干膜蚀刻不良特征图片f
干膜常见问题改善

1、显影后铜面上留残渣:原因分析处理方法1:显影不足*按资料确定显影的参数2:显影后曝于白光*有干膜的基板应在黄色照明下操作、目检及修补3:重氮底片上暗区之遮光不够*检查重氮片上暗区遮光密度,线路边缘之清晰度,一旦不足时则更换重氮底片4:板边已曝光之干膜崩落显影液中再附在板面上*在板面最外缘处加未曝光之边,使在显影时能洗掉而露铜且又可当成辅助阳极用5:显影后水洗不足*检查喷嘴有否被堵,并维持最低的水压12PSI*加强水冲洗6:显影液喷嘴被堵*要定时检查显影系统喷嘴情形7:图像上有修板液或污物*修板时戴纱手套,并注意不要使修板液污染线路图像8:压膜温度太高*检查压膜压辘温度,按资料调整9:显影液太旧*按资料确定更换太旧的显影液10:显影液缸及水缸被污染*定期保养显影液缸及水缸11:磨板磨辘号数不对,磨痕太深*磨板磨辘号数一般选用320~600号12:压膜至显影之间停放时间太长*不要超过24小时2、干膜起皱原因对策1:两热压辊轴向不平行,使干膜受压不均匀调整两个热压辊,使之轴向平行2:干膜太粘熟练操作,放板时多加小心3:贴膜温度太高调整贴膜温度至正常范围内4:贴膜前板太热板预热温度不宜太高3、盖孔效果不良原因对策1:通孔孔口周围有毛头,致使压膜不良*钻孔检查是否毛头太多,加强去毛头*镀铜液中固体粒子太多,加强过滤2:压膜温度较高,压膜压力太大*按资料确定压膜温度和压膜压力3:压膜时通孔中有水汽*压膜前板子要加强吹干赶走水汽4:干膜厚度不够*增加干膜厚度5:重氮底片上明区有缺点附着,如:缺口、毛头、污点、垃圾等等*检查及修补,太差时则更换重氮底片6:曝光台上有缺点附着,如:缺口、污点、垃圾等等*检查及加强清洁曝光台7:曝光能量偏低*按资料确定曝光能量8:显影过度*按资料确定的参数9:显影喷嘴压力太大*按资料确定显影的药水压力大小及水洗压力大小10:曝光前保护膜(Mylar)被撕起或曝光后保护膜(Mylar)被过早撕起*避免保护膜(Mylar)被撕起现象4、线路变幼或曝光区干膜显影时不易冲洗掉原因对策1:曝光过度*用21格曝光尺按资料正确曝光2:重氮底片上暗区之遮光不够*检查重氮底片上暗区遮光密度,线路边缘之清晰度,一旦不足时则更换重氮底片3:曝光前抽真空程度不够*检查曝光前抽真空度及碓定抽真空时间*换掉曝光上台不良的聚酯膜4:压膜之板面显影前曝露于白色光源*检查黄光室具有UV之白光情况5:压膜温度过高*按资料控制压膜温度6:显影不足,残膜冲洗不净*按资料确定显影点*更换太旧的显影液*加强水冲洗7:曝光时重氮底片药膜面与板上干膜面没有紧密结合*加强擦气及用导气条帮助抽真空或在重氮底片上明区位打出孔*检查重氮底片药膜面暗区及板上干膜面有无垃圾等杂物5、显影后干膜受损或发现干膜浮起或线路边缘不齐原因对策1:曝光不足*用21格曝光尺按资料正确曝光2:显影过度*按资料确定显影的参数3:曝光后放置时间不够*通常在撕开保护膜(Mylar)前至少放置要15分钟以上再显影4:显影药液温度太高*按资料设定正确显影温度5:压膜之前铜面处理不良*水膜测试大于15秒以上*保证磨痕宽度6:压膜温度不足,压膜压力不够*注意压膜速度及压膜温度、压膜压力7:显影喷嘴压力太大*按资料确定显影的药水压力大小及水洗压力大小6、线路镀锡铅时发现干膜边缘浮起而造成渗镀现象原因对策1:干膜性能不良,超过有效期使用*尽量在有效期内使用干膜2:压膜之前铜面处理不良*加强压膜前铜面处理控制*水膜测试大于15秒以上*保证磨痕宽度3:压膜参数条件不对*按资料确定压膜参数条件4:曝光不足*用21格曝光尺按资料正确曝光5:显影过度*按资料确定显影的参数6:电镀前处理药品及参数条件不对*按供应商资料确定参数条件7:电镀时电流密度过大*调整电镀层均匀性降低电流密度8:曝光前保护膜(Mylar)被撕起或曝光后保护膜(Mylar)被过早撕起*避免保护膜(Mylar)被撕起现象9:电镀液太陈旧或电镀液里有机杂质太多*对电镀液进行活性炭处理7、铜与铜之间附着力不良原因对策1:线路镀铜前处理及清洗不当*按供应商资料确定控制除油、微蚀、水洗2:压膜至显影之间停放时间太长*停放时间太长时,适当应加强微蚀处理使铜面撤底活化3:显影不足,暗区留有残渣*按资料确定显影的参数*更换太旧的显影液4:水冲洗不足*加强水冲洗8、板面电镀区发生跳镀(Skip Plating)或称漏镀现象原因对策1:在待镀区之裸铜面上留有干膜残渣或显影液中的干膜碎片又打回板面而重新附着*可能是棕片上有刮伤、缺口、应加修补*减少或避免干膜碎的产生2:在待镀区未曝光处显影不足,未撤底除尽残膜*按资料确定显影的参数*更换太旧的显影液3:电镀时板面受污染等问题*避免板面受污染,加强前处理工作4:电镀锡层较粗糙或剥膜工艺有问题*电镀锡不均匀,电流密度较大处较粗糙*电镀锡板放置于有污染环境处时间太长*剥膜药水浓度或温度太高或时间太长9、剥膜后发现铜面上尚留有残渣原因对策1:剥膜时间不足够*调整剥膜时间,但不宜过长2:电镀层厚度超过干膜厚度而发生夹膜现象*调整电镀层均匀性或用厚度较厚干膜(如2mil的干膜)3:电镀层厚,线路较幼剥膜较难*可以适当在剥膜药水中加定量3%丁基卡必醇4:剥膜液不良,剥膜液温度低,剥膜药液太旧*一般使用2~5%的苛性钾或钠的水溶液在50℃±2℃内操作,或更换新液5:已剥落的膜碎片又再附著上*加强冲洗的时间、压力及温度控制,加强过滤及溢流积渣,缩短剥膜及水洗间距及时间,要立即冲洗6:剥膜前已显影板曝露于白光中时间太长或显影后不当烘烤*板面各处被白光不均匀曝光延长剥膜时间*延长剥膜时间,取消烘烤10、电镀时干膜脱落原因对策1:前处理药水之温度太高或时间太长*按供应商资料确定参数条件2:曝光前保护膜(Mylar)被撕起或曝光后保护膜(Mylar)被过早撕起*避免