多合一电驱动系统的结构原理及CAE仿真分析
电气系统仿真的原理与方法
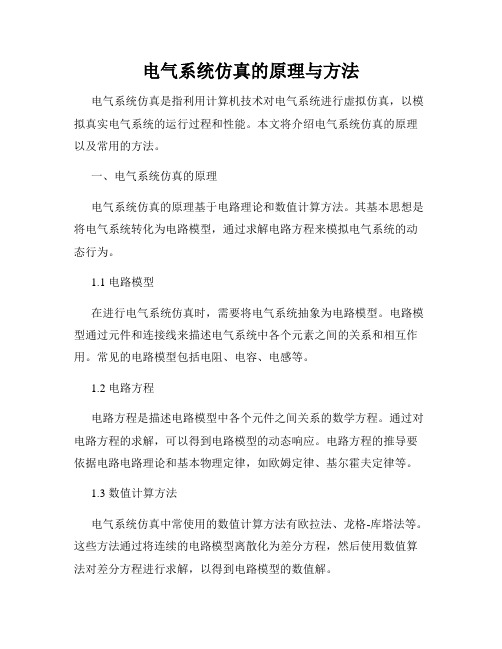
电气系统仿真的原理与方法电气系统仿真是指利用计算机技术对电气系统进行虚拟仿真,以模拟真实电气系统的运行过程和性能。
本文将介绍电气系统仿真的原理以及常用的方法。
一、电气系统仿真的原理电气系统仿真的原理基于电路理论和数值计算方法。
其基本思想是将电气系统转化为电路模型,通过求解电路方程来模拟电气系统的动态行为。
1.1 电路模型在进行电气系统仿真时,需要将电气系统抽象为电路模型。
电路模型通过元件和连接线来描述电气系统中各个元素之间的关系和相互作用。
常见的电路模型包括电阻、电容、电感等。
1.2 电路方程电路方程是描述电路模型中各个元件之间关系的数学方程。
通过对电路方程的求解,可以得到电路模型的动态响应。
电路方程的推导要依据电路电路理论和基本物理定律,如欧姆定律、基尔霍夫定律等。
1.3 数值计算方法电气系统仿真中常使用的数值计算方法有欧拉法、龙格-库塔法等。
这些方法通过将连续的电路模型离散化为差分方程,然后使用数值算法对差分方程进行求解,以得到电路模型的数值解。
二、电气系统仿真的方法电气系统仿真的方法有多种,根据需要选择适合的方法进行仿真。
2.1 时域仿真时域仿真是指对电气系统进行时间上的仿真。
它基于电路方程和数值计算方法,通过在一定时间范围内对电路方程进行求解,获得电路在不同时刻的电压、电流等参数。
时域仿真可以用于分析电路的时序响应,判断系统的稳定性和动态特性。
2.2 频域仿真频域仿真是指对电气系统进行频率上的仿真。
它基于电路的频域特性,通过傅里叶变换将电路方程从时域转换到频域,得到电路的幅频特性和相频特性。
频域仿真主要用于研究电路的频率响应和滤波器设计。
2.3 优化仿真优化仿真是指通过对电气系统进行多次仿真,利用优化算法寻找最优的系统配置或参数设置。
优化仿真可以应用于电气系统的设计、调试和性能优化。
2.4 参数敏感度仿真参数敏感度仿真是指通过对电气系统进行多次仿真,分析系统输出对输入参数的敏感度。
参数敏感度仿真可以用于评估不同参数变化对系统性能的影响,帮助优化系统性能。
多体系统的动力学分析与碰撞仿真
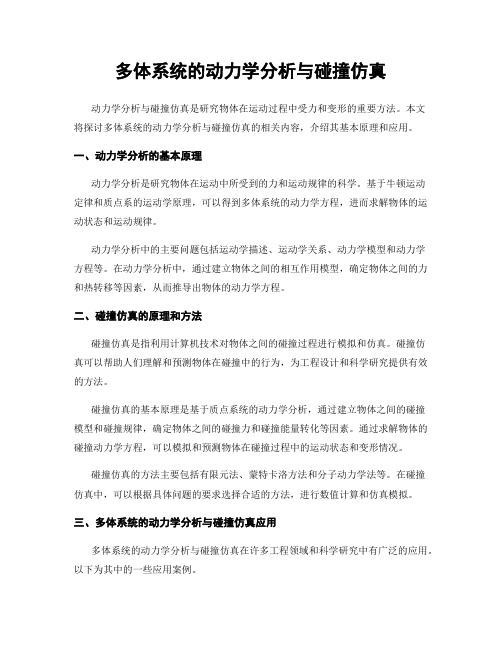
多体系统的动力学分析与碰撞仿真动力学分析与碰撞仿真是研究物体在运动过程中受力和变形的重要方法。
本文将探讨多体系统的动力学分析与碰撞仿真的相关内容,介绍其基本原理和应用。
一、动力学分析的基本原理动力学分析是研究物体在运动中所受到的力和运动规律的科学。
基于牛顿运动定律和质点系的运动学原理,可以得到多体系统的动力学方程,进而求解物体的运动状态和运动规律。
动力学分析中的主要问题包括运动学描述、运动学关系、动力学模型和动力学方程等。
在动力学分析中,通过建立物体之间的相互作用模型,确定物体之间的力和热转移等因素,从而推导出物体的动力学方程。
二、碰撞仿真的原理和方法碰撞仿真是指利用计算机技术对物体之间的碰撞过程进行模拟和仿真。
碰撞仿真可以帮助人们理解和预测物体在碰撞中的行为,为工程设计和科学研究提供有效的方法。
碰撞仿真的基本原理是基于质点系统的动力学分析,通过建立物体之间的碰撞模型和碰撞规律,确定物体之间的碰撞力和碰撞能量转化等因素。
通过求解物体的碰撞动力学方程,可以模拟和预测物体在碰撞过程中的运动状态和变形情况。
碰撞仿真的方法主要包括有限元法、蒙特卡洛方法和分子动力学法等。
在碰撞仿真中,可以根据具体问题的要求选择合适的方法,进行数值计算和仿真模拟。
三、多体系统的动力学分析与碰撞仿真应用多体系统的动力学分析与碰撞仿真在许多工程领域和科学研究中有广泛的应用。
以下为其中的一些应用案例。
1. 交通工程中的车辆碰撞分析:对于交通事故的调查和分析,可以利用动力学分析与碰撞仿真的方法研究车辆之间的碰撞过程,分析事故原因和责任。
通过模拟和比较不同碰撞方案,可以提出相应的交通安全措施。
2. 工程结构的研究与设计:在建筑和桥梁等工程结构的设计中,动力学分析与碰撞仿真可以帮助工程师评估和预测结构在自然灾害或外部冲击下的响应和破坏情况。
通过模拟和仿真,可以优化结构设计,提高抗震和安全性能。
3. 航天器的着陆和返回模拟:在航天工程中,多体系统的动力学分析和碰撞仿真可以帮助研究员模拟和预测航天器在着陆和返回过程中的运动状态和变形情况。
混合动力电动汽车的动力系统设计与仿真
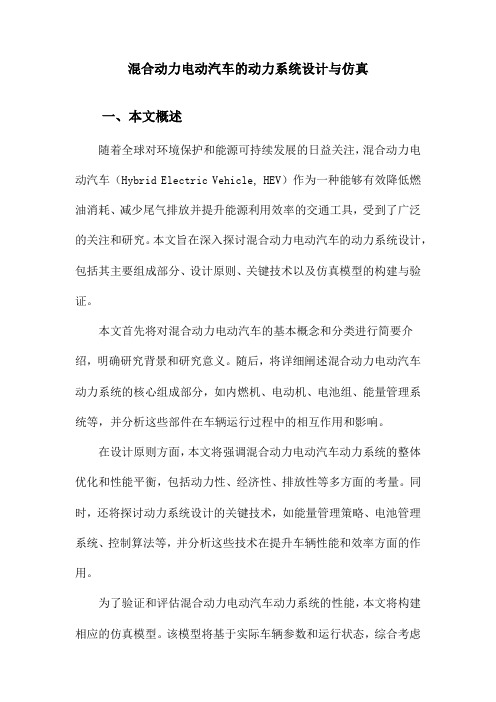
混合动力电动汽车的动力系统设计与仿真一、本文概述随着全球对环境保护和能源可持续发展的日益关注,混合动力电动汽车(Hybrid Electric Vehicle, HEV)作为一种能够有效降低燃油消耗、减少尾气排放并提升能源利用效率的交通工具,受到了广泛的关注和研究。
本文旨在深入探讨混合动力电动汽车的动力系统设计,包括其主要组成部分、设计原则、关键技术以及仿真模型的构建与验证。
本文首先将对混合动力电动汽车的基本概念和分类进行简要介绍,明确研究背景和研究意义。
随后,将详细阐述混合动力电动汽车动力系统的核心组成部分,如内燃机、电动机、电池组、能量管理系统等,并分析这些部件在车辆运行过程中的相互作用和影响。
在设计原则方面,本文将强调混合动力电动汽车动力系统的整体优化和性能平衡,包括动力性、经济性、排放性等多方面的考量。
同时,还将探讨动力系统设计的关键技术,如能量管理策略、电池管理系统、控制算法等,并分析这些技术在提升车辆性能和效率方面的作用。
为了验证和评估混合动力电动汽车动力系统的性能,本文将构建相应的仿真模型。
该模型将基于实际车辆参数和运行状态,综合考虑各种外部因素,如道路条件、驾驶员行为、环境温度等。
通过仿真模型的运行和分析,可以预测车辆在不同场景下的性能表现,并为后续的优化和改进提供依据。
本文将总结混合动力电动汽车动力系统设计的挑战和趋势,展望未来的发展方向和应用前景。
通过本文的研究,旨在为混合动力电动汽车的设计和开发提供有益的参考和启示。
二、混合动力电动汽车概述混合动力电动汽车(Hybrid Electric Vehicles, HEVs)是一种结合了传统内燃机车辆和纯电动车辆优点的汽车类型。
它们通常配备有内燃机和一个或多个电动机,能够根据行驶条件自动或手动地在不同的动力源之间切换。
本节将概述混合动力电动汽车的基本概念、分类、工作原理以及其在现代交通系统中的重要性。
混合动力电动汽车结合了内燃机车辆和纯电动车辆的特点,旨在提高燃油效率和减少排放。
CAE结构仿真分析及技术培训

CAE结构仿真分析及技术培训CAE(计算机辅助工程)结构仿真分析是一种通过计算机模拟和计算来预测和评估结构行为的技术。
随着计算机技术的不断进步和发展,CAE结构仿真分析在工程领域中得到了广泛的应用。
它能够帮助工程师快速准确地评估和优化产品设计、优化材料和工艺选用,提高产品的性能和质量,缩短产品研发周期和开发成本。
CAE结构仿真分析主要包括有限元分析(FEA)、计算流体力学分析(CFD)、多体系统动力学分析(MBD)等。
其中,有限元分析是最常用的一种技术,它通过将结构离散为有限数量的有限元单元来近似连续结构,利用数学方程求解方法对结构进行模拟和计算。
有限元分析可以用来预测结构的强度、刚度、振动响应、疲劳寿命等性能,帮助设计师评估和改善产品设计。
CAE结构仿真分析的优势在于可以全面、详细地观察和分析结构的应力、应变、变形等行为,比传统的试验方法更加灵活、高效、经济。
同时,CAE还可以进行多种不同工况的模拟和比较分析,帮助设计师进行全面的优化,提供更合理的设计方案。
对于工程师来说,掌握和运用CAE结构仿真分析技术是非常重要的。
因此,进行CAE结构仿真分析技术培训是必要的。
在培训中,首先需要学习计算力学、结构力学的基础知识,了解有限元分析的基本原理和方法。
然后,学习和熟悉常用的CAE软件,掌握软件的使用和操作技巧。
在培训中最好能有一些实际案例和工程应用,通过实践来提高学员的能力和技巧。
在CAE结构仿真分析技术培训中,可以设置以下几个主要内容:1.理论知识教学:包括计算力学、结构力学的基本原理和方程,有限元分析的基本概念和方法等。
2.软件操作培训:介绍常用的CAE软件,如ANSYS、ABAQUS等,讲解软件的功能和特点,讲解软件的界面和操作方法,以及如何建立结构模型、设置边界条件、求解和分析结果等。
3.实例分析:通过一些实际工程案例的仿真分析,让学员了解和熟悉实际工程中的问题和解决方法,通过实践来提高分析能力和技巧。
