铝板带热轧工艺润滑剂的使用探究
工艺润滑技术在热轧精轧机组中的应用
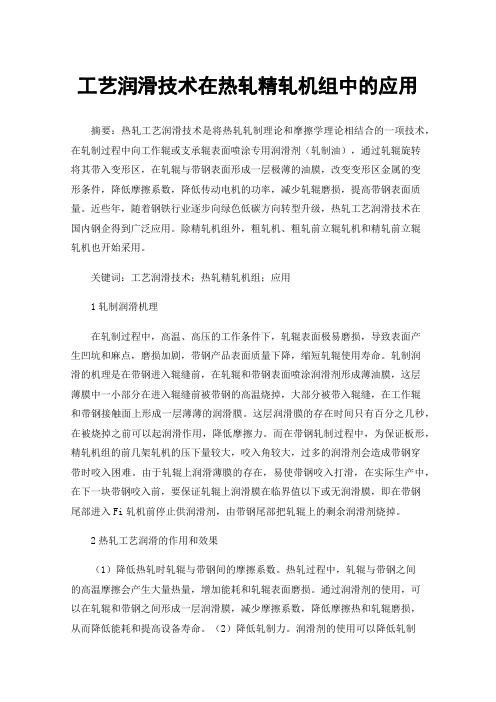
工艺润滑技术在热轧精轧机组中的应用摘要:热轧工艺润滑技术是将热轧轧制理论和摩擦学理论相结合的一项技术,在轧制过程中向工作辊或支承辊表面喷涂专用润滑剂(轧制油),通过轧辊旋转将其带入变形区,在轧辊与带钢表面形成一层极薄的油膜,改变变形区金属的变形条件,降低摩擦系数,降低传动电机的功率,减少轧辊磨损,提高带钢表面质量。
近些年,随着钢铁行业逐步向绿色低碳方向转型升级,热轧工艺润滑技术在国内钢企得到广泛应用。
除精轧机组外,粗轧机、粗轧前立辊轧机和精轧前立辊轧机也开始采用。
关键词:工艺润滑技术;热轧精轧机组;应用1轧制润滑机理在轧制过程中,高温、高压的工作条件下,轧辊表面极易磨损,导致表面产生凹坑和麻点,磨损加剧,带钢产品表面质量下降,缩短轧辊使用寿命。
轧制润滑的机理是在带钢进入辊缝前,在轧辊和带钢表面喷涂润滑剂形成薄油膜,这层薄膜中一小部分在进入辊缝前被带钢的高温烧掉,大部分被带入辊缝,在工作辊和带钢接触面上形成一层薄薄的润滑膜。
这层润滑膜的存在时间只有百分之几秒,在被烧掉之前可以起润滑作用,降低摩擦力。
而在带钢轧制过程中,为保证板形,精轧机组的前几架轧机的压下量较大,咬入角较大,过多的润滑剂会造成带钢穿带时咬入困难。
由于轧辊上润滑薄膜的存在,易使带钢咬入打滑,在实际生产中,在下一块带钢咬入前,要保证轧辊上润滑膜在临界值以下或无润滑膜,即在带钢尾部进入Fi轧机前停止供润滑剂,由带钢尾部把轧辊上的剩余润滑剂烧掉。
2热轧工艺润滑的作用和效果(1)降低热轧时轧辊与带钢间的摩擦系数。
热轧过程中,轧辊与带钢之间的高温摩擦会产生大量热量,增加能耗和轧辊表面磨损。
通过润滑剂的使用,可以在轧辊和带钢之间形成一层润滑膜,减少摩擦系数,降低摩擦热和轧辊磨损,从而降低能耗和提高设备寿命。
(2)降低轧制力。
润滑剂的使用可以降低轧制力,减少轧制过程中的变形阻力。
润滑剂能够在轧制过程中形成一层润滑膜,减少金属间的接触阻力,从而降低轧制力,提高轧制效率。
热轧工艺专业组——轧制工艺润滑

热轧生产也需要润滑 哪里需要?
1.2 热轧生产中的润滑
一、工艺润滑在热轧中的应用
1、设备润滑 2、轧制工艺润滑
1886年,润滑力学的创始人O.Reynolds推导出著名的雷诺方程。 20世纪初,开始在矿物油中加入活性添加剂以提高润滑效果,同时
在冷轧窄带钢工艺中已开始用水作为润滑剂。 20世纪30 年代,前苏联采用动物油进行热轧型钢工艺润滑。 1968年,美国国家钢铁公司GREAT LAKE在热轧精轧机组上成功地应
乳化剂
添加剂和水
两种不相溶的液相,如油 和水,不能形成稳定的平 衡体系,故加入表面活性 剂,也就是乳化剂
2.2 轧制工艺润滑剂的应用
二、轧制工艺润滑剂
热轧生产中使用乳化油。
基础油
乳化剂
添加剂
加热搅拌
乳化油
在使用时兑水即可应用于实际生产。
3.1 轧制工艺润滑技术的应用
三、轧制工艺机理
热轧生产中润滑应用的研究相对冷轧远远落后 主要原因就是温度
• 作用机理:降低轧辊与带钢之间的摩擦系数 • 工作状况:在高温、高压下,部分被燃烧,以残炭形式
存在;部分急剧汽化和分解,形成油膜将轧辊与带钢隔 开;部分以流体形式通过变形区
四、轧制工艺润滑应用实例
工艺润滑作用 降低轧辊与带钢之间的摩擦系数,减小轧制力、轧制扭矩降 低能耗 降低轧辊消耗,延缓工作辊的磨损,延长轧辊使用周期,提 高轧机作业率 改善产品质量,减少二次氧化皮的产生
最佳使用浓度由具体轧制钢种、厚度、温度等 而定
4.1 热轧应用区域
精轧区域 具体点? 喷射点
四、轧制工艺润滑应用实例
4.2 供油方式
四、轧制工艺润滑应用实例
按比例在管路中通过混合器直接混合 浓度0.1—0.8% 用喷嘴向辊面喷射 一般0.15—0.2L/min
浅谈铝板带轧制润滑

浅谈铝板带轧制润滑摘要:轧制润滑技术是铝板带、箔轧制技术的核心。
企业之间激烈的竞争,对实现高速、大压下量、保证轧制后铝板带表面的性能及表面质量的需求越来越大。
因此,高性能复合添加剂、水基轧制液、微量润滑等高端新型的润滑技术铝轧制润滑技术未来发展的方向。
随着轧制条件提高,润滑油的铝粉污染加重,如何提高轧制润滑油过滤技术,降低过滤介质的使用,降低环保问题也是润滑油技术发展不可少的手段。
关键词:轧制润滑;磨损;工艺;过滤一、产业现状近年来,中国铝加工产业投资规模逐渐变大,产能增长较快,技术装备水平起点高,冷连轧、双零箔产能集中投产,轧制装备全面升级。
随着铝板带轧制技术的不断深入和发展,其技术特点已经开始向高速化、宽幅化及大压下量等方向发展。
但是,更加严峻的问题摆在面前,行业产能过剩的情况越来越严重,企业之间的竞争非常激烈。
促应用、稳增长、求创新是铝加工企业突围的根本途径。
毋庸置疑,实现高速、大压下量是提高生产效率、降低生产成本的重要手段。
因此,铝轧制润滑组分科学组合,对实现高速、大压下量、保证轧制后铝板带的性能及表面质量起到至关重要的作用。
实际生产过程中,铝板带表面出现的划伤、粗糙化、光亮度及板型等质量问题往往是由于轧制润滑油选择不合适或性能不达标所造成的。
这就对铝板带轧制工艺润滑过程提出新的要求和挑战。
二、铝轧制润滑油的作用铝轧制润滑油在轧制过程中主要起清洗、冷却和润滑的作用。
轧制润滑油可以有效实现减摩降压,达到如下目的:1、降低轧制过程中的力能参数(轧制力、轧制力矩、主电机功率);2、减少轧辊的磨损,提高轧件的尺寸精度;3、冷却轧辊,控制辊型,减少轧件变形不均匀;4、清洗轧件表面,提高轧后表面质量;5、减少铝灰分对轧制油污染。