保护膜(Mylar)被撕起现象3:显影后停置时间过长及放置环境不当*应放置有温度及湿度控制黄光环境中4:压膜之前铜面处理不良*水膜测试大于15秒以上*保证磨痕宽度5:电镀液太陈旧或电镀液里有机杂质太多*对电镀液进行活性炭处理11、线路镀金发现干膜边缘浮起而造成渗镀现象原因对策1:压膜之前铜面处理不良*加强压膜前铜面处理控制*水膜测试大于15秒以上*保证磨痕宽度2:压膜参数条件不对*按资料确定压膜参数条件3:曝光不足*用21格曝光尺按资料正确曝光4:显影过度*按资料确定显影的参数5:电镀前处理药品及参数条件不对*按供应商资料确定参数条件6:电镀时电流密度过大*调整电镀层均匀性降低电流密度7:电镀金缸药水参数条件不对*调整电镀金药水含金量,调整电镀层均匀性降低电流密度12蚀刻时干膜破坏及浮起原因对策1:压膜前铜面处理不良*加强压膜之前铜面处理控制*水膜测试大于15秒以上*保证磨痕宽度2:曝光不足,但不宜过足*用21格曝光尺按资料正确曝光3:蚀刻液PH太高,温度太高,喷嘴压力太大*做适当调整4:水洗喷嘴压力太大*降低喷嘴压力5:显影后停置时间过长及放置环境不当*应放置有温度及湿度控制的黄光环境中6:显影后停置白光区时间过长干膜变脆*避免放置于白光下1。
PCB孔壁异常照片合集

反回蚀 2
反回蚀造成之孔破
反回蚀&胶渣
异物造成之铜瘤 1
孔塞 1
孔塞 2
孔塞所造成之孔破
气泡造成之对称性孔破 1
气泡造成之对称性孔破 2
气泡造成之对称性孔破 3
孔内气泡影响药液灌孔而发生之点状孔破
孔破 1
孔破 2
孔破 3
黑孔碳膜附着不良而引发之孔破 1
黑孔碳膜附着不良而引发之孔破 2
孔破-蚀刻液攻击(or镀锡气泡孔破)
孔破-蚀刻液攻击1
孔破-蚀刻液攻击2
钉头 1
多次重工后造成严重反回蚀而导致钉头处孔破
基板于镀铜时跑出阴极遮板外造成单边镀铜厚度不足
Crack 1
Crack 2
Hale Waihona Puke Smear 1Smear 2
Smear 3
wedge 1
wedge 2
反回蚀 1
孔破-干膜退洗不良 1
孔破-干膜退洗不良 2
未去胶渣前之SEM照片 1
未去胶渣前之SEM照片 2
正常线速去胶渣后之情形 1
正常线速去胶渣后之情形 2
正常线速去胶渣后之情形 3
胶片爆裂(爆板) 1
胶片爆裂(爆板) 2
楔形破口(Wedge void)及胶渣
轻微膜浮离产生之包镀现象
爆板 2
爆板 1
钻孔不良导致孔壁粗糙
铜颗粒 1
铜颗粒 2
干膜常见问题

干膜常见问题及措施1:贴膜不牢:A:板子前处理效果不好,是否干净、铜面粗糙度、是否被氧化?做水破试验验证;>15sB:注意查看贴膜温度是否太低、压力太小和速度太快; 1102:干膜与基板铜之间有气泡:A:贴膜温度过高,干膜抗蚀剂中的成分挥发,残留在膜和铜板之间形成气泡;B:热压辊表面不平,有凹痕或划伤;热压辊压力太小;C:板面不平,有划痕或凹坑;3:干膜起皱:A:贴膜温度太高,调整到正常范围内;B:两个热压辊轴向不平行,干膜受压不均;C:干膜太粘;贴膜前板子太热,调整板子预热温度;4:有余胶:A:干膜质量差(分子量太高或涂覆干膜过程中偶然热聚合等)B:干膜暴露在白光下部分聚合,操作应在黄光下进行;C:曝光时间过长,缩短曝光时间;D:生产底版最大光密度不够,造成紫外光透过部分聚合,曝光前应检查生产底版;E:曝光时生产底版和基板接触,不检查抽真空系统及曝光框架,曝光不良造成虚光;F:显影液温度太低,显影时间太短,喷淋压力不够或部分喷嘴堵塞;G:显影液中产生大量气泡,降低了喷淋压力,应该加消泡剂消除泡沫;F:显影液失效;5:显影后干膜图像模糊,抗蚀剂发暗发毛:A:曝光不足,用光密度尺校正曝光时间和能量;B:生产底版最小光密度太大,使紫外光受阻,生产前应检查生产底版;C:显影液温度过高或显影时间太长;6:图形镀铜与基体铜结合不牢或图像有缺陷:A:显影不彻底有余胶,加强显影并加强显影后清洗;B:图像上有修板液或者污物,修板时戴细砂手套,注意不要使修板液污染线路图像;C:化学镀铜前板面不清洁或粗化不够;粗化后清洗不干净;7:镀铜或镀锡铅有渗镀:A:干膜性能不良B:基板表面清洗不干净或粗化表面不良,干膜粘附不牢,加强板面处理;C:贴膜温度低,传送速度快,干膜贴的不牢;D:曝光过度导致抗蚀剂发脆,用光密度尺校正曝光时间和曝光能量;E:曝光不足或显影过度造成抗蚀剂发毛,边缘起翘,校正曝光量,调整显影温度和速度;F:电镀前处理液温度过高;8:显影后铜面上留有残渣:A:显影不足,确定正确的显影参数;B:显影后爆于白光下,显影后应该在黄光下操作;C:重氮底片上暗区之遮光不够,检查重氮区上的遮光密度,线路边缘之清晰度,一旦不足时则更换重氮底片;D:板边已曝光,干膜崩落显影液中再附在板面上,在板面最外缘处加未曝光之边,使在显影时能洗掉而露铜且又可当成辅助阳极用;E:显影后水洗不足,检查喷嘴是否被堵,并维持最低的水压12PSI,加强水冲洗;F:显影液喷嘴被堵,定时检查显影系统喷嘴状况;G:图像上有修板液或污物,修板时戴纱手套,注意不要让修板液污染线路图像;H:压膜温度太高,检查压膜压辊温度;I:显影液太旧没有及时更换;J:显影液缸及水缸被污染,及时保养显影液缸和水缸;K:磨痕太深,磨板磨棍号数不对,一般选用320--600号;L:压膜后停放时间太长,不超过24小时要显影;9:盖孔效果不良:A:通孔孔口周围有毛头,导致压膜不良;钻孔时候检查是否毛头太多,加强去毛头;镀铜液中固体粒子太多,加强过滤;B:压膜温度过高,压力过大;C:压膜时通孔中有水汽;压膜前板子要加强吹干赶走水汽;D:干膜厚度不够,增加干膜厚度;E: 