5s管理内容
5s管理内容和标准

5s管理内容和标准一、整理(Seiri)整理的目的是将工作场所中的物品区分为必要的与不必要的,去除不必要的物品,保留必要的物品,以腾出空间,防止误用。
内容:区分工作现场的必需品与非必需品。
清理非必需品,确保工作场所宽敞整洁。
对必需品进行合理布局,方便取用。
标准:工作场所内无多余物品,空间利用高效。
物品分类清晰,标识明确。
员工能迅速找到所需物品,减少时间浪费。
二、整顿(Seiton)整顿的目的是将必要的物品按照规定的位置摆放整齐,并做好标识,以便使用时能立即取到。
内容:确定物品的放置位置,制定放置方法。
对物品进行标识,方便识别。
摆放整齐,确保取用方便。
标准:物品摆放有序,整齐划一。
标识清晰,易于识别。
员工能迅速、准确地取用物品。
三、清扫(Seiso)清扫的目的是清除工作场所内的灰尘、垃圾和污物,保持环境干净明亮。
内容:定期对工作场所进行清扫,保持环境整洁。
清除设备、工具上的污垢和油渍。
检查设备、工具的运行状况,及时发现问题并处理。
标准:工作场所干净明亮,无垃圾、灰尘。
设备、工具清洁,运行良好。
员工养成良好的卫生习惯。
四、清洁(Seiketsu)清洁的目的是通过制度化、规范化的管理,维持清扫后的整洁状态,使整理、整顿、清扫的成果得以保持。
内容:制定清洁工作标准和流程。
定期检查清洁效果,及时纠正问题。
通过培训和教育,提高员工的清洁意识。
标准:清洁工作标准明确,流程规范。
工作场所始终保持整洁状态。
员工自觉遵守清洁规定,养成良好的清洁习惯。
五、素养(Shitsuke)素养的目的是培养员工良好的工作习惯和敬业精神,提高员工整体素质。
内容:培养员工遵守规章制度、安全操作规程的习惯。
提高员工团队协作能力和沟通能力。
培养员工积极进取、勇于创新的精神。
标准:员工遵守规章制度,安全意识强。
团队协作默契,沟通顺畅。
员工积极进取,具有创新精神。
六、标准制定制定明确的5S管理标准和操作规范,确保员工能够按照标准进行实施。
内容:制定详细的5S管理标准和操作流程。
5S管理内容及意义

5S管理内容及意义5S管理是一种管理方法,源自于日本的“整理、整顿、清扫、清洁、素养”五个以日语罗马拼音的词语的头字母。
它是通过改善工作环境及员工素养,强调整理、整顿、清扫、清洁、素养等环节,达到提高工作效率、减少浪费、降低事故风险以及改善企业文化的目的。
下面将详细介绍5S管理的内容及意义。
首先,5S管理包括以下五个步骤:1. 整理(Sort):清理工作场所,将所需和不需要的物品进行区分,保持只留下必需物品,去除多余、废弃的物品。
2. 整顿(Set in order):根据工作的频率及使用频率,将必需物品合理摆放,使工作场所更加整齐、有序。
3. 清扫(Shine):定期清洁工作场所,包括机器设备、工作台、地面等,避免灰尘和杂物的干扰,保持工作环境的清洁与安全。
4. 清洁(Standardize):建立清洁标准及规范,制定相关的工作程序和操作规程,确保清洁工作能持续进行下去。
5. 素养(Sustain):培养员工的素养和习惯,使他们能够主动参与到5S管理中,形成自觉遵守5S管理的工作习惯。
5S管理的意义在于:1.提高工作效率:通过整理、整顿、清扫等环节,减少时间浪费,保证所需物品的高效获取和使用,提高工作效率和生产效率。
2.降低浪费:通过整理和整顿,去除多余和废弃物品,减少物料、能源和时间的浪费,提高资源利用效率,降低成本。
3.优化工作环境:通过清扫和清洁,保持工作场所的整洁、干净,创造一个良好的工作环境,提高员工的工作积极性和工作质量。
4.提高安全性:通过整顿和清洁,清理工作区域的障碍物和危险品,减少事故风险,提高工作场所的安全性。
5.提升企业形象:通过5S管理,使企业形象更加整洁、规范,塑造一个良好的企业形象,增强消费者和合作伙伴的信任和合作意愿。
6.培养员工素养:通过素养环节,培养员工的自觉遵守规章制度的习惯,提高员工的工作素质和职业道德,促进员工的个人成长。
7.改善企业文化:通过5S管理,强调整理、整顿、清扫、清洁、素养等环节,培养企业员工的团队合作精神、自觉遵守规章制度的意识,改善企业的工作文化。
公司5s管理内容和标准

5S是一种现场管理方法,起源于日本,旨在通过整理、整顿、清扫、清洁和素养这五个步骤来改善工作环境,提高工作效率和产品质量。
以下是公司实施5S管理的内容和标准:
1. 整理(Seiri):
-判断工作现场的工具、材料和产品是否必要。
-移除不必要物品,只保留必要的物品。
-分类整理剩余物品,确保每一样物品都有固定的存放位置。
2. 整顿(Seiton):
-确保工作现场的物品摆放有序,易于取用。
-使用标签、颜色编码或其他标识方法,明确物品的存放位置和类别。
-定期检查和调整物品的存放位置,以保持整顿的效果。
3. 清扫(Seiso):
-定期清扫工作现场,保持清洁。
-清理垃圾和废料,保持工作区域的整洁。
-检查设备和工作台,确保其处于良好的工作状态。
4. 清洁(Seiketsu):
-建立清洁标准和工作流程,确保工作现场的清洁。
-使用适当的清洁工具和清洁剂。
-定期检查和评估清洁工作的质量。
5. 素养(Shitsuke):
-培养员工的良好工作习惯和遵守规定的意识。
-定期进行5S培训,提高员工的5S意识和技能。
-建立奖惩机制,鼓励员工积极参与5S活动。
实施5S管理时,公司应制定相应的标准和流程,并定期进行检查和评估,以确保5S 活动的有效实施。
同时,公司还应鼓励员工积极参与5S管理,提高工作环境和工作效率。
5s管理的具体内容