为了能更好的达到铝板带轧制目的,对轧制润滑油提出了新的要求:1、基础油的变化:低粘度、窄馏程、高闪点、低硫低芳烃含量;2、挤压抗磨剂的应用:种类及含量,轧制油发黑及铝板化学腐蚀;3、水基轧制液:表面水腐蚀问题、环保问题等。
板带热轧工艺润滑及喷油系统

愿与供应商和用户本着互惠互利的原则精诚合作
DAS Tech
公司创始人- 斯图尔特先生
建于1865年,有着140年的老公司,从做润滑脂起家, 现发展成为专业化的化学油脂品生产商,从事向汽车、 航空、矿山、钢业和铝业及金属加工业提供各种各样的 润滑油脂品。
D.A.Stuart 的业务遍及全球五大洲,总部设于美国芝 加哥,分别在美国、加拿大、巴西、澳洲、德国、英国 和南非建设有生产基地,为了更好地服务日益活跃和勃 勃生机的亚太地区,2005年1月在上海浦东浦江经济 开发区投资600万美元成立了斯图尔特上海有限公司, 将其作为亚太地区的生产和研发中心。
DAS Tech
热轧油油品的主要参数
序号
项目
1
外观
2
粘度
3
皂化值
4
游离脂肪酸
5
硫
6
闪点
7
着火点
8
倾点
9
比重
单位
40摄氏度下 cSt mgKOH/g % % 摄氏度 摄氏度 摄氏度 Mg/mm3
DAST HM400(例) 暗琥珀
100 111 2-3
0.1-6.5 270 315 -18 0.905
Sy stem
喷油系统示例图一
DRAIN
DSP
1
20A 20A 15A
DSP
1
20A 20A 15A
DAS Tech
to F1 ~ F3 Oil Application Sy stem
OIL Booster Pump Unit
2-Gear pump 5l/min x 1Mpa
10kgf /cm2 AC 0.75kw x
热轧工艺润滑问题与改进措施

热轧工艺润滑问题与改进措施高亮亮① 杨宝贵(北京首钢股份有限公司 河北唐山064400)摘 要 热轧工艺润滑能够明显提高热轧轧机效率、降低系统轧制力、改善板带表面质量、延长轧辊使用寿命等特点。
本文介绍了热轧工艺润滑系统组成,分析了在使用过程中存在的问题并提出了改进措施,通过改善极大的提高了工艺润滑的投入率及可靠性。
关键词 热轧 工艺润滑 改进中图法分类号 TG155.4 文献标识码 BDoi:10 3969/j issn 1001-1269 2022 Z2 0381 前言热轧工艺润滑轧制技术是指在轧制变形区内建立一层润滑油膜,改变辊面与轧件间的“金属—金属”直接接触,改善轧制过程,提高产品质量的一种手段[1]。
随着市场对热轧板带的质量要求越来越高,生产商不断提高生产率,大举开发新的钢材种类,新的金属轧制技术和设备的日益成熟,轧制应用的范围不断拓展,热轧工作辊的工作环境也变得越来越严酷。
为了保证质量,提高作业率,轧辊要具备长寿命、耐磨耐用的特性。
所以工艺润滑在轧制过程中逐步得到了更多地应用和研究[2]。
为了更好的在激烈的市场竞争中,不断拓宽产品结构、提升产品质量、降低产品成本,持续提升企业的核心竞争力,首钢股份公司2250热轧产线精轧机组实施工艺润滑改造,以提升热轧带钢表明质量、实现薄规格轧制高效稳定。
在工艺润滑投入后,出现了管路、喷嘴堵塞、油温提升缓慢、对轧制力改善效果不明显等多个问题,通过不断进行技术攻关及系列改善,工艺润滑系统得到充分的利用。
2 工艺润滑设备及润滑方式热轧工艺润滑系统采用专用喷嘴系统,以水为载体将油水混合后喷射在轧辊上,使热轧润滑达到最佳的使用效果,此系统容易控制、运行可靠、维护方便故障率低。
热轧工艺润滑油喷出后与高温带钢接触,燃烧后形成灰分,因而工艺润滑油不能重复利用,采用非循环方式。
工艺润滑可以降低轧机负荷、减少轧机能耗、改善工作辊面得工作状态、维持良好的带钢表面质量、提高生产率、提高轧机的稳定性等作用。
浅谈铝轧制工艺和润滑
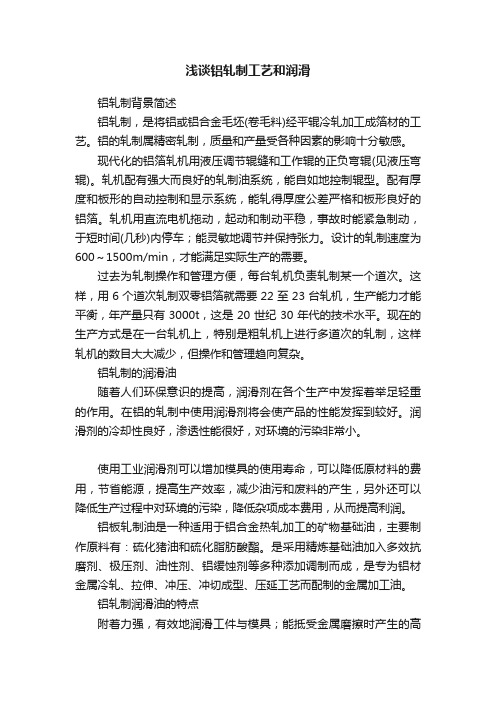
浅谈铝轧制工艺和润滑铝轧制背景简述铝轧制,是将铝或铝合金毛坯(卷毛料)经平辊冷轧加工成箔材的工艺。
铝的轧制属精密轧制,质量和产量受各种因素的影响十分敏感。
现代化的铝箔轧机用液压调节辊缝和工作辊的正负弯辊(见液压弯辊)。
轧机配有强大而良好的轧制油系统,能自如地控制辊型。
配有厚度和板形的自动控制和显示系统,能轧得厚度公差严格和板形良好的铝箔。
轧机用直流电机拖动,起动和制动平稳,事故时能紧急制动,于短时间(几秒)内停车;能灵敏地调节并保持张力。
设计的轧制速度为600~1500m/min,才能满足实际生产的需要。
过去为轧制操作和管理方便,每台轧机负责轧制某一个道次。
这样,用6个道次轧制双零铝箔就需要22至23台轧机,生产能力才能平衡,年产量只有3000t,这是20世纪30年代的技术水平。
现在的生产方式是在一台轧机上,特别是粗轧机上进行多道次的轧制,这样轧机的数目大大减少,但操作和管理趋向复杂。
铝轧制的润滑油随着人们环保意识的提高,润滑剂在各个生产中发挥着举足轻重的作用。
在铝的轧制中使用润滑剂将会使产品的性能发挥到较好。
润滑剂的冷却性良好,渗透性能很好,对环境的污染非常小。
使用工业润滑剂可以增加模具的使用寿命,可以降低原材料的费用,节省能源,提高生产效率,减少油污和废料的产生,另外还可以降低生产过程中对环境的污染,降低杂项成本费用,从而提高利润。
铝板轧制油是一种适用于铝合金热轧加工的矿物基础油,主要制作原料有:硫化猪油和硫化脂肪酸酯。
是采用精炼基础油加入多效抗磨剂、极压剂、油性剂、铝缓蚀剂等多种添加调制而成,是专为铝材金属冷轧、拉伸、冲压、冲切成型、压延工艺而配制的金属加工油。