重氮底片上明区有缺点附着,如:缺口、毛头、污点、垃圾等,检查及修补重氮底片,太差时则更换重氮底片;F:曝光台上有缺点附着,如:缺口、污点、垃圾等;检查及清洁曝光台;G:曝光能量偏低;H:显影过度;I:显影喷嘴压力太大,按资料确定的显影药水压力大小及水洗压力大小;J:曝光前保护膜被撕起或曝光后保护膜被过早撕起;10:线路变幼或曝光区干膜显影时不易冲洗掉:A:曝光过度,B: 压膜温度过高;C:重氮底片上暗区遮光不够,检查暗区遮光密度和线路边缘清晰度;D:曝光前抽真空度不够;E:压膜之板面在显影前暴露于白光之下,检查是否都是黄光;F:显影不足,残膜冲洗不尽;按资料确定显影点,检查显影液是否需要更换,加强水冲洗;G:曝光时重氮底片药膜面与板上干膜面没有紧密结合;加强擦气及用导气条帮助抽真空或在重氮底片上明区位打出孔,检查重氮底片药膜面暗区与板上干膜面是否有垃圾;11:显影后干膜受损或发现干膜浮起或线路边缘不齐:A:曝光不足;B:显影过度;C:曝光后放置时间不够,要达到15分钟;D:显影药液温度太高;E:压膜前铜板前处理不良,检查磨痕宽度和水痕测试大于15秒;F:压膜温度不足,压力不够;G:显影喷嘴压力太大,按照资料确定显影药水压力大小及水洗压力大小;12:线路镀锡铅时发现干膜边缘浮起而造成渗镀现象:A:干膜性能不良超过有效期B:前处理不良,磨痕宽度及水破试验;C:压膜参数条件不对;D:曝光不足;E:显影过度;F:电镀前处理药品及参数条件不对;G:电镀时电流密度过大;调整电镀层均匀性降低电流密度;H:曝光前干膜的保护膜被撕起或曝光后保护膜被过早撕起;I:电镀液太陈旧或电镀液里有机杂质太多;对电镀液进行活性炭处理;13:铜与干膜之间附着力不良:A:线路镀铜前处理及清洗不当;控制除油、微蚀及水洗;B:压膜至显影之间停放时间太长,不超过24小时,如必须较长时间停放,应适当加强微蚀处理使铜面彻底活化;C:显影不足,暗区留有残渣;按资料确定显影参数,更换使用太久的显影液;D:水冲洗不足;加强水冲洗;14:板面电镀区发生跳镀(也称漏镀)现象:A:在待镀区之裸铜面上留有干膜残渣或显影液中干膜碎片又打回板面而重新附着;可能是棕片上有刮伤和缺口,应修补;减少或避免干膜碎片的产生;B:在待镀区未曝光处显影不足,未彻底除尽残膜;按资料确定显影参数,更换太久的显影液;C:电镀时板面受污染;加强前处理避免污染;D:电镀锡层较粗糙或剥膜工艺有问题;电镀锡不均匀,电流密度较大处较粗糙;电镀锡板放置于有污染环境处时间太长;剥膜药水浓度、温度太高或时间太长;15:剥膜后发现铜面上有残渣:A:剥膜时间不够;调整剥膜时间但不宜过长;B:电镀层厚度超过干膜厚度而发生夹膜现象;调整电镀层均匀性或使用厚度较厚的干膜(如2mil);C:电镀层厚,线路较幼剥膜较难;可以适当的在剥膜药水中加定量3%的丁基卡必醇;D:剥膜液不良,剥膜液温度低,剥膜药液太旧;一般使用2%--5%的苛性钾或纳的水溶液在48--52度内操作,或更换新液;E:已剥落的膜碎片又再附着上;加强冲洗时间、压力及温度的控制,加强过滤及溢流积渣,缩短剥膜及水洗间距及时间,要立即冲洗;F:剥膜前已显影板暴露于白光中时间太长或显影后不当烘烤;板面各处被白光不均匀曝光;延长剥膜时间,取消烘烤;16:电镀时干膜脱落:A:前处理药水温度太高或时间太长;B:曝光前干膜的保护膜被撕起或曝光后保护膜被过早撕起;C:显影后停置时间过长及放置环境不当;应该放置于温度及适度正常的黄光环境下;D: 压膜之前铜面处理不良;保证磨痕的宽度,水破试验大于15秒;E:电镀液太陈旧或电镀液里有机杂志太多;对电镀液进行活性炭处理;17:线路镀金发现干膜边缘浮起而造成渗镀现象:A:压膜之前铜面处理不良;注意磨痕和水破测试;B:压膜工艺参数不对;注意压力、温度及速度;C:曝光不足;D:显影过度;E:电镀前处理药品及参数条件不对;按照供应商资料调整;F:电镀时电流密度过大;调整电镀层均匀性降低电流密度;G:电镀金缸药水参数条件不对;调整电镀金药水含金量,调整电镀层均匀性降低电流密度;18:蚀刻时干膜破坏及浮起:A:压膜之前铜面处理不良;注意磨痕和水破测试;B:曝光不足;注意测试曝光尺;蚀刻液PH太高、温度太高,喷嘴压力太大;做适当调整;D:水洗喷嘴压力太大;降低喷嘴压力; 显影后停置时间过长及放置环境不当,放置在白光下时间过长会使干膜变脆;应该在适合的温度、湿度及黄光条件下放置; *一,印制线路板加工中干膜掩孔出现破孔很多客户认为,出现破孔后,应当加大线路板生产贴膜温度和压力,以增强其结合力,其实这种观点是不正确的,因为温度和压力过高后,抗蚀层的溶剂过度挥发,使干膜变脆变薄,显影时极易被冲破孔,我们始终要保持干膜的韧性,所以,出现破孔后,我们可以从以下几点做改善:1,印制线路板加工中降低贴膜温度及压力2,印制线路板加工中改善钻孔披锋3,印制线路板加工中提高曝光能量4,印制线路板加工中降低显影压力5,印制线路板加工中贴膜后停放时间不能太长,以免导致拐角部位半流体状的药膜在压力的作用下扩散变薄6,印制线路板加工中贴膜过程中干膜不要张得太紧二,PCB打板中干膜电镀时出现渗镀之所以渗镀,说明干膜与覆铜箔板粘结不牢,使镀液深入,而造成“负相”部分镀层变厚,多数PCB快板厂家发生渗镀都是由以下几点造成:1,印制线路板加工中曝光能量偏高或偏低在紫外光照射下,吸收了光能量的光引发剂分解成游离基引发单体进行光聚合反应,形成不溶于稀碱的溶液的体型分子。
干法刻蚀制程工艺及相关缺陷的分析和改善

第I页
附着于装载腔室。从而进一步通过更改使用的工艺气体解决了 “冒烟”问题。
(2)对于刻蚀残留问题的解决对策是: 1.使用 DUMMY CLEAN RECEIPE 对腔室进行清扫,通过对比观察, 找出最合理的清扫间隔; 2.选定相关的工艺设备,调整 RF 的输出功率,通过对比,得出 比较合理的 RF 功率。 本文的实验结果及结论已经在干法刻蚀制程中得以应用。 关键词:面板,阵列,干刻,等离子体,排气速度
