首件标识卡
机加工首件检验记录表
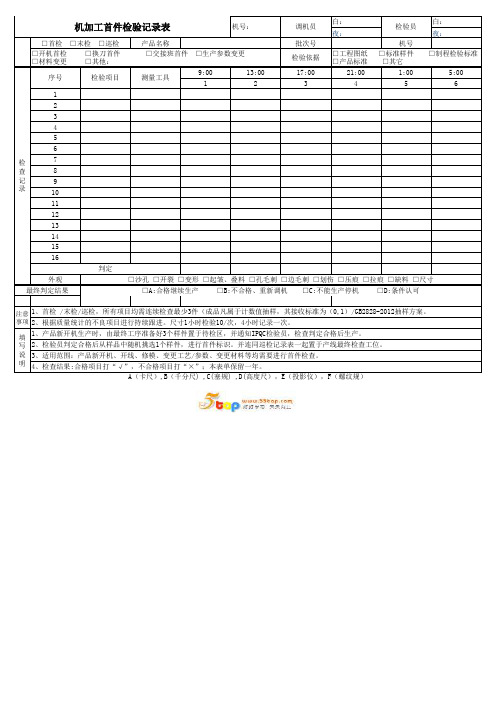
最终判定结果
□A:合格继续生产 □B:不合格、重新调机 □C:不能生产停机 □D:条件认可
注意 1、首检 /末检/巡检,所有项目均需连续检查最少3件(成品凡属于计数值抽样,其接收标准为(0,1)/GB2828-2012抽样方案。 事项 2、根据质量统计的不良项目进行持续跟进。尺寸1小时检验10/次,4小时记录一次。
A(卡尺),B(千分尺) ,C(塞规) ,D(高度尺),E(投影仪),F(螺纹规)
检验依据
□工程图纸 □产品标准
□标准样件 □其它
□制程检验标准
序号
检验项目
测量工具
9:00 1
13:00 2
17:00 3
21:00 4
1:00 5
5:00 6
1
2
3
4
5
6
检
7
查
8
记
9
录
10
11Hale Waihona Puke 121314
15
16
判定
外观
□沙孔 □开裂 □变形 □起皱、叠料 □孔毛刺 □边毛刺 □划伤 □压痕 □拉痕 □缺料 □尺寸
0010111213141516判定外观开裂变形起皱叠料孔毛刺边毛刺划伤压痕缺料尺寸最终判定结果开机首检交接班首件生产参数变更材料变更其他
机加工首件检验记录表
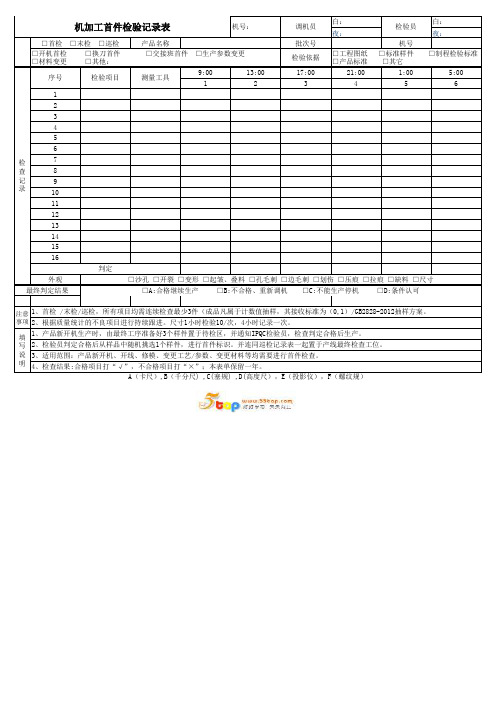
机号:
调机员
白: 夜:
检验员
白: 夜:
□首检 □末检 □巡检
产品名称
批次号
机号
□开机首检 □材料变更
□换刀首件 □其他:
□交接班首件 □生产参数变更
检验依据
□工程图纸 □产品标准
□标准样件 □其它
□制程检验标准
序号
检验项目
测量工具
9:00 1
13:00 2
17:00 3
21:00 4
A(卡尺),B(千分尺) ,C(塞规) ,D(高度尺),E(投影仪),F(螺纹规)1:ຫໍສະໝຸດ 0 55:00 61
2
3
4
5
6
检
7
查
8
记
9
录
10
11
12
13
14
15
16
判定
外观
□沙孔 □开裂 □变形 □起皱、叠料 □孔毛刺 □边毛刺 □划伤 □压痕 □拉痕 □缺料 □尺寸
最终判定结果
□A:合格继续生产 □B:不合格、重新调机 □C:不能生产停机 □D:条件认可
注意 1、首检 /末检/巡检,所有项目均需连续检查最少3件(成品凡属于计数值抽样,其接收标准为(0,1)/GB2828-2012抽样方案。 事项 2、根据质量统计的不良项目进行持续跟进。尺寸1小时检验10/次,4小时记录一次。
填 1、产品新开机生产时,由最终工序准备好3个样件置于待检区,并通知IPQC检验员,检查判定合格后生产。 写 2、检验员判定合格后从样品中随机挑选1个样件,进行首件标识。并连同巡检记录表一起置于产线最终检查工位。 说 3、适用范围:产品新开机、开线、修模、变更工艺/参数、变更材料等均需要进行首件检查。 明 4、检查结果:合格项目打“√”,不合格项目打“×”;本表单保留一年。