铝轧制润滑油的特点附着力强,有效地润滑工件与模具;能抵受金属磨擦时产生的高温。
保证连续有效的油膜厚度,避免模具的局部刮伤或烧结;具有优异的极压抗磨性,优良的润滑性能,减少模具磨损,减少产品毛刺;防锈性能好,防止工件腐蚀。
极高润滑效果,在塑性变化中不断提供高效润滑减摩膜,能有效地提高工件表面质量,有效减少划痕、划伤、烧结焊合、破裂等现象的发生;优异的极压性能保证在高、深、难的加工工况下,有效提高工件的质量和加工功率,增加模具寿命。
铝板带热轧乳液分析规程

铝板带热轧乳化液分析方法目录一、PH (1)1试验项目 (1)2试剂及仪器 (1)3试验步骤 (1)3.1开机 (1)3.2标定 (1)3.3测量PH值 (2)二、电导率 (3)1试验项目 (3)2试剂及仪器 (3)3电极的选择 (3)4试验步骤 (3)三、浓度 (4)1试验项目 (4)2试剂及仪器 (4)3试验步骤 (4)四、疏水粘度 (5)1试验项目 (5)2试剂及仪器 (5)3试验步骤 (5)4计算 (6)五、旋蒸粘度 (7)1试验项目 (7)2试剂及仪器 (7)3试验步骤 (7)4运动粘度的检测 (8)5计算 (8)六、ESI(稳定指数) (9)1试验项目 (9)2试验仪器 (9)3试剂 (9)4试验步骤 (9)5计算 (10)七、PSD乳化液激光衍射粒度 (10)1试验项目 (10)2试剂及仪器 (10)3试验步骤 (10)八、细菌、酵母菌和真菌的数量 (11)1试验项目 (11)2试剂及仪器 (11)3试验步骤 (11)4结果记录 (12)九、红外光谱定量分析 (12)1试验项目 (12)2试剂及仪器 (12)3试验步骤 (13)4红外分析 (13)4.1实验前的准备 (13)4.2实验步骤 (14)十、灰分(GB508-85) (14)1试验项目 (14)2试剂及仪器 (14)3准备工作 (14)4试验步骤 (15)5计算 (15)一、PH1试验项目PH。
2试剂及仪器去离子水或蒸馏水、缓冲液(PH4.00,PH6.86,和PH9.18)、数显PH计、100ml烧杯、滤纸。
3试验步骤3.1开机仪器的输入端必须保持清洁干燥。
取下电极套后,应避免电极的敏感玻璃泡与硬物质接触,因为任何破损都可能导致电极失效。
第一次使用的PH电极,使用前浸泡在去离子水或蒸馏水中活化24小时。
接通电源,按“开/关”键,使仪器预热三十分钟。
打开电极填液孔,拧下电极保护帽,用蒸馏水清洗电极,并用滤纸吸干备用。
如果PH计在八小时内标定过,不必重新标定,这可用缓冲溶液来检验,如果误差在0.02范围内(PH的精度范围),此标定仍有效,误差如果在0.02范围外(PH的精度范围),则需要进行标定。
铝热连轧乳液的润滑特点及其实现
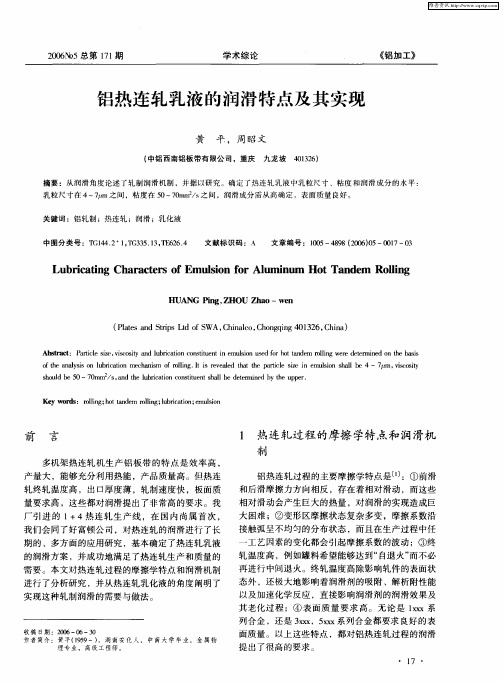
20 N5总 第 11 06 0 7 期
学术 综论
《 加工》 铝
铝热连轧乳液 的润滑特点及其实现
黄 平 ,周 昭 文
4 12 ) 0 36
( 中铝 西 南 铝 板 带 有 限公 司 ,重 庆 九 龙 坡
摘 要 :从 润 滑 角 度 论 述 了 轧 制 润 滑 机制 ,并 据 以研 究 。确 定 了热 连 轧 乳 液 中 乳 粒 尺 寸 、粘 度 和 润 滑 成 分 的水 平 乳 粒 尺 寸 在 4~7 之 间 ,粘 度 在 5 O~7mn/ 之 间 ,润 滑 成 分需 从 高 确 定 。表 面质 量 良好 。 Or s 2
大 困难 ;② 变形 区摩 擦状 态 复杂多 变 ,摩擦 系数沿 接 触弧 呈不 均匀 的分 布状 态 ,而且 在生 产过程 中任
一
我们会 同了好富 顿公 司 ,对 热连 轧的润 滑进行 了长
期 的 、多方 面 的应用研 究 ,基本确 定 了热 连轧 乳液 的润滑 方案 ,并 成功地 满足 了热连 轧生产 和质 量 的 需 要 。本 文对热 连轧过 程 的摩擦 学特点 和润滑 机制 进行 了分析研 究 ,并从 热连 轧乳 化液 的角度 阐明 了 实现这 种轧 制润 滑的需 要与做 法 。
列 合金 ,还是 3x ,5x 系 列合金 都要求 良好 的表 xx xx
收稿 日期 :20 0 06— 6—3 0 作 者 简 介 :黄 平 (99一) 湖 南 安 化 人 , 中南 大 学 毕 业 ,金 属 物 15 , 理 专 业 , 高级 工 程 师。
面质 量 。以上 这些特 点 ,都对 铝热连 轧过 程 的润滑
关 键 词 :铝 轧 制 ;热 连 轧 ;润 滑 ;乳 化 液
铝材轧制油添加剂润滑效果及复合机理研究
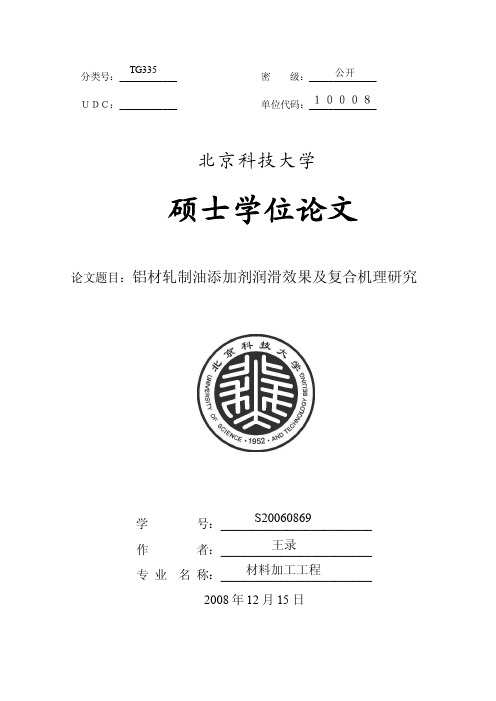
材料加工工程 专 业 名 称:_________________________ 2008 年 12 月 15 日
北合机理研究
王 录 作者:_________________________
指 导 教 师:
孙建林 教授
北京科技大学 单位:
孙建林 日期:____________ 王 录 2008.12.15 签名:___________ 导师签名:___________
- I-
北京科技大学硕士学位论文
摘
要