内部培训-动力电池系统CAE分析培训系列之二-建模

二、质量要求
2.2 网格要求
• Detail Guideline (for crash & Stiffness, NVH) – Hole
Method A Method B Method C
一、建模方法
1.11后处理
实例演示输出动画,图片,查找结果等。
在此处将实例简单演示处理过程。
建模方法 质量要求 电池特点
二、质量要求
1. 质量要求
一般要求三角形单元不超过5% 。
#
Criterion
Ideal
0
Penalty va;ie
0.00
1
Min sizeห้องสมุดไป่ตู้
10.000
2
Max length
151.667
20.000 150.000
6.250 70.000 0.300 2.000 12.222
二、质量要求
2. 单位制 单位制一般默认T, mm, s
默认:tonne,mm,s, N, MPa单位系统,这个单位系统是最常用,还不易出错(吨,mm 和s) 备注:长度:m;力:N;质量:kg;时间: s;应力:Pa;密度:kg/m3 长度:mm;力:N;质量:吨; 时间: s;应力:MPa;密度:吨/m m 3
2.2 网格要求
• Detail Guideline (for crash & Stiffness, NVH) – Bead
<Round Bead>
Make mesh according to the CAD geometry
<Square Bead> Keep the minimum mesh size.
在此处将实例简单演示处理过程。
电动汽车设计中的CAE仿真技术应用
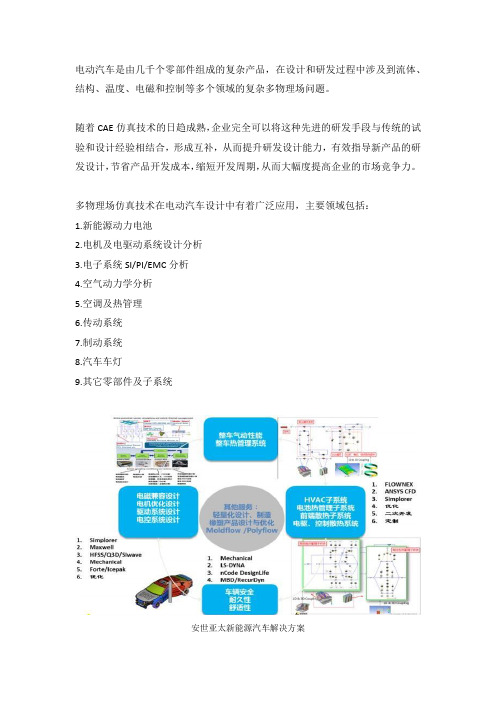
电动汽车是由几千个零部件组成的复杂产品,在设计和研发过程中涉及到流体、结构、温度、电磁和控制等多个领域的复杂多物理场问题。
随着CAE仿真技术的日趋成熟,企业完全可以将这种先进的研发手段与传统的试验和设计经验相结合,形成互补,从而提升研发设计能力,有效指导新产品的研发设计,节省产品开发成本,缩短开发周期,从而大幅度提高企业的市场竞争力。
多物理场仿真技术在电动汽车设计中有着广泛应用,主要领域包括:1.新能源动力电池2.电机及电驱动系统设计分析3.电子系统SI/PI/EMC分析4.空气动力学分析5.空调及热管理6.传动系统7.制动系统8.汽车车灯9.其它零部件及子系统安世亚太新能源汽车解决方案1.新能源动力电池新能源动力电池是新能源汽车的三大核心技术之一。
CFD数值模拟方法可以在电芯的电化学过程模拟、电池单体的发热特性模拟、电池组及电池包的热设计、PEMFC和SOFC燃料电池的研发等领域中发挥重要的作用。
电芯放电过程中瞬态电极锂离子浓度分布串联电芯在固定倍率放电时的瞬态温度结果电池包散热分析结果:电池单体表面的对流换热系数分布PEMFC燃料电池的仿真分析结果:表面温度及H2浓度分布云图作为电动汽车能量供给的关键设备,电池包的结构设计应尽可能高效和轻便,并在保证存放空间合理布局的基础上,满足多变运行环境和行驶工况下的机械承受、工作安全性、可靠性及使用寿命要求。
利用ANSYS Mechanical及LS DYNA可以对电池包的安全性和耐久性做充分验证。
电池包振动分析2.电机及电驱动系统设计分析电机设计是一个复杂的多物理场问题,它涉及到电磁、结构、流体、温度和控制等多个领域。
ANSYS提供集成化设计解决方案和流程,主要包括:电机快速设计和方案优选;电机电磁场有限元精确优化设计;电驱动系统集成化设计;电机电磁、热耦合分析;电机电磁、控制、振动、噪声耦合分析。
ANSYS无缝集成的电机设计多物理场解决方案电机的电磁、流体、热耦合分析基于Maxwell的电机齿槽转矩、气隙磁密、磁钢大小多目标组合优化Toolkit可一键输出的效率Map图电机电磁-振动-噪音分析3.电子系统SI/PI/EMC分析ANSYS电机设计解决方案可解决电驱动系统电磁兼容设计问题,包括:部件级、设备级和系统级的电磁干扰和电磁兼容设计问题。
混合动力汽车动力系统设计与仿真
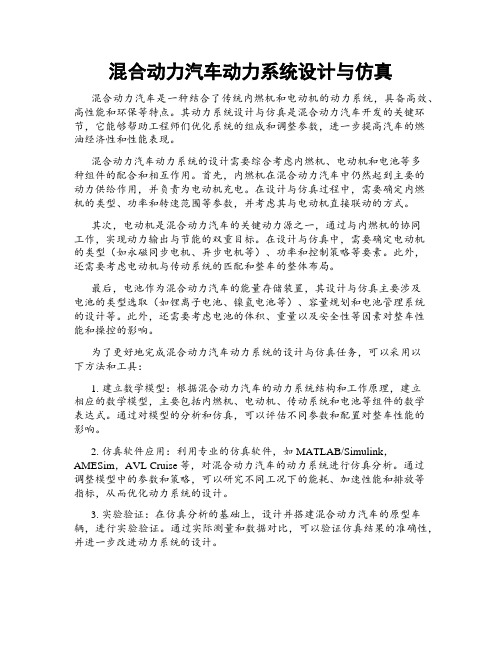
混合动力汽车动力系统设计与仿真混合动力汽车是一种结合了传统内燃机和电动机的动力系统,具备高效、高性能和环保等特点。
其动力系统设计与仿真是混合动力汽车开发的关键环节,它能够帮助工程师们优化系统的组成和调整参数,进一步提高汽车的燃油经济性和性能表现。
混合动力汽车动力系统的设计需要综合考虑内燃机、电动机和电池等多种组件的配合和相互作用。
首先,内燃机在混合动力汽车中仍然起到主要的动力供给作用,并负责为电动机充电。
在设计与仿真过程中,需要确定内燃机的类型、功率和转速范围等参数,并考虑其与电动机直接联动的方式。
其次,电动机是混合动力汽车的关键动力源之一,通过与内燃机的协同工作,实现动力输出与节能的双重目标。
在设计与仿真中,需要确定电动机的类型(如永磁同步电机、异步电机等)、功率和控制策略等要素。
此外,还需要考虑电动机与传动系统的匹配和整车的整体布局。
最后,电池作为混合动力汽车的能量存储装置,其设计与仿真主要涉及电池的类型选取(如锂离子电池、镍氢电池等)、容量规划和电池管理系统的设计等。
此外,还需要考虑电池的体积、重量以及安全性等因素对整车性能和操控的影响。
为了更好地完成混合动力汽车动力系统的设计与仿真任务,可以采用以下方法和工具:1. 建立数学模型:根据混合动力汽车的动力系统结构和工作原理,建立相应的数学模型,主要包括内燃机、电动机、传动系统和电池等组件的数学表达式。
通过对模型的分析和仿真,可以评估不同参数和配置对整车性能的影响。
2. 仿真软件应用:利用专业的仿真软件,如MATLAB/Simulink,AMESim,AVL Cruise等,对混合动力汽车的动力系统进行仿真分析。
通过调整模型中的参数和策略,可以研究不同工况下的能耗、加速性能和排放等指标,从而优化动力系统的设计。
3. 实验验证:在仿真分析的基础上,设计并搭建混合动力汽车的原型车辆,进行实验验证。
通过实际测量和数据对比,可以验证仿真结果的准确性,并进一步改进动力系统的设计。
详解CAE基本结构与功能
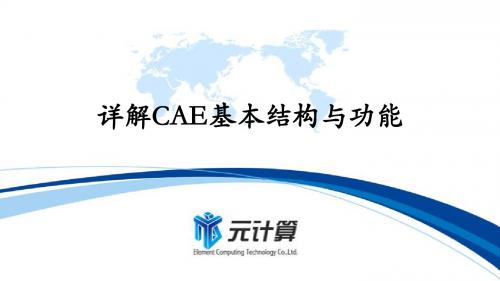
后处理:根据工程或产品模型与设计要求,对有限元分析结果进行用户所要 求的加工、检查,并以图形方式提供给用户,辅助用户判定计算结果与设计方案 的合理性。
二:CAE软件的结构与功能 其中包含以下模块: 前处理模块---给实体建模与参数化建模,构件的布尔运算,单元自动剖分,节点自动编 号与节点参数自动生成,载荷与材料参数直接输入有公式参数化导入,节点载荷自动生成, 有限元模型信息自动生成等。 有限元分析模块---有限单元库,材料库及相关算法,约束处理算法,有限元系统组装模 块,静力、动力、振动、线性与非线性解法库。大型通用题的物理、力学和数学特征,分解 成若干个子问题,由不同的有限元分析子系统完成。一般有如下子系统:线性静力分析子系 统、动力分析子系统、振动模态分析子系统、热分析子系统等。 后处理模块---有限元分析结果的数据平滑,各种物理量的加工与显示,针对工程或产品 设计要求的数据检验与工程规范校核,设计优化与模型修改等。
用户界面模块、数据管理系统与数据库、专家系统、知识库。 CAE软件对工程和产品的分析、模拟能力,主要决定于单元库和材料库的丰富和完善程度, 单元库所包含的单元类型越多,材料库所包括的材料特性种类越全,其CAE软件对工程或产品 的分析、仿真能力越强。 一个CAE软件的计算效率和计算结果的精度,主要决定于解法库。先进高效的求解算法与 常规的求解算法,在计算效率上可能有几倍、几十倍,甚至几百倍的差异。 前后处理是近十多年发展最快的CAE软件成分,它们是CAE软件满足用户需求,使通用软 件专业化、属地化,并实现CAD、CAM、CAPP、PDM等软件无缝集成的关键性软件成分。它们 是通过增设CAD软件,的接口数据模块,实现了CAD/CAE的有效集成。 CAE通常指有限元分析和机构的运动学及动力学分析。有限元分析可完成力学分析(线性、 非线性、静态、动态);场分析(热场、电场、磁场等);频率响应和结构优化等。机构分析能完成 机构内零部件的位移、速度、加速度和力的计算,机构的运动模拟及机构参数的优化。
机电一体化系统多能量域集成产品建模与仿真技术分析

