石灰石煅烧试验报告
氧化钙实验报告

一、实验目的1. 熟悉氧化钙的制备方法;2. 掌握氧化钙的性质及实验操作技巧;3. 分析实验数据,探讨氧化钙在实际应用中的潜在价值。
二、实验原理氧化钙(CaO),又称生石灰,是一种重要的无机化合物。
在工业生产中,氧化钙广泛应用于建筑材料、冶金、化工等领域。
本实验采用高温煅烧石灰石(CaCO3)的方法制备氧化钙。
CaCO3(石灰石)在高温下分解生成CaO(氧化钙)和CO2(二氧化碳),反应方程式如下:CaCO3(石灰石)→ CaO(氧化钙)+ CO2(二氧化碳)三、实验仪器与药品1. 仪器:高温炉、坩埚、烧杯、玻璃棒、电子天平、干燥器、温度计等;2. 药品:石灰石(CaCO3)、稀盐酸、蒸馏水等。
四、实验步骤1. 称取适量的石灰石(CaCO3),精确至0.01g;2. 将石灰石放入坩埚中,置于高温炉中;3. 调节高温炉温度至850℃,保温2小时;4. 关闭高温炉,待炉温降至室温后取出坩埚;5. 将氧化钙样品放入烧杯中,加入适量的蒸馏水,搅拌溶解;6. 观察溶液颜色变化,记录实验现象;7. 取少量溶液,加入稀盐酸,观察反应现象;8. 将氧化钙溶液过滤,收集滤液;9. 将滤液放入干燥器中,干燥至恒重;10. 称量干燥后的氧化钙样品,计算产率。
五、实验数据与结果1. 氧化钙的制备:实验过程中,高温炉温度保持在850℃左右,保温2小时后,石灰石(CaCO3)完全分解,生成氧化钙(CaO)和二氧化碳(CO2);2. 氧化钙溶液颜色变化:将氧化钙样品溶解于蒸馏水中,溶液呈无色;3. 氧化钙与稀盐酸反应:加入稀盐酸后,溶液产生气泡,反应方程式如下:CaO + 2HCl → CaCl2 + H2O4. 氧化钙产率:实验中制备的氧化钙产率为85.2%。
六、实验讨论与分析1. 高温煅烧石灰石是制备氧化钙的常用方法,实验过程中要注意控制高温炉温度,以确保石灰石完全分解;2. 氧化钙溶液无色,加入稀盐酸后产生气泡,说明氧化钙与稀盐酸反应生成氯化钙和水;3. 实验中氧化钙的产率为85.2%,说明该制备方法具有较高的经济效益。
木醋调质石灰石煅烧特性试验研究

有机 钙 ( 醋酸钙 、 酸钙 等 ) 醋 酸/ 酸 调质 法 经济 丙 , 丙 代价 高 的问题仍 然存 在 。
化 工产 品如木 醋 、 酒精 、 制糖 及制 药行业 生产 过
程 中排放 的废液 中含有 一 定 浓 度 的有 机 酸 , 能将 若
这些 廉价 废液 替 代醋 酸/ 酸溶 液 调 质 天然 石 灰石 丙 制备 有机 钙吸 收剂 , 既 能 有效 利用 废 液 中的 有机 则 酸成 分 , 能解 决有 机 钙协 同脱 硫脱 硝 技 术 实 际应 又
公 司所 生 产 的 T A S T 8 1 G / D A 5 e型 热 重 分 析 仪 上 进
行 。试 验 中称 取 1 0±0 1 g样 品 , 别 按 5、0 . m 分 2、
( )石灰石 a
4 / i 0K r n的升 温速 率在 3 3~1 2 a 0 3 3 K范 围 内进行 煅
f e o rp a tsmu t n o sy Ho v r t e hg c n i d p we l n i l e u l. we e ,h i h e o omi c s s wi s r u l f c t r c ia p l a i n r a c o t l e i sy a f ti p a t l p i t . l o e s c a c o
高温煅烧石灰石

高温煅烧石灰石
石灰石的主要成分为碳酸钙,其化学式为:CaCO3、煅烧石灰石
本质上相当于是煅烧碳酸钙,而碳酸钙是不溶于水的碳酸盐,受热容易分解为对应的金属氧化物和二氧化碳气体。
扩展资料:
高温煅烧石灰石的实验:
我们可以在实验室中进行高温煅烧石灰石的实验,大致步骤如下:点燃酒精灯,打开沉浮式贮气瓶的活塞导管,把细长的铁导管由下向上插进酒精灯的焰心位置,铁导管与酒精灯火焰成45°角,火
焰在氧气流的吹动下,形成向上倾斜45°角的高温焰锋。
用坩埚钳夹持石灰石薄片(或贝壳)在高温焰锋上灼烧1min,
而后把石灰石薄片(或贝壳)投入滴加了酚酞的水里,搅拌后可以看到水呈现红色。
高钙石灰煅烧试验
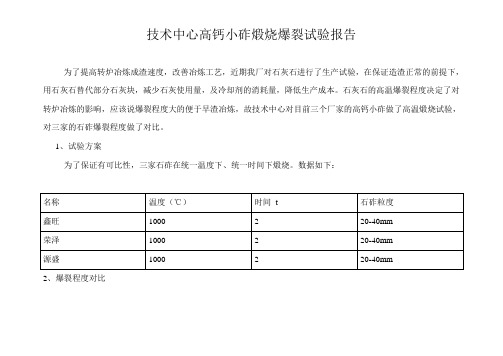
技术中心高钙小砟煅烧爆裂试验报告
为了提高转炉冶炼成渣速度,改善冶炼工艺,近期我厂对石灰石进行了生产试验,在保证造渣正常的前提下,用石灰石替代部分石灰块,减少石灰使用量,及冷却剂的消耗量,降低生产成本。
石灰石的高温爆裂程度决定了对转炉冶炼的影响,应该说爆裂程度大的便于早渣冶炼,故技术中心对目前三个厂家的高钙小砟做了高温煅烧试验,对三家的石砟爆裂程度做了对比。
1、试验方案
为了保证有可比性,三家石砟在统一温度下、统一时间下煅烧。
数据如下:
2、爆裂程度对比
3、对比分析
从以上煅烧情况看,鑫旺的爆裂程度比其他两家明显,但鑫旺的石砟密度高,统一时间下,有部分生烧。
其他两家源盛的比荣泽爆裂程度稍明显,但从对比图看荣泽的表面粉面明显比其他多。
以上数据分析有限,如需要可多次试验。
技术中心
2013-3-13。
高温煅烧石灰石实验结果记录表格

标题:高温煅烧石灰石实验结果详解在古代,人们发现高温煅烧石灰石可以得到一种新的物质,用于建筑、涂料等方面。
石灰石在高温下的变化引起了人们的好奇,也促使科学家进行了大量的实验来探索其奥秘。
在本文中,我们将深入研究高温煅烧石灰石的实验结果,并结合个人观点进行全面探讨。
实验一:温度对石灰石的影响1. 温度为800°C时石灰石经过800°C的高温煅烧后,发生了明显的变化。
