瓦楞纸板不良原因分析报告
瓦楞纸板常见纸病的解决方案

瓦楞纸板常见纸病的解决方案一、开胶、假粘1、里纸开胶原因分析:1.1胶质量不符生产要求或腐败变质;1.2上胶量太小;1.3车速过快,瓦楞辊、压力辊热量不足;1.4压力辊压力不足;1.5瓦楞辊、压力辊的中高严重磨损。
解决方法:1.1更换合格胶液;1.2适量调大涂胶量;1.3提高瓦楞辊、压力辊温度,保证180℃以上开机,同时根据温度情况调整车速;1.4适当调整压力辊压力,以里、瓦纸粘合良好,里纸不露楞、瓦纸不碎为宜;1.5打磨或更换新压力辊、瓦楞辊。
1、面纸开胶、夹芯开胶原因分析:2.1胶量过小、烘干机速度过慢;2.2胶液稀薄,涂胶辊挂胶不足;2.3烘干机热板温度不足,胶液未充分糊化;2.4烘干机车速过快,纸板烘干不足;2.5烘干机传输带上面的压载辊没完全落下。
解决方法:2.1适当加大涂胶量,并酌情提高车速;2.2更换胶液或在原胶液中加入适量乳化剂;2.3升高烘干机热板温度至180℃以上开机;2.4减慢车速;2. 5落下压载浮辊。
原因分析:3.1瓦楞辊温度不足;3.2胶量过小,温度过高;3.3车速缓慢造成萃胶;3.4胶液黏度不够。
解决方法:3.1提高单面机工作温度;3.2调整涂胶量,关闭热源,待温度下降至180℃以下,160℃以上开机;3.3提高单面机速度;3.4适当增加胶液黏度。
2、面纸假粘原因分析:4.1烘干机热板温度不足;4.2胶液沉淀变质;4.3纸板在烘干机内停留时间过长。
解决方法:4.1待温度达到胶液能糊化时开机;4.2更换新胶;4.3尽量减少停机时间,换单换纸和断纸再续时动作要果断迅速。
二、倒楞1、单面纸板倒楞原因分析:1.1瓦楞辊磨损;1.2上下瓦楞辊间隙过大;1.3瓦楞纸定量太高且厚度太厚;1.4瓦楞纸水分过大;1.5瓦楞纸未经预热器,可塑性差。
解决方法:1.1磨削或更换瓦楞辊;1.2调整瓦楞辊间隙至0.5mm;1.3更换瓦楞纸;1.4调大预热包角,增大预热面积;1.5将瓦楞纸穿过预热器。
瓦楞纸板脱胶原因及改善措施(一)
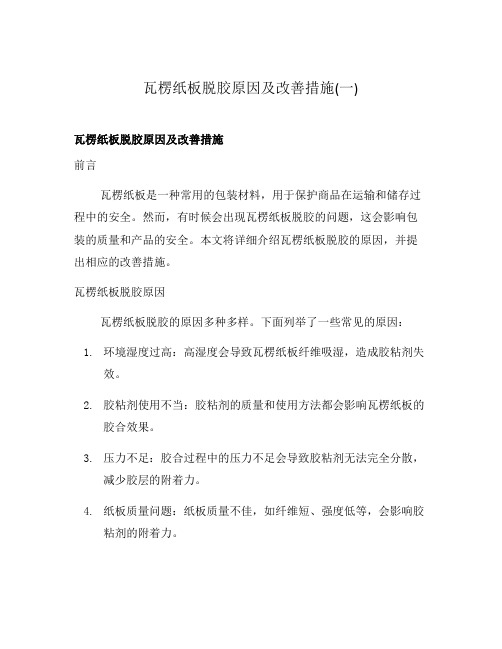
瓦楞纸板脱胶原因及改善措施(一)瓦楞纸板脱胶原因及改善措施前言瓦楞纸板是一种常用的包装材料,用于保护商品在运输和储存过程中的安全。
然而,有时候会出现瓦楞纸板脱胶的问题,这会影响包装的质量和产品的安全。
本文将详细介绍瓦楞纸板脱胶的原因,并提出相应的改善措施。
瓦楞纸板脱胶原因瓦楞纸板脱胶的原因多种多样。
下面列举了一些常见的原因:1.环境湿度过高:高湿度会导致瓦楞纸板纤维吸湿,造成胶粘剂失效。
2.胶粘剂使用不当:胶粘剂的质量和使用方法都会影响瓦楞纸板的胶合效果。
3.压力不足:胶合过程中的压力不足会导致胶粘剂无法完全分散,减少胶层的附着力。
4.纸板质量问题:纸板质量不佳,如纤维短、强度低等,会影响胶粘剂的附着力。
5.操作不当:胶粘剂施加不均匀、操作过程中的温度控制不当等,都会影响瓦楞纸板的胶合效果。
改善措施针对瓦楞纸板脱胶的原因,我们可以采取以下改善措施:1. 控制环境湿度•在生产车间中使用空调设备,保持温度和湿度在适宜范围内。
•安装湿度调节装置,及时调整湿度,确保在正常工作范围内。
2. 优化胶粘剂选择和使用方法•选用质量可靠的胶粘剂,并按照厂家建议的使用方法使用。
•加强对胶粘剂施加过程的监控和管理,确保胶粘剂的合理用量和均匀分布。
3. 提高胶合压力•针对胶粘剂的特性和纸板的厚度,调整瓦楞纸板生产设备中的压力参数,确保胶粘剂能够完全分散。
4. 选用优质纸板•选择纤维长、强度高的纸板材料,提高瓦楞纸板的质量。
•定期检查纸板供应商的资质和质量控制体系,确保所采购的纸板符合要求。
5. 加强操作培训与控制•对操作人员进行胶粘剂使用和设备操作的培训,提高其技能水平。
•建立操作规范和质量控制程序,确保每个环节都符合要求。
•定期检查和维护瓦楞纸板生产设备,确保其正常运行。
总结瓦楞纸板脱胶是一个影响包装质量的重要问题,但通过控制环境湿度,优化胶粘剂的选择和使用方法,提高胶合压力,选用优质纸板,并加强操作培训与控制,我们可以有效地解决这个问题。
瓦楞纸板不良原因分析

瓦楞纸板不良原因分析瓦楞纸板是由瓦楞纸板芯和面纸组成的一种多层结构材料。
它主要用于包装和运输行业,承载能力强,便于加工和加工。
然而,在实际生产和使用过程中,我们经常会遇到各种瓦楞纸板的不良问题,这直接影响了其使用效果和质量。
以下是对瓦楞纸板不良原因进行分析的一些常见问题。
1.压痕和划痕:瓦楞纸板在生产过程中可能会出现压痕和划痕的问题。
这可能是由于设备不当调整或操作不规范导致的。
例如,如果压痕辊的间距不正确,或者生产速度过快,纸板受到了太大的力,就会出现压痕。
而划痕则可能是由于切割工具不锋利或切割速度过快而导致的。
2.破裂和撕裂:瓦楞纸板在运输和使用过程中容易出现破裂和撕裂的问题。
这可能是由于纸板的强度不足造成的,可能是由于纸板芯的纸张质量不好,或者纸张的厚度不足。
此外,如果瓦楞纸板在存储或运输过程中受到了湿气或温度变化的影响,也会导致纸板的强度减小,容易发生破裂和撕裂。
3.潞水和水印:潞水是指瓦楞纸板表面出现水印痕迹,给纸板的外观质量带来影响。
潞水可能是由于纸张表面平整度不好,或者纸张吸水性能不佳导致的。
此外,如果生产过程中的湿度控制不当,或者纸板表面存在杂质或污染物,也会导致潞水问题的出现。
4.尺寸不一致:瓦楞纸板的尺寸一致性是其质量的重要指标之一、如果纸板的尺寸不一致,可能会导致包装箱的组合困难,影响使用效果。
尺寸不一致的原因可能是由于生产过程中的设备调整不准确或操作不规范,或者纸板芯的厚度不一致,造成纸板的尺寸差异。
5.外观缺陷:瓦楞纸板的外观缺陷可能是指纸板芯表面的起泡、蜂窝状,或者面纸的褶皱、异常颜色等问题。
这些缺陷可能是由于纸张质量不佳、生产过程中的设备故障或不良操作导致的。
例如,如果纸张含水量不均匀,或者设备温度过高,就会导致瓦楞纸板表面起泡或蜂窝状。
