常用粉末冶金模具材料
上千种粉末冶金材料化学成分

上千种粉末冶金材料化学成分
摘要:
一、粉末冶金材料概述
二、粉末冶金材料的分类
三、粉末冶金材料的应用领域
四、粉末冶金材料的发展趋势与前景
正文:
粉末冶金材料是一种以金属粉末或金属与非金属粉末的混合物为原料,通过成形和烧结等工艺制造的金属材料或复合材料。
粉末冶金材料因其独特的化学成分和物理、力学性能,在新材料的发展中起着举足轻重的作用。
粉末冶金材料可以分为以下几类:
1.粉末冶金结构材料:这类材料能承受拉伸、压缩、扭曲等载荷,具有良好的力学性能。
包括烧结结构材料、粉末冶金高速钢等。
2.粉末冶金工模具材料:包括硬质合金、粉末冶金高速钢等。
这类材料具有较高的硬度、韧性和耐磨性,可用于制造切削刀具、模具和零件的坯件。
3.多孔粉末冶金材料:这类材料具有孔隙度可控的特点,如多孔过滤材料、多孔含油轴承等。
4.粉末冶金磁性材料:如铁氧体磁性材料、永磁合金等。
这类材料具有较高的磁性能,广泛应用于磁性器件、磁力矫治等领域。
5.粉末冶金功能材料:如电催化材料、导电材料、热管理材料等。
这类材料具有独特的功能特性,可在电子、能源等产业中发挥重要作用。
粉末冶金材料广泛应用于航空航天、汽车、摩托车、家电、能源、电子、通讯、仪器仪表等领域。
随着科技的进步和产业的发展,粉末冶金材料在新能源、节能减排、环保等领域将发挥越来越重要的作用。
粉末冶金材料的分类及应用

粉末冶金材料的分类及应用粉末冶金材料的分类及应用粉末冶金材料的分类及应用【摘要】粉末冶金材料有着传统熔铸工艺不能获取的独特化学成分及物理性能,且具有一次成型等特点,因此被广泛应用。
本文主要从粉末冶金材料的主要分类入手,重点对其应用进行了阐述,希望给行业相关人士一定的参考和借鉴。
【关键词】:粉末冶金;材料;分类;应用0.引言所谓的粉末冶金材料指的是用几种金属粉末或者金属与非金属粉末为原料,通过配比、压制成型以及烧结等特殊工艺制成的各类材料的总称,而这种与熔炼和铸造明显不同的工艺也被统称为粉末冶金法。
因其生产流程与陶瓷制品比较类似,所以又被称为金属陶瓷法。
就目前而言,粉末冶金法不单是用来制取某些特殊材料的方法,也是一种优质的少切屑或者无切屑方法,且其具有材料利用率高、生产效率高,节省占地面积及机床等优点。
然而粉末冶金法也并非万能之法,其无论是金属粉末还是模具都有着较高的成本,且制品的形状和大小都受到一定的限制。
1.粉末冶金材料的主要分类1.1传统的粉末冶金材料第一,铁基粉末冶金材料。
作为最传统也是最基本的粉末冶金材料,其在汽车制造行业的应用最为普遍,并随着经济的迅猛发展,汽车工业的不断扩大,铁基粉末冶金材料的应用范围也就变得越来越广阔,因此其需求量也越来越大。
与此同时,铁基粉末冶金材料对其他行业来说也非常重要。
第二,铜基粉末冶金材料。
众所周知,经过烧结铜基制作的零件抗腐蚀性相对来说比较好,且其表面光滑没有磁性干扰。
用来做铜基粉末冶金材料的主要材料有:烧结的青铜材质、黄铜材质以及铜镍合金材料等,此外还有少量的具有弥散性的强化铜等材质。
在现代,铜基粉末冶金材料主要备用到电工器件、机械设备零件等各个制造类领域中,同时也对过滤器、催化剂以及电刷等有一定的作用。
第三,难熔金属材料。
因这类材料的熔点、硬度、强度都比较高,因此其主要成分为难熔性的金属及金属合金复合材料,主要被应用国防、航空航天以及和研究领域等。
第四,硬质合金材料。
粉末冶金模具及设计介绍
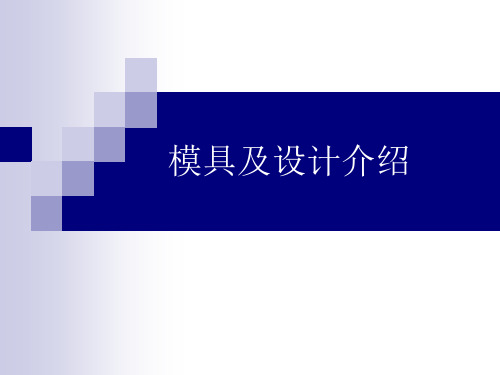
45°
30°
模具耐用设计
1.内外有效段不一样长,有效提高模 具强度; 2.尽可能的内有效段小于外有效段, 节省成本; 3.逃气孔尽可能向上开到根部,提高 强度避免粉末喷出,上二零件不开逃 气孔,在上二冲底部磨小缺口跑气; 4.尽可能大的R弧或斜角过渡,且光 洁度尽可能高,避免应力集中; 5.尽可能小的底座,防止垫片受力时 挠曲导致底座受力后折断; 6.底座倒5°角,防止垫片挠曲,模 冲受力面外移引起模具断裂
模具设计
1.根据产品外形和尺寸、强度要求,制定产品的工艺 流程。 2.计算和设计所需的成形和整形的机台和成形结构。 3.根据产品材质要求,选择成形原料。 4.根据原料变化率和整形、切削余量,设计模具结构 与尺寸。 5.依照成形方式,画出装配图。 6.画出模具各零件图。 7.设计各测量和装模治具。
3V
ห้องสมุดไป่ตู้淬火
HRC61~63 550
9V MH85 ASP23 ASP60 WC
淬火 淬火 淬火
HRC57-59
600
HRC58~60 800 HRC61~63 650 HRC66~69 700
一胜百晶粒特细PM高速工具钢, 成形上下冲,芯棒, 热处理稳定性好,高耐磨损高 适用温压 韧性 一胜百ASP23改进型,替代易崩 适用斜齿轮或台阶中 角的WC,高耐磨损高韧性 模(用40Cr包套)
