2017年工厂现场小改善集锦
工厂改善方案模板
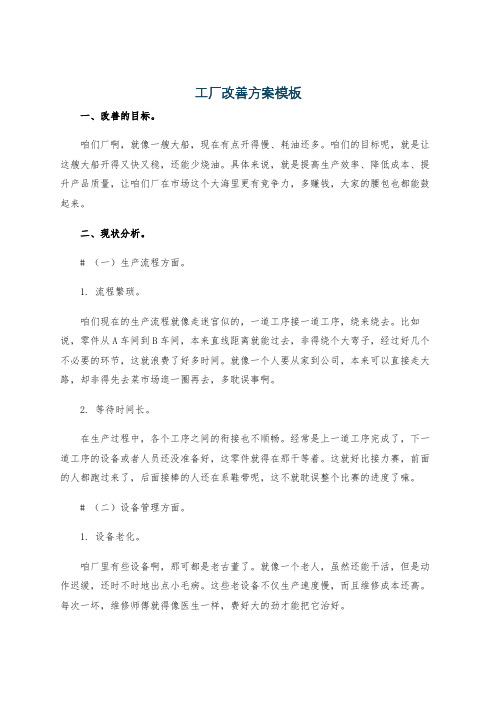
工厂改善方案模板一、改善的目标。
咱们厂啊,就像一艘大船,现在有点开得慢、耗油还多。
咱们的目标呢,就是让这艘大船开得又快又稳,还能少烧油。
具体来说,就是提高生产效率、降低成本、提升产品质量,让咱们厂在市场这个大海里更有竞争力,多赚钱,大家的腰包也都能鼓起来。
二、现状分析。
# (一)生产流程方面。
1. 流程繁琐。
咱们现在的生产流程就像走迷宫似的,一道工序接一道工序,绕来绕去。
比如说,零件从A车间到B车间,本来直线距离就能过去,非得绕个大弯子,经过好几个不必要的环节,这就浪费了好多时间。
就像一个人要从家到公司,本来可以直接走大路,却非得先去菜市场逛一圈再去,多耽误事啊。
2. 等待时间长。
在生产过程中,各个工序之间的衔接也不顺畅。
经常是上一道工序完成了,下一道工序的设备或者人员还没准备好,这零件就得在那干等着。
这就好比接力赛,前面的人都跑过来了,后面接棒的人还在系鞋带呢,这不就耽误整个比赛的进度了嘛。
# (二)设备管理方面。
1. 设备老化。
咱厂里有些设备啊,那可都是老古董了。
就像一个老人,虽然还能干活,但是动作迟缓,还时不时地出点小毛病。
这些老设备不仅生产速度慢,而且维修成本还高。
每次一坏,维修师傅就得像医生一样,费好大的劲才能把它治好。
2. 设备利用率低。
有些设备啊,一天到晚大部分时间都在闲着。
这就好比买了一辆豪车,结果一天就开那么一小会儿,多浪费啊。
这是因为咱们没有合理地安排生产任务,导致设备不能充分发挥作用。
# (三)人员管理方面。
1. 员工积极性不高。
我发现咱们厂里有些员工啊,工作起来就像没睡醒似的,提不起精神。
这是为啥呢?一方面是工资待遇可能不太合理,干多干少一个样,那谁还愿意拼命干啊?另一方面,员工的工作环境也不太好,又热又吵的,谁能有好心情工作呢?2. 员工技能参差不齐。
咱们厂的员工技能水平那是高低不一啊。
有的员工就像武林高手,干啥都又快又好;有的员工呢,就像刚入门的小徒弟,还得慢慢摸索。
工厂改善的101个技巧

工厂改善101技巧Number 01 . 制造“基本的基本”1、工厂中所进行的所有活动都为了满足顾客的需求;2、要彻底明白基本中的基本;3、缩短距离;4、同时使用双手;5、减少动作数量;6、轻松工作;7、一次拿到就不再放手;8、用手,不能动脚;9、不要吻合,要贴合;10、重复性工作方能彰显智慧水平;11、比起学习,要习惯工作;12、浪费有七种,最应注意过量生产所带来的浪费。
Number 02 . 现场改善1、对有损于安全以及给客户带来不利的改善,绝对不能做;2、只有必需品的工作场所称之为干净的工作场所;3、理想的整理整顿状态是一下子能够取出所需物品的状态;4、自信地迎接客人的水平称为清扫到位的清洁状态;5、不要将物品堆积到高于视线的位置;6、不要数,要摆成形状看;7、不要批量购买,只买需要的东西;8、要视螺丝为天敌;9、腰杆挺直了吗?10、先后顺序是安全第一、质量第二、生产周期和成本第三;11、在现场现物面前大声交流;12、改变公司的不是那些了不起的改善,而是谁都能执行的简单、可以模仿的改善;13、比起100个道理或想法,在现场付诸实践一次会产生100倍的价值;14、改善所必需的是主动性的量、速度及持续性;Number 03 . 结构改善1、及时形式上也要尝试,将不可见的东西可视化;2、将工厂内的所有位置赋予住址;3、给活动一个原创性的名字;4、每个操作现场配备垃圾箱;5、区分好真正的亲眼所见与非亲眼所见;6、监察室要用不同的方法重复一次;7、问题只有一个看不到,但聚集在一起就会显现出来;8、地面、墙壁都要使用;9、对有时间间隔的工作,要制作“回忆录”;10、工作指示书中的信息一定要以最终样式显示传达;11、比起倡导“后工序是顾客”一百次,不如实际观看后工序一次;12、不要拿着去,要去取;13、将问题透明化,问题将解决80%;14、多品种少量生产的关键在于制造操作的可视化;Number 04 . 操作改善1、不要说人手不足,要区分考虑人不足和手不足;2、教授全体员工能够独当一面地工作;3、不要教授操作,教授如何工作;4、包括教授方法在内,将工作系统化;5、小工作用电脑,大工作用图纸;6、伪专家是否在横行霸道?7、不要思考改善工作,要思考这个工作是否能够给公司带来利益;8、所有人都能够无数次反复实践的成为标准化;9、少数精锐从少数开始,从优秀的人开始选拔,实现精锐化;10、专门的管理人员的存在是现场运转不良的表现;11、靠人还战术无法解决索赔;12、没有订单就没有生产;Number 05 . 设备改善1、生产线缩短了、产品质量会提高、成本会下降;2、在机器或设备上标示能够确认工序的序号和流程布局的序号;3、实现生产信息传达数据化;4、制造只能以全部工序当中最慢的工序速度进行;5、如果工序间的流通未创造出来,引进系统反而必须进行管理,自会增加库存;6、没有销售流水生产设备的;7、材料在上,产品在下;8、不要用人力,要使用动力搬运;9、电灯,与其关掉不如让它自然熄灭;10、工厂里的门有必要考虑有防盗、防噪声、安全、卫生、节能、保温、符合法律要求等,从外观上看,其实没有必要;11、会调整设备才嫩独当一面,是设备內制化,实现独一无二;Number 06 . 强大的制造1、对照制造六个阶段的水平,掌握公司实力;2、设计改善优于现场改善一百倍;3、商品制造不是按产品类别,而是按客户类别;4、理想的库存量是零;5、比起提高生产速度,更需要提高工序的转换速度;6、工序转换中发现螺丝时,一定要引起重视,有改善余地;7、在发货期限内,以最慢的速度来生产;8、存在不会马上用到的物品的话,要考虑购买方法是够有问题,存在不会马上被移动的中间品的话,要考虑生产方式是否有问题;9、在物件管理中发挥人眼和电脑相辅相成的作用;10、要保有库存的话,最好接近原材料;11、制造在附加价值产生瞬间之外,是搬运或停滞;12、提高生产率与削减库存同时进行的话,成本必会降低;13、质疑物品的流动方式;14、信息虽各种各样,但如果追根溯源,其实只有“订购信息”一种;15、不要提前备齐必要物品,在必要的时候备齐;16、多品种变量生产时,人和设备都要实现多能工化;17、监督者监督工作流程,工厂长监督制造流程,管理者监督转钱流程;18、通过改善现场为开展新事业创造必要空间;19、东西扔掉,智慧萌生,创造空间,想法萌生。
