橡胶与金属的粘合技术
丁腈橡胶和金属粘接方法
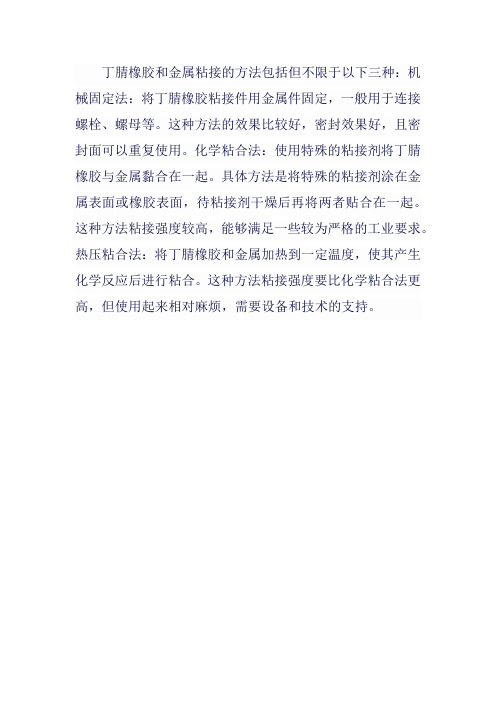
丁腈橡胶和金属粘接的方法包括但不限于以下三种:机械固定法:将丁腈橡胶粘接件用金属件固定,一般用于连接螺栓、螺母等。
这种方法的效果比较好,密封效果好,且密封面可以重复使用。
化学粘合法:使用特殊的粘接剂将丁腈橡胶与金属黏合在一起。
具体方法是将特殊的粘接剂涂在金属表面或橡胶表面,待粘接剂干燥后再将两者贴合在一起。
这种方法粘接强度较高,能够满足一些较为严格的工业要求。
热压粘合法:将丁腈橡胶和金属加热到一定温度,使其产生化学反应后进行粘合。
这种方法粘接强度要比化学粘合法更高,但使用起来相对麻烦,需要设备和技术的支持。
橡胶与金属热硫化粘接剂性能研究
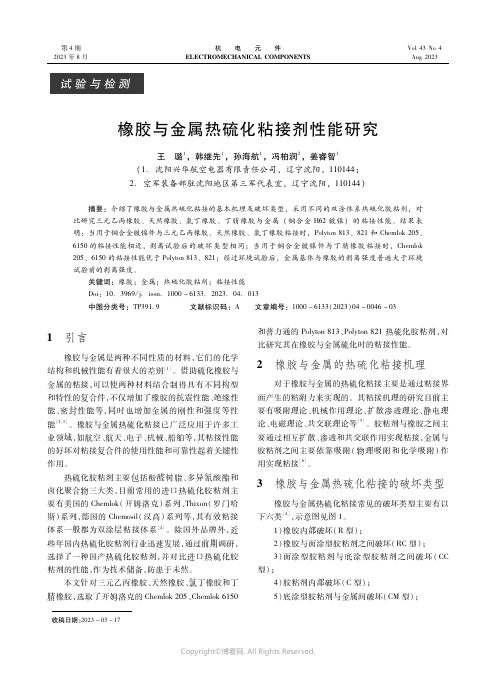
第4期2023年8月机电元件ELECTROMECHANICALCOMPONENTSVol 43No 4Aug 2023收稿日期:2023-03-17橡胶与金属热硫化粘接剂性能研究王 璐1,韩继先1,孙海航1,冯柏润2,姜睿智1(1.沈阳兴华航空电器有限责任公司,辽宁沈阳,110144;2.空军装备部驻沈阳地区第三军代表室,辽宁沈阳,110144) 摘要:介绍了橡胶与金属热硫化粘接的基本机理及破坏类型,采用不同的双涂体系热硫化胶粘剂,对比研究三元乙丙橡胶、天然橡胶、氯丁橡胶、丁腈橡胶与金属(铜合金H62镀镍)的粘接性能。
结果表明:当用于铜合金镀镍件与三元乙丙橡胶、天然橡胶、氯丁橡胶粘接时,Polyton813、821和Chemlok205、6150的粘接性能相近,剥离试验后的破坏类型相同;当用于铜合金镀镍件与丁腈橡胶粘接时,Chemlok205、6150的粘接性能优于Polyton813、821;经过环境试验后,金属基体与橡胶的剥离强度普遍大于环境试验前的剥离强度。
关键词:橡胶;金属;热硫化胶粘剂;粘接性能Doi:10.3969/j.issn.1000-6133.2023.04.013中图分类号:TP391 9 文献标识码:A 文章编号:1000-6133(2023)04-0046-031 引言橡胶与金属是两种不同性质的材料,它们的化学结构和机械性能有着很大的差别[1]。
借助硫化橡胶与金属的粘接,可以使两种材料结合制得具有不同构型和特性的复合件,不仅增加了橡胶的抗震性能、绝缘性能、密封性能等,同时也增加金属的刚性和强度等性能[2,3]。
橡胶与金属热硫化粘接已广泛应用于许多工业领域,如航空、航天、电子、机械、船舶等,其粘接性能的好坏对粘接复合件的使用性能和可靠性起着关键性作用。
热硫化胶粘剂主要包括酚醛树脂、多异氰酸酯和卤化聚合物三大类,目前常用的进口热硫化胶粘剂主要有美国的Chemlok(开姆洛克)系列、Thixon(罗门哈斯)系列,德国的Chemosil(汉高)系列等,其有效粘接体系一般都为双涂层粘接体系[4]。
谈橡胶材料与金属热硫化黏合

谈橡胶材料与金属热硫化黏合在现代社会各应用领域,,以高分子材料橡胶与不同种类金属生产金属黏合橡胶产品,越来越被广泛应用.因为有的配件结构设计,既要求具有橡胶的高弹性,又要求具有金属的刚性,这就需要橡胶与金属材料复合.众所周知,橡胶的杨氏模量约为IMPa,而金属材料的榻氏模量可达IOOOOoMPa.要使相对于金属,硬度低得多的有机高分子橡胶材质和高硬度金属粘合在一起,又能经得起要求的特定工况条件和介质的考验,而不会剥离,黏合工艺技术,则是最为关键.理想的黏合是要达到即使用强力把橡胶表层划坏了,底层橡胶依然紧紧粘贴在金属件表面.橡胶与金属热硫化型黏合,和橡胶与金属非硫化型”冷黏”,在黏合基理上有着明显不同,硫化型黏合,是通过热反应形成交联过程的化学反应.而非硫化型橡胶与金属黏合,则是与产生物理上表面张力现象有关.橡胶与金属热硫化黏合工艺,己有一百多年历史,从以硬质橡胶[硬度高的胶与金属黏合力优于硬度低的橡胶]或以^铜法[铜与天然橡胶黏合力较好]发展到用环化橡胶法,蛋白质法,配合炭黑配合法,多粘接层法,窗化橡胶法,酚醛树酯法和直至现在广为应用的异氟酸酯法和有机硅氧烷及有机钛酸酯法.在橡胶与金属热硫化黏合成各类制品中,最常用的橡胶是NR,SBR5NBR,CR,HNBR,FKM,MQ,EPDM等,与之相黏合的金属配件有铝件,铜件,铁件,铸铁件,不锈钢件等.这些金属配件在与橡胶黏合之前,都要对其表面进行处理.同时表面处理好与差,将直接影响橡胶与金属的粘合强度与耐久性,甚至使用寿命.