第一章数控加工编程基础.pptx
合集下载
《数控加工基础》PPT幻灯片PPT

数控编程: 根据零件图和制定的工艺内容,再按照所用数控系统规定的指令代码 及程序格式进行数控编程;
程序传输: 将编写好的程序通过传输接口,输入到数控机床的数控装置中。调整
好机床并调用该程序后,就可以加工出符合图纸要求的零件。
手工编程的内容和步骤
选择并 确定进 行数控 加工的
内容
数控加 工的工
艺分析
1. 坐标轴的运动方向及其命名
统一规定数控机床坐标轴及其运动的方向,可使编程方便,并 使编出的程序对同类型机床有通用性。同时也给 维修和使用带来极 大的方便。ISO和我国都拟定了命名的标准。
• 进给运动坐标系
ISO和中国标准规定: – 数控机床的每个进给轴(直线进给、圆进给) 定义为
坐标系中的一个坐标轴。
+X +Z
• Y坐标 (最后确定的坐标)
利用已确定的X.Z坐标的正方向,用右手定则 或右手螺旋法则,确定Y坐标的正方向。
• 右手定则:大姆指指向+X,中指指向+Z,则 +Y方向为食指指向。
• 右手螺旋法则:在X Z平面,从Z至X,姆指所 指的方向为+y。
2 坐标系
编程总是基于某一坐标系统的,为了编程方 便,一律假定工件不动,刀具运动,即编程 坐标系。因此,弄清楚数控机床坐标系和工 件坐标系的概念及相互关系是至关重要的。
控系统的自动控制所取代。
阅读零件图纸: 充分了解图纸的技术要求,如尺寸精度、形位公差、表面粗糙度、工 件的材料、硬度、加工性能以及工件数量等;
工艺分析: 根据零件图纸的要求进行工艺分析,其中包括零件的结构工艺性分析、 材料和设计精度合理性分析、大致工艺步骤等;
数学处理和制定工艺: 根据工艺分析制定出加工所需要的一切工艺信息——如:加工工艺路 线、工艺要求、刀具的运动轨迹、位移量、切削用量(主轴转速、进 给量、吃刀深度)以及辅助功能(换刀、主轴正转或反转、切削液开 或关)等,并填写加工工序卡和工艺过程卡;
程序传输: 将编写好的程序通过传输接口,输入到数控机床的数控装置中。调整
好机床并调用该程序后,就可以加工出符合图纸要求的零件。
手工编程的内容和步骤
选择并 确定进 行数控 加工的
内容
数控加 工的工
艺分析
1. 坐标轴的运动方向及其命名
统一规定数控机床坐标轴及其运动的方向,可使编程方便,并 使编出的程序对同类型机床有通用性。同时也给 维修和使用带来极 大的方便。ISO和我国都拟定了命名的标准。
• 进给运动坐标系
ISO和中国标准规定: – 数控机床的每个进给轴(直线进给、圆进给) 定义为
坐标系中的一个坐标轴。
+X +Z
• Y坐标 (最后确定的坐标)
利用已确定的X.Z坐标的正方向,用右手定则 或右手螺旋法则,确定Y坐标的正方向。
• 右手定则:大姆指指向+X,中指指向+Z,则 +Y方向为食指指向。
• 右手螺旋法则:在X Z平面,从Z至X,姆指所 指的方向为+y。
2 坐标系
编程总是基于某一坐标系统的,为了编程方 便,一律假定工件不动,刀具运动,即编程 坐标系。因此,弄清楚数控机床坐标系和工 件坐标系的概念及相互关系是至关重要的。
控系统的自动控制所取代。
阅读零件图纸: 充分了解图纸的技术要求,如尺寸精度、形位公差、表面粗糙度、工 件的材料、硬度、加工性能以及工件数量等;
工艺分析: 根据零件图纸的要求进行工艺分析,其中包括零件的结构工艺性分析、 材料和设计精度合理性分析、大致工艺步骤等;
数学处理和制定工艺: 根据工艺分析制定出加工所需要的一切工艺信息——如:加工工艺路 线、工艺要求、刀具的运动轨迹、位移量、切削用量(主轴转速、进 给量、吃刀深度)以及辅助功能(换刀、主轴正转或反转、切削液开 或关)等,并填写加工工序卡和工艺过程卡;
数控加工编程基础-PPT课件-PPT课件

下 一 页 上 一 页
之间实现通讯用的接口。随着DNC数控技术的发展,
数控机床已成为无人控制工厂的基本组成单元。
结
束
第1章 数控加工编程基础 我国在20世纪70年代初期,当时是采用分立元件, 性能不稳定,可靠性差。 《 1980年在引进、消化、吸收国外先进技术的基础 数 控 上,北京机床研究所又开发出BS03经济型数控和 编 BS04全功能数控系统,航天部706所研制出MNC864 程 与 数控系统。 操 作 20世纪90年代末,华中数控自主开发出基于PC-NC 》 胡 的HNC数控系统,达到了国际先进水平,加大了我国数 毅 控机床在国际上的竞争力度。 光
上 一 页
下 一 页
结
束
第1章 数控加工编程基础
《 数 控 编 程 与 操 作 》 胡 毅 光
Z X Z X Y
上 一 页
下 一 页
结
束
图1-2 数控机床的控制坐标数 (a) 两坐标数控车床;(b) 三坐标数控铣床
第1章 数控加工编程基础
《 数 控 编 程 与 操 作 》 胡 毅 光
上 一 页
下 一 页
径 半 具 刀
上 一 页
Y B
编程轨迹
下 一 页
结
X
刀具 ( c )
束
第1章 数控加工编程基础 刀补是指数控加工中的刀具半径补偿和刀具长度 补偿功能。 《 数 控 编 程 与 操 作 》 胡 毅 光
刀心轨迹 Y 4 3 2 1 0 1 2 3 4 5 X0 (a ) (b ) R A A
径 半 具 刀
上 一 页
下 一 页
结
束
第1章 数控加工编程基础 如某步进电机驱动的数控轴,其脉冲当量为0.002 mm,若数控装置在0.5分钟内发送出20 000个进给指令 《 数 控 编 程 与 操 作 》 胡 毅 光
之间实现通讯用的接口。随着DNC数控技术的发展,
数控机床已成为无人控制工厂的基本组成单元。
结
束
