降低企业生产成本与消除浪费控制-培训资料
企业精益生产精细化管理培训降低成本提高效益PPT模板

3.标准化任何人都可以操作的简单作业
4.训练员工成为掌握多种技能的能手 5.摒弃以工程定员的思想
推进 顺序
3
多工程操作
为了对应市场不断变化的要求,力求以更少的 人对应生产,以降低成本
推进 顺序
4
站立作业要彻底实施 04
01 1.明确划分人与机械的工作,作业
者尽可能让机器独立作业,人与机 械保持分离状态
精益生产的意义
r请e添a加d您y的 标 题
·精益生产是一套系统的以创造价 值为目标的方法,这套方法通过减 少浪费以实现提高速度、降低成 本的目的.
·精益生产是一种制造哲学,它通 过减少浪费来缩短从客户下单到 交付之间的时间.
03
精益生产的七大浪费
请添加你的标题的关键字;请添加你的标题的关键字;请添加 你的标题的关键字;请添加你的标题的关键字;
04 如何做精益生产
平准化
计划安排好出产产品的品种、数量的时间及种类
推进 顺序
6
02
以“循环钟”为基本作成周期 表
04
生产流程标准化
01
将月产量、日产量换算成循 环时间(循环钟)
03
缩短变化准备及零件更换(机种 切换)的时间
04 如何做精益生产
1.准备时间:内部准备时间+外部准备时间 2.需彻底实施5S基础
推进 顺序
9
看板管理
是作业指示及零件调配的依据
1.后工序至前工序拿取已被前工序用毕的看板 2.前工序只要生产后工序取去的数量 3.看板与现品一起流动,彻底执行目视管理 4.为避免生产误失,消除浪费,生产实施平准化 5.尽量减少看板的数量
1.以红牌与看板作战进行目视的整理、整顿 2.利用指示灯传达工程异常、零件供应、刀具
消除生产中的8大浪费培训教材PPT课件讲义
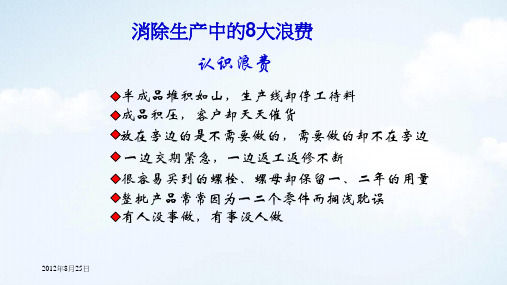
过剩的加工造成浪费
常见的加工浪费: ☆ 加工余量
☆ 过高的精度 ☆ 不必要的加工
过剩加工造成的浪费: ☆ 设备折旧 ☆ 人工损失
☆ 辅助材料损失 ☆ 能源消耗
2012年8月25日
库存 浪费
库存造成额外成本
常见的库存: ☆ 原材料、零部件
☆ 半成品 ☆ 成品 ☆ 在制品 ☆ 辅助材料 ☆ 在途品
库存的危害: ☆ 额外的搬运储存成本
消除生产中的8大浪费 认识浪费
半成品堆积如山,生产线却停工待料 成品积压,客户却天天催货 放在旁边的是不需要做的,需要做的却不在旁边 一边交期紧急,一边返工返修不断 很容易买到的螺栓、螺母却保留一、二年的用量 整批产品常常因为一二个零件而搁浅耽误 有人没事做,有事没人做
2012年8月25日
浪费新定义
除了使产品增值所需的材料,设备和人力资源之绝对最小量以外的东西
任何非必需的东西!
