第四章陶瓷坯体的成型
第四章 陶瓷工艺学 成型

颗粒大小和形状
一般地说颗粒愈细则比表面愈大,每个颗粒表面形成
水膜所需的水分愈多。此外,由细颗粒堆积而形成的毛细管 半径越小,产生的毛细管力越大,可塑性越高。 不同形状颗粒的比表面积是不同的,因而对可塑性的影 响也有差异。
液相数量和性质
可塑法成型基于坯 料有可塑性,成型 方法有雕塑、拉坯、 印坯、旋压、按压、
第一节 一、可塑成型工艺原理
可塑成型
(一)可塑泥团的成型性能
固相、液相及少量气相组成的弹性 —塑性系统。当 泥团受到外力作用而发生变形时,既有弹性性质又有 假塑性性质。生产中控制的两个重要参数:屈服值和 最大变形量。
应 力
σ
(二)成形工艺对流变特性的要求
泥料的流变特性,在成形工艺中,决定着泥料 的成形能力及其操作适应性,并通过屈服值和延展 量这两个重要参数进行描述。
注射、挤制、压制、
车坯和轧膜等操作
法。
三、旋压成形
1. 成形过程 旋压成形也称刀压成形。它是利用型刀和石膏模型进 行成形的一种方法。
成形时,取定量的可塑泥料,投入旋转的石膏模中, 然后将型刀慢慢压入泥料。由于型刀与旋转着的模型存
在相对运动,因此型刀以压挤和刮削的作用机理,随着
模型的旋转而把坯泥沿着石膏模型的工作面上展开形成
结构均匀,有一定的致密度;
成型过程应能多、快、好、省的组织生产。
成型是陶瓷生产过程的一个重要步骤。在成 型过程中形成的某些缺陷(如不均匀性等)仅靠烧结 工艺的改进是难以克服的。成型工艺已经成为制备 高性能陶瓷材料的关键技术,它对提高陶瓷材料的 均匀性、重复性和成品率,降低陶瓷制造成本具有
十分重要的意义。
第四章 成 型
陶瓷核燃料工艺第4章

第4章陶瓷粉末成型原理及工艺4.1 成型前粉末的预处理成型是粉末冶金工艺的第二个基本工序,是使粉末密实成具有一定形状、尺寸、孔隙度及强度的压坯的工艺过程。
为了改善粉末成型过程和制品最终性能,在成型之前一般都要对原料粉末进行预处理,包括:热处理(退火或煅烧)、混合、筛分、加成型剂和润滑剂、制粒等。
1.热处理(退火或煅烧)退火主要是针对金属粉末而言的,其目的为:使金属粉末中的氧化物还原,降低氧含量,提高粉末的纯度;消除金属粉末的加工硬化,恢复粉末的成型塑性(用还原法、机械球磨法、电解法、喷雾法以及羰基离解法等制备的金属粉末通常都要经过退火处理);使某些超细金属粉末表面钝化,以防止发生自燃现象。
例如,一般在300℃、H2气中将电解Cu粉进行退火处理;电解Fe粉或电解Ni 粉通常在700℃、H2气中或真空中进行退火处理。
煅烧主要是针对陶瓷粉末而言的,其目的是:除去所吸附的杂质;使两种或两种以上的混合粉末发生固态反应而形成所需要的相结构;调整粉末的粒度和松装密度以满足压型技术的需要。
对于象TiC、TiB2、UC、UN、U3Si2等一些易氧化和易燃的非氧化物陶瓷超细粉末,最好在低氧手套箱内进行操作,并且在移出手套箱之前要在氧分压可控的电炉内加热进行表面钝化处理。
2.混合混合是指将两种或两种以上不同成分的粉末混合均匀的过程。
而合批一般是指将不同批次生产的、成分相同、但粒度不同的粉末进行混合。
混合方法一般有机械法和化学法两种。
其中,最简单、应用最广泛的是机械法,即将不同成分的粉末机械地掺和均匀而不发生化学反应。
常用的混合机有V 型混合机、(单、双)锥型混合机、螺旋混合机、三维运动混合机、球磨机等。
机械法混料又可分为干混和湿混两种。
加入磨球有利于提高混合效率,甚至还能使粉末粒度减小;但是,有时为了避免金属粉末在混合过程中产生加工硬化,或为了避免金属或陶瓷粉末的粒度发生变化,一般就不用磨球。
干混法几乎对于所有物料都适用。
陶瓷成型技术

项目1:注浆成型技术
一、注浆成型 传统的定义:在石膏模的毛细管力作用下,含有一 定水分的粘土泥浆脱水硬化、成型的过程。 目前:将所有基于坯料具有一定液态流动性的成型 方法统归为注浆成型。 工艺特点: (1)适于成型各种产品,形状复杂、不规则、薄、 体积较大而且尺寸要求不严的器物,如花瓶、汤碗、 椭圆形盘、茶壶等。 (2)坯体结构均匀,但含水量大且不均匀,干燥 与烧成收缩大。