上下冲特别是长零件温压零件的上下3v淬火hrc6163550美国cpm粉末钢超级的尺寸稳定性可磨削性和韧性替代高合金钢可解决崩角问题成形上下冲特别是9v淬火hrc5759600美国cpm粉末钢超级的尺寸稳定性可磨削性韧性比3v更高可解决崩角问题mh85淬火hrc5860800大同高速钢高耐磨损高韧性齿形下一冲强制用料温压不可用asp23淬火hrc6163650一胜百晶粒特细pm高速工具钢热处理稳定性好高耐磨损高韧性成形上下冲芯棒适用温压asp60淬火hrc6669700一胜百asp23改进型替代易崩角的wc高耐磨损高韧性适用斜齿轮或台阶中模用40cr包套wchra91yg6hra89yg8hra87yg15国600进口1000g代表钴含量越高韧性越好耐磨性也较差一般采用超微粒春宝国产稍差常用模具材料热处理工艺牌号使用硬度热处理温度保温时回火时间温度冷却方式sldhrc5759hrc60611030125分钟3小时220160风v4hrc5657hrc60611130125分钟3小时220160风skh9hrc5759hrc6061119035分钟3小时605580风cr12hrc4550960100分钟3小时530风40crhrc4550860100分钟3小时450风1
冲压模具材料的种类及特性
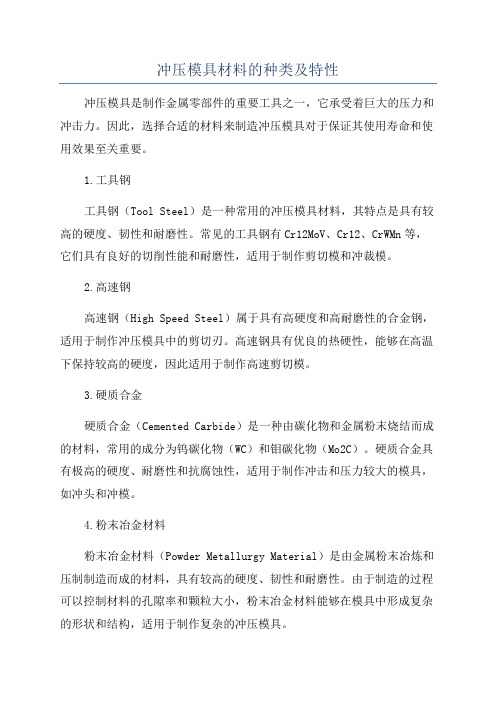
冲压模具材料的种类及特性
冲压模具是制作金属零部件的重要工具之一,它承受着巨大的压力和冲击力。
因此,选择合适的材料来制造冲压模具对于保证其使用寿命和使用效果至关重要。
1.工具钢
工具钢(Tool Steel)是一种常用的冲压模具材料,其特点是具有较高的硬度、韧性和耐磨性。
常见的工具钢有Cr12MoV、Cr12、CrWMn等,它们具有良好的切削性能和耐磨性,适用于制作剪切模和冲裁模。
2.高速钢
高速钢(High Speed Steel)属于具有高硬度和高耐磨性的合金钢,适用于制作冲压模具中的剪切刃。
高速钢具有优良的热硬性,能够在高温下保持较高的硬度,因此适用于制作高速剪切模。
3.硬质合金
硬质合金(Cemented Carbide)是一种由碳化物和金属粉末烧结而成的材料,常用的成分为钨碳化物(WC)和钼碳化物(Mo2C)。
硬质合金具有极高的硬度、耐磨性和抗腐蚀性,适用于制作冲击和压力较大的模具,如冲头和冲模。
4.粉末冶金材料
粉末冶金材料(Powder Metallurgy Material)是由金属粉末冶炼和压制制造而成的材料,具有较高的硬度、韧性和耐磨性。
由于制造的过程可以控制材料的孔隙率和颗粒大小,粉末冶金材料能够在模具中形成复杂的形状和结构,适用于制作复杂的冲压模具。
5.硬质合成材料
不同的冲压模具材料各有特点和适用范围。
在选择材料时,需要根据冲压件的形状、尺寸和使用环境等因素综合考虑。
同时,还需要结合实际工艺要求和经济效益进行综合评估,选择最合适的材料来制造冲压模具。
粉末冶金材料配方

粉末冶金材料配方粉末冶金(PowderMetallurgy,简称PM)是将金属(粉末)制成零件的一种技术,它比传统机械加工技术更省时、更可靠。
PM材料可用于制造锻件和其他类型的零件,它们的强度和耐久性比传统锻件要高。
PM材料的配方直接决定了最终零件的性能,因此非常重要。
PM 材料的配方通常包括金属、非金属和合金。
金属包括铁、钢、铝、镍、铜和锡等;非金属包括碳、氮、氧、硅、氟等;合金包括钨铁、铬钽、钛铌、钛钡和钛锌等。
PM材料通常需要经过多次添加材料来改变配方,以确保粉末在热压模具中获得高品质的零件。
PM材料的配方也可以用来制造膨胀体和其他特定形状、重量或力学性能的零件,这些零件经常用于涡轮机和制动器等电气设备。
PM 材料的配方还可以用来制造各种新型复合材料,用于特殊应用,如汽车零件、航天器零件和太阳能电池片。
为了达到最佳性能,PM材料的配方应该考虑其特性、性能和结构。
首先,应考虑金属和合金的粒子大小、元素组成和比例,以及非金属的种类和比例,这些都会影响PM材料的机械性能。
粒子大小和元素比例在确定烧结行为和结构的时候也很重要。
其次,应考虑PM 材料的热性能、弹性、疲劳和潮湿行为,以及高温、低温和抗腐蚀行为。
最后,应考虑PM材料的重量和形状,以及其制造的零件的尺寸和精度。
PM材料的配方是一项复杂的科学技术,需要考虑多因素因素,改变其中任何一个因素都会引起PM材料性能的变化。
经验丰富的冶金工程师可以根据用户的要求,研究不同的材料配方,确定最优的配方,并可以给出有关参数和具体的生产工艺要求。
PM材料的配方是一门复杂的科学技术,其配方的精密性和复杂性直接影响零件的性能,因此需要专业的冶金工程师研究原料配方,及时调整配方,以达到最佳性能。
只有通过正确的配方和工艺技术,才能达到最佳的性能要求,保证质量,并降低生产成本。