第1章 数控加工编程基础 我国在20世纪70年代初期,当时是采用分立元件, 性能不稳定,可靠性差。 《 1980年在引进、消化、吸收国外先进技术的基础 数 控 上,北京机床研究所又开发出BS03经济型数控和 编 BS04全功能数控系统,航天部706所研制出MNC864 程 与 数控系统。 操 作 20世纪90年代末,华中数控自主开发出基于PC-NC 》 胡 的HNC数控系统,达到了国际先进水平,加大了我国数 毅 控机床在国际上的竞争力度。 光
上 一 页
下 一 页
结
束
第1章 数控加工编程基础
《 数 控 编 程 与 操 作 》 胡 毅 光
Z X Z X Y
上 一 页
下 一 页
结
束
图1-2 数控机床的控制坐标数 (a) 两坐标数控车床;(b) 三坐标数控铣床
第1章 数控加工编程基础
《 数 控 编 程 与 操 作 》 胡 毅 光
上 一 页
下 一 页
径 半 具 刀
上 一 页
Y B
编程轨迹
下 一 页
结
X
刀具 ( c )
束
第1章 数控加工编程基础 刀补是指数控加工中的刀具半径补偿和刀具长度 补偿功能。 《 数 控 编 程 与 操 作 》 胡 毅 光
刀心轨迹 Y 4 3 2 1 0 1 2 3 4 5 X0 (a ) (b ) R A A
径 半 具 刀
上 一 页
下 一 页
结
束
第1章 数控加工编程基础 如某步进电机驱动的数控轴,其脉冲当量为0.002 mm,若数控装置在0.5分钟内发送出20 000个进给指令 《 数 控 编 程 与 操 作 》 胡 毅 光
数控编程教程(共95张PPT)

因此,这种格式具有程序简单、可读性强,易于检查等优点。
第二节 数控编程常用的指令及其格式
主程序、子程序
在一个零件的加工程序 中,若有一定量的连续 的程序段在几处完全重 复出现,则可将这些重 复的程序串单独抽出来, 按一定的格式做成子程 序。
11/7/2023
-25-
第二节 数控编程常用的指令及其格式
码的程序段中有效; ● 模态M功能(续效代码):一组可相互注销的 M功
能,这些功能在被同一组的另一个功能注销前一直 有效。
第三章 数控系统编程指令体系
模态 M功能组中包含一个缺省功能,系统上电时 将被初始化为该功能。
M 功能还可分为前作用 M 功能和后作用 M 功能二类。 ● 前作用 M 功能:在程序段编制的轴运动之前执行; ● 后作用 M 功能:在程序段编制的轴运动之后执行。
迹生成功能进行数控编程。
4.后置代码生成 后置处理的目的是形成数控指令文件,利用CAM系统提供的后置
处理器可方便地生成和特定机床相匹配的加工代码。
5.加工代码输出
第一节 数控编程的几何基础
1.1 机床坐标系 为了确定机床个运动部件的运动方向和移动距离,需要
在机床上建立一个坐标系,这个坐标系就叫做机床坐标系 1.2 机床坐标轴及其方向
常用地址码的含义如表所示
机能 程序号 顺序号 准备机能
坐标指令
进给机能 主轴机能 刀具机能
辅助机能
补偿 暂停 子程序调用 重复 参数
地址码
O N G X.Y.Z A.B.C.U.V.W R I.J.K F S T
M B
H.D P.X
I P.Q.R
意义
程序编号 顺序编号 机床动作方式指令 坐标轴移动指令 附加轴移动指令 圆弧半径 圆弧中心坐标 进给速度指令 主轴转速指令 刀具编号指令
第二节 数控编程常用的指令及其格式
主程序、子程序
在一个零件的加工程序 中,若有一定量的连续 的程序段在几处完全重 复出现,则可将这些重 复的程序串单独抽出来, 按一定的格式做成子程 序。
11/7/2023
-25-
第二节 数控编程常用的指令及其格式
码的程序段中有效; ● 模态M功能(续效代码):一组可相互注销的 M功
能,这些功能在被同一组的另一个功能注销前一直 有效。
第三章 数控系统编程指令体系
模态 M功能组中包含一个缺省功能,系统上电时 将被初始化为该功能。
M 功能还可分为前作用 M 功能和后作用 M 功能二类。 ● 前作用 M 功能:在程序段编制的轴运动之前执行; ● 后作用 M 功能:在程序段编制的轴运动之后执行。
迹生成功能进行数控编程。
4.后置代码生成 后置处理的目的是形成数控指令文件,利用CAM系统提供的后置
处理器可方便地生成和特定机床相匹配的加工代码。
5.加工代码输出
第一节 数控编程的几何基础
1.1 机床坐标系 为了确定机床个运动部件的运动方向和移动距离,需要
在机床上建立一个坐标系,这个坐标系就叫做机床坐标系 1.2 机床坐标轴及其方向
常用地址码的含义如表所示
机能 程序号 顺序号 准备机能
坐标指令
进给机能 主轴机能 刀具机能
辅助机能
补偿 暂停 子程序调用 重复 参数
地址码
O N G X.Y.Z A.B.C.U.V.W R I.J.K F S T
M B
H.D P.X
I P.Q.R
意义
程序编号 顺序编号 机床动作方式指令 坐标轴移动指令 附加轴移动指令 圆弧半径 圆弧中心坐标 进给速度指令 主轴转速指令 刀具编号指令
第1章 数控加工实用基础(3).ppt
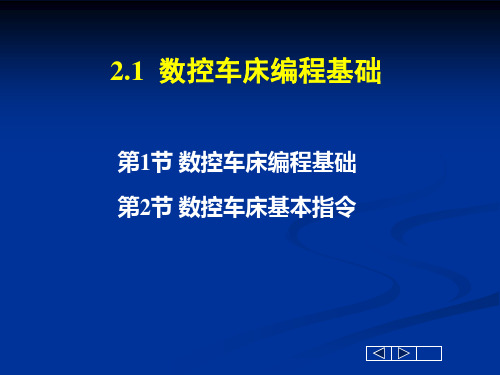
➢ 切削起点的确定与工件毛坯余量大小有关,应以刀具快
速走到该点时刀尖不与工件发生碰撞为原则。
❖退刀时,沿轮廓延长
线工进退出至工件附近, 再快速退刀。一般先退X 轴,后退Z轴。
五、 绝对编程与增量编程
数控编程通常都是按照组成图形的线段或圆弧的 端点的坐标来进行的。
绝对编程:指令轮廓终点相对于工件原点绝 对坐标值的编程方式。
说明
➢1、G54~G59是系统预置的六个坐标系,可根据
需要选用。
➢2、G54~G59建立的工件坐标原点是相对于机床
原点而言的,在程序运行前已设定好,在程序运行 中是无法重置的。
➢3、G54~G59预置建立的工件坐标原点在机床坐
标系中的坐标值可用 MDI 方式输入,系统自动记忆。
