磨削车间工作环境研究与改善[设计+开题+综述]
铝合金磨削加工的研究综述
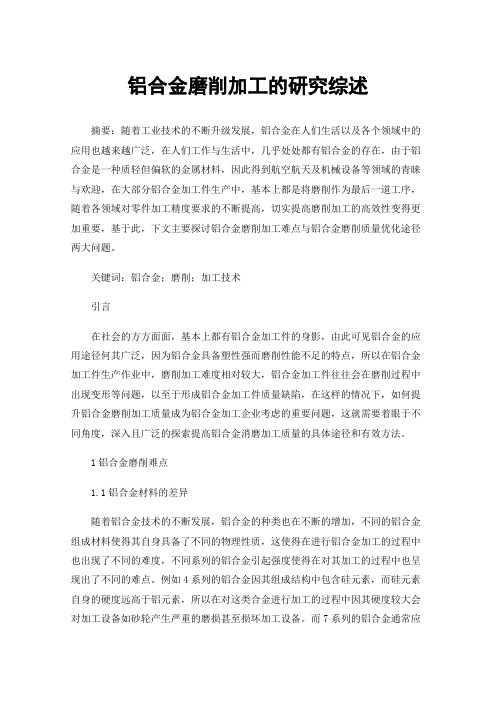
铝合金磨削加工的研究综述摘要:随着工业技术的不断升级发展,铝合金在人们生活以及各个领域中的应用也越来越广泛,在人们工作与生活中,几乎处处都有铝合金的存在,由于铝合金是一种质轻但偏软的金属材料,因此得到航空航天及机械设备等领域的青睐与欢迎,在大部分铝合金加工件生产中,基本上都是将磨削作为最后一道工序,随着各领域对零件加工精度要求的不断提高,切实提高磨削加工的高效性变得更加重要,基于此,下文主要探讨铝合金磨削加工难点与铝合金磨削质量优化途径两大问题。
关键词:铝合金;磨削;加工技术引言在社会的方方面面,基本上都有铝合金加工件的身影,由此可见铝合金的应用途径何其广泛,因为铝合金具备塑性强而磨削性能不足的特点,所以在铝合金加工件生产作业中,磨削加工难度相对较大,铝合金加工件往往会在磨削过程中出现变形等问题,以至于形成铝合金加工件质量缺陷,在这样的情况下,如何提升铝合金磨削加工质量成为铝合金加工企业考虑的重要问题,这就需要着眼于不同角度,深入且广泛的探索提高铝合金消磨加工质量的具体途径和有效方法。
1铝合金磨削难点1.1铝合金材料的差异随着铝合金技术的不断发展,铝合金的种类也在不断的增加,不同的铝合金组成材料使得其自身具备了不同的物理性质,这使得在进行铝合金加工的过程中也出现了不同的难度,不同系列的铝合金引起强度使得在对其加工的过程中也呈现出了不同的难点。
例如4系列的铝合金因其组成结构中包含硅元素,而硅元素自身的硬度远高于铝元素,所以在对这类合金进行加工的过程中因其硬度较大会对加工设备如砂轮产生严重的磨损甚至损坏加工设备。
而7系列的铝合金通常应用于航空航天领域,不仅其硬度较高而且具备较高的耐磨性。
所以在加工这种铝合金材料的时候要着重对磨削参数进行科学的设定,同时需要具备丰富的铝合金加工经验才能有效的设定相关参数。
考虑到航空航天领域所需要的各类零件和构件需要较强的耐腐蚀性能和表面性,因此在进行加工的过程中对加工环境有着较为苛刻的要求。
数控快速点磨削过程中的磨削力的研究的开题报告
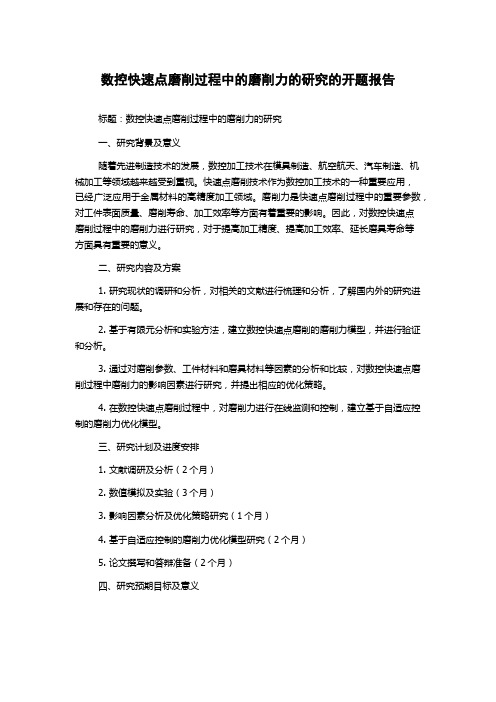
数控快速点磨削过程中的磨削力的研究的开题报告
标题:数控快速点磨削过程中的磨削力的研究
一、研究背景及意义
随着先进制造技术的发展,数控加工技术在模具制造、航空航天、汽车制造、机械加工等领域越来越受到重视。
快速点磨削技术作为数控加工技术的一种重要应用,
已经广泛应用于金属材料的高精度加工领域。
磨削力是快速点磨削过程中的重要参数,对工件表面质量、磨削寿命、加工效率等方面有着重要的影响。
因此,对数控快速点
磨削过程中的磨削力进行研究,对于提高加工精度、提高加工效率、延长磨具寿命等
方面具有重要的意义。
二、研究内容及方案
1. 研究现状的调研和分析,对相关的文献进行梳理和分析,了解国内外的研究进展和存在的问题。
2. 基于有限元分析和实验方法,建立数控快速点磨削的磨削力模型,并进行验证和分析。
3. 通过对磨削参数、工件材料和磨具材料等因素的分析和比较,对数控快速点磨削过程中磨削力的影响因素进行研究,并提出相应的优化策略。
4. 在数控快速点磨削过程中,对磨削力进行在线监测和控制,建立基于自适应控制的磨削力优化模型。
三、研究计划及进度安排
1. 文献调研及分析(2个月)
2. 数值模拟及实验(3个月)
3. 影响因素分析及优化策略研究(1个月)
4. 基于自适应控制的磨削力优化模型研究(2个月)
5. 论文撰写和答辩准备(2个月)
四、研究预期目标及意义
通过对数控快速点磨削过程中磨削力的研究,可以优化加工参数,提高加工品质和加工效率,延长磨具寿命,为制造业的发展提供技术支撑。
同时,研究成果可以为相关领域的理论研究和技术开发提供参考,具有重要的科学研究和应用价值。
磨削工艺的优化与改进

磨削工艺的优化与改进为了适应不断发展的工业需求,磨削技术在制造业中扮演着重要的角色。
磨削是一种通过磨削轮与工件的相对运动,去除工件表面的不规则部分,达到提高工件精度和表面质量的目的。
然而,随着产品复杂性的增加和质量要求的提高,传统的磨削工艺在面对一些新型材料和高精度要求时显得效率低下、技术单一。
传统磨削过程中存在着磨削轮的磨损、加工精度降低、工作效率低下等问题,需要通过改进优化工艺来提高生产效率和产品质量。
首先,在磨削工艺方面,可以通过选择合适的磨削轮来改善加工精度。
磨削轮的选择应根据工件材料和要求来确定。
例如,在对脆性材料的磨削时,选择具有良好自磨削能力和抗冷热疲劳性能的磨削轮,可以减小工件表面的热影响区和热应力区,提高工件表面质量。
此外,为了提高磨削轮的使用寿命,可以在磨削过程中采用适当的冷却液,降低磨削轮的温升和磨削轮与工件的摩擦系数,减少磨损。
其次,磨削工装的设计也是优化磨削工艺的关键之一。
磨削工装的设计应根据工件形状和磨削要求来确定。
例如,对于复杂形状的工件,可以设计出适合的磨具夹具,减少工件因磨具变形而导致的磨削误差。
此外,磨削工装的制造材料也应选择具有良好的刚度和耐磨性能,提高工装的稳定性和寿命。
此外,在磨削参数的选择上也是需要优化的。
磨削参数的选择应根据工件材料、磨削轮材料、磨削轮粒度、工作速度等因素来确定。
过大或过小的磨削压力都会影响磨削效果,而过大的磨削速度可能会产生过高的热量,从而降低磨削质量。
因此,在确定磨削参数时,需要综合考虑各种因素,通过试验和分析来找到最佳的磨削参数组合。
值得一提的是,近年来,随着人工智能和自动化技术的发展,磨削工艺也得到了进一步优化。
通过加入自动感测装置和控制系统,可以实现对磨削过程的自动监测和控制。
例如,通过对磨削力、温度和表面质量等参数的实时监测,可以及时调整磨削参数,提高加工精度和效率。
总之,磨削工艺的优化与改进对于提高产品质量和生产效率至关重要。
探讨木材加工机械中的工作环境优化与改善

探讨木材加工机械中的工作环境优化与改善木材加工机械是现代木材加工企业中不可或缺的设备,它可以极大地提高生产效率和产品质量。
但是,由于工作环境的特殊性,木材加工机械的操作工人常常面临一系列的工作环境问题,例如噪音、粉尘、高温等。
为了保障工人的身体健康和提高工作效率,优化和改善木材加工机械的工作环境势在必行。
首先,噪音问题是木材加工机械工作环境中最为常见的问题之一。
