qc4第三章因果图树图与
通过因果图轻松查找原因—QC因果图的实际应用技巧
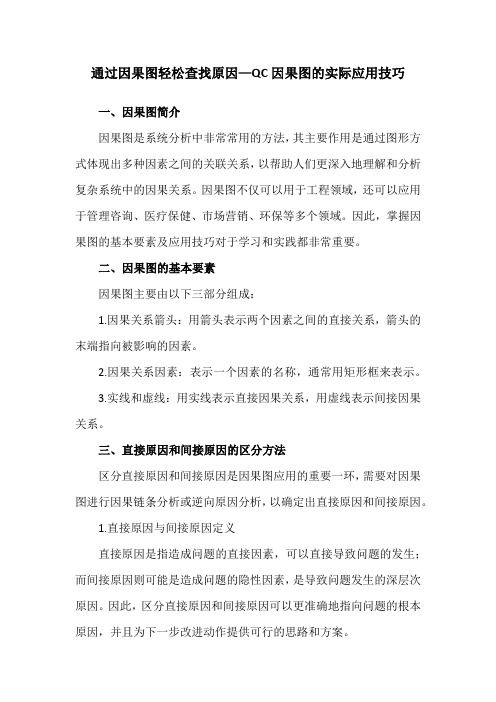
通过因果图轻松查找原因—QC因果图的实际应用技巧一、因果图简介因果图是系统分析中非常常用的方法,其主要作用是通过图形方式体现出多种因素之间的关联关系,以帮助人们更深入地理解和分析复杂系统中的因果关系。
因果图不仅可以用于工程领域,还可以应用于管理咨询、医疗保健、市场营销、环保等多个领域。
因此,掌握因果图的基本要素及应用技巧对于学习和实践都非常重要。
二、因果图的基本要素因果图主要由以下三部分组成:1.因果关系箭头:用箭头表示两个因素之间的直接关系,箭头的末端指向被影响的因素。
2.因果关系因素:表示一个因素的名称,通常用矩形框来表示。
3.实线和虚线:用实线表示直接因果关系,用虚线表示间接因果关系。
三、直接原因和间接原因的区分方法区分直接原因和间接原因是因果图应用的重要一环,需要对因果图进行因果链条分析或逆向原因分析,以确定出直接原因和间接原因。
1.直接原因与间接原因定义直接原因是指造成问题的直接因素,可以直接导致问题的发生;而间接原因则可能是造成问题的隐性因素,是导致问题发生的深层次原因。
因此,区分直接原因和间接原因可以更准确地指向问题的根本原因,并且为下一步改进动作提供可行的思路和方案。
2.因果链条分析因果链条分析是让人们理解和找到一个问题的直接和间接原因之间因果关系的过程。
在因果链条分析中,人们要通过绘制因果图或者思维导图等方式,系统地列出造成问题的因素,进行分析和引申,从而找出直接原因和间接原因。
举个例子,假设一个橡皮轮胎厂家生产的轮胎质量不佳,随机返修率居高不下。
使用因果链条分析的方法,可能发现以下几个原因:轮胎设计不当、设备维护不到位、材料品质不佳、工人生产技能不足、供应商质量不稳定、工艺不规范。
然后将这些因素作为起点,一步一步地往下延伸,找到每个因素之间的因果关系和影响,最后找出造成问题的直接原因和间接原因。
这种方法可以帮助人们清晰地了解问题的全貌,从而找到解决问题的最佳路径。
3.逆向原因分析逆向原因分析是一种侧重于问题解决的方法,其主要思想是从问题的发生形式逆向分析其根本原因,即在整个因果关系中,反向找出直接原因和间接原因的过程。
质量统计工具(QC工具)-因果图

5)针对绘制的草图组织集体讨论,讨论结果若认为是完善的, 可进行下一步步骤,若认为是不完善的,则应从2重复进行。
即4MIE。
3.针对要分析的质量问题,开展广泛深入的调查研究。本步骤 中要应用调查表和头脑风暴法等工具,目的在于尽可能多地收 集信息,争取能获得影响质量问题的全部原因。
4、绘制因果草图 1)开始绘图,把“质量问题”画入右边的方框中,然后把各类 原因放在左边,作为要分析的“质量问题”的输入。
尺寸 变异
c.矩阵图论证:按相关性加权计算后转为排列图论证 d.正交法论证:按正交试验设计法试验结果计算各因素位级 的贡献系数,极差 大 的为要因。 e.工艺试验论证:通过工艺试验,必要时应假设检验或方差 分析,具有显著性差异的要因。
f.经验论证:可以邀请多名有关的专家进行评价,最后以矩 阵评价表(包括专家会签法和两两对比法)的方式表达论证结 果。
2.原因的分析用分层法进行归纳;
3.因果图一般由小组集体绘制,但拥有足够过程知识和经验的 个人亦可独自担当。