防止粉化的方法有: ①适当降低模型的干燥速度,使水分能够从模型四 周均匀地蒸发; ②采取提前合模的办法,夜间让模型整体干燥,因 模型湿不宜提前合模的,可在芯子上部盖塑料布, 以防止大量的水分从顶点蒸发; ③待模型的外吃浆面刮去一层,增加透气性,使水 分向外吃浆面蒸发。
5、延长石膏模型的使用寿命 1)石膏模型有一定的使用寿命,一般可塑成型用 模型的使用寿命约100-250次,注浆成型用模型只 有50-150次。其损坏原因主要有以下三方面:其 一是模型本身强度不高,易被碰裂或压裂;其二是 模型工作面被坯料中泥粒磨损而报废;其三是注桨 用模型由于模型与坯料桨中电解质起休化学反应造 成模型的毛细孔中与表面上产生硫酸钠析晶,而降 低吸水能力。
石膏模的寿命不但取决于合理的使用,还与制模的 石膏质量和操作工艺过程有关。如石膏粉炒温度过 高或过低,石膏粉颗粒粗大,浇注时加水过多,混 合不均匀,制备好的石膏粉放在潮湿的地方等情况 均会影响模型使用寿命。 2)为了延长石膏模的使用寿命,应正确掌握制造 模型的工艺操作和合理使用外,还可从提高石膏模 的机械强度入手。
各类产品尽管加工方法不同,但是坯体修整是必要 的,不可忽视的,否则就不能保证瓷器半成品质量。 在修坯中也要防止坯体产生缺陷,并修整那些能修 整的带缺陷的坯体。 修坯分为干修和湿修两种方式。 湿修:坯体的水分16~19%。 干修:坯体的水分 < 2%。
陶瓷成型方法
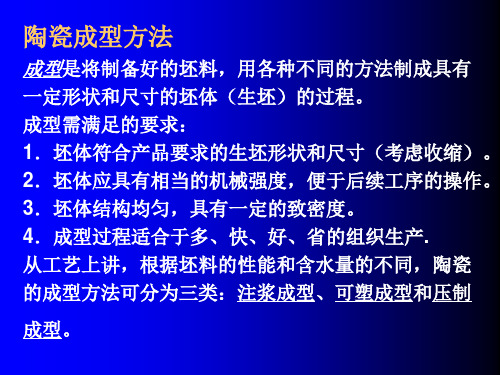
2、热压铸成型工艺
3、热压铸成型工艺 主要工艺参数:
(1) 腊浆温度:60~75℃,温度升 高,则腊浆的粘度下降,坯体致 密,但冷却收缩相应大。温度过 低,则易出现欠注、皱纹等缺陷。 (2) 钢模温度。决定坯体冷却凝固 的速度。一般为20~30℃。 (3) 成型压力:与浆桶深度、料浆 性能有关。压力升高,坯体的致 密度增加,坯体的收缩程度下降。 一般可以采用0.3~0.5 MPa。
3、强化注浆成型方法
(注浆方法的改进)
在注浆过程中人为地施加外力,加速注浆过程的进行,使吸浆 速度和坯体强度得到明显改善的方法。 1) 真空注浆 模具外抽真空,或模具在负压下成型,造成模具内外压力差, 提高成型能力,减小坯体的气孔和针眼。
2)
离心注浆
使模型在旋转情况下进浆,料浆在离心力的作用下紧靠 模壁形成致密的坯体。气泡较轻,易集中在中间最后破 裂排出,故可提高吸浆速度与制品质量。要求:泥浆中 的颗粒分布范围窄,否则大颗粒集中在靠近模型的坯体 表面,而小颗粒集中在坯体内面,造成坯体组织不均匀, 收缩不一致。
2. 滚压成型的主要控制因素 (1) 对泥料的要求:水分低、可塑性好。成型时模具 既有滚动,又有滑动,泥料主要受压延力的作用。要求有 一定的可塑性和较大的延伸量。可塑性低,易开裂;可塑 性高,水分多易粘滚头。阳模滚压和阴模滚压对泥料的要 求有差别。阴模滚压受模型的承托和限制,可塑性可以稍 低,水分可稍多。 (2) 滚压过程控制:分压下(轻)、压延(稳)、抬起 (慢)阶段。 (3) 主轴转速(n1)和滚头转速(n2) :控制生产效率; 对坯料的施力形式,控制坯体的密度均匀和表面光洁。 滚压头的温度热滚压:100~130℃,在泥料表面产生一 层气膜,防止粘滚头,坯体表面光滑。冷滚压:可用塑料 滚压头,如聚四氟乙烯。
陶瓷工艺学习题答案
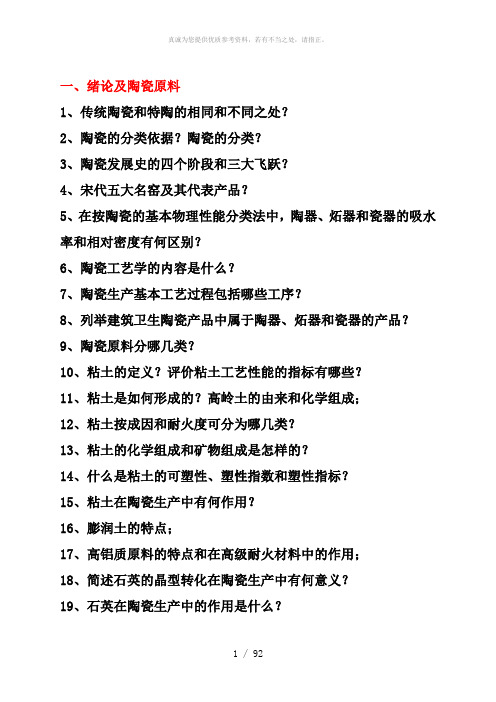
