水泥熟料形成过程.
水泥熟料生产工艺流程(一)

水泥熟料生产工艺流程(一)水泥熟料生产工艺1. 概述水泥熟料是生产水泥的主要原料,其生产工艺包括多个流程,涉及到破碎、混合、配料、烧结、冷却等多个环节。
2. 破碎破碎是将原料破碎成小颗粒,以便于后续的工艺处理。
这个环节主要包括以下步骤:•原石进厂•破碎机破碎•破碎后再过筛3. 混合不同种类的原料需要混合在一起,生成符合要求的熟料配料。
混合的步骤包括:•须按一定比例配料•混合机搅拌,使混合均匀•将混合完的配料送至烧结炉4. 配料配料是指按照熟料成分要求将各种配料分别称量并混合在一起,常用的配料有石灰石、黏土、铁矿石等,其步骤包括:•确定熟料成分要求•仓库里先把需要的原料装进坡底下的斗•电子秤称重•直接美穗机料仓添加各组分原料•变频机调节5. 烧结烧结是指将配合均匀的生料进入烧结炉,按一定的烧成温度和时间进行物理变化,使其变为操作性能稳定、化学成份和物理性能达到工艺要求的熟料。
烧结步骤主要包括以下几个过程:1.送进烧结炉2.炉内高温烧结3.熟料的成型4.把烧后的熟料送到冷却系统6. 冷却烧结完的熟料需要进行冷却,以保证熟料质量。
熟料冷却步骤主要包括以下几个过程:•熟料经回转窑进入烟气冷却器冷却•熟料在冷却器中加水淬火•熟料冷却后送入仓库存放针对水泥熟料生产工艺,以上就是主要的流程。
随着技术的不断发展,可能会有所变化,但总体上仍然会遵循这些步骤进行生产。
7. 最终品质检验水泥熟料生产完毕后,需要进行最终品质检验,以确保其符合工业标准和客户需求。
最终品质检验主要包括以下几个方面:•成分分析:检测熟料的主要成分,如CaO、SiO2、Al2O3、Fe2O3、SO3、MgO等;•物理性能测试:对熟料的物理性能进行测试,如熟料比表面积、压缩强度、细度等;•着色指标检测:检测熟料着色指标,确保其颜色符合要求;•水泥标号检测:检测熟料中的硅酸盐含量,以确定其水泥标号。
8. 结束语水泥熟料生产工艺是一个复杂而重要的过程。
水泥熟料的形成过程
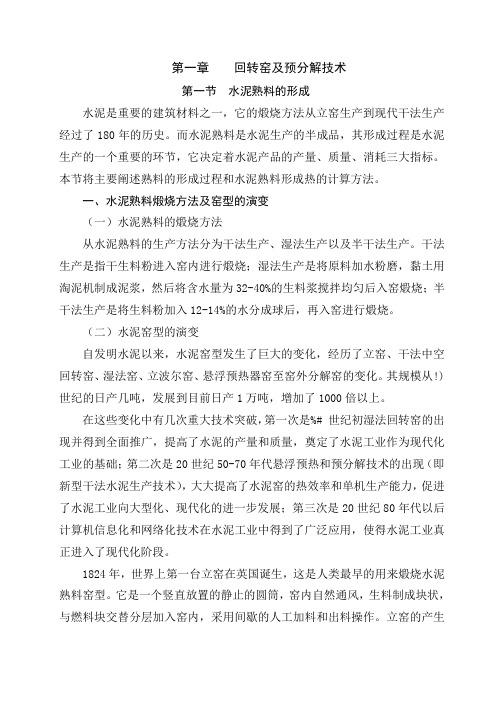
第一章回转窑及预分解技术第一节水泥熟料的形成水泥是重要的建筑材料之一,它的煅烧方法从立窑生产到现代干法生产经过了180年的历史。
而水泥熟料是水泥生产的半成品,其形成过程是水泥生产的一个重要的环节,它决定着水泥产品的产量、质量、消耗三大指标。
本节将主要阐述熟料的形成过程和水泥熟料形成热的计算方法。
一、水泥熟料煅烧方法及窑型的演变(一)水泥熟料的煅烧方法从水泥熟料的生产方法分为干法生产、湿法生产以及半干法生产。
干法生产是指干生料粉进入窑内进行煅烧;湿法生产是将原料加水粉磨,黏土用淘泥机制成泥浆,然后将含水量为32-40%的生料浆搅拌均匀后入窑煅烧;半干法生产是将生料粉加入12-14%的水分成球后,再入窑进行煅烧。
(二)水泥窑型的演变自发明水泥以来,水泥窑型发生了巨大的变化,经历了立窑、干法中空回转窑、湿法窑、立波尔窑、悬浮预热器窑至窑外分解窑的变化。
其规模从!) 世纪的日产几吨,发展到目前日产1万吨,增加了1000倍以上。
在这些变化中有几次重大技术突破,第一次是%# 世纪初湿法回转窑的出现并得到全面推广,提高了水泥的产量和质量,奠定了水泥工业作为现代化工业的基础;第二次是20世纪50-70年代悬浮预热和预分解技术的出现(即新型干法水泥生产技术),大大提高了水泥窑的热效率和单机生产能力,促进了水泥工业向大型化、现代化的进一步发展;第三次是20世纪80年代以后计算机信息化和网络化技术在水泥工业中得到了广泛应用,使得水泥工业真正进入了现代化阶段。
1824年,世界上第一台立窑在英国诞生,这是人类最早的用来煅烧水泥熟料窑型。
它是一个竖直放置的静止的圆筒,窑内自然通风,生料制成块状,与燃料块交替分层加入窑内,采用间歇的人工加料和出料操作。
立窑的产生揭开了水泥工业窑的历史。
1877年出现了回转窑,它是一个倾斜卧着的回转圆筒,生料粉由高端加入,低端有燃料燃烧,物料一方面运动一方面被煅烧。
这便是最早的干法回转窑生产(见图1-1)图1-1 回转窑的最初形式在干法回转窑的生产中,由于初期的回转窑窑体较短,出窑废气的温度较高,热耗较高,随后出现了干法长窑,即干法中空窑,以及带预热锅炉的回转窑。
1-1 水泥熟料的形成
