{品质管理八D方法}8D报告讲义PPT57页
合集下载
{品质管理八D方法}8D报告案例PPT78页
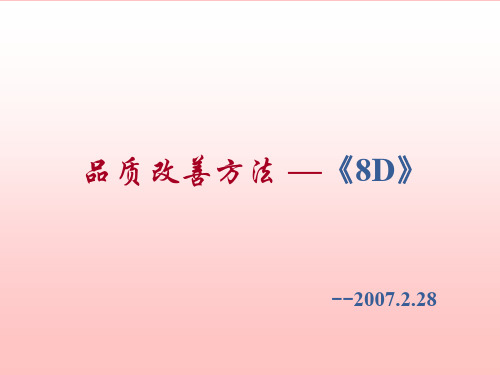
阅附图.该图虽已列出解决问题的各个步骤,但各 个步骤的先后順序可视问题的困难度及复杂程度 而异,不必拘泥于图示順序.且问题解决经过应有书 面记录. • 如:某一问题发生及团队组成时,可能制造人员已 经先行采取临时对策,惟其永久解决方案,则可能尚 需小组人员的共同参与,经多方研讨后才能产生。
了解問題
• 对现有生产、贮存、出货的20μMHT机用膜进行全数检验。 (许丽 完成日期99/11/05)
D4.识别并验证根本原因
问题提出
成立小组
问题描述
验证永久纠正措施
制订永久纠正措施
制订、执行围堵措施
预防再发生
祝贺结 案,肯定小组贡献
寻找根本原因
8D—问题改善手法 案例说明
案例1:
S公司为顾客制造零件A;根据顾客的工程规范,零件 A上必须镀银,否则顾客的产品无法完成规定功能。有一 天,他们收到顾客工厂发来的问题点如下:
D4、通过失效树(FTA)的方法确定根本原因
顾客零件没有电镀的抱怨
没有电镀 生产线停止 电路断开 电线接口松动 根本原因1
没有检验
操作者不按程 序及作业指导
书实施
没有安装 防错系统
操作者培训 不足
主管对问题 没有评审
根本原因2
D4、通过失效树(FTA)的方法确定根本原因
2.第一个根本原因是电线和电路接触器之间的连接点松动。 2.1 电镀的机制请见图-1 1) 喷银器和后板紧紧压住L/F以使银能被镀在正确的位置。 2) 电路接触器被关闭,开始工作。 3) 银液被从银槽泵到喷银器。 4) 整流器打开,银镀到L/F上。 2.2.由于电镀的电路因为连接点松动而断开,导致镀银没有实施。
了解問題
• 对现有生产、贮存、出货的20μMHT机用膜进行全数检验。 (许丽 完成日期99/11/05)
D4.识别并验证根本原因
问题提出
成立小组
问题描述
验证永久纠正措施
制订永久纠正措施
制订、执行围堵措施
预防再发生
祝贺结 案,肯定小组贡献
寻找根本原因
8D—问题改善手法 案例说明
案例1:
S公司为顾客制造零件A;根据顾客的工程规范,零件 A上必须镀银,否则顾客的产品无法完成规定功能。有一 天,他们收到顾客工厂发来的问题点如下:
D4、通过失效树(FTA)的方法确定根本原因
顾客零件没有电镀的抱怨
没有电镀 生产线停止 电路断开 电线接口松动 根本原因1
没有检验
操作者不按程 序及作业指导
书实施
没有安装 防错系统
操作者培训 不足
主管对问题 没有评审
根本原因2
D4、通过失效树(FTA)的方法确定根本原因
2.第一个根本原因是电线和电路接触器之间的连接点松动。 2.1 电镀的机制请见图-1 1) 喷银器和后板紧紧压住L/F以使银能被镀在正确的位置。 2) 电路接触器被关闭,开始工作。 3) 银液被从银槽泵到喷银器。 4) 整流器打开,银镀到L/F上。 2.2.由于电镀的电路因为连接点松动而断开,导致镀银没有实施。
8D报告培训资料ppt课件

已采取什么措施防止以后不生产不合格品?
考虑 措施
* 防错,试验,过程控制 负责人 部门
时间
7 对策确认 对策已经确认是有效的吗? 如何确认?