粉末冶金模具的设计与制造

粉末冶金模具的设计与制造1. 引言粉末冶金是一种重要的金属制造工艺,广泛应用于汽车、航空航天、电子、能源等领域。
在粉末冶金工艺中,模具的设计与制造是关键环节,直接影响产品的质量和性能。
本文将介绍粉末冶金模具的设计与制造过程,包括模具材料的选择、模具的结构设计、加工工艺等内容,以帮助读者全面了解粉末冶金模具的制造方法和技术要点。
2. 模具材料的选择模具材料的选择是粉末冶金模具设计的第一步。
模具材料需要具备一定的硬度、耐磨性和耐各种腐蚀介质的能力。
常用的模具材料有以下几种:•工具钢:具有较高的硬度和韧性,适用于大部分粉末冶金模具的制造。
•高速钢:具有更高的硬度和耐磨性,适用于对模具耐磨性要求较高的情况。
•硬质合金:具有较高的硬度和耐磨性,适用于对模具耐磨性要求极高的情况。
在选择模具材料时,需要根据具体应用场景和成本考虑,综合各种性能指标做出合理选择。
3. 模具的结构设计模具的结构设计是粉末冶金模具制造中的核心环节。
良好的模具结构设计可以提高产品的制造效率和质量,降低生产成本。
以下是模具结构设计的几个要点:•模具的整体结构应该合理,易于安装和拆卸。
模具的结构应简洁、牢固,能够承受制造过程中的力和压力。
•模具的导向和定位系统要设计到位,以确保模具在制造过程中的稳定性和精度。
•模具的开合系统要灵活可靠,能够实现快速开合和调节。
对于大型模具,可以考虑采用液压或气动开合系统。
•模具的冷却系统要充分考虑,以保证模具在制造过程中能够及时散热,提高产品质量和生产效率。
4. 模具的制造过程粉末冶金模具的制造过程主要包括以下几个步骤:4.1 模具设计在模具设计阶段,根据产品的形状和尺寸要求,通过CAD软件进行三维建模。
在设计过程中,要充分考虑模具的可行性和制造工艺,以确保模具的质量和可生产性。
4.2 模具加工模具加工是模具制造的关键环节。
常用的模具加工方法包括数控加工、线切割、铣削等。
在加工过程中,需要根据模具材料和结构要求选择合适的加工工艺,精确控制加工尺寸和表面质量。
内螺纹粉末冶金成型模具的制作方法

内螺纹粉末冶金成型模具的制作方法以内螺纹粉末冶金成型模具的制作方法为标题一、引言内螺纹粉末冶金成型模具是一种用于生产内螺纹零件的工具,它能够将粉末冶金材料压制成具有内螺纹形状的工件。
本文将介绍内螺纹粉末冶金成型模具的制作方法。
二、模具设计在制作内螺纹粉末冶金成型模具之前,首先需要进行模具设计。
模具设计是整个制作过程的基础,它包括模具的形状、尺寸、结构等方面的考虑。
设计师需要根据产品要求和工艺要求,确定模具的具体参数。
三、材料选择模具的材料选择对于模具的使用寿命和生产效率有着重要的影响。
一般而言,模具材料需要具备高硬度、高耐磨性和高强度等特点。
常用的模具材料有高速钢、硬质合金等。
根据具体的工件要求,选择合适的模具材料。
四、加工工艺1. 加工模具的毛坯:根据模具的形状和尺寸要求,选择合适的毛坯材料,然后进行粗加工,将毛坯加工成大致形状和尺寸。
2. 精密加工:进行模具的精密加工,包括车削、铣削、钻孔等工艺。
通过精密加工,将模具加工成最终的形状和尺寸。
3. 热处理:对加工好的模具进行热处理,以提高模具的硬度和耐磨性。
常用的热处理方法有淬火、回火等。
4. 表面处理:对模具进行表面处理,以提高模具的表面光洁度和耐腐蚀性。
常用的表面处理方法有电镀、喷涂等。
五、模具装配模具装配是将各个零部件组装成完整的模具的过程。
在模具装配过程中,需要保证各个零部件的精度和配合度,以确保模具的正常使用。
同时,还需要进行模具的调试和测试,以验证模具的性能和精度。
六、模具调试模具装配完成后,需要进行模具的调试。
调试的目的是检查模具的各个部分是否正常工作,是否符合设计要求。
在调试过程中,需要进行模具的试模和调整,以确保模具能够正常运行。
七、模具使用与维护模具制作完成后,需要进行模具的使用与维护。
在使用模具时,需要注意避免过度加载和过度磨损,以延长模具的使用寿命。
同时,还需要进行模具的定期维护和保养,包括清洁、润滑等,以确保模具的正常使用。
粉末冶金材料
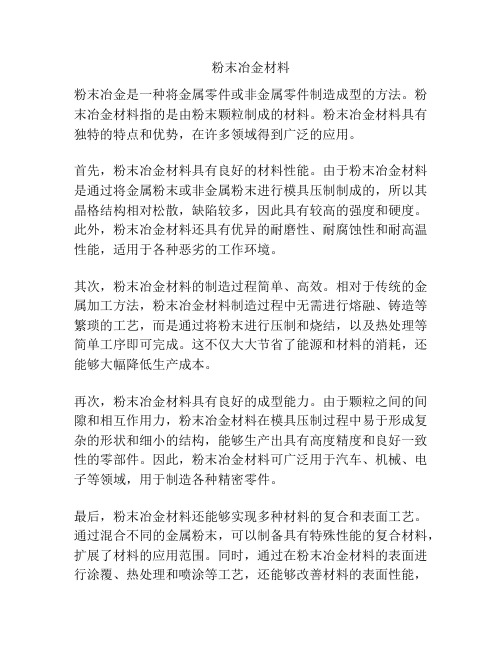
粉末冶金材料
粉末冶金是一种将金属零件或非金属零件制造成型的方法。
粉末冶金材料指的是由粉末颗粒制成的材料。
粉末冶金材料具有独特的特点和优势,在许多领域得到广泛的应用。
首先,粉末冶金材料具有良好的材料性能。
由于粉末冶金材料是通过将金属粉末或非金属粉末进行模具压制制成的,所以其晶格结构相对松散,缺陷较多,因此具有较高的强度和硬度。
此外,粉末冶金材料还具有优异的耐磨性、耐腐蚀性和耐高温性能,适用于各种恶劣的工作环境。
其次,粉末冶金材料的制造过程简单、高效。
