连续退火炉分压比计算公式 气体含水量和露点
天然气脱水
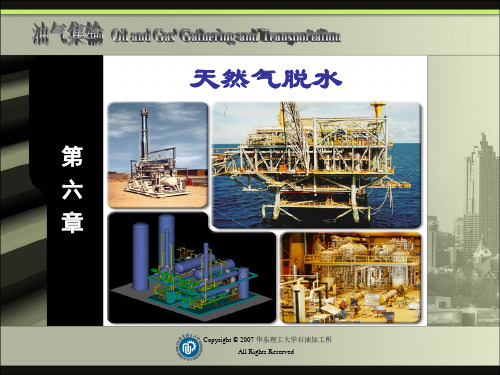
天
然
气
脱
水
Copyright © 2007 华东理工大学石油加工所 All Rights Reserved
• 除TEG脱水装置外,四川还有与轻烃回收或氦气
六
分离装置配套的分子筛脱水装置、硅胶一分子筛
天
复合床天然气脱水装置在运行,干气含水量均在
然
5mg/rn3以下。这些固体吸附法通常在需深度脱
气 脱
气
脱
水
Copyright © 2007 华东理工大学石油加工所 All Rights Reserved
• 其中三甘醇(TEG)法是应用最广泛的方法,美国
的甘醇脱水装置中有85%使用TEG,美国各气田
六
正在运行的天然气三甘醇脱水装置达40,000多套.
天 • 分子筛常用于需要深度脱水的场合;
然 • 而CaCl2水溶液法则在边远、严寒地区使用。
须大于1,越大越易分离。
Copyright © 2007 华东理工大学石油加工所 All Rights Reserved
2. 吸附速率
• 吸附过程:
六
天 • 吸附组分由流体主体 → 固体颗粒外表面 → 固体
然
颗粒内表面 → 吸附
气 脱
• 吸附组分A外扩散速率:
水
dqA
d
ky p (YA
YAi )
然
衡,此时达到吸附速率和脱附速率相等的动态平
气
脱
衡。
水 • 平衡吸附量是吸附量的极限,其数值常用吸附等
温线表示。
Copyright © 2007 华东理工大学石油加工所 All Rights Reserved
• 单组分气体在固体表面的吸附
• Langmuir方程:固体表面均匀的单分子层吸附。 • BET方程:多分子层吸附。
退火炉露点温度控制及其对冷轧带钢质量的影响

退火炉露点温度控制及其对冷轧带钢质量的影响摘要:本文首先介绍了影响退火炉露点温度的主要因素及其控制方法,。
接着,探讨了露点温度控制对冷轧带钢质量的影响,包括晶粒尺寸、晶界清晰度、残余应力、变形度、化学成分和相变行为等方面。
进一步进行了实验设计和结果分析,最后,提出了退火炉露点温度控制的优化策略,以期提高退火炉的生产效率和材料质量,对冷轧连续退火行业具有重要的指导意义。
关键词:退火炉;露点温度控制;影响前言退火炉是一种常用的热处理设备,广泛应用于金属材料的加工和制造过程中。
在退火过程中,控制退火炉的露点温度是非常重要的,它直接影响着材料的质量和性能。
露点温度是指在一定的压力条件下,空气中的水蒸气开始凝结成液态水的温度。
在冷轧连续退火过程中,如果露点温度过高,会导致带钢表面产生氧化,进而影响材料的表面质量和性能[1]。
因此,准确控制退火炉的露点温度对于保证材料的质量和性能至关重要。
一、退火炉露点温度控制的方法(一)传统控制方法:传统的退火炉露点温度控制方法主要包括PID控制和模糊控制。
PID控制是通过调节加热功率和风速来控制炉内温度,从而间接控制露点温度。
模糊控制则是根据经验规则和模糊推理来调节加热功率和风速,以实现露点温度的控制。
(二)先进控制方法:先进的退火炉露点温度控制方法主要包括模型预测控制(MPC)和自适应控制。
MPC是通过建立数学模型来预测系统的动态响应,并根据预测结果进行控制。
自适应控制则是根据实时的系统状态和参数变化来调节控制器的参数,以实现露点温度的精确控制。
(三)露点温度传感器的选择和应用:选择合适的露点温度传感器对于退火炉露点温度的控制至关重要。
常用的露点温度传感器包括湿度传感器和红外线传感器。
湿度传感器通过测量气体中的湿度来间接计算露点温度,而红外线传感器则是通过测量气体中的水蒸气浓度来直接计算露点温度。
根据具体的应用需求和精度要求,选择合适的传感器进行应用。
二、退火炉露点温度控制对材料质量的影响2.1冷轧带钢性能与露点温度的关系首先,露点温度的控制可以影响材料的表面质量。
论连续退火炉节能减排降耗的控制措施
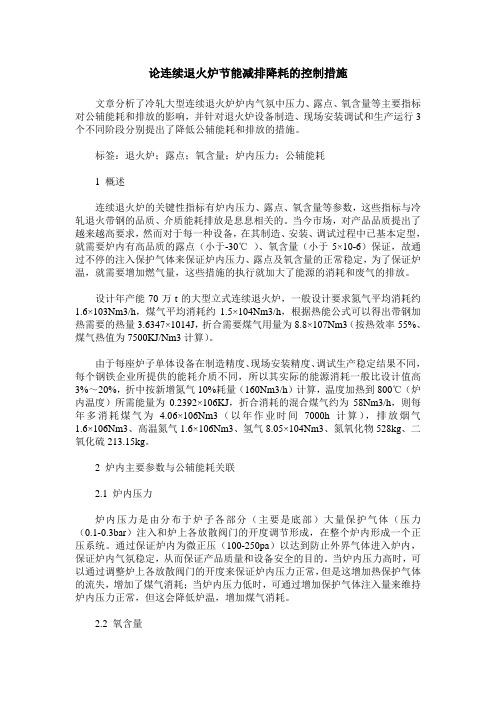
论连续退火炉节能减排降耗的控制措施文章分析了冷轧大型连续退火炉炉内气氛中压力、露点、氧含量等主要指标对公辅能耗和排放的影响,并针对退火炉设备制造、现场安装调试和生产运行3个不同阶段分别提出了降低公辅能耗和排放的措施。
标签:退火炉;露点;氧含量;炉内压力;公辅能耗1 概述连续退火炉的关键性指标有炉内压力、露点、氧含量等参数,这些指标与冷轧退火带钢的品质、介质能耗排放是息息相关的。
当今市场,对产品品质提出了越来越高要求,然而对于每一种设备,在其制造、安装、调试过程中已基本定型,就需要炉内有高品质的露点(小于-30℃)、氧含量(小于5×10-6)保证,故通过不停的注入保护气体来保证炉内压力、露点及氧含量的正常稳定,为了保证炉温,就需要增加燃气量,这些措施的执行就加大了能源的消耗和废气的排放。
设计年产能70万t的大型立式连续退火炉,一般设计要求氮气平均消耗约1.6×103Nm3/h,煤气平均消耗约1.5×104Nm3/h,根据热能公式可以得出带钢加热需要的热量3.6347×1014J,折合需要煤气用量为8.8×107Nm3(按热效率55%、煤气热值为7500KJ/Nm3计算)。
由于每座炉子单体设备在制造精度、现场安装精度、调试生产稳定结果不同,每个钢铁企业所提供的能耗介质不同,所以其实际的能源消耗一般比设计值高3%~20%,折中按新增氮气10%耗量(160Nm3/h)计算,温度加热到800℃(炉内温度)所需能量为0.2392×106KJ,折合消耗的混合煤气约为58Nm3/h,则每年多消耗煤气为 4.06×106Nm3(以年作业时间7000h计算),排放烟气1.6×106Nm3、高温氮气1.6×106Nm3、氢气8.05×104Nm3、氮氧化物528kg、二氧化硫213.15kg。