认识和消除所有浪费
2012年8月25日
等待浪费 搬运浪费
地下工厂
8 不良浪费
工
大 厂
动作浪费
常
浪 见
加工浪费
费 的
库存浪费
企业每生产一件产品就在制造一 份浪费。伴随企业运营中各业务 环节不被察觉或不被重视的浪 费,日本企业管理界将之形象地 比喻为“地下工厂”。
制造过多(过早)浪费
缺货损失
2012年8月25日
等待 浪费
2012年8月25日
等待பைடு நூலகம்创造价值
常见的等待现象: ☆ 物料供应或前工序能力不足造成待料
☆ 监视设备作业造成员工作业停顿 ☆ 设备故障造成生产停滞 ☆ 质量问题造成停工 ☆ 型号切换造成生产停顿
造成等待的常见原因: ☆ 线能力不平衡
TPS(JIT) 生产方式培训资料

TPS(JIT) 生产方式培训资料TPS(JIT)生产方式培训资料(一)本文旨在介绍TPS(JIT)生产方式的培训资料,包括其基本概念、主要原则以及实施过程。
希望通过本文的阅读,能让读者对TPS(JIT)生产方式有更深入的了解,并能够在实践中应用这一生产方式,提高生产效率和质量。
一、什么是TPS(JIT)生产方式TPS(Toyota Production System,丰田生产方式),又称JIT (Just-in-Time)生产方式,是丰田汽车公司发展而来的生产方式,其核心理念是"同时制造,零库存"。
其主要目标是通过消除浪费、优化生产流程,以实现缩短生产周期、减少库存、提高质量和降低成本等效果。
二、TPS(JIT)生产方式的原则1. 浪费的消除TPS(JIT)生产方式强调消除各类浪费,包括过产、等待、运输、库存、过程中的损耗和不合格品等。
通过减少这些浪费,企业可以提高生产效率、降低成本、优化资源利用。
2. 拉动式生产TPS(JIT)生产方式以顾客需求为导向,采取拉动式生产,即按照订单来生产产品,避免过去的"推动式"生产方式中产生的过剩和库存。
拉动式生产可以提高生产的敏捷性,降低产出的滞后性。
3. 灵活性和变动适应性TPS(JIT)生产方式要求企业具备灵活性和变动适应性,即能够及时调整生产线,以适应市场需求的快速变化。
通过灵活的生产方式,企业可以减少因生产周期长、库存过多而导致的资源浪费。
4. 经济批量和小批量化生产TPS(JIT)生产方式倡导经济批量和小批量化生产,通过灵活的生产线布局和合理的生产计划,实现生产成本的最优化。
5. 高质量和持续改进TPS(JIT)生产方式注重产品质量,强调全员参与质量控制,通过改善生产工艺,提高产品质量。
同时,TPS(JIT)生产方式倡导持续改进,不断挑战和提高自身的生产能力和竞争力。
三、TPS(JIT)生产方式的实施过程1. 价值流分析价值流分析是TPS(JIT)生产方式实施的基础,通过对生产过程中每个环节的价值创造和浪费进行分析,找出存在的问题,确定改进方向。
5S及消除浪费的培训资料

2
3
1
2
A
区域
号
单元
[A32]A区3单元2号
「哪里」, 「什么」, 「多少」要明确这三个, 做标牌、标签!
5. 物品保管方法 「3定原则 」
标牌战略 (可视化整顿 )
设备
库存
设备目录标示
多少[定量]数量标示
【 5-Why 】
☞ 5-Why是对问题指出疑问,反复地, 5次以上,找出根源。这个5次的次数是代表性的,而不是必须要做5次以上的指标,重点是找出问题的根源。
问题是什么? ………… 为什么这样? ……………
2. 现场观察方法
单纯动作或者附加动作是容易分别出发现的,即可改善。
Ⅱ. 显出浪费的活动
“ 发现浪费是从意识改革。。。" 没有思考转换发现浪费是不可能的。 目前的思考方式、基准白纸化。
1现 : 去现场2现 : 看现物3现 : 掌握现象
生产现场发生的问题,解决方案都在生产现场。
发现浪费 Point
1) 3现的原则
坐在办公桌子上判断现场的问题,建立改善对策,这样的话,很容易误导问题点,更是引起更多的问题,因此,必须到现场看现实现象掌握现场是最重要的。
程序5: 肉眼分别出做得好不好-可视化【习惯化】
区分 表示纵横方向的地址。 3定, 标牌, 定位置
准备: 拍下目前的我们的样子! 【现况】
2. 进行程序
3. “3定”是什么?