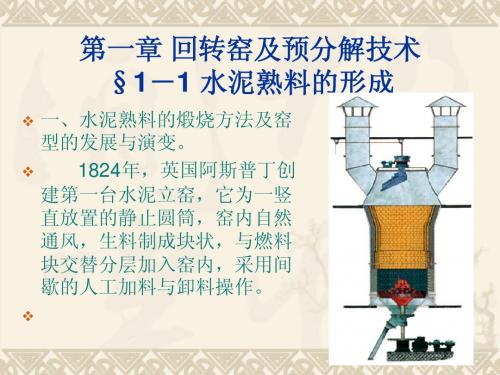
5、硅酸三钙(C3S)的形成和烧成反应: 硅酸三钙要在液相中才能大量形成。当温度升高到近 1300℃时,C3A、C4AF、R2O等熔剂矿物变成液相,C2S与 CaO溶解在高温液相中,互相反应生成C3S;C3S的生成速 度与烧成温度和反应时间有关。其生成温度范围一般为 1300~1450~1300℃。 熟料烧成后,温度开始下降,C3S形成速度减慢直至液 相凝固。 6、熟料的冷却过程: 在冷却过程中,将有部分熔剂矿物形成晶体析出,另一 部分来不及析晶而呈玻璃态存在。 C3S在1250℃时容易分解,所以要求在1300℃以下熟料 要快冷,使C3S来不及分解,越过1250℃以后,C3S就比较 稳定了。 C2S在<500℃时,由β-C2S转变为γ-C2S,密度减少 而使体积增大10%左右,从而使熟料块变成粉末状。粉化后 的γ-C2S与水反应时,几乎没有水硬性,因此在<500℃温 度段时应急冷,使其来不及转化。
三、水泥熟料的形成热: 熟料形成热(理论热耗)是指在一定生产 条件下,用某一基温度(0℃或20℃ )的干燥 物料,在没有物料损失和热量损失的条件下, 制成1kg同温度的熟料所需要的热量。 生产1kg熟料所需理论热耗,可根据热平 衡计算求得,熟料形过程中的各种热反应及其 效应见表1-1所示。 熟料形成热也可由下列经验公式计算: Qsh=G干(4.5Al2O3+29.6CaO+17MgO)-284
1928年,德国立列波博士与波列休斯公司 创造了带回转炉篦子的回转窑,即立波尔窑。 1934年,丹麦的约根生工程师研究成功悬 浮预热技术; 1951年德国的缪勒与洪堡公司生产了第一 台带悬浮预热器的回转窑。 1971年日本石川岛公司在悬浮预热窑基础 上,发明了预分解窑,即在悬浮预热器后增 加了分解炉,使物料的预热、分解都在回转 窑外完成后,再入窑进行煅烧。
水泥熟料生产工艺流程解析

水泥熟料生产工艺流程解析水泥熟料生产工艺流程解析1. 引言水泥是建筑工程中不可或缺的材料,而水泥熟料是水泥的主要原料。
水泥熟料生产工艺流程是指将原料经过一系列反应和处理,最终得到水泥熟料的过程。
本文将深入探讨水泥熟料生产工艺的各个环节,从而更好地理解水泥熟料的生产过程。
2. 原料的选取与预处理2.1 原料的选取水泥熟料的主要原料通常包括石灰石、粘土、铁矿石等。
这些原料需要具备一定的化学成分和物理性质,以确保最终生产出的水泥熟料具有良好的性能。
2.2 原料的预处理在进入生产线之前,原料需要经过一系列的预处理步骤。
如石灰石需要进行破碎、磨矿、筛分等处理,以获得合适的粒度,方便后续的反应和处理。
3. 原料的烧成原料的烧成是整个水泥熟料生产过程中最关键的步骤之一。
该步骤主要包括干法烧成和湿法烧成两种方法。
3.1 干法烧成干法烧成是指将原料直接送入旋转窑进行烧成的方法。
在旋转窑中,原料与高温燃烧气体进行交互作用,发生一系列的物理和化学反应,最终形成水泥熟料。
这种方法具有工艺简单、设备投资少的特点,但能耗较高。
3.2 湿法烧成湿法烧成是指将原料中的水分先进行脱除,然后再进行烧成的方法。
该方法能耗低,但工艺复杂、设备投资较大。
湿法烧成通常采用沟窑或滚筒窑进行。
4. 熟料的磨矿熟料的磨矿是将熟料进行细磨,以提高其活性和适应性的过程。
该步骤主要通过水泥磨来实现。
4.1 磨矿工艺磨矿工艺是指将熟料放入水泥磨中进行细磨的过程。
水泥磨通常采用滚筒式或滚压式磨机,通过磨碎和混合的作用,使熟料达到所需的细度要求。
4.2 磨矿过程中的辅助材料为了调整熟料的性能,磨矿过程中还可添加适量的矿渣、石膏等辅助材料,以改善水泥的性能和品质。
5. 总结与回顾通过对水泥熟料生产工艺流程的解析,我们可以看出,水泥熟料的生产过程经过了多个环节的处理和反应。
从原料的选取与预处理,到熟料的烧成和磨矿,每个环节都起到了关键的作用。
水泥熟料生产工艺流程的复杂性和多样性使得水泥的生产成为一门综合性较强的科学。
水泥的制作过程

水泥的制作过程
水泥是建筑工程中常用的建筑材料,它主要由石灰石、粘土等材料经过研磨、混合、煅烧等一系列工艺制成。
在生产过程中,水泥需要经历多个步骤才能最终成品,下面将详细介绍水泥的制作过程。
1. 原材料的选取
