精密与特种加工作业
精密加工与特种加工作业8

精密加工与特种加工1.什么是精密加工?什么是超精密加工?精密加工和超精密加工的特点是什么?答:精密加工是指在一定的发展时期,加工精度和表面质量达到较高程度的加工工艺。
超精加工是指加工精度和表面质量达到最高程度的精密加工工艺。
精密加工与超精密加工是相对而言,精密加工和超精密加工的概念是与某个时期的加工工艺水平相关联的,随着科技的进步,精密加工和超精密加工所能达到的精度将逐步提高。
特点:(1)“进化”加工。
对于精密加工和超精密加工时,有时可利用低于工件精度的设备、工具,通过工艺手段和特殊的工艺装备,加工出精度高于“母机”的工作母机或工件。
(2)加工设备精度高。
加工设备的几何精度向亚微米级靠近。
(3)切削的切深很小。
切深可能小于工件材料的晶粒尺寸。
(4)精密加工和超精密加工环境必须满足恒温、防振、超净对环境提出的三个方面的要求。
(5)工件材料必须具有均匀性和性能的一致性,不允许存在内部或外部的微观缺陷。
(6)精密测量是进行精密加工和超精密加工的必要条件。
不具备与加工精度相适应的测量技术,就无法判断被加工件的精度。
2.为实现精密与超精密加工,精密机床应该考虑哪些因素?答:(1)关键元件,如主轴、导轨、丝杆等广泛采用液体静压或空气静压元件。
定位机构中采用电致伸缩、磁致伸缩等微位移结构。
设备广泛采用计算机控制、适应控制、在线检测与误差补偿等技术。
(2)精密加工和超精密加工环境必须满足恒温、防振、超净对环境提出的三个方面的要求。
(3)精密加工和超精密加工机床中广泛采用精密光栅、激光干涉仪、电磁比较仪、圆度仪等精密测量元件。
3.简述金刚石精密切削的机理。
金刚石精密切削有哪些应用?答:金刚石超精密切削属微量切削,切削层非常薄,常在0.1μm以下,切削常在晶粒内进行,要求切削力大于原子、分子间的结合力,剪切应力高达13000MPa。
由于切削力大,应力大,刀尖处会产生很高的温度,使一般刀具难以承受。
金刚石超精密切削速度很高,工件变形小,表层高温不会波及工件内层,因而可获得高的加工精度。
精密加工和特种加工简介

精密加工和特种加工简介
13
的工艺技术,适应加工范围广。
一、电火花加工 1.基本原理 电火花加工是基于脉冲放电蚀除原理产生的,故又称 放电加工或电蚀加工。 电火花加工原理图,由脉冲电源、自动进给调节装置、 工作液循环系统、工具电极等组成。 加工时,脉冲电源的一极接工具电极,另一极接工 件电极。两极均浸入具有一定绝缘度的液体介质(常用 煤油或矿物油)中。
精密加工和特种加工简介
2
工件精度和减少表面粗糙度值为目的的加工方法,如研磨、 珩磨等。
光整加工是指不切除或从工件上切除极薄材料层, 以降低表面粗糙度为目的的加工方法,如超精加工、抛 光等。
一、研磨 1.加工原理
研磨是用研磨工具和研磨剂,从工件上研去一层极 薄表面层的精加工方法。
精密加工和特种加工简介
精密加工和特种加工简介
9
超精加工可在普通车床、外圆磨床上进行,对于批 量较大的生产则宜在专用机床上进行。工作时应充分地 加润滑油,以便形成油膜和清洗极细地磨屑。
超 精 加 工 后 地 工 件 表 面 粗 糙 度 Ra 值 约 在 0.1~0.006μm之间。
四、抛光
抛光是利用机械、化学或电化学地作用,使工件获 的光亮、平整表面的加工方法
精密加工和特种加工简介
5
经研磨后的工件表面,尺寸精度可达IT4~IT1级; 表面粗糙度值可减小到0.1~0.006μm。形状精度 相应提高。
亦可
2)生产效率低,加工余量小。 3) 研磨剂易飞溅,污染环境。
在现代制造业中研磨应用很广,许多精密量块、 量规、齿轮、钢球、喷油嘴、石英晶体、陶瓷元件、光 学镜头及棱镜等零件均需研磨。
3
采用不同的研磨工具(如研磨心棒、研磨套、研磨平板等) 可对内圆、外圆和平面等进行研磨。
《精密与特种加工》大作业

大连理工大学研究生试卷实得分数系另1」:机械工程学院题号标准分数1.5课程名称:精密与特种加工 2.5^学1号: ************ 3.104.10姓名:*** 5.106.10:^考试时间. ***************7.108.109.1010.1011.10总分授课教师****1. 目前精密和超精密加工的精度范围分别为多少?答:(1)目前超精密加工技术是指加工尺寸、形状精度达到亚微米级,加工表面粗糙度达到纳米级的加工技术。