谁都及时
看明白
回放
找到
3定
标准化
【 定位置 】 - 参考4
【 定品 】 在那里摆放的物品,你能否分别出什么物品?<Point> 单位物品标签 存放架子上标签 方便更换标签 方便变更存放位置
如何降低生产成本培训课件
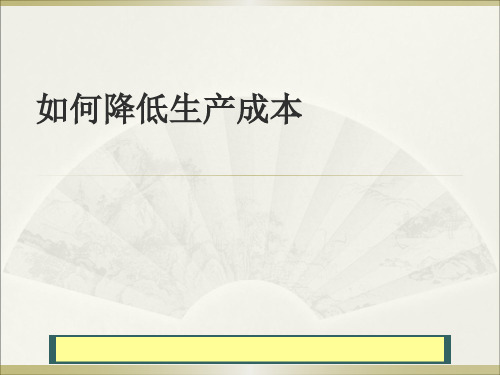
提案改善制度的意义
利用全体员工的____来推动 及改善公司的经营体质,以 分享公司成长及员工福利的 双重利益。
提案来自…
1.对每一项工作或动作都表示怀疑,并 从多方面深入观察。
(以chip电容之电极为例) ③家电外壳以塑钢/PVC等取代钢板
生產制程用料成本差异
①制造品质不良:重工多 ▪ 作业员责任(作业疏失) 对策:作业标准化/制程稽核/防呆工作设计/IPQC实施 ▪ 生产设备制程能力偏失(参数调整)
②投产用料品质变异
▪ 进料时品质就已不良 对策:供应商现场稽核、辅导改善、进料时作IQC检验。
■管理费用 非制造单位之间接员工薪资、伙食、福利、利息、 租税及杂项等相关之费用。
生产成本的结构
生产成本=
直接材料 +
直接人工 +
制造费用
生产成本的内涵
1.直接材料:一般企业,原材料大约为总成本的50%~70%,在成本 结构中所占的比例最大
2.直接人工:直接人工约占总成本的10%~20%,是削减成本的第二 大目标
3.间接人工:人数虽较直接人工少,但工资水平却较直接人工高, 对公司无直接产出
4.制造费用: A.厂房、设备折旧:属于固定资产,投资是否合理,将决定 费用的多寡 B.水及电力费用:使用节电的设备或采取省电措施来降低费用 C.厂房、设备维修费用:厂房越大,设备越多、越精密、功能 越多,维修的费用就越高 D.燃料费:设备的可动率、生产效率皆影响燃料费用的多寡
成本控制的重点
B.容许成本目标的成本管理实施的步骤
1.售价的确认 2.算出目标利益 3.算出容许总成本 4.算出容许一般管理费、销售所需的费用 5.算出制造成本 6.具体展开
迅速降低企业生产成本与消除浪费技巧陈鹏(推荐阅读)
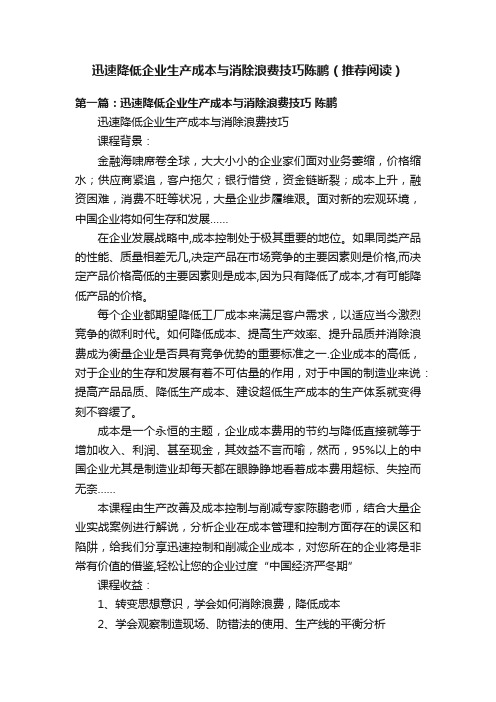
迅速降低企业生产成本与消除浪费技巧陈鹏(推荐阅读)第一篇:迅速降低企业生产成本与消除浪费技巧陈鹏迅速降低企业生产成本与消除浪费技巧课程背景:金融海啸席卷全球,大大小小的企业家们面对业务萎缩,价格缩水;供应商紧追,客户拖欠;银行惜贷,资金链断裂;成本上升,融资困难,消费不旺等状况,大量企业步履维艰。
面对新的宏观环境,中国企业将如何生存和发展……在企业发展战略中,成本控制处于极其重要的地位。
如果同类产品的性能、质量相差无几,决定产品在市场竞争的主要因素则是价格,而决定产品价格高低的主要因素则是成本,因为只有降低了成本,才有可能降低产品的价格。
每个企业都期望降低工厂成本来满足客户需求,以适应当今激烈竞争的微利时代。
如何降低成本、提高生产效率、提升品质并消除浪费成为衡量企业是否具有竞争优势的重要标准之一.企业成本的高低,对于企业的生存和发展有着不可估量的作用,对于中国的制造业来说:提高产品品质、降低生产成本、建设超低生产成本的生产体系就变得刻不容缓了。
成本是一个永恒的主题,企业成本费用的节约与降低直接就等于增加收入、利润、甚至现金,其效益不言而喻,然而,95%以上的中国企业尤其是制造业却每天都在眼睁睁地看着成本费用超标、失控而无奈……本课程由生产改善及成本控制与削减专家陈鹏老师,结合大量企业实战案例进行解说,分析企业在成本管理和控制方面存在的误区和陷阱,给我们分享迅速控制和削减企业成本,对您所在的企业将是非常有价值的借鉴,轻松让您的企业过度“中国经济严冬期”课程收益:1、转变思想意识,学会如何消除浪费,降低成本2、学会观察制造现场、防错法的使用、生产线的平衡分析3、学会识别、分析、解决问题的能力4、明确企业现场中的常见的浪费、掌握现场改善的有效方法5、普及学习和应用IE手法,提高生产效率和质量6、将IE技术与管理有机的结合,压缩成本,追求生产系统整体优化和效率的提升7、了解成本管理对利润增长的现实意义8、熟悉工厂成本的构成,树立强烈的成本意识及持续改善的目标;9、掌握工厂成本管理实战技巧,为您的企业找到降低生产成本的可行方案。
(1)迅速降低企业成本与消除浪费技巧
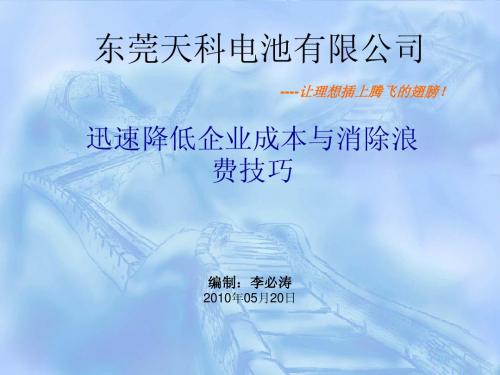
东莞天科电池有限公司
----让理想插上腾飞的翅膀! 让理想插上腾飞的翅膀!