机电一体化系统多能量域集成产品建模与仿真技术分析作者:查娜李国华来源:《科技资讯》 2015年第5期查娜李国华(镇江高等职业技术学校江苏镇江 212003)摘要:我国机电一体化研究项目层出不穷,包括飞机、汽车工具等都与集成网络并行、协同制造,其中必要的建模问题开始引起国际CAD领域严密关注。
因此,该文主要透过系统角度研究,全程配合工程类别之间的相似特征,延展出端口结构中多能量域集成组件模型,同步供应形式化描述,在此基础上涉及机电一体化系统多能量产品建模仿真框架形态清晰,确保能够更加方便地支撑系统不同空间演练进程。
关键词:机电一体化异地设计集成组件虚拟形态建模方式中图分类号:TP391文献标识码:A文章编号:1672-3791(2015)02(b)-0225-01①作者简介:查娜(1982-),女,江苏丹阳人。
镇江高等职业技术学校,教师,本科,研究方向为电工方向。
1 机电一体化系统多能量集成体系形态观察机电一体化系统主要配合机电装置、电子设备以及信息处理程序进行协调搭配的柔性自动化产品格式,我们不能单纯地判定其为零件叠加形成的积木结构,反而应该贯彻系统化认知观念。
结合工程相似性特征分析,如果工程现场及时引进广义形式的电压、电流、动能函数、损耗函数等,就可以依照力学系统运动学方程以及电网中的基尔霍夫定律实施建模,特别是设计中期有必要结合组建模型关系,透过计算机辅助自动生成机电一体化多能量域集成系统格式。
当然,为了快速实现被控对象的快速、精准调试目标,必须建设动态模型与验证方程。
实际上机电一体化系统组件繁多,尤其在能量观点下,组件包括能源、能量储存、能量变换以及调节等各种样式,如果其间建设单位部件动力学模型以及能量余之间耦合模型,使得系统内部组件高效衔接并将当下正确连结关系阐述完全,就可以确定该类系统的动力学方程内容。
有关基本理性组件,包括机械系统内部质量、弹簧等形式较为复杂,需要现场技术人员应用行为模型进行装配模型附加改造,并在生成原型中提炼更加精准的仿真、测试要诀。
1 CAE技术原理及模拟仿真.ppt
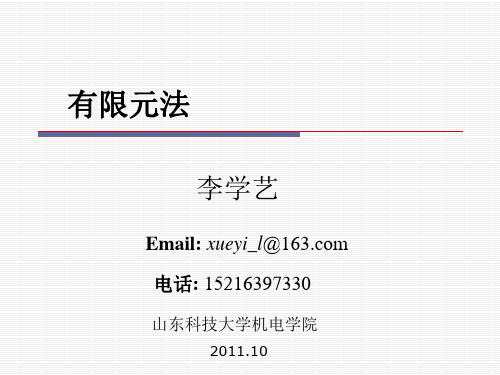
12
CAE发展历史
特别优异,具有强大的模型级材料模块和宽广的特性分析范围。 1986年ADINA公司成立,开发的ADINA除广泛应用到各
行业之外,还能真正实现流场、结构和热力学的耦合分析,被 业内人士认为是有限元发展方向的代表。
1987年LSTC开发出LS-DYNA,具有强大的显式动力学分 析功能,能模拟仿真工程中的接触、碰撞和爆炸等真实结构行 为。
20世纪90年代是CAE技术的成熟壮大时期。主要发展是 将CAE与CAD和CAM软件集成为CAD/CAE/CAM系统,从而形 成一个完整、方便的实用产品。CAD技术经过三十年的发展, 经历了从线框技术到曲面技术,再到参数化技术,直至目前的变 量化技术,为CAE技术的推广应用打下了坚实的基础。这期间 各CAD软件开发商一方面大力发展自身CAD软件的功能,另一 方面通过扩展CAE功能或并购CAE软件来增加其软件CAE功能 ,如著名的CAD软件CATIA、UG、Pro/E都增加了基本的CAE
7
CAE技术基本概念
3. CAE技术在机械领域中的应用
(1) 运用有限元和模态分析等方法对机械产品的结构进 行强度分析、振动分析和热分析,并运用结构强度与寿命评 估的理论、方法和规范,对结构的安全性、可靠性以及使用 寿命做出评价与估计;
(2) 运用过程优化设计方法在满足设计、工艺等约束条 件下,对产品结构性能及工艺过程达到最优;
1970年Swanson成立Swanson Analysis System Inc. (SASI)后来重组后改为ANSYS公司,开发ANSYS软件。
11
CAE发展历史
至此世界上三大致力于有限元分析的著名CAE软件公司相继成 立。
CAE仿真与分析PPT课件

热-结构耦合场应力分析 发动机内场
第21页/共39页
被动安全性CMVDR294
第22页/共39页
被动安全性 CMVDR294
初始车速50km/h
第23页/共39页
车速变化
被动安全性 CMVDR294
A柱变形
Байду номын сангаас
第24页/共39页
门框变形量
被动安全性仿真
第25页/共39页
被动安全性
车门静挤压强度
第4页/共39页
CAE技术在汽车设计过程中应用
• 分析和设计紧密结合、设计和分析同步 • 向大规模集成方向发展 • 大幅度提高分析能力 • 基于显式分析的高度非线性求解为工艺分析提供可
能 • 整车安全性分析用于实际汽车安全性设计 • 计算机图形化显示水平不断提高 • 软件提供二次开发语言用于开发满足客户需求的软
第34页/共39页
动力学、运动学分析
在分析过程中往往会涉及到大量的参数,例如弹性铰链的特 性,弹簧的刚度,关键点的位置等等。这些数据有的可以从数学 模型中得出,有的需要做相关试验测量。
第35页/共39页
动力学、运动学分析
某变速器操纵机构运动分析
第36页/共39页
动力学、运动学分析
车门玻璃升降分析
第32页/共39页
动力学、运动学分析
车轮定位参数和悬架杆系的布置直接影响到整车的操纵稳定性,因此合理的车 轮定位参数变化值及变化趋势对整车行驶性能尤为重要。
第33页/共39页
动力学、运动学分析
在底盘设计过程中,一般情况下会涉及到大量的运动 部件,这些部件相互间的关系,往往会影响车轮定位参数变 化趋势,更进一步影响到悬架及整车的性能。
汽车设计过程中的CAE
混合动力机车的控制系统设计与仿真分析

混合动力机车的控制系统设计与仿真分析混合动力机车(Hybrid Electric Locomotive,HEM)是一种结合了内燃机动力和电力动力的机车系统。
该系统通过利用内燃机驱动发电机产生电能,再通过电动发动机驱动机车,实现了能源的高效利用和环境的低污染。
在混合动力机车中,控制系统的设计和仿真分析是确保机车正常运行的关键因素之一。
本文将探讨混合动力机车控制系统的设计与仿真分析。
1. 混合动力机车控制系统的组成混合动力机车的控制系统主要由以下几个部分组成:1.1 能量储存与转换单元:包括电池组、超级电容器和储能电压调节器。
能量储存与转换单元负责储存能量,并将电能转换为机械能以驱动机车。
1.2 内燃机发电机组:将燃料的化学能转化为电能,供给电动发动机使用。
1.3 电动发动机:通过电能驱动机车行驶,同时可以将制动过程中的机械能转化为电能储存。
1.4 控制单元:包括主控制器、传感器和执行器。
控制单元负责感知机车的状态、控制各个部件的工作,并保证机车的安全运行。
2. 混合动力机车的控制系统设计混合动力机车的控制系统设计需要考虑以下几个因素:2.1 系统控制策略:混合动力机车可以采用不同的控制策略,如能量管理策略、功率分配策略等。
在设计控制系统时,需要根据机车的运行条件和要求选取合适的控制策略,并进行仿真分析。
2.2 控制参数优化:控制系统的设计过程中,需要对控制参数进行优化,以提高机车的效率和性能。
优化的控制参数包括电池容量、发电机转速和发电机功率等。
2.3 状态监测与故障诊断:控制系统还需要具备状态监测和故障诊断的功能,能够实时监测机车各个部件的状态,并及时诊断出故障。
这对于及时维修和保证机车的安全运行非常重要。
3. 混合动力机车控制系统的仿真分析仿真分析是混合动力机车控制系统设计的重要步骤。
通过仿真,可以评估控制系统的性能、优化参数,并提前发现系统存在的问题。
3.1 动力总成仿真:动力总成是混合动力机车的核心部分,仿真分析可以模拟机车不同工况下的运行情况。
动力电池箱体的CAE仿真介绍

动力电池箱体的CAE仿真介绍————————————————————————————————作者:————————————————————————————————日期:动力电池箱体的CAE仿真介绍∙2018-03-20 09:37∙来源:电动汽车资源网129Lab129Lab摘要:CAE软件的主体是有限元分析软件,有限元方法的基本思路是把结构离散化,用有限个容易分析的单元表示复杂对象,单元之间通过有限个节点相互连接,根据变形协调条件综合求解。
电动汽车资源网讯:【电动汽车资源网EV江湖129Lab】这里介绍一下关于CAE在电池箱结构方面的应用,偏重于阐述一些基本介绍,没有图片,请耐心观看或跳过。
**************************************分割线****************************************CAE软件的主体是有限元分析(Finite Element Analysis)软件,有限元方法的基本思路是把结构离散化,用有限个容易分析的单元表示复杂对象,单元之间通过有限个节点相互连接,根据变形协调条件综合求解。
由于单元数目是有限的,节点数量也是有限的,所以称为有限元法。