因为从金属层面微观来看,金属表面层往往存在附有的油脂,锈斑,而金属下面一层则是O2,N2,CO2等各种气体的吸附层,再往下一层则是氧化层,而氧化层下还存在着一至十纳米厚的“拜耳贝层”,再其下是加工硬化层,在这几层之下,才露出“庐山真面目”--金属的基体.金属表面所存在的上述几层微观结构,都会影响橡胶与金属的热硫化粘合.而金属件的表面处理目的就是要改变其表面的结构状态,以获得清洁,干燥,粗糙和具有活性的新表面,有利于胶粘剂对金属件的浸润,扩散,和渗透.提高金属件与橡胶胶料之间的黏合强度和耐久性.一般使用丙酮,汽油脱脂,清洁,再用打磨喷砂除锈,还可用化学原理氧化还原反应,如酸蚀,磷化,阳极化处理,去除金属件污垢,活化和糙化金属件表面,利于黏合.在橡胶与金属热硫化使用的黏合剂方面,随着科学进步与发展,新型的黏合剂不断在开发,并形成了针对不同胶种,不同金属黏合的系列产品,但这些黏合剂虽然生产厂家不同,但基本包含下列组分.1,碳-卤素的离解能较低的含卤成膜聚合物2胶膜增塑剂,如极性弹性体丁碣橡胶,PVC,甲基乙烯基毗噬橡胶,以及不同卤化度的各类橡胶和酯3黏合增进剂,芳香族的硝基化合物,对醍二后与氧化剂并用,间苯二酚与六亚甲基四胺的分子络合物,及黏合活性的合成树脂和偶联剂.4,胺类,含氮化合物,金属氧化物等交联剂.5,热稳定齐IJ,如金属盐,环氧化合物,胺等.6,填充剂如炭黑,白炭黑等.7,混合有机溶剂.特别是含氯丁二烯的均聚物与氯化橡胶并用,能配制出对橡胶与金属件具有优良的黏合力的单堡层型胶黏剂.现时常用的橡胶与金属件黏合剂有单壅和双壅[底壅和面壅]之分,底壅胶中含有一些可以与金属表面形成坚固而又持久黏结的,易于形成薄膜聚合物,有利于与面壁胶黏合.而面壅胶中含有的聚合物既要与底壅相容,又要与胶料黏结.使用Ia化橡胶,可以屏障化学介质对黏结键的侵蚀.而面壅胶中含有高效硫化体系,它同时与黏合剂的聚合物及被黏胶料进行交联反应.单壅黏合剂生产操作相对简化,成本比双壅低,但双壅[底壅,面壅]持黏性及耐工况环境,相对比单堡略胜一筹.可根据实际情况选用单壅或底壅加面壁.对于配制橡胶与金属黏结的胶黏剂,技术含量高,工艺复杂,不如买商品化成品.如Chem1ok t TyIok j MetaIok j Thixon等公司制造的胶黏剂可靠性较好.可以根据模压方式[压缩,注射,转移]胶料品种,选择对应的专用黏合剂.并要按规定的操作方法去使用.橡胶与金属热硫化黏合,是一门复杂,多学科交叉的科学,它包含着橡胶物理化学,表面处理科学,冶金学,黏合科学,及橡胶加工热反应工程,涉及多种相互作用.在进行橡胶与金属热硫化黏结工艺流程中,必须要严格清洗处理,选对胶黏剂,调节好与之匹配的不影响黏合的胶料,掌握好全过程质量及工艺控制,不放过每一个细节,这样黏合才有保证.。
橡胶与金属骨架粘合失效原因分析及解决方法探讨资料
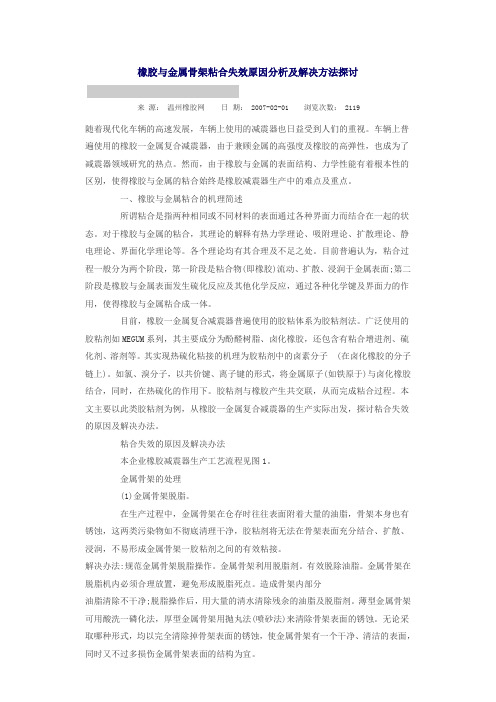
橡胶与金属骨架粘合失效原因分析及解决方法探讨来源:温州橡胶网日期: 2007-02-01 浏览次数: 2119随着现代化车辆的高速发展,车辆上使用的减震器也日益受到人们的重视。
车辆上普遍使用的橡胶一金属复合减震器,由于兼顾金属的高强度及橡胶的高弹性,也成为了减震器领域研究的热点。
然而,由于橡胶与金属的表面结构、力学性能有着根本性的区别,使得橡胶与金属的粘合始终是橡胶减震器生产中的难点及重点。
一、橡胶与金属粘合的机理简述所谓粘合是指两种相同或不同材料的表面通过各种界面力而结合在一起的状态。
对于橡胶与金属的粘合,其理论的解释有热力学理论、吸附理论、扩散理论、静电理论、界面化学理论等。
各个理论均有其合理及不足之处。
目前普遍认为,粘合过程一般分为两个阶段,第一阶段是粘合物(即橡胶)流动、扩散、浸润于金属表面;第二阶段是橡胶与金属表面发生硫化反应及其他化学反应,通过各种化学键及界面力的作用,使得橡胶与金属粘合成一体。
目前,橡胶一金属复合减震器普遍使用的胶粘体系为胶粘剂法。
广泛使用的胶粘剂如MEGUM系列,其主要成分为酚醛树脂、卤化橡胶,还包含有粘合增进剂、硫化剂、溶剂等。
其实现热硫化粘接的机理为胶粘剂中的卤素分子(在卤化橡胶的分子链上)。
如氯、溴分子,以共价键、离子键的形式,将金属原子(如铁原于)与卤化橡胶结合,同时,在热硫化的作用下。
胶粘剂与橡胶产生共交联,从而完成粘合过程。
本文主要以此类胶粘剂为例,从橡胶一金属复合减震器的生产实际出发,探讨粘合失效的原因及解决办法。
粘合失效的原因及解决办法本企业橡胶减震器生产工艺流程见图1。
金属骨架的处理(1)金属骨架脱脂。
