水泥厂立磨第七节 立磨(图立磨生料粉磨工艺)
立磨与水泥磨的操作要领

论窑操还是磨操,首先要明确系统内在的逻辑关系,这就要求操作员对系统工艺和设备的特性清楚了解。
把握好定性与定量的辨证关系。
接班时首先要向前一个班人员了解系统的运行情况。
哪些设备存在隐患,产、质量情况如何。
看全分析报告单,了解物料的易磨性,这样可以进行针对性地控制。
既要熟悉中控操作界面,又要对现场设备十分了解,所以要经常到现场了解设备的情况。
特别是当现场设备发生故障时,要知道发生故障的原因和解决故障的方法。
1 立磨立磨是利用磨辊在磨盘上的相对碾压来粉磨物料的设备。
对立磨正常运行的影响主要有几个方面:(1)磨机的料层。
合适的料层厚度和稳定的料层,是立磨稳定运行的基础。
料层太厚,粉磨效率降低,当磨机的压差达到极限时会塌料,对主电机和外排系统都将产生影响;料层太薄,磨机的推动力增加,对磨辊磨盘和液压系统都有损伤。
(2)磨机的振动。
磨机的振动过大,不仅会直接造成机械破坏,并且影响产、质量。
产生振动的因素有:磨机的基础、研磨压力、料层的厚度、风量及风温、蓄能器压力、辊面或磨盘的磨损状况等。
物料对磨机振动的影响及处理方法:物料对磨机振动的影响,主要表现在物料粒度、易磨性及水分。
在立磨运行过程中,要形成稳定的料层,就要求入磨物料具有适宜的级配,要有95%以上的粒度小于辊径的3%。
喂料粒度过大将导致易磨性变差。
由于大块物料之间空隙没有足够多的细颗粒物料填充,料床的缓冲性能差,物料碾碎时的冲击力难以吸收,导致磨机的振动增加。
喂料粒度过小,特别是粉状料多时,由于小颗粒物料摩擦力小,流动性好。
缺乏大块物料构成支撑骨架,不易形成稳定的料床。
磨辊不能有效地压料碾压,大量的粉状物料会使磨内气流粉尘浓度和通风阻力增大,当达到极限时会产生塌料,导致磨机振动增加。
当操作员发现物料过细,尤其是立磨内压差已明显上升时,应及时调整喂料,降低研磨压力和出口温度并加大喷水量,适当降低选粉机转速。
在保证压差稳定和料层厚度的前提下加大研磨压力。
物料的易磨性是影响产量的重要因素,当物料的易磨性变差时,立磨对物料的粉磨循环次数明显增多。
水泥粉磨站工艺流程

水泥粉磨站工艺流程
水泥粉磨站是水泥生产线的重要工艺环节之一,其主要功能是将熟料经过磨矿后得到所需的水泥粉末。
下面将详细介绍水泥粉磨站的工艺流程。
首先,原料破碎。
粉磨站的原料主要是熟料,熟料会先经过破碎机进行粗碎,将较大的熟料块破碎成较小的颗粒。
然后,熟料输送。
破碎后的熟料会通过皮带输送机或者斗式提升机输送到熟料仓,并将其存储起来。
熟料仓一般设置在粉磨机旁边,方便后续的工艺操作。
接着,熟料磨矿。
熟料从熟料仓中取出,通过给料系统定量地送入水泥粉磨机。
水泥粉磨机采用滚筒式或者球磨机式磨矿方式,将熟料进行细磨,使其达到所需的细度要求。
之后,水泥产出。
经过磨矿后的熟料成为水泥磨出料,通过气力输送管道将其送入水泥罐或水泥包装机。
最后,水泥储存和包装。
水泥磨出料会被输送到水泥罐进行临时储存。
根据需要,水泥可以通过螺旋输送机或气力输送管道送入水泥包装机进行包装。
包装后的水泥袋可以被直接销售或存放在仓库中。
除了以上主要的工艺流程,水泥粉磨站还有一些配套设备和工艺操作。
例如,粉磨机系统一般也包括磨辅机械、循环风机、回转炉风机、排风机等。
此外,工艺操作包括除尘、温度控制、
水泥品质监督和检测等。
总结起来,水泥粉磨站工艺流程包括原料破碎、熟料输送、熟料磨矿、水泥产出、水泥储存和包装等环节。
通过以上工艺流程,原料可以转化为所需的水泥粉末,从而满足市场的需求。
同时,水泥粉磨站需要配备相应的设备和工艺操作,以确保工艺流程的顺利进行和水泥品质的稳定。
水泥厂三大工艺流程简介

三大工艺流程简介第一,生料制备工艺流程简介石灰石预均化堆场采用φ90m圆形预均化堆场,堆料为环线连续布料,端面取料、中心卸料。
设有圆形混合预均化堆取料机(1102)一台套。
石灰石在矿山破碎后,经带式输送机送至石灰石转运站,经带式输送机(1101)转运至Φ90m圆形预均化堆场,圆形预均化堆场有效储量42000t。
经带式输送机(1101)送至预均化堆场的石灰石,由悬臂堆料皮带机(1102a)进行连续人字形堆料,由桥式刮板取料机(1102b)横切端面取料。
悬臂堆料皮带机堆料能力为1000t/h,取料机能力为500t/h。
物料由桥式刮板输送机取出进入带式输送机(1104),经带式输送机(1104)输送至Φ12m石灰石配料库内用于配料。
堆场内下部设有备用卸料坑,由棒闸(1103)控制,当堆场检修或取料机发生故障时,可由此旁路暂时卸料。
整个堆料和取料过程采用计算机全自动控制。
石灰石转运点设有单机脉冲袋除尘器对扬尘点进行收尘处理。
粒度≤400mm的砂岩、煤矸石由汽车运输进厂,先分别存放各自的露天堆场,然后分时段由铲车从露天堆场取出喂入喂料仓,经仓底板式喂料机(1301)卸入锤式破碎机(1302)破碎,破碎后物料(粒度≤25mm)由带式输送机(1309)送至辅助原料联合预均化堆场内储存,受料仓有效容积25t,破碎机生产能力为200t/h。
硫酸渣由装载机从铁粉堆场中取出卸入受料仓中(仓有效容积:45t),经仓底棒闸(1305)卸到带式输送机(1309)上并送至辅助原料联合预均化堆场中储存。
采用43×160m矩形联合预均化堆场对砂岩、煤矸石、硫酸渣进行预均化和储存。
所有辅助原料均由一台能力为250t/h的悬臂侧堆料机堆料,并共用一台能力为150t/h的侧式刮板取料机取料。
出均化堆场的砂岩、煤矸石、硫酸渣由带式输送机(1604)、电液动三通(1901)分两路,一路砂岩直接入库,另一路煤矸石、硫酸渣由正反转带式输送机(1902)分别送入各自的配料库中。
水泥厂生产流程及设备原理
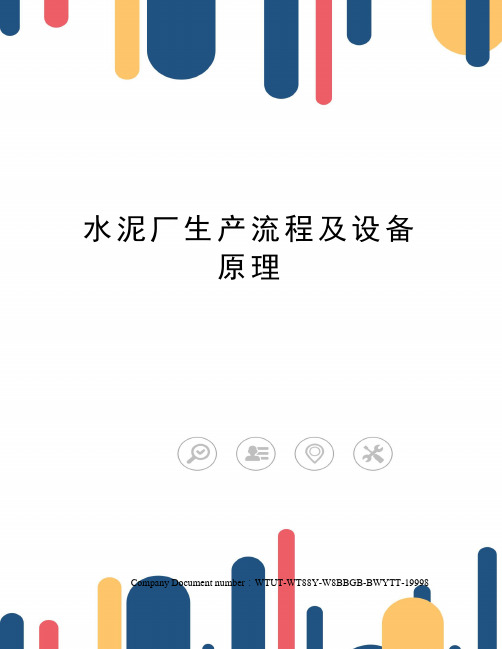
水泥厂生产流程及设备原理Company Document number:WTUT-WT88Y-W8BBGB-BWYTT-19998水泥厂生产流程及设备原理简介1、水泥厂生产流程水泥生产工艺水泥的生产工艺简单讲便是两磨一烧,即原料要经过采掘、破碎、磨细和混匀制成生料,生料经1450℃的高温烧成熟料,熟料再经破碎,与石膏或其他混合材一起磨细成为水泥。