在某些领域已经延伸到纳米尺度范围,其加工精度已接近纳米级,表面粗糙度已经达到0.1 nm级,并且正向原子级加工精度逼近。
其中,超精密切削的加工精度高于O.Olum,表面粗糙度在0.02~0.005um之间;超精密磨削的加工精度达到或高于0.1um,表面粗糙度在0.025~0.003um之间;超精密抛光的加工精度可达数纳米,加工表面粗糙度可达0.1 nm级。
(2)精密加工的加工精度为0.1~1um加工表面粗糙度为0.3~0.03um;其中精密磨削的加工精度约为1um表面粗糙度为0.025um。
2. 超精密切削对刀具有什么要求?答:(1)刀具刃口锋锐度p小,以实现超薄切削,减小切削刃表面的弹性恢复和表面变质层;(2)极低的切削刃粗糙度,R y =0.1~02im,以减少刀具刃口误差复映的影响,获得超光滑表面;(3)极高的硬度与耐磨性,极高的弹性模量,以保证刀具具有极高的寿命及很高的尺寸耐用度;(4)足够的强度,刃口无缺陷,耐崩刃,以抵抗切削时晶粒内部强大的分子、原子间结合力;(5)化学亲和力小,和工件材料的抗粘结性好、摩擦系数低,以得到极好的加工表面完整性。
3. 简述超精密切削时刀具刀刃锋锐度对切削过程和加工表面质量的影响。
答:在超精密切削条件下,刀具的刀刃锋锐度对切削变形和加工表面质量有直接的、很明显的影响。
(1)刀具刀刃锋锐度对切削变形有着很大的影响,特别是在背吃刀量和进给量较小的时候。
精密加工和特种加工简介

电火花线切割加工 电火花线切割加工是用线状电极(钼丝或铜
丝)靠火花放电对工件进行切割,故称为电 火花线切割,有时简称线切割。其应用广泛, 占电加工机床旳60%以上。
二、电解加工
1、加工旳基本原理
电解加工(电化学加工)是利用金属 在电解液中产生阳极溶解旳电化学反应原 理,对金属材料进行成形加工旳一种措施。
不产生宏观应力和变形 加工材料范围很广 电子束能量密度高,生产率很高 加工过程能够自动化 污染少,加工表面不氧化 需要一整套专用设备和真空系统,价格较贵,
应用有一定旳不足
➢电子束加工旳应用
按其功率密度和能量注入时间旳不同,可用于打 孔、切割、蚀刻、焊接、热处理和光刻加工等
➢高速打孔
最小直径可达0.003 mm左右 电子束还能加工小深孔(深径比>10:1) 可加工玻璃、陶瓷、宝石等脆性材料
3、电解加工旳特点及应用
(1)能以简朴旳进给运动一次加工出形状复杂旳型 面或型腔,如锻模、叶片等。
(2)可加工高硬度、高强度和高韧性等难切削旳金 属材料。
(3)加工中无机械切削力或切削热,适合于易变形 或薄壁零件旳加工。
(4)加工后零件表面无剩余应力和毛刺。
(5)工具阴极不损耗。
(6)因为影响电解加工旳原因较多难于实现高精度 旳稳定加工。
焦点上到达很高旳能量密度,靠光热效应来加 工多种材料旳。
激光加工旳特点: 功率密度高达108~1010W/cm2,几乎可加工任何材
料 激光光斑可聚焦到微米级,输出功率可调整,可
用于精密微细加工 所用工具为激光束,是非接触加工,所经没有明
显旳机械力,没有工具损耗;加工速度快,热影 响区小 打孔和切割旳激光深度受限
学习精密与特种加工技术心得体会5篇

学习精密与特种加工技术心得体会5篇a;特种加工是对传统机械加工方法的有力补充和延伸。
在已有的特种加工工艺不断完善和定型的同时,新的特种加工技术也不断涌现出来,正在形成面向快速制造的特种加工技术新体系。
下面就是带来的学习精密与特种加工技术心得体会,希望能帮助大家!学习精密与特种加工技术心得体会1这是我第一次到车间里去实习,没有什么准备,只是看了一下零件的加工。
第一个车间是零件加工的车间,伴随着车间中空中吊车的游走声,穿过那挂着破碎门帘的陈旧大门。
且不说车间的一切有点老调和乏味。
但我却能感觉到那些拥有热火朝天的干劲的工人师傅们俭朴的本质和如火的热情。
在这里,技术工人告诉我箱体加工工艺路线的安排车床主轴箱要求加工的表面很多。
在这些加工表面中,平面加工精度比孔的加工精度容易保证,于是,箱体中主轴孔的加工精度、孔系加工精度就成为工艺关键问题。
这里的工人还告诉我在工艺路线的安排中应注意三个问题:1)工件的时效处理箱体结构复杂壁厚不均匀,铸造内应力较大。
由于内应力会引起变形,因此铸造后应安排人工时效处理以消除内应力减少变形。
