钢水温度和成分智能建模控制系统
基于中包钢水连续测温的二冷配水控制模型与系统

中 图分 类号 : 7 7 TV 7 文 献标 识 码 :A 文章 编 号 :0 3 2 12 1)3 0 7 4 10 7 4 (0 00 0 7 0
Ca t g Se o d r oig Co t l d l n y t m si c n a yCo l n r n n o Mo e d S se a
lq i t e n CC Tu d s .Ba e n i, e tt a s e q a i n a d d n m i t r d s rb to o to i u d se li n i h s d o t a h a r n f re u to n y a c wa e it i u i n c n r lmo e r d la e
方程 的二冷水 动态控制 , 诸如 自适 应控 制 、模糊 专家系 统和神 经元网络等的智 能控 制[ 5。这些 方法 的实现都 4 1 - 离不 开 中间包钢水 温度 , 处理方法 或直接简单设 为 目 其 标温度 ; 或采用 间断式快速 热电偶测量 。前者不 能根据
s ia i t fmo e s a d s o h t h r p s d c n r l y t m u s r b s l n e i b y a d s ts i st e p o u to u t b l y o d l , n h wst a e p o o e o to se r n o u ty a d r la l n a i fe h r d c i n i t s r q ie e t . e u rm n s
钢铁冶炼中的钢水温度控制技术研究

钢铁冶炼中的钢水温度控制技术研究钢铁冶炼是现代工业中至关重要的一个环节,而钢水温度的控制则是钢铁冶炼中的关键技术之一。
本文将重点探讨钢水温度控制技术的研究进展,包括目前应用的方法、存在的问题以及未来的发展趋势。
首先,我们要了解钢水温度的控制对钢铁冶炼的重要性。
在整个炼钢过程中,钢水的温度控制直接影响着合金元素的溶解度、浇注工艺和成材的质量。
因此,如何有效地控制钢水的温度成为了提高钢铁生产效率和质量的关键。
目前,钢水温度的控制主要采用了自动化控制系统和传统的人工控制方法。
传统的人工控制方法主要依靠操作工人的经验和直观感觉来调节钢水的温度,虽然这种方法在一定程度上可以满足生产的需要,但是操作人员的主观因素会影响控制效果,而且操作过程容易受到熔炼环境的影响。
因此,需要更加科学和精确的技术手段来实现钢水温度的精准控制。
自动化控制系统则是针对传统人工控制方法的局限性而提出的解决方案。
通过在炼钢炉和相关设备上安装传感器和控制器,可以实现对钢水温度的实时监测和自动调节。
这种方法相对来说更加精准和可靠,不受外界因素的影响,可以有效提高钢水温度控制的精度和稳定性。
