【精品】精细化工企业重大风险检查清单
化工(危险化学品)企业安全检查重点明细清单

2、企业是否设置安全生产管理机构或配备专职安全生产管理人员的。
3、企业的主要负责人、安全负责人及其他安全生产管理人员是否按照规定经考核合格的。
4、企业的主要负责人、安全负责人、技术负责人是否具备相应的化工专业知识或者化工行业从业经历的。
查资料
1、动火作业是否按规定进行可燃气体分析.
2、受限空间作业是否按规定进行可燃气体、氧含量和有毒气体分析.
3、脱水、装卸、倒罐作业时,作业人员是否离开现场或油气罐区同一防火堤内切水和动火作业同时进行的。
4、作业过程是否安排专人进行现场安全管理遵守有关标准和规范,履行下列现场安全管理职责:
(1)确认现场作业条件以及符合安全要求;
4、如委托其他具有专业资质的单位进行前款规定的危险作业的,是否在作业前与受委托方签订安全生产管理协议,明确各自的安全生产管理责任。
25
危险化学品储存的管理
《危险化学品安全管理条例》第七十八条
查资料、
抽查现场
1、危险化学品专用仓库是否设专人负责管理.
2、对储存的剧毒化学品以及储存数量构成重大危险源的其他危险化学品是否实行双人收发、双人保管制度。
7
从业人员上岗过程中
《安全生产法》第五十四条
查资料、
抽查现场
1、是否将火种带入易燃易爆场。
2、是否存在脱岗、睡岗、酒后上岗行为的。
二、工艺管理
8
安全设计诊断和安全可靠性论证
《安全生产法》第三十八条、《危险化学品生产企业安全生产许可证实施办法》(国家安全监管总局令第41号)、《遏制危险化学品和烟花爆竹重特大事故工作意见》
化工企业20条重大生产安全事故隐患排查表
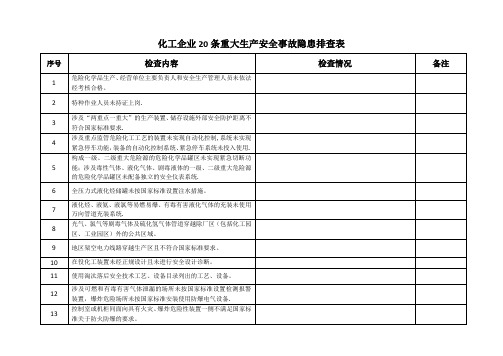
18 者制度未有效执行。
新开发的危险化学品生产工艺未经小试、中试、工业化试验直接进 行工业化生产;国内首次使用的化工工艺未经过省级人民政府有关
19 部门组织的安全可靠性论证;新建装置未制定试生产方案投料开
车;精细化工企业未按规范性文件要求开展反应安全风险评估。 未按国家标准分区分类储存危险化学品,超量、超品种储存危险化
构成一级、二级重大危险源的危险化学品罐区未实现紧急切断功
5
能;涉及毒性气体、液化气体、剧毒液体的一级、二级重大危险源
的危险化学品罐区未配备独立的安全仪表系统.
6
全压力式液化烃储罐未按国家标准设置注水措施。
液化烃、液氨、液氯等易燃易爆、有毒有害液化气体的充装未使用
7
万向管道充装系统.
光气、氯气等剧毒气体及硫化氢气体管道穿越除厂区(包括化工园
8
区、工业园区)外的公共区域。
9
地区架空电力线路穿越生产区且不符合国家标准要求。
10 在役化工装置未经正规设计且未进行安全设计诊断。
11 使用淘汰落后安全技术工艺、设备目录列出的工艺、设备。
涉及可燃和有毒有害气体泄漏的场所未按国家标准设置检测报警
12 装置,爆炸危险场所未按国家标准安装使用防爆电气设备.
化工企业 20 条重大生产安全事故隐患排查表
序号
检查内容
危险化学品生产、经营单位主要负责人和安全生产管理人员未依法
1
经考核合格。
2
特种作业人员未持证上岗.
涉及“两重点一重大”的生产装置、储存设施外部安全防护距离不
3
符合国家标准要求.
