高炉施工方案0406
高炉施工安全施工方案
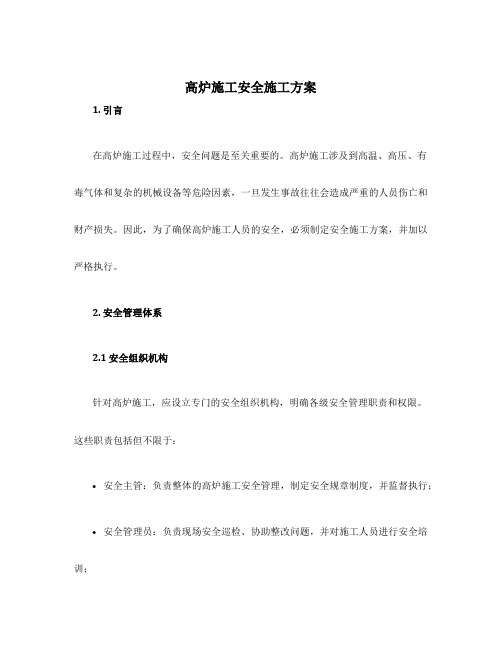
高炉施工安全施工方案1. 引言在高炉施工过程中,安全问题是至关重要的。
高炉施工涉及到高温、高压、有毒气体和复杂的机械设备等危险因素,一旦发生事故往往会造成严重的人员伤亡和财产损失。
因此,为了确保高炉施工人员的安全,必须制定安全施工方案,并加以严格执行。
2. 安全管理体系2.1 安全组织机构针对高炉施工,应设立专门的安全组织机构,明确各级安全管理职责和权限。
这些职责包括但不限于:•安全主管:负责整体的高炉施工安全管理,制定安全规章制度,并监督执行;•安全管理员:负责现场安全巡检、协助整改问题,并对施工人员进行安全培训;•安全监察员:负责对施工现场进行安全监督,检查施工作业是否符合安全规范;•急救人员:负责处理施工现场突发的安全事故,并提供急救服务。
2.2 安全培训和教育在高炉施工前,应进行全面的安全培训和教育,包括但不限于:•高炉施工规范和要求;•安全操作规程和标准;•紧急救援措施和技术;•危险因素识别和应对方法。
通过安全培训和教育,提高施工人员的安全意识和技能,确保他们能够正确应对施工中的各种危险情况。
3. 施工现场安全管理3.1 施工场地准备在施工前,应对施工场地进行全面的安全检查和准备:•清理施工现场,清除垃圾和杂物;•检查施工设备和工具的完好性;•设置安全标志和警示牌;•制定施工区域划分和通道设置。
3.2 施工作业控制在高炉施工过程中,应采取一系列措施对施工作业进行有效控制:•制定详细的施工计划和流程,明确施工工序和时间;•严格控制施工气压、温度和流量等关键参数;•保持施工现场的通风良好,确保有足够的新鲜空气;•确保施工现场的整洁和无障碍,防止人员跌倒和碰撞。
3.3 危险因素控制高炉施工中存在许多危险因素,需要采取相应措施进行控制:•对高温设备和工艺进行防护,确保人员不暴露于高温环境中;•设置适当的防护措施,防止人员接触有毒气体和有害物质;•对机械设备进行定期维护和保养,确保其正常运转;•建立严格的动火管理制度,避免火灾的发生。
高炉大修施工方案
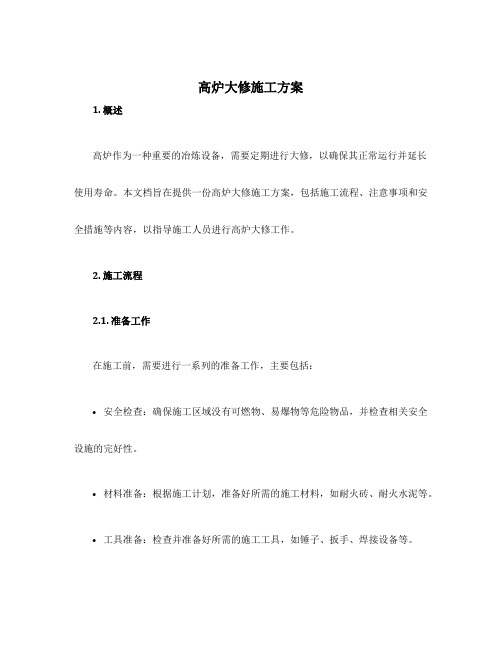
高炉大修施工方案1. 概述高炉作为一种重要的冶炼设备,需要定期进行大修,以确保其正常运行并延长使用寿命。
本文档旨在提供一份高炉大修施工方案,包括施工流程、注意事项和安全措施等内容,以指导施工人员进行高炉大修工作。
2. 施工流程2.1. 准备工作在施工前,需要进行一系列的准备工作,主要包括:•安全检查:确保施工区域没有可燃物、易爆物等危险物品,并检查相关安全设施的完好性。
•材料准备:根据施工计划,准备好所需的施工材料,如耐火砖、耐火水泥等。
•工具准备:检查并准备好所需的施工工具,如锤子、扳手、焊接设备等。
2.2. 拆除工作拆除工作是高炉大修的首要任务,需要按照以下步骤进行:1.关闭高炉:将高炉停机,切断电源和供气等设备的供应。
2.清理高炉:清理高炉内部的积灰和残渣,使用合适的清洁工具和设备进行清理。
3.拆除砖石:在清理完高炉后,开始拆除砖石。
使用专业的工具和设备进行拆除,并注意安全。
2.3. 检修工作在完成拆除工作后,需要进行高炉的检修工作。
具体步骤如下:1.检查设备:对高炉的各项设备进行细致的检查,包括炉壳、风口、渣口等,并记录损坏或需要修复的情况。
2.更换耐火材料:根据需要,对炉壳、风口、渣口等部位进行耐火材料更换,确保其正常使用。
3.修复设备:对损坏的设备进行修复或更换,如焦炉、风机等,并进行必要的检测和调试。
2.4. 安装工作在完成检修工作后,进行高炉的安装工作。
具体步骤如下:1.安装砖石:根据施工图纸和要求,使用合适的耐火砖对高炉进行砌筑。
2.铺设管道:根据需要,对高炉的燃气管道、风管等进行铺设和连接。
3.配置设备:安装和配置高炉的各项设备,如燃气阀门、启闭装置等。
2.5. 调试工作在完成安装工作后,需要对高炉进行调试,以确保其正常运行。
具体步骤如下:1.开启高炉:逐步开启高炉的电源和供气等设备。
2.检查设备运行情况:检查高炉的各项设备是否正常运行,并进行必要的调整和修复。
3.试运行:进行高炉的试运行,观察其运行情况,并进行必要的调整和修正。
高炉设备安装施工方案

1 编制依据1.1 安源钢铁有限公司120万吨钢技术改造工程1080m3高炉设备施工图纸;1.2《炼铁机械设备工程安装验收规范》(50372-2006)1.3 设备制造厂提供的设备安装、调试、维修技术资料1.4 本企业相关施工及管理资料文件;1.5 本企业承建类似工程施工成熟经验。
2 工程概况高炉有效容积为1080m3,年产120万吨生铁。
高炉本体的设备主要为冷却壁,分为铸铁冷却壁和铜冷却壁大约1257吨。
炉顶设备采用采用串罐无料钟炉顶装料设备,约90吨。
炉顶上料系统采用斜桥8.0m3料车上来上料。
风口平台出铁场,配置液压开铁口机和液压泥炮机各两台。
3、设备安装主要施工方法3.1、高炉设备安装3.1.1高炉冷却壁的安装a 冷却壁在施工现场安装前,必须进行通球、水压试验。
通球试验采用0.6倍水管内径的木球或尼绒球,用水为动力球从一头进另一头出,不能有堵塞现象。
冷却壁通球试验合格后,再进行1.5MPa水压试验,以0.75kg手锤敲击,检查后无漏水和冒汗现象,保压20分钟压力降不大于3%者为合格。