由于生料制备有干湿之别,所以将生产方法分为湿法、半干法或半湿法、干法3种。
全场平面布置图水泥厂的工艺流程简图图立磨原理图图图全厂主机设备与存储设备表全厂主机设备与存储设备列表生料磨、回转窑、水泥磨、煤磨、冷却机、储存设备(堆料场,配料站,均化库,熟料库,水泥库)(1)PC-2018反击锤式破碎机(2)板式喂料机(3)MLS3626立式辊磨机(4)LS型螺旋输送机(5)链斗输送机(6)O-Sepa选粉机(7)罗茨鼓风机(8)水泥窑尾引风机(9)调速型液力偶合器(10)陕西压强设备厂调速机(11)离心通风机2、生料制备矿山开采的工艺流程矿山开采的工艺流程:采矿工作面的整平→布置爆孔→钻孔→装药爆破→集矿→装车原料的破碎,预均化和生料粉磨从矿山开采的矿石用卡车运到水泥厂,由板式喂料机送入单段锤式破碎机,再用皮带送到预均化堆场,采用横堆竖取的方式取料,料经皮带送到石灰石仓.再加上从铁粉仓和粘土仓及粉煤灰仓经电子皮带称定量取料混合后送入生料磨(立磨).经立磨粉磨后粗细料被选粉机分离,粗料返回立磨继续粉磨,细料送入两个锥型仓暂时储存.生料储存,均化和输送由立磨出来的细粉经气力输送管道和皮带提升机送到均化库顶部,经四嘴下料机进入均化库.均化库既有均化的作用也有储存生料的作用.水泥厂生料工段工艺流程图石灰石→板式喂料机→单段锤式破碎机→皮带→堆料机→取料机→皮带→配料站→立磨→o-sepa选粉机→气力输送管道和皮带提升机→生料均化库生料工段主要设备,设备工作原理(1) 板式喂料机板式喂料机能承受较大的料压和冲击,适应大块矿石的喂料,该机给料均衡运转可靠,但设备较重,价格高.板式喂料机分轻型,中型和重型三种.立窑水泥厂石灰石破碎的喂料机一般选用中型的占多.(2)反击锤式破碎机工作原理:物料进入锤破中受到高速回转的锤头冲击而被破碎,物料从锤头处获得动能以高速冲向打击板而被第二次破碎,粒径合格的物料通过蓖条排出,较大粒径在蓖条上再经锤头附加冲击,研磨而被破碎,直至合格后通过蓖条排出.(3) 袋收尘——脉冲袋收尘器是一种新型高效袋式收沉器,利用脉冲阀使压缩空气定时地对滤袋进行喷吹清灰,滤袋寿命长,收尘效率高.工作原理:含尘气体由进风口进入箱体,气体由滤袋外进入滤袋内,经文氏管进入上箱体,从出风口排出,粉尘能截留在滤袋外表面.为了保持收尘器的阻力在一定的范围内(一般为1176~1470Pa)必须定期清灰.清灰时由脉冲控制仪按程序开启控制阀使气沧内的压缩空气由喷嘴管的孔眼高速喷出,每个孔眼对准一个滤袋中心,通过文氏管的诱导在高速气体周围引入相当于喷嘴空气5—7倍的二次空气冲进滤袋,使滤袋急剧膨胀,引起冲击震动.同时产生由袋内向袋外的逆向气流,是黏附在滤袋外表面的积灰被吹落.此时滤布空隙中的粉尘也被吹落,吹扫下来的积灰落入灰斗经排灰系统排出.(4)堆料机和取料机堆料机是:车式悬臂胶带堆料机.(一侧两轨)取料机是:桥式刮板取料机.(两侧两轨)(5)立磨工作原理:物料由三道锁风阀门下料溜子进入磨内,堆积在磨盘中间.由于磨盘的旋转带动磨辊转动物料受离心力的作用想磨盘边缘移动,并被齿入磨辊底部而粉磨.磨辊有液力系统增压以满足粉末需要.磨盘的转速比较高,比相同直径的球蘑机要快大约80%.物料不仅在辊下被压碎,而且被推向外缘,越过挡料圈落入风环,被高速气流入分离器,在回转风叶的作用下进行分选,粗粉重新返回磨盘再粉磨.合格的成品随气流带出机外被收集作为产品,由于风环外气流速度很高因此转热速率很快,小颗粒瞬时得到干燥,大颗粒表面被烘干,再折回重新粉碎过程中得到进一步干燥.(6)O~SEPA选粉机工作原理:待选物料由上部的两个喂料管喂入选粉机,通过撒料盘缓冲板充分分散,落如选粉区,选粉气流大部分来自磨机,通过切向一次风进口.来自收尘设备的收尘风通过二次风进口进入,经导向叶片水平进入选粉区.在选粉机内由垂直叶片和水平叶片组成笼式转子,回转时使内外压差在整个高度内上下保持一定,从而使气流稳定均匀,为精确选粉创造了条件,物料自上而下为每个颗粒提供了多次重复分选的机会,而且每次分选都在精确的离心力和水平风力的平衡条件下进行.细粉从外向内克服了边壁效应的不利影响.(7)电收尘工作原理:电收尘利用高压静电场的作用,使通过的含尘气体中的尘粒荷电,在电场的作用下,使尘粒沉积于电极上,将尘粒从气体中分离出来.电收尘器具有运行可靠,维护简单,电耗低,除尘效率高等优点,在合适条件下使用,其除尘效率可达99%以上. (8)均化库工作原理:该库直径较大,生料先送至顶生料分配器,再经放射状布置的空气输送斜槽入库,库顶还设有收尘器,仓满指示器等装置,在大库的下部中心建有一圈锥型混合室,当轮流向大库的环型库底冲气时生料呈流态化并经混合室周围的8—12个进料孔流入混合库中,同时大库内的生料呈旋涡状踏落,在生料下移的过程中产生重力混合,进入混合库的生料则按扁型四分区进行激烈的空气搅拌,即进行气力均化.混合室的另一作用是靠室内所存一定数量成分均匀的生料起缓冲作用,使进入混合室时略有成分波动的生料缩小其波动.(9)气力输送斜槽以高压离心通风机为动力源,使密闭输送斜槽中的粉状物料保持流态化向斜槽的一端缓慢流动,这种斜槽的主体部分无主动部件,结构简单,输送能力大,易改变输送方向.3、熟料的煅烧生料的预热和预分解系统物料从预热器的顶端加入,从一级旋风筒依次向下再经过分解炉最后入回转窑;从窑头来的高温气体先入分解炉,然后依次向上最后进入增湿塔,一句话概括就是料往下走,气往上流.预分解系统不但合理利用了来自于窑头的废气,节约了能源,而且使物料预先进行了预热和分解,从而为物料的煅烧提供了前提,提高了熟料的质量和生产效率.生料的预热和预分解系统预热与分解系统为五级旋风预热器和分解炉,从窑头来的三次风入分解炉,分解炉上有两个喷煤管来完成煤粉的供给.煅烧设备在预分解窑系统中,回转窑具有燃烧燃料功能,热交换功能,化学反应功能,物料输送功能,降解利用废气物五大功能.回转窑中分为干燥带,预热带,分解带,固相反应带,烧成带和冷却带,在尧柏水泥厂主要是采用ф×60m的回转窑,其放置的倾斜度为4%,传动装置采用的是直流电机单传动,窑体转速为~min.在回转窑的斜度和转速不变的情况下,物料在窑内各带的化学变化和物理状态不同,使得物料以不同的速度通过窑的各带.在烧成带硅酸二钙吸收氧化钙形成硅酸三钙微吸热,只是在熟料形成过程中生成液相时需极少量的熔融净热,在分解窑内,碳酸钙分解需要吸收大量的热量.熟料冷却水泥熟料出窑温度大约为1100~1300摄氏度,充分回收熟料带走的热量以预热二次要气,对提高燃烧速度和燃料温度以及窑和冷却机的热效率,都有主要意义,冷却熟料对于改善熟料的质量和易磨性有良好的效果,冷却良好的熟料可保证设备的安全运转.熟料冷却主要有三种类型:一是:筒式(包括单筒和多筒);二是:篦式(包括震动,回转推动篦式);三是:其他形式(包括立式及"g"式)烧成工段主要设备及其工作原理回转窑(旋窑)的工作原理水泥烧成设备有竖窑、湿法回转窑(旋窑)、普通中空干法窑、立波尔窑、预热机窑(SP)以及目前普遍使用的新型干法回转窑(旋窑)。