2 炉内主要参数与公辅能耗关联2.1 炉内压力炉内压力是由分布于炉子各部分(主要是底部)大量保护气体(压力(0.1-0.3bar)注入和炉上各放散阀门的开度调节形成,在整个炉内形成一个正压系统。
固定污染源烟气排放连续监测系统输出参数计算方法
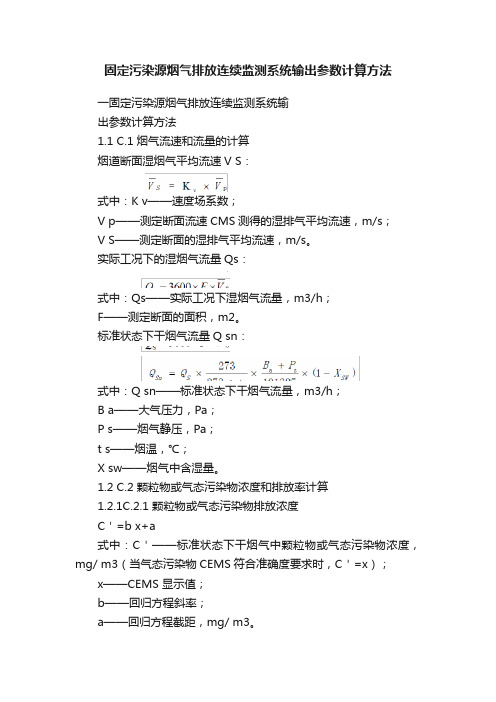
固定污染源烟气排放连续监测系统输出参数计算方法一固定污染源烟气排放连续监测系统输出参数计算方法1.1 C.1 烟气流速和流量的计算烟道断面湿烟气平均流速V S:式中:K v——速度场系数;V p——测定断面流速CMS测得的湿排气平均流速,m/s;V S——测定断面的湿排气平均流速,m/s。
实际工况下的湿烟气流量Qs:式中:Qs——实际工况下湿烟气流量,m3/h;F——测定断面的面积,m2。
标准状态下干烟气流量Q sn:式中:Q sn——标准状态下干烟气流量,m3/h;B a——大气压力,Pa;P s——烟气静压,Pa;t s——烟温,℃;X sw——烟气中含湿量。
1.2 C.2 颗粒物或气态污染物浓度和排放率计算1.2.1C.2.1 颗粒物或气态污染物排放浓度C'=b x+a式中:C'——标准状态下干烟气中颗粒物或气态污染物浓度,mg/ m3(当气态污染物CEMS符合准确度要求时,C'=x);x——CEMS 显示值;b——回归方程斜率;a——回归方程截距,mg/ m3。
当气态污染物显示浓度单位为μmol/mol 时,SO2、NO 和NO2 换算为标准状态下mg/ m3的换算系数:SO2:1μmol/mol=64/22.4 mg/ m3NO:1μmol/mol=30/22.4 mg/ m3NO2:1μmol/mol=46/22.4 mg/ m31.2.2C.2.2 污染物干基浓度和湿基浓度转换式中:C d——污染物干基浓度,mg/m3(μmol/mol);C w——污染物湿基浓度,mg/m3(μmol/mol);X SW——烟气绝对湿度(又称水分含量)。
上式中干基浓度与湿基浓度的工况状态条件应相同;含氧量干/湿基浓度转换计算方法与上式相同。
1.2.3C.2.3没有安装转化炉同时测量烟气中的NO和NO2的CEMS系统氮氧化物(NO X)质量浓度以NO2计,其质量浓度按公式(C6)或(C7)计算:………………………………(C6)式中:C NOX——氮氧化物质量浓度,mg/m3;C NO——一氧化氮质量浓度,mg/m3;C NO2——二氧化氮质量浓度,mg/m3;M NO2——二氧化氮摩尔质量,g/mol;M NO——一氧化氮摩尔质量,g/mol。
冷轧连续退火炉工艺论文资料
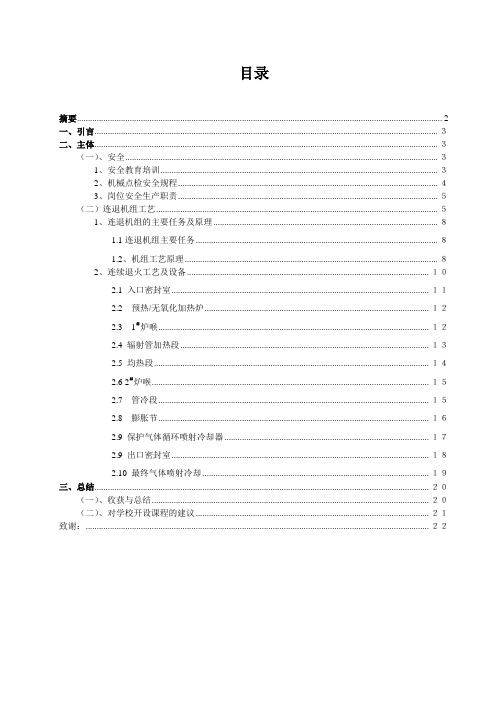
目录摘要 (2)一、引言............................................................................................................................................................ 3二、主体............................................................................................................................................................ 3(一)、安全.............................................................................................................................................. 31、安全教育培训.............................................................................................................................. 32、机械点检安全规程...................................................................................................................... 43、岗位安全生产职责...................................................................................................................... 5(二)连退机组工艺................................................................................................................................ 51、连退机组的主要任务及原理 ...................................................................................................... 81.1连退机组主要任务.............................................................................................................. 81.2、机组工艺原理................................................................................................................... 