FMEA--
第五版-FMEA-新版FMEA【第五版】

12345
6.FMEA时间节点
78
FMEA是一种“事前”行为,而不是“事后”行为; 基于APQP【先期产品质量策划】,识别FMEA关键节点;
APQP 各阶段
第一阶段 项目策划及定义
第二阶段
产品设计和开 发验证
第三阶段
第四阶段
第五阶段
过程设计和开发 产品和过程确 反馈、评估和
验证
在充分了 解生产概 念时,启 动 PFMEA
ML3
技术规范 批准
在用于报 价的设计 规范发布 之前,完 成 DFMEA 分析
ML4
生产规 划完成
在过程 最终过 程决策 之前完 成 PFMEA 分析
MHale Waihona Puke 5ML6量产工装, 备件和量 产设备完 成
产品和 过程批 准
ML7
项目结束, 责任移交 至批量生 产,开始 再确认
级或生产线的评估表 • FMEA方法能力以及使参与者熟悉
FMEA方法的能力 • 社交技能、能够在团队中工作 • 主持人、说服能力、组织和演讲技巧 • 管理FMEA软件文档能力
FMEA的 类型
FMEA
DFMEA PFMEA
根据产品功能进行风险分析 根据过程步骤进行风险分析
FMEA在实际的应用中还有:概念FMEA【CFMEA】、设备FMEA 【MFMEA】、监视系统与响应FMEA【FMEA-MSR】
ML0
VDA新零 件成熟度
保障
量产 开发 创新 批准
DFMEA
PFMEA
ML1
ML2
采购范围的需 求管理
确定供应 链并下订 单
在产品开发开 始之前,概念 阶段启动 FMEA计划; DFMEA到 PFMEA的信息 流; DFMEA和 PFMEA应在同 一时间段内执 行,以同时优 化产品和过程 设计
什么是FMEA(FMECA)
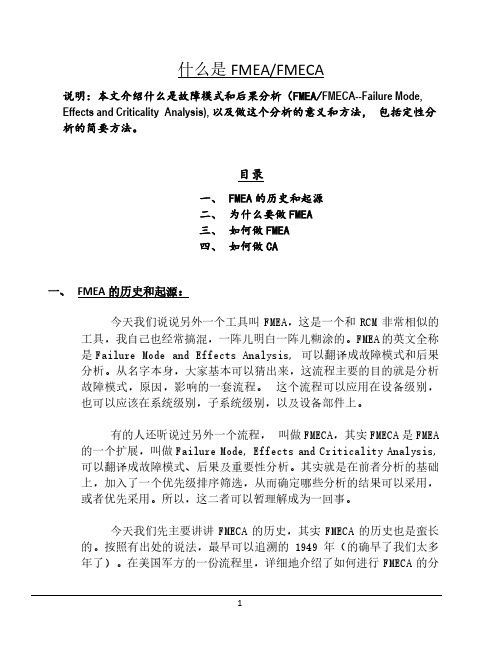
什么是FMEA/FMECA说明:本文介绍什么是故障模式和后果分析(FMEA/FMECA--Failure Mode, Effects and Criticality Analysis), 以及做这个分析的意义和方法,包括定性分析的简要方法。
目录一、FMEA的历史和起源二、为什么要做FMEA三、如何做FMEA四、如何做CA一、FMEA的历史和起源:今天我们说说另外一个工具叫FMEA,这是一个和RCM非常相似的工具,我自己也经常搞混,一阵儿明白一阵儿糊涂的。
FMEA的英文全称是Failure Mode and Effects Analysis, 可以翻译成故障模式和后果分析。
从名字本身,大家基本可以猜出来,这流程主要的目的就是分析故障模式,原因,影响的一套流程。
这个流程可以应用在设备级别,也可以应该在系统级别,子系统级别,以及设备部件上。
有的人还听说过另外一个流程,叫做FMECA,其实FMECA是FMEA 的一个扩展,叫做Failure Mode, Effects and Criticality Analysis,可以翻译成故障模式、后果及重要性分析。
其实就是在前者分析的基础上,加入了一个优先级排序筛选,从而确定哪些分析的结果可以采用,或者优先采用。
所以,这二者可以暂理解成为一回事。
今天我们先主要讲讲FMECA的历史,其实FMECA的历史也是蛮长的。
按照有出处的说法,最早可以追溯的1949年(的确早了我们太多年了)。
在美国军方的一份流程里,详细地介绍了如何进行FMECA的分析,流程编号是MIL-P-1629 (当然,这份流程后来在80年代又进行了修改,编号也变成了MIL-STD-1629A)。
在上世纪60年代初期,美国航空航天局(NASA)曾经大量使用了FMECA流程进行分析。
其中著名的阿波罗计划,维京计划,旅行者计划,麦哲伦计划,伽利略计划以及美国第一个空间站计划,都进行了FMECA分析。
我曾经拜读过1966年NASA编写的阿波罗计划FMECA实施流程,全文共37页,具体的实施方法和现如今没有太大改变。
FMEA-第五版全

课程总目标
AIAG&VDA FMEA的 基本概念以及FMEA 有效实施的基本方法 论
AIAG&VDA P FMEA有 效实施的基本方法(七 步法)
结合实际项目的 AIAG&VDA P FMEA的 实施以及后应用和动态 管理
FMEA的目的和范围
➢FMEA是一套面向团队的系统的、定性分析方法,目的: 评估产品/过程中失效的潜在技术风险 分析失效的起因和影响 记录预防和探测措施 针对降低风险的措施提出建议 FMEA仅用于分析计划风险,从而减少失效、提高产品和过程的安全性。
项目确定
分析范围可视 化
产品和过程的 功能可视化
建立失效链
为失效定制现有和/或计划 的控制措施和评级
项目规划、 目的、时间 安排、团队 、任务和工 具
FMEA分析中 包括什么, 不包括什么
DFEMA结构树或 等效的方法、 框图、边界图 、数字建模实 体部件;PFMEA 结构树或等效 的方法、过程 流程图;
项目确定
分析范围可视 化
产品和过程的 功能可视化
建立失效链
为失效定制现有 和/或计划的控制
措施和评级
识别降低风险 的必要措施
对降低风险的 措施进行固化
AIAG&VDA FMEA开发七步法
第1步 策划准备
第2步 结构分析
第3步 功能分析
第4步 失效分析
第5步 风险分析
第6步
改进优 化
第7步
结果文件化
AIAG&VDA FMEA概述
FMEA的定义
FMEA:潜在失效模式及后果分析 (Potential Failure Mode and Effects Analysis) FMEA是一种系统化的过程活动; 1.针对产品(系统、子系统、零件)或制造过程; 2.分析潜在失效原因、失效模式及失效后果; 3.识别现行的控制措施; 4.风险评价; 5.按行动优先级,制定改进措施并完成验证。
FMA与FMEA区别分类
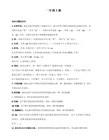
AFMEA(应用FMEA)
FMEA的发展史
60年代中期: 开始于航天业(阿波罗计划). 最初多少起了凈室文件的作用.
1974年: 美海军制定船上设备的标准, Mil-Std-1625(船)“实行船上设备失效模式及后果分析的程序”, FMEA第一次有机会进入军用品供货商界;
1994年: FMEA成为QS-9000证书获得的不可缺少的一部分. QS-9000是一个自发性项目, 是由美国三大汽车公司(克莱斯勒、福特及通用)组成的供货商质量要求工作队制定的.
1996年: 美FDA GMP (如今的质量体系规定)更新后, 结合设计控制及规定作风险分析, 如FMEA .
FMEA与 FMA之区别
FMA-失效模式分析的概念和定义:
失效模式分析(Failure Mode Analysis:简称FMA):指用来分析当前和以往过程的失效模式数据,以防止这些失效模式将来再发生的正式的结构化的程序。
关键词: 失效-已实际发生
100%既成事实
集中于: 诊断-处理已知问题
1990年: 美汽油协会建议将FMEA溶于设计之中(ANSI Z21.64 and Z21.47). 美铁道业建议用FMEA来提高火车车厢的安全性.
1991年: ISO9000系列改版后建议用FMEA来提高产品及过程的设计.
