机械强度分析
机械强度与刚度分析
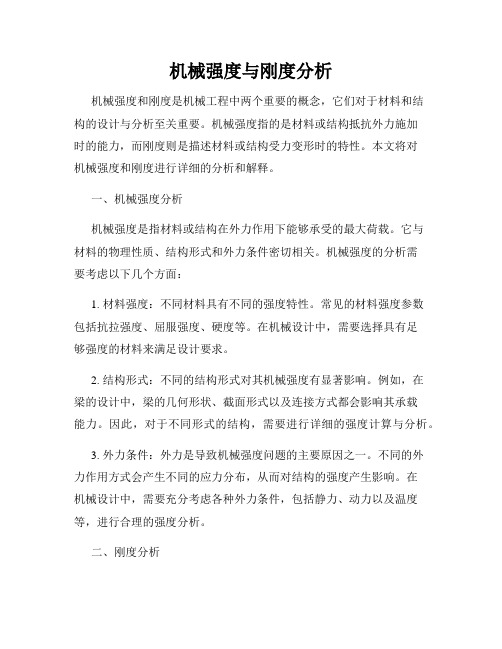
机械强度与刚度分析机械强度和刚度是机械工程中两个重要的概念,它们对于材料和结构的设计与分析至关重要。
机械强度指的是材料或结构抵抗外力施加时的能力,而刚度则是描述材料或结构受力变形时的特性。
本文将对机械强度和刚度进行详细的分析和解释。
一、机械强度分析机械强度是指材料或结构在外力作用下能够承受的最大荷载。
它与材料的物理性质、结构形式和外力条件密切相关。
机械强度的分析需要考虑以下几个方面:1. 材料强度:不同材料具有不同的强度特性。
常见的材料强度参数包括抗拉强度、屈服强度、硬度等。
在机械设计中,需要选择具有足够强度的材料来满足设计要求。
2. 结构形式:不同的结构形式对其机械强度有显著影响。
例如,在梁的设计中,梁的几何形状、截面形式以及连接方式都会影响其承载能力。
因此,对于不同形式的结构,需要进行详细的强度计算与分析。
3. 外力条件:外力是导致机械强度问题的主要原因之一。
不同的外力作用方式会产生不同的应力分布,从而对结构的强度产生影响。
在机械设计中,需要充分考虑各种外力条件,包括静力、动力以及温度等,进行合理的强度分析。
二、刚度分析刚度是指材料或结构在受力作用下的变形特性。
它对于结构的稳定性与变形控制至关重要。
刚度分析需要考虑以下几个方面:1. 弹性模量:弹性模量是衡量材料刚度的重要参数,它描述了材料在一定应力下的应变能力。
不同材料的弹性模量不同,因此在刚度分析中需要准确确定材料的弹性模量。
2. 结构刚度:结构的刚度与其几何形状和材料性质密切相关。
例如,在弹簧设计中,弹簧的刚度与其材料特性、直径和线圈数等因素有关。
因此,结构刚度分析需要充分考虑这些因素。
3. 变形控制:对于某些特定的机械结构,需要在一定范围内控制其变形,以保证其正常工作。
在刚度分析中,需要充分考虑结构变形的要求,并通过适当的方式对变形进行控制。
三、机械强度与刚度优化在机械设计中,机械强度和刚度的优化是一个重要的研究课题。
通过合理选择材料、优化结构形式以及合理设计外力条件,可以提高机械结构的强度和刚度,并满足设计要求。
电力变压器线圈结构分析及机械强度的问题探讨

电力变压器线圈结构分析及机械强度的问题探讨电力变压器线圈结构种类比较多,主要分为低压线圈、高压线圈和调压线圈三种,它们在保障变压器使用安全的过程中扮演着重要的角色。
电力变压器线圈质量对于变压器的运行安全性影响比较大,在变压器线圈机械强度检查活动中,技术人员应该检查线圈使之处于绕紧缠绕牢固的状态,并且对线圈的机械强度进行检验,确保其能够经久耐磨,并在用电高峰期时线圈结构处的电压处于较高状态下线圈不会出现失稳现象。
文章从电力变压器线圈结构安全保障的角度进行分析,提出几点有利于提升电力变压器运行安全性的可行性措施。
标签:变压器;线圈结构;机械强度;电力系统电力变压器的线圈结构应该采用紧密缠绕的方式进行设计,并且不同结构的线圈采用不同的绕组方式。
变压器不同绕组的线圈其径向力和轴向力之间应该满足一定的数值要求,达到径向力和轴向力的对应平衡。
并且,为了确保电力变压器线圈结构的使用安全,技术人员应该对线圈结构的机械强度进行精准控制。
从输入时间及压紧应力进行分析,技术人员应该认真做好短路电流的计算工作,根据电力变压器线圈短路电流的大小计算线圈的弹性系数。
重点对变压器线圈的阻尼因数进行认真计算,防止线圈在电流过大的情况下出现不规则。
计算上下铁圈结构夹件力的大小,保证其符合一定机械强度下的耐磨性能所需。
1 电力变压器线圈结构分析1.1 电力变压器调压线圈结构设计在变压器调压线圈设计方式中,一般有两种层式结构类型,主要分为单匝模型设计方法和双饼模型两种。
双饼模型设计活动中,技术人员应该考虑阻性参数对于铁芯结构的影响,一般来说,支路铁心电感应具有较强的阻抗矩阵效果,如果铁芯结构的设计不够合理,支路空气电感应效果不强。
在变压器的集合结构参数线圈的结构和形式设计活动中,技术人员还应该考虑到阻性参数对于变压器线圈结构的具体影响。
将焦耳损耗和电解质损耗降低到最低水平。
技术人员应该注意处理好铁芯半径与绕组内外半径之间的参数对应关系,总线匝数和饼间垫块数以及垫块宽度,都是影响电力变压器强度的关键参数。
机械强度优化设计分析
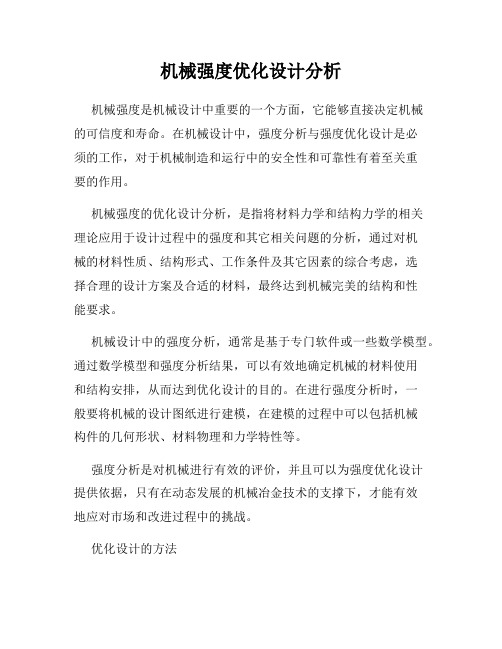
机械强度优化设计分析机械强度是机械设计中重要的一个方面,它能够直接决定机械的可信度和寿命。
在机械设计中,强度分析与强度优化设计是必须的工作,对于机械制造和运行中的安全性和可靠性有着至关重要的作用。
机械强度的优化设计分析,是指将材料力学和结构力学的相关理论应用于设计过程中的强度和其它相关问题的分析,通过对机械的材料性质、结构形式、工作条件及其它因素的综合考虑,选择合理的设计方案及合适的材料,最终达到机械完美的结构和性能要求。
机械设计中的强度分析,通常是基于专门软件或一些数学模型。
通过数学模型和强度分析结果,可以有效地确定机械的材料使用和结构安排,从而达到优化设计的目的。