82、连续退火工艺及设备.............................................................................................................. 102.1 入口密封室..................................................................................................................... 112.2 预热/无氧化加热炉...................................................................................................... 122.3 1#炉喉........................................................................................................................... 122.4 辐射管加热段................................................................................................................. 132.5 均热段............................................................................................................................. 142.6 2#炉喉.............................................................................................................................. 152.7 管冷段........................................................................................................................... 152.8 膨胀节........................................................................................................................... 162.9 保护气体循环喷射冷却器 ............................................................................................. 172.9 出口密封室..................................................................................................................... 182.10 最终气体喷射冷却....................................................................................................... 19三、总结........................................................................................................................................................ 20(一)、收获与总结.............................................................................................................................. 20(二)、对学校开设课程的建议.......................................................................................................... 21致谢:............................................................................................................................................................ 22摘要:硅钢被誉为钢铁行业的“工艺品”,广泛的应用于各种电机和变压器的中心部件,其制造工艺复杂,装备总类多,设备自动化程度较高,生产过程困难,对各项指标的要求较高。
干燥过程的物料平衡与热平衡计算

干燥过程的物料与热平衡计算1、湿物料的含水率湿物料的含水率通常用两种方法表示。
(1)湿基含水率:水分质量占湿物料质量的百分数,用ω表示。
100%⨯=湿物料的总质量水分质量ω(2)干基含水率:由于干燥过程中,绝干物料的质量不变,故常取绝干物料为基准定义水分含量。
把水分质量与绝干物料的质量之比定义为干基含水率,用χ表示。