5s管理的具体内容什么是5s管理?5s管理是一种以提高工作环境整洁度和效率为目标的管理方法,是源自日本的一种管理工具,五个日文单词的第一个字母“S”对应着整理、整顿、清扫、清洁、素养,每个“S”代表着一项具体的管理内容,目的是提高组织的效率、安全性和员工士气,推动持续改进。
5s管理的具体内容:1. 整理(Seiri)整理是指根据必要与不必要去分类和清除物品,将工作场所的杂物和不必要的物品清除出去,只保留必要的物品。
这有利于提高生产效率和工作效率,减少废品率,降低工作强度。
2. 整顿(Seiton)整顿是指合理摆放和整理工作场所的物品,确保物品摆放的合理有序,以便工作人员容易取用,减少找东西的时间浪费,提高工作效率。
3. 清扫(Seiso)清扫是指保持工作场所整洁,定期清洁工作场所,清除灰尘、杂物、污垢等,确保工作环境清洁卫生,提高员工的工作积极性。
4. 清洁(Seiketsu)清洁是指保持工作环境的整洁、清洁,规范作业程序和标准,确保工作环境的卫生,创造一个整洁、安全、高效的工作环境。
5. 素养(Shitsuke)素养是指培养员工的自律性和规范性,鼓励员工遵守规章制度,建立正确的工作态度和价值观,保持5s管理的长期有效性。
5s管理的意义:•提高生产效率:通过整理、整顿、清扫、清洁、素养,提高工作场所整洁度和规范性,减少浪费,提高生产效率。
•提高产品质量:减少废品率、杂物干扰,提升产品质量。
•降低成本:减少物料浪费和损耗,提高设备利用率,降低生产成本。
•改善工作环境:创造整洁、清洁、安全、有序的工作环境,提高员工的工作积极性。
•增强企业竞争力:通过5s管理,提高企业管理效率,优化生产流程,增强企业的市场竞争力。
结语5s管理是一种简单有效的管理方法,可以帮助企业提高效率、降低成本、改善工作环境,是企业持续改进的有力工具。
通过整理、整顿、清扫、清洁、素养的管理实践,促进企业的持续发展和进步。
5s管理内容是什么

5s管理内容是什么5S管理是一种以“整理、整顿、清扫、清洁、素养”五个日语词汇的首字母命名的管理方法,它是一种以创造整洁、有序的工作环境,提高工作效率和品质为目标的管理方式。
首先,整理是指把必要和不必要的物品分开,把不必要的物品清除出去,使工作场所变得整洁。
其次,整顿是指设定物品的摆放位置,使物品易于取用。
清扫是指定期对工作场所进行清扫,保持整洁。
清洁是指定期对机器设备、工作台等进行清洁,以保持生产环境的整洁。
素养是指培养员工的素质,使员工具备良好的工作态度和行为习惯。
5S管理的核心价值是在于通过整理、整顿、清扫、清洁、素养五项活动,使企业的生产现场变得整洁、有序、清洁,达到提高工作效率和品质的目标。
5S管理的实施可以使企业的管理更加规范化,工作环境更加整洁,员工的素质更加提高,从而提高企业的竞争力。
在实施5S管理时,首先需要进行现场整理,将工作现场的必要和不必要的物品进行分类,清除不必要的物品,使工作现场变得整洁。
然后进行整顿,对工作现场的物品进行合理的摆放,使物品易于取用。
接着进行清扫,定期对工作现场进行清扫,保持整洁。
再进行清洁,对机器设备、工作台等进行清洁,保持生产环境的整洁。
最后进行素养,培养员工的良好工作态度和行为习惯。
在实施5S管理时,需要全员参与,从领导到员工都要积极参与其中。
领导要起到表率作用,带头执行5S管理,员工要自觉遵守5S管理的要求,积极参与5S管理的活动。
同时,需要制定相应的5S管理制度和规范,明确5S管理的具体要求和责任,对5S管理进行考核和奖惩,使5S管理得到有效执行。
总之,5S管理是一种以创造整洁、有序的工作环境,提高工作效率和品质为目标的管理方式。
它通过整理、整顿、清扫、清洁、素养五项活动,使企业的生产现场变得整洁、有序、清洁,提高企业的竞争力。
在实施5S管理时,需要全员参与,制定相应的5S管理制度和规范,对5S管理进行考核和奖惩,使5S管理得到有效执行。
希望通过5S管理,能够使企业的管理更加规范化,工作环境更加整洁,员工的素质更加提高,从而提高企业的竞争力。
5s管理内容及要求