1993年: 美健康与人类服务部的FDA(食品与药品管理局)计划将目前的GMP利用可靠性工具改变成综合性的研发文件, 如FMEA及FTA, 来提高产品安全性及客户的保护.
1976年: 美国国防部采用FMEA来作为领导军队服务的研发, 及后勤工作的标准;
70年代未: 汽车业开始使用FMEA来作为危险性分析的工具, 以检讨目前市场上的汽车. 后期, 作为增强设计检讨活动的工具, 开始用列表形式.
FMEA-1
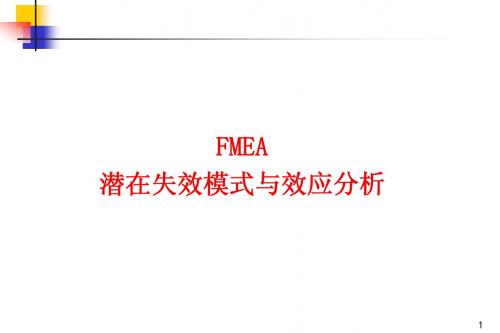
26
FMEA的开发:基本表格填写
标准: 对产品影响的严重度 (对顾客的影响) 潜在失效模式影响了汽车的安全运行:或者包含不 符合政府法律法规的情形,失效发生时无预警。 不符合安全性 或者法规要求 潜在失效模式影响了汽车的安全运行:或者包含不 符合政府法律法规的情形,失效发生时无预警。 标准: 对过程影响的严重度 (对制造/装配的影响) 会使操作员身处危险(机械或装配),失效 发生时无预警。 会使操作员身处危险(机械或装配),失效 发生时有预警。
7
b.定 义 范 围
范围建立起FMEA分析的边界,它根据FMEA的类型(即:系统、子 系统或零部件)来界定,明确了应包括的和不应包括的内容。在 开始FMEA之前,必须清楚地明白需要评估的究竟是什么。在分析 过程中,明确范围之外不包括的,和范围内应包括的都同样重要。 过程起始之初,就需要建立一个范围,来确保一致的方向和关注 点。 下面内容可以帮助小组界定FMEA范围:
2
1、何谓FMEA
FMEA是一组系统化的活动,其目的是:
发现、评价产品/过程中潜在的失效及其后 果。 找到能够避免或减少这些潜在失效发生的措 施。 书面总结上述过程。
它是对设计(产品/过程)过程的完善,以 明确什么样的设计才能满足顾客要求。
3
1、何谓FMEA
FMEA 思考方法
哪些原因可能 分析 现行预计的产品/过程 分析 对顾客或下 可能产生的失效模式 工程的影响 造成这个失效模式
最终顾客:坐垫松动,有噪音。 制造和装配:由于受影响的部分 ,因而进行额外挑选和返工 最终顾客:由于螺钉断裂导致座 垫松动,有噪音。 制造和装配:由于受影响的部分 ,因而进行额外挑选和返工 最终顾客:由于螺钉逐渐松动导 致座垫松动,有噪音。制造和装 配:由于受影响的部分,因而进 行额外挑选和返工 25
FMEA学习笔记
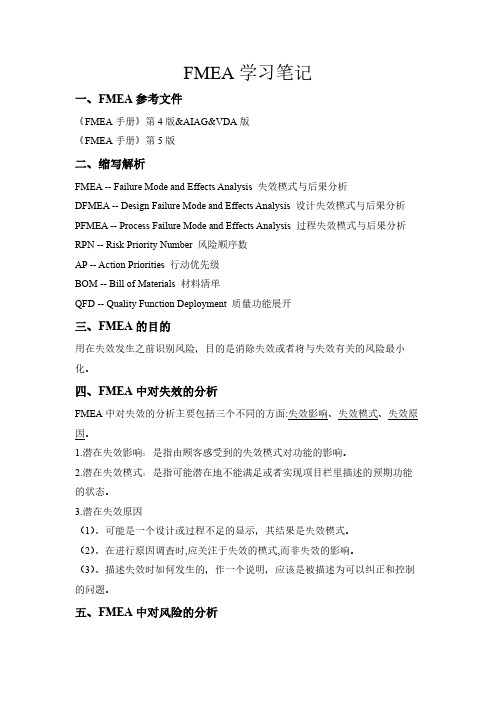
FMEA学习笔记一、FMEA参考文件《FMEA手册》第4版&AIAG&VDA版《FMEA手册》第5版二、缩写解析FMEA -- Failure Mode and Effects Analysis 失效模式与后果分析DFMEA -- Design Failure Mode and Effects Analysis 设计失效模式与后果分析PFMEA -- Process Failure Mode and Effects Analysis 过程失效模式与后果分析RPN -- Risk Priority Number 风险顺序数AP -- Action Priorities 行动优先级BOM -- Bill of Materials 材料清单QFD -- Quality Function Deployment 质量功能展开三、FMEA的目的用在失效发生之前识别风险,目的是消除失效或者将与失效有关的风险最小化。
四、FMEA中对失效的分析FMEA中对失效的分析主要包括三个不同的方面:失效影响、失效模式、失效原因。
1.潜在失效影响:是指由顾客感受到的失效模式对功能的影响。
2.潜在失效模式:是指可能潜在地不能满足或者实现项目栏里描述的预期功能的状态。
3.潜在失效原因(1)、可能是一个设计或过程不足的显示,其结果是失效模式。
(2)、在进行原因调查时,应关注于失效的模式,而非失效的影响。
(3)、描述失效时如何发生的,作一个说明,应该是被描述为可以纠正和控制的问题。
五、FMEA中对风险的分析FMEA中对风险分析是通过Severity (S) 严重度、Occurrence(O)发生频度和Detection(D)探测度来估计风险,并对需要采取的措施进行优先排序。
1.严重度(S):代表失效影响(后果)的严重程度。
评估失效对顾客影响的等级。
评分标准:按最严重失效影响评级。
2.发生度(O):表示失效原因发生度。
FEMA的定义及表头的填写方法及简介
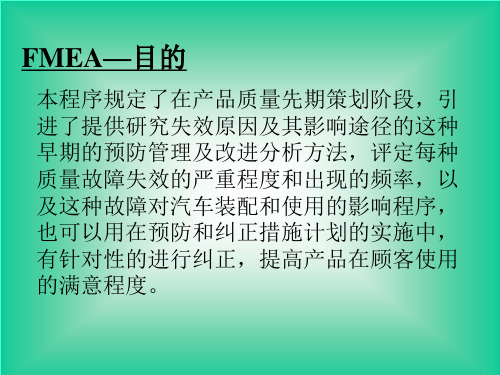
PFMEA —表头 表头
•关键日期(E):初次FMEA预定完成的日期。不 应超过计划开始生产的日期。 注:对于供方,初始的提交不应超过顾客要求的 PPAP的提交日期。 •FMEA日期(F):编制FMEA原始稿的日期及最新 修订的日期。 •核心小组(G):列出有权确定和/或执行任务的责 任部门和个人姓名。
PFMEA —格式 格式
潜在失效模式及后果分析
(PFMEA) )
项目名称:(B) 过程名称/产品型号(名称) :(D) 核心小组: (G) 过 程 潜 潜 严 级 潜 功能/ 在 在 重 别 在 要求 失 失 度 失 效 效 数 效 模 后 S 的 式 果 起 因 / 机 理 过程责任部门:(C) 关键日期:(E) 现 行 预 防 过 程 控 制 频 度 O 现 行 探 测 过 程 控 制 不 易 探 测 度 D 风 险 顺 序 数 R.P. N FMEA 编号: (A) 页码:第 页 共 页 编制:(H) 编制日期:(F) 修订日期:(F) 建 议 措 施 责任 部门/ 目标 完成 时 间 采 取 的 措 施 严 重 度 数 S 频 度 数 O 不 易 探 测 度 数 D 风 险 顺 序 数 R.P. N
度、不易探测度并计算RPN值。
•所有纠正后的RPN值都要复查,必要时应考虑
进一步的措施,并重复后面的步骤。
•负责PFMEA的人员应确保所有的纠正措施已实 施并得到落实。 •PFMEA是一个动态的过程。
PFMEA —频度(O)(g) 频度( ) 频度 •频度---是失效要因发生的可能性
•频度的分级着重在其含义,而不在数值。 •频度分1--10级,其中10级发生的频率最高。 •只有导致相应的失效模式发生,才考虑频度分级。 •建议评价准则: 在评价准则和排序系统上小组的意见应该一致并连续使 用。
FMEA--进阶篇
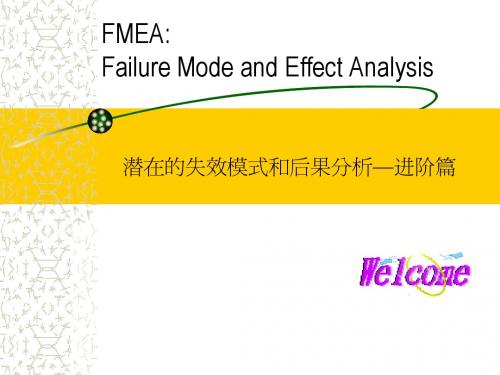
- 4
- 5
- 6
- 7
- 8
- 9
- 10
FMEA: Failure Mode and Effect Analysis
潜在的失效模式和后果分析—进阶篇
FMEA:一个用以达成以下目的的方法 :
1、确定产品或过程失败的模式; 2、估计造成失效的原因和风险; 3、确定应对哪些问题首先采取措施; 4、评估目前的设计或过程控制以防止失效的发生; 5、帮助采取预防措施,以改善产品或过程的质量、可 靠性和安全性; 6、提高客户满意度; 7、缩短产品开发时间,降低开发成本; 8、记录和跟踪减低风险的措施; 9、明确潜在的危险。
- 2
FMEA的类型 假设、分析与预防 的类型---假设 的类型 假设、
1、系统FMEA:在产品概念形成和设计的初期,分析系统。 集中于分析系统功能中可能存在的失效模式; 2、过程FMEA; 3 3、设计FMEA:侧重于产品的功能; FMEA 4、服务FMEA; 5、软件FMEA。
- 3
FMEA的前期工作 的前期工作
- 26
FMEA
谢谢! 谢谢!