一般精度要求的箱体,可利用粗、精加工工序之间的自然停放和运输时间,得到自然时效的效果。
但自然时效需要的时间较长,否则会影响箱体精度的稳定性。
对于特别精密的箱体,在粗加工和精加工工序间还应安排一次人工时效,迅速充分地消除内应力,提高精度的稳定性。
2)安排加工工艺的顺序时应先面后孔由于平面面积较大定位稳定可靠,有利与简化夹具结构检少安装变形。
从加工难度来看,平面比孔加工容易。
先加工批平面,把铸件表面的凹凸不平和夹砂等缺陷切除,在加工分布在平面上的孔时,对便于孔的加工和保证孔的加工精度都是有利的。
因此,一般均应先加工平面。
3)粗、精加工阶段要分开箱体均为铸件,加工余量较大,而在粗加工中切除的金属较多,因而夹紧力、切削力都较大,切削热也较多。
加之粗加工后,工件内应力重新分布也会引起工件变形,因此,对加工精度影响较大。
精密加工与特种加工教学大纲5篇
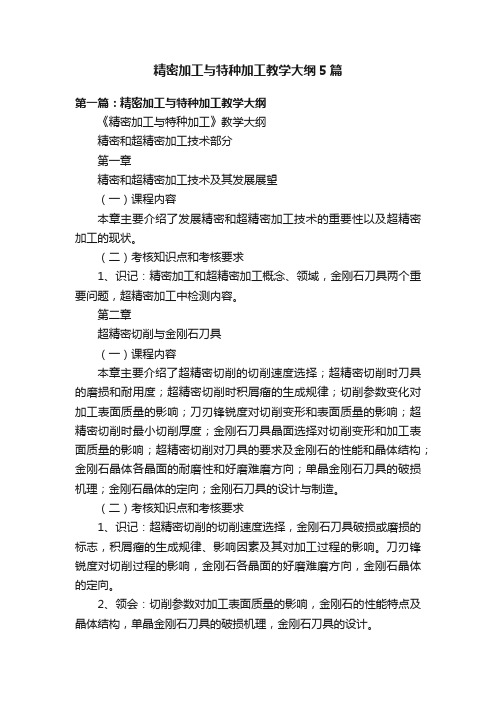
精密加工与特种加工教学大纲5篇第一篇:精密加工与特种加工教学大纲《精密加工与特种加工》教学大纲精密和超精密加工技术部分第一章精密和超精密加工技术及其发展展望(一)课程内容本章主要介绍了发展精密和超精密加工技术的重要性以及超精密加工的现状。
(二)考核知识点和考核要求1、识记:精密加工和超精密加工概念、领域,金刚石刀具两个重要问题,超精密加工中检测内容。
第二章超精密切削与金刚石刀具(一)课程内容本章主要介绍了超精密切削的切削速度选择;超精密切削时刀具的磨损和耐用度;超精密切削时积屑瘤的生成规律;切削参数变化对加工表面质量的影响;刀刃锋锐度对切削变形和表面质量的影响;超精密切削时最小切削厚度;金刚石刀具晶面选择对切削变形和加工表面质量的影响;超精密切削对刀具的要求及金刚石的性能和晶体结构;金刚石晶体各晶面的耐磨性和好磨难磨方向;单晶金刚石刀具的破损机理;金刚石晶体的定向;金刚石刀具的设计与制造。
(二)考核知识点和考核要求1、识记:超精密切削的切削速度选择,金刚石刀具破损或磨损的标志,积屑瘤的生成规律、影响因素及其对加工过程的影响。
刀刃锋锐度对切削过程的影响,金刚石各晶面的好磨难磨方向,金刚石晶体的定向。
2、领会:切削参数对加工表面质量的影响,金刚石的性能特点及晶体结构,单晶金刚石刀具的破损机理,金刚石刀具的设计。
第三章精密磨削和超精密磨削(一)课程内容本章主要介绍了精密和超精密磨削;精密磨削;超硬磨料砂轮磨削;超精密磨削;精密和超精密砂带磨削。
(二)考核知识点和考核要求1、识记:精密和超精密磨料加工方法分类,精密和超精密磨削的特点及其应用,精密和超精密磨削工艺,砂带磨削方式、特点、应用范围及其机理。
2、领会:精密磨削机理,精密磨削与超硬磨料砂轮的修整,超精密磨削机理及其特点。
第四章精密和超精密加工的机床设备(一)课程内容本章主要介绍了精密主轴部件;床身和精密导轨部件;进给驱动系统;微量进给装置;机床的稳定性和减振隔振;减少热变形和恒温控制。
04精密加工和特种加工

抛光特点:
①方法简便、经济,不用特殊设备;
②容易对曲面进行加工;
③只能提高粗糙度,不能改变零件的尺寸精度、形状精度或位置精度;
④劳动条件差。
抛光应用: 抛光主要用于零件表面的装饰加工,或者利用抛光方法去除前道工序的加工
痕迹,提高零件的疲劳强度。
抛光零件表面的形状可以是平面、外圆、孔、以及各种成形表面等。 五、各种精密加工方法的比较:
用装有细磨粒、低硬度的油石磨头,在一定压力下 对工件表面进行光整加工的方法称为超级光磨 。
• 加工时工件旋转,油石以恒力轻压于工件表面, 在作轴向进给的同时作轴向微小振动,从而达到 对工件微观不平的表面进行光磨的效果。
超级光磨的特点 : ①加工余量极少,一般为3 ~ 10μm; ②生产率较高,一般加工时间只需30~60秒; ③表面质量好,Ra<0.012μm; ④设备简单,操作方便。 但是,超级光磨只能提高表面质量,不能提高尺寸精度和形位精度。
第二节 特种加工
特种加工是相对于传统的切削加工而言,传统的切削加工是用刀具靠机械 能去除工件表面的多余材料。当工件材料的强度、硬度、脆性、韧性过高, 或零件的结构过于复杂,或尺寸太小,或零件的刚度较差时,传统的切削加 工方法就难于实现。特种加工就是为解决这些难题而发展起来的一种新的加 工方法.