但是,目前在钢水温度控制技术中仍然存在一些问题和挑战。
例如,传感器的精度和寿命、控制系统的稳定性和响应速度、以及在高温高压环境下的设备可靠性等方面都需要进一步改进和提高。
另外,由于钢铁冶炼生产现场的特殊环境,控制系统还需要具备一定的抗干扰能力和自适应能力,以应对各种突发情况和异常操作。
未来,可以通过引入先进的传感技术、人工智能和大数据分析等手段来提升钢水温度控制技术的水平。
例如,可以利用红外线测温技术和热像仪来实现对钢水温度的非接触式监测,通过大数据分析和建模来优化控制算法和参数,从而提高控制系统的精度和响应速度,降低能耗和生产成本。
另外,值得注意的是,钢水温度控制技术也需要与其他炼钢工艺相互配合,实现信息互通和智能化协同。
例如,在连铸过程中,可以将钢水温度和流量等数据与连铸机的参数进行联动控制,以实现整个生产过程的协同优化。
过程控制中的智能化技术应用实例分析
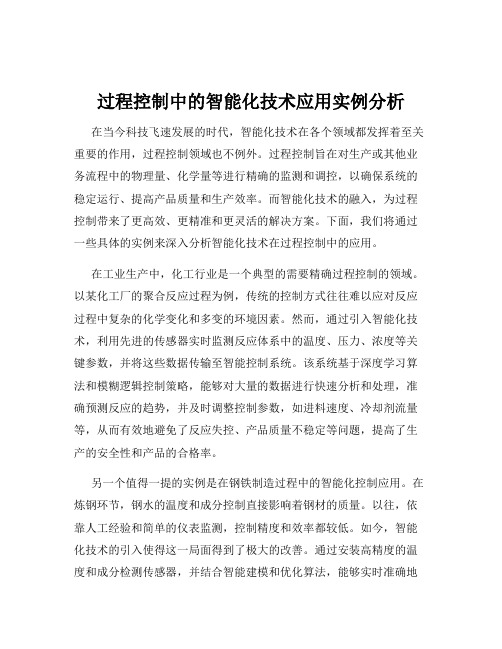
过程控制中的智能化技术应用实例分析在当今科技飞速发展的时代,智能化技术在各个领域都发挥着至关重要的作用,过程控制领域也不例外。
过程控制旨在对生产或其他业务流程中的物理量、化学量等进行精确的监测和调控,以确保系统的稳定运行、提高产品质量和生产效率。
而智能化技术的融入,为过程控制带来了更高效、更精准和更灵活的解决方案。
下面,我们将通过一些具体的实例来深入分析智能化技术在过程控制中的应用。
在工业生产中,化工行业是一个典型的需要精确过程控制的领域。
以某化工厂的聚合反应过程为例,传统的控制方式往往难以应对反应过程中复杂的化学变化和多变的环境因素。
然而,通过引入智能化技术,利用先进的传感器实时监测反应体系中的温度、压力、浓度等关键参数,并将这些数据传输至智能控制系统。
该系统基于深度学习算法和模糊逻辑控制策略,能够对大量的数据进行快速分析和处理,准确预测反应的趋势,并及时调整控制参数,如进料速度、冷却剂流量等,从而有效地避免了反应失控、产品质量不稳定等问题,提高了生产的安全性和产品的合格率。
另一个值得一提的实例是在钢铁制造过程中的智能化控制应用。
在炼钢环节,钢水的温度和成分控制直接影响着钢材的质量。
以往,依靠人工经验和简单的仪表监测,控制精度和效率都较低。
如今,智能化技术的引入使得这一局面得到了极大的改善。
通过安装高精度的温度和成分检测传感器,并结合智能建模和优化算法,能够实时准确地获取钢水的温度和成分信息。
控制系统根据这些信息,自动调整氧气吹入量、添加合金的种类和数量等,实现了对炼钢过程的精确控制,大大减少了废品率,提高了生产效率和产品质量。
在食品加工行业,智能化技术同样发挥着重要作用。
以某饮料生产厂为例,其灌装生产线采用了智能化的质量检测系统。
在灌装过程中,高速摄像机和图像识别技术能够实时检测每个瓶子的灌装量、瓶盖的密封情况以及标签的粘贴质量等。
