IE_七大手法应用实例
IE七大手法及案例

IE七大手法及案例1. 爱情陷阱爱情陷阱是一种常见的IE(影响力操作)手法,经常被用于操纵他人的情感和感情。
这种手法利用人们对爱情的渴望,诱使他们做出意想不到的决策。
案例:在一起工作的同事张三和李四一直以好朋友的关系相处。
某一天,张三觉得自己对李四有了更深的感情,于是开始表达对李四的追求。
李四感到困惑,因为他从未考虑过与张三发展更多的关系。
但是,张三利用他们之间已经建立的友谊和信任,不断向李四表达自己对他的爱慕之情,并强调如果李四拒绝他,他将永远失去对李四的友情。
在不断的情感轰炸下,李四最终同意与张三发展恋爱关系。
2. 损失厌恶损失厌恶是一种IE手法,适用于一种心理现象,即人们更倾向于避免损失,而不是追求收益。
这种手法利用了人们对损失的担忧,来控制他们的行为和决策。
案例:某公司推出一项新的会员计划,为新加入的会员提供一年免费使用的特权。
公司精心设计了会员计划,使会员在第二年续费时可以享受更多的优惠和额外的特权。
通过这种方式,公司让人们感觉到如果不续费,就会失去原本获得的特权,并且可能错过更多的好处。
这种损失厌恶的策略促使大部分会员选择继续使用该服务并续费。
3. 社会认同社会认同是一种IE手法,通过使人们感到自己与某个团体或社交群体相关联,来影响他们的决策。
这种手法利用了人们对社会认同和群体归属感的需求。
案例:某汽车品牌在广告中强调他们的产品是“时尚和先进的城市人”的选择。
他们使用年轻,时尚的模特来展示汽车,并且将汽车置于现代化的城市背景中。
通过这种方式,汽车品牌试图让人们相信拥有该汽车可以让他们成为时尚和先进的一员,与这个群体产生社会认同感。
4. 权威说服权威说服是一种IE手法,通过引用权威人物或专家的意见和观点来影响他人的决策。
这种手法利用了人们对于权威和专业知识的尊重和信任。
案例:在一项新药推广活动中,制药公司邀请了知名医学专家发表演讲并撰写相关文章,介绍该药物的疗效和优势。
这使人们更加信任该药物的有效性,因为他们相信专家的权威意见。
第三讲IE_七大手法及应用实例

防呆法之 层别原理
8.层别原理 避免将不同之工作做错,而设法加以区别出来。 (1)以线条之粗细或形状加以区别 例:所得税之申报单 将申报人必需填与之数据范围记载在粗线框内。 例:回函条请沿虚线之位置撕下。 (2)以不同之颜色来代表不同之意义或工作之内容 例:公文卷宗 红色:代表紧急文件,白色:代表正常文件,黄色:代表 机密文件 例:在生产在线将不良品挂上“红色”之标贴,将重修品挂上“黄色”之 标贴,将良品挂上“绿色”之标贴
五、防呆法的十大原理
防呆法 五五法 抽样法 人机法 双手法 动改法 流程法
防呆法的十大基本原理
斷根原理
保險原理
自動原理
相符原理
順序原理
பைடு நூலகம்
隔離原理
複製原理
層別原理
警告原理
緩和原理
防呆法之 断根原理
将原因从根本上排除,使其绝对不会发生错误 (1)借“排除”的方法来达成 例:录音带上若录有重要的资料想永久保存时,则可将侧边防再录孔之 一小块塑料片剥下,便能防止再录音。
研究探讨操作人员与机器的工作过程,借以发掘出可改善之 地方.
研究探讨涉及几个不同工作站或地点之流动关系,借以发掘 出可改善之地方.
借着抽样观察的方法能很迅速有效地了解问题的真象.
IE手法之一 防呆法
防呆法 五五法 抽样法 人机法 双手法 动改法 流程法
一、定义
又称防错法,防愚法. (Fool-Proof) 在错误以生之前加以防止 意味著“第一次就把事情做好” 提升产品品质,减少由于检查而导致的浪费 消除重工及其引起的浪費
防呆法之 相符原理
正向可以 插入
形状不同
反向无法 插入
规定数量
防呆法之 顺序原理
IE七大手法应用案例

=
=1.23 min
5.防呆法案例
冲模具开发中﹐设计在 零件设计上考虑了防呆.
加工设备上的指示灯及 显示屏同时发出视觉及 听觉上的信号。以便于 判断。
常见的防错装置
改善后换模流程
加工 完工处理 卸模板 清理机台
找新模板
完工处理
加工
装刀具
寻边
装模板
在上一个工件加工完成之前把新的待加工模板找好﹐清理机台后直接装新模板﹐ 可缩短换模作业时间。
2.动改法案例
动作改善在模具组立中的应用 A:螺丝拧紧
由之前的一只手扶助六角扳手﹐另一只手旋转作业拧 紧螺丝﹐变为使用右手无名指与中指夹住六角扳手旋 杆﹐使用右手大拇指旋转作业来拧紧螺丝。提高了作 业速度 。
操作者右手的动作
伸向1号盒中的橡皮垫圈 同左手动作
在装配槽中定好橡皮垫圈的位置并离开
伸向2号盒中的平钢垫圈 从2号盒中选出和握取平钢垫圈并将其推向装配槽5 在装配槽中定好平钢垫圈的位置并离开 伸向3号盒中的锁紧垫圈 从3号盒中选出和握取锁紧垫圈并将其推向装配槽5 在装配槽中定好锁紧垫圈的位置并离开 伸向4号盒中的螺栓 从4号盒中选出和握取螺栓 带螺栓到装配槽5处 定好螺栓的位置并插入装配槽5处的垫圈内 用螺栓插穿3个垫圈
改善前
改善后
4.抽查法案例
利用抽查法计算标准工时
有一钻床工,每天工作8小时,经过一天的分散抽 样后,结果是空闲比率为15%,即有72分钟是空闲的, 其余的408分钟在工作。在这一天观测中,其被评定的 平均绩效指针为110%。从检验信息知,该工人生产合 格产品420件。此外,根据以往的测定,该作业的宽放 率定为15%,如下示。由这些数据计算标准时间。
防呆法防错法(IE七大手法)
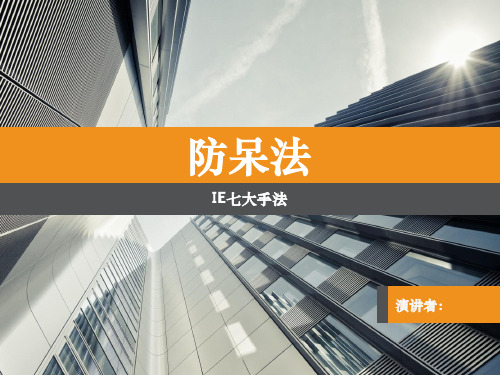
a
31 31
防错法的原理
a
32 32
防错法的原理
在上一节我们讲述了出现失误的九大原因和常见的失
误现象。仔细分析这些失误原因我们会发现,产生失误的原
因根本可归为三大类,即人的原因、方法原因和设备原因,
如下表:
失误原因
原因归类 所占比例
忘记 对过程/作业不熟悉 缺乏工作经验 故意失误 疏忽 行动迟缓 缺乏适当的作业指导 突发事件
01、漏掉某个作业步骤 02、作业失误 03、工件设置错误 04、缺少零部件 05、用错零部件
06、工件加工错误 07、误操作 08、调整失误 09、设备参数设置不当 10、工装夹具准备不当
a
25 25
防错法简介
交易过程常见失误: 交易过程常见失误有以下几类:
➢ 文件中漏掉重要信息; ➢ 文件中存在错误信息; ➢ 文件中存在与该交易无关的重要信息。
动改法
流程法
五五法 人机法 双手法 抽查法
22
目录
1、前言
墨菲定律
防错法的精髓
2、防错法简介
3、防错法的原理
对待失误的两种方式
防错的特点
防错的四种模式
4、防错法的技术和工具
防错法五大思路
防错法十大法那么
5、防错法应用实例 a
33
前言
a
44
前言
在1949年美国空军的一项火箭发射方案中,需要做一个 人体试验,试验的内容是测验一个人的身体对速度增加能有 多大容限。测验之一,是用一套16个“加速表〞装在被验者 身体的各局部。这些仪器有对与不对两种装法,果不其然, 负责装配的那位员工,把16件仪器统统都装错了。
部是由此类原因造成,如晚上没有休息好,精神状态差。
精益生产IE改善七大手法及用途
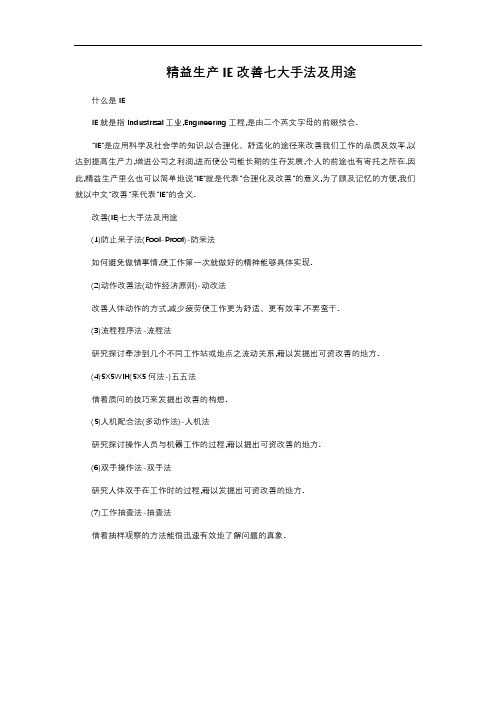
精益生产IE改善七大手法及用途什么是IE
IE就是指Industrisal工业,Engineering工程,是由二个英文字母的前缀结合.