在进行强度分析时,一般要将机械的设计图纸进行建模,在建模的过程中可以包括机械构件的几何形状、材料物理和力学特性等。
强度分析是对机械进行有效的评价,并且可以为强度优化设计提供依据,只有在动态发展的机械冶金技术的支撑下,才能有效地应对市场和改进过程中的挑战。
优化设计的方法在机械设计中,强度分析和优化设计需要结合特定的工作条件、维修和维护等因素。
此外,机械的快速操作、高可靠性和持久性等因素也需要考虑。
为了达到强度优化设计的目的,有以下几种优化方法。
1.确定对机械的强度分析在机械强度优化设计中,强度分析是必须的,只有通过强度分析才能确定机械的使用材料和结构形式,从而达到优化方案。
强度分析可以根据实际需要分别从静态和动态强度方面进行。
2.选择优化材料为了提高机械的强度和耐用性,机械的材质必须经过仔细的思考和选择,从而选择出最为优化的材料,能够实现机械的安全和可靠性。
3.合理分配结构参数在机械优化设计中,结构参数的分配也是至关重要的。
合理分配结构参数可以改善机械的强度,提高其使用寿命和耐用性,同时还可以增加机械的运行效率。
4.优化压力和温度压力和温度作为机械操作的指标之一,也是机械强度设计优化中需要考虑的内容。
通过对温度和压力的优化,可以提高机械的强度和安全性,同时还能保持机械的稳定状态。
膜的机械强度测定实验报告
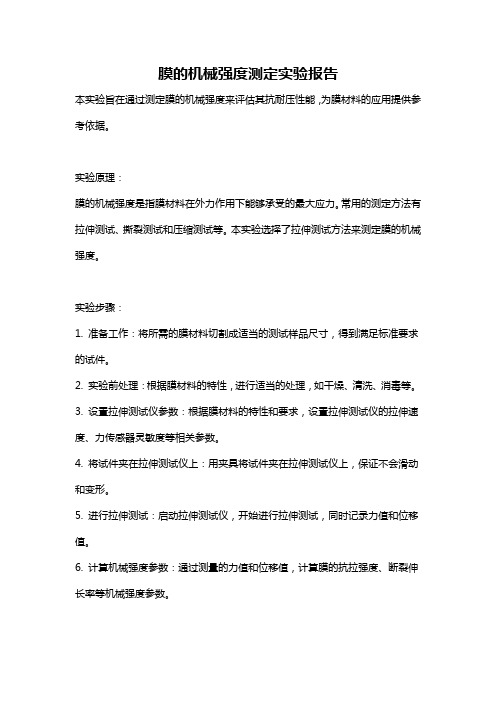
膜的机械强度测定实验报告本实验旨在通过测定膜的机械强度来评估其抗耐压性能,为膜材料的应用提供参考依据。
实验原理:膜的机械强度是指膜材料在外力作用下能够承受的最大应力。
常用的测定方法有拉伸测试、撕裂测试和压缩测试等。
本实验选择了拉伸测试方法来测定膜的机械强度。
实验步骤:1. 准备工作:将所需的膜材料切割成适当的测试样品尺寸,得到满足标准要求的试件。
2. 实验前处理:根据膜材料的特性,进行适当的处理,如干燥、清洗、消毒等。
3. 设置拉伸测试仪参数:根据膜材料的特性和要求,设置拉伸测试仪的拉伸速度、力传感器灵敏度等相关参数。
4. 将试件夹在拉伸测试仪上:用夹具将试件夹在拉伸测试仪上,保证不会滑动和变形。
5. 进行拉伸测试:启动拉伸测试仪,开始进行拉伸测试,同时记录力值和位移值。
6. 计算机械强度参数:通过测量的力值和位移值,计算膜的抗拉强度、断裂伸长率等机械强度参数。
实验结果及数据处理:根据实验测得的力值和位移值,计算得到膜的抗拉强度和断裂伸长率等机械强度参数。
将计算结果绘制成曲线,便于对膜的机械性能进行分析和比较。
实验讨论:膜的机械强度是影响其使用性能的重要指标之一。
通过本实验确定膜的机械强度参数,可以对膜材料的物理性能进行评估和比较,为膜材料的选择和应用提供参考依据。
同时,实验中可能会受到一些因素的干扰,如试件制备的误差、拉伸测试仪的精度等,需要注意这些因素对实验结果的影响。
实验总结:本实验通过测定膜的机械强度来评估其抗耐压性能。
实验结果可以用于膜材料的选择和应用。
在实验中,我们要注意试件制备的准确性和拉伸测试仪的精度,以保证实验结果的准确性和可靠性。
同时,我们还可以通过进一步的实验研究,探究膜材料的机械性能与其结构、成分等之间的关系,为膜材料的开发和改进提供理论基础。
机械强度
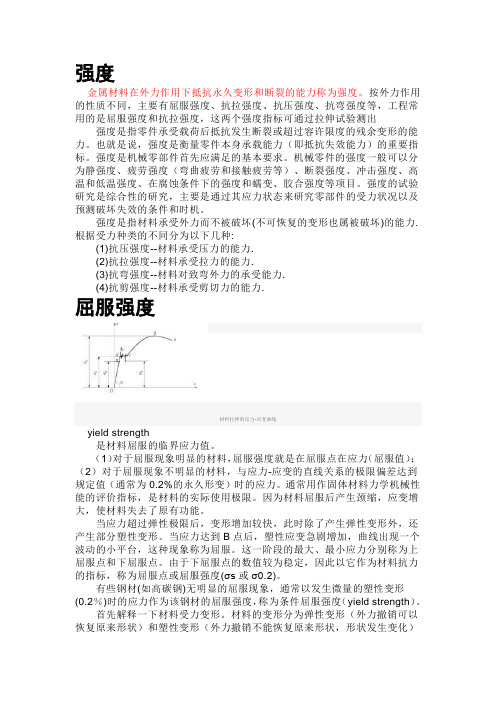
强度金属材料在外力作用下抵抗永久变形和断裂的能力称为强度。
按外力作用的性质不同,主要有屈服强度、抗拉强度、抗压强度、抗弯强度等,工程常用的是屈服强度和抗拉强度,这两个强度指标可通过拉伸试验测出强度是指零件承受载荷后抵抗发生断裂或超过容许限度的残余变形的能力。
也就是说,强度是衡量零件本身承载能力(即抵抗失效能力)的重要指标。
强度是机械零部件首先应满足的基本要求。
机械零件的强度一般可以分为静强度、疲劳强度(弯曲疲劳和接触疲劳等)、断裂强度、冲击强度、高温和低温强度、在腐蚀条件下的强度和蠕变、胶合强度等项目。
强度的试验研究是综合性的研究,主要是通过其应力状态来研究零部件的受力状况以及预测破坏失效的条件和时机。
强度是指材料承受外力而不被破坏(不可恢复的变形也属被破坏)的能力.根据受力种类的不同分为以下几种:(1)抗压强度--材料承受压力的能力.(2)抗拉强度--材料承受拉力的能力.(3)抗弯强度--材料对致弯外力的承受能力.(4)抗剪强度--材料承受剪切力的能力.屈服强度材料拉伸的应力-应变曲线yield strength是材料屈服的临界应力值。
(1)对于屈服现象明显的材料,屈服强度就是在屈服点在应力(屈服值);(2)对于屈服现象不明显的材料,与应力-应变的直线关系的极限偏差达到规定值(通常为0.2%的永久形变)时的应力。
通常用作固体材料力学机械性能的评价指标,是材料的实际使用极限。
因为材料屈服后产生颈缩,应变增大,使材料失去了原有功能。
当应力超过弹性极限后,变形增加较快,此时除了产生弹性变形外,还产生部分塑性变形。
当应力达到B点后,塑性应变急剧增加,曲线出现一个波动的小平台,这种现象称为屈服。
这一阶段的最大、最小应力分别称为上屈服点和下屈服点。
由于下屈服点的数值较为稳定,因此以它作为材料抗力的指标,称为屈服点或屈服强度(σs或σ0.2)。
