如何管控工厂UPPH
如何管控工厂UPPH
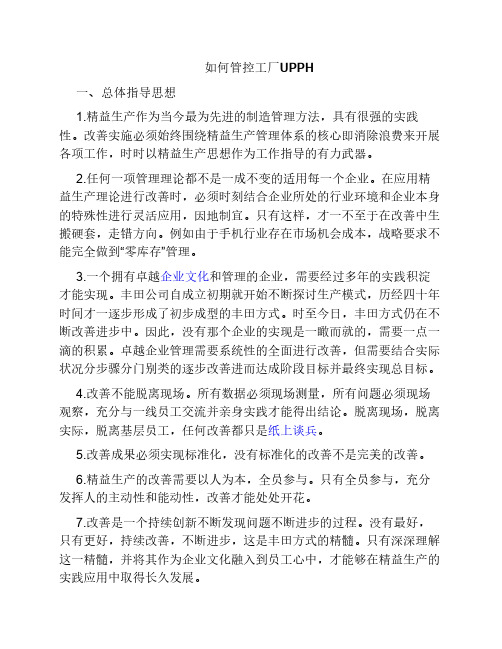
如何管控工厂UPPH一、总体指导思想1.精益生产作为当今最为先进的制造管理方法,具有很强的实践性。
改善实施必须始终围绕精益生产管理体系的核心即消除浪费来开展各项工作,时时以精益生产思想作为工作指导的有力武器。
2.任何一项管理理论都不是一成不变的适用每一个企业。
在应用精益生产理论进行改善时,必须时刻结合企业所处的行业环境和企业本身的特殊性进行灵活应用,因地制宜。
只有这样,才一不至于在改善中生搬硬套,走错方向。
例如由于手机行业存在市场机会成本,战略要求不能完全做到“零库存”管理。
3.一个拥有卓越企业文化和管理的企业,需要经过多年的实践积淀才能实现。
丰田公司自成立初期就开始不断探讨生产模式,历经四十年时间才一逐步形成了初步成型的丰田方式。
时至今日,丰田方式仍在不断改善进步中。
因此,没有那个企业的实现是一瞰而就的,需要一点一滴的积累。
卓越企业管理需要系统性的全面进行改善,但需要结合实际状况分步骤分门别类的逐步改善进而达成阶段目标并最终实现总目标。
4.改善不能脱离现场。
所有数据必须现场测量,所有问题必须现场观察,充分与一线员工交流并亲身实践才能得出结论。
脱离现场,脱离实际,脱离基层员工,任何改善都只是纸上谈兵。
5.改善成果必须实现标准化,没有标准化的改善不是完美的改善。
6.精益生产的改善需要以人为本,全员参与。
只有全员参与,充分发挥人的主动性和能动性,改善才能处处开花。
7.改善是一个持续创新不断发现问题不断进步的过程。
没有最好,只有更好,持续改善,不断进步,这是丰田方式的精髓。
只有深深理解这一精髓,并将其作为企业文化融入到员工心中,才能够在精益生产的实践应用中取得长久发展。
二、实施方案指导框架结合企业自身实际状况,借鉴国内外的精益生产理论指导和实践案例研究,研究将精益生产的各钟软硬件技术进行分类,提出了新的改善模型,作为公司推行精益生产管理的指导框架。
改善模型称为新“TPS”模型,T代表技术(Technology ),P代表人员(Person ),S代表系统(System)。
UPPH管理

30如何才能管控工厂UPPH如何管控工厂UPPH;如何管控工厂UPPHUPPH是unitsPerH;产量,UPP H=600÷(50×8)=1。
5;6。
精益生产的改善需要以人为本,全员参与;二、实施方案指导框架结合企业自身实际状况,借鉴国;(二)效率提升1。
效率革新指导框架通过研究之前的;嫁动率提升、操作效率提升、线平衡改善、合格率提升;2。
生产效率损失分析借鉴优秀工厂管理的实践经验,;如何管控工厂UPPH如何管控工厂UPPH UPPH是units Per Hour Per Person 单位人时产能的缩写,是公司作为衡量员工工作绩效的重要指标。
UPPH 是衡量员工单位时间工作量的一种绩效指标。
UPPH 计算方式如下:UPPH=工作量/(投入时间*投入人力)。
(投入时间以小时计算)。
先算出总工时(人数×工时),再用总产量除以总工时,例:50 人,8 小时,600产量,UPPH=600 ÷(50×8)=1.5。
由上式可见,员工绩效与UPPH 成正比关系。
大多数国际公司都以UPPH 作为员工绩效评比的重要指标。
UPH (uni ts per hour)单位小时产能,指每小时的产量,UPH=年生产量/(12*月工作日*日工作小时)或UPH=日生产量/日工作小时;UPPH(units per people per hour)人均时产能,指每小时每个人的产能,UPPH=年生产量/(12 月*月工作日*日工作小时*工人人数)或UPPH=日生产量/(日工作小时*投入人工). UPH 和UPP H 算出来的都是某个工位的产能。
先进的管控工厂UPPH 方案:一、总体指导思想1。
精益生产作为当今最为先进的制造管理方法,具有很强的实践性。
改善实施必须始终围绕精益生产管理体系的核心即消除浪费来开展各项工作,时时以精益生产思想作为工作指导的有力武器。
2。
任何一项管理理论都不是一成不变的适用每一个企业。
如何管控工厂 UPPH
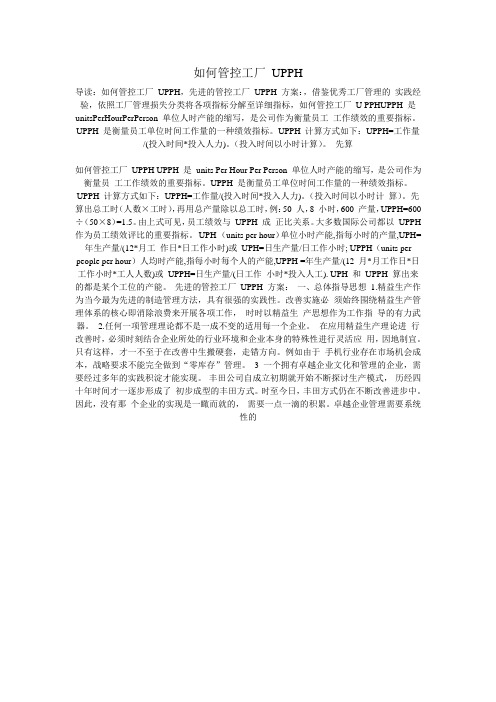
如何管控工厂UPPH导读:如何管控工厂UPPH,先进的管控工厂UPPH 方案:,借鉴优秀工厂管理的实践经验,依照工厂管理损失分类将各项指标分解至详细指标,如何管控工厂U PPHUPPH 是unitsPerHourPerPerson 单位人时产能的缩写,是公司作为衡量员工工作绩效的重要指标。
UPPH 是衡量员工单位时间工作量的一种绩效指标。
UPPH 计算方式如下:UPPH=工作量/(投入时间*投入人力)。
(投入时间以小时计算)。
先算如何管控工厂UPPH UPPH 是units Per Hour Per Person 单位人时产能的缩写,是公司作为衡量员工工作绩效的重要指标。
UPPH 是衡量员工单位时间工作量的一种绩效指标。
UPPH 计算方式如下:UPPH=工作量/(投入时间*投入人力)。
(投入时间以小时计算)。
先算出总工时(人数×工时),再用总产量除以总工时,例:50 人,8 小时,600 产量,UPPH=600÷(50×8)=1.5。
由上式可见,员工绩效与UPPH 成正比关系。
大多数国际公司都以UPPH 作为员工绩效评比的重要指标。
UPH (units per hour)单位小时产能,指每小时的产量,UPH=年生产量/(12*月工作日*日工作小时)或UPH=日生产量/日工作小时; UPPH(units per people per hour)人均时产能,指每小时每个人的产能,UPPH =年生产量/(12 月*月工作日*日工作小时*工人人数)或UPPH=日生产量/(日工作小时*投入人工). UPH 和UPPH 算出来的都是某个工位的产能。
先进的管控工厂UPPH 方案:一、总体指导思想1.精益生产作为当今最为先进的制造管理方法,具有很强的实践性。
改善实施必须始终围绕精益生产管理体系的核心即消除浪费来开展各项工作,时时以精益生产思想作为工作指导的有力武器。
2.任何一项管理理论都不是一成不变的适用每一个企业。
如何管控工厂UPPH
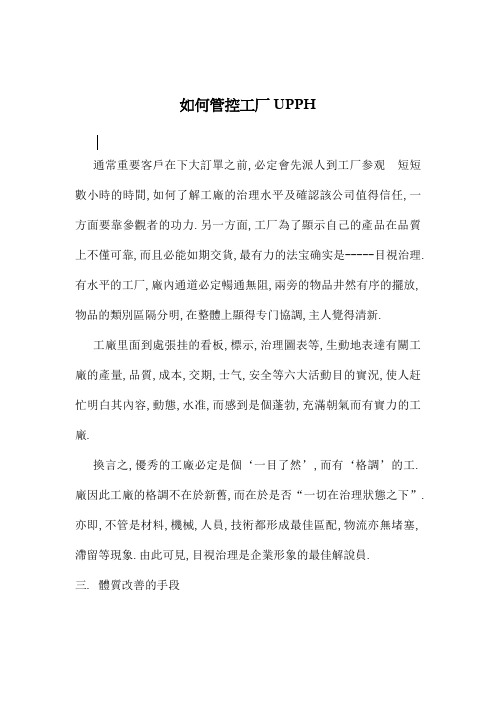
如何管控工厂UPPH通常重要客戶在下大訂單之前,必定會先派人到工厂参观短短數小時的時間,如何了解工廠的治理水平及確認該公司值得信任,一方面要靠參觀者的功力.另一方面,工厂為了顯示自己的產品在品質上不僅可靠,而且必能如期交貨,最有力的法宝确实是-----目視治理.有水平的工厂,廠內通道必定暢通無阻,兩旁的物品井然有序的擺放,物品的類別區隔分明,在整體上顯得专门協調,主人覺得清新.工廠里面到處張挂的看板,標示,治理圖表等,生動地表達有關工廠的產量,品質,成本,交期,士气,安全等六大活動目的實況,使人赶忙明白其內容,動態,水准,而感到是個蓬勃,充滿朝氣而有實力的工廠.換言之,優秀的工廠必定是個‘一目了然’,而有‘格調’的工.廠因此工廠的格調不在於新舊,而在於是否“一切在治理狀態之下”.亦即,不管是材料,機械,人員,技術都形成最佳區配,物流亦無堵塞,滯留等現象.由此可見,目視治理是企業形象的最佳解說員.三. 體質改善的手段目視治理通過生動的圖畫,醒目的顏色,如:海報,治理活動板,安全標誌等方式塑造‘一目了然’的工作場所,使信息共有化,視覺化且正確地傳達給相關人員.以形成一致的共識及采取杰出的行動,縮短治理循環週期(PDCA)時間.假如1-2,對於經過觀察后的事態,如屬於高難度的作業則由技術人員處理,反之,屬於低難度的作業則由作業員自選處理.萬一作業員未能擁有足夠的知識,此時只要保持現狀,依異常聯絡管道(圖1-3)聯絡相關人員協助處理,也不失為正確的行為.因此,目視化的實施如限度樣本,重點標準,看板及異常聯絡管道等可讓作業員采取杰出的行為.,使異常造成的損害降低至最低程度.