5s管理内容及要求一、5s管理概述5s管理是一种源自日本的管理实践方法,主要是通过整理、整顿、清扫、清洁和素养的五个步骤,使工作环境变得更加整洁、高效,提高工作效率和品质。
二、5s管理的五个步骤1.整理(Seiri)•内容:整理是指清除工作场所中没有必要的物品,只保留必要的物品,清理出不必要的杂物和过剩的物品。
•要求:员工需要彻底检查工作场所,识别并清除无用的工具、备件、文档等,确保只留下确实有用的物品。
2.整顿(Seiton)•内容:整顿是指对必须保留的物品进行整顿,合理布置,使物品易于找到、使用和管理。
•要求:设定固定的各项工具和物品存放区域,明确标识每种物品的固定位置,并保持整齐有序。
3.清扫(Seiso)•内容:清扫是指保持工作环境的清洁,包括清洁设备、工具、地面、车间等。
•要求:制定清洁计划,确保每日定时对工作场所进行清洁,保持整洁干净的工作环境。
4.清洁(Seiketsu)•内容:清洁是指保持工作环境的卫生、整洁,并严格执行相关标准。
•要求:培养员工的清洁习惯,确保每一个员工遵守清洁规范,养成良好的工作环境卫生习惯。
5.素养(Shitsuke)•内容:素养是指遵守规章制度,自觉遵守规范,形成良好的工作作风。
•要求:培养员工自觉遵守5s规范,加强对员工的相关培训和考核,促进员工之间的相互督促。
三、5s管理的要求和益处•要求:5s管理要求企业全员参与,持续改进和保持5s管理的持久性,不断创造整洁、高效、安全的工作环境。
•益处:通过5s管理,可以提高工作效率、减少浪费、增加工作舒适度,降低事故风险,提升品质和生产效率。
结语5s管理不仅是一种管理方法,更是一种企业文化的建设和提升。
通过全员参与、持续改进,不断提高5s管理的执行力和深度,将对企业的发展和成长产生积极影响。
希望企业能够将5s管理融入到日常工作中,实现管理的精细化和高效化,为企业的可持续发展打下坚实的基础。
简述5s管理的主要内容

简述5s管理的主要内容5S管理是一种常用于企业的管理方法,旨在提高工作环境的整洁度和效率。
它的主要内容包括整理、整顿、清扫、清洁和素养,下面将对这五个方面进行详细介绍。
整理是指对工作场所的物品进行分类、归纳和清理。
通过整理,可以清楚地了解每个物品的用途和位置,避免物品的混乱和浪费。
整理还可以发现和解决工作中的问题,提高工作效率。
整顿是指对工作流程和方法进行规范和优化。
通过整顿,可以制定标准化的工作流程和操作规范,确保工作的一致性和高效性。
整顿还可以发现和改进不合理的工作方法,提高工作效率和质量。
第三,清扫是指对工作场所进行定期的清理和维护。
通过清扫,可以清除工作场所的灰尘、垃圾和杂物,保持工作环境的整洁和有序。
清扫还可以发现和预防安全隐患,提高工作的安全性和舒适性。
第四,清洁是指对工作设备和工作工具进行定期的清洗和保养。
通过清洁,可以确保工作设备的正常运行和寿命,减少故障和损坏。
清洁还可以提高工作设备的效率和质量,减少能源和资源的浪费。
素养是指员工的职业道德和工作态度。
通过培养良好的素养,可以提高员工的责任心和自觉性,增强团队的凝聚力和合作性。
素养还可以提高员工的专业技能和创新能力,提升企业的竞争力和发展潜力。
5S管理的主要内容包括整理、整顿、清扫、清洁和素养。
这些内容旨在提高工作环境的整洁度和效率,优化工作流程和方法,保持工作设备的正常运行和寿命,并培养良好的职业道德和工作态度。
通过5S管理,企业可以提高工作效率和质量,降低成本和风险,提升竞争力和发展潜力。
因此,5S管理是企业管理中的重要工具,值得广泛应用和推广。
5s管理的内容及实施步骤

5S管理的内容及实施步骤什么是5S管理5S管理是源自于日本工业界的一种管理方法,旨在通过整理、整顿、清扫、清洁和素养等五项措施,提高工作环境的效率和效益。
5S管理以排序、整顿、清扫、清洁和素养为核心,通过改善工作环境,并达到预防和消除浪费的目的。
5S管理的内容5S管理的内容包括以下五个方面:1.排序(Seiri):指将工作场所的物品进行分类,只保留有用和必要的物品,剔除多余的物品。
在排序过程中,需要根据工作流程和使用频率判断物品的需求,并清理和整理工作区域。
2.整顿(Seiton):指对工作环境进行整顿,保持工作区域整洁有序。
整顿包括确定物品的归位位置,优化存储方式,并标识物品的归属和用途。
3.清扫(Seiso):指定期对工作场所进行清扫,保持工作区域的清洁。
清扫包括清理垃圾、清除积尘和保持设备设施的卫生。
4.清洁(Seiketsu):指对整个工作环境进行定期的清洁和保养,并确保工作区域的卫生质量。
清洁包括建立清洁标准、培养良好的清洁习惯和提高清洁技能。
5.素养(Shitsuke):指保持5S管理的长期效果,并将其纳入工作习惯之中,实现自觉遵守5S管理的目标。
素养需要通过培训和激励来推动,确保员工能够自觉参与5S管理,并持续改进工作环境。
5S管理的实施步骤实施5S管理需要按照以下步骤进行:1. 创建项目团队创建一个专门负责5S管理的项目团队,包括管理人员、专家和员工代表,确保有足够的资源和人力来推动5S管理的实施。
2. 明确目标和计划明确5S管理的目标和计划,包括时间安排、工作内容和工作量,制定可行的实施计划,并将其与团队成员共享。
3. 开展学习和培训组织5S管理的相关培训和学习活动,确保员工了解5S管理的概念、目标和操作方法,并掌握必要的技能。
4. 进行现场调研和分析对工作场所进行现场调研和分析,了解当前工作环境和问题,确定需要改进的地方,并针对性地制定改进措施。
5. 开展排序活动与团队成员一起进行排序活动,对工作区域的物品进行分类和整理,剔除多余的物品,并确定物品的归位位置和使用频率。
5s管理内容及要求

