海上大型钻孔灌注桩施工工艺分析
港口码头施工工法实现有效的海运与物流服务

港口码头施工工法实现有效的海运与物流服务港口码头是现代海运与物流服务的重要枢纽,承担着货物装卸、集散、保管和转运的重要功能。
港口码头的施工工法直接关系到港口的运营效率和服务质量。
本文将探讨港口码头施工的几种常见工法,以实现有效的海运与物流服务。
一、深水码头施工工法深水码头是适应大型船舶靠泊需求的重要设施,其施工工法主要包括桩基础施工、浮筒吊装和桥梁结构的建设。
1. 桩基础施工桩基础是深水码头的重要支撑结构,常见的施工工法包括钻孔灌注桩和海上钢管桩。
钻孔灌注桩采用大型钻机进行钻孔,并在孔洞内注入混凝土,形成坚固的基础。
海上钢管桩则需要使用大型起重设备将钢管定位于海底,并进行固定。
2. 浮筒吊装深水码头常常需要使用大型浮筒进行装卸作业,浮筒的吊装工法十分关键。
通常使用起重机将浮筒吊装到合适的位置,并进行固定,确保其稳定性和安全性。
3. 桥梁结构建设为了实现码头与陆地之间的连接和货物的顺畅流通,桥梁结构的建设尤为重要。
常见的桥梁结构工法包括悬索桥和斜拉桥。
这些桥梁需要经过精确的设计和施工,确保其承载能力和稳定性。
二、浅水码头施工工法浅水码头施工相对较为简单,主要包括填海、疏浚和码头建设。
1. 填海填海是浅水码头施工的首要工作,通过向海域中注入大量的泥沙和填料,逐渐扩展陆地面积。
填海工法需要综合考虑水流、水深等因素,确保填土能够稳定且不会对环境造成负面影响。
2. 疏浚浅水码头常需要进行疏浚工作,以确保船只的通航深度。
常用的疏浚工法包括机械疏浚和水力疏浚。
机械疏浚通过使用挖掘机等设备将海底的泥沙、杂物等物质清除,水力疏浚则是通过水流的力量将底泥推向其他区域。
3. 码头建设码头的建设工法主要包括填筑和混凝土浇筑。
填筑工法需要确保填料的紧密程度和稳定性,以确保码头的承重能力。
混凝土浇筑则需要经过仔细的施工计划和技术手段,以确保浇筑质量达到要求。
三、自动化码头工法为了提高港口码头的运营效率和服务质量,自动化码头工法得到了广泛应用。
谈谈钻孔灌注桩施工工艺要点及质量控制
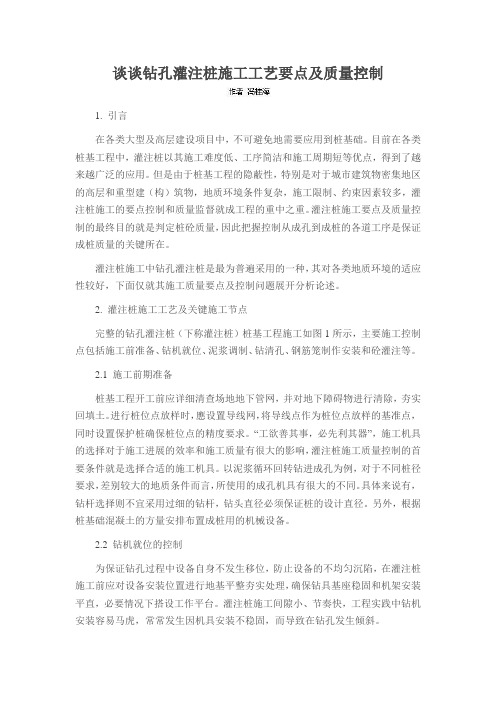
谈谈钻孔灌注桩施工工艺要点及质量控制1. 引言在各类大型及高层建设项目中,不可避免地需要应用到桩基础。
目前在各类桩基工程中,灌注桩以其施工难度低、工序简洁和施工周期短等优点,得到了越来越广泛的应用。
但是由于桩基工程的隐蔽性,特别是对于城市建筑物密集地区的高层和重型建(构)筑物,地质环境条件复杂,施工限制、约束因素较多,灌注桩施工的要点控制和质量监督就成工程的重中之重。
灌注桩施工要点及质量控制的最终目的就是判定桩砼质量,因此把握控制从成孔到成桩的各道工序是保证成桩质量的关键所在。
灌注桩施工中钻孔灌注桩是最为普遍采用的一种,其对各类地质环境的适应性较好,下面仅就其施工质量要点及控制问题展开分析论述。
2. 灌注桩施工工艺及关键施工节点完整的钻孔灌注桩(下称灌注桩)桩基工程施工如图1所示,主要施工控制点包括施工前准备、钻机就位、泥浆调制、钻清孔、钢筋笼制作安装和砼灌注等。
2.1 施工前期准备桩基工程开工前应详细清查场地地下管网,并对地下障碍物进行清除,夯实回填土。
进行桩位点放样时,應设置导线网,将导线点作为桩位点放样的基准点,同时设置保护桩确保桩位点的精度要求。
“工欲善其事,必先利其器”,施工机具的选择对于施工进展的效率和施工质量有很大的影响,灌注桩施工质量控制的首要条件就是选择合适的施工机具。
以泥浆循环回转钻进成孔为例,对于不同桩径要求,差别较大的地质条件而言,所使用的成孔机具有很大的不同。
具体来说有,钻杆选择则不宜采用过细的钻杆,钻头直径必须保证桩的设计直径。
另外,根据桩基础混凝土的方量安排布置成桩用的机械设备。
2.2 钻机就位的控制为保证钻孔过程中设备自身不发生移位,防止设备的不均匀沉陷,在灌注桩施工前应对设备安装位置进行地基平整夯实处理,确保钻具基座稳固和机架安装平直,必要情况下搭设工作平台。
灌注桩施工间隙小、节奏快,工程实践中钻机安装容易马虎,常常发生因机具安装不稳固,而导致在钻孔发生倾斜。
2.3 泥浆配制众多的桩基工程实践表明泥浆质量的好坏对施工质量有着举足轻重的作用。
水上钻孔灌注桩施工工艺
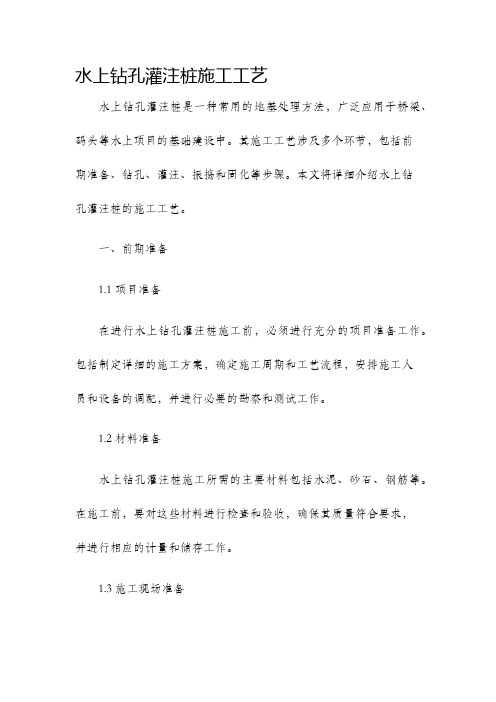
水上钻孔灌注桩施工工艺水上钻孔灌注桩是一种常用的地基处理方法,广泛应用于桥梁、码头等水上项目的基础建设中。
其施工工艺涉及多个环节,包括前期准备、钻孔、灌注、振捣和固化等步骤。
本文将详细介绍水上钻孔灌注桩的施工工艺。
一、前期准备1.1 项目准备在进行水上钻孔灌注桩施工前,必须进行充分的项目准备工作。
包括制定详细的施工方案,确定施工周期和工艺流程,安排施工人员和设备的调配,并进行必要的勘察和测试工作。
1.2 材料准备水上钻孔灌注桩施工所需的主要材料包括水泥、砂石、钢筋等。
在施工前,要对这些材料进行检查和验收,确保其质量符合要求,并进行相应的计量和储存工作。
1.3 施工现场准备施工现场的准备工作主要包括搭建施工平台和围护结构,清理施工区域,确保施工现场的平整和清洁,以及设置必要的安全警示标志和防护设施。
二、钻孔2.1 钻孔设备准备水上钻孔灌注桩的施工需要使用专用的钻孔设备,包括浮动式钻机、沉管钻机等。
在施工前,要对这些设备进行检查和保养,确保其正常运行。
2.2 钻孔过程钻孔过程中需要根据设计要求进行孔径和孔深的控制。
在钻孔过程中要注意保持孔壁的稳定,避免塌方和倾斜。
同时,还要进行岩土层的采样和测试工作,以便了解地层情况和选择灌注材料。
三、灌注3.1 灌注设备准备水上钻孔灌注桩的灌注过程需要使用混凝土搅拌车、抽注泵等设备。
在施工前,要对这些设备进行检查和保养,确保其正常运行。
3.2 灌注过程灌注过程中需要根据设计要求进行混凝土配比和浇注,以保证灌注桩的强度和稳定性。
同时,还要注意灌注速度和均匀度,避免发生冷接缝和孔口变形。