自行车厂现场改善案例

前言:中兴厂为一百多人生产自行车之小厂,有二栋三层楼之厂房,最近成为本公司外包协力厂,为提高其生产效率,并降低其代工价格,我方派出一改善小组去该厂指导,帮助该厂做现场改善。
改善小组成员包括IE一人,品管一人。
以下是现场改善的过程和改善后成果。
改善无处不存在,改善无人不会做,虽是小小的一个案例,主要说明我们日常解决问题的模式,积沙成塔、涓水成河,实践才是力量。
中兴厂现场改善案例:二、现状分析(改善前)1.总装作业员人数48人,产能22台/小时(平匀每天工作11小时,产出250台成车).2.各工序间的工作时间差太大,最长的时间为89.18秒,最短的时间为17.49秒.造成人员的心里不平衡,产出时间拉长.3.车架要用两人每次2支的从办公楼三楼搬至总装二楼.约移动47M.4.成车要一台一台的搬到一楼仓库.约移动20M5.作业员的积急性不高.三、改善实施(总装)(一)改善方法1.先测出振华厂各工作站的实际所需工时,经过合理的计算后,制订合理的标准工时,编排合理的上线人员,交总装主管审阅是否认可.2.工时及上线人员取得主管的认可后,仍无法执行,经调查从上至下都想依混时间来取得工资.故明明1小时可做完的事故意拖到2小时完成,故当时想采用计件的方式来消除此现象,经萧副总及周科合理计算后以大行但现场的员工都很聪明,先依以往的产能与现行的计件单价进行计算,以原方式每月可领1000元左右的工资,而依计件单价计算每月只有650元左右的工资,故执行不下去.3.按总经理的高额奖金的方试来测试总装的最高产能.先设定一个奖金额各目标产能,再用振华厂之前的最高产能与目标产能的百分比做基数,第一天的产能与目标产能的百分比减去原百分比的数值剩奖金额所得的数值为第一天的奖金, 第二天的产能与目标产能的百分比减去之前的最高百分比的数值剩奖金额所得的数值为第二天的奖金,一次类推.直到达到目标时为止.(当时预计需一个月左右才能达到)4. 员工对高客奖金不感相信,故积极性不高,但毕境是高额奖金,还是有一点吸引力的,所以第天员工先依试探的心态提高一点来试验我们的承诺的真实性.5. 第二天上午九点钟时财务部准时将奖金发到各科长手中,并要求十点钟之前发到员工手中,结果取得了员工的信任.之后仅用七天就达到了目标置.6. 开始公布计件单价,员工们看到单价后与他们最高产能计算,一个月不加一个班也可拿1150元左右.也就有了信心.7. 再进行物流方面的改善..8. 加装空中输送线,减少搬运人员及缩短搬运时间.9. 加装电梯(原振华厂已开始安装),使成品用栈板向成品仓绞库.10. 开始由振华厂自已自发的进行减员.2.成车的移动由原来的20M缩短到现在的9M.3.投资117000元人民币.4.总装线上线人数降到37有人,产能上升到45台/每小时(但因目前订单不足的原因现为336.单从人工费方计算投入回收时间:117000/60/8/26=9.375月≒10月7.制造成本方面的节约因资料不全的情况下只能用百分比来计算:现每天的产能以原来方式需用的小时数:45*8/22=16.36现在的直接费用与原费用比为:8/16.36*100%=49%五、现状分析(涂装)(一).问题分析1.贴花人员13人.2.前处理配员3人,喷手6人,调油由组长兼职,上挂4人,全检一人.3.产能25套/小时.4.烤漆件前处理后下挂专用台车太少.5.作业员的积急性不高.6.返修率偏高.7.以下油漆要喷两次面漆,7776/7775/7871/782/9177/9174/775/8860.8.线长283.5M,315个工位.线速为600时,每25秒可过一工位.要位间距09M.线走一周需7875秒.9.喷一次面漆时可全员生产.10.喷二次面漆时,第一遍由上挂,喷底漆,喷面漆人员(8人)作业,全检及喷金油人员(3人)处于等待状态.第二遍时由喷面漆,喷金油,全检人员(5人)作业,但喷金油及面漆人员(3人)分别有约1H及2H的等待时间.上挂及喷底漆人员完(6人)全处于等待状态.六、改善实施(涂装)(一).改善方法1.依配合总装生产且提高本部门的效率来作奖励的方式来测试最高产能.2.达到目标产能后再公布计件金额.3.结果出现更有效的现象,就时喷一次油漆时只要生产4小时就能完成生产任务啦.前处理只要4小时就能完成生产任务,而所得的新资比之前的还高.最还达到自已内部工作进行自发的调整,前处理上午上班,喷油下午上班.这样合整个车产的设备的运转时间减少了6时左右.直接节约了成本费.4.制定不良品奖惩制度.5.制定油漆使用量标准.(未执行)6.作业员互动.(未执行).七、改善后成果(涂装)1.贴花人员10人.2.喷涂人员13人.3.产能36台/小时(全月平均产能).5.单从人工费方计算每天可节约费用:3.211X11X8=282.48元6.制造成本方面的节约因资料不全的情况下只能用百分比来计算:现每天的产能以原来方式需用的小时数:36*8/25=11.52现在的直接费用与原费用比为:8/11.52*100%=71%.八、现状分析(焊接)(一).问题分析1.焊接组27人.2.冲压组10人.3.产能25套/小时.4.焊接及冲压之间往复搬运.5.作业员的积急性不高.6.一人可以作业的地方却按排两人作业.7.有些设备老化,影响生产进度.8.点焊方面的模治具设计不合理,造成无法完成一人作业.九、改善实施(一).改善方法1.将不合理的模治具及设备进行修改,尽量将一人可以作业的事情尽量避免两人作业.2.将多余的人员调到其它部门去.3.设备的位置进行调整,减少物料的搬运次数.(未完全执行)4.新购设备,改变生产流程.5.依配合总装生产且提高本部门的效率来作奖励的方式来测试最高产能.6.达到目标产能后再公布计件金额.7.但有部分主管却算到自已没有得到好处,故造出你现在这样做虽说工资高了,但拿之前的产能比,你比之前累多啦.故鼓动员工罢工.8.把参加罢工的员工全部开除,先从大行调人支持.确保正常生,让其知道,罢工是无用的.稳定了公司人员的心9.为了减少成本的投入,将焊接一班改为两班.将功能较差的焊机停用.十、改善后的成果(焊接)1.产能34套/小时.1.378X9X8=99.216元4.制造成本方面的节约因资料不全的情况下只能用百分比来计算:现每天的产能以原来方式需用的小时数:34*8/25=10.886.现在的直接费用与原费用比为:8/10.88*100%=73%.。