4.当图表完成时,填写上目的、问题、绘制日期及制作者。
说明:排列图和因果图均可找出关键因素,但排列图是在各 种原因比较清楚的条件下,找出关键,而因果图是先通过分析 找出原因,然后在找出关键因素。
6)绘制正式的因果图图形(最后要注明因果图的名称、绘图者、 绘图时间、参加分析的人员等)。
料
机 设备调整不准 人 不熟悉工艺
混料
电压不稳
设备调整不当
料扁
电压不准
冲断凹心马蹄形
一个新旧QC七大手法区别

新QC七大手法1. 关联图法--TQM推行, 方针管理, 品质管制改善, 生产方式,生产管理改善2.KJ法--开发, TQM推行, QCC推行, 品质改善3. 系统图法--开发, 品质保证, 品质改善4.矩阵图法--开发, 品质改善, 品质保证5.矩阵开数据解析法--企划, 开发, 工程解析6. PDPC法--企划, 品质保证, 安全管理, 试作评价, 生产量管理改善, 设备管理改善7. 箭法图解法--品质设计, 开发, 品质改善老七种工具:调查表、排列图、因果图、散布图、分层法、直方图、控制图。
新七种工具:关联图、亲亲和图(KJ法、A型图解)、系统图(树图)、矩阵图、网络图、PDPC法、过程决策图法)、矩阵数据解析法。
不同的方法有不同的作用。
这里篇幅有限,我就简单说下鱼骨图吧。
希望对你有帮助。
其实企业中发布会用的最多的就是鱼骨图(因果图)了,直观明了,我们公司常做发布会,用的都是这方法。
一般会结合5w2h分析方法使用。
这里不能贴上来图,其他的你就百度里就有一堆鱼骨图了。
鱼的几个刺一般都用来代表人、机、料、法、环。
之后从几个刺下面细分出来一些其他的原因,逐条分析、去掉非要因。
最终剩下来的就是影响问题的要因了。
其实做过一次后就会很简单了。
至于图嘛,这里不能粘上来。
给你个链接吧,里面PPT介绍的很详细。
图也很丰富。
最后我想说的是,哥们,俺说了很多很累。
请给分吧第一章概述一、起源新旧七种工具都是由日本人总结出来的。
日本人在提出旧七种工具推行并获得成功之后,1979年又提出新七种工具。
之所以称之为“七种工具”,是因为日本古代武士在出阵作战时,经常携带有七种武器,所谓七种工具就是沿用了七种武器。
有用的质量统计管理工具当然不止七种。
除了新旧七种工具以外,常用的工具还有实验设计、分布图、推移图等。
本次课程,主要讲的是QC七大手法,而SPC(管制图)是QC七大手法的核心部分,是本次培训的重点内容。
二、旧七种工具QC旧七大手法指的是:检查表、层别法、柏拉图、因果图、散布图、直方图、管制图。
QC工具介绍:因果图
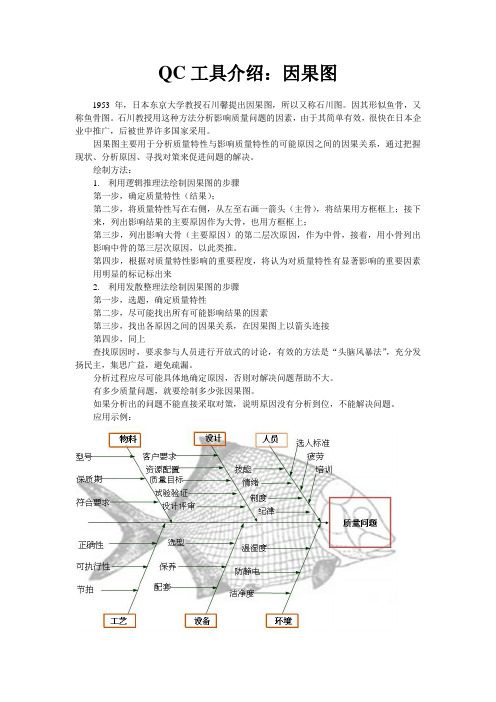
QC工具介绍:因果图
1953年,日本东京大学教授石川馨提出因果图,所以又称石川图。
因其形似鱼骨,又称鱼骨图。
石川教授用这种方法分析影响质量问题的因素,由于其简单有效,很快在日本企业中推广,后被世界许多国家采用。
因果图主要用于分析质量特性与影响质量特性的可能原因之间的因果关系,通过把握现状、分析原因、寻找对策来促进问题的解决。
绘制方法:
1.利用逻辑推理法绘制因果图的步骤
第一步,确定质量特性(结果);
第二步,将质量特性写在右侧,从左至右画一箭头(主骨),将结果用方框框上;接下来,列出影响结果的主要原因作为大骨,也用方框框上;