100%⨯=量湿物料中绝干物料的质水分质量χ(3)两种含水率的换算关系: χχω+=1 ωωχ-=1 2、湿物料的比热与焓(1)湿物料的比热m C湿物料的比热可用加和法写成如下形式:w s m C C C χ+=式中:m C —湿物料的比热,()C kg J ⋅绝干物料/k ; s C —绝干物料的比热,()C kg J ⋅绝干物料/k ; w C —物料中所含水分的比热,取值4.186()C kg J ⋅水/k (2)湿物料的焓I '湿物料的焓I '包括单位质量绝干物料的焓和物料中所含水分的焓。
(都是以0C 为基准)。
()θθχθχθm s w s C C C C I =+=+='186.4式中:θ为湿物料的温度,C 。
3、空气的焓I空气中的焓值是指空气中含有的总热量。
通常以干空气中的单位质量为基准称作比焓,工程中简称为焓。
它是指1kg 干空气的焓和它相对应的水蒸汽的焓的总和。
空气的焓值计算公式为:()χ1.88t 24901.01t I ++= 或()χχ2490t 1.881.01I ++=式中;I —空气(含湿)的焓,绝干空气kg/kg ;χ—空气的干基含湿量,绝干空气kg/kg ;1.01—干空气的平均定压比热,K ⋅kJ/kg ; 1.88—水蒸汽的定压比热,K ⋅kJ/kg ; 2490—0C 水的汽化潜热,kJ/kg 。
由上式可以看出,()t 1.881.01χ+是随温度变化的热量即显热。
而χ2490则是0C 时kg χ水的汽化潜热。
它是随含湿量而变化的,与温度无关,即“潜热”。
烟气露点计算及烟囱冷凝水量计算方法及结果

7 烟气露点计算及烟囱冷凝水量计算方法及结果7.1 烟气中水蒸汽露点温度的计算当已知烟气中的含湿量dg(g/kg 干烟气)时,可按下式计算烟气中的水蒸汽露点温度(水露点)t DP :1) 当dg=3.8g/kg ~160g/kg 时:t DP.O =]})/804(lg[21433.0{491.7]})/804(lg[21433.0{908.236dgP d dgP d g d gg g d g g +⋅+-+⋅+••ρρ, ℃;(7.1-1) 2) 当dg=61g/kg ~825g/kg 时t ’DP ·O =]})/804(lg[20974.0{4962.7]})/804(lg[20974.0{1.238dgP d dgP d g d gg g d gg +⋅+-+⋅+••ρρ , ℃;(7.1-2) 式中:Pg ——烟气的绝对压力, kPa ;dg ——烟气含湿量 g/kg 干烟气;ρg ——干烟气密度 kg/Nm 3。
7.2 烟气酸露点温度的计算a. 按燃煤成分为基准的计算方法燃煤锅炉的烟气酸露点按下述公式计算:t Dp =t Dp.o +n sp S05.1.)(31β ℃(7.2-1) 式中:t Dp.o ——烟气中纯水露点温度,按7.1确定。
S SP 。
——燃料折算硫分,%·g/kcal ,按可燃硫S c.ar 计算:S sP =S c.ar ×arnet Q .4182(7.2-1a) n ——指数,表征飞灰含量对酸露点影响的程度;n=αfly ·A sP 。
αfly ——飞灰份额,对煤粉炉αfly =0.8~0.9;A sP ——燃料折算灰分A sP =A ar ×ar net Q .4182 (7.2-1b) β——与炉膛出口过剩空气系数F α有关的参数,F α=1.2时β=121;F α=1.4~1.5时,β=129。
一般工程计算中可取β=125。
连续退火炉炉内露点温度高故障分析与控制
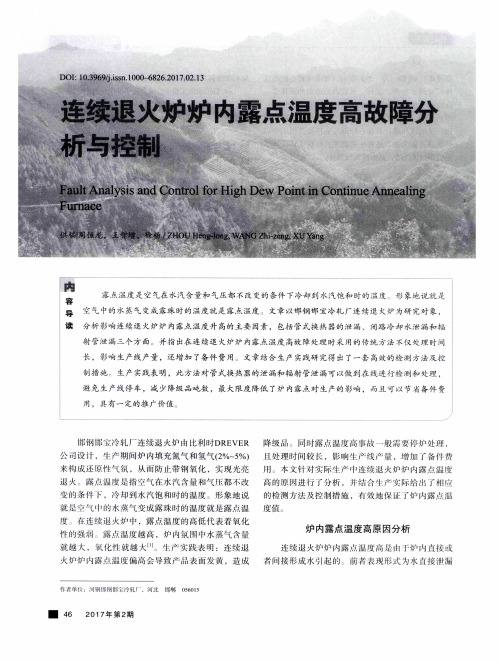
1 " 4 1 路 冷却水 主要 是川 来 对与炉 内直 接接 触 没备
期处 温状 态 l 损 坏 闭路 冷却水 泄漏 主要 足 南
寻找泄漏 点 ,这 样会导致 謦个 敞 处理时 『 H J 偏长 温度高事故 r l 1 .仅 寻找该泄漏点就牦费l 天时间
薹 l _ 、 = _ -
射 管泄 漏三 个方面 并指 出在连 续退 火炉炉内露点温度 高故 障处理 时采 用的传 统方法不仅 处理 时 间
长 ,影响 生产线产量 ,还增加 了备件 费用。文章 结合生产 实践研 究得 出了一套 高效的检测 方法及 控 制措施 生产 实践表 明,此 方法对管 式换 热器的泄漏和辐射 管泄漏 可以做 到在 线进行检测 和处理 ,
到炉1 人 】 ,包括 管式换 热 泄 漏和 闭路冷 却水泄 漏 ;
去,进 l f l j …观局部 岛温 ;= 址 燃 比参数设 小 碳变脆现 象 ,产生裂纹 一2 0 1 5  ̄ 1 i 3 月 ,加热段 l 2 … 现辐射管泄漏 导致炉内露点 温度商、 、
I ; 现渗 现为 气 巾的氧 ( J _ I j 炉『 大 】 的氢 气在高温 环境 合适 ,不 能满 足富氧燃烧 条件 ,导致辐 射管 } 卜 进 行化学反心 牛成 水,上 表现为辐射管_ 『 I I f 漏、
度 在连续 退火炉 中 ,露点 温度 的高低 代表着 氧化 性 的强弱 露点 温度越 高 ,炉 内氛 同巾水蒸 气 含量
就越 大 ,氧化 性 就越大 【 I I :生 产实践 表 明 :连 续退
炉 内露点 温度 高原 因分析
连续 退火 炉炉 内露 点温 度高 是 } { 1 丁' t J ’ , 1 人 】 白 : 接 或
公 司设计 ,牛产期 间炉 内填 充氮气 和 氢气 ( 2 %~ 5 %) 且处理 时 间较长 ,影响生 产线 产量 ,增 加 丁 备件 费
热镀锌专业技能培训

十三、连续退火工艺的目的
▪ 退火的目的: ▪ (1)完成带钢的再结晶退火过程,消除冷轧过
程中的加工硬化现象,降低屈服强度,提高延伸 率,易于塑性变形。恢复其工艺塑性以便进一步 进行冷加工,同时作为最终产品热处理,要控制 成品性能,得到不同的强度和塑性的组合,生产 出不同软硬状态的产品。