本文首先总体介绍了液晶显示的发展和现状,液晶显示器的制成 流程,侧重讲述了阵列(array)的制作工艺流程和工艺设备,然后 对干法刻蚀中的工艺设备进行详细说明。基于节约空间和提高效率的 考虑,行业内对于金属层的刻蚀普遍采用干法刻蚀的方式,但生产节 拍的加快,缺陷也随之而来。干法刻蚀中影响产品品质的主要因素为: 杂质颗粒、RF 电源、排气速度和真空度,其中生产节拍的加快对前 两因素的影响最为重大。在上海广电 NEC 工厂的 15-26 英寸工艺设备 进行实验并取得数据,绘制成趋势图,通过各种方法的结果的比对, 找出了干法刻蚀的最佳条件,重点针对干法刻蚀设备中的工艺缺陷进 行分析和跟踪,找出相关的对策,解决了生产中遇到的实际问题:
申请上海交通大学工程硕士专业学位论文
干法刻蚀制程工艺及相关缺陷的分析和改善
学 校:上海交通大学 院 系:电子信息与电子工程学院 工程硕士生:张新言 工程领域:平板显示 导 师Ⅰ:李荣玉(副教授) 导 师Ⅱ:陈勤达(高级工程师)
上海交通大学电子信息与电气工程学院 2009 年 9 月
A Dissertation Submitted to Shanghai Jiao Tong University for Master Degree of Engineering
干膜缺陷原因分析与预防措施
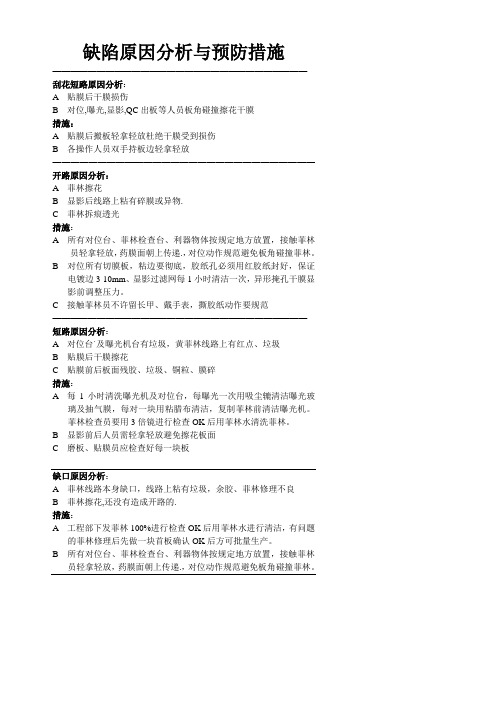
缺陷原因分析与预防措施—————————————————————————————刮花短路原因分析:A 贴膜后干膜损伤B 对位,曝光,显影,QC出板等人员板角碰撞擦花干膜措施:A 贴膜后搬板轻拿轻放杜绝干膜受到损伤B 各操作人员双手持板边轻拿轻放—————————————————————————————开路原因分析:A 菲林擦花B 显影后线路上粘有碎膜或异物.C 菲林拆痕透光措施:A 所有对位台、菲林检查台、利器物体按规定地方放置,接触菲林员轻拿轻放,药膜面朝上传递.,对位动作规范避免板角碰撞菲林。
B 对位所有切膜板,粘边要彻底,胶纸孔必须用红胶纸封好,保证电镀边3-10mm、显影过滤网每1小时清洁一次,异形掩孔干膜显影前调整压力。
C 接触菲林员不许留长甲、戴手表,撕胶纸动作要规范—————————————————————————————短路原因分析:A 对位台`及曝光机台有垃圾,黄菲林线路上有红点、垃圾B 贴膜后干膜擦花C 贴膜前后板面残胶、垃圾、铜粒、膜碎措施:A 每1小时清洗曝光机及对位台,每曝光一次用吸尘辘清洁曝光玻璃及抽气膜,每对一块用粘腊布清洁,复制菲林前清洁曝光机。
菲林检查员要用3倍镜进行检查OK后用菲林水清洗菲林。
B 显影前后人员需轻拿轻放避免擦花板面C 磨板、贴膜员应检查好每一块板缺口原因分析:A 菲林线路本身缺口,线路上粘有垃圾,余胶、菲林修理不良B 菲林擦花,还没有造成开路的.措施:A 工程部下发菲林100%进行检查OK后用菲林水进行清洁,有问题的菲林修理后先做一块首板确认OK后方可批量生产。
B 所有对位台、菲林检查台、利器物体按规定地方放置,接触菲林员轻拿轻放,药膜面朝上传递.,对位动作规范避免板角碰撞菲林。
残铜超标原因分析:A 板面凹坑、干膜与板面结合不紧、显影后分离、被镀上金属B 曝光机上及菲林透光处有垃圾,已曝光部位干膜区域露铜被镀上金属C 图形电镀之前干膜擦花被镀上金属,原非铜区域残留下铜皮措施:A 磨板前及贴膜前认真检查板面质量,重点检查凹坑及凸起铜粒及时处理打磨或标识。
PCB常见缺陷图片汇总1

接 不允许,需用油墨修补,补油
露铜
受 固化后不应有明显色差。
标
准
阻焊(SM)不良图片汇总
阻焊偏位
阻焊偏位
问 焊盘、孔环上有阻焊膜。 题 描 述
接 1、阻焊上独立方形焊盘浸入
受 长度5%或0.05MM允收;
外层干膜(ODF)不良图片汇总
问 残铜。
题
残铜
描
述
接 1、不影响线宽线距; 受 2、大铜面残铜允许1.0mm 标 且不可露铜,面积在 准 9平方公分内只允许1个。
外层干膜(ODF)不良图片汇总
磨坏板
问 磨板过程中卡板,磨坏板。 题 描 述
接 不接受。 受 标 准
外层干膜(ODF)不良图片汇总
显影不 净
问 曝光过程中有小膜碎或其
题 它异物附着在焊盘上导致
描 缺口。
缺口
述
接 1、IC、BGA、金手指 受 位不允许缺口; 标 2、方形、圆形焊盘中间 准 不允许缺口,周围允许5
%。
外层干膜(ODF)不良图片汇总
露基材
问 露基材。 题 描 述
接 1、IC位不允许缺口; 受 2、方形、圆形焊盘中间 标 不允许缺口,周围允许5 准 %。
外层干膜(ODF)不良图片汇总
蚀刻不 净
问 蚀刻不净。 题 描 述
接 符合MI规定的线宽间距要 受 求。 标 准
外层干膜(ODF)不良图片汇总
问 人为操作问题导致擦伤菲 题 林,擦伤。 描 述
擦伤
接 不接收。 受 标 准
外层干膜(ODF)不良图片汇总
问 蚀刻速度过慢,温度过高, 题 药水浓度过高导致线幼。 描 述
开料(CUT)不良图片汇总
问 1、操作不当或设备问题 题 导致尖锐物体撞到板面 描 使基铜脱落。 板边25.4mm范围
曝光蚀刻不良现象及对策

Control panel 指示计 比重实测确认 Control Panel 指示计 浓度实测确认 2.8± 0.2 mol/l Control Panel 指示计 铜范围设定구리값 범위 설정
5
140
比重实测 确认 日常点检 Sheet记录
5
140
浓度实测确认 日常点检 Sheet记录
5
90
日常点检 Sheet记录
低
INPUTS
F.M
EFFECT
S E V
CAUSE
O C C
Current Controls
D E T
R P N
对策
蚀刻药液 温度