一旦发现问题,系统会立即发出警报,并自动将不合格产品剔除,确保了产品的一致性和质量稳定性。
钢铁行业智能化冶炼工艺优化方案

钢铁行业智能化冶炼工艺优化方案第1章智能化冶炼工艺概述 (4)1.1 传统冶炼工艺的局限性 (4)1.1.1 能源消耗高:传统冶炼工艺在高温、高压环境下进行,能源消耗较大,导致生产成本较高。
(4)1.1.2 环境污染严重:传统冶炼工艺在产生大量废气、废水和固体废物的同时还伴严重的噪声污染,对生态环境造成严重影响。
(4)1.1.3 生产效率低:受限于人工操作和设备功能,传统冶炼工艺在生产效率方面存在一定的局限性。
(4)1.1.4 产品质量不稳定:由于人工操作和设备磨损等因素,传统冶炼工艺生产出的产品质量波动较大,影响产品竞争力。
(4)1.2 智能化冶炼工艺的发展趋势 (4)1.2.1 绿色环保:智能化冶炼工艺通过优化能源利用和减少污染物排放,实现绿色生产。
(4)1.2.2 高效节能:智能化冶炼工艺采用先进设备和技术,提高生产效率,降低能源消耗。
(4)1.2.3 自动化生产:智能化冶炼工艺通过自动化控制系统,实现生产过程的精确控制,提高产品质量。
(4)1.2.4 网络化协同:智能化冶炼工艺利用大数据、云计算等技术,实现生产过程的实时监控和远程调度,提高行业竞争力。
(4)1.3 智能化冶炼的关键技术 (5)1.3.1 智能控制系统:采用先进的控制算法和设备,实现冶炼过程的自动控制,提高生产效率。
(5)1.3.2 传感技术:利用高精度传感器实时监测冶炼过程中的各项参数,为智能控制系统提供数据支持。
(5)1.3.3 数据分析与处理技术:通过大数据分析技术,挖掘生产过程中的潜在规律,为优化冶炼工艺提供依据。
(5)1.3.4 机器学习与人工智能:利用机器学习和人工智能技术,实现冶炼工艺的智能优化,提高产品质量。
(5)1.3.5 网络通信技术:构建高效、稳定的网络通信系统,实现生产过程的数据传输和信息共享。
(5)1.3.6 技术:研发具有冶炼操作能力的,替代人工完成高危险、高强度的工作。
钢铁智能制造技术有哪些前沿应用
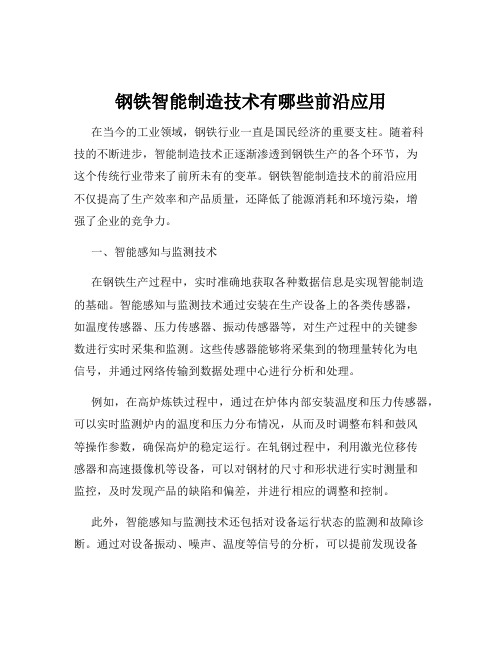
钢铁智能制造技术有哪些前沿应用在当今的工业领域,钢铁行业一直是国民经济的重要支柱。
随着科技的不断进步,智能制造技术正逐渐渗透到钢铁生产的各个环节,为这个传统行业带来了前所未有的变革。
钢铁智能制造技术的前沿应用不仅提高了生产效率和产品质量,还降低了能源消耗和环境污染,增强了企业的竞争力。
一、智能感知与监测技术在钢铁生产过程中,实时准确地获取各种数据信息是实现智能制造的基础。
智能感知与监测技术通过安装在生产设备上的各类传感器,如温度传感器、压力传感器、振动传感器等,对生产过程中的关键参数进行实时采集和监测。
这些传感器能够将采集到的物理量转化为电信号,并通过网络传输到数据处理中心进行分析和处理。
