DOE-全因子试验设计培训
DOE实验设计法培训报告.pptx

特性描述实验
最优化实验
验证实验
2x2全因子实验
效应和主效应定义
• 效应(Effect):指的是因子变化时,输出发生的变化。
• 我们希望的状态; 发电机的例子中,发电机的 例子中, 我们希望经过投资改造,B的产出 会增加;
• 寻找证据是为了证明这种假设; • 统计学上用符号Ha表示(H:Hypothesis;a:
alternative)
• 统计学对原假设的描述:
• Ha:mA<mB • Ha:mA-mB<d
• 假设检验的目标:证明给出的数据不是来个同一个总体,从而拒绝Ho和接受Ha
• 通常我们没有总体的数据,因为获得总体的数据很难,代价很高。所以我们通过分析样本来推测 总体的参数
平均值、极差与方差
平均值或者均值(Average or Mean):一组数据的平均值仅仅是所有数据的几何平均
这里X 代表观察到的变量,xi代表一组数据中的第i个数据,S代表求和,代表所有数据的平均。
P值
• 在数据服从正态分布的情况下,如果以下条件成立: 发电机A和发电机B的产出没有差异 统计上的描述:A的数据和B的数据来自同一个总体 假设真实差异为 0,P 值等于获得观测(通过样本计算出)差异的概率。
• 我们把这个概率叫做“P”值。直观的讲“P”值为根据样本计算出 原假设为真的概率。 • 如果“P”值很小,基于小概率事件原理,我们就可以说“发电机 A和发电机B的表现没有差异”
商供应,注塑工程师想了解不同供应商复合物的注塑件表面强度是否 不一样。 目的: 证明不同供应商原材料的注塑件表面强度一样 建立假设:
原假设:不同供应商原材料的注塑件表面强度一样 Ho: μ1=μ 2=μ 3=μ4
DOE实验设计培训(洪剑坪老师)
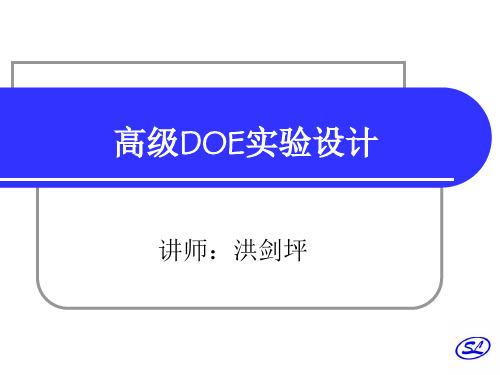
实验设计的基本术语
可控制的因子 (输入变量)
x1 x2
xp
输入
Process
输出
y(输出变量)
z1 z 2
zq
不可控制的因子 (杂音变量)
DOE常见术语
• 正因为正交试验是用部分试验来代替全 面试验的,它不可能像全面试验那样对各因 素效应、交互作用一一分析;当交互作用存 在时,有可能出现交互作用的混杂。虽然正 交试验设计有上述不足,但它能通过部分试 验找到最优水平组合 ,因 而 很 受实际工作 者青睐。
图10-1
• 3 因 素 3 水 平 的 全 面试验水平组合数为
5
-
-+
+
-
-
+
18.73 18.63 18.79 18.73
6
+
-+
-
+
-
-
19.17 18.76 18.94 18.96
7
-
++
-
-
+
-
18.40 18.73 19.04 18.73
8
+
++
+
+
+
+
18.54 19.46 18.97 18.99
Avg+
Avg△
2 部分因子正交实验设计
• 正交实验设计的基本概念
基本术语——交互作用
• 交互作用图示
产量
75 70
DOE实验设计培训教材 经典完整版

DOE实验设计培训教材经典完整版实验设计是科学研究中至关重要的一环,它能够帮助研究者准确、有效地得出结论,并为进一步的实验提供可靠的依据。
为了提高实验设计的质量和效果,了解并应用正交试验设计(Design of Experiments, DOE)成为必要的技能。
本教材将介绍DOE的基本原理和方法,帮助读者达到熟练运用DOE设计实验的能力。
DOE简介DOE作为一种系统的实验设计方法,可以同时考虑多个因素对实验结果的影响,通过设计合理的实验方案,得出可靠的结论。
相比于传统的试错法,DOE具有高效、精确、经济的特点,适用于各种科研和工程实验。
1. 实验设计基础1.1 可变因素与响应变量在实验中,可变因素是指可以被科学研究者操纵的因素,而响应变量则是受这些可变因素影响的实验结果指标。