木材加工机械在运行过程中会发出很高的噪音,给操作工人和周围环境带来不适。
为解决这一问题,企业可以在设计和购买木材加工机械时选择降噪设备或降噪材料,减少噪音的产生。
同时,操作工人可以佩戴耳塞或耳罩来降低对噪音的暴露。
此外,企业还应该合理安排工人上岗时间和轮班制度,以减少集中噪音对工人的影响。
其次,粉尘是木材加工机械工作环境中另一个不容忽视的问题。
木材加工过程中会产生大量的粉尘,对操作工人的身体健康带来潜在风险。
为了改善工作环境,企业应该加强粉尘的收集和处理措施。
例如,可以安装粉尘收集器、吸尘器等设备,及时清理工作场地上的粉尘。
同时,工人也应该佩戴防护口罩和手套,减少粉尘对身体的侵害。
此外,高温也是木材加工机械工作环境中需要解决的问题之一。
特别是在夏季或密闭环境中,机器运行时会产生高温,给工人的工作和身体带来不适。
为了改善工作环境,企业可以采取一些措施来降低温度。
例如,可以安装通风设备以增加空气流通,提供冷饮水或更换湿毛巾等,帮助工人降低体温。
此外,企业还应该合理安排工作时间和休息间隔,避免工人在高温环境中长时间工作。
除了以上具体的问题之外,还有一些工作环境改善的基本原则值得考虑。
首先,企业应该为操作工人提供良好的工作装备和个人防护设备,确保他们的安全和舒适。
其次,应该定期进行工作环境的检测和评估,及时发现和解决工作环境中的问题。
同时,培训工人关于工作环境和个人防护的知识,提高他们对工作环境的自我保护意识。
总体来说,木材加工机械的工作环境优化与改善是一项需要长期关注和努力的任务。
磨削机床改善方案
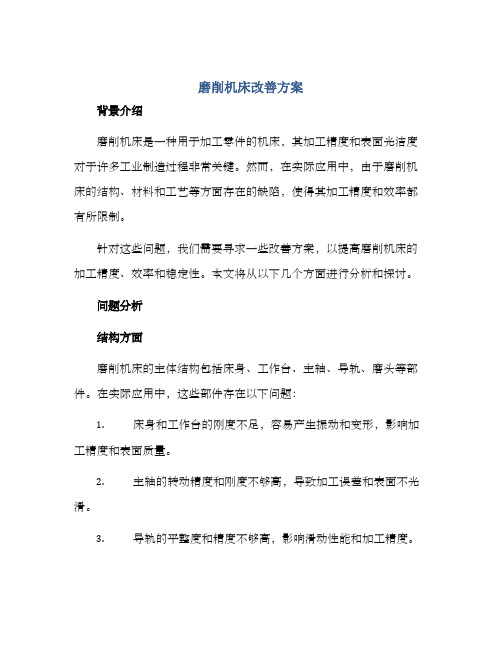
磨削机床改善方案背景介绍磨削机床是一种用于加工零件的机床,其加工精度和表面光洁度对于许多工业制造过程非常关键。
然而,在实际应用中,由于磨削机床的结构、材料和工艺等方面存在的缺陷,使得其加工精度和效率都有所限制。
针对这些问题,我们需要寻求一些改善方案,以提高磨削机床的加工精度、效率和稳定性。
本文将从以下几个方面进行分析和探讨。
问题分析结构方面磨削机床的主体结构包括床身、工作台、主轴、导轨、磨头等部件。
在实际应用中,这些部件存在以下问题:1.床身和工作台的刚度不足,容易产生振动和变形,影响加工精度和表面质量。
2.主轴的转动精度和刚度不够高,导致加工误差和表面不光滑。
3.导轨的平整度和精度不够高,影响滑动性能和加工精度。
材料方面磨削机床的材料质量对其加工精度、效率和稳定性都具有重要影响。
在实际应用中,常见的问题包括:1.部件材料的强度和硬度不够高,导致容易疲劳、变形和损坏。
2.部件材料的密度和组织结构存在缺陷,影响其物理性能和加工精度。
工艺方面磨削加工是一种高精度、高速度和高温度的加工过程,对于工艺的控制和调节也具有重要意义。
在实际应用中,常见的问题包括:1.磨削过程中的润滑和冷却不足,导致温度过高、表面质量不佳和砂轮寿命短。
2.磨削参数的选择和调整不合理,影响加工效率和精度。
改善方案结构改善方案1.加强床身和工作台的刚度和平整度,采用更高强度的材料。
2.优化主轴结构和转动精度,增加轴承数量和规格。
3.提高导轨的平整度和精度,采用线性滑动轴承。
材料改善方案1.采用高强度和高硬度的材料,如硬质合金、陶瓷等。
2.对于重要零部件,采用铸造或锻造工艺,以提高密度和组织性能。
工艺改善方案1.优化润滑和冷却系统,确保磨削过程中的润滑和冷却。
2.调整磨削参数,如砂轮转速、进给速度、磨削深度等,以达到更优的加工效果。
结论以上是本文针对磨削机床的改善方案。
当然,实际应用中还有很多细节问题需要考虑和解决。
但是,只有我们不断探索和实践,才能让磨削机床更加稳定、高效和精确地为我们服务。
刀具磨削技术的研究与优化

刀具磨削技术的研究与优化刀具磨削技术是切削加工的重要手段之一。
它的发展历程与数控技术的发展有着密不可分的关系。
随着制造业的不断发展,刀具磨削技术也得到了越来越广泛的应用。
刀具磨削技术的研究和优化已成为磨削技术领域的重要研究方向。
一、刀具磨削技术的研究趋势刀具磨削技术是很多行业制造工艺的重要环节,如航空工业、汽车工业、机床制造等。
随着磨削技术的不断发展,越来越多的刀具磨削技术被应用到了实际生产中。
刀具磨削技术的研究趋势主要包括以下几个方面:1、高效、高质量、低成本的刀具磨削技术研究。
刀具磨削技术的发展方向是高效化、智能化。
在高效性方面,除了磨削技术本身的效率提升外,适应性、通用性也越来越强。
在质量方面,磨削技术也应有相应改进。
低成本是磨削技术研究的另一 focuses。
2、刀具材料的研发。
随着材料科学的不断进步,出现了越来越多的新材料,如陶瓷材料、超硬合金材料等,这些材料的出现为刀具磨削技术提供了更广阔的发展空间。
刀具磨削技术研究的另外一个方向,就是开发能够适应新型材料的磨削技术。
3、数控刀具磨削技术的发展。
数控刀具磨削技术作为现代磨削技术的重要代表,以其高效、精度高、自动化程度高等优点受到了企业和科研人员的青睐。
未来,基于数控技术的刀具磨削技术将日益成熟和广泛应用。
二、刀具磨削技术的优化方向刀具磨削技术的优化工作需要从以下三个方面入手:1、工作质量的提高。
这是磨削技术优化的重点内容之一。
工作质量的提高需要依据工艺参数和刀具结构进行分析,对研磨机结构及各工作部件进行优化设计,同时研究刀具刃口的几何形状和磨削顺序等技术,提高工作效率和质量。
2、成本的优化。
磨削技术的优化在成本方面也具有重大意义。
材料的选择、耗损程度和研磨动力的选择对磨削成本的影响十分重要。
是要通过技术的优化来保证磨削成本可控。
3、制定良好的研磨规范。
研磨规范是刀具磨削技术研究的关键所在,包括刀具磨削的工艺流程和技术标准,以及适当的管理与控制措施,只要遵守研磨规范,就能获得更高质量的研磨产品。
平面磨床的自动化磨削工艺设计与优化

平面磨床的自动化磨削工艺设计与优化这篇文章将围绕着平面磨床的自动化磨削工艺设计与优化展开讨论。
首先,我将介绍平面磨床的基本工作原理以及其在工业制造中的重要性。
接着,我将探讨自动化磨削工艺的设计和实施,包括自动化系统的选择、磨削参数的优化以及磨削工具的选择和刀具磨损监控。
最后,将总结自动化磨削工艺设计与优化的关键问题和未来的发展方向。
平面磨床是一种用于加工平面和平行面的机床,广泛应用于汽车、飞机、机械制造等领域。
