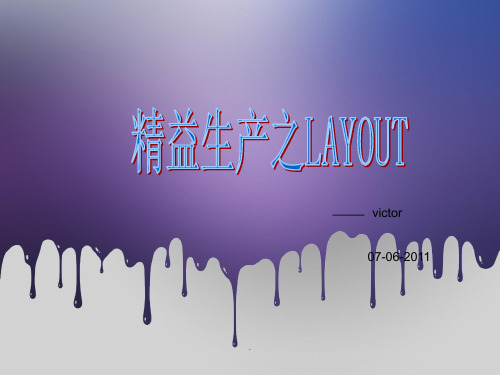
某公司产品P-.Q分析法
如上图式,按照2/8原则,可以将P1,P2,P3设计为专用生产线, 因为其量大,这样可以稳定生产,减少切换,提高品质效 率.P4~P10根据其工艺流程利用"产品分族矩阵"进行分析
分析后产品分族矩阵图
.
从上图可知: P4,P6,P9产品的工艺几乎相同 P5,P7产品的 工艺几乎相同 P8,P10产品的工艺几乎相同
.
二. 精益Layout设计原则
统一的原则 最短距离的原则 人流,物流畅通的原则 充分利用立体空间的原则 安全满意的原则 灵活机动的原则
.
三. Cell(单元)生产线布局
Cell生产式layout主要是对企业各类产品进行分类,以 相同的加工工艺流程作为一条生产线进行的layout设计
(1).Leadtime
一.Layout的定义
Layout的中文名称是“布局”,简单的说布局 就是对设备,作业台,物料,工装,半成品, 水,电,气等的综合配置。主要研究工序之间, 车间之间,部门之间及工厂整体的设备,作业 台,材料,仓库等配置与放置的合理性,已达 到整个生产系统人流与物料畅通化,流程最优 化,效率最大化的目标
螺丝 框架
B
焊接10
B单元生产人数 =40/5=8人
焊接10
#代表组
S铁芯 A
10
A单元生产人数 =10/5=2人
5
螺丝
底板
15
10
C
导线
C单元生产人数 =10/5=2人
.
Q1
某工厂收到一产品订单数量为20个,该产 品中间周转库存分别为500,600,和300个在 制品,该工厂有A,B,C三个工序,三个工序 生产能力相同,都是1秒/个,请问 1),生产该20个产品的生产周期要多少时间? 2),A,B,C三道工序的加工时间要多少时间?
线平衡和生产线布局ppt课件

并行作业,增加人员
1人
作业 作
业
作
时
业
间
时
2人
间
作业
拆解去除
工序 1 2 3 4 5
工序 1 2 3 4 5
15
平衡改善法则及注意事项
作业改善后合并
重排
作
作
业
业
时
时
间
间
工序 1
2
3
4
5
工序 1
2
3
4
5
16
平衡改善法则及注意事项
2.平衡改善过程中应注意事项:
A.需要同样工具和机器的作业要素可分配在同一专用设备工序内
Nt = 节拍时间
Nt
=
54.5秒 5. 9秒/个
= [9. 2人]取整 10人
22
H.A.I
Part 2.生产线布局
流水线的 “物流” 和“物留”
物流
顺畅流动 没有停滞
物留
中间停滞 隐藏问题
24
“传统”输送带和“成长型”输送带
传统输送带作业
①
② ③③ ④
传统输送带的4种浪费:
① 取放动作浪费 在制品取放至少浪费2~5秒时间。
12
平衡改善法则及注意事项
1.平衡改善法则-ECRS法则
符号
名称
说明
E
取消Eliminate 对于不合理、多余的动作或工序给予取消
C
合并Comebine
对于无法取消又是必要的,看是否可以合并以达到省时、 简化的目的
R
重排Rearrange
经过取消、合并后,可再根据“何人”“何时”“何处” 三个提问后进行重排
6
【培训】生产线布局PPT课件
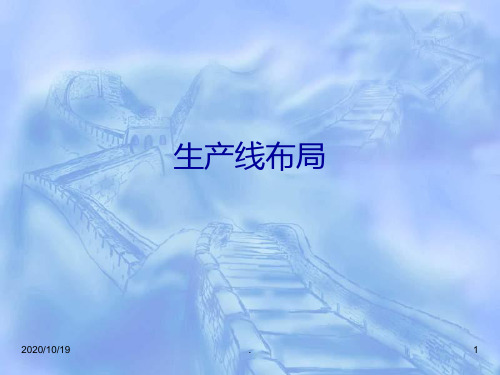
2020/10/19
.