迅速降低企业成本与消除浪 费技巧
编制: 编制:李必涛
2010年05月20日
目录
第一部分:如何降低采购成本 第二部分:如何降低生产成本 第三部分:如何降低品质成本 : 第四部分:如何降低仓库成本 第五部分:如何降低管理成本
第一部分
第三部分
如何降低品质成本
现场质量问题案例分析
差不多就行了何必那么精细?
现场质量问题案例分析
我只负责做,质量是检验员的事?
现场质量问题案例分析
我以为应该这么做?
现场质量管理问题案例分析
我刚来不知道怎么做?
现场质量问题案例分析
下次再出现类似的问题就罚你?
现场质量问题案例分析
这个问题不属于我管?
开发新的优质供应商; 寻找新的可能替代材料; 建立合理的仓储量; 合理的供货方式
降低采购成本的途径有哪些?
VA:Value analysis(价值分析) VE:value engineering (价值工程) 提高产品性价比,优化设计降低成本
降低采购成本的途径有哪些?
Negotiation (谈判) Quality(质量) Delivery( Delivery(货期) Cost(价格) Service(服务)
—样品控制
如何有效降低半成品库存?
1.源头控制---材料 2.生产过程的跟踪与统计
如何有效降低材料库存?
安全库存如何设置? 如何降低安全库存? 仓库账、物管理 JIT准时采购
第五部分
如何降低管理成本
精益生产之七大浪费培训资料

影响:增加成本、降低生产效率、影响产 品质量 单击此处输入你的正文,请阐述观点
案例分析:某企业精益生产实践案例 单击此处输入你的正文,请阐述观点
影响:增加运输成本、降低生产效率、影 响产品质量 精益生产之七大浪费培训资
培训效果评估:通过问卷调查、考试等方 式对培训效果进行评估 单击此处输入你的正文,请阐述观点
影响:增加生产成本,降低生产效率,影 响产品质量 精益生产之七大浪费培训资
料 精益生产之七大浪费培训资料
产生原因及影响:针对每种浪费进行深入 分析,提出改进措施
单击此处输入你的正文,请阐述观点
案例分析:分享成功案例,总结经验教 训
单击此处输入你的正文,请阐述观点
生产计划安排不合理
生产设备故障或维护 不当
生产流程不顺畅或瓶 颈问题
员工技能不足或操作 不当
物料供应不及时或短 缺
质量检查不合格或返 工返修
运输距离过长或运输 方式不当
产生原因:生产流程设计不合理、生产计 划安排不当、物料摆放不规范等 单击此处输入你的正文,请阐述观点
过量生产浪费产生原因及影响
影响:增加库存成本、降低设备利用率、增加搬 运和运输成本等 过量生产浪费产生原因及影响
过量生产浪费产生原因及影响
影响:增加库存成本、降低设备利用率、增加搬 运和运输成本等 过量生产浪费产生原因及影响
过量生产浪费产生原因及影响
影响:增加库存成本、降低设备利用率、增加搬 运和运输成本等
• 七大浪费产生原因及影响:不良品浪费产生原因及影响、过量的生产浪费产生原因及影响、 过多的库存浪费产生原因及影响、不必要的运输浪费产生原因及影响、不必要的人员浪费产 生原因及影响、等待时间的浪费产生原因及影响、过度加工的浪费产生原因及影响
管理资料-如何降低生产成本培训PPT课件讲义教材
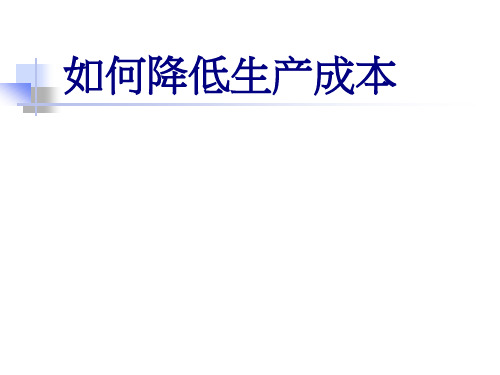
.改善传输方法 .制造方法改善 .标准化 .提高所购配件之品质 .检讨是否应自制或发 包 .改善采购技
22
捌、降低成本检核表
捌、降低成本检核表
降低成本检核表之二
检核项目
检核 品名
.为何一定要采用特定材料?