车间持续改善项目

车间持续改善项目
车间持续改善项目是一个长期的过程,旨在不断优化生产流程、提高效率、减少浪费、降低成本,并提高产品质量。
以下是一些常见的车间持续改善项目的例子:
1.5S管理:通过实施5S管理(整理、整顿、清扫、清洁、素养),提高生产现
场的整洁度和秩序,减少浪费,提高工作效率。
2.精益生产:通过消除生产过程中的浪费,降低成本,提高生产效率。
这可能包
括减少生产过剩、优化工作流程、减少库存等措施。
3.设备自动化:通过引入自动化设备,提高生产效率,减少人工错误和人力成本。
这可能包括自动化生产线、机器人等。
4.质量管理体系:通过实施质量管理体系(如ISO 9001),确保产品质量符合
标准,提高客户满意度。
5.环境管理体系:通过实施环境管理体系(如ISO 14001),确保生产过程中
的环境保护和可持续发展。
6.安全生产管理:通过加强安全生产管理,减少事故风险,保障员工的人身安全
和健康。
7.信息化管理:通过引入信息化管理系统,提高生产数据的管理和分析能力,为
决策提供支持。
这些项目通常需要跨部门的合作和持续的努力,以实现长期的效益。
在实施持续改善项目时,应注重数据分析和持续改进的方法,以确保改善的有效性和可持续性。
企业生产现场改善措施

企业生产现场改善措施引言在现代企业中,生产现场扮演着至关重要的角色。
一个高效、安全的生产现场可以帮助企业提高生产效率、降低成本、改善质量,并最终提升客户满意度。
然而,生产现场通常面临一系列的挑战,如物料混乱、流程繁琐、设备故障等。
本文将介绍一些企业可以采取的改善措施,以优化生产现场的运作。
1. 5S 实施5S 是一种改善生产现场管理的方法论,它由日本企业提出并广泛应用。
下面是5S 的五个步骤:•整理(Seiri):清理现场,将不必要的物品移除,只留下必需的物品。
•整顿(Seiton):为需要的物品提供一个固定的位置,并标识出来,以便易于找到。
•清扫(Seiso):持续保持现场干净整洁,每日清扫,发现并防止污垢和杂乱堆积。
•清晨(Seiketsu):使整个生产现场养成好习惯,正确使用5S 方法,保持长期改善。
•纪律(Shitsuke):培养员工负责任的态度,使 5S 成为日常工作中不可或缺的一部分。
通过实施 5S,企业可以改善生产现场的组织与整洁,消除浪费,提高生产效率。
2. 流程优化流程优化是指通过消除无效的操作和浪费来改善生产现场的工作流程,以提高生产效率。
下面是一些流程优化的方法:•定期进行价值流程分析(Value Stream Mapping),以确定从订单到交付的整个流程,找出非价值增加的活动,以便优化和改进。
•采用精益生产(Lean Production)方法,通过精确计算生产能力、库存和订单需求,实现生产和供应链的精细管理,避免过剩生产和库存积压。
•使用工时研究和工作标准化方法,确保每个工序的标准化,并根据实际情况进行调整,以提高产品的一致性和质量。
•引入自动化和智能化技术,减少人工操作,提高生产效率和质量,例如自动化的生产线、物流自动化系统等。
通过流程优化,企业可以降低生产成本,提高生产效率和质量,同时减少资源和时间的浪费。
3. 培训与员工参与一个成功的企业生产现场改善计划需要员工的积极参与和培训支持。
工厂改善提案案例大全
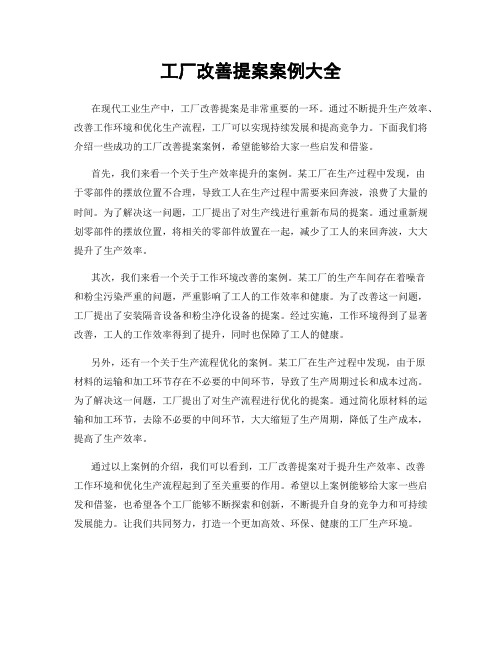
工厂改善提案案例大全在现代工业生产中,工厂改善提案是非常重要的一环。
通过不断提升生产效率、改善工作环境和优化生产流程,工厂可以实现持续发展和提高竞争力。
下面我们将介绍一些成功的工厂改善提案案例,希望能够给大家一些启发和借鉴。
首先,我们来看一个关于生产效率提升的案例。
某工厂在生产过程中发现,由于零部件的摆放位置不合理,导致工人在生产过程中需要来回奔波,浪费了大量的时间。
为了解决这一问题,工厂提出了对生产线进行重新布局的提案。
通过重新规划零部件的摆放位置,将相关的零部件放置在一起,减少了工人的来回奔波,大大提升了生产效率。
其次,我们来看一个关于工作环境改善的案例。
某工厂的生产车间存在着噪音和粉尘污染严重的问题,严重影响了工人的工作效率和健康。
为了改善这一问题,工厂提出了安装隔音设备和粉尘净化设备的提案。
经过实施,工作环境得到了显著改善,工人的工作效率得到了提升,同时也保障了工人的健康。
另外,还有一个关于生产流程优化的案例。
某工厂在生产过程中发现,由于原材料的运输和加工环节存在不必要的中间环节,导致了生产周期过长和成本过高。
为了解决这一问题,工厂提出了对生产流程进行优化的提案。
通过简化原材料的运输和加工环节,去除不必要的中间环节,大大缩短了生产周期,降低了生产成本,提高了生产效率。
通过以上案例的介绍,我们可以看到,工厂改善提案对于提升生产效率、改善工作环境和优化生产流程起到了至关重要的作用。
希望以上案例能够给大家一些启发和借鉴,也希望各个工厂能够不断探索和创新,不断提升自身的竞争力和可持续发展能力。
让我们共同努力,打造一个更加高效、环保、健康的工厂生产环境。
工厂改善措施
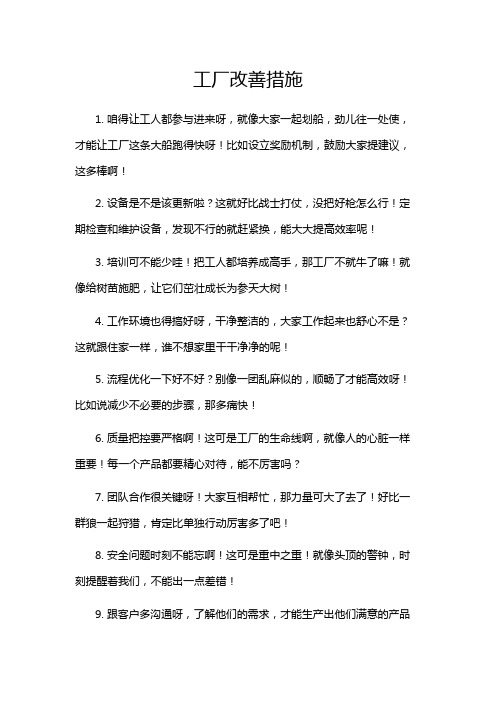
工厂改善措施
1. 咱得让工人都参与进来呀,就像大家一起划船,劲儿往一处使,才能让工厂这条大船跑得快呀!比如设立奖励机制,鼓励大家提建议,这多棒啊!