例如,在高炉炼铁过程中,通过在炉体内部安装温度和压力传感器,可以实时监测炉内的温度和压力分布情况,从而及时调整布料和鼓风等操作参数,确保高炉的稳定运行。
在轧钢过程中,利用激光位移传感器和高速摄像机等设备,可以对钢材的尺寸和形状进行实时测量和监控,及时发现产品的缺陷和偏差,并进行相应的调整和控制。
此外,智能感知与监测技术还包括对设备运行状态的监测和故障诊断。
通过对设备振动、噪声、温度等信号的分析,可以提前发现设备的潜在故障,并及时进行维修和保养,避免因设备故障导致的生产中断和损失。
二、智能建模与优化技术钢铁生产是一个复杂的物理化学过程,涉及到多个工序和环节。
为了实现生产过程的优化控制,需要建立精确的数学模型来描述生产过程中的各种关系和规律。
智能建模与优化技术结合了机器学习、人工智能和数值计算等方法,能够对钢铁生产过程进行建模和仿真,并根据生产目标和约束条件,优化生产工艺参数和操作策略。
例如,在炼钢过程中,可以建立钢液成分、温度和炉渣成分等之间的数学模型,通过优化配料和吹氧等操作参数,提高钢水的质量和产量。
在连铸过程中,建立铸坯凝固和冷却的数学模型,优化冷却水量和拉速等参数,减少铸坯的裂纹和偏析等缺陷。
此外,智能建模与优化技术还可以应用于生产计划和调度的优化。
基于智能技术的温度测量系统的设计

到钢水 温度 的连 续 变 化 的信 息 。多 年 来 , 内外 科 国 技 工作 者试 图借 助计 算 机 进 行 钢 水 温 度 预 报 , 要 主 有 机理 分 析 和 统 计 计 算 两 种 方 法 。机 理 分 析 基 于 机 理模 型 , 冶炼 阶段 分 别 建 立 钢包 、 氢 搅 拌 、 按 吹 冷 却水 、 烟尘 、 能量输 入 ( 热 、 应 热 ) 加 料 、 水 各 电 反 、 钢 单元 的能量平 衡 关 系 , 进 一 步进 行 综 合计 算 。这 再
种方 法需 要 大量 的前 提 , 需 现 场 提 供 大 量 的工 艺 且 数据 , 因而制 约 了机 理 模 型 的在 线 运 行 。统 计 计 算 方法 通过 大 量 数 据 找 到 预报 量 与 各 种 过 程 变 量 间
家规 则 进 行 修 正 , 钢 水 温 度 测 量 的 平 均 误 差 降 使 低, 满足 工艺 要求 。
20 07年 6月 l 2日收到
的显示 、 印 , 程 参 数 的 超极 限报 警 , 打 过 工艺 流 程 图 的 制作 、 显示 和过 程参 数 的动 态 显 示 。控 制 程 序 设 计 要 求 实现 的功 能 有过 程参 数 和数 据 采 集 , 据 处 数 理, 控制 算法 的选 择 和设 计 , 制量 的输 出 , 警 检 控 报
法无法得到钢水 温度的连续变化 的信 息。针对这种 情况 , 绍 了基 于智 能技术 的钢水 温度 的软测 量方 法。应用人 工神经 元 介 网络 B P算法对钢 水温度进 行初步预报 , 再根据专家 系统 知识 对一 些特殊 的情况进 行修 正 , 从而获 得 良好 的效 果。运行结 果