粉磨工艺流程(教案)

生料粉磨工艺流程(教案)唐山学院专科教育部彭宝利本节重点:生料闭路粉磨本节难点:烘干磨的构造及工作原理教学手段:采用多媒体教学手段,图文并茂,形象逼真。
本节要达到的目的:学生通过工艺流程图和磨机结构立体图、剖视图,直观的感受到生料粉磨的全过程,易于了解和掌握。
教学进程:一、粉磨系统定义:按一定的粉磨流程配备的主机和辅机构成的系统称为粉磨工艺系统,1、开路(开流)粉磨也是直进直出式,物料一次通过磨机粉磨就成为产品(确切的讲,生料是水泥的半成品)。
特点:流程简单,设备少,投资少,一层厂房就够用。
缺点:容易出现“过粉磨”现象.要保证被粉磨物料全部达到细度合格后才能卸出,被粉磨物料从入磨到出磨的流速就要慢一点(流速受各仓研磨体填充高度的影响),磨的时间长一点,这样台时产量就低了,相对电耗高了,而且部分已经磨细的物料颗粒要等较粗的物料颗粒磨细后一同卸出,大部分细粉不能及时排除(尽管磨内通风能带走一定量的细粉)在磨内继续受到研磨,因此容易出现“过粉磨”现象。
(钢球表面形成缓冲垫层,仿碍粗颗粒的进一步磨细).开路粉磨多用于小型磨机的水泥粉磨系统.2、闭路(圈流)粉磨将出磨物料送入分级设备,把粗细粉筛选出来,细粉成为产品,粗粉回到磨内重新粉磨,形成闭路循环粉磨.特点:消除了“过粉磨现象”, 有利于提高磨机产量和降低电耗。
缺点:流程较复杂,设备多,投资高,需多层厂房。
在闭路粉磨中,被磨物料在磨内的流速提高了,能把部分已经磨细的物料颗粒及时送到磨外,基本消除“过粉磨"现象和缓冲垫层,有利于提高磨机产量、降低电耗,一般闭路系统比开路系统(同规格磨机)产量高15%~25%,对于大部分还没有磨细的粗颗粒,由分级设备(一种分离粗粉和细粉的设备),把出磨物料通过提升机送到分级设备中,将细粉筛选出来作为合格生料送到下一道工序(均化、煅烧),粗粉再送入磨内重磨。
闭路粉磨系统涉及到的设备较多,工艺复杂,一层厂房是不够用的,因此投资大,操作、维护、管理等技术要求较高.闭路粉磨多用于大型磨机生料或水泥的粉磨系统.二、粉磨工艺流程把石灰石、粘土或砂岩、铁粉等原料烧制成熟料需要经过一系列的物理和化学反应过程。
水泥立磨工作原理
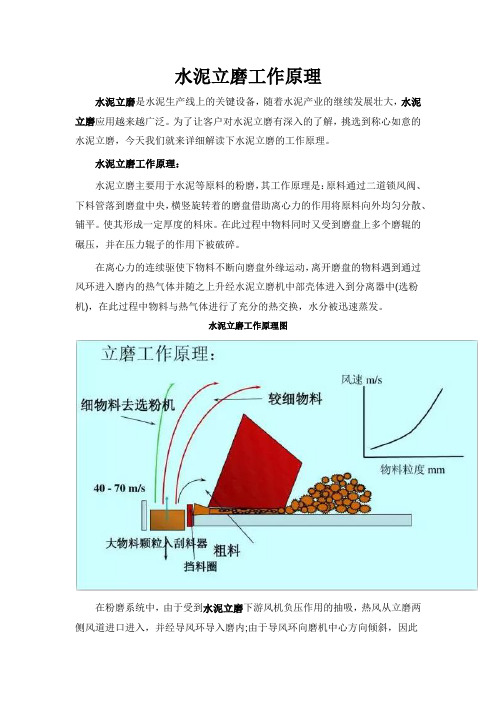
水泥立磨工作原理水泥立磨是水泥生产线上的关键设备,随着水泥产业的继续发展壮大,水泥立磨应用越来越广泛。
为了让客户对水泥立磨有深入的了解,挑选到称心如意的水泥立磨,今天我们就来详细解读下水泥立磨的工作原理。
水泥立磨工作原理:水泥立磨主要用于水泥等原料的粉磨,其工作原理是:原料通过二道锁风阀、下料管落到磨盘中央,横竖旋转着的磨盘借助离心力的作用将原料向外均匀分散、铺平。
使其形成一定厚度的料床。
在此过程中物料同时又受到磨盘上多个磨辊的碾压,并在压力辊子的作用下被破碎。
在离心力的连续驱使下物料不断向磨盘外缘运动,离开磨盘的物料遇到通过风环进入磨内的热气体并随之上升经水泥立磨机中部壳体进入到分离器中(选粉机),在此过程中物料与热气体进行了充分的热交换,水分被迅速蒸发。
水泥立磨工作原理图在粉磨系统中,由于受到水泥立磨下游风机负压作用的抽吸,热风从立磨两侧风道进口进入,并经导风环导入磨内;由于导风环向磨机中心方向倾斜,因此高速高温气流把从挡料圈溢出的被粉碎过的较大物块吹回磨盘,将颗粒较小的物料提升。
在提升过程中不断有不同粒度的物料下落到磨盘上,只有那些足以被风力携带的粒子才能到达上部分离器进行选粉。
经过组合式分离器的物料要进行两次对不合格粗颗粒的筛选过程。
首先在外围是固定叶片处,因为固定叶片与其所在圆成一定角度,一部分粗粒子因撞击叶片失去动能而落回磨盘。
气体进入分离器转子时,受到动叶片撞击,从而进一步将粗粒子剔除,只有符合力度要求的颗粒才能通过,经选粉后的气、料混合物从分离器出口排出,由系统中下游收尘设备收集。
水泥立磨结构图分离器的转速控制着物料的细度,由于采用变频调速电机,因此转子的转速可无极调节。
在物料粉磨提升回落过程中,与热气体进行着充分热交换,使物料水分蒸发,从而使成品水分控制在预定的范围内。
由于在喂入的物料中,可能会有一些难以粉碎的料块以及金属块偶然喂入磨内。
当他们越过挡料圈到达风环处时,不足以被喷出的气体吹起,因而顺风环落下至进风道,被刮料板刮到排渣阀处排出。
立磨的构造与原理

立磨的构造及原理一、立磨发展概况水泥生产主要设备:“三磨一烧”,“三磨”指煤磨、生料磨、水泥磨,“一烧”则指回转窑的熟料煅烧;都是主要的耗能设备.四大粉磨设备:立磨\辊压机\辊筒磨\球磨机而传统球磨机有效功太低,很大部分变为无用功而浪费,如热能;靠料床挤压原理粉磨的立磨(也称辊式磨),有效功是球磨机的2.5倍,可大量节省电能,粉磨煤和水泥原料单位电耗节省5kwh/t,较球磨机节电30%;磨水泥节省8kwh/t.上世纪60年代前,刚开发出的立磨,结构不完善,磨损件不耐磨,只能磨较软的煤,寿命也不长,仍主要靠球磨机.上世纪70年代,随着新型干法水泥技术的飞速发展以及规模的不断扩大,节能要求的提高,使立磨技术不断进步完善,特别是液压加压技术替代弹簧加压技术,在粉磨生料上应用越来越多.80年代,开展了立磨粉磨水泥和矿渣的研究,预粉磨或终粉磨,随着耐磨材料技术的不断发展,粉磨矿渣更具优势,节能50~60%.二、ZJTL3840立磨技术性能、结构概述、立磨的特点及工作原理;立磨是一种理想的大型粉磨设备,广泛应用于水泥、电力、冶金、化工、非金属矿等行业。