.这种材料与其目的比较是否 最经济?最合适?
.有无替代品?
.有无太浪费材料?
.可否利用较低价的标准规格?
26
玖、附录一领班们可以改善之151种浪费
一、时间的浪费:
1.缺乏适当的计划,使工作人员在换规格时产生等待, 或停工待料。
2.领班未能彻底了解其所接受之命令与指示。
3.缺乏对全天工作内容的认识。
4.对领班的命令或指示不清楚。
5.未确实督导工具、材料、小装置等应放置于一定之处 所。
6.不应加班的工作,造成加班。
产品 计划
产品 选择
产品需 求分析
降低成本
11
陆、减低成本(费用)特性要因图
规格 统一
企业 环境
配
产业 结构 推测
企业 合并
业务 合作
工专业 化
立地 件
多角化
工业区
降低成本
12
陆、减低成本(费用)特性要因图
收款 授信期间缩短
现金 收回准
提高
休闲 处理
加强收回
存货*转准提高
降低成本
短期*款之长 期化
.蒸气
.压缩空气:取卸成件 时宜续共应或机械停止 时能自动停吹。
.水(新水或循环水): 循环水之多方面利用。
.电力:停止不必要之 照明或不用时能目动断 路的设备。
.工业媒气
20
捌、降低成本检核表
捌、降低成本检核表
7S节约消除浪费的培训精编版
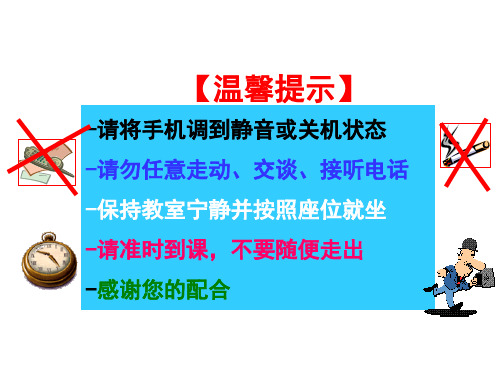
4、搬运的浪费
物品移动所需要的空间浪费;时间的耗费;人力、工具的占用。
搬运是一种不产生附加价值的动作;搬运的损失分为放置、堆积、移动、整理等动作浪费。
如何减少搬运浪费减少搬运浪费的措施之一就是进行生产布局调整,以减少搬运距离。另外一种方式就是改善搬运方式,充分利用包装箱、捆扎、托盘、搬运小车等,做到随时搬运、高效率搬运。
5、库存的浪费
如何减少库存浪费采用拉动式精益生产计划控制方式。采用精益采购JIT。
我们只在需要的时候发运需要的物料
拉动系统
地址0017-0010-002R
1
信息流
工作点
物料流
2
3
N-1
N
生产计划部门
1、下游为上游提供需求的信息;2、上游只提供给下游需要的物料
拉动式(Pull)控制系统计划
生产计划只下达到最后一道工序其余工序没有生产计划用“看板”传递——工序看板和补充看板各工序只生产后工序所需的产品——避免了生产不必要的产品只在后工序需要时才生产——避免和减少了不急需品的库存量生产指令只下达给最后一道工序——最后的成品数量与市场需求保持一致
快速转换的原则:
10、你要做多大的事情,就该承受多大的压力。11、自己要先看得起自己,别人才会看得起你。12、这一秒不放弃,下一秒就会有希望。13、无论才能知识多么卓著,如果缺乏热情,则无异纸上画饼充饥,无补于事。14、我只是自己不放过自己而已,现在我不会再逼自己眷恋了。
谢谢大家
【温馨提示】
-请将手机调到静音或关机状态-请勿任意走动、交谈、接听电话-保持教室宁静并按照座位就坐-请准时到课,不要随便走出-感谢您的配合
降低成本-减少浪费.详解
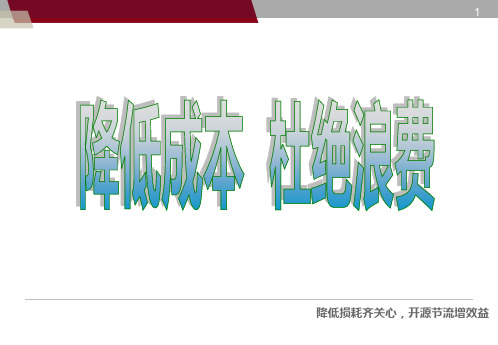
价值存在于顾客心里
6
生产过程中的八大浪费