综上所述,瓦楞纸板的不良问题可能是由于生产过程中的设备故障、操作不良、纸张质量不佳等因素导致的。
为了解决这些问题,生产厂家应该加强对设备的维护和调整,确保操作人员的培训和规范。
影响瓦楞纸板生产过程中质量的因素分析

1 0・
科 技 论 坛
影响瓦 楞纸板 生产过程 中质量 的因素分析
陈 敬 谦
( 广 东肇庆西江机械制造有 限公 司, 广 东 肇庆 5 2 6 0 6 0 )
摘 要: 随 着社 会 经 济 的 不 断 完善 和发 展 , 人 们 对 产 品 包装提 出 了更 高的要 求 , 彩 色纸 板 被 商 家广 泛的 运 用 , 而 且 彩 色纸 板 占据 很 大 的 市 场份 额 , 纸板 产品 的 质 量 受到人 们 的 关 注 。本 文 对 瓦楞 纸板 生产 过程 中的 质量 控 制 进行 论 述 , 在 一 定程 度 上 可 以 完善 瓦楞 纸板 的质 量 。 关键 词 : 瓦楞 纸板 ; 生产 ; 质 量
装。纸板
三层 瓦楞 纸板
五层瓦 楞纸板 七层 瓦楞纸 板 3瓦楞纸板生产过程中的质量控制 3 . 1 对瓦楞纸板生产过程中厚度的质量控制 图 1 瓦 楞 纸板 结构 分 类 通常 情况下 , 瓦楞纸板厚度越大, 纸箱成型后会产生较为严重的变 形, 造成变形系数的增大。所以, 如果包装中对纸箱的要求不高 , 可 以进 下 表面 指定部 位进 行加 湿 。 可 以根 据纸板 幅宽 的变 化调 整喷 头 的位置 , 行模切的打样试验, 通过对包装的检验后 , 可 以结合套装泡沫的类型和 也可以根据需要来调整加湿量的大小及气雾颗粒的大小。加湿器的控 护角材料的分析 , 确定包装的方式, 要与包装使用的客户进行联 系, 在 制系统与生产线联动 , 自动控制, 同时开机同时关机。 了解实物的基础上, 从而可 以对包装进行模拟 , 确定好包装的尺寸和规 3 . 4对 瓦楞纸 板模 切 的控制 格, 从而更好的满足客户的使用 。 瓦楞纸板与一般的纸张有很大的差别 , 其厚度 比较大。如果对瓦楞 3 . 2对生产过程中瓦楞纸板订和糊位置的质量控制 纸板的正面进行模切 , 会产生压痕, 导致纸张在折叠的过程中会产 生偏 不论是采用机械或者手工订制, 瓦楞纸板都会存在一定的误差, 对 差 。而 且瓦 楞纸 板 的厚 度对 纸箱 的 内径产 生直 接的影 响 。因此 , 为 了完 瓦楞纸箱的制作产生不 良的影响 ,导致纸箱 的成型规格受到影响。因 善 纸箱 的 内径 规格 , 应该 完善 瓦 楞纸 板 的反 向模切 , 这 样可 以确 保 纸箱 此, 要完善对瓦楞纸板 的订和糊 的工艺 , 从而确保瓦楞纸板制作成瓦楞 压痕的精确性 , 防止其对纸箱 内径产生影响 , 导致纸箱内径误差过大。 纸箱时可以有一定的标准, 防止误差过大 , 确保瓦楞纸箱在生产的过程 3 - 5 张 力 的控 制 中可 以严格按照标准执行 。 在瓦楞纸箱的制作中, 一般是采用 2片瓦楞 在具体的生产环节 , 会在开机 、 忽然停机或者更换卷纸的过程中 , } } { 纸 板制作 。 现纸卷直径的变化 , 纸的张力如果不能得到控制会导致废品率 的上升 , 3 l 3 瓦楞纸板含水量的质量控制 如果张力过大会导致碎瓦 、 塌瓦和爆裂等情况 , 如果张力过小会导致起 含水率是瓦楞纸板的重要指标之 ,它直接决定着瓦楞纸板的质 泡和纸的偏斜等 。 量, 上下面纸的含水量不均衡是瓦楞纸板翘 曲的主要原因。广义上 , 纸 在对张力进行控制 的环节中,可以充分的采用安装恒张力控制的 板翘曲是由瓦楞纸板上组合部件尺寸大小的不均匀变化产生 ,尤其是 方式 , 在检测 的过程 中, 可以对纸张的张力变化进行检测 , 并且根据实 芯纸造成的 ,通常发生在瓦楞楞尖和底纸牢 固粘和并且在两者之间不 际的张力变化 , 对原纸的制动器进行控制 , 形成一个检测 、 反馈和制动 再发生相对移动后 。 机器方 向( MD) 纸板翘曲是由于机件滚动方向各种 的闭环控制 回路 , 确保纸张可以抑制保持水平方 向的运行。如果需要非 力原先就不平衡和这种不平衡的周期变化所引起的上下面纸在机件滚 常小的张力 , 那么要借助高档的制动器来完成。 动方向的不均匀改变而产生的。 这里主要的作用力是纸幅张力 , 是由于 结束语 水份含量变化引起的 , 即所谓原纸的“ 湿涨性” 的特点引起的收缩力和 如今 , 瓦楞 纸板在 包装 中得 到 了广泛应 用 , 其 可 以减少 材料 的浪 费 , 扩张力 。 这种湿涨 l 生 在瓦楞方 向上远大于机器方向上 , 而且纸板周边环 起到保护环境的效果 , 而且成本 比较低。所以 , 应该完善瓦楞纸板 的制 境温度直接影响着纸板有含水量 ,温度的变化 同样造成纸板的尺寸大 作的质量控制。 小变化 。加上瓦楞纸板是由纤维原纸制成的, 受环境因素影 响非常大 , 参 考文献 因此瓦楞纸板包装存在的最大技术问题是难以抗水保湿。而在高温干 f 1 1 陈艳 琴. 浅谈 瓦楞 纸 箱 中瓦楞纸 板粘 合 强度 的测 定及 影响 其 质量 的 因 燥的环境中, 瓦楞纸板水分降到一定程度后会产生干脆现象, 纸板的耐 素Ⅲ. 计 量与 测试技 术, 2 0 1 5 , 1 1 : 7 8 - 7 9 . 折『 生 下降 , 最后使纸箱翻盖断裂。所以, 瓦楞纸板生产时最大缺陷就是 『 2 1曾欧.瓦楞纸板 生产过程 中废料的产生及控制研 究 .包装工程, 01 4, 1 2 : 2 7 5- 2 78 . 干燥时脆裂, 高湿时强度降低, 含水量不均衡产生翘曲。因此 , 如何控制 2 瓦楞纸板的含水量 ,确保瓦楞纸板周边生产环境的稳定是非常重要的 『 3 1 尤聪 娥 . 浅谈 影 响 瓦楞 纸 箱 质量 的若 干 因素及 其 应 对 措 施 【 J J . 湖 北造 工作。 在生产线各独立单元安装湿度控制系统对传送着的瓦楞纸板上 、 纸 , 2 0 1 4 , 1 : 2 6 - 2 8 .