它集破碎、干燥、粉磨、分级输送于一体,生产效率高,可将块状、颗粒状及粉状原料磨成所要求的粉状物料。
立磨的研发与生产技术要求很高,我国相关研究机构曾在80年代就提出在水泥行业大力推广立磨的建议,而且当时也有一些厂家推出了自己的立磨产品。
但在当时的研发水平局限下,这时的立磨产品具有不可避免的技术缺陷,因此很多水泥生产厂家最后重又转投球磨机。
近几年来,随着磨粉机械研发技术的大幅提升,国外磨粉机生产企业的立磨技术已经日臻成熟,立磨的产品技术优势也日益凸显。
在这种形势下,国磨粉机生产企业吸取国外成功经验,进行重大技术改革,也相继重新推出了具有自己相关专利技术的立磨产品,并逐渐的为国水泥、电力、化工行业所接受,成为行业粉磨首选设备。
三、技术性能1、型号:ZJTL38402、磨盘直径:3950mm3、磨辊数量:44、磨盘转速:29.4r/min5、磨机装机功率:2100KW6、入磨物料粒度:≤80mm7、入磨物料水分:≤12%8、磨机产量:200t/h9、出磨物料细度:≤12%10、出磨物料水分:≤0.5 %11、入磨风量:360000m³/h12、入磨温度:≤300℃13、出磨风量:400000m³/h14、出磨温度:≤95℃15、料层厚度:120mm四、立磨的特点1、磨盘和磨辊的相对滑动差小,因而允许磨石转速较快,磨辊工作压力较高,因而与其他型式磨辊在同规格的条件下相比,产量较高。
生料粉磨磨培训课件
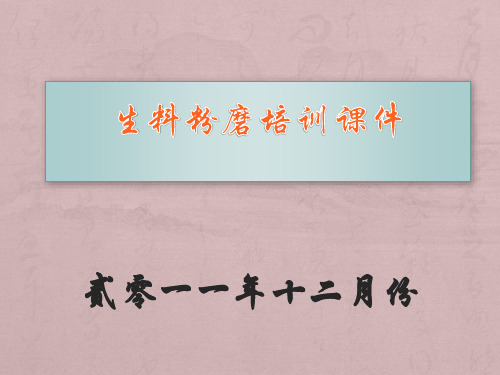
名称 粉煤灰
煤矸石 石煤 赤泥 电石渣
替代原料的化学成分
烧失
SiO2
Al2O3
Fe2O3
CaO
MgO
TiO2
R2O
量
8.36
46.51
30.31
10.45
2.65
0.76
—
1.27
11.50
45.40
35.00
4.60
2.00
0.60
—
—
3.25
52.52
20.80
7.83
4.55
0.87
—
1.19
—
99.78
煤灰渣
9.54
52.40
27.64
5.08
2.34
1.56
98.56
+ 硅酸盐水泥熟料的矿物组成:
硅酸三钙 3CaO·SiO2 阿利特 硅酸二钙 2CaO·SiO2 贝利特 铝酸三钙 3CaO·Al2O3 铁铝酸四钙4CaO·Al2O3·Fe2O3
55%~65% 15%~25% 8%~14% 才利特
8%~12%
玻璃体、方镁石、游离钙
+ 硅酸盐水泥熟料的化学组成
– CaO 62-67% – SiO2 20-24% – Al2O3 4-7% – Fe2O3 2.5-6.0% – 另外:MgO、K2O、Na2O 、f-CaO等
+ 原料预均化的基本原理就是在物料堆放时,由堆料机把 进来的原料连续地按一定的方式堆成尽可能多的相互平 行、上下重叠和相同厚度的料层。取料时,在垂直于料 层的方向,尽可能同时切取所有料层,依次切取,直到 取完,即“平铺直取”。
+ 意义: + (1)均化原料成分,减少质量波动,以利于生产质量
生料磨操作程序

生料磨操作程序由于立磨的诸多优点,现已成为水泥生料粉磨的首选设备。
但是在实际操作中,仍有诸多问题值得注意,介绍一些操作经验。
掌握磨机操作控制要点,使系统温度、压力的合理分布,保持立磨压差、料层厚度、主电机电流及磨机振动等参数波动处于正常范围,达到风量、料量、压力之间的平衡状态,稳定操作制度。
1)操作要点(1)稳定料床维持稳定料床,这是辊式磨料床粉磨的基础,正常运转的关键。
料层厚度可通过调节挡料圈高度来调整,合适的厚度以及它们与磨机产量之间的对应关系,应在调试阶段首先找出。
料层太厚粉磨效率降低,料层太薄将引起振动。
如辊压加大,则产生的细粉多,料层将变薄;辊压减少,磨盘物料变粗,相应返回的物料多,料层变厚。
磨内风速提高,增加内部循环,料层增厚,降低风速,减少内部循环,料层减薄。
在正常运转下辊式磨经磨辊压实后的料床厚度不宜小于40~50mm。
(2)控制粉磨压力粉磨压力是影响磨机产量、粉磨效率和磨机功率的主要因素。
立磨是借助于对料床施以高压而粉碎物料的,压力增加产量增加,但达到一定的临界值后不再变化,压力的增加随之而来的是功率的增加,导致单位能耗的增加,因此适宜的辊压要产量和能耗二者兼顾。
该值决定于物料性质、粒度以及喂料量。
在试生产时要找出合适的粉磨压力以及压力合理的风速可以形成良好的内部循环,使磨盘上的物料层适当、稳定,粉磨效率高。
在生产工艺中,当风环面积一定时,风速由风量决定。
与生产工艺能力之间的对应关系,来保证粉磨效果。
(3)保证一定的出磨温度立磨是烘干兼粉磨系统,出磨气温是衡量烘干作业是否正常的综合性指标。
为了保证原料烘干良好,出磨物料水分小于0.5%,一般控制磨机出口温度在90~C左右。
如温度太低则成品水分大,使粉磨效率和选粉效率降低,有可能造成收尘系统冷凝;如太高,表示烟气降温增湿不够,也会影响到收尘效果。
(4)控制合理的风速立磨主要靠气流带动物料循环。
合理的风速可以形成良好的内部循环,使盘上的物料层适当、稳定,粉磨效率高。
2 硅酸盐水泥生料的磨制(立磨)

立磨的ቤተ መጻሕፍቲ ባይዱ构及工作原理
立磨的形式不同,但其结构和工作原理基本相同。主 要区别在磨辊与磨盘的结构组合不同。磨辊沿水平圆形轨 迹在磨盘上运动,通过外部施加在磨辊上的垂直压力,使 磨盘上物料受到挤压和剪切作用,得以粉碎。主要的几种 立式辊磨碾辊、磨盘形状如图所示。
立磨由分离器、 磨辊、磨盘、加压装 置、减速机、电动机、 壳体等部分组成。
(5)工艺流程简单、布置紧凑,日常维护费用低,可 露天设置,基建投资约为球磨机的70%。
(6)整体密闭性能好、扬尘小、噪声低,环境优越。 (7)成品质量控制快捷,调整产品灵活,便于实现操 作智能化、自动化。 (8)立磨的缺点在于不适于粉磨硬质和磨蚀性大的物 料,衬板使用寿命较短,维修较频繁。磨损件比球磨机的 贵,但与其所取代的球磨机、提升机、选粉机等设备的总 维修量相比,仍显得维修简单、容易和工作量小。
磨机的密封性能较好,漏风量少,磨机的外形尺寸比同等 生产能力的莱歇磨要大,磨用风机功率比莱歇磨低约20%; 3个磨辊使用一个加压装置,每个辊子受力均匀,运转平 稳。
启动时需要一套高启动转矩(150%~200%静启动转 矩的高启动电动机)的辅助传动设施,正常运行时需带料 停机,要求前置输送设备能带负荷启动,操作烦琐,但辊 压低,磨盘转速慢,盘径大,相对风速低。