涉及重点监管危险化工工艺的装置未实现自动化控制,系统未实现
化工企业安全风险辨识分级管控清单

化工企业安全风险辨识分级管控清单为了降低化工企业的安全风险,保护人民生命财产安全,化工企业需要开展安全风险辨识分级管控。
针对此,本文提供的化工企业安全风险辨识分级管控清单,供化工企业参考和使用。
1.安全风险辨识分类标准1.1 事故影响范围:人身损害、影响周边环境等1.2 事故概率发生频率:高、中、低1.3 事故严重度:大(重大或重大以上)、中等(一般或一般以上)、小(较小或较小以上)2.化工企业安全风险辨识分级管控清单2.1 高风险区域高风险区域包括:储罐区、化学品输送管道附近、易燃易爆领域、高温区域、高压气体区域、危险场所等。
管控措施:1) 安装监测设备,如气体监测设备、测温设备等。
2) 配备防爆器材和消防设施。
3) 限制非相关人员进入。
4) 制定严格的工艺操作流程,工人进行相关岗位培训,确保操作规范,完全遵守操作流程。
5) 定期开展事故预案演练。
2.2 中等风险区域中等风险区域包括:储蓄区、废水处理区、垃圾处理区、危险废物储存区、危险品堆放区等。
管控措施:1) 配备安全设施,如硫酸铜中毒警示装置、安全防护栏杆等。
2) 制定合理的通风设计,确保室内空气流通。
3) 建设完善的处置系统和危险品处理方案。
4) 分类储存危险品,严禁混储。
5) 加强现场巡检,检查安全系数。
2.3 低风险区域低风险区域包括:办公区域、士工作区域、维护区域等。
管控措施:1) 定期开展安全培训,培训员工应急救援知识。
2) 制定工作规范,保证操作的正确性。
3) 定期开展演习,检查员工应对突发事件的能力。
4) 建立完善的管理制度,定期检查安全资料。
5) 在员工寝室、厕所等场所加装监控设备,预防事故发生。
化工企业安全风险辨识分级管控清单对化工企业来说非常重要。
只有根据实际情况,将实际风险进行分类,针对性地采取相应的管控措施,才能有效地防范和控制安全风险,减少安全事故的发生。
“防风险、除隐患、保安全”安全生产大排查大整治行动化工行业大排查大整治排查清单

序号排查事项排查内容备注123 4 5 安全生产责任制企业应建立健全全员安全生产责任制:1.应明确各级管理部门及基层单位的安全生产责任和考核标准。
2.应明确主要负责人、各级管理人员、一线从业人员(含劳务派遣人员、实习学生等)等所有岗位人员的安全生产责任和考核标准。
企业应将全员安全生产责任制教育培训工作纳入安全生产年度培训计划,对所有岗位从业人员(含劳务派遣人员、实习学生等)进行安全生产责任制教育培训,如实记录相关教育培训情况等。
企业应建立健全安全生产责任制管理考核制度,对全员安全生产责任制落实情况进行考核管理。
1.主要负责人应组织制定符合本企业实际的安全生产方针和年度安全生产目标;2.安全生产目标应满足:( 1 )形成文件,并得到所有从业人员的贯彻和实施;( 2 )符合或者严于相关法律法规的要求;( 3 )根据安全生产目标制定量化的安全生产工作指标。
企业应建立安全风险研判与承诺公告制度,董事长或者总经理等主要负责人应每天作出安全承诺并向社会公告。
序号67 8 91011 排查事项安全生产责任制排查内容企业主要负责人应严格履行其法定的安全生产职责:1.建立、健全本单位安全生产责任制;2.组织制定本单位安全生产规章制度和操作规程;3.组织制定并实施本单位安全生产教育和培训计划;4.保证本单位安全生产投入的有效实施;5.催促、检查本单位的安全生产工作,及时消除安全事故隐患;6.组织制定并实施本单位的生产安全事故应急救援预案;7.及时、如实报告生产安全事故。