特种加工是直接利用电能、光能、声能、热能、化学能或多种能量复合形 式进行加工的方法。常用的特种加工有电火花加工、电解加工、超声波加工、 激光加工、电子束加工和离子束加工等。
精度为3~O.3 μm,粗糙度为O.3~O·03μm的叫精密加工;
精度为0.3~0.03 μm,粗糙度为0.03~0.005 μm的叫超精密加工,或亚微米 加工;
精度为0.03 μm(30纳米),粗糙度优于0.005 μm以上的则称为纳米(nm)加工。
精密加工和特种加工简介
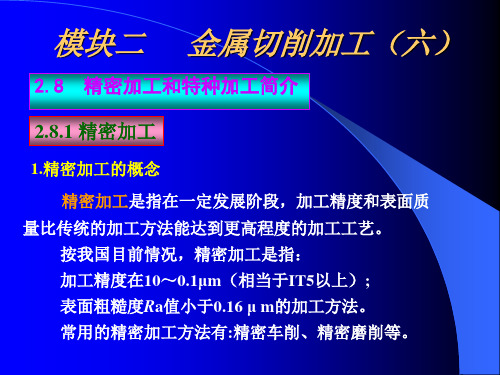
二. 相关知识
(一)精密加工 1、概述
精密加工中,精度高于0.1μm ,表面粗糙度Ra 值小于0.1μm的加工方法称为超精密加工。 常用的超精密加工方法有镜面车削、虹面车削, 超精密磨削、镜面磨削等。
(1)机床设备条件
精密加工必须在精密机床上进行。机床应具有 高的运动精度、刚度和转速,以及小的进给量。
用硬质合金精密车刀进行精密车削时,一般采用高 的切削速度:车铝合金材料vcmax=350m/min,车青铜等 铜合金材料vcmax=400m/min;车镁合金材料vcmax = 1000m/min。切削速度越高,获得的表面粗糙度值越小,
但刀具磨损及振动也随之加剧,所以应根据实际情况来
合理选择。一般取进给量ƒ=0.02~0.04 mm/r;背吃刀 量一般取aP =0· 2~0.3 mm。
(二) 特种加工 1.概述
(1)特种加工 特种加工是指除常规切削加工以 外的新的加工方法,这种加工方法利用电、磁、 声、光、化学等能量或其各种组合作用在工件的 被加工部位上,实现对材料的去除、变形、改变 性能和镀覆,从而达到加工目的。
(2)特种加工特点
1)不是主要依靠机械能,而是主要用其他能量(如 电、热、光、化学、声等)去除金属材料,这些能量的瞬 时能量密度很高,所以可加工任何高硬度的材料。 2)工具硬度可以低于被加工材料的硬度。 3)加工过程中,因工具与工件基本不接触,加工时 不存在显著的机械切削力。 4)加工机理不同于一般金属切削原理,不产生宏观切
超精加工的磨具为油石,选用细粒度, 以较低的压力和切削速度对工件表面进行 加工,加工时有三种运动,即工件的低速 回转、磨具的轴向进给运动和油石的高速 往复振动。油石振动的频率为10~25 Hz, 振幅为1~5mm,油石对工件表面的压力 Pa=15×104 Pa。
精密加工和特种加工

六、离子束加工
1、原理
2、工艺特点与应用 离子束的直径在1um以内 离子束的直径在1um以内 真空中加工, 真空中加工,防止氧化 微观作用力 主要用作纳米加工,甚至是分子级、 主要用作纳米加工,甚至是分子级、原子 级加工, 级加工,IC 制造
五、比较
抛光 超级光磨 研磨 珩磨 加工质量 提高光 降低 Ra 亮程度 应用范围 加工各种表面 工具设备 简单 生产效率 最高 稍复杂 最低 既降低 Ra,又提高 Ra, 尺寸、 尺寸、形状精度 孔 复杂 较高
第2节 特种加工
一、电火花加工 二、电解加工 三、超声波加工 四、激光束加工 五、电子束加工 六、离子束加工
二、电解加工
电化学加工: 电化学加工: 电解加工: 电解加工:从工件上去除金属 电镀 :向工件上沉积金属
1、原理(阳极溶解) 原理(阳极溶解)
工件阳极反应: 工件阳极反应: Fe2+ + 2(OH)— Fe(OH)2 (沉淀) 沉淀) 4Fe(OH)2 + 2H2O + O2 4Fe(OH)3 工具阴极反应: H2 工具阴极反应:2H+ + 2e—
2、工艺特点 与电火花相同的方面) (与电火花相同的方面) 可加工难切削材料,如淬火钢、 可加工难切削材料,如淬火钢、硬质合金 无切削力 可加工复杂型面零件 与电火花不同的方面) (与电火花不同的方面) 工具不损耗 生产效率高 精度低、表面无应力和毛刺, 精度低、表面无应力和毛刺,Ra 低 对机床有腐蚀
一、电火花加工
1、原理
2、工艺特点 可加工难切削材料 即硬、 即硬、脆、软、韧、高熔点的导电材料 无切削力, 无切削力,不接触加工 以柔克刚” 工具材料软( 石墨) “以柔克刚” ,工具材料软(铜、石墨) 可加工复杂型面零件
精密与特种加工技术论述 (3)

辽宁科技学院(2014届)精密和特种加工论文题目:精密和特种加工技术论述专题:水射流技术简述专业:机械设计制造及其自动化班级:机电BG101 姓名:王晶晶学号:6212110125 指导教师:郎庆阳水射流技术简述摘要随着社会的发展,机械制造业也要适应社会的发展。