第三步,列出影响大骨(主要原因)的第二层次原因,作为中骨,接着,用小骨列出影响中骨的第三层次原因,以此类推。
第四步,根据对质量特性影响的重要程度,将认为对质量特性有显著影响的重要因素用明显的标记标出来
2.利用发散整理法绘制因果图的步骤
第一步,选题,确定质量特性
第二步,尽可能找出所有可能影响结果的因素
第三步,找出各原因之间的因果关系,在因果图上以箭头连接
第四步,同上
查找原因时,要求参与人员进行开放式的讨论,有效的方法是“头脑风暴法”,充分发扬民主,集思广益,避免疏漏。
分析过程应尽可能具体地确定原因,否则对解决问题帮助不大。
有多少质量问题,就要绘制多少张因果图。
如果分析出的问题不能直接采取对策,说明原因没有分析到位,不能解决问题。
应用示例:。
QC小组常用图表汇总(共16张)

示例:晶振损坏统计
常用于以下阶段 • 选择课题
• 现状调查
• 确定要因
按不同的地区 按不同的环境 ……
晶振损坏情况统计
时间 使用数 损坏数
2006年5月 5000
300
损坏率 6.0%
晶振损坏情况分类统计(按供应商)
时间 供应商 使用数 损坏数 损坏率
2006年5月
甲供应商 乙供应商
3000 2000
MS127 MS125 MS104R
96.68% 97.00% 88.42%
97.14% 97.89% 88.20%
98.73% 98.32% 92.58%
97.33% 97.77% 93.31%
97.84% 97.25% 89.80%
97.42% 97.66% 88.15%
97.52% 97.58% 89.97%
20360 31.48
53.00 84.48
电性能不合格 浸锡不良 磁芯破损 其他不良
3
磁芯破损
7474
11.56
96.04
4
其他不良
2561
3.96
100.00
由排列图可知(kě zhī)影响MS104R系列产 品合格率的主要缺陷是“电性能不合格”
第8页,共16页。
5、因果(yīnguǒ)图(鱼骨图)应用
双圈测试模式
软件系统
电桥与测试机联机
机械控制系统 测量控制系统
硬件系统
电气控制系统
第2页,共16页。
2、 关联图应用
原因分析
根据现状调查可知,问题症结在于“电感量偏高”和“电感量偏低”,我们选用了关联(guānlián)图进行原因分析, 如下图如示:
QC七大手法之因果图(鱼骨图)
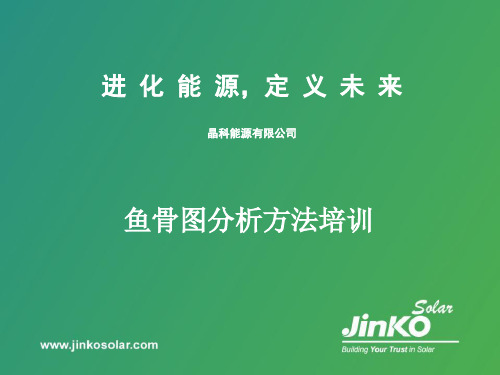
1
6
鱼骨图分析方法培训
⑦记入关联事项。
• 在制成的鱼骨图下栏标注名称。 • 标注制图日期。 • 标注制图人姓名。
制图日期及制图人
名称
「……」的特性要因图
2010年11月25日 ***、***、***
鱼骨图分析方法培训
绘制时,重点应放在为什么会有这样的原因,并依照5W1H的方法。
1.WHAT 做什么 2.WHERE 何地 去除不必要部门和动作, 改善对象是什么?改善目的是什么? 改变场所或场所的组合, 作业或作业者的方向是否在正确状态? 改变发生的时间、时期或顺序。 人的组合或工作的分担, 重新加以检查讨论。 改变方法或步骤,使所需人力更减少, 熟练度较低,使用费用更低的方法。 将所有的事情怀疑一次,把上面的5个质问, 均用WHY来商讨,并找出最好的改善方案。 是否无其他可做? 应该做些什么? 为什么在那地方做? 在何处做才是效率最高?