其基本工作原理是通过旋转砂轮和工件的接触来移除工件上的金属,从而实现对工件平面的加工。
平面磨床具有高精度、高效率和重复性好等特点,是磨削加工中不可或缺的工具。
自动化磨削工艺的设计和优化是提高平面磨削加工效率和质量的关键。
首先,选择适合的自动化系统是设计和实施自动化磨削工艺的首要任务。
常见的自动化系统包括数控系统、机器视觉系统和自动加载系统等。
数控系统可以实现对磨削过程中各个参数的精确控制,提高加工精度和稳定性。
机器视觉系统可以实时监测工件表面的形貌和表面质量,并根据监测结果调整磨削参数,实现自动化调整和优化。
自动加载系统可以实现对工件的自动装卸,减少人工干预,提高生产效率。
在磨削参数的优化方面,可以通过实验设计和数值模拟等方法,找到最佳的磨削参数组合。
磨削参数包括磨削速度、磨削深度、进给速度等。
通过优化磨削参数,可以最大限度地提高加工效率和降低工件表面粗糙度。
此外,磨削工具的选择也是优化工艺的重要方面。
合适的磨削工具可以提高加工效率和工件表面的质量。
常见的磨削工具包括砂轮、砥石和磨料等。
针对不同的工件材料和加工要求,选择合适的磨削工具进行加工。
另外,刀具磨损的监控也是自动化磨削工艺设计和优化的重要环节。
刀具磨损会导致加工精度下降、工件表面质量变差。
因此,实时监测刀具磨损情况,并及时调整磨削参数,可以保持加工效率和质量的稳定。
常见的刀具磨损监控方法包括声学监测、力信号监测和机器视觉监测等。
通过这些监测方法,可以提前预知刀具磨损的情况,并采取相应的措施进行调整和替换。
磨削机床改善方案

磨削机床改善方案概述磨削机床是一种用于精密磨削的机床,广泛应用于制造业中。
然而,由于长期使用和磨损,磨削机床可能会出现一系列问题,例如精度低、寿命短、噪音大等,影响了工作效率和质量。
因此,磨削机床改善方案是必要的。
具体措施1. 引入新材料磨削机床的材料是影响其性能的重要因素。
引入新材料可以提高磨削机床的耐久性、强度和精度。
例如,使用高强度钢材代替低强度材料,可以大大提高磨削机床的使用寿命。
2. 优化加工工艺加工工艺的优化可以提高磨削机床的加工精度和效率。
例如,采用先进的数控技术控制磨削机床的加工过程,可以提高加工精度和效率,避免误差和生产故障。
3. 设计更好的机构机构的设计是影响磨削机床性能的重要因素。
通过改进机构设计,可以提高磨削机床的加工精度和效率。
例如,在滚动轴承上安装轴承座,可以减小磨削过程的振动,提高加工精度。
4. 采用新技术新技术是推动磨削机床发展的关键。
例如,采用高速电机和水冷却技术,可以有效地减小机床的噪音和热量,提高机床的加工效率和精度。
5. 增强维护保养维护保养是磨削机床保持良好状态的必要条件。
定期对机床进行维护保养,例如清洁和润滑,可以延长机床的使用寿命,并避免故障和损坏。
总结磨削机床是制造业中不可缺少的重要设备,但由于长期使用和磨损,可能会出现一系列问题。
通过引入新材料、优化加工工艺、设计更好的机构、采用新技术、增强维护保养等措施,可以有效地改善磨削机床的性能,提高工作效率和质量。
然而,需要注意的是,不同型号的磨削机床可能需要采取不同的改善方案,因此在实际应用中需要根据具体情况选择合适的方案。
磨削加工技术的改进

磨削加工技术的改进引言磨削加工是一种常见且重要的金属加工工艺,广泛应用于各个行业,尤其是机械制造领域。
磨削加工旨在通过研磨工具与工件的相对运动,从而得到具有精密尺寸和良好表面质量的零件。
然而,传统的磨削加工技术存在一些问题,例如加工效率低、工件表面质量难以满足要求等。
为了提高磨削加工的效率和质量,人们不断进行技术改进和创新。
本文将介绍几种常见的磨削加工技术的改进方法。
1. 高速磨削技术传统磨削加工使用低速磨削,由于磨粒与工件之间的相对速度较小,加工效率较低。
为了提高加工效率,人们提出了高速磨削技术。
高速磨削利用高速旋转的砂轮,使磨粒与工件之间的相对速度增大,从而加快材料的去除速度。
同时,高速磨削还可以减少切削热量的积累,降低工件的热变形风险。
因此,高速磨削技术可以显著提高磨削加工的效率和质量。
2. 纳米磨削技术传统磨削加工存在着一些难以解决的问题,例如工件表面质量不佳、精度难以保证等。
为了提高工件的表面质量和精度,人们引入了纳米磨削技术。
纳米磨削技术是利用纳米尺度的磨粒进行加工,可以有效地去除工件表面的缺陷和毛刺,并减少磨削加工对工件的变形影响。
通过纳米磨削技术,工件的表面粗糙度和平行度可以得到显著改善,最终实现高精度加工。
3. 超声波磨削技术超声波磨削技术是一种结合了超声波振动和磨削的加工方法。
通过施加超声波振动,可以使磨粒与工件之间发生微小的振动,进一步改善磨削加工的质量。
超声波磨削技术可以有效地减小磨削力和磨粒与工件之间的压力,降低切削热量的积累,从而减少工件的热变形和表面损伤。
此外,超声波磨削技术还能提高磨削液的渗透性和冷却性能,进一步改善磨削加工的效果。
4. 智能磨削技术随着智能制造的发展,智能磨削技术逐渐应用于磨削加工领域。
智能磨削技术利用传感器、控制系统和人工智能算法等先进技术,实现对磨削加工过程的实时监控和控制。
通过对加工参数、工艺状态和材料特性等信息的综合分析,智能磨削技术可以自动调整磨削参数,优化磨削加工的效果。
磨削机床改善方案

磨削机床改善方案磨削机床是现代工业生产中必不可少的关键设备,它可以在工件表面上加工出极高精度的工件,是制造高品质零件的重要工具。
但是在使用过程中,磨削机床会受到磨损、变形、疲劳等因素的影响,导致加工精度下降,生产效率降低,需要及时进行维护和改善。
本文将介绍一些有效的磨削机床改善方案,来提升加工效率和加工精度。
1. 床身加工优化床身的加工质量直接影响着整个磨削机床的加工精度和生产效率,因此必须保持在极高水平。
在磨削机床的床身加工过程中,应注意以下几个方面:•选择优质材料:床身材料要求高强度、高硬度、高耐磨性能等,以提高床身的整体性能和稳定性。
•采用精密的机械加工设备:采用数控加工等高精度加工设备,以确保床身表面的光滑度和平整度。
•适当采用热处理工艺:热处理能提高床身硬度、耐磨性和稳定性,使其能够更好的承受磨削过程中的压力和振动。
2. 润滑系统改进磨削机床运行过程中需要润滑剂的滋润来减少运动部件之间的摩擦,延长机器的使用寿命,提高加工精度。
但是,润滑系统也会受到污染、泄漏等问题的影响,从而影响整个磨削机床的加工效率和精度。
因此,调整润滑系统的设计和优化润滑装置的安装位置是改善方案之一。