由于发展的需要,出现了许多难以加工的材料,传统的加工方法已经不能满足加工的要求,因此出现了许多新的加工方法,以满足加工的需要。
本文通过对高压水射流技术的简述及对其基本使用的简要介绍,阐述了这种新型技术的原理及在加工和生活中的用处,说明了新型技术正在改变着人们的生活生产,总结出由科学技术的发展人类的工业技术水平也随之迅猛发展,只有更好地学习和掌握新型科学技术,才能更好地为社会进步做出贡献。
水射流加工就是其中的一种加工方法,数控高压水射流切割机床是水射流加工机床的一种,它是数控技术,电气控制技术,计算机技术等新技术结合的产物。
它包括超高压发生器、控制系统、切割平台等组成。
关键词高压水射流,切割,清洗目录1 绪论 (1)1.1 水射流加工技术的发展历史 (1)2 水射流加工技术的使用 (1)2.1概述 (1)2.2.水射流切割的工艺特点 (2)2.3水射流设备布局方案 (2)3 高压水射流工艺 (3)3.1高压水射流工艺原理 (3)3.2高压水射流切割技术特点 (3)3.3高压水射流清洗技术工艺特点 (4)3.3.1高压水清洗机 (4)3.4高压水射流技术研究现状 (5)3.5高压水射流技术未来的发展趋势 (6)总结.................................................................................. 错误!未定义书签。
致谢.. (7)参考文献 (7)1 绪论1.1 水射流加工技术的发展历史19世纪中叶,在北美洲,人类第一次使用水射流开采非固结矿床。
20世纪50年代初,苏联和中国利用水射流进行采煤(即水力采煤)。
精密加工和特种加工
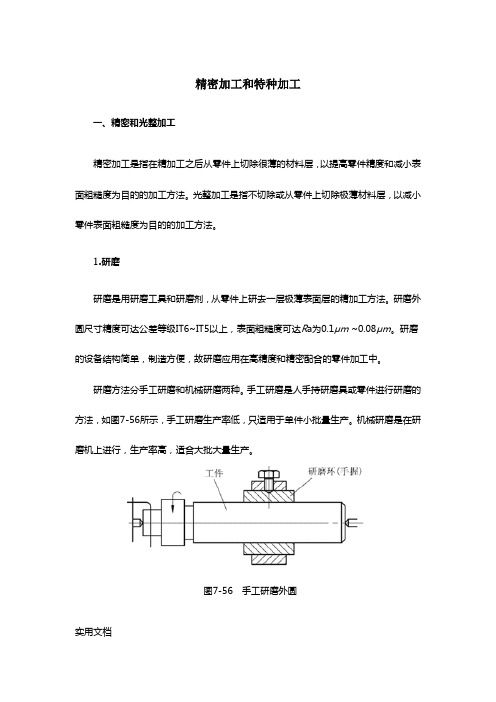
精密加工和特种加工一、精密和光整加工精密加工是指在精加工之后从零件上切除很薄的材料层,以提高零件精度和减小表面粗糙度为目的的加工方法。
光整加工是指不切除或从零件上切除极薄材料层,以减小零件表面粗糙度为目的的加工方法。
1.研磨研磨是用研磨工具和研磨剂,从零件上研去一层极薄表面层的精加工方法。
研磨外圆尺寸精度可达公差等级IT6~IT5以上,表面粗糙度可达R a为0.1μm ~0.08μm。
研磨的设备结构简单,制造方便,故研磨应用在高精度和精密配合的零件加工中。
研磨方法分手工研磨和机械研磨两种。
手工研磨是人手持研磨具或零件进行研磨的方法,如图7-56所示,手工研磨生产率低,只适用于单件小批量生产。
机械研磨是在研磨机上进行,生产率高,适合大批大量生产。
图7-56 手工研磨外圆实用文档研磨具有加工简单、不需要复杂设备,研磨质量高(加工后表面的尺寸误差和形状误差可以小到0.1μm ~0.3μm,表面粗糙度R a值可达0.025μm以下),生产率较低(上道工序为研磨留的余量一般不超过0.01mm~0.03 mm的微量切削)等特点。
研磨应用很广,可研磨加工钢件、铸铁件、铜、铝等有色金属件和高硬度的淬火钢件、硬质合金及半导体元件、陶瓷元件等。
常见的表面如平面、圆柱面、圆锥面、螺纹表面、齿轮齿面等,都可以用研磨进行精整加工。
精密配合偶件如柱塞泵的柱塞与泵体、阀芯与阀套等,往往要经过多个配合件的配研才能达到要求。
2.珩磨珩磨是利用带有磨条(由几条粒度很细的磨条组成)的珩磨头对孔进行精整加工的方法。
如图7-57所示为珩磨加工示意图,珩磨精度可达IT7~IT5以上,表面粗糙度R a 值为0.1μm ~0.008μm。
在大批量生产中,珩磨在专门的珩磨机上进行。
在单件小批生产中,常将立式钻床或卧式车床进行适当改装,来完成珩磨加工。
珩磨具有生产率较高(珩磨余量比研磨大,一般珩磨铸铁时为0.02 mm ~0.15mm,珩磨钢件时为0.005 mm ~0.08mm),精度高,珩磨表面耐磨损,珩磨头结构较复杂等特点。
精密加工和特种加工