5s管理内容及要求1. 5s管理概述5s管理是一种以“整顿(Seiri)”、“整理(Seiton)”、“清扫(Seiso)”、“清洁(Seiketsu)”、“素养(Shitsuke)”为主要内容的管理方法。
通过5s管理,可以提高工作效率,减少浪费,改善工作环境,提升员工素养,使企业更加高效。
2. 5s管理内容2.1 整顿(Seiri)整顿是指清除现场上不必要的物品,材料,设备等,确保场地整洁有序,避免工作混乱,提高工作效率。
在整顿过程中,要严格分类物品,决定保留和淘汰的标准,确保只保留必需的物品。
2.2 整理(Seiton)整理是指确定好放置每种物品的位置,确保工作场所物品摆放有序,易于取用。
在整理中,可以通过标识、分区等方式规范化物品放置,提高工作效率,减少寻找时间。
2.3 清扫(Seiso)清扫是指定期对工作场所进行彻底清洁,包括清除垃圾、清洁设备、清洁地面等。
通过定期清扫,可以改善工作环境,减少尘埃、细菌等对员工的影响,提高工作效率。
2.4 清洁(Seiketsu)清洁是指建立清洁标准,确保工作场所始终保持清洁整洁的状态。
清洁是维持整体5s管理效果的关键,通过制定清洁标准,培养员工良好的卫生习惯,持续改善工作环境。
2.5 素养(Shitsuke)素养是指坚持做到5s管理的规范要求,使之成为一种习惯,贯穿工作始终。
素养是5s管理的精髓,需要培养员工对5s管理的认同和执行力,使之成为企业文化的一部分。
3. 5s管理要求3.1 领导重视企业领导应高度重视5s管理,倡导全员参与、全员负责的理念,支持5s管理的开展,提供必要的资源和条件。
3.2 培训教育企业应对员工进行5s管理的培训教育,使之了解5s管理的重要性、方法和作用,培养良好的管理习惯。
3.3 制度完善建立健全的5s管理制度,明确5s管理的责任制度、操作规程,监督检查制度,奖惩机制等,保障5s管理顺利进行。
3.4 常态化执行5s管理应成为企业常态化工作,定期开展5s检查,并及时整改不足,确保5s管理的长期有效性。
5s管理内容及要求有哪些

5s管理内容及要求有哪些在现代管理中,5s管理是一种常用的管理方式,它通过整理、整顿、清洁、清扫、素养这5个步骤,提高工作效率、减少浪费、增强员工协作能力,进而推动企业的持续发展。
下面将详细介绍5s管理的内容以及对各项内容的要求。
1. 整理(Seiri)整理是指分清必需和非必需的物品,将不必要的东西分类清除,保留必要的物品。
对于整理而言,要求包括:•定期清点物品,及时剔除不需要的物品。
•保持工作场所整洁,避免杂物堆积。
•将物品分类存放,便于取用。
2. 整顿(Seiton)整顿是指将必要的物品整齐摆放,便于工作和管理。
对于整顿,要求包括:•制定合理的工作流程,确定工作站点。
•标示物品的存放位置,确保易于找到。
•维护工作环境整齐有序,防止乱放乱堆。
3. 清洁(Seiso)清洁是指保持工作环境的清洁卫生,有助于提高工作效率和安全。
对于清洁,要求包括:•定期清理工作区域,保持干净整洁。
•保持设备设施的清洁,并定期检查维护。
•培养员工保持个人卫生的好习惯。
4. 清扫(Seiketsu)清扫是指增强对整理、整顿、清洁的持续性,并形成良好的管理制度。
对于清扫,要求包括:•制定清洁计划,明确责任人和时间节点。
•对标准操作规程进行规范化,确保操作一致性。
•定期检查实施情况,及时处理问题。
5. 素养(Shitsuke)素养是指养成良好的工作习惯和态度,将5s管理贯彻到生活和工作中。
对于素养,要求包括:•培养团队合作和自我约束的意识。
•提高员工的责任心和主动性。
•不断加强培训,提升员工素养水平。
在实施5s管理中,企业要充分认识到每个步骤的重要性,并严格要求员工执行。
只有通过持续的培训和监督,才能确保5s管理的有效实施,提升企业的竞争力和效益。
5s管理制度的内容有什么

5s管理制度的内容有什么1. 5s管理制度的概述5s管理制度是一种重要的管理工具,广泛应用于企业和组织的生产、管理和服务过程中。
5s指的是整理(Seiri)、整顿(Seiton)、清扫(Seiso)、清洁(Seiketsu)和素养(Shitsuke)的五个日语词汇的首字母,也被认为是精益生产管理模式中的基础。
2. 整理(Seiri)整理是指通过淘汰、归类、清理工作区域,创造出一个有序、整洁的工作环境。
整理的目标是减少浪费、提高效率,并为后续的整顿、清扫和清洁奠定基础。
整理的内容包括:•淘汰不需要的物品:将工作区域中不再需要或过期的物品清理出去,避免占用空间和资源。
•归类和标识:将物品按照不同的类别归类,并为每个类别标识明确的标签,方便查找和管理。
•设置合理的存储位置:为每个物品设置合适的存储位置,减少寻找和取用物品的时间。
•保持工作区域清洁:定期检查和整理工作区域,保持工作区域的整洁和有序。
3. 整顿(Seiton)整顿是指将整理好的物品和设备有条不紊地摆放在合适的位置,使工作环境更加整洁和高效。
整顿的目标是减少非价值添加的工作流程,提高工作效率。
整顿的内容包括:•组织和布局:将物品按照使用频率、优先级或其他合适的标准进行组织和布局,使物品易于取用,并减少不必要的移动和运输。
•标准化工作区域:为工作区域设定标准,包括标识位置、标识物品和标识放置方式等,使所有人能够遵循相同的标准进行工作。
•制定管理规范和流程:制定相应的管理规范和流程,明确工作区域的使用和维护要求,以及相关责任和权限。
4. 清扫(Seiso)和清洁(Seiketsu)清扫和清洁是保持工作环境整洁和卫生的关键环节,也是5s管理制度中重要的一部分。
清扫和清洁的目标是预防事故和疾病,提升工作环境的可视性,促进员工的工作态度和素质。
清扫和清洁的内容包括:•定期清扫工作区域:定期对工作区域进行彻底的清扫,包括地面、墙壁、天花板和设备等,确保没有杂物和垃圾堆积。
5s管理的内容与作用