轧制过程中采用润滑剂可以有效地减小摩擦、提高轧制效率、节约材料和能源。润 滑剂的成分不同,其轧制速度、轧后金属表面光洁度等也不相同。目前国外铝板带轧制 机主要采用轻质矿物油作基础油,矿物油中加入添加剂能够改善油品性能,提高矿物油 润滑性能。本文主要论述了铝材轧制工艺润滑对轧制油的要求,并且通过轧制实验选择 合适的添加剂,研究不同的单体及复合添加剂对轧制油的极压性能、轧制工艺性能、退 火表面质量及轧后表面质量等参数的影响。 通过极压性能研究表明,基础油中加入添加剂能提高油膜强度,其中脂肪酸对油膜 强度的改善效果最为明显,而脂肪醇最弱;复合添加剂的油膜强度据添加剂成分及配 比、浓度不同而改变。实验表明十二酸和十二醇组成的复合添加剂具有较高的油膜强 度,当复合添加剂的成分配比改变时,其油膜强度呈周期性变化,添加剂浓度在 5%左 右时油膜强度较高。 研究认为单体添加剂中十二醇的轧制润滑效果最好;随着浓度的增加,复合添加剂 的轧制压力降低;复合添加剂成分影响轧制工艺性能,研究表明,同浓度下复合添加剂 中各组成成分比例的增大,轧制压力下降;复合添加剂比单体添加剂有更好的减摩降压 效果,同浓度比例下十二酸和十二醇的复合添加剂最为显著。 研究证明考虑轧后铝材表面质量,采用醇酯型和混合酯型复合添加剂轧制后铝板表 面粗糙度较低,退火时对铝板表面污染最少,具有优良的综合润滑性能。复合添加剂对 轧后铝材表面退火污染程度较低,基础油中加入添加剂后,由于添加剂被稀释因此退火 性能未能充分表现;退火温度升高,退火后铝材表面污染程度增加;而退火温度低,轧 制油充分挥发所需时间变长。
金属材料表面润滑剂的研究与优化

金属材料表面润滑剂的研究与优化一、前言金属材料作为重要的制造原材料,其表面润滑剂的研究与优化已成为近年来研究的热点。
随着人们对金属制造品质要求的不断提高,金属材料在生产过程中遇到的表面润滑问题越来越复杂,研究如何优化表面润滑剂的配方并应用于实践中,已成为各个领域工程技术人员共同面临的问题。
本文将就当前表面润滑剂研究领域中的现状、问题及发展趋势进行探讨,并对未来的研究方向提出一些建议。
二、表面润滑剂的研究现状(一)表面润滑剂的定义表面润滑剂是指在金属材料与工具或模具之间起润滑作用的物质。
表面润滑剂在工件表面形成润滑膜,减小工件表面与摩擦体之间的接触力,使得摩擦变得更加顺滑,以达到延长金属材料寿命、提高制造精度、减小能源损失等目的。
(二)表面润滑剂的研究进展自20世纪80年代以来,表面润滑剂的研究和应用有了长足的发展。
随着材料科学和表面技术的不断进步,表面润滑剂的配方和制备工艺得到了不断改进,研究范围也逐渐扩大。
目前,表面润滑剂的研究已经涉及到塑性加工、冷拔、冷轧、挤压、铸造和锻造等领域。
其中,在塑性加工方面,国内外学者已经提出了多种新型表面润滑剂,如有机硅润滑剂、纳米润滑剂、超高分子量聚乙烯润滑剂等。
在冷轧加工方面,研究者们已经探讨了多种新型表面润滑剂的制备方法,如微胶囊润滑剂、纳米润滑剂和有机硅润滑剂等。
这些新型表面润滑剂具有润滑效果好、无污染、易挥发等特点。
在挤压加工方面,新型表面润滑剂的研究也取得了重要进展。
如蜡液、挤压膏、纳米润滑剂和有机硅润滑剂等。
在铸造工艺中,许多新型表面润滑剂正在得到广泛应用,如氧化铝、石墨、纳米润滑剂和有机硅润滑剂等。
总之,近年来,全球各个领域的研究者们在表面润滑剂的研究领域取得了显著的进展,尤其是在新型润滑剂的制备和应用方面有很大的突破。
(三)表面润滑剂的问题表面润滑剂虽然在金属材料加工过程中发挥了重要作用,但也存在一些问题。
首先表面润滑剂涂覆等加工不太便捷,有时候甚至浪费了大量时间;另外,一些表面润滑剂在生产过程中污染环境,对人体健康也造成了潜在的威胁;此外,润滑剂的加工质量不佳对金属加工质量会形成污染。
铝厂设备的合理润滑研究与使用建议
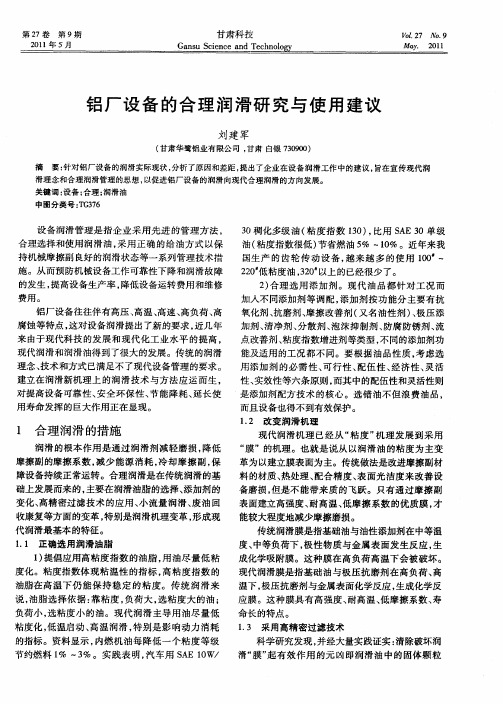
责 人 和执行人 ; 立设 备 使 用 档 案 以及 油 品检 测记 建
录; 编制 设备换 油计 划 和油量 需求计 划 ; 定油料 消 制
开 发合 成发 动机油 、 轮油等 , 齿 使用 合成 油能直 接节
省 燃料 3 ~5 。 % %
耗 定额 ; 制订 设 备 润 滑 “ 五定 ” 图表 ; 置 油 品 检测 添 仪, 对在 用油 进行 状态监 测 ; 设备 润滑故 障从摩擦 对 副材质 、 润滑 油品 的质量 、 滑方 法 和装 置 、 滑 系 润 润 统 等多 方面综 合分 析 。 4 作 为 设 备 的使 用 者 , 熟 悉 设 备 构 造 的 同 ) 在 时, 还应 熟悉设 备 的润 滑要 求 , 样 , 能从 设 备 润 这 方 滑的角 度对 设 备 进 行 评 价 ( 实 上 , 其 他 同 等条 事 在 件 下 , 备 的优 良运行 和寿命保 证 , 由其 完善 的润 设 是 滑系统 来保 证 的 ) 才 能 更 好 地 进 行 设 备 的润 滑管 , 理, 以确 保设 备 的长期稳 定运行 。
Hale Waihona Puke 1 合理润滑 的措施 润 滑 的 根本 作 用 是 通过 润 滑剂 减 轻 磨损 , 降低
现代 润滑 机理 已 经从 “ 度 ” 理发 展 到采 用 粘 机 “ ”的机 理 。也就 是 说 从 以润 滑 油 的粘 度 为 主变 膜
摩擦副的摩擦系数 , 减少能源消耗 , 冷却摩擦副 , 保 障设备持续正常运转。合理润滑是在传统润滑的基 础上发展而来 的, 主要在润滑油脂的选择、 添加剂的 变化 、 高精密过滤技术的应用、 流量润滑、 小 废油 回 收康复等方面的变革 , 特别是润滑机理变革 , 形成现 代润滑最基本的特征 。 1 1 正 确选 用润 滑 油脂 . 1 提倡应用高粘度指数 的油脂 , ) 用油尽量低粘
CSP热轧工艺润滑效果研究

润 滑 与 密 封
LUBRI AT 0N C 1 ENGI NEERI NG
Sp 2 0 e . 01
第3 5卷 第 9期
Vo . 5 No 9 13 .