在生产过程中,金属骨架在仓存时往往表面附着大量的油脂,骨架本身也有锈蚀,这两类污染物如不彻底清理干净,胶粘剂将无法在骨架表面充分结合、扩散、浸润,不易形成金属骨架一胶粘剂之间的有效粘接。
解决办法:规范金属骨架脱脂操作。
金属骨架利用脱脂剂。
有效脱除油脂。
四种橡胶与钢丝的黏合方法
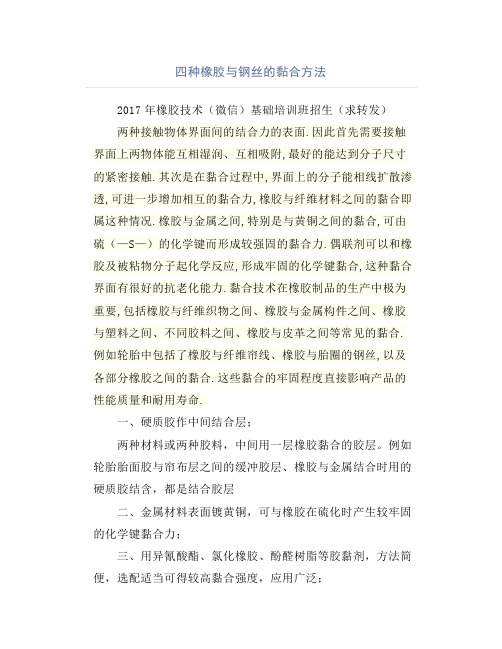
四种橡胶与钢丝的黏合方法2017年橡胶技术(微信)基础培训班招生(求转发)两种接触物体界面间的结合力的表面.因此首先需要接触界面上两物体能互相湿润、互相吸附,最好的能达到分子尺寸的紧密接触.其次是在黏合过程中,界面上的分子能相线扩散渗透,可进一步增加相互的黏合力,橡胶与纤维材料之间的黏合即属这种情况.橡胶与金属之间,特别是与黄铜之间的黏合,可由硫(—S—)的化学键而形成较强固的黏合力.偶联剂可以和橡胶及被粘物分子起化学反应,形成牢固的化学键黏合,这种黏合界面有很好的抗老化能力.黏合技术在橡胶制品的生产中极为重要,包括橡胶与纤维织物之间、橡胶与金属构件之间、橡胶与塑料之间、不同胶料之间、橡胶与皮革之间等常见的黏合.例如轮胎中包括了橡胶与纤维帘线、橡胶与胎圈的钢丝,以及各部分橡胶之间的黏合.这些黏合的牢固程度直接影响产品的性能质量和耐用寿命.一、硬质胶作中间结合层;两种材料或两种胶料,中间用一层橡胶黏合的胶层。
例如轮胎胎面胶与帘布层之间的缓冲胶层、橡胶与金属结合时用的硬质胶结含,都是结合胶层二、金属材料表面镀黄铜,可与橡胶在硫化时产生较牢固的化学键黏合力;三、用异氰酸酯、氯化橡胶、酚醛树脂等胶黏剂,方法简便,选配适当可得较高黏合强度,应用广泛;异氰酸酯是异氰酸的各种酯的总称。
若以-NCO基团的数量分类,包括单异氰酸酯R-N=C=O和二异氰酸酯O=C=N-R-N=C=O及多异氰酸酯等。
氯化橡胶是由天然橡胶或合成橡胶经氯化改性后得到的橡胶衍生产品,是橡胶领域中第1个工业化的橡胶衍生物,根据英国的资料,在为期30年的工业应用中,没有发生过一起因与氯化橡胶接触而引起的中毒事件L1。
氯化橡胶相对密度为1.596,其吸水率为0.1到0.3,热稳定温度为130℃,可溶于芳香烃、酯类、酮类、醚类、动植物油及氯化烃溶液中,但不溶于脂肪烃、醇类和水2。
工业用氯化橡胶一般呈白色或乳黄色粉末状、片状或纤维状,氯质量分数在62~65之间,具有较好的耐热性。
橡胶和金属的粘结技术

橡胶和金属的粘结技术橡胶和金属是两种不同性质的材料,将两者很好地粘接可以制得具有不同构型和特性的复合件,这种复合体系在工业中有着广泛的用途,如汽车工业、机械制造工业、固体火箭发动机的柔性接头、桥梁的支撑缓冲垫等。
橡胶与金属之间化学结构和力学性能巨大的差异,使获得具有高强度的粘接有着很大的困难。
研制出高性能粘接和适用范围更广的新型胶粘剂始终是研究的热点。
借助于胶粘剂在硫化过程中将橡胶与金属粘接起来是目前采用的基本方法之一。
本文将就其进展进行综述。
1金属-橡胶粘接体系发展现状橡胶与金属之间的粘接已有很久的历史,可以追溯到1850年,目前采用的粘接方法可分为直接粘接法、硬质橡胶法、镀黄铜法和胶粘剂粘接法。
直接粘接法工艺简单,操作方便,将粘接材料表面进行适当处理后直接在加热加压过程中实现粘接。
可通过在橡胶中加入一些组分、在胶料表面涂偶联剂或对对橡胶进行环化处理等来提高橡胶与金属的粘接性能。
尹寿琳、陈日生等在天然橡胶中加入多硫化合物粘合剂B和酸性化合物助剂C,用此粘合A3钢板作挖泥泵耐磨衬里,挖泥1000h以上未发现橡胶与金属脱开。
此法不足的是,处理的金属件要尽快与胶料粘接,以免金属表面深层氧化;在胶料中添加一些多价金属的有机盐和无机盐,虽可提高粘接效果,但会改变橡胶材料原先的物理机械性能,且造成出模困难。
硬质橡胶法是最古老的粘接体系,在金属表面贴一层硫磺含量较高的硬质胶料或一层硬质胶浆,通过硫化使橡胶与金属粘接起来,硬质橡胶法粘接力较强,工艺简便,适于粘接大型制件,但是不耐冲击和震动,60℃以上粘接强度发生显著下降。
镀黄铜法较硬质橡胶法有较好的耐高温性,黄铜或表面镀黄铜金属件不同胶粘剂,借助于被粘橡胶中的硫磺扩散到金属表面与CuO、ZnO结合形成界面粘接层与橡胶产生牢固粘合,至今在轮胎工业中钢丝圈的粘接、钢丝帘线与帘布层胶的粘接、内胎气门嘴的制造中仍采用此法。
胶粘剂法是目前应用最广和最有效的方法,已经历了酚醛树脂、多异氰酸酯、卤化橡胶、特种硫化剂的卤化橡胶、硅橡胶和水基胶粘剂等不同的发展阶段。
橡胶与金属的粘合是橡胶制品制造过程中的重要环节