企业应制定领导干部带班制度并严格落实,主要负责人应参加领导干部带班,其他分管负责人要轮流带班;生产车间也要建立由管理人员参加的车间值班制度并严格落实。
企业主要负责人应学习、贯彻落实国家安全生产法律法规,听取安全生产工作情况汇报,了解安全生产状况,研究重大问题,并催促落实情况。
1.企业应当依法设置安全生产管理机构或者配备专职安全生产管理人员;2.专职安全生产管理人员应不少于企业员工总数的2% (不足50 人的企业至少配备1人),要具备化工或者安全管理相关专业中专以上学历,有从事化工生产相关工作2 年以上经历;3.从业人员300 人以上的企业,应当按照不少于安全生产管理人员15%的比例配备注册安全工程师;安全生产管理人员在7人以下的,至少配备1 名注册安全工程师。
化工企业20条重大生产安全事故隐患排查表

化工企业 20 条重大生产安全事故隐患排查表
序号
检查内容
检查情况
危险化学品生产、经营单位主要负责人和安全生产管理人员未
1
依法经考核合格。
2
特种作业人员未持证上岗。
涉及“两重点一重大”的生产装置、储存设施外部安全防护距
3
离不符合国家标准要求。 涉及重点监管危险化工工艺的装置未实现自动化控制,系统未
9 有关部门组织的安全可靠性论证;新建装置未制定试生产方案投料
开车;精细化工企业未按规范性文件要求开展反应安全风险评估。
2
未按国家标准分区分类储存危险化学品,超量、超品种储存危
0 险化学品,相互禁配物质混放混存。
检查人员:
日
期:
.3
7
使用万向管道充装系统。
8
光气、氯气等剧毒气体及硫化氢气体管道穿越除厂区(包域。
《化工仪表及自动化》教学大纲
9 地区架空电力线路穿越生产区且不符合国家标准要求。
1 0
在役化工装置未经正规设计且未进行安全设计诊断。
1 1
使用淘汰落后安全技术工艺、设备目录列出的工艺、设备。
1
未建立与岗位相匹配的全员安全生产责任制或者未制定实施
6 生产安全事故隐患排查治理制度。
1 7
未制定操作规程和工艺控制指标。
1
未按照国家标准制定动火、进入受限空间等特殊作业管理制
.2
《化工仪表及自动化》教学大纲
8 度,或者制度未有效执行。
新开发的危险化学品生产工艺未经小试、中试、工业化试验直
1 接进行工业化生产;国内首次使用的化工工艺未经过省级人民政府
1
涉及可燃和有毒有害气体泄漏的场所未按国家标准设置检测
化工企业条重大生产安全事故隐患排查表

18 者制度未有效执行。
新开发的危险化学品生产工艺未经小试、中试、工业化试验直接进 行工业化生产;国内首次使用的化工工艺未经过省级人民政府有关
19 部门组织的安全可靠性论证;新建装置未制定试生产方案投料开
车;精细化工企业未按规范性文件要求开展反应安全风险评估。 未按国家标准分区分类储存危险化学品,超量、超品种储存危险化
20 学品,相互禁配物质混放混存。
检查人员: 日 期:
精选 word 范本!
构成一级、二级重大危险源的危险化学品罐区未实现紧急切断功
5
能;涉及毒性气体、液化气体、剧毒液体的一级、二级重大危险源
的危险化学品罐区未配备独立的安全仪表系统。
6
全压力式液化烃储罐未按国家标准设置注水措施。
液化烃、液氨、液氯等易燃易爆、有毒有害液化气体的充装未使用
7万向管道充ຫໍສະໝຸດ 系统。光气、氯气等剧毒气体及硫化氢气体管道穿越除厂区(包括化工园
精选 word 范本!
检查情况
.
备注
.