DOI 0 3 6 /.sn 0 5 :1 . 9 9 jis. 2 4—0 5 . 0 0 0 . 2 102 1.90 3
A s atT eefc f u r ai u n o l n f o at t ppo u t n( S bt c: h f t b i t nd r gh t ol go mp c r rd ci C P)w ss de ae ntep y — r e ol c o i r i c si o a t idb sdo h s u h
( c olo tr l ce c n n ier g nvri f ce c n e h ooy,B in 0 0 3, hn ) S h o f e a S in ea d E gn ei ,U iest o in ea dT c n lg Ma i n y S ej g1 0 8 C ia i
C P热 轧 工 艺 润 滑 效 果 研 究 S
马艳丽 孙建林 高 雅
北 京 10 8 ) 0 0 3
( 京科技大学材料科学与工程学院 北
摘 要 :在 理 化性 能 与摩 擦 学 性 能测 试 分析 的 基础 上 ,对 C P热轧 板 带 钢 工 艺 润 滑 应 用 效 果 进 行 轧 制 过 程 研 究 。 工 S 业 应 用试 验 表 明 : S C P热 轧板 带 钢过 程 中 ,并非 热 轧 油体 积 比越 高 ,工艺 润 滑 效果 越 好 ,选 择 中 低黏 度 、润 滑 性 能 良好 的热 轧油 ,其体 积 分 数在 0 2 时 即可 平均 降 低 轧制 力 1% ~ 0 ,使 连 轧 过 程张 力 波 动控 制 在 2 % 以 内 ,同 时对 冷 却 .% 0 2% 0 水 的 污染 也 不 明显 。摩 擦 学测 试 和 轧 制工 艺 润 滑应 用试 验 数 据 分析 表 明 ,控 制 热 轧油 体 积 分 数 在 l 以下 即可 满 足 热 轧 % 工 艺润 滑 作 用效 果 。 可根 据具 体 轧 制 产 品与 工艺 对 热 轧 油 黏 度 和 用 量 做 出 相应 调 整 ,应 以保 证 C P热 轧生 产平 稳 进 行 S
乳化液在铝板带轧制过程中的重要作用

乳化液在铝板带轧制过程中的重要作用【摘要】铝板带热轧制乳化液的特性和在生产轧制过程中发挥的冷却润滑作用。
【关键词】乳化液;润滑;冷却;分散相;浓度;油膜1.乳化液的特性两种互不相溶的液相,一种液相以0.1~100μm的微小液滴的形式,均匀的分布于另一种液相中,形成的两相平衡体系,称为乳化液。
乳化液的组成主要是基础油、水、乳化剂和各种添加剂。
在乳化液的两相平衡体系中,含量少的称为分散相,含量多的称为连续相。
若分散相是油,连续相是水,则形成o/w型乳化液,反之则形成w/o型乳化液。
铝板热轧一般使用o/w型乳化液,其基本性能如下:(1)无毒、无味,维护管理方便,使用周期长,并且破乳容易,排放达标,对环境无污染。
(2)对轧辊的洗涤作用强,轧后铝粉分离性好。
对轧辊及设备无腐蚀。
(3)良好的稳定性和热分离性。
乳化液的稳定性主要是由稳定性指数和乳粒的尺寸大小决定的。
乳化液是基础油和水在高速搅拌下形成的乳状液体,油和水是两种互不相溶的液体,这种乳状液体混合时不能形成稳定的平衡体系,极易分离,需要在油水混合体系中加入表面活性剂,即乳化剂,才能形成相对稳定的乳化液。
乳化液的稳定性指数,是在热力学上不安定的乳化液的安定性指标,数值越高,乳化液越稳定。
铝板热轧用乳化液的稳定性指数一般在0.4~0.8之间,太高,影响乳化液的热分离性,太低,增加乳化液耗量,严重的甚至影响乳化液的正常使用。
乳粒的尺寸越小,则乳液越稳定。
乳化液的乳粒尺寸取决于乳化体系的hlb值及乳化液循环系统的搅拌力和温度等因素。
随着使用时间的增加,乳化液的粒径逐渐粗化长大,乳化液的稳定性下降。
乳化液喷射到温度很高的铝板和轧辊上,平衡状态遭到破坏,油水迅速分离,水分蒸发带走了大量的热量,对轧辊和铝板起到冷却的作用,剩下的水和油形成的反乳均匀的扩散在金属的表面上,形成润滑油膜,对轧制起到润滑作用。
图1为乳化液的热分离原理图。
热分离性的过程越短,乳化液对轧辊的冷却润滑作用越强,反之亦反。
铝及铝合金热轧用乳化液应用技术
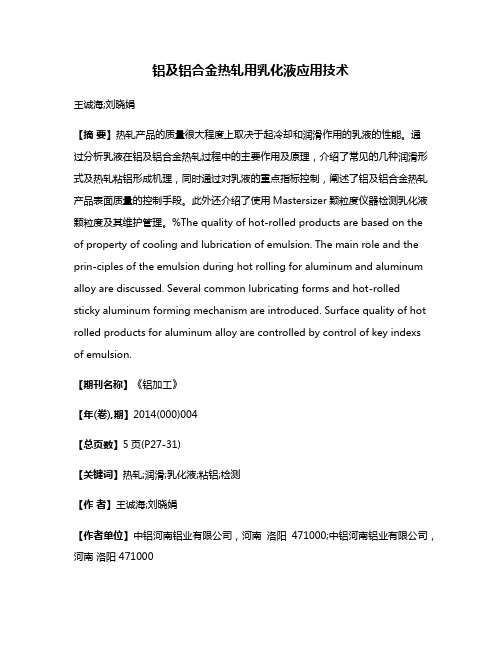
铝及铝合金热轧用乳化液应用技术王诚海;刘晓娟【摘要】热轧产品的质量很大程度上取决于起冷却和润滑作用的乳液的性能。
通过分析乳液在铝及铝合金热轧过程中的主要作用及原理,介绍了常见的几种润滑形式及热轧粘铝形成机理,同时通过对乳液的重点指标控制,阐述了铝及铝合金热轧产品表面质量的控制手段。
此外还介绍了使用Mastersizer颗粒度仪器检测乳化液颗粒度及其维护管理。