A
THANKS!
P FMEA
C
D
- 27
2、分支不清晰: 1)、一个失效模式可能有多个失效后果,只须将所有的 后果列在一起,不必分支; 2)、一个失效模式可能有多个失效机理,不同的机理下 失效发生的频率不同,需要按机理分支; 3)、针对一个失效机理有多个现行的控制方法,不同的 方法下的探测难度、控制效果不同,需要按现行控制 方法分支。
五大工具之FMEA

--汽车行业五大工具之FMEA--潜在失效模式及后果分析预防作用经验库FMEA 的作用质量是检验出来的质量是生产出来的质量是规划出来的检验部门生产\制造部门设计\规划部门质量意识三层次2. FMEA 成功的条件适时性:在“时间之窗”关闭之前+小组的努力:集体的智慧工作组组长/ 主持人主要职责:*成立跨部门的工作小组筹措基本设施和资料*对项目的期限、结果及进度负责调动小组成员的工作积极性*对采取的措施进行跟踪*确保FMEA 文件的现实性FMEA的跟踪-验证措施有效性•采取有效的预防/纠正措施并对这些措施加以适当的跟踪。
•如果没有积极有效的预防/纠正措施,其价值将是非常有限的。
•责任工程师负责确保所有的建议措施都得到实施或充分强调。
FMEA是动态文件始终反应最新水平以及最近的相关措施,包括开始生产以后发生的措施。
产品系统FMEA系统FMEA 部件FMEA 子系统FMEA 过程系统FMEA产品子系统FMEA 过程子系统FMEA设计FMEA过程FMEA系统FMEA –实施步骤风险评价缺陷分析系统单元与系统结构功能与功能结构第一步第二步第四步第三步第五步分解输入、输出、内部功能失效模式RPN 值采取措施优化FMEA 的种类系统-FMEA研究的是系统部件、模块之间的接口关系和相互作用,为避免产生系统上的设计缺陷。
设计-FMEA研究的是原件、部件的设计,涉及:设计、原材料选择、(加工和装配)。
过程-FMEA研究生产过程的策划,为避免策划、加工、装配中的缺陷,涉及:人、机器、材料、环境、工装模具和方法。
燃烧室活塞连杆活塞环活塞销气缸•Kolbenringe Dichtet der Kolben richtig zum Zylinder ab?•活塞活塞与气缸的间隙如何?•Pleul Ist das Pleul in jeder Lage im Package genügend Freigang •Zylinder Kann der Bolzen zur Zylinderwand hin wandern und ihn beschädigen?•Kolbenbolzen Kann der Kolbenbolzen zwischen Kolben und Zylinder abscheren?Bauteil im System betrachtet 系统FMEA 设计FMEA Bauteil konstruktiv betrachtet •活塞环Hält das Material den Dichtan-forderungen (z.B. Temp.) stand •活塞尺寸和材料是否满足间隙的需求?•连杆Ist die Pleulform den Anforder-ungen entsprechend konzipiert?•气缸Kann die gewünschte Oberflächengüte erreicht werden?•活塞销Ist das Material härt-oder vergütbar?Herstellung betrachtet•Kolbenringe Kann der Kolbenring …undicht“ montiert werden?•活塞活塞销能否被装错?•Kolbenbolzen Kann man den Kolben beim Ein-bauen des Bolzens beschädigen?过程FMEA•Pleul Ist es einem aus einer anderen Baureihe verwechselbar?•Zylinder Ist die Toleranz bei der Herstellung einhaltbar?二、设计FMEA设计FMEA是由负责设计的工程师/小组主要采用的一种分析技术,用以最大限度地保证各种潜在的失效模式及其相关的起因/机理已得到充分的考虑和说明。
FMEA

验收 acceptance
使用 In use
FMEA的益处和质量杠杆
时间线 计划和定义
产品设计 100:1
产品设计 和开发
过程设计 10:1
回收:效益
生产 1:1
制造过程设计 和开发 产品和过程 确认
用户 1:10
效益
产品
企业的产品开发周期的回收效益。计划越早,就会获得越大的回收效益
FMEA是什么?
顾客、项目主管、总负责人、市场或顾客服务机构、安全、制 造与装配、包装、物流、材料
顾客、项目主管、总负责人、市场或顾客服务机构、安全、制 造与装配、包装、物流、材料
顾客、制造与装配、包装、物流、材料、质量、可靠性、工程 分析、设备制造商、维护
顾客、制造与装配、包装、物流、材料、质量、可靠性、工程 分析、统计分析、设备制造商、维护
2.10、FMEA-方法论—建议措施和结果
建议措施的意图是降低综合风险和失效模式发生的可能性。建议措施 阐述严重度、发生率和探测度降低。 以下的应用可确保适当措施的采取,包括不局限于: ●确保包含可靠性在内的设计要求得以达成; ●评审工程图纸和规范; ● 确定在装配/制造过程的组织,和, ● 评审相关FMEAs,控制计划和操作指导书 完成建议措施的职责和时间应该予以记录。 一旦措施完成和获得成果,更新的严重度、发生率和探测度也应予以 记录。
潜在后果的确定包括失效的结果、严重度或这些后 果的严重性分析
2.7、FMEA-方法论—识别潜在要因
失效的潜在要因应按失效为何发生的迹象来确定,按照 可纠正或可控制的情形来描述。失效的潜在要因可能是设 计弱点的一种迹象,其后果是失效模式。
在要因和失效模式之间有一种直接关联(也即是: 要因发生,那么失效模式发生)。用充分的细节识别失效 模式的根本要因,能识别适当的控制和措施计划得到验证。 如果有多种要因,每一个要因都应进行单独分析。
FMEA-日版

失效模式效应分析(评价方式)
RPN评价:
1. 依RPN风险优先数值高低采取适当改善措施 2. 侦测性(Detection)或严重性(Severity)任
一项目数值在 8 以上纵使RPN不高仍需采取适 当改善措施 3. 若RPN值均为低数值,此时应则采取持续不断 改善措施
设计失效模式效应分析 (DFMEA)
DFMEA 设计图面规格 材料规格 材料表(BOM) 设计审查 设计验证 设备、工制模 具规划 量测设备规划 原型品管制计划
制程设计与 开发验证
制造流程图
PFMEA 量试管制计划 作业指导书 包装规范 制程能力研究 量测系统计划 可靠度计划
产品与 制程验收
试作检讨 制程能力分析 量测系统分析 可靠度分析 包装评价 量产管制计划
DRAWING •图面设计绘制 •ES规格订定 •材料规格订定
生产模具规划 (DRAWING)
制造流程图 •作业流程 •作业内容 •作业功能 •验明及研订
量试管制计划
检验标准书研定
原型品管制计划
原型品验证 产品规格确认
量、检、测 试设备变异 分析及对策
量
作业标准书研定
量试检讨
量
试
初期制程能力分析
Process FMEA 对策验证及修订
设计工程师应负责确认各项改正行动均经完成 或均经通知负责人确实执行
为一系统化对产品失效的分析方法,用以 评估新产品在设计时,可能缺点的发生机 率,及其发生后对顾客造成的影响。并且 针 对 高 风 险 ( RPN Risk Priority Number)项目,在设计前先评估其对产 品之影响,俾能订定适当的产品规格。
FMEA与质量规划之相关性
客户期望及要求 制造期望及要求
FMEA-培训

2. FMEA 成 功 的 条 件
适时性:在“时间之窗”关闭之
前+
小组的努力:集体的智慧
prepared by jiajianxin, Not copy
9
without permission.
