变形铝及铝合金热处理规范
变形铝及铝合金热处理规范

淬火设备和装卸装备的安装位置应保证淬火转移时间不得超过表5规定的最大淬火转移时间。
4.4.4 冲洗设备
根据需要应使用冲洗槽、喷嘴或其它适合的设备,以确保干燥后在金属表面没有盐液残留物或膜层存在。
4.4.5 支撑架、固定装置及其它工件架持装置的结构
铺设支承架时应当最低限地减少金属在固溶热处理时的振动或滑动。支架、固定装置、底座、吊篮的安装应保证在热处理时不会对所处理的产品表面产生影响。
GB/T 230 金属洛氏硬度试验方法
GB/T 231 金属布氏硬度试验方法
GB/T 3246.1铝及铝合金加工制品显微组织检验方法
GB/T 7998 铝合金晶间腐蚀测定方法
GB/T 9445 无损检测人员技术资格鉴定通则
GB/T 12966铝合金电导率涡流测试方法
GB/T 16475 变形铝及铝合金状态代号
W
T4、T41
T452
轧制环
516~552
W
T4、T41
T452
6063
挤压件
515~530
W
T4、T42
T4510、T4511
拉伸管
515~527
W
T4、T42
N/A
6262
线材、棒材
515~566
W
T4
T450
挤压件
515~566
W
T4
T4510、T4511
拉伸管
515~566
W
T4
—
表2 固溶热处理温度(续)
W
7A04
465~475
W
7A09
465~475
W
7010
厚板
变形铝合金时效热处理相关知识汇总

变形铝合金时效热处理相关知识汇总(1)时效 aging经固溶处理或冷变形后的合金,在室温或高于室温下,组织和性能随时间延续而变化,硬度、强度增高,塑性、韧性降低的现象。
在室温下发生时效称自然时效。
高于室温发生时效称人工时效。
时效现象除铝铜合金外,在钢、铜合金,铁基、银基、钻基高温合金中普遍存在,是提高合金强度的重要方法。
低碳钢冷变形后在常温长时放置即出现屈服强度提高。
硬铝合金经高斌520℃)淬火后在10g200℃时效,可获得最佳的强化效果。
马氏体时效钢,沉淀硬化不锈钢,铁基、镍基、钻基高温合金均可在固溶处理后选择不同温度时效处理,可以从中获得最佳的组织和性能。
(2)时效处理 aging treatment过饱和固溶体合金在室温或加热至一定温度保温,使溶质组元富集或析出第二相的热处理工艺。
常温下时效称自然时效。
高于室温加热时效称人工时效。
时效析出第二相获得强化的现象称时效强化。
低于或高于强化峰值温度的时效分别称为亚时效与过时效处理变后时效称形变时效或直接时效。
在应力下时效称应力时效强化效果取决于析出第二相的类数量、尺寸、形态、稳定性等因素。
广泛用于铝合金、钛合金、高温合金、沉淀硬化钢、马氏体时效钢等。
铝合金时效硬化峰值出现在溶质组元的富区(II)末期。
时效处理是强化合金的有效方法,可显著提高合金的强度和硬度,调整时效温度、时间可使合金的组织、性能满足使用要求,获得高的屈服强度、蠕变强度、疲劳性能等。
含铜的铝合金经自然时效后强度为0MPa比退火状态强度大一倍时效硬化合金使用时使用温度不应超过其时效温度。
(3)时效硬化 age hardening经固溶处理的过饱和固溶体在室温或室温以上时效处理,硬度或强度显著增加的现象。
原因是过饱和固溶体在时效过程中发生沉淀、偏聚、有序化等反应的产物,增加了位错运动的阻力形成的。
位错与析出产物交互作用下硬化机制有位错剪切析出相粒子,基体与粒子间相界面积增加,使外力转变为界面能析出相与基体的层错能差异基体与析出粒子的切变模量不同。
GBT 26492.3-2011 变形铝及铝合金铸锭及加工产品缺陷 第3部分:板、带缺陷

变形铝及铝合金板、带缺陷1范围本标准规定了变形铝及铝合金板、带产品中常见的缺陷的定义、特征,分析了其产生的原因,并附有相应部分图片。
本标准适用于变形铝及铝合金板、带缺陷的分析与判定。
2缺陷定义、特征、产生原因典型事例2.1非金属压入2.1.1缺陷定义及特征非金属杂物压入板、带表面。
表面呈明显的点状或长条状黄黑色缺陷。
2.1.2产生原因a)轧制工序设备条件不清净;b)轧制工艺润滑剂不清静;c)工艺润滑剂喷射压力不足;d)板坯表面有擦划伤。
图1非金属压入2.2金属压入2.2.1缺陷定义及特征金属屑或金属碎片压入板、带表面。
压入物刮掉后呈大小不等的凹陷,破坏了压入板、带表面的连续性。
2.2.2产生原因a)热轧时辊边道次少,裂边的金属屑、条掉在板坯表面后压入;b)圆盘剪切边工序质量差,产生毛刺掉在带坯上经轧制后压入;c)轧辊粘铝后,其粘铝又被压在板坯上;d)热轧导尺夹得过紧,带下来的碎屑掉在板坯上后被压入。
图2金属压入2.3划伤2.3.1缺陷定义及特征因尖锐的物体(如板角、金属屑或设备上的尖锐物等)与板面接触,在相对滑动时所造成的呈单条状分布的伤痕。
2.3.2产生原因a)热轧机辊道、导板上粘铝使板、带划伤;b)冷轧机导板、压平辊等有突出的尖锐物;c)精整时板角划伤;d)涂油包装时油中有金属屑带到涂油辊或毛毡上而划伤板面。
图3划伤2.4擦伤2.4.1缺陷定义及特征由于物体间棱与面,或面与面接触后发生相对滑动或错动而在板、带表面造成的成束(或组)分布的伤痕。
2.4.2产生原因a)板、带在加工生产过程中与导路、设备接触时,产生相对摩擦而造成擦伤;b)冷轧卷端面不齐正,在立式炉退火翻转时产生错动、层与层之间产生擦伤;c)冷轧时张力不当,开卷时产生层间错动而产生擦伤;d)精整验收或包装操作不当产生板间滑动而造成擦伤。
图4擦伤2.5碰伤2.5.1缺陷定义及特征铝板、铝卷与其他物体碰撞后在板、带表面或端面产生的划痕,且大多数在凹陷边际有被挤出的金属存在。
铝合金的热处理工艺

铝合金的热处理铸造铝合金的金相组织比变形铝合金的金相组织粗大;因而在热处理时也有所不同..前者保温时间长;一般都在2h以上;而后者保温时间短;只要几十分钟..因为金属型铸件、低压铸造件铸造铝合金的金相组织比变形铝合金的金相组织粗大;因而在热处理时也有所不同..前者保温时间长;一般都在2h以上;而后者保温时间短;只要几十分钟..因为金属型铸件、低压铸造件、差压铸造件是在比较大的冷却速度和压力下结晶凝固的;其结晶组织比石膏型、砂型铸造的铸件细很多;故其在热处理时的保温也短很多..铸造铝合金与变形铝合金的另一不同点是壁厚不均匀;有异形面或内通道等复杂结构外形;为保证热处理时不变形或开裂;有时还要设计专用夹具予以保护;并且淬火介质的温度也比变形铝合金高;故一般多采用人工时效来缩短热处理周期和提高铸件的性能..一、热处理的目的铝合金铸件热处理的目的是提高力学性能和耐腐蚀性能;稳定尺寸;改善切削加工和焊接等加工性能..因为许多铸态铝合金的机械性能不能满足使用要求;除Al-Si系的ZL102;Al-Mg 系的ZL302和Al-Zn系的ZL401合金外;其余的铸造铝合金都要通过热处理来进一步提高铸件的机械性能和其它使用性能;具体有以下几个方面:1消除由于铸件结构如璧厚不均匀、转接处厚大等原因使铸件在结晶凝固时因冷却速度不均匀所造成的内应力;2提高合金的机械强度和硬度;改善金相组织;保证合金有一定的塑性和切削加工性能、焊接性能;3稳定铸件的组织和尺寸;防止和消除高温相变而使体积发生变化;4消除晶间和成分偏析;使组织均匀化..二、热处理方法1、退火处理退火处理的作用是消除铸件的铸造应力和机械加工引起的内应力;稳定加工件的外形和尺热到280-300℃;保温2-3h;随炉冷却到室温;使固溶体慢慢发生分解;析出的第二质点聚集;从而消除铸件的内应力;达到稳定尺寸、提高塑性、减少变形、翘曲的目的..2、淬火淬火是把铝合金铸件加热到较高的温度一般在接近于共晶体的熔点;多在500℃以上;保温2h以上;使合金内的可溶相充分溶解..然后;急速淬入60-100℃的水中;使铸件急冷;使强化组元在合金中得到最大限度的溶解并固定保存到室温..这种过程叫做淬火;也叫固溶处理或冷处理..3、时效处理时效处理;又称低温回火;是把经过淬火的铝合金铸件加热到某个温度;保温一定时间出炉空冷直至室温;使过饱和的固溶体分解;让合金基体组织稳定的工艺过程..合金在时效处理过程中;随温度的上升和时间的延长;约经过过饱和固溶体点阵内原子的重新组合;生成溶质原子富集区称为G-PⅠ区和G-PⅠ区消失;第二相原子按一定规律偏聚并生成G-PⅡ区;之后生成亚稳定的第二相过渡相;大量的G-PⅡ区和少量的亚稳定相结合以及亚稳定相转变为稳定相、第二相质点聚集几个阶段..时效处理又分为自然时效和人工时效两大类..自然时效是指时效强化在室温下进行的时效..人工时效又分为不完全人工时效、完全人工时效、过时效3种..1不完全人工时效:把铸件加热到150-170℃;保温3-5h;以获得较好抗拉强度、良好的塑性和韧性;但抗蚀性较低的热处理工艺;2完全人工时效:把铸件加热到175-185℃;保温件加热到190-230℃;保温4-9h;使强度有所下降;塑性有所提高;以获得较好的抗应力、抗腐蚀能力的工艺;也称稳定化回火..4、循环处理把铝合金铸件冷却到零下某个温度如-50℃、-70℃、-195℃并保温一定时间;再把铸件加热到350℃以下;使合金中度固溶体点阵反复收缩和膨胀;并使各相的晶粒发生少量位移;以使这些固溶体结晶点阵内的原子偏聚区和金属间化合物的质点处于更加稳定的状态;达到提高产品零件尺寸、体积更稳定的目的..