其外观由灰白色变为浅黄色,质地变得更加坚硬。
在加热的过程中,石灰石释放出二氧化碳,产生了氧化钙。
这表明,800°C的高温已经使石灰石发生了部分煅烧,产生了新的化学物质。
2. 温度为1000°C时当温度升至1000°C时,石灰石的变化更加显著。
它的颜色更加深黄,质地变得更加坚硬,表面呈现出一些晶体结构。
此时,石灰石已经完全煅烧,变成了氧化钙。
实验二:煅烧时间的影响1. 煅烧时间为30分钟在800°C的温度下,煅烧30分钟后,石灰石的变化并不明显。
仍然保持着浅黄色,质地也没有太大的改变。
这表明,短时间的煅烧并不能使石灰石完全发生化学变化。
2. 煅烧时间为60分钟将石灰石煅烧60分钟后,其颜色变得更加深黄,质地更加坚硬。
虽然未达到完全煅烧的程度,但已经有了一定的变化。
结论与回顾:从以上实验结果可以得知,在高温下煅烧石灰石,石灰石会产生明显的变化,并最终转化为氧化钙。
温度和煅烧时间对石灰石的变化也有一定的影响。
在实际应用中,可以根据需要选择适当的温度和时间进行煅烧,以得到符合要求的氧化钙。
个人观点:高温煅烧石灰石是一个古老而神奇的实验,通过控制温度和时间,可以使石灰石转化为有用的化学物质。
这不仅在建筑、涂料等方面有着广泛的应用,也展示了人类对自然物质的探索和利用。
希望未来可以有更多的实验来深入研究石灰石高温煅烧的过程,以及其在环境保护和新材料研发方面的应用。
通过本文的全面讨论,相信你已经对高温煅烧石灰石有了更深入的了解。
石灰原材料实验报告

一、实验目的1. 了解石灰原材料的物理、化学性质;2. 掌握石灰原材料的制备方法;3. 分析石灰原材料的性能及其在建筑材料中的应用。
二、实验原理石灰是一种重要的建筑材料,其主要成分是氧化钙(CaO)。
石灰原材料的制备方法主要有生石灰和熟石灰两种。
生石灰是石灰石(CaCO3)经过高温煅烧得到的,熟石灰是生石灰与水反应得到的。
本实验主要研究石灰原材料的制备及其性能。
三、实验材料与仪器1. 实验材料:石灰石、水、砂子;2. 实验仪器:高温炉、烧杯、搅拌器、电子秤、温度计、硬度计、抗折试验机、抗压试验机。
四、实验步骤1. 生石灰制备:将石灰石放入高温炉中,在800-1000℃的温度下煅烧,得到生石灰;2. 熟石灰制备:将生石灰与水按一定比例混合,搅拌均匀,静置24小时,得到熟石灰;3. 物理性质测试:测量生石灰和熟石灰的密度、吸水率、细度等;4. 化学性质测试:测量生石灰和熟石灰的CaO含量、C/S比等;5. 性能测试:测量生石灰和熟石灰的抗压强度、抗折强度等;6. 应用实验:将熟石灰与砂子按一定比例混合,制作石灰砂浆,进行抗折强度和抗压强度测试。
五、实验结果与分析1. 生石灰制备:经过高温煅烧,石灰石得到生石灰,其CaO含量约为70%;2. 熟石灰制备:生石灰与水反应,生成熟石灰,其C/S比约为1.0;3. 物理性质:生石灰的密度约为3.2g/cm³,吸水率约为1.0%;熟石灰的密度约为2.4g/cm³,吸水率约为8.0%;4. 化学性质:生石灰的CaO含量约为70%,C/S比约为1.0;熟石灰的CaO含量约为30%,C/S比约为1.0;5. 性能:生石灰的抗压强度约为40MPa,抗折强度约为4MPa;熟石灰的抗压强度约为10MPa,抗折强度约为1MPa;6. 应用实验:石灰砂浆的抗压强度约为5MPa,抗折强度约为1MPa。
六、实验结论1. 生石灰和熟石灰是石灰原材料的两种主要形式,具有不同的物理、化学性质;2. 生石灰具有较高的CaO含量和C/S比,适合用于建筑材料中;3. 熟石灰具有较高的吸水率和较低的抗压强度,适合用于石灰砂浆等建筑材料中;4. 石灰原材料的性能与其制备工艺和组成有关,合理选用石灰原材料可以提高建筑材料的性能。
小粒度石灰石煅烧活性石灰研究

小粒度石灰石煅烧活性石灰研究石灰回转窑煅烧工艺对石灰石入窑粒度有着严格的要求,一般石灰石粒度比不宜大于3。
酒钢西沟矿供我公司石灰石粒度为10~65mm,石灰石粒度比大,如直接入窑煅烧,在煅炼过程中容易造成物料偏析,破坏物料塌落式运动轨迹;碎料被包裹在中间或和压在料层低端,影响分解速度,石灰石分解率下降,成品率降低[1];煅烧出的石灰中粉灰多,0~10mm 的粉灰占比20%~25%,石灰CaO 含量下降,不仅影响炼钢灰质量,还造成原料浪费。
为此,我们进行了小粒度石灰石煅烧试验,并在此基础上提出了三级筛分、分级煅烧的工艺方案。
一、煅烧试验试验采用西沟矿10~65mm 石灰石筛下10~20mm小粒度石灰石,其化学成分:CaO含量53%,MgO含量1.1%,SiO2含量1.3%。
(一)试验方法试验在马弗炉内进行,通过温度控制,在马弗炉内放入一定量的10~20mm 石灰石。
一般温度取1000℃、1050℃、1100℃、1150℃,煅烧时间取80min、120min、160min。
(二)试验结果及分析也随之由低到高;当温度达到1050℃并持续升高时,石灰活性度又呈下降趋势。
因此,最佳的煅烧温度在1000~1150 ℃之间,煅烧时间控制在2~2.3h,在此煅烧条件下生产出的石灰质量好、生烧率低、活性度能达到290ml 以上,完全能够满足烧结厂和炼钢厂使用要求。
试验结果表明,回转窑煅烧小粒度石灰石,进而实行石灰石分级煅烧的工艺方案是可行的。
二、原料预处理系统设备及预热器改造方案(一)原料预处理系统设备改造目前我公司上料系统配套有3台滚筒筛,滚筒筛无法实现分级筛分,故需要将滚筒筛分系统改为分级振动筛分系统。
在筛分设备的选型上,建议选择具备三级筛分效果的分级筛,将10mm以下粉料筛下入石灰石粉地仓,供烧结制粉用,10~20mm的入原料专用地仓,20~65mm 石灰石入原料专用地仓。