四、振捣在灌注完成后,需要进行振捣工作,以排除混凝土中的空气和水泡,并提高桩体的密实度和强度。
振捣设备通常使用振动棒或振动器进行。
五、固化灌注完成并振捣后,需要进行养护工作,以确保混凝土的正常固化和硬化。
养护时间通常为7天以上,具体时间根据地方气候和材料类型而定。
六、施工安全在水上钻孔灌注桩施工过程中,必须严格遵守相关的施工安全规范和操作规程,确保施工人员的生命安全和施工设备的正常运行。
超长、超大直径钻孔灌注桩施工工法(最终)

超长、超大直径钻孔灌注桩施工工法一、前言钻孔灌注桩是桥梁建设上常用的一种深基础形式。
近年来我国桥梁事业发展迅速,新建桥梁的跨径越来越大、结构越来越复杂,钻孔灌注桩的长度也就越来越长、直径也就越来越大。
中港第二航务工程局承建的苏通大桥C1标主4号墩由131根钻孔灌注桩组成,桩长均为120m,桩径2.5~2。
85m,为目前世界上最大的桥梁群桩基础。
为了促进该施工方法在我国类似桥梁工程项目中推广使用,根据苏通大桥施工经验与实践,特编制该工法。
该工法内容主要包括钻孔平台搭设、钻孔桩成孔工艺(钻机选型、泥浆的选用配置、成孔参数的选择)以及成桩工艺(水下砼的配制及浇注工艺),其中钻孔平台搭设工艺曾获2004年武汉市职工创新一等奖。
二、工法特点1、采用结构护筒直接作为钻孔平台的承重结构.2、采用了振动锤以及移动式导向架打设钢护筒.3、钻孔处多为粉沙、细沙、中粗沙及沙砾层等易坍孔地层,施工选用了大功率钻机成孔、优质PHP护壁泥浆。
4、钢筋笼采用镦粗直螺纹接头,并于后场同槽预制,采用大型浮吊大节段吊装。
5、桩基采用桩底后压浆技术。
三、使用范围适用于采用钻孔灌注桩(地质以砂层为主)为基础的特大桥桩基施工。
四、工艺原理钻孔桩施工工法主要分两部分:其一主要说明钻孔平台的搭设工法,其二介绍钻孔灌注桩的成孔、成桩以及桩底后压浆工艺。
五、施工工艺(一)、工艺流程1、传统钢管桩施工平台搭设工艺流程图5。
1 传统钢管桩施工平台搭设工艺流程2、采用钢护筒作为承重结构的钻孔平台搭设工艺流程图5。
2 采用钢护筒作为承重结构的钻孔平台搭设工艺流程3、钻孔灌注桩施工工艺流程图5。
3 钻孔桩施工流程图4、桩底后压浆流程图5.4 桩底后压浆施工流程图(二)、施工要点1、传统钢管桩施工平台搭设施工要点①钢管桩施工a、钢管桩制作、运输钢管桩均按设计规格拼装成整桩,按沉放顺序分批加工制作,出厂检验合格后,用驳船运输至施工现场.b、钢管桩沉设钢管桩沉设定位采用测量定位。
钻孔灌注桩的施工工艺与注意事项要点
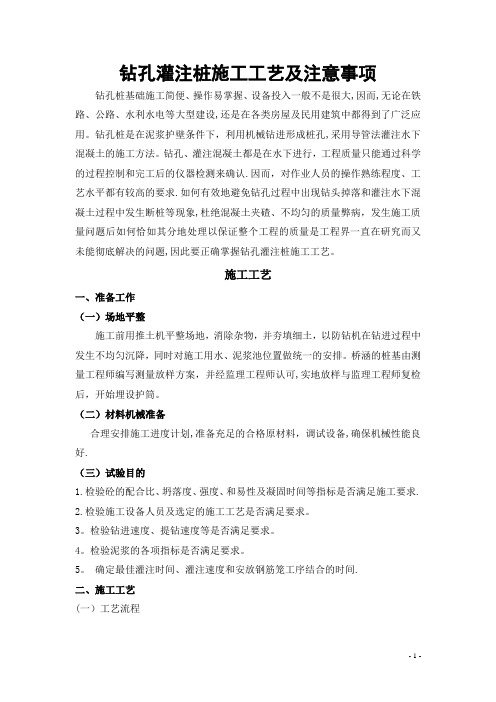
钻孔灌注桩施工工艺及注意事项钻孔桩基础施工简便、操作易掌握、设备投入一般不是很大,因而,无论在铁路、公路、水利水电等大型建设,还是在各类房屋及民用建筑中都得到了广泛应用。
钻孔桩是在泥浆护壁条件下,利用机械钻进形成桩孔,采用导管法灌注水下混凝土的施工方法。
钻孔、灌注混凝土都是在水下进行,工程质量只能通过科学的过程控制和完工后的仪器检测来确认.因而,对作业人员的操作熟练程度、工艺水平都有较高的要求.如何有效地避免钻孔过程中出现钻头掉落和灌注水下混凝土过程中发生断桩等现象,杜绝混凝土夹碴、不均匀的质量弊病,发生施工质量问题后如何恰如其分地处理以保证整个工程的质量是工程界一直在研究而又未能彻底解决的问题,因此要正确掌握钻孔灌注桩施工工艺。
施工工艺一、准备工作(一)场地平整施工前用推土机平整场地,消除杂物,并夯填细土,以防钻机在钻进过程中发生不均匀沉降,同时对施工用水、泥浆池位置做统一的安排。
桥涵的桩基由测量工程师编写测量放样方案,并经监理工程师认可,实地放样与监理工程师复检后,开始埋设护筒。
(二)材料机械准备合理安排施工进度计划,准备充足的合格原材料,调试设备,确保机械性能良好.(三)试验目的1.检验砼的配合比、坍落度、强度、和易性及凝固时间等指标是否满足施工要求.2.检验施工设备人员及选定的施工工艺是否满足要求。
3。
检验钻进速度、提钻速度等是否满足要求。
4。
检验泥浆的各项指标是否满足要求。
5。
确定最佳灌注时间、灌注速度和安放钢筋笼工序结合的时间.二、施工工艺(一)工艺流程测量放样→设置护桩→埋设钢护筒→钻孔→成孔检测→清孔→吊放钢筋笼→安装砼导管→灌筑砼→破桩头→成品检测。
以上所有流程须经监理全过程监控。
(二)施工方法及施工要点1、测量放样及埋设桩位(1)施工前先修便道,使施工机具顺利进出,能保证钻机在施工中平稳。
然后根据设计提供的导线点(经导线复测闭合后)及水准点用全站仪和水准仪定位,桥墩中线在桥轴线方向上的位置中误差不应大于±15cm,成排成列放样,放样后用钢尺校核。
钻孔灌注桩施工技术分析

钻孔灌注桩施工技术分析钻孔灌注桩是一种常用的基础工程技术,广泛应用于建筑、桥梁、水利工程等领域。
钻孔灌注桩施工技术的好坏直接影响到工程的质量和安全,因此对于钻孔灌注桩的施工技术进行分析和研究具有重要意义。
本文将从材料选用、施工工艺和质量控制等方面对钻孔灌注桩的施工技术进行分析和探讨。
一、材料选用1. 水泥:水泥是钻孔灌注桩中的主要材料,一般选用普通水泥。
水泥的质量直接关系到桩的强度和抗渗性能,因此在选用水泥时应选择质量可靠、符合标准的产品。
2. 砂石:选用合适的砂石是保证桩体密实性和抗压能力的关键。
砂石颗粒应均匀,不含有超过规定粒径的颗粒,且应保持一定的湿度。
3. 搅拌水:搅拌水应选用清洁、无杂质的自来水,且要注意水泥的用水量和稳定性。
4. 钢筋:钻孔灌注桩中的钢筋是起到加固和增强桩体抗压能力的重要材料。
在选用钢筋时要符合设计要求,并且应具有良好的延展性和抗腐蚀性。
二、施工工艺1. 钻孔施工:首先进行钻孔工程,根据设计要求选择合适的钻孔机具进行作业。
在施工现场应做好安全防护措施,保证作业人员的安全。
2. 灌注混凝土:在进行混凝土灌注时,应注意混凝土的配合比例和搅拌均匀性。
在灌注过程中要控制混凝土的流动性,使混凝土均匀填充整个孔内。
3. 钢筋安装:在混凝土灌注后需要立即进行钢筋的布置和安装。
钢筋应符合设计要求,并要求做好连接的处理,以保证桩体的整体性。