这种反复加热冷却的热处理工艺叫循环处理..这种处理适合使用中要求很精密、尺寸很稳定的零件如检测仪器上的一些零件..一般铸件均不作这种处理..5、铸造铝合金热处理状态代号及含义代号合金状态热处理的作用或目的说明T1人工时效在金属型或湿砂型铸造的合金;因冷却速度较快;已得到一定程度的过饱和固溶体;即有部分淬火效果..再作人工时效;脱溶强化;则可提高硬度和机械强度;改善切削加工性..对提高Zl104、ZL105等合金的强度有效..T2退火主要作用在于消除铸件的内应力铸造应力和机加工引起的应力;稳定铸件尺寸;并使Al-Si系合金的Si晶体球状化;提高其塑性..对Al-Si系合金效果比较明显;退火温度280-300℃;保温时间为2-4h..T4固溶处理淬火加自然时效通过加热保温;使可溶相溶解;然后急冷;使大量强化相固溶在α固溶体内;获得过饱和固溶体;以提高合金的硬度、强度及抗蚀性..对Al-Mg系合金为最T5固溶处理淬火加不完全人工时效用来得到较高的强度和塑性;但抗蚀性会有所下降;非凡是晶间腐蚀会有所增加..时效温度低;保温时间短;时效温度约150-170℃;保温时间为3-5h..T6固溶处理淬火加完全人工时效用来获得最高的强度;但塑性和抗蚀性有所降低..在较高温度和较长时间内进行..适用于要求高负荷的零件;时效温度约175-185℃;保温时间5h以上..T7固溶处理淬火加稳定化回火用来稳定铸件尺寸和组织;提高抗腐蚀非凡是抗应力腐蚀能力;并保持较高的力学性能..多在接近零件的工作温度下进行..适合300℃以下高温工作的零件;回火温度为190-230℃;保温时间4-9h..T8固溶处理淬火加软化回火使固溶体充分分解;析出的强化相聚集并球状化;以稳定铸件尺寸;提高合金的塑性;但抗拉强度下降..适合要求高塑性的铸件;回火温度约230-330℃;保温时间3-6h..T9循环处理用来进一步稳定铸件的尺寸外形..其反复加热和冷却的温度及循环次数要根据零件的工作条件和合金的性质来决定..适合要求尺寸、外形很精密稳定的零件..三、热处理工艺1、铸造铝合金热处理工艺参数合金牌号合金代号热处理固溶处理时效处理保温后空冷ZAlSi7MgZL101T2---300±102-4T4535±52-620-100--T5535±52-620-100150±52-4T6535±52-620-100200±52-5T7535±52-680-100225±53-5T8535±52-680-100250±103-5T5二阶段535±52-620-100190±100.5 150±52ZAlSi7MgAZL101AT1---190±53-4T2---300±102-4T4535±510-1620-100--T5535±510-1620-100175±56ZAlSi12ZL102T2---300±102-4ZAlSi9MgZL104T1---175±55-17T6535±52-620-100175±510-15 ZAlSi5Cu1MgZL105T1---180±55-10T5525±53-520-100175±55-10T6525±53-520-100200±53-5T7525±53-520-100230±103-5ZAlSi5Cu1MgAZL105AT1---180±55-10 T5525±53-520-100175±55-10T6525±53-520-100200±53-5ZAlSi8Cu1MgZL106T1---200±105-8T2---280±105-8T5515±54-820-100170±58-16T6515±54-820-100160±54-6T7515±54-820-100230±53-5ZAlSi7Cu4ZL107T6515±55-720-100170±105-7ZAlSi12Cu2Mg1ZL108T1---190±58-12T6515±56-820-70175±514-18T7515±53-820-70240±106-10ZAlSi12Cu1Mg1Ni1ZL109T1---205±58-12T6515±56-820-70180±514-18ZAlSi9Cu2MgZL111T6520±54-620-70180±56-8ZAlSi7Mg1AZL114AT5535±52-720-100150±51-3T6540±58-1265-100160±53-5ZALSi5Zn1MgZL115T4550±51665-100--T5550±51665-100160±54ZAlSi8MgBeZL116T1---190±53-4T2---300±102-4T4535±510-1620-100--T5535±510-1620-100175±56T6535±510-1620-100160±53-8ZAlCu5MnZAlCu5MnAZL201ZL201AT4545±510-1220-100--ZAlCu10ZL202T2---290±53ZAlCu4ZL203T4515±510-1520-100--T5515±510-1520-100150±52-4ZAlCu5MnCdAZL204AT6535±57-940-100175±53-5T7535±57-940-100190±53-5ZAlCu5MnCdVAZL205AT5535±510-1520-60155±58-10T6535±510-1520-60175±53-5T7535±510-1520-60195±53-5ZAlRE5Cu3Si2ZL207T1---200±55-10ZAlMg10ZL301T4430±1020100或油--ZAlMg8Zn1ZL305T4455±56-880-100--ZAlZn11Si7Zl401T1---200±105-10T2---300±102-4ZAlZn6MgZL402T1---175±56-8T5---室温20天T5---175±56-82、热处理操作技术要点1热处理前应检查热处理设备、辅助设备、仪表等是否合格和正常;炉膛各处的温度差是否在规定的范围之内±5℃;2装炉前应吹砂或冲洗;应无油污、脏物、泥土;合金牌号不应相混;3形性状易产生翘曲的铸件应放在专用的底盘或支架上;不答应有悬空的悬臂部分;5在保温期间应随时检查、校正炉膛各处温度;防止局部高温或烧化;6在断电后短时间不能恢复时;应将在保温中的铸件迅速出炉淬火;等恢复正常后;再装炉、保暖和进行热处理;7在硝盐槽中淬过火的铸件;应在淬火后立即用热水冲洗;消除残盐;防止腐蚀;8发现淬火后铸件变形;应立即予以校正;9要时效处理的零件;应在淬火后0.5h内进行时效处理;10如在热处理后发现性能不合格;可重复进行热处理;但次数不得超过2次;11应根据铸件结构外形、尺寸、合金特性等制定的热处理工艺进行热处理..3、热处理缺陷的产生原因和消除与预防办法缺陷名称缺陷表现产生原因消除与预防办法力学性能不合格退火状态δ5偏低;淬火或时效处理后强度和延伸率不合格..退火温度偏低或保温时间不足;或冷却太快;淬火温度偏低或保温时间不够;或冷却速度太慢淬火介质温度过高;不完全人工时效和完全人工时效温度偏高;或保温时间偏长;合金的化学成分出现偏差..再次退火;提高温度或延长保温时间;提高淬火温度或延长保温时间;降低淬火介质温度;如再次淬火;则要调整其后的时效温度和时间;如成分出现偏差;则要根据具体的偏差元素、偏差量、改变或调整重复热处理参数..变形、翘曲热处理后;或之后的机械加工中反映出来的铸件的尺寸、外形变化..加热速度或淬火冷却速度太快太激烈;淬火温度太高;铸件的设计结构不合理如两连接壁的壁厚相差太大;框形结构中加强筋太薄或太细小;淬火时工件下水方向不当及装料方法不当..降低升温速度;提高淬火介质温度;或换成冷却速度稍慢的淬火介质以防止合金内产生残余应力;在厚壁或薄壁部位涂敷涂料或用石棉纤维等隔热材料包覆薄壁部位;根据铸件结构、外形选择合理的下水方向或采用专用防变形的夹具;变形量不大的部位;则可在淬火后立即予以矫正..裂纹淬火后的铸件表面用肉眼可以看到的明显的裂纹或通过荧光检查肉眼看不到的微细裂纹..裂纹多曲折不直并呈暗灰色..加热速度太快;淬火时冷却太快淬火温度过高或淬火介质温度过低;或淬火介质速度太快;铸件结构设计不合理两连接壁壁厚差太大;框形件中间的加强筋太薄或太细小;装炉方法不当或下水方向不对;炉温不均匀;使铸件温度不均匀..减慢升温速度或采取等温淬火工艺;提高淬火介质温度或换成冷却速度慢的淬火介质;在壁厚或薄壁部位涂敷涂料或在薄壁部位包复石棉等隔热材料;采用专用防开裂的淬火夹具;并选择正确的下水方向..过烧铸件表面有结瘤;合金的延伸率大大下降..合金中的低熔点杂质元素如Cd、Si、Sb等的含量过高;加热不均匀或加热太快;炉内局部温度超过合金的过烧温度;测量和控制温度的仪表失灵;使炉内实际温度超过仪表指示温度值..