准关于防火防爆的要求。 化工生产装置未按国家标准要求设置双重电源供电,自动化控制系
14 统未设置不间断电源。 15 安全阀、爆破片等安全附件未正常投用。
未建立与岗位相匹配的全员安全生产责任制或者未制定实施生产
16 安全事故隐患排查治理制度。 17 未制定操作规程和工艺控制指标。
8
区、工业园区)外的公共区域。
9
地区架空电力线路穿越生产区且不符合国家标准要求。
10 在役化工装置未经正规设计且未进行安全设计诊断。
11 使用淘汰落后安全技术工艺、设备目录列出的工艺、设备。
涉及可燃和有毒有害气体泄漏的场所未按国家标准设置检测报警
化工(危险化学品)企业安全检查重点指导清单分析
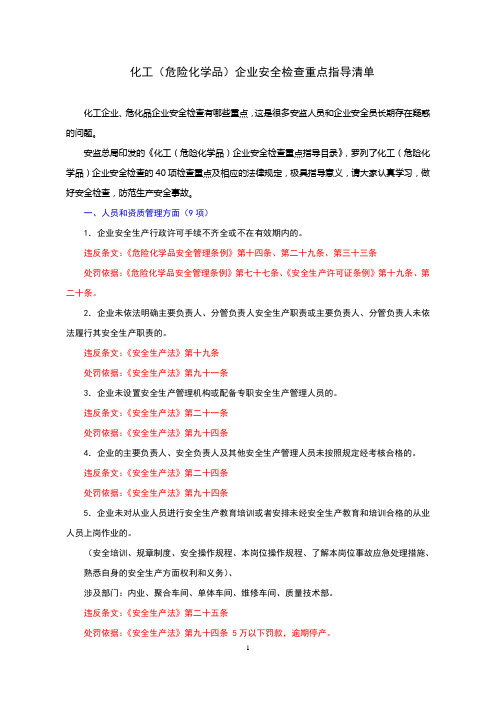
化工(危险化学品)企业安全检查重点指导清单化工企业、危化品企业安全检查有哪些重点,这是很多安监人员和企业安全员长期存在疑惑的问题。
安监总局印发的《化工(危险化学品)企业安全检查重点指导目录》,罗列了化工(危险化学品)企业安全检查的40项检查重点及相应的法律规定,极具指导意义,请大家认真学习,做好安全检查,防范生产安全事故。
一、人员和资质管理方面(9项)1.企业安全生产行政许可手续不齐全或不在有效期内的。
违反条文:《危险化学品安全管理条例》第十四条、第二十九条、第三十三条处罚依据:《危险化学品安全管理条例》第七十七条、《安全生产许可证条例》第十九条、第二十条。
2.企业未依法明确主要负责人、分管负责人安全生产职责或主要负责人、分管负责人未依法履行其安全生产职责的。
违反条文:《安全生产法》第十九条处罚依据:《安全生产法》第九十一条3.企业未设置安全生产管理机构或配备专职安全生产管理人员的。
违反条文:《安全生产法》第二十一条处罚依据:《安全生产法》第九十四条4.企业的主要负责人、安全负责人及其他安全生产管理人员未按照规定经考核合格的。
违反条文:《安全生产法》第二十四条处罚依据:《安全生产法》第九十四条5.企业未对从业人员进行安全生产教育培训或者安排未经安全生产教育和培训合格的从业人员上岗作业的。
(安全培训、规章制度、安全操作规程、本岗位操作规程、了解本岗位事故应急处理措施、熟悉自身的安全生产方面权利和义务)、涉及部门:内业、聚合车间、单体车间、维修车间、质量技术部。
违反条文:《安全生产法》第二十五条处罚依据:《安全生产法》第九十四条 5万以下罚款,逾期停产。
6.从业人员对本岗位涉及的危险化学品危险特性不熟悉的。
(安全教育和培训、基本知识、规章制度、劳动纪律、有关案例、操作规程、劳动防护、安全装置、生产设备)涉及部门:内业、聚合车间、单体车间、维修车间、质量技术部。
违反条文:《安全生产法》第二十五条处罚依据:《安全生产法》第九十四条 5万以下罚款,逾期停产。
化工企业重大风险清单及控制措施

1
1
焊接现场加强通风
维修车间
13
焊渣飞溅
烫伤、眼睛伤害
作业现场工作人员
1
1
1
作业时穿戴劳动防护用品
维修车间
14
焊光强烈。
眼睛伤害
作业现场工作人员
1
1
1
作业时穿戴劳动防护用品
维修Hale Waihona Puke 间16防护用品穿戴不全
人员伤害
作业现场工作人员
1
1
1
经常进行安全学习,加强安全监督
维修车间
17
搬运氧气瓶、乙炔瓶不当
着火
作业现场工作人员
1
3
3
经常进行安全学习,加强安全监督
维修车间
6
监护人不到位
出现事故不能及时处置,造成事故扩大
作业现场工作人员
1
2
2
经常进行安全学习,加强安全监督