高 低 高
线路宽减少 3 未蚀刻 Foot 发生 7 线路宽减少 线路宽减少 7 未蚀刻 线路宽减少 6 未蚀刻, Foot 发生 未蚀刻, Foot 发生 8 线路宽减少 未蚀刻, FOOT发生 线路宽减少 铜变色 发生 Migration 发生性 上升
CAUSE(原因 原因) 原因
O C C
Current Controls
D E T
R P N
对策
高 曝光量 低
Foot Short 发生 7 线路宽减少 刺状蚀刻 线路宽减少 7 Foot 发生 未蚀刻 线路宽减少 7 Foot 发生 未蚀刻 线路宽减少 8 Foot 发生 未蚀刻 Foot 发生 未蚀刻 9 线路宽减少
OPEN, 损伤
7
3
D/F coating后 roll按压
5
105
调准roll 水平
SHORT
5
3
肉眼确认
3
45
Coating 前 roll清扫
Particle 数
干膜蚀刻不良特征图片f
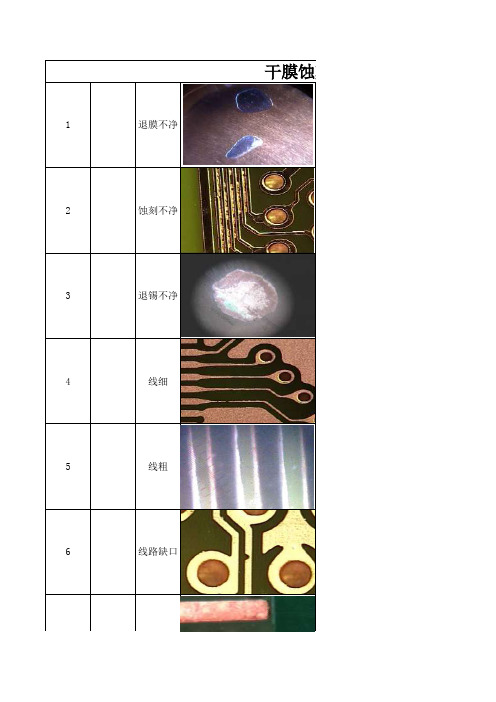
干膜蚀刻不1退膜不净2蚀刻不净退锡不净34线细5线粗6线路缺口7针孔78铜面污染针孔9线路锯齿1011干膜划伤短路线路划伤13焊前刮伤12膜碎返粘14干膜孔破15间距不足16蚀刻过度17焊盘残缺18线路残铜蚀刻不良特征分布1、喷嘴堵塞2、压力小3、药水浓度低4、速度快5、温度低1、清理喷嘴 2、检查调整压力 3、化验调整药水浓度 4、做退膜点确定调整速度 5、检测温度调整1、喷嘴堵塞2、压力小3、药水要求不在范围(比重)4、速度快5、温度低1、清理喷嘴 2、检查调整压力 3、化验调整药水比重 4、做退锡点(或首件)确定调整速度 5、检测温度调整1、喷嘴堵塞2、压力小3、药水要求不在范围(比重铜含量、氯离子、PH值)4、速度快5、温度低1、清理喷嘴 2、检查调整压力 3、化验调整药水浓度(比重铜含量、氯离子、PH值) 4、做蚀刻点(或首件)确定调整速度 5、检测温度调整1、压力大2、药水要求不在范围(比重铜含量、氯离子、PH值)3、速度慢4、温度高5、曝光不良1、、检查调整压力 2、化验调整药水浓度(比重铜含量、氯离子、PH 值) 3、做蚀刻点(或首件)确定调整速度 4、检测温度调整 5、制作曝光尺调整曝光能量1、喷嘴堵塞2、压力小3、药水要求不在范围(比重铜含量、氯离子、PH值)4、速度快5、温度低6、曝光不良1、清理喷嘴 2、检查调整压力 3、化验调整药水浓度(比重铜含量、氯离子、PH值) 4、做蚀刻点(或首件)确定调整速度 5、检测温度调整6、制作曝光尺调整曝光能量1、板面粘附异物显影不净2、显影膜碎反粘1、前处理、压膜按时保养清洁2、显影机按时保养清洁、使用合适匹配干膜压膜1、板面粘附异物显影不净2、显影膜碎反粘3、电镀不良1、前处理、压膜按时保养清洁2、显影机按时保养清洁、使用合适匹配干膜压膜3、检查电镀各项参数1、板面粘附异物显影不净2、显影膜碎反粘3、电镀不良1、前处理、压膜按时保养清洁2、显影机按时保养清洁、使用合适匹配干膜压膜3、检查电镀各项参数1、板面粘附异物显影不净2、显影后清洗不净1、前处理、压膜按时保养清洁2、显影机按时保养清洁3、转运放板工具按时清洁1、人员操作取拿搬运划伤线路2、工具不良造成划伤线路1、要求轻拿轻放,搬运不可拖拉、丢摔板 2、及时处理工具1、退膜温度高、速度慢2、退膜浓度高3、蚀刻温度高4、药水要求不在范围(比重铜含量、氯离子、PH 值)5、显影过度1、检测温度、调整速度 2、化验分析药水调整药水 3、检测温度调整4、化验调整药水浓度(比重铜含量、氯离子、PH值) 5、制作显影点调整速度1、人员操作取拿搬运划伤线路2、工具不良造成划伤线路1、要求轻拿轻放,搬运不可拖拉、丢摔板 2、及时处理工具1、喷嘴堵塞2、压力小3、药水浓度低4、速度快5、温度低6、水洗不净1、清理喷嘴 2、检查调整压力 3、化验调整药水浓度 4、做退膜点确定调整速度 5、检测温度调整 6、清洗更换水洗1、人员操作取拿搬运划伤线路2、工具不良造成划伤线路1、要求轻拿轻放,搬运不可拖拉、丢摔板 2、及时处理工具对位偏温湿度、更改底片 3、使用放大镜检查1、钻孔偏2、底片涨缩3、人员对位偏1、测量校正钻孔精度 2、管控调整温湿度、更改底片 3、使用放大镜检查1、喷嘴堵塞2、压力小3、药水要求不在范围(比重铜含量、氯离子、PH值)4、速度快5、温度低6、曝光不良1、清理喷嘴 2、检查调整压力 3、化验调整药水浓度(比重铜含量、氯离子、PH值) 4、做蚀刻点(或首件)确定调整速度 5、检测温度调整6、制作曝光尺调整曝光能量1、喷嘴堵塞2、压力小3、药水浓度低4、速度快5、温度低6、水洗不净1、清理喷嘴2、检查调整压力3、化验调整药水浓度4、做退膜点确定调整速度5、检测温度调整6、清洗更换水洗1、清理喷嘴2、检查调整压力3、化验调整药水浓度(比重铜含量、氯离子、PH值)4、做蚀刻点(或首件)确定调整速度5、检测温度调整6、制作曝光尺调整曝光能量7、调整退膜各项参数1、压力大2、药水要求不在范围(比重铜含量、氯离子、PH值)3、速度慢4、温度高5、曝光不良1、喷嘴堵塞 2、压力小 3、药水要求不在范围(比重铜含量、氯离子、PH值) 4、速度快 5、温度低6、曝光不良7、退膜不净1、、检查调整压力2、化验调整药水浓度(比重铜含量、氯离子、PH 值)3、做蚀刻点(或首件)确定调整速度4、检测温度调整5、制作曝光尺调整曝光能量。
PCB常见缺陷图片汇总1

接 不接受。 受 标 准
外层干膜(ODF)不良图片汇总
问 曝光垃圾导致开路。 题 描 述
开路
接 不接受。 受 标 准
外层干膜(ODF)不良图片汇总
问 曝光过程中有小膜碎或其
题 它异物附着在焊盘上导致
描 缺口。
缺口
述