同时,配套安装相应的辅助设备及单机除尘、收尘管道等环保设施。
石灰石煅烧试验报告

安钢冶金炉料公司石灰石煅烧试验报告一、目的任务对冶金炉料公司不同供户的石灰石进行试验研究,掌握其样品特性、煅烧性能,并根据这些特性进行分类,为石灰石供户优化选择提供依据。
二、试验设备及仪器箱式电阻炉,天平,化验分析仪器等。
三、取样制样与化验取样:到采石场现场取样,样品块度大于200mm,在每个采石场沿工作面按等距离跨度取10块样品。
制样:在白灰厂化验室制样,用锤子将取来的石灰石样品,制成约80mm、700g左右的球形煅烧样品。
同时,将剩余石灰石,用破碎机破碎后,制成青石化验样。
化验:青石样品送地质队化验室化验,化验项目分为CaO、MgO和SiO2三项,化验结果直接采用。
煅烧后的石灰,在白灰厂化验室化验活性度。
四、煅烧试验取6块同一供户的石灰石样品,在托盘天平上称重,记录重量,当箱式电阻炉升温至550℃时,将样品入炉,保持一定的升温速率(升温约30分钟到1050℃),当升温至1050℃时箱式电阻炉自动恒温,在此温度下煅烧60分钟,断电降温60分钟(炉内温度降至600℃以下),将煅烧后的石灰取出,在室内冷却至室温后称重,并送化验室化验石灰活性度。
五、试验数据煅烧试验数据表表1六、数据计算根据表1中的煅烧试验数据,计算烧失率、石灰石分解率、生烧率、白灰CaO含量、MgO含量、SiO2含量。
计算结果见表2。
计算结果表表2七、数据分析根据采样地点和有关资料推断,我公司目前焦炭石灰竖炉所采用的石灰石,产出地层分别是中奥陶统马家沟组第五岩性段和第七岩性段。
第五岩性段,其岩性特征为灰色、深灰色中厚层状、隐晶花斑石灰岩,是水泥用石灰岩的主要产出地层,由下而上划分五个亚层,因该岩性段石灰石杂质含量高(尤其是SiO2),一般不用作优质冶金石灰的原料。
第七岩性段,位于中奥陶统石灰岩地层最上部,为深灰色或灰色纯质石灰原料,局部夹浅黄褐色薄层状白云质灰岩,厚度大,质量佳,层位稳定,根据层位、岩性和化学成分的不同,由下而上划分七个亚层。
石灰石试验总结报告 (8月26日)
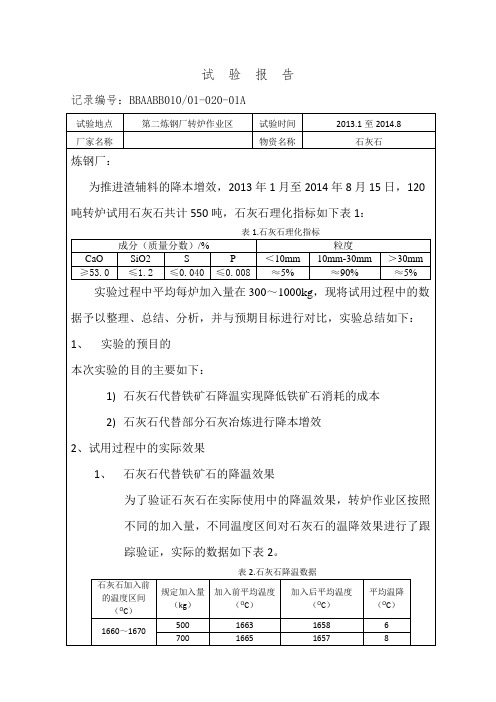
试验报告记录编号:BBAABB010/01-020-01A试验地点第二炼钢厂转炉作业区试验时间2013.1至2014.8厂家名称物资名称石灰石炼钢厂:为推进渣辅料的降本增效,2013年1月至2014年8月15日,120吨转炉试用石灰石共计550吨,石灰石理化指标如下表1:表1.石灰石理化指标成分(质量分数)/% 粒度CaO SiO2 S P <10mm 10mm-30mm >30mm ≥53.0≤1.2≤0.040≤0.008≈5% ≈90% ≈5%实验过程中平均每炉加入量在300~1000kg,现将试用过程中的数据予以整理、总结、分析,并与预期目标进行对比,实验总结如下:1、实验的预目的本次实验的目的主要如下:1)石灰石代替铁矿石降温实现降低铁矿石消耗的成本2)石灰石代替部分石灰冶炼进行降本增效2、试用过程中的实际效果1、石灰石代替铁矿石的降温效果为了验证石灰石在实际使用中的降温效果,转炉作业区按照不同的加入量,不同温度区间对石灰石的温降效果进行了跟踪验证,实际的数据如下表2。
表2.石灰石降温数据石灰石加入前的温度区间(O C)规定加入量(kg)加入前平均温度(O C)加入后平均温度(O C)平均温降(O C)1660~1670 500 1663 1658 6 700 1665 1657 81000 1668 1657 111670~1680 500 1673 1669 4 700 1676 1670 6 1000 1679 1671 8由表2的数据可以看出,加入石灰石前温度区间在1660~1670 ℃时,石灰石的温降效率达到了1.14 ℃/100kg,达到了预期效果;石灰石在冶炼过程中作为冷却剂加入时,570kg石灰石相当于300kg矿石的冷却效果,可降低钢水温度约5℃。
其中:570Kg石灰的价格为:0.57吨×90元/吨=51.3元300kg球团矿的价格为:0.3吨×970元/吨=291元在使用石灰石的炉次中,它的作用主要体现在降温效果上。
生石灰检验报告
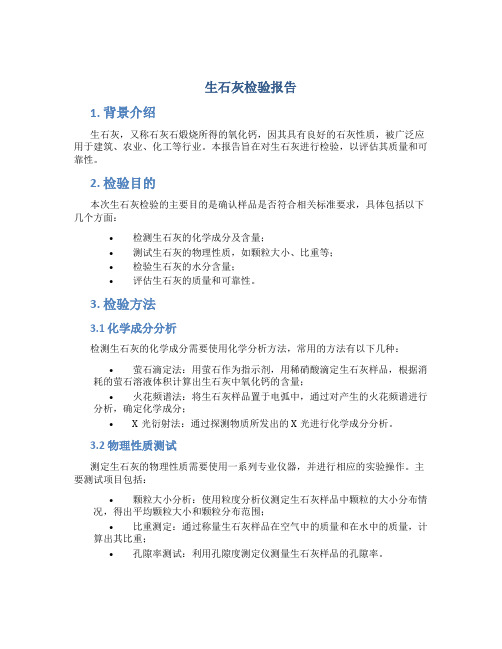
生石灰检验报告1. 背景介绍生石灰,又称石灰石煅烧所得的氧化钙,因其具有良好的石灰性质,被广泛应用于建筑、农业、化工等行业。
本报告旨在对生石灰进行检验,以评估其质量和可靠性。
2. 检验目的本次生石灰检验的主要目的是确认样品是否符合相关标准要求,具体包括以下几个方面:•检测生石灰的化学成分及含量;•测试生石灰的物理性质,如颗粒大小、比重等;•检验生石灰的水分含量;•评估生石灰的质量和可靠性。
3. 检验方法3.1 化学成分分析检测生石灰的化学成分需要使用化学分析方法,常用的方法有以下几种:•萤石滴定法:用萤石作为指示剂,用稀硝酸滴定生石灰样品,根据消耗的萤石溶液体积计算出生石灰中氧化钙的含量;•火花频谱法:将生石灰样品置于电弧中,通过对产生的火花频谱进行分析,确定化学成分;•X光衍射法:通过探测物质所发出的X光进行化学成分分析。
3.2 物理性质测试测定生石灰的物理性质需要使用一系列专业仪器,并进行相应的实验操作。
主要测试项目包括:•颗粒大小分析:使用粒度分析仪测定生石灰样品中颗粒的大小分布情况,得出平均颗粒大小和颗粒分布范围;•比重测定:通过称量生石灰样品在空气中的质量和在水中的质量,计算出其比重;•孔隙率测试:利用孔隙度测定仪测量生石灰样品的孔隙率。