橡胶与金属的粘合是橡胶制品制造过程中的重要环节,如果粘合不良或无法粘合,一些橡胶制品如轮胎、钢丝输送带、橡胶软管,橡胶骨架油封、汽门油封,橡胶金属组合垫圈、组合胶套等橡胶金属复合制品就无法制作。
就橡胶密封制品而言,上世纪80年代初,青岛密封件厂协同青岛化工厂研制成功了RM-1粘合剂,替代日本TD870成功生产出与国外同等水平的骨架油封,使引进的国外技术得以消化吸收,开辟了骨架油封制作的新工艺。
上世纪90年代,由于汽车工业的发展,不少厂家要求用氟橡胶制作骨架油封、汽车油封,但是粘合问题不好解决,严重的制约了该产品的开发,当时青岛双星集团密封件厂成功的研制了FG-1氟橡胶与黑色金属的热硫化粘合剂,使氟橡胶与金属骨架牢牢的粘合成一体,顺理成章的研发成功斯太尔发动机曲轴前后油封和气门油封替代了进口,满足了配套需要,该粘合剂一直使用至今。
因此橡胶与金属粘合是极其重要的应用技术,应引起生产企业的高度重视。
1 金属骨架的表面处理) 骨架表面无油污、无锈蚀,有一定粗糙度的新鲜表面才能有效的与金属粘合,因此骨架必须进行表面处理,处理大体有两种方法:一是机械法处理。
如采用履带式的抛丸清理机326或滚筒式的抛丸清理机Q3110,将粒径0.5mm的钢砂喷射到骨架表面,将表面的锈蚀等有害物料喷掉,使表面新鲜并增大表面积,加大骨架与胶粘剂间的接触面;二是化学法。
即酸洗处理,磷化钝化处理,其工艺过程是碱液去油,酸液去锈,磷化上磷化膜,然后进行钝化烘干,碱液是有多种材料如苛性钠、硅酸钠(表面湿润剂)、焦磷酸钠(阴离子表面活性剂)、烷基磺酸钠组成的水溶液,清洗温度80-90℃,时间视表面的油污多少而有差异,一般是5min左右。
去油污的骨架经流动的自来水冲洗后,进行酸洗处理,而不同的金属去锈时对酸的品种是有选择性的。
例如,铁件要用盐酸清洗处理。
铜件和不锈钢骨架采用硫酸、硝酸混合液协同去锈。
铝件用硫酸、铬酸混合液进行处理。
要求对周围环境不产生或少产生腐蚀时,而金属骨架锈蚀较轻的骨架,可采用以草酸为主,掺用少量硫酸和加入缓钝剂的水溶液进行处理。
橡胶金属硫化粘结
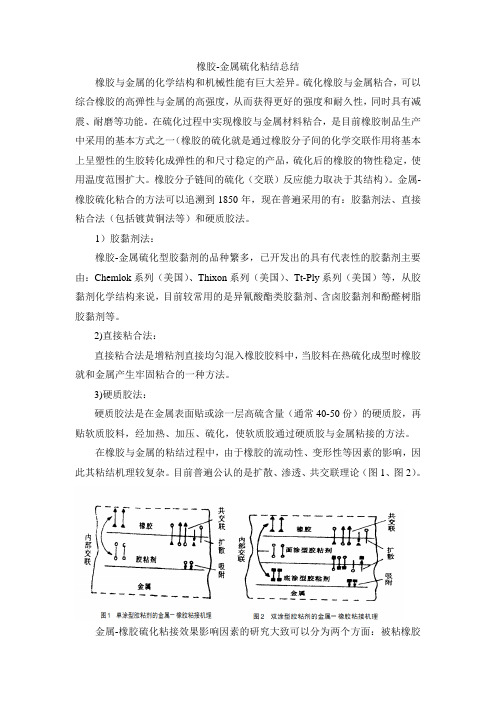
橡胶-金属硫化粘结总结橡胶与金属的化学结构和机械性能有巨大差异。
硫化橡胶与金属粘合,可以综合橡胶的高弹性与金属的高强度,从而获得更好的强度和耐久性,同时具有减震、耐磨等功能。
在硫化过程中实现橡胶与金属材料粘合,是目前橡胶制品生产中采用的基本方式之一(橡胶的硫化就是通过橡胶分子间的化学交联作用将基本上呈塑性的生胶转化成弹性的和尺寸稳定的产品,硫化后的橡胶的物性稳定,使用温度范围扩大。
橡胶分子链间的硫化(交联)反应能力取决于其结构)。
金属-橡胶硫化粘合的方法可以追溯到1850年,现在普遍采用的有:胶黏剂法、直接粘合法(包括镀黄铜法等)和硬质胶法。
1)胶黏剂法:橡胶-金属硫化型胶黏剂的品种繁多,已开发出的具有代表性的胶黏剂主要由:Chemlok系列(美国)、Thixon系列(美国)、Tt-Ply系列(美国)等,从胶黏剂化学结构来说,目前较常用的是异氰酸酯类胶黏剂、含卤胶黏剂和酚醛树脂胶黏剂等。
2)直接粘合法:直接粘合法是增粘剂直接均匀混入橡胶胶料中,当胶料在热硫化成型时橡胶就和金属产生牢固粘合的一种方法。
3)硬质胶法:硬质胶法是在金属表面贴或涂一层高硫含量(通常40-50份)的硬质胶,再贴软质胶料,经加热、加压、硫化,使软质胶通过硬质胶与金属粘接的方法。
在橡胶与金属的粘结过程中,由于橡胶的流动性、变形性等因素的影响,因此其粘结机理较复杂。
目前普遍公认的是扩散、渗透、共交联理论(图1、图2)。
金属-橡胶硫化粘接效果影响因素的研究大致可以分为两个方面:被粘橡胶配方和粘接工艺,在橡胶和金属的粘合过程中,工艺直接影响粘合强度。
工艺包括金属表面处理、硫化条件、镀层等。
橡胶与金属粘合时,不论采用什么方法,均要求对金属表面进行预处理,其目的在于清除金属表面的油污及氧化膜,使金属呈露新鲜表面,并进而适当改变金属表面的结构和极性,以便于它和胶黏剂或橡胶结合。
常用的处理方法有脱脂法、机械打磨法和化学处理法三种。
硫化条件是粘合工艺的核心部分,硫化温度是一个重要因素。
配方及工艺对橡胶与金属粘合性能的影响

题目:配方及工艺对橡胶与金属粘合性能的影响摘要文章综述了近十年来配方及工艺对橡胶与金属粘合性能的影响,橡胶与金属的发展现状、粘合基本原理及理论解释和粘合方法,从配方和工艺探讨橡胶与金属的粘合性能,针对橡胶与金属粘合过程出现的问题,分析粘合失效的类型和原因,并提出相应的解决对策。