相对于传统的金属加工方法,粉末冶金材料制造过程中无需进行熔融、铸造等繁琐的工艺,而是通过将粉末进行压制和烧结,以及热处理等简单工序即可完成。
这不仅大大节省了能源和材料的消耗,还能够大幅降低生产成本。
再次,粉末冶金材料具有良好的成型能力。
由于颗粒之间的间隙和相互作用力,粉末冶金材料在模具压制过程中易于形成复杂的形状和细小的结构,能够生产出具有高度精度和良好一致性的零部件。
因此,粉末冶金材料可广泛用于汽车、机械、电子等领域,用于制造各种精密零件。
最后,粉末冶金材料还能够实现多种材料的复合和表面工艺。
通过混合不同的金属粉末,可以制备具有特殊性能的复合材料,扩展了材料的应用范围。
同时,通过在粉末冶金材料的表面进行涂覆、热处理和喷涂等工艺,还能够改善材料的表面性能,
提高其耐磨、耐腐蚀和摩擦性能。
综上所述,粉末冶金材料是一种具有良好性能、制造过程简单高效、具有良好成型能力和适用于复合和表面工艺的材料。
在工业生产和科学研究中,粉末冶金材料已经得到广泛应用,并在不同领域发挥着重要作用。
粉末冶金模具介绍

粉末冶金模具介绍一、MIM概念及工艺流程金属粉末注射成形是传统粉末冶金技术与塑料注射成形技术相结合的高新技术,是小型复杂零部件成形工艺的一场革命。
它将适用的技术粉末与粘合剂均匀混合成具有流变性的喂料,在注射机上注射成形,获得的毛坯经脱脂处理后烧结致密化为成品,必要时还可以进行后处理生产工艺流程如下配料→混炼→造粒→注射成形→化学萃取→高温脱粘→烧结→后处理→成品二、MIM技术特点金属粉末注射成形结合了粉末冶金与塑料注射成形两大技术的优点,突破了传统金属粉末模压成形工艺在产品形状上的限制,同时利用塑料注射成形技术能大批量、高效率生产具有复杂形状的零件:如各种外部切槽、外螺纹、锥形外表面、交叉通孔、盲孔、凹台、键销、加强筋板,表面滚花等·MIM技术的优点a.直接成形几何形状复杂的零件,通常重量0.1~200gb.表面光洁度好、精度高,典型公差为±0.05mmc.合金化灵活性好,材料适用范围广,制品致密度达95%~99%,内部组织均匀,无内应力和偏析d.生产自动化程度高,无污染,可实现连续大批量清洁生产·MIM与精密铸造成形能力的比较特点精密铸造MIM最小孔直径2mm0.4mm2mm直径盲孔最大深度2mm20mm最小壁厚2mm<1mm最大壁厚无限制10mm4mm直径公差±0.2mm±0.05mm表面粗糙度(Ra)5μm1μm·MIM与其他成形工艺的比较项目 MIM粉末冶金精密铸造机加工密度98%86%98%100%拉伸强度高低高>高光洁度高中中高微小化能力高中低中薄壁能力高中低复杂程度高低中高设计宽容度高中中中材质范围高高中高三、MIM常用材质材料体系合成成分低合金钢Fe-2Ni、F-8Ni不锈钢316L、430L、17-4PH工具钢42Cr2Mo4、M2硬质合金WC-CO(6%)重合金W-Ni-Fe、W-Ni-Cu、W-Cu 四、几种MIM材料的基本性能材料密度(103kg/cm3)硬度拉伸强度Mpa延伸率铁基合金PIM46007.6885HRB40025PIM46507.68100HRB60015不锈钢316L7.9452HRB58045钨合金95%W18.131HRC93010五、MIM产品典型应用领域航空航天业:机翼铰链、火箭喷嘴、导弹尾翼、涡轮叶片芯子等汽车业:安全气囊组件、点火控制锁部件、涡轮增压器转子、座椅部件、刹车装置部件等电子业:磁盘驱动器部件、电缆连接器、电子封装件、手机振子、计算机打印头等军工业:地雷转子、枪扳机、穿甲弹心、准星座、集束箭弹小弹等日用品:表壳、表带、表扣、高尔夫球头和球座、缝纫机零件、电动玩具零件等机械行业:异形铣刀、切削工具、电动工具部件、微型齿轮、铰链等医疗器械:牙矫形架、剪刀、镊子、手术刀等。
常用模具材料
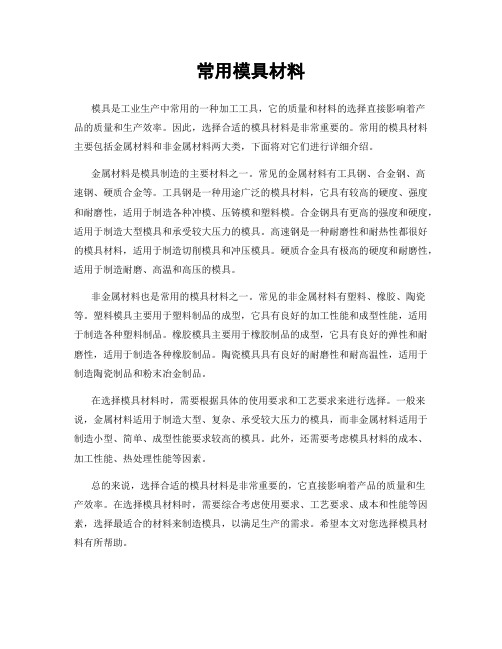
常用模具材料模具是工业生产中常用的一种加工工具,它的质量和材料的选择直接影响着产品的质量和生产效率。
因此,选择合适的模具材料是非常重要的。
常用的模具材料主要包括金属材料和非金属材料两大类,下面将对它们进行详细介绍。
金属材料是模具制造的主要材料之一。
常见的金属材料有工具钢、合金钢、高速钢、硬质合金等。
工具钢是一种用途广泛的模具材料,它具有较高的硬度、强度和耐磨性,适用于制造各种冲模、压铸模和塑料模。
合金钢具有更高的强度和硬度,适用于制造大型模具和承受较大压力的模具。
高速钢是一种耐磨性和耐热性都很好的模具材料,适用于制造切削模具和冲压模具。
硬质合金具有极高的硬度和耐磨性,适用于制造耐磨、高温和高压的模具。
非金属材料也是常用的模具材料之一。
常见的非金属材料有塑料、橡胶、陶瓷等。
塑料模具主要用于塑料制品的成型,它具有良好的加工性能和成型性能,适用于制造各种塑料制品。
橡胶模具主要用于橡胶制品的成型,它具有良好的弹性和耐磨性,适用于制造各种橡胶制品。