了解可变因素与响应变量的关系是进行实验设计的基础。
1.2 实验设计的目标实验设计的目标是寻找可变因素对响应变量的最佳组合,从而得到对研究问题有重要意义的结论。
常见的实验设计目标包括确定最优条件、寻找影响因素、找出因素间的相互作用等。
2. 正交试验设计2.1 正交试验设计的原理正交试验设计是一种基于统计学原理的实验设计方法,通过选定一组正交表,将试验因素进行组合,来实现对多个试验变量的全面考虑。
通过正交试验设计,可降低实验次数,并减少实验中因非试验因素带来的误差。
2.2 正交试验设计的步骤2.2.1 确定试验因素与水平在进行正交试验设计之前,需要明确研究中的试验因素及其各个水平。
试验因素可以是任何对响应变量产生影响的因素,而水平则是试验因素的具体取值。
2.2.2 构建正交表根据试验因素的水平个数,选择适当的正交表进行构建。
正交表的选择要满足试验因素个数和水平个数的要求,以保证实验设计的合理性。
2.2.3 设计实验方案根据所选正交表的要求,将试验因素与各个水平进行组合,得到实验的方案。
通过合理的组合,可以实现对多个试验因素的全面考虑。
试验设计DOE培训教材

优点
1. 与一次只改变一个参数的实验方法相比,可以减少试验次数(24:8) 2. 可以观察参数间的相互作用 3. 得到的结果适用范围更广——主效应和相互作用是在各参数各种可能的组 合的情况下得到的,与实际情况较接近。
缺点
所有可能的组合都必须加以深究,信息全面,但相当耗费时间、金钱 例如: 13因子,3水准就必须做了1,594,323次实验,如果每个实验花3分钟, 每天8小时,一年250个工作天,共须做40年的时间。 由于这个缺点,完全析因实验(特别是多参数的完全析因实验)在工业中并未得到广 泛的应用。 而如果可以假设一定的高阶相互作用是可以忽略的,则通过仅进行完全析因实验所要 求的一部分试验便可以得到主效应和低阶相互作用。实际经验表明,这样做往往是合 理的,这类实验称为部分因子实验。 20世纪50年代田口博士(Dr.Taguchi)把部分因子实验的应用技术进行了简化,大大方便 了普通工程师把这种实验设计应用于解决工程实际问题。因此也叫田口式实验法。
所以,用正交表来安排试验时,各因子的 各种水平的搭配是均衡的,这是正交表 的优点
1. 如有图所示输入因子资料(3因子,3水平) 2. 数据输入完毕,打开Stat 菜单,点选 DOE--- Taguchi ---Create Taguchi Design…
3. 在弹出的对话框中选择3-Level Design 4. “Number of factors”中选择3 5. 点击Design 6. 在对话框中选择L9,点击OK 普通试验需 做27次
特点: 1. 一条对角线上全是A,另一条对角线上是4。 2. 方块与梅花左右对称的,红桃与黑桃左右 对称。 3. 方块与黑桃,梅花与红桃上下对称。 4. A与4, 2与3左右对称。 5. A与4, 2与3上下对称。 6. 两条对角线上四种四种花色齐全。
实验设计(DOE)方法培训教案PPT课件

.
14
根据具体要求选择DOE实验方法
• DOE实验方法流程如图(二)所示
实验设计的基本策略
• 1、确定问题
• 为解决何种问题,需要进行的何种实验,应做到心中有数, 有的放矢。
• 2、建立实验目标
• 实验要达到何种目的,要达到怎样的指标,应从实际出发, 根据当时当地的实情,确定实验目标,不要夸大其辞,矫 揉造作。
复运行的结果计算出平均值(Y) 6. 按标准计算软件或EXCEL进行计算
.
19
7. 作出实验因子的影响及关系图
8. 进行方差分析,用以决定实验因子是否重要,用P值进 行衡量(P〈0.05)
9. 对方差分析结果进行评价,以确定因子对实验的影响程度
10. 选择重要因子(通常不超过4个)而进行全因子DOE实验,以 确定实验的最终结果
.