•定期更换润滑油:运用特殊、适应润滑条件的高品质润滑油品,通过正确的更换和检查机械零部件,保持润滑系统的有效性。
•加装滤油装置:通过加装滤油器或油水分离装置,能够有效过滤润滑油中的异物颗粒、水分等,防止其继续污染油路,提高润滑效果。
•安装增压泵:增压泵能够将润滑油提供给磨削机床中各运动部位的润滑装置,缓解润滑系统的压力,使其稳定正常运转。
3. 控制系统升级磨削机床的控制系统对于加工精度的影响非常大,一个优秀的控制系统能够使加工机床的稳定性和精度得到大幅提升。
针对磨削机床控制系统升级,建议从以下几点着手:•采用高精度传感器:通过更换高精度的传感器和测量系统,从而获得更为准确的加工数据,提高加工精度。
•使用具有自学能力的控制器:自学能力的控制器能够对加工机床的运行状态进行学习和分析,从而动态调整磨削机床的加工参数,确保加工精度稳定。
磨削机床改善方案

磨削机床改善方案1. 背景磨削是机械加工的一种重要方法,广泛应用于制造业领域。
而磨削机床作为磨削技术的主要工具,其对产品质量和生产效率的影响尤为重要。
然而,在实际生产中,磨削机床常常存在一系列问题,例如加工精度不高、表面粗糙度较大、易发生振动、寿命短等。
若不能有效解决这些问题,将直接影响到产品质量和生产效率。
因此,为了提高磨削机床的加工精度和稳定性,需要对其进行改善。
2. 磨削机床改善方案2.1 选用高精度磨削机床选择高精度的磨削机床是提高加工精度和稳定性的一个重要手段。
高精度磨削机床具有较高的加工精度和稳定性,能够有效降低产品加工误差和表面粗糙度,提高加工效率和质量。
此外,高精度磨削机床还具有寿命长、维修方便等优点。
2.2 优化机床结构通过优化机床结构,可以进一步提高其加工精度和稳定性。
优化机床结构包括改进机床的支撑结构、刚性、稳定性等,减少机床振动及其对加工精度的影响。
例如,在机床床身上增加减震器、加强床身刚性、增加加工过程的补偿机制等都能有效改善机床的结构。
2.3 选用合适的磨削工具磨削工具是影响磨削精度和加工效率的关键因素之一。
正确地选用合适的磨削工具能够大大提高磨削机床的加工效率和质量。
在选择磨削工具时,需要考虑磨削对象的材质、工件的形状和尺寸等因素,并结合机床的性能、磨削方式等进行合理选择。
2.4 做好机床维护和保养机床的维护和保养是保证其良好工作状态和稳定性的关键。
及时清洁、检查和维护机床,定期更换磨削工具、检查润滑油等是维护机床的常规工作。
此外,应定期进行机床的保养检修,检查机床各部件的运行状况,确保机床的各项指标处于正常范围内,以保证机床的长期稳定运行。
3. 结论在磨削机床的改善过程中,上述方案都是值得考虑的。
通过对机床的优化、选用高精度的磨削工具、合理维护和保养等一系列措施,能够有效地提高磨削机床的加工精度和稳定性,进一步提高产品的质量和生产效率。
磨削机床改善方案

磨削机床改善方案磨削机床是一种用于加工金属和非金属材料的机械设备,其主要功能是通过磨削研磨的方式去除工件表面上的一层材料,以达到工件尺寸、形状、粗糙度和平行度等方面的要求。
随着国民经济的快速发展和制造业的竞争加剧,磨削机床的性能和精度已成为制造业的关键所在,因此需要不断地对其进行改进和提高。
本文将从几个方面来讨论磨削机床的改善方案。
提高加工精度磨削机床的加工精度对于加工件的质量至关重要。
提高磨削机床的加工精度是一个长期的过程,需要从设计、制造、使用等多个方面入手。
设计磨削机床的设计是影响加工精度的关键。
在设计时,应考虑以下因素:•结构合理性:磨削机床的结构应具有稳定性和刚性,并考虑到加工过程中的各种力和振动。
例如,加入定位销、减震设备等,可以减少加工过程中的误差。
•材料和表面处理:机床的材料和加工表面处理也会影响加工精度,应选择高品质材料和表面处理技术,以保障机床的性能和寿命。
制造在制造过程中,应注意以下方面:•检测和调试:在机床制造过程中,应严格按照工艺流程进行检测和调试,以确保机床的精度和良品率。
•精度机床的制造:采用高精度机床和自动化加工生产线,制造出更精密的零部件,可以提高机床的加工精度。
使用在使用过程中,应注意以下方面:•维护保养:磨削机床是一种精密的机械设备,需要定期的保养维护,以确保机床的长期稳定运行和加工精度。
•操作规范:操作者应按照操作规范操作机床,避免疏忽造成加工误差。
稳定性和可靠性稳定性和可靠性是磨削机床最基本的性能要求。
只有具备了稳定性和可靠性,才能满足用户的需求。
为了提高机床的稳定性和可靠性,可以采取以下措施:•加强检测:定期检测机床的状态,发现问题及时解决。
•维护保养:定期维护保养机床,更换部件和润滑油等。
•设计合理:在设计时,考虑到机床使用环境的因素,使其更加稳定和可靠。
提高加工效率提高加工效率可以有效地降低生产成本,提高产能。
下面列举一些提高机床加工效率的方案:•优化加工程序:合理编写加工程序,避免重复操作和浪费时间。
磨床总体设计开题报告
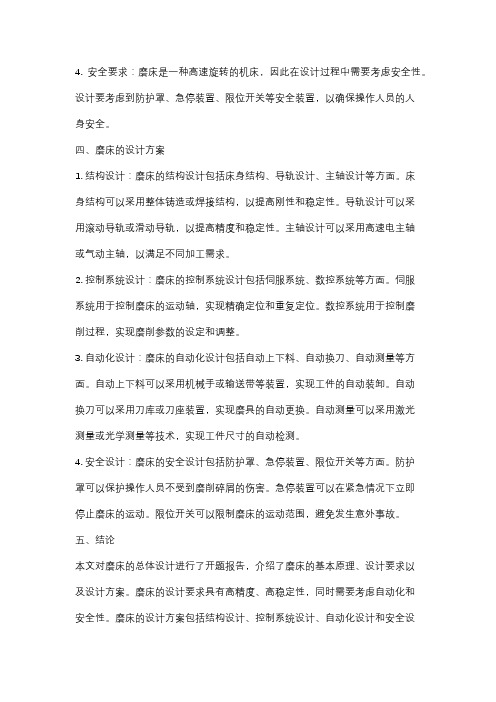
磨床总体设计开题报告磨床总体设计开题报告一、引言在现代制造业中,磨床是一种重要的加工设备,被广泛应用于金属加工、精密零件加工等领域。
磨床的设计与优化对于提高产品质量、提高生产效率具有重要意义。
本文将对磨床的总体设计进行开题报告,介绍磨床的基本原理、设计要求以及设计方案。
二、磨床的基本原理磨床是一种通过磨削工艺将工件加工至精确尺寸和表面质量的机床。
其基本原理是利用磨削磨具与工件之间的相对运动,在磨削力的作用下,将工件表面的金属材料剥离,从而实现加工的目的。
磨床的工作过程包括工件夹持、磨削过程控制以及冷却润滑等环节。
三、磨床的设计要求1. 精度要求:磨床是一种高精度加工设备,因此其设计要求具有高精度、高稳定性。
在设计过程中需要考虑磨削精度、定位精度、重复定位精度等因素,以确保加工出的工件尺寸和表面质量满足要求。
2. 刚性要求:磨床在工作过程中需要承受较大的切削力和振动力,因此其设计要具备足够的刚性。
刚性设计包括床身结构、导轨设计、主轴设计等方面,以确保磨床在高速运动和高负荷下不易变形,保持加工精度。
3. 自动化要求:随着制造业的发展,自动化生产已成为趋势。
磨床的设计要考虑自动化程度,包括自动上下料、自动换刀、自动测量等功能,以提高生产效率和降低人工成本。
4. 安全要求:磨床是一种高速旋转的机床,因此在设计过程中需要考虑安全性。