白天作業員班長組長生技課,課長副理經理廠長 1夜間作業員班長組長課長,生技課副理經理廠長圖1-3 異常聯絡管道舉世聞名的丰田生產方式,确实是利用目視治理進行作業標準化,異常檢出,缘故追究,改善活動等,諸如燈號与呼出燈,標準作業票,看板,數位式顯示看板,產品放置區顯示看板與庫存品顯示看板等,借此達到自動化的境域,讓監督者及作業員自動發掘不對勁的地点,進而矯正異常.因此,目視治理為生產治理的重要輔助工具之一,其作用表現在:(一)促進治理異常改善不管誰看到目視治理的工具,都能清晰不對勁的地点,促其盡早採取改善對策,設法使損失降至最低程度.(二)保持生產的彈性作業員只要稍用眼睛看一下目視治理的工具之后,就能赶忙清晰物流的狀態,因此,每一位作業員都清晰目前的工作量約有多少,下一步應該做什麼工作,能做到自主操纵並採取適當的行動調整目前的工作量.(三)實施預防治理工廠日常治理活動中,對異常問題的處理方式一样為:1.預防治理2.即時治理3.事後治理例如,生產部門因某种缘故移動一臺設備,但工廠的生技部門並未徹底清理露出地面的固定螺絲,結果造成有人走過時未留意而摔傷,事發后赶忙將傷者送醫院急救,這确实是即時治理.生技部門為了防止再次發生類似的事件,赶忙派人將地面清理乾淨,這确实是事后治理.假如當時有人走過時警覺到螺絲露出地面太危險,赶忙要求生技部門派人將螺絲拔掉,确信不會發生上述俊事件,這确实是預防治理.預防治理是未來治理的必定趨勢,為使預防治理能在生產現場中徹底實施,必須徹底實施生產現場的目視治理,形成用眼睛看馬上能發現異常,並能迅速擬定對策的現場.即使平時不在了解生產現場情況的總經理或部長,經理等,只要走到現場看看,也會清晰現場的情況而指出問題的重點與對策.預防治理在許多工廠已普遍應用.如:1.安全方面的危險預知活動2.品質制程管制3.設備診斷技術豐田的JIT生產方式确实是最好的例証,它活用看板方式,多能工化,目視治理,燈號操纵方式,卡入式前置作業等治理手段,充公縮短治理循環(PDCA)時間,以及將事後治理體系轉換於預防治理體系.其轉換方式下:由年度,季度,月度,每周,每日治理每班治理每小時治理事后治理每秒治理預防治理(加速PDCA的時間) 即時治理為了徹底實施預防治理,確實把握制程上的問題點,了解現狀是否正常,要有效利用各種預防治理的資料,如:1.各種標準,如檢驗,操作標準.2.管制圖3.完備規格書,設計卡,制令單等內容,並定期檢討與修訂,幸免有遺漏或彼此間有矛盾,出入之處.4.储存過去的記錄諸如產品的試驗成績表,檢驗報告,日報表,查核表,不良記錄,保養點檢簿等.通過對上述資料預防先充分的研究,進一步採取以下行動:1.點檢目前設備及儀表的情況通過對儀表的觀測,發掘設備故障前的征兆與傾向,諸如異常的溫度,異常的聲音,異常的味道,異常的振動,異常的泄漏(油,水,蒸汽等).同時有關電壓,電流,速度,壓力等操作條件,由儀表上亦可看出是否超出設定範圍之外,事先採取對策,防止設備重大故障,人員重大公傷或產品大量不良.2.做好交接班工作前一班次對產品生產与設備運轉進行監控並詳細記錄,按照記錄進行面對面交班.专门是重要的產品,連續性生產的產品更要執行,另外,在日夜倒班時,若有時間上的間隔,務必詳細填交接記錄.3.作業前的點檢1.產品(含半成品)經過路徑的點檢,確認路徑是否順暢,平穩?有無卡死,移位等現象,以免產品壓,刮傷,變形等,借此確保品質,2.計測器的點檢,諸如查核分厘卡的精度,查核溫度計等儀表的指針能否全程擺動,3.閥門開關的正誤杳核(開關標簽的確認)4.查核剎車機能4.定時舉行朝會利用重點訓示,將提醒及注意事項簡單扼要的寫在一張A4的紙上,內容再輔以漫畫,照片,示意圖等,每周利用一次約30-60分鐘的周會,或每日一次約10-15分鐘的朝會,對作業員進行諸如安全,保養,品質等方面在職訓練5.善用目視治理(諸如標簽,標示,顏色等)達到認識,警告,戒备,判定等功能6.巧思防呆措施為防止作業員因失神,忘記或習慣而犯錯,幸免造成重大的損害,利用電气或機械操纵方式,所設計的一种措施,諸如安全島,安全蓋的電氣連鎖等裝置.四. 工廠目視治理對象(一)生產現場的目視治理生產現場的目視治理,即對生產現場的進度狀況,物料或半成品的庫存量,品質不良,設備故障,停機缘故等,以視覺化的工具,進行預防治理.使任何人都能了解好與壞的狀態,即使新進人員也能专门快縮小作業上的品質差異.一样工廠的業務流程差不多上從同意訂單開始進行生產,直至產品出貨為止.在產品實現的過程管制中,必須滿足下列條件:1.按照計劃需要的日期,投入品質優良的物料,2.嚴格執行產品製造的標準,規格,條件3.生產設備保持正常狀態4.作業員按作業標準生產5.生產進度籤預定的交期生產現場的目視治理正是針對上述項目進行治理,改善,因此,目視治理的對象涵蓋(產量,品質,成本,交期,安全,士气),即:1.作業治理一. 目視作業標準:利用照片,圖片作成的標準書二. 色別治理:工具,零件置場的顏色治理三. 限度樣本四. 異常警示燈(蜂鳴器)五. 標示,看板,:依管制圖展開的工程治理六. 區域線:不良品,半成品置場的治理七. 人員配置圖八. 安全標誌,危險區域的標示2.排程,交期治理一. 生產進度治理板二. 產量治理板三. 生產計劃表四. 派工板或排班板3.品質治理一. 檢查工,量具的層別治理二. 不良品層別治理三. 量儀校正色別治理:檢測器具精度在規定值內,外的顏色區別四. 不良品的直方圖治理五. 圖示的檢查標準書4.設備治理一. 加油色別治理,加油口的顏色標示二. 操作動作的順序指引三. 保養部位色別治理,定期保養部位的標示四. 危險動作部位用顏色加以區分緊急停止開關(紅色)五. 換模部位與固定部位的顏色區分六. 儀表安全範圍色別治理,在管制內,外的顏色區分七. 螺,絲螺栓的配合記號八. 管路色別治理,相似的油及溶齊的顏色區分(二)事務現場的目視治理工廠為了追求生產治理的高度化,僅生產現場導入目視治理,就想獲得充分的成效,並不是一件容易的事.例如,在生產現場的裝配線設置排程治理看板,由現場治理人員編訂小日程計劃,讓作業員依“制令單”進行作業,但由於材料未能如期進廠,就可能使作業停頓,即使現場治理人員急忙打電話給採購人員,詢問有關交期,往往得不到确信的答復.如此一來,當然裝配線無法生產,而造成等待的浪費,為了幸免發生這類情況,與生產再紧密合作的事務現場(非制造部門)中,专门有關采購,貨倉,生管,技術,設計等部門,也要導入目視治理至於事務現場方面的目視治理,要紧指資訊的共有化,業務的標準化,並有效解決問題.即:一. 文件治理1.文件的分類標示2.文件的保管場所標示3.文件的定位標示二. 行動治理1.人員的動態治理2.個人的月行動計劃3.出勤狀況治理三. 業務治理1.業務標準的手冊化2.教育訓練的推進狀況四. QA設備治理1.QA機器及資訊的保管場所2.QA機器,空調等的治理狀況1.目視治理實施作用一. 治理透亮化目視治理即任何人利用視覺化工具,只要略微看一下,就明白是怎麼一回事,應該怎麼辦.例如,現場治理人員在現場巡視時,通過目視化工具可了解同類型機器的速度或不同時段同一臺機的速度有不一樣的異常狀況,確實把握人機稼動,物品的流動情況是否合理,均一.依排程計劃生產時,可利用標示,看板,表單,區域線等目視化工具,治理有關原物料,配件,半成品,成品等現場的動態,是否處於搬運,移動,停滯,保管等狀況,把握物品的加工,數量位置,確保現場符合JIT的要求,達到“必要的物品只在必要時間,必要場所供應”二. 誰都能迅速判斷目視化工具可作為事態是否正常及水準如何的判定標準,且任何人都能迅速判斷及遵守例如,進行5S的整頓活動時,地面上用油漆畫上或用膠帶貼上三种線,那确实是區域線(白線,黃線,紅線).亦即,要將物品放在規定的放置區(白線),不能超出安全道(黃線).如此一來,發生事故時,不管是人員或機器(包括叉車,電動拖板車等)都可全速在安全道上奔馳.另外,在配電盤或消防器材前面,用紅線畫上一標放區,不許任何物品侵入其中(紅線).