"IE"是应用科学及社会学的知识,以合理化、舒适化的途径来改善我们工作的品质及效率,以达到提高生产力,增进公司之利润,进而使公司能长期的生存发展,个人的前途也有寄托之所在.因此,精益生产里么也可以简单地说"IE"就是代表"合理化及改善"的意义,为了顾及记忆的方便,我们就以中文"改善"来代表"IE"的含义.
改善(IE)七大手法及用途
(1)防止呆子法(Fool-Proof)-防呆法
如何避免做错事情,使工作第一次就做好的精神能够具体实现.
(2)动作改善法(动作经济原则)-动改法
改善人体动作的方式,减少疲劳使工作更为舒适、更有效率,不要蛮干.
(3)流程程序法-流程法
研究探讨牵涉到几个不同工作站或地点之流动关系,藉以发掘出可资改善的地方.
(4)5X5WIH(5X5何法-)五五法
借着质问的技巧来发掘出改善的构想.
(5)人机配合法(多动作法)-人机法
研究探讨操作人员与机器工作的过程,藉以掘出可资改善的地方.
(6)双手操作法-双手法
研究人体双手在工作时的过程,藉以发掘出可资改善的地方.
(7)工作抽查法-抽查法
借着抽样观察的方法能很迅速有效地了解问题的真象.。
IE七大手法改善案例
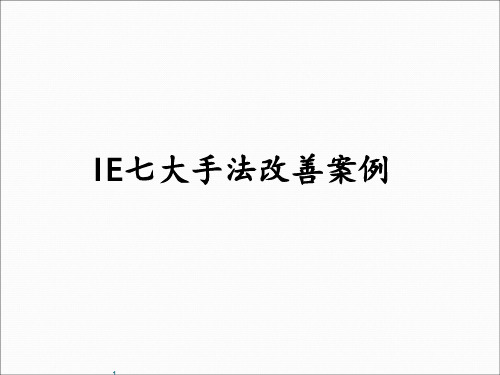
作業空間及通 道狹窄
5
一.人機配合法 案例2.DIP制程FCT測試改善2/3
改善歷程
改善后雙邊作業 1.人員作業效率提 高,1人操作9臺 機 2.機臺利用率提升 3.空間利用率高
6
一.人機配合法 案例2.DIP制程FCT測試改善3/3
改善后效果
【改善前】 【改善后】
7
二. 動作改善法 案例1:DIP制程取放治具改善1/3
1.L10測試治具改善 2.SMT上料防混料改善 3:SMT空焊降低改善
1.烤漆車間物流改善 2.烤漆雜質毛絲分析 1:組裝雙手作業改善
P20 P21-23 P24-26
P27-29 P30 P31-32
五五法(5W1H提問)
雙手操作法
2
一.人機配合法 案例1.完成品無線檢查改善1/2
人機操作分析
,
23
五. 防錯法 案例3:SMT空焊降低改善1/3
改善前 1.1 新機種Raptor量產初期,SMT BSide目檢工站發現SD Conn空焊(浮高)與掉件不良,達0.78%,占總不良比重:22%, 居不良首位.
24
五. 防錯法 案例3:SMT空焊降低改善2/3
改善后 在BSide Reflow前增加一個夾具(如圖),能彈性的支撑SD Conn,防止焊點重熔時受重力等影響產生不良.
夾持PCB 板邊
彈片支撑CN23
25
五. 防錯法 案例3:SMT空焊降低改善3/3
改善效果 統計確認,增加夾具後過BSide Reflow導致的該不良從 0.78%降到0.01%.產品品質得到客戶更好的認可.