维修车间
7
消防器材不到位
不能及时灭火,造成事故扩大
作业现场工作人员
1
1
1
按规程作业
维修车间
8
作业证手续不全
造成各类责任事故
作业现场工作人员
1
系好安全带,专人监护
各部门
3
进入容器内作业不办证
中毒窒息
作业现场工作人员
1
2
2
遵守管理制度,专人监护
各部门
4
违章动火
火灾、爆炸
作业现场工作人员
1
2
2
遵守管理制度,动火前要制定方案
各部门
5
不按规定穿戴防护用品
各种伤害都可能
作业现场工作人员
1
化工行业20条重大隐患专项检查表

爆破片未定期更换的,不判定为重大隐患。
16
未建立与岗位相匹配的全员安全生产责任制或者未制定实施生产安全事故隐患排查治理制度。
未制定安全生产责任制,判定为重大隐患。
安全生产责任制中,缺少企业主要负责人、管理层、安全管理机构或安全管理人员及与生产有关的重点单位(安全、生产技术、设备、生产车间等)的安全职责的,判定为重大隐患。缺少其他单位的安全职责,不判定为重大隐患。
开展特殊作业未办理作业许可证的,判定为重大隐患。
开展动火(易燃易爆场所)、进入受限空间作业未进行作业分析的、未进行危险源辨识的,判定为重大隐患。
特殊作业现场安全管控措施严重缺失的,判定为重大隐患。
特殊作业审批程序错误(如动火作业先批准,后动火分析等;不是指有关时间填写错误)、弄虚作假的,判定为重大隐患。
20
未按国家标准分区分类储存危险化学品,超量、超品种储存危险化学品,相互禁配物质混放混存。
未按国家标准分区分类储存危险化学品,超量、超品种储存危险化学品,相互禁配物质混放混存。
1.依据GB50493,企业可能泄漏可燃和有毒有害气体的主要释放源未设置检测报警器,判定为重大隐患。
2.企业设置的可燃和有毒有害气体检测报警器种类错误(如检测对象错误、可燃或有毒类型错误等),视为未设置,判定为重大隐患。
3.企业可能泄漏可燃和有毒有害气体的主要释放源设置了检测报警器,但检测报警器未处于正常工作状态(故障、未通电、数据有严重偏差等),判定为重大隐患。
4
涉及重点监管危险化工工艺的装置未实现自动化控制,系统未实现紧急停车功能,装备的自动化控制系统、紧急停车系统未投入使用。
涉及危险化工工艺的大型化工装置应装设紧急停车系统;危险化工工艺装置的自动化控制和紧急停车系统应正常投入使用。
精细化工企业重大风险检查清单

精细化工企业重大风险检查清单案例回顾案例1江苏连云港某精细化工企业爆炸,导致10人死亡。
直接原因:尾气处理系统的氮氧化物(夹带硫酸)串入保温釜,与釜内物料发生化学反应,持续放热升温,最后导致爆炸。
案例2浙江临海某医药中间体公司爆炸,导致3人死亡。
直接原因:在减压蒸馏浓缩反应液过程中,操作人员打开夹套蒸气旁通阀,导致高温联锁失去保护作用,釜内温度超过反应产物分解热温度,反应产物急剧分解放热,体系压力、温度迅速上升,最终导致反应釜超压物理爆炸。
案例3浙江绍兴某精细化工企业爆炸,导致3人死亡。
直接原因:在500ml规模小试的基础上放大10000倍进行试验,在进行中间体[1,4,5]氧二氮杂庚烷脱溶作业后期物料浓缩时,由于加热方式不合理、测温设施无法检测釜内液体的真实温度等原因,使浓缩的[1,4,5]氧二氮杂庚烷温度过高发生剧烈热分解,导致设备内压力骤升并发生爆炸。
案例4浙江临海某制药企业爆炸,导致1人死亡。
直接原因:未按操作规程的要求对离心机进行充氮保护的情况下,打开下料阀门开启离心机,由于含哌嗪的甲苯溶液进入高速旋转的离心机,产生静电火花引爆了甲苯混合气体,致使离心机发生爆炸。