钢水车的智能监控与远程控制系统研发
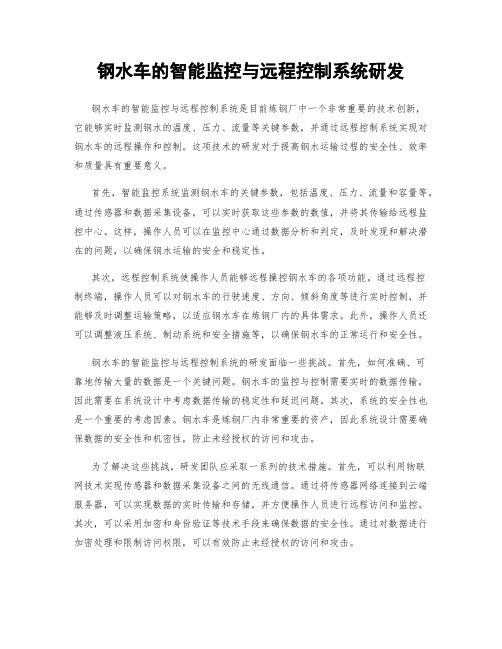
钢水车的智能监控与远程控制系统研发钢水车的智能监控与远程控制系统是目前炼钢厂中一个非常重要的技术创新,它能够实时监测钢水的温度、压力、流量等关键参数,并通过远程控制系统实现对钢水车的远程操作和控制。
这项技术的研发对于提高钢水运输过程的安全性、效率和质量具有重要意义。
首先,智能监控系统监测钢水车的关键参数,包括温度、压力、流量和容量等。
通过传感器和数据采集设备,可以实时获取这些参数的数值,并将其传输给远程监控中心。
这样,操作人员可以在监控中心通过数据分析和判定,及时发现和解决潜在的问题,以确保钢水运输的安全和稳定性。
其次,远程控制系统使操作人员能够远程操控钢水车的各项功能。
通过远程控制终端,操作人员可以对钢水车的行驶速度、方向、倾斜角度等进行实时控制,并能够及时调整运输策略,以适应钢水车在炼钢厂内的具体需求。
此外,操作人员还可以调整液压系统、制动系统和安全措施等,以确保钢水车的正常运行和安全性。
钢水车的智能监控与远程控制系统的研发面临一些挑战。
首先,如何准确、可靠地传输大量的数据是一个关键问题。
钢水车的监控与控制需要实时的数据传输,因此需要在系统设计中考虑数据传输的稳定性和延迟问题。
其次,系统的安全性也是一个重要的考虑因素。
钢水车是炼钢厂内非常重要的资产,因此系统设计需要确保数据的安全性和机密性,防止未经授权的访问和攻击。
为了解决这些挑战,研发团队应采取一系列的技术措施。
首先,可以利用物联网技术实现传感器和数据采集设备之间的无线通信。
通过将传感器网络连接到云端服务器,可以实现数据的实时传输和存储,并方便操作人员进行远程访问和监控。
其次,可以采用加密和身份验证等技术手段来确保数据的安全性。
通过对数据进行加密处理和限制访问权限,可以有效防止未经授权的访问和攻击。
在研发过程中,还可以考虑集成人工智能技术,以进一步提高智能监控与远程控制系统的性能。
例如,可以开发基于机器学习的算法,用于预测钢水车可能出现的故障和问题,并提供相应的处理措施。
钢水温度和成分智能建模控制系统
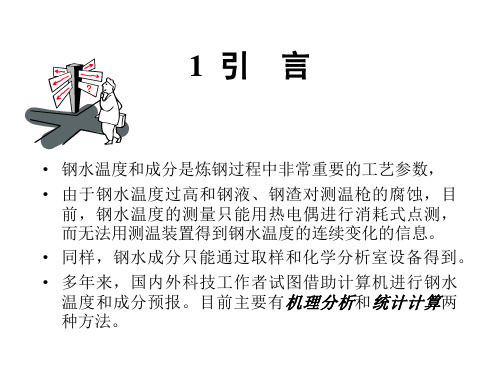
• 以往功率设定点仅根据静态的电气圆
图,制订出各种电压档下的功率曲线, 由操作工根据自己的经验选取。这种 静态分析假设电气线路电阻、电抗不 变和三相独立,由于冶炼工艺过程的 复杂性,随机干扰因素多,三相电气 变量间耦合严重,这种假设并不成立。
温度和成分预报。目前主要有机理分析和统计计算两
种方法。
1引 言
机理分析基于机理模型, 按冶炼阶段分别建立各 单元的平衡关系,再进 一步进行综合计算。
– 物理意义清楚,对改进操 作和冶炼工艺有指导意义;