4. 抽管:在混凝土灌注完成后,要及时进行管壁抽取处理,防止管道被混凝土封堵。
5. 桩顶整平:在桩顶出口部位进行整平处理,以保证桩顶符合设计高程和平整度要求。
三、质量控制1. 检测方法:采用合适的检测手段对钻孔灌注桩进行检测,如超声波检测、静载试验等,以验证桩体的质量和抗压性能。
2. 质量管理:在施工过程中要进行严格的质量管理,确保每个施工环节符合设计要求和施工规范,如水泥的用量、混凝土的配合比例、灌注工艺等。
3. 桩身质量:要对每根钻孔灌注桩进行质量验收,验证桩身的密实性和抗压能力,确保每根桩的质量合格。
海上钻孔桩专项施工方案

福州至平潭铁路新建工程FPZQ-4标钻孔桩施工方案编制:复核:审批:中铁十三局集团福平铁路项目部一分部二0一三年十一月十三日目录1.工程概况 (3)1.1桥址概况 (3)1.2工程地质条件 (3)1.3水文特征 (3)1.4不良地质情况 (3)1.5桥梁结构 (3)1.6适用范围 (4)2.主要应用标准和规范 (4)3.主要施工工艺 (4)3.1施工准备 (4)3.1.1技术资料准备 (4)3.1.2场地的布置 (4)3.1.3人员准备 (5)3.1.4机具准备 (6)3.1.5材料准备 (6)3.2施工工艺流程图 (6)3.3主要施工方法 (7)3.3.1孔桩钻进 (7)3.3.1.1测量放样 (7)3.3.1.2护筒制作、埋设 (7)3.3.1.3泥浆池布置及制备 (8)3.3.1.4钻孔 (9)3.3.1.5清孔 (10)3.3.1.6钻孔桩事故的预防和处理 (10)3.3.1.7验收 (11)3.3.2钢筋笼制作、安装 (11)3.3.2.1钢筋笼制作 (11)3.3.2.1钢筋骨架的安装 (12)3.3.3灌注混凝土 (12)3.3.4桩基检测、验收 (16)3.3.5钻孔灌注桩施工中常见质量通病的预防措施 (16)3.3.5.1主要风险 (16)4.施工质量、安全措施 (17)4.1 施工质量保证措施 (17)4.1.1.质量管理机构 (17)4.1.2质量制度制定 (20)4.1.3原材料、半成品质量控制 (21)4.1.4施工过程质量控制 (22)4.1.5工程质量资料 (22)4.1.6质量目标及创优计划 (23)5.确保工程安全的措施 (23)5.1安全管理机构 (24)5.1.1建立安全管理组织机构 (24)5.2安全保证措施 (26)5.2.1安全组织措施 (26)5.2.2安全技术措施 (26)6.施工环保、水保措施 (27)6.1施工环保、水土保持目标 (27)6.2 施工环保、水土保持管理体系 (27)6.2.1施工环保、水土保持管理组织机构 (27)6.2.2施工环保、水土保持管理检查制度 (29)6.3施工环保、水土保持措施 (29)6.3.1环境保护措施 (29)6.3.2水土保持措施 (30)7.应急预案 (31)7.1应急预案启动的条件和程序 (31)7.1.1启动条件 (31)7.1.2启动程序 (31)7.1.3事故处理程序 (31)7.1.4抢险(救援)程序 (31)7.1.5 应急响应(预防措施) (32)7.1.6总结、事后处理 (33)钻孔桩施工方案1.工程概况1.1桥址概况本桥位于平潭县大练乡渔限村,穿越山谷,右侧为东海,毗邻海坛海峡,起讫里程为DK70+654.7~DK71+476.11,总长911.41m。
船闸及航道工程长螺旋钻孔压灌桩施工技术研究
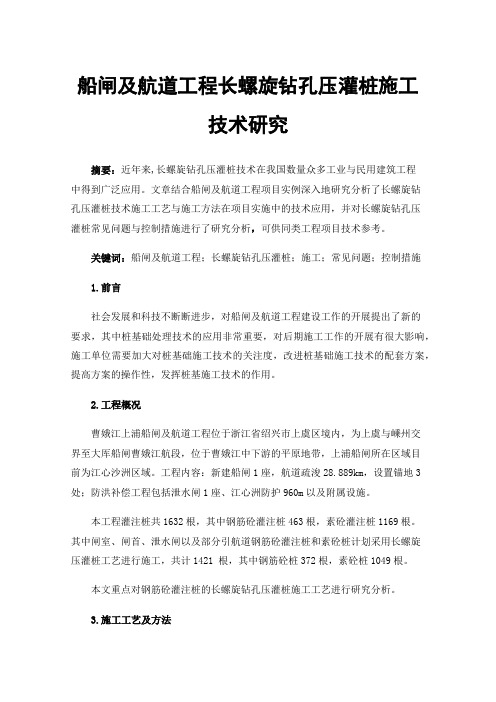
船闸及航道工程长螺旋钻孔压灌桩施工技术研究摘要:近年来,长螺旋钻孔压灌桩技术在我国数量众多工业与民用建筑工程中得到广泛应用。
文章结合船闸及航道工程项目实例深入地研究分析了长螺旋钻孔压灌桩技术施工工艺与施工方法在项目实施中的技术应用,并对长螺旋钻孔压灌桩常见问题与控制措施进行了研究分析,可供同类工程项目技术参考。
关键词:船闸及航道工程;长螺旋钻孔压灌桩;施工;常见问题;控制措施1.前言社会发展和科技不断断进步,对船闸及航道工程建设工作的开展提出了新的要求,其中桩基础处理技术的应用非常重要,对后期施工工作的开展有很大影响,施工单位需要加大对桩基础施工技术的关注度,改进桩基础施工技术的配套方案,提高方案的操作性,发挥桩基施工技术的作用。
2.工程概况曹娥江上浦船闸及航道工程位于浙江省绍兴市上虞区境内,为上虞与嵊州交界至大厍船闸曹娥江航段,位于曹娥江中下游的平原地带,上浦船闸所在区域目前为江心沙洲区域。
工程内容:新建船闸1座,航道疏浚28.889km,设置锚地3处;防洪补偿工程包括泄水闸1座、江心洲防护960m以及附属设施。
本工程灌注桩共1632根,其中钢筋砼灌注桩463根,素砼灌注桩1169根。
其中闸室、闸首、泄水闸以及部分引航道钢筋砼灌注桩和素砼桩计划采用长螺旋压灌桩工艺进行施工,共计1421 根,其中钢筋砼桩372根,素砼桩1049根。
本文重点对钢筋砼灌注桩的长螺旋钻孔压灌桩施工工艺进行研究分析。
3.施工工艺及方法根据地勘资料,经多方考察研究,本工程引入长螺旋压灌桩施工工艺。
3.1.1工艺优点1、无噪音、无振动、不扰民,夜间也可连续施工;2、无需使用泥浆护壁,不产生泥浆,施工非常环保;3、干作业施工,桩底沉渣极少;4、钻进速度快;5、钻进深度大,根据地层情况,最深可达到38米;6、成孔垂直度精高,最优达到1/300;7、不会产生塌孔现象,成孔质量高;8、对于超厚填土层、砂层、渗透系数大的粉砂粉土层、卵石层、富水透水层等疑难复杂地层具有非常良好的成孔效果,克服了旋挖钻机、正反循环泥浆护壁桩机在上述疑难地层中成孔遇到的坍孔、扩径、缩颈以及无法有效成孔的问题。
海上大直径钻孔灌注桩施工探讨

收稿日期))5作者简介刘启蛟(6)),男,山东齐河人,工程师。
海上大直径钻孔灌注桩施工探讨刘启蛟1,王颖川2(1.济南铁路局建管处,山东济南250001;2.铁道战备舟桥处,山东齐河251100)摘要:对青岛海湾大桥试桩专题中海上大直径钻孔桩的钻孔、海水泥浆应用、高性能混凝土灌注等施工工艺进行了探讨。