3.3 水分含量检测生石灰的水分含量是衡量其质量和稳定性的一个重要指标,可使用以下方法进行检测:•烘箱法:将生石灰样品置于特定温度下,经过一段时间后再称量样品的质量,计算出水分含量;•气相色谱法:通过气相色谱仪测定生石灰样品中水分的含量。
4. 检验结果与讨论经过以上的检验方法,我们得到了以下生石灰样品的检验结果:•化学成分分析:氧化钙(CaO)含量为XX%,符合标准要求;•物理性质测试:平均颗粒大小为Xμm,颗粒分布范围为X-Xμm,比重为Xg/cm³,孔隙率为X%;•水分含量检测:水分含量为X%。
根据以上检验结果,可以得出结论:本次生石灰样品符合相关标准要求,化学成分、物理性质及水分含量均在合理范围内。
石灰材料实验报告范文(3篇)

第1篇实验名称:石灰材料性质研究一、实验目的1. 了解石灰材料的来源、组成及用途。
2. 掌握石灰材料的物理性质和化学性质。
3. 研究石灰材料在不同条件下的反应及变化。
二、实验原理石灰材料主要成分为氧化钙(CaO),俗称生石灰。
生石灰遇水后,会发生水化反应生成氢氧化钙(Ca(OH)2),俗称熟石灰。
熟石灰与空气中的二氧化碳(CO2)反应,会生成碳酸钙(CaCO3),俗称石灰石。
三、实验用品1. 生石灰2. 熟石灰3. 碳酸钙粉末4. 水5. 澄清石灰水6. 烧杯7. 试管8. 滴管9. 滤纸10. 酒精灯11. 移液管四、实验步骤1. 物理性质观察(1)观察生石灰的颜色、形状、质地等物理性质。
(2)观察熟石灰的颜色、形状、质地等物理性质。
(3)观察碳酸钙粉末的颜色、形状、质地等物理性质。
2. 化学性质研究(1)生石灰与水反应取一定量的生石灰放入烧杯中,加入适量水,观察反应现象,并记录。
(2)熟石灰与二氧化碳反应取一定量的熟石灰放入试管中,加入适量澄清石灰水,观察反应现象,并记录。
(3)碳酸钙粉末与盐酸反应取一定量的碳酸钙粉末放入烧杯中,加入适量盐酸,观察反应现象,并记录。
3. 实验现象分析(1)生石灰与水反应:生石灰遇水后,迅速放热,产生大量气泡,形成白色沉淀。
(2)熟石灰与二氧化碳反应:熟石灰与澄清石灰水反应,产生白色沉淀,使澄清石灰水变浑浊。
(3)碳酸钙粉末与盐酸反应:碳酸钙粉末与盐酸反应,产生气泡,溶液变浑浊。
五、实验结论1. 生石灰遇水会发生水化反应,生成氢氧化钙。
2. 熟石灰与二氧化碳反应,生成碳酸钙。
3. 碳酸钙粉末与盐酸反应,生成二氧化碳气体。
六、实验讨论1. 生石灰、熟石灰和碳酸钙粉末在物理性质和化学性质上有所不同,通过实验可以观察到明显的差异。
2. 生石灰遇水放热,反应剧烈,需要注意安全。
3. 熟石灰与二氧化碳反应,生成碳酸钙,可用于制备建筑材料。
4. 碳酸钙粉末与盐酸反应,产生二氧化碳气体,可用于检验二氧化碳的存在。
白云石、石灰石的检测分析

白云石、石灰石的全分析灼烧减量的测定一、分析方法称取干燥的试样0.25g于已恒重的瓷坩埚中, 置于960度的马沸炉中灼烧1小时, 取出在干燥器中冷却至室温, 称重二、计算:%=(G-G1)/G*100%式中G----为干燥后试样重即0.25gG1---为烧后试样重 g三、注意事项1 温度一般为960度, 时间白灰1小时, 石灰石1.5小时二氧化硅的测定一、试剂:1 盐酸 1+12 动物胶 0.4%(又叫明胶)3 硝酸比重1.42的浓硝酸二、分析方法:将灼烧后的试样置于有柄瓷坩埚中, 加1+1的盐酸25ml;于电热板上加热溶解, 待试样完全溶解后加入1-2滴浓硝酸继续加热至体积为8-10毫升取下冷却至50-60度时, (约1分钟)加入0.4%的动物胶溶液10毫升, 搅拌均匀后静止1分钟, 加20毫升热蒸馏水, 然后搅拌5分钟, 至于电热板低温处保温15分钟取下, 用热水冲洗表面皿及瓷坩埚,以快速滤纸过滤(滤前加纸浆),于400ml烧杯中,沉淀用5%的热盐酸洗涤4—5次,再用热水洗5—6次(即洗到无氯离子为止).1 将滤液作为测定R2O3的母液,如果不测R2O3,此滤液则作为测定CaO,MgO的母液.2 将沉淀连同滤纸放在瓷坩埚中灰化,然后在1000+_50度的马费炉内灼烧30分钟,取出冷却至室温后立即称重.三、计算:SiO2%=G1/G*100%式中:G1-----为沉淀重量,gG------为试样重量,即0.25g;四、注意事项:1 加入动物胶后搅拌时间必须充分,否则结果偏低.2 沉淀必须先灰化,直接灼烧易生成碳化硅.三氧化二物的测定一、试剂:1 氨水(NH4OH):比重0.9的浓氨水;2 氯化铵(NH4CL):20%,2%;二、分析方法:将测定SiO2后的母液稀释至150ml,加入20%的氯化铵20ml,用氨水中和至略有氨味后,再过量3—4滴(此时溶液的PH值=8-9),加热至沸,并至于电热板上保温至沉淀凝聚后取下,以快速滤纸(加纸浆)过滤,沉淀用2%的氯化铵溶液洗涤5-6次.1 滤液作为测定CaO,MgO的母液;2 将沉淀连同滤纸放在瓷坩埚中灰化,然后在960度的马费炉中灼烧30分钟取出,冷却至室温后立即称重.三、计算:R203=G2/G*100%式中:G2---为沉淀重量,g;G----为试样重量,g;即0.25g;氧化钙的测定1、一、试剂:2、氢氧化钾溶液: 20%3、钙试剂: 1克钙试剂与100克氯化钾研细混匀;4、EDTA标准溶液: 0.01783M;5、三乙醇胺溶液:1+1;二、分析方法:吸取母液50ml,与200ml烧杯中,加盐酸羟胺0.1克,三乙醇胺10ml,氢氧化钾25ml,钙试剂约0.1克,搅拌均匀后,用0.01783M的EDTA标准溶液滴定,至溶液由粉红色变为兰色即为终点,记录所消耗EDTA标准溶液的毫升数V.