一、绪论及陶瓷原料1、传统陶瓷和特陶的相同和不同之处?2、陶瓷的分类依据?陶瓷的分类?3、陶瓷发展史的四个阶段和三大飞跃?4、宋代五大名窑及其代表产品?5、在按陶瓷的基本物理性能分类法中,陶器、炻器和瓷器的吸水率和相对密度有何区别?6、陶瓷工艺学的内容是什么?7、陶瓷生产基本工艺过程包括哪些工序?8、列举建筑卫生陶瓷产品中属于陶器、炻器和瓷器的产品?9、陶瓷原料分哪几类?10、粘土的定义?评价粘土工艺性能的指标有哪些?11、粘土是如何形成的?高岭土的由来和化学组成;12、粘土按成因和耐火度可分为哪几类?13、粘土的化学组成和矿物组成是怎样的?14、什么是粘土的可塑性、塑性指数和塑性指标?15、粘土在陶瓷生产中有何作用?16、膨润土的特点;17、高铝质原料的特点和在高级耐火材料中的作用;18、简述石英的晶型转化在陶瓷生产中有何意义?19、石英在陶瓷生产中的作用是什么?20、各种石英类原料的共性和区别,指出它们不同的应用领域;21、长石类原料分为哪几类?在陶瓷生产中有何意义?22、钾长石和钠长石的性能比较;23、硅灰石、透辉石、叶腊石(比较说明)作为陶瓷快速烧成原料的特点;24、滑石原料的特点,为什么在使用前需要煅烧?25、氧化铝有哪些晶型?为什么要对工业氧化铝进行预烧?26、氧化锆有哪些晶型?各种晶型之间的相互转变有何特征?27、简述碳化硅原料的晶型及物理性28、简述氮化硅原料的晶型及物理性能。
二、粉体的制备与合成1、解释什么是粉体颗粒、一次颗粒、二次颗粒、团聚?并解释团聚的原因。
2、粉体颗粒粒度的表示方法有哪些?并加以说明。
3、粉体颗粒粒度分布的表示方法有哪些?并加以说明。
4、粉体颗粒粒度测定分析的方法有哪些?并说明原理。
5、粉体颗粒的化学表征方法有哪些?6、粉碎的定义及分类,并加以说明。
7、常用的粉碎方法有哪些?画出三种粉碎流程图。
8、机械法制粉的主要方法有哪些?并说明原理。
9、影响球磨机粉碎效率的主要因素有哪些?10、化学法合成粉体的主要方法有哪些?并说明原理。
《陶瓷工艺原理》学习指南
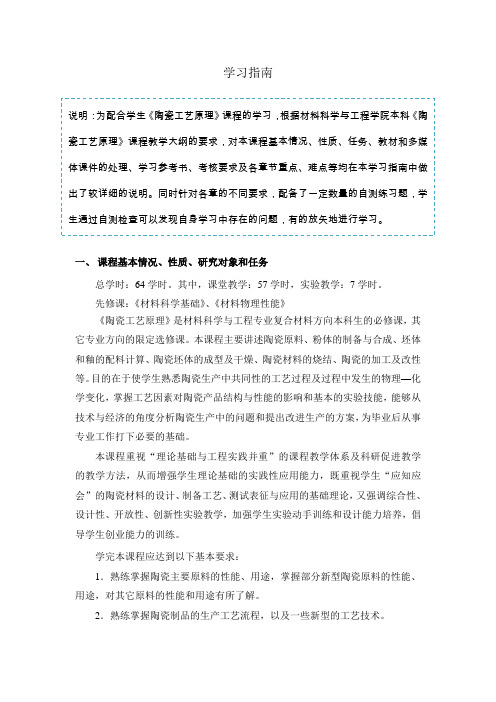
学习指南一、课程基本情况、性质、研究对象和任务总学时:64学时。
其中,课堂教学:57学时,实验教学:7学时。
先修课:《材料科学基础》、《材料物理性能》《陶瓷工艺原理》是材料科学与工程专业复合材料方向本科生的必修课,其它专业方向的限定选修课。
本课程主要讲述陶瓷原料、粉体的制备与合成、坯体和釉的配料计算、陶瓷坯体的成型及干燥、陶瓷材料的烧结、陶瓷的加工及改性等。
目的在于使学生熟悉陶瓷生产中共同性的工艺过程及过程中发生的物理—化学变化,掌握工艺因素对陶瓷产品结构与性能的影响和基本的实验技能,能够从技术与经济的角度分析陶瓷生产中的问题和提出改进生产的方案,为毕业后从事专业工作打下必要的基础。
本课程重视“理论基础与工程实践并重”的课程教学体系及科研促进教学的教学方法,从而增强学生理论基础的实践性应用能力,既重视学生“应知应会”的陶瓷材料的设计、制备工艺、测试表征与应用的基础理论,又强调综合性、设计性、开放性、创新性实验教学,加强学生实验动手训练和设计能力培养,倡导学生创业能力的训练。
学完本课程应达到以下基本要求:1.熟练掌握陶瓷主要原料的性能、用途,掌握部分新型陶瓷原料的性能、用途,对其它原料的性能和用途有所了解。
2.熟练掌握陶瓷制品的生产工艺流程,以及一些新型的工艺技术。
3.掌握陶瓷制品的化学组成、显微结构和产品性能之间的相互关系。
正确理解工艺因素对陶瓷制品显微结构和性能的影响。
4.掌握陶瓷生产的基本实验方法,并能对陶瓷制品的性能进行分析。
二、教材及多媒体课件说明1教材:《陶瓷工艺学》,张锐主编,化学工业出版社,2007。
本教材内容精炼、结构合理、理论性强。
由于计划学时有限,不可能在课堂上对教材所有内容一一进行详细讲解。
因此,学生应该抓住每章节的重点、难点,搞清分析问题、解决问题的基本思路,并注意寻找同类问题间的内存规律。
真正做到举一反三,将问题由“繁”变“易”,将课本由“厚”读“薄”。
2多媒体课件:陶瓷工艺学多媒体教学课件是本校材料基础学科组集体创作的,它综合了图、文、声、像、二维图形、三维动画等多种媒体手段,经科学、合理的重组、整合、加工,构筑了一种虚拟实际场景的教学氛围。
复习思考题解答--陶瓷工艺学