水泥的主要原料包括石灰石、粘土、煤矸石等。
这些原料需要经过严格挑选,确保质量符合生产要求。
其中石灰石和粘土是水泥的主要成分,而煤矸石则是用作燃料的辅助原料。
2. 研磨混合
原料经过挑选后,需要进行研磨和混合的工序。
石灰石和粘土等原料先是经过破碎机破碎,然后通过研磨机进行细磨,最后将各种原料按一定比例混合均匀。
3. 煅烧
混合好的原料进入回转窑内进行煅烧。
回转窑是水泥生产的关键设备,原料在高温下经过煅烧,逐渐变成熟料。
煅烧过程中,原料在回转窑内不断旋转,使得石灰石和粘土等原料充分反应,形成水泥熟料。
4. 磨矿
煅烧后的熟料需要进一步磨矿成水泥粉。
熟料经过水泥磨矿机进行磨矿,将其研磨成细度适中的水泥粉,以便后续的使用。
5. 包装
磨矿好的水泥粉需要进行包装,以便运输和销售。
水泥通常被装在纸袋或编织袋中,然后进行包装封口,标注生产日期、规格等信息。
通过以上几个步骤,水泥的制作过程就完成了。
水泥作为建筑材料,在建筑工程中有着重要的作用,它可以用于混凝土、砂浆等建筑材料的制作,广泛应用于房屋建设、道路修建等领域。
水泥的制作过程虽然复杂,但是通过科学的工艺和技术手段,可以高效地生产出优质的水泥产品,为建筑工程提供坚实的保障。
水泥生产工艺及水泥熟料的形成
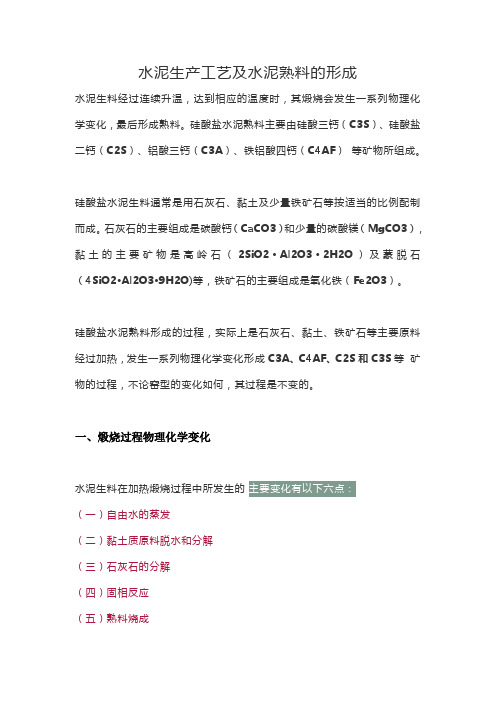
水泥生产工艺及水泥熟料的形成水泥生料经过连续升温,达到相应的温度时,其煅烧会发生一系列物理化学变化,最后形成熟料。
硅酸盐水泥熟料主要由硅酸三钙(C3S)、硅酸盐二钙(C2S)、铝酸三钙(C3A)、铁铝酸四钙(C4AF)等矿物所组成。
硅酸盐水泥生料通常是用石灰石、黏土及少量铁矿石等按适当的比例配制而成。
石灰石的主要组成是碳酸钙(CaCO3)和少量的碳酸镁(MgCO3),黏土的主要矿物是高岭石(2SiO2·Al2O3·2H2O)及蒙脱石(4SiO2·Al2O3·9H2O)等,铁矿石的主要组成是氧化铁(Fe2O3)。
硅酸盐水泥熟料形成的过程,实际上是石灰石、黏土、铁矿石等主要原料经过加热,发生一系列物理化学变化形成C3A、C4AF、C2S和C3S等矿物的过程,不论窑型的变化如何,其过程是不变的。
一、煅烧过程物理化学变化水泥生料在加热煅烧过程中所发生的(一)自由水的蒸发(二)黏土质原料脱水和分解(三)石灰石的分解(四)固相反应(五)熟料烧成(六)熟料的冷却(一)自由水的蒸发无论是干法生产还是湿法生产,入窑生料都带有一定量的自由水分,由于加热,物料温度逐渐升高,物料中的水分首先蒸发,物料逐渐被烘干,其温度逐渐上升,温度升到100~150℃时,生料自由水分全部被排除,这一过程也称为干燥过程。
(二)黏土质原料脱水和分解黏土主要由含水硅酸铝所组成,其中二氧化硅和氧化铝的比例波动于2:1~4:1之间。
当生料烘干后,被继续加热,温度上升较快,当温度升到450℃时,黏土中的主要组成高岭土(Al2O3·2SiO2·2H2O)失去结构水,变为偏高岭石(2SiO2·Al2O3)。
高岭土进行脱水分解反应时,在失去化学结合水的同时,本身结构也受到破坏,变成游离的无定形的三氧化二铝和二氧化硅,其具有较高的化学活性,为下一步与氧化钙反应创造了有利条件。
在900-950℃,由无定形物质转变为晶体,同时放出热量。
硅酸盐水泥熟料的形成过程
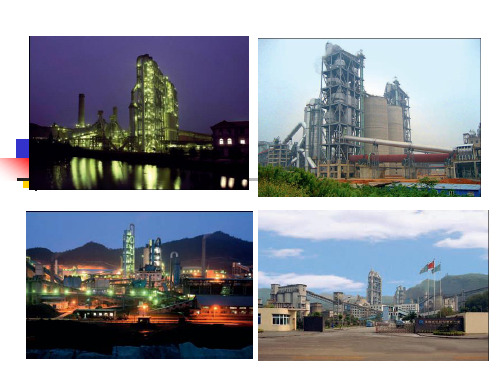
影响CaCO3分解速度的因素
分解由5个过程中最慢的一个过程决定,所 有影响传热和化学反应的因素均会影CaCO3的 分解速度。 ——温度 ——CO2分压 ——生料粒度 ——生料悬浮分散程度 ——原材料自身特性
固相反应
特点:发生在固相之间的反应 首先在界面上反应,然后扩散到内部 条件:合适的温度压力、反应物间均匀混合、 颗粒紧密接触 在水泥熟料矿物形成过程中,在CaO和SiO2、 Al2O3、Fe2O3之间发生的反应,主要生成C2S、 C3A、C4AF
影响C3S形成的因素
2.液相量 与生料组成(SM、IM)和煅烧温度有关, 温度升高,液相量增加;生料(或熟料)组 成中Fe2O3+Al2O3含量增加,液相量增多;同 时还与Al2O3 、Fe2O3比值有关。
熟料中液相量与铝氧率关系