有些钢材(如高碳钢)无明显的屈服现象,通常以发生微量的塑性变形(0.2%)时的应力作为该钢材的屈服强度,称为条件屈服强度(yield strength)。
机械强度及寿命仿真分析
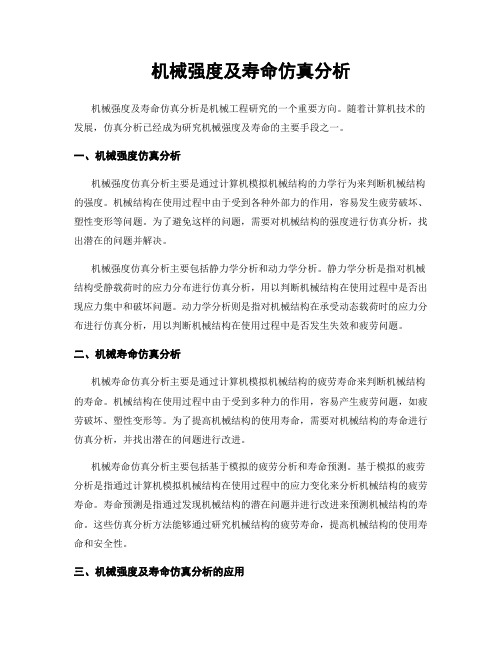
机械强度及寿命仿真分析机械强度及寿命仿真分析是机械工程研究的一个重要方向。
随着计算机技术的发展,仿真分析已经成为研究机械强度及寿命的主要手段之一。
一、机械强度仿真分析机械强度仿真分析主要是通过计算机模拟机械结构的力学行为来判断机械结构的强度。
机械结构在使用过程中由于受到各种外部力的作用,容易发生疲劳破坏、塑性变形等问题。
为了避免这样的问题,需要对机械结构的强度进行仿真分析,找出潜在的问题并解决。
机械强度仿真分析主要包括静力学分析和动力学分析。
静力学分析是指对机械结构受静载荷时的应力分布进行仿真分析,用以判断机械结构在使用过程中是否出现应力集中和破坏问题。
动力学分析则是指对机械结构在承受动态载荷时的应力分布进行仿真分析,用以判断机械结构在使用过程中是否发生失效和疲劳问题。
二、机械寿命仿真分析机械寿命仿真分析主要是通过计算机模拟机械结构的疲劳寿命来判断机械结构的寿命。
机械结构在使用过程中由于受到多种力的作用,容易产生疲劳问题,如疲劳破坏、塑性变形等。
为了提高机械结构的使用寿命,需要对机械结构的寿命进行仿真分析,并找出潜在的问题进行改进。
机械寿命仿真分析主要包括基于模拟的疲劳分析和寿命预测。
基于模拟的疲劳分析是指通过计算机模拟机械结构在使用过程中的应力变化来分析机械结构的疲劳寿命。
寿命预测是指通过发现机械结构的潜在问题并进行改进来预测机械结构的寿命。
这些仿真分析方法能够通过研究机械结构的疲劳寿命,提高机械结构的使用寿命和安全性。
三、机械强度及寿命仿真分析的应用机械强度及寿命仿真分析已经成为工业和科研领域不可或缺的重要工具。
在机械制造中,通过仿真分析可以大大降低机械结构的设计成本,加快机械生产速度,提高机械的使用寿命和安全性。
在科学研究领域,仿真分析可以提供机械结构的强度和寿命预测,这对于提高机械制造的精度和稳定性很有帮助。
总之,机械强度及寿命仿真分析是机械工程研究的重要方向之一。
通过仿真分析可以发现机械结构的弱点和潜在问题,并及时采取措施进行改进,提高机械的安全性和使用寿命。
机械刚度与强度

机械刚度与强度机械刚度和强度是工程设计中非常重要的指标,它们直接影响着机械结构的性能和可靠性。
本文将对机械刚度和强度进行详细介绍,并探讨它们之间的关系和相互影响。
一、机械刚度的概念及意义机械刚度是指物体在受力作用下产生的形变量与所施加的力之间的比值。
简单地说,机械刚度反映了物体在外力作用下的变形程度,能够衡量结构是否能承受外部载荷而保持稳定。
机械刚度的大小与结构的刚性有关。
刚性较大的结构在受力作用下变形较小,具有较高的机械刚度。
而刚性较小的结构在受力作用下变形较大,具有较低的机械刚度。
机械刚度在工程设计中具有重要意义。
一方面,机械刚度可保证结构在工作条件下保持稳定,避免产生过大的变形和振动。
另一方面,机械刚度还对结构的工作性能和寿命产生直接影响。
二、机械强度的概念及意义机械强度是指物体在承受外部力作用下不断发生形变或破坏之前所能承受的最大力的大小。
简单地说,机械强度反映了物体的抗力能力,即承受外部载荷而不会发生破坏的能力。
机械强度与材料的物理和化学性质有关,不同材料的机械强度可以有很大差异。
例如,金属材料的机械强度通常较高,而塑料材料的机械强度较低。
机械强度在工程设计中也具有重要意义。
首先,机械强度可以评估结构是否能够承受预期的外部载荷,保证结构的安全可靠。
其次,机械强度还对结构的抗疲劳性能和使用寿命产生直接影响。
三、机械刚度与强度的关系机械刚度和强度虽然都与结构的力学性能有关,但并不是完全等同的概念。
机械刚度关注结构的形变程度,即结构在受力作用下的变形量。
而机械强度关注结构的承载能力,即结构能够承受的最大力。
机械刚度和强度在很多情况下是相互制约的。
一方面,提高结构的刚度可以降低结构的变形量,减小破坏的可能性,从而提高结构的强度。
例如,在设计桥梁时,增加梁的截面尺寸可以提高其刚度,从而增强桥梁的承载能力。
另一方面,提高结构的强度也可以增加结构的刚度。
例如,在设计高层建筑时,为了提高其整体抗风能力,可以采用更坚固的结构材料和加强梁柱的尺寸,这样既提高了结构的强度,同时也增加了结构的刚度。
800kVGIS长母线管道变工况下机械强度分析
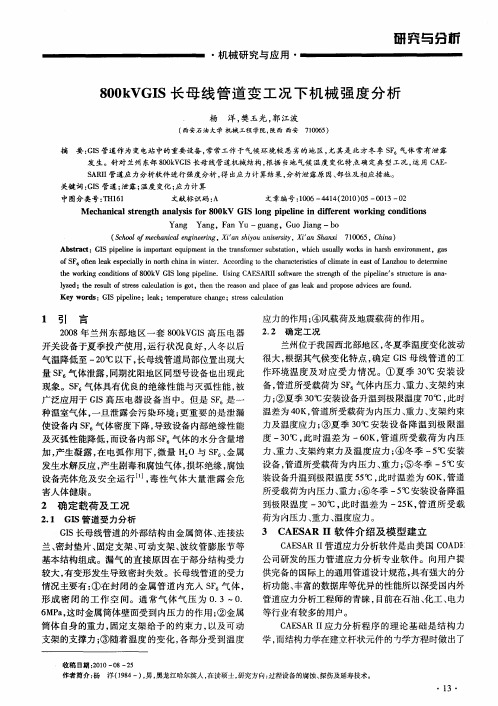
Y n Ya g a ag n ,F n Yu—g a g u n ,Gu in oJa g—b o
( colfm ca i legnei , i,si uui r t, i S ni 70 6 , hn ) Sho o eh n a ie n X n h o nv sy X h x 1o 5 C i c n rg o y ei一套 80 V I 压 电器 0 k G S高
应 力 的作 用 ; ④风 载荷 及地 震载荷 的作 用 。
2 2 确 定 工 况 .