NO 1 2 3 4 5 6 7 8 制造现场的浪费 库存的浪费 生产过剩的浪费 等待的浪费 搬运的浪费 动作的浪费 不良的浪费 加工的浪费 人的潜力未发挥 说明 成品、中间品、原材料的库存浪费 在不必要的时候制造不必要的产品 人、机械、部件在不必要时发生的各种 等待 物料搬运的浪费 步行、放置、大幅度的动作 管理部门的浪费 超前储备的浪费带来大量的管理浪 费 超前预计市场的结果 等待的浪费 搬运步行的浪费 动作的浪费
①定义:将成品或原材料从一个地方转移到另个地方,并没有增加产品价值。 ②表现: 中转环节过多----重复的放置、堆放、移动、整理 车间及设备平面布局不合理的往返运输、腾挪 搬运工具不合理、搬运容器不合理 计划不周及不良品增多造成的搬运
③改善:
减少不必要的周转环节,减少装卸、搬运,同时避免了由此 产生的碰撞。
►
由于错误的认识提高运转率或追求
表面的生产效率(前述)
►
► ►
害怕生产线停止 生产系统有问题,计划失误,信息传递失误 成品积压,客户却 在天天催 货。。。
③影响:
► ► ► ► ► ►
工序在制品积压; 使先进先出作业困难; 增加周转箱等设备成本; 库存增加; 占用资金; 掩盖问题、能力不足被隐藏……
1、管理者管理上的浪费 2、员工潜力未挖掘的浪费
精神状态差,缺乏热情
动作散慢,消极怠工 迟到、早退、缺勤
在每一位员工身上,永远都 存在着没有发挥出的潜力。 如果不通过适当的管理方式 让这种潜力发挥出来,就是 一种最大的浪费 !
离岗、串岗、聊天。。。 抽烟、看手机、打电话
人是企业最大的资产,而领导是最好的培训师
1
迅速降低企业生产成本与消除浪费技巧
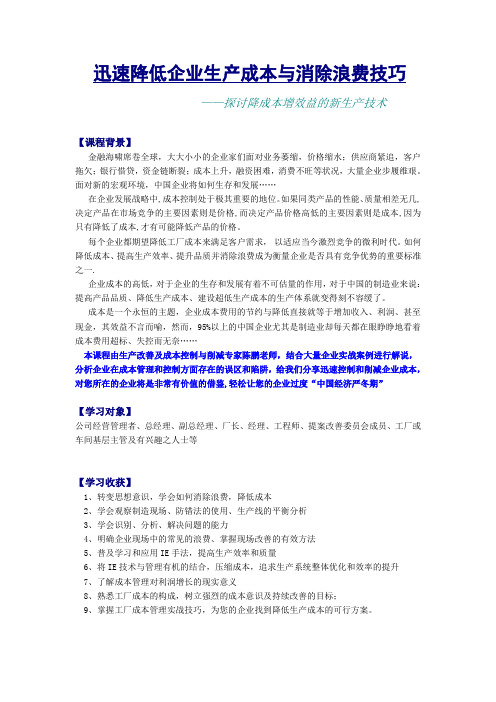
迅速降低企业生产成本与消除浪费技巧——探讨降成本增效益的新生产技术【课程背景】金融海啸席卷全球,大大小小的企业家们面对业务萎缩,价格缩水;供应商紧追,客户拖欠;银行惜贷,资金链断裂;成本上升,融资困难,消费不旺等状况,大量企业步履维艰。
面对新的宏观环境,中国企业将如何生存和发展……在企业发展战略中,成本控制处于极其重要的地位。
如果同类产品的性能、质量相差无几,决定产品在市场竞争的主要因素则是价格,而决定产品价格高低的主要因素则是成本,因为只有降低了成本,才有可能降低产品的价格。
每个企业都期望降低工厂成本来满足客户需求,以适应当今激烈竞争的微利时代。
如何降低成本、提高生产效率、提升品质并消除浪费成为衡量企业是否具有竞争优势的重要标准之一.企业成本的高低,对于企业的生存和发展有着不可估量的作用,对于中国的制造业来说:提高产品品质、降低生产成本、建设超低生产成本的生产体系就变得刻不容缓了。
成本是一个永恒的主题,企业成本费用的节约与降低直接就等于增加收入、利润、甚至现金,其效益不言而喻,然而,95%以上的中国企业尤其是制造业却每天都在眼睁睁地看着成本费用超标、失控而无奈……本课程由生产改善及成本控制与削减专家陈鹏老师,结合大量企业实战案例进行解说,分析企业在成本管理和控制方面存在的误区和陷阱,给我们分享迅速控制和削减企业成本,对您所在的企业将是非常有价值的借鉴,轻松让您的企业过度“中国经济严冬期”【学习对象】公司经营管理者、总经理、副总经理、厂长、经理、工程师、提案改善委员会成员、工厂或车间基层主管及有兴