接 1、IC、BGA、金手指 受 位不允许缺口; 标 2、方形、圆形焊盘中间 准 不允许缺口,周围允许5
原 因
3、蚀刻参数不对。
改 1、调整蚀刻均匀性;
善 2、疏通喷嘴;
措 施
3、调整蚀刻参数。
内层干膜(IDF)不良图片汇总
问 内层开路。 题 描 述
接 不允许。 受 标 准
层压(ML)不良图片汇总
基材白 点
问 基材白点。 题 描 述
接 除用于高压区以外,基材 受 白点对所有产品来说都是 标 可以接受。 准
钻孔(DR)不良图片汇总
二钻偏位
问 定位不理想,定位孔大于 题 销钉导致二钻孔偏离了了 描 图形。 述
接 不接受。 受 标 准
沉铜(PTH)不良图片汇总
铜皮起泡
问 电镀铜有起泡 。 题 描 述
接 不接受。 受 标 准
沉铜(PTH)不良图片汇总
问 铜缸药水污染,外部环境 题 灰尘进入铜缸,导致板面 描 有颗粒状的铜。 述
距要求;
3、 起泡或分层跨距不大于相 邻导电图形之间距离的25%;
4、模拟的热测试没有扩大。
层压(ML)不良图片汇总
问 压板时钢板未清洁干净或 题 钢板不平导致凹痕。 描 述
接 1、在线路位置若超越修补
受 准则需报废;
凹痕
标 2、在大铜面上缺陷长度
准 <7mm及每一单元不超一
干膜介绍及干膜工艺详解(40页)

COOH COOH
COOH COOH
COOH
COOH COOH
COOH
去膜
N a O H /H 2O
COOH COOH
COOH
C
O
O- N
a+
C O O- N a+
C O O- N a+
C O O H- N a+
C
O
O- N
a+
C
O
O- N
a+
C
O
O- N
a+
C
O
O- N
a+
C O O- N a+
C
曝光后静置时间:15min~24H
工序注意事项
• 曝曝光光能量均匀性≥90%;
每4H测定曝光能量; 抽真空时间不能太短,防止曝光不良; 曝光台面温度太高会造成底片变形; 板面、底片或曝光台面不能有脏点; 干膜、底片小心操作,防止划伤; 曝光机空气过滤芯定期清洁或更换。
SES工艺流程详显细影介:绍
曝光: 曝光的作用是曝光机的紫外线通过底片使干膜 上部分图形感光,从而使图形转移到铜面上。
底片 干膜 Cu
基材
SES工艺流程详细介绍
曝光反应机理
COOH COOH
单体 聚合体主链
起始剂
COOH COOH
COOH
COOH COOH
COOH
紫外线 曝光
COOH COOH
C OOH
※
COOH
※
COOH
反应核心
显影的作用: 将未曝光部分的干膜去掉,留下感光的部分。
显影的原理: 未曝光部分的感光材料没有发生聚合反应,遇
弱碱Na2CO3(0.8-1.2%)或K2CO3溶解。而聚合的 感光材料则留在板面上,保护下面的铜面不被蚀刻 药水溶解。
PCB各制程不良分析手册

3.板弯板曲或V-CUT刀具运转不稳
不允许
77
V-CUT
过
反
1.未按进料方向放板过V-CUT
2.程式错误
不允许
78
V-CUT
伤
铜
1.V-CUT两边挡板不平行
2.板子外型有偏差
3. V-CUT间距过小
4. V-CUT刀角度偏大或刀片磨损过重
不允收
79
V-CUT
过
穿
1.调刀过深或铣刀不水平
4.显影、水洗喷压过大或显影速度过慢
不允许
61
板
面
沾
污
1.板面沾胶/沾油垢等不良物
不允许
62
干
膜
脱
落
1.干膜挈性不足,较脆
2.CU板板面杂物或巴厘过高
3.贴膜后静置时间过长或显影速度过慢
不允许
63
干
膜
沾
膜
1.棕片之暗区被刮伤
2.显影不尽或显影时残膜反沾
大铜每面不超过2个点,每点小于10mil,其它部位不允收
干
膜
站
64
线
路
突
出
1.贴膜后沾有脏点或底片上沾有脏点
2.操作刮伤干膜
不超过原稿线径的20%
65
干
膜
断
路
1.底片之暗区被刮伤
2.显影不尽或显影时残膜反沾
不允许
66
干
膜
短
路
1.棕片上沾有点状杂物或贴膜前板面沾点状油污
2.贴膜或曝光后因人为操作不当将铜面干膜刮伤
不允许
67
干
膜
对
偏
1.干膜站对底片时未保证孔环之ring各方向宽度相等(前提为孔正),
蚀刻污分析图解
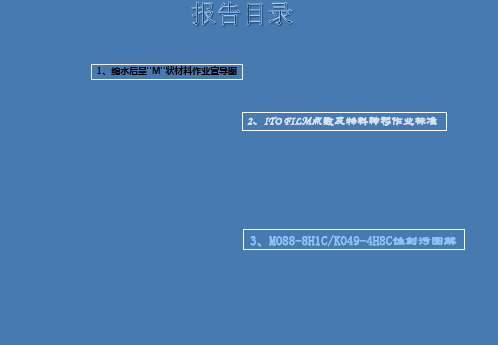
ቤተ መጻሕፍቲ ባይዱ
2、ITO FILM点数及物料转移作业标准
3、MO88-8H1C/KO49-4H8C蚀刻污图解
3、MO88-8H1C/KO49-4H8C蚀刻污图解
MO88-8H1C X射线能谱分析法(EDS)
MO88-8H1C光学显微镜成像
MO88-8H1C光学显微镜成像
MO88-8H1C光学显微镜成像
类别
图例
备注
蚀刻后 ITO上有 耐酸残 留
耐酸未完全与NaOH反应,ITO 表面有耐酸油墨残留,导致有 ITO区域透光时比ITO区发雾, 产生白雾不良
ITO gap UC层有 损伤产 生变化
UC层被NaOH溶液损伤,导致UC 层特性变化,产生雾状不良
THE END
3、MO88-8H1C/KO49-4H8C蚀刻污图解
KO49-4H8C电子显微镜成像
KO49-4H8C电子显微镜成像
KO49-4H8C电子显微镜成像
KO49-4H8C光学显微镜成像
KO49-4H8C光学显微镜成像
KO49-4H8C光学显微镜成像
3、MO88-8H1C/KO49-4H8C蚀刻污图解
1)不良现象在透光检查的情况下,可见与ITO 图案之间的gap区域有白雾状不良,形状与gap一样; 2)不良品使用无尘布蘸酒精或者石油醚擦拭,雾状不良不可擦拭。
ITO可视性透射检查示意图
3、MO88-8H1C/KO49-4H8C蚀刻污图解
造成白雾状不良的原因分析
导致白雾状不良主要原因可能为:白雾产生区域有残留异物或者此处的ITO被蚀刻后UC层有发生变化导致(如下图)
(整理)TFT不良定义及图解.