2. 设备是不是该更新啦?这就好比战士打仗,没把好枪怎么行!定期检查和维护设备,发现不行的就赶紧换,能大大提高效率呢!
3. 培训可不能少哇!把工人都培养成高手,那工厂不就牛了嘛!就像给树苗施肥,让它们茁壮成长为参天大树!
4. 工作环境也得搞好呀,干净整洁的,大家工作起来也舒心不是?这就跟住家一样,谁不想家里干干净净的呢!
5. 流程优化一下好不好?别像一团乱麻似的,顺畅了才能高效呀!比如说减少不必要的步骤,那多痛快!
6. 质量把控要严格啊!这可是工厂的生命线啊,就像人的心脏一样重要!每一个产品都要精心对待,能不厉害吗?
7. 团队合作很关键呀!大家互相帮忙,那力量可大了去了!好比一群狼一起狩猎,肯定比单独行动厉害多了吧!
8. 安全问题时刻不能忘啊!这可是重中之重!就像头顶的警钟,时刻提醒着我们,不能出一点差错!
9. 跟客户多沟通呀,了解他们的需求,才能生产出他们满意的产品
呀!这不是很简单的道理嘛,就像朋友之间要多交流感情一样!
10. 创新也得搞起来呀!不能老是老一套,得有点新花样,这样工厂才能有活力呀!就像给生活加点调料,变得有滋有味!
我觉得这些措施要是都能好好落实,那工厂肯定能越来越好,发展得越来越棒!
原创不易,请尊重原创,谢谢!。
生产制造现场改善技巧
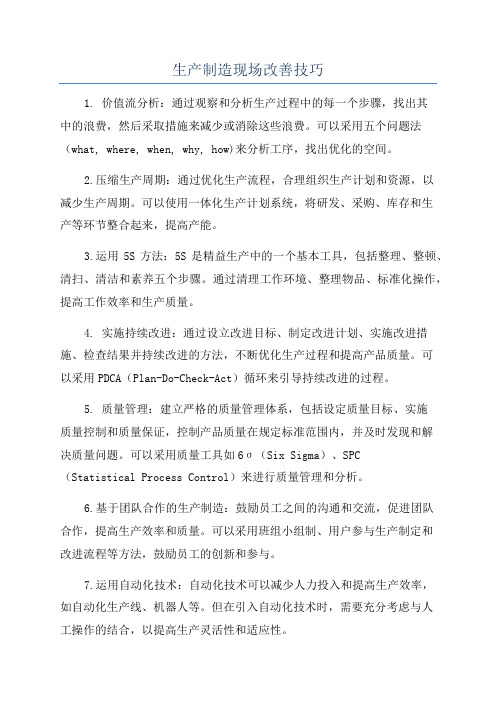
生产制造现场改善技巧1. 价值流分析:通过观察和分析生产过程中的每一个步骤,找出其中的浪费,然后采取措施来减少或消除这些浪费。
可以采用五个问题法(what, where, when, why, how)来分析工序,找出优化的空间。
2.压缩生产周期:通过优化生产流程,合理组织生产计划和资源,以减少生产周期。
可以使用一体化生产计划系统,将研发、采购、库存和生产等环节整合起来,提高产能。
3.运用5S方法:5S是精益生产中的一个基本工具,包括整理、整顿、清扫、清洁和素养五个步骤。
通过清理工作环境、整理物品、标准化操作,提高工作效率和生产质量。
4. 实施持续改进:通过设立改进目标、制定改进计划、实施改进措施、检查结果并持续改进的方法,不断优化生产过程和提高产品质量。
可以采用PDCA(Plan-Do-Check-Act)循环来引导持续改进的过程。
5. 质量管理:建立严格的质量管理体系,包括设定质量目标、实施质量控制和质量保证,控制产品质量在规定标准范围内,并及时发现和解决质量问题。
可以采用质量工具如6σ(Six Sigma)、SPC(Statistical Process Control)来进行质量管理和分析。
6.基于团队合作的生产制造:鼓励员工之间的沟通和交流,促进团队合作,提高生产效率和质量。
可以采用班组小组制、用户参与生产制定和改进流程等方法,鼓励员工的创新和参与。
7.运用自动化技术:自动化技术可以减少人力投入和提高生产效率,如自动化生产线、机器人等。
但在引入自动化技术时,需要充分考虑与人工操作的结合,以提高生产灵活性和适应性。
8. 专注缺陷预防:通过设立缺陷预防机制,提前发现和预防潜在的质量问题。
可以采用FMEA(Failure Mode and Effects Analysis)等方法来识别潜在问题,并采取相应的预防措施。
9.设备养护管理:定期检查和维护设备,保持设备的良好状态和正常运转,减少突发故障和停机时间。
生产现场改善8个技巧

生产现场改善8个技巧1. 价值流图法(Value Stream Mapping):通过绘制价值流图,清晰地展示了整个生产流程中的价值、非价值和浪费步骤,从而可以针对性地进行改进。
通过消除浪费,提高工作流程,使得生产现场运转更加高效。
2.5S工作法:5S工作法分别是整理、整顿、清扫、清洁、素养的五个步骤。
这种方法通过减少时间浪费和杂乱无章的情况,提高工作效率,同时还有助于改善安全和质量问题。
3. 精益生产(Lean Production):精益生产是一种以减少资源浪费为中心的生产方式。
它通过去除无价值的步骤,减少库存,实现适应性和灵活性,提高效率和质量。
该方法可以通过改进生产流程,降低生产成本,并提高客户满意度。
4. 产能平衡(Capacity Balancing):产能平衡是指在生产过程中对工作站的工作负荷进行合理分配,以实现流程平衡。