b 安装各段冷却壁前必须先将铁口框,风口法兰等设备安装完后,再进行安装。
c冷却壁进出水管、螺栓开孔由制造厂预先开好,遇有偏差处,可用火焊适当切割。
d 每层冷却壁中有一块合门冷却壁应最后安装。
e 固定冷却壁的螺栓安装时要拧紧,并及时焊接封罩。
f 高炉冷却壁的安装技术要求应符合下表规定:3.1.2 高炉风口法兰的安装在高炉设备安装中,风口设备的安装质量关系到高炉的生产能力和运行工况,如风口设备的安装质量不好气流就不会在炉内均衡地分布,严重时会出现不正常的炉况而产生故障。
所以本工程在施工时必须要重视风口的安装,尽可能地保证将各风口中心线交汇在炉体中心线上,并距炉体中心线等距。
3.1.2.1 安装风口的关键是风口法兰。
在风口带炉壳安装、焊接、检查合格后,再安装风口法兰。
3.1.2.2 安装风口法兰之前,应首先将炉内安装用的活动吊篮(活动工作台)在风口中心线下约1m处予以固定,并将炉体中心点投放在平台上,以平台上的中心点为基准用经纬仪将风口中心线的垂直和水平座标投放在炉壳内壁,投点应在风口法兰外圆尺寸之外,这样在炉壳上开孔时才不会破坏投点。
高炉本体大修安全施工方案

施工进度安排
根据施工流程和设备状况 ,制定详细的施工进度计 划,确保施工按时完成。
应急预案制定
针对可能出现的突发情况 ,制定相应的应急预案, 确保在遇到紧急情况时能 够迅速响应和处理。
人员培训与资质认证
施工人员培训
对施工人员进行安全知识和技能培训,提高施工人员的安全意识 和操作技能水平。
特种作业人员资质认证
加强电气设备的维护和保 养,确保其安全可靠;定 期对电气线路进行检查和 更换,防止线路老化引发 事故;加强电气作业人员 的安全培训,提高其安全 意识和操作技能。
加强密闭空间和有毒有害 环境的通风措施,确保空 气流通;为作业人员配备 合格的个人防护用品,如 防毒面具等;建立应急救 援机制,确保在发生中毒 窒息事故时能够及时救援 。
对施工过程中可能出现的危险源进行辨识和分类
物体打击
施工过程中,可能因操作不当 或设备故障导致物体飞溅、弹 出,对人员造成伤害。
中毒窒息
在密闭空间或有毒有害环境中 作业,可能因通风不良或防护 措施不到位导致中毒窒息。
高空坠落
在高空作业过程中,由于防护 措施不到位或操作不当,可能 导致人员或物品坠落。
严格搭设标准
按照相关标准和规范进行脚手架和平台的搭设,确保 搭设过程中每个环节的准确性和安全性。
穿戴合格的个人防护用品
安全帽
高空作业人员必须佩戴 符合安全标准的安全帽
,以防止头部受伤。
安全带
作业人员需穿戴安全带 ,并将其固定在稳固的 支撑点上,以防止意外
坠落。
防护服
穿着符合要求的防护服 ,以防止身体受到飞溅
高炉本体大修安全施工方案
汇报人:XX 2024-01-08
目录
• 施工前准备 • 施工过程中的安全保障 • 高空作业安全防护措施 • 电气设备及线路安全防护措施 • 危险源辨识与风险评估及应对措施 • 环境保护与节能减排举措
高炉大修安全施工方案
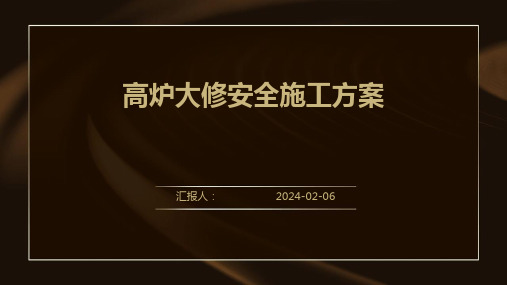
CHAPTER 03
现场施工安全措施
危险源辨识与风险控制策略
辨识危险源
对高炉大修现场进行全面勘查, 识别潜在的危险源,如高处坠落 、物体打击、机械伤害、触电等
。
风险评估
对辨识出的危险源进行风险评估, 确定风险等级,并制定相应的控制 措施。
未来安全生产管理趋势预测
智能化安全监测技术将得 到广泛应用,实现对高炉 大修施工全过程的实时监 控和预警。
应急管理体系将进一步完 善,实现对应急预案、应 急资源、应急队伍等全方 位管理。
ABCD
安全生产标准化建设将深 入推进,提高高炉大修施 工的安全管理水平和效率 。
安全文化建设将成为企业 安全生产管理的重要组成 部分,提高员工的安全意 识和素养。
操作人员资质审核和培训考核
ห้องสมุดไป่ตู้
操作人员必须持有有效的特种作 业操作证,经过专业培训并考核
合格。
熟悉焊接切割设备的安全操作规 程,了解设备性能和使用方法。
掌握相关安全知识和应急处理技 能,确保施工过程中的安全。
现场环境监测及通风换气保障
对施工现场进行环境监测,确保空气质 量符合安全要求。
采取有效的通风换气措施,降低有害气 配备专业的气体检测仪器,实时监测有
电气设备选型及采购质量控制
设备选型
根据高炉大修施工需求,选择性 能稳定、技术成熟的电气设备, 确保设备能够满足施工要求。
采购质量控制
严格把控电气设备采购质量,选 择有资质、信誉良好的供应商, 对设备进行全面的质量检查,确 保设备质量符合标准。
安装调试过程中注意事项提示
安装前准备
高炉施工方案
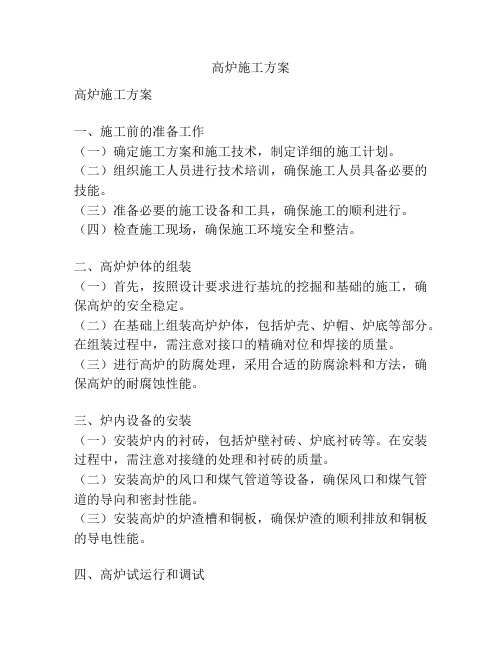
高炉施工方案高炉施工方案一、施工前的准备工作(一)确定施工方案和施工技术,制定详细的施工计划。
(二)组织施工人员进行技术培训,确保施工人员具备必要的技能。
(三)准备必要的施工设备和工具,确保施工的顺利进行。
(四)检查施工现场,确保施工环境安全和整洁。
二、高炉炉体的组装(一)首先,按照设计要求进行基坑的挖掘和基础的施工,确保高炉的安全稳定。
(二)在基础上组装高炉炉体,包括炉壳、炉帽、炉底等部分。
在组装过程中,需注意对接口的精确对位和焊接的质量。
(三)进行高炉的防腐处理,采用合适的防腐涂料和方法,确保高炉的耐腐蚀性能。