趣之人士等【学习收获】1、转变思想意识,学会如何消除浪费,降低成本2、学会观察制造现场、防错法的使用、生产线的平衡分析3、学会识别、分析、解决问题的能力4、明确企业现场中的常见的浪费、掌握现场改善的有效方法5、普及学习和应用IE手法,提高生产效率和质量6、将IE技术与管理有机的结合,压缩成本,追求生产系统整体优化和效率的提升7、了解成本管理对利润增长的现实意义8、熟悉工厂成本的构成,树立强烈的成本意识及持续改善的目标;9、掌握工厂成本管理实战技巧,为您的企业找到降低生产成本的可行方案。
- 1、下载文档前请自行甄别文档内容的完整性,平台不提供额外的编辑、内容补充、找答案等附加服务。
- 2、"仅部分预览"的文档,不可在线预览部分如存在完整性等问题,可反馈申请退款(可完整预览的文档不适用该条件!)。
- 3、如文档侵犯您的权益,请联系客服反馈,我们会尽快为您处理(人工客服工作时间:9:00-18:30)。
2.等待的浪费
双手均未抓到及摸到东西的时间
材料、作业、搬运、检查之所有等待,以及宽放和监视作业
表现形式:
•自动机器操作中,人员的“闲视”等待 •作业充实度不够的等待 •设备故障、材料不良的等待 •生产安排不当的人员等待 •上下工程间未衍接好造成的工程间的等待
3、头脑风暴法分析提高成本因素原因
依据工厂的现实情况,采用头脑风暴法,各舒己见, 提出浪费和改进的办法与对策。
➢举例
4、使用5W2H分析提高成本因素
讨论互动:针对目前车间现状,您最难解决的问题在什么?
第二讲
降低成本从 清除浪费根源开始
竞争力提升
改善 消除浪费 标准化 现场5S
动作改善、作业流程改善、物流改善、设 备模夹治具改善、品质改善、管理改善等
不可见成本
库存资金成本:资金占用 质量成本:不合格品、废品 浪费成本:八种浪费
关注制造全过程,消除一切浪费与低效率!
内部价值链分析始于原材料、外购件的采购,终于产品的销售——顾客价 值的实现。其目的是找出最基本的价值链、企业生产作业的成本动因及与竞争 对手的成本差异,区分增值与非增值的作业,探索提高增值作业效率的途径。
货款回收 成品发运 成品存储 检验返工 加工 三 加工 二 加工 一 存储搬运
来料 检验 供应商备料 采购下单 订单处理
制造周期 交付周期
增值时间:是指站在客户立场看制造 过程中增值动作的时间,如:改变形 状、改变性能、组装、包装等。只有 增值时间的活动才会产生价值!
➢顾客是不会为那些没有价值的活动付钱的!
工厂常见的生产线现场
SPC Chart
3/22/93 UCL X LCL
#$*&!!! ???
UCL X
LCL
XX
X
XX
X
XX XXXXXXXX
成品废次半成品废料 Nhomakorabea1.制造过多的浪费
无法保证可卖出的产品做了太多
表现形式:
是浪费的源头
•物流阻塞 •库存、在制品增加 •产品积压造成不良发生 •资金回转率低 •材料、零件过早取得 •影响计划弹性及生产系统的适应能力
2)运行效率是否正常?
3)能按工艺要求加工吗?
4)工作准确度如何?
5)是否经常出故障?
6)保养情况如何?
7)是否正确润滑了?
8)噪音如何?会影响生产吗?
9)设备布置正确吗?
10)设备数量够吗?