5s管理的内容与作用
5S管理的内容包括:常整理、整顿、清扫、清洁和修养。
具体来说,整理
是指对工作场所进行全面检查,制定需要和不需要的判别基准,并根据物品的使用频率进行分层管理;整顿则是要对可供放的场所和物架进行划线定位,将物品在规划好的地方摆放整齐,并标示所有的场所、物品;清扫则是指建立清扫责任区,执行定期扫除,清理脏污,并调查污染源,予以杜绝或隔离;清洁是指建立清扫标准,开展一次全公司的大清扫,每个地方都要清洗干净;修养则是指每位成员养成良好习惯,遵守规则做事。
5S管理的作用包括:
1. 确保安全:通过推行5S管理,企业可以避免因漏油而引起的火灾或滑倒,以及因灰尘或油污所引起的公害等,从而确保生产安全。
2. 扩大销售:一个拥有清洁、整齐、安全、舒适的环境以及良好素养的员工队伍的企业,往往更能获得客户的信赖,从而扩大销售。
3. 标准化:通过推行5S管理,企业可以在内部养成守标准的习惯,使得各项活动和作业均按标准的要求运行,为提供稳定的质量打下基础。
以上内容仅供参考,如需更多信息,建议查阅相关文献或咨询企业管理人员。
简述5s管理内容

简述5s管理内容5S管理是一种精益生产工具,旨在通过整理、整顿、清洁、标准化和自律的方式来提高工作环境的效率和质量。
本文将从以下几个方面进行详细介绍:5S管理的含义、五项基本步骤、实施5S管理的好处以及注意事项。
一、5S管理的含义5S管理是源于日本的一种生产管理方法,其名字来源于日语中五个单词的首字母:Seiri(整理)、Seiton(整顿)、Seiso(清洁)、Seiketsu(标准化)和Shitsuke(自律)。
这五个单词代表了五个基本步骤,每一个步骤都有其独特的目标和方法。
二、五项基本步骤1. 整理(Seiri)整理是指将工作场所中不必要或无用的物品清除。
这些物品可能包括废弃物品、过时文件或设备等。
通过清除这些无用物品,可以使工作场所更加整洁和有序,并且可以避免浪费时间和资源在处理无用物品上。
2. 整顿(Seiton)整顿是指对工作场所进行重新布置,使得所有必要的物品都能够迅速找到并使用。
这需要对工作场所进行标记和分类,以便于人们快速找到所需的物品。
整顿还可以帮助减少不必要的移动和寻找时间,从而提高生产效率。
3. 清洁(Seiso)清洁是指对工作场所进行彻底清洗和维护。
这包括清除污垢、灰尘和杂乱物品等。
通过保持一个干净、整洁的工作环境,可以提高工作效率,并且有助于保持员工健康和安全。
4. 标准化(Seiketsu)标准化是指制定规定和标准,以确保所有员工都按照同样的方式执行任务。
这有助于避免混乱和错误,并提高生产效率。
标准化还可以使管理者更容易检查并评估员工的表现。
5. 自律(Shitsuke)自律是指通过培养良好的习惯和行为来保持5S管理系统的有效性。
这需要员工始终遵守规定,保持积极主动的态度,并不断改进自己的表现。
三、实施5S管理的好处1. 提高生产效率通过5S管理系统,可以优化生产流程并消除浪费。
这有助于提高生产效率和质量,从而提高企业的竞争力。
2. 改善工作环境通过清洁、整洁和有序的工作环境,可以使员工更加舒适、健康和安全。
5s管理的内容具体有哪些

5s管理的内容具体有哪些
1. 整理 (Sort)
整理是5s管理的第一步,它是指清除现场上不必要的物品,确保只有必要的
物品才会留在工作场所。
整理的目的是提高工作效率,减少浪费和避免混乱。
在整理过程中,需要对工作场所进行分类和标记,以便员工快速找到需要的物品。
2. 整顿 (Set in order)
整顿是指对工作场所进行布局和组织,使其更加整洁、高效和易于操作。
通过
整顿,可以确保每个物品都有固定的位置,并且标记清晰明了。
这样可以减少寻找物品的时间,提高工作效率。
3. 清扫 (Shine)
清扫是保持工作场所整洁和清洁的关键步骤。
定期清扫工作场所可以减少灰尘、垃圾和污垢的堆积,提高工作环境的舒适度和安全性。
清扫也有助于发现工作场所存在的问题和隐患,及时进行整改。
4. 标准化 (Standardize)
标准化是指制定一套标准化的工作流程和规范,使所有员工都按照相同的标准
进行工作。
通过标准化,可以降低出错率,提高质量和效率。
标准化还可以使工作更加标准化、可持续,从而提高整体的生产效率。
5. 节约 (Sustain)
节约是指保持整个5s管理系统的长期有效性和稳定性。
通过建立和执行定期
检查和维护工作,可以确保5s管理制度长期有效地运行。
同时,需要培养员工的
良好习惯和意识,使他们始终保持对整个工作场所的注意和维护。
5s管理的主要内容有哪些