▪ (2)将带钢冷却到入锌锅温度,使带钢具有清 洁的无氧化物的活性表面,并使带钢密封地进入 锌锅进行镀锌。
八、本机组清洗段的喷淋压力控制
▪ 为了保证清洗质量,本机组刷辊都采用逆 向带钢方向运动进行刷洗,此时喷淋的方 向与角度,必须与刷辊旋转一致的方向, 角度必须保证喷水的角度处于刷辊与带钢 相切处略偏向刷辊的位置,根据经验,此 角度约在30°-40°之间,喷淋压力控制在 0.2-0.5Mpa之间。清洗效果最好。
▪ 快冷段由2套单独的快冷循环风机、2套气水换热器,2组保气循环冷 却风箱组成。风机将炉内热的保护气体抽出,经过气水换热器冷却后 鼓入风箱,冷却后的保护气体从风箱喷出后均匀地喷射在带钢表面。 使退火后的带钢温度降到470°C左右,快冷风机采用2台变频调速风 机,控制保护气体循环量,对带钢进行强制冷却。快冷段总长约 6.5m。快冷段布置少量电阻带。
▪ 带钢带负电脱脂时,表面析出的是氢气, 分子体积小、气泡小、数量多、面积大, 所以除油和乳化作用较强。但会因造成带 钢渗氢,带来氢脆缺陷。
六、影响预脱脂和电解脱脂清洗效果 的因素(一)
▪ (1)脱脂液中碱浓度对清洗效果的影响 ▪ 预脱脂段的化学脱脂液,碱浓度应控制在1%~3%之间,不宜过高。
提高碱浓度可提高化学脱脂的速度,但是过高的浓度会使脂肪酸钠的 溶解度和乳浊液的稳定性下降,反而降低了除油的效果,而且增加成 本和环保的难度。 ▪ 电解液中电解脱脂剂浓度增加,电导率随之升高,电解电流增大。 如果电解液中电解脱脂剂浓度低于一定范围,电解电流不能满足工艺 要求。生产中,不仅要满足清洗效果,又要考虑成本、环保,电解脱 脂剂浓度控制在2%~5%比较合适。 ▪ (2)脱脂液温度对清洗效果的影响 ▪ 预脱脂段的化学脱脂液,温度控制在60℃±5℃。在碱浓度一定时, 提高化学脱脂液的温度,可加速动植物油的皂化反应速度,形成的脂 肪酸钠在热碱中溶解,同时还能降低油膜的粘度,从而降低油和带钢 的表面张力,促进乳化作用。 ▪
水-气-声计算公式汇总
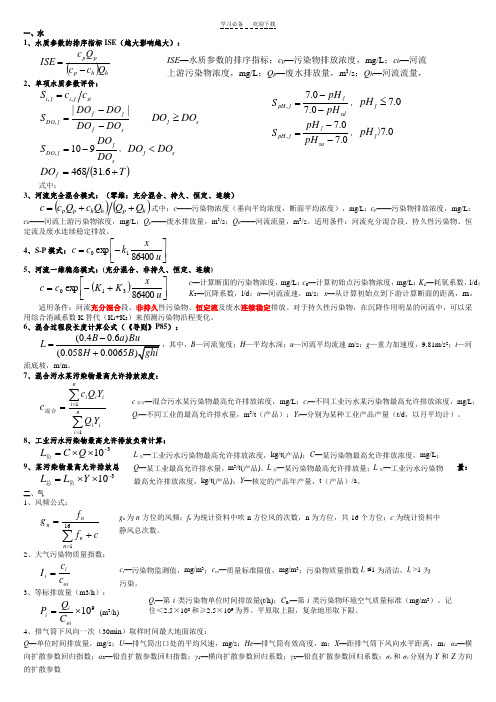
学习必备 欢迎下载一、水1、水质参数的排序指标ISE (越大影响越大):()hh ppp Q c cQ c ISE -=2、单项水质参数评价:si j i j i c c S ,,=sf j f j DO DO DO DO DO S --=||,s j DO DO ≥sjj DO DO DO S 910,-=,s j DO DO <()T DO f +=6.31468sd j j pH pH pH S --=0.70.7,,0.7≤j pH 0.70.7,--=su j j pH pH pH S ,0.7〉j pH式中:3、河流完全混合模式:(零维:充分混合、持久、恒定、连续)()()h p h h p p Q Q Q c Q c c ++=式中:c ——污染物浓度(垂向平均浓度,断面平均浓度),mg/L ;c p——污染物排放浓度,mg/L ;c h ——河流上游污染物浓度,mg/L ;Q p ——废水排放量,m 3/s ;Q h ——河流流量,m 3/s 。
适用条件:河流充分混合段、持久性污染物、恒定流及废水连续稳定排放。
4、S-P 模式:⎥⎦⎤⎢⎣⎡-=u x k c c 86400exp10 5、河流一维稳态模式:(充分混合、非持久、恒定、连续)()⎥⎦⎤⎢⎣⎡+-=u x K K c c 86400exp 310适用条件:河流充分混合段、非持久性污染物、恒定流及废水连续稳定排放。
对于持久性污染物,在沉降作用明显的河流中,可以采用综合消减系数K 替代(K 1+K 3)来预测污染物沿程变化。
6、混合过程段长度计算公式(《导则》P85):(0.40.6)(0.0580.0065)B a Bu L H B ghi-=+,其中,B —河流宽度;H —平均水深;u —河流平均流速m/s ;g —重力加速度,9.81m/s 2;i —河流底坡,m/m 。
7、混合污水某污染物最高允许排放浓度:∑∑===ni ii ni ii i YQ YQ c c 11混合8、工业污水污染物最高允许排放负荷计算:310-⨯⨯=Q C L 负9、某污染物最高允许排放总量:310-⨯⨯=Y L L 负总二、气1、风频公式:∑=+=161n n nn cf f g2、大气污染物质量指数:oii i c c I =3、等标排放量(m3/h ):910⨯=oii i C QP (m 3/h)4、排气筒下风向一次(30min )取样时间最大地面浓度:Q —单位时间排放量,mg/s ;U —排气筒出口处的平均风速,mg/s ;He —排气筒有效高度,m ;X —距排气筒下风向水平距离,m ;α1—横向扩散参数回归指数;α2—铅直扩散参数回归指数;γ1—横向扩散参数回归系数;γ2—铅直扩散参数回归系数;σy 和σz 分别为Y 和Z 方向的扩散参数c —计算断面的污染物浓度,mg/L ;c 0—计算初始点污染物浓度,mg/L ;K 1—耗氧系数,l/d ;K 3—沉降系数,l/d ;u —河流流速,m/s ;x —从计算初始点到下游计算断面的距离,m 。
gdd数据计算