通过产能平衡,可以避免生产线上的过度和不足,提高各个工作站的效率和产品质量。
5. 标准化工作(Standardized Work):标准化工作是通过制定一系列规程和标准来规范工作流程。
这种方法可以提供一种明确的、可复制的工作流程,使生产现场的工作更加高效和一致。
6.人员培训和技能提升:通过为员工提供培训和技能提升的机会,可以提高他们的生产能力和工作效率。
这包括传授新的生产技术、培养团队合作精神和解决问题的能力等。
7. 持续改进(Continuous Improvement):持续改进是指通过定期评估和改进生产工艺和流程来提高效率和质量。
这需要建立一种改进的文化,鼓励员工提出改进建议,并与他们一起制定和实施改进计划。
8.自动化和数字化技术的应用:通过引入自动化和数字化技术,可以大大提高生产效率和质量水平。
这包括使用机器人和自动化设备来替代手工操作,使用数据分析来优化生产过程,以及使用物联网技术来实现生产过程的实时监控。
通过采用以上八个技巧,可以有效改善生产现场,提高生产效率和产品质量,并最终提高企业的竞争力和市场份额。
工厂车间改善提案

工厂车间改善提案《工厂车间改善提案》嘿,各位工友们!咱今天就来聊聊咱这工厂车间那些能改进的地儿。
咱就先从那个照明说起哈。
有一回啊,我上夜班,那车间里的灯啊,有的亮有的暗。
我正忙着干活呢,一抬头,差点被那暗的地方给绊倒喽。
哎呀妈呀,这多危险呐!咱这车间那么大,灯光可得整均匀了呀。
要是都亮堂堂的,咱干活不也得劲儿嘛。
就像咱家里晚上开灯一样,亮堂堂的看着就舒服,干活心情都好。
还有那工具摆放的地方,也得整整。
有一次我找个扳手,嘿,找了半天都没找着。
东翻翻西翻翻,急得我满头大汗。
后来好不容易在一个角落里找到了,可浪费了不少时间呢。
咱就不能弄个专门的工具架,把各种工具都摆得整整齐齐的,标上标签,这样找起来多方便呐。
就像超市里摆货一样,啥都一目了然。
再说说那休息区吧。
咱这干活累了,也得有个舒服的地儿休息休息不是。
现在那休息区啊,就几个小板凳,硬邦邦的。
咱能不能弄点软和点的椅子,再摆上几盆花啥的,看着也舒心呐。
有一回我累得不行了,想坐那歇会儿,一屁股坐下去,差点没把我屁股硌开花喽。
还有啊,车间里的通风也得加强加强。
夏天的时候,那热得呀,跟蒸笼似的。
干活干得一身汗,那味道可不好闻了。
咱要是把通风弄好了,空气流通起来,不就凉快多了嘛。
就像咱在公园里一样,有风吹过来,多舒服呀。
咱这车间的卫生也得重视起来。
有时候地上乱七八糟的,有废材料啊,垃圾啥的。
有一回我不小心踩在一块废材料上,差点滑倒了。
咱得安排专人定时打扫打扫,保持车间干净整洁。
这样咱干活的时候也安全,看着也舒服。
最后啊,咱这车间的安全标识也得弄得更明显点。
有些地方安全标识都不清晰了,新来的工友们都不知道哪里危险哪里安全。
咱就像在路上开车一样,那些交通标识得清清楚楚的,这样大家才能更安全地干活嘛。
总之啊,咱这工厂车间要是能把这些地方都改善改善,那咱干活肯定更有效率,也更安全更舒服。
咱大家一起努力,让咱这车间变得越来越好,咱干活也更带劲不是!嘿嘿,就这么着吧,期待咱车间的新变化哟!。
生产车间改善提效方案,生产现场改善的一些措施与细节
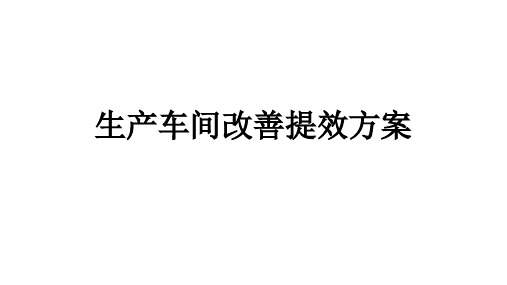
• 6、工具设备状态 • 在好的工厂里,设备整洁而且保养良好,设备相关信息一目了然
并且即时更新。 • 在一个铸造厂的机加工车间,虽然各种车床都不是很先进,甚至
否有异味,噪音是否太大,车间是否整洁,因为这些也会直接影 响工人的工作状态,进而影响生产效率和产品质量。
• 2、空间利用与布局
• 例如同一批零件从A区搬到B区加工完后再搬回A区做后道加工, 然后搬到C区处理,最后还要再搬回B区,搬运的浪费简直达到极 致。
• 原则上当天使用的生产物料应沿生产线存放,而不是在几个库存 区分隔存储,工具和工装摆放应尽量靠近机器。
一、现场管理篇
• 质优价廉、适销对路、按期交货的产品是生产 现场中制造出来的,要靠现场管理来保证.从这 种意义来讲,现场管理水平的高低,是决定企业 优势和实力的基础.