➢4、使用该组指令前,必须先回参考点。
增量编程:指令轮廓终点相对于轮廓起点坐 标增量的编程方式。
有些数控系统还可采用极坐标编程
绝对编程G90 增量编程G91
均为模态指令
绝对编程:G90 G01 X100.0 Z50.0; 增量编程:G91 G01 X60.0 Z-100.0;
绝对编程和增量编程
在越来越多车床中
X、Z表示绝对编程 U、W表示增量编程
允许同一程序段中二者混合使用
直线A→B ,可用: 绝对: G01 X100.0 Z50.0; 相对: G01 U60.0 W-100.0; 混用: G01 X100.0 W-100.0;
或 G01 U60.0 Z50.0;
第二节 数控车床基本G指令应用
一、坐标系设定
1、用G50设定工件坐标系 指令:G50 格式:G50 X _ Z_
1.快速点位移动G00
格式:G00 X(U)_Z(W)_;
速走到该点时刀尖不与工件发生碰撞为原则。
❖退刀时,沿轮廓延长
线工进退出至工件附近, 再快速退刀。一般先退X 轴,后退Z轴。
五、 绝对编程与增量编程
数控编程通常都是按照组成图形的线段或圆弧的 端点的坐标来进行的。
绝对编程:指令轮廓终点相对于工件原点绝 对坐标值的编程方式。
说明
➢1、G54~G59是系统预置的六个坐标系,可根据
需要选用。
➢2、G54~G59建立的工件坐标原点是相对于机床
原点而言的,在程序运行前已设定好,在程序运行 中是无法重置的。
➢3、G54~G59预置建立的工件坐标原点在机床坐
标系中的坐标值可用 MDI 方式输入,系统自动记忆。
➢4、使用该组指令前,必须先回参考点。
增量编程:指令轮廓终点相对于轮廓起点坐 标增量的编程方式。
有些数控系统还可采用极坐标编程
绝对编程G90 增量编程G91
均为模态指令
绝对编程:G90 G01 X100.0 Z50.0; 增量编程:G91 G01 X60.0 Z-100.0;
绝对编程和增量编程
在越来越多车床中
X、Z表示绝对编程 U、W表示增量编程
允许同一程序段中二者混合使用
直线A→B ,可用: 绝对: G01 X100.0 Z50.0; 相对: G01 U60.0 W-100.0; 混用: G01 X100.0 W-100.0;
或 G01 U60.0 Z50.0;
第二节 数控车床基本G指令应用
一、坐标系设定
1、用G50设定工件坐标系 指令:G50 格式:G50 X _ Z_
1.快速点位移动G00
格式:G00 X(U)_Z(W)_;
第1章 数控加工基础知识.ppt

上一页 下一页 返回
1.1 数控机床相关知识
①点位控制数控机床。这类数控机床的主要特点是,只控制刀具(或工 作台)从一点移动到另一点的准确定位,数控机床移动部件在移动中不 进行加工,只要求以最快的速度从一点移动到另一点。至于点与点之间 的移动轨迹(路径与方向)并无严格要求,各坐标轴之间的运动并不相关, 如图1-3。如数控钻床、数控镗床和数控冲床等; ②直线控制数控机床。这类机床是在定位控制基础上,除控制点与点之 间的准确定位外,还要求从一点到另一点之间按直线移动、按指定的进 给速度做直线切削,如图1-4所示。例如平面铣削的数控铣床、阶梯车 削的数控车床、磨削加工的数控磨床等都按指定的进给速度做直线切削。 ③轮廓控制数控机床。轮廓控制数控机床也称为连续控制数控机床,
上一页 下一页 返回
1.1 数控机床相关知识
③产品一致性好。由于数控机床按照预定的加工程序自动进行加工,在 加工过程中消除了操作者人为的操作误差,因而零件加工的一致性好。 ④能够实现复杂零件的加工。由于数控机床能够实现多轴联动,可加工 出普通机床无法完成的空间曲线和曲面,因而在航空、航天领域和对复 杂型面的模具加工中得到了广泛应用。 ⑤生产效率高。数控机床的刚性好,功率大,主轴转速高,进给速度范 围宽,平滑无级变速,容易选择较大及合理的切削用量,可减少许多调 整时间。此外,数控机床加工可免去划线工序,节省加工过程的中间检 验时间。由于空行程速度远高于普通机床,因此也能节省很多时间。
上一页 下一页 返回
1.1 数控机床相关知识
⑥机械传动链短,结构简单。数控机床的主传动多采用分段无级变速, 主轴箱结构简单;进给采用伺服电动机驱动,省去了庞杂的进给变速箱。 因此传动链短,机械结构简单。 ► 2.数控机床的分类
数控机床可从不同的角度进行分类,通常的分类方法有:按控制系统 的特点分类、按控制联动的坐标轴分类、按伺服系统控制的方式分类、 按工艺用途分类、按数控装置类型分类以及按数控系统的功能水平分类。 (1)按控制系统的特点分类
1.1 数控机床相关知识
①点位控制数控机床。这类数控机床的主要特点是,只控制刀具(或工 作台)从一点移动到另一点的准确定位,数控机床移动部件在移动中不 进行加工,只要求以最快的速度从一点移动到另一点。至于点与点之间 的移动轨迹(路径与方向)并无严格要求,各坐标轴之间的运动并不相关, 如图1-3。如数控钻床、数控镗床和数控冲床等; ②直线控制数控机床。这类机床是在定位控制基础上,除控制点与点之 间的准确定位外,还要求从一点到另一点之间按直线移动、按指定的进 给速度做直线切削,如图1-4所示。例如平面铣削的数控铣床、阶梯车 削的数控车床、磨削加工的数控磨床等都按指定的进给速度做直线切削。 ③轮廓控制数控机床。轮廓控制数控机床也称为连续控制数控机床,
上一页 下一页 返回
1.1 数控机床相关知识