%The quality of hot-rolled products are based on the of property of cooling and lubrication of emulsion. The main role and the prin-ciples of the emulsion during hot rolling for aluminum and aluminum alloy are discussed. Several common lubricating forms and hot-rolled sticky aluminum forming mechanism are introduced. Surface quality of hot rolled products for aluminum alloy are controlled by control of key indexsof emulsion.【期刊名称】《铝加工》【年(卷),期】2014(000)004【总页数】5页(P27-31)【关键词】热轧;润滑;乳化液;粘铝;检测【作者】王诚海;刘晓娟【作者单位】中铝河南铝业有限公司,河南洛阳471000;中铝河南铝业有限公司,河南洛阳 471000【正文语种】中文【中图分类】TG339;TH117.2+2铝及铝合金热轧产品的质量很大程度上取决于起冷却和润滑作用的乳化液的性能,乳化液是油分布在水中形成的宏观均匀的两相体系,一般情况下水相是连续相,起冷却作用,油相是分散相体现和承载了润滑性能。
热轧工艺润滑
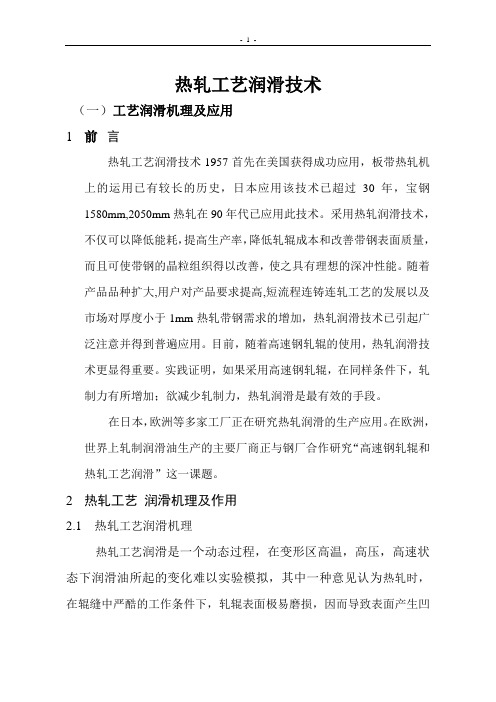
热轧工艺润滑技术(一)工艺润滑机理及应用1前言热轧工艺润滑技术1957首先在美国获得成功应用,板带热轧机上的运用已有较长的历史,日本应用该技术已超过30年,宝钢1580mm,2050mm热轧在90年代已应用此技术。
采用热轧润滑技术,不仅可以降低能耗,提高生产率,降低轧辊成本和改善带钢表面质量,而且可使带钢的晶粒组织得以改善,使之具有理想的深冲性能。
随着产品品种扩大,用户对产品要求提高,短流程连铸连轧工艺的发展以及市场对厚度小于1mm热轧带钢需求的增加,热轧润滑技术已引起广泛注意并得到普遍应用。
目前,随着高速钢轧辊的使用,热轧润滑技术更显得重要。
实践证明,如果采用高速钢轧辊,在同样条件下,轧制力有所增加;欲减少轧制力,热轧润滑是最有效的手段。
在日本,欧洲等多家工厂正在研究热轧润滑的生产应用。
在欧洲,世界上轧制润滑油生产的主要厂商正与钢厂合作研究“高速钢轧辊和热轧工艺润滑”这一课题。
2热轧工艺润滑机理及作用2.1 热轧工艺润滑机理热轧工艺润滑是一个动态过程,在变形区高温,高压,高速状态下润滑油所起的变化难以实验模拟,其中一种意见认为热轧时,在辊缝中严酷的工作条件下,轧辊表面极易磨损,因而导致表面产生凹坑和麻点;而凹坑和麻点又加剧磨损,造成恶性循环,轧辊因磨损而迅速报废。
如果能在轧件进入辊缝之前,在轧件表面喷涂润滑物质,形成润滑膜,尽管这层膜有一小部分可能在进入辊缝前即被高热的轧件烧掉,但大部分还是被咬入辊缝,在工作辊和轧件的接触面上形成一层薄薄的润滑膜。
虽然油膜与轧辊的接触时间只有百分之几秒的暂短瞬间,但是油膜在烧掉之前可以起到润滑作用,可减轻轧辊磨损,避免很快出现凹坑和麻点。
由于现代热轧工艺特点是高温,高压,高速,热轧工作辊辊面瞬时温度可达600∽700℃,经冷却散热而稳定在50∽80℃,因此,为适应热轧工艺特点,热轧润滑油应具有以下特性:(1)具有高极性分子的构成,在轧辊表面有极好的湿润性,可迅速形成均匀的薄层润滑膜,降低摩擦,减少磨损。
铝合金及其复合材料制备过程中润滑剂的应用
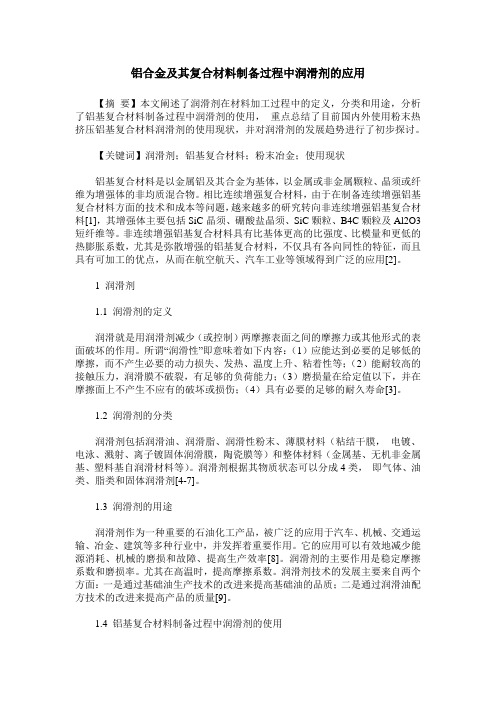
铝合金及其复合材料制备过程中润滑剂的应用【摘要】本文阐述了润滑剂在材料加工过程中的定义,分类和用途,分析了铝基复合材料制备过程中润滑剂的使用,重点总结了目前国内外使用粉末热挤压铝基复合材料润滑剂的使用现状,并对润滑剂的发展趋势进行了初步探讨。
【关键词】润滑剂;铝基复合材料;粉末冶金;使用现状铝基复合材料是以金属铝及其合金为基体,以金属或非金属颗粒、晶须或纤维为增强体的非均质混合物。
相比连续增强复合材料,由于在制备连续增强铝基复合材料方面的技术和成本等问题,越来越多的研究转向非连续增强铝基复合材料[1],其增强体主要包括SiC晶须、硼酸盐晶须、SiC颗粒、B4C颗粒及Al2O3短纤维等。
非连续增强铝基复合材料具有比基体更高的比强度、比模量和更低的热膨胀系数,尤其是弥散增强的铝基复合材料,不仅具有各向同性的特征,而且具有可加工的优点,从而在航空航天、汽车工业等领域得到广泛的应用[2]。
1 润滑剂1.1 润滑剂的定义润滑就是用润滑剂减少(或控制)两摩擦表面之间的摩擦力或其他形式的表面破坏的作用。
所谓“润滑性”即意味着如下内容:(1)应能达到必要的足够低的摩擦,而不产生必要的动力损失、发热、温度上升、粘着性等;(2)能耐较高的接触压力,润滑膜不破裂,有足够的负荷能力;(3)磨损量在给定值以下,并在摩擦面上不产生不应有的破坏或损伤;(4)具有必要的足够的耐久寿命[3]。
1.2 润滑剂的分类润滑剂包括润滑油、润滑脂、润滑性粉末、薄膜材料(粘结干膜,电镀、电泳、溅射、离子镀固体润滑膜,陶瓷膜等)和整体材料(金属基、无机非金属基、塑料基自润滑材料等)。
润滑剂根据其物质状态可以分成4类,即气体、油类、脂类和固体润滑剂[4-7]。
1.3 润滑剂的用途润滑剂作为一种重要的石油化工产品,被广泛的应用于汽车、机械、交通运输、冶金、建筑等多种行业中,并发挥着重要作用。
它的应用可以有效地减少能源消耗、机械的磨损和故障、提高生产效率[8]。
润滑条件对热轧润滑剂润滑性能的影响研究
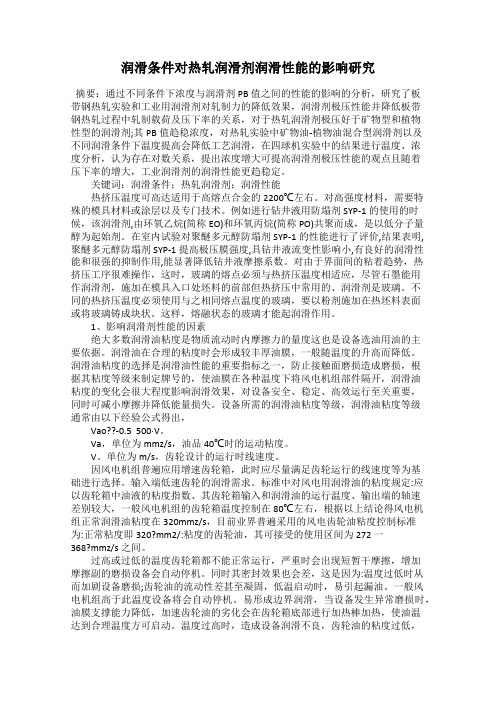