– 需要大量的前提假设,且 需现场提供大量的工艺数 据,在正常生产时得不到 的, 因而制约了机理模型 的在线运行。
通过对电流电压瞬时值的高速采 集和信号处理,还原了电量非正 弦畸变掩盖下的有效值、有功无 功功率、功率因数、耗电量的本 来面目,
2 智能钢水温度预报
• 用人工神经元网络技术建立反映钢水温度与各种非线性、时变因 素间对应关系的钢水温度预报模型,辅之以专家规则进行修正。
模型输 入
神经元网络输入 量
专家系统输入量
PID控制与 ANN控制的比较表
三相耦合性
信号检测
设定点优化 系统预报 增益自适应
弧稳定性控制
PID控制 基于三相理想情况下的完全解 耦, 认为三相电压, 三相电流间 彼此独立,与实际情况相去甚远 基于理想正弦波的假设, 检测的 平均值不能
ANN控制 考虑三相之间的耦合性, 其算法 具有三相敏感性
5 合金补加计算
智能合金计算模型:
(1)基于冶金物化反应机理和冶金工艺专家的经验, 建立了物理化学特性要求量化的专家系统和合金料的 料种选择和加入次序的专家系统,将各种定性的、启 发式的知识信息,通过各种推理过程进行非结构化的 问题求解,形成量化的控制成分约束; (2)进行料种选择,然后利用线性规划模型(LP)进 行合金补加优化计算; (3)合金元素收得率利用神经元网络进行自适应学习, 以反映钢水温度、炉况和渣制度的影响。
钢水控制系统
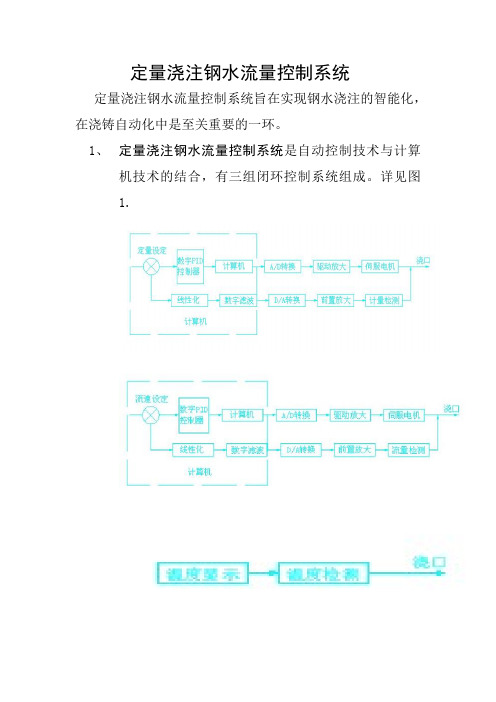
定量浇注钢水流量控制系统
定量浇注钢水流量控制系统旨在实现钢水浇注的智能化,在浇铸自动化中是至关重要的一环。
1、定量浇注钢水流量控制系统是自动控制技术与计算
机技术的结合,有三组闭环控制系统组成。
详见图
1.
流量检测安装在浇口杯中,检测钢水柱的截面,测定
钢水的流速,计算机时间,流量通过前置计算对执行
机构发出执行指令实现控制。
2、执行机构见下图:
碳棒通过夹持器与执行机构硬性连接,由导轨和滚珠丝杆及滑台伺服电机执行控制,伺服电机为力矩控
制方式,通过位差回零补偿碳棒和浇口套的融失。
检
测单元对流量和流速进行检测,检测的信号通过前馈
方式输出给运动控制,同时在关闭状态时如有漏液输
出报警。
红外检测位于用于准确检测出水口温度
为保温提供准确参数,保证浇铸质量。
3、由于钢水流量检测没有先例,还没有可以借签的参
数,需要对传感器的设计需要进行基础性试验研究。
电弧炉炼钢厂钢水成分与温度预报模型的研究

电弧炉炼钢厂钢水成分与温度预报模型的研究
杨凌志;朱荣;宁建成;宋景凌;韦波
【期刊名称】《工业加热》
【年(卷),期】2013(042)001
【摘要】基于实际生产数据分析研究影响钢水成分与温度的因素,通过利用BP神经网络的理论,建立了钢水成分与温度预报模型,实现了提前对铜水成分与温度的预报.钢水成分预报值与实测值基本吻合,钢水温度预报的命中率在84.0%以上,模型具有较高的预报精度.