③产品一致性好。由于数控机床按照预定的加工程序自动进行加工,在 加工过程中消除了操作者人为的操作误差,因而零件加工的一致性好。 ④能够实现复杂零件的加工。由于数控机床能够实现多轴联动,可加工 出普通机床无法完成的空间曲线和曲面,因而在航空、航天领域和对复 杂型面的模具加工中得到了广泛应用。 ⑤生产效率高。数控机床的刚性好,功率大,主轴转速高,进给速度范 围宽,平滑无级变速,容易选择较大及合理的切削用量,可减少许多调 整时间。此外,数控机床加工可免去划线工序,节省加工过程的中间检 验时间。由于空行程速度远高于普通机床,因此也能节省很多时间。
上一页 下一页 返回
1.1 数控机床相关知识
⑥机械传动链短,结构简单。数控机床的主传动多采用分段无级变速, 主轴箱结构简单;进给采用伺服电动机驱动,省去了庞杂的进给变速箱。 因此传动链短,机械结构简单。 ► 2.数控机床的分类
数控机床可从不同的角度进行分类,通常的分类方法有:按控制系统 的特点分类、按控制联动的坐标轴分类、按伺服系统控制的方式分类、 按工艺用途分类、按数控装置类型分类以及按数控系统的功能水平分类。 (1)按控制系统的特点分类
第1章数控加工的编程基础ppt课件

3.数控编程的种类 (1〕手工编程
手工编程就是从分析零件图样、确定加 工工艺过程、数值计算、编写零件加工程序 单、制备控制介质到程序校验都是由人工完 成。对于加工形状简单、计算量小、程序不 多的零件,采用手工编程较容易,而且经济、 及时。 (2〕自动编程
自动编程是利用计算机专用软件对复杂 零件进行数控加工程序编制的过程。
零件图纸
图纸工艺分析
计算运动轨迹
修
程序编制
正
制备控制介质
校验和试切
错误
(4〕制备控制介质
将程序单上的内容记录在 控制介质上,作为数控系 统的输入信息,若程序较 简单,也可直接通过键盘 输入。
零件图纸
图纸工艺分析
计算运动轨迹
修
程序编制
正
制备控制介质
校验和试切
错误
(5〕程序的校验和试切
校般检所验采查制和 用 机备试 空 床的切 走 运控削 刀 动制,校轨介才验迹质能、与,用空动必于运作须正转的经式画正过加图确进工校性一。验。步一以的
2.数控系统的功能
数控系统是数控机床的核心。数控机床根据功能和性能要求,配置不 同的数控系统。无论何种数控系统,其基本功能有5种,分别是: (1〕准备功能——准备功能是使数控机床作好某种操作准备的指令,用地址G 和数字表示,如G00、G01、G94等。 (2〕刀具功能——刀具功能字T。由地址功能码T和数字组成。刀具功能的 数字是指定的刀号,数字的位数由所用的系统决定。 (3〕主轴速度功能——主轴转速功能字S,由地址码S和数字组成,主要用 于主轴速度控制。 (4〕进给功能——进给功能字F表示刀具中心运动时的进给速度,进给功 能用F代码直接指定各轴的进给速度。由地址码F和数字构成。 (5〕辅助功能——辅助功能也叫M功能或M代码,它是控制机床或系统的开 关功能的一种命令。由地址码M和数字组成。常用的辅助功能有程序停、主 轴正/反转、冷却液接通和断开、换刀等。
数控机床编程与操作教学课件(全)

围较广,可以加工平面、锥度表面、多型腔工件表面等,主轴带有旋转 功能的机床还可以进行螺旋面加工。此外,电火花成形加工还可以与其 他加工工艺结合形成复合加工,例如,可以利用电能、电化学能、声能对 材料进行复合加工。
(4)可以获得较好的表面质量。电火花成形加工的表面质量较好, 加工表面微观形貌光滑,工件的棱边、尖角处无毛刺。
动主轴头型(见图1)和十字工作
台型(见图2)两种形式。
24 第 一 章 数 控 电 加 工 基 础
2-十字工作台型双立柱式电火花成形机床 1—床身2—立柱3—工作台(Y′轴) 4—滑板(X′轴) 5—工作液槽6—主轴头(W轴)7—主轴(Z轴)8—电极安装板
9—旋转轴(C轴)10—电极11—槽梁
第二节 数控电火花加工机床
20世纪80年代后期,大型高速线切割机床(加工速度在200 mm2/min以上)和四轴联动线切割机床研制成功,可切割锥度在6°以上 的零件。
4 第一章 数控电加工基础
第一节 数控电加工概述
一、电加工技术的发展
20世纪90年代,国内快走丝线切割机床的加工速度达到了60~80 mm2/min,进一步拓宽了电加工技术的应用范围。
电火花加工原理及应用 a)电火花加工原理 b)电火花镜面加工
1—工具电极 2—工件
8 第一章 数控电加工基础
第一节 数控电加工概述
1.电火花线切割加工原理 电火花线切割加工简称线切割加工,属于电火花加工方法之一。它
是以一根移动的金属丝(电极丝)作为工具电极,与工件之间产生火花 放电,对工件进行切割,故称为线切割加工。在正常的线切割加工过程 中,电极丝与工件保持较小的间隙,彼此不接触。在电极丝与工件之间 施加一定的电压,使其与工件之间产生局部的击穿放电,放电产生的瞬 时高温使工件局部熔化甚至汽化而被蚀除。同时,电极丝不断进给直至 加工出理想的工件形状。
(4)可以获得较好的表面质量。电火花成形加工的表面质量较好, 加工表面微观形貌光滑,工件的棱边、尖角处无毛刺。
动主轴头型(见图1)和十字工作
台型(见图2)两种形式。
24 第 一 章 数 控 电 加 工 基 础
2-十字工作台型双立柱式电火花成形机床 1—床身2—立柱3—工作台(Y′轴) 4—滑板(X′轴) 5—工作液槽6—主轴头(W轴)7—主轴(Z轴)8—电极安装板
9—旋转轴(C轴)10—电极11—槽梁
第二节 数控电火花加工机床
20世纪80年代后期,大型高速线切割机床(加工速度在200 mm2/min以上)和四轴联动线切割机床研制成功,可切割锥度在6°以上 的零件。
4 第一章 数控电加工基础
第一节 数控电加工概述
一、电加工技术的发展
20世纪90年代,国内快走丝线切割机床的加工速度达到了60~80 mm2/min,进一步拓宽了电加工技术的应用范围。
电火花加工原理及应用 a)电火花加工原理 b)电火花镜面加工
1—工具电极 2—工件
8 第一章 数控电加工基础