温度 2.0 1338℃ C3S—C2S—C3A— C4AF界面处 1400℃ 1500℃ 18.3 23.5(1365℃) 24.3 24.8 IM 1.25 21.1 22.2(1339℃) 23.6 24.0 0.64 0 20.2(1348℃) 22.4 22.9
3.2 硅酸盐水泥熟料的形成过程
水泥制备过程
水泥——水泥熟料——水泥生料——水泥原料
高 温 煅 烧
+适量石膏 +混合材 粉磨
原料预均化 生料配料及粉磨 生料均化
两磨一烧
熟料形成过程中的物理化学变化
干燥与脱水(预热) 碳酸盐分解 固相反应 液相烧结 熟料冷却
湿法回转窑内水泥熟料形成过程
影响C3S形成的因素:液相黏度
3.液相黏度—影响C2S和CaO分子的扩散速度,从而影响C3S的 形成。 与组成和温度有关(见图)
水泥熟料形成过程
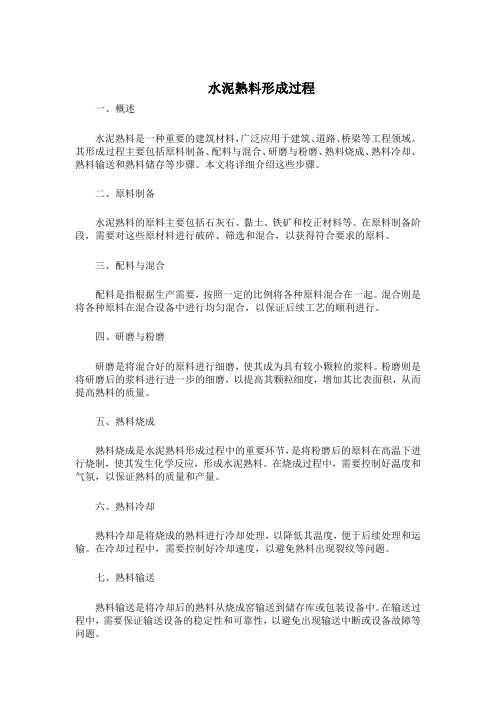
水泥熟料形成过程一、概述水泥熟料是一种重要的建筑材料,广泛应用于建筑、道路、桥梁等工程领域。
其形成过程主要包括原料制备、配料与混合、研磨与粉磨、熟料烧成、熟料冷却、熟料输送和熟料储存等步骤。
本文将详细介绍这些步骤。
二、原料制备水泥熟料的原料主要包括石灰石、黏土、铁矿和校正材料等。
在原料制备阶段,需要对这些原材料进行破碎、筛选和混合,以获得符合要求的原料。
三、配料与混合配料是指根据生产需要,按照一定的比例将各种原料混合在一起。
混合则是将各种原料在混合设备中进行均匀混合,以保证后续工艺的顺利进行。
四、研磨与粉磨研磨是将混合好的原料进行细磨,使其成为具有较小颗粒的浆料。
粉磨则是将研磨后的浆料进行进一步的细磨,以提高其颗粒细度,增加其比表面积,从而提高熟料的质量。
五、熟料烧成熟料烧成是水泥熟料形成过程中的重要环节,是将粉磨后的原料在高温下进行烧制,使其发生化学反应,形成水泥熟料。
在烧成过程中,需要控制好温度和气氛,以保证熟料的质量和产量。
六、熟料冷却熟料冷却是将烧成的熟料进行冷却处理,以降低其温度,便于后续处理和运输。
在冷却过程中,需要控制好冷却速度,以避免熟料出现裂纹等问题。
七、熟料输送熟料输送是将冷却后的熟料从烧成窑输送到储存库或包装设备中。
在输送过程中,需要保证输送设备的稳定性和可靠性,以避免出现输送中断或设备故障等问题。
八、熟料储存熟料储存是将输送至储存库中的熟料进行储存和管理。
在储存过程中,需要保持储存库的干燥和通风,以防熟料受潮或变质。
同时,还需要定期对储存库进行检查和维护,以确保其安全和正常使用。
总结:水泥熟料形成过程是一个复杂的过程,需要经过多个步骤才能得到高质量的熟料产品。
在实际生产中,需要严格控制每个环节的工艺参数和质量标准,以确保熟料的质量和产量。
同时,还需要加强设备的维护和管理,以保证生产的稳定性和可靠性。
水泥熟料形成过程

第四章
水泥熟料煅烧过程和设备
水泥熟料煅烧是个复杂的气-固、液-固和固-固相之间 的高温反应过程。既有某些天然矿物的分解,又有众多氧化物 之间的合成。 最终所形成的矿物,即熟料,其品种、数量和特征都要 合乎规范的要求,才能保证成品达到既定的性能指标。 虽然煅烧过程总的理论耗热量不是很多,但因所要求的反 应温度很高,因此单位产品实际燃料消耗量却比较多。 自从水泥生产工业化以来,煅烧熟料的主要设备是立窑和 回转窑。但本世纪下半叶以来,回转窑上预热和预分解技术的 开发应用,无论是在生产规模、生产指标和产品质量以及相应 科学技术水平方面,都有重大进展与突破。
影响碳酸盐分解速率的因素 温度 随温度升高,分解速率常数和压力倒数差相 应增大,分解速率和时间缩短;
t d 1 1 K( — ) p P0 (1— 3 1—ε )
式中:
t—分解时间;K—分解常数;
P—CO2的分压;ε—分解率 d—生料等效粒径; (单个颗粒碳酸盐分解动力学方程)
窑系统的CO2分压 通风良好, CO2分压较 低,有利于碳酸盐分解; 生料细度和颗粒级配 生料细度细,颗粒均 匀,粗粒少,分解速率快; 生料悬浮程度 生料悬浮分散良好,相对减 小颗粒尺寸,增大了传热面积,提高了碳酸盐分解速率; 石灰石的种类和物理性质 结构致密,结晶 粗大的石灰石,分解速率慢; 生料中粘土质组分和性质 粘土质中的矿 物组分的活性依次按高岭土、蒙脱石、伊利石、石英 降低.粘土质原料活性越大,可加速碳酸盐的分解过程.