GJB9001程序文件——首件鉴定控制程序

XXXXXXXXXXXXXX有限公司
首件鉴定控制程序
1 目的
按照图纸及技术文件的要求,对试制和批量生产的第一个(批)铸件或机加工件进行全面的工序和成品检查,以确定生产工艺和设备能否生产出符合要求的产品。
2 适用范围
本程序仅适用于公司军品、航空航天产品及客户要求的产品的首件鉴定。
3 职责
3.1总工程师负责组建首件鉴定小组;
3.2技术部负责编制航空航天产品的“首件鉴定目录”,质量控制部会签;
3.3质量控制部负责对工序和成品的检查。
3.4首件鉴定小组:
a)监督首件的制造;
b)召开鉴定会,做出鉴定结论;
c)对鉴定中提出的有异议的问题进行复验。
4 工作程序
4.1首件鉴定的范围
当出现下列情况之一时,应进行首件检验:
a)生产工艺定型前试制的零部件的首件;
b)设计图样有重大变更(如涉及性能、安全性、可靠性等)后制造的首件;
c)工艺规程的重大变更(如涉及工艺方法、检测方法等)对产品符合性产
生影响的首件;
d)产品转厂生产后的首件;
e)非连续生产批次生产的首件;。
首末检管理规定
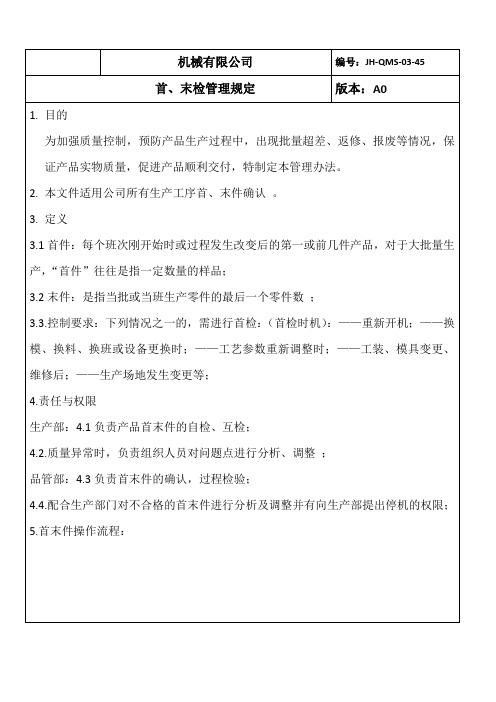
首件类别: □新产品首件 □批次首件 □停、开机首件 □材料规格变更首件
产品/零件名称:
订单号:
生产日期
操作者:
生产时间
检验结果
QC 确认结果
QC 签名:
表格编号:JH-JL-07-57
机械有限公司
首末检管理规定 JH-QMS-03-45
编制/日期: 审核/日期:
批准/日期:
版本:A0
说明
责任部门
相关记录
班、组长对操和工进行必须的岗前培训,准 备好生产所需的技术文件和工装治具,并确 认文件和治具正确性和适用后,派发给操作 工,作业前对人、机、料、法、环进行确认
生产部
《作业准备验证记录表》
经培训合格的员工允许上岗,并按照技术资 料和步骤,第个独立的作业单位首先生产第 一件产品
流程图
机械有限公司 末件流程图 说明
编号:JH-QMS-03-45
版本:A0
责任部门
相关记录
产结束前
OK
作业员
OK
班组长
OK
通知 当班 班长 立即 调查 原因 并整 改
检验员
NG
OK
》
作业员需对当班或当批次生产的末件进行自 检
1. 当班班长需对作业员自检的末件进行互 检
2. 确认后如末件合格,需通知当班检验员 对末件进行确认
品管部 《自检记录表》
品
当 班 生 《自检记录表,并在样件上巾上末件标签进
标
产 的 产 行封样
识
品进行
标识
流入下 道工序
不良品进 行标识
检验员对当班生产合格的零件贴上合格标识 在流转卡上签字确认,并通知生产部门可流 入到下道工序
品管部 生产部
首末件管理规定
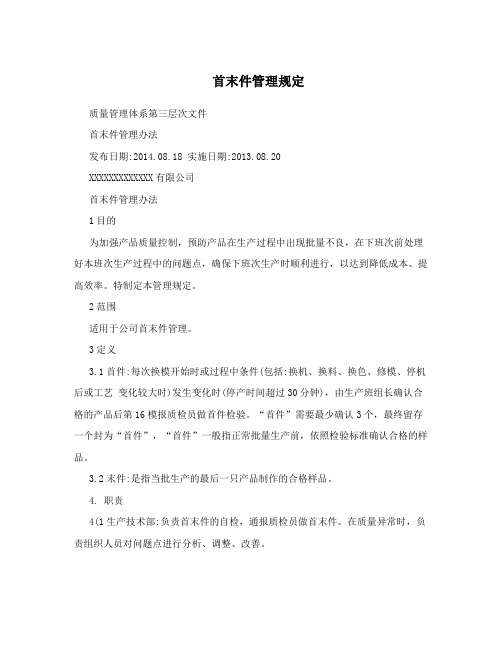