45
产品原则布局
▪ 第五步对工作站安排作业,工作站周期:50.4秒
工作站 作业 时间(S)
工作站1 A
45
工作站2 D
50
工作站3 B
11
E
15
C
9
F
12
工作站4 G
12
H
12
I
12
J
8
工作站5 K
1. 采用了看板管理,拉动生产方式 2. 车间布局U型布局; 3. 不同类型的机器摆放在一块; 4. 实现了单件流的生产; 5. 机器小型化 ; 6. 工序中间很少甚至没有库存; 7. 实现了作业标准化; 8. 对工人实行了多技能培训; 9. 具有完善的作业改善活动制度
2020/10/19
.
3
看谁摘的果子最多!
2020/10/19
.
12
鉴别七大浪费
六、来自工序不当的浪费
工作本身产生的浪费,当机器不正常运作而使操作人员 需要花额外时间,或当操作人员出于习惯或花了过多的 时间使清洁工作超过了规格的要求。
多余的检查也是过程浪费的另一个表现形式。
2020/10/19
.
13
鉴别七大浪费
七、不需要的动作的浪费
人们在工作设置中经常将工作中的动作搞混乱,实际做的动 作和工作要求的动作往往是不同的。
如果按照工作单,每天应该生产160K个产品,那么:
节拍时间 =
每天有效时间 每天须生产数
= 1140 分钟 = 0.007 分钟/产品 160K 个产品
换句话说,每分钟生产140单位的产品。
2020/10/19
.
40
产品原则布局
精益生产--精益布局课件

3、提高场地利用率;
4、站立或走动操作,提高工作效率,减少职业伤害;
5、降低劳动强度;
6、提高作业质量和效率;
7、适应多品种少批量生产;
8、可以跟随产量的变化增减人员;
9、改善作业环境;
10、……。
37
3
精益布局简介
精益布局与传统布局的区别:
传统布局:
精益布局:
1、产品一批批的下线; 1、产品一件一件下线;
51
5 实现精益布局的步骤
实现精益布局的步骤:1、现场布局图绘制
充分尊重和考虑现状布局,在此基础上改善!
52
5 实现精益布局的步骤
实现精益布局的步骤:2、根据产品族确定分析对象 确定要分析的产品对象,获取一个产品的生产工艺过程作
为主线来综合考虑布局结构的合理性和通用性。
选择工序最多、产 量最大或工艺流程
设备有效工作时间;
生产批量大小;操作工数量;
有效工作时间;废品率;……
54
5 实现精益布局的步骤
实现精益布局的步骤:4、生产过程节拍分析及定拍 在布局结构分析的过程中, 节拍是一个非常重要的分析信
息,他的作用是确定生产能力、工作量大小等,从而给给各个 产品系列设计需求的人机料法环(4M1E)等各个生产要素 。
= 40/((8X3600X85%)/(450000/300)) = 2.4510(条)
57
5 实现精益布局的步骤
实现精益布局的步骤:6、现场库存状况分析 通过现场观察和员工沟通来获取库存产生的原因,并与基
内容: 配置时要使搬运距离、时间最短。
理由: 移动距离越短、物料搬运所花费的费用和时间就越短。
42
4
精益布局的原则
车间生产线布局不错 ppt课件

第二部分 车间布置设计的原则
二、原则
3、车间布置应符合设备安装、检修要求的原则 (1)根据设备大小及结构,考虑设备安装、检修及拆卸所 需要的空间和面积; (2)满足设备能顺利进出车间的要求; (3)通过楼层的设备,楼面上要设置吊装空; (4)考虑设备的检修和拆卸以及运送所需要的起重运输设 备。
第二部分 车间布置设计的原则
二、车间布置设计的依据
1、生产工艺流程图 2、物料衡算数据及物料性质、包括原料、半成品、成品、 副产品的数量及性质;三废的数量及处理方法 3、设备资料,包括设备外形尺寸、重量。支撑形式、保温 情况极其操作条件,设备一览表等 4、公用系统用量,供排水、供电、供热、冷冻、压缩空气、 外管资料等
二、车间布置设计的依据
二、原则