陶瓷模具具有良好的耐磨性和耐高温性,适用于制造陶瓷制品和粉末冶金制品。
在选择模具材料时,需要根据具体的使用要求和工艺要求来进行选择。
一般来说,金属材料适用于制造大型、复杂、承受较大压力的模具,而非金属材料适用于制造小型、简单、成型性能要求较高的模具。
此外,还需要考虑模具材料的成本、加工性能、热处理性能等因素。
总的来说,选择合适的模具材料是非常重要的,它直接影响着产品的质量和生产效率。
在选择模具材料时,需要综合考虑使用要求、工艺要求、成本和性能等因素,选择最适合的材料来制造模具,以满足生产的需求。
希望本文对您选择模具材料有所帮助。
粉末冶金高速钢模具工艺流程

粉末冶金高速钢模具工艺流程
1.原材料制备:粉末冶金高速钢模具材料的原料包括金属粉末和其他添加剂。
金属粉末一般由高速钢的主要成分,如铁、碳、铬、钼、钴等金属制成。
其他添加剂可能包括增强剂、增湿剂等。
2.粉末混合:将金属粉末和其他添加剂按一定比例混合均匀,可以采用机械搅拌或者其他方法进行混合。
3.压制成型:将混合好的粉末放入模具中进行冷压成型,一般采用注射成型、压制成型等方法。
冷压成型可以使粉末呈固态状态,便于后续烧结。
4.烧结:将冷压成型的模具进行烧结,提高模具的密实度和强度。
烧结一般在高温下进行,使金属粉末颗粒相互连结成型。
5.热处理:对烧结好的模具进行热处理,改善其力学性能。
热处理可以包括淬火、回火等工艺,使模具达到适应工作环境的要求。
6.加工:热处理后的模具可以进行粗加工和精加工。
粗加工可以包括车削、铣削等工艺,将模具的形状和尺寸加工到接近最终要求。
精加工可以包括打磨、抛光等工艺,提高模具的表面质量。
粉末冶金材料牌号

粉末冶金材料牌号
目前市场上常见的粉末冶金材料牌号有很多,以下是其中一些常见的
粉末冶金材料牌号。
1.高速钢:M2、M35、M42等是常见的高速钢牌号,它们具有优秀的
耐磨性和耐热性能,适用于切削工具和冲击工具等领域。
2.不锈钢:316L、304L、410L等是常见的不锈钢粉末冶金材料牌号,它们具有耐腐蚀性能和优异的力学性能,广泛应用于航空航天、汽车、化
工等领域。
3.铝合金:AlSi10Mg、Al7075等是常见的铝合金粉末冶金材料牌号,它们具有较高的强度、硬度和耐磨性能,广泛应用于航空航天、汽车、船
舶等领域。
4.铜合金:CuNi10、CuCrZr等是常见的铜合金粉末冶金材料牌号,
它们具有良好的导电性、导热性和耐磨性能,广泛应用于电子器件、汽车、船舶等领域。
5.铁基材料:FC-0205、FC-0208等是常见的铁基粉末冶金材料牌号,它们具有良好的机械性能和耐磨性能,广泛应用于汽车、机械设备等领域。
6.硬质合金:YG6、YG8等是常见的硬质合金粉末冶金材料牌号,它
们具有优异的硬度和耐磨性能,广泛应用于切削工具、矿山设备等领域。
7.钼钨合金:Mo70W30、Mo60W40等是常见的钼钨合金粉末冶金材料
牌号,它们具有较高的熔点和优异的耐热性能,广泛应用于航空航天、化
工等领域。
8.钛合金:Ti-6Al-4V、Ti-3Al-2.5V等是常见的钛合金粉末冶金材料牌号,它们具有较好的强度和耐腐蚀性能,广泛应用于航空航天、医疗器械等领域。
以上是一些常见的粉末冶金材料牌号,每种材料具有不同的特性和应用领域。
随着技术的进步和应用的不断拓展,粉末冶金材料的牌号也在不断增加和更新。
粉末冶金材料的分类及应用
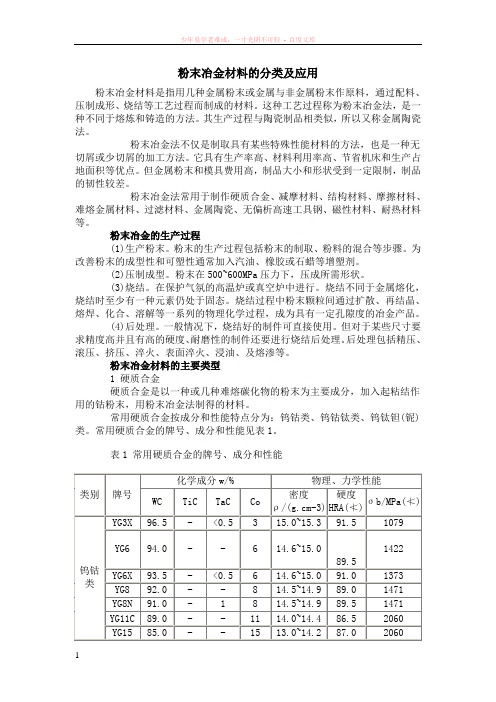
粉末冶金材料的分类及应用粉末冶金材料是指用几种金属粉末或金属与非金属粉末作原料,通过配料、压制成形、烧结等工艺过程而制成的材料。
这种工艺过程称为粉末冶金法,是一种不同于熔炼和铸造的方法。
其生产过程与陶瓷制品相类似,所以又称金属陶瓷法。
粉末冶金法不仅是制取具有某些特殊性能材料的方法,也是一种无切屑或少切屑的加工方法。
它具有生产率高、材料利用率高、节省机床和生产占地面积等优点。
但金属粉末和模具费用高,制品大小和形状受到一定限制,制品的韧性较差。
粉末冶金法常用于制作硬质合金、减摩材料、结构材料、摩擦材料、难熔金属材料、过滤材料、金属陶瓷、无偏析高速工具钢、磁性材料、耐热材料等。
粉末冶金的生产过程(1)生产粉末。
粉末的生产过程包括粉末的制取、粉料的混合等步骤。
为改善粉末的成型性和可塑性通常加入汽油、橡胶或石蜡等增塑剂。
(2)压制成型。
粉末在500~600MPa压力下,压成所需形状。
(3)烧结。
在保护气氛的高温炉或真空炉中进行。
烧结不同于金属熔化,烧结时至少有一种元素仍处于固态。
烧结过程中粉末颗粒间通过扩散、再结晶、熔焊、化合、溶解等一系列的物理化学过程,成为具有一定孔隙度的冶金产品。
(4)后处理。
一般情况下,烧结好的制件可直接使用。
但对于某些尺寸要求精度高并且有高的硬度、耐磨性的制件还要进行烧结后处理。