三、计算:CAO%=(V*M*0.05608)/(G/5)*100%式中:V------所消耗EDTA标准溶液的毫升数,ml;M-----为EDTA标准溶液的浓度,0.01783M;0.05608------CAO毫摩尔质量G-----试样重量, 即0.25克;氧化镁的测定一、试剂:1.氨水: 比重0.90的浓氨水;2.镁试剂: 1克铬黑T与100克氯化钾研细混匀;3.EDTA标准溶液: 0.01783M;4.三乙醇胺溶液: 1+1;5.氯化铵溶液: 20%;二、分析方法:吸取母液50ml于200ml烧杯中,加盐酸羟胺0.1克,三乙醇胺10ml,加入氯化铵溶液(20%)5ml,氨水(密度为0.90g/ml)15ml,镁指示剂0.1克,搅拌均匀后,用EDTA标准溶液滴定至兰色为终点,记录所消耗EDTA标准溶液的毫升数V1.三、计算:MgO=(V1-V)*M*0.04032/(G/5)*100%式中:V1----为滴定钙镁时所消耗的EDTA标准溶液的毫升数ml;V-----为滴定钙时所消耗的EDTA标准溶液的毫升数ml;M-----为EDTA标准溶液的浓度,0.01783M;0.04032---为氧化镁的毫摩尔质量;G------为试样重量, 即0.25克;活性度的测定一、试剂:1.0.1%的酚酞溶液(称取0.1克酚酞与100ml无水乙醇溶解)2.4M的盐酸(833ml的浓盐酸与1667ml的蒸馏水混匀,配成2500ml4M的盐酸)二、分析方法:取1000ml40度的水,加0.1%的酚酞试剂7—8滴,开动搅拌限时10分钟,把称好的试样(25克粒度大于1mm小于3mm)倒入烧杯中,用4M的盐酸中和溶液的红颜色,时间到后,记录所用盐酸的毫升数.三、计算:盐酸的毫升数*2。
钙化焙烧法实验报告
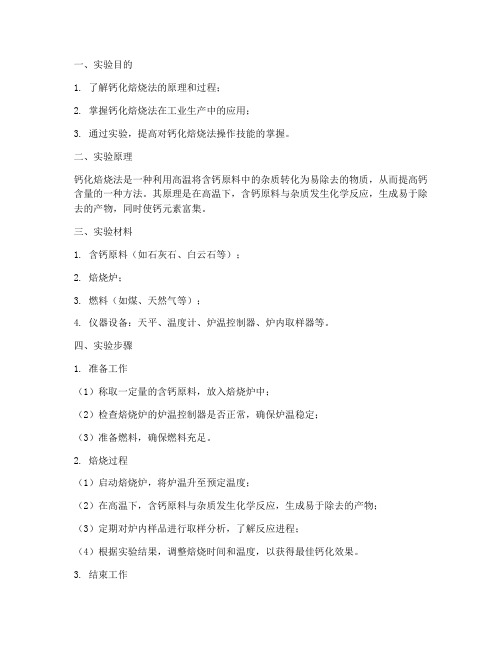
一、实验目的1. 了解钙化焙烧法的原理和过程;2. 掌握钙化焙烧法在工业生产中的应用;3. 通过实验,提高对钙化焙烧法操作技能的掌握。
二、实验原理钙化焙烧法是一种利用高温将含钙原料中的杂质转化为易除去的物质,从而提高钙含量的一种方法。
其原理是在高温下,含钙原料与杂质发生化学反应,生成易于除去的产物,同时使钙元素富集。
三、实验材料1. 含钙原料(如石灰石、白云石等);2. 焙烧炉;3. 燃料(如煤、天然气等);4. 仪器设备:天平、温度计、炉温控制器、炉内取样器等。
四、实验步骤1. 准备工作(1)称取一定量的含钙原料,放入焙烧炉中;(2)检查焙烧炉的炉温控制器是否正常,确保炉温稳定;(3)准备燃料,确保燃料充足。
2. 焙烧过程(1)启动焙烧炉,将炉温升至预定温度;(2)在高温下,含钙原料与杂质发生化学反应,生成易于除去的产物;(3)定期对炉内样品进行取样分析,了解反应进程;(4)根据实验结果,调整焙烧时间和温度,以获得最佳钙化效果。
3. 结束工作(1)停止燃料供应,关闭焙烧炉;(2)待炉温降至室温后,取出焙烧后的产物;(3)对产物进行取样分析,计算钙含量。
五、实验结果与分析1. 实验数据(1)焙烧前含钙原料钙含量:X1(%)(2)焙烧后产物钙含量:X2(%)(3)焙烧时间:T(h)(4)焙烧温度:T1(℃)2. 结果分析(1)通过对比焙烧前后含钙原料的钙含量,可以看出钙化焙烧法在提高钙含量方面具有显著效果;(2)根据实验结果,优化焙烧时间、温度等参数,以获得最佳钙化效果;(3)分析不同焙烧条件下产物钙含量的变化,了解钙化焙烧法的反应机理。
六、实验总结1. 钙化焙烧法是一种有效提高含钙原料钙含量的方法,具有广泛的应用前景;2. 通过实验,掌握了钙化焙烧法的操作技能,为今后工业生产提供了实践经验;3. 实验过程中,需要注意焙烧温度、时间等参数的调整,以确保实验结果的准确性。
七、参考文献[1] 张三,李四. 钙化焙烧法在工业生产中的应用[J]. 化工进展,2018,37(2):123-128.[2] 王五,赵六. 钙化焙烧法的研究进展[J]. 矿物加工与提取,2019,38(3):45-50.。
节能型立窑煅烧小块石灰石的实践与体会
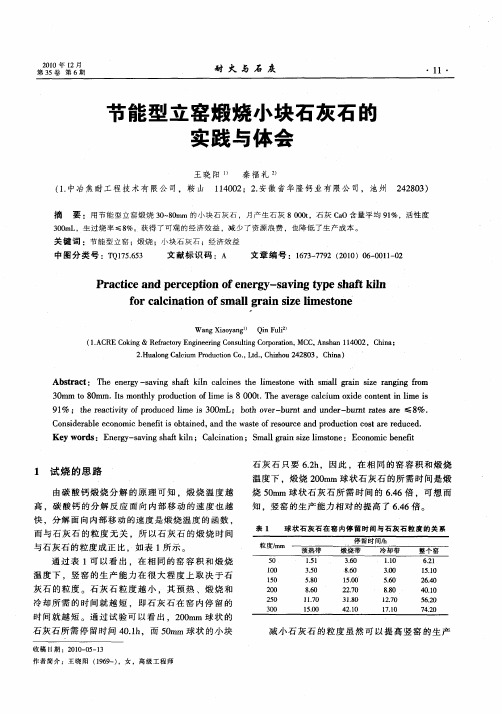
快 ,分 解 面 向 内 部 移 动 的 速 度 是 煅 烧 温 度 的 函 数 ,
石 灰 石 只要 62 ,因此 ,在 相 同 的窑 容 积 和 煅烧 .h
Ab t a t T e e e g s v n h f k l a c n s t e l so e wi mal g an sz a gn r m s r c : h n r y— a i g s at i c l i e h i t n t s l r i ie r n i g fo n me h 3 mm 0 0 t 8 mm. t n h y p o u t n o mei 0 t T ea e a e c l i m xd o tn n l o I mo t l r d c i f i 8 0 0 . h v r g a cu o i e c n e t i i s o l s i me s 9 % : t e r a t i fp o u e i s 3 0 1 h e c i t o r d c d l vy me i 0 mL; b t v r b r t n n e - u t ae r ≤ 8 . o h o e - u n d u d r b r t sa e a n r % C n i e a l c n mi e e t so ti e , n h s f e o r e a d p o u t n c s a er d c d o sd r b ee o o c b n f b an d a d t ewa t o s u c n r d c i o t r e u e . i i e r o