第一节 数控电加工概述
1.电火花线切割加工原理 电火花线切割加工简称线切割加工,属于电火花加工方法之一。它
是以一根移动的金属丝(电极丝)作为工具电极,与工件之间产生火花 放电,对工件进行切割,故称为线切割加工。在正常的线切割加工过程 中,电极丝与工件保持较小的间隙,彼此不接触。在电极丝与工件之间 施加一定的电压,使其与工件之间产生局部的击穿放电,放电产生的瞬 时高温使工件局部熔化甚至汽化而被蚀除。同时,电极丝不断进给直至 加工出理想的工件形状。
数控机床的加工程序编制 ppt课件
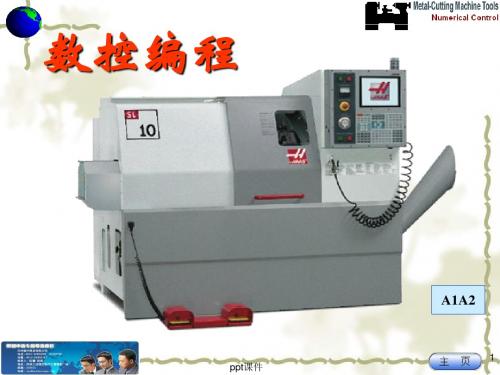
ppt课件 14
手工编程过程框图
ppt课件
15
3 字符与代码 字符(Character)是一个关于信息交换的术 语。它是用来组织、控制或表示数据的一些符号, 如数字、字母、标点符号、数学运算符等,是机器 能进行存储或传送的记号,是加工程序的最小组成 单位。常规加工程序用的字符分四类: 一:字母,由大写26个英文字母组成; 二:数字和小数点,由0~9及一个小数点组成; 三:符号,由+、-号组成; 四:功能字符,由程序开始(结束)符(如 “%”)、程序段结束符(如“;”)、跳过任选 程序段符(如“/”)等组成。
程序段各功能字的先后次序不严格规定。
ppt课件 19
程序段功能字按其功能的不同可分为7种类型, 分别是:顺序号字、准备功能字、尺寸字、进给功 能字、主轴转速字、刀具功能字和辅助功能字。 1)顺序号字 顺序号又称程序段号或程序段序号。位于程序 段之首,由地址符N和后续2~4数字组成。 顺序号的作用:对程序的校对和检索修改;作 为条件转向的目标,即作为转向目的程序段的名称。 有顺序号的程序段可以进行复归操作,指加工可以从 程序的中间开始,或回到程序中断处开始。 顺序号的使用规则:为正整数,编程时将第一 程序段冠以N10,以后以间隔10递增,以便于修改。
8
ppt课件
数控加工流程:
ppt课件
9
2)数控程序样本: O10 N10 N20 N30 N40 N50 N60 N70 … N80 N90
G55 M03 G01 G01 G01 G01 G03
M05 M30
G90 G01 Z40 F2000 S500 X-50 Y0 Z-5 F100 G42 X-10 Y0 H01 X60 Y0 X80 Y20 R20
数控机床编程的演变过程 1) 数控的基本含义 数控,即数字控制(Numerical Control-NC), 指用数码化的信号对机床运动及其加工过程进行控 制的一种方法。这种机床以数字字符指令方式控制 机床各部件相对运动,实现机床的加工。相应地这 种机床称为NC机床(NC Machine Tool)。 2) 数控编程的发展 控制介质:数控机床加工零件所需的控制信 息和数据的载体,即用来存放加工程序的载体,也 称程序载体。如穿孔带、穿孔卡、磁带或磁盘等。
手工编程过程框图
ppt课件
15
3 字符与代码 字符(Character)是一个关于信息交换的术 语。它是用来组织、控制或表示数据的一些符号, 如数字、字母、标点符号、数学运算符等,是机器 能进行存储或传送的记号,是加工程序的最小组成 单位。常规加工程序用的字符分四类: 一:字母,由大写26个英文字母组成; 二:数字和小数点,由0~9及一个小数点组成; 三:符号,由+、-号组成; 四:功能字符,由程序开始(结束)符(如 “%”)、程序段结束符(如“;”)、跳过任选 程序段符(如“/”)等组成。
程序段各功能字的先后次序不严格规定。
ppt课件 19
程序段功能字按其功能的不同可分为7种类型, 分别是:顺序号字、准备功能字、尺寸字、进给功 能字、主轴转速字、刀具功能字和辅助功能字。 1)顺序号字 顺序号又称程序段号或程序段序号。位于程序 段之首,由地址符N和后续2~4数字组成。 顺序号的作用:对程序的校对和检索修改;作 为条件转向的目标,即作为转向目的程序段的名称。 有顺序号的程序段可以进行复归操作,指加工可以从 程序的中间开始,或回到程序中断处开始。 顺序号的使用规则:为正整数,编程时将第一 程序段冠以N10,以后以间隔10递增,以便于修改。
8
ppt课件
数控加工流程:
ppt课件
9
2)数控程序样本: O10 N10 N20 N30 N40 N50 N60 N70 … N80 N90
G55 M03 G01 G01 G01 G01 G03
M05 M30
G90 G01 Z40 F2000 S500 X-50 Y0 Z-5 F100 G42 X-10 Y0 H01 X60 Y0 X80 Y20 R20
数控机床编程的演变过程 1) 数控的基本含义 数控,即数字控制(Numerical Control-NC), 指用数码化的信号对机床运动及其加工过程进行控 制的一种方法。这种机床以数字字符指令方式控制 机床各部件相对运动,实现机床的加工。相应地这 种机床称为NC机床(NC Machine Tool)。 2) 数控编程的发展 控制介质:数控机床加工零件所需的控制信 息和数据的载体,即用来存放加工程序的载体,也 称程序载体。如穿孔带、穿孔卡、磁带或磁盘等。
数控加工原理与编程基础.pptx

• 数控机床与普通机床比较:
数控机床在普通机床基础上增加了对机床运动和
动作自动控制 的功能部件,使数控机床能够自动
完成 对零件加工的全过程。
其控制的媒介:数字程序(学习重点)
二、不同加工方式示例
成型零件
成形车刀
仿 型加工
靠模板
数控加工
采用数控机床加工零件时,只需要将零件图 形和工艺参数、加工步骤等以数字信息的 形式,编成程序代码输入到机床控制系统 中,数控机床便按照事先编好的加工程序, 自动地对被加工零件进行加工.