3.2干吸工序工艺计算干燥塔处理的气体量:Q*22.4*1000Vd=98*b*y由 Q=2450000/(24*340)=b=9.00%y=99.9%*99.65%=300.25*22.4*1000得 Vd=98*0.09*0.9955035气体含水量:B=18/22.4*Vd*Pw/(P-Pi-Pw)(kg/t 100%H2SO4) P——大气压力(Pa)Vd——处理的干燥气体量(m3/h)所以B=18/22.4*(7.73/(95-7.73))*765971.4=进入吸收塔成为H2SO4的SO3量=300.25*99.9%*99.65%*1000/98=3.3 干燥塔及其循环槽的物料衡算3.3.1干燥塔的物料衡算(1)干燥塔入口炉气成分1 净化工序补加空气量:3.1设计计算条件式中:Pw——在一定温度下饱和水蒸汽压(Pa);Pi——干燥塔入口的操作压力(Pa)式中:Q——H2SO4的产量(100%H2SO4计) b——气体中SO2的浓度 (%) y——硫的利用率 (%)干燥塔入口补加空气量=872625.69-765971.42=2 干燥塔入口炉气含水量:设补加空气全部在电除雾之后加入,空气由湿气图查得含水量 6.7则补加空气带水量=106654.2489*0.0067=干燥塔入口炉气总含水量=54519.46+714.58=(2) 干燥塔出口气体带水量干燥后指标:水分≤0.1则干燥后气体含水量=0.1/1000*872625.67=(3)循环酸量由于塔径还未确定,故按酸浓度差计算。
入塔酸:浓度:93.00%温度:50℃干燥塔的吸水量=55234.05-87.263=由物料平衡得:x*1.7993*1000*93%=(x*1.7993*1000+55146.78)*92.7%解得:x=9470.54762(4)干燥系统各塔串酸量1.吸收塔循环酸与干燥塔循环酸对串酸量。
设:93%硫酸~98%硫酸为 x(kg/h);98%硫酸~93%硫酸串酸量为y1(kg/h)由H2O平衡得:55146.78+19.59%*y1=24.08%*x由SO3平衡得:80.41%y1=75.92%xx= 1.06将(3-3)式代入(3-1)55146.78+19.59%y1=0.24081.055y1得:y1=x=2 吸收塔循环酸与104.5%H2SO4塔循环酸对串酸量104.5%吸收SO3量=3036.24*30% =104.5%硫酸产量=300.25*1000*30%/104.5%=其中: 水量=86194.765(1-0.853)=设: 105%酸——98%酸串酸量为z(kg/h)98%酸——105%酸串酸量为y2(kg/h)由H2O平衡得:0.19592y2=0.1469z+12670.63由SO3平衡得:0.8041y2+73199=0.8531z+73199y2= 1.06将(3-6)代入(3-4)式得:0.1959*1.06z=0.1469z+12670.63解得: z=207927.63y2= 1.06*207927.63=3.3.2干燥塔循环酸槽的物料衡算干燥塔循环酸槽的物料衡算见表3-33.4 干燥塔及其循环槽的热量衡算3.4.1干燥塔的热量衡算1. 炉气带入热量 Q1(t=40℃)SO2带入热量:q1=3049.95*40*41.57=O2带入热量: q2=3242.98*40*29.37=N2带入热量:q3=32314.02*40*28.45=H2O蒸汽带入热量:q4=3068.56*40*32.716=式中: 41.57,29.37,28.45,32.716分别为0~40℃时SO2,O2,N2,H2Q1=q1+q2+q3+q4=49670308.082. 水的冷凝热Q2水在40℃时冷凝热为24.6(KJ/kg)Q2=(55234.05-87.263) 24.6=1356610.8923. 入塔酸带入热量Q350℃ 93% H2SO4的热焓I1=78.7(KJ/kg)Q3=9470.55*1.7993*1000*78.7=134********. 93%酸稀释热Q4式中:Q——稀释热(J/mol H2SO4)n——对于1mol硫酸所用水的摩尔数对于浓度为C1的硫酸,当稀释到浓度为C2时,放出热量按下式计算:式中:Q2-Q1——每摩尔H2SO4放出的热量(J)n2 n1——浓度分别为C2 C1时每摩尔H2SO4所含水的摩尔数93.00% H2SO4→92.70% H2SO4Q2-Q1=14403-13900=503(KJ/kmol)Q4=503*9470.55*1.7993*1000/98=87462237.15. 炉气带出热量Q5(t=45℃)SO2带出热量:q1=3049.95*45*41.64=O2带出热量:q2=3242.98*45*29.295=N2带出热量:q3=32314.02*45*28.5=H2O蒸汽带出热量:q4=3068.56*45*32.74=式中:41.64,29.395,28.51,32.74分别为0~45℃时SO2,O2,N2,Q5=q1+q2+q3+q4=55953779.456. 出塔酸带出热量Q6和酸温(KJ/kmol)(KJ/kmol )1868.47983.117860⨯+⨯=n n Q 1868.4]7983.1178607983.117860[112212⨯+⨯-+⨯=-n n n n Q Q 41.098/9318/71==n 139001868.47983.141.01786041.01=⨯+⨯=Q 429.098/7.9218/3.72==n 144031868.47983.1429.017860429.02=⨯+⨯=QQ6=Q1+Q2+Q3+Q4-Q5=1423611420则出塔酸的热焓:I2=查表知:92.7% H2SO4 I2=83.274(KJ/kg)时的温度t= ℃3.4.2干燥塔循环槽的热量衡算1) 从干燥塔冷却器来的92.7% H2SO4带入热量Q1=17095474.92*I2) 从98%酸循环系统串来98.5% H2SO4带入热量Q2=1227939.97*79.34=97424757.563) 混合热由98.5% H2SO4,92.7% H2SO4两种浓度的H2SO4,混合成93% H2SO4。
连续退火炉炉内气氛分析与控制

( 1 ) 预热段入 口密封棍密封不严或密封氮气效果不佳 ; ( 2 ) 3 J I 热炉 辐射管烧穿 , 导致加热段氧气含量高 图4 为辐射管烧穿( 裂) 实例 。 ( 3 )
…
…
上接 第6 9 页
2 . 5完善技 术管 理