鱼骨图分析方法培训
特性:例2
搬运空箱较费时间
不能放到作业工程内 从工程下来的空箱多 需要箱子组装的零件种类较多 放空箱架子尺寸大 放空箱的架子和工程分离
设备 花费时间是为什么 事实 分离是为什么 推定 不能放是为什么 推定 大是为什么 推定 多是为什么 推定 放空箱架子尺寸大
中骨【事实】 所以
放空箱的架子和工程分离
大骨
孙骨
4
小骨
曾孙骨
中骨
鱼骨图分析方法培训
⑤记入中骨、小骨、孙骨的“要点”。
• 要因记入 [没有对策的反馈」。 例:「没有照明」 「没有报警」 「学习不足」 「没有盖子」 「没有干劲」 「注意不足」
• 反复寻找为什么,摸索探询的话比较好
• 要因是 「主语+谓语」的形式比较好。 例:「软管 → 软管长」
QC七大手法因果图

1
▐ 定义
1953年,日本管理大师石川馨先生所提出的一种把握结果(特性) 与原因(影响特性的要因)的极方便而有效的方法,故名“石川 图”。
因其形状很像鱼骨,是一种发现问题“根本原因”的方法,是一种 透过现象看本质的分析方法,也既称为“鱼骨图”或者“鱼刺图”。
问题的特性总是受到一些因素的影响,我们通过头脑风暴法找出这 些因素,并将它们与特性值一起,按相互关联性整理而成的层次分 明、条理清楚,并标出重要因素的图形就叫“特性要因图”、“因 果图” 。
步骤7:记下制图部门和人员、制图日期、参加人员以及其他备查事 项。 因果图提供的是抓取主要原因的工具,所以参加的人员应包括 对此项工作具有经验者,才易奏效。
5
▐ 因果图绘制步骤示意图
人
机
料
问题/特性/结果
小原因
中间原因
法
环
测
6
▐ 因果图绘制注意事项
中骨「事实」。 ( 不从事实开始的话,要做出对策的要因的真实味就淡了。)
步骤3:由集合的人员就影响问题的主要因素发言,中途不可批评或 质问(脑力激荡法),发言内容用短箭头记入图上各要因箭头的两侧。
步骤4:搜集20-30个原因则可结束。
步骤5:就所搜集的要因,何者影响最大,再由大家轮流发言,经大 家磋商后,认为影响较大的予圈上红色圈(或画上方框)。
步骤6:与步骤5一样,针对已圈上一个红圈的,若认为最重要的可 以再圈上两圈、三圈。
放空箱的架子和工程分离
中骨【事实】
放空箱的架子和工程分离 不能放到作业工程内 放空箱架子尺寸大 从工程下来的空箱比较多 需要箱子的组装零件种类多
8
所以 所以 所以 所以 所以
▐ 案例分析2
QC小组概述

QC小组概述序言QC是英文Quality Control的简称,中文意义是品质控制,其在ISO8402:1994的定义是“为达到品质要求所采取的作业技术和活动”。
有些推行ISO9000的组织会设置这样一个部门或岗位,负责ISO9000标准所要求的有关品质控制的职能,担任这类工作的人员就叫做QC人员,相当于一般企业中的产品检验员,包括进货检验员(IQC)、制程检验员(IPQC)和最终检验员(FQC)。
QC小组指企业员工围绕企业经营战略、方针目标和现场存在的问题,以改进质量、降低消耗、提高素质和经济效益为目的组织起来的,运用质量管理理论和方法开展活动的小组。
QC小组是企业中群众性质量管理活动的一种有效组织形式,是提高产品质量,提高经济效益的有效途径。
QC小组具有以下几个特点:1、广泛的群众性。
QC小组成员不仅包括管理人员、技术人员,而且更注重吸引生产、服务一线人员。
2、高度的民主性。
自愿参加,自主管理,成员平等,充分民主,互相启发,集思广益。
3、严密的科学性。
QC活动小组遵循科学的工作程序,坚持用数据说明事实,利用统计工具,用科学方法分析与解决问题。
QC活动小组,既是一种循序改进的方法,也是追求卓越的精神追求,是企业管理的哲学和人生的态度。
通过比较5S与QC活动小组,可以发现,两者有许多共同之处。
5S的目的是改善现场、减少损耗、提高效率、提高质量,这个目的与QC小组根本目的是一致的。
5S活动需要全员参与,具有广泛性,这与QC小组群众性特点相一致。
5S活动从五方面都有明确要求和内涵,具有明显的科学性和实用性,这与QC活动小组具有一定的相似性。
在民主性方面,5S既有规范化要求,也有需要自我素养方面的要求,体现了民主性,这与QC小组特点相符合。
通过比较,企业可借鉴QC活动小组的流程和方法,开展群众性5S活动。
可将5S作为QC活动小组的内容,采取QC活动的典型流程,组成5S活动小组,运用PDCA循环,开展相关工作。