25
3、考核指标 考核指标是在试验设计中,根据试验目的而选定的用来
衡量试验效果的量值(指标)。 考核指标可以是定量的,也可以是定性的。定量指标如
硬度、强度、寿命、成本、几何尺寸、各种特性等。定量 指标根据试验结果的预期要求,又可分为望目值、望小值、 望大值三种类型。定性指标不是按数而是按质区分,如质 量的好与坏,天气的晴与阴,指标可以用加权的方法 量化为不同等级。
.
10
36) 材料的影响 37) 机器设备的影响 38) 测试设备的影响 39) 领导者的支持 40) 制造者支持 41) 工程部门的支持 42) 优化后的合格率 43) 配合度 44) 测量精密 45) 随机抽样 46) 块的区分 47) 决定区分程度 48) 假设构造
49) 测量方法 50) 管理者支持 51) 将实验结果图表化 52) 确定主要因子 53) 计算出各因子影响大小 54) 作出相关因子影响图 55) 连续样本 56) 从样本收集到样本测量的时
六西格玛doe实验设计培训
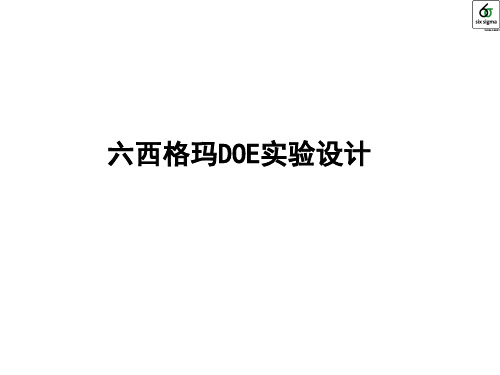
部分因子实验 在23全因子实验法的基本设计上追加2个因子. 因子数 : 5 实验数= 8次 D=AB E=AC 即ABD=1 ACE=1 BDCE=1 , BD=CE
-1,1
1,1
-1,1
时 间 1,1
-1,-1
1,1
湿度 温度
实验次数= 23 +3 2为水准数,3为因子数,3为中心点数量
追定
为了改善的大概 方向
(线形效果)
主效果和局部 交互作用
所有的主效果 和交互作用 可估计弯曲
输出变量的预测
模型 (曲率效果)
因全阶乘因子实验,实验次数过多,实验较复杂
通常使用2k 两水平全因子实验法(增加中心点后近似可代替3水平因子实验),实验次数大幅减少
2因子实验
未编码
温度
200 300 250 250 200 250 300
中心点 1 1 1 1 1 1 1 1 1 1 1 1 1 1 1 1
部分因子实验例题 2. Minitab路径: 统计-DOE-因子-分析因子设计 选择输出变量数据列,图形选项勾选正态和4合1图
从两个图中可以看出,显著因子为B D BD E DE五个 (Catalyst Temp Conc三个因子及Catalyst*Temp Conc*Temp两个交互项)
部分因子间关系
所有 因子之间的关系
X与Y的二次关系 X的最优点
分析
改善的粗略方向 (线形效果)
最重要的因素
主效果和局部 交互作用
实验设计(DOE)方法培训

和偏差。
控制干扰因素
02
考虑并控制可能干扰实验结果的干扰因素,如仪器误差、环境
变化等。
可重复性与可扩展性
03
确保实验方案具有可重复性和可扩展性,以便验证实验结果和
推广应用。
注意数据收集与分析的准确性
数据质量
确保数据收集过程中准确记录和处理数据,避免数据失真或遗漏 。
数据分析方法
根据实验目的和数据类型选择合适的数据分析方法,如回归分析 、方差分析、主成分分析等。
降低成本
通过优化实验设计,可以 减少不必要的实验次数和 资源消耗,从而降低成本 。
提高生产效率
通过实验设计,可以确定 最佳的工艺参数和操作条 件,从而提高生产效率。
DOE的历史与发展
历史
实验设计起源于20世纪20年代的统计学领域,随着计算机技术的发展,实验设 计方法得到了广泛应用。
发展
现代实验设计方法已经广泛应用于各个领域,如制造业、医药、生物技术等。 同时,随着大数据和人工智能技术的发展,实验设计方法也在不断创新和发展 。