一次又一次惨痛的事故教训为精细化工企业敲响了安全警钟。
当前,精细化工生产多以间歇和半间歇操作为主,且涉及危险化学品种类多、工艺复杂控制难度大、自动化程度不高、人员素质参差不齐,容易导致火灾、爆炸、中毒事故。
为推动精细化工企业强化风险研究、风险评估和风险控制能力,进一步提升本质安全水平,促进行业安全发展,北京安必达科技有限公司召集国内精细化工领域多名专家,把精细化工领域的事故风险从设施缺陷、静电危险、反应与物料危险、粉尘爆炸、固体废弃物存放混乱五个方面予以梳理总结,为企业找准危险源、排查隐患、稳妥应对,提供遵循参照。
1设施缺陷1.1涉及重点监管危险化工工艺的装置没有设置SIS系统;1.2构成一级、二级重大危险源的危险化学品罐区未实现紧急切断功能;1.3涉及毒性气体、液化气体、剧毒液体的一级、二级重大危险源的危险化学品罐区未配备独立的安全仪表系统;1.4涉及可燃和有毒有害气体泄漏的场所未按国家标准设置检测报警装置;1.5爆炸危险场所未按国家标准安装使用防爆电气设备;1.6没有采用防泄漏泵(磁力泵、屏蔽泵、隔膜泵)输送易燃有毒液体物料。
化工危化品安全生产隐患排查清单

化工危化品安全生产隐患排查清单化工危化品安全生产是一个重要的问题,必须进行隐患排查和处理。
下面是一份化工危化品安全生产隐患排查清单,共。
一、危险源和危险设备:1、化工生产过程中的储罐、输送管道、反应釜、加热设备等设备,会存在泄漏、爆炸等危险情况,需要加强管理和维护。
2、进料、排料、加料、卸料等操作设备,需要进行定期检修和清洗。
3、机械设备的使用人员需要进行岗前、岗中、岗后的安全教育和操作技能培训,以减少操作失误造成的事故。
4、设备运行声音要保持平稳,如出现嘈杂、异响等情况,要及时排查处理。
5、应设立气体检测设备,随时掌握生产环境中毒气分布情况,并采取相应的防护措施。
二、现场安全和环境卫生:1、生产场地内部和周边环境要保持清洁卫生,避免积存垃圾和污染物等,防止污染臭气和废气释放,切实保护环境。
2、场地内要有清晰的标识和路线示意图,明确人员、车辆、原材料、成品等通道和安全区域的位置。
3、员工要正确携带和使用个人防护装备,如安全帽、安全鞋、呼吸器等,严禁穿拖鞋进入生产现场。
4、现场应设置相应的消防设施,包括灭火器、消防水带、消防喷淋等,确保及时灭火和疏散。
5、设备定期检验维护,对于存在故障或隐患问题的设备进行拆卸处理或更换。
三、人员安全:1、生产人员应配备在岗证、安全教育合格证等相关证件,并进行定期体检。
2、在化工生产过程中,工人应认真执行各项安全规章制度,如禁止吸烟、禁止携带火种等。
3、生产人员应配备保护装备,如防护手套、护目镜、安全带等,并正确使用。
4、生产人员应定期接受职业健康检查,确保健康并及时发现职业病症。
5、生产过程中严禁酗酒、吸毒和滥用刺激性药物等不良嗜好行为。
以上是化工危化品安全生产隐患排查清单,该清单可作为化工企业和相关部门的参考依据。
通过排查和处理隐患,化工企业能够落实安全生产方针,保障生产人员安全,预防事故发生。
XX化工有限公司重大风险源控制清单

XX化工有限公司重大风险源控制措施清单
为了加强公司重大风险源的安全管理,结合公司生产的实际情况,制定重大风险源的控制措施,具体如下:
一、公司的重大风险源清单
序号部门
作业位置
或区域
作业活动
(内容)
危害(危
险源)
可能导致的
事故类别
D值
危险程
度等级
1 合成车间氨库储存过程易燃液
体、雷电、
静电
火灾、爆炸、
中毒、冻伤
135 3
2 合成操作间生产过程液化气体