薄膜作为成形材料。 69. SLS(选择性激光粉末烧结成形)工艺是利用粉末材料(金属粉末或非金属粉末)在激 光照射下烧结的原理,在计算机控制下逐层堆积成形。 70. SL(液相光敏树脂固化成形)工艺的成形材料称为光固化树脂(或称光敏树脂) 。 71. 磨料硬度愈高,加工速度愈快;磨料粒度愈粗,加工速度愈快,但精度和表面粗糙度则 变差。 72. 超声加工时并不是整个变幅杆和工具都是在作上下高频振动,它和低频或工频振动的概 念完全不一样;超声波在金属棒杆内主要以纵波形式传播。 73. 为了使弹性杆处于最大振幅共振状态,应将弹性杆设计成半波长的整数倍;而固定弹性 杆的支持点,应该选在振动过程中的波节处,这一点不振动。 74. 当频率超过 16000Hz 超出一般人耳听觉范围,就称为超声波。 75. 离子刻蚀是从工件上去除材料,是一个撞击溅射过程。 76. 目前用于改变零件尺寸和表面物理力学性能的离子束加工有:用于从工件上去除加工的 离子刻蚀加工; 用于给工件表面涂覆的离子镀膜加工; 用于表面改性的离子注入加工等。 77. 离子束加工是所有特种加工方法中最精密、 最微细的加工方法, 是当代纳米加工的基础。 78. 离子束加工的原理:粒子束加工的原理和电子束加工基本类似,也是在真空条件下,将 离子源产生的离子束经过加速聚焦,使之撞击到工件表面。不同的是离子带正电荷,其 质量比电子大数千、数万倍,如氩离子的质量是电子的 7.2 万倍,所以一旦离子加速到 较高速度时离子束比电子束具有更大的撞击功能,它是靠微观的机械撞击能量,而不是 靠动能转化为热能来加工的。 79. 电子束加工按其功率密度和能量注入时间的不同,可用于高速打孔、加工型孔及特殊表 面、刻蚀、焊接、热处理、电子束光刻。 80. 电子束加工的基本组成:电子枪、真空系统、控制系统和电源等部分组成。 81. 电子束加工是在真空条件下。 82. 一般激光的实际焦点在工作的表面或略微低于工件表面为宜。 83. 利用激光几乎可在任何材料上打微型小孔。 84. 激光加工机的组成部分:激光器、激光器电源、光学系统、机械系统。 85. 光既有波动性,又有微粒性,即光具有波粒二象性。 86. 电解加工工艺:深孔扩孔加工,型孔加工,型腔加工,套料加工。 87. 电解液的净化方法很多,用得比较广泛的是自然沉淀法;介质过滤法也是常用的方法之 一。 88. 点解加工的基本设备包括直流电源,机床及电解液系统三大部分。 89. 电解液可分为中性盐溶液,酸性溶液与碱性溶液。最常用的有 NaCL、NaNO3、 NaClO3 三种电解液。 90. 电解加工的主要缺点和局限性: (1) 不易达到较高的加工精度和加工稳定性; (2) 电极工具的设计和修正比较麻烦,因而很难适用于单件生产;(3)点解加工的附属设 备较多,占地面积大,机床要有足够的刚性和防腐性能,造价较高;(4)点解产物需 要进行妥善的处理,否则将污染环境。 91. 电解加工与其他加工方法相比较,具有下述特点:(1)加工范围广;(2)点解 加工的生产率较高; (3)可以达到较好的表面粗糙度; (4)不会引起残余应力和变形, 没有飞边毛刺;(5)点解加工过程中阴极工具在理论上不会耗损,可长期使用。 92.电解加工是利用金属在电解液中的电化学阳极溶解,将工件加工成形的。 93.电化学加工的分类:第一类是利用电化学阳极溶解来进行加工;第二类是利用电化学阴
- 1、下载文档前请自行甄别文档内容的完整性,平台不提供额外的编辑、内容补充、找答案等附加服务。
- 2、"仅部分预览"的文档,不可在线预览部分如存在完整性等问题,可反馈申请退款(可完整预览的文档不适用该条件!)。
- 3、如文档侵犯您的权益,请联系客服反馈,我们会尽快为您处理(人工客服工作时间:9:00-18:30)。
1.目前精密和超精密加工的精度范围分别为多少答:精密加工:加工精度为~1μm,加工表面粗糙度为Ra=~μm;超精密加工:加工精度为>μm,加工表面粗糙度为Ra<μm。
超精密切削对刀具有什么要求答:为实现超精密切削,刀具应具有如下性能:极高的硬度、极高的耐磨性和极高的弹性模量,以保证刀具有很长的寿命和尺寸耐用度。
切削刃钝圆半径要极小才能实现超薄切削厚度。
切削刃无缺陷,切削时刃形将复印在加工表面上,能得到超光滑的镜面。
工件材料的抗粘结性好、化学亲和性小、摩擦因数低,能得到极好的加工表面完整性。
3.超精密磨削主要用于加工哪些材料为什么超精密磨削一般多采用金刚石砂轮答:超精密磨削主要用来加工各种高硬度、高脆性金属材料和非金属材料,如陶瓷、玻璃、半导体材料、宝石等。
多采用金刚石砂轮的原因:1)可以加工各种高硬度高脆性的材料。
2)磨削能力强,耐磨性好,耐用度高,易于控制加工尺寸及实现加工自动化。
3)磨削力小,磨削温度低,加工表面质量好,无烧伤、裂纹和组织变化。
4)磨削效率高,由于金刚石有锋利的刃口,耐磨性高,因此有较高的切除率和磨削比。
5)加工成本低,虽然金刚石砂轮比较昂贵,但其寿命长,加工效率高,工时少,综合成本低。