世界上最早开发立磨的是联邦德国的Loesche(莱歇) 公司,1 925年就拥有了比较成熟的设计。经过不断发展 和完善,目前最大的LM63.4,产量达到840t/h,磨盘直 径6.3m,装机功率为5 600kW,4个磨辊。
目前国外生产立磨的厂家及产品主要有:Loesche(莱 歇)公司、Fuller(富勒)公司、UBE公司生产的LM磨, FLS(史密斯)公司生产的Atox磨、KHD洪堡公司生产的RM 磨和Pfeiffer公司的MPS型立磨。国内生产立磨的厂家及 产品有沈阳的MLS、天津的TRM、合肥的HRM立磨等。
水泥厂立磨第七节立磨(图立磨生料粉磨工艺)

第七节立磨(图立磨生料粉磨工艺)、立磨的工作原理及立磨的类型1.立式磨的工作原理主要工作部分为磨盘及磨辊。
电动机通过减速器带动磨盘转动,磨辊在磨盘上绕自身轴心滚动。
物料通过锁风喂料装置经下料溜管落到磨盘中央,由于离心力的作用形成环形料床,并被钳入磨辊和磨盘之间,受到挤压作用而被粉碎,并由于相对滑动产生剪切力,使物料被磨细。
立磨上部带有选粉设备,从下部侧面通入热空气,对物料进行烘干。
在磨盘的惯性离心力作用下,被粉磨的物料从磨盘边缘溢出,被高速气流扬起到分离器进行分级,粗粉返回磨盘再次受到粉磨(称为内循环),细粉则被气流带到磨外。
没有被热空气带起的粗颗粒物料,溢出磨盘后被斗式提升机重新喂入选粉机,再次挤压粉磨(称为外循环)。
理解挤压粉磨、悬浮烘干,选粉分级三位一体的工作过程。
2.立磨的分类按磨辊、磨盘的几何形状分为:(1)莱歇磨(锥辊--平盘式)(2) MPS 磨(鼓辊--碗式)(3)雷蒙磨(锥辊--碗式) (4)伯力鸠斯磨(双鼓辊--碗式) (5)彼得斯磨,又称E 型磨(球--环式) (6)ATOX 磨(圆柱辊--平盘式)二、立磨的构造1.磨盘:包括导向环、风环、挡料圈、衬板、盘体、刮料板和提升装置等。
2.磨辊:辊套为易磨损件,要求有足够的韧性和良好的耐磨性能。
3.选粉机,可分为静态、动态和高效组合式选粉机三大类。
a.静态选粉机工作原理类似于旋风筒,结构简单,无可动部件,不易出故障。
但调整不灵活,分离效率不高。
b.动态选粉机这是一个高速旋转的笼子,含尘气体穿过笼子时,细颗粒由空气摩擦带入,粗颗粒直接被叶片碰撞拦下,转子的速度可以根据要求来调节,转速高时,出料细度就越细,和离心式选粉机的分级原理是一样的。
它有较高的分级精度,细度控制也很方便。
c.高效组合式选粉机将动态选粉机(旋转笼子)和静态选粉机(导风叶)结合在一起,即圆柱形的笼子作为转子,在它的四周均布了导风叶片,使气流上下均匀地进入选粉机区,粗细粉分离清晰,选粉效率高。
水泥生产工艺重点环节

二、水泥生产中重点工艺安全环节
近年来,新型干法窑每年以较快的速度增长,由于技术和管理人员增长不能与新型干法窑发展同步, 时常出现新型干法窑工艺安全事故,造成停产和设备损坏,甚至出现人员伤亡事故,给企业造成较大的 经济损失。
新型干法干法生产中容易发生事故的时间段是: 调试阶段--施工未结束,如楼梯栏杆未装齐;孔洞没有遮盖;人员多杂;人员缺乏经验。 点火阶段—操作不当引发的煤粉不完全燃烧;造成的爆炸、中毒;投料造成的窜料。 检修阶段—交叉作业;抢时间;临时雇佣人员等。
于二级圈流系统。喂入的物料经烘干仓进入粗磨仓,从磨机中部卸出,由提升机送入选粉机。选粉机 的回料大部分回入细磨仓,小部分回到粗磨仓。大部分热风从磨头进,少部分从磨尾进。
特点:对原料适应性强,易于操作和管理,维护工作量小,有较强的烘干能力强,在生料粉磨系统 中使用较多。
Page:2
一、水泥生产主要工艺流程介绍
5、辊压机终粉磨系统 系统由辊压机、 V型选粉机、动态选粉机组成。物料喂入V型选粉机,经打散烘干后,经提升机、
稳流仓喂入辊压机辊压后,辊压后的物料经提升机再进入V型选粉机进行分选,细粉由气流带入动 态选粉机进行选粉,成品入生料库,粗粉回辊压机辊压。
辊压机单位产品能耗较低,较立磨低2-3kwh/t,本部电耗低到约11-13kwh,越来越多的生料系统 采用了生料辊压机终粉磨系统。 6、分别粉磨 根据原料的不同特性,将钙质和硅质原料分别粉磨,控制不同细度,在降低生料电耗的同时,改 善易烧性降低熟料烧成电耗。
若过长时间不着火时,要关闭油阀,暂停点火,查明原因后再点(防止柴油挥发爆燃)。操作人员 在窑头看火时,必须使用看火面罩,随时注意对喷出气体的闪避。(回火发生烫伤事故) 2)点火初期,窑内温度偏低时不能过早、过快增加喂煤量,如果发生“打枪”,窑尽快调节一次风压, 调整不正常的燃烧状态。 3)升温期间防止系统负压过大。有的操作员担心点火过程中有CO出现,就加大尾排拉风,以至造成火 焰脱离燃烧器而抽灭,或造成窑尾电收尘发生燃爆或窑尾袋收尘器滤袋烧坏。(案列:某厂窑尾收尘 器烧损事故) 4)点火过程中,有的操作者为控制窑内高温区不后移,常将窑头排风机开起来,如果用风过大,热量 会被抽至篦冷机、窑头电收尘,如煤粉不完全燃烧(常见窑头烟囱冒黑烟),在窑头电收尘内富积煤 粉后,易发生爆燃。
水泥厂生产流程及设备原理

水泥厂生产流程及设备原理简介1、水泥厂生产流程水泥生产工艺水泥的生产工艺简单讲便是两磨一烧,即原料要经过采掘、破碎、磨细和混匀制成生料,生料经1450℃的高温烧成熟料,熟料再经破碎,与石膏或其他混合材一起磨细成为水泥。
由于生料制备有干湿之别,所以将生产方法分为湿法、半干法或半湿法、干法3种。