严格控制低熔点合金元素的含量不超标;以不超过3℃/min的速度缓慢升温;检查和控制炉内各区温度不超过±5℃;定期检查或校准测控仪表;确保仪表测温、示温、控温准确无误..表面腐蚀铸件的表面出现斑纹或块状等与铝合金铸件表面的不同色泽..硝盐液中氯化物含量超标>0.5%而对铸件表面尤其是疏松、缩孔处造成腐蚀;从硝盐槽中取出后没得到充分的清洗;硝盐粘附在铸件表面尤其是窄缝隙、盲孔、通道中造成腐蚀;硝盐液中混有酸或碱或铸件放在浓酸或浓碱四周受到腐蚀..尽量缩短铸件从炉内移到淬火槽的时间;检查硝盐中氯化物的含量是否超标;如超标;则应降低其含量或浓度;从硝盐槽中加热的铸件应立即用温水或冷水冲洗干净;检查硝盐中酸和碱的含量;如有酸或碱则应中和或停止使用;淬火不均匀铸件的厚大部位的延伸率和硬度低非凡是其内部中心;薄壁部位硬度高非凡是其表层..铸件加热和冷却不均匀;厚大部位冷却慢;热透性差..重新作热处理;降低升温速度;延长保温时间;使厚薄部位温度均衡;在厚壁部位涂敷保温性的涂料或包覆石棉等隔热性材料;尽量使铸件各部位同时冷却;使厚大部位先下水;换成有机淬火剂;降低冷却速度..四、热处理设备、材料1、热处理设备的主要技术要求1由于铝合金淬火和时效温度温差范围不大因其淬火温度接近合金内低熔点共晶成分的熔点;故其炉内的温度差应控制在±5℃;2要求测温、控温仪表灵敏、准确;以确保温度在上述误差范围内;3炉内各区的温度应均匀;差别在1-2℃的范围内;4淬火槽有加热装置和循环装置;保证水的加热和温度均匀;5应定期检查并更换已污染的冷却水..2、淬火介质淬火介质是保证实现各种热处理目的或作用的重要因素..淬火介质的冷却速度越高;铸件冷却的越激烈快;金属组织中α固溶体的过饱和程度越高;铸件的力学性能也就越好;因为大量的金属间化合物等强化相被固溶到Al的α固溶体中去了..淬火介质按其对铸件的冷却速度的快慢依次为:干冰和丙酮的混合物-68℃、冰水、室温的水、80-90℃的水、100℃的水、经雾化过的水、各种油菜籽油等、加热到200-220℃的各种油、空气等..近年国内研制出来的铝合金淬火介质CL-1的冷却速度介于水和油之间;它可以任何比例与水互溶;其混合比例不同;冷却速度各异;故很便于根据淬火对象调整其冷却速度..它淬火之后无须再进行冲洗且表面光洁;对铸件无污染、无毒害;且能防锈..其主要技术指标是;外观:淡黄色到黄色粘稠状均匀液体;密度:1.085-1.1234mg/㎡;粘度Y38:≥154MPa·s;逆熔点:80-87℃;折光n:1.4138-1.4450;临界冷却速度:≥260℃/s450-260℃..CL-1有机淬火剂水溶液之所以具有优良的淬火特性;其机理是此溶液在对工件的淬火过程中;可在温度升到一定值时;从水溶液中析出有机成分并分解;并在工件的表面形成一层均匀的导电性薄膜;淬火气泡对工件是直接作用在此薄膜上;而不是直接作用在工件上;从而降低了形成淬火应力的直接捶击作用;因而减少了工件的变形和裂纹;并且在淬火之后;水溶液冷却到一定温度时;此有机薄膜又溶于水溶液中;恢复成原来的均匀的水溶液状态;不妨碍重复使用效果..3、测温、控温仪表及材料测温、控温仪表的精度不应低于0.5级;热处理加热炉应配有能自动测暖和控温的自动记录、自动报警、自动断电、复电的装置和仪表;以保证炉内温度显示和控制准确及温度均匀..热电偶用镍铬-镍硅、镍铬-镍铝质的直径为2.0-0.5㎜的偶丝..为提高温度仪的灵敏度、缩小温度的波动范围;最好使用Ф0.5-1.0㎜的上述材质的偶丝..并在使用前和使用过程每3个月1次检测、校准1次..。
常用变形铝合金退火热处理工艺规范标准

常用变形铝合金退火热处理工艺规1 主题容与适用围本规规定了公司变形铝合金零件退火热处理的设备、种类、准备工作、工艺控制、技术要求、质量检验、技术安全。
2 引用文件GJB1694变形铝合金热处理规YST 591-2006变形铝及铝合金热处理规《热处理手册》91版3 概念、种类3.1 概念:将变形铝合金材料放在一定的介质加热、保温、冷却,通过改变材料表面或部晶相组织结构,来改变其性能的一种金属热加工工艺。
3.2 种类车间铝合金零件热处理种类:去应力退火、不完全退火、完全退火、时效处理。
4 准备工作4.1 检查设备、仪表是否正常,接地是否良好,并应事先将炉膛清理干净;4.2 抽检零件的加工余量,其数值应大于允许的变形量;4.3工艺文件及工装夹具齐全,选择好合适的工夹具,并考虑好装炉、出炉的方法;4.4 核对材料与图样是否相符,了解零件的技术要求和工艺规定;4.5在零件的尖角、锐边、孔眼等易开裂的部位,应采用防护措施,如包扎铁皮、石棉绳、堵塞螺钉等;5 一般要求5.1 人员:热处理操作工及相关检验人员必须经过专业知识考核和操作培训,成绩合格后持证上岗5.2 设备5.2.1 设备应按标准规要求进行检查和鉴定,并挂有合格标记,各类加热炉的指示记录的仪表刻度应能正确的反映出温度波动围;5.2.2 热电温度测定仪表的读数总偏差不应超过如下指标:当给定温度t≤400℃时,温度总偏差为±5℃;当给定温度t>400℃时,温度总偏差为±(t/10)℃。
5.2.3 加热炉的热电偶和仪表选配、温度测量、检测周期及炉温均匀性均应符合QJ 1428的Ⅲ类及Ⅲ类以上炉的规定。
5.3 装炉5.3.1 装炉量一般以装炉零件体积计算,每炉零件装炉的有效体积不超过炉体积一半为准。
5.3.2 零件装炉时,必须轻拿轻放,防止零件划伤及变形。
5.3.3堆放要求:a.厚板零件允许结合零件结构特点,允许装箱入炉进行热处理,叠放时允许点及较少的线接触,避免面接触,叠放间隙不小于10mm.b.厚度t≤3mm的板料以夹板装夹,叠放厚度≤25mm,零件及夹板面无污垢、凸点,零件间、零件与夹板间应垫一层雪花纸,以防止零件夹伤。
铝的热处理

铝的热处理铝合金铸件的热处理是指按某一热处理规范,控制加热温度、保温时间和冷却速度,改变合金的组织,其主要目的是:提高力学性能,增强耐腐蚀性能,改善加工性能,获得尺寸的稳定性。
铝合金铸件的热处理工艺可以分为如下四类:1。
退火处理将铝合金铸件加热到较高的温度,一般约为300 ℃左右,保温一定的时间后,随炉冷却到室温的工艺称为退火。
在退火过程中固溶体发生分解,第二相质点发生聚集,可以消除铸件的内应力,稳定铸件尺寸,减少变形,增大铸件的塑性。
2。
固溶处理把铸件加热到尽可能高的温度,接近于共晶体的熔点,在该温度下保持足够长的时间,并随后快速冷却,使强化组元最大限度的溶解,这种高温状态被固定保存到室温,该过程称为固溶处理。
固溶处理可以提高铸件的强度和塑性,改善合金的耐腐蚀性能。
固溶处理的效果主要取决于下列三个因素:(1)固溶处理温度。
温度越高,强化元素溶解速度越快,强化效果越好。
一般加热温度的上限低于合金开始过烧温度,而加热温度的下限应使强化组元尽可能多地溶入固溶体中。
为了获得最好的固溶强化效果,而又不便合金过烧,有时采用分级加热的办法,即在低熔点共晶温度下保温,使组元扩散溶解后,低熔点共晶不存在,再升到更高的温度进行保温和淬火。
固溶处理时,还应当注意加热的升温速度不宜过快,以免铸件发生变形和局部聚集的低熔点组织熔化而产生过烧。
固溶热处理的悴火转移时间应尽可能地短,一般应不大于15s,以免合金元素的扩散析出而降低合金的性能。
(2)保温时间。
保温时间是由强化元素的溶解速度来决定的,这取决于合金的种类、成分、组织、铸造方法和铸件的形状及壁厚。
铸造铝合金的保温时间比变形铝合金要长得多,通常由试验确定,一般的砂型铸件比同类型的金属型铸件要延长20%-25% 。
(3)冷却速度。
淬火时给予铸件的冷却速度越大,使固溶体自高温状态保存下来的过饱和度也越高,从而使铸件获得高的力学性能,但同时所形成的内应力也越大,使铸件变形的可能性也越大。
变形铝合金热处理标准
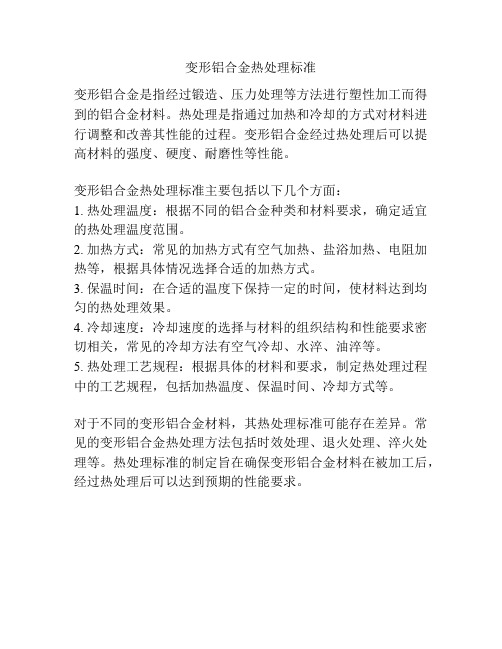
变形铝合金热处理标准
变形铝合金是指经过锻造、压力处理等方法进行塑性加工而得到的铝合金材料。
热处理是指通过加热和冷却的方式对材料进行调整和改善其性能的过程。
变形铝合金经过热处理后可以提高材料的强度、硬度、耐磨性等性能。
变形铝合金热处理标准主要包括以下几个方面:
1. 热处理温度:根据不同的铝合金种类和材料要求,确定适宜的热处理温度范围。
2. 加热方式:常见的加热方式有空气加热、盐浴加热、电阻加热等,根据具体情况选择合适的加热方式。
3. 保温时间:在合适的温度下保持一定的时间,使材料达到均匀的热处理效果。
4. 冷却速度:冷却速度的选择与材料的组织结构和性能要求密切相关,常见的冷却方法有空气冷却、水淬、油淬等。
5. 热处理工艺规程:根据具体的材料和要求,制定热处理过程中的工艺规程,包括加热温度、保温时间、冷却方式等。
对于不同的变形铝合金材料,其热处理标准可能存在差异。
常见的变形铝合金热处理方法包括时效处理、退火处理、淬火处理等。
热处理标准的制定旨在确保变形铝合金材料在被加工后,经过热处理后可以达到预期的性能要求。