瓦楞纸板不良原因分析

瓦楞纸板不良原因分析瓦楞纸板是一种由多层纸板互相粘合而成的材料,具有良好的抗压性能和缓冲性能,广泛应用于各个行业的包装中。
然而,在生产和使用过程中,瓦楞纸板可能会出现一些不良现象,影响其使用效果和寿命。
下面将分析一些可能导致瓦楞纸板不良的原因。
1.原材料质量不良:瓦楞纸板的质量主要受原材料的影响,如果原材料质量不好,会直接影响到瓦楞纸板的质量。
比如,纸张的纤维长度不足、杂质过多、含湿率过高等都会导致瓦楞纸板的强度下降和易碎性增加。
2.生产过程不规范:瓦楞纸板的生产过程包括纸张的加工、糊合、干燥等环节,如果操作不规范或控制不当,会导致质量不良。
比如,糊合时糊胶的浓度不合适、温度控制不好、糊胶的均匀性不好等都会影响瓦楞纸板的强度和质量稳定性。
3.设备老化或损坏:生产瓦楞纸板需要使用一系列的设备,如纸张预处理机、糊合机、干燥机等。
如果这些设备老化或损坏,就会影响生产过程的正常进行,进而导致瓦楞纸板的质量下降。
4.储存条件不好:瓦楞纸板在生产出来后需要进行储存,如果储存条件不好,比如温度过高或者潮湿,会导致纸张变形、发霉,进而影响瓦楞纸板的强度和质量。
5.运输和包装不当:瓦楞纸板在运输和包装过程中也容易遭受挤压、湿泡等不良影响,特别是在长途运输或者储存时间较长的情况下,容易出现不均匀应力分布,导致瓦楞纸板强度下降或出现划痕、弯曲等问题。
6.设计不合理:瓦楞纸板在使用过程中有时受到外力的作用,特别是在堆叠、挤压等情况下,如果设计不合理,纸板可能容易变形、产生断裂、划痕等不良现象。
综上所述,瓦楞纸板不良的原因多种多样,涉及到原材料、生产过程、设备、储存和运输等多个方面。
为了提高瓦楞纸板的质量,减少不良现象的发生,需要从原材料的选择和质量控制、生产过程的改善和规范、设备的维护和更新、储存和运输条件的优化以及设计的合理性等方面进行改进和管理。
只有全面有效地把控这些方面,才能保证瓦楞纸板的质量和可靠性,满足各个行业对包装的需求。
瓦楞纸板质量影响因素分析
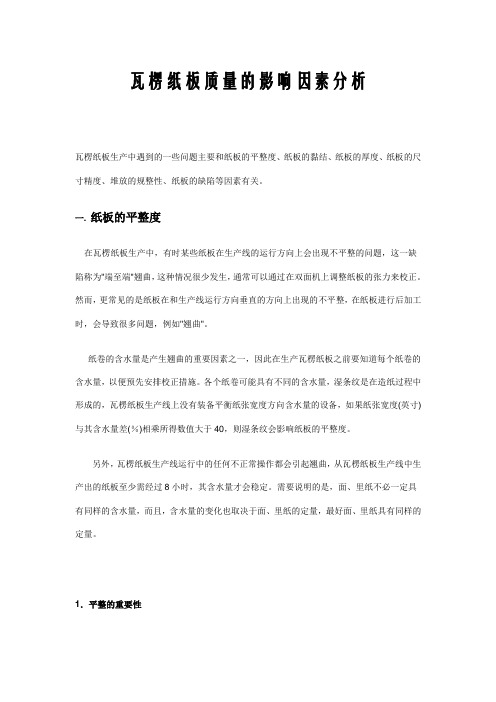
瓦楞纸板质量的影响因素分析瓦楞纸板生产中遇到的一些问题主要和纸板的平整度、纸板的黏结、纸板的厚度、纸板的尺寸精度、堆放的规整性、纸板的缺陷等因素有关。
一. 纸板的平整度在瓦楞纸板生产中,有时某些纸板在生产线的运行方向上会出现不平整的问题,这一缺陷称为"端至端"翘曲,这种情况很少发生,通常可以通过在双面机上调整纸板的张力来校正。
然而,更常见的是纸板在和生产线运行方向垂直的方向上出现的不平整,在纸板进行后加工时,会导致很多问题,例如"翘曲"。
纸卷的含水量是产生翘曲的重要因素之一,因此在生产瓦楞纸板之前要知道每个纸卷的含水量,以便预先安排校正措施。
各个纸卷可能具有不同的含水量,湿条纹是在造纸过程中形成的,瓦楞纸板生产线上没有装备平衡纸张宽度方向含水量的设备,如果纸张宽度(英寸)与其含水量差(%)相乘所得数值大于40,则湿条纹会影响纸板的平整度。
另外,瓦楞纸板生产线运行中的任何不正常操作都会引起翘曲,从瓦楞纸板生产线中生产出的纸板至少需经过8小时,其含水量才会稳定。
需要说明的是,面、里纸不必一定具有同样的含水量,而且,含水量的变化也取决于面、里纸的定量,最好面、里纸具有同样的定量。
1.平整的重要性当纸板直接作为成品出售时,翘曲往往被用户认为是质量问题而成为扯皮的根源。
更进一步说,瓦楞纸板的平整度对以后的加工操作有很大的影响。
在自动堆积机中,纸板平整才能堆积稳定,才能很方便地由滚轮传送器运出去,堆积的稳定性对于从瓦楞纸板生产线终端传送到库房,再从库房传送到后加工设备是很重要的。
后加工设备的自动进料器不能接受过于翘曲的纸板,翘曲的纸板会引起阻塞和机器停车,大大降低生产效率。
同时,如果后加工设备不能够连贯地传送纸板,就会导致不准确的印刷记数和模切操作.纸板翘曲也会导致粘盒、粘箱困难。
另外,纸板翘曲会降低纸箱的抗压强度,因为箱壁偏移使纸箱易垮塌。
2。
翘曲度的测量为了在瓦楞纸板生产线上进行各种调整以平整翘曲也为了纸板在厂内、外的质量控制,都需要测量翘曲度。
瓦楞纸板及印刷不良问题产生的原因及解决办法

•六 楞折皱
•产生原 因
•瓦楞辊平行度不好
•瓦楞辊磨损
•瓦楞原纸质量不 •好或水分不均衡
•瓦楞原纸张力太小
•解决办 法
•修正、调整瓦楞辊的平行度
•修复或更换瓦楞辊
•更换瓦楞原纸或 •改善预热器效果
•适当调整张力控 •制系统,加大张力
•七 瓦楞横切断、纵裂 断
•产生原 因
•检查、修正、清 •理或更换导纸板
•加大输送过桥的张力控制 •系统,增大或减少张力
•产生原 因
•双面机加热板表面有异物
•瓦楞原纸、箱纸 •板含水量不均衡 •瓦楞原纸张力过大
•胶黏剂黏度不够
•胶黏剂附着量太大
•解决办 法
•清除异物,保持表面清洁
•适当预热或更 •换原纸、箱纸板
•减少张力系统的摩擦
•调整胶黏剂制作, •检查各种原料质量
•调整托架使之平行
•更换轴承
•适当调整张力控制
•产生原 因
•涂胶辊、浮 •动辊间隙不当
•胶黏剂质量不好
•箱纸板和瓦楞原纸含 •水量不均匀、张力小
•对瓦楞原纸的 •蒸汽喷雾不足
•解决办 法
•调整两者的贴合间隙 •更换胶黏剂
•适当预热并加大张力控制
•调整预调器的蒸汽喷雾量
•二 楞倾斜(倒楞)
•产生原 因
•涂胶辊和浮动辊之间间隙太 小
•解决办 法