首末件管理规定质量管理体系第三层次文件首末件管理办法发布日期:2014.08.18 实施日期:2013.08.20XXXXXXXXXXXXX有限公司首末件管理办法1目的为加强产品质量控制,预防产品在生产过程中出现批量不良,在下班次前处理好本班次生产过程中的问题点,确保下班次生产时顺利进行,以达到降低成本、提高效率。
特制定本管理规定。
2范围适用于公司首末件管理。
3定义3.1首件:每次换模开始时或过程中条件(包括:换机、换料、换色、修模、停机后或工艺变化较大时)发生变化时(停产时间超过30分钟),由生产班组长确认合格的产品后第16模报质检员做首件检验。
“首件”需要最少确认3个,最终留存一个封为“首件”,“首件”一般指正常批量生产前,依照检验标准确认合格的样品。
3.2末件:是指当批生产的最后一只产品制作的合格样品。
4. 职责4(1生产技术部:负责首末件的自检,通报质检员做首末件。
在质量异常时,负责组织人员对问题点进行分析、调整、改善。
4(2质量保证部:负责首末件的确认及过程检验。
配合生产技术部门对不合格的首末件进行分析,并有权提出停机要求及改善要求。
5. 控制流程开机生产NG追溯首件检验OK末件留样首批OK 件量留生NG 样产检验生产结束6. 流程说明6(1生产开始时根据本规定的第3.1条款,需要制作首件时,由生产技术部班组长提供产品通报当班质检员进行首件检验。
6.1.1当班质检员接到生产技术部班长通知后,根据《生产计划单》和《检验指导书》对该机台的产品进行检验判定。
6.1.2质检员需在10分内做出外观判定,20分钟内做出最终判定,判定中包含原材料确认。
6.1.3若检验结果符合要求的要及时做好首件样品(样品包括:日期、时间、质检员签名)和加工样品并挂于相应的机台上,检验结果不符合标准要求的,质检员需立即通报生产班组长重新调试,重新报检。
6.2首件再确认:当首件确认合格后生产了1.6-2小时时,质检员要对生产中的产品进行一次再确认。
首件检验程序
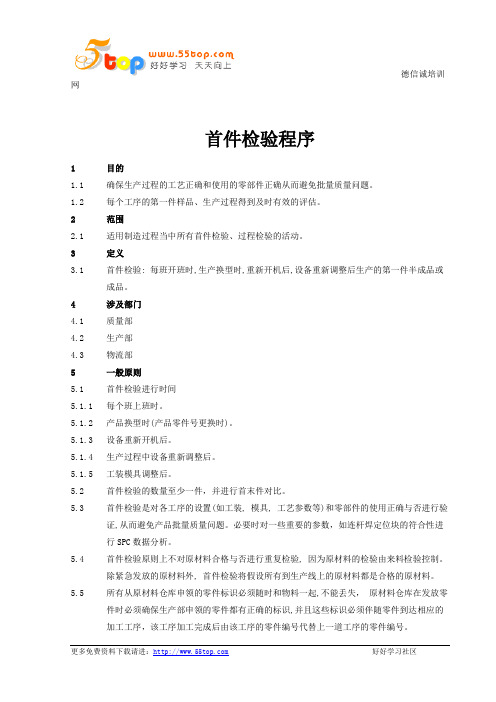
德信诚培训网
首件检验程序
1目的
1.1确保生产过程的工艺正确和使用的零部件正确从而避免批量质量问题。
1.2每个工序的第一件样品、生产过程得到及时有效的评估。
2范围
2.1适用制造过程当中所有首件检验、过程检验的活动。
3定义
3.1首件检验: 每班开班时,生产换型时,重新开机后,设备重新调整后生产的第一件半成品或
成品。
4涉及部门
4.1质量部
4.2生产部
4.3物流部
5一般原则
5.1首件检验进行时间
5.1.1每个班上班时。
5.1.2产品换型时(产品零件号更换时)。
5.1.3设备重新开机后。
5.1.4生产过程中设备重新调整后。
5.1.5工装模具调整后。
5.2首件检验的数量至少一件,并进行首末件对比。
5.3首件检验是对各工序的设置(如工装, 模具, 工艺参数等)和零部件的使用正确与否进行验
证,从而避免产品批量质量问题。
必要时对一些重要的参数,如连杆焊定位块的符合性进
行SPC数据分析。