后处理包括精压、滚压、挤压、淬火、表面淬火、浸油、及熔渗等。
粉末冶金材料的主要类型1 硬质合金硬质合金是以一种或几种难熔碳化物的粉末为主要成分,加入起粘结作用的钴粉末,用粉末冶金法制得的材料。
常用硬质合金按成分和性能特点分为:钨钴类、钨钴钛类、钨钛钽(铌)类。
常用硬质合金的牌号、成分和性能见表1。
表1 常用硬质合金的牌号、成分和性能类别牌号化学成分w/% 物理、力学性能WC TiC TaC Co密度ρ/(g.cm-3)硬度HRA(≮)σb/MPa(≮)钨钴类YG3X 96.5 - <0.5 3 15.0~15.3 91.5 1079 YG6 94.0 - - 6 14.6~15.089.51422 YG6X 93.5 - <0.5 6 14.6~15.0 91.0 1373 YG8 92.0 - - 8 14.5~14.9 89.0 1471 YG8N 91.0 - 1 8 14.5~14.9 89.5 1471 YG11C 89.0 - - 11 14.0~14.4 86.5 2060 YG15 85.0 - - 15 13.0~14.2 87.0 2060YG4C 96.0 - - 4 14.9~15.2 89.5 1422 YG6A 92.0 - 2 4 14.6~15.0 91.5 1373 YG8C 92.0 - - 8 14.5~14.9 88.0 1716钨钛钴类YT5 85.0 - 10 12.5~13.2 89.5 1373 YT15 79.0 - 6 11.0~11.7 91.0 1150 YT30 66.0 - 4 9.3~9.7 92.5 883通用合金YW1 84.0 3 6 12.6~13.5 91.5 1177 YW2 82.0 3 8 12.4~13.5 90.0 13241) 硬质合金的性能硬度高,常温下硬度可达69~81HRC。
粉末冶金

7.爆炸成形
借助爆炸波的高能量使粉末固结的成形方法。 可加工普通压制和烧结工艺难以成形的材料,如难熔金属、高 合金材料等,且成形密度接近于理论密度。还可压制普通压力机 无法压制的大型压坯。
5.2.4 烧结
按一定的规范加热到规定高温并保温一段时间,使 压坯获得一定物理与力学性能的工序。 1.连续烧结和间歇烧结 (1)连续烧结:待烧结材料连续地或平稳、分段地通过具有脱腊、
预热、烧结或冷却区段的烧结炉进行烧结的方式。 生产效率高,适用于大批、大量生产 (2) 间歇烧结:在炉内分批烧结零件的方式。 通过对炉温控制进行所需的预热,加热及冷却循环 生产效率较低,适用于单件、小批生产
2.固相烧结和液相烧结 (1)固相烧结:烧结速度较慢,制品强度较低 (2) 液相烧结:烧结速度较快,制品强度较高,用于具有特殊性能
5.1.2 粉末冶金的机理
1.压制的机理
压制是在模具或其它容器 中,在外力作用下,将粉末紧 实成具有预定形状和尺寸的工 艺过程。 压缩过程中,从而形成具有一定密度和强度的压 坯。随着粉末的移动和变形,较大的空隙被填充,颗 粒表面的氧化膜被破碎,接触面积增大,使原子间产 生吸引力且颗粒间的机械楔合作用增强。
5.2
粉末冶金工艺
金属粉末的制取→预处理→坯料的成形→烧结→后处理等
5.2.1 粉末的制取 机械法和物理化学法两大类 1.机械法
用机械力将原材料粉碎而 化学成分基本不发生变化的 工艺过程。
球磨法:用于脆性材料及合金
研磨法:用于金属丝或小块边
角料
雾化法:用于熔点较低的金属
a) 高速气流雾化 b) 离心雾化 c) 旋转电极雾化
4.等静压制
对粉末(或压坯)表面或对装粉末(或压坯)的软膜表面施以各 向大致相等的压力的压制方法
粉末冶金材料模具设计
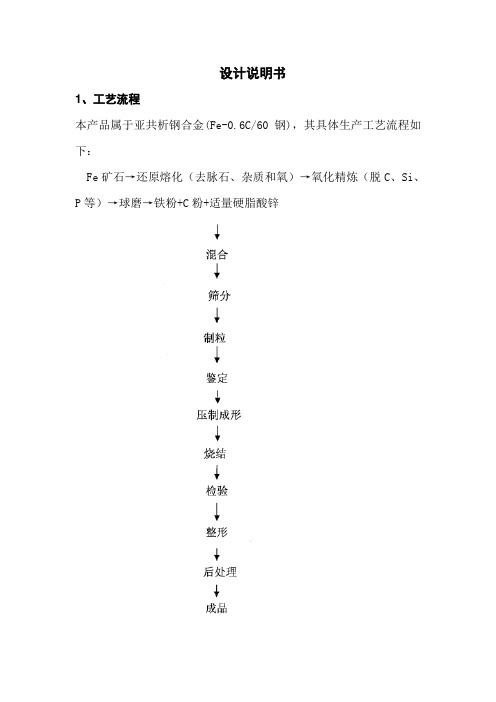
设计说明书1、工艺流程本产品属于亚共析钢合金(Fe-0.6C/60钢),其具体生产工艺流程如下:Fe矿石→还原熔化(去脉石、杂质和氧)→氧化精炼(脱C、Si、P等)→球磨→铁粉+C粉+适量硬脂酸锌2、压坯设计2.1产品零件分析该产品采用Fe-0.6C(60钢),属于铁基制品,其制品密度依靠较高的压坯密度来达到,因此,在压制成形时需要采用较高的单位压力(一般在400-500MPa)。
由于该产品零件形状比较简单,带一个外台阶,采用简单的单上双下模冲即可成形,并使其密度分布均匀。
有配合、定位、相对运动要求的零部件,产品尺寸精度和形位精度及表面粗糙度要求较高,因此,该产品的的尺寸精度定义为IT8、形位精度如图所示为7级,表面粗糙度精度要求为7级。
2.2压坯精度设计由模具设计任务书的零件成品图可得知该产品压坯同轴度需控制在0.08mm,相当于IT10级;压坯垂直度控制为0.1mm,相当于IT11级;压坯侧面平行度为0.15mm,相当于IT12级。