开关设备于夏季投产使用 , 运行状况 良好 , 入冬 以后 气温降低至 一 O 2 ℃以下 , 长母线管道局部位置出现大 量 s F 气体泄露 , 同期沈阳地区同型号设备也 出现此 现象。S6 F 气体具有优 良的绝缘性能与灭弧性能 , 被 广 泛应用 于 GS高 压 电 器 设 备 当 中 。但是 S 6 一 I F是 种 温室气 体 , 一旦 泄 露 会 污染 环 境 ; 重 要 的是 泄漏 更
研 夯 与 分 析
・
机械 研 究 与应 用 ・
8 0 V S长 母 线 管 道 变 工 况 下 机械 强 度 分 析 0 k GI
杨 洋 , 玉光 , 樊 郭江波
70 6 ) 10 5 ( 安石油大学 机械工程学院, 西 西安 西 陕
摘
要 :I G S管道作为 变电站 中的重要设备 , 常常工作 于气候环境较 恶劣 的地 区, 尤其是 北方冬 季 S 6气体 常有 泄露 F
力; ②夏 季 3  ̄ 0C安装设 备 升温到 极 限温度 7  ̄ 此 时 0C, 温 差为 4 K, 0 管道 所受 载荷 为 内压 力 、 重力 、 架 约束 支
力 及温 度应 力 ; 夏 季 3  ̄ 装 设 备 降 温 到极 限 温 ③ 0C安
机械强度与刚度分析中的有限元模拟

机械强度与刚度分析中的有限元模拟机械强度和刚度是工程设计中非常重要的两个参数,对于材料和结构的强度和刚度特性进行分析和预测,可以帮助工程师合理选择材料和设计结构,确保产品在使用过程中具有足够的可靠性和安全性。
而有限元模拟是一种广泛应用于工程领域的计算机模拟方法,可以对复杂的结构和材料进行力学性能分析和优化。
本文将重点探讨机械强度与刚度分析中的有限元模拟方法和应用。
在机械工程中,强度常常指材料在外加载荷作用下的抵抗能力。
材料的强度与其内部的原子结构、晶粒结构和组织等有关,不同材料之间的强度差异很大。
通过有限元模拟可以对材料的强度进行分析,可以确定材料在不同应力下的应变和变形情况,并计算出应力分布、应力集中和破坏点等重要参数。
利用这些信息,工程师可以调整设计方案,选择更合适的材料,减少结构的失效风险。
与强度不同,刚度是指材料在外加载荷作用下的变形能力。
刚度与材料的弹性模量有关,其值越大表示材料的变形能力越小。
有限元模拟可以模拟材料在外加载荷下的变形情况,通过计算结构的刚度系数,可以预测在实际使用中材料或结构的变形情况,进而优化设计,提高产品的稳定性和使用寿命。
有限元模拟包括以下几个主要步骤:建模、离散化、施加边界条件、求解、后处理。
首先,根据实际工程需求,将待分析的物体建模为合适的几何形状。
通过有限元网格划分,将连续的结构离散化为有限个小单元,在每个单元内部选择适当的数学函数进行表达,从而使得整个结构的力学性能满足给定的边界条件。
然后,通过施加边界条件,确定物体的约束条件和加载方式。
在求解过程中,利用数值方法解析结构的力学方程,计算每个单元的应力和应变。
最后,通过后处理,分析各个单元的应力分布,确定结构在外加载荷下的强度和刚度特性。
有限元模拟在机械强度与刚度分析中具有广泛的应用。
例如,在航空航天领域,有限元模拟可以帮助工程师评估飞机结构的强度和刚度,优化设计方案,提高飞机的整体性能。
在汽车工程中,有限元模拟可以对汽车车身和车架的强度和刚度进行分析,确保车辆在行驶过程中具有足够的稳定性和安全性。
机械设计基础机械强度计算
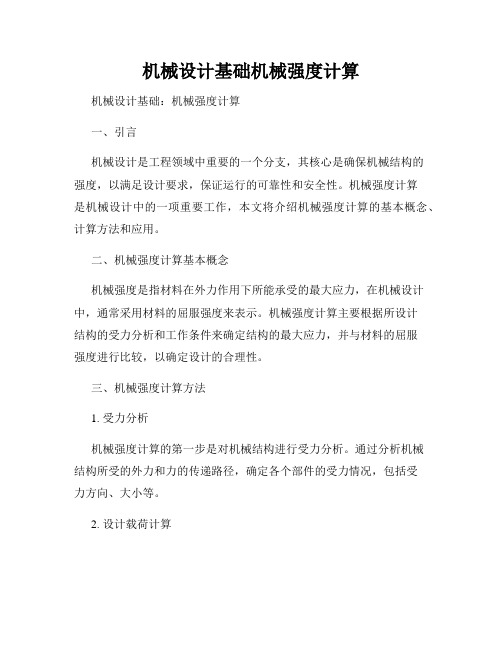
机械设计基础机械强度计算机械设计基础:机械强度计算一、引言机械设计是工程领域中重要的一个分支,其核心是确保机械结构的强度,以满足设计要求,保证运行的可靠性和安全性。
机械强度计算是机械设计中的一项重要工作,本文将介绍机械强度计算的基本概念、计算方法和应用。
二、机械强度计算基本概念机械强度是指材料在外力作用下所能承受的最大应力,在机械设计中,通常采用材料的屈服强度来表示。
机械强度计算主要根据所设计结构的受力分析和工作条件来确定结构的最大应力,并与材料的屈服强度进行比较,以确定设计的合理性。
三、机械强度计算方法1. 受力分析机械强度计算的第一步是对机械结构进行受力分析。
通过分析机械结构所受的外力和力的传递路径,确定各个部件的受力情况,包括受力方向、大小等。
2. 设计载荷计算根据机械结构的工作条件和使用要求,确定机械结构的设计载荷。
设计载荷包括静载荷和动载荷,静载荷是指机械结构在静止状态下所受的力,动载荷是指机械结构在运动过程中所受的力。
3. 应力分析根据受力分析和设计载荷计算,计算机械结构各个部件的应力分布情况。
应力分析包括正应力和剪应力的计算,正应力是指垂直于截面的应力,剪应力是指平行于截面的应力。
4. 强度校核根据材料的强度性能参数和所设计结构的应力情况,进行强度校核。
强度校核是通过将结构所受的最大应力与材料的屈服强度进行比较,判断结构是否满足设计要求。
四、机械强度计算的应用机械强度计算广泛应用于各个工程领域中的机械设计中,例如汽车工程、航空航天工程、机械加工等。
机械强度计算可以帮助设计师合理选择材料、确定结构尺寸和形状,以保证机械结构的强度和稳定性。
五、结论机械强度计算是机械设计中不可或缺的一部分,它通过分析受力情况、计算设计载荷和应力分析,校核结构的强度,以确保机械结构的可靠性和安全性。
在实际工程中,机械强度计算是提高机械设计质量的重要手段,也是保障工程安全的关键环节。