实施严格的工艺技术管理 , 保障每个采矿小组至少配备一名专 利用系数。 其次 , 尽量让工艺车停靠位置贴近挖掘机装矿岩 附近 , 让 对工艺进行控制 。 以提升挖掘效率 以生产力为 目 挖掘机回转角度小于9 0 度, 这样 可以避 免因挖掘机 回转而支 出不必 业采矿技术人员 , 对挖掘顺序进行合理分配 。 要 的时间 , 为生产 能力赢得 时间。 最后, 不要让挖掘机与工艺车处于 标 , 同一水 平面可以让工 艺车停泊在挖掘机下步台阶 , 减少挖掘机提斗 3结语 时间和 回转时 间 , 这 也是提升挖掘机生产 能力 的有效措施之一 。 本文主要对影响单斗挖掘机生 产能力的因素进行 分析 并结 合 2 . 2避 免 不 必 要 的 挖 掘 机 移 动 编制月度生产计划过程中要将 生产连续. 陛问题考 虑其 中, 解决 因采场分散 而加大运距 的难题 , 减少挖掘机不必要的移动可以从作 业时间上赢得更大 的生 产力 及挖掘效率 。 2 , 3重视 挖 掘 设备 养护 工 作 提 出因素给予提高单斗挖掘机生产能力的对 应策略 , 其中影响露天 矿单斗挖掘机 生产能力的最大 因素莫过于挖 掘机 的工 作时间与时 间利用系数 , 我国矿部之所 以对挖掘机生 产效率严 抓 , 其 目的就在 于宣传及明确有效时 间利用和小 时产能对挖 掘机 生产能力影响的 重要性 。 随着 我 国矿 产 业 的 发展 , 对 单 斗 挖 掘 机 的 利 用 将 会 继 续 下
退火工艺技术解析
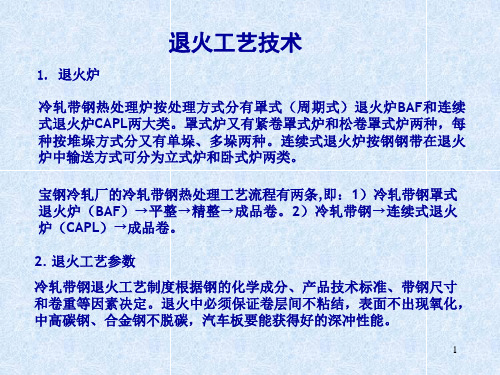
4. 某厂罩式炉车间简介
罩式退火所用原料及产品 年产量:600,000 t/a 原料/产品: 钢种为低碳软钢、高强度低合金钢。 钢等级为:CQ, DQ, DDQ, HSLA 原料规格 钢带厚度: 0.3-2.0 mm 钢带宽度: 900-1665 mm 钢卷外径: φ1100mm -- φ2000mm 钢卷内径: φ610 mm 最大钢卷重量: 33.3t 最大堆垛高度: 5500mm
2. 退火工艺参数
冷轧带钢退火工艺制度根据钢的化学成分、产品技术标准、带钢尺寸 和卷重等因素决定。退火中必须保证卷层间不粘结,表面不出现氧化, 中高碳钢、合金钢不脱碳,汽车板要能获得好的深冲性能。
1
(1)加热速度
钢的导热系数越大,加热速度可以越快。含碳量或合金含量高时,钢 的导热系数小, 故加热速度应适当慢些。从室温到 400 ℃,加热速度一般不加限制, 因为在此期间,带钢内部组织无显著变化,尚未发生再结晶,在这个 温度区间加热速度快慢对性能和表面质量影响不大。实际生产中,加 热罩(外罩)都是由上一炉保温结束,立即转移到另一炉上,由于罩 体温度很高,钢卷温度很快从室温升到 400 ℃,此期间温度变化是难 以控制的。 从 400℃到保温温度,加热速度对带钢的性能和表面质量影响很大。 对于氮氢型保护气体罩式炉,一般规定为 30~50℃/h;对特殊钢、易 出质量问题的钢种和较厚的带钢,加热速度应有不同的规定,如厚度 较大(大于 1.2mm)的 09MnAl(Re)、Q235F等钢种,易出性能问 题,不易出现粘结,加热速度应慢些,使钢卷温度比较均匀。
3
硅钢在高温成品退火中,高斯织构是通过二次再结晶来形成的。对于碳 素钢,晶粒粗大会降低强度、塑性、冲击韧性及冷弯工艺性能,因此不 希望发生二次再结晶。 (3)冷却速度和出炉温度
冷轧带钢退火原理及连退炉内露点测量与控制综述

冷轧带钢退火原理及连退炉内露点测量与控制综述作者:王冬冬来源:《科学与信息化》2018年第32期摘要结合首钢京唐公司冷轧连退炉机组实例,分析了带钢退火原理,同时对连退炉露点进行论述,并积极总结经验,对连退炉内露点的测量与控制提出方法和措施。
经过一段时间的试运行,取得了一定的效果,有效控制了连退炉内露点的分布量,提高了带钢表面质量和退火后的机械性能。
关键词冷轧;带钢;连退炉;露点前言连续退火是连续地将带钢加热到一定温度保温后再冷却的工艺。
退火目的是使热轧带钢软化、消除内应力、恢复塑性、改善带钢的金相组织[1]。
带钢经冷轧变形后,金属晶粒将沿着变形的方向被拉长。
冷变形会引起晶粒取向的转动,从而在多晶体内形成一定类型的织构[2]。
其内部组织产生大量位错,形成胞状结构,产生加工硬化,使带钢的强度和硬度大大提高,而塑性、韧性、冲压性能降低,给进一步的冷加工带来困难。
金属内部组织发生晶粒拉长,晶粒破碎和晶体缺陷而导致金属内部自由能升高,处于不稳定状态,为了消除这种不稳定状态及所产生的缺陷,使其塑性、韧性提高,强度、硬度下降,所以需要对冷轧产品进行退火处理。
1 冷轧板退火原理形变金属的退火又称再结晶退火,是冷轧薄板生产过程中的关键工艺环节,直接影响带钢最终的产品质量。
再结晶退火就是将冷变形后的金属加热到再结晶温度以上、Ac1以下,保持适当时间,使其具有较高的原子活动能力,其晶粒的外形便开始发生变化,从破碎拉长的晶粒重新结晶为均匀等轴晶粒后进行冷却从而消除加工硬化的热处理工艺[3]。
再结晶退火主要经历回复、再结晶和晶粒长大三个过程[1]。
2 首钢京唐公司冷轧连退炉设备概况首钢京唐公司冷轧2230退火机组是主要生产机组,年处理量为000t,产品以高质量表面的汽车板、家电板为主,生产的品种包括: CQ、DQ、DDQ、EDDQ、SEDDQ、CQ-HSS、DQ-HSS、DDQ-HSS、BH-HSS、DP-HSS、TRIP-HSS等[4]。
连续退火炉炉内气氛分析与控制

连续退火炉炉内气氛分析与控制作者:贺有赵赛胡树森马凯来源:《中国科技纵横》2015年第11期【摘要】介绍了连续退火炉炉内气氛的组成及监测,说明了炉内气氛主要组成成分,阐述了氢气含量配比控制和炉内正常生产控制以及有害成份控制,分析了有害成分含量升高的主要常见原因,并提供了具体问题的解决措施,在实际生产中,特别适用于特种钢材的生产操作炉内气氛要求,使得退火炉炉内氛围得到有效控制,保证了带钢退火生产工艺稳定,满足各类带钢退火要求,提高产品质量。