假如作業員都能遵守區域線的規定,萬一發生事故時,就能赶忙拿到消防器材或切斷電源開關,而不會延誤搶救時機.如此一來,物品既可放得井然有序,又可確保人員,物品安全因此,通過目視治理的實施.假如作業員未按區域線的規定放置物品,班長或組長赶忙會發現,當場就可對作業員加以指正三. 層別問題在作業現場,假如人員,設備都在稼動,從表面上無法了解進行的工作是否符合預定的進度,是否達成目標,例如:1.制程是否穩定?工序能力如何?趨勢如何?2.機械的振動是否在安全範圍內?潤滑油濃度是否在管制狀態?3.正在進行何种作業?何時完成?能否如期交貨?4.工作是否依預定計劃完成?為何這臺機器停機?5.如何採取對策挽救生產落后?對於上述情況,必須借助目視化的機電化燈號或治理圖表,從燈號,圖表上了解必要的信息,進而作為改善,追蹤的有效工具.目視治理专门能够使工廠一些隱沒的狀況變為顯在的事實.使所有看不見的異常,浪費,問題點暴露無遺.例如:成豐電子公司共有A.B.C.D.E五個部門,在1998年時,全公司故障件數為1900件,1999年降至1520件,而在2000年更降至950件,僅為1998年的一半,可說是成績斐然.但假如深入追究的話,可獲知(表1)的表達方式為分不清責任的“吃大鍋飯”方式.我們假如再依A.B.C.D.E各個部門的故障件數,加以層別的話,如(表2)所示,可發現全公司因此進步专门大.於是,但三年來C.D兩部門全然是原地踏步,一點也沒進步.於是,針對C.D兩部門再下功夫改善,那麼,2000年度的故障件數必定低於950件.此即借目視治理,引導“由潛在化轉為顯在化”的案例2.目視治理實施要點工廠推行目視治理活動時,第一要設法塑造容易治理的環境,即任何人看到目視治理工具后,赶忙了解現有狀態是否異常.因此,導入目視治理不僅僅是利用文字或數字,還必須對現場治理方面的治理界限通過視覺化的工具,比如理劃,線設定顏色,高度等表達方式,顯示現有狀態是否異常及應有狀態的治理基準,以起到預警的作用,提醒相關人員不正常時應採取“停止作業”或“停機”等措施.目視治理看似間單,在許多工廠都有導人和6推行,但真正實施時,確未能達到預期成效,雖然作業場所挂滿了治理看板及圖表,但往往“有其形而無起魂”,以致流于形式,例如:1.雖然設有不良品放置場所,並以顏色予以標示.由於未追究不良的真正缘故,因此,反复發生同樣的不良現象,未能達到特地設置不良品放置區”的目視治理目的.2.雖然生產現場張貼“良品率治理圖表”,然而,即使良品率有下降的趨勢.甚至已是過時的數據,但有關人員每天超過看板卻視而不見,一直未採取任何改善對策3.雖然裝配線上設有警示燈號,但未充分適用,即使燈號亮起來,治理者也未赶忙前往查詢怎么说而予以處理4.雖然裝配線上設有“生產日程治理板”,但即使排程已發生延誤,卻未充分追究缘故,當然更談不上採取適當的對策對於上述情況,究其缘故,不外乎以下方面:1.未能徹底明白得目視治理的目的及建立推行組織;2.未設定具體的活動項目、目標;3.目視治理工具有理想;4.未能對目視治理用具運用實施教育;5.治理者的策劃力、領導力、改善力不足;6.治理者對目視治理的關心程度不夠,各部門難以合作.因此,工廠在實施目視治理活動時,讓全員擁有問題意識,通過不斷的教育訓練,形成全員挑戰目標、把握問題點、追究要因、采取對策的持續活動.目視治理實施能否成功,有賴於推行委員會的組織、指導,使工廠各相關部門達成共識,步調一致地展開活動.一、全員教育訓練通過教育訓練,讓全員了解目視治理的涵義,活動目的及內容、方法、要領.教育訓練由推行委員會組織人員,依據工廠的實際狀況,編制適用的目視治理教材.二、設立治理項目、標準對於作業及檢查項目的標準,要有清晰明白的標示,一有異常,員工可赶忙與標準比較,進行判定的限度樣本,如電鍍、噴油的表面狀態、印刷品的清晰度等.目視判定標準的制定要讓作業員參與,而不只是現場治理人員清晰目視治理的規定及辦法.三、從5S活動開始5S是工廠治理的基礎,未徹底進行5S的工作聲所,無法期待活躍的改善活動,5S要能夠徹底實施與維持,目視治理不可或缺.因此,全廠徹底實施5S,是目視治理實施的基礎.通過整理、整頓活動,徹底確立物品的放置場所、保管方法、包裝方式的標示,使目視治理變得容易.四.、按規定執行目視治理自導入階段起,即要求全員嚴守目視治理規定及辦法.一有任何異常狀態,赶忙採取適當的對策,以免目視治理成表面工夫.例如架各層都有標示,那麼必須按標示去放置物品,拒絕亂擺亂放.五、与QCC、提案制度結合活動及提案制度的運作,借此集思廣益,群策群力,構思有創意的目視化工具,進而提高目視治理成效.六、制定激勵辦法制定目視治理活動競賽辦法,對於積極推行而且成績優秀的部門,予以適當的獎勵,對於表現不佳的部門,予以適當的懲罰,如列入績效考核,對於表現不佳的部門,予以適當的懲罰,如列入績效考核.在目視治理競賽活動中產生的樣板單位,由推行委員會統一安排時間進行參觀、學習,以激發更好的創意.3.目視治理推行步驟目視治理活動導入與推行流程(圖2-1):設定工作目標建立推行組織推行委員會制定活動計劃設定目視治理項目把握問題點與改善點確定展開方法目視治理展開活動追蹤目視治理的導入流程(圖2-1) 一、設定工作目標目視治理導入第一要明確治理的目的、期望目標、活動期間、推行方法等,並形成文件.二、建立推行組織目視治理的實施不能由公司各個部門各做各樣,而應成立全公司推行委員會,協調各部門有組織、有計劃、步調一致地展開. 三、制定活動計劃推行委員會組織人力制定目視治理活動計劃、辦法、獎懲條例及宣導事宜等,並通過各种渠道進行宣導,讓全體員工了解目視治理實施的作用、目的.四、設定治理項目目視治理實施之際,要讓生產現場的治理者,作業員明確哪些項目必須治理,並依治理的重要性與緊迫,性制作必要的治理看板、大項目可區分為:(一)生產管及交期治理(二)品質治理(三)作業治理(四)現品治理(五)設備、治工具治理(六)改善目標治理預制程治理、交期治理改防品質管理善管作業管理目現品管理標管理設備治理、治工具治理理目視治理大項目(圖2-2)上述1-5項要能徹底實現預防治理,必須轉動治理循環.而改善目標治理是1-5項及作業方法等不斷進行改善時所需要的治理方法,要以目視化的方式在現場對照標明改善目標与實績,以謀求對治理者、督導者及作業員的激勵與改善意識的提高.目視治理提昇治理水準與改善水準(圖2-3)五.把握問題點與改善點設定了目視治理的活動項目,必須設計,製作查檢表,檢討有關設定項目是否已實現及實施成效如何.能否做到一目了然 ?並说明問題點與改善點.(一)徹底推動5S實施目視治理,第一要徹底推動5S,5S是實施目視治理最差不多的工具,通過5S的實施,徹底做好整理,整頓,使物流順暢,目視治理才能够實施,同時改善材料,零件,產品等存放位置的布置及保管方法.(二)準備目視治理用具要實施目視治理,最重要的是準備好目視治理的用具,例如:檢討現有的日程計劃與進度治理體系,設置標示生產計劃實績的生產治理板及裝配生產線的呼叫燈,對物料,產品放置場所編號及品名標示, (三)建立目視治理體系針對全部工作場所,按工作場所的工作別,個人別,建立一目了然的目視治理體系,清晰明白個人的作業內容,作業量及作業計劃進度超前或落後及其對策等,以確實把握現狀,發現問題,迅速採取有效對策,建立預防治理體系.七.目視治理活動展開在目視治理進入實施階段的時候,為了保證實施的實際成效及不流於形式,必須在推行委員會的統一指導下,有計劃,有步驟的展開.(一)導入教育(二)制定活動辦法(含激勵方式)(三)展開活動1.經營階層宣誓實施決心2.設計並張貼海報,標語3.編制“目視治理Q〥A集”4.規劃責任區5.規劃辦公室,各制程,設備,公共場所等標示,治理看板,治理圖表6.制定目視治理活動評審準則7.現場巡回,指導及評審8.成果發表八.實施成效追蹤除非目視治理已完全實施,而且實施成果已得到鞏固,否則推行委員會及高階層治理層都要定期稽查,追蹤.4.目視治理活動方法實例一:泰達電子(目視治理活動方法)1.