设计要考虑到防护罩、急停装置、限位开关等安全装置,以确保操作人员的人身安全。
四、磨床的设计方案1. 结构设计:磨床的结构设计包括床身结构、导轨设计、主轴设计等方面。
床身结构可以采用整体铸造或焊接结构,以提高刚性和稳定性。
导轨设计可以采用滚动导轨或滑动导轨,以提高精度和稳定性。
主轴设计可以采用高速电主轴或气动主轴,以满足不同加工需求。
2. 控制系统设计:磨床的控制系统设计包括伺服系统、数控系统等方面。
伺服系统用于控制磨床的运动轴,实现精确定位和重复定位。
数控系统用于控制磨削过程,实现磨削参数的设定和调整。
磨削机床改善方案
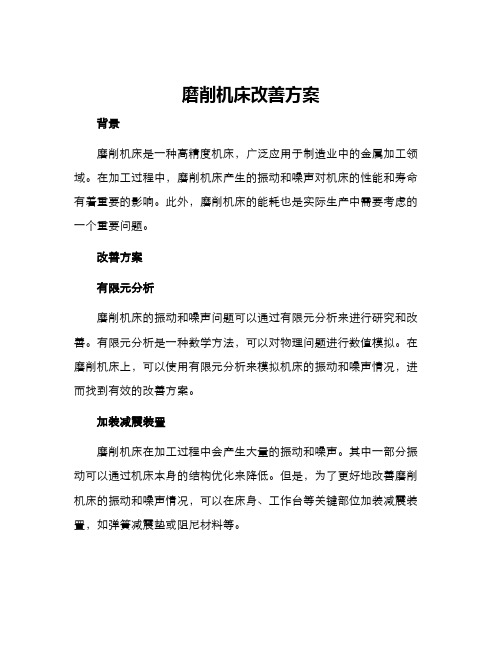
磨削机床改善方案背景磨削机床是一种高精度机床,广泛应用于制造业中的金属加工领域。
在加工过程中,磨削机床产生的振动和噪声对机床的性能和寿命有着重要的影响。
此外,磨削机床的能耗也是实际生产中需要考虑的一个重要问题。
改善方案有限元分析磨削机床的振动和噪声问题可以通过有限元分析来进行研究和改善。
有限元分析是一种数学方法,可以对物理问题进行数值模拟。
在磨削机床上,可以使用有限元分析来模拟机床的振动和噪声情况,进而找到有效的改善方案。
加装减震装置磨削机床在加工过程中会产生大量的振动和噪声。
其中一部分振动可以通过机床本身的结构优化来降低。
但是,为了更好地改善磨削机床的振动和噪声情况,可以在床身、工作台等关键部位加装减震装置,如弹簧减震垫或阻尼材料等。
采用低噪声润滑系统磨削机床在加工过程中需要使用润滑油来降低磨损和摩擦力,从而提高加工质量和效率。
但是,传统的润滑系统往往会产生大量的噪声和震动,影响磨削机床的使用效果。
为了解决这个问题,可以采用低噪声润滑系统,如无油润滑系统、静压轴承系统等。
变频控制技术磨削机床在加工过程中需要不断调节转速和进给量,以保证加工质量和效率。
传统的控制方法往往采用恒转速和定进给量的方式,但这样容易产生能耗浪费和材料损失。
为了更好地解决这个问题,可以采用变频控制技术来调节转速和进给量,提高机床的加工效率。
总结磨削机床是制造业中重要的加工工具,因为其高精度和高效率的特点被广泛应用。
然而,磨削机床在加工过程中会产生各种问题,如振动、噪声和能耗等。
通过有限元分析、加装减震装置、采用低噪声润滑系统和变频控制技术等方法,可以有效地改善这些问题,提高磨削机床的加工质量和效率。
24多用刀具磨削机设计(车削类刀具)毕业设计开题报告

3.学生须在小组内进行报告,并进行讨论;
4.本报告作为指导教师、毕业论文(设计)指导小组审查学生能否承担该毕业设计(论文)课题和是否按时完成进度的检查依据,并接受学校的抽查。
其他一些具体的结构设计就需要多了解现阶段与此类密切相关的的磨床结构。而且目前对此类磨床技术研究比较多,成果也不少,通过参照这些已有成果,对这一项目的完成很有帮助。
总之,完成这一项目需要多查阅相关的资料和自己不断的思考创新。因为这种磨床技术发展不是很成熟,其技术空间很大,能够创新的地方也很多。我有信心能通过自己的努力完成这一设计。
经过三个礼拜的毕业调研和查阅资料,我对本课题的主要意图还是有一定的了解,大至的了解了要完成的设计任务,综合起来,我认为最需要解决的主要问题有:
由于以前没有看到过相关产品的机构,所以设计起来许多基本的理论知识都不够。其设计过程中所需要的一些参数也了解不多,如磨削刀具所要的共同机构的参数设计,刀具角度的换算,如何实现传动结构的精确平稳性等等。要很好的完成这一项目,首先必须解决这些基本理论问题。
因此,我们可以根据各种刀具的相关步骤找出其共同点。然后根据这些特点找出几种机构组成一个可以满足产品成型的方案来。从而制造出来我们设想的产品,达到产品的预期。由于很多企业没有这样的专用设备,因此市场前景很大。但很多企业不是很重视这一道工序,对其投入不大,所以在设计过程中要尽量注重起制造成本。
2.本课题有待Biblioteka 决的主要关键问题虽然市场上也有不少这产品,但是要想有深入的了解和深刻的体会还有待于做出更深的调研,通过相互比较,最后选择一种更加合理的经济划算的并且操作较为方便的机构。
刀具的磨削不仅要求操作者了解刀具切学部分的构成要素,如(1)前刀面(2)主后刀面(3)副后刀面(4)主切削刃(5)副切削刃(6)刀尖,而且要求操作者了解刀具的材料等等。所以要解决这一问题不仅要求设计者拥有较为系统的理论知识还要求设计者能够运用一些相关原理设计出满足这些共同特性的巧妙机构来。
磨削机床改善方案
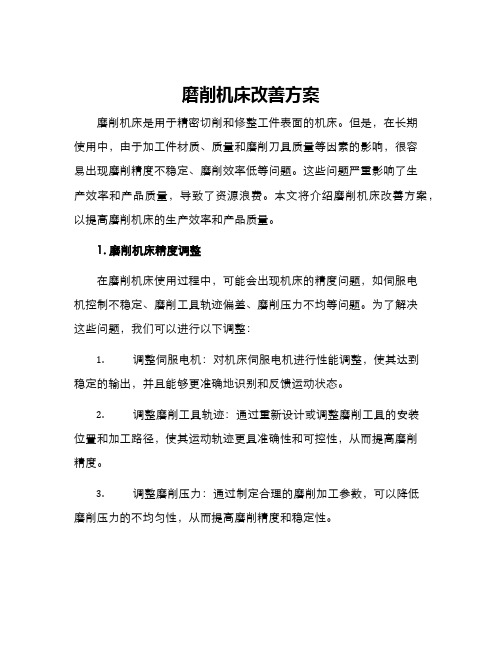
磨削机床改善方案磨削机床是用于精密切削和修整工件表面的机床。
但是,在长期使用中,由于加工件材质、质量和磨削刀具质量等因素的影响,很容易出现磨削精度不稳定、磨削效率低等问题。
这些问题严重影响了生产效率和产品质量,导致了资源浪费。
本文将介绍磨削机床改善方案,以提高磨削机床的生产效率和产品质量。
1. 磨削机床精度调整在磨削机床使用过程中,可能会出现机床的精度问题,如伺服电机控制不稳定、磨削工具轨迹偏差、磨削压力不均等问题。
为了解决这些问题,我们可以进行以下调整:1.调整伺服电机:对机床伺服电机进行性能调整,使其达到稳定的输出,并且能够更准确地识别和反馈运动状态。
2.调整磨削工具轨迹:通过重新设计或调整磨削工具的安装位置和加工路径,使其运动轨迹更具准确性和可控性,从而提高磨削精度。
3.调整磨削压力:通过制定合理的磨削加工参数,可以降低磨削压力的不均匀性,从而提高磨削精度和稳定性。
2. 磨削机床工具刀具优化磨削工具刀具是影响磨削效率和精度的重要参数。
现在市场上有许多高性能的磨削工具刀具,可以满足不同的磨削需求。
如何选择合适的磨削工具刀具也是一个非常重要的问题。
1.选择合适的材质:高效的磨削工具刀具材料可以有效降低磨削力和磨损率,提高加工效率和切削精度。
2.优化设计:通过设计和改进刀具的形状和尺寸,可以降低加工力和热量,提高磨削精度和加工效率。
3.确定正确的切削参数:制定合理的切削参数,最大限度地利用磨削工具的性能,提高磨削效率和精度。
3. 磨削机床冷却系统优化磨削过程会产生大量的热量,如果不能及时去除,会导致加工效率下降、加工质量下降、工件变形、刀具磨损过度等问题。
因此,冷却系统的优化非常重要。
1.选择适当的冷却介质:根据加工材料的特性和加工工艺的要求,选择合适的冷却介质,例如水、液氮、液碳等。