石灰石煅烧产物活性分析

文章编号 : 1 0 0 6 — 4 9 9 0 ( 2 0 1 3 ) 0 3 — 0 0 1 2 — 0 3
Ac t i v i t y a na l y s i s o f l i me s t on e c a l c i ne d p r o du c t Ch e n Ha i , Zh a ng S h i ho n g, Ya n g Ha i pi n g, Wa ng Xi a n hu a, Che n Ha n p i n g
( S t a t e K e yL a b o r t a o r y o f C o a l C o m b u s t i o n , H u a z h o n gU n i v e r s i t y fS o c i e n c e a n d T e c h n o l o g y , W u h a n4 3 0 0 7 4 , C h i n a )
Ab s t r a c t : I n o r d e r t o ma k e e f f e c t i v e u s e o f t h e l i me s t o n e wi t h s na i i l p a r t i c l e s ( ~1 0 mm) , t h e me t h o d o f s t a t i c c a l c i n a t i o n w a s
u s e d t o c a l c i n e t h e l i me s t o n e s a mp l e o f wh i c h t h e p a r t i c l e s i z e wa s a t 0 . 5 - 1 0 mm , a n d t h e i n l f u e n c e o f c a l c i n i n g t e mp e r a t u r e, c a l c i n i n g t i me , a n d p a r t i c l e s i z e o n t h e a c t i v i t y o f c a l c i n e d p r o d u c t wa s a n a l y z e d . Re s u l t s s h o w e d t h a t : c a l c i n i n g t e mp e r a t u r e a n d t i me c o u l d b o t h a f f e c t t h e l i me a c t i v i t y . Wi t h l o w c a l c i n i n g t e mp e r a t u r e a n d s h o t r t i me , l i me s t o n e c a n n o t b e c o mp l e t e l y c a l c i n e d, a n d t h e a c t i v i t y o f l i me w a s l o w; wi t h h i g h t e mp e r a t u r e a n d l o n g t i me, l i me s t o n e wo u l d b e e a s i l y o v e r b u r n t , a n d a c t i v i t y o f l i me wa s s t i l l n o t h i g h, a n d t h e h i g h e r t h e t e mp e r a t u r e w a s , t h e s o o n e r o v e r — b u r n i n g a p p e a r e d . T h e p r o d u c t o f t h e b e s t a c t i v i t y c a n b e o b t a i n e d wh e n t h e l i me s t o n e s a mp l e wa s c a l c i n e d f o r 6 0 mi n a t 9 5 0℃ . T h e p a r t i c l e s i z e o f l i me s t o n e a l s o h a d e f f e c t o n c a l c i n e d p r o d u c t S a c t i v i t y , a n d l i me a c t i v i t y d i d n o t i n c r e a s e wi t h p a t r i c l e s i z e o n a s i n g l e i n c r e a s i n g t r e n d, b u t r a t h e r r o u g h l y f i r s t i n c r e a s e d, t h e n d e c r e a s e d . I n t h i s t e s t t h e b e s t l i me a c t i v i t y a p p e a r e d wh e n p a r t i c l e s i z e wa s a t 2 - 3 on t i .