02
实验设计(DOE)基本原理
因子与水平
因子
影响产品、过程或系统性能的变量称为因子。
水平
因子的不同状态或取值。
因子与水平的选择
根据实际需求和条件选择合适的因子和水平。
实验设计类型
完全随机设计
每个因子在每个水平上的 组合都是随机的。
部分因子设计
只选取部分因子和水平进 行实验。
饱和设计
包含所有因子和水平的组 合。
确定实验设计的主要目的和研究问题,确保实验结果能够解 决实际问题。
确定研究范围
明确实验研究的范围和边界条件,避免不必要的复杂性和确定影响实验结果的关键因素或变量 ,这些因素可能对实验结果产生影响 。
DOE 全因子设计

Improve- 完全要因实验 - 7
- 高),数率平均也增加
主效果 Plot
反应温度对数率影响大,但浓度对此几乎没有影响。但此因 子间交互作用,可能是歪曲的判断结果,所以没有交互作用 的前提下才能说这结论是准确。
Improve- 完全要因实验 - 8
交互作用(Interaction Effect)
交互作用
除了各因子的个别效果之外,因子组合特别效果有无? 交互作用:因2因子以上特定因子水准组合而出现的效果。
交互作用存在与否
- 一个因子的效果随着另一个因子水准的变化而变化时, 存在交互作用效果。
交互作用(Interaction Effect)
交互作用的有•无
数 率 +1 B=+1 +1 -1
没有交互作用时,对应相对因子各水准的 输出变量变化是平行。 有交互作用时,对应相对因子各水准的输 出变量变化是交叉或不平行。
-1
-1 +1 无交互作用状态
B=-1 A
数 率
+1 -1 -1
Process Engineer知道对半导体数率的温度,浓度及压力的效果。
2阶段: 设定因子及水准,用Minitab作成实验DATA SHEET
因子及水准
反应温度 (℃) : 160℃ (-1) , 180 ℃ (+1) B 浓度 (%) : 20% (-1) , 40% (+1)
C 压力(psi) : 5 psi (-1) , 10 psi (+1)
DOE(试验设计)培训课件

正交设计
利用正交表安排多因素多水平的 试验,寻找最优组合。
均匀设计
在一定范围内均匀选取试验点, 进行多因素多水平的试验,寻找 最优组合。
03
试验设计的应用
试验设计在产品研发中的应用
80%
确定产品性能指标
通过试验设计,确定产品的性能 指标,确保产品能够满足用户需 求。
100%
优化产品设计
试验设计可以帮助优化产品设计 ,提高产品的性能、可靠性和安 全性。
DOE的重要性
• 试验设计在生产或制造过程中具有非常重要的意义。通过试验设计,可以有效地确定影响产品或过程的关键因素,提高产品质量和生效率 。此外,试验设计还可以帮助企业优化资源配置,降低生产成本,提高市场竞争力。
DOE的发展历程
试验设计作为一种科学方法,最初起源于20世纪20年代的农业科 学研究。随着工业革命的推进,试验设计逐渐被应用于工业制造 领域。在20世纪60年代,美国通用电气公司成功应用试验设计方 法优化了其生产过程,取得了显著的经济效益。此后,试验设计 逐渐受到全球各行各业的关注和应用。
DOE(试验设计)培训课件
汇报人:
2023-12-05
目
CONTENCT
录
• DOE简介 • DOE基本原理 • 试验设计的应用 • DOE案例分析 • DOE实践建议 • 相关工具介绍
01