润滑条件对热轧润滑剂润滑性能的影响研究摘要:通过不同条件下浓度与润滑剂PB 值之间的性能的影响的分析,研究了板带钢热轧实验和工业用润滑剂对轧制力的降低效果,润滑剂极压性能并降低板带钢热轧过程中轧制载荷及压下率的关系,对于热轧润滑剂极压好于矿物型和植物性型的润滑剂;其PB值趋稳浓度,对热轧实验中矿物油-植物油混合型润滑剂以及不同润滑条件下温度提高会降低工艺润滑,在四球机实验中的结果进行温度、浓度分析,认为存在对数关系,提出浓度增大可提高润滑剂极压性能的观点且随着压下率的增大,工业润滑剂的润滑性能更趋稳定。
关键词:润滑条件;热轧润滑剂;润滑性能热挤压温度可高达适用于高熔点合金的2200℃左右。
对高强度材料,需要特殊的模具材料或涂层以及专门技术。
例如进行钻井液用防塌剂SYP-1的使用的时候,该润滑剂,由环氧乙烷(简称EO)和环氧丙烷(简称PO)共聚而成,是以低分子量醇为起始剂。
在室内试验对聚醚多元醇防塌剂SYP-1的性能进行了评价,结果表明,聚醚多元醇防塌剂SYP-1提高极压膜强度,具钻井液流变性影响小,有良好的润滑性能和很强的抑制作用,能显著降低钻井液摩擦系数。
对由于界面间的粘着趋势,热挤压工序很难操作,这时,玻璃的熔点必须与热挤压温度相适应,尽管石墨能用作润滑剂,施加在模具入口处坯料的前部但热挤压中常用的、润滑剂是玻璃。
不同的热挤压温度必须使用与之相同熔点温度的玻璃,要以粉剂施加在热坯料表面或将玻璃铸成块状。
这样,熔融状态的玻璃才能起润滑作用。
1、影响润滑剂性能的因素绝大多数润滑油粘度是物质流动时内摩擦力的量度这也是设备选油用油的主要依据。
润滑油在合理的粘度时会形成较丰厚油膜,一般随温度的升高而降低。
润滑油粘度的选择是润滑油性能的重要指标之一,防止接触面磨损造成磨损,根据其粘度等级来制定牌号的,使油膜在各种温度下将风电机组部件隔开,润滑油粘度的变化会很大程度影响润滑效果,对设备安全、稳定、高效运行至关重要,同时可减小摩擦并降低能量损失。
关于铝板轧制工艺润滑剂的几个问题
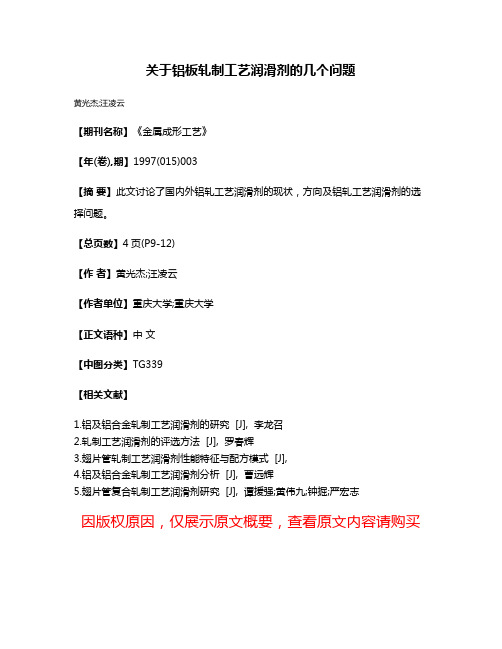
关于铝板轧制工艺润滑剂的几个问题
黄光杰;汪凌云
【期刊名称】《金属成形工艺》
【年(卷),期】1997(015)003
【摘要】此文讨论了国内外铝轧工艺润滑剂的现状,方向及铝轧工艺润滑剂的选择问题。
【总页数】4页(P9-12)
【作者】黄光杰;汪凌云
【作者单位】重庆大学;重庆大学
【正文语种】中文
【中图分类】TG339
【相关文献】
1.铝及铝合金轧制工艺润滑剂的研究 [J], 李龙召
2.轧制工艺润滑剂的评选方法 [J], 罗春辉
3.翅片管轧制工艺润滑剂性能特征与配方模式 [J],
4.铝及铝合金轧制工艺润滑剂分析 [J], 曹远辉
5.翅片管复合轧制工艺润滑剂研究 [J], 谭援强;黄伟九;钟掘;严宏志
因版权原因,仅展示原文概要,查看原文内容请购买。
- 1、下载文档前请自行甄别文档内容的完整性,平台不提供额外的编辑、内容补充、找答案等附加服务。
- 2、"仅部分预览"的文档,不可在线预览部分如存在完整性等问题,可反馈申请退款(可完整预览的文档不适用该条件!)。
- 3、如文档侵犯您的权益,请联系客服反馈,我们会尽快为您处理(人工客服工作时间:9:00-18:30)。
铝板带热轧工艺润滑剂的使用探究
摘要:中国铝加工业在20世纪80年代中期建成了一条(1+3)式或(1+4)式热轧生
产线,因此,从90年代起就可以不进口那么多罐料或少进口一些。
据粗略统计,自1986年长江电工厂的中国首条全铝易拉罐生产线投产以来到2004年为止的19年内共进口罐料约2000kt,按2004年的平均进口价2400美元t计算,进口金额达48
亿美元,可建西南铝业(集团)有限责任公司那样的(1+4)式热连轧线30条。
当然,中
国铝加工业的一批有识之士不是没有想到这一点,只是由于某些原因未建成。
例如80年代后期渤海铝业有限公司与澳大利亚合资建的热连轧线即将正式签字,由于1989年众所周知的事件而作罢;90年代中期东北轻合金有限责任公司与以色列的
合资项目都已在人民大会堂正式签约,后由于合资方掌门人埃森伯格先生的去世而
终止建设。
这两个项目未建成的后果是:使中国在热连轧方面的差距又拉长了约
20年;增加了约40亿美元的罐料进口量;引爆了目前的热连轧线建设浪潮,导致生
产能力形成过于集中。
关键词:铝板带热轧;润滑剂;使用
引言
随着铝、铝合金板材质量的提高和铝加工能力的不断提高,市场竞争加剧,
铝厂致力于不断提高产品质量,降低生产成本。
铝及铝合金的热轧温度350 - 520℃之间,通常在热轧过程中铝板与强粘结辊表面,在热轧过程中很容易形成在轧辊和
轧件粘铝层之间,和铝容易和磨料辊表面附着,导致产品的质量下降轧制后表面。
因此,通过润滑、冷却、洗涤和减少辊磨损来保证轧制产品的表面质量是非常重
要的。
1铝热轧工艺润滑的特征及机理
当前铝板带箔加工过程中,铝箔对除对内部织构要求高外,对箔面的要求也
非常高,由于表面的损伤(例如擦划伤、粘铝、起皮等),都会在后续的腐蚀工
序中暴露出来,对产品的稳定性、可靠性都带来一定的影响。
因此,在铝箔的生
产过程中,我们除了对道次压下、退火温度及退火时间的把控外,还要对轧制过