1.现场管理的含义,现场管理的 对象和范围
• 目标
企业经营目标
• 现场管理
一线干部 科学管理制度、标准和方法
计划、组织、协调、控制和激励
历史很长,但都在良好的状态下运转。 • 每台机器的侧面都醒目地贴着一张卡片,上面记录着该设备的型
号、采购日期、价格、供应商、维修记录、保养记录等等。 • 日常点检表也记录得很完整,有的点检表上清晰地记录着操作工
发现的隐患,以及设备部门的签字及处理方案。
• 此外,一线工人和参与产品开发和生产的人员最清楚新设备的优 缺点,也最了解生产线的实际需求。在很多工厂设备采购都是由 高层或设备部决定,很少征求一线人员意见,这也会导致后续使 用中大量问题产生。
生产现场有24个明显改善点,普通员工一看就懂,一学就会

生产现场有24个明显改善点,普通员工一看就懂,一学就会很多时候,改善并没有多大难度,员工往往缺乏的是识别的能力,不知道哪里有问题,不知道从哪里入手。
本篇归纳了现场24种常见的不合理现象,并教大家一些简单实用的方法,可以发动现场所有员工进行识别改进。
1、观察人的动作1、频繁走动。
通过布局优化,搬运规划,自动化小车,线旁布置等实现。
2、大幅弯腰。
通过设计桌台,增加底座高度,物料小车等实现。
3、反复转身。
通过改变设施位置,改善作业方式,增加辅助工具等实现。
4、重物高举。
通过辅助设施(如电葫芦),滑轮辅助,踏台或降低需求高度等实现。
5、尽力伸手。
通过布局改进,简易自动化物料存储架等实现轻松拿取。
6、用力推拉。
通过减少批量,改进移动小车,设计滑轨,或自动搬运设施实现。
7、扭曲身姿。
通过改进作业对象位置,移动座椅,或工具改善等实现。
8、危险动作。
识别具有安全隐患的动作行为,通过改善进行预防。
2、观察一项作业1、人机等待。
通过人机分析,消除一切作业过程等待行为,使人机工作协作合理化。
2、分工问题。
通过个人工作负荷平衡,改善作业时间,使各个环节任务均衡。
3、缺乏标准。
作业中每个环节应该有明确的工艺标准和操作标准,保障输出合格。
4、缺乏方法。
作业中每个环节应该有通过实践提炼的工作方法和对应技能并固化。
5、资源配置。
关于作业中所需的所有资源应该被按时、按量放置在距离最近的地方。
6、工具设施。
所有设施、工装、工具、量检具等硬件,被合理的规划在作业区域周围。
7、目视管理。
使用标识、标牌、标签、标线、颜色、形状、信号灯等消除作业障碍。
8、防呆管理。
对所有容易出现异常的地方,借鉴防错法10大原理改进,从源头防错。
3、观察一条生产线1、资源缺失。
生产物料、人员、图纸、工具、辅助物品等按时到位,位置数量固定。
2、明显瓶颈。
识别生产线中明显的瓶颈环节,通过改善缩短时间,平衡作业内容。
3、停线异常。
识别导致停线的所有因素,测量数据,按影响程度排序,逐个发起改善。
21个经典生产车间改善案例

提案人
项目类别
作业改善
实施人
Before(图片)
邹龙庚 邹龙庚
提案时间 完成时间
09/08/18
提案部门
IE
09/08/18
确 认人
车间
After(图片)
问题点 改善
前 原因分析
改善对策
保护膜上方用纸板档风,导致有灰尘掉到产品上
风大把保护膜吹起,所以用纸板把风挡住,但纸屑 易掉下。
改善 后
重新制作保护膜架,把保护膜架加高。
09/08/19
提案部门
车间
09/08/19
确 认人
IE
After(图片)
问题点 改善 前 原因分析
改善对策
批锋到处飞
产品为尼龙料,批锋多,用刀批时风扇将批锋吹 得到处。
改善 后
将用大胶盒放到桌面,在盒上批后批锋将掉在盒 子中。
现 状 已执行
改 善结 果 5S明显改善.
改善成果个案
项目名称
创维3020面板
提案部门
IE
09/08/12
确 认人
车间
After(图片)
问题点 改善
前 原因分析
改善对策
保护膜卷经常掉下 保护膜没有被固定 将两头固定使得保护膜不会掉下
改善 后
现 状 已执行
改 善结 果 保护膜卷不再掉下
改善成果个案
项目名称 项目类别
三星LED键
提案人
操作改善
实施人
Before(图片)
车间 车间
改
善
没有统一规定地方,放置散乱倒置会漏返工
后
规定每班次QC抽检不良品放到办工室前门口.
现 状 已执行
改 1,不再会漏掉 善结 果 2,不良品会引起班组长,主管的高度 重视
2017年精益生产提案改善报告 精品

438×4>343×5
?4条支线供5 条主线! Front Housing组装段瓶颈工站UPH=438;
主线瓶颈工站UPH=343
改善方案:
将4条Front Housing组装段合并成为 1条Front Housing前加工线。
改善后产 线照片
五条主线
节省5人
Ⅳ
改善成果展示
(一)有形绩效
线
别
提升效率(%) 精减人力(人) 年节约成本(RMB) 30.6% 33.3% 110人 15人 264万元 36万元
合并工站还有20号装夹具/扫描/开机工站;7号贴IC绝缘 片/金属底盘黑色贴片。
根据工时数据,将18号工站“装主镜片组件”由3人 精简为2人。
人力配置
取 消 前
1 1 1
工站名称
18.装主镜片组件
工站工时
16.71s
标准工时
16.71/3=5.57s
根据以上数据,取消18号工站1人。改动后工站时间为8.36s。 取 消 前
自动检测, 提升品质。
工厂生产车间改善提案
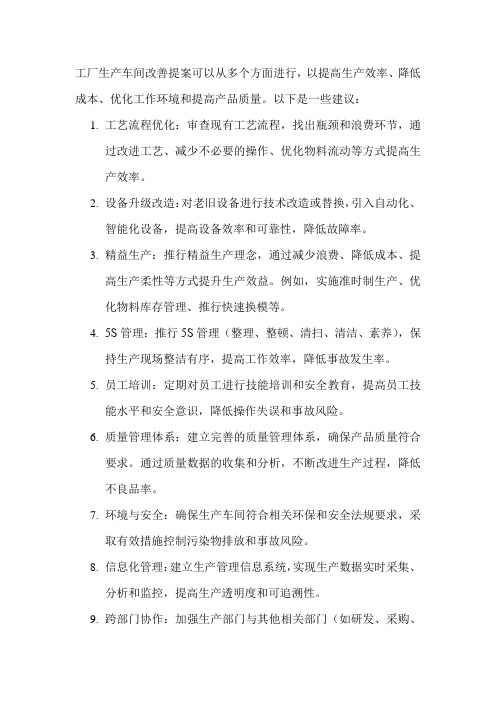
工厂生产车间改善提案可以从多个方面进行,以提高生产效率、降低成本、优化工作环境和提高产品质量。
以下是一些建议:
1.工艺流程优化:审查现有工艺流程,找出瓶颈和浪费环节,通
过改进工艺、减少不必要的操作、优化物料流动等方式提高生产效率。
2.设备升级改造:对老旧设备进行技术改造或替换,引入自动化、
智能化设备,提高设备效率和可靠性,降低故障率。
3.精益生产:推行精益生产理念,通过减少浪费、降低成本、提
高生产柔性等方式提升生产效益。
例如,实施准时制生产、优化物料库存管理、推行快速换模等。