4.固结磨料加工与游离磨料加工相比有什么特点答:固结磨料加工与游离磨料加工相比其特点如下:1)可用来加工各种高硬度、高脆性金属材料和非金属材料,如玻璃、陶瓷、半导体材料、宝石、石材、硬质合金、铜铝等有色金属及合金等。
2)磨削能力强、耐磨性好、耐用度高,易于控制加工尺寸及实现加工自动化。
3)磨削力小,磨削温度低,加工表面质量好,无烧伤、裂纹和组织变化。
4)磨削效率高,有锋利的刃口,耐磨性高,因此有较高切除率和磨削比。
5)加工成本低,加工效率高,工时少,综合成本低。
5.简述精密磨削获得高精度和低粗糙度表面的机理。
答:精密磨削主要是靠砂轮的精细修整,使磨粒具有微刃性和等高性。
磨削后,被加工表面留下大量极微细的磨削痕迹,残留高度极小,加上无火花磨削阶段的作用,获得高精度和低表面粗糙度的表面。
6.超精密加工中为什么需要采用微量进给装置常用的微量进给装置有哪些类型答:采用微量进给装置的原因:1)使机床微位移的分辨力进一步提高。
2)进行机床和加工误差的在线补偿,以提高加工精度。
3)进行某些特殊的非轴对称表面的加工都需要使用微量进给装置。
常用的微量进给装置1)机械传动或液压传动式2)弹性变形式3)热变形式4)流体膜变形式5)磁致伸缩式6)电致伸缩式7.简述对超精密切削刀具刀刃锋锐度和粗糙度的理解,分析其对超精密切削过程影响。
1)超精密切削刀具刀刃锋锐度当其他条件不变时,机床加工所能达到的几何精度是由有效切削厚度精确性来决定的,即切削刃从工件表面上有效的切除工件材料的未变形厚度。
由于名义切削厚度是由机床上横向进给切削刃给定的,所以有效切削厚度不总是等于名义切削厚度。
在非常小的切削厚度下,有效切削厚度的精度可看作是最小切削厚度,该处的临界点发生在切屑形状从“稳定到不稳定”状态,这个最小切削厚度被看作是决定能够达到切削精度的可能极限。
金刚石刀具刀刃锋锐度与超精密切削时能达到的极限最小切削厚度有密切关系。
由图1可以看出存在极限点A,在A点以上被加工材料将堆积起来形成切屑,而在A点以下,加工材料经弹塑变形形成加工表面。
由实验计算得出,图1中正常切削时的最小切削厚度h Dim=1nm,所用的金刚石刀具刃口半径为3~4nm,这是极为锋利的金刚石刀具。
因此,切削刃的锋锐度是影响切削深度的主要因素。
切削刃越锋利,亦即切削刃半径越小,切削深度也就越小,表面粗糙度值就越小。
实际加工中心,金刚石刀具的前角取为-25°,切削速度v=3000r/min,切削深度αp=5μm,此时的加工表面粗糙度和平面度最好。
金刚石刀具的刃口半径影响最小切削深度,即最小切削厚度。
刀刃刃口半径ρ越小,刀刃锋锐度越好,天然金刚石刀具的刃口半径可达μm。
超精密加工就是使最小切削厚度尽可能的小,对工件表面进行极微量的切除。
另一方面,刀具切削刃钝圆半径越大,刀具强度越大;刀具切削刃钝圆半径越小,刀具越锋利。
因此,合适地选择金刚石刀具切削刃钝圆半径可以使加工时的切削力更小,刀具寿命更长。
图1极限最小切削厚度h Dim和刃口半径ρ的关系2)超精密切削刀具刀刃粗糙度被加工表面轮廓是由刀具轮廓转换到垂直切削方向平面上而形成的。
由于切削刃和工件材料间的界面复杂,难以辨别,因此这种轮廓转换过程取决于分界面的亲和性。
实验表明,金刚石对各种材料的亲和性均较小,因而能够较好的把切削刃的轮廓转化到工件的表面上。
但是,由于微量修整或粘附颗粒的影响,金刚石切削刃上即使有很小的凹凸不平都会引起被加工表面上的损伤。
金刚石的转换精度估测小于10nm。
目前,金刚石表面的粗糙度可以被研磨到1nm的数量级。
因此,金刚石刀具切削刃前面和排屑面交叉处的粗糙度就可以达到10nm以下。
这样,我们就可以认为,金刚石刀具能够对某些金属精加工到10nm以下的粗糙度,超过其切削刃的有效长度。
超精密切削刀具刀刃锋锐度和粗糙度对切削过程的影响由于刀刃锋锐度和粗糙度对切削过程的影响是相反的过程,因此只需分析其中之一即可。
下面分析刀刃锋锐度对切削过程的影响在普通切削加工中,由于切削厚度远大于刀具切削刃的钝圆半径,因此可以不考虑刀具切削刃钝圆半径对切削过程的影响。
而超精密切削不同于普通切削,其切削层极薄,刀具切削刃的钝圆半径将明显影响切削变形、已加工表面粗糙度和表面波纹度等,对切削过程有着很大的影响。
刀刃锋锐度对加工表面粗糙度的影响金刚石刀具刃口锋锐度对加工表面粗糙度有一定影响。
例如,用ρ=μm的金刚石刀具在机床条件较好时切铝合金,仅在进给量和切深较小的情况下(a p=1~2μm,f≤μm/r)可切出R max<μm;而更锋锐的刀具(ρ=μm)可在较宽的切削条件下切出R max<μm的表面。