第三篇陶瓷工艺学第一章绪论1 、答:( 1 )传统陶瓷:指以粘士和其它天然矿物为原料,经过粉碎、成型、焙烧等工艺过程所制得的各种制品。
(2 )现代陶瓷:指用陶瓷的生产方法制造生产的无机非金属固体材料和制品。
2 、答:( 1 )按用途来分:①传统陶瓷(普通陶瓷)、②特种陶瓷或新型陶瓷亦称精密陶瓷( 2 )按物理性能分:陶器、炻器、瓷器。
3 、答:吸水率相对密度陶器 3-15% 1.5-2.4炻器 1-3% 1.3-2.4瓷器<1% 2.4-2.64 、答:由陶瓷原料到制成陶瓷制品的整个工艺过程中的技术及其基本原理。
5 、答:有原料选定(进厂)、配料、坯釉料制备、成型、干燥、施釉烧成等工序。
6 、答:陶器:内墙砖;炻器:建筑外墙砖;瓷器:卫生洁具、地砖。
第二章原料1 、答:可塑性原料;熔剂类原料和瘠性类原料。
炻炻2 、答:粘土是一种或多种呈疏松或胶状密实的含水铝硅酸盐矿物的混合物。
3 、答:粘土主要是由铝硅酸盐类岩石,如长石、伟晶花岗岩等经过长期地质年代的自然风化作用或热液浊变作用而形成的。
长石转化为高岭石的反应大致如下:2[KAlSi 3 O 8 ]+H 2 CO 3 ------Al 2 Si 2 O 5 (OH) 4 +4SiO 2 +K 2 CO 34 、答:按成因分类:( 1 )原生粘土。
又称一次粘土、残留粘土,它是由母岩风化后残留在原地形成的。
( 2 )次生粘土。
又称二次粘土、沉积粘土。
按耐火度分类:( 1 )耐火粘土。
其耐火度> 158 0 ℃。
( 2 )难熔粘土。
耐火度为 1350~ 158 0 ℃( 3 )易熔粘土。
耐火度在 135 0 ℃以下。
5 、答:化学成分:(1)SiO 2 : 40-78%(2)AL 2 O 3 : 12~40%(3)R 2 O+RO : R 2 O=0.5~5%, RO=1~6%( 4 ) Fe 2 O 3 、 TiO 2 ≤ 1%( 5 )灼减量。
粘土的矿物组成:( 1 )高岭石( Al 2 O 3 · 2SiO 2 · 2H( 2 )蒙脱石( Al 2 O 3 · 4SiO 2 · nH 2 O , n > 2( 3 )伊利石( K 2 O · 3Al 2 O 3 · 6SiO 2 · 2H 2 O · nH 2 O )。
陶瓷制作中常见的成型方法
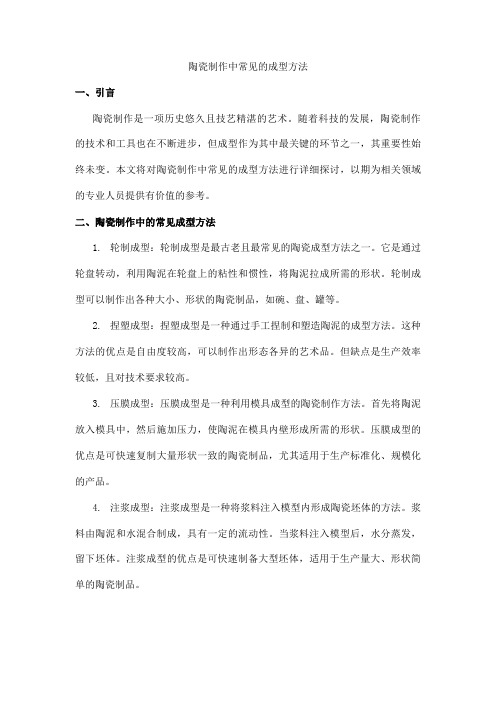
陶瓷制作中常见的成型方法一、引言陶瓷制作是一项历史悠久且技艺精湛的艺术。
随着科技的发展,陶瓷制作的技术和工具也在不断进步,但成型作为其中最关键的环节之一,其重要性始终未变。
本文将对陶瓷制作中常见的成型方法进行详细探讨,以期为相关领域的专业人员提供有价值的参考。
二、陶瓷制作中的常见成型方法1.轮制成型:轮制成型是最古老且最常见的陶瓷成型方法之一。
它是通过轮盘转动,利用陶泥在轮盘上的粘性和惯性,将陶泥拉成所需的形状。
轮制成型可以制作出各种大小、形状的陶瓷制品,如碗、盘、罐等。
2.捏塑成型:捏塑成型是一种通过手工捏制和塑造陶泥的成型方法。
这种方法的优点是自由度较高,可以制作出形态各异的艺术品。
但缺点是生产效率较低,且对技术要求较高。
3.压膜成型:压膜成型是一种利用模具成型的陶瓷制作方法。
首先将陶泥放入模具中,然后施加压力,使陶泥在模具内壁形成所需的形状。
压膜成型的优点是可快速复制大量形状一致的陶瓷制品,尤其适用于生产标准化、规模化的产品。
4.注浆成型:注浆成型是一种将浆料注入模型内形成陶瓷坯体的方法。
浆料由陶泥和水混合制成,具有一定的流动性。
当浆料注入模型后,水分蒸发,留下坯体。
注浆成型的优点是可快速制备大型坯体,适用于生产量大、形状简单的陶瓷制品。
5.热压成型:热压成型是一种利用热压工艺将陶泥压制成型的工艺方法。
该方法能够在较低的压力下制备出密度高、机械强度大的陶瓷制品。
同时,热压成型能够有效地减少坯体中的气泡和裂纹,提高产品质量。
三、成型方法的比较与选择在选择陶瓷成型方法时,需综合考虑以下因素:1.产品形状和尺寸:不同成型方法适用于不同形状和尺寸的陶瓷制品。