•修复或更换瓦楞辊
•检查相关部件,修正贴面间隙
•保持辊面干净,检查 •冷凝水排放和供气系统 •修正位置、更换或清理导纸板
•减少堆积量,降低输出张力
•适度调整、保持正常的工作间隙
•产生原 因
•涂胶机涂胶量大,使楞峰变形
瓦楞纸板各种常见纸病的解决方案
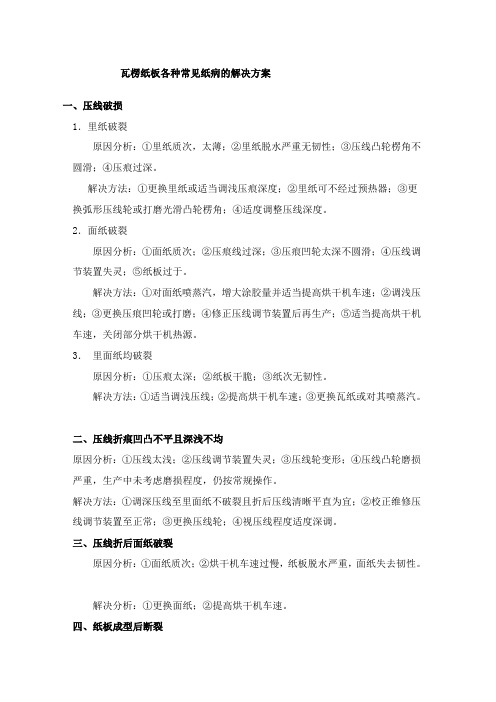
瓦楞纸板各种常见纸病的解决方案一、压线破损1.里纸破裂原因分析:①里纸质次,太薄;②里纸脱水严重无韧性;③压线凸轮楞角不圆滑;④压痕过深。
解决方法:①更换里纸或适当调浅压痕深度;②里纸可不经过预热器;③更换弧形压线轮或打磨光滑凸轮楞角;④适度调整压线深度。
2.面纸破裂原因分析:①面纸质次;②压痕线过深;③压痕凹轮太深不圆滑;④压线调节装置失灵;⑤纸板过于。
解决方法:①对面纸喷蒸汽,增大涂胶量并适当提高烘干机车速;②调浅压线;③更换压痕凹轮或打磨;④修正压线调节装置后再生产;⑤适当提高烘干机车速,关闭部分烘干机热源。
3.里面纸均破裂原因分析:①压痕太深;②纸板干脆;③纸次无韧性。
解决方法:①适当调浅压线;②提高烘干机车速;③更换瓦纸或对其喷蒸汽。
二、压线折痕凹凸不平且深浅不均原因分析:①压线太浅;②压线调节装置失灵;③压线轮变形;④压线凸轮磨损严重,生产中未考虑磨损程度,仍按常规操作。
解决方法:①调深压线至里面纸不破裂且折后压线清晰平直为宜;②校正维修压线调节装置至正常;③更换压线轮;④视压线程度适度深调。
三、压线折后面纸破裂原因分析:①面纸质次;②烘干机车速过慢,纸板脱水严重,面纸失去韧性。
解决分析:①更换面纸;②提高烘干机车速。
四、纸板成型后断裂原因分析:①瓦纸质次;②纸板过分干燥;③成型工序设备调节不当;④压线太浅,瓦楞未压扁或成型后折叠摇盖时高强瓦楞将面纸撑破,瓦楞随之断裂。
解决方法:①更换瓦纸;②保证纸板含水量在10±3左右;③注意成形各工序的设备调节并调至最佳状态;④烘干机加速并加大涂胶量,压线调深。
五、纵切毛边原因分析:①分纸刀已钝或刀刃有缺口;②上下刀咬合过深;③上下刀之间有间隙。
解决方法:①打磨或更换新刀;②调节上下刀重合至最佳状态;③将上下两刀靠紧,用手转动刀轮,灵活不伤刀为宜。
六、横切纸板拖尾原因分析:①横刀已钝;②横切刀上下两片咬合不正,纸板切不断的部位在机械力作用下带起撕裂的面瓦纸;③横切机瞬时加速调节不当,引起阻纸。
瓦楞纸板常见质量问题和产生原因及解决办法

修正瓦楞辊的贴合间隙 清理瓦楞表面异物
瓦楞辊贴合间隙大
• 修正瓦楞辊的贴合间隙
瓦画辊贴合间隙不平衡 •
导纸板位置不正、磨损或带
脏
瓦楞原纸含水水均衡
•
瓦楞原纸的张力太小
•
检查并修正或更换导纸 板
加大予热包角 适当调整张力控制
瓦楞纸板常见质量问题和产生原因及 解决办法
质量问题
平行度
• 瓦楞辊表面带脏
• 清理瓦楞辊,保持干净
• 导纸板位置不正,、带脏或磨损 • 检查、修正、清理或更换导
纸板
• 涂胶辊、浮动辊间隙不当
• 调整二者的贴合间隙
• 粘合剂质量不好
• 检查并重新制作粘合剂
• 瓦楞原纸含水不均衡张力小 • 适当予热并加大张力控制
• 过纸天桥张力不均衡
瓦楞纸板常见质量问题和产生原因及 解决办法
1. 面纸予热包角太大 2. 里纸予热包角太小 3. 过纸天桥堆积过多 4. 单面机涂胶量过大
5.涂胶仙涂胶量偏少
6.车速太低
7.双面机热板温度高
8.重量辊施加压力过大
解决办法
• 减少包角、降低予热 • 增大包角、加强予热 • 减少过纸天桥的堆积 • 适当控制单面机的着胶
量 • 适当增大涂胶机的着胶
7.双面机热板温度高 8.重量辊施加压力过大
解决办法
• 减少包角、降低予热
• 增大包角、加强予热 • 减少过纸天桥的堆积 • 适当控制单面机的着胶
量 • 适当增大涂胶机的着胶
量 • 根据实际运行质量,适
当提高车速
• 提高车速或人为降低热 板
• 适当投放重量辊
PPT文档演模板
瓦楞纸板常见质量问题和产生原因及 解决办法
瓦楞纸箱缺陷及产生原因

5
1
原纸 原纸纸色差异
5
1
1
1:水墨上机时混进太 多水,成膜效果差 2:送出的水墨粘度 低,成膜效果差
1:水墨上机时操作员准确判定水排干 净后才将水墨进入循环 2:加新墨提高粘度
5
1:水墨快干度没有按 需要调整
1:按季节调整水墨干燥速度: 2:生产时按需要在机上调整 3:调整生产速度改善
1:趁纸板热时生产,提高水墨干燥速
制作色卡严格按标准色对照,符合要求 才可使用
印刷 样箱保存不当
5
3
印刷 油墨号错误
5
0
1:样箱未避光保存
1:不用样箱用色卡 2:样箱避光保存
0
1:未认真对照号码拿 1:按指定的标准颜色号码对照取
墨
墨:2:首检对色
检测 设备
检测光源问题
5
0
色差
印刷 印刷速度不适合 5
1
0 1:非标准光源
用标准光源
1:印刷时速度不稳 1:用稳定速度和固定粘度生产
油墨原因
1
0
0
印刷
纸屑、灰尘等异 物
1
6
6
1:纸板线横切刀及飞 边刀不利产生纸尘 2: 纸板边沿有纸屑 3:没有及时擦版
1:定期检查和保养横切刀及飞边刀 2:生产纸板时发现纸屑多影响印刷, 通知磨刀或换刀. 3:印刷机生产时发现纸屑及时擦板
露白
缺墨
1
1
1:水墨管堵塞上不上
墨
1:停机及时清洗管道,定期清理水墨
时调整水墨
首检
1:操作员未按标准要
印刷
调机不良品未剔 除
5