5S管理的主要内容有哪些
1.整理 (Seiri)
–精简和清除工作场所中不必要的物品和工具,只保留必须的项目和材料。
–将所有物品分类并标记清楚,使得每个物品都有固定的位置,方便寻找和管理。
2.整顿 (Seiton)
–将工作场所的物品和设备进行合理的排列组织,确保工作场所井然有序,提高工作效率。
–制定合理的工作流程和标准化操作程序,确保每个工作岗位都能够高效运作。
3.清扫 (Seiso)
–定期清洁工作场所,保持工作环境清洁整洁,减少事故发生的可能性。
–培养员工对清洁和卫生的重视,增强员工对于工作场所环境的责任感。
4.清洁 (Seiketsu)
–建立持续的清洁和卫生制度,保持工作场所始终保持清洁和整洁的状态。
–常态化的清洁检查和保养,确保工作场所环境持续改善和维护。
5.素养 (Shitsuke)
–培养员工遵守5S管理规范的习惯和纪律,使之成为每个员工的工作习惯。
–建立5S管理的长期机制和体系,持续改进和完善5S管理制度,确保其持续有效性和可持续性。
通过以上5个步骤的实施,公司可以建立起高效的管理体系,提高员工对工作
环境的质量和责任感,提升工作效率和生产效益。
5S管理不仅可以改善工作环境,还可以培养员工的良好工作习惯和态度,为公司的可持续发展打下坚实的基础。
简述5s管理内容

简述5s管理内容
5S管理是一种质量管理方法,主要用于提高工作场所的效率和
安全。
5S由日语中的五个词汇开始,它们是:整理(Seiri)、整顿(Seiton)、清扫(Seiso)、清洁(Seiketsu)和纪律(Shitsuke)。
1. 整理(Seiri):这一步是清理工作场所,清除不必要的物品和杂乱的垃圾。
目的是优化工作空间,减少材料浪费,并降低操作成本。
2. 整顿(Seiton):在这一步骤中,关注的是如何有效地管理物品。
将设备、工具和材料归置到特定的地方,以便易于找到和使用。
目的是提高工作效率,减少生产停滞和生产线堵塞。
3. 清扫(Seiso):这一步骤的目的是保持工作场所的清洁。
这不仅包括日常清洁和维护,还包括检查设备和材料的状态并进行修理或更换。
目的是提高生产效率,减少工作地点的安全隐患。
4. 清洁(Seiketsu):这一步骤是为了确保工作场所的清洁度保持在
高水平。
要建立标准操作规程,保持固定的检查周期以及纠正各种问题和缺陷。
目的是使整个工作场所优化,使其变得更加安全、清洁和有序。
5. 纪律(Shitsuke):这一步是为了确保所有的5S活动能够持续实施。
要建立各种规章制度和标准操作过程,以确保所有工作人员都能遵守规定。
目的是使持续改进成为一种固化的行为模式,从而持续提高工作场所的效率和安全性。
总之,通过5S管理,组织可以优化工作环境和流程,提高工作效率和安全性。
这种方法可以用于制造业、服务行业等各种领域,并已被证明是一种非常有效的工作管理方法。
简述5s管理的主要内容

简述5s管理的主要内容5S管理的主要内容:提高效率、改善工作环境、优化流程、保证质量、提升员工素质5S管理是一种以提高效率、改善工作环境、优化流程、保证质量、提升员工素质为目标的管理方法。
它通过整理、整顿、清扫、清洁、素养这五个步骤,来优化组织的工作环境和流程,提高工作效率和质量。
下面将对5S管理的主要内容进行详细介绍。
整理(Seiri)是5S管理的第一个步骤。
它的目标是清理和整理工作场所,去除不必要的物品和杂乱无章的物品。
通过整理,可以减少工作场所的杂乱和拥挤,提高工作效率。
整理的过程中,需要根据物品的使用频率和价值,进行分类和标记,以便于工作人员能够快速找到需要的物品。
整顿(Seiton)是5S管理的第二个步骤。
它的目标是按照一定的规则和标准,对整理后的物品进行摆放和归纳。
通过整顿,可以使工作场所更加有序和美观,方便员工的操作和使用。
整顿的过程中,需要制定相应的标准和规则,确保物品的摆放和归纳符合工作的需要和流程。
第三,清扫(Seiso)是5S管理的第三个步骤。
它的目标是保持工作场所的清洁和整洁。
通过定期的清洁和维护,可以防止杂物和灰尘的积累,减少事故和污染的发生。
清扫的过程中,需要制定相应的清洁计划和清洁标准,确保工作场所的清洁和卫生。
清洁(Seiketsu)是5S管理的第四个步骤。
它的目标是确保工作场所的清洁和整洁。
通过培养良好的卫生习惯和行为规范,可以保持工作场所的清洁和整洁。
清洁的过程中,需要对员工进行培训和教育,提高他们的卫生意识和责任感。
素养(Shitsuke)是5S管理的第五个步骤。
它的目标是培养员工的素质和自律能力。
通过定期的培训和考核,可以提高员工的业务水平和素质,增强他们的责任感和自律能力。
素养的过程中,需要制定相应的培训计划和考核标准,确保员工的素质和能力得到提升。
5S管理的主要内容包括整理、整顿、清扫、清洁、素养这五个步骤。
通过这些步骤,可以优化工作环境和流程,提高工作效率和质量。
5s管理是指哪五项
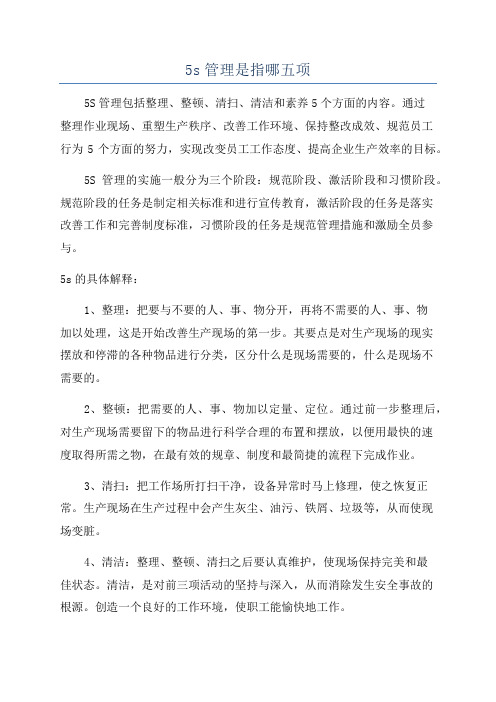
5s管理是指哪五项5S管理包括整理、整顿、清扫、清洁和素养5个方面的内容。
通过整理作业现场、重塑生产秩序、改善工作环境、保持整改成效、规范员工行为5个方面的努力,实现改变员工工作态度、提高企业生产效率的目标。
5S管理的实施一般分为三个阶段:规范阶段、激活阶段和习惯阶段。
规范阶段的任务是制定相关标准和进行宣传教育,激活阶段的任务是落实改善工作和完善制度标准,习惯阶段的任务是规范管理措施和激励全员参与。
5s的具体解释:1、整理:把要与不要的人、事、物分开,再将不需要的人、事、物加以处理,这是开始改善生产现场的第一步。
其要点是对生产现场的现实摆放和停滞的各种物品进行分类,区分什么是现场需要的,什么是现场不需要的。
2、整顿:把需要的人、事、物加以定量、定位。
通过前一步整理后,对生产现场需要留下的物品进行科学合理的布置和摆放,以便用最快的速度取得所需之物,在最有效的规章、制度和最简捷的流程下完成作业。
3、清扫:把工作场所打扫干净,设备异常时马上修理,使之恢复正常。
生产现场在生产过程中会产生灰尘、油污、铁屑、垃圾等,从而使现场变脏。
4、清洁:整理、整顿、清扫之后要认真维护,使现场保持完美和最佳状态。
清洁,是对前三项活动的坚持与深入,从而消除发生安全事故的根源。
创造一个良好的工作环境,使职工能愉快地工作。
5、素养:素养即努力提高人员的修身,养成严格遵守规章制度的习惯和作风,这是“5S”活动的核心。
没有人员素质的提高,各项活动就不能顺利开展,开展了也坚持不了。
所以,抓“5S”活动,要始终着眼于提高人的素质。
5s管理制度的内容有哪些