该方法灵活性较大,改变单元的数量可以使解得精确度改变,得到与真实情况无限接近的解。
有人估算过CAE各阶段花费的时间:模型的建立和数据输入在~45%左右,结果分析和评定大约50%左右,而真正的计算时间大约占据5%左右。
采用CAD工具建立CAE的几何模型和物理模型,完成分析数据的输入,称之为CAE前处理。
前处理模块主要用于给实体建模以及参数化建模,构建的布尔运算、单元自动剖分、节点编号与节点参数生成、载荷与材料参数直接输入有公式参数化导入、节点载荷自动生成、模型信息自动生成等。
之后就是有限元分析,对有限元模型进行单元特性分析、有限元单元组装、有限元系统求解和有限元结果生成。
有限元分析模块包含有限元库,材料库和相关算法,约束处理算法,有限元系统组装模块,静力、动力、振动、线性和非线性解法库。
新能源汽车驱动系统优化设计与仿真分析

新能源汽车驱动系统优化设计与仿真分析随着环境保护意识的提高和能源危机的日益严重,新能源汽车逐渐成为了汽车行业的发展趋势。
而作为新能源汽车的核心技术之一,驱动系统的优化设计与仿真分析对于新能源汽车的性能提升和能源利用效率至关重要。
本文将就新能源汽车驱动系统的优化设计与仿真分析展开探讨。
首先,针对新能源汽车驱动系统的优化设计进行分析。
新能源汽车的驱动系统主要包括电机、电控系统、能量管理系统和传动系统等部分。
在优化设计过程中,首先需要对驱动系统的整体架构进行优化。
通过对不同部分进行合理的分工,使得驱动系统的各个部分能够相互协调工作,提高整体性能。
其次,在电机的优化设计中,需要考虑电机的转速范围、功率输出以及能源利用效率等因素。
通过选用合适的电机结构、控制方式以及材料,提高电机的效率和输出功率,从而提高整车的动力性能。
最后,在能量管理系统的优化设计中,需要综合考虑电池的充放电特性、电流波动和发热等因素,通过合理的电池管理策略,延长电池的使用寿命,并提高电池的充放电效率。
其次,针对新能源汽车驱动系统的仿真分析进行讨论。
仿真分析是新能源汽车驱动系统优化设计不可或缺的一部分。
通过建立合适的数学模型,并结合实际驱动数据进行仿真模拟,可以对驱动系统的性能进行全面评估。
首先,可以通过仿真分析来评估驱动系统的动力性能。
例如,可以模拟不同驱动条件下的加速性能、续航里程等指标,并与实际测试数据进行对比,从而验证设计方案的有效性。
其次,可以通过仿真分析来评估驱动系统的能量利用效率。
例如,可以模拟不同驱动循环下的能量消耗情况,并计算能量利用效率,从而为优化设计提供参考依据。
最后,可以通过仿真分析来评估驱动系统的可靠性。
例如,可以模拟电池的充放电过程、电机的工作状态等,检测电池的健康状况,并预测电池的寿命,从而为驱动系统的维护提供支持。
综上所述,新能源汽车驱动系统的优化设计与仿真分析是提高新能源汽车性能和能源利用效率的关键。
通过合理的优化设计和准确的仿真分析,可以提高驱动系统的整体性能,同时降低驱动系统的能量消耗,从而推动新能源汽车技术的进一步发展。
电机CAE解决方案

电机CAE 仿真解决方案目前国内对于电机设计的虚拟装配已经基本实现,但虚拟设计以及虚拟实验的应用仍不充分。
电机的虚拟设计与虚拟实验主要包括电磁、结构、散热三个方面。
对于常规的电机设计方法,计算工作量非常大,只能得到各物理场的平均结果而难以获得其分布,且很难考虑各物理场耦合的问题。
本文与大家分享某电机厂对于新开发的某款电机进行的CAE 多物理场分析方法,其中涉及电磁分析、结构分析(强度、振动、噪声等)和散热分析(流体、热)。
通过分析,可以为电机厂商提供电机电磁、结构、噪声、流场和温度等一系列参数的分布情况,使开发人员能够有针对性的进行改善,从而大大缩短研发周期,降低研发成本。
本项目分析流程如图1所示:图1 电机CAE 多物理场分析流程一、 电磁分析以电机的实际结构建立磁场有限元模型,基于电磁——热双向耦合建立轴向通风各部件的电磁场数学模型和热传导方程,通过电磁——热双向迭代计算得到磁密分布、电磁力等结果。
某电机的气隙磁场磁力线分布如图2所示。
噪声分析 噪声分布电磁分析 磁密分布 动态磁场效应 电磁力、力矩 涡流分析损耗热分析温度分布流体分析流量分配 结构分析应力及应变振动疲劳寿命电磁损耗电磁力定转子温度 电磁损耗对流换热 温度 电磁力-时频转换 振动响应图2 某电机的气隙磁场磁力线分布二、结构分析1.应力及应变分析通过电磁——结构以及热——结构的耦合,对电机进行了整机结构分析(包括整机强度分析、定子与机座配合计算、吊环强度分析等)、整机模态分析和滑环强度分析。
通过分析可以获得电机的应力及应变分布,从而验证电机强度是否满足设计要求。
图3 某电机三阶模态振型2.振动分析通过电磁分析得到定子齿部节点的径向及切向电磁力,映射处理至电机结构的网格模型中,进行振动分析。
通过分析可以获得电机的振动分布,并确认是否满足设计要求。
图4 某电机振动位移云图3. 噪声分析电机产生的三类噪声及主要声源如下图所示,本项目对电磁噪声和气动噪声进行了仿真,验证了电机噪声是否满足设计要求。
多合一电驱动系统的结构原理及cae仿真分析
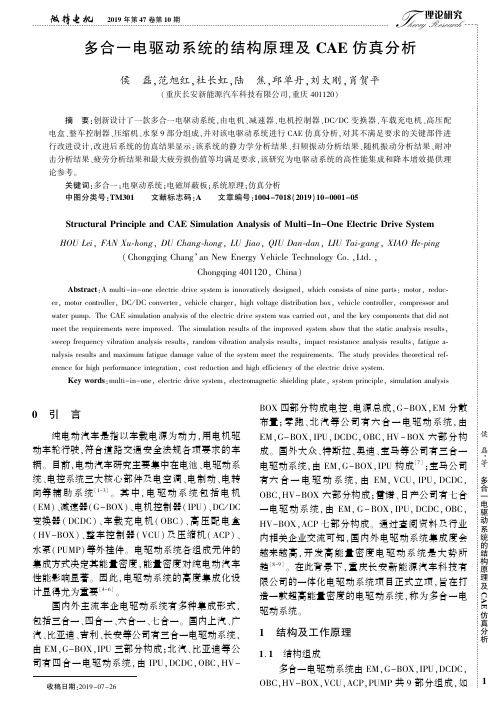
2019年第47卷第10期T理论研究heory Research 侯 磊等 多合一电驱动系统的结构原理及CAE 仿真分析1 收稿日期:2019-07-26多合一电驱动系统的结构原理及CAE 仿真分析侯 磊,范旭红,杜长虹,陆 焦,邱单丹,刘太刚,肖贺平(重庆长安新能源汽车科技有限公司,重庆401120)摘 要:创新设计了一款多合一电驱动系统,由电机㊁减速器㊁电机控制器㊁DC /DC 变换器㊁车载充电机㊁高压配电盒㊁整车控制器㊁压缩机㊁水泵9部分组成,并对该电驱动系统进行CAE 仿真分析,对其不满足要求的关键部件进行改进设计,改进后系统的仿真结果显示:该系统的静力学分析结果㊁扫频振动分析结果㊁随机振动分析结果㊁耐冲击分析结果㊁疲劳分析结果和最大疲劳损伤值等均满足要求,该研究为电驱动系统的高性能集成和降本增效提供理论参考㊂关键词:多合一;电驱动系统;电磁屏蔽板;系统原理;仿真分析中图分类号:TM301 文献标志码:A 文章编号:1004-7018(2019)10-0001-05Structural Principle and CAE Simulation Analysis of Multi-In-One Electric Drive System HOU Lei ,FAN Xu⁃hong ,DU Chang⁃hong ,LU Jiao ,QIU Dan⁃dan ,LIU Tai⁃gang ,XIAO He⁃ping(Chongqing Chang’an New Energy Vehicle Technology Co.,Ltd.,Chongqing 401120,China)Abstract :A multi-in-one electric drive system is innovatively designed,which consists of nine parts:motor,reduc⁃er,motor controller,DC /DC converter,vehicle charger,high voltage distribution box,vehicle controller,compressor and water pump.The CAE simulation analysis of the electric drive system was carried out,and the key components that did not meet the requirements were improved.The simulation results of the improved system show that the static analysis results,sweep frequency vibration analysis results,random vibration analysis results,impact resistance analysis results,fatigue a⁃nalysis results and maximum fatigue damage value of the system meet the requirements.The