铝合金零件热处理变形控制

铝合金零件热处理变形控制摘要:铝合金的最大优点是其密度约为铁的三分之一。
它是一种轻金属材料。
良好的导电性和传热性;在空气中具有良好的耐腐蚀性;具有较强的生产、加工和使用性能。
它具有良好的塑性,可以通过冷热交替变形来生产和加工,并通过热处理来提高其性能。
铝合金固溶处理的目的是获得高浓度的过饱和固溶体,以获得良好的综合物理性能。
因此,铝合金被广泛应用于当代航空航天工业的生产和制造。
同时,铝合金在固溶处理过程中会发生变形。
相对较大的变形也会增加后期尺寸调整的工作量和零件的表面质量。
因此,本文重点研究了在固溶处理过程中减少铝合金变形的方法。
关键词:铝合金;零件;热处理;变形控制1热处理工艺方法热处理是将产品工件放入特定材料中进行加热、隔热和冷却,并根据工件表面的成分或内部结构和微观结构,给出或提高工件的性能指标,使其具有所需的物理、工艺和化学性能。
热处理通常不会改变工件形状的整体成分。
它可能被安排到生产和制造过程的原始工艺流程、中间工艺流程和最终工艺流程。
它受到产品工件的原材料、结构类型、使用模式、使用场景和变形程度等因素的影响,同时受到左右工艺流程的制约。
有时,各种热处理方法植根于一些大型、中型、高精度或特殊要求工件的全过程生产过程。
谈到热处理人们通常会想到四把火:退火、淬火、回火、正火。
对于热处理技术工程师来说,热处理工艺的设计方案、处理方法中的问题以及技术性能的实现都是他的首要任务。
然而,当某一类型的“火”布置在加工工艺的某一阶段时,精通自己专业的加工工艺工人需要掌握产品工件技术标准、原材料、规格、型号和形状规格、热处理特性以及热处理的实际效果。
在此基础上,部署兵力,统筹合理布局,制定有效可行的工艺路线,确保产品加工质量。
此外,工艺路线和热处理方法的开发还需要专业技术人员考虑课程的本质,追根溯源,梳理生产制造中的冲突点和问题原因,探索优质、高效、节能的加工思路,把握关键环节,在制造的重要节点上相对高度地结合热处理,并将生产技术和加工技术紧密结合起来,创造出优质的企业产品,创造出符合市场需求的商品,获得更多的经济效益和社会经济效益,促进社会经济的快速发展。
铝合金热处理方法
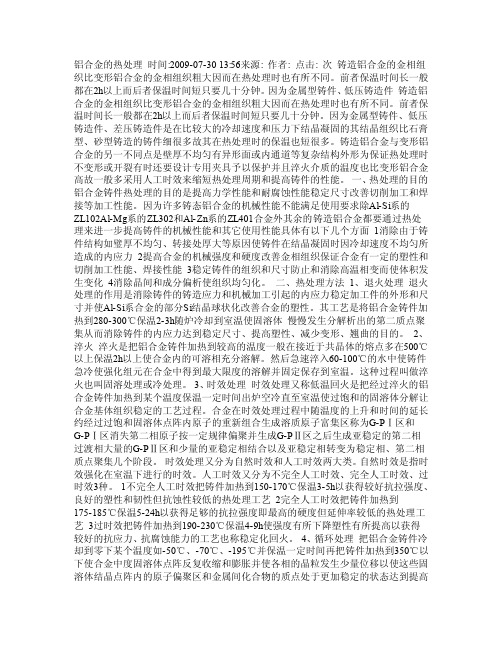
铝合金的热处理时间:2009-07-30 13:56来源: 作者: 点击: 次铸造铝合金的金相组织比变形铝合金的金相组织粗大因而在热处理时也有所不同。
前者保温时间长一般都在2h以上而后者保温时间短只要几十分钟。
因为金属型铸件、低压铸造件铸造铝合金的金相组织比变形铝合金的金相组织粗大因而在热处理时也有所不同。
前者保温时间长一般都在2h以上而后者保温时间短只要几十分钟。
因为金属型铸件、低压铸造件、差压铸造件是在比较大的冷却速度和压力下结晶凝固的其结晶组织比石膏型、砂型铸造的铸件细很多故其在热处理时的保温也短很多。
铸造铝合金与变形铝合金的另一不同点是壁厚不均匀有异形面或内通道等复杂结构外形为保证热处理时不变形或开裂有时还要设计专用夹具予以保护并且淬火介质的温度也比变形铝合金高故一般多采用人工时效来缩短热处理周期和提高铸件的性能。
一、热处理的目的铝合金铸件热处理的目的是提高力学性能和耐腐蚀性能稳定尺寸改善切削加工和焊接等加工性能。
因为许多铸态铝合金的机械性能不能满足使用要求除Al-Si系的ZL102Al-Mg系的ZL302和Al-Zn系的ZL401合金外其余的铸造铝合金都要通过热处理来进一步提高铸件的机械性能和其它使用性能具体有以下几个方面1消除由于铸件结构如璧厚不均匀、转接处厚大等原因使铸件在结晶凝固时因冷却速度不均匀所造成的内应力2提高合金的机械强度和硬度改善金相组织保证合金有一定的塑性和切削加工性能、焊接性能3稳定铸件的组织和尺寸防止和消除高温相变而使体积发生变化4消除晶间和成分偏析使组织均匀化。
二、热处理方法1、退火处理退火处理的作用是消除铸件的铸造应力和机械加工引起的内应力稳定加工件的外形和尺寸并使Al-Si系合金的部分Si结晶球状化改善合金的塑性。
其工艺是将铝合金铸件加热到280-300℃保温2-3h随炉冷却到室温使固溶体慢慢发生分解析出的第二质点聚集从而消除铸件的内应力达到稳定尺寸、提高塑性、减少变形、翘曲的目的。
铝及铝合金的热处理
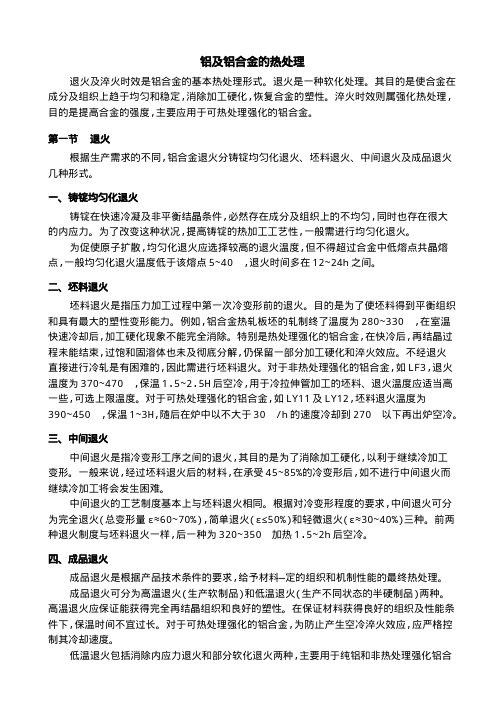
铝及铝合金的热处理退火及淬火时效是铝合金的基本热处理形式。
退火是一种软化处理。
其目的是使合金在成分及组织上趋于均匀和稳定,消除加工硬化,恢复合金的塑性。
淬火时效则属强化热处理,目的是提高合金的强度,主要应用于可热处理强化的铝合金。
第一节 退火根据生产需求的不同,铝合金退火分铸锭均匀化退火、坯料退火、中间退火及成品退火几种形式。
一、铸锭均匀化退火铸锭在快速冷凝及非平衡结晶条件,必然存在成分及组织上的不均匀,同时也存在很大的内应力。
为了改变这种状况,提高铸锭的热加工工艺性,一般需进行均匀化退火。
为促使原子扩散,均匀化退火应选择较高的退火温度,但不得超过合金中低熔点共晶熔点,一般均匀化退火温度低于该熔点5~40℃,退火时间多在12~24h之间。
二、坯料退火坯料退火是指压力加工过程中第一次冷变形前的退火。
目的是为了使坯料得到平衡组织和具有最大的塑性变形能力。
例如,铝合金热轧板坯的轧制终了温度为280~330℃,在室温快速冷却后,加工硬化现象不能完全消除。
特别是热处理强化的铝合金,在快冷后,再结晶过程未能结束,过饱和固溶体也未及彻底分解,仍保留一部分加工硬化和淬火效应。
不经退火直接进行冷轧是有困难的,因此需进行坯料退火。
对于非热处理强化的铝合金,如LF3,退火温度为370~470℃,保温1.5~2.5H后空冷,用于冷拉伸管加工的坯料、退火温度应适当高一些,可选上限温度。
对于可热处理强化的铝合金,如LY11及LY12,坯料退火温度为390~450℃,保温1~3H,随后在炉中以不大于30℃/h的速度冷却到270℃以下再出炉空冷。
三、中间退火中间退火是指冷变形工序之间的退火,其目的是为了消除加工硬化,以利于继续冷加工变形。
一般来说,经过坯料退火后的材料,在承受45~85%的冷变形后,如不进行中间退火而继续冷加工将会发生困难。
中间退火的工艺制度基本上与坯料退火相同。
根据对冷变形程度的要求,中间退火可分为完全退火(总变形量ε≈60~70%),简单退火(ε≤50%)和轻微退火(ε≈30~40%)三种。
铝及铝合金热处理工艺
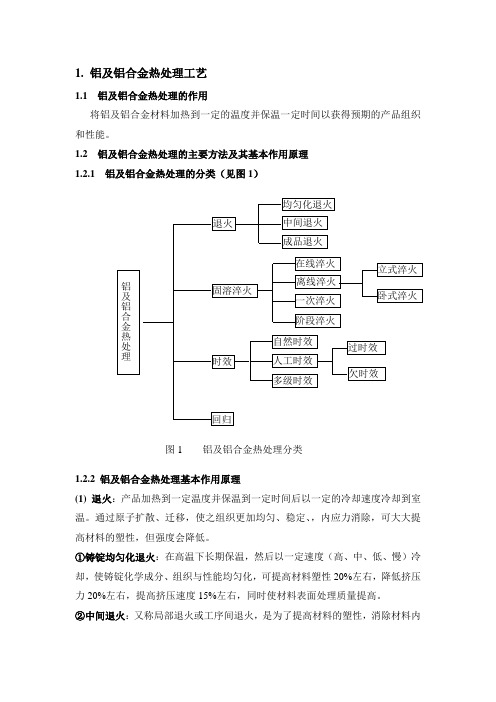
1. 铝及铝合金热处理工艺1.1 铝及铝合金热处理的作用将铝及铝合金材料加热到一定的温度并保温一定时间以获得预期的产品组织和性能。
1.2 铝及铝合金热处理的主要方法及其基本作用原理1.2.1 铝及铝合金热处理的分类(见图1)图1 铝及铝合金热处理分类1.2.2 铝及铝合金热处理基本作用原理(1) 退火:产品加热到一定温度并保温到一定时间后以一定的冷却速度冷却到室温。
通过原子扩散、迁移,使之组织更加均匀、稳定、,内应力消除,可大大提高材料的塑性,但强度会降低。
①铸锭均匀化退火:在高温下长期保温,然后以一定速度(高、中、低、慢)冷却,使铸锭化学成分、组织与性能均匀化,可提高材料塑性20%左右,降低挤压力20%左右,提高挤压速度15%左右,同时使材料表面处理质量提高。
②中间退火:又称局部退火或工序间退火,是为了提高材料的塑性,消除材料内部加工应力,在较低的温度下保温较短的时间,以利于续继加工或获得某种性能的组合。
③完全退火:又称成品退火,是在较高温度下,保温一定时间,以获得完全再结晶状态下的软化组织,具有最好的塑性和较低的强度。
(2)固溶淬火处理:将可热处理强化的铝合金材料加热到较高的温度并保持一定的时间,使材料中的第二相或其它可溶成分充分溶解到铝基体中,形成过饱和固溶体,然后以快冷的方法将这种过饱和固溶体保持到室温,它是一种不稳定的状态,因处于高能位状态,溶质原子随时有析出的可能。
但此时材料塑性较高,可进行冷加工或矫直工序。
①在线淬火:对于一些淬火敏感性不高的合金材料,可利用挤压时高温进行固溶,然后用空冷(T5)或用水雾冷却(T6)进行淬火以获得一定的组织和性能。
②离线淬火:对于一些淬火敏感性高的合金材料必须在专门的热处理炉中重新加热到较高的温度并保温一定时间,然后以不大于15秒的转移时间淬入水中或油中,以获得一定的组织和性能,根据设备不同可分为盐浴淬火、空气淬火、立式淬火、卧式淬火。
(3)时效:经固溶淬火后的材料,在室温或较高温度下保持一段时间,不稳定的过饱和固溶体会进行分解,第二相粒子会从过饱和固溶体中析出(或沉淀),分布在α(AL)铝晶粒周边,从而产生强化作用称之为析出(沉淀)强化。
铝合金时效处理工艺说明

铝合金的热处理铸造铝合金的金相组织比变形铝合金的金相组织粗大,因而在热处理时也有所不同。
前者保温时间长,一般都在2h以上,而后者保温时间短,只要几十分钟。