石灰石烧裂率测试实验报告
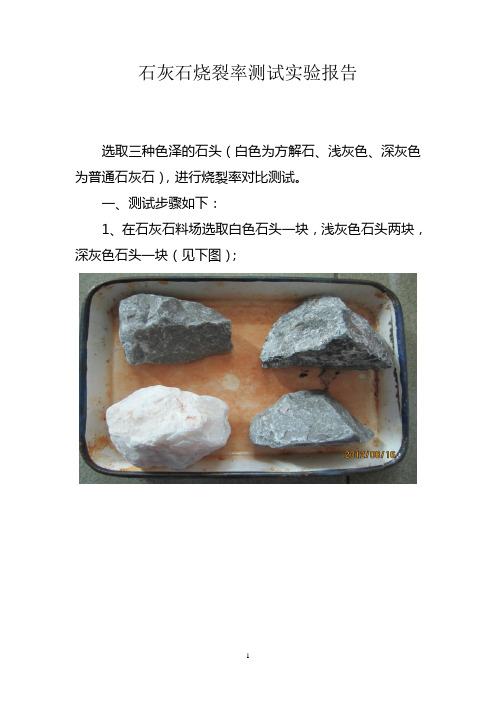
石灰石烧裂率测试实验报告
选取三种色泽的石头(白色为方解石、浅灰色、深灰色为普通石灰石),进行烧裂率对比测试。
一、测试步骤如下:
1、在石灰石料场选取白色石头一块,浅灰色石头两块,深灰色石头一块(见下图);
2、将三种色泽石头共四块放置于马弗炉热电偶两侧(见下图),缓慢升温至950℃,然后保温两个小时;
3、关闭马弗炉,待温度稍降取出四块团灰置于托盘上观察实验结果(见下图)。
二、实验结果对比如下
1、白色石头(方解石)实验前:
2、浅灰色石头(普通石灰石)实验前:
3、深灰色石头(普通石灰石)实验前:
4、强度测试,轻度挤压前四块石灰状态:轻度挤压后四块石灰状态:
三、实验结论及建议:
1、浅灰色石头为普通石灰石,煅烧后石灰颜色较白,强度符合要求;
2、深灰色石头也是普通石灰石占有一定比例,煅烧后石灰颜色白中带黄,其强度略高于白色石灰;
3、白色石头为方解石,煅烧后石灰颜色较白,表面布满裂纹,轻轻碰触后就碎裂,其强度低。
4、本次实验是在马弗炉内进行的静态、低温(950℃)煅烧实验,若将其置于麦窑的动态、高温(1050℃)工况下,则方解石会在煅烧带因高温分解爆裂、物料间的磨擦撞击下
碎裂,并在石灰冷却风的作用下风化成粉(既使有块状方解石灰出窑,也会在后步提升、运输、筛分、入仓过程中碎裂成小粒或粉状)。
5、方解石在煅烧带碎裂后也会局部气路堵塞,使石灰窑内热气流分布不均、窑压升高而不利于优质、低耗、高效生产,因此应严格进厂原材料控制,杜绝方解石和其他杂石进窑,以充分发挥石灰窑的技术优势。
石灰烧失量报告

石灰烧失量报告1. 引言石灰烧失量是指在石灰石烧制过程中,石灰石中所含的水分、二氧化碳和杂质等挥发和流失的部分。
石灰烧失量的准确测量对于生产过程的控制和成本分析具有重要意义。
本报告将对石灰烧失量进行分析和评估,并探讨影响石灰烧失量的因素。
2. 方法和过程石灰烧失量的测定通常采用工业炉或实验室炉进行石灰石的烧制,并通过对烧制前后石灰石质量的测量,计算石灰烧失量的百分比。
具体的实验过程如下:1.准备样品:从原料库中取出一定质量的石灰石作为样品。
2.称重:使用天平将样品的质量记录下来。
3.烧制:将样品放入实验室炉中进行烧制,烧制温度和时间根据实验要求确定。
4.冷却:待烧制完成后,将炉内的样品取出并放置在室温下进行冷却。
5.称重:冷却后,使用天平对烧制后的石灰石进行再次称重。
6.计算石灰烧失量:根据烧前后的质量差异,计算石灰烧失量的百分比。
3. 结果和分析对于不同的石灰石样品,进行了多次烧制实验,并记录了烧前后的质量以及计算得到的石灰烧失量。
下表给出了对三个样品进行的石灰烧失量实验的结果:样品编号烧前质量 (g) 烧后质量 (g) 石灰烧失量 (%)样品1 100 85 15样品2 200 180 10样品3 150 120 20从实验结果可以看出,石灰烧失量的百分比在不同样品之间存在一定的差异。
这可能是由于石灰石的成分、质量以及烧制过程中的温度和时间等因素的影响。
4. 影响因素分析石灰烧失量的大小受到多种因素的影响,主要包括以下几点:4.1 石灰石成分石灰石的成分是影响石灰烧失量的重要因素之一。
不同成分的石灰石在烧制过程中会产生不同的反应,从而导致石灰烧失量的差异。
4.2 烧制温度和时间烧制温度和时间是影响石灰烧失量的重要参数。
较高的温度和较长的烧制时间会导致石灰石中的水分、二氧化碳和其他挥发物质更多地被释放出来,从而增大石灰烧失量。
4.3 环境气氛石灰石烧制过程中的环境气氛也对石灰烧失量产生影响。
不同的气氛可能促进或阻碍石灰石中各种挥发物质的释放,从而导致石灰烧失量的变化。
高温煅烧石灰石。

高温煅烧石灰石。
高温煅烧石灰石-探索石灰石的奥秘石灰石是一种常见的矿石,在建筑、冶金、化工等领域有广泛的应用。
其中,高温煅烧是石灰石的一种重要处理方式,在其过程中,石灰石中的碳酸钙会发生热分解,生成二氧化碳和氧化钙。
这篇文章将围绕“高温煅烧石灰石”展开,从高温煅烧的原理、应用以及对环境的影响等方面进行探索。
一、高温煅烧石灰石的原理高温煅烧石灰石是通过将石灰石加热到高温下,使其发生热分解反应,从而得到氧化钙和二氧化碳。
石灰石中的主要成分是碳酸钙(CaCO3),其分子式为CaCO3。
在高温煅烧的过程中,石灰石中的碳酸钙会分解为氧化钙(CaO)和二氧化碳(CO2)。
这个反应可以用以下化学方程式表示:CaCO3→CaO+CO2二、高温煅烧石灰石的应用高温煅烧石灰石在工业生产中有着广泛的应用。
首先,氧化钙是建筑材料、冶金原料和化工原料的重要组成部分。
在建筑领域,氧化钙常常用于制备石灰和石膏等材料,用于砌筑建筑物和修复古建筑。
在冶金领域,氧化钙可用于炼钢、冶金反应和矿石的焙烧等。
在化工领域,氧化钙是生产石碱、氯碱和化肥等化学品的重要原料。
另外,高温煅烧石灰石还可以用于环保领域。
石灰石中的二氧化碳是温室气体的一种,对于全球气候变化有重要影响。
高温煅烧石灰石可以将石灰石中的二氧化碳释放出来,使其不再对大气产生温室效应。
此外,高温煅烧石灰石还可以用于处理工业废气和净化大气。
三、高温煅烧石灰石的环境影响尽管高温煅烧石灰石在应用中有很多好处,但它也会对环境产生一定的影响。
首先,在石灰石的高温煅烧过程中,会产生大量的二氧化碳。
这些二氧化碳如果排放到大气中,将会增加温室效应,加剧全球气候变化。
因此,在高温煅烧石灰石的过程中,需要采取措施来减少二氧化碳的排放。
其次,高温煅烧石灰石的过程还会产生一些其他的污染物,如硫酸、氮氧化物等。
这些污染物对于大气和水体都会造成一定的污染,对环境和生态系统产生负面影响。
因此,在高温煅烧石灰石的过程中,也需要采取措施来减少这些污染物的排放,以保护环境。
石灰石煅烧试验报告

石灰石煅烧试验报告试验目的:了解石灰石的煅烧性能,确定其煅烧温度对生产石灰的影响。