是
否
Hale Waihona Puke 请附上相关数据,如:尺寸测量结果,过程能力,特性数据等
8 跟踪措施—水平展开 该重大问题的结果是否按以下项目进行追踪?
考虑: 工序作业/检查指导书 过程流程图 质量保证标准
禁止暗示原因 禁止直接给出措施
再发?
是否
分析工具:排列图、趋势图等
What :什么材料发生异常?Lot NO.? Who :谁发现的?谁导致异常发生? Where:在什么地点发现? When :何时发生?此问题是否为第一次发生? Why :为什么会发生此异常? How :问题是如何发生的?问题的大小和广度?
D7
D8
预防措施 团队庆祝
8D问题解决流程
D1 D2 D3 D4
选择团队 建立跨部门,跨学科的问题解决团队。团队成员应具
备有效解决问题所需的专业技能和权限。
小组成员由具备相关技术知识的生产工程师和质量工程师组成, 避免仅有一两个人在实施该过程。
定义问题 应包括两部分:1.描述客户到底说了什么?
2.描述工程师或专家对问题的意见?
※描述不良发生的背景 ※确定不良发生的统计数据 ※使用顾客明白的术语叙述
投入数/不良数/不良率 从客户的角度/观点出发陈述问题
一个有效的问题描述是 具体的 它明确地解释了有什么不对,并从类似的问题中找出不足; 可观察的 它描述了问题的可见迹象; 可测量的 它描述了“多少”或“多少频度”,以定量的术语指明了问题的范围。 可控制的 一个可控制的问题是一个可以在一定期限内解决的问题。如果一个问题太大,它应被 分解成几个更小的可控制的问题。
8D报告讲解 ppt课件
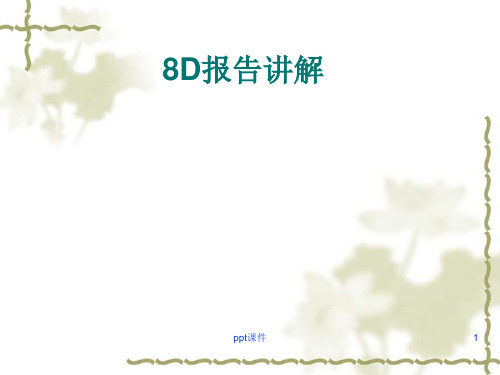
此方式宜由公司各部门人员的共同投入,求 得创造性及永久性的解决方案。
此方式可适用于任何问题,而且能促进相关目 标的各部门间有效的沟通。
ppt课件
3
何謂8D
所谓“八个步骤”,其每个步骤意义及其流程请参阅 附图.该图虽已列出解决问题的各个步骤,但各个步 骤的先后順序可视问题的困难度及复杂程度而异,不 必拘泥于图示順序.且问题解决经过应有书面记录.
如:某一问题发生及团队组成时,可能制造人员已经 先行采取临时对策,惟其永久解决方案,则可能尚需 小组人员的共同参与,经多方研讨后才能产生。
ppt课件
4
Hale Waihona Puke 8D 精神面对问题不可以各自
面对问题应群策群
为政、自我本位主义,否 力,互相帮助、相互提
则将无法有效解决问题。 拔、如此才能彻底解决
问题。
ppt课件
E-mail
lpz@
Activity QA engineer
Team Members
黎卓华 李连明 阳耀翠
李培贞( SS QA)
Corrective Action Report (CAR)
Date Opened: 6-Aug-07 Next Status Due Date:
因为有问题的按键不稳定,按键合格的时候检查员会判定为OK。
(5) CORRECTIVE ACTIONS (纠正措施)
Interim Actions:
(暂定对策)
Responsible Person
TARGET DATE
EFFECTIVE (6) VERIFICATION
DATE
METHODS
生产线禁止使用外观水清洁PCB铜箔接触点后立刻贴保护膜。
此方式可适用于任何问题,而且能促进相关目 标的各部门间有效的沟通。
ppt课件
3
何謂8D
所谓“八个步骤”,其每个步骤意义及其流程请参阅 附图.该图虽已列出解决问题的各个步骤,但各个步 骤的先后順序可视问题的困难度及复杂程度而异,不 必拘泥于图示順序.且问题解决经过应有书面记录.