修订记录1、减薄不良图解序号不良名词定义/不良原因图片/实物判定缺陷分类1 表面划伤定义:玻璃基板表面被划伤。
原因:1、玻璃基板含有杂质,蚀刻后脱落成划痕。
2、玻璃在蚀刻前受到划伤,蚀刻后划痕变大且带有酸刻条纹。
3、擦拭玻璃的无尘布多次使用,会导致无尘布硬化,无尘布有胶粒或玻璃碎直接与玻璃发生摩擦导致划伤而出现划痕。
宽W(mm),长L(mm)当0.03<W≤0.05;L≤3时,允许1条;注:两条刮花间距须大于5mm。
2 表面污定义:玻璃表面受到污染。
原因:1、玻璃在蚀刻前表面受到污染,如:油脂、手指印等污物粘在玻璃表面,形成表面污。
2、玻璃表面有残留酒精痕迹(丙酮痕迹)蚀刻后形成表面污。
参照限度样品3 破裂定义:裂痕延伸进入玻璃表面。
原因:1、玻璃与硬物形成猛撞造成;2、插篮、倒边过程中,拿取玻璃不当,造成玻璃夹破;3、测玻璃厚度时,千分尺操作不符造成玻璃破裂;4、擦拭玻璃时,桌面不平整或用力不均,导致边缘缺口延伸裂入。
不可有4 角崩边崩定义:玻璃边有、角部出现崩缺。
原因:1、插篮、插箱时,与邻边玻璃碰撞,造成崩边或崩角;2、玻璃与硬物形成碰撞,造成崩边崩角。
不可进入整片玻璃的外围切割标的外边线内。
5凹凸点、白点定义:玻璃表面有小坑点或有突出的圆点。
原因:1、玻璃基板内有杂质和气泡,蚀刻后脱落形成凹点,如有化学物质,造成不反应或反应不完全时,导致不脱落,则形成凸点;2、玻璃表面的胶粒没有及时清理,蚀刻后胶粒脱落,与胶粒接触处不被蚀刻从而突出形成凸点;3、蚀刻时由于玻璃粉粘在玻璃表面没有及时清洗或清洗不到位,则形成凸点。
Φ=(长+宽)/2当0.1≤Φ≤0.2;允许1个。
当Φ≤0.1,允许多个。
注:Φ≤0.1出现2个时必须距离5mm以上。
6 酸刻条纹定义:蚀刻后玻璃表面出现凹凸不平的条状波纹。
原因:1、酸液浓度过高,速北出现不均匀情况,蚀刻完成的玻璃没及时进入QDR槽清洗,残留于玻璃表面的酸液继续蚀刻玻璃(表面会出现直线酸刻条纹);2、多次蚀刻的酸液,含有大量玻璃粉,再蚀刻时玻璃粉会依附玻璃表面,阻碍酸液蚀刻玻璃,玻璃粉若没有及时清洗掉,则会出现严重酸刻条纹,清洗不彻底会出现点状的条纹;3、蚀刻时,玻璃脱轨重叠在一起,清洗不到的玻璃面会出现条纹;4、蚀刻篮档条的凹槽深浅会有产生条纹的可能;如篮底档条直径大,抛动时引起酸液变化(速率变快),出现蚀刻不均匀导致严重条纹;5、酸液液面不能完全覆盖玻璃,蚀刻后严重的条纹。
蚀刻不良分析
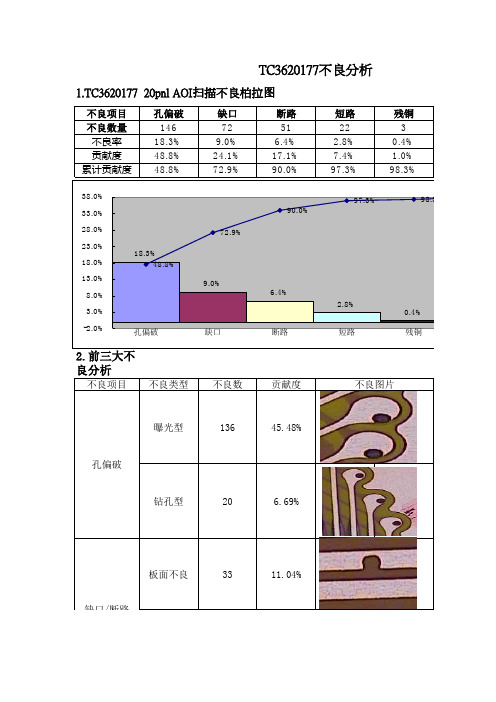
不良项目孔偏破缺口断路短路残铜不良数量1467251223不良率18.3%9.0% 6.4% 2.8%0.4%贡献度48.8%24.1%17.1%7.4% 1.0%累计贡献度48.8%72.9%90.0%97.3%98.3%2.前三大不良分析不良项目不良类型不良数贡献度曝光型13645.48%钻孔型20 6.69%板面不良3311.04%1.TC3620177 20pnl AOI 扫描不良柏拉图TC3620177不良分析缺口/断路不良图片孔偏破18.3%9.0%6.4%2.8%0.4%48.8%72.9%90.0%97.3%98.3%-2.0%3.0%8.0%13.0%18.0%23.0%28.0%33.0%38.0%孔偏破缺口断路短路残铜缺口/断路曝光型9030.10%3.小结1.此料号主要不良为:a 曝光型不良 贡献度30.1%,主要为曝光干膜上异物造成对策:压膜后曝光前用粘尘轮进行正反面清洁非曝光型不良 贡献度 11.04%主要为来料压点、折伤造成对策:前处理来料检验,并追踪前站压点产生源b 孔偏破不良 贡献度52.17% 1.此料号ring(0.135mm),作业时会有偏,板子折皱造成曝2.套PIN时未完全套下3.板子折皱造成曝光偏移对策:1.对孔破部分进行拉胶带作业,作业后使用放大镜进行检验,超过2PCS以上退洗处理业时会有偏,板子折皱造成曝光偏移。
f1f干膜工艺的质量检验
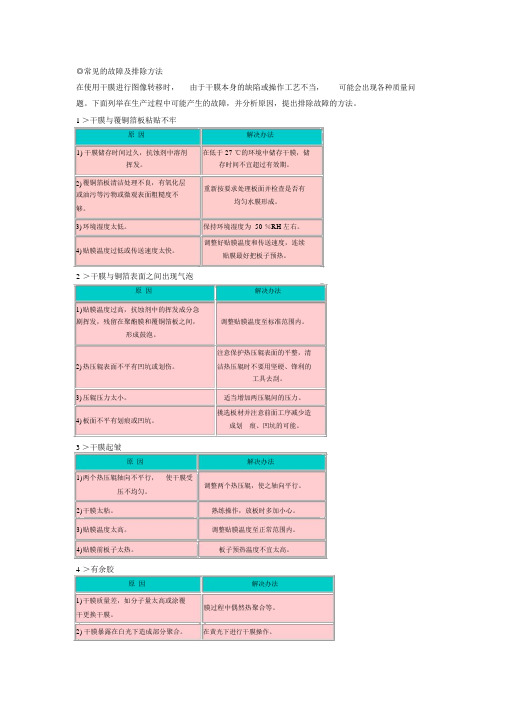
◎常见的故障及排除方法在使用干膜进行图像转移时,由于干膜本身的缺陷或操作工艺不当,可能会出现各种质量问题。
下面列举在生产过程中可能产生的故障,并分析原因,提出排除故障的方法。
1>干膜与覆铜箔板粘贴不牢原因解决办法1) 干膜储存时间过久,抗蚀剂中溶剂在低于 27 ℃的环境中储存干膜,储挥发。
存时间不宜超过有效期。
2)覆铜箔板清洁处理不良,有氧化层重新按要求处理板面并检查是否有或油污等污物或微观表面粗糙度不均匀水膜形成。
够。
3)环境湿度太低。
保持环境湿度为 50 %RH 左右。
4)贴膜温度过低或传送速度太快。
调整好贴膜温度和传送速度,连续贴膜最好把板子预热。
2 >干膜与铜箔表面之间出现气泡原因解决办法1)贴膜温度过高,抗蚀剂中的挥发成分急剧挥发,残留在聚酯膜和覆铜箔板之间,调整贴膜温度至标准范围内。
形成鼓泡。
注意保护热压辊表面的平整,清2)热压辊表面不平有凹坑或划伤。
洁热压辊时不要用坚硬、锋利的工具去刮。
3)压辊压力太小。
适当增加两压辊问的压力。
4)板面不平有划痕或凹坑。
挑选板材并注意前面工序减少造成划痕、凹坑的可能。
3>干膜起皱原因解决办法1)两个热压辊轴向不平行,使干膜受压不均匀。
调整两个热压辊,使之轴向平行。
2)干膜太粘。
熟练操作,放板时多加小心。
3)贴膜温度太高。
调整贴膜温度至正常范围内。
4)贴膜前板子太热。
板子预热温度不宜太高。
4 >有余胶原因解决办法1)干膜质量差,如分子量太高或涂覆膜过程中偶然热聚合等。