全场平面布置图水泥厂的工艺流程简图图立磨原理图图图全厂主机设备与存储设备表全厂主机设备与存储设备列表生料磨、回转窑、水泥磨、煤磨、冷却机、储存设备(堆料场,配料站,均化库,熟料库,水泥库)(2)板式喂料机(3)MLS3626立式辊磨机(4)LS型螺旋输送机(5)链斗输送机(6)O-Sepa选粉机(7)罗茨鼓风机(8)水泥窑尾引风机(9)调速型液力偶合器(10)陕西压强设备厂调速机(11)离心通风机2、生料制备矿山开采的工艺流程矿山开采的工艺流程:采矿工作面的整平→布置爆孔→钻孔→装药爆破→集矿→装车原料的破碎,预均化和生料粉磨从矿山开采的矿石用卡车运到水泥厂,由板式喂料机送入单段锤式破碎机,再用皮带送到预均化堆场,采用横堆竖取的方式取料,料经皮带送到石灰石仓.再加上从铁粉仓和粘土仓及粉煤灰仓经电子皮带称定量取料混合后送入生料磨(立磨).经立磨粉磨后粗细料被选粉机分离,粗料返回立磨继续粉磨,细料送入两个锥型仓暂时储存.生料储存,均化和输送由立磨出来的细粉经气力输送管道和皮带提升机送到均化库顶部,经四嘴下料机进入均化库.均化库既有均化的作用也有储存生料的作用.水泥厂生料工段工艺流程图石灰石→板式喂料机→单段锤式破碎机→皮带→堆料机→取料机→皮带→配料站→立磨→o-sepa选粉机→气力输送管道和皮带提升机→生料均化库生料工段主要设备,设备工作原理(1) 板式喂料机板式喂料机能承受较大的料压和冲击,适应大块矿石的喂料,该机给料均衡运转可靠,但设备较重,价格高.板式喂料机分轻型,中型和重型三种.立窑水泥厂石灰石破碎的喂料机一般选用中型的占多.(2)反击锤式破碎机工作原理:物料进入锤破中受到高速回转的锤头冲击而被破碎,物料从锤头处获得动能以高速冲向打击板而被第二次破碎,粒径合格的物料通过蓖条排出,较大粒径在蓖条上再经锤头附加冲击,研磨而被破碎,直至合格后通过蓖条排出.(3) 袋收尘——脉冲袋收尘器是一种新型高效袋式收沉器,利用脉冲阀使压缩空气定时地对滤袋进行喷吹清灰,滤袋寿命长,收尘效率高.工作原理:含尘气体由进风口进入箱体,气体由滤袋外进入滤袋内,经文氏管进入上箱体,从出风口排出,粉尘能截留在滤袋外表面.为了保持收尘器的阻力在一定的范围内(一般为1176~1470Pa)必须定期清灰.清灰时由脉冲控制仪按程序开启控制阀使气沧内的压缩空气由喷嘴管的孔眼高速喷出,每个孔眼对准一个滤袋中心,通过文氏管的诱导在高速气体周围引入相当于喷嘴空气5—7倍的二次空气冲进滤袋,使滤袋急剧膨胀,引起冲击震动.同时产生由袋内向袋外的逆向气流,是黏附在滤袋外表面的积灰被吹落.此时滤布空隙中的粉尘也被吹落,吹扫下来的积灰落入灰斗经排灰系统排出.(4)堆料机和取料机堆料机是:车式悬臂胶带堆料机.(一侧两轨)取料机是:桥式刮板取料机.(两侧两轨)(5)立磨工作原理:物料由三道锁风阀门下料溜子进入磨内,堆积在磨盘中间.由于磨盘的旋转带动磨辊转动物料受离心力的作用想磨盘边缘移动,并被齿入磨辊底部而粉磨.磨辊有液力系统增压以满足粉末需要.磨盘的转速比较高,比相同直径的球蘑机要快大约80%.物料不仅在辊下被压碎,而且被推向外缘,越过挡料圈落入风环,被高速气流入分离器,在回转风叶的作用下进行分选,粗粉重新返回磨盘再粉磨.合格的成品随气流带出机外被收集作为产品,由于风环外气流速度很高因此转热速率很快,小颗粒瞬时得到干燥,大颗粒表面被烘干,再折回重新粉碎过程中得到进一步干燥.(6)O~SEPA选粉机工作原理:待选物料由上部的两个喂料管喂入选粉机,通过撒料盘缓冲板充分分散,落如选粉区,选粉气流大部分来自磨机,通过切向一次风进口.来自收尘设备的收尘风通过二次风进口进入,经导向叶片水平进入选粉区.在选粉机内由垂直叶片和水平叶片组成笼式转子,回转时使内外压差在整个高度内上下保持一定,从而使气流稳定均匀,为精确选粉创造了条件,物料自上而下为每个颗粒提供了多次重复分选的机会,而且每次分选都在精确的离心力和水平风力的平衡条件下进行.细粉从外向内克服了边壁效应的不利影响.(7)电收尘工作原理:电收尘利用高压静电场的作用,使通过的含尘气体中的尘粒荷电,在电场的作用下,使尘粒沉积于电极上,将尘粒从气体中分离出来.电收尘器具有运行可靠,维护简单,电耗低,除尘效率高等优点,在合适条件下使用,其除尘效率可达99%以上. (8)均化库工作原理:该库直径较大,生料先送至顶生料分配器,再经放射状布置的空气输送斜槽入库,库顶还设有收尘器,仓满指示器等装置,在大库的下部中心建有一圈锥型混合室,当轮流向大库的环型库底冲气时生料呈流态化并经混合室周围的8—12个进料孔流入混合库中,同时大库内的生料呈旋涡状踏落,在生料下移的过程中产生重力混合,进入混合库的生料则按扁型四分区进行激烈的空气搅拌,即进行气力均化.混合室的另一作用是靠室内所存一定数量成分均匀的生料起缓冲作用,使进入混合室时略有成分波动的生料缩小其波动.(9)气力输送斜槽以高压离心通风机为动力源,使密闭输送斜槽中的粉状物料保持流态化向斜槽的一端缓慢流动,这种斜槽的主体部分无主动部件,结构简单,输送能力大,易改变输送方向.3、熟料的煅烧生料的预热和预分解系统物料从预热器的顶端加入,从一级旋风筒依次向下再经过分解炉最后入回转窑;从窑头来的高温气体先入分解炉,然后依次向上最后进入增湿塔,一句话概括就是料往下走,气往上流.预分解系统不但合理利用了来自于窑头的废气,节约了能源,而且使物料预先进行了预热和分解,从而为物料的煅烧提供了前提,提高了熟料的质量和生产效率.生料的预热和预分解系统预热与分解系统为五级旋风预热器和分解炉,从窑头来的三次风入分解炉,分解炉上有两个喷煤管来完成煤粉的供给.煅烧设备在预分解窑系统中,回转窑具有燃烧燃料功能,热交换功能,化学反应功能,物料输送功能,降解利用废气物五大功能.回转窑中分为干燥带,预热带,分解带,固相反应带,烧成带和冷却带,在尧柏水泥厂主要是采用ф×60m的回转窑,其放置的倾斜度为4%,传动装置采用的是直流电机单传动,窑体转速为~min.在回转窑的斜度和转速不变的情况下,物料在窑内各带的化学变化和物理状态不同,使得物料以不同的速度通过窑的各带.在烧成带硅酸二钙吸收氧化钙形成硅酸三钙微吸热,只是在熟料形成过程中生成液相时需极少量的熔融净热,在分解窑内,碳酸钙分解需要吸收大量的热量.熟料冷却水泥熟料出窑温度大约为1100~1300摄氏度,充分回收熟料带走的热量以预热二次要气,对提高燃烧速度和燃料温度以及窑和冷却机的热效率,都有主要意义,冷却熟料对于改善熟料的质量和易磨性有良好的效果,冷却良好的熟料可保证设备的安全运转.熟料冷却主要有三种类型:一是:筒式(包括单筒和多筒);二是:篦式(包括震动,回转推动篦式);三是:其他形式(包括立式及"g"式)烧成工段主要设备及其工作原理回转窑(旋窑)的工作原理水泥烧成设备有竖窑、湿法回转窑(旋窑)、普通中空干法窑、立波尔窑、预热机窑(SP)以及目前普遍使用的新型干法回转窑(旋窑)。
水泥粉磨工艺PPT课件
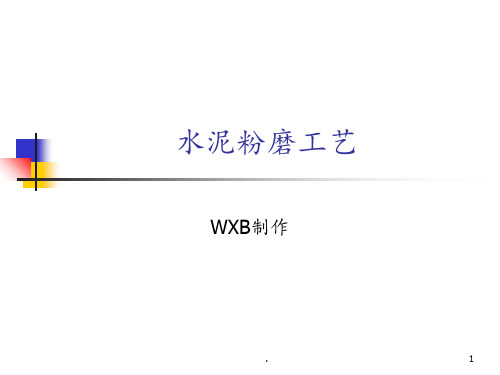
.