因果分析图

因果分析图——以红珠实验为例现代的质量管理工作是以数理统计方法及现代管理方法作为基本手段,来控制、预防质量问题。
QC是Quality Control的简称。
“QC工具”是开展主题活动必要的手段,主要是针对特定的工作失误或品质不良运用QC工具展开分析讨论,并将结果整理在大家容易看到的地方,以提醒防止发生这样的问题,而且大家随时可以提出新的建议并进行讨论修订。
“以数据说话”是质量管理的基本特点之一。
为了形象化地描述、分析问题,而采用排列图、因果分析图、调查表、直方图、散布图、控制图和数据分层法等QC七种常用工具。
戴明的红珠实验:材料:1)4000粒木珠,其中800红色、3200白色;2)有50个孔的勺子,且可以一次性盛起来50粒珠子;3)一大一小两个长方形容器,分别可以放下4000粒木珠假设:现在有一个新的工厂要生产珠子,并且只要白色的。
工厂首先招募员工,需要6名作业员、2名检验员、1名检验长、1名记录员。
a.作业员有3天的培训期,期间可以提问,在实习期满投入工作之后只可以埋头苦干;b.整个生产程序非常严格,不可以随意变动;c.若作业员绩效不好,会被解雇过程:1)混合材料:将珠子全部倒进大容器中,再由大容器倒入小容器,随后又倒入大容器,中间无需搅拌;2)勺子放入大容器中搅拌,取出50粒珠子;3)两名检验员分别点算,并最终以检验长的点算为准;4)记录结果:第一天:只有作业员甲生产的红珠数量最少(4粒),得到奖励,工厂规定第二天,没人生产的红珠数量要在3粒以下;第二天:甲情况变糟,乙情况改善;第三天:规定为零缺陷日,但是最终结果不好,工厂成本失控,若再无好转则面临倒闭清算第四天:只保留三位绩效好的作业员,解雇其他人;第五天:结果不如预期,依旧没有改进启示:1)实验本身是一个稳定的系统,工人的产出及其变异程度都是可以预测的;2)所有变异(包括工人之间产出红珠数量的差异)来自于过程本身,无所谓更优秀或者是最佳工人;3)产出白珠是一种稳定的状态;4)对作业员的奖惩毫无意义,因为作业员的表现与其努力程度无关,只受工作过程的左右。
新旧QC七大手法区别(1)
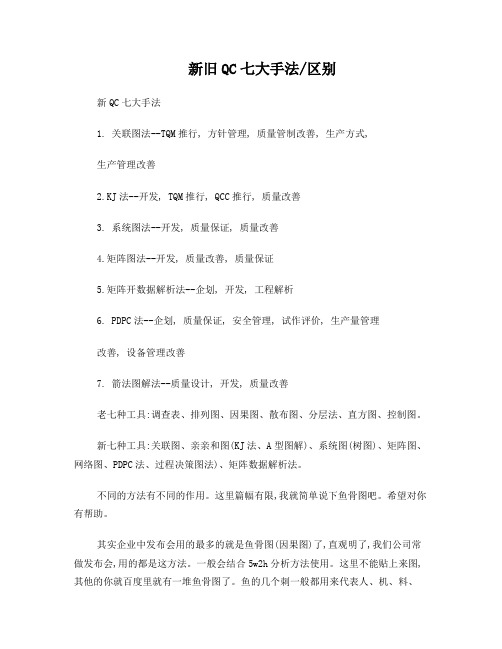
新旧QC七大手法/区别新QC七大手法1. 关联图法--TQM推行, 方针管理, 质量管制改善, 生产方式,生产管理改善2.KJ法--开发, TQM推行, QCC推行, 质量改善3. 系统图法--开发, 质量保证, 质量改善4.矩阵图法--开发, 质量改善, 质量保证5.矩阵开数据解析法--企划, 开发, 工程解析6. PDPC法--企划, 质量保证, 安全管理, 试作评价, 生产量管理改善, 设备管理改善7. 箭法图解法--质量设计, 开发, 质量改善老七种工具:调查表、排列图、因果图、散布图、分层法、直方图、控制图。
新七种工具:关联图、亲亲和图(KJ法、A型图解)、系统图(树图)、矩阵图、网络图、PDPC法、过程决策图法)、矩阵数据解析法。
不同的方法有不同的作用。
这里篇幅有限,我就简单说下鱼骨图吧。
希望对你有帮助。
其实企业中发布会用的最多的就是鱼骨图(因果图)了,直观明了,我们公司常做发布会,用的都是这方法。
一般会结合5w2h分析方法使用。
这里不能贴上来图,其他的你就百度里就有一堆鱼骨图了。
鱼的几个刺一般都用来代表人、机、料、法、环。
之后从几个刺下面细分出来一些其他的原因,逐条分析、去掉非要因。
最终剩下来的就是影响问题的要因了。
其实做过一次后就会很简单了。
至于图嘛,这里不能粘上来。
给你个链接吧,里面PPT介绍的很详细。
图也很丰富。
最后我想说的是,哥们,俺说了很多很累。
请给分吧第一章概述一、起源新旧七种工具都是由日本人总结出来的。
日本人在提出旧七种工具推行并获得成功之后, 1979年又提出新七种工具。
之所以称之为“七种工具”,是因为日本古代武士在出阵作战时,经常携带有七种武器,所谓七种工具就是沿用了七种武器。
有用的质量统计管理工具当然不止七种。
除了新旧七种工具以外,常用的工具还有实验设计、分布图、推移图等。
本次课程,主要讲的是QC七大手法,而SPC(管制图)是QC七大手法的核心部分,是本次培训的重点内容。
QC七大手法-因果图16页PPT

2.2由日本著名的质量管理专家石川馨先生 于1953年的提出,并在日本企业得到广泛应 用.又称石川图,特性要因图,鱼刺图,树枝图.