4.5S管理:推行5S管理(整理、整顿、清扫、清洁、素养),保
持生产现场整洁有序,提高工作效率,降低事故发生率。
5.员工培训:定期对员工进行技能培训和安全教育,提高员工技
能水平和安全意识,降低操作失误和事故风险。
6.质量管理体系:建立完善的质量管理体系,确保产品质量符合
要求。
通过质量数据的收集和分析,不断改进生产过程,降低不良品率。
7.环境与安全:确保生产车间符合相关环保和安全法规要求,采
取有效措施控制污染物排放和事故风险。
8.信息化管理:建立生产管理信息系统,实现生产数据实时采集、
分析和监控,提高生产透明度和可追溯性。
9.跨部门协作:加强生产部门与其他相关部门(如研发、采购、
销售等)的沟通和协作,确保生产过程的顺畅进行。
10.持续改进:鼓励员工提出改进意见和建议,建立持续改进机制,
不断完善生产车间的运作和管理。
生产现场七大改善要点

生产现场七大改善要点1、工艺流程查一查即向工艺流程要效益。
分析现有生产、工作的全过程,哪些工艺流程不合理,哪些地方出现了倒流,哪些地方出现了停放,包括储藏保管、停放状态、保管手段(如储存容器配备、货架配备、设施条件)、有无积压状态?哪些工艺路线和环节可以取消、合并、简化?寻找最佳停放条件,确定经济合理的工艺路线。
2、平面图上找一找即向平面布置要效益。
仔细检查和分析工厂平面布置图、车间平面布置图和设备平面布置图,分析作业方式和设备、设施的配置,按生产流程的流动方向,有无重复路线和倒流情况,找出不合理的部分,调整和设计一种新的布局,使生产流程在新的布置图上路线最短,配置最合理。
3、人机工程挤一挤即向人机联合作业要效益。
人和设备构成了人机工程,在分析时要分析作业者和机器在同一时间内的工作情况,有无窝工、等待、无效时间,通过调整工作顺序改进人机配合,寻求合理的方法,使人的操作和机器的运转协调配合,将等待时间减少到最大限度,充分发挥人和机器的效率。
4、关键路线缩一缩即向网络技术要效益。
将现有的工序和作业流程绘制成网络图。
从中找出关键路线,然后从非关键路线上抽调人财物,加强关键路线,或采用平行作业。
交差作业等等形式,实现时间和费用的优化。
5、流水线上算一算即向流水线要效益。
研究流水线的节拍、每个工序的作业时间是否平衡,如果发现不平衡,就要通过裁并、简化、分解等等手法,平衡流水线。
消除因个别工序缓慢而导致的窝工和堆积。
6、动作分析测一测即向动作分析要效益。
研究工作者的动作,分析人与物的结合状态,消除多余的动作、无效动作或缓慢动作,如弯腰作业、站在凳子上作业、蹲着作业、作业场所不畅、没有适合的工位器具、人与物处于寻找状态等,通过对人的动作和环境状态的分析和测定,确定合理的操作或工作方法;探讨减少人的无效劳动,消除浪费,解决现场杂乱,实现人和物紧密结合,提高作业效率。
7、搬运时空压一压即向搬运时间和空间要效益。
据统计,在产品生产中搬运和停顿时间约占70-80%,搬运的费用约占加工费的25-40%,要通过对搬运次数、搬运方法、搬运手段、搬运条件、搬运时间和搬运距离等综合分析,尽量减少搬运时间和空间,寻找最佳方法、手段和条件。
工厂现场改进方案
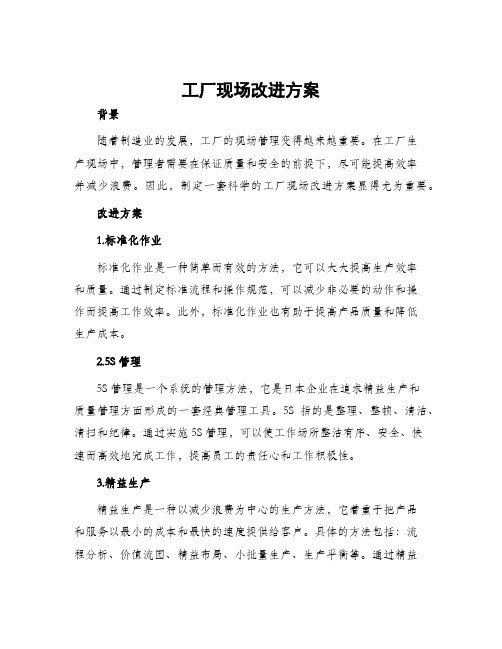
工厂现场改进方案背景随着制造业的发展,工厂的现场管理变得越来越重要。
在工厂生产现场中,管理者需要在保证质量和安全的前提下,尽可能提高效率并减少浪费。
因此,制定一套科学的工厂现场改进方案显得尤为重要。
改进方案1.标准化作业标准化作业是一种简单而有效的方法,它可以大大提高生产效率和质量。
通过制定标准流程和操作规范,可以减少非必要的动作和操作而提高工作效率。
此外,标准化作业也有助于提高产品质量和降低生产成本。
2.5S管理5S管理是一个系统的管理方法,它是日本企业在追求精益生产和质量管理方面形成的一套经典管理工具。
5S指的是整理、整顿、清洁、清扫和纪律。
通过实施5S管理,可以使工作场所整洁有序、安全、快速而高效地完成工作,提高员工的责任心和工作积极性。
3.精益生产精益生产是一种以减少浪费为中心的生产方法,它着重于把产品和服务以最小的成本和最快的速度提供给客户。
具体的方法包括:流程分析、价值流图、精益布局、小批量生产、生产平衡等。
通过精益生产,可以不断地消除浪费,提高生产效率,减少库存,提高客户满意度。
4.人性化管理人性化管理是指在生产过程中注重员工的合理化、安全化和享受化,实现员工自主和终身学习的管理方法。
人性化管理包括:工作环境改善、员工培训、激励和奖励等。
通过这些管理手段,可以提高员工的工作积极性和工作满意度,从而提高生产效率和产品质量。
5.信息化管理信息化管理是一种以信息技术和管理相结合的管理方法,它可以帮助管理者更好地了解生产过程和产品质量状况,并及时地采取措施。
信息化管理的具体实践包括:生产跟踪系统、生产计划排程系统、质量管理系统、库存管理系统等。
通过信息化管理,可以提高生产效率、缩短生产周期和提高产品质量。
结论对于工厂现场的改进,应该采取多种方法相结合的方式,结合企业的实际情况加以实施。
标准化作业、5S管理、精益生产、人性化管理和信息化管理是一些有效的手段,可以提高生产效率、降低成本、提高产品质量和员工工作满意度。
工厂改善提案范文

工厂改善提案范文尊敬的领导:您好!我在咱这工厂里摸爬滚打也有段日子了,心里就一直琢磨着怎么能让咱这地方变得更好。
今天呢,就斗胆跟您提几个改善的小点子。
一、员工休息区的“大变身”咱们工人在车间里忙乎半天,休息的时候就想找个舒坦的地儿歇会儿。
可现在那休息区啊,真有点寒碜。
椅子破破烂烂的,坐着就跟坐针毡似的;桌子也晃晃悠悠,放杯水都怕它倒了。
我就想啊,咱能不能给换点新的桌椅呢?不用太高级,结实耐用就行。
然后再在休息区添个小冰箱,夏天的时候大家可以冰个汽水、放个冰棒啥的,那一口凉丝丝的,立马就能把干活的疲劳给赶跑一半。
还有啊,墙上可以挂个小电视,放点儿轻松的节目或者安全操作的小视频,大家一边休息一边看看,既能放松又能学习,多好的事儿。
二、工具管理得整整。
咱这工具啊,现在就像一群没爹没妈的孩子,到处乱放。