2.设计合理的喷淋系统:通过设计喷淋系统的数量、位置和喷淋角度,使冷却液覆盖面积更大,降低磨削加工区域的热量。
3.优化冷却系统的管道:将冷却管道设置得更加合理,减少阻力,提高冷却效率。
磨削加工的改进方案

磨削加工的改进方案引言磨削加工是一种常见的精密加工方法,用于加工各种材料的表面,以获得更高的平整度和精度。
在工业生产中,磨削加工常被用于制造精密零件、模具、工具等。
然而,传统的磨削加工存在一些问题,如工艺复杂、能量浪费、磨削效率低等。
为了提高磨削加工的效率和质量,需要进行一些改进方案的研究和实施。
本文将介绍几种磨削加工的改进方案,以期能够在实际应用中取得更好的效果。
1. 刀具材料的改进在磨削加工中,刀具材料的选择直接影响着加工的效率和质量。
传统的磨削加工中常使用金刚石砂轮作为刀具,但其切削效率并不高。
因此,可以考虑改进刀具材料,例如采用复合材料或高性能陶瓷材料来制作砂轮。
这些材料具有更高的硬度和耐磨性,能够提高切削效率和使用寿命。
2. 润滑液的改进磨削加工中,润滑液不仅能够降低磨削过程中的摩擦系数,还能冷却和清洁工件和刀具,保证加工过程的稳定性和质量。
因此,改进润滑液的性能和使用方式对于提高磨削加工效果至关重要。
可以探索使用新型的润滑液或添加剂来改善摩擦系数和冷却效果,提高工件表面质量,并减少刀具的磨损。
3. 增加辅助工具或装置为了改善磨削加工的效率和质量,可以考虑增加一些辅助工具或装置。
例如,可以采用自动化设备来控制磨削过程,提高加工精度和稳定性。
另外,还可以设计和使用专门的夹具或固定装置,以确保工件在加工过程中的稳定性和一致性。
4. 利用机器学习和人工智能技术近年来,机器学习和人工智能技术在许多领域取得了显著的进展,磨削加工也不例外。
利用这些技术可以对磨削加工进行优化和自动化。
通过对磨削加工参数和工件特性进行数据分析和建模,可以实现更精确的加工控制和优化。
例如,可以利用机器学习算法来预测砂轮的磨损和寿命,从而实现及时更换和调整,提高加工效率和工件质量。
5. 加强操作人员培训和管理虽然改进磨削加工的技术和设备是重要的,但操作人员的技能和经验同样不可忽视。
加强操作人员的培训和管理,提高其对磨削加工过程的理解和把握能力,对于提高加工效率和质量至关重要。
模具车间环境改善方案
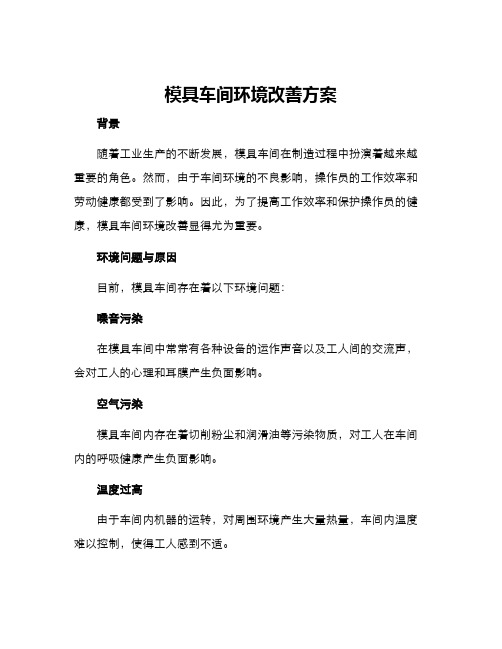
模具车间环境改善方案背景随着工业生产的不断发展,模具车间在制造过程中扮演着越来越重要的角色。
然而,由于车间环境的不良影响,操作员的工作效率和劳动健康都受到了影响。
因此,为了提高工作效率和保护操作员的健康,模具车间环境改善显得尤为重要。
环境问题与原因目前,模具车间存在着以下环境问题:噪音污染在模具车间中常常有各种设备的运作声音以及工人间的交流声,会对工人的心理和耳膜产生负面影响。
空气污染模具车间内存在着切削粉尘和润滑油等污染物质,对工人在车间内的呼吸健康产生负面影响。
温度过高由于车间内机器的运转,对周围环境产生大量热量,车间内温度难以控制,使得工人感到不适。
光线照射不足在模具车间中,有时会因为照明设施不足,导致工人在操作中的视野不够明确,容易出现安全事故。
解决方案模具车间环境的改善,需要采用多种措施,下面列出了一些可行的方案。
噪音控制•研发降噪耳塞,减少工人噪音暴露量。
•安装隔音材料和振动吸收器,降低机器噪音。
•将会话和交流限制在特定的区域内,减少对周围的干扰。
空气污染控制•安装新的通风设备和空气过滤器,清洁车间空气。
•定期更换切削液和润滑剂,减少化学污染物质的暴露量。
•鼓励工人佩戴口罩,保护呼吸道健康。
温度控制•安装空调系统,控制车间内的温度。
•定期对车间进行清洁,减少积尘的堆积,保持空气流通。
•研发出更为高效的机器,并且减少热量损失。
光线优化•安装更高效的照明设备,以确保足够的光照度。
•避免照明设备直接照在工人的眼中,使用反光材料来提高照射效果。
•增加照明设备的数量,以确保完美周围环境的光线照射均衡。
结语模具车间改善环境方案的目的是保护工人健康和提高生产效率,因此各种方案的实施都要根据实际情况而定。
应关注环境改善的成本和效益,并在实施过程中加强对工人的培训和意识教育,以充分利用环境改善的优势。
模具车间环境改善方案

模具车间环境改善方案背景介绍模具车间是一个重要的制造领域,主要生产各种模具。
然而,在车间环境整体质量方面,模具车间经常面临挑战。
这些挑战可能涉及噪声、空气和水质量问题。
这些因素不仅会影响员工的生产效率和安全,还可能影响他们的身体健康。
因此,必须采取措施对模具车间环境进行改善。
噪声问题噪声对员工的健康产生负面影响,因此在模具车间中必须对噪声进行合理控制。
在车间中进行如下操作可能会有所帮助:•安装隔音墙或吸音材料。
•采用低噪声设备。
•加强维护和保养。
通过这些措施减少噪声的扰动,可让员工更好地集中注意力,提高他们的工作效率。
空气污染车间中的空气中可能存在各种有害气体和颗粒物,如甲醛、氨气等。
如果不进行及时的处理,这些有害气体和颗粒物可能会对员工造成长期性的健康问题,如呼吸系统疾病等。
为改善空气质量,应采用以下方法:•安装先进的通风设备来保证良好的空气对流。
•采用过滤器和空气净化设备来去除空气中的颗粒物和有害气体。
•对车间进行定期清洁,确保空气中的杂质得到有效清除。
通过上述措施可以改善空气质量,减少员工对空气污染的暴露几率。
水质处理水质的质量也是一个非常关键的问题。
在模具车间中,水是必不可少的,用来冷却机器、清洗设备和工作表面等。
因此,必须确保水的质量达到一定的标准。
应采用以下方法改善水质:•对车间的水源进行定期检测,确保水质符合相关标准。
•安装过滤设备来去除杂质。
•对水箱定期清洁和消毒。
通过上述措施,可以确保水质稳定并帮助员工在车间中更安全地工作。
结论通过改善模具车间环境质量,我们可以提高员工效率和安全,并可能大幅降低他们因车间环境造成的健康风险。
虽然改善车间环境质量的完整列表很长且复杂,但以上提到的方法应当对业界有所帮助。
磨削机床改善方案

磨削机床改善方案1. 前言磨削机床广泛应用于金属加工、电子制造、汽车制造、航空航天、医疗器械等各个领域。
磨削机床在加工过程中,具有加工精度高、表面质量好、效率高等优点。
随着社会经济的不断发展,磨削机床的应用范围也不断扩大。
然而,现实中,磨削机床存在一些问题,如产生噪音、精度低下、易损坏等。