目的為塑造一目了然的工廠,改善工作環境,使工作合理化,提高工作場所的安全,品質與效率,以達到(強化體質,永續經營)的目的,特制定本辦法2.適用範圍本公司所有部門,員工3.活動目標3.1明確並繪制區域線3.1.1黃線安全道不可有物品超出線外3.1.2白線物品放置區物品不可亂放,且在白線區內堆放整齊3.1.3紅線禁放區在消防器材或配電盤前之紅線區內,不可放任何物品3.2進行物品的標示,100%的實現物品“三定”: 定品名.定位置,定數量3.2.1物品與放置區的標志必須一致3.2.2柜子,架子各層物品必須歸類,且標示清晰3.3活動重點標準,重點訓示,查核表3.4活用治理看板,治理圖表3.5確立“廠用設備顏色標準”3.6統一製作全廠安全標志4.活動期間:共四個月4.1中間評核五次(占60%)4.2最終評審(占25%)4.3發表會(占15%)5.組織及職責5.1組織:目視治理推行委員會(見附表)5.2職責5.2.1推行委員會✧擬定有關目視治理活動的年度推行計劃✧擬定有關目視治理活動辦法並推動✧擬定有關目視治理活動的教育計劃並實施✧擬定有關目視治理活動的宣導事宜✧擬定修定有關目視治理活動的組織規定,實施辦法與標準5.2.2主任委員:設主任委員一人,由總經理擔任,主持委員會會議,宣示有關專案活動的策略,方針,並進行指導事宜5.2.3執行長:設執行長一人,由主任委員派任,配合公司方針及執行主任委員的標示,統籌專案活動事宜,產督導各工作小組的工作5.2.4執行秘書:設執行秘書一人,由委員中選任,任期為一年,連選得連任,其職責如下:➢開會通知,資料準備及記錄➢協助執行長推行目視治理專案活動➢協調各工作小組的業務5.2.5工作小組委員會之下策劃小組,宣導教育小組,評鑒小組等三個工作小組,各設小組長一人,由委員會中選任,任期為一年,連選得連任,負責綜理各小組事務與推行.各小組由3—5名成員(含各小組長)組成,由小組長聘任,成員不一定為執行委員,若非執行委員會者,則以主任委員名義發予聘書,以示慎重.工作小組職責如下:1.策劃小組a 編制年度活動計劃及預算b 策劃活動辦法2.宣導教育小組a設計,製作海報或標語等b編印宣傳資料等(如卡片)c擬定教育計劃e實施教育訓練及輔導事宜。
工厂UPPH 的管理方法
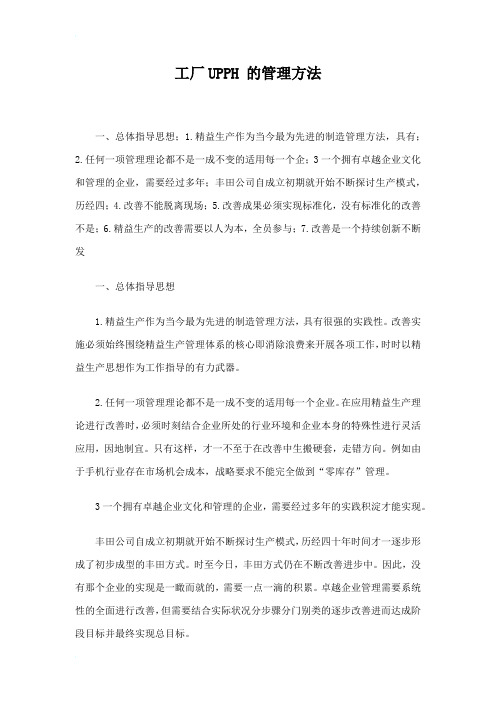
工厂UPPH 的管理方法一、总体指导思想;1.精益生产作为当今最为先进的制造管理方法,具有;2.任何一项管理理论都不是一成不变的适用每一个企;3一个拥有卓越企业文化和管理的企业,需要经过多年;丰田公司自成立初期就开始不断探讨生产模式,历经四;4.改善不能脱离现场;5.改善成果必须实现标准化,没有标准化的改善不是;6.精益生产的改善需要以人为本,全员参与;7.改善是一个持续创新不断发一、总体指导思想1.精益生产作为当今最为先进的制造管理方法,具有很强的实践性。
改善实施必须始终围绕精益生产管理体系的核心即消除浪费来开展各项工作,时时以精益生产思想作为工作指导的有力武器。
2.任何一项管理理论都不是一成不变的适用每一个企业。
在应用精益生产理论进行改善时,必须时刻结合企业所处的行业环境和企业本身的特殊性进行灵活应用,因地制宜。
只有这样,才一不至于在改善中生搬硬套,走错方向。
例如由于手机行业存在市场机会成本,战略要求不能完全做到“零库存”管理。
3一个拥有卓越企业文化和管理的企业,需要经过多年的实践积淀才能实现。
丰田公司自成立初期就开始不断探讨生产模式,历经四十年时间才一逐步形成了初步成型的丰田方式。
时至今日,丰田方式仍在不断改善进步中。
因此,没有那个企业的实现是一瞰而就的,需要一点一滴的积累。
卓越企业管理需要系统性的全面进行改善,但需要结合实际状况分步骤分门别类的逐步改善进而达成阶段目标并最终实现总目标。
4.改善不能脱离现场。
所有数据必须现场测量,所有问题必须现场观察,充分与一线员工交流并亲身实践才能得出结论。
脱离现场,脱离实际,脱离基层员工,任何改善都只是纸上谈兵。
5.改善成果必须实现标准化,没有标准化的改善不是完美的改善。
6.精益生产的改善需要以人为本,全员参与。
只有全员参与,充分发挥人的主动性和能动性,改善才能处处开花。
7.改善是一个持续创新不断发现问题不断进步的过程。
没有最好,只有更好,持续改善,不断进步,这是丰田方式的精髓。
管控工厂UPPH
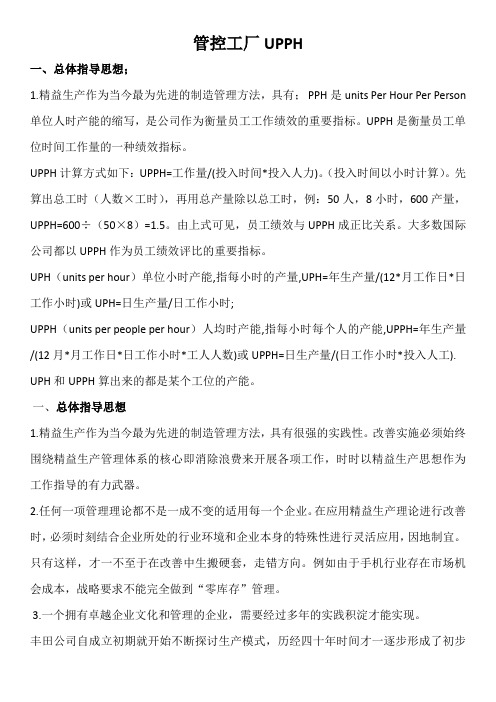
管控工厂UPPH一、总体指导思想;1.精益生产作为当今最为先进的制造管理方法,具有; PPH是units Per Hour Per Person 单位人时产能的缩写,是公司作为衡量员工工作绩效的重要指标。
UPPH是衡量员工单位时间工作量的一种绩效指标。
UPPH计算方式如下:UPPH=工作量/(投入时间*投入人力)。
(投入时间以小时计算)。
先算出总工时(人数×工时),再用总产量除以总工时,例:50人,8小时,600产量,UPPH=600÷(50×8)=1.5。
由上式可见,员工绩效与UPPH成正比关系。
大多数国际公司都以UPPH作为员工绩效评比的重要指标。
UPH(units per hour)单位小时产能,指每小时的产量,UPH=年生产量/(12*月工作日*日工作小时)或UPH=日生产量/日工作小时;UPPH(units per people per hour)人均时产能,指每小时每个人的产能,UPPH=年生产量/(12月*月工作日*日工作小时*工人人数)或UPPH=日生产量/(日工作小时*投入人工). UPH和UPPH算出来的都是某个工位的产能。
一、总体指导思想1.精益生产作为当今最为先进的制造管理方法,具有很强的实践性。
改善实施必须始终围绕精益生产管理体系的核心即消除浪费来开展各项工作,时时以精益生产思想作为工作指导的有力武器。
2.任何一项管理理论都不是一成不变的适用每一个企业。
在应用精益生产理论进行改善时,必须时刻结合企业所处的行业环境和企业本身的特殊性进行灵活应用,因地制宜。
只有这样,才一不至于在改善中生搬硬套,走错方向。
例如由于手机行业存在市场机会成本,战略要求不能完全做到“零库存”管理。
3.一个拥有卓越企业文化和管理的企业,需要经过多年的实践积淀才能实现。
丰田公司自成立初期就开始不断探讨生产模式,历经四十年时间才一逐步形成了初步成型的丰田方式。
时至今日,丰田方式仍在不断改善进步中。
工厂单位人时产能UPPH管控的思路和方法7.doc
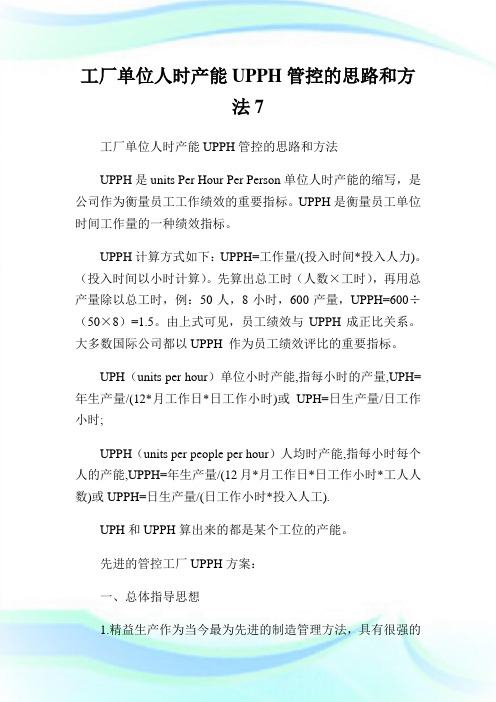
工厂单位人时产能UPPH管控的思路和方法7工厂单位人时产能UPPH管控的思路和方法UPPH是units Per Hour Per Person单位人时产能的缩写,是公司作为衡量员工工作绩效的重要指标。
UPPH是衡量员工单位时间工作量的一种绩效指标。
UPPH计算方式如下:UPPH=工作量/(投入时间*投入人力)。
(投入时间以小时计算)。
先算出总工时(人数×工时),再用总产量除以总工时,例:50人,8小时,600产量,UPPH=600÷(50×8)=1.5。
由上式可见,员工绩效与UPPH成正比关系。
大多数国际公司都以UPPH 作为员工绩效评比的重要指标。
UPH(units per hour)单位小时产能,指每小时的产量,UPH=年生产量/(12*月工作日*日工作小时)或UPH=日生产量/日工作小时;UPPH(units per people per hour)人均时产能,指每小时每个人的产能,UPPH=年生产量/(12月*月工作日*日工作小时*工人人数)或UPPH=日生产量/(日工作小时*投入人工).UPH和UPPH算出来的都是某个工位的产能。
先进的管控工厂UPPH方案:一、总体指导思想1.精益生产作为当今最为先进的制造管理方法,具有很强的实践性。
改善实施必须始终围绕精益生产管理体系的核心即消除浪费来开展各项工作,时时以精益生产思想作为工作指导的有力武器。
2.任何一项管理理论都不是一成不变的适用每一个企业。