【总页数】4页(P15-17,20)
【作者】杨凌志;朱荣;宁建成;宋景凌;韦波
【作者单位】北京科技大学冶金与生态工程学院,北京 100083;北京科技大学冶金与生态工程学院,北京 100083;北京科技大学冶金与生态工程学院,北京 100083;衡阳华菱钢管有限公司,湖南衡阳 421000;衡阳华菱钢管有限公司,湖南衡阳 421000;衡阳华菱钢管有限公司,湖南衡阳 421000
【正文语种】中文
【中图分类】TF741.5
【相关文献】
1.RH-MFB精炼时钢水温度预报模型的开发 [J], 吴扬;倪红卫;张华;吴建荣
2.炼钢厂连铸钢水温度预报模型 [J], 曹永国;杨守礼
3.LF-RH工艺生产超低硫钢钢水温度预报模型 [J], 樊智勇;熊玮;胡汉涛;黄翼飞
4.LF炉钢水温度预报和最优供电模型 [J], 任铁良;王卫红;刘硕;李宝东;马赫;王辉
5.钢包精炼过程中钢水成分微调及温度预报 [J], 李晶;傅杰;王平;毕其富;黄成钢因版权原因,仅展示原文概要,查看原文内容请购买。
- 1、下载文档前请自行甄别文档内容的完整性,平台不提供额外的编辑、内容补充、找答案等附加服务。
- 2、"仅部分预览"的文档,不可在线预览部分如存在完整性等问题,可反馈申请退款(可完整预览的文档不适用该条件!)。
- 3、如文档侵犯您的权益,请联系客服反馈,我们会尽快为您处理(人工客服工作时间:9:00-18:30)。
2 智能钢水温度预报
• 通过200炉左右冶炼数据的训练、学习,钢水温度预报的平均误差 即可降低到±7℃ ,足以满足工艺要求。
• 从第一次钢水测温开始,每一分钟预报一次,从而计算出整个冶 炼过程的钢水温度变化情况。
PID控制与 ANN控制的比较表
三相耦合性
信号检测
设定点优化 系统预报 增益自适应
弧稳定性控制
PID控制 基于三相理想情况下的完全解 耦, 认为三相电压, 三相电流间 彼此独立,与实际情况相去甚远 基于理想正弦波的假设, 检测的 平均值不能反映有效值的变化
基于静态优化设定点 无
简单分段线性化
无
ANN控制 考虑三相之间的耦合性, 其算法 具有三相敏感性
统计计算基于统计分析 方法,通过大量数据找 到预报量与各种过程变 量间关系。
– 算法简单,且很容易在线 实现;
– 只能反映线性关系,关系 错综复杂,统计模型的精 度不高。
1引 言
• 智能建模控制原理
现实世界
假说、猜测、惯例、经验、规则 、常识等经验
模型
1引 言
基于专家系统技术,建
立了能量设定点的动态
ANN 模型
温度变化 网络当前预报温度:T’
专 家系 统 模 型 温度变化Δ T
Tt =Δ T+T’
模型预报温度: Tt
图1 钢水温度预报模型的逻辑结构
2 智能钢水温度预报
• 人工神经元网络模型采用带隐含层的BP网络,输入量 选取与能量平衡有关的能量输入(电能、氧、油等)、 原料加入量、冶炼时间、初始温度、能量损耗相关量, 输出为钢水温度变化。
优化,综合考虑以下因
素:
•电气设备容量
•电弧弧长控制
•电效率和热效率 •耐材指数
工艺要求
•三相功率平衡
•冶炼阶段
•生产节奏
能量设定点
动态优化
基于人工神经元网络和专家系统技术 ,进行了钢包精炼炉热平衡计算和钢 水温度预报,在冶炼过程中,钢水温 度的变化一目了然,能量输入有的放 矢。
热平衡和 温度预报
工艺参数 计算
检测电流电压的瞬时值, 能真实 的反映实际的电流电压波形, 从 而得到控制所需的各种信息 基于动态优化的设定点 可预测系统变量的变化, 从而防 患于未然 根据系统的状态情况, 不断调整 系统的ANN权值,从而, 得到优化 的控制性能 有
4 智能调节器
炉子仿真人工神经元网络 用于预报炉子相关状态的 变化, 调节器人工神经元网络则 根据预报结果和优化设定点 之间的差计算电极升降控制
1引 言
• 钢水温度和成分是炼钢过程中非常重要的工艺参数, • 由于钢水温度过高和钢液、钢渣对测温枪的腐蚀,目
前,钢水温度的测量只能用热电偶进行消耗式点测, 而无法用测温装置得到钢水温度的连续变化的信息。 • 同样,钢水成分只能通过取样和化学分析室设备得到。 • 多年来,国内外科技工作者试图借助计算机进行钢水
的输出值.