18.05.2020
制作与讲解:彭顺国
2
QC七大手法之一
因果图
3,因果图的绘制:
绘制不是一件轻而易举的工作,可以说质量问题能 否顺利解决,绘制因果图是关键.
4.6验证
分析出的原因要能采取措施为止,否则是只能算是练 习了.
记住: 做到“重要的因素不要遗漏”和“不重要的 因素不要绘制.最终的因果图是短小精悍.实用为好.
”
18.05.2020
制作与讲解:彭顺国
9
QC七大手法之一
因果图
4.7容易产生的大,中,小原因混乱,归类混乱的 现象,大原因,质量问题不明确是常见的毛病, 要特别注意.
充填时模型腔易卷气,形成砂孔
产品料较厚, 大件压铸时容易产生沙孔 大件充填时间长
地面污垢,车间嘈杂 压铸车间环境 光线暗淡,目视难发现沙孔
工作环境可能引发因素
机台漏氮现象
射料时 夹有气体
与机台保养有关
射料系统较差
锌压铸机台性能
一速0.3S, 保压0.8-1.0S
锌压铸机台一般调机
排气与保压 关系控制
加讨论的人员,和可供参考查询的信息.
18.05.2020
制作与讲解:彭顺国
11
QC七大手法之一
因果图
5.4图形要美观,大骨与小骨的倾斜度为5060°.
5.5图画好后,要落实主要因项目,订出措施,措 施出后,与柏拉图结合使用,检查其效果.也就 是说之前,之后都可能柏拉图法,来结合用.
18.05.2020
制作与讲解:彭顺国
QC常用手法_因果图

方法
分析名称:314变压器为 什么测定时间长
特性要因图的画法
2.特性要因图的画法 • (1)决定评价特性 • 自左向右画一横粗线代表作程,并将评价特性写在 箭头右边,以“为何×××不良”的方式表示。 • • • (2)列出大要因。 评价特性 ①大要因可直接依过程别分类,一般依 4M1E(人、 机械,材料、方法、 环境)分类。 ②大要因以“□”圈起来,加上箭头的大分之连接 到横粗线上。
特性要因图的用途
4.特性要因图的用途
• 特性要因图用途极广,现场、事务、研究、营业, 甚至军事上等都可以使用。特性要因图的制作以脑 力激荡法的方式进行,可使全员参加成为可能,使 全员的知识得以收集、整理,并使思想统一,发挥 更大的效果。其用途可依目的分类: ①改善解析:以改善品质、提高品质、降低成本目 标,进行现状解析,采取改善措施时用。 ②管理:发生很多抱怨、不良品、或异常时,为寻 找原因,采取改善措施时用。 ③制定作业标准:制定或修改作业的方法、管理点、 管理方法等的作业标准。 ④品质管理导入及教育:导入品质管理,全员参加 讨论时用特性要因图整理问题。对新人进行教育和 工作说明时用特性要因图。
THE END!
魚骨图
材料
绝缘胶 带太松 材料不 良多 材料切
换快
设备
人员
4284A不稳定 疲 新人作业 电流不稳定 L METER 劳 電流不穩定 判定慢 不良 情緒 电流源 教育不足 102速度慢 不佳 不适用 無 GPIB 接口 身体不适 无 GPIB 接口 客戶要求耐压测试时间为2秒
为什 么测 定时 间长 ?