不同温度下,液相的计算公式: 1400℃ L=2.95Al2O3+2.20Fe2O3 +R 1450℃ L=3.00Al2O3+2.25Fe2O3 +R 1500℃ L=3.30Al2O3+2.60Fe2O3 +R
水泥熟料生产工艺流程

水泥熟料生产工艺流程一、水泥熟料生产工艺概述水泥熟料是水泥生产的重要原料,其生产工艺流程主要包括原材料的采集、研磨、混合和烧成等过程。
这些过程需要通过先进的设备和技术来实现,以保证产品质量和生产效率。
二、原材料采集1. 矿山开采:水泥熟料的主要原材料包括石灰岩、粘土、铁矿石等,这些物质通常需要从地下或表层进行开采。
2. 原材料运输:将采集到的原材料通过运输设备如卡车、铁路或船舶等运输到生产厂区。
三、原材料预处理1. 破碎:将大块的原材料通过颚式破碎机或圆锥式破碎机等设备进行粉碎。
2. 磨细:将粉碎后的原材料通过球磨机或辊压机等设备进行细化处理,以便于后续混合使用。
四、混合制备1. 原材料称量:将不同种类的原材料按比例称量,并送入混合机中进行混合。
2. 水泥熟料制备:将混合好的原材料送入旋转窑中进行烧结,烧结后产生的水泥熟料通过冷却机进行冷却处理。
五、旋转窑烧成1. 窑头预热:将原材料送入旋转窑头部分,利用高温气体对原材料进行预热处理。
2. 窑体烧成:将预热后的原材料沿着旋转窑逐渐下降,经过高温气体的作用逐步变成水泥熟料。
3. 窑尾冷却:将生产出来的水泥熟料通过冷却机进行冷却处理,并通过输送设备运输到储存区域。
六、水泥生产1. 水泥制备:将水泥熟料与适量的石膏等辅助材料混合后,在球磨机等设备中进行细化处理,制成水泥。
2. 包装和储存:将制成的水泥通过包装设备包装,并存放在仓库中等待出售或使用。
七、环保措施1. 除尘设备:在生产过程中,通过安装除尘设备如电除尘器、袋式除尘器等,减少粉尘排放对环境的污染。
2. 废气处理:通过烟气脱硝、烟气脱硫等技术,降低烟气中的有害物质浓度,保护环境。
3. 节能减排:采用节能技术如余热回收、高效节能设备等,降低生产过程中的能耗和废气排放量。
八、总结水泥熟料生产工艺流程是一个复杂而又关键的过程,需要通过科学的管理和先进的技术设备来实现。
同时,在生产过程中应该注重环保和节能减排措施的实施,以保护环境和可持续发展。
水泥回转窑工作原理

水泥回转窑工作原理
水泥回转窑是一种常用的水泥生产设备,它通过回转运动来完成水泥熟料的烧成过程。
其工作原理主要包括以下几个步骤:
1.给料:原料(水泥熟料、燃料和辅助材料)从回转窑的进料
口进入回转窑内,形成料层。
2.回转运动:回转窑开始回转,物料在重力和离心力的作用下
逐渐下滑并向前推进。
3.干燥带:物料在窑筒的上部由于高温气流的流动和强烈的辐
射热作用下逐渐干燥,失去部分水分。
4.预热带:物料进入窑筒的中部后,与窑内旋转的燃料混合燃烧,产生大量的热量。
燃料的燃烧使物料逐渐升温,进行预热。
5.煅烧带:物料进一步下滑进入窑筒的下部,此处温度最高,
达到水泥熟料的煅烧温度。
在高温作用下,水泥熟料发生化学反应,产生熟料矿物。
6.冷却带:熟料通过窑筒下部的冷却带,利用逆向流动的冷却
气体(常为热风或冷风)对熟料进行冷却。
这一过程对于保证熟料质量和降低生产成本非常重要。
7.排料:冷却后的熟料从回转窑的排料口排出,送入到熟料仓
进行储存。
以上即为水泥回转窑的工作原理,通过回转窑的连续运转,将原材料转化为熟料,完成水泥生产的过程。
生料在煅烧过程中的物理化学变化
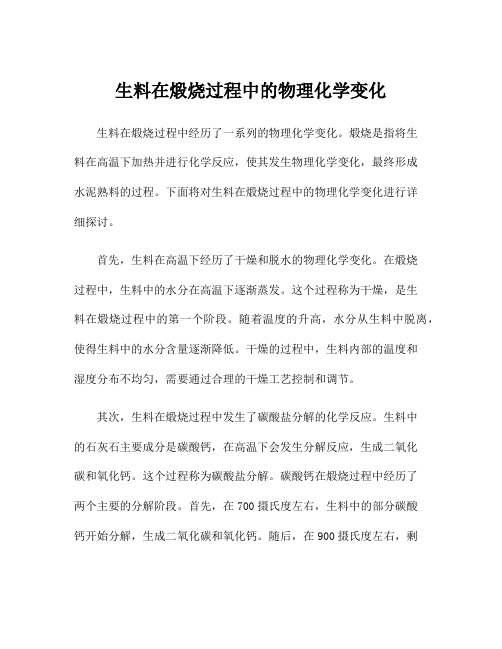
生料在煅烧过程中的物理化学变化生料在煅烧过程中经历了一系列的物理化学变化。
煅烧是指将生料在高温下加热并进行化学反应,使其发生物理化学变化,最终形成水泥熟料的过程。
下面将对生料在煅烧过程中的物理化学变化进行详细探讨。
首先,生料在高温下经历了干燥和脱水的物理化学变化。
在煅烧过程中,生料中的水分在高温下逐渐蒸发。
这个过程称为干燥,是生料在煅烧过程中的第一个阶段。
随着温度的升高,水分从生料中脱离,使得生料中的水分含量逐渐降低。
干燥的过程中,生料内部的温度和湿度分布不均匀,需要通过合理的干燥工艺控制和调节。
其次,生料在煅烧过程中发生了碳酸盐分解的化学反应。
生料中的石灰石主要成分是碳酸钙,在高温下会发生分解反应,生成二氧化碳和氧化钙。