三、炉内设备的安装(一)安装炉内的衬砖,包括炉壁衬砖、炉底衬砖等。
在安装过程中,需注意对接缝的处理和衬砖的质量。
(二)安装高炉的风口和煤气管道等设备,确保风口和煤气管道的导向和密封性能。
(三)安装高炉的炉渣槽和铜板,确保炉渣的顺利排放和铜板的导电性能。
四、高炉试运行和调试(一)进行高炉的冷负荷试运行,包括喷水冷却和模拟燃烧等试验。
在试运行过程中,需监测高炉的温度和压力变化。
(二)进行高炉的热负荷试运行,包括进料、风量和燃料控制等试验。
在试运行过程中,需监测高炉的产气量和成品率等指标。
(三)进行高炉的正式生产,根据实际情况调整操作参数,确保高炉的稳定运行和高效生产。
以上是高炉施工方案的主要内容,通过合理的施工计划和科学的施工技术,能够确保高炉的安全性和稳定性,并且达到预期的生产效果。
在实施过程中,需严格按照规范进行操作,确保施工质量和安全效果。
同时,还需根据实际情况进行及时的调整和改进,确保高炉的长期稳定运行。
高炉工程基础施工方案模板

高炉工程基础施工方案模板1. 工程概述高炉是冶炼铁矿石的设备,它是由一系列的基础工程组成的,包括地基、基础、支承、固定和安装系统等。
高炉道四周的土石方一般称矿石堆场,炉腹为承矿炉前灌铁池。
输入矿石的输送设备和煤气硫化铁的输送设备也常视为基础组件。
2. 工程内容基础施工的主要内容包括:平整基础场地,挖土填方,预留地脚螺栓孔,浇筑混凝土基础,安装支撑系统。
3. 施工前的准备工作(1)施工前的测量在施工前需要对基础场地进行测量,确定地面的高度和平整度,并根据确定的高程设计挖土填方计划。
(2)地质勘察根据基础施工地点的地质情况,进行地质勘察,了解地下水位、土壤类型和地基承载力等情况,以便合理设计基础结构。
(3)环境保护和安全措施在施工前需要对施工场地进行环境评估,保护周围环境,同时对施工人员进行安全教育,确保施工过程中安全生产。
4. 场地平整在进行基础施工前需对施工场地进行平整,清除杂物和杂草,确保施工场地的整洁,并进行场地复尺验收。
5. 挖土填方(1)挖土根据设计要求和测量结果,确定挖土的具体位置和深度,进行挖土作业。
(2)填方将挖出的土方用于填方,根据设计要求进行填方,保证填方后的土层平整和致密。
6. 预留地脚螺栓孔地脚螺栓是高炉基础结构中的重要支撑组件,需要根据设计要求,在基础中预留地脚螺栓孔,用于固定支撑系统。
7. 浇筑混凝土基础(1)基础浇筑前的准备在进行混凝土浇筑前,需要准备混凝土模板和支撑设备,保证浇筑过程中的平整度和结构稳定。
(2)混凝土浇筑根据设计要求进行混凝土浇筑,确保混凝土的密实度和表面平整度。
8. 安装支撑系统根据设计要求和现场测量结果,进行支撑系统的安装,确保支撑系统的稳固性和安全性。
9. 施工验收在完成基础施工后,进行基础结构的验收,包括基础的平整度、密实度和支撑系统的稳固性等方面的验收。
10. 现场管理在施工过程中,需要加强对现场施工人员的管理,确保安全生产,合理安排施工进度,保证基础施工的质量和进度。
钢铁厂高炉设计施工方案
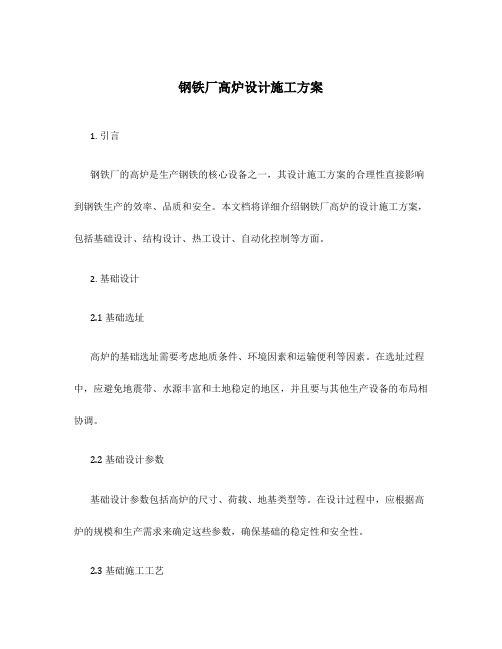
钢铁厂高炉设计施工方案1. 引言钢铁厂的高炉是生产钢铁的核心设备之一,其设计施工方案的合理性直接影响到钢铁生产的效率、品质和安全。
本文档将详细介绍钢铁厂高炉的设计施工方案,包括基础设计、结构设计、热工设计、自动化控制等方面。
2. 基础设计2.1 基础选址高炉的基础选址需要考虑地质条件、环境因素和运输便利等因素。
在选址过程中,应避免地震带、水源丰富和土地稳定的地区,并且要与其他生产设备的布局相协调。
2.2 基础设计参数基础设计参数包括高炉的尺寸、荷载、地基类型等。
在设计过程中,应根据高炉的规模和生产需求来确定这些参数,确保基础的稳定性和安全性。
2.3 基础施工工艺基础施工工艺包括地表开挖、基坑处理、灌注桩施工等。
在施工过程中,应根据地质条件和基础设计要求,采用适当的工艺和设备,确保基础的牢固和可靠。
3. 结构设计3.1 结构材料高炉的主要结构材料为钢结构和混凝土。
钢结构用于高炉的外壳和内部设备支撑,混凝土用于高炉的炉壁和炉底。
3.2 结构设计参数结构设计参数包括高炉的尺寸、结构荷载、抗震性能等。
在设计过程中,应根据高炉的规模和使用条件来确定这些参数,确保结构的强度和稳定性。
3.3 结构施工工艺结构施工工艺包括钢结构的焊接、混凝土的浇筑和养护等。
在施工过程中,应根据设计要求,采用适当的工艺和设备,确保结构的质量和可靠性。
4. 热工设计4.1 热工参数高炉的热工参数包括燃料消耗、风温、炉温、炉压等。
在设计过程中,应根据炼铁工艺和产品品质要求,确定这些参数,确保高炉的热工效果和生产效率。
4.2 热工设备热工设备包括燃烧系统、风机系统、排烟系统等。
在设计过程中,应根据热工参数和炼铁工艺要求,选择适当的设备类型和规格,确保设备的稳定运行和高效能耗。
4.3 热工控制热工控制包括燃烧控制、风量控制、温度控制等。
在设计过程中,应根据热工参数和自动化程度要求,选择适当的控制策略和仪表设备,确保高炉的热工过程稳定可控。
高炉大修施工方案

高炉大修施工方案高炉大修施工方案一、施工前准备:1. 组织编制详细施工计划,明确施工任务和分工。
2. 进行安全预评价,制定安全施工方案和应急预案。
3. 制定施工进度计划,合理安排施工时间和资源。
4. 确保施工人员具备相关资质和技能,进行培训和考核。