例如,轮制成型适用于制作圆形或扁形的陶瓷制品;捏塑成型适用于制作形态各异的艺术品;压膜成型适用于复制大规模、标准化生产的陶瓷制品;注浆成型适用于制备大型、形状简单的陶瓷坯体;热压成型适用于生产高密度、高质量的陶瓷制品。
2.生产效率和成本:不同成型方法的生产效率和成本各不相同。
陶瓷成型工艺原理及方法
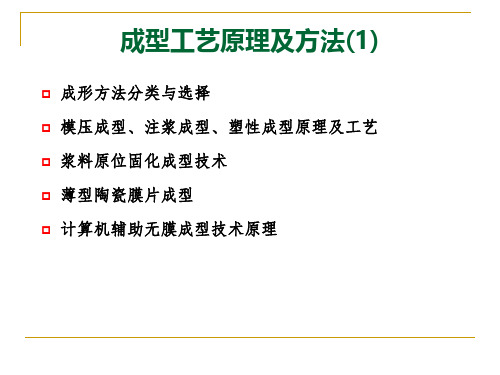
干压成型设备
注浆成型
(1)石膏模注浆成型 利用石膏吸水性的一种成形方法。其过程: (水+粉料)倒入事先制作
好、吸水性很强的石膏模中,浆料中之水分向石膏模壁渗透,因而浆料 便沿石膏模壁固化。到一定厚度后,可倾出剩余浆料。
对注浆成型所用的料浆,必须具备以下性能: 流动性和稳定性好(不易分层和沉淀)、触变性要小、含水量尽
加压方式与压力分布
单向加压 一端加压,受压面密度大,未加压端密度小
双向加压:坯体两边受压,两端密度大,中间密度小 改进的双向加压:
(1) 先上加压,后下加压 (2) 加润滑剂并造粒
模压成型工艺参数控制及特点
➢ 成型压力 取决于坯体的形状、高度、粘合剂种类与用量、粉体的流动性、
坯体的致密度 ➢ 加压速度与保压时间
从工艺上来讲,根据坯料的性能和含水量的不同,陶瓷的成型方 法可分为三类:注浆成型、可塑成型和压制成型
成型 方法
成型方法分类
注浆成型法
热法(热压铸法):钢模
冷法
常压冷法注浆 加压冷法注浆 抽真空冷法注浆
石膏模
坯料含水量 30%~40%
有模 可塑成型法 无模
坯料含水量18%~26%
干压成型法:使用钢模,坯料含水量6%~8% 等静压成型法:使用橡皮模,坯料含水量1.5%~3%
4. 加热装置
5.9阀门
6. 活塞
7. 模具
8. 温度计
10.脚控踏板 11. 压缩空气进口
蜡浆制备
熟瓷粉 石蜡 硬脂酸
预热
60~80℃
熔化
12成腊饼存放
要点1: 热压铸成型必须用熟料,目的: (1) 保证铸浆有良好的 流动性;(2) 减少坯体的收缩率和变形。 要点2: 石蜡是亲油而憎水的, 而瓷粉与油之间缺乏很大的亲和 力,需加入硬脂酸或油酸一类两性物质。
【精品文章】氮化铝(AlN)陶瓷常见的坯体成型与烧结方法概述
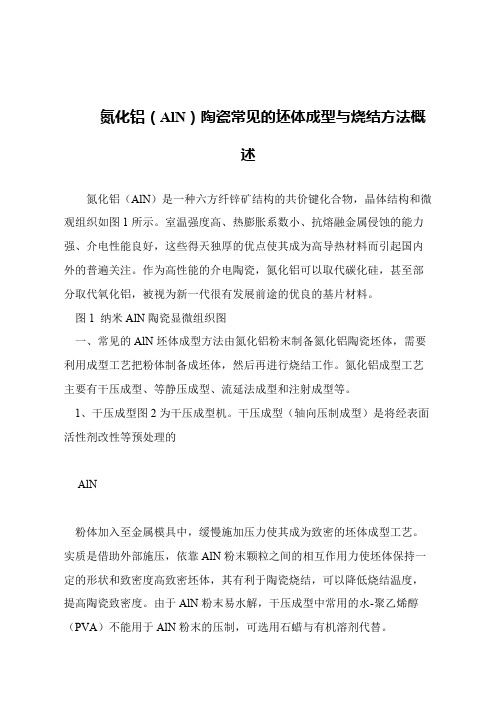
氮化铝(AlN)陶瓷常见的坯体成型与烧结方法概
述
氮化铝(AlN)是一种六方纤锌矿结构的共价键化合物,晶体结构和微观组织如图1所示。
室温强度高、热膨胀系数小、抗熔融金属侵蚀的能力强、介电性能良好,这些得天独厚的优点使其成为高导热材料而引起国内外的普遍关注。
作为高性能的介电陶瓷,氮化铝可以取代碳化硅,甚至部分取代氧化铝,被视为新一代很有发展前途的优良的基片材料。
图1 纳米AlN陶瓷显微组织图
一、常见的AlN坯体成型方法由氮化铝粉末制备氮化铝陶瓷坯体,需要利用成型工艺把粉体制备成坯体,然后再进行烧结工作。
氮化铝成型工艺主要有干压成型、等静压成型、流延法成型和注射成型等。
1、干压成型图2为干压成型机。
干压成型(轴向压制成型)是将经表面活性剂改性等预处理的
AlN
粉体加入至金属模具中,缓慢施加压力使其成为致密的坯体成型工艺。
实质是借助外部施压,依靠AlN粉末颗粒之间的相互作用力使坯体保持一定的形状和致密度高致密坯体,其有利于陶瓷烧结,可以降低烧结温度,提高陶瓷致密度。
由于AlN粉末易水解,干压成型中常用的水-聚乙烯醇(PVA)不能用于AlN粉末的压制,可选用石蜡与有机溶剂代替。
实验 陶瓷坯体的干压成形
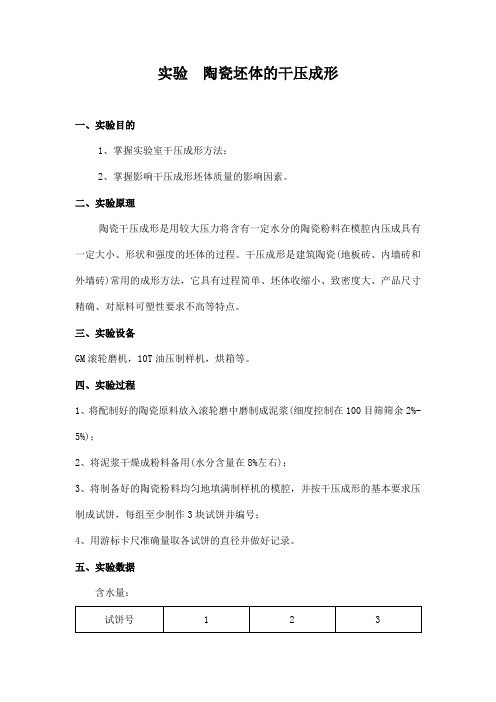
实验陶瓷坯体的干压成形
一、实验目的
1、掌握实验室干压成形方法;
2、掌握影响干压成形坯体质量的影响因素。
二、实验原理
陶瓷干压成形是用较大压力将含有一定水分的陶瓷粉料在模腔内压成具有一定大小、形状和强度的坯体的过程。