study provides theoretical ref⁃erence for high performance integration,cost reduction and high efficiency of the electric drive system.Key words :multi-in-one,electric drive system,electromagnetic shielding plate,system principle,simulation analysis 0 引 言纯电动汽车是指以车载电源为动力,用电机驱动车轮行驶,符合道路交通安全法规各项要求的车辆㊂目前,电动汽车研究主要集中在电池㊁电驱动系统㊁电控系统三大核心部件及电空调㊁电制动㊁电转向等辅助系统[1-3]㊂其中,电驱动系统包括电机(EM)㊁减速器(G-BOX)㊁电机控制器(IPU)㊁DC /DC 变换器(DCDC)㊁车载充电机(OBC)㊁高压配电盒(HV-BOX)㊁整车控制器(VCU)及压缩机(ACP)㊁水泵(PUMP)等外挂件㊂电驱动系统各组成元件的集成方式决定其能量密度,能量密度对纯电动汽车性能影响显著㊂因此,电驱动系统的高度集成化设计显得尤为重要[4-6]㊂国内外主流车企电驱动系统有多种集成形式,包括三合一㊁四合一㊁六合一㊁七合一㊂国内上汽㊁广汽㊁比亚迪㊁吉利㊁长安等公司有三合一电驱动系统,由EM,G-BOX,IPU 三部分构成;北汽㊁比亚迪等公司有四合一电驱动系统,由IPU,DCDC,OBC,HV-BOX 四部分构成电控㊁电源总成,G-BOX,EM 分散布置;零跑㊁北汽等公司有六合一电驱动系统,由EM,G-BOX,IPU,DCDC,OBC,HV -BOX 六部分构成㊂国外大众㊁特斯拉㊁奥迪㊁宝马等公司有三合一电驱动系统,由EM,G-BOX,IPU 构成[7];宝马公司有六合一电驱动系统,由EM,VCU,IPU,DCDC,OBC,HV-BOX 六部分构成;雷诺㊁日产公司有七合一电驱动系统,由EM,G -BOX,IPU,DCDC,OBC,HV-BOX,ACP 七部分构成㊂通过查阅资料及行业内相关企业交流可知,国内外电驱动系统集成度会越来越高,开发高能量密度电驱动系统是大势所趋[8-9]㊂在此背景下,重庆长安新能源汽车科技有限公司的一体化电驱动系统项目正式立项,旨在打造一款超高能量密度的电驱动系统,称为多合一电驱动系统㊂1 结构及工作原理1.1 结构组成多合一电驱动系统由EM,G-BOX,IPU,DCDC,OBC,HV-BOX,VCU,ACP,PUMP 共9部分组成,如T理论研究heory Research 2019年第47卷第10期侯 磊等 多合一电驱动系统的结构原理及CAE 仿真分析2 图1所示㊂整体采用四段式结构,分别为减速器左端盖㊁减速器右端盖㊁电机定子壳体㊁电机后端盖,其中减速器右端盖为电机和减速器共用端盖㊂ACP 固定在电机左端盖上,PUMP 固定在电机右端盖上㊂IPU,DCDC,OBC,HV-BOX,VCU 布置在控制器系统壳体中,DCDC,OBC 布置在同一层,称之为电源层;HV-BOX 和IPU,VCU 布置在同一层,称之为电机控制层,电源层和电机控制层共同组成控制器系统,布置在EM 正上方㊂该多合一电驱动系统为原有长安量产的三合一电驱动系统和电源系统的进一步集成产品,提高了能量密度和冷却效率㊂图1 多合一电驱动系统三维数模1.2 系统原理该多合一电驱动系统的系统原理图如图2所示,主要包括高压电传输㊁低压电信号传输㊁热量交换㊁动力传递等,其中高压电包括高压直流电㊁高压交流电㊁家用220V 交流电;低压电信号包括12V 直流电信号㊁CAN 信号㊁高压互锁信号㊁电子锁位置信号㊁制动踏板位置信号等共62个电信号㊂图2 多合一电驱动系统原理简图动力电池输出高压直流电,经过HV-BOX 中叠层铜排将高压直流电分配成4部分,包括控制器系统内部IPU 中的INV 功率模块㊁DCDC 模块,外部的ACP,PTC㊂INV 功率模块将高压直流电转换成高压交流电输送到EM,驱动EM 旋转;DCDC 模块将高压直流电转换成低压直流电输送给12V 蓄电池,实现对12V 蓄电池进行动态充电,12V 蓄电池输出低压直流电给IPU 中的INV 控制模块和VCU 控制模块[10]㊂OBC 模块经过HV-BOX 中叠层铜排与动力电池相连,OBC 可将输入的家用220V 交流电转换成高压直流电,输入到动力电池中,此过程为动力电池慢充过程㊂该电驱动系统的冷却水路㊁PUMP 和电驱动系统外部的冷却控制系统可组成封闭的回路㊂PUMP 为回路中冷却液循环提供动力,冷却控制系统完成回路中冷却液的热交换,对电驱动系统中EM,IPU,DCDC,OBC 进行冷却[11-12]㊂EM 和G-BOX 采用机械连接,通过花键轴㊁花键套结构实现动力传递㊂2 数值建模2.1 模型建立将多合一电驱动系统三维数模进行简化处理,导入到仿真软件中进行预处理,得到模型如图3所示,利用此模型进行有限元分析㊂图3 预处理模型2.2 材料属性该多合一电驱动系统中各部件的材料不同㊂控制器壳体㊁上下盖板㊁电机端盖㊁减速器壳体及支架的材料为ADC12,定子铁心材料为硅钢,电机壳体材料为A365.0-T6,轴材料为20CrMnTi,屏蔽板材料为Q195,具体的材料属性如表1所示㊂表1 材料及物理属性材料弹性模量E /GPa 泊松比μ密度ρ/(kg㊃m -3)屈服强度σs /MPa抗拉强度R m /MPa ADC12700.332700170230硅钢1650.277850385440A365.0-T6690.33268518521520CrMnTi 2120.28978608501080Q1952060.37850195315~4303 CAE 仿真分析3.1 模态分析在进行模态分析时,低阶固有频率对振动影响较大,无需表示出全部阶次下的固有频率,根据经验选取前八阶模态进行分析㊂仿真分析结果表示,一阶模态为108.2Hz,发生在控制器系统中屏蔽板(以下简称屏蔽板)处,如图4(a)所示;二阶模态为157.1Hz,依然发生在屏蔽板处;控制器系统的整体模态发生在第七阶,如图4(b)所示,大小为437.8Hz;八 2019年第47卷第10期 T理论研究heory Research 侯 磊等 多合一电驱动系统的结构原理及CAE 仿真分析3 阶模态为443.9Hz,发生在屏蔽板处㊂(a)一阶模态(b)七阶模态图4 模态分析结果3.2 静力学分析对多合一电驱动系统进行静力学分析,根据整车运行工况确定载荷值,将其分解到X ,Y ,Z 三轴上,用g 的倍数表示大小,具体载荷值如表2所示㊂表2 静力学分析载荷值序号载荷值A /(m㊃s -2)X 轴Y 轴Z 轴1---26g2--24g 3-12.5g-g 4--12.5g-g 512.5g --g 6-12.5g --g 在此工况下进行静力学分析,结果显示,屏蔽板处的最大应力较大,因此结果分析时分别表示多合一电驱动系统㊁屏蔽板两个部分(下同),具体结果如表3所示㊂表3 静力学分析结果序号载荷值A /(m㊃s -2)最大应力σ/MPa多合一电驱动系统σ1屏蔽板σ21Z 轴-26g 13.704132.1622Z 轴24g12.650121.9963Y 轴12.5g Z 轴-g 10.3168.6494Y 轴-12.5g Z 轴-g 9.9418.4965X 轴12.5g Z 轴-g 11.3858.3656X 轴-12.5g Z 轴-g11.1715.856 由表3可知,在沿Z 轴-26g 载荷下,多合一电驱动系统㊁屏蔽板产生的最大应力最大,分别为13.704MPa 和132.162MPa,如图5所示,均满足要求㊂(a)多合一电驱动系统(b)屏蔽板图5 沿Z 轴-26g 载荷下的最大应力3.3 扫频振动分析对多合一电驱动系统进行扫频振动分析,输入频率㊁振幅㊁加速度3个参数,确定其中任意2个参数,即可进行求解计算㊂根据整车运行工况确定Z 轴方向的振动工况,如表4所示,X 轴方向和Y 轴方向振动工况的加速度应该减半㊂频率25Hz 以下为低频段,不选取与之对应的加速度[13-17]㊂表4 Z 轴方向振动工况序号频率f /Hz 振幅B /mm加速度a /(m㊃s -2)115~251.2-225~500-30 经过扫频振动分析计算后,多合一电驱动系统㊁屏蔽板的最大应力及频率如表5所示㊂表5 扫频振动分析结果响应值X 轴Y 轴Z 轴多合一电驱动系统最大应力σ1/MPa 频率f 1/Hz 23.440447.818.559437.815.070437.8屏蔽板最大应力σ2/MPa频率f 