5. 配备必要的施工设备和工具,确保施工质量和安全。
二、主要工程内容:1. 检修高炉炉体和炉喉,包括清理炉缸、炉底和炉壁,修补和更换损坏的炉衬。
2. 检修高炉炉腹和炉身,包括清理炉缸和炉腹的积尘和结垢,修补和更换损坏的炉壁和炉腹。
3. 检修高炉鼓风系统,包括清理和更换鼓风机和风管,检修鼓风机的滚动轴承和密封件。
4. 检修高炉煤气系统,包括清理和更换煤气管道和阀门,维修煤气发电机和煤气净化设备。
5. 检修高炉铁水系统,包括清理和更换铁水管道和阀门,检修铁水泄漏和测温设备。
三、施工步骤:1. 准备工作:组织人员、设备和材料到达施工现场,进行安全检查和施工布置。
2. 炉体和炉喉检修:清理炉缸、炉底和炉壁,进行炉衬修补和更换。
3. 炉腹和炉身检修:清理炉缸和炉腹的积尘和结垢,修补和更换炉壁和炉腹。
4. 鼓风系统检修:清理和更换鼓风机和风管,检修鼓风机的滚动轴承和密封件。
5. 煤气系统检修:清理和更换煤气管道和阀门,维修煤气发电机和煤气净化设备。
6. 铁水系统检修:清理和更换铁水管道和阀门,检修铁水泄漏和测温设备。
7. 收尾工作:清洁施工现场,进行施工质量和安全验收。
四、安全措施:1. 确保施工人员的人身安全,配备个人防护装备,遵守相关操作规程。
2. 严格按照施工方案和安全方案进行施工,避免事故和环境污染。
3. 定期进行现场巡视和安全检查,及时发现和处理安全隐患。
4. 配备专职安全监督人员,负责监督施工过程中的安全工作。
五、施工管理:1. 成立施工现场管理小组,负责协调和监督施工进度和质量。
2. 严格执行施工计划和进度计划,确保按时完成施工任务。
3. 进行定期的工程进度会议,及时解决施工过程中的问题和困难。
高炉施工方案
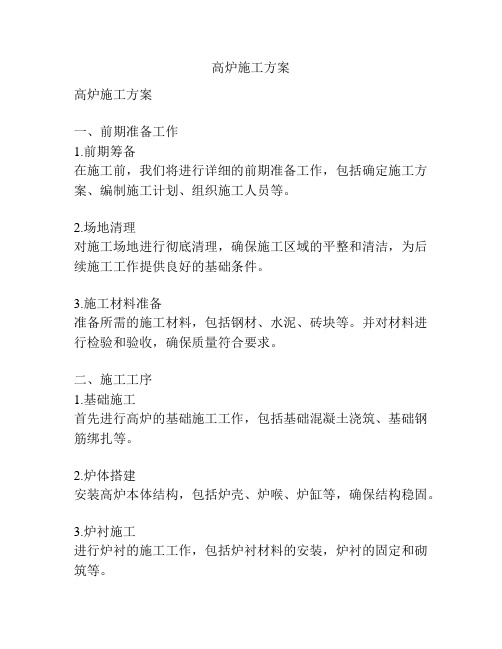
高炉施工方案高炉施工方案一、前期准备工作1.前期筹备在施工前,我们将进行详细的前期准备工作,包括确定施工方案、编制施工计划、组织施工人员等。
2.场地清理对施工场地进行彻底清理,确保施工区域的平整和清洁,为后续施工工作提供良好的基础条件。
3.施工材料准备准备所需的施工材料,包括钢材、水泥、砖块等。
并对材料进行检验和验收,确保质量符合要求。
二、施工工序1.基础施工首先进行高炉的基础施工工作,包括基础混凝土浇筑、基础钢筋绑扎等。
2.炉体搭建安装高炉本体结构,包括炉壳、炉喉、炉缸等,确保结构稳固。
3.炉衬施工进行炉衬的施工工作,包括炉衬材料的安装,炉衬的固定和砌筑等。
4.加热设备安装安装高炉的加热设备,包括高炉燃烧器、加热炉等。
5.管道布置布置高炉内的各种管道,包括风管、水管等,确保高炉运行期间的正常供气供水。
6.电气设备安装安装高炉的电气设备,包括电缆、电机等,确保高炉的正常运行。
7.防腐保温处理对高炉进行防腐和保温处理,保证高炉的正常使用寿命。
8.试车调试进行高炉的试车调试工作,包括点火、升温等,确保高炉的性能和安全。
三、安全保障措施1.施工现场设置安全警示标志,划定施工区域,禁止无关人员进入施工区域。
2.施工人员必须佩戴安全帽、安全鞋等个人防护装备,并进行必要的安全培训。
3.施工中必须遵守现场施工规定,禁止乱堆乱放材料,保持作业现场的整洁和安全。
4.对施工现场进行定期巡查,及时发现和排除安全隐患。
5.配备安全监测设备,对施工过程进行监控,确保施工的安全性。
四、质量控制1.根据相关技术规范和标准,对施工过程进行质量控制,并进行必要的检测和验收。
2.对施工材料进行检验和验收,确保质量符合要求。
3.加强施工人员的技术培训和管理,确保施工的质量和安全。
4.定期进行施工质量的检查和评估,及时发现和处理质量问题。
五、环保措施1.根据国家环保要求,进行高炉施工过程中的环保措施,包括减少粉尘和废气的排放等。
2.配备相应的环保设备,如除尘器等,对高炉产生的废气进行处理。
高炉施工方案

第1篇
高炉施工方案
一、项目背景
随着我国经济的持续快速发展,钢铁产业作为国民经济的重要支柱产业,其产能和需求不断扩大。为满足市场需求,提高企业经济效益,某钢铁公司决定新建一座高炉。为确保高炉施工的顺利进行,特制定本施工方案。
二、施工目标
1.确保施工安全,降低安全事故发生率。
2.保证施工质量,满足设计要求。
1.建立健全质量、安全、环保管理体系,确保施工过程中各项措施得到有效执行。
2.加强施工现场监督检查,对施工过程进行动态管理。
3.对施工现场进行定期安全、环保检查,发现问题及时整改。
4.提高施工人员质量、安全、环保意识,加强培训和教育。
八、验收
工程完成后,组织相关单位进行验收,确保工程质量满足设计要求。
本施工方案旨在为高炉施工提供全面、严谨的指导,以确保工程顺利进行。在实际施工过程中,应结合现场实际情况,灵活调整施工方法及措施。全体施工人员应严格遵守国家法律法规,确保施工安全、质量、进度及环保目标的实现。
第2篇
高炉施工方案
一、项目概述
本高炉施工项目为响应我国钢铁产业升级和结构调整的要求,旨在提高生产效率,降低能耗,提升企业竞争力。为确保施工顺利进行,特制定本方案。以下内容将详细阐述施工过程中的关键环节、技术要求及管理措施。
4.调试与试运行
(1)制定调试与试运行方案,明确调试流程和职责分工。
(2)对设备进行单机调试、联动调试,确保设备正常运行。
(3)按照试运行方案,分阶段进行高炉烘炉、煮炉及试运行。
5.环保设施施工