2.3压坯密度和单重的确定由于已知压坯密度ρ=6.6g/cm3,因此压坯单重W=ρ×V ,由成品图给数据计算其压坯体V=h×S,算的V=166.8cm3 ,所以求的压坯单重W=6.6×166.8=1100.8g。
3、压机与压制方式选择3.1压机压力选择铁基制品一般采用固相烧结,其制品密度除了依靠烧结温度、保温时间之外,在一定程度上还依靠较高的压坯密度来达到,因此该产品采用500MPa的单位压力。
根据任务书要求,截面积S=74.0cm2 ,所以F=P×S=5×74=370t脱模压力,根据实际生产经验,铁基压坯的脱模压力P脱模≈0.13P=0.13×500MPa=65MPa3.2压制类型的选择年生产量为50万件,假设每年的工作时间为300天,每天工作时间为8小时,则p=500000/300/8/60=3.47=4件/min,所以选择自动压制。
Powder metallurgy粉末冶金
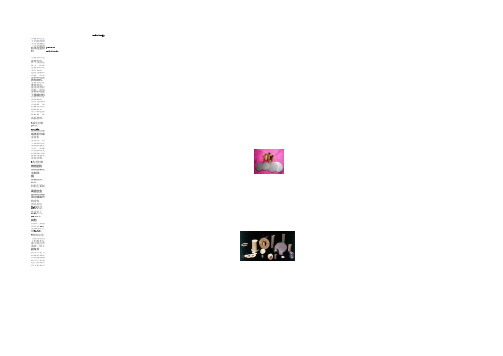
Powder metallurgy粉末冶金用粉末冶金工艺制得的多孔、半致密或全致密材料(包括制品)。
粉末冶金材料具有传统熔铸工艺所无法获得的独特的化学组成和物理、力学性能,如材料的孔隙度可控,材料组织均匀、无宏观偏析(合金凝固后其截面上不同部位没有因液态合金宏观流动而造成的化学成分不均匀现象),可一次成型等。
粉末冶金材料powder metallurgy material①粉末冶金减摩材料。
又称烧结减摩材料。
通过在材料孔隙中浸润滑油或在材料成分中加减摩剂或固体润滑剂制得。
材料表面间的摩擦系数小,在有限润滑油条件下,使用寿命长、可靠性高;在干摩擦条件下,依靠自身或表层含有的润滑剂,即具有自润滑效果。
广泛用于制造轴承、支承衬套或作端面密封等。
②粉末冶金多孔材料。
又称多孔烧结材料。
由球状或不规则形状的金属或合金粉末经成型、烧结制成。
材料内部孔道纵横交错、互相贯通,一般有30%~60%的体积孔隙度,孔径1~100微米。
透过性能和导热、导电性能好,耐高温、低温,抗热震,抗介质腐蚀。
用于制造过滤器、多孔电极、灭火装置、防冻装置等。
③粉末冶金结构材料。
又称烧结结构材料。
能承受拉伸、压缩、扭曲等载荷,并能在摩擦磨损条件下工作。
由于材料内部有残余孔隙存在,其延展性和冲击值比化学成分相同的铸锻件低,从而使其应用范围受限。
④粉末冶金摩擦材料。
又称烧结摩擦材料。
由基体金属(铜、铁或其他合金)、润滑组元(铅、石墨、二硫化钼等)、摩擦组元(二氧化硅、石棉等)3部分组成。
其摩擦系数高,能很快吸收动能,制动、传动速度快、磨损小;强度高,耐高温,导热性好;抗咬合性好,耐腐蚀,受油脂、潮湿影响小。
主要用于制造离合器和制动器。
⑤粉末冶金工模具材料。
包括硬质合金、粉末冶金高速钢等。
后者组织均匀,晶粒细小,没有偏析,比熔铸高速钢韧性和耐磨性好,热处理变形小,使用寿命长。
可用于制造切削刀具、模具和零件的坯件。
⑥粉末冶金电磁材料。
包括电工材料和磁性材料。
粉末冶金模具设计说明书

粉末冶金模具设计说明书姓名:学号:班级:粉末冶金模具设计说明书一、产品分析生产一批圆环状钢制模坯,内径40mm,外径80mm,高度40mm二、压坯设计1.产品分析该产品采用Fe-0.6C(60钢),属于铁基制品,在压制成型时需要采用较高的单位压力(一般在400~500MPa)。
该产品零件形状比较简单,采用上下模冲压制成型。
2.松装密度和压坯密度的确定采用水雾化铁粉压制,松装密度为:ρ松=2.8g/cm3压坯密度为:ρ压=6.6g/cm3三、压机与压制方式选择1.压制压力选择采用400MPa的单位压力,且压坯截面积为:S=12.56cm2则压制压力为:F=P×S=400MPa×12.56cm2=502KN2.压制类型选择因为采用大批量生产,故使用自动压制。
3.压制方式选择采用双向压制。
4.装粉高度、压缩比的确定查表B-2,可得压缩比K=2.35,又压坯高度H坯=40mm,则装粉高度为:H粉=H坯×K=40×2.35=94mm四、成型设备与压制工具系统1.装粉方式选择该产品压坯高度一致,粉料组元之间密度差别不大,模腔形状简单不易产生成分偏析,粉末易于填充,因此采用落下式方法正常装粉。
2.模架选择查表4-26,模架选用上-下一式A型模架。
3.压机类型选择H受力=H坯(K-1)H受力=0.15SmaxSmax =(K-1)H坯/0.15=360mm根据最大压制压力和最大装粉高度要求选择液压式压机。
五、压模主要零件结构设计1.结构组成模具由阴模、上冲模、芯棒、下冲模组成。
2.尺寸计算①阴模高度:由松装粉末高度、下模冲定位高度、上模冲压缩粉末进入阴模前的高度确定:H阴=H粉+H下+H上=94+20+20=134mm。
②阴模内径:D阴内=80mm③阴模外径:查表知当压坯密度为6.6g/cm3时,m=D/d≈2.5~2.8,因此D阴外=200mm。