适时性
成功实施FMEA项目 的最重要因素之一
FMEA是预防性的 不是反应性的
应当尽量避免失效 而不是等着顾客提出申诉
如果没有积极有效的预防/纠正措施,其价值 将是非常有限的。
责任工程师负责确保所有的建议措施都得到 实施或充分强调。
FMEA是动态文件
始终反应最新水平以及最近的相关措施,包括 开始生产以后发生的措施。
prepared by jiajianxin, Not copy
19
without permission.
4
without permission.
FMEA的作用
预防作用 经验库
质 量 质量是规划出来的 意 识 质量是生产出来的 三 层 质量是检验出来的 次
设计\规划部门 生产\制造部门
检验部门
prepared by jiajianxin, Not copy
5
without permission.
FMEA的起源
• 六十年代中期美国航天工业(NASA) 的一项技术革新。
• 在美国质量控制协会汽车部和汽车 工业集团主持下,克莱斯勒、福特 和通用汽车公司对其各自有关 FMEA的参考手册、程序、报告格 式和技术术语进行标准化处理,形 成统一的标准。
prepared by jiajianxin, Not copy
6
部件FMEA
设计FMEA 过程FMEA
prepared by jiajianxin, Not copy
5.4-相关技术---FMEA简介
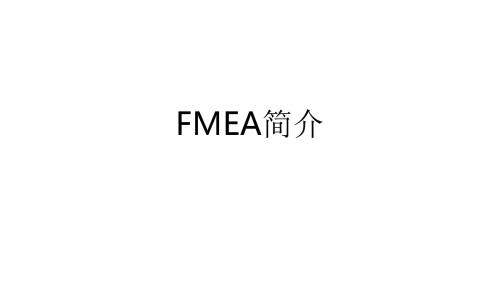
类型
• SFMEA---对产品开发、过程策划综合评估,通过系统、子系统不 同层次展开,自上而下逐级分析,更注重整体性、逻辑性; • DFMEA---对设计输出评估、识别和消除产品及每一个零部件的设 计缺陷; • PFMEA---对工艺流程的评估、识别和消除制造/服务过程中每一环 节的潜在隐
时间
对团队的影响
FMEA是企业内的一项重要活动,涉及整个产品的实现过程 FMEA需要有足够的资源 明确FMEA的职责 实施FMEA全面培训,包括:管理者、使用者、供方、推动者
基本架构
被分析的产品或过程的功能、要求和输出 当功能要求不符时的失效模式 失效模式的后果和结果 失效模式的潜在起因 针对失效模式的起因所采取的行动和控制手段 防止失效模式再发生的措施
20世纪60年代,美国的航天工业首次使用FMEA的概念和方法; 20世纪70年代,美国的海军和国防部相继采用并推广FMEA技术, 并制定标准; 20实际70年代后期,美国汽车工业界引入FMEA技术,作为设计评 审的一种工具; 1994年,美国汽车工程师学会SAE发布SAEJ1739—潜在失效模式及 后果分析标准;
何时使用FMEA
1)新设计、新技术或新过程。FMEA的范围是全部设计、技术和过 程; 2)对现有设计和过程的修改; 3)将现有的设计或过程用于新的环境、场所和应用
FMEA目的
帮助预防问题发生 识别和分析风险 确定关键特性与重要特性 持续改进 将全部过程形成文件
FMEA是预防风险,而不是被动事后处理问题
DFMEA
输出 特殊特性的确认 设计验证计划DVP PFMEA
编制 DVP
设计验证计划
TS16949五大手册
前沿
宇宙万物都是一个过程:生命周期
FMEA 手册-第三版
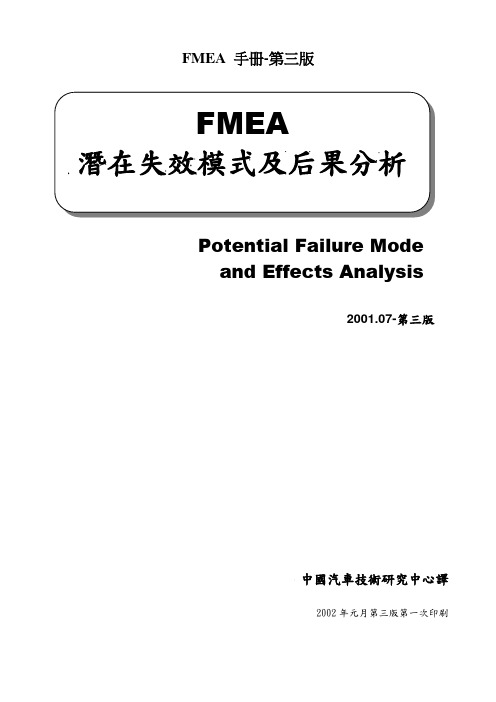
FMEA 手册-第三版Potential Failure Mode and Effects Analysis2001.07-第三版中國汽車技術研究中心譯2002年元月第三版第一次印刷目錄概要----------------------------------------------------------------------------------------------------頁碼概述-----------------------------------------------------------------------------------------------------1什麼是FMEA--------------------------------------------------------------------------------------1手冊格式-----------------------------------------------------------------------------------------------1FMEA的實施--------------------------------------------------------------------------------------2跟蹤-----------------------------------------------------------------------------------------------------4設計FMEA-----------------------------------------------------------------------------------------7簡介------------------------------------------------------------------------------------------------------9 顧客的定義---------------------------------------------------------------------------------------------9 小組的努力---------------------------------------------------------------------------------------------9 設計FMEA的開發-----------------------------------------------------------------------------------101)FMEA編號----------------------------------------------------------------------------------------132)系統、子系統或零件部件的名稱及編號-----------------------------------------------------133)設計責任-------------------------------------------------------------------------------------------134)編制者----------------------------------------------------------------------------------------------135)車型年/項目---------------------------------------------------------------------------------------136)關鍵日期-------------------------------------------------------------------------------------------137)FMEA日期----------------------------------------------------------------------------------------138)核心小組-------------------------------------------------------------------------------------------159)項目/功能------------------------------------------------------------------------------------------1510)潛在失效模式-------------------------------------------------------------------------------------1511)潛在失效的後果----------------------------------------------------------------------------------1712)嚴重度(S) ------------------------------------------------------------------------------------------17推薦的DFMEA嚴重度評價準則-----------------------------------------------------------------1913)級別-------------------------------------------------------------------------------------------------1914)失效的潛在起因/機理----------------------------------------------------------------------------1915)頻度(O) ---------------------------------