2、车间布置应符合生产操作要求的原则 (1)每一个设备要考虑一定的位置。 (2)设备布置应考虑为操作工人能管理多台设备或多种设备 创造条件。 (3)设备布置不宜过挤或过松,宜尽量对称紧凑,排列整齐, 充分利用空间。 (4)要考虑相同设备或相似设备互相使用的可能性和方便性 (5)设备的自动测量仪表要集中控制,阀门控制集中,便于 工人操作。
二、原则
7、车间布置应符合生产发展的要求。
第三部分 车间布置设计的内容
第三部分 车间布置设计的内容
设计内容
车间布置设计的内容可分为厂房布置和设备布置。厂 房布置是对整个车间的厂房和各个组成部分,按照它们在 生产中和生活中所起的作用进行合理的平面布置和安排; 设备布置是根据生产流程情况及各种有关因素,把各种工 艺设备在一定的区域内进行排列。
在进行设备布置时,可搞出几个方案,反复 评比,选出较理想的方案,绘出设备草图。
设备布置的步骤
(5)绘制正式设备布置图 根据设备布置草图,考虑以下因素加以修改: 总管排列的位置,做到管路短而顺;检查各 设备基础大小,设备安装、起重、检修的可 能性;设备支架的外形、结构,常用设备的 安全距离;外管及上、下水管进、出车间的 位置;操作平台、局部平台的位置大小等。
- 1、下载文档前请自行甄别文档内容的完整性,平台不提供额外的编辑、内容补充、找答案等附加服务。
- 2、"仅部分预览"的文档,不可在线预览部分如存在完整性等问题,可反馈申请退款(可完整预览的文档不适用该条件!)。
- 3、如文档侵犯您的权益,请联系客服反馈,我们会尽快为您处理(人工客服工作时间:9:00-18:30)。
2021/3/1
9
2021/3/1
10
鉴别七大浪费
四、来自生产过剩的浪费
公司有时会生产比他们可能卖出去的更多的产品,因为他 们想要建立库存,作为一个安全保证措施来防止可能出错 而造成的后果,或者因为他们想要保证他们的设备和设施 的运转。
无论什么原因,没有直接的需求就生产的产品都是浪费。
如果有些项目的需求没有了,那这时,这些项目将不得不被放弃或者 降价处理。
二、运输中的浪费
具有代表性的是,有些项目总是无工作性质地移动,时间 花费了在路途中,这是浪费。
2021/3/1
8
鉴别七大浪费
三、来自库存的浪费
库存代表着某些项目正等待某些事情的发生,这里的浪 费表现在:和保存着这些项目来等待有关联的成本,对 这些项目无增值而导致时间的损失。
安全库存是为了保证生产部门的正常运作和弥补不良品 的损失而存在的,但是安全库存不能够超出它们的正常 需要。
▪ 问:
• 金额如何计算出来的? • 组合布局方法或排列有多少种? • 如何排列的才是有效的?
2021/3/1
23
工艺原则布局
▪ 成本矩阵——方案一,总成本合计3474
11 2 3 4 5 6 7 82021/3/1
2
3
175 50
0
4
5
6
7
0
60 400 60
100 150 180 240
17 88 125 198
▪ 使用范围:
• 批量小 • 体积大
▪ 布局特点
• 以产品为中心 • 不考虑物流成本和复杂程度
2021/3/1
18
工艺原则布局
▪ 定义:
• 将相似的设备或功能集中放在一起的布局方式 • 也称车间布局,如车床车间
▪ 使用范围
• 生产设备密集型 • 设备专业性 • 自动化程度高 • 资本密集型 • 产品重量轻
2021/3/1
次数
1 1 2 3 4 5 6 7 8
23 175 50
0
45 0 30 100 75 17 88
20
678 200 20 25 90 80 90 125 99 180 5 0 25 0 180 187
347 103 7
21
▪ 玩具厂各车间年物流成本示意图
2021/3/1
22
工艺原则布局
其间,它们储存在仓库里,造成成本的增加和库存的浪费。
2021/3/1
11
鉴别七大浪费
五、来自时间等待的浪费
时间等待的浪费是很容易被鉴别的,它有很多的表现形态, 包括有:
• 为定单而等待 • 为批准而等待 • 为零部件而等待 • 为物料而等待 • 为前面过程中叙述的项目而等待 • 为设备的维修而等待
生产线布局
2021/3/1
1
精益生产五项基本原则
• 价值 (VALUE) : 决定于客户是否愿意为了它而付钱。
• 价值流 (VALUE STREAM) : 从产品设计到客户服务的所有
活动的描述和鉴别,都需要消除非增值活动。
• 流畅 (FLOW) : 消除所有工序的阻滞使价值流“流畅”而没有
中断。
• 拉动 (PULL) : 通过客户的需求来达到产品和工序能够畅通的
2021/3/1
19
工艺原则布局
▪ 案例:玩具厂有8个车间,采用物料集中搬 运方式,每次只能搬运一个周转箱,车间之 间运输成本为1元,每隔一个车间增加1元
1 收发部
3 铸造
5
小型玩具 转配线
7 喷漆
2
4
68Biblioteka 塑模与冲 缝纫 大型玩具 机械装配
压
转配线
线
2021/3/1
20
工艺原则布局
车间之间的流动表
2021/3/1
15
生产线布局类别
▪ 定位原则布局 ▪ 工艺原则布局 ▪ 产品原则布局 ▪ 成组技术(单元式)布局
2021/3/1
16
定位原则布局
▪ 定义:
• 将原材料和设备按照使用次序和移动的难易程度 在产品的四周进行生产
▪ 起源
• 19世纪初亨利福特的汽车装配线
2021/3/1
17
定位原则布局
6σ=?
2021/3/1
4
σ
2 3 4 5 6
2021/3/1
6σ标准
PPM 308,537
66,807 6,210 233 3.4
PPM等于 多少?
缺陷减少5倍 缺陷减少11倍 缺陷减少26倍 缺陷减少68倍
5
鉴别七大浪费
一、生产产生的不良引起的浪费
任何产品的不良都是浪费的一个主要来源。
2021/3/1
6
产生更严重的成本连锁反应……
更多的
“一人错误百人忙” 防火成本 的成本暴增曲线
更多的 救火成本
2021/3/1
更多的 返工成本
正常成本
救火、防火、多余监 督、过度控制、多余 检验、投诉处理、退 货维修、商誉损失、 顾客流失等效应连锁 扩大成本! 重工、返修、报废成本
日常管销/制造成本
7
鉴别七大浪费
流动的一种能力。
• 尽善尽美(PERFECTION) : 通过持续改善的应用,来提倡“
第一次就做好”的一种能力。
2021/3/1
2
大规模生产和精益生产方式的区别
大规模生产方式
精益生产方式
1. 采用推动生产方式 2. 车间布局是按功能区划分; 3. 相同类型的机器摆放在一块; 4. 大批量的生产; 5. 机器适合于大批量生产 ; 6. 工序中间容易堆积库存 ; 7. 未实现作业标准化; 8. 工人一般只会一种操作; 9. 没有或只有个体的作业改善活动
1. 采用了看板管理,拉动生产方式 2. 车间布局U型布局; 3. 不同类型的机器摆放在一块; 4. 实现了单件流的生产; 5. 机器小型化 ; 6. 工序中间很少甚至没有库存; 7. 实现了作业标准化; 8. 对工人实行了多技能培训; 9. 具有完善的作业改善活动制度
2021/3/1
3
看谁摘的果子最多!
2021/3/1
12
鉴别七大浪费
六、来自工序不当的浪费
工作本身产生的浪费,当机器不正常运作而使操作人员 需要花额外时间,或当操作人员出于习惯或花了过多的 时间使清洁工作超过了规格的要求。
多余的检查也是过程浪费的另一个表现形式。
2021/3/1
13
鉴别七大浪费
七、不需要的动作的浪费
人们在工作设置中经常将工作中的动作搞混乱,实际做的动 作和工作要求的动作往往是不同的。
作为一个确定的目的,工作是要作为一组精确的动作来考虑 的,哪些是增值的,那些是不增值的。
一个人在每天的恒定的工作中(例如一个很忙的人)可能实 际上只是很少一部分是增值工作。
工作中的不需要的动作被认为是浪费的,不增值的。
2021/3/1
14
生产布局前的准备工作
▪ 产能评估 ▪ 生产线顺流 ▪ 库存周转评估