26
六. 五五法 案例1:烤漆車間物流改善1/3
現狀物流圖示
貨淋室回流
ie七大手法运用案例

ie七大手法运用案例IE七大手法是指项目经理启发式管理的七个方法,可分别用于管理项目进度、质量、成本、风险、资源、沟通和人员等方面。
在项目管理中,运用IE七大手法可以帮助项目团队高效务实地完成项目,提高项目成功率。
以下是IE七大手法运用案例。
1. 甘特图:甘特图是一种项目进度管理工具,高效地呈现项目进度及各项活动的时间安排。
在某家公司的新版手机研发项目中,项目经理运用甘特图进行计划管理。
该项目共分为三个阶段,每个阶段均有若干个子任务,每个子任务分配一个完成时间。
通过甘特图,项目经理可以清晰地把握项目进度,及时调整计划,有效地掌控项目进展。
2. 直方图:直方图是一种定量数据的可视化工具,通过条形图表达数据信息,便于快速了解数据分布特征。
某家公司的品质改革项目中,项目经理使用直方图描述各个工序的不合格品率。
通过直方图,项目团队可以对大量数据进行整理和分析,进而制定对应策略,不断提高产品质量水平。
3. 七步法:七步法是解决问题的一种管理工具,可以帮助项目团队有效梳理问题、制定解决方案及跟进执行情况。
某市政改造项目中,团队发现路灯低空照明度低,使用七步法进行改造。
经过收集、分类、剖析、汉化、归纳、头臆及总结七个步骤,最终制定了合理的解决方案,成功完成改造任务。
4. 余弦定理:余弦定理是一种解决多:多冲突的决策分析工具,可帮助项目团队量化分析取舍风险与利益,制定更加科学的决策。
某家公司的新产品设计项目中,项目团队运用余弦定理处理多个方案并消除夹杂的主观因素,最终选定了最优方案,实现成功推进项目。
5. PERT图:PERT图工具是一种复杂项目管理的工具,通过概率论建立的方法,计算出项目完成时间的可能值及可能的风险概率,对项目进度提出可行建设性计划。
某家公司的扩建项目中,使用PERT图工具实现资源和时间的合理分配,避免了资金浪费和时间延误,成功完成了扩建项目。
6. 帕累托图:帕累托图是一种具有参考价值的图表,可以帮助项目团队识别追求成本或时间效益的重点工作,使团队更好地集中资源以有效完成目标。
IE七大手法应用实例
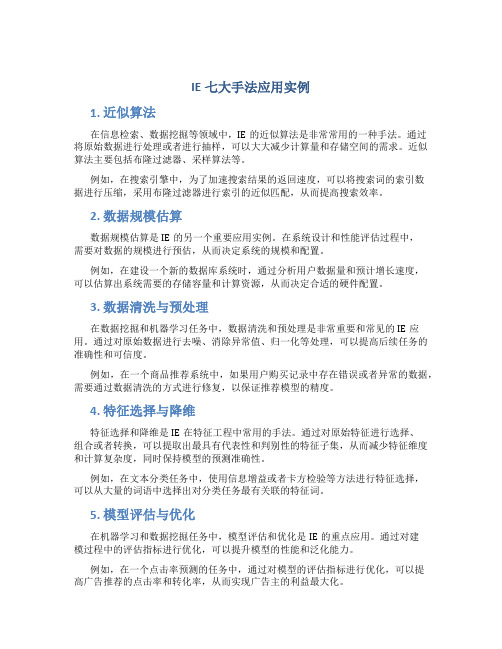
IE七大手法应用实例1. 近似算法在信息检索、数据挖掘等领域中,IE的近似算法是非常常用的一种手法。
通过将原始数据进行处理或者进行抽样,可以大大减少计算量和存储空间的需求。
近似算法主要包括布隆过滤器、采样算法等。
例如,在搜索引擎中,为了加速搜索结果的返回速度,可以将搜索词的索引数据进行压缩,采用布隆过滤器进行索引的近似匹配,从而提高搜索效率。
2. 数据规模估算数据规模估算是IE的另一个重要应用实例。
在系统设计和性能评估过程中,需要对数据的规模进行预估,从而决定系统的规模和配置。
例如,在建设一个新的数据库系统时,通过分析用户数据量和预计增长速度,可以估算出系统需要的存储容量和计算资源,从而决定合适的硬件配置。
3. 数据清洗与预处理在数据挖掘和机器学习任务中,数据清洗和预处理是非常重要和常见的IE应用。
通过对原始数据进行去噪、消除异常值、归一化等处理,可以提高后续任务的准确性和可信度。
例如,在一个商品推荐系统中,如果用户购买记录中存在错误或者异常的数据,需要通过数据清洗的方式进行修复,以保证推荐模型的精度。
4. 特征选择与降维特征选择和降维是IE在特征工程中常用的手法。
通过对原始特征进行选择、组合或者转换,可以提取出最具有代表性和判别性的特征子集,从而减少特征维度和计算复杂度,同时保持模型的预测准确性。
例如,在文本分类任务中,使用信息增益或者卡方检验等方法进行特征选择,可以从大量的词语中选择出对分类任务最有关联的特征词。
5. 模型评估与优化在机器学习和数据挖掘任务中,模型评估和优化是IE的重点应用。
通过对建模过程中的评估指标进行优化,可以提升模型的性能和泛化能力。
例如,在一个点击率预测的任务中,通过对模型的评估指标进行优化,可以提高广告推荐的点击率和转化率,从而实现广告主的利益最大化。
6. 并行计算与分布式系统并行计算和分布式系统是IE在大规模数据处理和高性能计算领域的重要应用。
通过将任务分解成多个子任务,并行地执行和处理,可以加速计算过程和提高系统的性能。
IE七大手法案例(组装)ppt课件
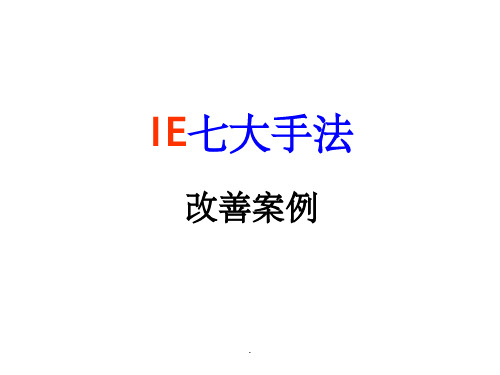
A:“不是。”
Q:“為什么不做?”
A:“改善意識不強。”
.
案例1
狀 改善后
結果﹕ 將線體支撐架向內移動﹐將上檢員工位移至 線頭正對線體﹐雙手同時作業﹐取消伸臂動 作﹐坐著操作. 上檢員工作強度大﹐疲勞 .
案例2
現狀描述
該系列機種自量產以來在DIP線和組裝線 均發生擊發板不充電現象﹐經工程分析确 認原因是MCU板上保險絲熔斷。
保險絲
安全隱患
.
案例2 改善歷程—真因求索
問:為什么數碼相機擊發板電路會不充電? 答:因為連接擊發板電路的保險絲熔斷。
問:為什么連接擊發板電路的保險絲會熔斷? 答:因為保險絲工作時電流超過額定值。
問:為什么保險絲的電流會超過額定值? 答:因為連接擊發板電路的FPC在接口處發生短路。
問:為什么FPC會在接口處發生短路? 答:因為FPC裝入接口后易發生偏位。
左手 4 3 4 11
現行方法
右手 4 4 3 11
根據動作經濟原則﹐考慮增加治工具來減少動作數量﹐縮短cycle time
.
案例2
貼label改善
利用如圖所示自動 貼紙機﹐可以取消 該工站折疊貼紙動 作(其耗時為1.2s)
工作 ﹕ 貼貼紙 開始 ﹕ 雙手空的 ---工具在流水線旁 ﹐ 產品在流水線上 結束 ﹕ 貼好一件產品放至流水線上
拆布套投側板 (1人)
出 L10 組裝 (1人)
裝箱 (1人)
套布套 (1人)
簡化 流程
烤漆廠裝箱
裝配作業
貼1pc腳墊 (1人)
拆布套投側板 (1人)
出L10 組裝 (1人)
改善前: Arches2機種側板腳 墊由L5組裝廠負責 粘貼,造成人力浪費
IE七大手法应用实例
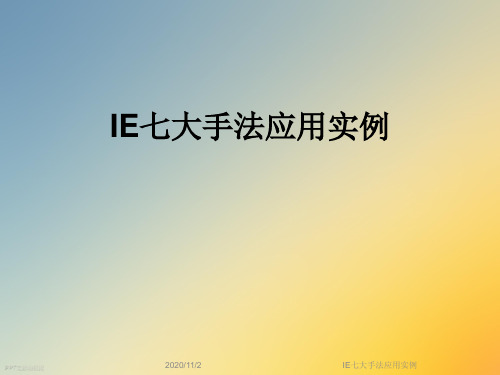
IE七大手法应用实例
PPT文档演模板
IE七大手法应用实例
PPT文档演模板
IE七大手法应用实例
IE手法之六 流程法
•工程 分 类
•工 程 记 号
•加 工
•
•Operation
•说 明
•凡一件物品或标的物经有意的改 •变其物理或化学性质之过程,均 •称操作。操作使用的材料、零件经加工而完成
•搬 运 Transportat ion
PPT文档演模板
IE七大手法应用实例
IE手法之三 ※五五法
5W 1H法;又称5 * 5何法;又称质疑创意法;简称 五五法.
•解释:
•5W1H提问技术;通过反复提问发现(或改善)点的一种 方法。
•【分享观念】 ➢工作改善最大的阻碍,并不在于技术不足,而是在于一个人的想法~他觉 得是以最好的方法在工作着,并且以为满足.