------------------------------------------------------------21推薦DFMEA頻度評價準則-----------------------------------------------------------------------2316)現行設計操纵--------------------------------------------------------------------------------------2317)控測度(D) ------------------------------------------------------------------------------------------25推薦的DFMEA控測度評價準則--------------------------------------------------------------2718)風險順序數(RPN) --------------------------------------------------------------------------------2719)建議的措施-----------------------------------------------------------------------------------------2920)建議的措施和責任--------------------------------------------------------------------------------2921)採取的措施-----------------------------------------------------------------------------------------3122)措施的結果-----------------------------------------------------------------------------------------31 跟蹤措施------------------------------------------------------------------------------------------------31 過程FMEA---------------------------------------------------------------------------------------------33 簡介------------------------------------------------------------------------------------------------------35 顧客的定義---------------------------------------------------------------------------------------------35 小組的努力---------------------------------------------------------------------------------------------35 過程FMEA的開發------------------------------------------------------------------------------------37 1)FMEA編號------------------------------------------------------------------------------------------372)項目---------------------------------------------------------------------------------------------------373)責任---------------------------------------------------------------------------------------------------394)編制者------------------------------------------------------------------------------------------------395)車型年/項目-----------------------------------------------------------------------------------------396)關鍵日期---------------------------------------------------------------------------------------------397)FMEA日期-------------------------------------------------------------------------------------------398)核心小組----------------------------------------------------------------------------------------------399)項目/功能---------------------------------------------------------------------------------------------3910)潛在失效模式----------------------------------------------------------------------------------------3911)潛在失效的後果-------------------------------------------------------------------------------------4112)嚴重度(S) ---------------------------------------------------------------------------------------------41推薦的DFMEA嚴重度評價準則--------------------------------------------------------------------4313)級別-----------------------------------------------------------------------------------------------------4514)失效的潛在起因/機理-------------------------------------------------------------------------------4515)(O) ----------------------------------------------------------------------------------------------------47推薦DFMEA頻度評價準則--------------------------------------------------------------------------4716)現行設計操纵-----------------------------------------------------------------------------------------4917)控測度(D) ---------------------------------------------------------------------------------------------51推薦的DFMEA控測度評價準則-----------------------------------------------------------------5318)風險順序數(RPN) -----------------------------------------------------------------------------------5319)建議的措施--------------------------------------------------------------------------------------------5520)建議的措施和責任-----------------------------------------------------------------------------------5721)採取的措施--------------------------------------------------------------------------------------------5722)措施的結果--------------------------------------------------------------------------------------------5723)跟蹤措施-----------------------------------------------------------------------------------------------57附錄A設計FMEA質量目標車型年/項目------------------------------------------------------------------13 