DOE简介
什么是DOE
• DOE(Design of Experiments)是试验设计的英文缩写,它是一种系统性的方法,用于确定和优化在生产或制造过程中影 响关键输出的因素。试验设计通过合理地选择试验因子和水平,以及科学地安排试验顺序,来揭示影响关键输出的因素, 并为优化关键输出提供依据。
DOE实验设计培训教材
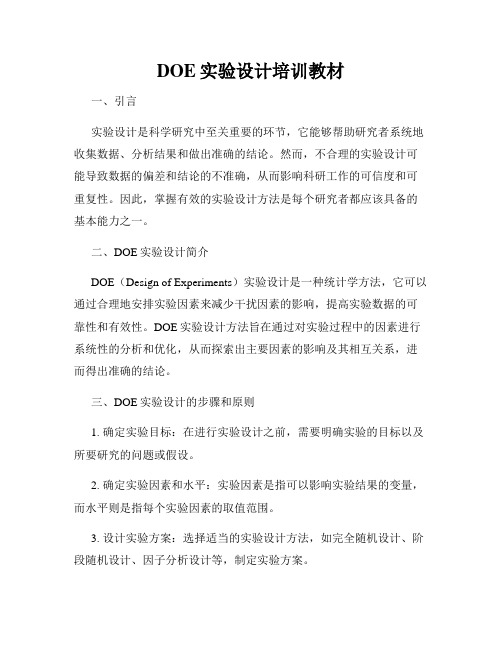
DOE实验设计培训教材一、引言实验设计是科学研究中至关重要的环节,它能够帮助研究者系统地收集数据、分析结果和做出准确的结论。
然而,不合理的实验设计可能导致数据的偏差和结论的不准确,从而影响科研工作的可信度和可重复性。
因此,掌握有效的实验设计方法是每个研究者都应该具备的基本能力之一。
二、DOE实验设计简介DOE(Design of Experiments)实验设计是一种统计学方法,它可以通过合理地安排实验因素来减少干扰因素的影响,提高实验数据的可靠性和有效性。
DOE实验设计方法旨在通过对实验过程中的因素进行系统性的分析和优化,从而探索出主要因素的影响及其相互关系,进而得出准确的结论。
三、DOE实验设计的步骤和原则1. 确定实验目标:在进行实验设计之前,需要明确实验的目标以及所要研究的问题或假设。
2. 确定实验因素和水平:实验因素是指可以影响实验结果的变量,而水平则是指每个实验因素的取值范围。
3. 设计实验方案:选择适当的实验设计方法,如完全随机设计、阶段随机设计、因子分析设计等,制定实验方案。
4. 进行实验:按照实验设计方案进行实验,记录实验数据。
5. 数据分析和结论:利用统计学方法对实验数据进行分析,得出结论,并评估实验结果的可靠性和有效性。
6. 优化实验设计:根据实验结果和结论,对实验设计进行优化并进行进一步的实验,以获得更准确和可靠的结果。
四、常用的DOE实验设计方法1. 完全随机设计(Completely Randomized Design,CRD):适用于因素水平较少、实验设计简单的情况。
2. 阶段随机设计(Randomized Complete Block Design,RCBD):适用于因素水平较多、可能存在随机误差的情况。
3. 因子分析设计(Factorial Design):用于分析多个因素对实验结果的影响及其相互作用。
4. 方案比较设计(Comparative Design):用于比较不同实验方案的效果,并确定最佳方案。
DOE实验设计培训教材(经典完整版)MinitabPPT课件

• 流程中的关键变量是:
Y原料卖主。(A,B,C)
Y原料放进混合桶中的温度。(高,中,低)
Y在混合桶顶部的温度。 (高,中,低)
Y在混合桶底部的温度。 (高,中,低)
Y混合桶中的压力。(高,中,低)
Y桶中的原料量。(20,50,100,150公吨)
Y原料拿离混合桶的温度02
6Sigma实 验
S IGM
A
确定 衡量 分析
1.识别回应衡量
YS 实验设计 2.识别因素和
XS
3.选择设计和障碍
实验分 析
4.任意排列 运行 5. 收集资 6料.分析资料
7. 得出结论 8. 核实结果
改进 控制
Version Nov 2002
Page
S
实验-实验设计范
I G
例
M
• 项目声明-背景
11 12 13 14 15 16 17 18 19
20 21 22 23 24 25 26 27 28 29 30 31
32
. . .