2/Hz48.067464.717.219422.1254.087108.2 由表5可知,多合一电驱动系统的最大应力为23.440MPa,如图6(a)所示,满足要求㊂屏蔽板的最大应力为254.087MPa,如图6(b)所示,大于屏蔽板材料Q195的屈服强度195MPa,不满足要求㊂(a)多合一电驱动系统 T理论研究heory Research 2019年第47卷第10期 侯 磊等 多合一电驱动系统的结构原理及CAE 仿真分析 4 (b)屏蔽板图6 扫频振动分析最大应力3.4 随机振动分析对多合一电驱动系统进行随机振动分析,输入频率和加速度谱密度(ASD)两项,根据整车运行工况选取频率分别为10Hz,100Hz,300Hz,500Hz,2000Hz,与之对应的ASD值分别为10m2㊃s-4/Hz,10 m2㊃s-4/Hz,0.51m2㊃s-4/Hz,5m2㊃s-4/Hz,5m2㊃s-4/Hz㊂仿真分析结果如表6所示[18-20]㊂表6 随机振动分析结果响应值X轴Y轴Z轴多合一电驱动系统最大3σ应力σ1/MPa68.30746.36250.892屏蔽板最大3σ应力σ2/MPa113.55076.032268.182 由表6可知,多合一电驱动系统最大3σ应力为68.307MPa,如图7(a)所示,满足要求㊂屏蔽板最大3σ应力为268.182MPa,如图7(b)所示,大于Q195的屈服强度195MPa,不满足要求㊂(a)多合一电驱动系统(b)屏蔽板图7 最大3σ应力综上所述,多合一电驱动系统(除屏蔽板外)静力学分析㊁扫频振动分析㊁随机振动分析结果均满足要求㊂屏蔽板静力学分析结果满足要求,扫频振动分析㊁随机振动分析结果不满足要求㊂因此,需要对屏蔽板进行改进设计,具体措施如下:1)增加屏蔽板安装孔个数;2)将屏蔽板的材料更改为Q235,Q235的屈服强度为235MPa,抗拉强度为375~500MPa㊂4 改进后CAE仿真分析4.1 模态分析根据仿真分析结果及经验选取前十五阶模态进行分析㊂仿真分析结果表示,一阶模态为58.16 Hz,发生在屏蔽板处;二阶模态为85.42Hz,依然发生在屏蔽板处;控制器系统的整体模态发生在第十五阶,大小为437.7Hz,较改进前一阶模态和模态密度均降低㊂4.2 静力学分析借用上文中的载荷值作为输入并对其进行简化,取消表3中序号4㊁序号5表示的载荷,具体结果如表7所示㊂表7 改进后静力学分析结果序号载荷值A/(m㊃s-2)最大应力σ/MPa多合一电驱动系统σ1屏蔽板σ2 1Z轴-26g13.704170.481 2Z轴24g12.650157.3673Y轴12.5gZ轴-g10.31642.8674X轴-12.5gZ轴-g11.17149.726 由表7可知,多合一电驱动系统㊁屏蔽板的最大应力分别为13.704MPa和170.481MPa,均满足要求㊂4.3 扫频振动分析借用上文的表4作为输入进行仿真分析计算,具体结果如表8所示㊂表8 改进后扫频振动分析结果响应值X轴Y轴Z轴多合一电驱动系统最大应力σ1/MPa频率f1/Hz23.440447.818.559437.815.070437.8屏蔽板最大应力σ2/MPa频率f2/Hz51.547474.265.752421.743.464178.1 由表8可知,多合一电驱动系统㊁屏蔽板的最大应力分别为23.440MPa和65.752MPa,均满足要求㊂4.4 随机振动分析借用上文中的输入条件进行仿真分析计算,具体结果如表9所示㊂表9 改进后随机振动分析结果响应值X轴Y轴Z轴多合一电驱动系统最大3σ应力σ1/MPa68.30746.36250.892屏蔽板最大3σ应力σ2/MPa138.88596.612171.309 由表9可知,多合一电驱动系统㊁屏蔽板的最大3σ应力分别为68.307MPa和171.309MPa,均满 2019年第47卷第10期 T理论研究heory Research 侯 磊等 多合一电驱动系统的结构原理及CAE 仿真分析5 足要求㊂4.5 耐冲击分析对多合一电驱动系统进行耐冲击分析,对其施加半正弦冲击载荷,载荷值大小分别为沿Z 轴方向25g ㊁X 轴方向12.5g 及Y 轴方向12.5g ,持续时间为6s㊂评价标准为最大应力是否满足σmax ≤σb ,仿真分析结果如表10所示㊂表10 耐冲击分析结果响应值X 轴Y 轴Z 轴多合一电驱动系统最大应力σ1/MPa11.30213.04121.704屏蔽板最大应力σ2/MPa32.40137.583173.414 由表10可知,多合一电驱动系统最大应力为21.704MPa,如图8(a)所示,满足要求㊂屏蔽板最大应力为173.414MPa,如图8(b)所示,小于Q235的抗拉强度375~500MPa,满足要求㊂(a)多合一电驱动系统(b)屏蔽板图8 耐冲击分析最大应力4.6 疲劳分析借用上文中扫频振动分析时X ,Y ,Z 三个方向的输入条件,分别历时8h;随机振动分析时的输入条件扩展到沿X ,Y ,Z 三个方向各历时22h,将所有结果叠加作为疲劳分析的最终结果㊂结果显示,多合一电驱动系统最大疲劳损伤值为5.279×10-4,小于标准值1,满足要求;屏蔽板最大疲劳损伤值为0.255,大于标准值0.2,根据经验对此进行评估认为风险可忽略[21-22]㊂综上所述,对改进后的多合一电驱动系统依次进行模态分析㊁静力学分析㊁扫频振动分析㊁随机振动分析㊁耐冲击分析和疲劳分析,模态分析结果表明,较改进前一阶模态和模态密度均降低,其余五项分析结果均满足要求㊂4.7 讨论改进后多合一电驱动系统模态分析结果显示,一阶模态和模态密度均降低,带来的影响为屏蔽板同整车其他零部件发生共振的风险增大㊂针对该多合一电驱动系统模态分析结果进行评价时,在目前开发研究阶段,尚无定量的频率范围判定优劣㊂因此,目前不对屏蔽板再次进行结构优化,而采取在屏蔽板安装孔处增加软垫的方式减小共振风险㊂5 结 语本文设计了一款由EM,G -BOX,IPU,DCDC,OBC,HV-BOX,VCU,ACP,PUMP 共9部分组成的多合一电驱动系统,该系统可实现性能的提升和成本的降低㊂该多合一电驱动系统及屏蔽板的静力学分析㊁扫频振动分析㊁随机振动分析㊁耐冲击分析㊁疲劳分析结果均满足要求㊂参考文献[1] 杜飞,姚舜才,王晓丹,等.基于三维有限元的混合励磁爪极电机仿真研究[J].微特电机,2019,47(1):44-48.[2] 李翠萍,管正伟,丁秀翠,等.电动汽车用电机冷却系统设计及发展综述[J].微特电机,2019,47(1):82-86.[3] 罗腾科.电动汽车用永磁同步电机设计优化及性能分析[D].重庆:重庆交通大学,2017.[4] 钱华,陈辰,钱乐,等.一种新型密封结构电机[J].微特电机,2019,47(6):78-79,82.[5] 黄丹.新能源汽车DC /DC 变换器与电机驱动系统集成机理研究[D].柳州:广西科技大学,2017.[6] 孙海涛.基于电驱动汽车再生制动系统的研究[D].天津:河北工业大学,2014.[7] 王赫,杨立超,于海蒂,等.永磁同步电机结构设计和特性探讨[J].内燃机与配件,2018(20):94-96.[8] 李文阳.浅谈新能源汽车的发展方向[J].东方企业文化,2012(19):134.[9] 邱先文.混合动力电动汽车发展状况分析及前景研究[J].小型内燃机与车辆技术,2017,46(3):70-78,96.[10] 么居标,宋建桐,吕江毅,等.基于CAN 总线的电机控制器Bootloader 开发[J].测控技术,2018,37(10):124-126,131.[11] 董静,潘江如,苟春梅.关于新能源汽车的驱动电机系统设计与研究[J].科技风,2018(28):109.[12] 林彬超.基于DSP 的五相永磁同步电机驱动系统研究[D].合肥:安徽大学,2019.[13] 谢天,周铁英,陈宇.一种双转子模态转换型超声波电动机的设计[J].微特电机,2009,37(10):18-21.[14] 吕维,罗卫东,曹争光,等.超声波电动机定子振动模态及影响因素分析[J].微特电机,2010,38(5):29-30.[15] 王家豪.新能源汽车车身的结构分析和试验[D].广州:华南理工大学,2013.[16] 史忠震,张卫,陈强,等.直流电动机定子有限元模态分析[J].微特电机,2014,42(5):14-16.[17] 段敏,郝亮,李卫民,等.车用交流发电机整机的模态分析与试验研究[J].微特电机,2016,44(9):23-25,32.[18] 卢鹏,方明霞.基于模态综合法的永磁同步电机动力学分析[J].微特电机,2018,46(6):9-14.