六、参考文献[1] 李明华. 机械设计基础[M]. 北京:机械工业出版社,2010.[2] 赵海山. 机械设计课程教程[M]. 北京:机械工业出版社,2015.。
机械强度参数的试验与分析
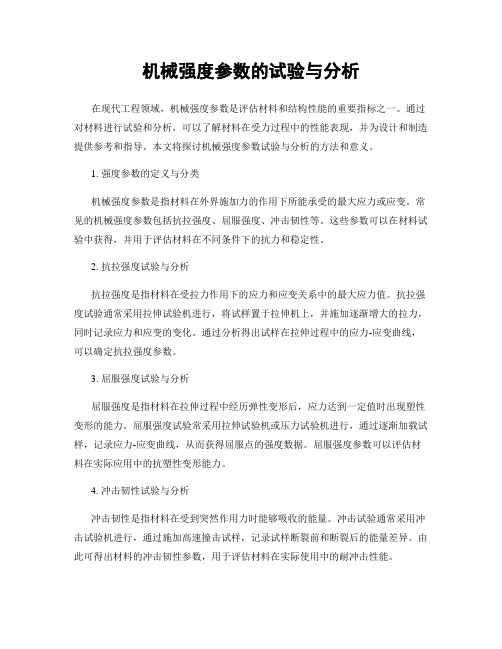
机械强度参数的试验与分析在现代工程领域,机械强度参数是评估材料和结构性能的重要指标之一。
通过对材料进行试验和分析,可以了解材料在受力过程中的性能表现,并为设计和制造提供参考和指导。
本文将探讨机械强度参数试验与分析的方法和意义。
1. 强度参数的定义与分类机械强度参数是指材料在外界施加力的作用下所能承受的最大应力或应变。
常见的机械强度参数包括抗拉强度、屈服强度、冲击韧性等。
这些参数可以在材料试验中获得,并用于评估材料在不同条件下的抗力和稳定性。
2. 抗拉强度试验与分析抗拉强度是指材料在受拉力作用下的应力和应变关系中的最大应力值。
抗拉强度试验通常采用拉伸试验机进行,将试样置于拉伸机上,并施加逐渐增大的拉力,同时记录应力和应变的变化。
通过分析得出试样在拉伸过程中的应力-应变曲线,可以确定抗拉强度参数。
3. 屈服强度试验与分析屈服强度是指材料在拉伸过程中经历弹性变形后,应力达到一定值时出现塑性变形的能力。
屈服强度试验常采用拉伸试验机或压力试验机进行,通过逐渐加载试样,记录应力-应变曲线,从而获得屈服点的强度数据。
屈服强度参数可以评估材料在实际应用中的抗塑性变形能力。
4. 冲击韧性试验与分析冲击韧性是指材料在受到突然作用力时能够吸收的能量。
冲击试验通常采用冲击试验机进行,通过施加高速撞击试样,记录试样断裂前和断裂后的能量差异。
由此可得出材料的冲击韧性参数,用于评估材料在实际使用中的耐冲击性能。
5. 应力-应变曲线分析除了以上具体的机械强度参数试验外,对材料进行应力-应变曲线分析也是了解机械强度的重要手段。
通过应力-应变曲线可以了解材料在变形过程中的不同阶段和变化规律,从而对材料性能做出综合评估和判断。
综上所述,机械强度参数的试验与分析对于材料性能评估和工程设计具有重要意义。
通过不同试验方法,可以获得具体的强度参数值,并在实际应用中为相关领域提供参考和指导。
此外,应力-应变曲线的分析也有助于深入了解材料的力学性能和变形行为。
3D打印材料的机械强度性能及应用案例分析
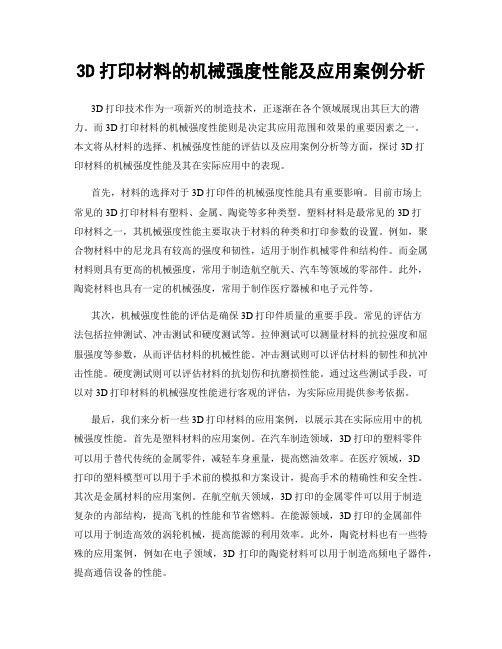
3D打印材料的机械强度性能及应用案例分析3D打印技术作为一项新兴的制造技术,正逐渐在各个领域展现出其巨大的潜力。
而3D打印材料的机械强度性能则是决定其应用范围和效果的重要因素之一。
本文将从材料的选择、机械强度性能的评估以及应用案例分析等方面,探讨3D打印材料的机械强度性能及其在实际应用中的表现。
首先,材料的选择对于3D打印件的机械强度性能具有重要影响。
目前市场上常见的3D打印材料有塑料、金属、陶瓷等多种类型。
塑料材料是最常见的3D打印材料之一,其机械强度性能主要取决于材料的种类和打印参数的设置。
例如,聚合物材料中的尼龙具有较高的强度和韧性,适用于制作机械零件和结构件。
而金属材料则具有更高的机械强度,常用于制造航空航天、汽车等领域的零部件。
此外,陶瓷材料也具有一定的机械强度,常用于制作医疗器械和电子元件等。
其次,机械强度性能的评估是确保3D打印件质量的重要手段。
常见的评估方法包括拉伸测试、冲击测试和硬度测试等。
拉伸测试可以测量材料的抗拉强度和屈服强度等参数,从而评估材料的机械性能。
冲击测试则可以评估材料的韧性和抗冲击性能。
硬度测试则可以评估材料的抗划伤和抗磨损性能。
通过这些测试手段,可以对3D打印材料的机械强度性能进行客观的评估,为实际应用提供参考依据。
最后,我们来分析一些3D打印材料的应用案例,以展示其在实际应用中的机械强度性能。
首先是塑料材料的应用案例。
在汽车制造领域,3D打印的塑料零件可以用于替代传统的金属零件,减轻车身重量,提高燃油效率。
在医疗领域,3D打印的塑料模型可以用于手术前的模拟和方案设计,提高手术的精确性和安全性。
其次是金属材料的应用案例。
在航空航天领域,3D打印的金属零件可以用于制造复杂的内部结构,提高飞机的性能和节省燃料。
在能源领域,3D打印的金属部件可以用于制造高效的涡轮机械,提高能源的利用效率。
此外,陶瓷材料也有一些特殊的应用案例,例如在电子领域,3D打印的陶瓷材料可以用于制造高频电子器件,提高通信设备的性能。
462Q活塞机械强度的有限元分析

随着 社会 工 业化 的发 展 , 车发 动 机 性 能要 求 汽 日益 提高 。活塞 组作 为 内燃机 的关 键 部 件, 为发 作 动 机 中工 作 条件 最 严酷 的零 部件 , 的结 构 和所 处 它 的工作 环 境 十分 复 杂, 在工 作 状 态下 受 到高 压燃 气 压 力 、 速 往 复 运 动 产 生 的 惯性 力 、 向压 力 和 摩 高 侧
气 缸 内工质 作用 在活 塞上 的总气 体压 力 P 为 :
P = G P P — 0
2
内 燃 机 与 配 件
21 0 1年 第 l 期 l
作用 在 曲柄 连杆 机构 上 的力 P为 :
P= P Pj
式 中 ,。 P 为缸 内绝 对压 力 , = . MP ;o P 89 a P 为 大气 压力 . 一般 取 01MP 。 . a
其 中 入为 曲柄 半 径 和 连 杆 长 度 的 比 . = .5 r h O3 :
为 曲轴半 径 ,= 0mm, n= r r4 X ̄ 2。 x
22 活 塞 瞬 时速 度 .