3
15
求隔离调机品 2:操作员没有养成规
瓦楞纸板出现变形现象的原因和解决方法
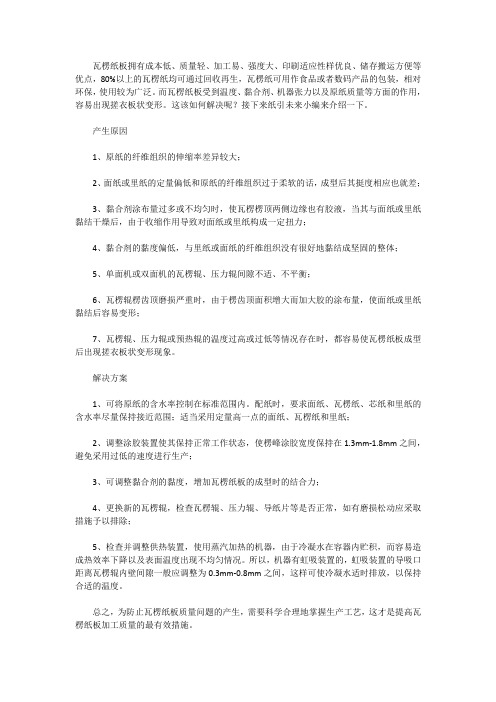
瓦楞纸板拥有成本低、质量轻、加工易、强度大、印刷适应性样优良、储存搬运方便等优点,80%以上的瓦楞纸均可通过回收再生,瓦楞纸可用作食品或者数码产品的包装,相对环保,使用较为广泛。
而瓦楞纸板受到温度、黏合剂、机器张力以及原纸质量等方面的作用,容易出现搓衣板状变形。
这该如何解决呢?接下来纸引未来小编来介绍一下。
产生原因1、原纸的纤维组织的伸缩率差异较大;2、面纸或里纸的定量偏低和原纸的纤维组织过于柔软的话,成型后其挺度相应也就差;3、黏合剂涂布量过多或不均匀时,使瓦楞楞顶两侧边缘也有胶液,当其与面纸或里纸黏结干燥后,由于收缩作用导致对面纸或里纸构成一定扭力;4、黏合剂的黏度偏低,与里纸或面纸的纤维组织没有很好地黏结成坚固的整体;5、单面机或双面机的瓦楞辊、压力辊间隙不适、不平衡;6、瓦楞辊楞齿顶磨损严重时,由于楞齿顶面积增大而加大胶的涂布量,使面纸或里纸黏结后容易变形;7、瓦楞辊、压力辊或预热辊的温度过高或过低等情况存在时,都容易使瓦楞纸板成型后出现搓衣板状变形现象。
解决方案1、可将原纸的含水率控制在标准范围内。
配纸时,要求面纸、瓦楞纸、芯纸和里纸的含水率尽量保持接近范围;适当采用定量高一点的面纸、瓦楞纸和里纸;2、调整涂胶装置使其保持正常工作状态,使楞峰涂胶宽度保持在1.3mm-1.8mm之间,避免采用过低的速度进行生产;3、可调整黏合剂的黏度,增加瓦楞纸板的成型时的结合力;4、更换新的瓦楞辊,检查瓦楞辊、压力辊、导纸片等是否正常,如有磨损松动应采取措施予以排除;5、检查并调整供热装置,使用蒸汽加热的机器,由于冷凝水在容器内贮积,而容易造成热效率下降以及表面温度出现不均匀情况。
所以,机器有虹吸装置的,虹吸装置的导吸口距离瓦楞辊内壁间隙一般应调整为0.3mm-0.8mm之间,这样可使冷凝水适时排放,以保持合适的温度。
总之,为防止瓦楞纸板质量问题的产生,需要科学合理地掌握生产工艺,这才是提高瓦楞纸板加工质量的最有效措施。
常见的瓦楞纸板缺陷及其解决方法

常见的瓦楞纸板缺陷及其解决方法瓦楞纸板产生质量问题的原因是多方面的,有原纸质量缺陷的因素,也有生产工艺不当的原因;有机器不良造成的,亦与操作技术的把握程度有关等等。
防止瓦楞纸板质量问题的产生,首先要注重从质量的源头上进行控制,即要加强原纸的质量检验和控制,并对生产设备进行认真的保养和维修。
生产质量源头控制好了,还要注意把握好操作技术和工艺技术关,如不同质量的原纸、不同含水率的原纸、不同生产环境条件下,单面机的生产速度若一概开快车,就很容易产生质量缺陷问题。
所以,科学合理地掌握生产工艺,也是提高瓦楞纸板加工质量的有效措施。
瓦楞纸板翘曲变形消除办法采用适量而又均匀、恒定的涂胶量;控制原纸的水分不能超标;保持适度的预热;控制瓦楞纸板过纸天桥中应保持一定的滞留量;根据原纸的水分,调整机器的生产速度;纸卷的张力要控制适度,不可过紧或过松,两边也不可存在松紧不一情况;重量辊的压力要调整保持适度;通过增大或减少预热或喷蒸汽的办法,来调整原纸水分的平衡;控制单面机或双面机生产环境保持稳定的温湿度;瓦楞辊、压力辊、活动辊和预热辊要调整保持平衡状态;对使用磨损厉害的瓦楞辊应更换新辊;切忌将含水率高低悬殊过大的瓦楞纸、面纸或里纸(箱板纸)进行配套成型加工。
瓦楞纸板出现搓衣板状变形的原因瓦楞纸板由于受到温度、黏合剂和机器张力和原纸质量等方面的作用,就容易出现搓衣板状变形。
产生原因:1、原纸的纤维组织的伸缩率差异较大;2、面纸或里纸的定量偏低和原纸的纤维组织过于柔软的话,成型后其挺度相应也就差;3、黏合剂涂布量过多或不均匀时,使瓦楞楞顶两侧边缘也有胶液,当其与面纸或里纸黏结干燥后,由于收缩作用导致对面纸或里纸构成一定扭力;4、黏合剂的黏度偏低,与里纸或面纸的纤维组织没有很好地黏结成坚固的整体;5、单面机或双面机的瓦楞辊、压力辊间隙不适、不平衡;6、瓦楞辊楞齿顶磨损严重时,由于楞齿顶面积增大而加大胶的涂布量,使面纸或里纸黏结后容易变形;7、瓦楞辊、压力辊或预热辊的温度过高或过低等情况存在时,都容易使瓦楞纸板成型后出现搓衣板状变形现象。
瓦楞纸板各种常见纸病的解决方案
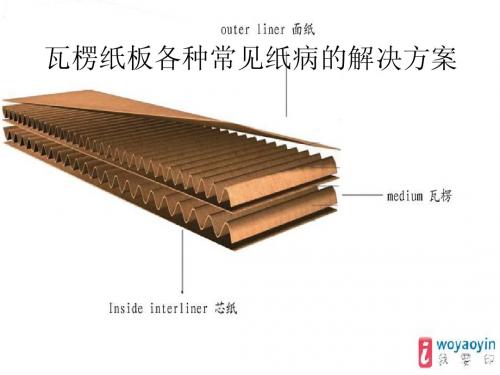
十一、纵切毛边
原因分析:①分纸刀已钝或刀刃有缺口;②上下刀咬合过深;③上下 刀之间有间隙。 解决方法:①打磨或更换新刀;②调节上下刀重合至最佳状态;③将 上下两刀靠紧,用手转动刀轮,灵活不伤刀为宜。
十二、横切纸板拖尾
原因分析:①横刀已钝;②横切刀上下两片咬合不正,纸板切不断的 部位在机械力作用下带起撕裂的面瓦纸;③横切机瞬时加速调节不当, 引起阻纸。 解决方法:①换刀、打磨;②校正下两刀的位置;③根据纸板长短, 正确调节瞬时加速。
原因分析:烘干机车速过慢,热板温度过高,白卡面纸被过分烘烤所 致,胶液碱量过重。 解决方法:提高烘干机车速,减少白卡板在烘干机内的停留时间,适 当减少胶液用碱量。
二十二、纸板里纸布满皱痕
原因分析:里纸定量低于150g,经烘干机传输带压迫即出现米粒大小 的凸凹小坑。 解决方法:更换大克重的里纸,若不影响产品质量也可不必更换。