每次要用个工具,都得找半天,那时间就这么白白浪费了。
我建议啊,咱们专门做个工具墙,每个工具都有自己的“小窝”,还贴上标签,就像给每个工具都发了个身份证似的。
谁用完了就放回原处,这样找起来方便,也不容易丢。
而且,定期得有个人来检查检查工具的情况,看看有没有坏的,及时修或者换,不然到了用的时候才发现是坏的,那可就抓瞎了。
三、生产线上的小改进。
您看咱那生产线,有时候就像个老黄牛,慢慢吞吞的。
为啥呢?我发现有些工序其实可以合并或者简化。
比如说,有两个步骤,一个是先把零件擦干净,然后再检查有没有瑕疵。
其实啊,这擦的过程中就能顺便检查了,这样就能节省不少时间。
还有啊,有些机器设备的操作按钮位置不太合理。
工人操作的时候,得扭着身子、伸着胳膊,就跟跳奇怪的舞蹈似的,一天下来腰酸背痛的。
咱们能不能调整一下按钮的位置,让工人操作的时候更顺手呢?就像给机器做个“小手术”,让它变得更人性化。
四、员工培训来点新花样。
咱这员工培训,每次都是那老一套,在会议室里干巴巴地讲,大家听着听着就犯困。
我觉得啊,可以来点有趣的。
比如说,咱可以在车间里搞个小型的操作比赛,就像做游戏似的。
- 1、下载文档前请自行甄别文档内容的完整性,平台不提供额外的编辑、内容补充、找答案等附加服务。
- 2、"仅部分预览"的文档,不可在线预览部分如存在完整性等问题,可反馈申请退款(可完整预览的文档不适用该条件!)。
- 3、如文档侵犯您的权益,请联系客服反馈,我们会尽快为您处理(人工客服工作时间:9:00-18:30)。
现场改善Part8 内存治具升级改善
改善成员:吕稼辰、刘莹、汪旵正、敬向华
背景概述 新主板B250-N外形为L型,现有的治具无法适用。
改善前
图示
新主板外形示意图:
成果 缩短主板定位边,重新调整治具压合开关位置。
改善前
图示
总结
满足了新产品导入生产线。 提案评价:
现场改善Part9 包材滑道降噪改善
改善成员:夏岗 、刘莹、张俊杰、孙灿然
背景概述 包装箱直接撞击滑道底部,噪音较大。
改善前
图示
成果 制作降噪减震垫固定在滑道底部,减缓低了包材滑梯噪音,改善了现场作业环境。 提案评价:
现场改善Part10 包装组工作台改善
改善成员:孙国臣、刘莹、汪旵正、敬向华、黄永攀、董鹏
改善前
图示
总结
设备定置存放,提升使用寿命,改善现场6S。 提案评价:
知识回顾 Knowledge Review
祝您成功!
提案评价:
现场改善Part7 包装组外观工位增加检查镜
改善成员:李文 、杨芳、刘莹、董丽平
背景概述
机箱底部位于外观岗位作业员的对面位置,不方便外观检 查,存在外观不良未检出的风险。
改善前
图示
成果
在作业员对面安装检查镜,可提高检查效率、降低质量风 险。
改善前
图示
总结
提高了外观岗位的检查效率,降低质量风险。 提案评价:
改善成员:张寅、严芳、孙国臣、刘莹、李勇刚
背景概述
OQC作业员采用手动封箱和打包,劳动强度大,效率较 低。
改善前
图示
成果
设计制作精益管滚杠线并导入了自动封箱机、打包机,降 低了员工劳动强度,提升了OQC封箱打包效率。
改善前
图示
总结
1. 降低了员工劳动强度,提升了OQC封箱打包效率。 2. 提升了工厂自动化程度。
提案评价:
现场改善Part6 服务器工作垫改善
改善成员:张俊杰 、孙灿然、李勇刚、董丽平
背景概述
原服务器线工装垫破损严重,且高度较低,不利于伸手从 机箱底部进行搬运。
改善前
图示
成果
用防静电胶皮和黑色工装垫设计制作符合操作需要的工装 垫。
改善前
图示
总结
1. 降低了工装制作难度,从外购改成自制; 2. 方便产线搬运机箱操作,提升了生产效率。
现场改善Part3 抱主机工位胶带底座固定
改善成员:夏岗、孙国臣、敬向华、董丽平
背景概述
透明胶带座无固定位置放置在工作台面上,有划伤机箱的 隐患。
改善前
图示
成果
在略低于抱主机工作台面的位置设置左右两个胶带座固定 架以满足产线 工位调整。
改善前
图示
总结
消除了此工位胶带底座划伤主机的隐患。 提案评价:
现场改善Part4 包材二楼上料口安全改造
改善成员:孙国臣、刘莹、董丽平
背景概述 包材二楼上料口过大,护栏较低,存在安全隐患。
改善前
图示
成果
降低作业安全隐患: 1.缩小上料口(预留1.5个栈板位置); 2.重新用方管增高护栏。
改善前
图示
总结
降低了车间员工作业安全隐患。 提案评价:
现场改善Part5 OQC自动封箱机、打包机改造
现场改善Part1
包装组CPU标贴治具
改善成员:孙国臣、李勇刚、董丽平、杨芳
背景概述 CPU标贴无固定点存放,影响标贴拿取效率。
改善前
图示
成果
改善小组组织人员进行现场调研讨论, 设计制作出“治具+料箱+工作凳”三合一的治具。
改善前
图示
总结
改善措施不仅解决现有问题,同时优化了该各工位的工作 凳和物料存放架。
背景概述 原有的工作台使用周期长,破损严重,占地面积大。
改善前
图示
成果 用精益管制作工作台,适宜操作,占地面积小。
改善前
图示
总结
制作精益管工作台,有效地改善了包装现场工作环境。 提案评价:
现场改善Part11 包装组清洁工具架优化
改善成员:孙国臣、李勇刚、董丽平、敬向华
背景概述 原有的工具尺寸过大,占用现场位置过多,现场乱。
提案评价:
现场改善Part2 防静电手环存放点标识定位
改善成员:夏岗 、刘莹、敬向华、王金磊
背景概述
防静电手环闲置时,作业员直接把手环搭在线体上,影响 现场美观,同时会降低手环使用寿命。
改善前
图示
成果
在手环检测器附近统一设定固定存放点,固定磁环定位并 做出明显标识。
改善前
图示
总结
改善措施解决了现场6S问题,降低了设备成本。 提案评价:
改善前
图示
成果 重新设计制作,缩小架子占地面积,美化现场。
改善前
图示
总结
工具分类放置,改善现场6S。 提案评价:
现场改善Part12 电动改锥适配器固定治具
改善成员:孙国臣、刘莹、汪旵正。王金磊
背景概述 适配器散乱在地面,易摔坏,缩短使用寿命,影响现场6S。
改善前
图示
成果 导入治具固定存放适配器。