④上模冲高度:94-40=54mm。
模具常用材料(电子版)

硬质合金;YE50 或
(Cr12MoV)
YE65 钢结硬质合
Cr6WV、(Cr12)、 金(另附模套,模
Cr4W2MoV、
套材料可采用中
Cr2Mn2SiWMoV、 碳钢或 T10A)
(Cr12MoV)
60~62
60~64
形状简单,冲裁材料 厚度≤4mm 的凸、凹
模
T10A、9Mn2V、 9SiCr、GCr15
5CrW2Si、 Cr4W2MoV、 (Cr12MoV)
60~64
T10A、T12A、
形状简单的
修(切)
9Mn2V、GCr15
-
边模
CrWMn、9Mn2V、
形状较复杂的
Cr2Mn2SiWMoV
56~60
58~62
注 : 表 中 有 括 号 的 牌 号 , 因 铬 含 量 高 不 推 荐 采 用 , 可 用 Cr6WV 或 Cr4W2MoV 、
复杂
推荐使用钢号 T10A
MnCrWV
Cr12MoV
SiMnMo Ni-Cr 合金铸铁 Cr12MoV(大型)
CrW5(小型) T10A T7A
MnCrWV Cr12MoV
Cr12MoV
5CrMnMo
代用钢号 Cr2
9Mn2V,CrWMn Cr6WV Cr12 球墨铸铁 GT-15
9CrWMn
5CrNiMo
了解模具失效形式,就可以进一步分析模具的失效原因,找出影响模具失效的各种因素, 从而提高模具质量,延缓模具失效。 模具的性能要求
模具的服役条件 模具是机械工业重要的基础工艺装备。模具成形具有效率高、质量好、节约原材料、降
低成本等许多优点,被广泛应用于机械工业生产的各个领域。 一般情况下,模具的服役条件与安装模具的机床类型、吨位、精度、形成次数、生产效
常用粉末冶金模具材料

粉末冶金模压模工作零件材料及技术要求
零件名称:
凹模芯棒
选用材料:
碳素工具钢:T10A,T12A
合金工具钢:GCr15,Cr12,Cr12Mo,Cr12W,Cr12MoV,9CrSi,CrWMn,CrW5
高速钢:W18Cr4V,W9Cr4V,W12Cr4V4Mo
硬质合金:钢结硬质合金,YG15,YG8(芯棒用硬质合金时,一般为钢与硬合金的焊接镶接形式)
热处理要求:
钢:60~63HRC
钢结硬质合金:64~72HRC
硬质合金:88~90HRA(钢的细长芯棒可降至55~58HRC,带接杆芯棒连接处局部35~40HRC)
其它技术要求:
1. 平磨后退磁
2. 粗糙度要求:
工作面:Rα 0.4~0.1μm
配合面及定位面:
Rα 1.6~0.4μm
非配合面:
Rα 3.2~1.6μm
3. 工作面及配合面公差等级:
IT5~IT7
零件名称:
模冲
选用材料:
碳素工具钢:T8A,T10A
合金工具钢:GCr15,Cr12,Cr12Mo,9CrSi,CrWMn,CrW5 热处理要求:
56~60HRC
其它技术要求:
1. 平磨后退磁
2. 粗糙度要求:
工作面:Rα 0.8~0.4μm
配合面及定位面:
Rα 0.4~0.1μm
非配合面:
Rα 3.2~0.8μm
3. 工作面及配合面公差等级:
IT5~IT7。
- 1、下载文档前请自行甄别文档内容的完整性,平台不提供额外的编辑、内容补充、找答案等附加服务。
- 2、"仅部分预览"的文档,不可在线预览部分如存在完整性等问题,可反馈申请退款(可完整预览的文档不适用该条件!)。
- 3、如文档侵犯您的权益,请联系客服反馈,我们会尽快为您处理(人工客服工作时间:9:00-18:30)。
粉末冶金模压模工作零件材料及技术要求
零件名称:
凹模芯棒
选用材料:
碳素工具钢:T10A,T12A
合金工具钢:GCr15,Cr12,Cr12Mo,Cr12W,Cr12MoV,9CrSi,CrWMn,CrW5
高速钢:W18Cr4V,W9Cr4V,W12Cr4V4Mo
硬质合金:钢结硬质合金,YG15,YG8(芯棒用硬质合金时,一般为钢与硬合金的焊接镶接形式)
热处理要求:
钢:60~63HRC
钢结硬质合金:64~72HRC
硬质合金:88~90HRA(钢的细长芯棒可降至55~58HRC,带接杆芯棒连接处局部35~40HRC)
其它技术要求:
1. 平磨后退磁
2. 粗糙度要求:
工作面:Rα 0.4~0.1μm
配合面及定位面:
Rα 1.6~0.4μm
非配合面:
Rα 3.2~1.6μm
3. 工作面及配合面公差等级:
IT5~IT7
零件名称:
模冲
选用材料:
碳素工具钢:T8A,T10A
合金工具钢:GCr15,Cr12,Cr12Mo,9CrSi,CrWMn,CrW5 热处理要求:
56~60HRC
其它技术要求:
1. 平磨后退磁
2. 粗糙度要求:
工作面:Rα 0.8~0.4μm
配合面及定位面:
Rα 0.4~0.1μm
非配合面:
Rα 3.2~0.8μm
3. 工作面及配合面公差等级:
IT5~IT7。