AbstractThis article reviewed the formula and process over the past decade on the rubber and metal adhesion property, the development of rubber and metal status of the basic principles and theories to explain agglutinate and adhesive methods, from the formula and technology of adhesion property of rubber and metal for rubber to metal agglutinate process problem, analyze the types and causes of adhesion failure, and corresponded countermeasures.关键词:配方工艺胶黏剂橡胶与金属粘合Key word: Formula Technology Adhesive Rubber and metal Agglutinate目录引言 (1)1 橡胶与金属粘合发展现状 (2)2 粘合的基本原理和理论解释 (3)2.1 粘合的基本原理 (3)2.2 理论解释[3] (4)2.2.1 热力学理论 (4)2.2.2 吸附理论 (4)2.2.3 扩散理论 (5)2.2.4 静电理论 (5)3 橡胶与金属的粘合 (5)3.1 橡胶与金属的粘合方法 (5)4 配方对橡胶与金属粘合性能的影响[5] (6)4.1 橡胶材料对粘合性能的影响 (6)4.1.1 胶种 (7)4.1.2 硫化体系 (7)4.1.3 硫化剂 (8)4.1.4 增塑剂 (8)5 工艺对橡胶与金属粘合性能的影响[6] (9)5.1表面处理工艺 (9)5.1.1 抛丸工艺 (9)5.1.1.1抛丸时间 (10)5.1.1.2钢丸粒径 (10)5.2 磷化工艺 (11)5.2.1 磷化液的酸点对粘合性能的影响 (11)5.2.2 磷化时间对粘合性能的影响 (12)5.2.3 磷化温度对粘合性能的影响 (13)5.3 胶粘剂工艺对粘合性能的影响[7] (14)6 橡胶与金属粘合失效类型、失效分析以及解决对策[8] (14)6.1 橡胶与金属粘合失效类型 (14)6.2 橡胶与金属粘合失效的原因分析以及解决对策 (14)6.2.1底涂型胶粘剂与金属间破坏 (14)6.2.1.1金属表面处理不当 (14)6.2.1.2 胶粘剂选择不当 (15)6.2.1.3 涂胶工艺不当 (16)6.2.2 胶粘剂内部破坏、面涂型胶粘剂与底涂型胶粘剂之间破坏 (16)6.2.3 橡胶与面涂型胶粘剂之间破坏 (17)6.2.3.1 橡胶胶料不合适 (17)6.2.3.2 胶粘剂因素 (17)6.2.3.3 硫化工艺不合适 (18)6.2.4 橡胶内部破坏 (18)结语 (19)参考文献 (20)引言19世纪发明了用硫黄硫化橡胶,这种方法可以在许多领域使用。
氟橡胶与金属的硫化粘合

Viton®氟橡胶与金属的硫化粘合肖风亮机械科学研究院密封研究所(510700,,)摘要:讨论了Viton氟橡胶与金属的粘合,阐述了配方设计、粘合剂选择、骨架处理工艺方法、二段硫化、模腔压力等因素对粘合剂质量的影响。
分析了含一氧化铅难粘胶料的粘结方法关键词:氟橡胶,金属,粘合如果将金属表面作适当的处理并使用合适的粘合剂,就可实现氟橡胶与金属在模压硫化时获得良好的粘合效果。
对预混型氟弹性体(Viton E-60C,E-430,B-910)来说,要获得与金属良好的粘合效果,需要专门的配合才行。
下面就结合生产实际来阐述配合技术对粘合的影响。
以前专用于预混胶的硫化系统,现在可以用在所有的Viton®氟橡胶硫化系统中。
本文考察了硫化剂20#与硫化剂30#在Viton® A 和A-HV中所产生的影响。
金属的处理、粘合剂的选择、二次硫化条件均是影响良好粘合效果的重要的因素,本文也将分别给予详细的阐述。
在改善粘合性能方面,尤其针对难粘合应用方面,文中提供了一些技术数据。
这些应用包括低硬度或高硬度胶料、含有一氧化铅的胶料以及硫化过程中模腔压力较低时的情况。
1配方的影响1.1氧化镁/氢氧化钙酸吸收系统含硫化剂的氟橡胶通常与高活性氧化镁(一般为3份)和氢氧化钙(3~6 份)配合即可获得良好的贮存、加工与硫化性能。