5.4首件检验原则上不对原材料合格与否进行重复检验, 因为原材料的检验由来料检验控制。
除紧急发放的原材料外, 首件检验将假设所有到生产线上的原材料都是合格的原材料。
5.5所有从原材料仓库申领的零件标识必须随时和物料一起,不能丢失,原材料仓库在发放零
件时必须确保生产部申领的零件都有正确的标识,并且这些标识必须伴随零件到达相应的
加工工序,该工序加工完成后由该工序的零件编号代替上一道工序的零件编号。
首件确认制度

首件确认制度1、目的为了证实车间在生产大货前首件产品是否符合客户确认样及相关规格的工艺技术要求,防止造成产品批量不合格检验员一定要对车间各道工序、半成品、成品进行高标准检验,对每款大货首件样的工艺、做工、尺寸、规格、款式、颜色等进行全面细致的对比客户确认样及相关技术要求,做到有问题早发现、早处理、尽最大努力保证大货质量及交货期。
2、范围此程序适用于各新产品及每批次产品。
3、职责品质部门负责安排所有产品的首件检验和记录工作。
4、程序4.1各生产阶段及生产成品完成时的第一件货品应及时安排检验员检验,以比对客户确认样,作业书及订单等,并执行外观,包装,功能,测试等既定检验以确认货品符合产品规格及安全标准,首件检验应填写检验记录并报品质主管确认合格后才能放产大货;首件检验报告及问题应及时安排生产,检验员及跟单等有关人员举行质量会议,首件检验发现任何与产品功能及安全要求等不符合的缺陷时,应授权检验员立即停止生产,并确保问题改善后再次首件检验确认合格后才能放产。
4.2大货生产前,检验员知会各工序主要技术人员了解客户的订单资料:包括生产工艺、品质样、最终确认样、色卡、色样、客人确认意见或更正资料,特殊情况可携带客签样作对照。
确认所掌握的所有资料之间《客户原样、最终确认样、工艺单等》完全统一。
对于有不符之处及时反映给生产部、业务部相关人员,以便及时确认。
4.3新产品上线前应小批量试生产,由检验员跟踪检查各工序特别是首件产品可及时发现并改进在大货生产中可能出现的一系列问题,确保批量生产的质量。
4.4各工序对正在加工的首件产品,要按照图样、确认样、进行加工并自检,认为符合要求后,送检验员给予确认。
4.5检验员对首件检验应严格对比客户签样及相关规格确认合格后,贴合格标签,挂卡,作标识。
对个别实测数据有差异时,应会同车间共同测量协调认定。
4.6对发现首件不合格时,应再做第二件直至首检合格后,才能投入批量生产,否则在加工第三件还不合格时,检验员要立即报告生产部给予及时排故和技术指导,保证产品部件的合格。
工序首件标识卡

有限公司
首件标识卡
单号: 品名/型号: 颜色: 生产签字: 综合判定: 确认日期: 品管签字: □合格 年 月 □不合格 日 点 单号: 品名/型号: 颜色: 生产签字: 综合判定: 确认日期:
品有限公司
首件标识卡
品管签字: □合格 年 月 □不合格 日 点
有限公司
首件标识卡
品管签字: □合格 年 月 □不合格 日 点
品有限公司
首件标识卡