B過程FMEA質量目標----------------------------------------------------------------------------------60 C設計FMEA的框圖例如-------------------------------------------------------------------------------61 D設計FMEA的標準表格(操纵欄分1欄和2欄----------------------------------------------------62 E設計FMEA例如-----------------------------------------------------------------------------------------64 F系統FMEA------------------------------------------------------------------------------------------------65 G過程FMEA的標準表格(操纵欄分1欄和2欄) ---------------------------------------------------68 H過程FMEA的標準表格(操纵欄分1欄和2欄) ---------------------------------------------------70 I帶有PPK值的頻度評價準則---------------------------------------------------------------------------71概要一.概要本手冊介紹了潛在失效模式及後果分析(FMEA)這一專題,給出了應用FMEA技術的通用指南.二.什麼FMEAFMEA能够描述為一組系統化的活動,其目的是:a)認可并評價產品/過程中的潛在失效以及該失效的後果;b)確定能夠排除或減少潛在失效發生機會的措施;c)將全部過程形成文件.FMEA是對確定設計或過程必須做哪些情况才能夠使顧客滿意這一過程的補充.三.手冊格式本參考文件介紹了兩種類型的FMEA:設計FMEA和過程FMEA.採用QS-9000或其等效文件的公司的供方應使用本手冊.FMEA小組能够使用手冊中給出的指南,但要以對於給定情況最有效的方式使用.四. FMEA的實施由於一样的工業傾向是要盡可能持續地改進產品和過程的質量,因此將FMEA作為專門的技術應用以識別并幫助最大程度地減少潛在的隱患一直是专门重要的,對車輛召回的研究結果说明,FMEA項目的全面實施可能會防止专门多召回事件的發生.成功實施FMEA項目的最重要因素之一是時間性.其含義是指〞事件發生前〞的措施,而不是〞事實出現后〞的演練.為實現最大價值,FMEA必須在產品或過程失效模式被納入到產品或過程之前進行.事先花時間专门好地完FMEA分析,能夠最容易、低成本地對產品或過程進行更换,從而最大程度地降低后期更换的危機.FMEA能夠減少或排除實施可能會帶來更大隱患的預防/糾正性更换的機會.應在所有FMEA小組間提倡交流和協作.圖1描述了進行FMEA的順序.這並不是簡單地填寫一下表格,而是明白得FMEA的過程,以便排除風險并策劃適宜的操纵方法以確保顧客滿意.在進行FMEA時有三種差不多情形,每一種都有其不同的範圍或關注重點:情形1:新設計、技術或新過程.FMEA的範圍是全部設計、技術或過程.情形2:對現有設計或過程的修改(假設對現有設計或過程已有FMEA).FMEA的範圍應集中於對設計或過程的修改、由於修改可能產生的相互影響以及現場的歷史情況.情形3:將現有的設計或過程用於新的環境、場所或應用(假設對現有設計或過程已有FMEA).FMEA的範圍是新環境或場所對現有設計或過程的影響.]雖然FMEA的編制責任通常都指派到某個人,然而FMEA的輸入應是小組努力.小組應由知識豐富的人員組成(如設計、分析/試驗、製造、裝配、服務、回收、質量及可靠性等方面有豐富經驗的工程師).FMEA由責任單位的工程師開始啟動,責任單位可能是原設備製造廠(OEM,即生產最終產品)、供方或分承包方.即使產品/過程看起來完全相同,將一個小組FMEA 的評分結果與另一個小組FMEA的評分結果進行比較也是不適宜的,因為每個小組的環境是不同的,因而各自的評分必定是不同的(也确实是說,評分是帶有主觀性的).建議根據FMEA的質量目標(見附錄A和附錄B)對FMEA文件進行評審,包括治理評審.跟蹤採取有效的預防/糾正措施對這些措施加以適當的跟蹤,對這方面的要求怎樣強調也不算過分.措施應傳遞到所有受影響的部門.一個經過徹底摸索、周密開發的FMEA,假如沒有積極有效的預防/糾正措施,其價值將是专门有限的.責任工程師負責確保所有的建議措施都得到實施或充分的強調.FMEA是動態文件,應始終反映最新水平以及最近的相關措施,包括開始生產以后發生的.責任工程師有幾種方法來確保建議的措施得到實施,包括但不限於以下幾種:a.對設計、過程及圖樣進行評審,以確保建議的措施得到實施.b.確認更换已納入到設計/裝配/製造文件中.c.以設計/過程FMEA、FMEA的专门應用以及操纵計劃進行評審.設計中潛在失效模式和後果分析(設計FMEA)簡介設計FMEA是由負責設計的工程師/小組要紧採用的一種分析技術,用以最大限度地保證各種潛在的失效模式及其相關的起因/機理已得到充分的考慮和說明.對最終的項目以及與之相關的每個系統、子系統和部件都應進行評估.FMEA以最嚴密的方式總結了設計一個部件,子系統或系統時小組的設計思想(其中包括根據以往的的經驗可能會出錯的一些項目的分析).這種系統化的方法體現了一個工程師在任何設計過程中下沉經歷的思維過程,並使之規範化和文件化.設計FMEA為設計過程提供支持,它以如下的方式降低失效(包括產生不期望的結果)的風險:‧為客觀的評價設計,包括功能要求及設計方案,提供幫助;‧評價為生、裝配、服務和回收要求所做的初步設計;‧提高潛在失效模式及其對系統和車輛運行影響已在設計和開發過程中得到考慮的可能性.‧為完整和有效的設計、開發和確認項目的策劃提供更多的信息;‧根據潛在的失效模式後果對〞顧客〞的影響,開發潛在失效模式的排序清單,從而為設計改進、開發和確認試驗/分析建立一套優先操纵系統;‧為推薦和跟蹤降低風險的措施提供一個公開的討論形式;‧為將來分析研究現場情況,評價設計的更换及開發更先進的設計提供參考(如獲得的教訓).‧顧客的定義設計FMEA中〞顧客〞的定義,不僅僅是〞最終使用者〞,而且也包括負責整車或更高一層總成設計的工程師/設計組以及負責生產、裝配和服務活動的生產/工藝工程師.小組的努力在最初的設計FMEA過程中,期望負責設計的工程師能夠直截了当地、主動地聯繫所有關部門的代表.這些專長和責任領域應包括(但不限於)裝配、製造、設計、分析/試驗、可靠性、材料、質量、服務和供方以及負責更高或更低一層次的總成或系統、子系統或部件的設計領域.FMEA應成為促進各相關部門之間相互交換意見的一種催化劑,從而推進小組協作的工作方式.除非負責的工程師有FMEA和團隊工作推進經驗,否則,有一位有經驗的FMEA 推進員來協助小組的工作是专门有益的.設計FMEA是一份動態的文件,應:‧在一個設計概念最終形成之時或之前開始;‧在產品開發的各個階段,發生更换或獲得更多的信息時,持續予以更新‧在產品加工圖樣完工之前全部完成考慮到製造/裝配需求已經包容在內,設計FMEA針對設計意圖並且假定該設計將按此意圖進行生產/裝配.製造或裝配過程中可能發生的潛在失效模式和/或其缘故/機理不需、但也可能包括在設計FMEA當中.當這些未包含在設計FMEA當中時,它們的識別、後果及操纵應包括在過程FMEA當中.設計FMEA不依靠過程操纵來克服潛在的設計缺陷,然而它的確要考慮製造/裝配過程的技術/身體的限制,例如:‧必要的拔模(斜度)‧表面處理的限制‧裝配空間/工具的可接近性‧鋼材淬硬性的限制‧公差/過程能力/性能設計FMEA還應考慮產品維護(服務)及回收的技術/身體的限制,例如: ‧工具的可靠性‧診斷能力‧材料分類符號(用於回收)‧設計FMEA的開發負責設計的工程師把握一些有益於設計FMEA準備工作的文件是有幫助的.設計FMEA從列出的設計期望做什麼和不期望做什麼的清單,即設計意圖開始.顧客的期望和需求__可通過質量功能展開(QFD)、車輛要求文件、的產品要求和/或製造/裝配/服務/回收要求等確定,應包括在內.期望特性定義的越明確越容易識別潛在的失效模式,以便採取預防/糾正措施.設計FMEA應從應所要分析的系統、子系統或零部件的框圖開始.附錄C給出了框圖的一個例如.框圖還能够批示信息、能源、力、流體等的流程.其目的是要明確向方框交付的內容(輸入),方框中完成的過程(功能)以及由方框所交付的內容(輸出).框圖說明了分析中的各項目之間的要紧關係,並建立了分析的邏輯順序.在FMEA準備工作中所有的框圖的復制件應伴隨FMEA過程.為了便於潛在的失效模式及影響後果分析的文件化,附錄D給出了設計FMEA 的空白表.設計FMEA順序1)FMEA編號填入FMEA文件編號,以便查詢.注:1-22項的舉例見表一2)系統、子系統或零件的名稱及編號注明適當的分析級別并填入被分析的系統、子系統或部件的名稱及編號.FMEA小組必須為他們特定的活動確定系統、子系統或部件的組成.劃分系統、子系統和部件的實際界限是任意的並且必須由FMEA小組來確定.