如:某一问题发生及团队组成时,可能制造人员已经 先行采取临时对策,惟其永久解决方案,则可能尚需 小组人员的共同参与,经多方研讨后才能产生。
ppt课件
4
Hale Waihona Puke 8D 精神面对问题不可以各自
面对问题应群策群
为政、自我本位主义,否 力,互相帮助、相互提
则将无法有效解决问题。 拔、如此才能彻底解决
问题。
ppt课件
lpz@
Activity QA engineer
Team Members
黎卓华 李连明 阳耀翠
李培贞( SS QA)
Corrective Action Report (CAR)
Date Opened: 6-Aug-07 Next Status Due Date:
因为有问题的按键不稳定,按键合格的时候检查员会判定为OK。
(5) CORRECTIVE ACTIONS (纠正措施)
Interim Actions:
(暂定对策)
Responsible Person
TARGET DATE
EFFECTIVE (6) VERIFICATION
DATE
METHODS
生产线禁止使用外观水清洁PCB铜箔接触点后立刻贴保护膜。
8D报告品质PPT课件

最新课件
13
1. 设备线路定期检查维护确保设备正常生产:OK
生产工艺方法 漏失:NG
Method
故障(设备 运行):NG
Machine
设备故障 报警:OK
设备周期性 保养:OK
设备运行 信号:OK
Measure
浙江同泽新材料有限公司 最新课件
6
D4.2: 鱼刺图原因剖析
(5M1E)
可能问题点汇总
A: 投料时分散轴未开,导致粉料积聚 成团。
1. 投料时分散轴未开,导致 粉料积聚成团。MAY
2.包装时过没有经过滤网过
。 滤 (缸壁粉团结块/
吸尘器管道粉团坠落)MAY
1. 生产过程中按 规定作业,严 格管控。:NG (生产过程)
2.包装清桶时按 规定作业.NG (生产过程)
生产工艺按 要求作业: NG
设备故障紧急预案中未 注明此问题要求要:NG
品质事故报告 8D Report
浙江同泽新材料有限公司 最新课件
品质部:张军 日期:14.6.2 制作:谭冬平
1
D0:发生时间线
(Time-Line)
2014.6.13日接到新疆 &嘉兴分厂品质反馈:产品在生 产过程中发现有粉团结块状.从 而导致分厂在生产过程中喷枪堵塞 现象,给分公司造成了生产不便, 也给公司造成了不良影响.
(5M1E)
Environment
操作平台是否有大量残留 AL{OH}3粉尘为清理干净导致: NG
Material AL(OH)3原料是否有块状 NG
Man
操作人员未按作业 规范作业:MAY
操作平台: 投料未投干净,散落平台。洒 落包装桶。:NG(投料过程)
1. 原料进料抽样细度未发现异 常:OK
8D报告以及案例分析PPT课件

D1:成立处理团队
挑选并登录内部及外部小组成员 (Compaq的物料工程人员及供货商 的业务代表为外部小组成员).
挑选小组捍卫者(应由能排除小组工作 障碍的管理阶层人员担当).
挑选小组长(应为能直接投入问题处理 并承当小组责任的人).
需要供货商,客户加入团队吗 ?
8D
这些队员分别担当什么任务 ? 撰写8D之前,小组成员开会了吗 ? 采取脑力激荡来解决问题吗 ? 推敲人员的能力 - 不是有人就好
2.1 查最近冲压修模记录发觉, 11/14,2k曾因箭头模糊而将冲子高度垫高0.03mm. 确认冲子的
01 字模设计高度为0.10mm, (以下图,spec 0.10+/-0.05mm), 目前已磨损至0.07mm. 对应生产出
来的字模高度亦由本来的0.06mm降至0.03mm.故当冲压换料或调机时, 以手动方式送料, 此时 冲子可能没法完全压到下死点, 因此即会有箭头未冲出之零件产生.
8D
D6:成效验证
01
验证紧急计策及 永久计策之有效 性,应以量化表示 验证结果(如: Cpk值可达1.33, 或不良产生率降
至 0 等).
02
在永久计策 验证有效之 前,应连续进 行紧急计策.
03
追踪永久计 策实行后之 品质推移状
态
04
在没有完全掌 控问题已彻底 解决之前 , 不 要草率的结案 .