三、数控加工的特点(优点)
1. 加工精度高,加工质量稳定 ☻ 数控机床的机械精度高 ☻ 数控机床的控制精度高(0.001mm/P) ☻ 无人为误差,加工的一致性好
2. 数控加工的生产效率高 ☻极大地缩短加工的辅助时间(快速行程、自
动换刀) ☻免划线工序 ☻粗、精加工一次装夹完成 ☻无需中途停车检测
选择和交换刀具的刀具指令信号
辅助指令信号:冷却、润滑、夹经 紧、松开、分度等.
3. 伺服系统:数控机床的动力装置
作用:接受数控装置的输出 驱动与放大 实现电→机转换
§1.3 数控加工原理
数控加工过程
加工检验 对刀试切 安装工件 编制并输入程序 数值计算 工艺分析 零件图纸
数控加工原理概述
数控加工原理就是将零件图形和工艺参数、 加工步骤等以数字信息的形式,编成程序代码 输入到机床控制系统中,再由其进行运算处理 后转成驱动伺服机构的指令信号,从而控制机 床各部件协调动作,自动完成零件的加工。
插补运算的任务就是把这种时实计算出的各个轴的 位移指令输入伺服系统,实现成形运动.
逐点比较法
逐点比较法插补运算是以区域判别为特征,每走 一步都要将加工点的瞬时坐标与相应给定的图形 上的点相比较,判别一下偏差,然后决定下一步 的走向。这样就能得到一个接近给定图形的轨迹, 其最大偏差不超过一个脉冲当量
数控入门基础大全PPT课件

1、数控加工过程
2、数据转换与控制过程
数
①译码
控 编
②刀补运算 ③插补计算 ④PLC控制
程
与 加 工 技 术
4
1.2 数控机床的坐标系
一、机床坐标系 二、坐标轴及其运动方向 三、工件坐标系 四、坐标原点 五、工件坐标系的设定 六、绝对坐标编程及增量坐标编程
辽宁工程技术大学职业技术学院
5
LGDZY 一、机床坐标系
UC=20,VC=-10。
程 与
增量坐标编程在程序段中用 G91指令来设定,该指令表示后 续程序中的所有编程尺寸,都是
加 按增量坐标值给定的。有的数控 系统在程序段中不用G91指令设
工 技
定增量坐标编程,直接用U,V, W给定刀具(或工件)运动轨迹 在X,Y,Z方向的增量坐标值。
术 增量坐标值与刀具(或工件) 的运动方向有关,当刀具运动的
控 利用绝对坐标系确定刀具(或 工件)运动轨迹坐标值的编程方法,
编 称为绝对坐标编程。
程
如图所示,A,B,C三点的坐
与Байду номын сангаас标是以固定的坐标原点O计算的, 其值为:
加
XA=20,YA=10;
工
XB=10,YB=40; XC=30,YC=30。
技 术 绝对坐标编程在程序段中用G90
指令来设定,该指令表示后续程序中
2
LGDZY 一、数控系统及数控机床 1、数字控制
数
用数字化信号对机构的运动过程进行控制。
控 2、数控系统
编
程
实现数字控制相关功能的软、硬件模块的集成。
与 3、计算机数控系统
加 以计算机为核心的数控系统
工 4、数控机床
技
2、数据转换与控制过程
数
①译码
控 编
②刀补运算 ③插补计算 ④PLC控制
程
与 加 工 技 术
4
1.2 数控机床的坐标系
一、机床坐标系 二、坐标轴及其运动方向 三、工件坐标系 四、坐标原点 五、工件坐标系的设定 六、绝对坐标编程及增量坐标编程
辽宁工程技术大学职业技术学院
5
LGDZY 一、机床坐标系
UC=20,VC=-10。
程 与
增量坐标编程在程序段中用 G91指令来设定,该指令表示后 续程序中的所有编程尺寸,都是
加 按增量坐标值给定的。有的数控 系统在程序段中不用G91指令设
工 技
定增量坐标编程,直接用U,V, W给定刀具(或工件)运动轨迹 在X,Y,Z方向的增量坐标值。
术 增量坐标值与刀具(或工件) 的运动方向有关,当刀具运动的
控 利用绝对坐标系确定刀具(或 工件)运动轨迹坐标值的编程方法,
编 称为绝对坐标编程。
程
如图所示,A,B,C三点的坐
与Байду номын сангаас标是以固定的坐标原点O计算的, 其值为:
加
XA=20,YA=10;
工
XB=10,YB=40; XC=30,YC=30。
技 术 绝对坐标编程在程序段中用G90
指令来设定,该指令表示后续程序中
2
LGDZY 一、数控系统及数控机床 1、数字控制
数
用数字化信号对机构的运动过程进行控制。
控 2、数控系统
编
程
实现数字控制相关功能的软、硬件模块的集成。
与 3、计算机数控系统
加 以计算机为核心的数控系统
工 4、数控机床
技
- 1、下载文档前请自行甄别文档内容的完整性,平台不提供额外的编辑、内容补充、找答案等附加服务。
- 2、"仅部分预览"的文档,不可在线预览部分如存在完整性等问题,可反馈申请退款(可完整预览的文档不适用该条件!)。
- 3、如文档侵犯您的权益,请联系客服反馈,我们会尽快为您处理(人工客服工作时间:9:00-18:30)。
• 2.数控装置
• 数控装置是数控机床的核心。数控装置从内部存储器中取 出或接受输入装置送来的一段或几段数控加工程序,经过 数控装置的逻辑电路或系统软件进行编译、运算和逻辑处 理后,输出各种控制信息和指令,控制机床各部分的工作, 使其进行规定的有序运动和动作。
• 3.伺服驱动装置及检测反馈装置
•
驱动装置接受来自数控装置的指令信息,经功率放大
•
齐齐哈尔第二机床集团公司与清华大学合作研制的加工 水轮机叶轮的混联机构机床
一、数控机床的组成
Z轴伺服电机 变频主轴 行程开关
机床本体
数控系统及其 操作面板
控制电柜
x-y数控拖板
如图所示是一台三坐标数控铣床组成图
• 1.信息输入
• 输入装置可以是光电阅读机、磁带机或软盘驱动器等。数 控机床加工程序也可通过键盘用手工方式直接输入数控系 统;数控加工程序还可由编程计算机用RS232C或采用网 络通信方式传送到数控系统中。
第1章 数控加工编程基础
1.1 数控加工的基本概念 1.2 数控机床的坐标系 1.3 数控编程的步骤与方法 1.4 数控加工工艺基础 1.5 数控车削工艺基础 1.6 数控铣床和加工中心工艺基础 1.7 数控加工常用刀具