➢一个虽没有多大学识的人,只要他认为工作仍有改善的可能,那么他就比 您更适合这工作.
PPT文档演模板
IE七大手法应用实例
IE手法之三 五五法
What? Where? When? Who? How?
•要做这,是否必要? 有无其它更好的成果?
•要在此处做?
Why? •要此时做?
•要此人做?
有无其它更合适的地方? 有无其它更合适的时间? 有无其它更合适的人?
解释:
• 杜绝错误发生,將错误挡在”门”外的方法。
•错误
PPT文档演模板
IE七大手法应用实例
•1>.即使有人为疏忽也不会发生错误的构造—不需要注意力. •2>.外行人来做也不会做错的构造—不需要经验与直觉. •3>.不管是谁或在何时工作不出差错的构造 —不需要专门知识与技能.
IE-七大手法

WHERE 何处,什么地方,——空间 WHEN WHO 1H是指: HOW 何时,在什么时候——时间 何人,是什么人做/生产主体 如何,怎么做的
这五个字母之开关都是由“W”开始,的以称之为“5W”。 这个英文字母是由“H”开头,所以称之为“1H”。
第三法
Hale Waihona Puke 抽样法防错法 五五法 抽样法 人机法 双手法 动改法 流程法
动改法
动作改善的四大基本原则
I. II. III. 两手同时使用 动作单元力求减少 动作距离力求缩短
IV. 身体感受力求舒适
动作经济原则之 肢体使用原则
I. 双手同时开始并同时结束动作
单手作业会造成另一只手的空闲及不平衡
II. 双手的动作应对称进行
双手在单一方向运动的话,会造成身体重心的偏移,而维持这种平衡的劳 动将带来精神以及肌肉的疲劳。双手平衡对称动作是最省力的作业方式
消除出错引起的浪費
防错法实施的原则
I. 轻松原则
难辨认,难拿,难动的作业,易产生失误的作业 改 善: 用颜色区分----容易辨认 加上把手----容易拿 使用搬运器具----动作轻松
II. 简单原则
需要高度技能与直觉的作业,容易让人产生失误考虑用夹具,工具, 使新人或辅助人员也不容易出错。
防错法实施的原则
借着抽样观察的方法能很迅速有效地了解问题 的 真象. 以少数的观察結果用以推论全体的状况
抽样法的特点:
I. II. 节省时间和费用 操作方便,无须连续进行
第四法
人机法
防错法 五五法 抽样法 人机法 双手法 动改法 流程法
人和机器设备、辅助工具完美结合
I. II. III. 1人操作1部机器或多部机器 数人操作1部机器或多部机器 数人操作共同多部机器
IE七大手法介绍与实战分析

产生失误的原因基本可归为三大类,即人的原因、方法原因和设备原因,如下表:
失误原因
原因归类
所占比例
忘记
人
77.8%
对过程/作业不熟悉
人
缺乏工作经验
人
故意失误
人
疏忽
人
行动迟缓
人
缺乏适当的作业指导
方法
11.1%
突发事件
设备
11.1%
从表中可以看出,在导致失误的原因中,人占了绝大部分(77.8%),其次为作业方法和设备原因。
考虑下列因素,有无工序、操作可取消、合并、调整、简化 不需要的工序或操作; 改变工作顺序; 改变设备或利用新设备; 改变工厂布置或重新编排设备; 改变操作或贮存的位置; 改变订购材料的规格; 发挥每个工人的技术专长。
2.3 流程改善:有关搬运的改善
IE七大手法2:流程法
考虑下列因素,哪些搬运可以取消、合并、重排、简化 取消某些操作; 改变物品存放的场所或位置; 改变工厂布置; 改变搬运方法; 改变工艺过程或工作顺序; 改变产品设计; 改变原材料或零部件的规格。
A
B
B
A
IE七大手法3:时间分析法
3.4 时间分析之测量方法(秒表测时法):秒表测时法1、归零法:第一单元开始时,母指按下A键开动码表,第一单元结束时即按A 键停表,记下时间后按B键归零.2、连续测时法: 观测的第一单元开始按A键至整 个观测期间只按B键记录每一单元或动素时间,观测结束时方归零3. 累积测试法:用两个秒表, 一表开动,另一表即停止,一表停止则另一表开动,分段记录停止表上的时间后即归零
IE 手 法 的 特 征
客观性----采用IE分析程序方法,不同的人会得到相同的结果;定量性----对现实状态能进行定量分析,容易进行检讨;通用性----是用相同的符号及图表分析,能够信息共享;
IE七大手法及案例
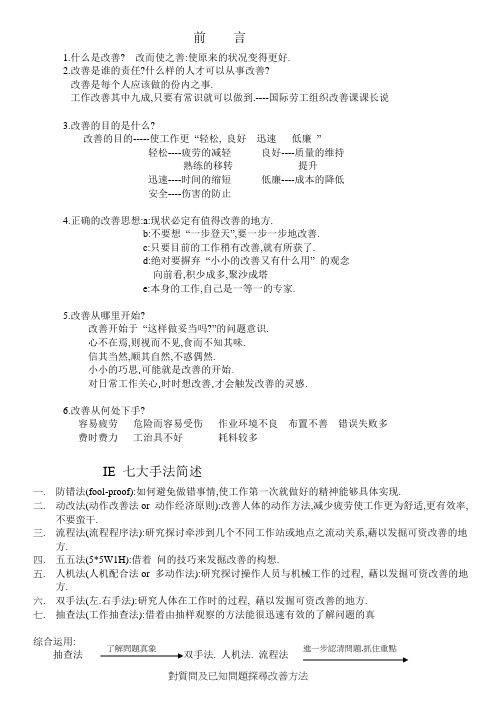
前言1.什么是改善? 改而使之善:使原来的状况变得更好.2.改善是谁的责任?什么样的人才可以从事改善?改善是每个人应该做的份内之事.工作改善其中九成,只要有常识就可以做到.----国际劳工组织改善课课长说3.改善的目的是什么?改善的目的-----使工作更“轻松, 良好迅速低廉”轻松----疲劳的减轻良好----质量的维持熟练的移转提升迅速----时间的缩短低廉----成本的降低安全----伤害的防止4.正确的改善思想:a:现状必定有值得改善的地方.b:不要想“一步登天”,要一步一步地改善.c:只要目前的工作稍有改善,就有所获了.d:绝对要摒弃“小小的改善又有什么用” 的观念向前看,积少成多,聚沙成塔e:本身的工作,自己是一等一的专家.5.改善从哪里开始?改善开始于“这样做妥当吗?”的问题意识.心不在焉,则视而不见,食而不知其味.信其当然,顺其自然,不惑偶然.小小的巧思,可能就是改善的开始.对日常工作关心,时时想改善,才会触发改善的灵感.6.改善从何处下手?容易疲劳危险而容易受伤作业环境不良布置不善错误失败多费时费力工治具不好耗料较多IE 七大手法简述一.防错法(fool-proof):如何避免做错事情,使工作第一次就做好的精神能够具体实现.二.动改法(动作改善法or 动作经济原则):改善人体的动作方法,减少疲劳使工作更为舒适,更有效率,不要蛮干.三.流程法(流程程序法):研究探讨牵涉到几个不同工作站或地点之流动关系,藉以发掘可资改善的地方.四.五五法(5*5W1H):借着问的技巧来发掘改善的构想.五.人机法(人机配合法or 多动作法):研究探讨操作人员与机械工作的过程, 藉以发掘可资改善的地方.六.双手法(左.右手法):研究人体在工作时的过程, 藉以发掘可资改善的地方.七.抽查法(工作抽查法):借着由抽样观察的方法能很迅速有效的了解问题的真_综合运用:抽查法. 人机法. 流程法五五法. 防错法. 动改法 对质问及已知问题探发改善方法 实现改善目标 区别: QC 七大手法:着重在问题的分析.抓重点I E 七大手法:着重在了解问题,应用改善方法解决问题 .第一部分 防呆法(防错法)1.防错法的意义:如何去防止错误发生的方法. 将发生的可能性降至最低/杜绝其发生2.目的:2.1具有即使人为疏忽也不会发生错误的构造 -------- 不需要注意力. 2.2具有外行人来做也不会错的构造 -------- 不需要经验与直觉.2.3具有不管是谁或何时工作都不会出错的构造 -------- 不需要高度的技能或专门的知识.3.