的 力 P只要 研 究 气 体 压 力 和 机 构 运 动 质量 的惯 性
力。
根据 活 塞 的位 移规 律 , 曲轴 转 角 仅求 倒 得 到 对 活塞 的 瞬时速 度 V 随 曲轴 转 角 o 的变化 规律 : L
1 本 文 设 计 所 需 汽 油 机 性 能 参 数
42 6Q汽油 机是 四冲程 、 列式 的普 通 车用 内燃 直
机 , 活 塞行 程 为 8 rm, 缩 比为定 7 l , 均有 其 0 a 压 ~2平
IEC 62368-1玻璃部件机械强度试验分析
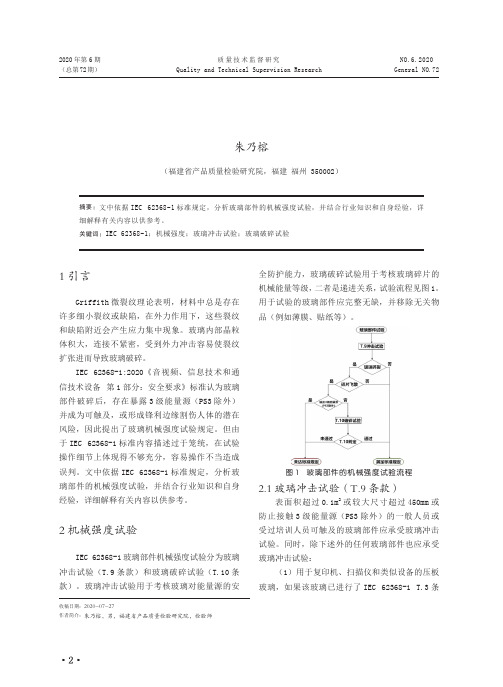
质量技术监督研究2020年第6期(总第72期)Quality and Technical Supervision ResearchNO.6.2020General NO.72IEC 62368-1玻璃部件机械强度试验分析朱乃榕(福建省产品质量检验研究院,福建 福州 350002)摘要:文中依据IEC 62368-1标准规定,分析玻璃部件的机械强度试验,并结合行业知识和自身经验,详细解释有关内容以供参考。
关键词:IEC 62368-1;机械强度;玻璃冲击试验;玻璃破碎试验收稿日期:2020-07-27作者简介:朱乃榕,男,福建省产品质量检验研究院,检验师1引言Griffith 微裂纹理论表明,材料中总是存在许多细小裂纹或缺陷,在外力作用下,这些裂纹和缺陷附近会产生应力集中现象。
玻璃内部晶粒体积大,连接不紧密,受到外力冲击容易使裂纹扩张进而导致玻璃破碎。
IEC 62368-1:2020《音视频、信息技术和通信技术设备 第1部分:安全要求》标准认为玻璃部件破碎后,存在暴露3级能量源(PS3除外)并成为可触及,或形成锋利边缘割伤人体的潜在风险,因此提出了玻璃机械强度试验规定。
但由于IEC 62368-1标准内容描述过于笼统,在试验操作细节上体现得不够充分,容易操作不当造成误判。
文中依据IEC 62368-1标准规定,分析玻璃部件的机械强度试验,并结合行业知识和自身经验,详细解释有关内容以供参考。
2机械强度试验IEC 62368-1玻璃部件机械强度试验分为玻璃冲击试验(T.9条款)和玻璃破碎试验(T.10条款)。
玻璃冲击试验用于考核玻璃对能量源的安全防护能力,玻璃破碎试验用于考核玻璃碎片的机械能量等级,二者是递进关系,试验流程见图1。
用于试验的玻璃部件应完整无缺,并移除无关物品(例如薄膜、贴纸等)。
图1 玻璃部件的机械强度试验流程2.1玻璃冲击试验(T.9条款)表面积超过0.1m 2或较大尺寸超过450mm 或防止接触3级能量源(PS3除外)的一般人员或受过培训人员可触及的玻璃部件应承受玻璃冲击试验。
机械强度分析
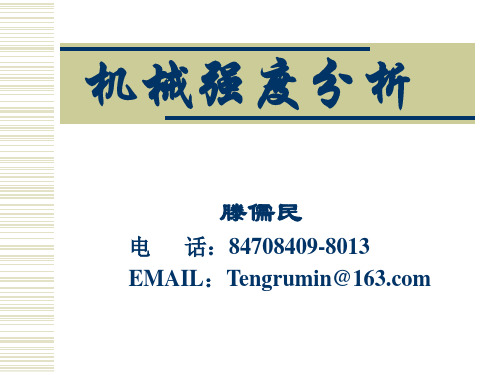
绪论
板梁结构形式
绪论
箱体结构形式
绪论
绪论
结构在一定的工作条件(静态、动态)下,实 现一定的功能(传递运动、动力、承载),要 求具有如下性能:
强度 刚度 寿命 可靠性
三类基本机械性能指标:强度、变形和能量。
绪论
所谓强度,简单说是能力的程度,表征结 构材料的承载能力。
第一章
1.2 机械结构力学模型举例
1. 搅拌釜主轴应力分析
主轴的实际工况分析,主要受力有: 1. 传递机组的功率而引起的扭转应 力; 2. 轴向拉力; 3. 主轴联接法兰的过渡区域,有一 定的局部应力集中。
第一章
1.2 机械结构力学模型举例
水坝的力学模型
第一章
1.3建立力学模型的几个原理
绪论
结构强度分析方法:
理论分析 实验分析 二者结合
在进行理论分析时,应考虑机构设备在工作条 件下的失效形成(破坏、过量变形、失稳等), 建立强度分析所需要的力学模型。应用强度理 论进行分析计算,提供常用的计算公式和数据 图表
绪论—理论分析
绪论—实验分析
绪论—实验分析
绪论—实验分析
对于工作的零部件,在承载时,即不发生任 何形式的破坏,也不超过容许限度的残余变 形,就认为该零件具有了所要求的强度。这 个要求通常是以满足一定的强度条件的方法 来加以保证的。强度要求是应保证的重要准 则。
绪论
强度条件:
所采用的强度条件有许用应力式,安全系数 式等。无论哪种方法本质都是把代表构件受 力程度的一方(载荷或应力)与代表构件对 破坏的抵抗能力的一方(构件或材料的极限 载荷或应力)加以对比来判断构件的强度。 机械结构强度是合理设计机械的一个重要方 面。要满足安全、可靠、经济耐用,都必须 进行有效的力学分析和计算。
港口船舶牵引机械强度及稳定性分析

S t a t i c Pe r f o r m an c e a nd St a bi l i t y Ana l ys i s o f Bo a t — Ha u l a g e M ac hi ne
HA N L o n g , Q I A N Y i
Ke y wor ds:f i ni t e e l e me nt a na l y s i s,s t a t i c an a l y s i s,b oa t — ha u l a g e
船舶牵 引 机械是 中大 型港 口常用 的港 口设 备 ,
定性 求 解 , 同 时参 照 相 关 起 重 机 设计 规 范 , 对 于 机 构 的初 步设计 方 案进行 合理性 评估 。
其作用 在 于拉动 货船 沿岸 边 平 行移 动 , 便 于 装 卸货
物。 由于该 机械 属 悬臂 细长 结 构 , 其强 度 、 刚度 和稳 定性决 定牵 引机 械 的T作 可 靠 性 和安 全 性 , 在 结构 设计时, 必 须 分 析满 载 时结 构 的强 度 、 刚度 和稳 定 性。 冈此 , 正 确 的设 计 过 程 是 给 出结 构 的初 步设 计 方 案 一 运用有 限元 软件 A N S Y S Wo r k b e n c h仿真 平 台建立 船舶 牵 引机械 的整体 结 构 有 限元 模 型 , 并 对
( S c h o o l o f Me c h a n i c a l E n g i n e e r i n g , J i a n g n a n U n i v e r s i t y , Wu x i 2 1 4 1 2 2 ,C h i n a )
Ab s t r a c t : A f i n i t e e l e me n t mo d e l o f t h e b o a t — h a u l a g e ma c h i n e w a s e s t a b l i s h e d b y u s i n g PRO / E a n d ANS YS W ORKBE NCH. B o u n d a r y c o n d i t i o n s a n d l o a d c o mb i n a t i o n s o f{ h e in f i t e e l e me n t mo d e l we r e d i s c u s s e d .T h e s t r e s s d i s t r i b u t i o n a n d t h e b u c k l i n g l o a d o f t h e ma c h i n e d u r i n g w o r k i n g we r e o b t a i n e d . Ac c o r d i n g t o t h e c a l c u l a t i o n r e s u l t s , t h e r a t i o n a l i t y o f t h e s t r u c t u r a l d e s i g n wa s e v a l u a t e d .