干更换干膜。
2) 干膜暴露在白光下造成部分聚合。
在黄光下进行干膜操作。
3) 曝光时间太长。
缩短曝光时间。
4)照相底版最大光密度不够,造成紫曝光前检查照相底版。
外光透过,部分聚合。
5)曝光时照相底版与基板接触不良造检查抽真空系统及曝光框架。
成虚光。
6) 显影液温度太低,显影时间太短,调整显影液温度和显影时的传送速度,喷淋压力不够或部分喷嘴堵塞。
检查显影设各7)显影液中产生大量气泡,降低了喷在显影液中加入消泡剂消除泡沫。
- 1、下载文档前请自行甄别文档内容的完整性,平台不提供额外的编辑、内容补充、找答案等附加服务。
- 2、"仅部分预览"的文档,不可在线预览部分如存在完整性等问题,可反馈申请退款(可完整预览的文档不适用该条件!)。
- 3、如文档侵犯您的权益,请联系客服反馈,我们会尽快为您处理(人工客服工作时间:9:00-18:30)。
干膜蚀刻不1退膜不净
2蚀刻不净
退锡不净
3
4线细
5线粗
6线路缺口
7针孔
7
8铜面污染
针孔
9线路锯齿10
11干膜划伤短路线路划伤
13焊前刮伤12膜碎返粘
14
干膜孔破15间距不足16蚀刻过度17
焊盘残缺18线路残铜
蚀刻不良特征分布
1、喷嘴堵塞
2、压力小
3、药水浓度低
4、速度快
5、温度低1、清理喷嘴 2、检查调整压力 3、化验调整药水浓度 4、做退膜点确定调整速度 5、检测温度调整
1、喷嘴堵塞
2、压力小
3、药水要求不在范围(比重)
4、速度快
5、温度低1、清理喷嘴 2、检查调整压力 3、化验调整药水比重 4、做退锡点(或首件)确定调整速度 5、检测温度调整
1、喷嘴堵塞
2、压力小
3、药水要求不在范围(比重铜含量、氯离子、PH值)
4、速度快
5、温度低1、清理喷嘴 2、检查调整压力 3、化验调整药水浓度(比重铜含量、氯离子、PH值) 4、做蚀刻点(或首件)确定调整速度 5、检测温度调整
1、压力大
2、药水要求不在范围(比重铜含量、氯离子、PH值)
3、速度慢
4、温度高
5、曝光不良1、、检查调整压力 2、化验调整药水浓度(比重铜含量、氯离子、PH 值) 3、做蚀刻点(或首件)确定调整速度 4、检测温度调整 5、制作曝光尺调整曝光能量
1、喷嘴堵塞
2、压力小
3、药水要求不在范围(比重铜含量、氯离子、PH值)
4、速度快
5、温度低
6、曝光不良1、清理喷嘴 2、检查调整压力 3、化验调整药水浓度(比重铜含量、氯离子、PH值) 4、做蚀刻点(或首件)确定调整速度 5、检测温度调整6、制作曝光尺调整曝光能量
1、板面粘附异物显影不净
2、显影
膜碎反粘
1、前处理、压膜按时保养清洁
2、显影机按时保养清洁、使用合适匹配
干膜压膜
1、板面粘附异物显影不净
2、显影膜碎反粘
3、电镀不良
1、前处理、压膜按时保养清洁
2、显影机按时保养清洁、使用合适匹配干膜压膜
3、检查电镀各项参数
1、板面粘附异物显影不净
2、显影膜碎反粘
3、电镀不良
1、前处理、压膜按时保养清洁
2、显影机按时保养清洁、使用合适匹配干膜压膜
3、检查电镀各项参数
1、板面粘附异物显影不净
2、显影后清洗不净
1、前处理、压膜按时保养清洁
2、显影机按时保养清洁
3、转运放板工
具按时清洁
1、人员操作取拿搬运划伤线路
2、工具不良造成划伤线路1、要求轻拿轻放,搬运不可拖拉、丢摔板 2、及时处理工具
1、退膜温度高、速度慢
2、退膜浓度高
3、蚀刻温度高
4、药水要求不在范围(比重铜含量、氯离子、PH 值)
5、显影过度1、检测温度、调整速度 2、化验分析药水调整药水 3、检测温度调整4、化验调整药水浓度(比重铜含量、氯离子、PH值) 5、制作显影点调整速度
1、人员操作取拿搬运划伤线路
2、工具不良造成划伤线路1、要求轻拿轻放,搬运不可拖拉、丢摔板 2、及时处理工具
1、喷嘴堵塞
2、压力小
3、药水浓度低
4、速度快
5、温度低
6、水洗不净1、清理喷嘴 2、检查调整压力 3、化验调整药水浓度 4、做退膜点确定调整速度 5、检测温度调整 6、清洗更换水洗
1、人员操作取拿搬运划伤线路
2、工具不良造成划伤线路1、要求轻拿轻放,搬运不可拖拉、
丢摔板 2、及时处理工具
对位偏温湿度、更改底片 3、使用放大镜检
查
1、钻孔偏
2、底片涨缩
3、人员对位偏1、测量校正钻孔精度 2、管控调整温湿度、更改底片 3、使用放大镜检
查
1、喷嘴堵塞
2、压力小
3、药水要求不在范围(比重铜含量、氯离子、PH值)
4、速度快
5、温度低
6、曝光不良1、清理喷嘴 2、检查调整压力 3、化验调整药水浓度(比重铜含量、氯离子、PH值) 4、做蚀刻点(或首件)确定调整速度 5、检测温度调整6、制作曝光尺调整曝光能量
1、喷嘴堵塞
2、压力小
3、药水浓度低
4、速度快
5、温度低
6、水
洗不净
1、清理喷嘴
2、检查调整压力
3、化验调整药水浓度
4、做退膜点确定调整速度
5、检测温度调整
6、清洗
更换水洗
1、清理喷嘴
2、检查调整压力
3、化验调整药水浓度(比重铜含量、氯离子、PH值)
4、做蚀刻点(或首件)确定调整速度
5、检测温度调整
6、制作曝光尺调整曝光能量
7、调
整退膜各项参数
1、压力大
2、药水要求不在范围(比重铜含量、氯离子、PH值)
3、速度慢
4、温度高
5、曝光不良1、喷嘴堵塞 2、压力小 3、药水要求不在范围(比重铜含量、氯离子、PH值) 4、速度快 5、温度低
6、曝光不良
7、退膜不净
1、、检查调整压力
2、化验调整药水浓度(比重铜含量、氯离子、PH 值)
3、做蚀刻点(或首件)确定调整速度
4、检测温度调整
5、制作曝
光尺调整曝光能量。