在应用精益生产理论进行改善时,必须时刻结合企业所处的行业环境和企业本身的特殊性进行灵活应用,因地制宜。
只有这样,才一不至于在改善中生搬硬套,走错方向。
例如由于手机行业存在市场机会成本,战略要求不能完全做到“零库存”管理。
3一个拥有卓越企业文化和管理的企业,需要经过多年的实践积淀才能实现。
丰田公司自成立初期就开始不断探讨生产模式,历经四十年时间才一逐步形成了初步成型的丰田方式。
如何管控工厂UPPH

如何管控工厂UPPH导读:如何管控工厂UPPH,先进的管控工厂UPPH方案:,借鉴优秀工厂管理的实践经验,依照工厂管理损失分类将各项指标分解至详细指标,如何管控工厂U PPHUPPH是unitsPerHourPerPerson单位人时产能的缩写,是公司作为衡量员工工作绩效的重要指标。
UPPH是衡量员工单位时间工作量的一种绩效指标。
UPPH 计算方式如下:UPPH=工作量/(投入时间*投入人力)。
(投入时间以小时计算)。
先算如何管控工厂UPPHUPPH是units Per Hour Per Person单位人时产能的缩写,是公司作为衡量员工工作绩效的重要指标。
UPPH是衡量员工单位时间工作量的一种绩效指标。
UPPH计算方式如下:UPPH=工作量/(投入时间*投入人力)。
(投入时间以小时计算)。
先算出总工时(人数×工时),再用总产量除以总工时,例:50人,8小时,600产量,UPPH=600÷(50×8)=1.5。
由上式可见,员工绩效与UPPH成正比关系。
大多数国际公司都以UPPH作为员工绩效评比的重要指标。
UPH(units per hour)单位小时产能,指每小时的产量,UPH=年生产量/(12*月工作日*日工作小时)或UPH=日生产量/日工作小时;UPPH(units per people per hour)人均时产能,指每小时每个人的产能,UPPH =年生产量/(12月*月工作日*日工作小时*工人人数)或UPPH=日生产量/(日工作小时*投入人工). UPH和UPPH算出来的都是某个工位的产能。
先进的管控工厂UPPH方案:一、总体指导思想1.精益生产作为当今最为先进的制造管理方法,具有很强的实践性。
改善实施必须始终围绕精益生产管理体系的核心即消除浪费来开展各项工作,时时以精益生产思想作为工作指导的有力武器。
2.任何一项管理理论都不是一成不变的适用每一个企业。
在应用精益生产理论进行改善时,必须时刻结合企业所处的行业环境和企业本身的特殊性进行灵活应用,因地制宜。
工厂UPPH管控
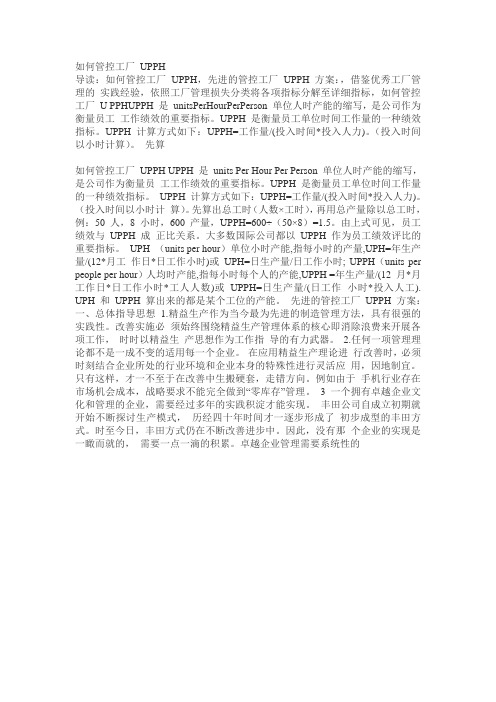
如何管控工厂UPPH导读:如何管控工厂UPPH,先进的管控工厂UPPH 方案:,借鉴优秀工厂管理的实践经验,依照工厂管理损失分类将各项指标分解至详细指标,如何管控工厂U PPHUPPH 是unitsPerHourPerPerson 单位人时产能的缩写,是公司作为衡量员工工作绩效的重要指标。
UPPH 是衡量员工单位时间工作量的一种绩效指标。
UPPH 计算方式如下:UPPH=工作量/(投入时间*投入人力)。
(投入时间以小时计算)。
先算如何管控工厂UPPH UPPH 是units Per Hour Per Person 单位人时产能的缩写,是公司作为衡量员工工作绩效的重要指标。
UPPH 是衡量员工单位时间工作量的一种绩效指标。
UPPH 计算方式如下:UPPH=工作量/(投入时间*投入人力)。
(投入时间以小时计算)。
先算出总工时(人数×工时),再用总产量除以总工时,例:50 人,8 小时,600 产量,UPPH=600÷(50×8)=1.5。
由上式可见,员工绩效与UPPH 成正比关系。
大多数国际公司都以UPPH 作为员工绩效评比的重要指标。
UPH (units per hour)单位小时产能,指每小时的产量,UPH=年生产量/(12*月工作日*日工作小时)或UPH=日生产量/日工作小时; UPPH(units per people per hour)人均时产能,指每小时每个人的产能,UPPH =年生产量/(12 月*月工作日*日工作小时*工人人数)或UPPH=日生产量/(日工作小时*投入人工). UPH 和UPPH 算出来的都是某个工位的产能。
先进的管控工厂UPPH 方案:一、总体指导思想 1.精益生产作为当今最为先进的制造管理方法,具有很强的实践性。
改善实施必须始终围绕精益生产管理体系的核心即消除浪费来开展各项工作,时时以精益生产思想作为工作指导的有力武器。
2.任何一项管理理论都不是一成不变的适用每一个企业。
如何管控工厂UPPH
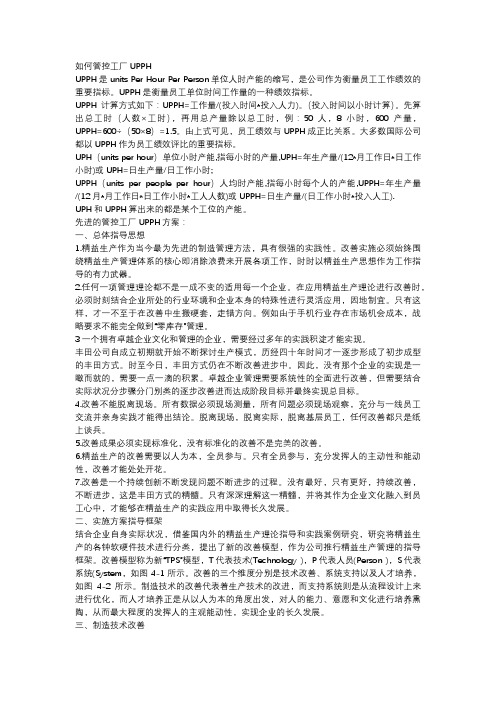
如何管控工厂UPPHUPPH是units Per Hour Per Person单位人时产能的缩写,是公司作为衡量员工工作绩效的重要指标。
UPPH是衡量员工单位时间工作量的一种绩效指标。
UPPH计算方式如下:UPPH=工作量/(投入时间*投入人力)。
(投入时间以小时计算)。
先算出总工时(人数×工时),再用总产量除以总工时,例:50人,8小时,600产量,UPPH=600÷(50×8)=1.5。
由上式可见,员工绩效与UPPH成正比关系。
大多数国际公司都以UPPH作为员工绩效评比的重要指标。
UPH(units per hour)单位小时产能,指每小时的产量,UPH=年生产量/(12*月工作日*日工作小时)或UPH=日生产量/日工作小时;UPPH(units per people per hour)人均时产能,指每小时每个人的产能,UPPH=年生产量/(12月*月工作日*日工作小时*工人人数)或UPPH=日生产量/(日工作小时*投入人工).UPH和UPPH算出来的都是某个工位的产能。
先进的管控工厂UPPH方案:一、总体指导思想1.精益生产作为当今最为先进的制造管理方法,具有很强的实践性。
改善实施必须始终围绕精益生产管理体系的核心即消除浪费来开展各项工作,时时以精益生产思想作为工作指导的有力武器。
2.任何一项管理理论都不是一成不变的适用每一个企业。
在应用精益生产理论进行改善时,必须时刻结合企业所处的行业环境和企业本身的特殊性进行灵活应用,因地制宜。
只有这样,才一不至于在改善中生搬硬套,走错方向。
例如由于手机行业存在市场机会成本,战略要求不能完全做到“零库存”管理。
3一个拥有卓越企业文化和管理的企业,需要经过多年的实践积淀才能实现。
丰田公司自成立初期就开始不断探讨生产模式,历经四十年时间才一逐步形成了初步成型的丰田方式。
时至今日,丰田方式仍在不断改善进步中。
因此,没有那个企业的实现是一瞰而就的,需要一点一滴的积累。
工厂单位人时产能UPPH管控的思路和方法

工厂单位人时产能UPPH管控的思路和方法UPPH是units Per Hour Per Person单位人时产能的缩写,是公司作为衡量员工工作绩效的重要指标。
UPPH是衡量员工单位时间工作量的一种绩效指标。
UPPH计算方式如下:UPPH=工作量/(投入时间*投入人力)。
(投入时间以小时计算)。
先算出总工时(人数×工时),再用总产量除以总工时,例:50人,8小时,600产量,UPPH=600÷(50×8)=1.5。
由上式可见,员工绩效与UPPH成正比关系。
大多数国际公司都以UPPH 作为员工绩效评比的重要指标。
UPH(units per hour)单位小时产能,指每小时的产量,UPH=年生产量/(12*月工作日*日工作小时)或UPH=日生产量/日工作小时;UPPH(units per people per hour)人均时产能,指每小时每个人的产能,UPPH=年生产量/(12月*月工作日*日工作小时*工人人数)或UPPH=日生产量/(日工作小时*投入人工).UPH和UPPH算出来的都是某个工位的产能。
先进的管控工厂UPPH方案:一、总体指导思想1.精益生产作为当今最为先进的制造管理方法,具有很强的实践性。