程中的表面情况进行控制,特别是在热轧工序,一方面是轧制的缺陷具有遗传性,热轧出现的很多缺陷都会在后续工序显现。
铝板材热轧时乳液润滑的机制如图1所示,根据摩擦与润滑理论,在变形区
入口处,轧辊与轧件表面形成楔形缝隙,当向轧辊与轧件喷入充足而均匀的乳化
液时,由流体动力学基本原理可知,旋转的轧辊和轧件表面将使润滑剂增压进入
楔形前区,越接近楔顶,润滑楔内产生的压力越大。
轧辊与轧件间的摩擦也逐渐
从干摩擦、边界摩擦、过渡到液体摩擦。
在工作辊的入口处喷射的乳化液在高温
高压作用下发生热分离现象,即轧辊的表面上乳化被破坏,逐渐热分离为油相和
水相,分离出来的油相吸附在金属表面,与添加剂一起和铝屑反应,形成一层细
密的辊面涂层。
涂层虽不太厚,但足以避免轧辊和轧件直接直接接触,并附着在
轧辊表面上,进入轧辊和轧板相接触的弧内,减小摩擦,形成润滑油层,起防粘
减磨作用,而水则起冷却作用,乳化液正是通过该种热分离来达到润滑、冷却的
目的。
表1是几种有代表的铝热轧乳化液。
图1 铝热轧机变形区润滑原理图
2铝热轧润滑的关键指标
2.1灰分。
灰分表示乳化液在规定条件下完全燃烧后,剩下的残留物,以质
量百分数表示。
随着乳液的使用,灰分值会逐渐升高,灰分值的升高,主要原因
是乳液中金属离子的含量增加,主要是制作过程中铝粉的混入,这会导致乳化液
油相颗粒变大,也会对所加入的添加剂活性产生影响,鉴于这个问题,热轧乳液
必须经过过滤装置,在停机时也要进行内循环操做,将乳液充分过滤,除去混入
的铝粉,保证乳化液的稳定性。
2.2浓度。
乳液浓度即乳液中除水外其他成分的含量,如前文所述,铝材热
轧乳液中有80%至90%以上都是水分。
因此水对乳化液的稳定性及使用效果有
着较大的影响,尤其是水的硬度,故我公司使用的是软水。
当乳液浓度偏低时,
即乳化液中油的比例不足,这样就会导致润滑不足,表现出轧制力偏大,前滑量
偏小,料面与轧辊之间易产生擦划伤,而当浓度偏高时,最明显的表现是容易出
现打滑,多次咬入,这样的过程会加重物料头尾的损伤程度,引起产品表面缺陷
问题的发生。
2.3粘度。
乳液的疏水粘度是指将乳液油水分离后,油相本身的粘度,乳液
润滑的功能主要是通过油相和添加剂来完成润滑功能的,对于铝箔轧制而言,对
粘度要求是基本稳定的,但因为在生产过程中重油(齿轮油、润滑油等)的污染,润滑剂的粘度可能会有比较大的变化,对轧制过程中的稳定性产生一定的干扰,
在此过程中,我们采用扎完一个炉次进行撇浮油的操作,将无法与水结合的重油
除去,并及时补充原液,保证乳液的稳定。
2.4pH值、生物活性及温度。
pH值偏高时,会导致润滑性能下降,偏低时可
能引起润滑过度;生物活性表示乳液中细菌的含量,细菌含量过高易引起乳化液
的变质,导致乳液大量报废;当乳液温度过高时,也易引起乳液变质。
3铝热轧常见问题与乳化液的对应关系
3.1粘铝。
原因为乳化液润滑能力不足,应提高乳液浓度及粘度,根据比例
计算添加原液。
3.2铝板表面铝粉含量高。
该现象主要原因也是乳液润滑能力不够,可根据比例添加原液及对应添加剂,使得润滑脂含量增高。
3.3打滑。
原因为乳液浓度过高、粘度过大以及杂油的影响,可采用加水稀
释的方法降低,并且将浮油撇除。
3.4轧制力偏高。
原因为乳液润滑能力不足,解决方法为添加原液及添加剂,提高乳液浓度及润滑脂的含量。
3.5咬入困难。
主要为乳液浓度过高,可采用加水稀释浓度,或者提高咬入
速度等。
4铝板带热轧工艺润滑剂中乳化液的使用
铝板带热连轧工程中,乳化液工艺润滑占重要的位置,乳化液系统运行的好
坏直接影响到热轧产品的质量。
综合分析比较各铝板带热连轧工程的乳化液冷却
系统。
(1)系统功能:该乳化液系统分别向轧机区各冷却润滑用户点提供经过滤、加热(或冷却)的乳化液,轧机上乳化液喷射系统提供支撑辊冷却、工作辊冷却及轧制
辊缝润滑冲洗等,乳化液温度和压力均可调节,实现轧制工艺润滑、轧辊温度和
辊型控制、轧件清洗等功能。
(2)系统组成:乳化液系统包括乳化液配置系统、供净乳化液系统、乳化液循环加热冷却系统、乳化液循环过滤系统、乳化液排污系统、乳化液控制阀组及内联
管路等。
(3)系统工艺流程:参与工艺润滑及铝板带冷却后的乳化液流人轧机底部乳化液
收集坑,溢流到布置在地下的乳化液系统污油箱。
污油经过撇油装置将表面的污染物或混人系统的杂油撇到油箱外废油收集装置,污油箱中的乳化液经过过滤器过滤后进人净油箱。
根据轧制工艺及净油箱中乳化液情况可对乳化液系统加热、冷却或添加补充去离子水及乳化油。
净油箱中的乳化液经泵组及阀组分配给轧机各用户点。
乳化液系统中的乳化液经过长期使用,各项指标达到其使用极限后,可通过油箱的排污系统排至工厂废水处理装置,处理达到排放标准后方可外排。
结语
铝热轧摩擦润滑机理的特点决定了其乳液组成的特殊性,即在工作中分离两个相,油相的润滑效果应该足够好。
鉴于高纯铝乳剂浓度的实际情况,应控制在4.0 - 7.0%的范围内,确保良好的润滑,基本不会再发生滑移现象,也可使轧制力控制在合理范围内。
铝热轧制乳化液除降低轧制力外,还对产品表面情况影响巨大,合理的乳液配置,对生产出表面完好的产品至关重要。
参考文献
[1]周强.铝箔生产.中国有色工业总公司,1991年.
[2]傅祖铸.有色金属板带材生产.中南大学出版社.2012.
[3]辛达夫.当代铝箔生产工艺及装备.北京.冶金工业出版社.2013.。