3.里纸假粘 原因分析:①瓦楞辊温度不足;②胶量过小,温度过高;③车速缓慢, 造成粹胶;④胶液粘度不够。 解决方法:①提高单面机温度;②调整涂胶量,关闭热源待温度降至 180℃以下,160℃以上开机;③提高单面机速度;④适当增加胶液粘 度。 4.面纸假粘 原因分析:①烘干机热板温度不足;②胶液沉淀变质; 解决方法:①待温度达到胶液能糊化时开机;②更换新胶;
九、压线折后面纸破裂
原因分析:①面纸质次;②烘干机车速过慢,纸板脱水严重,面纸失 去韧性。 解决分析:①更换后断裂
原因分析:①瓦纸质次;②纸板过分干燥;③成型工序设备调节不当; ④压线太浅,瓦楞未压扁或成型后折叠摇盖时高强瓦楞将面纸撑破, 瓦楞随之断裂。 解决方法:①更换瓦纸;②保证纸板含水量在10±3左右;③注意成 形各工序的设备调节并调至最佳状态;④烘干机加速并加大涂胶量, 压线调深。
瓦楞纸板质量不良现象及原因

瓦楞纸板质量不良现象及原因露楞:指在纸面上能明显看到坑纹的楞高。
一般厂家生产的纸板的底纸均有露楞现象,此属正常,但露坑不能超过3mm且面纸不得露楞。
缺材:指纸板的宽度不够。
引起缺材的原因可能是原纸不足度、原纸经加热后缩水、错边(也叫纸边不齐)。
引起这些原因可能是驳纸未对齐、纸架走位、原纸简端面不平整。
此外,还与面纸、底纸、见坑纸在运行中的张紧度有关。
露坑:指纸面上能明显看到坑纹,由面纸或底纸缺材引起。
塌楞:指坑纸的峰楞受到超过其承受本领的压力而被压塌。
引起塌楞的原因可能是坑机运转、调机不正常(原则上每天均应试机),双面机内有杂物也与见坑纸所受的压力大小有关(如浆糊轮压不到位或压辊不平衡)。
脱坑:指纸板的各层纸黏合不良。
检验脱坑的方法有三种:(1)将纸板长度的一边靠近地面约成60°,用手掌在纸面上推动;(2)拿住纸板幅寬的两边,用适当的力向中心挤压;(3)剥离法,如黏合处的纸张纤维未受到破坏,则说明纸黏合不良。
脱坑产生的原因可能是施胶量小、异物堵塞浆糊管道、浆位调试不妥、浆糊黏度较小、受热时间与温度不合要求;纸板胀缩比例悬殊较大(如面、底、见坑);面纸、底纸、见坑纸受压不妥。
起泡:一般显现在面纸或底纸,原因有以下几方面:(1)原纸所含水分大(2)原纸的质量差(厚度不均、杂质较多);(3)施胶量不合要求(头机涂胶太少,吹风后甩坑或头机涂胶太多,抽风散热时间短,水分来不及蒸发);(4)浆糊水分蒸发慢,在纸板内形成空膜;(5)温度掌控不妥,紧要为热板;(6)压力不妥,如浆糊轮压不到位。
油污、斑点:纸板内外不得有油污,面纸不得有斑点(C纸除外)。
破损:纸板中心不能破损,纸板边沿破损以不影响外观为准。
折皱:指纸板面纸或底纸有明显皱纹,引起原因有以下几方面:(1)原纸来料折皱;(2)生产中未将纸面舒张平整;(3)张力掌控器没有掌控好面纸与底纸的张紧度:(4)面纸与底纸的张紧不协调。
弯曲:弯曲度是指纸板弯曲后水平面之间的最高高度与纸板弯曲方向的长度的百分比,分为横向弯曲(坑纹方向)和纵向弯曲(纸板长度方向)两种,一般横向弯曲情况较多。
瓦楞纸板制造产生的故障及解决(二)
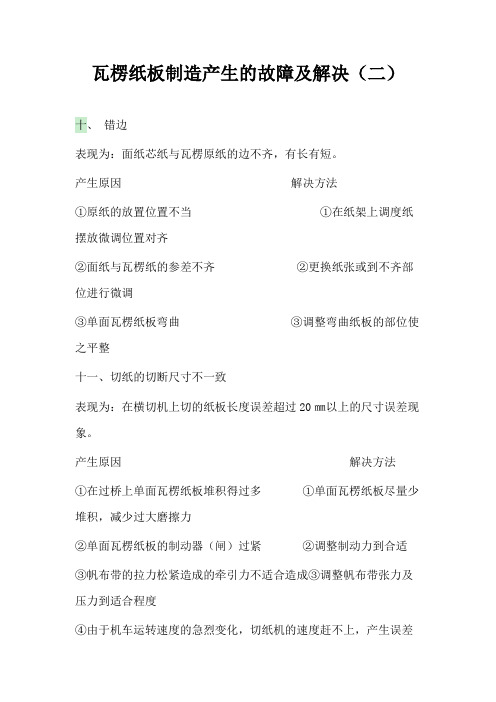
瓦楞纸板制造产生的故障及解决(二)十、错边表现为:面纸芯纸与瓦楞原纸的边不齐,有长有短。
产生原因解决方法①原纸的放置位置不当①在纸架上调度纸摆放微调位置对齐②面纸与瓦楞纸的参差不齐②更换纸张或到不齐部位进行微调③单面瓦楞纸板弯曲③调整弯曲纸板的部位使之平整十一、切纸的切断尺寸不一致表现为:在横切机上切的纸板长度误差超过20㎜以上的尺寸误差现象。
产生原因解决方法①在过桥上单面瓦楞纸板堆积得过多①单面瓦楞纸板尽量少堆积,减少过大磨擦力②单面瓦楞纸板的制动器(闸)过紧②调整制动力到合适③帆布带的拉力松紧造成的牵引力不适合造成③调整帆布带张力及压力到适合程度④由于机车运转速度的急烈变化,切纸机的速度赶不上,产生误差④尽量避免急停,短时间连续加速减速的生产方式,尽可能使车速平稳十二、翘曲1.翘曲分为:横向向下翘曲、横向向上翘曲、纵向向上翘曲、纵向向下翘曲、S形翘曲、双向翘曲2.翘曲产生的危害:①在瓦楞纸板机切断后不能自动码纸,即不能使用自动堆积机需人工反转堆积,费时费力费工。
②瓦楞纸板耐压强度下降。
③在开槽、印刷机上使用造成制造困难,易产生不良品。
④造成尺寸精确度下降,自动化程度降低。
⑤造成工作效率和损失增大。
(1)横向向下翘曲表现为:在横切断方向上,有向下弯曲的趋势。
产生原因解决方法①涂胶机涂胶量过小①适当加大涂胶机着胶量②双面机热板温度不够②增加热板温度③过纸天桥单面瓦楞纸板含水不够③适当增加过纸天桥纸板的水份和堆积,保持水分(根据当时气候而定)④三重预热器加热过量④减小预热包角⑤单面机涂胶量过小⑤增大单面机的施胶量⑥车速太快⑥适当减低车速⑦单面瓦楞纸板运行张力不够⑦调整张力控制系统,增大阻力⑧B机或面版纸水分含量过高⑧减少B机瓦纸或芯纸面纸水分,降低车速⑨单面机纸板预热水份张力与双面机面版预热水份张力不一致⑨调整系统使之水份含量和张力一致(2)横向向上翘曲表现同上,方向向上。
产生原因解决方法①面版预热包角太大①减少包角,降低预热②里纸预热包角太小②增大包角,加强预热③过纸天桥堆积过多③减少过纸天桥的堆积④单面机涂胶量过大④适当控制单面机的着胶量⑤涂胶机涂胶量偏少⑤适当增大涂胶机的着胶量⑥车速太低⑥根据实际情况及运行质量适当提高车速⑦双面机热板温度过高⑦提高车速或人为降低热低温度⑧重量辊施加压力过大⑧适当投放重量辊(3)纵向向上翘曲表现为:在纸板制造方向上,向下产生弯曲趋势。