2
X1 X2 X3 X4
S I G M X5 ... Xk
A
Page
Version Nov 2002
S
概要:因数策略(2)
I G
k
M
• 当因素增加,运行次数成指数倍增加 A
Number of factors:3
实验设计
3. 选择设计和障 碍
Select Designs Full or fractional Number of replicates Number of blocks Select Factors Names Low Level High Level
4. 任意排列 运 行
实验设计DOE全因子设计实验(2K设计)培训课件讲义

区组 协变量
难改变因子 (HTC)
异同点
特征
是过程因子,往往是非可控管理因子
往往将所有试验游程分段(如:上午/下午)
是过程因子,往往是非可控因子
在所有试验游程中一直存在,随时变化, 对效应往往有明显影响,如:环境温度
是过程因子,可控因子,但在试验中因子 水平的调整很难或时间/成本较高。 对应“易改变因子EHC”
作为试验设计的研究分析对象,水平会改 变。不按完全随机,在HTC上一次调整做 多次试验。
32
2.3. 全因子设计 - 2k设计 – 分析因子设计
权重:每次游程(试验过程)输出“质量”可能会不同
对象域:存 在需要考虑 的权重时, 在数据表中 写明(某一 列),该变 量会在“对 象域”显示, 通过“选择” 按钮选选择。
➢ 使用了水平代码 -1(低),+1(高)
25
2.1. 全因子设计 - 2k设计- 创建因子设计
26
DOE流程5 实施实验及收集数据
27
2.2. 全因子设计 - 2k设计 – 试验实施和记录
23 试验次数8,增加4个中心点,仿行数1 的全因子设计结果;共12次试验。 每次试验后对Y进行测量,建议使用多次测量均值;测量系统具有很好的分辨力,可接 受重复性/再现性,可接受的偏倚/稳定性和线性(见MSA测量系统分析)。 做好记录
通过数学计算实施分析判定不一定可 靠,对数学计算借助图形进行直观的观察 和分析在Mintab是不可或缺的一步。
14
1.4. 全因子设计 - 2k设计 – 分析判定
在实施全因子设计和部分因子设计(又称析因设计)实验结果分析中,Minitan 给出回归分析和方差分析结论,生成供我们分析的信息 — 工程师要学会解释这些数 据并作出正确的决策。 包括6项分析指标:
DOE试验设计培训的策划与安排

张驰咨询向全国各地的各行业提供六西格玛、精益六西格玛、DFSS 咨询培训与项目辅导咨询!(客户续签率连续10多年来高达95%以上) /DOE 试验设计培训的策划与安排人类认识自然就的过程是循序渐进的。
一般是先根据已有的知识提出某种设想,设计一个试验去验证或否定它,从试验中获得的数据帮人们验证或修正初始的设想,然后提出一个更新、更深入的设想,再设计新的试验...这个反复的过程会一直持续下去,直到形成了较为完整的理论结果为止。
我们进行试验也是一个学习过程,不可能一蹴而就。
我们不要企图“毕其功于一役”,进行一次试验就结束战斗。
一般来说,试验要进行好几批,一般采用下面几个步骤:一次试验就结束战斗。
一般来说,试验要进行好几批,一般采用下面几个步骤:一、用部分实施的因子设计进行因子的筛选最开始,情况不很清楚,考虑到影响相响应变量的因子个数可能较多(大于或等于5),这是应在较大的试验范围内,先进行因子的筛选,通常应使用部分实施的因子试验设计法,这样获得的结果可能较为粗糙,但试验次数可以大节省,筛选的目的能够达到就行了。
如果认为部分实施的因子试验费用仍然太昂贵,则可以使用试验次数更少的“Plackett-Burman ”方法来筛选因子。
二、用全因子试验设计法对因子效应和交互作用进行全面的分析当因子的个数被筛选到少于等于5个之后,我们可以进一步在稍小范围内进行全因子试验设计以获得全部全部因子效应和交互作用的准确信息,并进一步筛选因子直到因子个数不超过3个。
三、用响应曲面方法(RSM )确定回归关系并求出最优设置当因子个数不超过3个时,我们就有条件采用更细致得多的响应曲面设计分析方法,在包含最优点的一个较小区域内,对响应变量拟合一个二次方程,从而可以得到试验区域内的最优点。
以上所说的是典型的步骤。
在实际工作中,可能跳过某个环节,也可能在某个步骤上反复进行好几次。
总之,要不断地筛选因子,不断地调整试验的范围和因子水平的选择,经过几轮试验后才能最终达到我们试验的总目标。
- 1、下载文档前请自行甄别文档内容的完整性,平台不提供额外的编辑、内容补充、找答案等附加服务。
- 2、"仅部分预览"的文档,不可在线预览部分如存在完整性等问题,可反馈申请退款(可完整预览的文档不适用该条件!)。
- 3、如文档侵犯您的权益,请联系客服反馈,我们会尽快为您处理(人工客服工作时间:9:00-18:30)。
试验的定义
■试验:为了能观察到对于输出变化的影响,对过程和系统的
输入变量进行有计划的设置,测试并分析结果的方法.