数控机床的产生
• 1948年,美国帕森斯公司接受美国空军委托,研制 飞机螺旋桨叶片轮廓样板的加工设备。
• 1949年,该公司在美国麻省理工学院伺服机构研究 室的协助下,开始数控机床研究,并于1952年试制 成功第一台由大型立式仿形铣床。
• 1959年,加工中心 • 1967年,柔性制造系统 • 20世纪80年代初,柔性制造单元 • 20世纪80年代末90年代初,计算机集成制造系统
我国数控机床现况
• 中国数控机床的发展,大致经历三个阶段: • 1.起步阶段(1958-1979年) • 2.引进技术与开发阶段(1980-1989年) • 3.产业化阶段(1990-2005年)
• (4)加工阶段
•
当执行程序时,机床数控系统(CNC)将加工程序语句
译码、运算,转换成驱动各运动部件的动作指令,在系统的
统一协调下驱动各运动部件的适时运动,自动完成对工件的
加工。
数控机床的特点
• 数控机床的特点 • 1.自动化程度高,减轻劳动强度,改善劳动条件 • 数控机床对零件的加工是按事先编好的程序自动完成的,
• 3.复合加工机床促进新一代高效机床的形成
• 复合机床的含义是在一台机床上实现或尽可能完成从毛坯 至成品的全部加工。复合机床根据其结构特点,可以分为 工艺复合型和工序复合型两类。
• 4.工艺适用性的专门化数控机床正不断涌现 • 近年来对并联机构机床和混联机构机床的研究(图)以
及对可重构机床(RMT)技术的探索,反映了对制造装 备能更方便地实现个性化、多样化发展的一个追求。 • 5.智能化和集成化成为数字化制造的重要支撑技术 • 采用智能技术来实现多信息融合下的重构优化的智能决 策、过程适应控制、误差补偿智能控制、复杂曲面加工 运动轨迹优化控制、故障自诊断和智能维护以及信息集 成等功能,将大大提升成形和加工精度、提高制造效率。 • 6.发展适应敏捷制造和网络化分布式的制造系统 • 近10年来制造系统的发展历程,基本上遵循以下两个方 向: 增强制造系统的智能化和自治管理功能;发展新型 制造系统以适应不确定性的市场环境。 • 7.向大型化和微小化两极发展 • 8.配套装置和功能部件的品种质量日臻完善
后,严格按照指令信息的要求驱动机床移动部件,以加工
出符合图样要求的零件。因此,它的伺服精度和动态响应 性能是影响数控机床加工精度、表面质量和生产率的重要 因素之一。驱动装置包括控制器(含功率放大器)和执行 机构两大部分。目前大都采用直流或交流伺服电动机作为 执行机构。
•
位置检测装置将数控机床各坐标轴的实际位移量检测
出来,经反馈系统输入到机床的数控装置之后,数控装置
将反馈回来的实际位移量值与设定值进行比较,控制驱动
装置按照指令设定值运动。
• 4.机床本体
•
机床主机是数控机床的主体。它包括床身、底座、立
柱、横梁、滑座、工作台、主轴箱、进给机构、刀架及自
动换刀装置等机械部件。它是在数控机床上自动地完成各
种切削加工的机械部分。
数控机床发展趋势
• 高精化、高速化、高效化、柔性化、智能化和集成化,并 注重工艺适用性和经济性。
• 1.持续地提高经济加工精度 • 1950-2000年的50年内加工精度提升100倍左右。 • 2.推进全面高速化实现高效制造
• 在刀具材料和刀具结构不断发展的支持下,切削速度不断 地提高。高速化加工另一个特点是大多从单一的高速切削 发展至全面高速化,不仅要缩短切削时间,也要力求降低 辅助时间和技术准备时间。
• (2)编程阶段
•
根据加工工艺信息,用机床数控系统能识别的语言编写
数控加工程序(对加工工艺过程的描述),并填写程序单。
• (3)准备信息载体
•
根据已编好的程序单,将程序存放在信息载体(穿孔带、
磁带、磁盘等)上,通过信息载体将全部加工信息传给数控
系统。若数控加工机床与计算机联网时,可直接将信息载入
数控系统。
•
由于可编程逻辑控制器(PLC)具有响应快,性能可
靠,易于使用、编程和修改程序并可直接启动机床开关等
特点,现已广泛用作数控机床的辅助控1)准备阶段
•
根据加工零件的图纸,确定有关加工数据(刀具轨迹坐
标点、加工的切削用量、刀具尺寸信息等)。根据工艺方案、
选用的夹具、刀具的类型等选择有关其他辅助信息。
操作者除了操作面板、装卸零件、关键工序的中间测量以 及观察机床的运行之外,其他的机床动作直至加工完毕, 都是自动连续完成、不需要进行繁重的重复性手工操作, 劳动强度与紧张程度均可大为减轻,劳动条件也得到相应 的改善。 • 2.适应性强 • 利用数控机床加工改型零件,只需要重新编制程序就能实 现对零件的加工。 • 3.精度高 • 首先是在结构上引入了滚珠丝杠螺母机构、各种消除间隙 结构等,使机械传动的误差尽可能小;其次是采用了软件 精度补偿技术,使机械误差进一步减小;第三是用程序控 制加工,减少了人为因素对加工精度的影响。
• 5.辅助控制装置
•
辅助控制装置的主要作用是接收数控装置输出的开关
量指令信号,经过编译、逻辑判别和运动,再经功率放大
后驱动相应的电器,带动机床的机械、液压、气动等辅助
装置完成指令规定的开关量动作。这些控制包括主轴运动 部件的变速、换向和启停指令,刀具的选择和交换指令,
冷却、润滑装置的启动停止,工件和机床部件的松开、夹 紧,分度工作台转位分度等开关辅助动作。
• 数控装置是数控机床的核心。数控装置从内部存储器中取 出或接受输入装置送来的一段或几段数控加工程序,经过 数控装置的逻辑电路或系统软件进行编译、运算和逻辑处 理后,输出各种控制信息和指令,控制机床各部分的工作, 使其进行规定的有序运动和动作。
• 3.伺服驱动装置及检测反馈装置
•
驱动装置接受来自数控装置的指令信息,经功率放大
•
齐齐哈尔第二机床集团公司与清华大学合作研制的加工 水轮机叶轮的混联机构机床
一、数控机床的组成
Z轴伺服电机 变频主轴 行程开关