然而采用这些酸吸收系统对于标准的粘合剂(例如Chemlok607或Chemosil511)来说,其粘合质量往往不均匀或者不理想,粘结状况取决于制品结构和生胶的选择。
采用高用量低活性氧化镁(15~17份)和低用量氢氧化钙(2份)能使绝大多数预混胶模压粘合性能获得改善。
以Viton E-60C、Viton E-430和Viton B-910为例,粘合性能的改善如表1所示。
4----橡胶撕裂100%3----橡胶撕裂>90%2----橡胶撕裂≧75%1----橡胶撕裂25%~50%0----橡胶撕裂<25%②Viton®E-60C采用标准的酸吸收系统的配方1A在轴密封件中表现出良好的结合,但在实际生产中,模压条件不适宜时并不常常是这样。
四种橡胶与钢丝的黏合方法

四种橡胶与钢丝的黏合方法
橡胶与钢丝的黏合方法主要有四种:机械黏合、冷胶黏合、热胶黏合
和化学黏合。
下面将详细介绍这四种黏合方法。
1.机械黏合
机械黏合是通过橡胶和钢丝之间的咬合或挤压来实现黏合的方法。
这
种方法通常使用钢丝缠绕在橡胶上,并通过机械力量使其与橡胶紧密结合。
机械黏合方法的优点是操作简单,黏结牢固,但容易造成钢丝与橡胶之间
的局部应力集中,容易导致接头的疲劳破坏。
2.冷胶黏合
冷胶黏合是将涂有特殊胶水的钢丝与橡胶进行黏合。
黏合过程中,首
先将钢丝涂上胶水,然后将橡胶放置在钢丝上,并施加适当的压力使其黏
合在一起。
冷胶黏合方法的优点是操作简单,工艺成熟,黏结牢固,但需
要胶水具有良好的粘接性能。
3.热胶黏合
热胶黏合是将钢丝和橡胶通过热胶进行黏合的方法。
黏合过程中,首
先将热胶涂在钢丝上,然后将橡胶与涂有热胶的钢丝加热,使热胶熔化并
与橡胶黏结在一起。
热胶黏合方法的优点是黏结牢固,耐高温性能好,但
操作复杂,需要控制好加热温度和时间,否则容易导致黏结不牢或橡胶烤焦。
4.化学黏合
化学黏合是通过其中一种化学物质将橡胶和钢丝黏合在一起的方法。
黏合过程中,首先将化学胶涂在钢丝上,然后将橡胶与涂有化学胶的钢丝
接触,通过化学反应使其黏合。
化学黏合方法的优点是黏结牢固,耐高温性能好,黏合面积较大,但需要选用合适的化学胶,并且操作复杂,需要控制好黏接条件。
以上是橡胶与钢丝的四种黏合方法。
每种方法都有各自的特点和适用范围,选择合适的黏合方法应根据具体的应用要求和材料特性来决定。
橡胶与金属骨架粘合失效原因分析及解决方法探讨
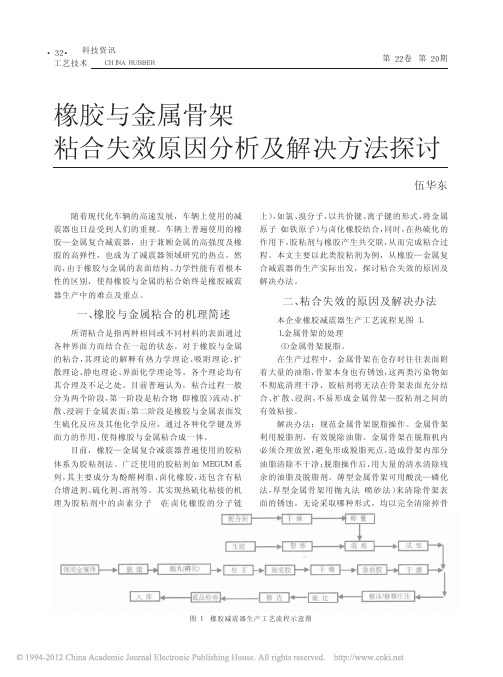
CHINARUBBER橡胶与金属骨架粘合失效原因分析及解决方法探讨伍华东随着现代化车辆的高速发展,车辆上使用的减震器也日益受到人们的重视。
车辆上普遍使用的橡胶—金属复合减震器,由于兼顾金属的高强度及橡胶的高弹性,也成为了减震器领域研究的热点。
然而,由于橡胶与金属的表面结构、力学性能有着根本性的区别,使得橡胶与金属的粘合始终是橡胶减震器生产中的难点及重点。
一、橡胶与金属粘合的机理简述所谓粘合是指两种相同或不同材料的表面通过各种界面力而结合在一起的状态。
对于橡胶与金属的粘合,其理论的解释有热力学理论、吸附理论、扩散理论、静电理论、界面化学理论等。
各个理论均有其合理及不足之处。
目前普遍认为,粘合过程一般分为两个阶段,第一阶段是粘合物(即橡胶)流动、扩散、浸润于金属表面;第二阶段是橡胶与金属表面发生硫化反应及其他化学反应,通过各种化学键及界面力的作用,使得橡胶与金属粘合成一体。
目前,橡胶—金属复合减震器普遍使用的胶粘体系为胶粘剂法。
广泛使用的胶粘剂如MEGUM系列,其主要成分为酚醛树脂、卤化橡胶,还包含有粘合增进剂、硫化剂、溶剂等。
其实现热硫化粘接的机理为胶粘剂中的卤素分子(在卤化橡胶的分子链上),如氯、溴分子,以共价键、离子键的形式,将金属原子(如铁原子)与卤化橡胶结合,同时,在热硫化的作用下,胶粘剂与橡胶产生共交联,从而完成粘合过程。
本文主要以此类胶粘剂为例,从橡胶—金属复合减震器的生产实际出发,探讨粘合失效的原因及解决办法。
二、粘合失效的原因及解决办法本企业橡胶减震器生产工艺流程见图1。
1.金属骨架的处理(1)金属骨架脱脂。
在生产过程中,金属骨架在仓存时往往表面附着大量的油脂,骨架本身也有锈蚀,这两类污染物如不彻底清理干净,胶粘剂将无法在骨架表面充分结合、扩散、浸润,不易形成金属骨架—胶粘剂之间的有效粘接。
解决办法:规范金属骨架脱脂操作。
金属骨架利用脱脂剂,有效脱除油脂。
金属骨架在脱脂机内必须合理放置,避免形成脱脂死点,造成骨架内部分油脂清除不干净;脱脂操作后,用大量的清水清除残余的油脂及脱脂剂。
橡胶及金属的粘合