瓦楞纸板常见故障原因分析与排除
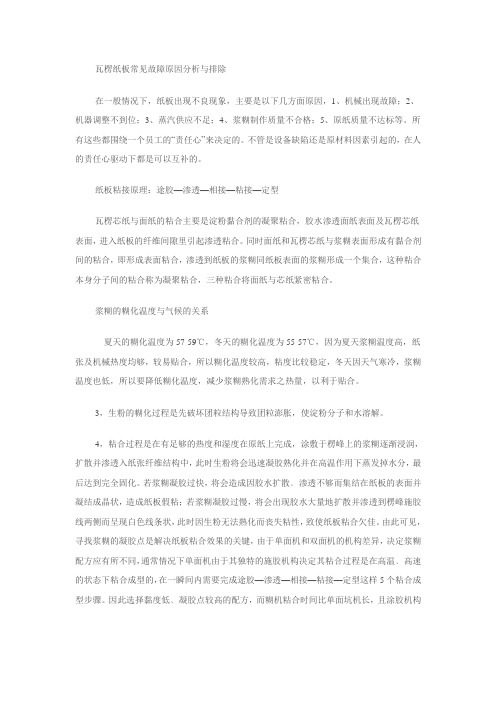
瓦楞纸板常见故障原因分析与排除在一般情况下,纸板出现不良现象,主要是以下几方面原因,1、机械出现故障;2、机器调整不到位;3、蒸汽供应不足;4、浆糊制作质量不合格;5、原纸质量不达标等。
所有这些都围绕一个员工的“责任心”来决定的。
不管是设备缺陷还是原材料因素引起的,在人的责任心驱动下都是可以互补的。
纸板粘接原理:途胶—渗透—相接—粘接—定型瓦楞芯纸与面纸的粘合主要是淀粉黏合剂的凝聚粘合,胶水渗透面纸表面及瓦楞芯纸表面,进入纸板的纤维间隙里引起渗透粘合。
同时面纸和瓦楞芯纸与浆糊表面形成有黏合剂间的粘合,即形成表面粘合,渗透到纸板的浆糊同纸板表面的浆糊形成一个集合,这种粘合本身分子间的粘合称为凝聚粘合,三种粘合将面纸与芯纸紧密粘合。
浆糊的糊化温度与气候的关系夏天的糊化温度为57-59℃,冬天的糊化温度为55-57℃,因为夏天浆糊温度高,纸张及机械热度均够,较易贴合,所以糊化温度较高,粘度比较稳定,冬天因天气寒冷,浆糊温度也低,所以要降低糊化温度,减少浆糊熟化需求之热量,以利于贴合。
3,生粉的糊化过程是先破坏团粒结构导致团粒澎胀,使淀粉分子和水溶解。
4,粘合过程是在有足够的热度和湿度在原纸上完成,涂敷于楞峰上的浆糊逐渐浸润,扩散并渗透入纸张纤维结构中,此时生粉将会迅速凝胶熟化并在高温作用下蒸发掉水分,最后达到完全固化。
若浆糊凝胶过快,将会造成因胶水扩散﹑渗透不够而集结在纸板的表面并凝结成晶状,造成纸板假粘;若浆糊凝胶过慢,将会出现胶水大量地扩散并渗透到楞峰施胶线两侧而呈现白色线条状,此时因生粉无法熟化而丧失粘性,致使纸板粘合欠佳。
由此可见,寻找浆糊的凝胶点是解决纸板粘合效果的关键,由于单面机和双面机的机构差异,决定浆糊配方应有所不同,通常情况下单面机由于其独特的施胶机构决定其粘合过程是在高温﹑高速的状态下粘合成型的,在一瞬间内需要完成途胶—渗透—相接—粘接—定型这样5个粘合成型步骤。
因此选择黏度低﹑凝胶点较高的配方,而糊机粘合时间比单面坑机长,且涂胶机构为冷态施胶,它的粘合过程是在常温下完成粘合成型,这就要求选择黏度高﹑凝胶点较低的配方,以满足纸板粘合成型的需要。
- 1、下载文档前请自行甄别文档内容的完整性,平台不提供额外的编辑、内容补充、找答案等附加服务。
- 2、"仅部分预览"的文档,不可在线预览部分如存在完整性等问题,可反馈申请退款(可完整预览的文档不适用该条件!)。
- 3、如文档侵犯您的权益,请联系客服反馈,我们会尽快为您处理(人工客服工作时间:9:00-18:30)。
車速未避開共震點
單瓦機真空吸風吸力太大當單瓦 要離開中轆輪與隔離銅叉時刮傷
糊料溢出轆輪跳動
前後彎翹
材料
人員
原因分析
機器
方法
氣油壓缸漏氣壓力不足 油壓缸,蓄壓器漏油壓力不足
短暫停機轆輪變型
吸風真空泵浦濾網未清
單瓦吸風真空泵浦磨損 瓦楞轆輪跳動電硬鉻脫
瓦楞與中轆輪分離銅叉磨損
單瓦吸風真空箱阻隔板
瓦楞轆落輪製作或研磨不良 真空吸力不足瓦楞無法
增加單瓦機上糊量 增加三重預熱面紙烘烤面積 熱板部壓輪或壓板適度降低
單瓦楞適度噴水
適度增加二次貼合機張力
生產後之變形 原紙存放不當
原紙水份差異太大 更換原紙
正反面堆疊
抄製低材質轉換為高材質 糊料配置不佳單瓦機與
及時昇溫
二次貼合機倍水率差異太大
蒸氣管路未按規定操作
下彎
材料
人員
原因分析
機器
單瓦機卻水器積水或故障 單瓦機三重預熱輪積水 或虹吸管斷裂 各轆輪軸承磨損
洗衣板現象(排骨紋)
上糊多
洗衣板現象
倒楞
理論上的厚度漢城品的厚度
(H)
(H’)
H' H C 10
H=A+B+C+D
牛皮紙薄
牛皮紙厚
倒楞原因 單面機
˙預熱輪 ˙芯紙 ˙瓦楞轆輪的加壓及平衡度不良
二次貼合機車 雙面機
˙糊輪上的平衡度,停止器,平衡調整 ˙熱板的磨損或平行度不良 ˙棉織帶的磨損 ˙重力軸的跳動 ˙輸送軸的平衡度停止氣的平衡調整度 ˙夾層輸送帶
維修
機器維修的必要性 1) 維持機器的最佳狀態 2) 維修的效果
檢查
零件更換
維修 潤滑 清潔
調整 原紙
維修
零件
人
油
工具,器具
設備
機械
減少故障 延長壽命
損耗 減
製品 量
增
操作容易
人
減少錯誤
糊
減
油
減
無公害
蒸氣
減
空氣
安全
電氣
減
質
良
防止下次工程的停機 交期確保
瓦楞紙板發生不良原因與處理
瓦楞轆輪
加壓
振動
平板製造過程不良原因處理基本的對策
水份給予
牛皮紙的噴水 芯紙的噴水(或蒸氣) 糊料
乾燥
熱
溫度(蒸氣)
接觸面積
熱板
氣膜(冷凝水)
預熱輪烘烤面積
接觸時間=速度
加壓
熱板壓板,壓輪增減
棉織帶磨損
單瓦機座輪的加壓
S 型的發生原因
原紙不良原因 機械原因
水份不均
攝取量的多少
噴水的狀態
上糊不均
糊輪、刮糊輪、中轆輪平衡度不良
單瓦機虹吸管斷裂 單瓦機轆輪磨損
方法
降低熱板溫度
增加單瓦機烘烤面積
減少二次貼合機烘烤面積 增加二次貼合機上糊量
提昇二次貼合機車速
增加三重預熱輪單瓦烘烤 減少單瓦機上糊量
熱板部壓輪或壓板適度升 高
二次貼合機面紙適度噴水
增加天橋單瓦機推積量 適度增加單瓦機張力
生產後之變型 原紙存放不當
原紙水份差異太大 更換原紙
加工不良 瑕疵
系統不具合乎不倗
機械整體震動