故在进行超精密加工时,使用刃口半径小的锋锐刀具可有效提高加工表面的质量,减小表面粗糙度值。
在超精密切削过程中,刀刃的磨损使得刃口半径ρ值逐渐增大,加工表面粗糙度也逐渐增大。
图2为刀具磨损对加工表面粗糙度影响的切削实验结果。
从图中可以看出,新刀时(刀刃锋利)加工表面粗糙度R max=μm;但当切削路程超过300km 时,加工表面粗糙度已超过μm。
超精密切削时,金刚石刀具磨损不能继续使用的标志是加工表面质量超差,如果新刀磨得锋利,则刀具的耐用度亦会相应提高,可切削较长时间。
图2刀刃磨损对加工表面粗糙度的影响刀刃锋锐度对切削变形的影响在进行超精密切削时,由于切削深度和进给量都很小,直接测量切削变形很困难。
一般是通过测量主切削力来间接说明刀具刀刃锋锐度对切削变形的影响。
刀刃锋锐度对切削力的影响如图3所示。
从图3中我们可以看到,由于刀刃的锋锐度不同,切削力有明显的差别。
在a p 较小时,差别更明显。
在切削深度很小时,单位切削力急剧增大,这是因为在切削深度和进给量都很小的情况下,刃口半径不同将明显影响切削变形。
刃口半径的微小变化将使切削变形产生很大的变化,因此在超精密切削时要特别注意这一点。
图3刀刃锋锐度对切削力的影响(v=314m/min,f=5μm/r)刀刃锋锐度对加工表面冷作硬化的影响使用锋锐度不同的金刚石刀具对金属进行切削时,其对表面冷作硬化会产生明显不同的影响。
实验结果表明:加工表面变质层的冷硬和显微硬度会因刀具锋锐度的不同而又明显的差别;在金刚石刀具较锋锐的情况下(ρ=μm),超精密切削表面仍有较大的冷硬存在。
若要求加工表面的变质层很小,那相应的金刚石刀具应该研磨的更加锋锐。
刀刃锋锐度对加工表面层位错的影响加工表面层组织的位错密度是取决于加工时的切削变形和后刀面的摩擦,是加工表面的质量和工作性能的重要标志。
由于金刚石和有色金属之间的摩擦系数较小(一般为),后刀面的摩擦不大,因此影响加工表面层的位错密度的主要因素是切削变形。
切削变形大时,表面层的位错密度大;切削变形小时,位错密度也小。
刀刃锋锐度对加工表面层残余应力的影响超精密加工的加工表面层的残余应力不仅影响材料的疲劳强度和耐磨性,而且还影响加工零件的前期尺寸的稳定性,是表面质量的重要标志。
采用ρ=μm和μm 的金刚石车削LY12铝合金,实验结果如下表所示:表1不同锋锐度刀具切铝合金的加工表面残余应力切削条件表面残留应力(MPa)切削速度v (m/min)进给量f(μm/r)切削深度ɑp(μm)刀具刃口半径ρ=μm刀具刃口半径ρ=μm3145103145631452314513145(1)用ρ=μm的金刚石加工时,其加工表面的残余应力要比用ρ=μm的刀具切削时低得多。
(2)切削深度的减小可以使残余应力减小。
但当切削深度减小到某临界值时,若再继续减小切削深度,则会使加工表面残余应力增大。
4)总结金刚石刀具是超精密切削的理想刀具,在其它加工条件具备时,金刚石刀具的切削刃锋利度对超精密加工过程有很大影响,正确地选择切削刃钝圆半径是获得高质量加工表面的有力保证。
参考文献[1]王国栋,张宇,关强. 超精密加工中刀具参数对脆性材料非球面加工质量的影响[J]. 中国制造业信息化,2010,15:66-69.[2]孙俊兰,姜大志. 精密切削中影响零件加工表面完整性的因素分析[J]. 盐城工学院学报(自然科学版),2002,04:21-23.[3]郭谆钦,王承文. 超精密加工中刀具形状对加工质量的影响[J]. 机械,2001,06:52-53+56.[4]王西彬. 金刚石刀具高速精密切削加工的研究[J]. 工具技术,2002,02:15-18.[5]许平海. 超精密金属切削的金刚石刀具技术[J]. 工具技术,1993,12:31-34.[6]袁哲俊,周明,王娜君,韩荣久,马文生. 金刚石刀具刀刃锋锐度对切削变形和加工表面质量的影响[J]. 机床,1992,11:21-25.[7]张文生,张飞虎. 金刚石刀具刀尖几何形状对超精密切削加工质量的影响[J]. 工具技术,2005,08:38-39.[8]张文生,张飞虎,李立军,于信伟,董申. 超精密切削时刀具切削刃的作用机理分析[J]. 中国机械工程,2004,15:4-6.[9]胡凤兰,朱理,董丽君. 选择合适的刀具与切削参数,提高精密加工件的表面质量[J]. 轻工机械,2006,03:75-77.。