改善实施必须始终围绕精益生产管理体系的核心即消除浪费来开展各项工作,时时以精益生产思想作为工作指导的有力武器。
2.任何一项管理理论都不是一成不变的适用每一个企业。
在应用精益生产理论进行改善时,必须时刻结合企业所处的行业环境和企业本身的特殊性进行灵活应用,因地制宜。
只有这样,才一不至于在改善中生搬硬套,走错方向。
例如由于手机行业存在市场机会成本,战略要求不能完全做到“零库存”管理。
3一个拥有卓越企业文化和管理的企业,需要经过多年的实践积淀才能实现。
丰田公司自成立初期就开始不断探讨生产模式,历经四十年时间才一逐步形成了初步成型的丰田方式。
时至今日,丰田方式仍在不断改善进步中。
如何管控工厂UPPH汇总

如何管控工厂UPPHUPPH是units Per Hour Per Person单位人时产能的缩写,是公司作为衡量员工工作绩效的重要指标。
UPPH是衡量员工单位时间工作量的一种绩效指标。
UPPH计算方式如下:UPPH=工作量/(投入时间*投入人力)。
(投入时间以小时计算)。
先算出总工时(人数×工时),再用总产量除以总工时,例:50人,8小时,600产量,UPPH=600÷(50×8)=1.5。
由上式可见,员工绩效与UPPH成正比关系。
大多数国际公司都以UPPH作为员工绩效评比的重要指标。
UPH(units per hour)单位小时产能,指每小时的产量,UPH=年生产量/(12*月工作日*日工作小时)或UPH=日生产量/日工作小时;UPPH(units per people per hour)人均时产能,指每小时每个人的产能,UPPH=年生产量/(12月*月工作日*日工作小时*工人人数)或UPPH=日生产量/(日工作小时*投入人工).UPH和UPPH算出来的都是某个工位的产能。
先进的管控工厂UPPH方案:一、总体指导思想1.精益生产作为当今最为先进的制造管理方法,具有很强的实践性。
改善实施必须始终围绕精益生产管理体系的核心即消除浪费来开展各项工作,时时以精益生产思想作为工作指导的有力武器。
2.任何一项管理理论都不是一成不变的适用每一个企业。
在应用精益生产理论进行改善时,必须时刻结合企业所处的行业环境和企业本身的特殊性进行灵活应用,因地制宜。
只有这样,才一不至于在改善中生搬硬套,走错方向。
例如由于手机行业存在市场机会成本,战略要求不能完全做到“零库存”管理。
3一个拥有卓越企业文化和管理的企业,需要经过多年的实践积淀才能实现。
丰田公司自成立初期就开始不断探讨生产模式,历经四十年时间才一逐步形成了初步成型的丰田方式。
时至今日,丰田方式仍在不断改善进步中。
因此,没有那个企业的实现是一瞰而就的,需要一点一滴的积累。
如何管控工厂 UPPH
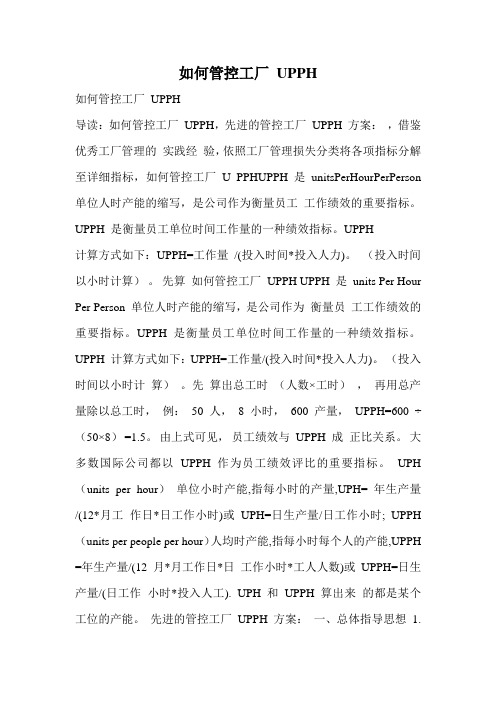
如何管控工厂UPPH如何管控工厂UPPH导读:如何管控工厂UPPH,先进的管控工厂UPPH 方案:,借鉴优秀工厂管理的实践经验,依照工厂管理损失分类将各项指标分解至详细指标,如何管控工厂U PPHUPPH 是unitsPerHourPerPerson 单位人时产能的缩写,是公司作为衡量员工工作绩效的重要指标。
UPPH 是衡量员工单位时间工作量的一种绩效指标。
UPPH计算方式如下:UPPH=工作量/(投入时间*投入人力)。
(投入时间以小时计算)。
先算如何管控工厂UPPH UPPH 是units Per Hour Per Person 单位人时产能的缩写,是公司作为衡量员工工作绩效的重要指标。
UPPH 是衡量员工单位时间工作量的一种绩效指标。
UPPH 计算方式如下:UPPH=工作量/(投入时间*投入人力)。
(投入时间以小时计算)。
先算出总工时(人数×工时),再用总产量除以总工时,例:50 人,8 小时,600 产量,UPPH=600 ÷(50×8)=1.5。
由上式可见,员工绩效与UPPH 成正比关系。
大多数国际公司都以UPPH 作为员工绩效评比的重要指标。
UPH (units per hour)单位小时产能,指每小时的产量,UPH= 年生产量/(12*月工作日*日工作小时)或UPH=日生产量/日工作小时; UPPH (units per people per hour)人均时产能,指每小时每个人的产能,UPPH =年生产量/(12 月*月工作日*日工作小时*工人人数)或UPPH=日生产量/(日工作小时*投入人工). UPH 和UPPH 算出来的都是某个工位的产能。
先进的管控工厂UPPH 方案:一、总体指导思想1.精益生产作为当今最为先进的制造管理方法,具有很强的实践性。
改善实施必须始终围绕精益生产管理体系的核心即消除浪费来开展各项工作,时时以精益生产思想作为工作指导的有力武器。
工厂UPPH 的管理方法

工厂UPPH 的管理方法一、总体指导思想;1.精益生产作为当今最为先进的制造管理方法,具有;2.任何一项管理理论都不是一成不变的适用每一个企;3一个拥有卓越企业文化和管理的企业,需要经过多年;丰田公司自成立初期就开始不断探讨生产模式,历经四;4.改善不能脱离现场;5.改善成果必须实现标准化,没有标准化的改善不是;6.精益生产的改善需要以人为本,全员参与;7.改善是一个持续创新不断发一、总体指导思想1.精益生产作为当今最为先进的制造管理方法,具有很强的实践性。
改善实施必须始终围绕精益生产管理体系的核心即消除浪费来开展各项工作,时时以精益生产思想作为工作指导的有力武器。
2.任何一项管理理论都不是一成不变的适用每一个企业。
在应用精益生产理论进行改善时,必须时刻结合企业所处的行业环境和企业本身的特殊性进行灵活应用,因地制宜。
只有这样,才一不至于在改善中生搬硬套,走错方向。
例如由于手机行业存在市场机会成本,战略要求不能完全做到“零库存”管理。
3一个拥有卓越企业文化和管理的企业,需要经过多年的实践积淀才能实现。
丰田公司自成立初期就开始不断探讨生产模式,历经四十年时间才一逐步形成了初步成型的丰田方式。
时至今日,丰田方式仍在不断改善进步中。
因此,没有那个企业的实现是一瞰而就的,需要一点一滴的积累。
卓越企业管理需要系统性的全面进行改善,但需要结合实际状况分步骤分门别类的逐步改善进而达成阶段目标并最终实现总目标。
4.改善不能脱离现场。
所有数据必须现场测量,所有问题必须现场观察,充分与一线员工交流并亲身实践才能得出结论。
脱离现场,脱离实际,脱离基层员工,任何改善都只是纸上谈兵。
5.改善成果必须实现标准化,没有标准化的改善不是完美的改善。
6.精益生产的改善需要以人为本,全员参与。
只有全员参与,充分发挥人的主动性和能动性,改善才能处处开花。
7.改善是一个持续创新不断发现问题不断进步的过程。
没有最好,只有更好,持续改善,不断进步,这是丰田方式的精髓。
UPPH管理
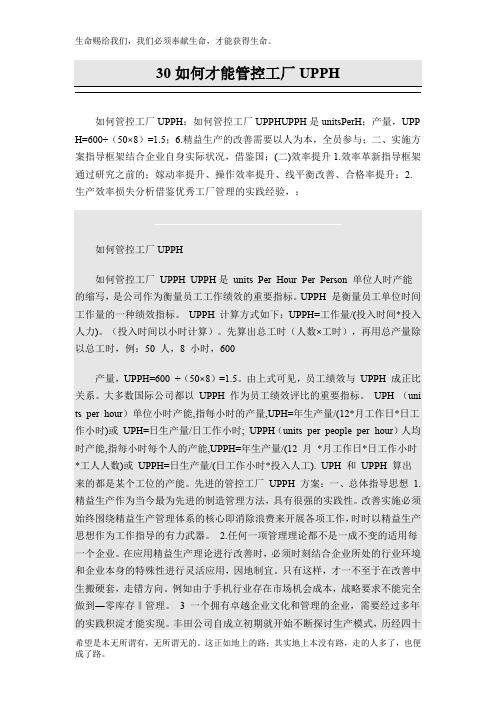
如何管控工厂UPPH;如何管控工厂UPPHUPPH是unitsPerH;产量,UPP H=600÷(50×8)=1.5;6.精益生产的改善需要以人为本,全员参与;二、实施方案指导框架结合企业自身实际状况,借鉴国;(二)效率提升1.效率革新指导框架通过研究之前的;嫁动率提升、操作效率提升、线平衡改善、合格率提升;2.生产效率损失分析借鉴优秀工厂管理的实践经验,;如何管控工厂UPPH如何管控工厂UPPH UPPH是units Per Hour Per Person 单位人时产能的缩写,是公司作为衡量员工工作绩效的重要指标。
UPPH 是衡量员工单位时间工作量的一种绩效指标。
UPPH 计算方式如下:UPPH=工作量/(投入时间*投入人力)。
(投入时间以小时计算)。
先算出总工时(人数×工时),再用总产量除以总工时,例:50 人,8 小时,600产量,UPPH=600 ÷(50×8)=1.5。
由上式可见,员工绩效与UPPH 成正比关系。
大多数国际公司都以UPPH 作为员工绩效评比的重要指标。