下面給出了一些說明,具體例如見附錄F.系統FMEA的範圍一個系統能够看作是由各個子系統組成的.這些子系統往往是由不同的小組設計的.一些典型的系統FMEA可能包括以下系統:底盤系統、傳動系統、內飾系統等.因此,系統FMEA的焦點是要確保組成系統的各子系統間的所有接口和交互作用以及該系統與車輛其他系統和顧客的接口都要覆蓋.子系統FMEA的範圍一個子系統FMEA通常是一個大系統的一個組成部份.例如,前懸持系統是底盤系統的一個組成部份.因此,子系統FMEA的焦點确实是確保組成子系統的各個部件間的所有的接口和交互作用都要覆蓋.部件FMEA的範圍部件FMEA通常是一個以子系統的組成部份為焦點的FMEA,例如,螺杆是前懸挂(底盤系統的一個子系統)的一個部件.3)設計責任填入整車廠、部門和小組.如適用,還包括供方的名稱.4)編制者填入負責編制FMEA的工程師的姓名、電話和所在公司的名稱.5)車型年/項目填入所分析的設計將要應用和/或影響的車型/項目(如的話)6)關鍵日期填入初次FMEA應完成的時間,該日期不應超過計劃的生產設計發佈日期.7)FMEA日期填入編制FMEA原始稿的日期及最新修訂的日期.8)核心小組列出有權確定和/或執行任務的責任部門的名稱和個人的姓名(建議所有參加人員的姓名、部門、電話、地址等都應記錄在一張分發表上.)9)項目/功能填入被分析項目的名稱和其他相關信息(如編號、零件級別等).利用工程圖紙上標明的名稱并指明設計水平.在初次發佈(如在概念階段)前,應使用試驗性編號.用盡可能簡明的文字來說明被分析項目滿足設計意圖的功能,包括該系統運行環境(規定溫度、壓力、溫度範圍、設計壽命)相關的信息(度量/測量變量).假如該項目有多種功能,且有不同的失效模式,應把所有的功能單獨列出.10)潛在失效模式所謂潛在失效模式是指部件、子系統或系統有可能會未達到或不能實現項目/功能欄中所描述的預期功能的情況(如預期功能失效).這種潛在的失效模式可能會更高一級的子系統或系統的潛在失效模式的起因或者是更低一級的部件的潛在失效模式的影響後果.對於特定的項目及其功能,列出每一個潛在的失效模式.前提是這種失效可能發生,但不一定發生.推薦將對以往TGW(運行出錯)研究、疑慮、報告和小組頭腦風暴結果的回顧作為起點.只可能出現在特定的運行條件下(如熱、冷、乾燥、粉塵,等)和特定的使用條件下(如超過平均里程、不平和路面、僅在都市內行駛等)的潛在失效模式應予以考慮.典型的失效模式可包括,但不限於:裂紋變形松動泄漏粘結氧化斷裂不傳輸扭矩打滑(不能承担全部扭矩) 無支撐(結構的)支撐不足(結構的) 剛性嚙合脫離太快信號不足信號間斷無信號EMC/RFI 漂移注:潛在失效模式應該以規範化或技術術語來描述,不必與顧客察覺的現象相同.11)潛在失效的后果潛在失效的後果定義為顧客感受到的失效模式對功能的影響.要根據顧客可能發現或經歷的情況來描述失效的後果,要記住顧客既可能是內部的顧客也可能是最終用戶.假如失效模式可能影響安全性或對法規的符合性,要清晰地予以說明.失效的後果應按照所分析的具體的系統、子系統或部件來說明.還應記住不同級別的部件、子系統和系統之間存在著一種系統層次上的關係.例如,一個零件可能會斷裂,這樣會引起總成的振動、從而導致一個系統間歇性運行.系統的間歇性運行可能會造成性能的下降并最終導致顧客的不滿.分析的意圖确实是在小組所擁有的知識層次上,盡可能地預測到失效的後果.典型的失效後果可能是不限於以下情況:噪音粗糙工作不正常不起作用外觀不良異味不穩定工作減弱運行間歇熱衰變泄漏不符合法規12)嚴重度(S)嚴重度是一給定失效模式最嚴重的影響後果的級別.嚴重度是單一的FMEA 範圍內的相對定級結果.嚴重度數值的降低只有通過發改設計才能夠實現.嚴重度應以表2為導則進行估算:推薦的評價準則不組應對評定準則和分級規則達成一致意見,盡管個別產品分析可做修改.(見表2)注:不推薦修改確定為9和10的嚴重數值.嚴重度數值定級為1的失效模式不應進行進一步的人分析.注:有時,高的嚴重度定級能够通過修改設計、使之補償或減輕失效的嚴重度結果來予以減小.例如,〞癟胎〞能够減輕突然爆胎的嚴重度,〞安全帶〞能够減輕車輛碰撞的嚴重程度.13)級別本欄目可用於對那些可能需要附加的設計或過程操纵的部件、子系統枵系統的產品专门特性的分級(如關鍵、要紧、重要、重點).本欄目還可用於突出高優先度的失效模式,以便在小組認為有所幫助對部門治理者要求時進行工程評價.產品或過程专门屬特性符號及其使用服從於特定的公司規定,在本文件中不予以標準化.14)失效的潛在起因/機理所謂失效的潛在起因是指設計薄弱部份的跡象,其結果确实是失效模式.盡可能地列出每一失效模式的每一個潛在的起因和/或失效機理.起因/機理應可能簡明而全面地列出,以便有針對性地採取補救的努力.典型的失效起因可包括但不限於:規定的材料不正確設計壽命設想不足應力過大潤滑能力不足維護說明書不充分算法不正確維護說明書不當軟件規範不當表面精加工規範不當行程規範不足規定的磨擦材料不當過熱規定的公差不當典型的失效機理包括但不限於:屈服化學氧化疲勞電移材料不穩定性蠕變磨損腐蝕15)頻度(O)頻度是指某一特定的起因/機理在設計壽命內出現的可能性.描述出現的可能性的級別數具有相對意義,而不是絕對的數值,通過設計變更或設計過程變更(如設計檢查表、設計評審、設計導則)來以預防或操纵失效模式的起因/機理是可能影響頻度數降低的唯独的途徑.(見表3)潛在失效起因/機理出現頻度度評估分為1到10級.在確定此值時,需考慮以下問題:‧類似的部件、子系統或系統的維修史/現場經驗如何?‧部件是沿用先前水平的部件、子系統或系統不是與其類似?‧相對於先前水平的部件、子系統或系統變化有多明顯?‧部件是否與先前水平的部件有著全然不同?‧部件是否是全新的?‧部件的用途是否有所變化?‧環境有何變化?‧針對該用途,是否採用了工程分析(如可靠性)來估計其預期的可比較的頻度數?‧是否採用了預防性操纵的措施?應採用一致的頻度分級規則,以保持連續性.頻度數是FMEA範圍內的相對級別,它不一定反映實際出現的可能性.推薦的評價準則小組應對相互一致的評定準則和定級方法達成一致意見,盡管對個別產品分析可能作調整.(見表3)頻度應採用表3做導則來進行估算:注:級數1專用於〞极低:失效不太可能發生〞的情況.16)現行設計操纵列出已經完成或承諾要完成的預防措施、設計確認/驗證(DV)或其它活動,並且這些活動將確保設計對於所考慮的失效模式和/或起因/機理是足夠的.現行操纵是指已被或正在被同樣或類似的設計所採用那些措施(如設計評審,失效與安全設計(減壓閥),數學研究,台駕/試驗室試驗,可行性評審,樣件試驗,道路試驗,車隊試驗).小組應一直致力於設計操纵的改進;例如,在實驗室創立新的系統試驗或創立新的系統模型化運算方法等.要考慮兩種類型的設計操纵:預防:防止失效的起因/機理或失效模式出現,或者降低其出現的幾率.探測:在項目投產之前,通過分析方法或物理方法,探測出失效的起因/機理或者失效模式.假如可能,最好的途徑是先採用預防操纵.假如預防性操纵被融入設計意圖并成為一部份,它可能會影響最初的頻度定級.探測度的最初定級將以探測失效起因/機理或探測失效模式的設計操纵為基礎.對於設計操纵,本手冊中的設計FMEA表中設有兩欄(即單獨的預防操纵欄和探測操纵欄),以幫助小組清晰地區分這兩種類型的設計操纵.這可迅速而直觀地確定這兩種設計操纵均已得到考慮.最好採用這樣的兩欄表格.注:在這里的例如中,小組沒有確定任何預防操纵.這可能是因為同樣或類似的設計沒有應用過預防操纵.設計操纵假如使用單欄表格,應使用以下前綴.在所列的每一個預防操纵前加上一個字母〞P〞.在所列的每一個探測操纵前加上一個字母〞D〞.一旦確定了設計操纵,評審所有的預防措施以決定是否有需要變化的頻度數. 17)探測度(D) 探測度是與設計操纵中所列的最正确探測相關聯的定級數.探測度是一個在某一FMEA範圍內的相對級別.為了獲得一個較低的定級,通常計劃的設計操纵(如確認和/或驗證活動)必須予以改進.推薦的評價準則小組應對相互一致的評定準則和定級方法達成一致意見,盡管對個別產品分析可作調整在設計開發過程中,最好是盡中早採用探測操纵注:在確定了探測度級別之后,小組應評審頻度數定級別并確保頻度數定級仍是適宜的.探測度應用表4作為估算導則.注:級數1專用於〞幾乎确信〞的情況.19)建議的措施應第一針對高嚴重度,高RPN值和小組指定的其它的項目進行預防/糾正措施的工程評價.任何建議措施的意圖差不多上要依以下順序降低其風險級別:嚴重度,頻度和探測度.一样實踐中,不管其RPN值是多大,當嚴重度是9或10時,必須予以特別注意,以確保現行的設計操纵或預防/糾正措施針對了這種風險.在所有的已確定潛在失效模式的後果可能會最終用戶造成危害的情況下,都應考慮預防/糾正措施,以便通過排除,減弱或操纵起因來幸免失效模式的產生.在對嚴重度值為9或10的項目給予特別關注之后,小組再考慮其它的失效模式,其意圖在於降低來得度,其次頻度,再次探測度.應考慮但不限於以下措施:‧修改設計幾何尺寸和/或公差‧修改材料規範‧試驗設計(专门是存在多重或相互作用的起因時或其它解決問題的技術,和‧修改試驗計劃建議措施的要紧目的是通過改進設計,降低風險,提高顧客滿意度.只有設計更换才能導致嚴重度的降低.只有通過設計更换排除或操纵失效模式的一個或多個起因/機理才能有效地降低頻度.增加設計確認/驗證措施將僅能導致探測度值的降低.由於增加設計確認/驗證不是針對失效模式的嚴重度和頻度的,因此,該種工程措施是不太期望採用的.對於一個特定的失效模式/起因/操纵的組合,假如工程評價認為無需採用建議措施,則應在本欄內注明〞無〞.20)建議措施的責任填入每一項建議的措施的責任組織的名稱和個人的姓名以及目標完成日期.21) 採取的措施在措施實施之后,填入實際措施的簡要說明以及生效日期.22) 措施的結果在確定了以預防/糾正措施以后,估計并記錄嚴重度、頻度和探測度值的結果.計算并記錄RPN的結果.假如沒有採取任何措施,將相關欄空白即可.所有修改了的定級數值應進行評審. 假如認為有必要採取進一步措施的話,重復該項分析.焦點應永遠是持續改進.跟蹤措施負責設計的工程師應負責保證所有的建議措施已被實施或已妥善落實.FMEA 是一個動態文件,它不僅應體現最新的設計水平,而且還應體現最新的相關措施,包括開始生產后所發生的措施.負責設計的工程師可採用幾種方式來保證所關注的問題得到明確並且所建議的措施得到實施.這些方式包括但不限於以下內容:‧保證設計要求得到實現‧評審工程圖樣和規範‧確認這些已反映在裝配/生產文件之中‧評審過程FMEA和操纵計劃。