这些问题显著影响了磨削机床的稳定性和效率。
本文将针对这些问题提出一个改善方案。
2. 问题分析2.1 噪音问题磨削机床主要产生噪音来源于磨削时磨削轮与工件的摩擦,金属切削时润滑条件变化幅度大、冷却液流量不足等引起的摩擦。
噪音是不仅影响工人的身心健康,同时也污染了环境。
2.2 精度低下问题磨削机床的精度低下问题,主要源于磨削轮的轮廓误差、切削力变化引起的变形、温度变化导致的机床变形等因素。
2.3 易损坏问题磨削机床易损坏问题,主要表现为磨削轮的磨损、机床零配件材料使用不当等因素引起的损坏。
3. 改善方案3.1 噪音问题的改善方案3.1.1 优化冷却液流量冷却液在金属加工中,可以起到降温、润滑和清洁效果。
增加冷却液的流量可以减少金属切削时摩擦带来的热量和噪音,同时可以减少切屑缠绕在磨削轮上的可能,从而降低噪音。
3.1.2 采用新型降噪材料使用新型降噪材料覆盖磨削机床的金属表面,可有效地吸收和反射噪音。
这将在一定程度上降低噪音,并有益于保护工人的健康。
3.2 精度低下问题的改善方案3.2.1 优化磨削轮的轮廓采用新型的磨削轮,可以改善磨削轮的轮廓误差。
这有助于提高磨削精度。
3.2.2 增加机床刚度增加磨削机床的刚度,可以减少切削力变换引起的变形。
这将有利于提高磨削精度。
3.3 易损坏问题的改善方案3.3.1 选择高质量磨削轮选择质量优良的磨削轮,可以有效地减少磨削轮的磨损,延长机器的使用寿命。
3.3.2 使用原厂配件使用原厂配件,可以保证机床零配件材料的使用质量。
这将有助于减少机床零配件的损坏。
4. 结论综上所述,针对磨削机床存在的问题,本文提出的改善方案包括:优化冷却液流量、采用新型降噪材料、优化磨削轮的轮廓、增加机床刚度、选择高质量的磨削轮和使用原厂配件等。
- 1、下载文档前请自行甄别文档内容的完整性,平台不提供额外的编辑、内容补充、找答案等附加服务。
- 2、"仅部分预览"的文档,不可在线预览部分如存在完整性等问题,可反馈申请退款(可完整预览的文档不适用该条件!)。
- 3、如文档侵犯您的权益,请联系客服反馈,我们会尽快为您处理(人工客服工作时间:9:00-18:30)。
开题报告工业工程磨削车间工作环境研究及改善1、选题的背景与意义随着企业的发展,员工的工作环境就决定生产的效率和生产的质量。
而工厂的车间机器的增加使得车间的工作环境的噪音变得不够好。
无论是环境照明或者环境噪音总是有一些令人不满意的地方。
对于达克轴承厂来说,改善车间的工作环境是企业发展的必要过程。
员工对环境的满意就决定企业的生产有一定的保障。
工作环境的提升对员工的身体的影响就少,而健康的员工他们会付出更多的激情来投入到生产中,从而使企业有较高的竞争能力。
这些都是企业所必须注意的。
因此,完全有必要改善磨削车间的工作环境,而工业工程的方法研究恰恰在改善车间环境方面有较好的应用。
本次设计主要是研究和改善磨削车间的工作环境,应用方法研究的有关原则和知识改善磨削车间的工作环境等非人为因素方面的不足之处,提升员工的工作效率和生产质量。
不仅能帮助我更熟练地运用、巩固方法研究的有关知识,而且也锻炼了我分析问题,解决问题能力。
同时,对于磨削车间工作环境的改善也具有一定的现实意义。
2.研究的基本内容与拟解决的主要问题2.1、研究的基本内容(1)研究衡量工作环境的方法车间环境是客观性很强的指标,研究起来是一件有很多面得工作。
此时,就着重研究照明、噪音及空气流通等方面的问题。
这些都是有一定得标准。
通过对环境方面的研究,继而现场对照明、噪音的测量,为后续的研究做准备.( 2 )研究如何改善磨削车间工作环境得照明、噪音,并探索工业工程知识在改善工作环境上的运用针对已经测量好的照明、噪音的有关数据和结果进行分析研究,结合工业工程的有关知识,并探索方法研究在改善工作环境上的运用,并提出改善的建议。
2.2、拟解决的问题(1)根据车间的布局确定测量的位置,使其能够满足实际要求,并对磨削车间工作环境进行测量在本次的实验设计中,不但要学习和探究测量磨削车间工作环境的方法,确定测量的位置,并在磨削车间实地测量时,通过现场的测量,为下一步的研究做数据资料的准备。
(2)根据磨削车间工作环境的情况,如何进行测量数据汇总整理,分析工作环境的好坏收集测量数据之后,对数据进行汇总整理,保证数据的直观、有效,根据测量关照、噪音的结果,直接磨削车间环境的不足,分析其与环境要求达到的照明、噪音方面的标准之间的差距,进而判断磨削车间工作环境的好坏。
(3)如何提出改善磨削车间工作环境的建议和措施针对磨削车间现在工作环境方面的不足和缺陷,进行分面整理,运用方法研究的有关知识,从照明强度、噪音和客气流通等各个方面进行分析研究,并结合现有的一些关系车间工作环境的方法,听出改善的建议。
同时,也要保证这些建议和措施对企业方面具有较高的可行性和良好的执行性。
3.研究的方法与技术路线:3.1、研究方法在该课题的研究过程中,我将本着理论与实践相结合的方法来进行研究分析。
首先是查阅大量有关改善和提升车间工作环境的文献,确定符合磨削车间工作环境的方法;其次是通过实证调研的方法,到达克轴承有限公司进行现场测量和调查,分析标准与现状的差距,继而运用方法研究的有关知识,提出改善的建议,并逐步完善该实验项目。
3.2、技术路线4.研究的总体安排与进度1.熟悉课题相关知识,文献综述;(2周)2.现场调研;(2周)3.工作环境分析与改善;(7周)整理, 撰写毕业论文;(2周)参考文献[1] Lena Abrahamsson P,roduction economics analysis of investment initiatedto improve working environment,[J],Applied Ergonomics 31 (2000) 1-7[2] Murray Hodgson. Ray-tracing evaluation of empirical models forpredicting noise in industrial workshops,[J],Applied Acoustics 64 (2003) 1033–1048[3] Nibel,B,Freivalds,A,方法、标准与作业设计[M], 北京:清华大学出版社,2007.4[4] 聂振帮,改善锻造车间环境,[M],METALLURGIA1989,NO.10.[5] 陶睿,浅谈纺织车间降噪的意义及措施[J],山东纺织经济2009年第6期,152-153、[6] 王继然孟广弟,生产车间照明节电改造浅谈[J],资源节约与环保2010年第二期,68-69[7] 高志霞,由振甫,李金虎,原煤准备车间噪音的控制[J],河北煤炭2002年第2期,51-52[8] 孙鹏子,姜淑媛,织布厂整理车间照明问题的分析探讨[J]辽宁丝绸2000年第4期,9-10、13毕业论文文献综述工业工程磨削车间工作环境研究及改善摘要:本文在阅读了大量关于研究及改善车间工作环境的基础上,阐述了工作环境的背景知识以及目前研究照明环境、噪音环境的方法,综合阐述了工业工程领域的方法研究在改善照明、噪音环境的应用,探索其在车间工作环境研究及改善的应用和发展。