(1)严格按照环保设计要求,进行环保设施土建及设备安装。
(2)对环保设施进行调试,确保其正常运行,满足环保要求。
(3)加强施工现场环保管理,降低对周边环境的影响。
高炉工程基础施工方案

高炉工程基础施工方案一、概述高炉是冶金工业中用于炼铁的重要设备,其基础施工是高炉建设的重要环节。
高炉基础施工方案的编制是为了确保高炉建设质量和安全,合理安排施工任务,有效管理施工过程,提高施工效率。
本施工方案以某高炉基础工程为例,结合工程具体情况,对高炉基础施工进行了合理规划和安排,以期能为高炉建设提供可靠的技术支持和施工保障。
二、工程概况某高炉基础工程位于中国北方地区,总投资约为10亿元人民币。
项目规模大,施工周期长,技术要求高,土质条件复杂,是一项重大的基础工程建设项目。
基础主要包括高炉底冷风布设备及敷设基础、高炉本体基础、炉壳、高炉平设备基础等。
三、施工方案1. 高炉底冷风布设备及敷设基础1.1 设备安装根据设计要求,先将底冷风设备进行安装,确保设备的水平和垂直度,保证设备安装准确无误。
1.2 基础敷设以设备为中心,按照设计图纸要求,进行基础的敷设和浇筑。
确保基础的平整、牢固和防水性。
2. 高炉本体基础2.1 地基处理根据地基勘测的情况,对地基进行处理,确保地基的承载力和稳定性。
2.2 基础开挖按照设计图纸要求,进行基础的开挖和挖土作业。
并对挖土的过程进行监测和记录。
2.3 基础浇筑在基础开挖完毕后,进行基础的混凝土浇筑。
确保混凝土品质和浇筑厚度符合设计要求。
3. 高炉炉壳基础3.1 基础图纸要求按照设计图纸要求,进行炉壳基础的布置和浇筑。
3.2 钢筋焊接对基础的钢筋进行焊接工作,确保钢筋的牢固和连接质量。
3.3 碾压和表面处理在混凝土浇筑完毕后,进行基础的碾压和表面处理,确保基础的平整和牢固。
4. 高炉平设备基础4.1 设备布置根据设计要求,进行设备的布置和安装工作,确保设备的准确位置。
4.2 基础浇筑在设备布置完毕后,进行基础的混凝土浇筑,确保基础的牢固和防水性。
4.3 环境保护在施工过程中,要严格遵守环境保护规定,确保施工过程对环境的影响最小化。
四、安全管理在施工过程中,要根据高炉基础施工的特点和工艺要求,制定详细的安全管理措施和操作规程,确保施工人员的安全,减少施工事故的发生。
高炉土建工程施工方案

高炉土建工程施工方案介绍高炉是冶金行业常见的设备,主要用于炼铁过程中将铁矿石还原成熔融铁的设备。
高炉的建设需要涉及到许多土建工程,包括高炉基础、炉壳、渣口、风口、煤气洗涤器等。
本文详细介绍高炉土建工程施工方案。
施工前准备在施工前,需要进行详细的施工方案和施工计划编制工作以及现场勘探、地基测量等工作。
在开工前还需核实各种材料、设备的库存,采购和租赁设备,并且制定施工安全计划、环保方案和质量验收标准。
施工流程高炉土建工程的施工通常可以分为以下步骤:1. 高炉基础施工首先,需要按照设计图纸,在现场建立起高炉基础的构造。
这个过程中需要使用钢筋框架、混凝土等材料。
施工中要注意混凝土的浇筑技术,保证基础质量和密实度,并做好保温、防水和防腐的措施。
2. 炉壳制作炉壳是高炉的主体结构,是整个高炉建设中最为重要的部分。
炉壳的制作需要按照高炉的设计图纸,使用合适的钢材,构建出准确、牢固的结构。
炉壳制作中还需要安装隔离层、保温层和气体锁定层,同时实施有效的质量控制和质检程序。
3. 渣口和风口的制作在高炉熔炼的过程中,需要通过渣口和风口来进行冶炼作用。
因此,在高炉土建工程中,渣口和风口是不可或缺的一步。
渣口和风口的制作需要对钢材进行加工和焊接,确保高炉的正常运作和冶炼效果。
4. 煤气洗涤器的构造煤气洗涤器是将高炉炉顶煤气中的粉尘、烟雾等杂质清洗除去的部件。
在高炉建设中,煤气洗涤器的构造和安装也不可缺少。
煤气洗涤器的制作需要按照设计方案,使用合适的材料进行制作和安装,并保证其稳定性和安全性。
施工注意事项在高炉土建工程的施工过程中,需要特别注意以下事项:•安全问题是重中之重,施工人员必须时刻保持注意,遵守各项安全规定;•钢筋混凝土浇注需要按照规范操作,保证基础质量和安全性;•高炉主体结构的施工需要进行严密的质检,确保结构牢固;•设备和材料的安装要按照设计方案进行,保证其耐久性和可靠性。
施工完结高炉土建工程施工完成后,需要进行检验、调试、验收等过程,确保高炉的正常运作。
高炉工程安装施工方案

高炉工程安装施工方案高炉工程是冶金行业中重要的设备之一,主要用于生产铁和钢铁。
在高炉的安装施工过程中,需要进行详细的方案制定,确保施工工作的顺利进行。
下面是一份高炉工程安装施工方案,供参考。
一、项目背景高炉工程是钢铁公司的新建项目,旨在扩大生产能力,提高钢铁产量。
项目总投资为X亿元,计划建设一座X立方米的高炉。
二、施工方案制定1.概述根据项目需求和施工条件,制定施工方案。
方案包括高炉工程的总体布置、主要设备的安装方法、工期计划、安全措施等内容。
2.工作组织成立高炉工程施工组织小组,负责方案的制定和实施。
该小组由项目经理、施工经理、技术员、质检员等专业人员组成。
每个人员的职责需明确,并制定相应的工作计划。
3.工期计划根据工程量和施工条件,制定详细的工期计划。
包括各个施工阶段的时间安排、人力资源需求、材料配送等。
确保工程按时完成。
4.安装方法高炉工程的安装包括总体设备的安装和各个细节的施工安装。
根据设备的特点和施工条件,制定相应的安装方法。