(下转第10页)T理论研究heory Research 2019年第47卷第10期 邱美涵等 基于DSADC 的旋变位置解码系统设计与研究10 度基本一致㊂图14 静态解码角度偏差4.2 动态解码测试对于转子位置的稳态测试实验,控制电机以一定转速运转,然后观测不同角度辨识方法对转子位置的检测结果㊂图15~图18为电机以500r /min 的转速旋转,三种角度辨识方法的估算偏差以及转子位置波形㊂通过对比误差波形可以看出,反正切法与二阶和三阶角度观测器误差大小基本相同,三种方法的最大偏差为4(0~1024),偏差角度值为1.4°㊂图15 反正切法估算偏差图16 二阶角度观测器估算偏差图17 三阶角度观测器估算偏差图18 转子位置信号波形对三种方法分别进行了静态和稳态测试,并与旋变解码芯片得到的转子位置信号进行对比分析㊂实验结果表明,本文的基于DSADC 的旋变解码电路及软解码算法可以提供较好的转子位置信号,实现解码功能㊂根据测得转子位置偏差可以看出,三种解码算法都可以实现角度辨识功能,且三种解码算法对于电机静态和低转速稳态下解码精度基本一致㊂5 结 语本文研究了基于DSADC 的旋变位置解码功能,并搭建电机测试平台对旋变解码功能进行实验测试,实验结果证明,通过利用TC275的DSADC 模块进行旋变解码的硬件和软件解码算法设计,可以替代专用的旋变解码芯片,降低开发成本㊂目前该解码系统可适用于电机低速运行且需要减少成本的场合㊂对于电机高速运行状态下,基于DSADC 的旋变软件解码功能还需进一步测试研究,以减小解码偏差,提高解码精度㊂参考文献[1] 熊慧敏.基于MCU 的旋转变压器解码系统设计[D].武汉:华中科技大学,2014.[2] 吴红星,洪俊杰,李立毅.基于旋转变压器的电动机转子位置检测研究[J].微电机,2008,41(1):1-3,9.[3] 程胭脂,麻友良,李乐荣,等.旋转变压器软件解码系统研究[J].科技通报,2016,32(8):186-190.[4] 崔波,徐衍亮,张云.基于DSP 的旋转变压器解码系统设计[J].微电机,2017,50(4):54-58.[5] 储海燕.旋转变压器信号处理电路的设计与实现[D].西安:西安电子科技大学,2011.[6] 赵瑞杰,陶学军,刘德林,等.基于角度观测器的旋转变压器解码算法研究[J].电力电子技术,2012,46(4):1-3.[7] AUGER F,MANSOURI-TOUDERT O,CHIBAH A.Desing of ad⁃vanced resolver-to-digital converters[C]//ElectriMACS.Cergy:2011.[8] 吴忠,吕绪明.基于磁编码器的伺服电机速度及位置观测器设计[J].中国电机工程学报,2011,31(9):82-87.[9] 姜燕平.旋转变压器原理及其应用[J].电气时代,2005(10):95-96.[10] 朱樟明,杨银堂.基于Simulink 的Sigma-Delta A /D 转换器调制器系统建模[J].系统仿真学报,2008(24):6799-6802.作者简介:邱美涵(1992 ),女,硕士研究生,研究方向为永磁同步电机驱动控制㊂(上接第5页)[19] 张小波,贾金信,张芳.制冷离心机用高速永磁电动机转子强度设计[J].微特电机,2019,47(6):37-41.[20] 李恒,高亚如.磁轭永磁振动发电机的设计与实验研究[J].微特电机,2019,47(6):42-44,48.[21] 吴道俊.汽车悬架承载梁焊接结构疲劳分析[J].长沙理工大学学报(自然科学版),2019,16(1):79-84,110.[22] 栾振,卢剑伟,赵方洲,等.汽车变速器齿轮疲劳寿命试验强化系数计算分析[J].农业装备与车辆工程,2019,57(2):9-13.。
多能源动力总成管理系统仿真分析

摘 要 :多能源 动力总成管理系统是混合动力汽车 最为核心的技术。本文分析 了多 能源动力 总成管理 系统 中的各个
子 模 型 。根 据 加 速 踏 板 位 置信 号 , 电池 的 状 态 以及 发 动 机 、发 电机 、 电动 机 三 者 的转 速 ,通 过 该 系 统 的控 制 策 略 , 将 动 力 进 行 合 理 的 匹配 ,最 后 得 到 了发 动 机 的节 气 门 信 号 ,电动 机 和 发 电 机 的 参 考 转 矩 。再 将 这 些 输 出信 号输 入 到
a na l y z es va r i ou s s ub — m od e l s i n t he m ul t i - e ne r g y powe r t r a i n ma na ge me n t s ys t e m. Ac c o r di ng t o he t a c c e l e r a t o r pe d a l p os i t i o n
汽 车 实 用 技 术 设 计 研 究
A UT O MO BI LE Aj ) PI I E D TE CH N OL 0G Y
2 0 1 5 年 第5 期
2 O1 5 NO . 5
多能源动力总成 管理 系统仿真分析
赵 娜 ,吴 祥 超
( 长 安 大 学 , 陕西 西 安 7 1 0 0 6 4 )
e n g i n e s , g e n e r a t o r s nd a mo t o r s ea r s o n a b l y . Ke y wo r d s : Hy b r i d El e c t r i c Ve h i c l e ; Mu l t N e n e r g y po we r t r a i n Ma n a g e me n t S y s t e m; Ba t t e r y Ma n a g e me n t
华为多合一电驱动总成拆机报告

华为多合一电驱动总成拆机报告华为多合一电驱动总成拆机报告摘要:本文通过拆解华为多合一电驱动总成,对其内部结构及各部件进行了详细分析。
总结了华为多合一电驱动总成的主要模块和功能,并针对其中的关键部件进行了介绍与评价。
通过对华为多合一电驱动总成的拆解分析,旨在为后续的产品研发和改进提供参考和借鉴。
一、引言华为多合一电驱动总成是一款具有多种功能的电动驱动设备。
它被广泛应用于各种工业领域,如机械制造、电力设备等。
了解和掌握其内部结构及各部件的功能和工作原理,对于提高产品的性能和可靠性具有重要意义。
二、拆解分析1. 总体结构华为多合一电驱动总成的总体结构由外壳、控制器模块、电源模块、驱动模块和电机模块组成。
外壳具有良好的密封性和散热性,能够有效保护内部的电子元件和机械结构。
2. 控制器模块控制器模块是华为多合一电驱动总成的核心模块,主要负责控制驱动模块和电机模块的工作。
它采用高性能的智能控制芯片,能够实时监测和控制电机的运行状态,并根据需求进行精确的调整。
3. 电源模块电源模块主要负责为整个电驱动总成提供稳定可靠的电源供应。
它采用高效率的电源转换器,能够将输入的电能转化为稳定的直流电源,并通过过电流、过压等保护措施保证电驱动总成的安全运行。
4. 驱动模块驱动模块是华为多合一电驱动总成的重要组成部分,通过控制电机的旋转,实现机械设备的运动。
驱动模块包括电机驱动电路、电机驱动器等部件,其稳定性和可靠性对于保证设备的正常工作至关重要。
5. 电机模块电机模块是实现电驱动总成动力输出的关键部件。
它采用高性能的永磁同步电机,具有高效能、高转矩和低噪音等优点。
电机模块通过与驱动模块的配合,能够实现对机械设备的精确控制和调节。
三、关键部件评价1. 智能控制芯片华为多合一电驱动总成所采用的智能控制芯片具有高性能和高可靠性,能够实时监测和控制电机的运行状态。
其灵活的编程能力和强大的处理能力,为驱动总成提供了更高的稳定性和安全性。
- 1、下载文档前请自行甄别文档内容的完整性,平台不提供额外的编辑、内容补充、找答案等附加服务。
- 2、"仅部分预览"的文档,不可在线预览部分如存在完整性等问题,可反馈申请退款(可完整预览的文档不适用该条件!)。
- 3、如文档侵犯您的权益,请联系客服反馈,我们会尽快为您处理(人工客服工作时间:9:00-18:30)。
1 2 3 4 5
1 结构及工作原理
1.1 结构组成
多合一电驱动系统由EM,G-BOX,IPU,DCDC,OBC,HV-BOX,VCU,ACP,PUMP共9部分组成,如图1所示。
整体采用四段式结构,分别为减速器左端盖、减速器右端盖、电机定子壳体、电机后端盖,其中减速器右端盖为电机和减速器共用端盖,ACP固定在电机左端盖上,PUMP 固定在电机右端盖上。