关键词:大直径钻孔桩;施工;海水泥浆;高性能混凝土中图分类号:U445.55文献标识码:BD iscu ssi on on the constructi on of sea l arge-d i am eter bored p ileLIU Q i-ji ao 1,W A NG Yi ng -chuan2(1.J inan Ra il w ay Co n s tru ctio n and M anag e m ent Offic e ,Shando ng J i nan 250001Ch i na;2.Ra il w ay R ead ines s Zh o uqi ao Office ,Shandon g Q i h e 251100C hina)Ab stract :The paper d iscussed so m e constructi on techno-l ogy i n clud i ng the drilli ng of sea large -d ia m eter bored p ile ,the app licati on of sea water sl u rr y ,the pou ri ng ofh i gh -perf or mance concr ete i n Qingdao Bay Bri dge testp ile p r ojec.tK ey word s :lar ge -d i a meter bor ed p ile ;c on str u ction ;sea water s l urr y ;h i gh-perf or m ance concrete1概述青岛海湾大桥位于胶州湾内湾中北部,是连接青岛、黄岛、红岛的跨海大桥工程,工程全长3514k m,海上段长度26175k m 。
钻孔灌注桩施工工艺论文

钻孔灌注桩施工工艺论文摘要:钻孔灌注桩是一种常用的地基处理方式,具有承载力强、变形小等优点,广泛应用于建筑工程领域。
本文主要介绍了钻孔灌注桩的施工工艺,包括勘察设计、钻孔施工、灌注浆液、钢筋布置等环节。
通过分析工艺流程和注意事项,探讨了影响施工质量的主要因素,并提出了相应的解决办法。
此外,对于常见的问题及其处理方法进行了分析和总结。
本文旨在为钻孔灌注桩施工提供一定的参考和指导。
1. 引言钻孔灌注桩作为一种常用的地基处理方式,其在各类土壤和地质条件下都有着广泛的应用。
其优点主要体现在承载力强、变形小、施工便捷等方面。
本文对钻孔灌注桩的施工工艺进行了详细的介绍和分析,以供相关从业人员参考。
2. 施工前的勘察设计在进行钻孔灌注桩施工之前,需要进行详细的勘察设计工作。
主要包括地质勘察、设计方案的制定等。
地质勘察是为了了解地下地质条件和土层的情况,以便合理选择施工工艺和材料。
设计方案的制定是根据勘察结果,结合工程要求和设计要求,确定施工方案和参数。
3. 钻孔施工钻孔施工是钻孔灌注桩的重要环节。
其施工过程包括预埋大直径钢管桩、钻孔、清孔等步骤。
预埋大直径钢管桩是为了增强桩身支撑能力,防止土体崩塌。
钻孔是将埋入土中的钢管桩延伸到预定的深度。
清孔是钻孔过程中产生的土屑清除出来,以便后续的灌注工作。
4. 灌注浆液灌注浆液是钻孔灌注桩中的关键环节之一。
其主要作用是填充钻孔中的空隙,提高桩体的强度和稳定性。
灌注过程需要控制浆液的稠度和流动性,保证其能够充分填充钻孔。
同时,需要注意浆液的配比和浆液的注入速度,以确保施工质量。
5. 钢筋布置钢筋布置是钻孔灌注桩中的重要工作之一。
钢筋的质量和布置对桩体的承载能力和稳定性有着直接影响。
合理的钢筋布置应根据设计要求进行,同时注意钢筋与周围土体的间隔和连接方式等。
在施工过程中,需要采取相应的措施保证钢筋的正确安装和定位。
6. 影响施工质量的主要因素及处理方法钻孔灌注桩的施工质量受到多个因素的影响,主要包括地质条件、浆液配比、施工参数等。
大孔径钻孔灌注桩施工工艺[最新]
![大孔径钻孔灌注桩施工工艺[最新]](https://img.taocdn.com/s3/m/bd635cdbb9f67c1cfad6195f312b3169a451eaea.png)
大直径钻孔灌注桩施工工法自1966年我国XX生产出第一台旋转钻机,大直径钻孔灌注桩就在我国许多特大桥梁桩基中得到了广泛的应用。
而随着经济建设的不断发展,大跨径桥梁建设和城市大型重点工程逐渐增多,为大直径钻孔灌注桩桩基的采用提供了更广阔的市场。
一、工法内容1.工艺特点1.1.大直径钻孔桩根据桩径、桩长、地质条件、水文情况等诸多因素来选择钻机的型号、扭矩与钻具的各项参数。
一般在地层强度较高、钻孔深度较深地质情况较复杂则选用较大型号钻机,另其反。
1.2.在陆地上施工时,其泥浆循环可在陆地开挖泥浆沟和泥浆池,护筒的埋设只受表层不稳定土层影响。
而在在水上施工时,需搭设平台。
护筒的埋设较深,既要保重平台的稳定又要保证钻孔壁的安全。
1.3.成孔过程泥浆的循环方法可分正循环和反循环泵,而反循环又可分泵吸反循环和气举反循环两种。
1.4.大直径钻孔桩泥浆的作用主要为:①保护壁,②悬浮钻渣③冷却钻具;大口径成孔对泥浆质量要求很高,一般检测指标有:①相对密度,②粘度,③含砂率,④胶体率等。
1.5.在江上或海上作业时,材料供应和正常施工不可避免的要受到潮汐、风浪、季节性的影响,另由于平台的局限性需在平台配制专门的泥浆箱或利用护筒的连接作为泥浆池或泥浆循环管。
2.适用X围2.1.本工法适用X围:孔径≥2000mm,孔深150m以内的孔径、垂直度要求较高,水上(陆地)竖向承重桩的施工。
2.2.适用地层:粘土层、砂层、砾石层、卵石层、岩层等地层。
3.工艺原理结合工程与地质条件,利用大扭矩钻机进行大直径成孔,下放钢筋笼、导管法水下混凝土灌注,从而实现成桩达到竖向承重的目的。
4.施工工艺4.1.施工顺序在施工前,先对钻孔中心进行校对然后钻机就位成孔。
成孔中钢筋笼进行制备,成孔验收后下笼、下导管进行二次清孔验收,最后进行灌注成桩。