FMEA-培训

失效模式
在規定条件 下, (环境、 操作、时间 ) 不能完成既 定功能。
产品在工作范 围內 , 导致零 组件的破裂、 断裂、卡死、 損坏現象
失效
I类:不能完 成规定的功能; II 类: 产 生了 非期望的功能
13
FMEA基本要素间的关联
FMEA计划
原因 失效模式 后果
频度
探测度
严重度
风险分析和潜在的失效模式及后果分析解释 执行建议措施并验证其有效性 实施措施
系方式以及工程师的所属组织。
38
潜在失效模式及后果分析(设计FMEA)
27
DFMEA的概述
DFMEA中顾客的定义: 1)最终使用者
2)OEM组装和制造中心
3)政府法规机构
28
DFMEA实施流程
1.组织小组;
2.DFMEA功能框图;
3.列出每一个零件、部件、子系统的失效模式; 4.确定失效模式的等级(关键、重要、一般) 5.优先关注关键零件特性; 6提出改进和预防措施建议;
35
如何做DFMEA
◇ 部件FMEA的范围
部件FMEA通常是一个以子系统的组成部分为焦点的
FMEA,例如,螺杆是前悬挂(底盘系统的一个子系统) 的一个部件。
36
设计FMEA表头
设计职责(C):输入负责设计的OEM、组织、部门或小
组;适用时,输入供应商组织名称。
车型年/项目(D):输入将使用或者受分析的设计影响的预期
“早知道… …就不会” 早知道 早知道 早知道 早知道 作好防震设计 改进电力输配设计 不滥砍滥伐 作好桥梁设计 就不会 就不会 就不会 就不会 造成大楼倒塌 造成美国等国的大停电 造成泥石流 造成大桥倒塌
FMEA软件 -- IATF16949中的17条FMEA相关要求

汽车行业质量管理体系标准IATF16949提出了至少16条FMEA的相关要求。
满足这些要求会提高组织FMEA工作的成熟度,降低产品和过程的风险,降低生产成本的同时满足顾客要求。
▲在“质量管理体系及其过程”的“产品安全”章节,标准要求对产品安全相关的DFMEA和PFMEA实行特殊批准。
特殊批准需要遵循顾客要求或者组织内部流程的定义,一般由有资质的人员进行。
该项条款的目的是让特殊批准人员通过批准FMEA对安全产品的设计和生产进行风险管理。
▲在“能力”的“内部审核员能力”和“第二方审核员能力”章节,标准要求审核员了解FMEA的要求并具有待审核的产品和过程的FMEA知识。
此项条款强调了审核员的FMEA能力,通过FMEA,审核员可以了解产品或过程的实现以及风险和控制,并有可能发现产品设计、过程执行以及FMEA中的不足之处。
▲在“产品和服务的设计和开发”的“设计和开发策划”章节,标准要求FMEA的开发和评审需要使用多方论证的方法。
此项条款要求由团队进行FMEA工作,团队工作能利用群体的知识、经验、能力和智慧,最大可能地降低产品和过程的风险。
▲在“产品和服务的设计和开发”的“特殊特性”章节,标准要求PFMEA需要记录相关的特殊特性。
特殊特性是指那些一旦失效便会导致安全、法律法规或者功能影响,需要特殊管控的特性。
在PFMEA中标识特殊特性,以便策划对它们的特殊管控。
▲在“产品和服务的设计和开发”的“设计和开发输出”章节,标准要求产品和服务的设计和开发的输出应包含DFMEA。
此项条款明确了设计和开发的潜在失效分析和风险降低是设计和开发的工作之一,而不是额外工作。
▲在“产品和服务的设计和开发”的“制造过程设计输出”章节,标准要求制造过程设计的输出应包含PFMEA。
此项条款明确了制造过程的潜在失效分析和风险降低是制造过程设计的工作之一,而不是额外工作。
▲在“生产和服务提供”的“控制计划”章节,标准要求制订控制计划时应考虑FMEA的输出,当FMEA变更时,需要评审,必要时更新控制计划。
FMEA(五版)
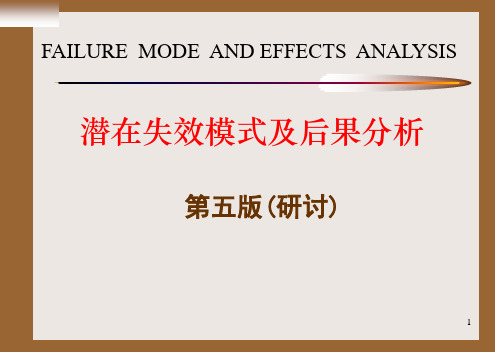
功能逐级分析:找出每个要素的功能和作用
45
46
5. 失效分析:以工步为核心进行分析
• 工步的失效分析是从产品特性和过程特性 中推断出。
• 包括: – 不合格 – 部分不合格 – 非预期的活动(操作安全隐患等) – 不必要的活动(浪费等)
IATF16949:2016 版权所有
IATF16949:2016 版权所有
step2:结构分析
DFMEA----清楚识别分析对象的内外部接口
外部接口---外部环境要求,顾客要求,生产制造,维修维护以及相关联的系 统、子系统或零部件的关联。
内部接口---系统内的子系统、零部件的相互关联。
PFMEA----依据流程图和工艺要求,重点清楚分析--过程及活动
PFMEA 的控制为:
IATF16949:2016 版权所有 27
• 过程控制当在产品到达顾客前发现缺陷! • 过程控制有三种类型:
(1) 防止原因出现或降低其出现的可能性 (2) 查明失效的原因并找出纠正措施 (3)列出现有过程控制——探测(对失效模式的 把关。
发生频率(O):是在设计寿命内由特定要因/机理将导致失效 模式发生的可能性
– 目的旨在:
A、评估产品或过程的潜在失效风险。 B、分析这些失效的原因和影响 C、记录预防和探测手段 D、建议采取措施以降低风险
3
2、FMEA发展历程
1950年,美国GRUMMAN飞机制造公司提出,飞机主操纵 系统的失效分析;
60年代初用于航天; 70年代用于三大汽车公司。 80年代被美国军方确认为军方规范(MIL-STD-1629A) 随着汽车的召回要求,现在在国内越来越重视.
move 搬运
FMEA

严重度、发生度与难检度的计分介于1~10之间
Risk Priority Number(RPN) Rankings. RPN=(S)×(O)×(D)
Process FMEA
Scope
Includes all processes from incoming material through shipping/warehousing , including subcontracted operations.
计分 1 2 3 4 5 6 7
出现于上下限以外的可能性 1/10,000 1/5,000 1/2,000 1/1,000 1/500 1/200 1/100
8 9 10
1/50 1/20 1/10+
•难检度评分表范例
列印日期:2000/4/11 难检度计分说明 可能性极小-由于性能上之不良,而被出送厂的可能性 极小。 计分 1 相关之 FMEA: 01.03/Body Closures 将有缺点之品目出厂之机率 1/10,000
FMEA实施步骤流程
任务确认 决定 分析层级 机能 方块图 可靠性 方块图
列举 故障模式 故 障 事 例
经验累积 提出 对策案 制件 FMEA表
试验报告 不良报告 顾客抱怨 列举 故障原因
选定对象
选定 故障模式ቤተ መጻሕፍቲ ባይዱ
设 计
性 能 、 精 度
基本 设计 细部 设计
子系统 解析水准 项目
系
统
系 统
子系统
组 件 图面原案
可靠性 方块图 可靠性问题点 对策案 FMEA 检讨表 故障经验 故障等级
可 可靠性点检 靠 性 设计修正﹑变更 正式图面
Bottom Up (FMEA)
- 1、下载文档前请自行甄别文档内容的完整性,平台不提供额外的编辑、内容补充、找答案等附加服务。
- 2、"仅部分预览"的文档,不可在线预览部分如存在完整性等问题,可反馈申请退款(可完整预览的文档不适用该条件!)。
- 3、如文档侵犯您的权益,请联系客服反馈,我们会尽快为您处理(人工客服工作时间:9:00-18:30)。
****过程责任部门:
*************
**********
XXX/PE XXX/QA XXX/ED XXX/PR XXX/PU
****
关键日期:
***
FMEA 编号:
**********
***
***主要联系电话:
FMEA 修订日期:填表者:
初始 FMEA 日期:
零件号
/更改水平等级零件名称/描述横向小组成员
过程潜在失效模式和后果分析(PFMEA)
样件
PPAP
生产
功能:判定产品是否符合要求
高
面和内
部出现裂纹
功能:使原料温度达到锻压要求
要求:材料温度470±10℃
080-5
位
后有飞边遗留
满
报废或客户投
诉
料
功能:将坯料锻压
成型
要求:零件外形结构、尺寸满足要求,无明显外观缺
陷
080-6
报废或客户投
诉
要求:零件外形结构、尺寸满足要求,无明显外观缺
陷
080-6
报废或客户投诉
客户抱怨
功能:将坯料锻压
成型
要求:零件外形结构、尺寸满足要求,无明显外观缺陷
080-6
泡,影响外观
质量。
严重时导致产品过烧,影响产品的力学性能。
高
高(后果与上功能:使零件获得
均
加工尺寸、粗糙度满足要求、无毛刺。
或顾客抱怨
毛刺和划痕
功能:将毛坯加工
成半成品200-3
寸/反平面拉槽 /。