因为金属型铸件、低压铸造件、差压铸造件是在比较大的冷却速度和压力下结晶凝固的, 其结晶组织比石膏型、砂型铸造的铸件细很多,故其在热处理时的保温也短很多。
铸造铝合金与变形铝合金的另一不同点是壁厚不均匀,有异形面或内通道等复杂结构外形,为保证热处理时不变形或开裂,有时还要设计专用夹具予以保护,并且淬火介质的温度也比变形铝合金高,故一般多采用人工时效来缩短热处理周期和提高铸件的性能。
一、热处理的目的铝合金铸件热处理的目的是提高力学性能和耐腐蚀性能,稳定尺寸,改善切削加工和焊接等加工性能。
因为许多铸态铝合金的机械性能不能满足使用要求,除Al-Si 系的ZL102,Al-Mg系的ZL302和Al-Zn系的ZL401合金外,其余的铸造铝合金都要通过热处理来进一步提高铸件的机械性能和其它使用性能,具体有以下几个方面:1 消除由于铸件结构(如璧厚不均匀、转接处厚大等原因使铸件在结晶凝固时因冷却速度不均匀所造成的内应力;2提高合金的机械强度和硬度,改善金相组织,保证合金有一定的塑性和切削加工性能、焊接性能;3稳定铸件的组织和尺寸,防止和消除高温相变而使体积发生变化;4消除晶间和成分偏析,使组织均匀化。
二、热处理方法1、退火处理退火处理的作用是消除铸件的铸造应力和机械加工引起的内应力,稳定加工件的外形和尺寸,并使Al-Si系合金的部分Si结晶球状化,改善合金的塑性。
其工艺是:将铝合金铸件加热到280-300℃,保温2-3h,随炉冷却到室温,使固溶体慢慢发生分解,析出的第二质点聚集,从而消除铸件的内应力,达到稳定尺寸、提高塑性、减少变形、翘曲的目的。
2、淬火淬火是把铝合金铸件加热到较高的温度(一般在接近于共晶体的熔点,多在500℃以上,保温2h以上,使合金内的可溶相充分溶解。
变形铝及铝合金标准
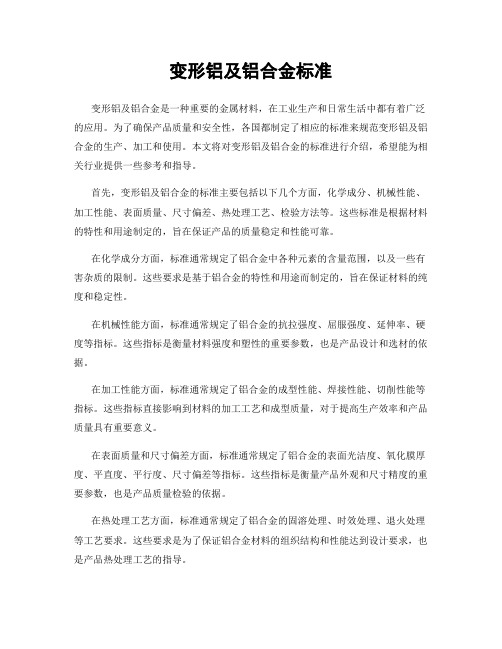
变形铝及铝合金标准变形铝及铝合金是一种重要的金属材料,在工业生产和日常生活中都有着广泛的应用。
为了确保产品质量和安全性,各国都制定了相应的标准来规范变形铝及铝合金的生产、加工和使用。
本文将对变形铝及铝合金的标准进行介绍,希望能为相关行业提供一些参考和指导。
首先,变形铝及铝合金的标准主要包括以下几个方面,化学成分、机械性能、加工性能、表面质量、尺寸偏差、热处理工艺、检验方法等。
这些标准是根据材料的特性和用途制定的,旨在保证产品的质量稳定和性能可靠。
在化学成分方面,标准通常规定了铝合金中各种元素的含量范围,以及一些有害杂质的限制。
这些要求是基于铝合金的特性和用途而制定的,旨在保证材料的纯度和稳定性。
在机械性能方面,标准通常规定了铝合金的抗拉强度、屈服强度、延伸率、硬度等指标。
这些指标是衡量材料强度和塑性的重要参数,也是产品设计和选材的依据。
在加工性能方面,标准通常规定了铝合金的成型性能、焊接性能、切削性能等指标。
这些指标直接影响到材料的加工工艺和成型质量,对于提高生产效率和产品质量具有重要意义。
在表面质量和尺寸偏差方面,标准通常规定了铝合金的表面光洁度、氧化膜厚度、平直度、平行度、尺寸偏差等指标。
这些指标是衡量产品外观和尺寸精度的重要参数,也是产品质量检验的依据。
在热处理工艺方面,标准通常规定了铝合金的固溶处理、时效处理、退火处理等工艺要求。
这些要求是为了保证铝合金材料的组织结构和性能达到设计要求,也是产品热处理工艺的指导。
在检验方法方面,标准通常规定了铝合金材料的化学成分分析、机械性能测试、加工性能测试、表面质量检验、尺寸检测、热处理工艺验证等方法和要求。
这些方法是为了保证产品质量的可控性和可靠性,也是产品质量检验的技术支撑。
综上所述,变形铝及铝合金的标准是保证产品质量和安全性的重要依据,对于生产企业和产品设计者来说,必须严格遵守相关标准要求,才能生产出合格的产品,满足市场和用户的需求。
同时,相关部门和行业组织也应加强标准的宣传和培训,提高企业和从业人员的标准意识和执行力,共同推动行业的健康发展和持续进步。
铝合金的热处理工艺

铝合金的热处理铸造铝合金的金相组织比变形铝合金的金相组织粗大,因而在热处理时也有所不同。
前者保温时间长,一般都在2h以上,而后者保温时间短,只要几十分钟。
因为金属型铸件、低压铸造件铸造铝合金的金相组织比变形铝合金的金相组织粗大,因而在热处理时也有所不同。
前者保温时间长,一般都在2h以上,而后者保温时间短,只要几十分钟。
因为金属型铸件、低压铸造件、差压铸造件是在比较大的冷却速度和压力下结晶凝固的,其结晶组织比石膏型、砂型铸造的铸件细很多,故其在热处理时的保温也短很多。
铸造铝合金与变形铝合金的另一不同点是壁厚不均匀,有异形面或内通道等复杂结构外形,为保证热处理时不变形或开裂,有时还要设计专用夹具予以保护,并且淬火介质的温度也比变形铝合金高,故一般多采用人工时效来缩短热处理周期和提高铸件的性能。
一、热处理的目的铝合金铸件热处理的目的是提高力学性能和耐腐蚀性能,稳定尺寸,改善切削加工和焊接等加工性能。
因为许多铸态铝合金的机械性能不能满足使用要求,除Al-Si系的ZL102,Al-Mg系的ZL302和Al-Zn系的ZL401合金外,其余的铸造铝合金都要通过热处理来进一步提高铸件的机械性能和其它使用性能,具体有以下几个方面: 1〕消除由于铸件结构〔如璧厚不均匀、转接处厚大〕等原因使铸件在结晶凝固时因冷却速度不均匀所造成的内应力; 2〕提高合金的机械强度和硬度,改善金相组织,保证合金有一定的塑性和切削加工性能、焊接性能; 3〕稳定铸件的组织和尺寸,防止和消除高温相变而使体积发生变化; 4〕消除晶间和成分偏析,使组织均匀化。
二、热处理方法1、退火处理退火处理的作用是消除铸件的铸造应力和机械加工引起的内应力,稳定加工件的外形和尺寸,并使Al-Si系合金的部分Si结晶球状化,改善合金的塑性。
其工艺是:将铝合金铸件加热到280-300℃,保温2-3h,随炉冷却到室温,使固溶体慢慢发生分解,析出的第二质点聚集,从而消除铸件的内应力,到达稳定尺寸、提高塑性、减少变形、翘曲的目的。
铝及铝合金热处理工艺讲解学习
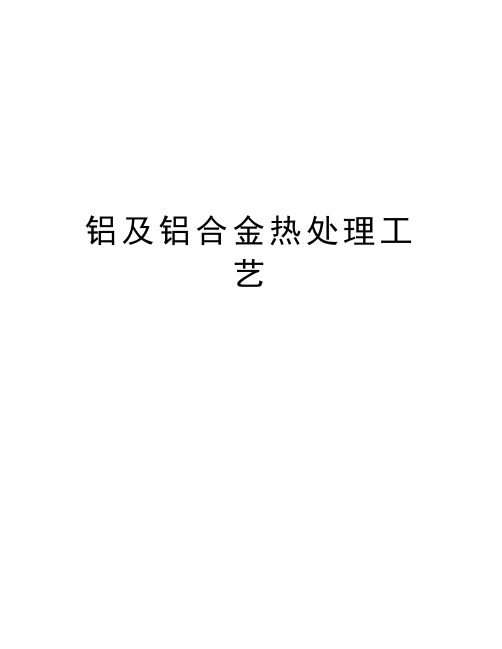
铝及铝合金热处理工艺1. 铝及铝合金热处理工艺1.1 铝及铝合金热处理的作用将铝及铝合金材料加热到一定的温度并保温一定时间以获得预期的产品组织和性能。
1.2 铝及铝合金热处理的主要方法及其基本作用原理 1.2.1 铝及铝合金热处理的分类(见图1)图1 铝及铝合金热处理分类1.2.2 铝及铝合金热处理基本作用原理(1) 退火:产品加热到一定温度并保温到一定时间后以一定的冷却速度冷却到室温。
通过原子扩散、迁移,使之组织更加均匀、稳定、,内应力消除,可大大提高材料的塑性,但强度会降低。
①铸锭均匀化退火:在高温下长期保温,然后以一定速度(高、中、低、慢)冷却,使铸锭化学成分、组织与性能均匀化,可提高材料塑性20%左右,降低挤压力20%左右,提高挤压速度15%左右,同时使材料表面处理质量提高。
②中间退火:又称局部退火或工序间退火,是为了提高材料的塑性,消除材料内部加工应力,在较低的温度下保温较短的时间,以利于续继加工或获得某种性能的组合。
③完全退火:又称成品退火,是在较高温度下,保温一定时间,以获得完全再结晶状态下的软化组织,具有最好的塑性和较低的强度。
(2)固溶淬火处理:将可热处理强化的铝合金材料加热到较高的温度并保持一定的时间,使材料中的第二相或其它可溶成分充分溶解到铝基体中,形成过饱和固溶体,然后以快冷的方法将这种过饱和固溶体保持到室温,它是一种不稳定的状态,因处于高能位状态,溶质原子随时有析出的可能。
但此时材料塑性较高,可进行冷加工或矫直工序。
①在线淬火:对于一些淬火敏感性不高的合金材料,可利用挤压时高温进行固溶,然后用空冷(T5)或用水雾冷却(T6)进行淬火以获得一定的组织和性能。
②离线淬火:对于一些淬火敏感性高的合金材料必须在专门的热处理炉中重新加热到较高的温度并保温一定时间,然后以不大于15秒的转移时间淬入水中或油中,以获得一定的组织和性能,根据设备不同可分为盐浴淬火、空气淬火、立式淬火、卧式淬火。
变形铝合金时效热处理相关知识汇总

变形铝合金时效热处理相关知识汇总(1)时效 aging经固溶处理或冷变形后的合金,在室温或高于室温下,组织和性能随时间延续而变化,硬度、强度增高,塑性、韧性降低的现象。
在室温下发生时效称自然时效。
高于室温发生时效称人工时效。
时效现象除铝铜合金外,在钢、铜合金,铁基、镍基、钴基高温合金中普遍存在,是提高合金强度的重要方法。
低碳钢冷变形后在常温长时放置即出现屈服强度提高。
硬铝合金经高温(520℃)淬火后在100~200℃时效,可获得最佳的强化效果。
马氏体时效钢,沉淀硬化不锈钢,铁基、镍基、钴基高温合金均可在固溶处理后选择不同温度时效处理,可以从中获得最佳的组织和性能。
(2)时效处理 aging treatment过饱和固溶体合金在室温或加热至一定温度保温,使溶质组元富集或析出第二相的热处理工艺。
常温下时效称自然时效。
高于室温加热时效称人工时效。
时效析出第二相获得强化的现象称时效强化。