34
6.2研磨体装载量、材质及其级 配
6.2.1研磨体装载量
在一定范围内增加研磨体装载量可以提 高磨机产量,降低单位产品电耗,超过 一定范围仍可提高产量,但是却提高单 位电耗。中长磨和长磨的填充系数分别 为25%~35%,30%~35%时产量较高; 30%左右时电耗较低。
.
35
6.2.2钢球装填方式
.
26
5.生产工艺的影响
水泥粉磨工艺有开路和闭路两种工艺流 程。一般来说开路粉磨工艺台时产量较 低,闭路粉磨工艺台时产量较高。水泥 车间都是闭路粉磨工艺。
.
27
5.1开路粉磨工艺
5.1.1磨机开路粉磨工艺流程
该工艺流程只有一台磨机,磨头入料,磨尾出 料即为成品,磨内为多仓磨,相应磨机较长。 该流程出磨水泥颗粒级配比较宽,水泥性能较 好,这是最早出现的粉磨工艺。但是该工艺存 在很大的缺点,粉磨能耗高,产品的强度指标 较低,物料流速慢、磨内物料温度高、造成石 膏脱水、容易使水泥产生假凝现象,台式产量 低。
.
32
6.生产工艺调整的影响
选粉效率和循环负荷 研磨体装载量、材质及其级配 磨机通风
.
33
6.1选粉效率和循环负荷
选粉效率就是选粉机选出的产品中的细粉量占 进入选粉机中细粉量的百分数。循环负荷是指 选粉机的回粉量与成品量之比,以百分数表示。
当选粉机成品细度不变时,循环负荷随选粉机 喂料量变粗而增加,随回料变粗而降低;选粉 效率随喂料变粗而降低,随回料变粗而增加。 选粉效率随循环负荷提高而降低,随成品细度 降低而下降。
31?1522辊压机ckp立磨球磨选粉机系统?该工艺流程为闭路粉磨改进流程由于球磨机入料大小决定了磨机台时产量为了降低入磨粒度在球磨机前面加上辊压机或立磨进行初级破碎这使得入磨粒径大大的降低使得总的台时产量有很大程度的提高而且水泥质量各种性能也较好
- 1、下载文档前请自行甄别文档内容的完整性,平台不提供额外的编辑、内容补充、找答案等附加服务。
- 2、"仅部分预览"的文档,不可在线预览部分如存在完整性等问题,可反馈申请退款(可完整预览的文档不适用该条件!)。
- 3、如文档侵犯您的权益,请联系客服反馈,我们会尽快为您处理(人工客服工作时间:9:00-18:30)。
第七节立磨(图立磨生料粉磨工艺)一、立磨的工作原理及立磨的类型1.立式磨的工作原理主要工作部分为磨盘及磨辊。
电动机通过减速器带动磨盘转动,磨辊在磨盘上绕自身轴心滚动。
物料通过锁风喂料装置经下料溜管落到磨盘中央,由于离心力的作用形成环形料床,并被钳入磨辊和磨盘之间,受到挤压作用而被粉碎,并由于相对滑动产生剪切力,使物料被磨细。
立磨上部带有选粉设备,从下部侧面通入热空气,对物料进行烘干。
在磨盘的惯性离心力作用下,被粉磨的物料从磨盘边缘溢出,被高速气流扬起到分离器进行分级,粗粉返回磨盘再次受到粉磨(称为内循环),细粉则被气流带到磨外。
没有被热空气带起的粗颗粒物料,溢出磨盘后被斗式提升机重新喂入选粉机,再次挤压粉磨(称为外循环)。
理解挤压粉磨、悬浮烘干,选粉分级三位一体的工作过程。
2.立磨的分类按磨辊、磨盘的几何形状分为:(1)莱歇磨(锥辊--平盘式)(2) MPS磨(鼓辊--碗式)(3)雷蒙磨(锥辊--碗式)(4)伯力鸠斯磨(双鼓辊--碗式)(5)彼得斯磨,又称E型磨(球--环式)(6)ATOX磨(圆柱辊--平盘式)二、立磨的构造1.磨盘:包括导向环、风环、挡料圈、衬板、盘体、刮料板和提升装置等。
2.磨辊:辊套为易磨损件,要求有足够的韧性和良好的耐磨性能。
3.选粉机,可分为静态、动态和高效组合式选粉机三大类。
a.静态选粉机工作原理类似于旋风筒,结构简单,无可动部件,不易出故障。
但调整不灵活,分离效率不高。
b.动态选粉机这是一个高速旋转的笼子,含尘气体穿过笼子时,细颗粒由空气摩擦带入,粗颗粒直接被叶片碰撞拦下,转子的速度可以根据要求来调节,转速高时,出料细度就越细,和离心式选粉机的分级原理是一样的。
它有较高的分级精度,细度控制也很方便。
c.高效组合式选粉机将动态选粉机(旋转笼子)和静态选粉机(导风叶)结合在一起,即圆柱形的笼子作为转子,在它的四周均布了导风叶片,使气流上下均匀地进入选粉机区,粗细粉分离清晰,选粉效率高。
不过这种选粉机的阻力较大,因此叶片的磨损也大。
4.加压装置:液压装置,储能器5.监视装置:摇臂监视、振动监视6.传动装置:电动机、减速器7.喷水系统:降低温度、稳定料层8.粗粉外循环系统:提升机三、立磨的优缺点:立磨的缺点1.电耗低:立磨采用滚压料层的方式料磨物料,同时本身带有选粉装置,能及时排出细粉避免了过粉碎现象。
因而粉磨效率高,节能效果非常显著。
较球磨机可节电20~30%左右。
随着物料水分的增加,节能效果更加显著。
2.入磨粒度较大:立磨的入磨粒度一般在50~150mm之间。
而球磨机的入磨粒度一般要求小于30mm。
因此可以省去二级破碎设备。
3.烘干能力大:立式磨采用气体为烘干和输送物料的介质。
因此特别适于烘干兼粉磨作业,可充分利用预热器和煅烧窑排出的300~500℃低温废气作为烘干介质,来烘干和粉磨水分8-10%的物料,而各种烘干球磨机,只能烘干和粉磨水分为3.5~5.0%的物料。
如果另设辅助热风炉,入磨气温升高到450℃左右,立磨则可烘干和粉磨水分为15~20%的物料,因而可省去烘干系统。
4.产品粒度较均齐,调整产品细度和成分容易,便于自动控制。
由于立式磨粉磨和选粉均在同一机壳内进行,产品粒度均齐。
而且,调节分离器转子转速或导风叶开度,能够很快得到需要的产品细度。
对生产不同细度的产品很有利,物料在磨内停留时间很短(2~3min),易于自动控制配料和产品的化学成分。
从粉磨一种物料改变为粉磨另一种物料,几分钟即可实现。
而物料在球磨机内停留时间则需15~20min。
立式磨机尤其适用于立窑水泥厂粉磨全黑生料或半黑生料。
5.工艺流程简单,占地面积小。
6.噪音低,扬尘少,操作维修方便。
立磨的缺点:不适于粉磨硬质和磨蚀性的物料,使用寿命较短,维修较频繁。
而且它的磨损件比磨机的贵,但和其所取代的球磨机、提升机、选粉机等设备的总维修量相比,仍显得维修简单、容易和工作量小。
生料优先选用立磨,而熟料选用球磨的主要原因?立磨相对球磨而言,能耗利用率较高,这是目前粉磨系统优先选用立磨主要原因,但立磨的成品细度太均齐了,没有合理颗粒级配,这是限制立磨使用于熟料磨的主要原因。
为了保证混凝土的早期强度,水泥颗粒中0-3μm颗粒应达10%左右,而保证混凝土后期强度,3—30μm的水泥颗粒则需70%以上。