在施工过程中,保证设备的准确安装,避免任何损坏。
5.安全措施高炉工程的施工过程中存在一定的安全隐患,需要采取相应的安全措施。
制定详细的安全规程和作业指导书,保证施工人员的安全。
其中包括工人的防护设备、设备的安全操作、施工现场的安全管理等。
6.质量控制高炉工程是重大工程,质量控制至关重要。
建立完善的质量控制体系,对施工过程中的每一个环节进行严格的把关。
包括材料的采购、设备的安装、工艺流程的控制等。
确保高炉的运行效果达到设计要求。
7.操作培训完成高炉工程的安装后,需要对操作人员进行培训,使其熟悉设备的操作和维护。
制定详细的操作规程和维护手册,逐一进行培训。
确保设备的正常使用和维护。
三、总结高炉工程安装施工方案的制定是保证工程顺利进行的重要步骤。
在方案中明确每个工作环节的职责,制定详细的工作计划,采取必要的安全措施和质量控制措施。
确保工程安全、质量和进度的达到设计要求。
大高炉工程施工方案
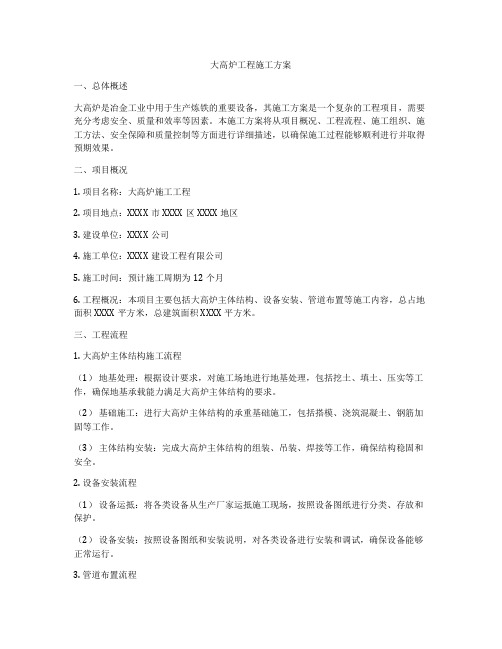
大高炉工程施工方案一、总体概述大高炉是冶金工业中用于生产炼铁的重要设备,其施工方案是一个复杂的工程项目,需要充分考虑安全、质量和效率等因素。
本施工方案将从项目概况、工程流程、施工组织、施工方法、安全保障和质量控制等方面进行详细描述,以确保施工过程能够顺利进行并取得预期效果。
二、项目概况1. 项目名称:大高炉施工工程2. 项目地点:XXXX市XXXX区XXXX地区3. 建设单位:XXXX公司4. 施工单位:XXXX建设工程有限公司5. 施工时间:预计施工周期为12个月6. 工程概况:本项目主要包括大高炉主体结构、设备安装、管道布置等施工内容,总占地面积XXXX平方米,总建筑面积XXXX平方米。
三、工程流程1. 大高炉主体结构施工流程(1)地基处理:根据设计要求,对施工场地进行地基处理,包括挖土、填土、压实等工作,确保地基承载能力满足大高炉主体结构的要求。
(2)基础施工:进行大高炉主体结构的承重基础施工,包括搭模、浇筑混凝土、钢筋加固等工作。
(3)主体结构安装:完成大高炉主体结构的组装、吊装、焊接等工作,确保结构稳固和安全。
2. 设备安装流程(1)设备运抵:将各类设备从生产厂家运抵施工现场,按照设备图纸进行分类、存放和保护。
(2)设备安装:按照设备图纸和安装说明,对各类设备进行安装和调试,确保设备能够正常运行。
3. 管道布置流程(1)管道预制:将各类管道按照图纸要求进行预制,包括切割、焊接、涂漆等工作。
(2)管道安装:将预制好的管道按照图纸要求进行布置和连接,确保管道稳固和通畅。
四、施工组织1. 领导机构:设立项目部,由项目经理负责整个施工工程的组织和管理工作。
2. 分包管理:根据施工内容和工程进度,将工程分成若干分包,分别由专业施工队伍负责。
3. 人员配备:项目部设立施工人员、安全管理人员、质量检测人员等岗位,确保每个工程环节有专业的人员负责。
4. 设备配备:根据施工需要,配备各类起重机、混凝土搅拌机、焊接设备等施工机械设备。
高炉土建工程施工方案

一、工程概况本工程为某钢铁有限公司高炉土建工程,主要内容包括高炉本体、炉顶设备基础、炉前平台、炉后平台、炉身平台、出铁场、冷却水系统、通风系统等。
工程总投资XX万元,工期为XX个月。
二、施工组织设计1. 组织机构成立项目经理部,下设工程技术部、施工管理部、质量安全管理部、物资供应部、财务部等职能部门。
项目经理为工程总负责人,各部门负责人直接向项目经理汇报工作。
2. 施工准备(1)技术准备:组织技术人员进行现场勘查,了解工程地质、水文、气象等条件,制定施工组织设计,编制施工方案。
(2)物资准备:根据施工方案,提前购置、租赁各类施工设备、材料,确保施工顺利进行。
(3)人员准备:组织施工队伍,进行技术培训和安全教育,提高施工人员素质。
三、施工方法及技术措施1. 施工流程(1)土方开挖:根据设计要求,进行土方开挖,确保高炉基础施工顺利进行。
(2)基础施工:按照设计图纸,进行基础钢筋绑扎、混凝土浇筑,确保基础质量。
(3)主体结构施工:按照设计要求,进行高炉本体、炉顶设备基础、炉前平台、炉后平台、炉身平台等主体结构的施工。
(4)配套设施施工:按照设计要求,进行冷却水系统、通风系统等配套设施的施工。
2. 施工技术措施(1)土方开挖:采用机械开挖,确保开挖深度、宽度、坡度符合设计要求。
(2)基础施工:采用现浇混凝土,严格按照施工规范进行施工,确保基础质量。
(3)主体结构施工:采用钢结构、钢筋混凝土结构,严格按照施工规范进行施工,确保主体结构质量。
(4)配套设施施工:按照设计要求,进行冷却水系统、通风系统等配套设施的施工,确保系统运行稳定。
四、质量控制措施1. 严格按设计要求进行施工,确保工程质量。
2. 加强原材料、半成品、成品的质量检验,确保工程质量。
3. 严格执行施工规范,确保施工过程符合要求。
4. 加强施工现场管理,确保施工环境整洁、安全。
五、安全措施1. 制定安全生产责任制,明确各级人员的安全责任。
2. 加强施工现场安全管理,确保施工安全。
- 1、下载文档前请自行甄别文档内容的完整性,平台不提供额外的编辑、内容补充、找答案等附加服务。
- 2、"仅部分预览"的文档,不可在线预览部分如存在完整性等问题,可反馈申请退款(可完整预览的文档不适用该条件!)。
- 3、如文档侵犯您的权益,请联系客服反馈,我们会尽快为您处理(人工客服工作时间:9:00-18:30)。