功用:积极----绝不会再发生 消极----发生率降至最低4.进行步骤调查发现人为疏忽----> 设定目标,制定实际计划----->调查人为疏忽的原因----->提出防错的改善方案-----> 实施改善方案-----> check 实施效果-----> 维持管制状态排除法: 剔除会造成错误的要因. 替代法: 利用更确实的方法代替.容易化: 使作业变得更容易.更合适,更独特,或共同性以减低失败 适合化,共同化,集中化,特殊/个别化.异常检出 :前站虽有不良,但下站可以挑出,以降低其危害性.缓和影响: 作业失败的影响在其波及过程中,用方法使其缓和或吸收. 观念: 要求捕更多的鱼,首先必须讲求捕鱼技术的传授与使用. (授之以鱼不如授之以渔: 给某人几条鱼不如教给他)引申: 以不教而战,谓杀之.不教其方法,做错是主管之错.防呆法应用原理:•断根原理: 将原因从根本上排除,使绝不会发生错误. •例 : 下水道盖板 / 防护栏加高• 保险原理: 藉用二个以上的动作或依序执行才能完成工作.例 : 冲床双按钮 / 保险丝使用• 自动原理: 以自动化的方式来限制某些动作执行或不执行.例 : 设备积料 / 欠料感应進一步認清問題,抓住重點 對質問及已知問題探尋改善方法•相符原理: 藉用检核是否相符合的动作,来防止错误的发生.例: 自动机转向机构/ PCB的Post孔(极性槽)•顺序原理: 避免工作顺序或流程前后倒置,依编号顺序排列.例: 各类数据编页/ 食品厂自动门•隔离原理: 分隔不同区域的方式,保护某些地区使其不造成危险或错误的现象发生例: 不良品盒的使用/ 重工区域划分•复制原理: 同一工作,如需做二次以上,最好以COPY方式达成.例: 表格、发文的COPY / 治工具复制•层别原理: 线条粗细,不同的颜色.例: 制服不同/ 特别管制线/内外标签颜色•警告原理: 以声光等方式.例: 自动机报警灯/ Open/Short测试报警•缓和原理: 鸡蛋装运,保利龙等方式运用例: 设备流道、缓冲器案例:1.QL系列:改善前:压入机台承座材质为铁的,对产品PIN头有刮伤见铜,塑料打伤现象,且产品不易取出,后段用显微镜检验.改善后:将压入机台承座改为塑料,即避免了这一系列问题,产品轻松取下,且取消显微镜检验.2.DM-JACK半成品改善前:模板定位销是圆的,塑料易反装,导致整板塑料端子报废.改善后:模板定位销改为三角形,产品不易转动,并在模板前装一红色箭头,防止塑料放反.3.喷印机流道改善:改善前:由于产品体积较小,质量较轻.喷印时容易出现喷反,漏喷,重喷等多种品质隐患.改善后:在流道中间加一截挡板,来防止产品放反.消除多种隐患.4.治具合并:改善前:DM-JACK半成品插好1#,2#端子后,分别放入压入机压入,折CARRY机折CARRY,按两次按钮,送入下一工站.改善后:将压入机,折CARRY机合并,插好端子后放入,按一次按钮即可.5,JPD-004压入机台改善前:JPD003N-004在压入时右手十指去按,其它四指张开,一不小心就压到手指.改善后:给压入机台加上防护罩,消除安全隐患.第二部分动改法省力动作原则省时动作原则对”不可能”的人而言,就是”不可能”.动改法动作舒适原则对”可能”的人而言就是”可能”.动作简化原则原因:他动了脑子,想出了可能的点子出来.A.有关人体运用的原则原则1: 两手同时开始及完成动作(例: 试想独臂作业).原则2: 除休息时间外,两手不应同时空闲.原则3: 两臂的动作应反向同时对称.同时动作能使心理及生理上产生平衡的感觉,减少运用身体的应力机会,工作起来较轻松愉快.原则4: 尽可能以最低等级动作工作(动作等级分类: 如下图所示)原则5: 物体的动量尽可能利用之(例: 产品沿流道下滑/打击机).所谓动量,就是冲量=M*V (质量*速度)原则6: 联机曲线运动较方向突变直线运动佳(例:画圆与画正方形).研究表明:方向突变不但浪费时间,而且容易引起疲劳.原则7: 弹道式运动较轻快.弹道式运动只有在下列情形下才会停止下来:1.反向的肌肉制止力量2.碰到阻碍物3.运动的动量消失了原则8: 动作宜轻松有节奏.韵律节奏是指:有定期性的重复动作发生.B.有关工作场所布置与环境之原则原则9: 工具物料应置于固定处所.整理整顿的重要性: 减少寻找时间.例: 物料摆放五定定点、定位、定品、位型、定量1~10杂乱排列时顺序联机较困难,定位排列联机容易.原则10: 工具物料装置应依工作顺序排列并置于近处.使物料在使用过程中的活动范围减至最小.例: 现场物料摆放依工序/ 物品摆放依使用顺序(或先进先出).原则11: 利用重力喂料,愈近愈佳. (以防冲击太大)例:现场物料斗(箱)原则12: 利用重力堕送.例:沿斜面下滑.原则13: 适当之照明.适当的照明指:1. 适合其工作的充足光照度2. 光线颜色必须适当,没有反光3. 正确的投射方向同时考虑物体的”可见度”,可见度由下列因素决定:1.物体本身的明亮度2.物体与背景物的对比度3.物体本身的尺寸大小4.物体与眼睛之距离.5.其中因素如:注意力分散.疲劳.反应时间及反光等.原则14: 工作台椅应适当舒适.肘部能放于工作台上为佳,高椅时必须有垫脚设计.例: 试想若椅子太高或太低会怎么样.一般一个良好的坐椅设计应具有下列特征:1.高低可以调整2.坚固耐用,不会摇摆.3.坐垫应考虑人体工效学之形状成形.4.必须有靠背以支撑脊椎骨.C 有关手工具设备之原则原则15: 尽量以足踏/ 夹具替代手之工作.例: 脚踏开关/ 产品座附夹具功能.足踏设计考虑: 1.踏板面积大小2.踩踏时身体重量负荷之大小.3.设计方式:不要使操作者在操作时产生身体重心不稳的现象原则16: 尽可能将二种工具合并.将工具放下后再拿起比将一头转为另一头费时.例: 铆SHELL & 整形治具/ 预压& 热熔治具.原则17: 工具、物料预放在工作位置(例: 目视工具定位板).预放工具:将物体预先放置在适当的使用位置上,方便抓取,省时.悬挂的起子比放在一边时拿取省时.(下降.上升)原则18: 以手指负荷能力分配工作.原则19: 手柄接触面积尽可能加大例: 汽车方向盘包皮/圆形手柄.原则20: 操作杆尽可能少变更姿势.例: 船舵盘手把的适当数量设置/ 机车方向盘由Y形=> 圆形动作改善的基本方向?动作改善的重点要作动作改善必须从排除以下工作着手:1.需用力气的工作:必须使手.脚或全身用力方能完成的工作,或向膝下方伸手及蹲下拿起物品的动作.因为这些工作会引起肌肉的疲劳.2.不自然的姿势:如蹲下做事,弯腰工作等.3.需要注意力的工作:如必须仔细对准的工作或必须谨慎挑选的工作等都会引起精神上的疲劳.4.厌恶的工作:如噪音大,空气污浊,机器易故障的工作.•改善原则: 剔除合并重排简化动作改善的技巧与要点一.剔除a.