【关键词】退火炉炉内气氛氢气含量控制1 前言邯钢西区冷轧厂连续退火炉由比利时DREVER公司设计的立式退火炉,按照带钢走向和热处理功能分为预热段、加热段、均热段、缓冷段、快冷段、过时效段和终冷段。
炉内氛围为氮气和氢气按照一定比例混合构成的还原性气氛,保证带钢在炉内不被氧化,去除带钢表面残留的氧化物,达到保证带钢表面质量的条件要求下进行退火。
2 炉内气氛含量的测量邯钢西区冷轧厂连续退火炉炉内气氛检测仪按区段布置共有3台CAA(炉内氛围分析柜),每台分析内都包含3种分析仪,分别检测氢气含量、氧气含量和露点。
氢气含量使用ABB AO2040氢气分析仪,采用热导原理进行分析,氧气含量分析使用Delta F 150氧气分析仪,采用电化学原理进行分析,露点分析仪采用Vaisla DMT 142露点分析仪。
CAA01检测预热段2个区、加热段3个区、均热段炉内气氛;CAA02检测缓冷段2个区、快冷段3个区、过时效段2个区炉内气氛;CAA03检测过时效段2个区、终冷5个区炉内气氛。
各段特征气氛含量的测量是利用分析仪巡回扫描的方式进行的,一个周期大约45分钟,通过对炉内各段气体含量的监测,控制炉内还原气氛状况。
3 炉内气氛控制连续退火炉炉内气氛是由氮气和氢气组成的还原性保护气体,为了防止外界空气进入炉内,连续退火炉正常生产时采用微正压操作。
为了保证一定的炉压需要持续注入一定比例的保护气体和还原性气体氢气。
连续退火炉基础知识
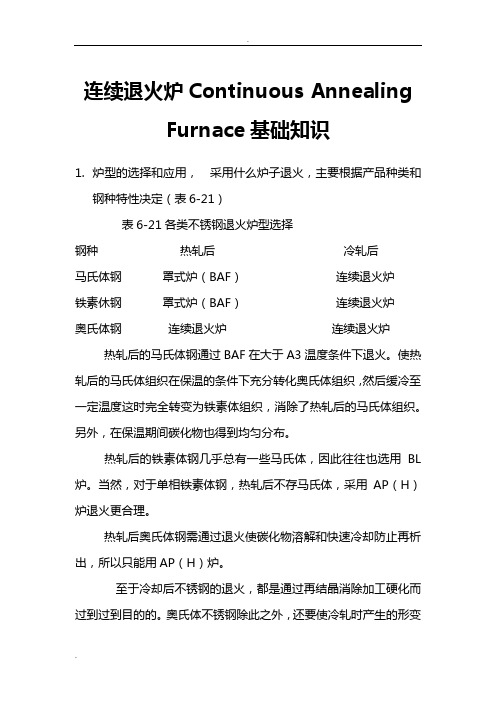
连续退火炉Continuous AnnealingFurnace基础知识1.炉型的选择和应用,采用什么炉子退火,主要根据产品种类和钢种特性决定(表6-21)表6-21各类不锈钢退火炉型选择钢种热轧后冷轧后马氏体钢罩式炉(BAF)连续退火炉铁素休钢罩式炉(BAF)连续退火炉奥氏体钢连续退火炉连续退火炉热轧后的马氏体钢通过BAF在大于A3温度条件下退火。
使热轧后的马氏体组织在保温的条件下充分转化奥氏体组织,然后缓冷至一定温度这时完全转变为铁素体组织,消除了热轧后的马氏体组织。
另外,在保温期间碳化物也得到均匀分布。
热轧后的铁素体钢几乎总有一些马氏体,因此往往也选用BL 炉。
当然,对于单相铁素体钢,热轧后不存马氏体,采用AP(H)炉退火更合理。
热轧后奥氏体钢需通过退火使碳化物溶解和快速冷却防止再析出,所以只能用AP(H)炉。
至于冷却后不锈钢的退火,都是通过再结晶消除加工硬化而过到过到目的的。
奥氏体不锈钢除此之外,还要使冷轧时产生的形变马氏体转变为奥氏体,因此都用AP(C)BA 这样的连续炉退火。
如果用BL 炉,则存在以下问题:1. 不管在什么条件下退火,由于退火时间长表面都会氧化,生成不均匀的铁鳞,存在显著的退火痕迹2. 退火温度较高时,容易粘结和发生层间擦伤等表面缺陷。
⑵退火条件①退火条件的确定按下面的程序框图确定退火条件。
应注意的事项:用记的加工制造方法变化或对材质的要求变动时,应修订退火条件。
初期阶段没有充分把握,应按用户对退火产品的质量评价判定退火条件是否合适。
再结晶特性调查用碳矽棒热处理作实验(画出硬度曲线、晶粒度曲线、确认金相组织)退火温度设定设定退火温度上、下限值及退火时间出炉口目标材料温度的设定设定材温仪表指示值的目标值(上、下限温度)各段炉温和机组速度设定根据理论计算进行初步设定机组实际运行试验确认燃烧状况(烧咀负荷等)和通板状况(机组速度、除鳞性前后操作状况)判定性能是否合格根据检查标准判定退火条件确定前部工序,如炼钢、热轧、甚至冷轧的条件发生变化,需要修改冷轧后的退火条件。
露点仪标定数据变化对测量值的影响

露点仪标定数据变化对测量值的影响俞鸿毅;石燕【摘要】为了保证露点仪测量的准确性,要定期进行标定.在使用过程中,发现露点仪测量值存在明显的单边下降异常,而同期工艺情况并没有发生明显的异常.通过对比发生异常的探头前后两次的标定数据,发现标定数据间的变化与单边下降的异常有显著的相关性.由此,得出了为了保证测量准确性,除了定期标定外,还要关注前后两次标定数据变化范围的结论.【期刊名称】《宝钢技术》【年(卷),期】2016(000)003【总页数】4页(P59-62)【关键词】露点仪;露点温度;标定【作者】俞鸿毅;石燕【作者单位】宝山钢铁股份有限公司,上海201900;宝钢工程技术集团有限公司,上海201900【正文语种】中文【中图分类】TB943露点仪是检测各类气体中水分含量的仪器,广泛应用于电力、石化、天然气、钢铁、微电子等众多行业。
冷轧连续退火炉炉内的露点情况也是主要的工艺控制点之一。
准确地反映炉内气氛真实的露点,对产品的质量,如氧化、锌层附着性能等,有着十分重要的意义。
目前冷轧厂使用最多的是电容式露点仪,这类仪器的共同特点是稳定性差,需要定期标定和校准来保持其测量精度[1]。
露点温度(dew temperature,以下简称露点)是指空气在水气含量和气压都不改变的条件下,冷却到饱和时的温度,就是空气中的水蒸气变为露珠时的温度。
空气中的含水量与气体的露点直接相关:含水量越低,露点越低;反之,含水量越高,露点越高。
露点仪是一种测量气体露点的仪器,按照检测原理分类,通常可以分为冷镜式露点仪和电容式露点仪。
冷镜式露点仪是直接测量,电容式是间接测量。
1.1 冷镜式露点仪让采样气体流经露点冷镜室的冷凝镜,对冷凝镜进行冷却(常用的冷却方法有半导体制冷、液氮制冷和高压空气制冷),当镜面温度达到采样气体的露点时,会发生结露现象。
采用光电检测技术,检测出结露层并测量结露时镜面温度,从而获知采样气体的露点。
冷镜式露点仪采用的是直接测量方法,在保证检测准确、镜面制冷高效率和结露温度测量精密前提下,该种露点仪可作为标准露点仪使用。