4.2.工艺流程5.施工要求5.1.根据设计施工图要求确定施工工艺方法和总体施工顺序5.1.1.根据设计要求与施工特点来确定施工的工艺方法,根据施工环境来制定施工的总体顺序。
钻孔灌注桩的施工工艺及施工要点

钻孔灌注桩的施工工艺及施工要点第一节钻孔灌注桩施工流程钻孔灌注桩施工工序包括场地准备、桩位放样、埋设护筒、钻孔、清孔、吊放钢筋笼、灌注混凝土等,施工工艺流程如图3-1所示。
钻孔灌注桩施工是一项质量要求高,须在一个短时间内连续完成多道工序的地下隐蔽工程,施工必须要认真按照施工工艺流程进行。
钻孔灌注桩工艺流程图第二节施工准备3.2.1 放桩放桩是指将设计好的桩中心点位的坐标用相关仪器投放到施工场地中。
放桩流程为:核对坐标→架设仪器→输入坐标→放点。
(1)核对坐标此过程往往被众多测量人员所忽略,图纸中给定的坐标可能会是错误的,因此在实地放桩前需要进行坐标核算,核对坐标可用Execel表格。
(2)架设仪器将全站仪位于控制点位处,固定两支架,伸缩第三只架。
使圆水准器泡偏向的方向与固定两只架中的一个处于同一直线上,然后固定支架再调节和气泡在一直线上的支架。
一般情况只要精平后再对中精平就可以了,棱镜立于另一控制点位处作为后视。
(3)输入坐标将要测放桩号的点位坐标输入到全站仪中,全站仪就可以计算出控制点位与测放点位的距离与角度。
(4)放点调整全站仪使镜头方向指向测放点位的方向,误差在2”左右以内,将棱镜立于测放点位附近,不断调整棱镜的位置,是全站仪对准棱镜头,然后通过全站仪测距后给定的移动距离移动棱镜,直到全站仪经过测算后给定的移动距离1mm左右以内为止,再将木桩或钢桩钉在棱镜架设处并喷漆,此时一个桩的桩位即投放完成。
3.2.2 人工挖探坑施工厂区内地下管线复杂,为保证管线安全及施工正常进行,在钻孔桩施工前需进行人工挖探坑探明管线准确位置,并加以保护后方可施工钻孔桩。
探坑深度不小于2.0m(挖到原状土),如果2.0m以下仍然为回填土,不能确定管线位置的,必须继续挖,直到原状土或确定管线位置为止。
为保证施工安全必须浇注混凝土护壁,探坑开挖至1m后必须开始施做混凝土护壁,严防土质疏松导致孔口坍塌。
3.2.3 符桩符桩的过程大致与放桩相同,略有不同的是桩位标识是安放在人工挖探坑后的盖板上,以便钻机中心对准标识准确下钻。
海上冲孔灌注桩施工技术

抛石堤海上灌注桩施工技术[摘要]本文以实际施工为基础,注重施工细节和技术难点,从海上平台搭设、抛石层和粉砂层灌注桩施工等方面介绍了海上冲孔灌注桩施工技术及意外防治措施。
[关键词]冲孔灌注桩、抛石堤、海上平台1、工程概况连云港港旗台作业区防波堤工程导助航设施分别在南北防波堤堤头建设一座灯塔及附属登陆设施(图1),其中南防波堤是全清淤施工,北防波堤是爆破挤淤施工。
单座导助航工程共包含了4根灯桩灌注桩(陆地桩,图1中浅色桩)和2根海上登陆点灌注桩(海上桩,图1中深色桩),灯桩灌注桩直径1米,长40米,穿过抛石层18米,登陆点灌注桩直径1.2米,长45米,穿过抛石层10米,其余基本为粉砂层和少量粉质粘土层(图2)所示。
图1 工程结构示意图图2 工程灌注桩位置结构2、主要施工技术2.1 施工平台搭设海上灌注桩通过搭设海上平台施工,国内施工平台有的用槽钢和工字钢陆上整体制作、海上整体安装,要求使用大型起重设备。
本工程规模不大而且处于防波堤最顶头,租用浮吊和使用大型吊车的方案为无论从成本还是施工空间考虑均不易行,于是改为采用贝雷片桁架逐步推进搭设,变“先柱后梁”的常规工艺流程为“先梁后柱”,一台20T吊车即可满足工程需求。
搭建过程如图3所示。
施工时,挖(1)(2)号基础基槽→埋钢管→混凝土灌实→(1)号基础嵌焊钢板于钢管上作为锚板,开槽(2)号基础钢管,搁置工钢后焊接→销连接①②号贝雷片→安装①②号贝雷片,并将①号贝雷片与(1)号基础焊牢作为固定支座,②号贝雷片与(2)号基础搭接作为滑动支座→安装③④号贝雷片,②③间上下铰均铰连接,③④间仅有上铰铰连接→(3)号立柱下挂墩袋混凝土(1吨)安放,混凝土初凝前,应将(3)号立柱贝雷片临时搭焊,以保证垂直度→墩袋混凝土产生强度后,割除(3)号立柱搁置槽钢位置以上的部分并开槽→如图示方法,吊起④号贝雷片,搁置(3)号立柱的工钢并焊接→放下④号贝雷片,将③④号贝雷片下铰铰接→完成后续立柱、贝雷片安装,→满铺40#槽钢、间距50mm。
水上钻孔灌注桩施工方案

水上钻孔灌注桩施工方案1. 引言水上钻孔灌注桩是一种常用的基础施工工艺,适用于河流、湖泊、水库等水体周边的桥梁、码头、船坞等水上建筑物的基础工程。
本文档将详细介绍水上钻孔灌注桩的施工方案,包括施工前准备、施工工艺、施工步骤和注意事项等内容。
2. 施工前准备在进行水上钻孔灌注桩施工前,需要进行以下准备工作:1.安排人员:组建施工队伍,包括施工人员、监理人员和安全人员等,确保施工过程安全顺利进行。
2.设计方案审查:对设计方案进行审查,确保施工方案符合设计要求。
3.资源准备:准备所需的施工设备和材料,包括钻机、灌注桩配件、水泥、砂、石等。
4.现场勘察:对施工现场进行详细勘察,了解水深、水质、水流情况等特点,做好施工准备工作。
3. 施工工艺水上钻孔灌注桩的施工主要包括以下步骤:1.钻孔前期准备:在施工现场设置施工平台,并确保它足够稳定。
准备好钻孔机械设备,并对其进行检查和调试。
2.钻孔过程:按照设计方案确定的孔径和孔深,使用钻机进行钻孔作业。
在钻孔过程中,要根据孔壁情况及时采取支护和涌水处理措施。
3.清孔处理:钻孔完成后,使用洗孔液进行清孔处理,以确保孔洞无杂物和泥沙,并保持孔口状态良好。
4.灌注桩施工:根据设计要求,将混凝土和配料按比例进行搅拌,并使用泵送设备将混凝土灌注至钻孔中。
灌注过程中要注意控制灌注速度和浆液的均匀性。
5.灌注完成后,使用振动棒对灌注桩进行振捣,使其成型密实。
6.桩顶处理:根据设计要求,对灌注桩进行顶面处理,如修剪、修平等。
4. 施工步骤4.1 施工前期准备1.设置施工平台:根据现场情况,搭建稳定的施工平台,确保施工安全。
2.检查设备:对钻机和泵送设备等施工设备进行检查和调试,确保正常工作。