单号: 品名/型号: 颜色: 生产签字: 综合判定: 确认日期: 品管签字: □合格 年 月 □不合格 日 点 单号: 品名/型号: 颜色: 生产签字: 综合判定: 确认日期:
有限公司
首件标识卡
品管签字: □合格 年 月 □不合格 日 点
有限公司
首件标识卡
单号: 品名/型号: 颜色: 生产签字: 综合判定: 确认日期: 品管签字: □合格 年 月 □不合格 日 点 单号: 品名/型号: 颜色: 生产签字: 综合判定: 确认日期:
有限公司
首件标识卡
品管签字: □合格 年 月 □不合格 日 点
用品有限公司
首件标识卡
单号: 品名/型号: 颜色: 生产签字: 综合判定: 确认日期: 品管签字: □合格 年 月 □不合格 日 点 单号: 品名/型号: 颜色: 生产签字: 综合判定: 确认日期:
产品的首件检验

任何产品的设计及生产过程中,经常会出现设计变更、工艺变更、制程调整、非计划停线及转产、转线等活动。
那么,如何确保这些活动不会对后续的生产品质产生影响呢?这就需要在作业准备验证、停产后验证阶段进行首件检验了。
Part 1首件及首件检验的定义过程改变生产过程中,5M1E(人、机、料、法、环、测)中任何一个或多个生产要素发生改变,如人员的变动、设备的调整和维修、换料和换工装夹具、设计变更、停线等等。
首件每个班次/产线生产投入开始时或过程发生改变后,生产线加工的第一件或前几件产品。
对于大批量生产来说,“首件”往往是指一定数量的样品。
首件检验对每个班次刚开始时或过程发生改变后,生产线加工的第一或前几件产品进行的检验。
检验的数量,可以根据不同企业或客户的要求制定。
一般来说,至少需要对连续生产的3-5件产品进行检验,合格后方可继续加工后续产品。
在设备或制造工序发生任何变化,以及每个工作班次开始加工前,都要严格进行首件检验。
Part 2首件检验的目的生产过程中的首件检验主要是防止产品出现成批超差、返修、报废,它是预先控制产品生产过程的一种手段,是产品工序质量控制的一种重要方法,是企业确保产品质量,提高经济效益的一种行之有效、必不可少的方法。
首件检验是为了尽早发现生产过程中影响产品质量的因素,预防批量性的不良或报废。
首件检验合格后方可进入正式生产,主要是防止批量不合格品的发生。
长期实践经验证明,首检制是一项尽早发现问题、防止产品成批报废的有效措施。
通过首件检验,可以发现诸如工夹具严重磨损或安装定位错误、测量仪器精度变差、看错图纸、投料或配方错误等系统性原因存在,从而采取纠正或改进措施,以防止批次性不合格品发生。
Part 3首件检验的时机/场合1. 每个工作班开始;2. 更换操作者;3. 更换或调整设备、工艺装备(包括刀具更换或刃磨);4. 更改技术条件、工艺方法和工艺参数(如粗糙度要求变更、内孔铰孔更改为镗孔、数控程序中走刀量或转速等的改变);5. 采用新材料或材料代用后(如加工过程中材料变更等);6. 更换或重新化验槽液等(如磷化、氮化等)。