低于或高于强化峰值温度的时效分别称为亚时效与过时效处理。
形变后时效称形变时效或直接时效。
在应力下时效称应力时效。
强化效果取决于析出第二相的类型、数量、尺寸、形态、稳定性等因素。
广泛用于铝合金、钛合金、高温合金、沉淀硬化钢、马氏体时效钢等。
铝合金时效硬化峰值出现在溶质组元的富集G-P区(Ⅱ)末期。
时效处理是强化合金的有效方法,可显著提高合金的强度和硬度,调整时效温度、时间可使合金的组织、性能满足使用要求,获得高的屈服强度、蠕变强度、疲劳性能等。
含铜4%的铝合金经自然时效后强度为400MPa,比退火状态强度大一倍。
时效硬化合金使用时,使用温度不应超过其时效温度。
(3)时效硬化 age hardening经固溶处理的过饱和固溶体在室温或室温以上时效处理,硬度或强度显著增加的现象。
原因是过饱和固溶体在时效过程中发生沉淀、偏聚、有序化等反应的产物,增加了位错运动的阻力形成的。
位错与析出产物交互作用下硬化机制有位错剪切析出相粒子,基体与粒子间相界面积增加,使外力转变为界面能; 析出相与基体的层错能差异; 基体与析出粒子的切变模量不同。
铝合金的热处理工艺
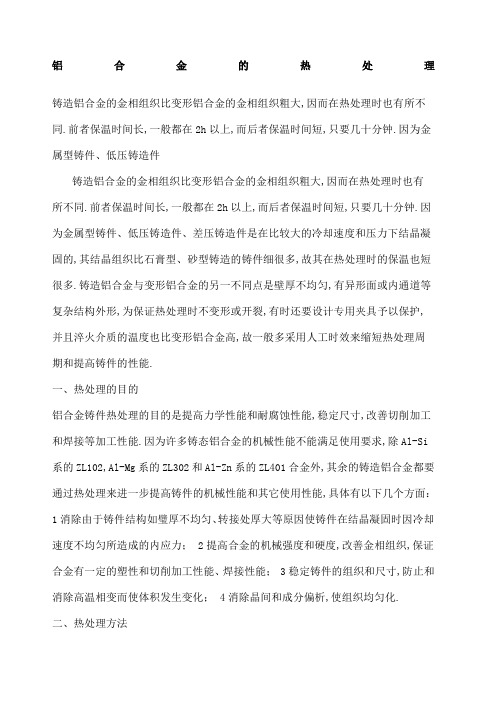
铝合金的热处理铸造铝合金的金相组织比变形铝合金的金相组织粗大,因而在热处理时也有所不同.前者保温时间长,一般都在2h以上,而后者保温时间短,只要几十分钟.因为金属型铸件、低压铸造件铸造铝合金的金相组织比变形铝合金的金相组织粗大,因而在热处理时也有所不同.前者保温时间长,一般都在2h以上,而后者保温时间短,只要几十分钟.因为金属型铸件、低压铸造件、差压铸造件是在比较大的冷却速度和压力下结晶凝固的,其结晶组织比石膏型、砂型铸造的铸件细很多,故其在热处理时的保温也短很多.铸造铝合金与变形铝合金的另一不同点是壁厚不均匀,有异形面或内通道等复杂结构外形,为保证热处理时不变形或开裂,有时还要设计专用夹具予以保护,并且淬火介质的温度也比变形铝合金高,故一般多采用人工时效来缩短热处理周期和提高铸件的性能.一、热处理的目的铝合金铸件热处理的目的是提高力学性能和耐腐蚀性能,稳定尺寸,改善切削加工和焊接等加工性能.因为许多铸态铝合金的机械性能不能满足使用要求,除Al-Si 系的ZL102,Al-Mg系的ZL302和Al-Zn系的ZL401合金外,其余的铸造铝合金都要通过热处理来进一步提高铸件的机械性能和其它使用性能,具体有以下几个方面:1消除由于铸件结构如璧厚不均匀、转接处厚大等原因使铸件在结晶凝固时因冷却速度不均匀所造成的内应力; 2提高合金的机械强度和硬度,改善金相组织,保证合金有一定的塑性和切削加工性能、焊接性能; 3稳定铸件的组织和尺寸,防止和消除高温相变而使体积发生变化; 4消除晶间和成分偏析,使组织均匀化.二、热处理方法1、退火处理退火处理的作用是消除铸件的铸造应力和机械加工引起的内应力,稳定加工件的外形和尺寸,并使Al-Si系合金的部分Si结晶球状化,改善合金的塑性.其工艺是:将铝合金铸件加热到280-300℃,保温2-3h,随炉冷却到室温,使固溶体慢慢发生分解,析出的第二质点聚集,从而消除铸件的内应力,达到稳定尺寸、提高塑性、减少变形、翘曲的目的.2、淬火淬火是把铝合金铸件加热到较高的温度一般在接近于共晶体的熔点,多在500℃以上,保温2h以上,使合金内的可溶相充分溶解.然后,急速淬入60-100℃的水中,使铸件急冷,使强化组元在合金中得到最大限度的溶解并固定保存到室温.这种过程叫做淬火,也叫固溶处理或冷处理.3、时效处理时效处理,又称低温回火,是把经过淬火的铝合金铸件加热到某个温度,保温一定时间出炉空冷直至室温,使过饱和的固溶体分解,让合金基体组织稳定的工艺过程.合金在时效处理过程中,随温度的上升和时间的延长,约经过过饱和固溶体点阵内原子的重新组合,生成溶质原子富集区称为G-PⅠ区和G-PⅠ区消失,第二相原子按一定规律偏聚并生成G-PⅡ区,之后生成亚稳定的第二相过渡相,大量的G-PⅡ区和少量的亚稳定相结合以及亚稳定相转变为稳定相、第二相质点聚集几个阶段.时效处理又分为自然时效和人工时效两大类.自然时效是指时效强化在室温下进行的时效.人工时效又分为不完全人工时效、完全人工时效、过时效3种.1不完全人工时效:把铸件加热到150-170℃,保温3-5h,以获得较好抗拉强度、良好的塑性和韧性,但抗蚀性较低的热处理工艺; 2完全人工时效:把铸件加热到175-185℃,保温5-24h,以获得足够的抗拉强度即最高的硬度但延伸率较低的热处理工艺; 3过时效:把铸件加热到190-230℃,保温4-9h,使强度有所下降,塑性有所提高,以获得较好的抗应力、抗腐蚀能力的工艺,也称稳定化回火.4、循环处理把铝合金铸件冷却到零下某个温度如-50℃、-70℃、-195℃并保温一定时间,再把铸件加热到350℃以下,使合金中度固溶体点阵反复收缩和膨胀,并使各相的晶粒发生少量位移,以使这些固溶体结晶点阵内的原子偏聚区和金属间化合物的质点处于更加稳定的状态,达到提高产品零件尺寸、体积更稳定的目的.这种反复加热冷却的热处理工艺叫循环处理.这种处理适合使用中要求很精密、尺寸很稳定的零件如检测仪器上的一些零件.一般铸件均不作这种处理.5、铸造铝合金热处理状态代号及含义代号合金状态热处理的作用或目的说明T1 人工时效在金属型或湿砂型铸造的合金,因冷却速度较快,已得到一定程度的过饱和固溶体,即有部分淬火效果.再作人工时效,脱溶强化,则可提高硬度和机械强度,改善切削加工性. 对提高Zl104、ZL105等合金的强度有效.T2 退火主要作用在于消除铸件的内应力铸造应力和机加工引起的应力,稳定铸件尺寸,并使Al-Si系合金的Si晶体球状化,提高其塑性. 对Al-Si系合金效果比较明显,退火温度280-300℃,保温时间为2-4h.T4 固溶处理淬火加自然时效通过加热保温,使可溶相溶解,然后急冷,使大量强化相固溶在α固溶体内,获得过饱和固溶体,以提高合金的硬度、强度及抗蚀性. 对Al-Mg系合金为最终热处理,对需人工时效的其它合金则是预备热处理.T5 固溶处理淬火加不完全人工时效用来得到较高的强度和塑性,但抗蚀性会有所下降,非凡是晶间腐蚀会有所增加. 时效温度低,保温时间短,时效温度约150-170℃,保温时间为3-5h.T6 固溶处理淬火加完全人工时效用来获得最高的强度,但塑性和抗蚀性有所降低. 在较高温度和较长时间内进行.适用于要求高负荷的零件,时效温度约175-185℃,保温时间5h以上.T7 固溶处理淬火加稳定化回火用来稳定铸件尺寸和组织,提高抗腐蚀非凡是抗应力腐蚀能力,并保持较高的力学性能. 多在接近零件的工作温度下进行.适合300℃以下高温工作的零件,回火温度为190-230℃,保温时间4-9h.T8 固溶处理淬火加软化回火使固溶体充分分解,析出的强化相聚集并球状化,以稳定铸件尺寸,提高合金的塑性,但抗拉强度下降. 适合要求高塑性的铸件,回火温度约230-330℃,保温时间3-6h.T9 循环处理用来进一步稳定铸件的尺寸外形.其反复加热和冷却的温度及循环次数要根据零件的工作条件和合金的性质来决定. 适合要求尺寸、外形很精密稳定的零件.三、热处理工艺1、铸造铝合金热处理工艺参数合金牌号合金代号热处理固溶处理时效处理保温后空冷加热温度℃ 保温时间h 淬火温度℃ 加热温度℃ 保温时间hZAlSi7Mg ZL101 T2 - - - 300±10 2-4T4 535±5 2-6 20-100 - -T5 535±5 2-6 20-100 150±5 2-4T6 535±5 2-6 20-100 200±5 2-5T7 535±5 2-6 80-100 225±5 3-5T5 二阶段535±5 2-6 20-100 190±10150±5 2ZAlSi7MgA ZL101A T1 - - - 190±5 3-4T2 - - - 300±10 2-4T4 535±5 10-16 20-100 - -T5 535±5 10-16 20-100 175±5 6ZAlSi12 ZL102 T2 - - - 300±10 2-4ZAlSi9Mg ZL104 T1 - - - 175±5 5-17T6 535±5 2-6 20-100 175±5 10-15ZAlSi5Cu1Mg ZL105 T1 - - - 180±5 5-10T5 525±5 3-5 20-100 175±5 5-10T6 525±5 3-5 20-100 200±5 3-5T7 525±5 3-5 20-100 230±10 3-5ZAlSi5Cu1MgA ZL105A T1 - - - 180±5 5-10 T5 525±5 3-5 20-100 175±5 5-10T6 525±5 3-5 20-100 200±5 3-5T7 525±5 3-5 20-100 230±10 3-5T8 525±5 3-5 20-100 250±10 3-5ZAlSi8Cu1Mg ZL106 T1 - - - 200±10 5-8T2 - - - 280±10 5-8T5 515±5 4-8 20-100 170±5 8-16T7 515±5 4-8 20-100 230±5 3-5ZAlSi7Cu4 ZL107 T6 515±5 5-7 20-100 170±10 5-7ZAlSi12Cu2Mg1 ZL108 T1 - - - 190±5 8-12T6 515±5 6-8 20-70 175±5 14-18T7 515±5 3-8 20-70 240±10 6-10ZAlSi12Cu1Mg1Ni1 ZL109 T1 - - - 205±5 8-12T6 515±5 6-8 20-70 180±5 14-18ZA lSi9Cu2Mg ZL111 T6 520±5 4-6 20-70 180±5 6-8ZAlSi7Mg1A ZL114A T5 535±5 2-7 20-100 150±5 1-3T6 540±5 8-12 65-100 160±5 3-5ZALSi5Zn1Mg ZL115 T4 550±5 16 65-100 - -T5 550±5 16 65-100 160±5 4ZAlSi8MgBe ZL116 T1 - - - 190±5 3-4T2 - - - 300±10 2-4T4 535±5 10-16 20-100 - -T5 535±5 10-16 20-100 175±5 6T6 535±5 10-16 20-100 160±5 3-8ZAlCu5Mn ZAlCu5MnA ZL201 ZL201A T4 545±5 10-12 20-100 - - T5 545±5 5-9 20-100 175±5 3-6T7 545±5 5-9 20-100 250±10 3-10ZAlCu10 ZL202 T2 - - - 290±5 3ZAlCu4 ZL203 T4 515±5 10-15 20-100 - -T5 515±5 10-15 20-100 150±5 2-4ZAlCu5MnCdA ZL204A T6 535±5 7-9 40-100 175±5 3-5T7 535±5 7-9 40-100 190±5 3-5ZAlCu5MnCdVA ZL205A T5 535±5 10-15 20-60 155±5 8-10T6 535±5 10-15 20-60 175±5 3-5T7 535±5 10-15 20-60 195±5 3-5ZAlRE5Cu3Si2 ZL207 T1 - - - 200±5 5-10ZAlMg10 ZL301 T4 430±10 20 100或油 - -ZAlMg8Zn1 ZL305 T4 455±5 6-8 80-100 - -ZAlZn11Si7 Zl401 T1 - - - 200±10 5-10T2 - - - 300±10 2-4ZAlZn6Mg ZL402 T1 - - - 175±5 6-8T5 - - - 室温 20天T5 - - - 175±5 6-82、热处理操作技术要点1热处理前应检查热处理设备、辅助设备、仪表等是否合格和正常,炉膛各处的温度差是否在规定的范围之内±5℃;2装炉前应吹砂或冲洗,应无油污、脏物、泥土,合金牌号不应相混;3形性状易产生翘曲的铸件应放在专用的底盘或支架上,不答应有悬空的悬臂部分;4检查铸件性能的单铸或附铸试棒应随零件一起同炉处理,以真实反映铸件的性能;5在保温期间应随时检查、校正炉膛各处温度,防止局部高温或烧化;6在断电后短时间不能恢复时,应将在保温中的铸件迅速出炉淬火,等恢复正常后,再装炉、保暖和进行热处理;7在硝盐槽中淬过火的铸件,应在淬火后立即用热水冲洗,消除残盐,防止腐蚀;8发现淬火后铸件变形,应立即予以校正;9要时效处理的零件,应在淬火后内进行时效处理;10如在热处理后发现性能不合格,可重复进行热处理,但次数不得超过2次;11应根据铸件结构外形、尺寸、合金特性等制定的热处理工艺进行热处理.3、热处理缺陷的产生原因和消除与预防办法缺陷名称缺陷表现产生原因消除与预防办法力学性能不合格退火状态δ5偏低,淬火或时效处理后强度和延伸率不合格. 退火温度偏低或保温时间不足,或冷却太快;淬火温度偏低或保温时间不够,或冷却速度太慢淬火介质温度过高;不完全人工时效和完全人工时效温度偏高,或保温时间偏长,合金的化学成分出现偏差. 再次退火,提高温度或延长保温时间;提高淬火温度或延长保温时间,降低淬火介质温度;如再次淬火,则要调整其后的时效温度和时间;如成分出现偏差,则要根据具体的偏差元素、偏差量、改变或调整重复热处理参数.变形、翘曲热处理后,或之后的机械加工中反映出来的铸件的尺寸、外形变化. 加热速度或淬火冷却速度太快太激烈;淬火温度太高;铸件的设计结构不合理如两连接壁的壁厚相差太大,框形结构中加强筋太薄或太细小;淬火时工件下水方向不当及装料方法不当. 降低升温速度,提高淬火介质温度,或换成冷却速度稍慢的淬火介质以防止合金内产生残余应力;在厚壁或薄壁部位涂敷涂料或用石棉纤维等隔热材料包覆薄壁部位;根据铸件结构、外形选择合理的下水方向或采用专用防变形的夹具;变形量不大的部位,则可在淬火后立即予以矫正.裂纹淬火后的铸件表面用肉眼可以看到的明显的裂纹或通过荧光检查肉眼看不到的微细裂纹.裂纹多曲折不直并呈暗灰色. 加热速度太快,淬火时冷却太快淬火温度过高或淬火介质温度过低,或淬火介质速度太快;铸件结构设计不合理两连接壁壁厚差太大,框形件中间的加强筋太薄或太细小;装炉方法不当或下水方向不对;炉温不均匀,使铸件温度不均匀. 减慢升温速度或采取等温淬火工艺;提高淬火介质温度或换成冷却速度慢的淬火介质;在壁厚或薄壁部位涂敷涂料或在薄壁部位包复石棉等隔热材料;采用专用防开裂的淬火夹具,并选择正确的下水方向.过烧铸件表面有结瘤,合金的延伸率大大下降. 合金中的低熔点杂质元素如Cd、Si、Sb等的含量过高;加热不均匀或加热太快;炉内局部温度超过合金的过烧温度;测量和控制温度的仪表失灵,使炉内实际温度超过仪表指示温度值. 严格控制低熔点合金元素的含量不超标;以不超过3℃/min的速度缓慢升温;检查和控制炉内各区温度不超过±5℃;定期检查或校准测控仪表,确保仪表测温、示温、控温准确无误.表面腐蚀铸件的表面出现斑纹或块状等与铝合金铸件表面的不同色泽. 硝盐液中氯化物含量超标>%而对铸件表面尤其是疏松、缩孔处造成腐蚀;从硝盐槽中取出后没得到充分的清洗,硝盐粘附在铸件表面尤其是窄缝隙、盲孔、通道中造成腐蚀;硝盐液中混有酸或碱或铸件放在浓酸或浓碱四周受到腐蚀. 尽量缩短铸件从炉内移到淬火槽的时间;检查硝盐中氯化物的含量是否超标,如超标,则应降低其含量或浓度,从硝盐槽中加热的铸件应立即用温水或冷水冲洗干净;检查硝盐中酸和碱的含量,如有酸或碱则应中和或停止使用;不把铝合金铸件放在有浓酸或浓碱的四周.淬火不均匀铸件的厚大部位的延伸率和硬度低非凡是其内部中心,薄壁部位硬度高非凡是其表层. 铸件加热和冷却不均匀,厚大部位冷却慢,热透性差. 重新作热处理,降低升温速度,延长保温时间,使厚薄部位温度均衡;在厚壁部位涂敷保温性的涂料或包覆石棉等隔热性材料,尽量使铸件各部位同时冷却;使厚大部位先下水;换成有机淬火剂,降低冷却速度.四、热处理设备、材料1、热处理设备的主要技术要求1由于铝合金淬火和时效温度温差范围不大因其淬火温度接近合金内低熔点共晶成分的熔点,故其炉内的温度差应控制在±5℃;2要求测温、控温仪表灵敏、准确,以确保温度在上述误差范围内;3炉内各区的温度应均匀,差别在1-2℃的范围内;4淬火槽有加热装置和循环装置,保证水的加热和温度均匀;5应定期检查并更换已污染的冷却水.2、淬火介质淬火介质是保证实现各种热处理目的或作用的重要因素.淬火介质的冷却速度越高,铸件冷却的越激烈快,金属组织中α固溶体的过饱和程度越高,铸件的力学性能也就越好,因为大量的金属间化合物等强化相被固溶到Al的α固溶体中去了.淬火介质按其对铸件的冷却速度的快慢依次为:干冰和丙酮的混合物-68℃、冰水、室温的水、80-90℃的水、100℃的水、经雾化过的水、各种油菜籽油等、加热到200-220℃的各种油、空气等.近年国内研制出来的铝合金淬火介质CL-1的冷却速度介于水和油之间,它可以任何比例与水互溶,其混合比例不同,冷却速度各异,故很便于根据淬火对象调整其冷却速度.它淬火之后无须再进行冲洗且表面光洁,对铸件无污染、无毒害,且能防锈.其主要技术指标是,外观:淡黄色到黄色粘稠状均匀液体,密度:,粘度Y38:≥154MPa·s,逆熔点:80-87℃,折光n:,临界冷却速度:≥260℃/s450-260℃.CL-1有机淬火剂水溶液之所以具有优良的淬火特性,其机理是此溶液在对工件的淬火过程中,可在温度升到一定值时,从水溶液中析出有机成分并分解,并在工件的表面形成一层均匀的导电性薄膜,淬火气泡对工件是直接作用在此薄膜上,而不是直接作用在工件上,从而降低了形成淬火应力的直接捶击作用,因而减少了工件的变形和裂纹,并且在淬火之后,水溶液冷却到一定温度时,此有机薄膜又溶于水溶液中,恢复成原来的均匀的水溶液状态,不妨碍重复使用效果.3、测温、控温仪表及材料测温、控温仪表的精度不应低于级,热处理加热炉应配有能自动测暖和控温的自动记录、自动报警、自动断电、复电的装置和仪表,以保证炉内温度显示和控制准确及温度均匀.热电偶用镍铬-镍硅、镍铬-镍铝质的直径为的偶丝.为提高温度仪的灵敏度、缩小温度的波动范围,最好使用Ф的上述材质的偶丝.并在使用前和使用过程每3个月1次检测、校准1次.。