山西通才工贸有限公司淘汰落后设备技术改造工程1580m3高炉炉壳施工方案编制:年月日审核:年月日批准:年月日华北冶建工程建设有限公司建邦项目部目录1、编制依据 (3)2、工程概况 (3)3、施工部署 (3)4、编制材料计划 (3)5、工厂制作 (5)6、结构运输 (12)7、高炉炉壳拼装 (12)8、高炉炉壳安装 (22)9、安全注意事项 (30)10、措施材料 (34)11、工机具清单 (35)1580m3高炉炉壳施工方案1 编制依据1.1山西通才工贸有限公司1580m3高炉安装工程合同。
1.2国家及行业现行施工标准、规程、规范及质量验评标准。
1.3钢结构施工设计总说明,《钢结构工程施工质量验收规范》(GBJ50205-2001)、《冶金机械设备安装工程施工及验收规范》(YBJ208-85)、《炼铁工艺炉壳结构技术规范》(GB50567-2010)。
1.4 我公司所能调动的施工技术力量。
1.5 施工现场情况。
2 工程概况:本施工方案为高炉炉壳的开孔、卷制、拼装、吊装、找正及焊接等内容。
3 施工部署:在高炉正南方向布置一台250t履带吊为主吊(主要进行高炉炉壳的吊装工作),另配小吊车配合(主要进行高炉炉壳的拼装工作)。
在正北方向布置一台150t履带吊作为主吊(主要进行高炉下部框架的吊装工作),另配小车配合。
高炉在安装过程中,一边安装炉壳,一边安装水冷系统,当炉喉钢砖安装完后,炉内开始砌筑,外部则将热风围管整体套上,形成有序地流水作业,同时,在不影响炉体安装的前提下,安装框架和各层平台,进行平行作业,以达到最佳工效。
但夜间不进行吊装作业。
4 编制材料计划:4.1 根据设计施工图纸编制钢材计划,高炉壳体材料定尺订货进料,由于高炉炉壳定尺,需提前订货。
4.2 铸件、锻压件提前评审协作厂家,签订合同,委托加工。
注:炉壳材料订货尺寸以炉壳厚度中径为依据,请业主复核。
详见高炉炉壳分带图。
注:粗虚线为高炉炉壳分带线,细实线为水冷壁分段线。
1~3带炉壳板厚为50mm、4~5带15~16带及带炉壳板厚为55 mm、6~14炉壳带板厚为45mm、炉底板厚为20mm、炉底环板厚为55mm图一高炉炉壳主视图及分带图(本图根据设计图号S1653JG6.2.1-3、4和冷却壁订货图绘制)5 工厂制作5.1 场地准备高炉炉壳的卷制在加工厂内进行制作,加工厂内场地平整,安装制作设备,如龙门吊车、卷板机、切割机、焊机、矫正机、型钢组对机、喷丸装置、喷漆装置、空压机等。
设备安装先进行试运行,合格后投入使用。
炉壳以零部件形式分块出厂,运输到现场进行拼装和安装。
在新建制作场地搭设临建,包括办公室、焊材库、金属室、工具库、开水房、厕所、金加工间、警卫室、配电室等等。
搭设制作、组装、预装用钢平台,设置材料堆场,电焊机棚,喷砂场等等。
安装临时水、电,制作用电负荷约400kw。
布置消防设施。
硬化道路,确保运输通畅,大型吊车、拖车能顺利进出。
场地必须有排水沟,排水沟能确保生产用水和暴雨积水能及时排出。
制作场地周围用铁丝网设临时围栏,并有场地照明。
5.2 制作程序制作顺序有先后,即每带炉壳的摆放→钢板的切边→钢板开孔→钢板的定位及编号→钢板的卷制→炉壳的预拼装。
5.3 炉壳工厂制作过程概述高炉炉壳制作的技术要求高炉炉壳制作应符合《冶金机械设备安装工程施工及验收规范——炼钢设备》及行业标准(YB4079-91)的有关规定,框架和其它结构要求符合GB 50205—2001《钢结构工程质量验收规程》的规定。
高炉炉壳在制造厂分块制作,预装合格后,在制造厂开孔,分块出厂。
5.3.1 材料检验:材料进厂后,应进行全面检验,主要内容有:定尺材料检查实际尺寸和余量,所有板材均检验厚度。
L1-1.51000直尺①轮廓线;②加工线;③检查线;④半自动切割机轨道线。
轮廓线与检查线间的距离为50mm,半自动切割机轨道线的距离根据设备的性能来确定。
划线后应在各个线印上打上冲印以保证切割精度。
在各个构件上应标明标号。
已划线号料完毕的钢板,检查合格后,方允许切割及边缘加工。
5.3.3 切割钢板切割后边缘必须平整,切割线应符合设计尺寸,切割后尺寸极限偏差±1mm,两对角线长度之差不得大于3mm,并考虑焊接时焊缝的收缩余量。
本工程下料主要方法是氧-乙炔气割,用数控自动或半自动切割机,厚度小于12mm的钢板且在环境温度允许时用剪板机下料。
在钢板卷制之前应先进行开孔工作,根据冷却壁水管孔在炉壳上的放样图来进行在钢板上实际放样画图,并把每一带炉壳的0°、90°、180°、270°的相对位置标明打上样冲眼,以便于安装。
坡口加工用自动切割,手工修理。
5.3.4 卷板加工炉壳展开后为扇形或矩形,为了准确的加工出锥形炉壳和圆柱,卷板按下列顺序进行:根据一带钢板的宽度L和扇形板两端的弯曲半径之差(d1-d2)计算出滚床上辊的斜度:i=(d1-d2)/L实际i值应稍有增加,因钢板有回弹,第一块板滚圆后进行检查,以实际测量值确定上辊斜度。
用粉线在钢板的内表面上,以展开面中心将钢板分成若干等份并划出等份的中心线。
滚圆后的钢板用弦长大于1500mm的样板进行检查内弧,钢板与样板的间隙不应大于2mm(见图五)。
图五检验卷制炉壳的样板示意图修圆方法可以用火焰、压力机、夹具等方法进行修圆,严禁用锤打。