5S管理制度的内容有哪些1. 简介5S管理制度是一种用于改善工作场所效率和组织能力的管理方法,起源于日本的制造业,被广泛用于世界各个行业。
它强调通过整顿、整理、清扫、清洁和纪律化的方法来创建一个安全、有序、高效、舒适的工作环境。
本文将介绍5S管理制度的具体内容,以便企业了解和实施。
2. 五个S的含义2.1 整顿 (Seiri)整顿意味着清理工作场所,将不必要的物品和杂物移除出工作区域。
目标是减少浪费和混乱,创造一个功能齐全、清晰明了的工作环境。
这可以提高工作效率、缩短工作时间,并帮助员工专注于工作任务。
2.2 整理 (Seiton)整理指的是对工作区域进行布置和组织,以方便员工获取需要的工具、材料和信息。
通过标记工具的位置、使用工具储存设备和实施易于理解的标识系统,可以减少员工的搜索时间,提高生产效率。
2.3 清扫 (Seiso)清扫是指保持工作区域的清洁和卫生。
定期进行清洁工作可以防止灰尘和杂物的积聚,减少事故和质量问题的发生。
清扫还有助于形成员工良好的卫生习惯,并提高员工工作的满意度和舒适度。
2.4 清洁 (Seiketsu)清洁是指确保整个工作环境保持清洁、整洁和有序。
通过实施标准化的清洁程序和周期性的维护工作,可以减少污垢和污染物的积聚,提高工作环境的质量和员工的安全感。
2.5 纪律化 (Shitsuke)纪律化是指建立并遵守5S管理制度的意识和规范。
员工需要接受培训和教育,以了解5S的重要性,并积极参与和贡献。
纪律化还包括定期的5S审核和奖励措施,以激励员工继续遵守制度。
3. 5S管理制度的好处3.1 提高工作效率:通过整顿和整理工作场所,员工可以更快地找到需要的工具和材料,减少等待时间和工作停滞,提高生产效率。
3.2 提高质量:通过清洁和清洁工作区域,可以减少污染和污垢,从而减少生产中的质量问题和瑕疵率。
3.3 降低成本:通过减少浪费、提高工作效率和减少质量问题,可以有效降低生产成本。
- 1、下载文档前请自行甄别文档内容的完整性,平台不提供额外的编辑、内容补充、找答案等附加服务。
- 2、"仅部分预览"的文档,不可在线预览部分如存在完整性等问题,可反馈申请退款(可完整预览的文档不适用该条件!)。
- 3、如文档侵犯您的权益,请联系客服反馈,我们会尽快为您处理(人工客服工作时间:9:00-18:30)。
生产过程 中经常有一些残余物料、待修品、待返品、报废品等滞留在现场,既占据了地 方又阻碍生产,包括一些已无法使用的工夹具、量具、机器设备,如果不及时清除,会 使现场变得凌乱。
生产现场摆放不要的物品是一种浪费: 即使宽敞的工作场所,将俞变窄小。 棚架、橱柜等被杂物占据而减少 使用价值 。 增加了寻找工具、零件等物品的困难,浪费时间。
5S现场管理法:素养通过晨会等手段,提高全员文明礼貌水准。培养每位成员养成良好的习惯,并遵守规则 做事。开展5S容易,但长时间的维持必须靠素养的提升。
o稳定品质
o减少工业伤害
责任化、 制度化 。
实施要领:
建立清扫责任区(室内、外)执行例行扫除,清理脏污 调查污染源,予以杜绝或隔离 建立清扫基准,作为规范
5S
将上面的3S实施的做法制度化、规范化,并贯彻执行及维持结果。 目的:
维持上面3S的成果
制度化,定期检查。
实施要领:
落实前面3S工作
制订考评方法 制订奖惩制度,加强执行 高阶主管经常带头巡查,以表重视
1955年,日本的5S的宣传口号为 “安全始于整理,终于整理整顿 ”。当时只推行了前两
个S,其目的仅为了确保作业空间和安全。后因生产和品质 控制的需要而又逐步提出了3S,
也就是清扫、清洁、修养,从而使应用空间及适用范围进一步拓展,到了1986年,日本的5S的著作逐渐问世,从而对整个现场管理模式起到了冲击的作用,并由此掀起了5S的热潮。
5S
应用于 制造业 、服务业 等改善现场环境的质量和员工的 思维方法 ,使企业能有效地迈向 全面质量管理 ,主要是针对 制造业 在生产现场,对材料、设备、人 员等 生产要素 开展相应 活动。
5S对于塑造 企业 的形象、降低成本、准时交货、 安全生产 、高度的标准化、创造令人 心旷神怡的工作场所、现场改善等方面发挥了巨 大作用,是日本产品品质得以迅猛提高行 销全球的成功之处。