干压成形是建筑陶瓷(地板砖、内墙砖和外墙砖)常用的成形方法,它具有过程简单、坯体收缩小、致密度大、产品尺寸精确、对原料可塑性要求不高等特点。
三、实验设备
GM滚轮磨机,10T油压制样机,烘箱等。
四、实验过程
1、将配制好的陶瓷原料放入滚轮磨中磨制成泥浆(细度控制在100目筛筛余2%-5%);
2、将泥浆干燥成粉料备用(水分含量在8%左右);
3、将制备好的陶瓷粉料均匀地填满制样机的模腔,并按干压成形的基本要求压制成试饼,每组至少制作3块试饼并编号;
4、用游标卡尺准确量取各试饼的直径并做好记录。
五、实验数据
含水量:
六、实验分析
讨论分析影响陶瓷干压成形坯体性质的因素。
陶瓷工艺学---第四章 陶瓷的显微结构与性质
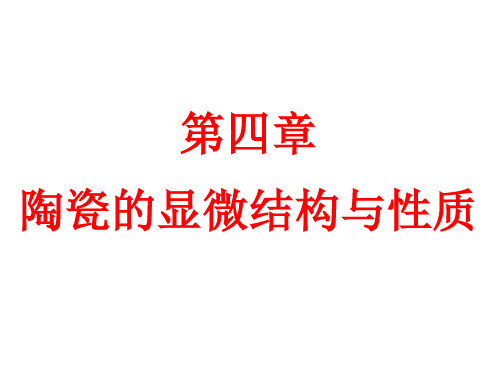
5.高温色釉 5.1 青釉 是我国历史上最早出现的颜色釉。各地青釉质感不同,原因 是釉层结构不同。 1)钧窑青釉 釉面乳浊 高硅质釉中含有磷酸盐,产生液-液分相乳浊。 2)龙泉青瓷、汝官窑青瓷、枢府青白瓷釉 3)临汝青釉瓷 透明 釉面乳浊 高铝低硅釉玻璃中含有小气泡和细小钙长石晶体产生乳浊。
釉层中无晶体析出,只有少量大气泡存在。
晶相强度 > 普通玻璃相强度 减少玻璃相的含量,提高玻璃相的强度,瓷坯的强度提高。 特种陶瓷生产,对于添加剂形成的少量玻璃相进行晶化处理。
1.5 气相对强度的影响
通过对多孔陶瓷的研究,得到气孔率与强度的关系。
经验公式:
= 0 exp( p)
式中:P——气孔率,%;
0——P=0时的强度,Mpa;
铝质瓷中引入氧化镁0.5~1%。
3)晶型与晶粒形貌对强度的影响
常温下的晶型转变,导致瓷坯的强度降低;
一种晶体以不同的晶型存在时,晶体的形状不同,强度不同; 一种晶体以不同的形状(球形、柱状)存在,瓷坯强度不同;
4)晶界对强度的影响
晶界愈多,抑制裂纹的扩展,界面上如有气孔降低强度。
1.4 玻璃相对强度的影响
=Kd
式中:K——与晶体结构及材料显微结构有关的比例常数。
d——晶粒直径。
——与材料特性和实验条件有关的经验常数。 =1/8~1 随d的增大而增大。 P254~255表4-21、图4-32、4-33 各种陶瓷材料强度与粒径关系
细晶粒提高强度机理:
1. 晶粒愈细小,比表面积愈大,晶界愈多,裂纹扩展阻力愈大
第四章 陶瓷的显微结构与性质
主要内容
1.坯体的显微结构
2.釉层的显微结构 3.釉层的物理化学性质
4.陶瓷性能的控制
陶瓷的成型、施釉及烧成 52页PPT文档
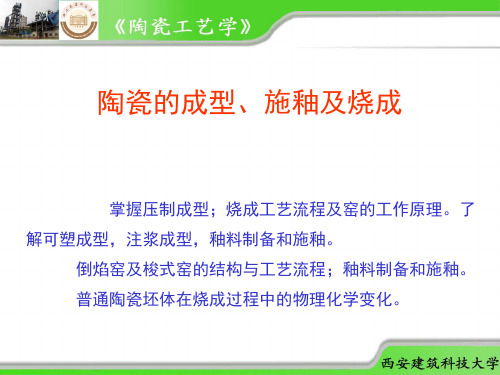
一般用烧成温度曲线来表示,主要包括各阶段的升温速 度、最 高烧成温度(止火温度)、保温时间和冷却速度。
(2)气氛制度 氧化焰:空气供给充足,燃烧完全时产生的一种无烟而透明的火焰, 氧含量在弱氧化焰时2~5%,强氧化焰时大于5% 还原焰:空气供给不充足,燃烧不完全时产生的一种有烟而混浊的 火焰,此时空气过剩系数0.7~0.9
d. 刷釉法:多用于工艺瓷的施釉及补釉
e. 气化施釉、荡釉、滚釉等
五、干燥与烧成
1、陶瓷制备过程中需要干燥的环节
(1)由泥浆或泥饼制备成型粉料;
(2)成型后坯体的干燥; (3)施釉前的干燥; (4)施釉后的干燥。
2、陶瓷坯体的干燥过程
水的存在状态
晶体配位水
化学结合水 (结晶水)
层间水
物理结合水
自由水(游离水、机械结合水)
二次烧成特点:
(1)有利于提高釉面光泽度和白度 (2)素烧后坯体吸水性能改善,容易上釉,且釉面质量好 (3)经素烧后坯体强度提高,降低半成品破损率
(4)釉烧时收缩较小,有利于Байду номын сангаас止产品变形
(5)素烧后不合格的素坯可返回到配料中,提高了釉烧的合 格率,减少了原料损失
5、坯体烧成的四个阶段
6、烧成制度:
几个关键参数:零压位、预热带最大负压、窑头微正压、冷却 带压力
7、烧成窑炉
根据烧成过程连续与否分为间歇式窑、连续式窑。
连续式窑内分为预热带、烧成带、冷却带,使用最广泛 的是隧道窑和辊道窑。