- 1、下载文档前请自行甄别文档内容的完整性,平台不提供额外的编辑、内容补充、找答案等附加服务。
- 2、"仅部分预览"的文档,不可在线预览部分如存在完整性等问题,可反馈申请退款(可完整预览的文档不适用该条件!)。
- 3、如文档侵犯您的权益,请联系客服反馈,我们会尽快为您处理(人工客服工作时间:9:00-18:30)。
T4、T41
T452
轧制环
516~552
W
T4、T41
T452
6063
挤压件
515~530
W
T4、T42
T4510、T4511
拉伸管
515~527
W
T4、T42
N/A
6262
线材、棒材
515~566
W
T4
T450
挤压件
515~566
W
T4
T4510、T4511
拉伸管
515~566
W
T4
—
表2 固溶热处理温度(续)
淬火槽应具备足够的加热和冷却能力,以保证淬火介质的温度达到4.7规定的范围。同时,应配备必要的仪表以确保对温度进行控制。该仪表读数与实际温度的偏差应在±3℃范围内。
4.4.3.2.4 浸没速度
淬火系统应有控制固溶处理部件进入淬火介质速度的方法,如果该控制方法作为所要求的热处理工艺规程的一部分,不应超过所允许的最大淬火转移时间(见4.7.3)。
W
T4
—
2117
其他线材、棒材
496~510
W
T4
—
铆钉线
477~510
W
T4
—
2A17
520~530
W
2018
模锻件
504~521
W
T4、T41
—
2218
模锻件
504~516
W
T4、T41
—
2618
模锻及自由锻件
524~535
W
T4、T41
—
2219
薄板
549~541
W
T316、T376、T42
—
5.2
定期产品监测
4.3
5.4
4.1.2工艺操作规程重新审定的条件
下列情形多次出现,则有必要重新审定工艺操作规程。
a. 原已验收的热处理设备,更换部件、彻底磨损、毁坏或改型需要磨合(见4.5.1~4.5.3);
b. 现有热处理设备或其工艺操作规程不能满足本标准规定的质量要求(见5.6.4);
c. 在定期工艺制度检查(见4.2)或定期产品监测过程中(见4.3)测出任何不合格(见5.1.3和5.6.4)。
GB/T 16865 变形铝、镁及其合金加工制品拉伸试验用试样
13
下列术语、定义适用于本标准。
13.1
热处理
本标准中所使用的“热处理”一词是本标准所包含的所有热处理的总称,例如:时效、稳定化处理和退火。
13.2
热处理批次
一个热处理批次是指:由同一合金、同一产品形式、状态以及经历同一工艺过程的一定数量的一批金属。
4.4.2温度控制设备
4.4.2.1基本原则
所有热处理设备都应装有符合工艺控制要求的温度控制设备和记录设备,以确保所有加热区和保温区的温度控制均达到本标准的要求。
4.4.2.2温度控制和记录
传感器的位置应由热处理炉的特性决定,并且传感器应置于能够准确测量工件和加热介质温度的位置。记录应能正确反应温度控制情况,并可存贮记录以备查阅。
4.4.1.3盐浴槽
盐浴槽液不应与待处理的合金起反应。
4.4.1.4时效热处理设备
进行时效热处理的设备应能满足本标准规定的所有要求,同时生产出的产品能满足相应标准要求。
4.4.1.5炉温均匀性检验
炉温均匀性应符合有关工艺要求的规定。
4.4.1.6温度均匀性
4.4.1.6.1周期性加热炉和盐浴槽
周期性加热炉和盐浴槽的设计与建造应满足以下要求。在保温期间,保温区内任何一点的加热介质的温度都应受到控制,确保金属温度不会超过4.6.1规定的保温温度范围最大值、固溶热处理温度范围、时效温度范围(见4.9)。
厚板
549~541
W
T316、T376、T42
T351
铆钉线
549~541
W
T4
—
其他线材、棒材
549~541
W
T316、T42
T351
挤压件
549~541
W
T316、T42
T3510、T3511
模锻及自由锻件
530~540
W
T4
T352
表2 固溶热处理温度(续)
合 金
产品类型1
(不包括锻件)
固溶热处理(金属)温度/℃5
——定期工艺制度检查;
——定期产品监测;
——零部件的热处理
——热处理设备;
——固溶热处理参数及工艺规程;
——淬火参数及工艺规程;
——装架和间距;
——建议时效热处理;
——质量保证措施。
本标准的附录A为资料性附录。
本标准由全国有色金属标准化技术委员会提出。
本标准由全国有色金属标准化技术委员会归口并负责解释。
4.4.1.6.2连续式加热炉
对连续式加热炉,保温区紧连加热区。在保温区内,金属温度应在4.6.1规定的热处理温度范围内,或在所适用的时效温度范围内(见4.9)。当保温区内的所有炉料都达到所规定的温度范围的最低值后,该保温区的加热介质和炉料的温度波动最大值应为10℃(或按表2、表6要求)。但6061合金,温度波动允许达到15℃(见表2附注5和表6附注4)。
13.3
工作区
工作区是指在一个热处理工艺的保温过程中,热处理设备被部件或原材料所占据的部分封闭空间。该区通常(但不总是)占据整个封闭空间的大部分。
13.4
固溶热处理造成的砂眼和气孔
这种情况在过去被称为高温氧化。现已公认,在固溶热处理过程中,进入到铝合金中的氢是造成表面砂眼和表层下面气孔出现的原因。
14
W
T4 、T361、T42
T3510、T3511
拉伸管
487~499
W
T36、T42
—
模锻及自由锻件
488~499
W
T4
T352
2124
厚板
487~499
W
T42、T42
T351
2025
模锻件
510~521
W
T4
—
2048
板材
487~499
W
T3 、T42
T351
2A50
510~520
2B50
510~520
W
2A04
502~508
W
2A06
495~505
W
2A10
510~520
W
2A11
495~505
W
2B11
495~505
W
2A12
490~500
W
2B12
490~500
W
2014
板材
496~507
W
T36、T42
—
卷材
496~507
W
T4 、T42
—
厚板
496~507
W
T4 、T42
T451
线材、棒材
4.4.3.4 淬火设备的位置
淬火设备和装卸装备的安装位置应保证淬火转移时间不得超过表5规定的最大淬火转移时间。
4.4.4 冲洗设备
根据需要应使用冲洗槽、喷嘴或其它适合的设备,以确保干燥后在金属表面没有盐液残留物或膜层存在。
4.4.5 支撑架、固定装置及其它工件架持装置的结构
铺设支承架时应当最低限地减少金属在固溶热处理时的振动或滑动。支架、固定装置、底座、吊篮的安装应保证在热处理时不会对所处理的产品表面产生影响。
GB/T 230 金属洛氏硬度试验方法
GB/T 231 金属布氏硬度试验方法
GB/T 3246.1铝及铝合金加工制品显微组织检验方法
GB/T 7998 铝合金晶间腐蚀测定方法
GB/T 9445 无损检测人员技术资格鉴定通则
GB/T 12966铝合金电导率涡流测试方法
GB/T 16475 变形铝及铝合金状态代号
目 次
1
本标准首次制定。
本标准是在美国军用规范MIL—H—6088G《铝合金热处理规范》和GJB1694—1993《变形铝合金热处理规范》基础上,根据我国铝合金民用材料生产应用中的实际情况,参考GJB509A—1995《热处理工艺质量控制要求》等标准编制而成的。
本标准对以下几个方面提出了要求:
——建立工艺规程和工艺规程重新审定;
淬火槽应具备内部或外部循环系统,以保证淬火介质流动,如果搅拌充分,能保证淬火均匀,同时满足所有的要求。产品可以进行搅动以代替盐浴循环。根据5.2可对其监控,来效验。
4.4.3.2.2 气体搅拌
如果根据5.2,对淬火槽液进行监测、效验,证明淬火均匀,允许淬火槽进行气体搅动。
4.4.3.2.3 加热和冷却
2A70
525~535
2A80
525~535
2A90
512~522
4A11
525~535
4032
模锻件
504~521
W
T4
—
6A02
515~525
6010
薄板
563~574
W
T4
—
6013
薄板
563~574
W
T4
—
6151
模锻件
510~527
W
T4
—
轧制环
510~527
W
T4
T452
6951
薄板
524~535
4.4.2.3精确度
应保证仪表的精确度,并进行定期检定。
4.4.3淬火设备和介质
4.4.3.1基本原则
淬火介质为水、空气、水聚合物溶液、液态气体或油,并为这些介质配备适当的设备。
4.4.3.2淬火槽
淬火槽具备足够尺寸以保证材料能够完全浸没在淬火介质中,并保证能充分除去待淬火的预期载荷内的热量。