瓦楞轆調整不當 磨損 磨損
楞形不良 糊黏著
沾紙層油垢 角度調整不良
污損
不足 機器性能不佳
BRG 老舊 共震點運轉
蒸氣壓力不足 折損
卻水器動作不良
過 不足 位置錯誤
過 芯紙預熱輪 的轉速
變形 變動
鏈條(皮帶)鬆弛
安裝固定不良
噴水
冷卻水滯留
張力控制 攝取量 水份
轆輪,導輪表面殘渣未 清除乾淨
設備保養不良 超出機器之調整之範圍
對角蹺
材料
人員
原因分析
機器
方法
熱板表面磨損
二次貼合機糊輪壓板磨損
噴水過量
瓦楞轆輪加壓不當
瓦楞轆輪或底輪磨損 中轆輪與糊輪間隙 太小或不平行
各相關轆輪軸承磨損 熱板壓輪培林損壞
切紙機前壓輪壓力太大
上轆輪或底轆輪壓力調整不當 二次貼合機糊輪與壓板 間隙太小或不平行
吸力
中轆輪
糊輪
處理上彎下彎的對策
上彎翹
上彎
(下)增加面紙的水份 (上)增加底紙的烘烤面積
1.提高二次貼合機的車速 2.把熱板的(傾斜箱)由後面降低 3.減少面紙預熱輪烘烤面積 4.正面(下)線的捲入量的制定應降低 5.紙片的捲入量制至應提高 6.增加預熱器的捲量面積 7.減少單面機上的糊量 8.減少芯紙的噴水 9.增加貼合機的糊量
原紙複捲不良 原紙不圓(夾扁)
面紙材質差異太大
正反面堆疊 增加二次貼合機車速
教育訓練不足
單瓦機面紙張力太大
人員疏忽控制不當
前後彎翹
材料
人員
原因分析
機器
面紙預熱輪烘烤面積太大 (產生張力死角)
二次貼合機單瓦吸風導紙 架吸力不足
方法
關閉單瓦三重預熱輪ˊ 轉動電源
單瓦機面紙張不足
二次貼合機面紙張力太 吸風導紙架大吸力不足兩 側夾板太鬆
正反面轉方向堆疊
刮糊板未清洗乾淨或糊渣
單瓦機與二次貼合機刮糊板 磨損或未清洗乾淨
原紙架,接紙機張力不均
原紙張力不均
原紙水份嚴重不均 原紙存放不當
更換原紙
車速,噴水作適當調整
S 型彎翹
材料
人員
原因分析
機器
方法
單瓦機與二次貼合機距離
太長又無輸送設備
單瓦預熱輪烘烤面積太大
二次貼合機面紙張力不足
吸風導紙架吸力太大兩 關閉面紙三重預熱輪轉動電源 側夾板太緊
瓦楞轆輪研磨不良
各轆輪有軸承磨損
方法
原紙張力控制不良 原紙夾頭未夾緊
車速慢烘烤過度縮水
單瓦面紙芯紙邊未對齊 上轆輪壓力調整不當
工單修邊不足
棉織帶接頭歪斜棉織帶游動 單瓦機底輪兩側加壓不均
原紙架夾頭未夾緊空轉
棉織帶磨損打滑
原紙複捲不良
原紙嚴重縮水 原紙不圓(夾扁)
紙邊未對齊 糊料溢出轆輪跳動
人員疏忽 教育訓練不足
二次貼合轉速與棉織帶轉速差 預熱輪或瓦楞輪虹吸管斷裂
糊輪間隙設定不當
單瓦機.真空泵浦磨損吸力不足
底轆輪調整不當或中高 太高中高磨損
上轆輪與中轆輪咬合角 度調整不良
單瓦機真空風箱阻隔板 間隙調整不良
中轆輪與糊輪間隙不良 糊盤內有膠化糊渣硬塊在 糊輪底下
蒸氣溫度調整不當上糊寬度不足
糊輪與刮糊輪嚴重磨損
卻水器積水或損壞
熱板,冷卻部水平不良
原紙複捲不良
面底紙基重差異太大
正反面堆疊 教育訓練不足
人員疏忽控制不當
前後下彎
材料
人員
原因分析 機器
三重預熱輪虹吸管 斷裂或卻水器損壞
二次貼合機糊輪網目太粗
熱板部卻水器積水故障 楞形不良 楞形不良
方法
單瓦機天橋減少堆積量
減少單瓦機烘烤面積
增加二次貼合機烘烤面積 減少二次貼合機上糊量 降低二次貼合機車速
調整不當
上轆輪或底轆輪中高或太高
正常被誘導出來
各相關轆輪培林磨損跳動 瓦楞轆輪咬合調整不當
糊輪與刮糊輪不平行
單瓦真空吸風風箱兩側隔板磨 損或上下阻隔板磨損
油,氣壓調整不當
芯紙破損(交織不良) 芯紙原紙不圓(夾扁) 芯紙的不良雜質太多
芯紙水份太高 原紙複捲不良
天橋輸送帶間隙調整不當 糊料溢出轆輪跳動
車速未避開共震點
瓦楞轆輪電硬鉻脫落
單瓦二次貼合機噴水不當
各轆輪表面未保持乾淨
各轆輪軸承磨損
面底紙張力過大
未避開共震點
中底轆輪外徑差異產生線 速度不同造成共振
原紙水份過高 配料材質不符
原紙破裂強度不足
未依規定接換紙 上糊量過多
殘捲紙走完
配料材質不符 教育訓練不足
破裂強度 不足
材料
人員
原因分析
機器
方法
瓦楞轆輪楞型不良
歪邊
材料
人員
原因分析
機器
方法
刀具潤滑不良
刀具熱處理硬度不足或外徑大小
紙邊未對齊
修邊刀下夾具卡紙屑
刀具轉速太慢
導紙 磨損或歪斜
噴水過量
修邊尺寸太小或太大
磨刀座角度調整不當或磨石磨損
修邊刀下夾具未夾緊或磨損 修邊刀座培林磨損或軸 心磨損棉織帶接頭歪斜
熱板內紙板蛇行
紙板太軟
二次貼合機吸風導紙架調整不當
上中轆輪角度歪斜不平行
上糊量太多,溫和不足
上下棉絲帶有糊渣 芯紙張力調整不當
二次貼合機導紙架 張力太大
熱板壓輪或壓板高度調整不當 上下棉織帶轉速差異太大
熱板內有糊渣或異物 熱板棉織帶轉速與二次貼合糊
輪轉速差異太大
熱板壓輪或板水平不佳
單輪機輸送皮帶接頭不 良或間隙太小
芯紙材質不良 原紙外徑不圓
芯紙水份不良 芯紙基重太低
熱板壓輪,培林損坏
熱板不平整或磨損
熱板內有異物或糊渣
配料材質不符
原紙水份太高 芯紙張力不均
教育訓練不足 殘捲紙走完
未依規定接換紙 操作疏忽精神不集中
耐壓強度 不足
材料
人員
原因分析
機器
方法
瓦楞轆輪磨損
熱板磨損或壓輪水平不良
壓力計不準確棉織帶磨損
糊輪與刮糊輪真圓度不 良軸承磨損
糊輪與刮糊輪間隙不良
二次貼合機糊輪與壓板間隙 不良或彈簧疲乏壓板磨損
下彎翹
下彎
(下)使正面(下)線更乾燥 (上)增加反面(上)線的水份