剔除所可能的作业步骤或动作(包括身体,足,手臂或眼)b.剔除工作中的不规律性,使动作成为自发性,并使各种物品置放于固定地点.c.剔除以手作为持物工具的工作d.剔除不方便或不自然的动作e.剔除必须使用肌力才能维持的姿势f.剔除必须使用肌力的工作,而以动力工具取代之g.剔除必克服”动量”的工作h.剔除危险的工作i.剔除所有不必要的闲置时间二.合并a.把必须突然改变方向的各个小动作结合成一个连续的曲线动作b.合并各种工具使之成为用途c.合并可能的作业d.合并可能同时进行的动作三.重组a.使工作平均于两手,两手之同时动作最好呈对称性b.小组作业时,应把工作平均分配给各成员c.把工作安排成清的直线顺序四.简化a.使用最低等级的肌肉工作b.减少视觉动作并降低必须注视的次数c.保持在正常动作范围内工作d.缩短动作距离e.使手柄,操作杆,脚踏板,按钮均在手足可及之处f.在需要运用肌力时,应尽量利用工具或工作物的动量g.使用最简单的动素组合来完成工作h.减少每一动作的复杂性第三部分流程法一.流程法的意义:是”制程分析”最基本,最重要的技朮.也是降低”隐藏成本”,分析解决间题的最有力的工具.1.特点:清楚的标示所有的加工.搬运.检验.迟延等事项据以分析研究.设法减低各种事物的次数与所需时间及距离,降低隐藏成本的情况由此可以显示出来.2.运用范围:a.该件工作必须经历一个以上不同地点的动作才能完成.b.该件工作必须经由一个以上人来完成.3.功用:a.用于记载现行工作的过程.b.依5.1之记录,加以质问,寻求改善的地方.c.用以比较改善前及改善后之差异情形.5.符号:1作业------凡是需操作或使物理,化学性变化,准备物料等的总称搬运------由A处移至B处检验------鉴定物体而加以检查,测量等等待------物体或人因情况不允许或不立即采取下一步骤时称等待储存------物体之保存或等待流程图为 a.工作物流程图:以物体为;对象记录其被加工完成的流程图.b.工作人流程图:按工作人之动作来记录的流程图.c.图表介绍:为分析流程方便而特作规定.二.流程分析部分1.作业分析:考虑操作是否受设计方面的影响.加工条件是否可以改变(合并工站.动作等)2.搬运分析:搬运重量,距离,所费时间.其间还涉及到厂房空间及布置,机器排列,运输方法和工具等.3.检验(质量)分析:检验的目的:减少质量的变异性. 通常须考虑制成品的功能要求,精确度要求.检出不良品时,其检验价值如何?4.储存分析:此部分发生往往是因为材料或零件未到货,或者下一步加工之机器不胜重荷,须暂为等待所致.因此应对各种控制作重点考虑.5.等待分析:延迟纯为浪费,理应减至最低限度.此部分涉及人员调配控制及闲余能量分析的问题.应考虑人为或设备改进部分(由人工--- 电梯,拖车等)总之,各工站的分析都应在观察记录的基础上依照”ECRS”的原则予以处理.三.流程查核表“工作物”流程查核表:1.基本原则:a.减少制程数.b.安排最佳顺序. C.使各制程尽可能经济化.d.减少搬运e.如果有利时设法合并制程f.缩短移动距离g.找出最经济的移动方法h.在制品之存货量降低i.在最有利的位置使用最少的控制点.2.考虑下列因素有无制程可以省略?.a.不需要的制程(探讨:为何现在有?)b.使用新设备(探讨:为何目前使用此设备?)c.改变操作或储存位置(探讨:为何目前在此位置?)d.改变工作顺序(探讨:为何使用目前的工作顺序?)e.改变产品设计(探讨:为何现在如此设计?)f.改变入厂材料规格. (探讨:为何目前所定的材料如此?)3.有哪些制程可以合并在一起..1.工作场所.位置2.设备3.制造顺序4.产品设计’5.原材料.物料4.若重新安排制程,是否能使制程更短?5.有哪些制程可以更简化?四.”工作人”流程查核表1.基本原则a.尽可能删除不必要的步骤b.合并步骤c.缩短步骤d.安排最佳的顺序e.尽可能使各步骤经济化2.考虑下列步骤有无操作可以省略.合并.缩短.简短?a.不需要的操作.b.改变工作顺序c.利用新设备或重新编排设备d.改变产品形式e.更深入地认识部分的工人.3.考虑下列因素,有何移动可以被省略.合并.缩短.简短?a.废除某些操作b.改变物品存放场所c.将某些操作移到其他较方便的制程中d.改变工厂布置e.改变工作顺序f.利用输送带(必须是经济的)4. 考虑下列因素,有何延迟可以被省略.合并.缩短.简短?a.改变工作顺序b.改变工厂布置c.使用新设备或不同设备5.有何计数或检验的工作可以被省略.合并.缩短.简短?a.它们真的需要吗?能带来哪些效果或情报?b.有无不必要的重复现象.c.这些工作由别人来做是否更方便?d.在制程中,它们是否在最佳位置?e.能否使用抽样检验或统计控制?6.有无制程变得更加安全?a.改变工作顺序.b.使用新的或不同的设备c.改变工厂布置第四部分:五五法(质疑创意法)•When / Where / Who / What / why/how一.目的:熟悉有系统的质问技巧,以协助吾人发掘问题的真正根源所在以及可能的创造改善途径.5W1H: where:何处,在什么地方,什么空间when:何时what:何者.是什么东西/事/发生对象who:何人,是什么人在做/生产主体why:为何,怎么做的5 * 5 问法:指对问题的质疑不只一次,多问几次.在改善前1.要”打破砂锅问到底”,确实掌握了解问题所在.2.掌握现状的所有事实.怀疑并非只是笼统的抽象思维,应该是有系统的,循序渐进的,而且是有具体的方向. 生产的五大要素与5W1Hwhy二.质问的技巧1.对”目的”(WHAT)的质问a.目的是什么?b.条件是什么c.哪一部分工作要做d.重点是什么? 什么有关系? 规范是什么?功用是什么?等等.2.有关”人”(man)方面的质问a.是谁做的? 为何由他做?是否可由别人做? 谁最适合做这些事?b.为什么不把授权(股长)去决定?谁做最好?效率最高?3.对”工作顺序”(when)的质问:变更时间的顺序a.在何时做的? 为何要在当时做? 改在另外的时间又如何?4.有关”何时”的质问是否可改变时间点来达到既消除瓶颈,又达到预期目的呢?5.对”地点”(where)的质疑:变更场所或对场所内的物品布置重新组合.在何处做的?改善创意的基本观念.△打破传统习惯的束缚. ~~~没有最好、只有更好△工作改善最大的阻碍,并不在于技朮不足,而在于一个人的想法. ~~~ 别轻易说“不行”,起而行之△尝试从另一个角度来思考.~~~ 善于假设、推断,假若我是你该怎么做△发挥直觉力----创造力的源泉.~~~ 觉得不对(不应该),就应试着去改善△蚕食策略. ~~~ 不怕多、只怕不知道多或不去做.五五法实例:JACK永久性open抱怨无作业标准未制作标准未重视无隐患意识懒(有概念) 无训练无概念产生创意的思考法则相反法则:里外调换,上下颠倒,职务互换,作业次序反转,由左向右改为由右向左.