本章学习小结
陶瓷的原料 可塑料的制备及成型 注浆料的制备及成型 压制粉料的制备及成型 釉料的制备及施釉 陶瓷的干燥及烧成
注浆成型的方法 a. 空心注浆(单面注浆) b. 实心注浆(双面注浆) c. 压力注浆 d. 离心注浆 e. 真空注浆
坯体成型

2.3.4 热压铸成型 特殊的注浆成型方法,用于瘠性料的特种瓷,电子陶瓷, 氧化物陶瓷和金属陶瓷。 以有机结合剂为分散介质,固体颗粒为分散相,在一定 温度(70—85)配成料浆,在金属模具中成型。 2.3.4.1 工艺过程 (1)、制蜡浆 • 蜡浆组成:粉料,塑化剂(石蜡),表面活性剂(油酸) • 粉料的制备: • 预烧(目的:降低烧成收缩,保证产品规格。提高料浆的 流动性,减少石蜡的用量) • 粉料要求: • 细度:万孔筛余2—3%。颗粒小,流动性差,石蜡用量多。 • 含水率:小于0.5%
第四章 坯体的成型
第一节 注浆成型 第二节 压制成型 第三节 可塑成型
1
成型方法的分类:
1、注浆成型 30%—40% 2、可塑成型 18%—25% 有模和无模 3、干压成型 6%—8% 4、等静压成型 1.5%—3% 湿等静压和干等静压
成型方法的选择:
1、产品的形状,大小,厚薄。 2、坯料的工艺性能。 3、产品的产量和质量。 4、保证质量的前提下,成型设备简单,劳动强度要小,劳动 条件好,经济效益好。
4
•物理脱水过程
•化学凝聚过程:
(1)泥浆溶解少量的CaSO4 (2) CaSO4和泥浆中的Na—粘土、硅酸钠发生离子交换。 Na—粘土+ CaSO4—— Ca—粘土 +CaSiO3 +Na2SO4 近石膏模表面的Na—粘土变为Ca—粘土,泥浆聚沉在 石膏模壁上。 Na2SO4 是水溶性的,进入毛细管中,烘干模型时, 以白色丛毛状结晶的形态析出。
16
17
18
19
20
21
22
23
24
第二节 压制成型
25
2.1 干法压制的基本原理
1、粉料的基本性质 (1) 粒度和粒度的分布 V=a×b×c=4πr3/3 即该颗粒等效半径为:
- 1、下载文档前请自行甄别文档内容的完整性,平台不提供额外的编辑、内容补充、找答案等附加服务。
- 2、"仅部分预览"的文档,不可在线预览部分如存在完整性等问题,可反馈申请退款(可完整预览的文档不适用该条件!)。
- 3、如文档侵犯您的权益,请联系客服反馈,我们会尽快为您处理(人工客服工作时间:9:00-18:30)。
第一节 概述
陶瓷的成型技术对于制品的性能具有重要影响。新型陶瓷成型方法的选择, 应当根据制品的性能要求、形状、尺寸、产量和经济效益等综合确定。
2020/5/21
陶瓷材料学
4.1.1成型方法分类
成型方法
注浆成型法 可塑成型法
热法(热压注法):钢模
冷法 有模 无模
常压冷法注浆 加压冷法注浆 抽真空冷法注浆
空心注浆(单面注浆)
陶瓷材料学
2020/5/21
实心注浆(双面注浆)
陶瓷材料学
2、注浆用石膏模的主要缺陷 (1)开裂 (2)气孔与针眼 (3)变形 (4)塌落 (5)粘膜
2020/5/21
陶瓷材料学
第三节 干压成型
4.3.1 干法压制的基本原理
1、粉料的基本性质 (1) 粒度和粒度的分布
V=a×b×c=πr3 即该颗粒等效半径为:
石膏模
坯料含水量18~26%干Biblioteka 成型法:使用钢模 ,坯料含水量6~8%
坯料含水量 30~40%
等静压成型法:使用橡皮膜,坯料含水量1.5~3%
2020/5/21
陶瓷材料学
4.1.2 成型方法的选择
以图纸或样品为依据,确定工艺路线,选择合适的成型方法。选择成型 方法时,要从下列几方面来考虑:
(1)产品的形状、大小、厚薄等。 (2)坯料的工艺性能。 (3)产品的产量和质量要求。 (4)成型设备要简单,劳动强度要小,劳动条件要好。 (5)技术指标要高,经济效益要好。
4.3.3.5 弹性后效
加荷卸荷压力与变形的关系示意图
2020/5/21
弹性后效: 外力取消后,弹 性力引起坯体的 膨胀的现象!