(不可控因子) U1 U2 U3-------------- Um
Input
Output 。 。
(可控因子)
X1 ,X2…XK
艺条件。这几个因子及准备安排的试验水平如下: A:加热温度, 低水平:820 ,高水平860(摄氏度) B:加热时间,低水平:2 , 高水平:3 (分钟)
C:转换时间, 低水平:1.4 , 高水平:1.6(分钟) D:保温 时间, 低水平:50 , 高水平:60 (分钟) 解:由于要细致考虑到各因子及其交互作用,因此采用全因子试验最为合适,
强度 残差图
正态概率图
99 90 10 5
与拟合值
百分比
50 10 1 -10 -5 0 残差 5 10
残差
0 -5 520 540 拟合值 560 580
直方图
4.8 3.6 10 5
与顺序
频率
2.4 1.2
残差
-6 -4 -2 0 残差 2 4 6 8
0 -5
0.0 2 4 6 8 10 12 观测 值 顺序 14 16 18
案例:合成氨试验1
例:在合成氨生产中,考虑两个因子(A,B),每个因子皆2水平,A:温 度,低水平 700℃,高水平:720 ℃。B:压力, 低水平: 1200帕, 高水 平:1250帕。以产量y为响应变量(单位:kg),列表如下:
A
B
低温( 700℃)
200 230
高温( 720 ℃)
220 250
强度 交互作用图
数据平均值
2.0 2.5 3.0 1.4 1.5 1.6 50 55 60 560
加热 温度 820 840 860 加热 温度 820 840 860
点类型 角点 中心 角点 点类型 角点 中心 角点
加热温度
540
520 560
加热时间
540
520 560
加热 加热 温度 时间 点类型 点类型 820 2.0 角点 角点 840 中心 2.5 中心 860 3.0 角点 角点 加热 时间 点类型 2.0 角点 2.5 中心 3.0 角点 转换 时间 点类型 1.4 角点 1.5 中心 1.6 角点
1-拟合选定模型
2-进行残差诊断
3-模型要改进吗?
N
Y
4-对选定模型进行分析解释
5-判定目标是否达成
Y
N
进行验证试验
进行下批试验
全因子试验设计案例:
例:改进热处理工艺提高钢板断裂强度问题,合金钢板经热处理后将提高某 抗断裂性能,但工艺参数的选择是个复杂的问题。我们希望考虑可能影响断
裂强度的4个因子,确认哪些因子影响确实是显著的,进而确定出最佳的工
A B
低温( 700℃)
200 230
高温( 720 ℃)
220 270
低压(1200) 高压(1250)
因子A的主效应=Y的平均值|A=高- Y的平均值|A=低 =245-215=30kg 因子B的主效应= Y的平均值|B=高- Y的平均值|B=低 =250-210=40kg 因子B在低水平时A的效应=220-200=20kg 因子B在高水平时A的效应=270-230=40kg AB交互效应=(A的效应|B=高- A的效应|B=低)/2 =(40-20)/2=10kg
0
-8
-4
B
0 残差
4
8
2
4
6
8 10 12 观测 值 顺序
14
16
18
项
D
因子
名称
BD
A B D
加热温度 加热时间 保温时间
0
1
2
3
4 5 标准化效应
6
7
8
Step5:对选定模型进行分析解释—回归方程
Y(强度)=213.1+0.5009A-61.35B-2.445D+1.4225BD
Step5.对选定模型进行分析解释---因子主效应 Minitab>统计>DOE>因子>因子图
转换时间
540
520
保温时间
Step5.对选定模型进行分析解释---输出等值线,响应曲线图
Minitab>统计>DOE>因子>等值线/曲面图
强度 与 保温时间 , 加热时间 的等值线图
60
525 530 535 540 强度 < 525 – 530 – 535 – 540 – 545 > 545
58
并在因子中心点组合处进行3-4次试验。总试验次数共19次=24+3
Step1:创建试验计划 Minitab>统计>DOE>因子>创建因子
Step1:创建试验计划---计划矩阵
实验因子
Step1:创建试验计划
实验结果
Step2:拟合选定模型 Minitab>统计>DOE>因子>分析因子设计