在ANN调节器投入运行时,我们 考虑了一个智能PID保驾算法, 综合输出通过几条规则判断ANN 输出的正确性, 选择ANN控制输 出还是PID控制输出, 确保系统运行的安 全可靠.
4 智能调节器
5 合金补加计算
• 合金补加计算的目的是计算加入钢水中的各种辅料和 合金料,使得在满足钢种成分和物料要求的前提下, 加入的辅料和合金料的成本最低。
温度和成分预报。目前主要有机理分析和统计计算两
种方法。
1引 言
机理分析基于机理模型, 按冶炼阶段分别建立各 单元的平衡关系,再进 一步进行综合计算。
– 物理意义清楚,对改进操 作和冶炼工艺有指导意义;
– 需要大量的前提假设,且 需现场提供大量的工艺数 据,在正常生产时得不到 的, 因而制约了机理模型 的在线运行。
智能 调节器
EF/LF
基于人工神经元网络技 术,建立了变压器二次 侧电阻、电抗的动态计 算模型,并进而计算出 二次有功功率、弧功率 、弧压、弧长、耐材指 数等工艺参数,为系统 优化提供定量依据
ANN电气线路 仿真模型
信号予处理 u,i
采用人工神经元网络预报弧流变化,与 设定点相比较,不断调整三相敏感的调 节算法的权值,得到优化控制性能。同 时,采用模糊控制抑制底吹氩引起的强和信号处理,还原了电量非正 弦畸变掩盖下的有效值、有功无 功功率、功率因数、耗电量的本 来面目,
2 智能钢水温度预报
• 用人工神经元网络技术建立反映钢水温度与各种非线性、时变因 素间对应关系的钢水温度预报模型,辅之以专家规则进行修正。
模型输 入
神经元网络输入 量
专家系统输入量
3 能量输入设定点动态优化
4 智能调节器
• 电极升降控制的目的是通过马达或液压站比例阀或伺服阀调节 电极末端距废钢或钢水液面的距离, 来保证冶炼过程中电量的 状态变量跟踪优化后的输入功率设定点. 传统电极升降PID控 制都是以阻抗控制为基础即保持电流和电压反馈信息保持电压 和电流之间 的恒定比例。
3 能量输入设定点动态优化
能量输入设定点优化: • 通过神经元网络预报冶炼过程中电气参数的变化 • 利用电气特性曲线计算满足约束条件的最大电弧 功率 • 根据专家工艺知识确定工作电压和工作电流的组 合设定点
根据冶炼过程中各阶段的不同特性,将冶炼功率曲线分 解成化渣、成分调整升温和出钢前升温三个阶段,在 不同阶段,根据预报的钢水温度值、电气特性曲线、 冶炼工艺和生产节奏对温升的要求进行弧压和弧流设 定点的调整,实现电能输入的优化。
• 智能钢水温度预报 可用于转炉、电炉、 钢包精炼炉、连铸大包、 中间包等的钢水温度预 报。
温度曲线
3 能量输入设定点动态优化
• 能量输入设定点动态优化功能可归结为选择合理的决策变量(弧压 和弧流), 在满足一定约束条件下,使得输入到钢包炉内的电弧功 率满足工艺要求。考虑生产节奏、钢水温度和冶炼工艺的
要求,在满足这些非线性、时变的约束 条件下,寻求最优功率设定点。
• 以往功率设定点仅根据静态的电气圆
图,制订出各种电压档下的功率曲线, 由操作工根据自己的经验选取。这种 静态分析假设电气线路电阻、电抗不 变和三相独立,由于冶炼工艺过程的 复杂性,随机干扰因素多,三相电气 变量间耦合严重,这种假设并不成立。