特性要因图的特点
③特性要因图可显示出技术水准。 • 特性要因图若绘制得好。说明对作程的内容 已经有充分把握。技术水平越高,所绘制出 来的特性要因图内容越充实。一个特性要因 图只要做上30分钟的脑力激荡法,至少可举 出50个甚至多达100个以上的原因。。
QC七大手法之因果图

工件不固定 汽缸气压过低
汽缸漏气 夹具夹紧力不够
切断的尺寸混乱
中骨【理想】
切断尺寸混乱 工件不固定 夹具夹紧力不够 汽缸气压过低 从汽缸漏气
所以 所以 所以 所以 所以
鱼骨图剖析方法培训
特性:例2
搬运空箱较费时间
理想 推定 推定 推定 推定
设备 破费时间是为什么 分别是为什么 不能放是为什么 大是为什么 多是为什么
名称
「……」的特性要因图
制图日期及制图人
2010年11月25日 ***、***、***
鱼骨图剖析方法培训
绘制时,重点应放在为什么会有这样的缘由,并依照5W1H的方法。
1.WHAT 去除不必要部门和动作, 做什么 改善对象是什么?改善目的是什么?
是否无其他可做? 应该做些什么?
2.WHERE 改变场所或场所的组合, 何地 作业或作业者的方向是否在正确状态?
无不尽。 与会人员一概对等,各种想象全部记载。
鱼骨图剖析方法培训
④中骨、小骨、孙骨。 中骨「理想」。
〔 不从理想末尾的话,要做出对策的要因的真实 味就淡了。〕 小骨要围绕「为什么会那样?」来写。 孙骨要更进一步来清查「为大什骨 么会那样?」来写。
孙骨
4
小骨
曾孙骨
中骨
鱼骨图剖析方法培训
⑤记入中骨、小骨、孙骨的〝要点〞。 要因记入 [没有对策的反响」。
裂缝 裂缝问题
管道缺陷
供应商未认可
扩产
设备更换
错误的程 序
态度不端正 没有紧跟的程序
程序不可用
未培训
人
无预算
设备缺陷 未保养
没有人保 养
管道焊接裂缝
无人监控裂缝 销售额下降
- 1、下载文档前请自行甄别文档内容的完整性,平台不提供额外的编辑、内容补充、找答案等附加服务。
- 2、"仅部分预览"的文档,不可在线预览部分如存在完整性等问题,可反馈申请退款(可完整预览的文档不适用该条件!)。
- 3、如文档侵犯您的权益,请联系客服反馈,我们会尽快为您处理(人工客服工作时间:9:00-18:30)。
PPT文档演模板
qc4第三章因果图树图与
应用树图的步骤
1. 简明扼要地讲述清楚要研究的主题(如质量问题); 2. 确定该主题的主要类别,即主要的层次; 3. 构造树图,把主题放在左框内,主要类别放在右边的方框内; 4. 针对这个主要类别确定其组成要素和子要素; 5. 把针对每个主要类别的组成要素及其子要素放在主要类别右边的方
• 因果图常同排列图、对策表联合起来应用。
PPT文档演模板
qc4第三章因果图树图与
实例-噪声超标因果图
• 在提高135W电机的一次装机合格率时,运用因果图对 “噪声超标” 进行原因分析:
•人
•料
•装配经验不足
•外圆跳动大
•垂直度不够
•未按要求做
•转子部件
•端盖
•端盖的轴承室与 •轴承配合不当
•定、转子间 •的间隙小
PPT文档演模板
qc4第三章因果图树图与
第三节 关联图
• --关联图的用途: 1. 制定全面质量管理计划; 2. 制定质量方针; 3. 制定生产过程的质量改进措施; 4. 推进外购、外协件的质量管理工作; 5. 制定质量管理小组活动规划与目标展开; 6. 解决工期、工序管理上的问题; 7. 改进职能部门的工作; 8. 其他。
qc4-第三章____因果图 、树图与
PPT文档演模板
2020/11/3
qc4第三章因果图树图与
第一节 因果图
•应用因果图的步骤:
1) 简明扼要地规定结果,即规定需要解决的质量问题; 2) 规定可能发生的原因的主要类别,这时可以考虑下列因素作为因 素的主要类别:数据和信息系统、人员、机器设备、材料、方法、度 量和环境等; 3) 开始画图,把“结果”画在右边的矩形框中,然后把各类主要原 因放在它的左边,作为“结果”框的输入; 4) 寻找所有下一个层次的原因并画在相应的枝上,继续一层层地展 开下去。
框内;
6. 评审画出的树图,确保无论在顺序上或逻辑上都没有差错和空档。
PPT文档演模板
qc4第三章因果图树图与
画树ห้องสมุดไป่ตู้的注意事项