Step3,4:进行残差诊断和判断模型是否要改进
保温时间
56
保持值 加热温度 820
54
52
50 2.0
2.2
2.4 2.6 加热时间
2.8
3.0
Step5.对选定模型进行分析解释-----实现最优化 Minitab>统计>DOE>因子>响应优化器
Step5: 实现最优化配置工艺参数。
Step6:进行试验验证---判定目标是否达到
主要是将预计的最佳值与原试验目标相比较,如果离目标尚远,则应考虑安排 新一轮试验,通常在本次获得的或预计的最佳点附近,重新选定试验的各因子 及其水平。继续做因子设计。以获得更好结果。
低压(1200) 高压(1250)
因子A的主效应=Y的平均值|A=高- Y的平均值|A=低 =235-215=20kg 因子B的主效应= Y的平均值|B=高- Y的平均值|B=低 =240-210=30kg 因子B在低水平时A的效应=220-200=20kg 因子B在高水平时A的效应=250-230=20kg AB交互效应=(A的效应|B=高- A的效应|B=低)/2 =(20-20)=0kg
AB无交互作用时的效应图
Y(产量)交互作用图数据平均值
250 240
B(压力)
低 高
平 230 均 值 220
210
200
低
高
A(温度)
案例:合成氨试验2
例:在合成氨生产中,考虑两个因子(A,B),每个因子皆2水平,A:温度,低水平 700℃,高水平:720 ℃。B:压力, 低水平: 1200帕, 高水平:1250帕。以产量y 为响应变量(单位:kg),列表如下:
标准化效应的 P a r e t o 图
(响应为 强度,Alpha = 2.306 A B D BD C 因子 A B C D 名称 加热温度 加热时间 转换时间 保温时间 .05)
项
AD BC CD AB AC 0 1 2 3 4 标准化效应
5
6
7
Step4:模型改进 Minitab>统计>DOE>因子>分析因子设计
过程
。 。
(品质特性值) Y1 ,Y2…Ys
数学模型:
Y=f(X1, X2…XK)+ε
我们在试验设计中建立的输出和输入之间数学模型,其中ε由不可控因子(或噪音引起 试验误差)
试验设计目的和用语
试验目的:
一是明确哪些自变量x显著地影响着y; 二是找出y与x间关系式,从而进一步找出自变量x取什么值时会使y达到最佳值. 用语 响应变量:模型中y1 ,y2…ys是我们关心的s个输出变量。
4.选择试验计划 5.实施阶段
根据试验目的,选择正确的试验类型,确定区组状况,试 验次数,并按随机化原则安排好试验顺序衣试验单元的分 配。排好计划矩阵 按计划矩阵安排试验。 使用minitab分析。
6.分析阶段
全因子试验设计定义和试验原则
1.全因子试验设计:所有因子的所有水平的所有组合都至少要进行一次试验的这种设 计.适用范围:全因子试验设计适应于因子个数不超过5个。
AB有交互作用时的效应图
Y(产量)有交互作用图数据平均值
270 260 250 240
B(压力) 低 高
平 均 值
230
220
210 200
低
高
A(温度)
试验设计的基本步聚
1. 阐述目标 2. 选择响应变量 3.选择因子及水平
团队成员都要投入讨论,明确目标及要求。究竟是为了筛 选因子还是为了寻找关系式? 在一个试验中若有多种响应,则要选择起关键作用的且最 好是连续型指标作为响应变量。 用流程图及因果图先列出所有可能对响应变量有影响的因 子清单,然后根据数据和各方面的知识及专业经验,进行 细致分析并作初步筛选。
因
子:我们将影响响应变量哪些变量称为试验问题中的因子。
水 平:为了研究因子对响应变量的影响,需要用到因子的两个或更多个不同 的取值。 处 理:各因子皆选定了水平后,其组合被称为处理 主效应:响应变量在某因子处于不同水平时平均值差异称为某因子的主效应 交互效应:当因子B处于不同水平时,因子A的效应到底差多少? 交互作用:如果因子A的效应依赖于因子B所处的水平,则称为AB有交互作用
试验原则:
1.随机原则: 以完全随机的方式安排各次试验的顺序和或所用试验单元. 2.完全重复原则: 一个处理要施于多个试验单元. 3.(分区组原则):为了使试验单元或试验环境具有同质齐性而以某种方式对试验单 元分区组如:需要长期的数据收集的情况,通常以日别、周别等区分组,在区组内