UPH (uni ts per hour)单位小时产能,指每小时的产量,UPH=年生产量/(12*月工作日*日工作小时)或UPH=日生产量/日工作小时; UPPH(units per people per hour)人均时产能,指每小时每个人的产能,UPPH=年生产量/(12 月*月工作日*日工作小时*工人人数)或UPPH=日生产量/(日工作小时*投入人工). UPH 和UPPH 算出来的都是某个工位的产能。
先进的管控工厂UPPH 方案:一、总体指导思想 1.精益生产作为当今最为先进的制造管理方法,具有很强的实践性。
改善实施必须始终围绕精益生产管理体系的核心即消除浪费来开展各项工作,时时以精益生产思想作为工作指导的有力武器。
2.任何一项管理理论都不是一成不变的适用每一个企业。
教你如何管控工厂UPPH
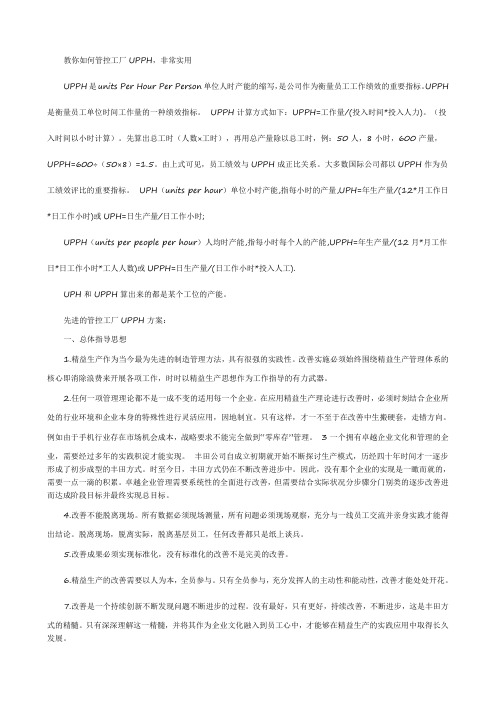
教你如何管控工厂UPPH,非常实用UPPH是units Per Hour Per Person单位人时产能的缩写,是公司作为衡量员工工作绩效的重要指标。
UPPH 是衡量员工单位时间工作量的一种绩效指标。
UPPH计算方式如下:UPPH=工作量/(投入时间*投入人力)。
(投入时间以小时计算)。
先算出总工时(人数×工时),再用总产量除以总工时,例:50人,8小时,600产量,UPPH=600÷(50×8)=1.5。
由上式可见,员工绩效与UPPH成正比关系。
大多数国际公司都以UPPH作为员工绩效评比的重要指标。
UPH(units per hour)单位小时产能,指每小时的产量,UPH=年生产量/(12*月工作日*日工作小时)或UPH=日生产量/日工作小时;UPPH(units per people per hour)人均时产能,指每小时每个人的产能,UPPH=年生产量/(12月*月工作日*日工作小时*工人人数)或UPPH=日生产量/(日工作小时*投入人工).UPH和UPPH算出来的都是某个工位的产能。
先进的管控工厂UPPH方案:一、总体指导思想1.精益生产作为当今最为先进的制造管理方法,具有很强的实践性。
改善实施必须始终围绕精益生产管理体系的核心即消除浪费来开展各项工作,时时以精益生产思想作为工作指导的有力武器。
2.任何一项管理理论都不是一成不变的适用每一个企业。
在应用精益生产理论进行改善时,必须时刻结合企业所处的行业环境和企业本身的特殊性进行灵活应用,因地制宜。
只有这样,才一不至于在改善中生搬硬套,走错方向。
例如由于手机行业存在市场机会成本,战略要求不能完全做到―零库存‖管理。
3一个拥有卓越企业文化和管理的企业,需要经过多年的实践积淀才能实现。
丰田公司自成立初期就开始不断探讨生产模式,历经四十年时间才一逐步形成了初步成型的丰田方式。
时至今日,丰田方式仍在不断改善进步中。
因此,没有那个企业的实现是一瞰而就的,需要一点一滴的积累。
如何管控工厂UPPH
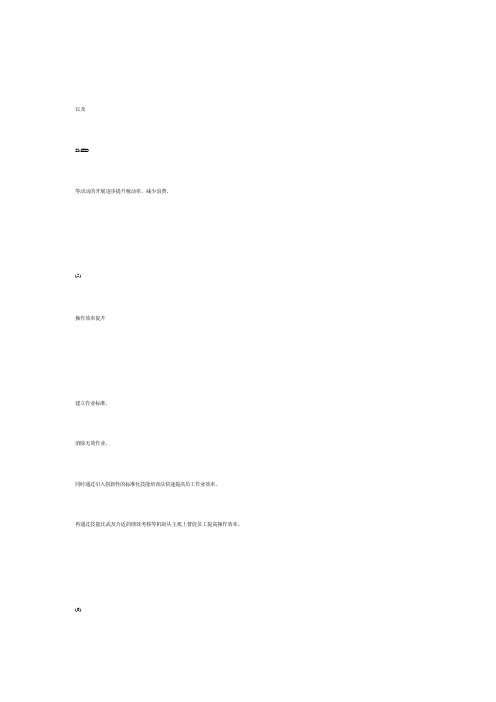
以及SMED等活动的开展逐步提升稼动率,减少浪费。
(5)操作效率提升建立作业标准,消除无效作业,同时通过引入创新性的标准化技能培训法快速提高员工作业效率,再通过技能比武及合适的绩效考核等机制从主观上督促员工提高操作效率。
(6)线平衡率提升:通过应用工业工程ECRS原则、作业研究、程序分析、动作经济原则等技巧进行生产线平衡的分析,从工艺角度进行改善,减少不平衡生产带来的损失。
(7)省人化:多能工作为实现均衡生产非常重要的策略,可有效提高工作利用率,达到少人化的目的。
而自动化或半自动化设备的使用可有效减少人员操作时间或直接把人解放出来,从而减少操作人力。
手机制造的组装动作主要由贴、熔、点、锁、装、测、检、包、送九大操作动作完成,当前可实现的主要作业有自动贴膜、自动锁螺丝等。
(8)快速反应系统首先逐步建立完善的NDON系统,实现缺料呼叫、设备故障呼叫、作业延迟呼叫、质量问题呼叫等自动报警功能,再将管理看板与信息系统、NDON系统等链接,即时显示生产计划达成、品质合格率、现场异常等相关信息,促使管理者快速采取应对措施,如图4-7所示。
(三)品质提升当前公司现行的质量体系主要缺陷有三点:专题研究不够深入、缺少预防性的防错研究、质量体系执行不到位。
要解决这一问题,依照精益生产TQM思想指导,需在企业内部展开全流程、全部门、全员参与的品质改善活动,主要包括三方面:质量改善专题研究、区域管理责任人机制、全员参与质量改善活动。
1.质量改善专题研究(1)建立质量专题项目团队,通过分析选择改善课题并做现状调查,再通过原因分析进行对策制定,最后通过改善执行反馈改善效果并进行标准化推广一。
(2)在改善过程中,本着科学客观的态度,充分应用多方面的统计方法和工具进行分析,主要方法有头脑风暴法、亲和图、树图、流程图、排列图、FME,分层法、散布图、直方图、因果图、五五法、DOE、田口方法、防呆法、SPC控制图、抽样检测、目视管理、TPM等。
- 1、下载文档前请自行甄别文档内容的完整性,平台不提供额外的编辑、内容补充、找答案等附加服务。
- 2、"仅部分预览"的文档,不可在线预览部分如存在完整性等问题,可反馈申请退款(可完整预览的文档不适用该条件!)。
- 3、如文档侵犯您的权益,请联系客服反馈,我们会尽快为您处理(人工客服工作时间:9:00-18:30)。
如何管控工厂UPPHUPPH是units Per Hour Per Person单位人时产能的缩写,是公司作为衡量员工工作绩效的重要指标。
UPPH是衡量员工单位时间工作量的一种绩效指标。
UPPH计算方式如下:UPPH=工作量/(投入时间*投入人力)。
(投入时间以小时计算)。
先算出总工时(人数×工时),再用总产量除以总工时,例:50人,8小时,600产量,UPPH=600÷(50×8)=1.5。
由上式可见,员工绩效与UPPH成正比关系。
大多数国际公司都以UPPH作为员工绩效评比的重要指标。
UPH(units per hour)单位小时产能,指每小时的产量,UPH=年生产量/(12*月工作日*日工作小时)或UPH=日生产量/日工作小时;UPPH(units per people per hour)人均时产能,指每小时每个人的产能,UPPH=年生产量/(12月*月工作日*日工作小时*工人人数)或UPPH=日生产量/(日工作小时*投入人工).UPH和UPPH算出来的都是某个工位的产能。
先进的管控工厂UPPH方案:一、总体指导思想1.精益生产作为当今最为先进的制造管理方法,具有很强的实践性。
改善实施必须始终围绕精益生产管理体系的核心即消除浪费来开展各项工作,时时以精益生产思想作为工作指导的有力武器。
2.任何一项管理理论都不是一成不变的适用每一个企业。
在应用精益生产理论进行改善时,必须时刻结合企业所处的行业环境和企业本身的特殊性进行灵活应用,因地制宜。
只有这样,才一不至于在改善中生搬硬套,走错方向。
例如由于手机行业存在市场机会成本,战略要求不能完全做到“零库存”管理。
3一个拥有卓越企业文化和管理的企业,需要经过多年的实践积淀才能实现。
丰田公司自成立初期就开始不断探讨生产模式,历经四十年时间才一逐步形成了初步成型的丰田方式。
时至今日,丰田方式仍在不断改善进步中。
因此,没有那个企业的实现是一瞰而就的,需要一点一滴的积累。
卓越企业管理需要系统性的全面进行改善,但需要结合实际状况分步骤分门别类的逐步改善进而达成阶段目标并最终实现总目标。
4.改善不能脱离现场。
所有数据必须现场测量,所有问题必须现场观察,充分与一线员工交流并亲身实践才能得出结论。
脱离现场,脱离实际,脱离基层员工,任何改善都只是纸上谈兵。
5.改善成果必须实现标准化,没有标准化的改善不是完美的改善。
6.精益生产的改善需要以人为本,全员参与。
只有全员参与,充分发挥人的主动性和能动性,改善才能处处开花。
7.改善是一个持续创新不断发现问题不断进步的过程。
没有最好,只有更好,持续改善,不断进步,这是丰田方式的精髓。