橡胶与金属的粘合在汽车工业中,橡胶与金属的粘合是很普遍的,骨架油封、发动机及变速箱支承、摆壁衬套、车身支撑等都是典型的金属——橡胶结构。
金属和橡胶的结合强度对产品的性能有着至关重要的影响。
金属橡胶件的寿命很大程度上取决于两种材料的粘接质量。
粘接技术因此成为许多工厂的研究课题。
众所周知,增大粘接面的表面积及静电吸附力、提高粘接材料之间的化学作用力是获得高粘接强度的关键。
本文通过对金属粘合表面不同处理工艺的试验,得出了操作方便、经济性好、粘接性能优异的骨架表面处理方法。
一、实验1.主要材料CHEMLOK 252上海洛德公司产品;CHEMLOK 205上海洛德公司产品;10#钢;20目石英砂;天然胶SCR5海南天然胶联合产业集团;丁腈胶N41兰州化学工业公司。
2.设备普压干喷砂机(空气压力>0.6MPa);磷化处理线;400×400电热平板硫化机;0-200℃老化箱;0-2500N电子拉机。
3.粘接橡胶基本配方天然胶SCR5 100;硬脂酸1;氧化锌(间接法)5;防老剂3;防护蜡4;软化剂10;炭黑70;硫黄2;促进剂1.5。
丁腈胶N41 10;硬脂酸1;氧化锌(间接法)5;防老剂3;聚酯增塑剂10;炭黑60;DCP 1.5;硫黄0.5;促进剂1.5。
粘合剂:①单涂氧化锌(间接法);②底涂CHEM-LOK 205,面涂CHEMLOK 252。
4.粘接橡胶的常规机械性能天然胶邵尔A型硬度65度,拉伸强度22MPa,拉断伸长率450%。
丁腈胶邵尔A型硬度70度,拉伸强度24MPa,拉断伸长率340%。
5.试样制备①在K360×160开放式炼胶机上将配方物料混合均匀;②试块表面处理;③在400×400电热平板硫化机上压制试样;④试样制备工艺。
NR硫化工艺条件为155℃×6min。
NBR硫化工艺条件为160℃×6min。
6.测试按GB/T 13936标准对已硫化的试样进行测试。
金属包胶工艺流程
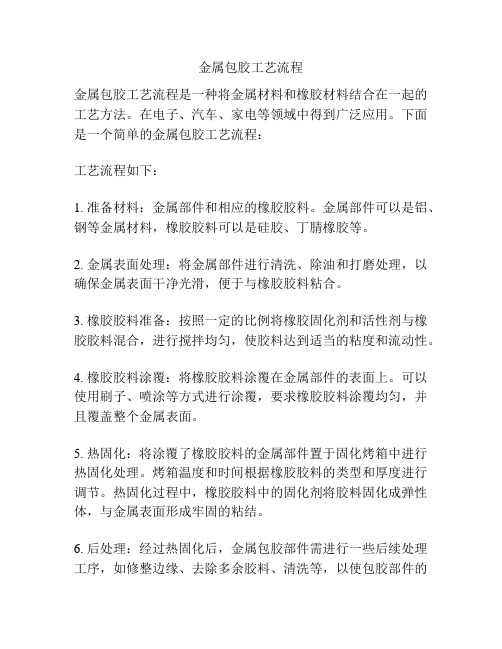
金属包胶工艺流程
金属包胶工艺流程是一种将金属材料和橡胶材料结合在一起的工艺方法。
在电子、汽车、家电等领域中得到广泛应用。
下面是一个简单的金属包胶工艺流程:
工艺流程如下:
1. 准备材料:金属部件和相应的橡胶胶料。
金属部件可以是铝、钢等金属材料,橡胶胶料可以是硅胶、丁腈橡胶等。
2. 金属表面处理:将金属部件进行清洗、除油和打磨处理,以确保金属表面干净光滑,便于与橡胶胶料粘合。
3. 橡胶胶料准备:按照一定的比例将橡胶固化剂和活性剂与橡胶胶料混合,进行搅拌均匀,使胶料达到适当的粘度和流动性。
4. 橡胶胶料涂覆:将橡胶胶料涂覆在金属部件的表面上。
可以使用刷子、喷涂等方式进行涂覆,要求橡胶胶料涂覆均匀,并且覆盖整个金属表面。
5. 热固化:将涂覆了橡胶胶料的金属部件置于固化烤箱中进行热固化处理。
烤箱温度和时间根据橡胶胶料的类型和厚度进行调节。
热固化过程中,橡胶胶料中的固化剂将胶料固化成弹性体,与金属表面形成牢固的粘结。
6. 后处理:经过热固化后,金属包胶部件需进行一些后续处理工序,如修整边缘、去除多余胶料、清洗等,以使包胶部件的
外观和质量得到改善。
以上是金属包胶工艺流程的基本步骤。
在实际应用中,还需要根据具体的要求进行调整和改进,以确保包胶部件的质量和性能满足需求。
- 1、下载文档前请自行甄别文档内容的完整性,平台不提供额外的编辑、内容补充、找答案等附加服务。
- 2、"仅部分预览"的文档,不可在线预览部分如存在完整性等问题,可反馈申请退款(可完整预览的文档不适用该条件!)。
- 3、如文档侵犯您的权益,请联系客服反馈,我们会尽快为您处理(人工客服工作时间:9:00-18:30)。
橡胶与金属的粘合技术
橡胶与金属的粘合技术
粘合剂分类:1.溶剂型:如CH205、CH252、CH220(用酮、苯为溶剂)
2.水性:如E1542 (运输存储较困难、有良好的模具耐脏性,环保型)
3.环保型:CH6100、CH6109、2000TEF(不含重金属、不产生臭氧化合物、不含氯化溶剂)
粘合剂涂层的组成和作用:
♣底胶:提供腐蚀环境的耐抗性、提供与金属高强度的附着力和面胶的化学粘结性
♣面胶:用于弹性体与底胶的粘结、提供弹性体与金属的充分附着(经验法则单涂的效果通常不如双涂的效果)、提供对外部环境长期耐久性的屏障、提供必要的抗磨性。
♣单涂:用于特种胶如MVQ、FKM、HNBR等粘合,能提供较薄且坚硬的漆膜、且无色,用于有色弹性体,提供较高的耐热和抗溶剂性、抗腐蚀性。
粘结性能的影响因素:
♣弹性体选择
橡胶的硬度♣
碳黑用量和类型♣