立磨同球磨机相比,水泥虽然28天强度相同,由于颗粒级配范围狭窄,3-30μm颗粒高达82%,0~3μm颗粒约为6%,致使其早期强度低、需水量大、易于结块和假凝、并有龟裂,混凝土的和易性也不符合要求。
球磨机能耗利用率较低,目前有被立磨、辊压机等设备替代的趋势,但球磨机有“颗粒形貌近似球形,有利于生料煅烧及水泥的水化硬化”独特优点,这是目前熟料磨依然多数选用球磨机的主要原因。
四、立磨的流程1. 设有旋风筒和循环风的粉磨系统:优点:循环风减少收尘风量,降低了入收尘器的浓度,对收尘器的要求降低了。
缺点:系统较复杂,阻力增加。
观察流程图,回答立磨的热风来自主窑,为什么还要设置热风炉?2、不设旋风筒和不设循环风的粉磨系统。
3、立磨也有体外分级的系统类似球磨机的尾卸提升循环系统本次作业:1、绘制设有旋风筒和循环风的立磨系统的流程图,并文字说明。
2、对比立式磨和球磨机优缺点,并说明目前干法水泥生产为什么生料选用立式磨,而熟料依然选用球磨机的主要原因。
五、工艺参数1.磨盘转数k1—系数(表4-5,4-6)n=K1D-0.5 r/min D —磨盘直径,m2.生产能力G=K2D2.5; t/h K2-系数D ;-磨盘直径,m3.辊压一般为10~35MPa。
辊压增加,产量增加,但功率也增加。
4.磨辊、磨盘的相对尺寸(表4-7)5.风量、风速风扫式、半风扫式、机械提升式立磨用风量不同,风扫式、半风扫式立磨磨内风扫速度对磨机的生产起重要作用,必须控制好两个关键处的风速。
一个是风环处的喷口风速。
其作用是将从磨盘溢出的物料返吹回磨盘重新再磨,不让物料颗粒掉落下来。
风速的大小一方面控制掉落粗颗粒的大小,一方面控制循环量和料床厚度。
在风扫系统,该风速达60~100m/s,有利于传热,但阻力大大增加。
降低风环处压损的措施:(P71 )a. 降低风速b. 适当调整风环圆周方向各区段之间的风速另一个是筒体截面风速。
目的是将物料提升至选粉机进行分选。
磨盘增大,风速增大。
实际生产中该风量必须其极限最低风量的要求,一般不低于正常风量的70 %。
6.磨机功率N=KD2.5 kWK-常数,(表4-10)D-磨盘直径,m7.磨损第八节立磨的控制和操作一、立磨的工艺参数表立式生料磨正常运转基本操作参数显示值序号参数性质项目5000t/d 备注1 调节喂料量400t/h 控制料层厚度2 控制入磨风温210℃3 控制出磨风温80℃反映通风量、物料水分4 调节选粉风叶转速1400rpm 控制细度5 控制细度R0.08≤14%6 控制水分≤1%7 调节磨辊压力11MPa8 调节冷风阀0% 调节入磨风温、风量序号参数性质项目5000t/d 备注9 调节热风阀90% 调节入磨风温、风量10 调节循环风阀90% 调节入磨风温、风量11 控制振动值≤3mm/s 反映料层情况12 控制磨内压差5500Pa 反映磨内通风阻力13 控制料层厚度辊径×2%±20mm14 控制喷水量15t/h 控制料层情况、出磨风温15 调节喷水阀门70% 控制喷水量表立式煤磨正常运转基本操作参数显示值参数性质项目5000t/d 备注1 调节喂煤量40t/h 控制料层厚度2 控制入磨风温80℃3 控制出磨风温50℃反映通风量、物料水分4 调节选粉风叶转速600rpm 调节细度5 控制细度R0.08≤14%6 控制水分≤1.5%7 调节磨辊压力5000Pa8 调节冷风阀35%调节风温、风量9 调节热风阀35%10 控制磨内压差5000Pa 反映通风量大小及料层厚度11 控制振动值≤3mm/s 反映料层情况12 控制料层厚度二、立磨操作中的主要控制参数1.振动值振动是辊式磨机工作中普遍存在的情况,合理的振动是允许的,但是若振动过大,则会造成磨盘和磨辊的机械损伤,以及附属设备和测量仪表的毁坏。
料层厚薄不均(不稳定)是产生振动的主要原因,其它原因还有:磨内有大块金属物体;研磨压力太大;耐磨件损坏;储能器充气压力不等;磨通风不足等。
料层不稳定的原因:a. 喂料量和立磨生产能力不适应b.入磨物料不均匀(混合料仓物料离析)c.物料的易磨性d.挡料环高度e.饱磨:下料量大;选粉机转速过快;选粉效率低使内循环负荷大,超过磨内气体携带能力;磨内通风不足。
在操作上应当严格将振动控制在允许范围内,才能为稳定运行创造先决条件。
2.料层厚度立磨稳定运转的另一重要因素是料床稳定。
料层稳定,风量、风压和喂料量才能稳定,否则就要通过调节风量和喂料量来维持料层厚度。
若调节不及时就会引起振动加剧,电机负荷上升或系统跳停等问题。
理论上讲,料层厚度应为磨辊直径的2%±20 mm 。
此外,最佳料层厚度主要取决于原料质量,如含水量、粒度、颗粒分布和易磨性。
运转初期,为了找到最佳的料层厚度,得调试挡料圈的高度。
而在挡料圈高度一定的条件下,稳定料层厚度的重要条件之一是喂料粒度及粒度级配合理。
喂料平均粒径太小或细粉太多,料层将变薄;平均粒径太大或大块物料太多时料层将变厚,磨机负荷上升。
可通过调整喷水量、研磨压力、循环风量和选粉机转数等参数来稳定料层。
喷水是形成坚实料床的前提,适当的研磨压力是保持料床稳定的条件,磨内通风是保证生料细度和水份的手段。
3.压差压差是指风环处的压力损失,也是重要的控制参数之一。
压差是磨内情况的一面镜子,操作员可通过观察压差了解磨内情况,判断料多、料少、风大、风小、粉磨效率等。
若压差过大,说明磨内阻力大,内循环量大,此时应采取减料措施,加大通风量,加大喷水,稳定料层,也可暂时减小选粉机转数,使积于磨内的细粉排出磨外,待压差恢复正常,再适当恢复各参数。
若压差过小,说明磨内物料太少,研磨层会很快削薄,引起振动增大,因此应马上加料,增加喷水,使之形成稳定料层。
4. 磨机通风a.风量、风速风扫式系统风环处风速高达60~90m/s;半风扫式风速可降低至40~50m/s。
磨内风量可在70~105%范围内调整,但窑磨串联系统应不影响窑系统的操作。
b.出磨温度出磨气温是可以变化的,主要看出磨产品的水分能否保证≤0.5%。
出磨温度由入口温度和喷水量来调节控制。
喷水过多会形成料饼导致磨内工况恶化;喷水量过少,料层不稳,振动加剧;当喂料量和风量一定时,喷水量可稳定在最低量。
c. 系统漏风在总风量一定的情况下,系统漏风使喷嘴风环处的风速降低,导致吐渣量增大。
5.产品细度产品细度主要靠选粉机转速来调节,转数大,产品细;转数小,产品粗。