Problem description Containment plan
Describe the cause
成效验证
避免再发
恭喜你的 团队
Permanent C/A plan
Verification of effectiveness
8D报告培训教材(经典) ppt课件
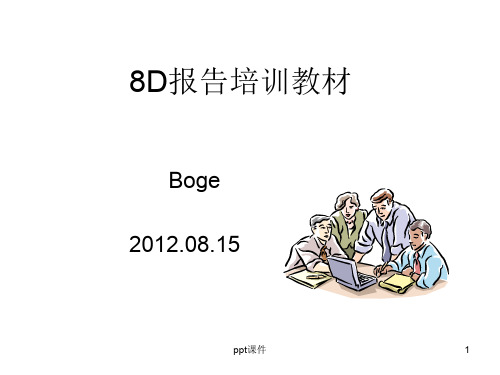
ppt课件
25
四. 8D步骤—D5长期对策
选取最佳的的长期对策来解决根本原因。 同时也选取最佳的长期对策来控制根本原 因的影响。
需要考虑的问题:
1. 一定是针对根本原 因来制定措施,一个 原因可能有几条措施。
2.必要时对已 经明确的措 施进行验证。
ppt课件
3.措施 尽量具 体化。
26
四. 8D步骤—D6预防再发对策
有历史数据的对数据
疑
进行初步分析
点
验
关键原因确认
证
统计分析
DOE验证
机理分析
质量问题5M1E分析
(鱼翅图分析)
ppt课件
关键原因-是否为根本原因
5-WHY分析
20
四. 8D步骤—D4原因分析
鱼骨图分析
手工喷涂
员工品质意识淡薄
标准执行 力差
人员变动大
输送链台车 漆渣太厚
素材表面 要打磨
喷涂房 环境差
ppt课件
4
一.什么是8D
此方法以团队运作导 向以事实为基础,避 免个人主见之介入, 使问题之解决能更具 条理。
面对问题应群策群力, 互相帮助、相互提拔、 如此才能彻底解决问题。
ppt课件
5
二.为什么要推行8D
通过建立小组训练内部合作的技 巧。
提供问题有效解决的方法。
防止相同或类似问题的再发生。
4W
WHY 中间原因
5W
WHY 根本原因23
四. 8D步骤—D4原因分析
5-WHY分析案例1 状态1 一辆汽车出了故障不能行驶(WHY1)
状态2-原因1 引擎故障(WHY2)
状态3-原因2
火花塞不点火(WHY3)
{品质管理八D方法}8DTRAINING培训讲义PPT85页

• 按时开始和结束 • 迅速选择角色 • 公开工作 • 帮助组长 • 其它(头脑风暴,每人至少一个观点)
8D 步驟
D0
准备
D1
建立团队
D2
问题描述
D3
制定实施临时措施(ICA)
D4
确定根本原因和失控点
D5
选择并验证PCA
D6
实施并确认PCA
D7
防止再发生
D8
认可贡献、庆祝胜利
D2 目的
• 通过下面的技术描述内部/外部问题
问题陈述——第二步
• 一旦确定了对象和缺陷,第二步就是问“为什 么缺陷发生在这个对象身上?”
• 精炼陈述为了
– 努力集中于只有一个根本原因的简单问题 – 利用现有的数据尽可能地接近根本原因 – 检查问题的根因是否未知
• 一遍一遍重复“为什么缺陷发生在这个对象身 上?”称为重复为什么
– 连续询问直至无答案为止
8D
2008-2-27
什么是8D?
8D(8 Disciplines of Problem Solving),是解决问题的8个步 骤,是在问题原因不确定时,运 用特定的系统过程推动问题的根 本解决。
8D 步驟
D0
准备
D1
建立团队
D2
问题描述
D3
制定实施临时措施(A)
D4
确定根本原因和失控点
• 职责类别:
– 组长 – 时间管理 – 板书 – 记录
组长
• 小组管理者 • 小组发言人 • 与小组一起工作,设定目标和任务 • 收集并概括成员的意见 • 指导使用8D方法 • 集中关注会议的目的和议程 • 可以向小组提供各种信息 • 指导确定结论 • 概括结论 • 成立子组 • 参加讨论时放弃领导的 角色
8D 步驟
D0
准备
D1
建立团队
D2
问题描述
D3
制定实施临时措施(ICA)
D4
确定根本原因和失控点
D5
选择并验证PCA
D6
实施并确认PCA
D7
防止再发生
D8
认可贡献、庆祝胜利
D2 目的
• 通过下面的技术描述内部/外部问题
问题陈述——第二步
• 一旦确定了对象和缺陷,第二步就是问“为什 么缺陷发生在这个对象身上?”