抗氧化物/Antiozonants♣
♣硫化剂
混合硫化
增塑剂用量和类型
3.粘合剂的组成:
溶剂:78-72%;树脂、聚合物、反应性固体:22-28%
没有溶剂或水的蒸发,固体的含量不会增加;
注意:
♣客户不允许任意混合的不同牌号的粘合剂;
粘合剂的溶剂量按以下排列:刷涂= 滚涂<浸涂<喷涂;♣
♣固体含量是影响黏度的因数之一;
溶剂与固体含量是否充分混合,第一次使用前是否充分搅拌;♣
♣稀释液必须是和粘合剂中的固体有兼容性的溶剂;
总是将溶剂加入粘合剂而不能相反,加入溶剂时必须搅拌;♣
♣在通风的地方转移溶剂;
必须能秤重式测量体积;♣
酮类和酒精应是高等级水含量少的溶剂;♣
♣涂了粘合剂的金属工件在热模具中时间应相对多于橡胶;
♣预烘的时间越久,模具消耗和积聚的化学活性就越多,这就相应减少用于粘结橡胶化合物的活性;
♣如果粘合剂中的交联剂在预烘中遗失和释放,那么橡胶和金属粘结会失败;
♣如果粘合剂化学成分活性太高或容易焦化,与橡胶的硫化不匹配,也会造成粘结失败。
粘合剂的使用方法:
♣黏度由黏合剂中的固体成分和各成分间的相互作用决定。
沉积在硬基体上的固体数量决定了干膜厚度。
♣
♣稀释剂改变黏合剂的固体单位含量。
固体含量高的黏合剂比固体含量低的黏合剂更容易得到厚的干膜♣
♣黏合剂的反应性固体,在储藏期间会沉积在桶的底部。
黏合剂含聚合物,树脂和溶剂,在储藏期间会分开。
♣
♣使用前进行充分的搅拌是非常重要的,确保固体,聚合物和树脂被搅拌均匀。
如果不经充分搅拌,产品可能不起作用。
♣
♣粘度的测定应在21℃时测定
♣干膜厚度的确定:底胶:0.2-0.4千分之一寸;面胶:0.5-1.0千分之一寸;单涂:0.8-1.5千分之一寸。
♣粘度的确定:刷涂:底胶(原液)不稀释;面胶(原液)不稀释;
浸涂:底胶:8.5-9.5秒;面胶12.5-13.5秒(2号杯)
喷涂:低胶:9-11秒;面胶:11-16秒(2#杯)
透明的特殊黏合剂(硅烷基) 比较典型,干膜厚度太薄,比较难以测量。
♣
♣面涂的干膜厚不够会造成不能提供足够的黏接力黏接橡胶混合物导致橡胶黏接失败。
♣面涂过厚的干膜会造成在黏合剂内部产生多个膜层,从而导致黏接失败。
粘合剂三种涂布方法:
■喷涂:1. 可以安装一个特殊的空气过滤器来过滤压缩机里产生的油和水,对喷枪进
行相关的检查。
正确的喷涂方法:★移动喷枪时避免产生弧度,保持喷枪和目标的距离一致。
★喷涂时喷枪应前后移动,移动时保持喷枪和目标0.8-1.0英尺的距离
■刷涂:★在通风的区域中刷涂
★刷涂的缺点是不同操作员造成的结果可能是不一致的
★选择天然的聚毛刷子能够耐溶剂
★不要使用泡沫刷子和塑料刷子
★一个刷子只用于一种产品,防止交叉污染。
■浸涂:★不能选择金属复盖区域。
★金属部件的凹孔或沟的周围黏合剂的附着会有变化,易堆积。
储存:涂布后的粘合剂应在较短的时间内使用完,因为它的粘结力是随储存时间的延长而下降的。
橡胶金属粘合失效模式和结果分析:
1. 发生于第一涂层(底胶)和金属表面的粘结失效
▲已清洁的金属久置生产绣
▲磷化时造成闪绣
▲喷沙周期不够
▲喷沙压力不够或涂胶前金属上残留喷沙介质
▲喷沙设备故障
▲车间灰尘太重,空气被污染
▲磷化等经处理的金属骨架未涂粘合剂过期储存
▲磷化膜晶体破坏
▲粘合剂在初期或使用中未正确混合(搅拌)
▲不正确的稀释量或用不正确的溶剂来稀释
▲膜层太薄,不能完全覆盖于目标粘合区
▲粘合剂未充分干燥
▲底层粘合剂忘记涂布或错误的选择底层粘合剂
▲骨架上残留有金属冷却液、污垢
▲返工骨架原底层残留的粘合剂未彻底清理干净
2.发生于涂层(底胶)与涂层(面胶)或涂层(面胶)与橡胶间的粘结失效:▲粘合剂被污染
▲粘合剂与溶剂未充分混合
▲模温偏低,不能激活粘合剂
▲在传递(如注压)或加工中橡胶被部分硫化
▲已涂粘合剂的骨架超过储存期限
▲已涂粘合剂的骨架被污染
▲粘合剂膜层不恰当或使用过期的粘合剂
▲选用了不正确的粘合剂与弹性体不匹配
▲在橡胶转移(如注压)过程中,粘合剂被脱离(冲刷)
▲粘合剂在喷涂时,混入了油污染的空气
▲选择了错误的脱模方式
▲模温过高造成粘合剂早期交联,造成脱胶。
▲粘合剂在储存、转运过程中被磕碰。
环保健康安全
▲避免皮肤和眼睛接触:
▲避免蒸汽或水沫雾的吸入:
▲避免吸入溶剂
▲喷涂粘合剂的地方要求排气通风
▲吃饭,抽烟前洗手。
▲远离热,电源,火花,明火和其他火的来源
▲置于通风良好的区域
▲当不在使用中的时候,密闭容器
▲在一个凉爽的、干燥、和通风良好的区域中储存黏合剂。
▲倒溶剂及黏合剂时避免静电产生。