由于此炉壳的钢板比较厚,用卷板机进行卷制时,钢板的两侧约有300mm 的直边,考虑到此工程的工期紧张,因此,采购炉壳钢板时,在每块定尺的钢板上加长600mm来消除上述问题。
5.3.5 工厂预装外壳预装配应在专门设置的预装平台上进行,预装平台表面高低差不得大于2mm,并应在每组装一段前检测其水平度,调整合乎要求后,方可进行组装工作。
在平台上放出高炉炉壳中心线,组装时,每带均放出内圆边线(设计以内圆直径为准),焊接限位板。
外壳预装配从下往上按顺序进行,每次在平台上组装一圈,逐圈检查合格后,将组装好的单圈再叠加组装,最多为3圈,检查每圈炉皮的高度,用桥尺和吊线坠法检查外壳上口中心,外壳钢板圈的最大直径与最小直径之差;外壳钢板圈上口水平差,对口错边量;坡口端部间隙等并作好记录,提供给安装单位,作为现场安装的依据,并打上标记,焊好纵缝和环缝定位器,然后拆开下面两圈作为成品,最上面一圈要留作下一组装段的底圈。
图六上下对口限位装置单对材料: 钢板 -30 0.0045m2每块外壳钢板上焊脚手架挂耳、夹具、固定器等。
图七炉壁脚手架挂耳图单个材料:钢板-6 0.045m2脚手架挂耳每隔约3000mm弧长焊上一个,距离上口约1000mm,便于操作,内外两面设置,遇焊缝时要错开焊缝~200mm,并对其间距作适当调整。
夹具固定应在预装时设置,在每块钢板上,横缝每2m弧长设一对,还要注意相邻带的排列关系,使上、下带配置成一组,立缝每1m弧长设一对,每带立缝一般设2~3对,固定块钢板距边缘为180mm。
炉壳预装配合格后,应标出构件标号和对位中心线(以0°线为准),壳体应标出十字中心线,在拆开的接头处或上、下圈间应用油漆和钢印作出明显标记,并提供展开的组装图作为现场安装的依据。
炉壳预拼装允许偏差:炉底板预拼装允许偏差:径的1.3倍,每一组孔的偏差不得大于±2mm,切口不得有裂纹和大于1mm的缺棱,切割截面与钢材表面不垂直度不得大于1mm。
高炉炉壳与铁口框、风口法兰、上升管、检修门、人孔,都应在炉壳安装完毕后进行现场开口,其质量应符合下列要求:铁口框架的法兰面、中心位置依设计图纸要求,沿炉壳圆周以规定的起点分度,极限偏差为±4′,中心距、标高偏差为±5mm。
法兰面水平中心线的水平度,在法兰全宽内水平差为3mm。
风口法兰应根据法兰面上的水平中心线和垂直中心线的标记组装在炉壳上,并经检查后可焊接固定,风口法兰定位支架不拆除作为安装的依据。
法兰面风口中心位置应沿炉壳圆周以规定的起点按角度均匀等分,极限偏差为±4′(此值根据图纸实际尺寸计算),中心标高偏差为±3mm,全部法兰面风口中心应在同一个水平面内,高低差不得大于5mm,且相邻两法兰面不得大于3mm。
各相对法兰风口中心的水平连线与炉体中心线应相交,公差为10mm。
法兰面水平中心线的水平度在法兰直径内公差为2mm。
法兰的倾角,对设计规定角度的偏斜,挂设铅垂线检查,边长L极限偏差为±2mm。
法兰伸出炉壳表面距离,在法兰上端检查,极限偏差为+5mm~0mm。
高炉系统工艺钢结构成品出厂前应根据其几何形状进行加固,加固后应标出重心位置和起重吊耳的配置焊接,以保证在运输、装卸施工过程中不产生永久变形。
炉壳每带钢板分别由技术检查部门进行验收,并在每块钢板上打上合格标记。
高炉系统钢结构工程由制造厂绘制施工详图,安装卡具布置图(包括挂耳、固定铁件、吊耳、组装用的各种夹具、冲子、间隙板、引弧板等详图及材料表。
种类夹具、冲子间隙板、引弧板按安装工程需要加工随构件配套出厂,固定铁件、吊耳(按整带吊装设置)挂耳在工厂焊接在构件上。
制造厂向安装部门提供如下资料:A炉皮施工详图B安装卡具布置图C预装配检查结果记录及预装配时各带钢板每块安装部位顺序编号图。
D构件合格证并附钢材材质证明书要盖有红图章。
注:在绘制施工详图如发现与上述要求有矛盾,再予以协商。
6 结构运输本工程根据炉带分片尺寸和重量选用50吨拖车进行运输。
炉壳构件在运输过程中应用胎具或道木垫平,绑扎受力均匀,防止变形,同时钢绳应绑扎牢固,用手拉葫芦封车。
运输过程中做到不超载、不超速,不违章。
结构运输前与交通管理部门联系,尽量排除行政干扰。
7 高炉炉壳拼装由于高炉炉壳体积大,其必须在施工现场进行拼装,根据施工现场的实际情况,为不影响其他工程的进行,炉壳拼装场地与主吊车站位设在高炉基础的北侧(临近厂区马路)。
(详见高炉安装布置图)高炉炉壳拼装与吊装直接相关,用250t履带吊作主吊,增加地面拼装量,尽量减少空中作业,各带吊装重量如下:①炉底板约26.0t,②第1带约37.5t,③第2带约37.3t,④第3带约19.2t,⑤第4带约35.7t,⑥第5带约16.5t,⑦第6带约22.5t,⑧第7带约21.5t,⑨第8带约26t,⑩第9带约24.8t,⑾第10带约22.5t,⑿第11带约21.2t,⒀第12带约23.6t,⒁第13带约21.7t,⒂第14带约16.8t,⒃15~16带约26.5t,以上为炉壳净重,不包括临时走台、加固支撑、吊钩等重量(约4t)。
根据吊车的性能,部分炉壳可拼成两带进行吊装。
厂区马路高炉基础西出铁场东出铁场主控楼重力除尘器基础热风炉系统场地厂区马路铁水车线路此基础暂不施工1#炉壳组对平台2#炉壳组对平台250吨履带吊组对炉壳汽车吊土建单位钢筋棚图八 高炉炉壳拼装场地及250t 履带吊布置平面图CC1400型250t履带吊车性能摘录,75%图九 250t履带吊基本尺寸图图十高炉吊装立面图7.1 搭设拼装平台现场需设两座拼装小平台或一座大平台,以扩大工作面。