o现物的表示和放置场所的表示
o某些表示方法全公司要统一
o在表示方法上多下工夫
整顿的"3定"原则:定点、定容、定量
o定点:放在哪里合适(具备必要的存放条件,方便取用、还原放置的一个或 若干个固定的区域)
o定容:用什么容器、颜色(可以是不同意义上的容器、器皿类的物件,如: 筐、桶、箱篓等,也可以是车、特殊存放平台甚至是一个固定的存储空间等均 可当作容器看待)
推行
1、提高 企业形象
2、提高 生产效率
3、提高 库存周转率
4、减少故障,保障品质
5、加强安全,减少安全隐患
6、养成节约的习惯,降低 生产成本
7、缩短作业周期,保证交期
8、改善 企业精神 面貌,形成良好 企业文化
5S
5S起源于日本,通过规范现场、现物,营造一目了然的 工作环境 ,培养员工良好的工作习 惯,是日式企业独特的一种 管理方法 ,其最终目的是提升人的品质:
o定量:规定合适的数量(对存储的物件在量上规定上下限,或直接定量,方 便将其推广为容器类的看板使用,一举两得)
常用方法:
引线法 形迹法 标识法 固定容器法 红牌作战法 定置管理法 颜色管理法 看板管理法
5S
o将工作场所清扫干净。
o保持工作场所干净、亮丽的环境。 目的:
o消除赃污,保持职场内干干净净、明明亮亮
根据企业进一步发展的需要,有的企业在原来5S的基础上又增加了安全(Safety),即形成了“6S;"有的企业再增加了节约(Save),形成了 “7S";也有的企业加上习惯化(Shiukanka)、服务(Service)及坚持(Shikoku),形成了“10S",有的企业甚至推行 “12S",但是万变不离其宗,都是从“5S里"衍生出来的, 例如在整理中要求清除无用的东西或物品, 这在某些意义上来说, 就能涉及到节约和安全, 具体一点例如横在安全通道中无用的垃圾, 这就是安全应该关注的 内容。
革除马虎之心,养成凡事认真的习惯 (认认真真地对待工作中的每一件"小事") 遵守规定的习惯
自觉维护工作环境整洁明了的良好习要的与不必要的:
o把必要的东西与不必要的东西明确地、严格地区分开来;
o不必要的东西要尽快处理掉。
目的:
腾出空间,空间活用
防止误用、误送
物品杂乱无章的摆放,增加 盘点 的困难, 成本核算 失准。
要有决心,不必要的物品应断然地加以处置。
实施要领 :
自己的工作场所(范围)全面检查,包括看得到和看不到的 制定「要」和「不要」的判别基准 将不要物品清除出工作场所 对需要的物品调查使用频度,决定日常用量及放置位置 制订废弃物处理方法
每日自我检查
流程布置,确定放置场所 规定放置方法、明确数量
划线定位
场所、物品标识
整顿的"3要素":场所、方法、标识
放置场所
o物品的放置场所原则上要100%设定
o物品的保管要 定点、定容、定量
o生产线附近只能放真正需要的物品 放置方法
o易取
o不超出所规定的范围
o在放置方法上多下工夫 标识方法
o放置场所和物品原则上一对一表示
常用的方法 :
使用频率法
价值分析法
定点拍照法
红牌作战法 看板管理法 等等
5S现场管理法:整顿对整理之后留在现场的必要的物品分门别类放置,排列整齐。 明确数量,并进行有效地标识。
目的: 工作场所一目了然 整整齐齐的 工作环境 消除找寻物品的时间 消除过多的积压物品
这是提高效率的基础。
实施要领 :
前一步骤整理的工作要落实
5S的发展
日本式企业将5S运动作为管理工作的基础,推行各种品质的管理手法,第二次世界大 战后, 产品品质得以迅速地提升, 奠定了经济大国的地位, 而在丰田公司 的倡导推行下,5S对于塑造 企业的形象、降低 成本 、准时交货、 安全生产 、高度的标准化、创造令人心旷神怡 的工作场所、 现场改善 等方面发挥了巨大作用, 逐渐被各国的管理界所认识。 随着世界经济 的发展,5S已经成为 工厂管理 的一股新潮流。
什么是
5S:整理(SEIRI)、整顿(SEITON)、清扫(SEISO)、清洁(SEIKETSU)、素养SHITSUKE),又被称为 “五常法则 ”或 “五常法 ”。
5S
5S的沿革
5S起源于日本,是指在生产现场中对人员、机器、材料、方法等 生产要素 进行有效的 管理 ,这是日本企业独特的一种管理办法。