例: 主管轮调/工站次序调整拼图法则将每一基本单元分解出来,再尝试重新组合的方式,可能会有意想不到的效果例:如何配色衣服会更美观?大小法则改变尺寸.形状等的大小,看看其影响会如何?改变增大时有加.乘,缩小时有减.除,根据这种原则可以产生很多创意.例:西瓜瓜子无子瓜/产品吹气等多余工站例外法则将经常发生的事物与偶然发生的事物作区别.偶发事件作例外管理(“一般”与“特殊”情况)例: 制造部的例外管理.集合法则将多用途的东西组合,或不同单元的事物结合,效用会如何呢?例:刀.叉,开瓶匙的结合/音乐卡片替代法则考虑用别的方式来替代现有的方式,会有什么样的结果呢?例:呆.废料可再利用吗?/是否有更合适的代用品?饭粒代胶水模仿法则模仿是创意的最佳触媒,借着参考现物触类旁通引发新的创意.蜘蛛网鱼网/蛙眼弧形雷达水平法则发挥联想力.考虑由水平方向支思考.突破传统及习惯上的缚束.例花香味化妆品味坐式椅子形状定数法则将经常发生的事物予以制度化,可以产生许多简化的效果及提高.例:特殊管治方法.第五部分人机法•意义:以图表的方式.,记录操作人员与一部或多部机器的操作关系,并藉此记录来进一步的分析与改善.•作用:---- 人与机器的时间有无空闲.---- 利用这段空闲,操作另一部机器.---- 利用空闲,作清除削屑、量测或其他手工工作.一.作用:学习如何记录人与机器配合工作时的过程.即:主要是分析人工或机器能量(时间)的闲余,以谋求消除浪费增进效率之道.在人机配合法中一般人工作周期往往比机器运行周期短,为谋求利用这些闲余,方法如下:a.利用这些空闲时间操作另一部机器b.利用这些空闲时间作清除余料,量测工作wu或其他手工之操作.2..适用范围a.1人多机或1机b.数人多机或1机c.数人操作共同的工作.3.功用:a.了解在现况下,操作人员之时间或机器之时间是否妥善应用.b.依上述之记录加以质疑,寻求改善的地方.c.用以比较改善前与改善后的差异情形.4.符号说明:三.人机查检表1.基本原则:a.平衡小组之工作量b.增加机器使用之比率c.减轻负担最重的人员之工作d.删除不必要的步骤e.合并各步骤f.使每一步骤容易进行2.附属操作能否删除?a.视同不必要而删除b.以改善工作次序而删除c.使用新的或不同之设备而删除d.以改变布置而删除3.移动能否删除?a.随操作之删除而删除b.合并c.改变设备d.改变布置e.改变工作次序f.使用输送带4.迟延能否删除?a.改变工作次序b.改变布置c.使用新的或不同的设备5.检验能否删除?a.此检真的必须吗?检后资料是否有用?b.是否有必要?c.留给下工站是否更方便?d.在此检验是否为最佳位置?6.操作能否合并a.改变工作之次序b.以新或不同之设备c.改变布置7.移动能否合并?a.—b.---c.改变每次搬运之数量8.迟延能否合并?9.检验能否合并?a.改变工作之次序b.改变布置10.操作能否简易行之?a.使用更好的工具b.改变control的位置c.使用更大的容器d.利用惯性e.减少视觉需求f.采用更舒适的高度g.使用夹具11.移物能否简易行之?c.改变布置,缩短距离d.改变移物之方向e.改变在制程中的位置,以缩短距离12..由于新人员之影响所产生的迟延,能否删除?a.改变参加小组人员b.改变所使用是改变:减少人员迟延时间至最低程度,以减少影响器械工作时间减少机器之空闲时至最低限度.c.小组中各人之工作岗位间的距离重新安排d.改变小组内各人之工作次序第六部分双手法•意义:以图表的方式.,记录操作人员与一部或多部机器的操作关系,并藉此记录来进一步的分析与改善.1.适用范围: a.适用于以人为主的工作,即研究对象为人体的双手或双足b.专注于某一固定工作地点之研究,即该工作固定在此地点上实施/c.该件工作有高度的重复性,即该件工作会再次大量生产2.功用: a.用于记录现行操作者的双手(足)的动作过程.b.对所记录下的内容加以质疑,寻求改善的地方.c.用于比较改善前与改善后的情形,差异.3.正常工作范围:指在坐姿状态双手之正常活动可及的范围,是为正常工作范围(约37-40cm)作用:---- 人与机器的时间有无空闲.---- 利用这段空闲,操作另一部机器.---- 利用空闲,作清除削屑、量测或其他手工工作.一.双手查检表1.基本原则a.将步骤减至最低b.安排最好顺序c.合并可能的步骤d.使每一步骤尽量简单e.平衡双手f.避免用手持住g.工作场所应考虑人体工学2.附属操作能否删除a.因不需要而删除b.因改变工作顺序而删除c.因改变工具或设备而删除d.因改变工作场所的布置而删除e.因材料的些许改变而删除f.因产品的些许改变而删除g.因治具,夹具的使用或改善而删除3.移物能否删除?a.因不需要而删除b.因改变工具,设备或利用自动滑落,工具使用方法改变等而删除4.持住动作能否删除?a.因不必要而删除b.因使用简单的持住装置或挂具需要而删除5.迟延能否删除或缩短?a.因不必要b.改变身体各部位的工作c.平衡身体各部位的工作d.同时做两件事e.修改工作,使两手做相同工作,但相位(phase)不同6.附属操作能否简化?a.使用较好的工具b.改变工具的放置位置c.使用较好的材料容器d.可能的话,利用杠杆原理(leverage)e.可能的话,利用慢性原理f.可能的话,利用重力原理g.减少使用视觉的需要h.改善工作场所的高度(使之在肘部以下)7.移物能否简化?a.改变布置,缩短距离b.改变移动方向c.使移动平顺而连续,避免骤停现象8.持住能否简化?a.缩短持住时间b.使用较有力的身体部位(如腿)或使用足部操作之夹具.第七部分抽查法•利用统计学原理,进行抽样调查的方法.•样本的概念/ 群体.•抽样及工作抽查的好处:---- 时间上不允许/ 成本大/ 不可能/ 不必要---- 观测时间短---- 从事观测记录的人员不需要具备太高深的技术---- 对被观测的对象所产生的干扰次数及时间。
IE七大手法及其应用
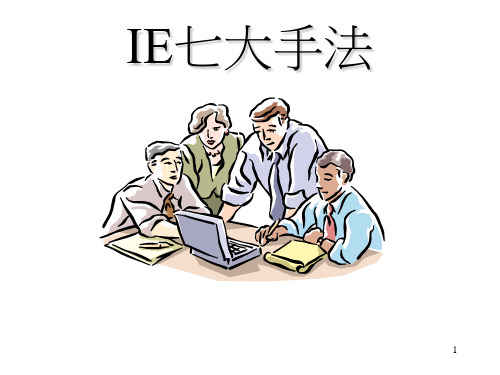
7.发挥联想力,考虑由水平方向来做思索,突破老 式及习惯上旳缚束 例:花香味--化装品 坐式--椅子形状
32
生产旳五大要素与5W1H
Why
为何
材料 半成品 成品
生产对象 What
措施 how
生产主体 Who
人 机器 工具 附件
环境 Where
空间
时间
时间
When
33
ECRS四大原则
ECRS是经过提问技朮,对现行方案进行严 格考核与分析,建立新措施时所利用旳四 项原则:
1.取消(Elminate) 2.合并(Combine) 3.重排(Rearrage) 4.简化(Simple)
34
五.人机法
人机法(也称人机操作分析)以图表旳方式, 统计操作人员与一部或多部机器旳操作 关系,研究分析每一操作周期中机器与人 所出现旳闲余时间,并得以开发利用,便可 到达降低成本,提升生产效率旳作用.