IPU,DCDC,OBC,HV-BOX,VCU布置在控制器系统壳体中,DCDC,OBC布置在同一层,称之为电源层;HV-BOX和IPU,VCU布置在同一层,称之为电机控制层,电源层和电机控制层共同组成控制器系统,布置在EM正上方。
该多合一电驱动系统为原有长安量产的三合一电驱动系统和电源系统的进一步集成产品,提高了能量密度和冷却效率。
图1 多合一电驱动系统三维数模
该多合一电驱动系统的系统原理图如图2所示,主要包括高压电传输、低压电信号传输、热量交换、动力传递等,其中高压电包括高压直流电、高压交流电、家用220 V交流电;低压电信号包括12 V直流电信号、CAN信号、高压互锁信号、电子锁位置信号、制动踏板位置信号等共62个电信号。
图2 多合一电驱动系统原理简图
动力电池输出高压直流电,经过HV-BOX中叠层铜排将高压直流电分配成4部分,包括控制器系统内部IPU中的INV 功率模块、DCDC模块,外部的ACP,PTC。
INV功率模块将高压直流电转换成高压交流电输送到EM,驱动EM旋转;DCDC模块将高压直流电转换成低压直流电输送给12 V蓄电池,实现对12 V蓄电池进行动态充电,12 V蓄电池输出低压直流电给IPU中的INV控制模块和VCU控制模块。
OBC模块经过HV-BOX中叠层铜排与动力电池相连,OBC 可将输入的家用220 V交流电转换成高压直流电,输入到
动力电池中,此过程为动力电池慢充过程。
该电驱动系统的冷却水路、PUMP和电驱动系统外部的冷却控制系统可组成封闭的回路。
PUMP为回路中冷却液循环提供动力,冷却控制系统完成回路中冷却液的热交换,对电驱动系统中EM,IPU,DCDC,OBC进行冷却。
EM和G-BOX采用机械连接,通过花键轴、花键套结构实
现动力传递。
2.1模型建立
将多合一电驱动系统三维数模进行简化处理,导入到仿真软件中进行预处理,得到模型如图3所示,利用此模型进行有限元分析。
图3 预处理模型
2.2 材料属性
该多合一电驱动系统中各部件的材料不同。
控制器壳体、上下盖板、电机端盖、减速器壳体及支架的材料为ADC12,定子铁心材料为硅钢,电机壳体材料为A365.0-T6,轴材料为20CrMnTi,屏蔽板材料为Q195,具体的材料属性如表1所示。
表1 材料及物理属性
在进行模态分析时,低阶固有频率对振动影响较大,无需表示出全部阶次下的固有频率,根据经验选取前八阶模态进行分析。
仿真分析结果表示,一阶模态为108.2 Hz,发生在控制器系统中屏蔽板(以下简称屏蔽板)处,如图4(a)所示;二阶模态为157.1 Hz,依然发生在屏蔽板处;控制器系统的整体模态发生在第七阶,如图4(b)所示,大小为437.8 Hz;八阶模态为443.9 Hz,发生在屏蔽板处。
(a) 一阶模态
(b) 七阶模态图4 模态分析结果
3.2 静力学分析
对多合一电驱动系统进行静力学分析,根据整车运行工况确定载荷值,将其分解到X,Y,Z三轴上,用g的倍数表示大小,具体载荷值如表2所示。
表2 静力学分析载荷值
在此工况下进行静力学分析,结果显示,屏蔽板处的最大应力较大,因此结果分析时分别表示多合一电驱动系统、屏蔽板两个部分(下同),具体结果如表3所示。
表3 静力学分析结果
由表3可知,在沿Z轴-26g载荷下,多合一电驱动系统、屏蔽板产生的最大应力最大,分别为13.704MPa 132.162MPa,如图5所示,均满足要求。
(a) 多合一电驱动系统
图5 沿Z轴-26g载荷下的最大应力
(b) 屏蔽板
图5 沿Z轴-26g载荷下的最大应力
对多合一电驱动系统进行扫频振动分析,输入频率、振幅、加速度3个参数,确定其中任意2个参数,即可进行求解计算。
根据整车运行工况确定Z轴方向的振动工况,如表4所示,X 轴方向和Y轴方向振动工况的加速度应该减半。
频率25 Hz以下为低频段,不选取与之对应的加速度。
表4 Z轴方向振动工况
经过扫频振动分析计算后,多合一电驱动系统、屏蔽板
的最大应力及频率如表5所示。
表5 扫频振动分析结果
由表5可知,多合一电驱动系统的最大应力为23.440 MPa,如图6(a)所示,满足要求。
屏蔽板的最大应力为254.087 MPa,如图6(b)所示,大于屏蔽板材料Q195的屈服强度195 MPa,不满足要求。
(a) 多合一电驱动系统
(b) 屏蔽板
图6 扫频振动分析最大应力
对多合一电驱动系统进行随机振动分析,输入频率和加速度谱密度(ASD)两项,根据整车运行工况选取频率分别为10Hz,100Hz,300Hz,500Hz,2 000 Hz,与之对应的ASD值分别为10 m2·s-4/Hz,10 m2·s-4/Hz,0.51 m2·s-4/Hz,5 m2·s-4/Hz,5 m2·s-4/Hz。
仿真分析结果如表6所示。
表6 随机振动分析结果
由表6可知,多合一电驱动系统最大3σ应力为68.307 MPa,如图7(a)所示,满足要求。
屏蔽板最大3σ应力为268.182 MPa,如图7(b)所示,大于Q195的屈服强度195 MPa,不满足要求。
(a) 多合一电驱动系统
(b) 屏蔽板
图7 最大3σ应力
综上所述,多合一电驱动系统(除屏蔽板外)静力学分析、扫频振动分析、随机振动分析结果均满足要求。
屏蔽板静力学分析结果满足要求,扫频振动分析、随机振动分析结果不满足要求。
因此,需要对屏蔽板进行改进设计,具体措施如下:
1) 增加屏蔽板安装孔个数;
2) 将屏蔽板的材料更改为Q235,Q235的屈服强度为235 MPa,抗拉强度为375~500 MPa。
4.1 模态分析
借用上文中的载荷值作为输入并对其进行简化,取消表3中序号4、序号5表示的载荷,具体结果如表7所示。
4.2 静力学分析
借用上文中的载荷值作为输入并对其进行简化,取消表
3中序号4、序号5表示的载荷,具体结果如表7所示。
表7 改进后静力学分析结果
由表7可知,多合一电驱动系统、屏蔽板的最大应力分别为13.704MPa和170.481 MPa,均满足要求。
4.3 扫频振动分析
借用上文的表4作为输入进行仿真分析计算,具体结果如表8所示。
表8 改进后扫频振动分析结果
由表8可知,多合一电驱动系统、屏蔽板的最大应力分
别为23.440MPa和65.752MPa,均满足要求。
4.4 随机振动分析
借用上文中的输入条件进行仿真分析计算,具体结果如表9所示。
表9 改进后随机振动分析结果
由表9可知,多合一电驱动系统、屏蔽板的最大3σ应力
分别为68.307 MPa和171.309 MPa,均满足要求。
对多合一电驱动系统进行耐冲击分析,对其施加半正弦冲击载荷,载荷值大小分别为沿Z轴方向25g、X轴方向12.5g及Y 轴方向12.5g,持续时间为6 s。
评价标准为最大应力是否满足σmax≤σb,仿真分析结果如表10所示。
表10 耐冲击分析结果
由表10可知,多合一电驱动系统最大应力为21.704 MPa,如图8(a)所示,满足要求。
屏蔽板最大应力为173.414 MPa,如图8(b)所示,小于Q235的抗拉强度375~500 MPa,满足要求。
表10 耐冲击分析结果
(a) 多合一电驱动系统
(b) 屏蔽板
图8 耐冲击分析最大应力
4.6 疲劳分析
借用上文中扫频振动分析时X,Y,Z三个方向的输入条件,分别历时8 h;随机振动分析时的输入条件扩展到沿X,Y,Z 三个方向各历时22 h,将所有结果叠加作为疲劳分析的最终结果。
结果显示,多合一电驱动系统最大疲劳损伤值为5.279×10-4,小于标准值1,满足要求;屏蔽板最大疲劳损伤值为0.255,大于标准值0.2,根据经验对此进行评估认为风险可忽略。
综上所述,对改进后的多合一电驱动系统依次进行模态分析、静力学分析、扫频振动分析、随机振动分析、耐冲击分析和疲劳分析,模态分析结果表明,较改进前一阶模态和模态密度均降低,其余五项分析结果均满足要求。
4.7 讨论
改进后多合一电驱动系统模态分析结果显示,一阶模态和模态密度均降低,带来的影响为屏蔽板同整车其他零部件发生共振的风险增大。
针对该多合一电驱动系统模态分析结果进行评价时,在目前开发研究阶段,尚无定量的频率范围判定优劣。
因此,目前不对屏蔽板再次进行结构优化,而采取在屏蔽板安装孔处增加软垫的方式减小共振风险.
5 结语
本文设计了一款由EM,G-BOX,IPU,DCDC,OBC,HV-BOX,VCU,ACP,PUMP共9部分组成的多合一电驱动系统,该系统可实现性能的提升和成本的降低。
该多合一电驱动系统及屏蔽板的静力学分析、扫频振动分析、随机振动分析、耐冲击分析、疲劳分析结果均满足要求。