这个过程称为碳酸盐分解。
碳酸钙在煅烧过程中经历了两个主要的分解阶段。
首先,在700摄氏度左右,生料中的部分碳酸钙开始分解,生成二氧化碳和氧化钙。
随后,在900摄氏度左右,剩余的碳酸钙分解,生成更多的二氧化碳和氧化钙。
碳酸盐分解反应是生料煅烧过程中释放二氧化碳的重要来源之一。
此外,煅烧过程中还发生了烧结和矿化的物理化学变化。
烧结是指生料颗粒在高温下发生颗粒结合的过程。
在烧结过程中,生料颗粒之间的一些成分发生了反应,使得颗粒相互结合在一起。
这个过程改变了生料的物理结构,使其形成硬度较大的颗粒。
矿化是指通过添加适量的辅料来调整生料组分和矿化物的含量。
矿化对于改善生料的热稳定性和提高水泥熟料的质量有着重要的作用。
此外,在生料煅烧过程中还发生了一系列的化学反应,如氧化、还原、硫化等。
这些反应在高温下进行,使得生料中的各种化合物发生转化,并最终形成水泥熟料。
例如,生料中的氧化钙在煅烧过程中会与其他化合物发生反应,形成硅酸钙、铝酸钙等化合物。
这些化合物是水泥熟料的主要成分之一,对于水泥的性能和品质有着重要的影响。
总结起来,生料在煅烧过程中经历了干燥和脱水、碳酸盐分解、烧结和矿化等一系列的物理化学变化。
技术水泥熟料的形成
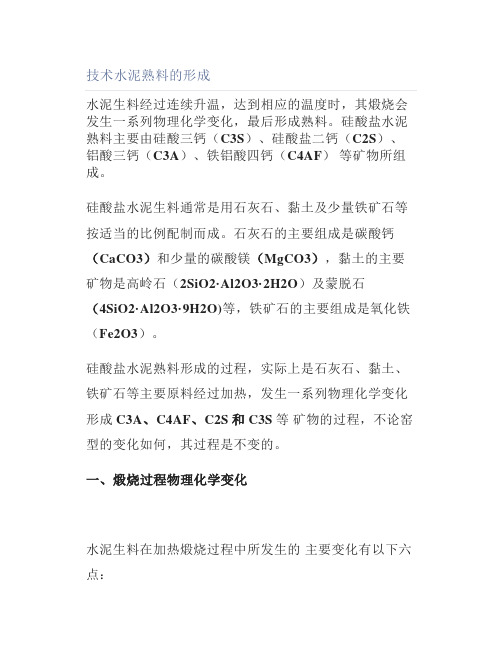
高岭土进行脱水分解反应时,在失去化学结合水的同时,本身结构也受到破坏,变成游离的无定形的三氧化二铝和二氧化硅,其具有较高的化学活性,为下一步与氧化钙反应创造了有利条件。在900-950℃,由无定形物质转变为晶体,同时放出热量。
表1 C3S-C2S-C3A系统熟料矿物组成
在熟料的冷却过程中,将有一部分熔剂矿物(C3A和C4AF)形成结晶析出,另一部分熔剂矿物则因冷却速度较快来不及析晶而呈玻璃态存在。C3S在高温下是一种不稳定的化合物,在1250 ℃时,容易分解,所以要求熟悉产自1300℃以下要进行快冷,使C3S来不及分解,越过1250℃以后C3S就比较稳定了。
(四)固相反应
黏土和石灰石分解以后分别形成了CaO、MgO、SiO2、Al2O3等氧化物,这时物料中便出现了性质活泼的游离氧化钙,它与生料中的二氧化硅、三氧化二铁和三氧化二铝等氧化物进行固相反应,其反应速度随温度升高而加快。
水泥熟料中各种矿物并不是经过一级固相反应就形成的,而是经过多级固相反应的结果,反应过程比较复杂,其形成过程大致如下:
技术水泥熟料的形成
水泥生料经过连续升温,达到相应的温度时,其煅烧会发生一系列物理化学变化,最后形成熟料。硅酸盐水泥熟料主要由硅酸三钙(C3S)、硅酸盐二钙(C2S)、铝酸三钙(C3A)、铁铝酸四钙(C4AF)等矿物所组成。
硅酸盐水泥生料通常是用石灰石、黏土及少量铁矿石等按适当的比例配制而成。石灰石的主要组成是碳酸钙(CaCO3)和少量的碳酸镁(MgCO3),黏土的主要矿物是高岭石(2SiO2·Al2O3·2H2O)及蒙脱石(4SiO2·Al2O3·9H2O)等,铁矿石的主要组成是氧化铁(Fe2O3)。
水泥制造过程简述
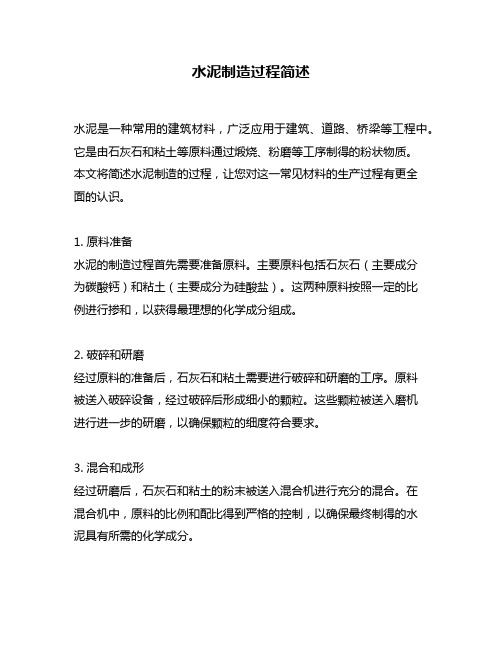
水泥制造过程简述水泥是一种常用的建筑材料,广泛应用于建筑、道路、桥梁等工程中。
它是由石灰石和粘土等原料通过煅烧、粉磨等工序制得的粉状物质。
本文将简述水泥制造的过程,让您对这一常见材料的生产过程有更全面的认识。
1. 原料准备水泥的制造过程首先需要准备原料。
主要原料包括石灰石(主要成分为碳酸钙)和粘土(主要成分为硅酸盐)。
这两种原料按照一定的比例进行掺和,以获得最理想的化学成分组成。
2. 破碎和研磨经过原料的准备后,石灰石和粘土需要进行破碎和研磨的工序。
原料被送入破碎设备,经过破碎后形成细小的颗粒。
这些颗粒被送入磨机进行进一步的研磨,以确保颗粒的细度符合要求。
3. 混合和成形经过研磨后,石灰石和粘土的粉末被送入混合机进行充分的混合。
在混合机中,原料的比例和配比得到严格的控制,以确保最终制得的水泥具有所需的化学成分。
4. 煅烧混合和成形后的原料被送入水泥窑,进行煅烧的工序。
水泥窑是一种巨大的旋转筒状设备,通过高温的燃烧来使原料中的化学成分发生反应,形成水泥熟料。
煅烧过程中,水泥窑不断旋转,使原料受到均匀的加热和混合。
5. 粉磨经过煅烧后,得到的水泥熟料需要进行粉磨,以获得所需的细度和物理性能。