• 精炼陈述为了
– 努力集中于只有一个根本原因的简单问题 – 利用现有的数据尽可能地接近根本原因 – 检查问题的根因是否未知
• 一遍一遍重复“为什么缺陷发生在这个对象身 上?”称为重复为什么
– 连续询问直至无答案为止
8D
2008-2-27
什么是8D?
8D(8 Disciplines of Problem Solving),是解决问题的8个步 骤,是在问题原因不确定时,运 用特定的系统过程推动问题的根 本解决。
8D 步驟
D0
准备
D1
建立团队
D2
问题描述
D3
制定实施临时措施(A)
D4
确定根本原因和失控点
• 职责类别:
– 组长 – 时间管理 – 板书 – 记录
组长
• 小组管理者 • 小组发言人 • 与小组一起工作,设定目标和任务 • 收集并概括成员的意见 • 指导使用8D方法 • 集中关注会议的目的和议程 • 可以向小组提供各种信息 • 指导确定结论 • 概括结论 • 成立子组 • 参加讨论时放弃领导的 角色
品质部培训8D课程PPT培训课件

实施永久措施
总结词
制定并实施永久措施,从根本上解决问题, 防止问题再次发生。
详细描述
在8D方法实施流程中,实施永久措施是为 了从根本上解决问题,防止问题再次发生。 这些措施应该是经过深思熟虑和充分验证的, 具有长期性和稳定性。在实施永久措施的过 程中,团队需要密切关注措施的效果,及时 调整和完善,以确保问题得到彻底解决。
详细描述
在8D方法实施流程中,实施临时措施是为了控制问题的进一步发展,减轻其对产品、过程和客户的影 响。这些措施通常是紧急的、临时的,旨在稳定局势,为后续的深入分析和改进提供基础。
确定并验证根本原因
总结词
深入分析问题,找出根本原因,为制定 永久措施提供依据。
VS
详细描述
在8D方法实施流程中,确定并验证根本 原因是关键的一步。团队需要运用科学的 方法和工具,对问题的根本原因进行深入 分析,并对其进行验证。只有确定了问题 的根本原因,才能制定出有效的永久措施 ,从根本上解决问题。
04
8D方法应用案例分析
应用案例一:汽车行业中的8D方法应用
总结词
广泛采用、标准化流程
VS
详细描述
汽车行业是8D方法应用最为广泛的领域 之一。各大汽车制造商采用8D方法来解 决生产过程中出现的各种质量问题,确保 产品的一致性和可靠性。通过标准化流程 ,8D方法在汽车行业中实现了高效的问 题解决和持续的质量改进。
02
8D方法实施流程
成立专项团队
总结词
组建跨部门、跨领域的团队,确保问题解决的有效性和效率。
详细描述
在8D方法实施流程中,第一步是成立一个由不同部门和领域专家组成的专项团 队,以确保问题解决的全面性和专业性。这个团队应该具备丰富的经验和技能, 能够针对不同的问题进行深入分析和有效解决。
{品质管理八D方法}8D管理模式讲义ppt54页

• 以魚骨圖為架構,用腦力激盪的方式找出可 能的原因(POTENTIAL ROOT CAUSES)
• 以5WHY 深入追蹤直到分析出真正原因 (ROOT CAUSE)
• 儘可能以實際模擬的方式+數據圖表驗證真 正的原因.
Page 35 of 111
常用原因解析手法
魚骨圖
MATERIAL(因 1)
8D 的本質: 問題解決程序
當我們觀察到 或發現………時
這現象是否正常 跟標準或目標比較的差 異(偏離程度) 其差異是否不該在
為什麼會發生異常 ?
如何改善異常 ? 如何控制發生異 常的 原因 ?