3.准备施工材料:包括水泥、砂、石等,按照设计方案要求进行配料准备。
4.2 钻孔过程1.钻孔机械设备安装:将钻机按照设计要求安装在施工平台上,并进行固定。
2.钻孔操作:按照设计要求的孔径和孔深,使用钻机进行钻孔作业。
大孔径冲孔灌注桩施工工艺问题及控制要点分析

大孔径冲孔灌注桩施工工艺问题及控制要点分析摘要:冲孔灌注桩技术是我国目前建筑工程基础施工中最常见的施工方法,其在我国建筑史上有着悠久的历史。
随着近年来社会科学技术的不断发展,各种施工技术和施工机械在建筑工程中的不断应用,钻孔灌注桩施工工艺也取得了一定的发展。
本文主要阐述针对大孔径及土石回填层的冲孔灌注桩的施工工艺及控制要点,旨在为日后同行施工提供借鉴依据。
关键词:冲孔灌注桩地基处理成孔引言目前,我国沿海地区建筑工程施工中,天然地基无法满足建筑工程承载力要求,造成这种因素的主要原因是受到地理因素的影响,使得在当前的建筑工程施工中各个施工缺陷不断涌现。
不良土壤和土质对建筑工程所带来的影响逐步增加。
在沿海地区工程施工中,由于土壤大多为淤泥、软粘土和砂砾土,而地基施工之中所采用的回填土也大多为在周围开山的时候所挖掘出的废弃土和石料。
针对这些措施处理之中,容易造成由于土壤成分和材料的不足造成施工的缺陷和隐患,因此在目前的建筑工程施工中通常都是采用先进的技术体系针对软土地区存在的各种问题及时处理,合理有效的提出各种处理方法和措施。
1、施工工艺1.1 开工准备在冲孔灌注桩施工之前,首先要根据设计要求,针对施工中所存在的各种要求和问题进行处理,提高工程组织设计报表和价格表,对工程材料、配构建和接管单位的节省措施进行应用。
同时还要针对工程在施工中所需要的定位报告、进度计划表严格控制。
其次,要做好测量工作。
1.2 冲孔前准备测量员要对施工的桩号进行测量;机组人员进行护筒埋设;而且要根据护筒位置的要求和处理措施形成有效的测量数据模式。
测量是每个施工中都不容忽视的关键环节之一,成孔的前提便是测量,在测量的过程中要合理的利用地质因素综合分析,确保测量位置能够满足设计需求。
在成孔环节施工中,首先要考虑在施工的过程中容易受到的影响因素,针对桩体的各个影响因素和影响环节进行综合的处理与分析。
1.3 冲孔:冲击成孔,参照地质勘探资料控制落锤冲程,宜低锤密冲,每成孔50cm-100cm置换一次泥浆,将孔内粗颗粒排出。
东海大桥海上大口径超深钻孔灌注桩施工工艺
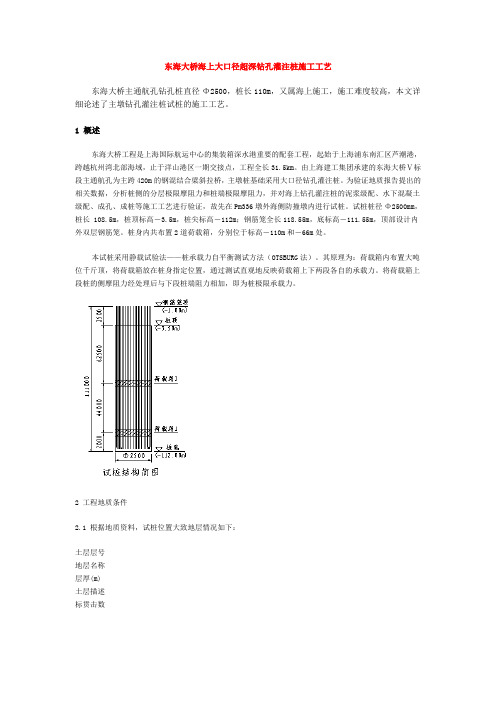
东海大桥海上大口径超深钻孔灌注桩施工工艺东海大桥主通航孔钻孔桩直径Φ2500,桩长110m,又属海上施工,施工难度较高,本文详细论述了主墩钻孔灌注桩试桩的施工工艺。
1 概述东海大桥工程是上海国际航运中心的集装箱深水港重要的配套工程,起始于上海浦东南汇区芦潮港,跨越杭州湾北部海域,止于洋山港区一期交接点,工程全长31.5km。
由上海建工集团承建的东海大桥Ⅴ标段主通航孔为主跨420m的钢混结合梁斜拉桥,主墩桩基础采用大口径钻孔灌注桩。
为验证地质报告提出的相关数据,分析桩侧的分层极限摩阻力和桩端极限摩阻力,并对海上钻孔灌注桩的泥浆级配、水下混凝土级配、成孔、成桩等施工工艺进行验证,故先在Pm336墩外海侧防撞墩内进行试桩。
试桩桩径Φ2500mm,桩长 108.5m,桩顶标高―3.5m,桩尖标高―112m;钢筋笼全长118.55m,底标高―111.55m,顶部设计内外双层钢筋笼。
桩身内共布置2道荷载箱,分别位于标高―110m和―66m处。
本试桩采用静载试验法——桩承载力自平衡测试方法(OTSBURG法)。
其原理为:荷载箱内布置大吨位千斤顶,将荷载箱放在桩身指定位置,通过测试直观地反映荷载箱上下两段各自的承载力。
将荷载箱上段桩的侧摩阻力经处理后与下段桩端阻力相加,即为桩极限承载力。
2 工程地质条件2.1 根据地质资料,试桩位置大致地层情况如下:土层层号地层名称层厚(m)土层描述标贯击数淤泥质粉质粘土5.4夹较多薄层砂,土质极软④1淤泥质粘土9.75夹少量薄层砂,水平层理发育⑤1粘土5.4局部有粉细砂夹层⑥粉质粘土2含氧化铁斑,下部变为砂质粉土⑦1-1砂质粉土5.65土质不均,局部夹少量薄层粘性土28.5⑦1-2粉细砂10.25夹薄层粉质粘土,局部含Φ2~5cm砾石39.3⑦2粉细砂32.5局部含少量Φ1~5cm砾石,下部夹薄层粉质粘土及粉土61.1⑨含砾中粗砂8.4夹较多薄层粉砂,含有5cm厚的半腐木材62.2粉质粘土11.4夹粉土,局部为坚硬状态,下部含有40mm砾石3711-1粉细砂13.3夹少量粉质粘土及粉土70.42.2 影响成孔主要地层⑦2层粉细砂标贯击数大于60,相当密实,且该层厚度达32~33米,是全孔钻进耗时最多的地层。
钻孔灌注桩的施工工艺及方法

钻孔灌注桩的施工工艺及方法(一)、施工工艺流程测量定位→埋设护筒→钻机就位→钻进成孔→下放钢筋笼→下放导管→灌注混凝土→起拔护筒(二)、施工方法和技术措施(1)、桩位由专业测量人员测定后做好保护,然后挖埋钢护筒。
护筒中心和桩位中心的偏差不得超过20MM。
埋设护筒时护筒四周要用土填埋夯实。
钻机就位偏差控制在20MM以内。
(2)、钻机采用自然造浆机械加压钻孔的方法,在钻进过程中主要控制好泥浆比重和钻进速度的关系。
针对本工程地层状况,钻进过程泥浆比重宜控制在1.2--1.3范围内。
钻至终孔标高后要进行清孔,具体方法就是先把钻头提离孔底50公分左右,慢慢转动,加大泵量以使孔内浮渣大量排出孔外。
同时加入清水稀释泥浆,降低泥浆比重在1.25左右。
然后提钻。
(3)、钻成孔后的后续工作应尽力抓紧。
提钻后立即组织下放钢筋笼。
钢筋笼下放焊接时应保持竖直,孔口连接焊好后慢慢下放入孔内。
下放到预定位置后孔口用吊筋固定。
(4)、钢筋笼放好后开始下导管,下导管前检查导管的管壁完好性和内壁的光滑度。
下放过程中每一节对接时加放橡胶密封圈,保证对接部位不漏水。
导管放好后进行第二次清孔,沉渣合格后尽快浇注混凝土。
(5)、浇注混凝土前先把导管提离孔底30--50公分,以保证浇注畅通。
浇注混凝土应做到连续浇注。