有毒气体
火灾、爆炸、
中毒触电
150 3
二、重大风险源控制措施
1.液氨库
1)加强储存过程的安全管理,实行管理人员定点承包管机制,管理人员对承包区域负有安全管理责任。
2)对该区域安装电脑监控装置,实行24小时监控。
3)对储存设施每半年进行一次维护保养。
4)雷雨天停止接卸作业。
5)每年对防雷接地装置进行检测。
6)职工在操作期间,穿戴好劳动防护用品,提高自我保护意识,防止中毒。
7)加强设备巡检,防止跑、冒、低、漏现象的发生。
8)现场配备一定数量的消防器材,并保证完好。
9)岗位使用防爆电器设施。
10)严格对操作人员进行培训,做到持证上岗。
11)严格执行工艺规程和安全操作规程。
12)严按照规定现场配置必要的应急救援器材和防护用品。
13)生产现场严禁烟火,禁止无证动火。
14)对设备进行静电接地,防止静电聚集引起事故。
XX化工有限公司
2013年4 月25 日。
重点危险化学品特殊管控安全风险隐患排查清单

液化石油气球罐上的阀门的设计压力不应小于2.5MPa。
《石油化工液化烃球形储罐设计规范》(SH3136)第6条
13
丙烯、丙烷、混合C4、抽余C4及液化石油气的球形储罐应采取防止液化烃泄漏的注水措施。注水压力应能满足需要。
《石油化工液化烃球形储罐设计规范》(SH3136)第7.4条
14
丁二烯球形储罐应采取以下措施:
《关于氯气安全设施和应急技术的指导意见》(中国氯碱工业协会〔2010〕协字第070号)第四条
20
液氯仓库必须设置事故氯吸收(塔)装置,具备24小时连续运行的能力,并与电解故障停车、动力电失电联锁控制;至少满足紧急情况下处理能力,吸收液循环槽具备切换、备用和配液的条件,保证热备状态
或有效运行。
《关于氯气安全设施和应急技术的指导意见》(中国氯碱工业协会〔2010〕协字第070号)第四条
(《关于氯气安全设施和应急技术的指导意见》(中国氯碱工业协会〔2010〕协字第070号)第三条
8
使用氯气作为生产原料时,宜使用盘管式或套管式气化器的液氯全气化工艺,液氯气化温度不得低于71℃,建议热水控制温度75~85℃;采用特种气化器(蒸汽加热),温度不得大于121℃,气化压力与进料调节阀联锁控制,气化温度与蒸汽调节阀联锁控制。
《危险化学品生产装置和储存设施风险基准》(国标36894-2018)
2
禁止将油和氯离子带入硝酸铵溶液系统。
《首批重点监管的危险化学品安全措施和应急处置原则》(安监总厅管三〔2011〕142号)
3
硝酸铵贮存过程中,禁止混入下列物质:
1.硫、磷、硝酸钠、亚硝酸钠及其还原类物质;
2.硫酸、盐酸、硝酸等酸类物质;
1.设置氮封系统;
2.储存周期在两周以下时,应设置水喷淋冷却系统;储存周期在两周以上时,应设置冷冻循环系统和阻聚剂添加系统;
- 1、下载文档前请自行甄别文档内容的完整性,平台不提供额外的编辑、内容补充、找答案等附加服务。
- 2、"仅部分预览"的文档,不可在线预览部分如存在完整性等问题,可反馈申请退款(可完整预览的文档不适用该条件!)。
- 3、如文档侵犯您的权益,请联系客服反馈,我们会尽快为您处理(人工客服工作时间:9:00-18:30)。
【精品】精细化工企业重大风险检查清单
01、设施缺陷
1.1 涉及重点监管危险化工工艺的装置没有设置SIS系统;
1.2 构成一级、二级重大危险源的危险化学品罐区未实现紧急切断功能;
1.3 涉及毒性气体、液化气体、剧毒液体的一级、二级重大危险源的危险化学品罐区未配备独立的安全仪表系统;