只有深深理解这一精髓,并将其作为企业文化融入到员工心中,才能够在精益生产的实践应用中取得长久发展。
二、实施方案指导框架结合企业自身实际状况,借鉴国内外的精益生产理论指导和实践案例研究,研究将精益生产的各钟软硬件技术进行分类,提出了新的改善模型,作为公司推行精益生产管理的指导框架。
改善模型称为新“TPS”模型,T代表技术(Technology ),P代表人员(Person ),S代表系统(System,如图4-1所示。
改善的三个维度分别是技术改善、系统支持以及人才培养,如图4-2所示。
制造技术的改善代表着生产技术的改进,而支持系统则是从流程设计上来进行优化,而人才培养正是从以人为本的角度出发,对人的能力、意愿和文化进行培养熏陶,从而最大程度的发挥人的主观能动性,实现企业的长久发展。
以新“TPS”管理模型作为公司精益生产应用推广的指导框架,针对当前生产中存在的主要问题从制造技术、支持系统以及人才培养三个维度进行深入分析及改善方案研究。
三、制造技术改善(一)生产模式优化从当一前的生产模式来看,产品从原材料入库到产品最终出货,中间需要五处等待,半成品需要入暂存仓两次,等待时一间占整个生产周期的96.5%,浪费巨大。
依照精益生产单件流和连续流的指导思想,需要做进一步的改善优化。
当然,生产模式的优化需要逐步推进,结合公司现状,提出以下四步走的改善建议。
第一步,通过改善,将整机组装测试段与包装段连在一起,实现整机组装的连续流;第二步,通过改善,将主板加工测试段与整机组装测试包装段连在一起,实现整个生产流程的连续流;第三步,通过改善,逐步实现手机生产的单元化生产(Cell生产线);第四步,通过进一步全业务流程的优化设计,实现真正意义上的的准时制生产。
生产模式的变革需要全公司各个部门尤其是生产计划及信息系统的支持,所以这是一个很大的业务流程优化工程,需要逐步实现。
(二)效率提升1.效率革新指导框架通过研究之前的数据收集及分析,公司缺少相应的效率数据收集、分析改善及监控体系。
本着消除浪费的目的,逐步建立全面的效率革新体系。
首先建立标准工时数据库,再依次通过嫁动率提升、操作效率提升、线平衡改善、合格率提升、省人化改善等基础措施来实现流程化、准时化、信息化的快速反应体系,最终达到效率的最大化,如图4-3。
2.生产效率损失分析借鉴优秀工厂管理的实践经验,研究将效率的损失划分为22大类,除管理效率损失需要其它部门协助整理信息外,其它资料都需要在生产车间现场收集,如图4-4。
3.效率革新步骤通过研究归纳总结,将效率革新分为九大步骤:(1)意识革命通过课程培训,使精益生产改善的主体对“浪费”及“价值”有初步的认识。
然后通过“现场寻找浪费活动”,使精益生产改善的主体切实体会到发生在周围的诸多浪费现象并作记录,然后拟定改善计划并自己动手实施改善,将认识转化为行动。
(2)标准工时基础建立首先聘请专业技术人员应用工业工程作业测定法对标准工时制定人员进行培训,然后由IE工程师主导建立标准工时基础数据库,最后通过各级审核后由文件管控中心作为标准文件发行管控。
(3)效率衡量标准构建依照工厂管理损失分类将各项指标分解至详细指标,并将每项数据收集工作落实至每个责任部门并确保信息收集的准确性。
然后通过定期检讨会议,汇报效率达成并分析主要瓶颈问题及责任部门,建立全面效率监控体系,以制度督促责任部门持续改善。
生产效率损失统计分析报表主要包括以下内容:一级报表(高层管理):产量日周月推移图、UPPH日周月推移图、损失工时柏拉图;二级报表(中层管理):区域产量日周月推移图、区域UPPH日周月推移图、区域损失工时柏拉图;三级报表(基层管理):、班组产量小时推移图、班组UPPH小时推移图、班组工时损失录入。
(4)嫁动率提升:通过计划排程优化、设施布局合理规划、供应商质量提升、全员TPM活动、现场异常快速处理、以及SMED等活动的开展逐步提升稼动率,减少浪费。
(5)操作效率提升建立作业标准,消除无效作业,同时通过引入创新性的标准化技能培训法快速提高员工作业效率,再通过技能比武及合适的绩效考核等机制从主观上督促员工提高操作效率。
(6)线平衡率提升:通过应用工业工程ECRS原则、作业研究、程序分析、动作经济原则等技巧进行生产线平衡的分析,从工艺角度进行改善,减少不平衡生产带来的损失。
(7)省人化:多能工作为实现均衡生产非常重要的策略,可有效提高工作利用率,达到少人化的目的。
而自动化或半自动化设备的使用可有效减少人员操作时间或直接把人解放出来,从而减少操作人力。
手机制造的组装动作主要由贴、熔、点、锁、装、测、检、包、送九大操作动作完成,当前可实现的主要作业有自动贴膜、自动锁螺丝等。
(8)快速反应系统首先逐步建立完善的NDON系统,实现缺料呼叫、设备故障呼叫、作业延迟呼叫、质量问题呼叫等自动报警功能,再将管理看板与信息系统、NDON系统等链接,即时显示生产计划达成、品质合格率、现场异常等相关信息,促使管理者快速采取应对措施,如图4-7所示。
(三)品质提升当前公司现行的质量体系主要缺陷有三点:专题研究不够深入、缺少预防性的防错研究、质量体系执行不到位。
要解决这一问题,依照精益生产TQM思想指导,需在企业内部展开全流程、全部门、全员参与的品质改善活动,主要包括三方面:质量改善专题研究、区域管理责任人机制、全员参与质量改善活动。
1.质量改善专题研究(1)建立质量专题项目团队,通过分析选择改善课题并做现状调查,再通过原因分析进行对策制定,最后通过改善执行反馈改善效果并进行标准化推广一。
(2)在改善过程中,本着科学客观的态度,充分应用多方面的统计方法和工具进行分析,主要方法有头脑风暴法、亲和图、树图、流程图、排列图、FME,分层法、散布图、直方图、因果图、五五法、DOE、田口方法、防呆法、SPC控制图、抽样检测、目视管理、TPM等。
2.区域管理责任人机制当前公司质量管理体系执行不到位的最主要问题在于部门间利益方向的矛盾J性,从而导致出现问题相互抱怨相互推i}而并不能解决实质性问题。
为解决这一问题,提出以下两点改善建议:(1)将生产线所有相同组装、包装线依车间划分至制造部三大部门各经理,由生产部、品质部、工程部经理作为各区域品质指标负责人,由其负责组织各部门人员进行质量改善分析,并进行定期检讨及评比公告。
(2)将责任区域质量达成状况计入管理责任人绩效考核指标;3.全员参与质量改善活动(1) TQM质量管理的核心思想是全员参与质量改善。
研究认为应通过意识宣讲引导全员紧紧围绕质量改善参与到活动中来,并结合全员提案改善机制建立相应的激励机制。
需要特别指出,在实际的质量改善过程中,事前预防并进行防呆防错控制是质量管理的最高境界,而不断持续改善是质量管理的最大支柱所在。
在实施全面质量管理时,需适时奖励优秀项目和个人并加大力度全面宣传,从意识思维上引导员工树立正确的品质观念。
(四)TPM全员生产保全依照精益生产TPM思想,其首要目的就是要事先预防、并消除设备故障所造成的七大损失:准备调整、器具调整、加速老化、检查停机、速度下降和生产不良品。
做到零故障、零不良、零浪费和零灾害,在保证生产效益最大化的同时,实现费用消耗的合理化。
公司当前设备管理处于初级水平,具有一些事前维护思想,但管理不系统不完善,且都是专业技术人员执行。
经过分析,建议成立TPM管理改善项目,推进设备管理的改善进步。
(五)5S及目视化管理尽管当前公司曾经开展过初级SS活动,但活动仅浮于表面流于形式,并没有产生实际效果,也并没有维持下去。
时至今日,生产现场又回到了原先脏乱差的环境,更无系统性的目视化管理。
而作为精益生产管理应用的基础之一,5S和目视化管理不仅要做好还要持续下去。
解决这一问题的根本方法就是通过培训使得员工逐步意识到5S和目视化管理带来的好处,并建立相应的管理机制,从制度监督开始到主动进行活动开展。
研究经过分析,针对公司SS及目视化管理提出以下改善策略。
1.5S管理推行首先,为了有效地推进SS活动,需要建立一个符合企业条件的推进组织一5S推行委员会。