保证足够的初灌量,埋管深度控制在2--5米。
灌注到桩顶标高部位时保证有足够的超灌量,确保桩头质量。
(三)、施工中质量技术控制要点(1)、桩位定位后,严格控制护筒埋设偏差和钻机就位偏差,以上两项偏差指标都是不超过2公分。
(2)、钻孔灌注桩成孔设备就位后,必须平正、稳固,确保在施工中不发生倾斜、移动。
(3)、钻孔灌注桩施工现场所有设备、设施、安全装置、工具配件以及个人劳保用品必须经常检查,确保完好和使用安全。
(4)、钻孔灌注桩施工期间,护筒内的泥浆面应高出地下水位1.0米以上。
(5)、钻孔灌注桩应采取隔桩施工,在相邻桩混凝土到达70%的设计强度后,方可成孔施工。
海上特大型钻孔灌注桩施工技术_secret
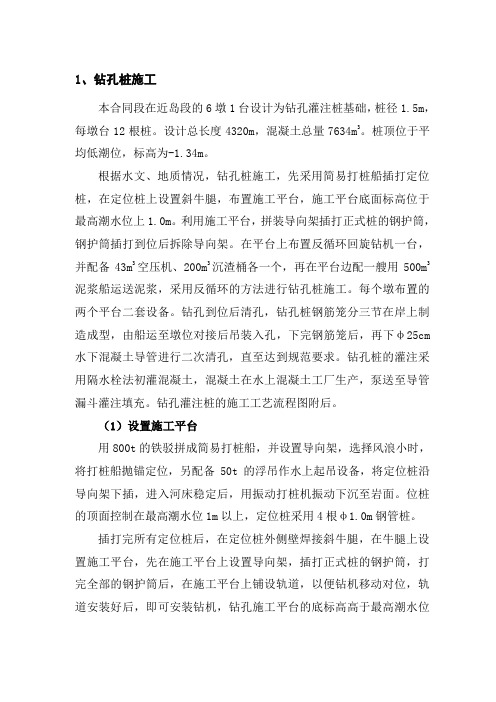
1、钻孔桩施工本合同段在近岛段的6墩1台设计为钻孔灌注桩基础,桩径1.5m,每墩台12根桩。
设计总长度4320m,混凝土总量7634m3。
桩顶位于平均低潮位,标高为-1.34m。
根据水文、地质情况,钻孔桩施工,先采用简易打桩船插打定位桩,在定位桩上设置斜牛腿,布置施工平台,施工平台底面标高位于最高潮水位上1.0m。
利用施工平台,拼装导向架插打正式桩的钢护筒,钢护筒插打到位后拆除导向架。
在平台上布置反循环回旋钻机一台,并配备43m3空压机、200m3沉渣桶各一个,再在平台边配一艘用500m3泥浆船运送泥浆,采用反循环的方法进行钻孔桩施工。
每个墩布置的两个平台二套设备。
钻孔到位后清孔,钻孔桩钢筋笼分三节在岸上制造成型,由船运至墩位对接后吊装入孔,下完钢筋笼后,再下φ25cm 水下混凝土导管进行二次清孔,直至达到规范要求。
钻孔桩的灌注采用隔水栓法初灌混凝土,混凝土在水上混凝土工厂生产,泵送至导管漏斗灌注填充。
钻孔灌注桩的施工工艺流程图附后。
(1)设置施工平台用800t的铁驳拼成简易打桩船,并设置导向架,选择风浪小时,将打桩船抛锚定位,另配备50t的浮吊作水上起吊设备,将定位桩沿导向架下插,进入河床稳定后,用振动打桩机振动下沉至岩面。
位桩的顶面控制在最高潮水位1m以上,定位桩采用4根φ1.0m钢管桩。
插打完所有定位桩后,在定位桩外侧壁焊接斜牛腿,在牛腿上设置施工平台,先在施工平台上设置导向架,插打正式桩的钢护筒,打完全部的钢护筒后,在施工平台上铺设轨道,以便钻机移动对位,轨道安装好后,即可安装钻机,钻孔施工平台的底标高高于最高潮水位1m以上。
(2)插打钢护筒在施工平台上设置导向架,利用50t的浮吊起吊钢护筒,并将钢护筒沿导向架下插,进入河床稳定后,再用振动打桩机振动下沉至预定标高。
在整个插打过程中,测量人员全过程跟踪控制,以保证钢护筒倾斜度在1%以内,孔口偏差在5cm以内。
(3)钻机的选型与配置根据墩位处的地质条件,选择泵吸反循环的回旋钻机,采用刮刀钻头和滚刀钻头,覆盖层采用刮刀钻头,基岩处采用滚刀钻头,并配置43m3的空压机一台,用500m3的泥浆船。
海上超长钻孔灌注桩旋挖钻机成孔施工技术

桩 基 直 径 为中2 O 2 c 5 2 0 m的 变 截 面 桩 .根 据 墩 位 所 在 地
的 地 质 条 件 分 析 . 要 为砂 土 亚 粘 土 夹 杂 分 布 . 以 砂 性 土 为 主 且 主 .d L S T 过程 中 易 发 生 倾 斜 . 钻 头 宜 选 用 单 腰 带 四 翼 刮 刀 钻  ̄ 故
间 内稳 定 不坍 孔 是 关键 。
叠 合 梁 斜 拉 桥 , 跨 4 0 , 墩 采 用 3 中22 25 主 6m 主 7 .~ .m变 截 面 钻 孔 灌 注桩 , 长 8 — 0 , 位 地 质 描 述 见 表 1 桩 61 m 墩 1 。
表 1 墩 位 各 地 层 地 质 描 述
收 稿 日期 : 0 2 0 — 3 2 1 — 1 1
机。
根 据 墩 位 地 层 物 理 力 学 性 质 , 需 钻 压 宜 在 2 0 4 0 N, 所 0— 2k 考 虑 到 为 保 证 钻 孔 垂 直 度 必 须减 压 钻 进 ,施 加 在 孔 底 的 钻 压
Ab ta t 11 i ir fHana n p o ssaBrdg r o e ie,8 — 0 m ng wiht aib eco sscin o 3 q .— 5 . hi s r c : 1emanp eso i nYa g uCr s—e i ea eb r dpls 6 1 c l 1 o , t hev ra l r s—e to f 7b222.m T s te i o usso ec n tu to c n l g n u ly c nr l e s rso rl n oe io eln o e i sb oaydil grg nd rc r - h ssf c e nt o sr cint h o o ya dq ai o to a ue fd ii gh lsol v ro gb r dpl yrtr rln isu e o h e t m l e i n
- 1、下载文档前请自行甄别文档内容的完整性,平台不提供额外的编辑、内容补充、找答案等附加服务。
- 2、"仅部分预览"的文档,不可在线预览部分如存在完整性等问题,可反馈申请退款(可完整预览的文档不适用该条件!)。
- 3、如文档侵犯您的权益,请联系客服反馈,我们会尽快为您处理(人工客服工作时间:9:00-18:30)。
海上大型钻孔灌注桩施工工艺分析
摘要:海上大桥工程主通航孔钻孔桩直径大,桩长较长,海上施工条件差、施工难度高,海上超大型钻孔灌注桩施工较少。
本文作者针对实际施工的广东省南澳大桥工程特点和难点探索出一套切实可行的施工工艺,取得了理想的施工效果。
关键词:海上钻孔平台,减压钻进,直螺纹,预拼装,海工混凝土
1 概述
随着国民经济的不断发展,特别是交通行业的高速发展,钻孔灌注桩作为高层建筑、桥梁等结构的基础形式得到广泛应用。
随着高层建筑荷载及桥梁跨度的不断发展,对钻孔灌注桩承载力的要求越来越高,桩径和桩长不断增大[1,2]。
本文主要对于广东省南澳大桥大型钻孔灌注桩施工工艺进行探讨。