塑胶五金制程控制程序

塑胶五金制程控制程序1.目的:为确保产品品质的符合性,对产品生产过程进行有效的控制,并对制程的异常状况加以预防和改善,使产品品质能符合客户要求2.范围:2.1本厂五金产品制造、加工的制程品质管控。
2.2本厂塑胶产品的制造、加工的制程品质管控。
2.3 本厂产品组装、装配的制程品质管控。
3.定义:IPQC:In-Process Quality Control 制程品质控制。
4.职责:4.1 品质部:首件确认、巡回检验的执行及制程不良的处理。
4.2 五金部、塑胶部、装配部:生产计划的执行,产品自主检验的执行,模具故障、机器故障的维修,制程不良问题的改善和控制。
4.3 PIE部:制程异常的分析、改善,相关工艺流程图、作业指导书、标准参数值等生产必备资料的提供。
4.4 资材部:生产排期的制定,物料的管控,套料单等生产安排资料的制定。
5.作业程序:5.1 资材部PMC依市场部“生产制单”,排定“生产排期表”及分发“生产排期表”、“套料单”等资料至生产部门,依“生产计划控制程序”办理。
5.2 生产部门主管依PMC“生产排期表”,制定本部门的生产计划安排,进行产前条件的确认,确认内容包括:(1)产品工艺流程图;(2)作业指导书;(3)参数标准及测试标准;(4)生产样板;5.2.1 生产作业前,IPQC必须确认是否有生产样板、检验标准,生产部门必须确认是否有作业性文件等。
5.2.2 若生产条件不完善,必须到相关部门领取生产资料,以达到生产条件的要求。
5.3 生产使用的物料、工模具、设备状况5.3.1 制程生产领用的物料必须是经IQC判定合格,贴有“合格”标识或经批准“特采”使用之物料。
5.3.2 生产前确认工模、设备等状况是否能满足生产要求。
5.4 生产部门主管对生产必须使用的工艺性文件、作业指导书及物料等状况确认后,对作业人员进行必要的解说,使作业人员明白产品特性及品质要求,自检方法和重要的工序参数的设定,同时将作业指导书悬挂于操作现场附近。
首件鉴定格式

首件生产过程原始记录
首件鉴定目录
共页第
页
首件鉴定检验报告
生产单位:编号:
注1:“图样要求”栏中记录所有图样要求。
例如图样上带有名义值和公差的尺寸特性、图样附注等。
注2:特性标识是指关键特性或重要特性的标识。
注3:如果在检验和试验中使用的是专用测量设备时,在“测量设备”栏中记录其设备的编号。
注4:当发现不符合的特性时,在“备注”栏中注明是否重新进行了首件鉴定及其“首件鉴定检验报告”的编号。
首件鉴定审查报告
编号:
注1:在对首件鉴定的状况进行审查时,如发现不符合规定要求时在“备注”栏中加以说明。
注2:鉴定结论可分合格或不合格。
注3:当不适用时,在“鉴定结果”栏中注明“不适用”。
标识使用和管理规定

德信诚培训网更多免费资料下载请进: 好好学习社区 标识使用和管理规定1.目的确保产品的可识别和在需要时对产品质量的形成过程可实现追溯,同时确保合格的产品才投入使用。