分析工厂浪费和低效率的方法
C、材料 ( Material )
1)数量是否足够或太多? 3)标识标牌是否正确? 5)进货周期是否适当? 7)材料运输有差错吗? 9)材料设计是否正确?
1.制造过多的浪费
制造过多是一种浪费的原因:
•只是提前用掉了费用(材料费、人工费)而已,并
无其它好处
•会把等待的浪费隐藏起来,掩盖稼动不够的问题
•会使制程间积压在制品,制程时间变长,现场工作
空间变大 •会产生搬运、堆积的浪费 •使先进先出的工作产生困难 •会造成库存空间的浪费
?
1.制造过多的浪费
分析生产浪费和低效率的方法
A、人员 ( Man )
1)是否遵循作业标准?
2)是否有明显的作业过失?
3)工作能力是否充分发挥?
4)是否适合于该工作?
5)有足够经验吗?
6)还需要哪些培训?
7)责任心怎样?
8)有解决问题意识吗?
9)人际关系怎样?
10)工作热情是否高?
B、设备 ( Machine )
1)设备能力足够吗?
D、方法 ( Methode )
1)工艺标准合理吗? 3)工作方法安全吗? 5)这种方法高效吗? 7)工艺卡是否正确? 9)通风和光照良好吗?
2)是否符合质量要求? 4)有杂质吗?会影响加工吗? 6)材料浪费情况如何? 8)是否对加工要求过高? 10)质量标准合理吗?
2)工艺标准提高了吗? 4)这种方法能保证质量吗? 6)工序安排合理吗? 8)温度和湿度适宜吗? 10)前后工序衔接好吗?
产品价值 W
产品价值W=C+V+M
生产过程中消耗的生产资料的转移价值 C
活劳动新 创造的价值
以工资及其附加费等 分配给劳动者个人部分 V 以税金和利润的形式
上缴或企业留利 M
产品 成本
产品 价格
产品价值的货 币表现
生产成本构成
可见成本
人工成本:奖金工资 原材料成本:原辅材料 设备成本:设备购买、维护 能源成本:水电气汽 管理成本:管理费用、培训费用
降低企业生产成本与消除浪费 控制
公司内训
课程大纲
一、成本的概念 二、降低成本从清除浪费根源开始
三、从现场作业过程分析成本
四、制造成本管理控制 五、产品质量成本控制
六、通过工厂的现场改善来清除浪费
七、成本管理与个人利益的实现
第一讲
成本的概念--------
成本概念——
产品成本是工业企业在一定时间内为制造、 销售一定数量的产品所支出的费用总和。也就是产 品再生产经营过程中消耗的物化劳动的货币表现。 从其经济实质看,成本是产品价值的一部分:
对策:
•顾客为中心的弹性生产系统
•单件流动—一个流生产线
•看板管理的贯彻
•快速换线换模
•少人化的作业方式
•均衡化生产
原因:
•人员过剩 •设备稼动过剩 •生产浪费大 •业务订单预测有误 •生产计划与统计错误
注意:
•生产速度快并不代表效率高 •设备余力并非一定是埋没成本 •生产能力过剩时,应尽量先考虑减 少作业人员,但并非辞退人员,而 是更合理、更有效率地应用人员
2、分析浪费原因及改善对策
使用鱼骨图分析法,对寻找到的浪费和低效率进行 分析,找到其产生的原因何在?
主要因素
次要因素
主要因素
次要因素
主要因素
次要因素
次要因素
主要因素
问题 瓶颈
① 确定需要分析的问题; ② 确定原因的主要类别。 ③ 头脑风暴找详细原因; ④ 删除无用因素;
⑤ 讨论剩余的原因并明确哪一个最重要 ; ⑥ 研究最重要的因素; ⑦ 消除、减少或控制这些因素。
物料从进厂到出厂,只有 不到 10% 的时间是增值的!
1、寻找生产成本因素(浪费和低效率)
①从产品生产流程入手,寻找制约生产正常运营的 瓶颈问题。
输入
活动A
活动B
活动C
输出
痛则不通!通则不痛! 举例
——流程分析是寻找问题的最佳途径!
②从人、机、料、法入手,寻找制造现场成本因素。
(浪费与低效率)
人、机、料、法
七大浪费
动作标准化、作业流程标准化、操作流程 标准化、包装运输标准化等
整理、整顿、清扫、清洁、素养等
何谓浪费?
用不同的评判标准去判断一 个动作、行为、方法或计划时, 所得到的浪费程度都会不同。
1.制造过多的浪费 2.等待的浪费 3.搬运的浪费 4.加工的浪费 5.库存的浪费 6.动作的浪费 7.制作不良的浪费