机械强度学中的疲劳失效现象分析
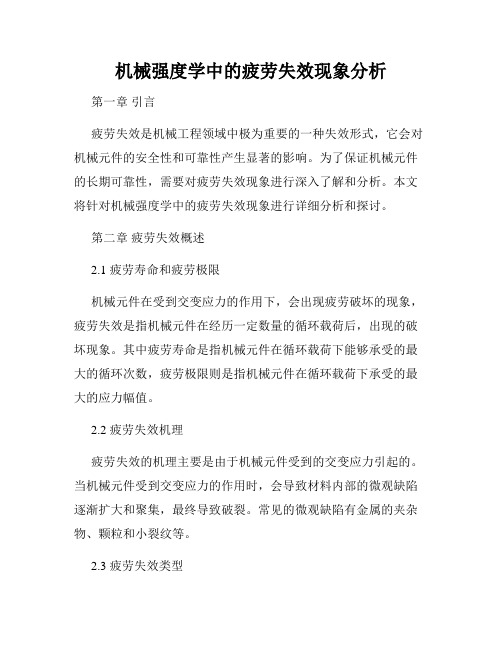
机械强度学中的疲劳失效现象分析第一章引言疲劳失效是机械工程领域中极为重要的一种失效形式,它会对机械元件的安全性和可靠性产生显著的影响。
为了保证机械元件的长期可靠性,需要对疲劳失效现象进行深入了解和分析。
本文将针对机械强度学中的疲劳失效现象进行详细分析和探讨。
第二章疲劳失效概述2.1 疲劳寿命和疲劳极限机械元件在受到交变应力的作用下,会出现疲劳破坏的现象,疲劳失效是指机械元件在经历一定数量的循环载荷后,出现的破坏现象。
其中疲劳寿命是指机械元件在循环载荷下能够承受的最大的循环次数,疲劳极限则是指机械元件在循环载荷下承受的最大的应力幅值。
2.2 疲劳失效机理疲劳失效的机理主要是由于机械元件受到的交变应力引起的。
当机械元件受到交变应力的作用时,会导致材料内部的微观缺陷逐渐扩大和聚集,最终导致破裂。
常见的微观缺陷有金属的夹杂物、颗粒和小裂纹等。
2.3 疲劳失效类型疲劳失效通常分为两种类型:表面疲劳和内部疲劳。
表面疲劳是指因机械元件表面的应力集中导致的疲劳破坏,例如滚动轴承上的点蚀和磨损。
内部疲劳则是指机械元件内部出现的疲劳破坏,例如金属疲劳裂纹和脱落等。
第三章疲劳失效分析方法3.1 应力幅值确定应力幅值是进行疲劳失效分析的基础。
应力幅值是指机械元件在循环载荷作用下的最大应力值和最小应力值之间的差值。
3.2 S-N曲线S-N曲线是衡量机械元件疲劳寿命的一种基本指标。
S-N曲线可以表示机械元件在不同循环载荷下的寿命,是疲劳试验中最常见的曲线。
3.3 应力范围法应力范围法是一种常用的疲劳分析方法,可以通过测量机械元件在疲劳试验中的最大应力幅值和最小应力幅值,来预测机械元件在不同工况下的疲劳寿命。
第四章疲劳失效控制方法4.1 材料强度提高为了提高机械元件的疲劳寿命,可以从材料的角度入手,选择强度更高的材料并保证材料的质量与可靠性。
4.2 合理的设计合理的机械结构设计可以减小应力集中,从而降低机械元件的疲劳强度,增强其耐疲劳的能力。
催化剂机械强度测定方法
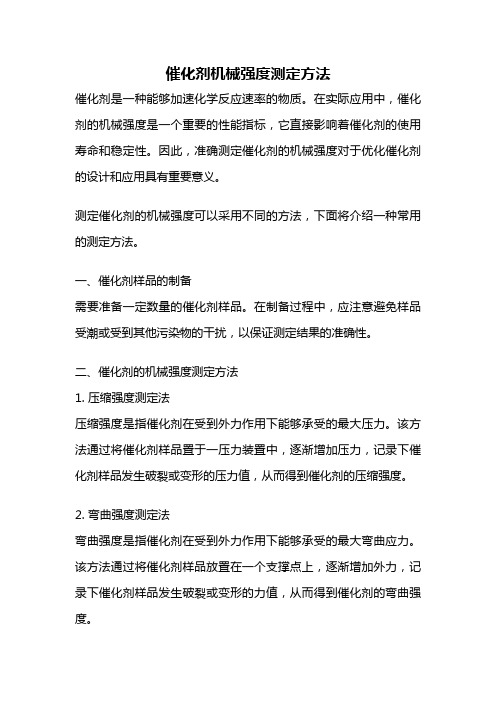
催化剂机械强度测定方法催化剂是一种能够加速化学反应速率的物质。
在实际应用中,催化剂的机械强度是一个重要的性能指标,它直接影响着催化剂的使用寿命和稳定性。
因此,准确测定催化剂的机械强度对于优化催化剂的设计和应用具有重要意义。
测定催化剂的机械强度可以采用不同的方法,下面将介绍一种常用的测定方法。
一、催化剂样品的制备需要准备一定数量的催化剂样品。
在制备过程中,应注意避免样品受潮或受到其他污染物的干扰,以保证测定结果的准确性。
二、催化剂的机械强度测定方法1. 压缩强度测定法压缩强度是指催化剂在受到外力作用下能够承受的最大压力。
该方法通过将催化剂样品置于一压力装置中,逐渐增加压力,记录下催化剂样品发生破裂或变形的压力值,从而得到催化剂的压缩强度。
2. 弯曲强度测定法弯曲强度是指催化剂在受到外力作用下能够承受的最大弯曲应力。
该方法通过将催化剂样品放置在一个支撑点上,逐渐增加外力,记录下催化剂样品发生破裂或变形的力值,从而得到催化剂的弯曲强度。
3. 抗压强度测定法抗压强度是指催化剂在受到外力作用下能够承受的最大抗压应力。
该方法通过将催化剂样品置于一压力装置中,逐渐增加压力,记录下催化剂样品发生破裂或变形的压力值,从而得到催化剂的抗压强度。
以上三种方法中,压缩强度测定法、弯曲强度测定法和抗压强度测定法是比较常用的,可以根据具体需求选择适合的方法进行测定。
三、测定结果分析与应用通过上述测定方法得到的机械强度数据可以用于评估催化剂的稳定性和使用寿命。
机械强度越高,催化剂在使用过程中抗压、抗弯曲能力越强,使用寿命也相对较长。
因此,在实际应用中,催化剂的机械强度是选择合适催化剂的重要指标之一。
测定催化剂的机械强度还有助于催化剂设计和制备过程的优化。
通过了解催化剂的机械强度,可以根据具体的应用需求选择合适的催化剂载体和制备工艺,以提高催化剂的稳定性和使用寿命。
催化剂的机械强度测定方法对于优化催化剂的设计和应用具有重要意义。
机械设计中的机械强度与刚度分析

机械设计中的机械强度与刚度分析在机械设计中,机械强度与刚度是两个重要的概念。
机械强度指的是机械结构在受到外界力的作用下能够保持稳定的能力,而机械刚度则指的是机械结构在受到外力作用时不发生过大变形的能力。
本文将对机械强度与刚度的分析方法以及影响因素进行讨论。
第一部分:机械强度分析机械强度的分析是为了确保机械结构在工作过程中不会出现破坏的情况。
在机械设计中,我们通常使用强度分析来评估机械结构的强度。
强度分析可以分为静态强度分析和动态强度分析两种情况。
静态强度分析主要是通过分析机械结构在静态载荷作用下的受力情况来评估其强度。
常见的静态强度分析方法包括弹性力学分析、有限元分析等。
这些方法可以帮助工程师计算和评估机械结构在静态载荷下的应力、变形等参数,从而确定结构的破坏强度,为设计提供依据。
动态强度分析是指机械结构在动态载荷作用下的强度分析。
动态载荷包括冲击载荷、振动载荷等。
在进行动态强度分析时,需要考虑到载荷的频率、幅值等因素,以及材料的动态性能。
常见的动态强度分析方法包括动力学分析、模态分析等。
第二部分:机械刚度分析机械刚度的分析是为了保证机械结构在工作时不会发生过大的变形,从而满足设计要求。
机械刚度的分析方法包括静态刚度分析和动态刚度分析两种情况。
静态刚度分析通过计算机械结构受到外力作用时的变形情况来评估其刚度。
常见的静态刚度分析方法包括刚度矩阵分析、有限元分析等。
这些方法可以帮助工程师计算和评估机械结构在静态载荷下的变形和刚度参数,从而确定结构的刚度,为设计提供依据。
动态刚度分析是指机械结构在动态载荷作用下的刚度分析。
动态刚度的计算需要考虑载荷的频率、幅值等因素,以及材料的动态性能。
常见的动态刚度分析方法包括模态分析、振动分析等。
第三部分:影响机械强度与刚度的因素机械强度和刚度受多种因素的影响,包括结构形状、材料性能、载荷情况等。
结构形状是影响机械强度和刚度的重要因素之一。
不同的结构形状将导致不同的应力分布和变形情况。
- 1、下载文档前请自行甄别文档内容的完整性,平台不提供额外的编辑、内容补充、找答案等附加服务。
- 2、"仅部分预览"的文档,不可在线预览部分如存在完整性等问题,可反馈申请退款(可完整预览的文档不适用该条件!)。
- 3、如文档侵犯您的权益,请联系客服反馈,我们会尽快为您处理(人工客服工作时间:9:00-18:30)。
常见的工程断裂问题
据美国和欧共体的权威专业机构统计:世界上 由于机件、构件及电子元件的断裂、疲劳、腐蚀、 磨损破坏造成的经济损失高达各国国民生产总值 的6~8%。
据我国劳动部统计,我国在20世纪80年代发 生的锅炉和压力容器的爆炸事故约五千起,人员 累计伤亡近万人,居国内劳动安全事故的第二位。
断裂力学的研究意义在于防范上述的破坏行为, 降低由断裂和破坏造成的经济损失,减少事故的 发生。
机械强度分析
2020/11/18
机械强度分析
机械强度分析
课程内容
断裂强度分析(24)
材料断裂、裂纹
接触强度分析(2)
接触静强度、接触疲劳
联接强度分析(4)
金属结构联接方法、螺 栓联接强度、焊接联接、 焊缝强度
压力容器强度分析(2)
薄壁容器强度分析方法
机械强度分析
断裂强度分析
➢ 绪论
断裂力学的发展史,断裂的跨尺度特性
实验表明:对塑性材料,此理论比第三强度理 论更符合试验结果,在工程中得到了广泛应用。
机械强度分析
四种常用的强度理论 强度理论的统一表达式:
相当应力
机械强度分析
传统强度理论的弊端
➢ 从物理学角度上,它不能识别固体材料的典型特征破坏过程;
(1)微裂纹汇合成宏观裂纹,进而发展成脆性断裂;(2)孔洞形成、 长大、片状汇合到持续撕裂的韧性断裂;(3)驻留滑移带处累积塑 性变形导致疲劳裂纹形成,继而呈花纹状碾压扩展的疲劳断裂。
Welding J., 1963, 10: 563-570.