1.4 涉及可燃和有毒有害气体泄漏的场所未按国家标准设置检测报警装置;
1.5 爆炸危险场所未按国家标准安装使用防爆电气设备;
1.6 没有采用防泄漏泵(磁力泵、屏蔽泵、隔膜泵)输送易燃有毒液体物料。
02、静电危险
2.1 内衬搪瓷或内衬聚四氟乙烯釜或容器,没有设置氮封装置,且没有有效导出静电设施;
2.2 易燃物料的反应釜、高位槽、中间罐,采用上部进料时,没有设置氮封;
2.3 使用非导电软管转移易燃液体;
2.4 使用平板离心机甩干含易燃溶剂物料,没有氮封,未设置氧气含量与离心机启动的联锁保护;
2.5 使用超过5升的普通塑料桶装易燃液体;
2.6 非导电塑料管或玻璃钢管道输送易燃气体;
2.7 洗涤/吸收塔采用不导静电材料,废气为易燃蒸气或气体;
2.8 没有通过密闭加料器往含有有机溶剂反应釜内加固体粉料;
2.9 可燃气体压缩机、甲乙类易燃液体泵、离心机使用非导电皮带传动;
2.10 易燃易爆区域地坪非导电地坪,人员没有穿导静电工作鞋;
2.11 抽含易燃气体或蒸气的真空机组,没有设置停机后切断机组入口阀门的联锁。
03、反应与物料危险
3.1 通过蒸馏方法从含物料的母液中回收有机溶剂或者浓缩反应液,没有测试母液热稳定性;
3.2 在绝热温升下的反应最高温度大于技术最高温度的反应釜,没有设置高高温联锁切断滴加物料,或者没有采用滴加方式进行反应,对于有分批加入固体物料参与的反应,固体物料没有设置合适的分批加料的工程措施;
3.3 反应釜夹套热源温度超过反应原料或反应产物(包括中间体)分解温度,且分解热超过400J/g,没有设置高高温切断热源;
3.4 在绝热温升下的反应最高温度大于反应原料或反应产物分解温度,且分解热超过400J/g,没有设置高高温切断滴加物;
3.5遇水分解且产生大量气体的反应釜,没有定期检查反应釜的搪瓷破损情况;
3.6 互相反应的物料共用一根废气总管,企业没有对流经车间尾气排空管道的废气做兼容性分析;
3.7 往含有易燃物料的反应釜内通空气或氧气的氧化反应釜,废气出口没有设置在线氧分析仪与进气联锁,没有设置爆破片;
3.8 通过高压钢瓶或管排车减压后的氢气作为加氢反应釜的氢气源,减压阀后安全阀的设定值大于反应釜的设计压力;
3.9 强放热反应,或者原料易分解,原料为桶装时,没有设置防止人员操作失误,把两种物料都打入高位槽或者反应釜;
3.10 自燃类物质如钯碳、雷尼镍、正丁基锂等的操作未采用密闭式的操作;
3.11 存在同一操作区域内的原料投料错误,会造成重大过程安全问题,没有分开设计;
3.12 对于通气反应(例如加氢、氧化、氯化等),没有设置高高压切断气源的联锁;
3.13 对于产生气体的反应,没有设置高高压切断滴加液或者密闭加料器;
3.14 对于在低温情况下反应速度慢导致原料累计的反应,在高温情况下迅速反应且放热量大或者产生气体时,没有设置低温联锁切断滴加进料或固体进料;
3.15 含高能基团物料(如硝基、叠氮基团等),未评估其储存临界尺寸、临界温度、临界时间导致物料发生自燃或者爆炸。
04、粉尘爆炸
4.1 有粉尘爆炸危险的固体中间体或产品,在打粉过程中,未进行N2惰化处理,触发粉尘爆炸危险;
4.2 机械热表面温度高于固体粉尘,导致粉尘自燃着火。
05、固体废弃物存放混乱
5.1 固体废弃物存放地点未分区存放设置,废弃物存在相互反应的风险;
5.2 固体废弃物中残留有易分解的物质或遇到空气自燃的物质,在转移至固废堆场时未进行灭活处理;
5.3 有自分解可能非固体废弃物堆放过高,通风不好,自分解热量无法释放,导致自燃,甚至爆炸。