2.适用范围2.1适用于需进行检验的产品的状态标识。
2.2适用于产品(包含原辅材料、半成品、成品接收、生产设备及其配件)的标识和追溯。
2.3适用于对公司区域,产品,工艺过程的标识和管理。
3.职责3.1物流按本规定执行有关产品和区域的标识规定。
3.2生产车间按本规定执行有关产品、区域和工艺过程的标识规定。
3.3质量部按本规定执行有关产品的标识规定。
3.4采购部确保供应商配合执行本规定有关产品标识的规定。
4.内容4.1原辅材料进库时,供方应提供材料名称、规格、供方名称、数量、重量等。
4.2仓管员经核对、检查后,以标识卡形式作为标识,明确其加工指令,产品来源、客户名称(订单号、计划单号)、数量,以及待检、已检待定、待处理等标识,分类存放在固定场所或规定货架上。
公司生产的产品经检验后,也应做好标识,内容为产品名称、型号、规格、订单号、产品代号、数量、及有关要求规定的产品、性能参数指标等。
4.3不合格的材料须挂不合格品标识,贴不合格品标签,放置在不合格品区。
4.4对标识不齐全或错误的,应及时补充及更正。
4.5更换包装或重新包装时应核对外箱标识,确保内外统一、一致。
4.6领料时,领料员应根据指令内容、确认核对原材料标识与实物是否相符,对标识错误的原材料拒绝领料。
4.7作业前,各员工应根据《工序操作卡》上的“使用材料”及“材料规格”,“订单号”等相关要求,核对原始材料标识与实物是否相符,核对正确后方可作业。
4.8 作业后,各员工应根据《工序操作卡》以工序流程单形式对完成的半成品进行标识,标。
首件检验单
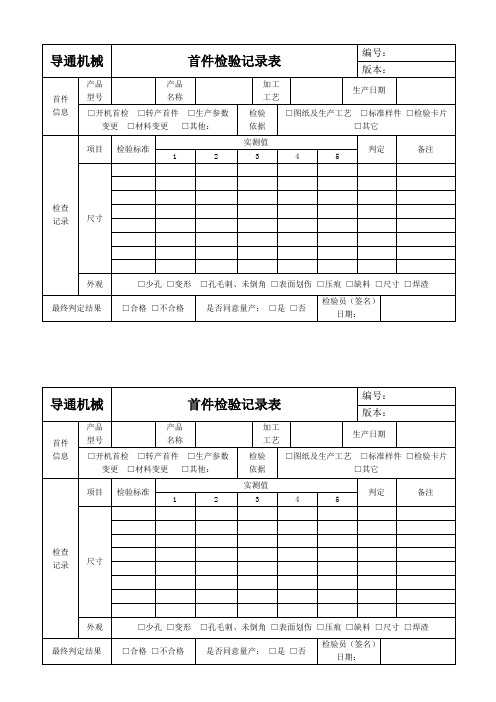
首件检验记录表
编号:
版本:
首件
信息
产品型号
产品
名称
加工
工艺
生产日期
□开机首检□转产首件□生产参数变更□材料变更□其他:
检验
依据
□图纸及生产工艺□标准样件□检验卡片□其它
检查
记录
项目
检验标准
实测值
判定
备注
1
2
3
4
5
尺寸
外观
□少孔□变形□孔毛刺、未倒角□表面划伤□压痕□缺料□尺寸□焊渣
最终判定结果
□合格□不合格
是否同意量产:□是□否
检验员(签名)日期:
导通机械
首件检验记录表
编号:
版本:
首件
信息
产品型号
产品
名称
加工
工艺
生产日期
□开机首检□转产首件□生产参数变更□材料变更□其他:
检验
依据
□图纸及生产工艺□标准样件□检验卡片□其它
检查
记录
项目
检验标准
实测值
判定
备注
1
2
3
4
5
尺寸
外观
□少孔□变形□孔毛刺、未倒角□表面划伤□压痕□缺料□尺寸□焊渣
最终判定结果
□合格□不合格
是否同意量产:□是□否
检验员(签名)日期:
注意
事项
1、所有项目均需连续检查最少5件。
2、根据质量检测的不良项目进行持续跟进。
填写
说明
1、产品新开机生产时,由最终工序准备好5个样件置于待检区,并通知检验员,检查判定合格后生产。
2、检验员判定合格后从样品中随机挑选1个样件,进行首件标识。