机床本体
数控系统及其 操作面板
控制电柜
x-y数控拖板
如图所示是一台三坐标数控铣床组成图
• 1.信息输入
• 输入装置可以是光电阅读机、磁带机或软盘驱动器等。数 控机床加工程序也可通过键盘用手工方式直接输入数控系 统;数控加工程序还可由编程计算机用RS232C或采用网 络通信方式传送到数控系统中。
第1章 数控加工编程基础
1.1 数控加工的基本概念 1.2 数控机床的坐标系 1.3 数控编程的步骤与方法 1.4 数控加工工艺基础 1.5 数控车削工艺基础 1.6 数控铣床和加工中心工艺基础 1.7 数控加工常用刀具
数控机床的产生
• 1948年,美国帕森斯公司接受美国空军委托,研制 飞机螺旋桨叶片轮廓样板的加工设备。
• 1949年,该公司在美国麻省理工学院伺服机构研究 室的协助下,开始数控机床研究,并于1952年试制 成功第一台由大型立式仿形铣床。
• 1959年,加工中心 • 1967年,柔性制造系统 • 20世纪80年代初,柔性制造单元 • 20世纪80年代末90年代初,计算机集成制造系统
我国数控机床现况
• 中国数控机床的发展,大致经历三个阶段: • 1.起步阶段(1958-1979年) • 2.引进技术与开发阶段(1980-1989年) • 3.产业化阶段(1990-2005年)
• (4)加工阶段
•
当执行程序时,机床数控系统(CNC)将加工程序语句
译码、运算,转换成驱动各运动部件的动作指令,在系统的
统一协调下驱动各运动部件的适时运动,自动完成对工件的
加工。
数控机床的特点
• 数控机床的特点 • 1.自动化程度高,减轻劳动强度,改善劳动条件 • 数控机床对零件的加工是按事先编好的程序自动完成的,
• 3.复合加工机床促进新一代高效机床的形成
• 复合机床的含义是在一台机床上实现或尽可能完成从毛坯 至成品的全部加工。复合机床根据其结构特点,可以分为 工艺复合型和工序复合型两类。
• 4.工艺适用性的专门化数控机床正不断涌现 • 近年来对并联机构机床和混联机构机床的研究(图)以
及对可重构机床(RMT)技术的探索,反映了对制造装 备能更方便地实现个性化、多样化发展的一个追求。 • 5.智能化和集成化成为数字化制造的重要支撑技术 • 采用智能技术来实现多信息融合下的重构优化的智能决 策、过程适应控制、误差补偿智能控制、复杂曲面加工 运动轨迹优化控制、故障自诊断和智能维护以及信息集 成等功能,将大大提升成形和加工精度、提高制造效率。 • 6.发展适应敏捷制造和网络化分布式的制造系统 • 近10年来制造系统的发展历程,基本上遵循以下两个方 向: 增强制造系统的智能化和自治管理功能;发展新型 制造系统以适应不确定性的市场环境。 • 7.向大型化和微小化两极发展 • 8.配套装置和功能部件的品种质量日臻完善
后,严格按照指令信息的要求驱动机床移动部件,以加工
出符合图样要求的零件。因此,它的伺服精度和动态响应 性能是影响数控机床加工精度、表面质量和生产率的重要 因素之一。驱动装置包括控制器(含功率放大器)和执行 机构两大部分。目前大都采用直流或交流伺服电动机作为 执行机构。
•
位置检测装置将数控机床各坐标轴的实际位移量检测
出来,经反馈系统输入到机床的数控装置之后,数控装置
将反馈回来的实际位移量值与设定值进行比较,控制驱动
装置按照指令设定值运动。
• 4.机床本体
•
机床主机是数控机床的主体。它包括床身、底座、立
柱、横梁、滑座、工作台、主轴箱、进给机构、刀架及自
动换刀装置等机械部件。它是在数控机床上自动地完成各
种切削加工的机械部分。
数控机床发展趋势
• 高精化、高速化、高效化、柔性化、智能化和集成化,并 注重工艺适用性和经济性。
• 1.持续地提高经济加工精度 • 1950-2000年的50年内加工精度提升100倍左右。 • 2.推进全面高速化实现高效制造
• 在刀具材料和刀具结构不断发展的支持下,切削速度不断 地提高。高速化加工另一个特点是大多从单一的高速切削 发展至全面高速化,不仅要缩短切削时间,也要力求降低 辅助时间和技术准备时间。
• (2)编程阶段
•
根据加工工艺信息,用机床数控系统能识别的语言编写
数控加工程序(对加工工艺过程的描述),并填写程序单。
• (3)准备信息载体
•
根据已编好的程序单,将程序存放在信息载体(穿孔带、
磁带、磁盘等)上,通过信息载体将全部加工信息传给数控
系统。若数控加工机床与计算机联网时,可直接将信息载入
数控系统。
•
由于可编程逻辑控制器(PLC)具有响应快,性能可
靠,易于使用、编程和修改程序并可直接启动机床开关等
特点,现已广泛用作数控机床的辅助控1)准备阶段
•
根据加工零件的图纸,确定有关加工数据(刀具轨迹坐
标点、加工的切削用量、刀具尺寸信息等)。根据工艺方案、
选用的夹具、刀具的类型等选择有关其他辅助信息。
操作者除了操作面板、装卸零件、关键工序的中间测量以 及观察机床的运行之外,其他的机床动作直至加工完毕, 都是自动连续完成、不需要进行繁重的重复性手工操作, 劳动强度与紧张程度均可大为减轻,劳动条件也得到相应 的改善。 • 2.适应性强 • 利用数控机床加工改型零件,只需要重新编制程序就能实 现对零件的加工。 • 3.精度高 • 首先是在结构上引入了滚珠丝杠螺母机构、各种消除间隙 结构等,使机械传动的误差尽可能小;其次是采用了软件 精度补偿技术,使机械误差进一步减小;第三是用程序控 制加工,减少了人为因素对加工精度的影响。
• 5.辅助控制装置
•
辅助控制装置的主要作用是接收数控装置输出的开关
量指令信号,经过编译、逻辑判别和运动,再经功率放大
后驱动相应的电器,带动机床的机械、液压、气动等辅助
装置完成指令规定的开关量动作。这些控制包括主轴运动 部件的变速、换向和启停指令,刀具的选择和交换指令,
冷却、润滑装置的启动停止,工件和机床部件的松开、夹 紧,分度工作台转位分度等开关辅助动作。