陶瓷材料学
4.3.4影响层裂的因素及防止方法
1、气体的影响。 2、坯体水分的影响。 3、加压次数对层裂的影响。 4、压制时间及压力的影响。
2020/5/21
陶瓷材料学
第四节 可塑成型
2020/5/21
陶瓷材料学
第二节 注浆成型
注浆成型工艺简单,适于生产一些形状复杂且不规则、外观尺寸要求不严格、 壁薄及大型厚胎的制品。
4.2.1影响泥浆流动性的因素
1、固相的含量、颗粒大小和形状的影响 2、泥浆温度的影响 3、粘土及泥浆处理方法的影响 4、泥浆的pH值的影响
2020/5/21
陶瓷材料学
4.2.2注浆过程的物理化学变化
1.注浆时的物理脱水过程 2.注浆时的化学凝聚过程:
Na-粘土+CaSO4+Na2SiO3→Ca-粘土+CaSiO3↓+Na2SO4
2020/5/21
陶瓷材料学
4.2.3陶瓷坯体的注浆成型
1、基本注浆方法 :空心注浆(单面注浆) 实心注浆(双面注浆)
2020/5/21
坯体密度与压力的关系
2020/5/21
坯体密度变化率与压力的关系
陶瓷材料学
影响因素: 1 振动或粒度控度 2 增加压力 3 加压时间 4 减少摩擦 5 形状、尺寸和粉体性质
2020/5/21
密度 孔隙率
陶瓷材料学
4.3.2.2 强度的变化
第一阶段强度并不大 第二阶段强度直线提高 第三阶段强度变化也较平坦
2020/5/21
陶瓷材料学
2、热压铸成型工艺
2020/5/21
陶瓷热蜡铸工艺流程图
陶瓷材料学
3、热压铸成型的特点
热压铸成型适用于以矿物原料、氧化物、氮化物等为原料的新型陶瓷 的成型,尤其对外形复杂、精密度高的中小型制品更为适宜。其成型设备 不复杂,模具磨损小,操作方便,生产效率高。
热压铸成型的缺点是,工序较繁,耗能大,工期长,对于壁薄,大而 长的制品不宜采用。
2020/5/21
陶瓷材料学
(2)粉料的堆积性质
等径球体堆积形式及孔隙率
2020/5/21
陶瓷材料学
(3) 粉料的拱桥效应(或称桥接)
2020/5/21
陶瓷材料学
2、粉料的流动性
F=
N
c os
s in
粉料自然堆积的外形
2020/5/21
陶瓷材料学
4.3.2压制过程坯体的变化
4.3.2.1 密度的变化
可塑成型主要是通过胶态原料制备、加工,从而获得一定形状的陶瓷坏体。
4.4.1可塑成型分类
可塑成型是古老的一种成型方法。我国古代采用的手工拉坯就是最原始的可塑 法。常用的可塑成型方法主要是挤压成型、热压铸成型、胶态成型等。
2020/5/21
陶瓷材料学
1、挤压成型 挤压成型时应该注意以下工艺问题: (1)挤制的压力; (2)挤出速率; (3)挤出管子时,管壁厚度必须能承受本身的重力作用和适应工艺要求; (4)挤压成型的缺陷。
2020/5/21
陶瓷材料学
4.4.2
造粒类型 熔融成行 回转筒型 回转盘型 析晶型
原料状态 熔融液 粉末、液体 粉末、液体 溶液
喷雾干燥型
溶液、泥浆
造 喷雾冷水型 粒 成 喷雾空冷型 型
液相反应型
烧结炉型
挤压成型
熔融液 熔融液 反应液 粉末 溶解液糊剂
板上滴下型
熔融液
铸造型
压片型
机械型
2020/5/21
2020/5/21
坯体强度与压力的关系
陶瓷材料学
4.3.2.3 坯体中压力的分布 坯体中压力分布不均匀,H/D比值愈大,则不均匀分布现象愈严重。
轴力图
2020/5/21
F(x)=-F-ρg A x
陶瓷材料学
4.3.3加压制度对坯体质量的影响
4.3.3.1 成型压力的影响
P= P 1+ P 2 P 1是静压力,克服粉体的阻力; P 2是消耗压力,粉体对模壁的消耗。
2020/5/21
陶瓷材料学
4.3.3.2 加压方式的影响
加压方式和压力分布关系图 (横条线为等密度线)
a-单面加压;b-双面同时加压;c-双面先后加压;d-四面加压
2020/5/21
陶瓷材料学
4.3.3.3 加压速度的影响
开始时压力小些,加压速度稍快,利于排 气;接着高压,缓慢加压,即减慢加压速 度,延长时间;可以采用多次加压,逐步 放气,防止气体导致的裂纹;多次换向加 压,同时振动粉料。
乳化型
熔融液 粉末 板棒
造粒机理 冷却、结晶、 削除
毛细管吸附力、化学 反应
毛细管吸附力、化学 反应
结晶化、冷却
粒子形状 板状、 花料状 球状
球状
各种形状
主要适用领域
“一轻、二重、慢提起”
2020/5/21
陶瓷材料学
4.3.3.4 添加剂的选用三原则: (1)减少粉料颗粒间及粉料与模壁之间的摩擦,这种添加物又称润滑剂; (2)增加粉料颗粒之间的粘结作用,这类添加物又称粘合剂; (3)促进粉料颗粒吸附、湿润或变形,通常采用表面活性物质。
2020/5/21
陶瓷材料学