水泥熟料被送入水泥磨机,经过磨破后成为细小的水泥颗粒。
水泥磨机通常采用滚筒磨机或者立式磨机,通过高速旋转的磨盘和磨辊对水泥熟料进行研磨,使其细度逐渐增加。
6. 包装和运输经过粉磨后,水泥袋装或散装装入包装袋中,并根据需要进行包装和标识。
包装后的水泥可以直接用于运输和销售,应用于各种工程和建筑项目中。
总结与回顾:水泥的制造过程经历了原料准备、破碎和研磨、混合和成形、煅烧、粉磨以及包装和运输等多个环节。
每个环节都需要严格的控制和操作,以确保最终水泥的质量和性能符合要求。
水泥的制造过程中,煅烧是一个关键步骤,通过高温燃烧使原料中的化学成分发生反应,形成水泥熟料。
经过粉磨的水泥颗粒细度逐渐增加,最终得到成品。
水泥的制造过程是一个复杂而精细的工艺,为各种工程提供了坚实的基础材料。
- 1、下载文档前请自行甄别文档内容的完整性,平台不提供额外的编辑、内容补充、找答案等附加服务。
- 2、"仅部分预览"的文档,不可在线预览部分如存在完整性等问题,可反馈申请退款(可完整预览的文档不适用该条件!)。
- 3、如文档侵犯您的权益,请联系客服反馈,我们会尽快为您处理(人工客服工作时间:9:00-18:30)。
硅酸盐水泥熟料的矿物组成
在硅酸盐水泥熟料中,氧化钙、氧化硅、氧化铝和氧化铁并不是以 单独的氧化物存在,而是经高温燃烧后,以两种或两种以上的氧化 物反应生成的多种矿物集合体,其结晶细小,通常,在硅酸盐水泥 熟料中主要形成四种矿物; 硅酸三钙 3CaO· SiO2,可简写为C3S,38-55%; 硅酸二钙 2CaO· SiO2,可简写为C2S,20-33% 铝酸三钙 3CaO· Al2O3:可简写为C3A:4-15% 铁相固溶体 通常以铁铝酸四钙4CaO· Al2O3· Fe2O3代替,可简写为 C4AF:10-18%。 另外,还有少量的游离氧化钙(f-CaO)、方镁石(结晶氧化镁f-MgO)、 合碱矿物以及玻璃体等。
3、碳酸钙分解反应的动力学关系 碳酸钙分解反应的动力学表达式,根据A ·Mü lle 大量试验结果,将温度、粒度尺寸及环境条件考虑在 内,有如下实用关系:
1 1 e0 A e
1 3
E RT
1 1 1 PCO2 eq PCO2环境 dp /2
式中: e0 —碳酸钙分解率,%; A—反应的频率因子,3.05×106Pa· m/s; E—反应活化能,171.850J/mol· K;
R—气体常数,8.314 J/mol· K; T—反应温度,℃;
d p —颗粒直径,m;
PCO2eq —碳酸钙分解时,CO 平衡压力,其值是温度函 2
数,Pa;
三、熟料矿物形成
在碳酸盐分解的同时,石灰质与粘土质组分间 进行固相反应,其过程如下: ~800℃:CaO•Al2O3,CaO•Fe2O3与2CaO•SiO2 开始形成; 800 ~ 900 ℃:开始形成12CaO•7Al2O3(C12A7); 900 ~ 1000 ℃: 2CaO• Al2O3•SiO2(C2AS)形成后 又分解。开始形成3CaO•Al2O3(C3A)和4CaO• Al2O3•Fe2O3(C4AF)。所有碳酸盐均分解,游离氧化钙 达到最高值。 1100 ~ 1200℃:大量形成C3A和C4AF,C2S含量 达最大值。
硅酸盐水泥熟料的化学组成
化学组成:主要由氧化钙(CaO)、二氧化硅(SiO2)、三氧化二铝 (A12O3)和三氧化二铁 (Fe2O3)四种氧化物组成,通常占 熟料的95%以上,同时,含有5%以下的少量氧化物, 如氧化镁(MgO)、三氧化硫(SO3)、二氧化钛(TiO2)、五 氧化二磷(P2O5)、以及碱(K2O和Na2O)等。 据统计,四种主要氧化物的波动范围一般为: CaO:62-67 %; SiO2:20-24%;Al2O3:4-7%;Fe2O3:2.5-6.0%。
影响因素:物料的化学组成、煅烧方法、升温速率、矿 化剂与其他微量元素等。
熟料的冷却 目的:回收熟料带走的热量,预热二次空气,提高窑的 热效率;改善熟料质量与易磨性;便于熟料运输、贮存 与粉磨。 熟料为何要急冷? 减少C3S分解;防止β-C2S向γ-C2S转化,提高熟料 质量;防止方镁石晶体长大,有利于水泥安定性;急冷 熟料晶粒小,活性高;C3A主要呈玻璃体,抗硫酸盐性 能提高;易磨性好等。 过程:液相的凝固和相变两个过程.