机械强度分析
宏观断裂力学发展史
➢ 20世纪60年代,Rice的J积分和Hutchinson等的HRR场理论使得 弹塑性断裂力学趋于成熟;
• Rice J R. A path independent integral and the approximate analysis of strain concentration by notches and cracks. J. Appl. Mech., 1968, 35: 379-386. • Hutchinson J W. Singular behavior at the end of a tensile crack tip in a hardening material. J. Mech. Phys.Solids, 1968, 16:13-31. • Rice J R, Rosengren G F. Plane strain deformation near a crack tip in power-law hardening material. J. Mech. Phys.Solids, 1968, 16:1-12.
机械强度分析
四种常用的强度理论
形状改变比能理论(第四强度理论) 无论材料处于什么应力状态,只要发生屈服,都是 由于微元的最大形状改变比能达到一个极限值。 -构件危险点的形状改变比能
-形状改变比能的极限值,由单拉实验测得
机械强度分析
四种常用的强度理论
形状改变比能理论(第四强度理论) 屈服条件 强度条件
机械强度分析
破坏力学的三个发展阶段
➢ 第一阶段(16世纪末---第二次世界大战前)
以强度理论为中心的破坏准则体系; 不引入任何缺陷尺度; 材料本构行为的连续介质描述;
推动了变形体力学的发展
无缺陷经验理论
➢ 第二阶段(第二次世界大战结束---20世纪末)
以断裂韧性理论为中心的破坏准则体系;
引入宏观缺陷,但不考虑细-微观缺陷;
➢ 20世纪50年代,G.Irwin完成了应力强度因子理论的基本框架;
• Irwin G R. Analysis of stresses and strains near the end of a crack transversing a plate. J.Appl.Mech., 1957, 24:361-364.
为了建立复杂应力状态下的强度条件,而提出 的关于材料破坏原因的假设及计算方法。
机械强度分析
传统材料力学的强度问题
两大假设:均匀、连续机械强来自分析四种常用的强度理论
最大拉应力理论(第一强度理论) 材料发生断裂的主要因素是最大拉应力达到极限值
-构件危险点的最大拉应力 -极限拉应力,由单拉实验测得
断裂条件 强度条件
杨氏模量
表面能密度
English engineer
13 June 1893 – 13 Oct 1963 材料的理论强度
晶格间距
Theory
A flaw would propagate in a stressed material only when, by doing so, it
brought about a reduction in elastically stored energy W more than sufficient
机械强度分析
Griffith 脆断理论
Motivation
Griffith's work was motivated by two contradictory facts:
The stress needed to fracture bulk glass is around 100 MPa (15,000 psi). The theoretical stress needed for breaking atomic bonds is approximately 10,000 MPa (1,500,000 psi).
机械强度分析
四种常用的强度理论
最大切应力理论(第三强度理论) 屈服条件 强度条件
低碳钢拉伸
低碳钢扭转
机械强度分析
四种常用的强度理论
最大切应力理论(第三强度理论) 实验表明:此理论对于塑性材料的屈服破坏能够得到 较为满意的解释。并能解释材料在三向均压下不发生 塑性变形或断裂的事实。
局限性: 1、未考虑 的影响,试验证实最大影响达15%。 2、不能解释三向均拉下可能发生断裂的现象,
to meet the free energy requirements of newly formed frac机t械ur强e度s分u析rfaces.
Griffith 脆断理论
Griffith裂纹
1913年,Inglis给出了关于含椭圆孔的无 限大平面介质的数学解
Griffith认为宏观材料强度的剧烈下降, 主要原因在于材料中存在大量缺陷
带裂纹标准试件的断裂指标;
宏观缺陷
破坏力学上升为独立学科
宏观断裂力学
➢ 第三阶段(20世纪末---至今)
追溯从变形、损伤至断裂的全过程;
引入多层次的缺陷几何结构;
微观缺陷
宏微观理论
本构行为的宏—细—微观相结合的描述-----材料的微结构; 机械强度分析
传统强度理论
强度理论:人们根据大量的破坏现象,通过判断推 理、概括,提出了种种关于破坏原因的假说,找出 引起破坏的主要因素,经过实践检验,不断完善, 在一定范围与实际相符合,上升为理论。
• Barenblatt G I. The mathematical theory of equillibrium cracks in brittle fracture.
Adv. Appl. Mech. V.7. New York: Academic Press, 1962. 55-129.
• Wells A A. Application of fracture mechanics a and beyond general yielding. British
➢ 从力学角度上,它不能描述由于裂纹状缺陷存在而于裂纹尖 端产生的严重应力集中;
无法表征裂纹尖端的奇异场
➢ 从材料学角度上,它不能解释理论强度远高于实际强度的原
因;
无法考虑宏观、微观的缺陷
➢ 从工程应用角度上,它不足以防止工程结构的破坏。
如低应力脆断事故
机械强度分析
断裂力学
均匀性假设仍成立,但且仅在缺陷处不连续
机械强度分析
常见的工程断裂问题
压力容器发生破裂
天然气和其他压力管道的裂纹扩展
机械强度分析
常见的工程断裂问题
飞机机身和船体开裂
铁轨与车轴等构件的疲劳断裂
机械强度分析
常见的工程断裂问题
断裂问题的分类: 线弹性断裂力学——脆性断裂 弹塑性断裂力学——延性断裂(韧性断裂)
脆性断裂
延性断裂
机械强度分析
机械强度分析
宏观断裂力学发展史
➢ 20世纪初,英国科学家A.A.Griffith建立了脆断理论的基本框架;
• Griffith A A. The phenomena of rupture and flow in solids. Phil.Trans., Ser.A. 1920, 221:163-198. • Griffith A A. The theory of rupture. Proc.of the First Int. Congr. For Appl. Mech. Delft, 1924, 55-63. • Inglis C E. Stresses in a plate due to the presence of cracks and sharp corners. Trans. Naval Arch., 1913, 55:219-241.
Griffith将Inglis的数学解中椭圆的一个
轴趋近于零,得到Griffith裂纹
Inglis, Sir Charles Edward (1875–1952), civil engineer
In 1913 he published a paper on the stresses in a plate due to the presence of cracks and sharp corners. This may well be his most far-reaching contribution, since A. A. Griffith's classic explanation of the discrepancy between observed and calculated strengths of amorphous substances, such as glass and silica fibres, was based on it.