1. 用于因果分析的树图一般是单目标的,即一个质量问题用一张树图; 2. 树图中的主要类别一般可以不先从 5M1E 出发,而是根据具体的质
量问题或逻辑关系去选取。
PPT文档演模板
•刚性不够
•噪
•声
•超
•标
•环境噪声大
•轴承公差不合理
•转子外圆大
•工作间距小
PPT文档演模板
•设计
•环
qc4第三章因果图树图与
第二节 树图
• 树图又叫系统图。用来表示某个质量问题与其他组成要素之间的关 系,从而明确问题的重点,寻求达到目的所应采取的最适当的手段和措 施的一种树枝状图。
• 树图常用于单目标的展开。
PPT文档演模板
qc4第三章因果图树图与
第三节 关联图
• --应用关联图的步骤: 1. 确定要分析的“问题”。“问题”宜用简洁的“主语+ 谓语”的短 语表示,一般用粗线方框□ 圈起。一个粗方框只圈一个“问题”,多个 问题则应用多个方框圈起来。“问题”识别规则是“箭头只进不出”。 2. 召开诸葛亮会。与会者应用“头脑风暴法”就分析的“问题”充分 发表意见,找“因素”(手段)。 3. 边记录,边绘制,反复修改关联图。 4. 用箭头表示原因与结果(目的与手段)的关系;箭头指向是:原因 → 结果。 5. 原因要深入细致地分析,直至找出末端原因。末端原因应是可以直 接采取对策的原因,其识别标志是:箭头只出不进。
第三节 关联图
• --关联图又叫关系图。它是解决关系复杂、因素之间又相互关联 的原因与结果或目的与手段等的单一或多个问题的图示技术,是根据逻 辑关系理清复杂问题、整理语言文字资料的一种方法。
• --关联图的基本类型: 1. 中央集中型:把要分析的问题放在图的中央位置,把同“问题”发 生关联的因素逐层排列在其周围。 2. 单侧汇集型:把要分析的问题放在右(或左)侧,与其发生关联的 因素从右(左)向左(右)逐层排列。
• 一张完整的因果图展开的层次至少应有二层,一些情况下还可以有 三层以上。
PPT文档演模板
qc4第三章因果图树图与
第一节 因果图
•画因果图的注意事项:
1) 画因果图时必须开“诸葛亮会”,充分发扬民主,各抒己见,集思 广益,把每个人的意见都一一记录在图上; 2) 确定要分析的主要质量问题(特性)不能笼统,一个主要质量问题 只能画一张因果图,多个主要质量问题则应画多张因果图,因果图只能 用于单一目标的分析; 3) 因果关系的层次要分明,最高层次的原因应寻求到可以直接采取对 策为止; 4) 对分析出来的所有末端原因,都应到现场进行观察、测量、试验等 加以确认。
PPT文档演模板
qc4第三章因果图树图与
树图的主要用途
1. 企业方针目标实施项目的展开; 2. 在新产品开发中进行质量设计展开; 3. 为确保质量保证活动而进行的保证质量要素(事项)的展开; 4. 对为解决企业内质量、成本、产量等问题所采取的措施加以展开; 5. 企业承包责任制项目的展开; 6. 工序分析中对质量特性进行主导因素的展开; 7. 探求明确部门职能、管理职能和提高效率的方法; 8. 可以用于因果分析。
PPT文档演模板
qc4第三章因果图树图与
第三节 关联图
• --应用注意事项: 1. 用因果分析关联图时,“要因”必是由对其末端原因逐一经现场验 证并作出“标识”; 2. 图中一定有若干相互关联的因素。
PPT文档演模板
qc4第三章因果图树图与
演讲完毕,谢谢听讲!
再见,see you again
•原材料性能不稳定 •室温过高或过低 •卫生条件差
•子要素
•没定机、定人
•新调入人员经验少
•压力、温度、时间控制不严
•设备密封不严
•模具设计不合理
•模具厚度大
•电热板间垫层不匀
•毛坯厚度偏差大
•压辊调节不当
•混炼时间不统一
•塑化时间不统一
•杂质
•塑化时间不统一
•暖气片少
•没有排风设备
•工作台不洁
qc4第三章因果图树图与
qc4第三章因果图树图与
实例-塑料试片麻坑厚度超差龟裂因果分析数图
•主题
•试 •片 •麻 •坑 •厚 •度 •超 •差 •龟 •裂
PPT文档演模板
•主要类别 •组成要素
•人员 •设备 •工艺
•操作不熟练
•执行工艺不严 •压力不稳定 •模具不适 •电热板不平行 •毛坯质量差
•塑炼时间不准
•原料 •环境