2 工程特点和难点
1)结构复杂、施工难度大、桩径达3.1m,同时具备大口径超深变径的特点;钢筋笼为内外双层结构,主筋数量多、主筋连接困难、制作要求高;混凝土设计对电通量和氯离子渗透系数有特殊要求。
2)施工条件差“施工区海况恶劣、风浪较大,对钢护筒施打定位精度影响较大;巨大的涨落潮差对成孔施工有一定影响;施工平台场地狭小,
泥浆循环系统布置困难;海水对钢筋有弱腐蚀作用,海水配置出的泥浆具有稳定性差、易沉淀的缺点。
3 施工方案优化和实施
3.1 施工平台和钢护筒设计
在施工条件恶劣的海上搭设施工平台、打设钢护筒不仅施工难度大、周期长,而且其精度要求难以保证,经方案比选,设计采取蜂窝状海上钻孔平台形式。
采用Φ800*12mm的钢管桩和桩基钢护筒共同受力组建钻孔平台基础,上部结构采用型钢焊接而成,表面铺设钢板、轨道等。
主墩施工钢平台平面尺寸为53.5×27m,首先采用打桩船施打钢管桩,海上钻孔平台在搭设过程中为钢护筒区域预留Φ3.1m钢护筒施打位置,平台搭设完成后以导向架为导向和定位采用龙门吊打入钢护筒,克服了海上钢护筒施打平面偏位大、垂直度不能保证的缺点。
3.2 成孔工艺
(1)选择设备
根据地层情况和钻孔深度,选配ZJD3500型钻机(扭矩120kN·m),钻头选用防斜梳齿钻头,并采取措施增加钻头的稳定性、刚度和耐磨性能,提高钻进效率。
钻杆设计采用双壁大通径高强度抗扭气举钻杆,Φ273mm,每节钻杆设4个剪力销。
钻杆扭矩达21t·m,大于钻机扭
矩75%,保证成孔顺利。
为有效保证钻孔垂直度、防止孔斜,同时提高钻进效率,采用加配重块“减压悬吊钻进”,在钻进成孔过程中使钻杆始终保持受拉状态。
根据地质条件和钻具性能确定配重块重量为10t。
(2) 泥浆配制方案,.
a)泥浆用水的选用为克服淡水运输对天气和海况的依赖、保证工程顺利进行,制定了直接抽取平台位置地下承压水、并与淡水勾兑成氯离子含量小于1100mg/L的泥浆用水的方案,试验证明可以满足钻孔施工对泥浆的要求;b)泥浆配置在钢护筒内自然造浆,出护筒后根据泥浆性能在砂质粘土层或粉细砂层中利用反循环人工造浆,同时加入纯碱对膨润土进行钠化改良。
纯碱具有充分分解膨润土、增加PH值、提供成孔所需的碱性环境,有效减少沉淀速度和沉渣厚度的作用。
根据经验和试验结果,在本工程中添加优质纯碱量为膨润土量的 1.8~4%较为合适,掺量较常规泥浆高。
每方泥浆配比;水:膨润土:纯碱=1000:80~100:2~3.6(kg)。
钻进过程中泥浆比重控制在1.10~1.25,具有一定的液柱压力,以达到平衡孔壁外围地层压力、稳定孔壁、满足反循环施工工艺的要求;粘度控制在18~25s,以满足钻进护壁和二次清孔的要求;PH值维持在8~9,使泥浆处于碱性状态、提高粘土的分散度;c)泥浆循环系统设计由于施工平台场地狭小、无法布置较长的多级沉淀池,故采用粗颗粒砂沉淀桶和旋流除渣器弥补循环系统的不足。
粗颗粒沉淀桶上设计4mm间隙的筛网,将大于
4mm的渣粒从泥浆中完全分离;过滤后的泥浆再通过旋流除渣器进行悬流处理,将5mm以下的砂砾分离出来。
通过沉淀桶和旋流除渣器后的泥浆比重可以降至1.15以下。
砂率减低至2~3%,效果极为明显。
(3)钢筋笼制作安装工艺
a)主筋连接工艺。
主筋连接形式有三种:焊接、挤压套筒连接和直螺纹连接。
由于本工程主筋直径大、数量较多、间距密,桩顶部又为内外双层钢筋笼,采用传统的焊接连接工艺显然无法完成,而挤压套筒连接工艺又存在耗时长、操作不便等缺点,故采取直螺纹连接工艺。
b) 卡板台座生产工艺。
钢筋笼在自重作用下即可产生较大的变形。
给钢筋笼制作带来很大的困难,而且直螺纹连接工艺对主筋间距和位置要求极为严格,为此专门设计卡板台座加工和堆放钢筋笼,有效消除钢筋笼的自重变形,同时有效控制主筋间距和位置,保证制作质量。
台座总长度36m,卡板根据加强筋间距每2m铺设一道,用经纬仪布设,保证两节钢筋笼在台座上对接预拼装。
卡板上根据主筋直径和间距布设限位以固定主筋,随后安装加强筋,最后安装其余主筋和螺旋筋。
c)预拼装技术。
为克服直螺纹连接工艺对主筋长度偏差和平面偏差的特殊要求,保证孔口对接顺利,故在钢筋笼制作时采取预拼装技术。
当第一节24m钢筋笼制作完成后直接将下节笼的上半节12m钢筋笼进行预拼装对接,该12m钢筋笼全部制作完成后再解除直螺纹连接;随后将第一节钢筋笼吊走并将12m钢筋笼吊至台座
端部完成第二节钢筋笼的制作。
解除预拼装前在每节钢筋笼上标出一根对位钢筋,确保孔口主筋能顺利对接。
d )固定架辅助孔口安装钢筋笼采用三点吊,用海上钻孔平台上安装的龙门吊起吊。
由于吊车微调能力差,上下节钢筋笼无法顺利实现准确对接,给施工带来较大困难,为此专门设计钢筋笼固定架予以克服。
固定架上均匀挂设4个20t手拉葫芦,用以悬挂已完成下放的钢筋笼,用手拉葫芦微调下节钢筋笼,使其与龙门吊吊住的上节钢筋笼的所有主筋完全对中,用固定架微调对接钢筋笼使孔口安装更为简便易行。
4 施工效果
由于合理设计选择钢筋笼制作、安装工艺,每根桩直螺纹连接下笼时间仅为10h左右,比采用挤压套筒连接缩短工期30h,保证钻孔桩按期完成施工任务,为后续工作打下坚实的基础。
通过实践有以下几点体会。
1)在海况条件复杂的海域进行钻孔桩施工时,操作平台以及钢护筒的设计应充分研究其使用功能和可操作性,应把海上钢护筒的定位作为一个重要的参数在平台设计时予以考虑,确保钻孔桩平面偏位符合规范要求。
2)海上钻孔桩成孔施工的关键在于泥浆性能,应根据实际情况比选确定最合理的泥浆配比方案以获得最好的泥浆护壁效果,并较好地克服天气和海况影响。
3)应确定合理高效的钢筋笼制作、连接工艺,克服海上施工平台狭小、运输不便的缺点,保证钻孔施工有序进行,确保进度目标。
本工程所采用的主筋直螺纹连接工艺、预拼装法卡板台座生产工艺可以作为海上超大型钻孔桩钢筋笼施
工的最佳工艺之一。
4)抗渗混凝土的设计是保证混凝土质量的关键,可以通过添加适量粉煤灰和矿粉来增加混凝土的密实度和耐久性,提高泵送性能,使之符合电通量和氯离子渗透系数指标。