熟料的煅烧过程直接决定水泥的产量、质量、燃料与衬料 的消耗以及窑的安全运转。水泥窑有多种功能:反应炉、 熔炉、燃烧炉和传热设备、物料和气体的输送设备。
生料煅烧过程中的物理、化学变化
尽管煅烧过程因窑型不同而有所差异,但物 理、化学变化过程基本相似.其过程可概括为: 干燥与脱水 熟料的冷却 碳酸盐分解 固相反应
熟料粉磨
粉磨
煤粉制备 熟料烧成
贮存
水泥粉磨及贮存
一、水泥熟料的形成过程
硅酸盐水泥熟料的煅烧
石灰石、粘土质和少量铁质原料,按一定要求的比例(大体上75: 20:5)配合,经过均化、粉磨、调配以后即制成生料。由于制备方法不 同,生料可制成料浆(含水份约32~40%)、料球(成球水份约12~14 %)和料粉(含水份≤1%)。喂入水泥窑系统内,相应经烘干、预热、 预煅烧(包括预分解)、最后烧制成熟料的全过程统称煅烧过程。
a) SiO2主要离解为SiO44-阴离子团。Si-O价键较强,在粘 滞流动时,不易断裂,因而液相粘度较高; b) Al2O3和Fe2O3为两性化合物,可同时离解成MeO45-和 Me3+离子,两者的比例视各自金属离子半径和液相酸碱 度而异。 以MeO45-离子状态存在时,有4个O2-配位,构成 较紧密的四面体,Me-O价键较强,在粘滞流动时, 不易断裂,因而液相粘度较高; 以Me3+离子状态存在时,有6个O2-配位,构成松散的 八面体,Me-O价键较弱,在粘滞流动时,易于断裂, 因而液相粘度较低。
液相和熟料的烧结
熟料煅烧过程概述如下:
150℃以前 500℃左右 900℃左右 生料中物理水蒸发 粘土质原料释放出化合水;并开始分解为单独氧化 物如SiO2,Al2O3; 碳酸盐分解放出CO2和新生态CaO; 粘土的无定形脱水产物结晶,各种氧化物间进行固 相反应; 所产生的矿物部分熔融出现液相; 液相量增多,C2S通过液相吸收CaO形成C3S。直 至熟料矿物全部形成; 熟料矿物冷却。
影响固相反应的因素
生料的细度 生料愈细,比表面积越大,组分接触面越大, 同时表面质点的自由能越大,使扩散和反应能力增 强,因而反应速率加快; 生料的均化程度 生料的均匀混合,可增加各组分间接触, 也有利于加速反应; 压力 在固相反应中,增大压力可加速物质的传递过程. 但熟料烧结过程是多相共存、多反应同时进行的过 程.因此,提高压力有时并不表现出积极作用; 矿化剂 矿化剂可通过与反应物形成固溶体使晶格活化, 反应能力加强;也可以形成低共熔物,使物料在较 低温度下形成液相,从而加速扩散和和固相的溶解 作用
不同温度下,液相的计算公式: 1400℃ L=2.95Al2O3+2.20Fe2O3 +R 1450℃ L=3.00Al2O3+2.25Fe2O3 +R 1500℃ L=3.30Al2O3+2.60Fe2O3 +R
可以认为水泥熟 料中的其它组分 全部进入液相。
液相的粘度:它直接影响硅酸三钙的形成速率及晶体 发育。其大小与液相的组分性质与温度有关。温度越 高,粘度越低;铝率越高,粘度越大;多数微量元素 可降低液相粘度。
第四章
水泥熟料煅烧过程和设备
水泥熟料煅烧是个复杂的气-固、液-固和固-固相之间 的高温反应过程。既有某些天然矿物的分解,又有众多氧化物 之间的合成。 最终所形成的矿物,即熟料,其品种、数量和特征都要 合乎规范的要求,才能保证成品达到既定的性能指标。 虽然煅烧过程总的理论耗热量不是很多,但因所要求的反 应温度很高,因此单位产品实际燃料消耗量却比较多。 自从水泥生产工业化以来,煅烧熟料的主要设备是立窑和 回转窑。但本世纪下半叶以来,回转窑上预热和预分解技术的 开发应用,无论是在生产规模、生产指标和产品质量以及相应 科学技术水平方面,都有重大进展与突破。
脱水
指黏土矿物分解释放化学结合水。
层间水在100℃左右即可排除,而配位水则必须 高达400~600℃以上才能脱去。
粘土矿物的化合水存在形式: 层间水:以水分子形式吸附于晶层结构中。 配位水:以OH-状态存在于晶体结构中。 (1)高岭石脱水 (2)蒙脱石脱水 Al2O3.4SiO2.mH2O→Al2O3.4SiO2+m H2O (晶体结构—活性低)
影响碳酸盐分解速率的因素 温度 随温度升高,分解速率常数和压力倒数差相 应增大,分解速率和时间缩短;
t d 1 1 K( — ) p P0 (1— 3 1—ε )
式中:
t—分解时间;K—分解常数;
P—CO2的分压;ε—分解率 d—生料等效粒径; (单个颗粒碳酸盐分解动力学方程)
窑系统的CO2分压 通风良好, CO2分压较 低,有利于碳酸盐分解; 生料细度和颗粒级配 生料细度细,颗粒均 匀,粗粒少,分解速率快; 生料悬浮程度 生料悬浮分散良好,相对减 小颗粒尺寸,增大了传热面积,提高了碳酸盐分解速率; 石灰石的种类和物理性质 结构致密,结晶 粗大的石灰石,分解速率慢; 生料中粘土质组分和性质 粘土质中的矿 物组分的活性依次按高岭土、蒙脱石、伊利石、石英 降低.粘土质原料活性越大,可加速碳酸盐的分解过程.
900~1200℃
1250~1280℃ 1280~1450℃ 1450~1300℃
生料的干燥与脱水
干燥 自由水的蒸发。这一过程由于煅烧方式的不同而有 所差异。干法窑生料含水量一般不超过1.0%;半干法立 波尔窑和立窑为便于生料成球,通常含水12-15%,半湿 法立波尔窑过滤水分后的料块通常为18-22%;湿法为保 证料浆的可泵性则通常为30-40%。 自由水蒸发热耗: 100℃时,2257kJ/kgH2O(539kCal/kg)
(3)伊利石脱水 产物也是晶体结构,伴随体积膨胀
二、碳酸盐分解反应机制
1、碳酸盐分解反应 碳酸盐的分解主要为碳酸钙和碳酸镁的分解,其 化学反应式为:
碳酸盐(主要是碳酸钙、少量碳酸来自)的分解反 应是典型的缩核型强吸热的气固相反应。
2、石灰石颗粒的分解机制
CaCO3
分解过程分五步进行:
CaO
(1)气流向颗粒表面的传热过程; (2)热量由表面以热传导方式向分解面传递过程; (3)碳酸盐在一定温度下吸收热量,进行分解并放出 CO2的化学过程; (4)分解出的CO2,穿过CaO层面向表面扩散的传质 过程; (5)表面的CO2向周围介质气流扩散过程
本章主要介绍新型干法水泥生产过程中的熟料煅烧技术以及煅烧过程中的物理化学变化, 以旋风筒—换热管道—分解炉—回转窑—冷却机为主线,着重介绍当代水泥工业发展的 主流和最先进的煅烧工艺及设备、生产过程的控制调节等。
第一节 硅酸盐水泥的生产方法
水泥熟料的形成过程 生料制备 熟料煅烧 水泥粉磨
硅酸盐水泥生产过程
PCO2环境
—环境介质中CO2分压,包括分解产生的CO2和 燃气中CO2之和,Pa。