关键词:照明环境;噪音环境;磨削车间;研究;改善1.引言车间是企业生产的基本实施组织。
而随着企业的发展壮大,员工的身体健康是一个不容忽视的问题。
而决定着员工身体的因素除了生产的产品之外还包括照明环境、噪音环境以及空气的流通。
这都对产品的质量有一定的保证,所以车间的环境是企业必须重视的一个环节。
照明对产品加工的是必须充足的,否则极易导致产品的不合格率和产量。
而噪音对人的影响是巨大的。
对于这两种环境的改善是企业发展的必要过程。
2.工作环境工作环境包括照明、噪音环境及空气流通。
达克轴承有限公司的生产车间具有良好的空气流动行且具有专门的通风口。
所以这里就不在研究及改善。
侧重于照明、噪音方面的研究和改善。
2.1照明环境的标准照明是利用各种光源照亮工作和生活场所或个别物体的措施。
利用太阳和天空光的称“天然采光”;利用人工光源的称“人工照明”。
照明的首要目的是创造良好的可见度和舒适愉快的环境。
工业企业的照明具有一定的标准。
例GB50034-92。
【1】2.2噪音的标准高志霞、由振甫、李金虎在《原煤准备车间噪音的控制》所提及的标准。
噪声即噪音。
是一类引起人烦躁、或音量过强而危害人体健康的声音。
从环境保护的角度看,凡是影响人们正常学习、工作和休息的声音、凡是人们在某些场合“不需要的声音”,都统称为噪声。
从物理角度看,噪声是发生体做无规则振动时发出的声音。
工业企业的噪声是有一定的的标准的。
在工业企业噪声卫生标准中规定, 工业企业的生产车间和作业地点的噪音标准为85dB, 现有工业企业经努力达不到标准的可适当放宽, 但不得超过90dB,连续生产的单位, 其标准应控制在85dB~ 90dB, 否则必须采取降噪措施。
【2】2.3照明不足对车间的影响照明的不足会对工人的视力和产品质量产生影响。
会使工人视力下降。
例如孙鹏子、姜淑媛在《织布厂整理车间照明问题的分析探索》中有提到。
整理车间照明对工人视力的影响及产生原因。
一般的验布机视距为56cm, 识别物最小直径为0. 15mm, 修布工视距为22cm,按规定整理车间工人属于精细作业工人。
调查中发现, 整理车间很多工人都存在视力下降的问题, 部分工人还存在着眼疾, 一部分工人还有晨起眼肿的现象。
许多资料也介绍, 整理车间的确存在着较严重视疲劳, 视疲劳表现为视力下降、头痛头晕、视物不清等, 如新工人进厂2 年后, 视力由1. 5 降到1. 2。
验布机工人产生视疲劳原因在于:①.所检验疵点小;②.验布作业随着布匹机械传送而运动, 视标的移动使视距不断地变化, 从而使腱状肌处于不断舒缩状, 以便调节晶状体能形成最清晰形象, 因而眼睛容易疲劳;③.有大部分工厂亮度分布不均匀;④.有的工厂验布机照度太低。
修布工人产生视疲劳原因是:①.布匹疵点较小, 而视距只有22cm 左右, 长时期在这种环境下工作易使调节紧张, 产生视疲劳。
②.照明不合适, 有的工厂工作面照度值只有150Lx , 在这样低照度下工人视力不能不受到损伤。
照明不合适的另一个原因是照度值太高, 有的工厂照度值偏高, 而照度偏高也会使工人疲劳。
我国标准为300Lx , 对这种照度值工人反映良好。
③.灯的显色性不合适。
一般工厂应用灯显色性一般为60~80 左右, 比较低些。
【3】2.4噪音对车间的影响陶睿在《浅谈纺织车间降噪的意义及措施》中有论述。
2.4.1噪声对人的影响噪声对人体最直接的危害是听力损伤。
人们在进入强噪声环境时,暴露一段时间,会感到双耳难受,甚至会出现头痛等感觉。
有研究表明,噪声污染是引起老年性耳聋的一个重要原因。
此外,听力的损伤也与生活的环境及从事的职业有关,如农村老年性耳聋发病率较城市为低,纺织厂工人、锻工及铁匠与同龄人相比听力损伤更多。
但听觉器官只是“入口”,通过这个入口,噪声侵入人体而影响神经系统,结果内颅侧与血压发生变化,视觉敏锐性被破坏,注意力减弱,在同样体力劳动强度下增加能量的消耗,并且使心理反应的速度变得迟钝。
由于这些原因在纺织车间中工作的人员易产生疲劳,遭受头痛和失眠的折磨。
据统计,噪声会使劳动生产率降低10~50%,由此可见,噪声会分散人的注意力,导致反应迟钝,容易疲劳,工作效率下降,差错率上升。
2.4.2噪声对设备的影响特强噪声会损伤仪器设备,甚至使仪器设备失效。
噪声对仪器设备的影响与噪声强度、频率以及仪器设备本身的结构与安装方式等因素有关。
当噪声级超过150dB 时,会严重损坏电阻、电容、晶体管等元件。
当特强噪声作用于机械结构时,由于受声频交变负载的反复作用,会使材料产生疲劳现象而断裂。
2.4.3噪声对建筑的影响一般的噪声对建筑物几乎没有什么影响,但是噪声级超过140dB 时,对轻型建筑开始有破坏作用。
【4】3.文献中改善工作环境方法的汇总在确立提高产品生产质量为企业的经营目标之一前提下,改善工作环境是企业努力的方向,也是员工所希望的结果。
企业应关注自己企业生产车间的工作环境,发现工作环境中与工业企业的各个标准之间的差距,采取有效的方法来改善车间的工作环境。
才能更好的提高员工的工作效率。
这要求企业始终重视生产车间的工作环境,通过提高照明的强度、降低噪音源产生的噪音、加隔音层隔音间、采取个人防护措施等,以此来改善生产车间的工作环境。
改善照明环境。
孙鹏子、姜淑媛在《织布厂整理车间照明问题的分析探索》中提出的织布厂整理车间照明问题的改善建议。
首先, 提高认识。
全社会都应重视工效学的问题, 尤其是工厂的领导更应重视。
因为只有这样才能够提高产品质量, 保护工人身心的健康。
工人本身也应加强自我保护意识。
另外, 可采取以下几方面措施:①.照明要适宜, 即工作面照度值既不能太高也不能太低, 一般以300~400Lx较为适宜。