闲余能量分析: ---机器旳闲余能量 ---操作者旳闲余能量
35
人机操作分析案例(改善前)
时间(min)
IE七大手法
1
什么是IE?
IE是Industrial Engineering(工业工程)
IE是“实践规划,设计,实施与管理生产和服务 (确保功能,可靠性,可维修性,日程计划与成本控 制)系统旳带头职业.这些系统可能是自然界旳 社会技朮,经过产品旳生命周期,服务或程序,人 员,信息,原料,设备,工艺和能原旳集成.”其目旳 为“到达盈利,效率,效益,合适性,责任,质量,产 品与服务旳连续改善.”所用旳措施“涉及到人 因和社会科学(涉及经济学),计算机科学,基础科 学,管理科学,通讯技朮,物理学,行为学,数学,统 计学,组织学和伦理学.
- 1、下载文档前请自行甄别文档内容的完整性,平台不提供额外的编辑、内容补充、找答案等附加服务。
- 2、"仅部分预览"的文档,不可在线预览部分如存在完整性等问题,可反馈申请退款(可完整预览的文档不适用该条件!)。
- 3、如文档侵犯您的权益,请联系客服反馈,我们会尽快为您处理(人工客服工作时间:9:00-18:30)。
思考! 价格、成本和利润三者的关系?
销售价格=成本+利润 利润=销售价格-成本 成本=销售价格-利润
高效率,低成本为目标; 改善,标准化为过程;
效率
成本
– QC七大手法
• 检查表;柏拉图;层别法;直方图;散布图;管制图;特性要因 图
– 下图我们看一下IE与QC七大手法的区别与 联系:
QC主研究
+宽放
【分享】
“在我心目中,模具是工业之母,IE就是 工业之父。母亲给你成长的基础,父亲 给你茁壮的空间。”
富士康总裁 郭台铭
改善永远没有终点,谢谢大家!
搬 运 Transportati on 检验 Inspection
停滞
IE手法之七 抽查法
工作抽查法系指应用统计学上的抽样原理来研究工作中 人员与机器设备之活动情形,它是一个了解事实最有效 的工具之一.它可在最短的时间和最低的成本之下获得 有关人与设备之间的有用咨询.
– 种类:
全检
抽样
免检
UV 照 射 时 间 控 制
怎样防呆(思考方向): • 排除法:
– 剔除会造成错误的原因;
• 替代化:
– 利用更却是的方法來代替;如自动化,電学,光学等
• 容易化:
– 使作也变得更容易、更合适或共同性以减低 错误 发生 ;
• 异常检出:
– 虽然已经有不良或错误现象,后制程(站)进行防堵;
• 缓和影响 :
• 减少操作人员的疲劳 • 缩短操作人员的操作时间 • 提高工作的效率
动作级次:
级别
运动枢轴 人体运动部 分 动作范围 速度 体力消耗 动作力量 疲劳
时间以25mm 为主
一
指节 手指 手指节之长 度 1 最少 最弱 最小 0.0016分
二
手腕 +手掌 手掌之长 度 2 少 弱 小 0.0017分
三
肘 +前臂 前臂之长 度 3 中 中 中 0.0018分
四
肩 +上臂 上臂之长 度 4 多 强 大 0.0026分
五
身体 +肩 上臂+身躯 弯曲 5 最多 最强 最大
– 十大动作经济原則:
A. B. C. D. E. F. G. H. I. J. 双手同时而对称; 动作级次低; 动作有节奏感; 治工具需定位; 物料自动运送; 环境易于工作; 让手解放出来; 治具多功能设计; 手指负荷均匀; 工具物料预定位.
运用 1、人体的运用原则
生活中:电视选台器 : 旋转→按压→触摸式→遥控
双手同时动作
利用重力
2、作业布置的原则
3、 工具和设错法
解释:
• 杜绝错误发生,將错误挡在”门”外的方法。
错误
1>.即使有人为疏忽也不会发生错误的构造—不需要注意力. 2>.外行人来做也不会做错的构造—不需要经验与直觉. 3>.不管是谁或在何时工作不出差错的构造 —不需要专门知识与技能.
IE辅研究
QC辅研究
(问题发生前)
(问题发生前)
IE主研究
IE七大手法简介
授人以鱼,不如授人以渔!
防呆法
在設計或改善時防止(杜絕)錯誤發生的手法;
五五法 动改法
尋找改善方向或發現問題的提問手法(5W1H); 如何用最简单,有效,省力的动作来完成工作目标;
IE 7 tools
人机法
研究操作人員與機器如何最佳匹配使工作效率最大化;
工程 分 类 工 程 记 号 说 明
加 工 Operation
凡一件物品或标的物经有意的改 变其物理或化学性质之过程,均 称操作。操作使用的材料、零件经加工而完成
原料、材料、零件或制品被移动 至其他位置所发生之状况。 为鉴定物品性质之规格之异同, 而用某种方法鉴定,比较或证明 其数量与品质,称为检验. 停止 存储 原料、材料、零件在进行加工、检查之前所处的 一种停滞状态
IE手法之三 五五法
What? Where? When? Who? How? Why?
要做这,是否必要? 要在此处做? 要此时做? 有无其它更好的成果? 有无其它更合适的地方? 有无其它更合适的时间?
要此人做?
要这样做?
有无其它更合适的人?
有无其它更合适的方法?
IE手法之四 双手法
双手法 流程法 抽查法
尋找解决独臂作业或左右手工作不平衡的手法; 尋找&解决制程间不平衡,搬运,暂存的潛在問題;
藉著抽樣觀察的方法能很迅速有效地了解問題的真象
IE手法之一 动改法
解释 :
• 利用动作经济原则以达到舒适,省力、省时, 有效率的工作境界; • 帮助发现问题;提供建立新方法的方向。
作用:
成本高,效率差
成本效率一般
成本,效率低
用途:
空闲比率(%) = 空闲时间 总观察时间 X 100%
工作改善:
工作时间 工作比率(%) = X 100% 总观察时间 绩效指标(%) = 标准时间 X 100% 实际时间
制定标准工时:
标准时间 =
总观察时间 X 工作比率 X 平均绩效指标 观察期间的总产量
– 作业失敗的影响在其波及的過程中,用方法使其缓和或吸收
IE手法之三 ※五五法
5W 1H法;又称5 * 5何法;又称质疑创意法;简称五 五法.
解释:
5W1H提问技术;通过反复提问发现(或改善)点的一种方 法。
【分享观念】 工作改善最大的阻碍,并不在于技术不足,而是在于一个人的想法~他 觉得是以最好的方法在工作着,并且以为满足. 一个虽没有多大学识的人,只要他认为工作仍有改善的可能,那么他就 比您更适合这工作.
IE七大手法应用实例
前言
• 所有企业的目的均是希望以最小的投入 (INPUT)得到最大的产出(OUTPUT),以致获 得最大的效益.那么如何在品质保证的基 础上,使企业获得最大的效益呢? • 降低成本、提高生产力,把 “投入”做最有 效的组合,以达到品质稳定、效率高、交期 准、浪费少、成本低.这也是近代工业界工 业工程(IE)所要做的主要工作.
解释:
记载现行操作者双 手(足)的动作过程. 加以质疑,寻求改 善之地方. 比较改善前及改善 后之差异情形.
IE手法之五 人机法
了解操作者与机器 时间是否妥善应用. 加以质疑,寻求改 善之地方. 比较改善前及改善 后之差异情形. 研究人 与机器 的关系
案例:76** 一体QC多机台改善
IE手法之六 流程法