试验原理:石灰石在高温下进行煅烧,产生二氧化碳和石灰,并释放出热量。
石灰石主要由碳酸钙(CaCO3)组成,煅烧时,碳酸钙分解成二氧化碳和氧化钙(CaO)。
二氧化碳挥发,氧化钙则称为生石灰,可用于水泥、钢铁、冶金等工业。
试验设备:1800℃高温电炉、研磨器、计时器、天平等。
试验步骤:1. 将石灰石样品研磨成粉末,粒径控制在3mm以下。
2.将石灰石样品放入高温电炉中,加热到1000℃,保持1小时。
3. 以100℃/min的速率将温度升至1200℃,保持1小时。
4.将试验结束后的石灰石样品冷却,并称量质量。
5.对比不同煅烧温度下的石灰石样品质量,分析煅烧温度对产量的影响。
试验结果:根据试验结果,得到以下数据:煅烧温度(℃),石灰石质量(g)-------------,--------------1000,501200,40根据数据可以看出,煅烧温度对石灰石的质量有一定影响。
在相同时间内,较高的煅烧温度导致石灰石的质量减少。
这是因为高温下,碳酸钙分解的速度加快,二氧化碳挥发速度加快,导致石灰石的质量减少。
结论:根据试验结果可以得出结论,煅烧温度越高,石灰石质量越小。
因此,在生产石灰时,选择合适的煅烧温度对于保证石灰石产量是非常重要的。
同时,在石灰石煅烧过程中,还需要考虑其他因素,如煅烧时间、研磨细度等,以便获得更理想的石灰产品。
展望:本次试验只考察了不同温度下的石灰石质量变化,下一步可以对其他因素进行进一步研究,如煅烧时间、研磨细度等的影响。
通过进一步深入的研究,可以得到更全面的石灰石煅烧性能,为石灰产业的发展提供科学依据。
- 1、下载文档前请自行甄别文档内容的完整性,平台不提供额外的编辑、内容补充、找答案等附加服务。
- 2、"仅部分预览"的文档,不可在线预览部分如存在完整性等问题,可反馈申请退款(可完整预览的文档不适用该条件!)。
- 3、如文档侵犯您的权益,请联系客服反馈,我们会尽快为您处理(人工客服工作时间:9:00-18:30)。
安钢冶金炉料公司
石灰石煅烧试验报告
一、目的任务
对冶金炉料公司不同供户的石灰石进行试验研究,掌握其样品特性、煅烧性能,并根据这些特性进行分类,为石灰石供户优化选择提供依据。
二、试验设备及仪器
箱式电阻炉,天平,化验分析仪器等。
三、取样制样与化验
取样:到采石场现场取样,样品块度大于200mm,在每个采石场沿工作面按等距离跨度取10块样品。
制样:在白灰厂化验室制样,用锤子将取来的石灰石样品,制成约80mm、700g左右的球形煅烧样品。
同时,将剩余石灰石,用破碎机破碎后,制成青石化验样。
化验:青石样品送地质队化验室化验,化验项目分为CaO、MgO和SiO2三项,化验结果直接采用。
煅烧后的石灰,在白灰厂化验室化验活性度。
四、煅烧试验
取6块同一供户的石灰石样品,在托盘天平上称重,记录重量,当箱式电阻炉升温至550℃时,将样品入炉,保持一定的升温速率(升温约30分钟到1050℃),当升温至1050℃时箱式电阻炉自动恒温,在此温度下煅烧60分钟,断电降温60分钟(炉内温度降至600℃以下),将煅烧后的石灰取出,在室内冷却至室温后称重,并送化验室化验石灰活性度。
五、试验数据
煅烧试验数据表表1
六、数据计算
根据表1中的煅烧试验数据,计算烧失率、石灰石分解率、生烧率、白灰CaO含量、MgO含量、SiO2含量。
计算结果见表2。
计算结果表表2
七、数据分析
根据采样地点和有关资料推断,我公司目前焦炭石灰竖炉所采用的石灰石,产出地层分别是中奥陶统马家沟组第五岩性段和第七岩性段。
第五岩性段,其岩性特征为灰色、深灰色中厚层状、隐晶花斑石灰岩,是水泥用石灰岩的主要产出地层,由下而上划分五个亚层,因该岩性段石灰石杂质含量高(尤其是SiO2),一般不用作优质冶金石灰的原料。
第七岩性段,位于中奥陶统石灰岩地层最上部,为深灰色或灰色纯质石灰原料,局部夹
浅黄褐色薄层状白云质灰岩,厚度大,质量佳,层位稳定,根据层位、岩性和化学成分的不同,由下而上划分七个亚层。
从表1和表2的数据可以看出,育新、英雄、南街、后街、石堂、东傍佐石灰石中CaO+MgO含量都大于55%,SiO2含量小于%,石灰中SiO2含量小于%。
而新兴、宏达、马辛庄、铜冶、卜居头、东脑、鑫发石灰石中CaO+MgO 含量都小于55%,SiO2含量大于%,石灰中SiO2含量在石灰石没有完全分解的情况下已大于%(冶金一级灰标准SiO2含量<%)。
从段烧性能上分析,因东脑石灰石样品在煅烧过程中一块破碎,分解率最高,达到%,其他石灰石样品在该煅烧条件下分解率基本维持在60%左右。
分解率大于65%的有东脑、铜冶和育新,分解率大于60%小于65%的有宏达、卜居头、马辛庄、鑫发和英雄,分解率低于60%的有后街、南街北和石堂。
从段烧后的石灰质量分析,活性度大于300ml的有育新,活性度大于250ml小于300ml的有宏达、马辛庄、英雄、鑫发、卜居头、南街北和后街,活性度小于等于250ml的有石堂、新兴、东傍佐、铜冶和东脑。
八、结论
⒈除东脑因一块石灰石在段烧过程中碎裂分解率异常外,其他石灰石分解率均在60%左右,煅烧性能因石灰石产出地层不同,石灰石中杂质含量不同而存在差异,但总体上来看差异性不大。
⒉从产地和有关资料知,育新、英雄、南街、后街、鑫发、石堂和东傍佐为中奥陶统马家沟组第七岩性段石灰岩,除鑫发异常外,其他CaO+MgO 含量高,SiO2等杂质含量低,为煅烧优质冶金石灰的原料。
新兴、宏达、马辛庄、铜冶、卜居头、东脑为中奥陶统马家沟组第五岩性段石灰岩,石灰
石中CaO+MgO含量比第七岩性段石灰岩低,SiO2含量高于国家一级灰标准。
⒊在相同煅烧条件下,13家供户样品煅烧出的石灰活性度与石灰石中CaO和MgO含量的关系规律性不强,与分解率的关系规律性亦不强。
⒋本次试验因取样方法、取样数量、煅烧次数及化验误差等原因,代表性可能不强,试验结果不可避免地存在一定误差,试验数据和结论仅作为参考。
安全生产技术部
物资供销部
政工部
二OO六年六月十九日。