現
象
確認並定義問題
例如: 人員出勤率93%
WHAT, WHEN, WHERE, WHO, WHY,
HOW, HOW MUCH
時間 地點 產品類型 作業人員 原材料 機器 方法 相關條件 環境 計劃
Page 32 of 111
D3:Develop Containment Action (暫時改善措施)
• 以 P-D-C-A 循環的方法暫時執行.執行過 程中要確認ICA的效果(例如PPM顯著降 低,CPK, YIELD顯著提升, 避免問題再 發生,直到永久改善行動完成為止就可以 功成身退.
Page 19 of 111
PDCA 與 SDCA
屬於兵力的提昇 (提昇製程的能力)
AP CD
AP CD
AS CD
AS CD
屬於兵力的維持 (將製程穩定化)Page 20 of 111
PDCA , CA-PDCA 與 SDCA
AP CD
AS CD
(+)
GAP
Analysis
• 以5WHY 深入追蹤直到分析出真正原因 (ROOT CAUSE)
• 儘可能以實際模擬的方式+數據圖表驗證真 正的原因.
Page 35 of 111
常用原因解析手法
魚骨圖
MATERIAL(因 1)
8D 的本質: 問題解決程序
當我們觀察到 或發現………時
這現象是否正常 跟標準或目標比較的差 異(偏離程度) 其差異是否不該在
為什麼會發生異常 ?
如何改善異常 ? 如何控制發生異 常的 原因 ?
現
象
確認並定義問題
例如: 人員出勤率93%
WHAT, WHEN, WHERE, WHO, WHY,
HOW, HOW MUCH
時間 地點 產品類型 作業人員 原材料 機器 方法 相關條件 環境 計劃
Page 32 of 111
D3:Develop Containment Action (暫時改善措施)
• 以 P-D-C-A 循環的方法暫時執行.執行過 程中要確認ICA的效果(例如PPM顯著降 低,CPK, YIELD顯著提升, 避免問題再 發生,直到永久改善行動完成為止就可以 功成身退.
Page 19 of 111
PDCA 與 SDCA
屬於兵力的提昇 (提昇製程的能力)
AP CD
AP CD
AS CD
AS CD
屬於兵力的維持 (將製程穩定化)Page 20 of 111
PDCA , CA-PDCA 與 SDCA
AP CD
AS CD
(+)
GAP
Analysis
8D培训教材 ppt课件

8D简介
QC七大手法
机理分析法
FMEA
统计过程控制
以上4种也是质量工具,后续会有专业的同仁授课,敬请期待~。
8D简介
D5 长期对策
当根本原因找出后,长期对策往往应运而生,但是如何针对性的制定最佳改善对策,以避免问 题再发,仍需要整个团队讨论决议。
值得注意的是一个原因可能有几条措施,同步实施时需要保障解决最根本问题的措施务必被贯 彻落实。
8D简介
D4 根因探究: 寻真因如求医问诊,误诊或诊断不全,后患无穷。 1.不良解析 解析即要求对不良现象的充分了解,包括其历史背景,弄清不良的特性(外观? 性能?)和规格(国标?安全?)。 2.排定可能原因 2.1 如有历史数据,统计分析观察集中性、趋势性。 2.2 与一线员工充分沟通,如有可能现时、现地、现物 2.3 向相关专家咨询请教,推敲问题可能造成的原因 3.验证可疑原因 选用合适的方法找出根本原因
1
装配 合格
150mA
60s
焊穿
B
2
不合格
150mA
50s
合格
A
2
合格
B
1
不合格
在这组实验中,我们优先固定1组参数,另一组取其 上下限进行实验,当两者都超出我们的要求时,选 取中值达到要求。
我们仍可以进行其他组合实验,但实际情况中,我 们总会有一定的倾向,可以缩减排列组合数量。 比如自产能考量,我们会优先选择焊接速度40s不变, 调整焊接电流来达到我们要的结果。
交叉实验法是在已知不合格状态下,通过单因素变动 寻找不良再现。上组实验中A外壳无论搭配内胆1还是2 都是合格状态,但B外壳无论搭配内胆1和2都是不合格 状态,不良嫌疑集中在B外壳。 注意:当实验进行到A+2合格时,并不能完全判定B外
品质管理八D方法8D报告起源及运用ppt47页
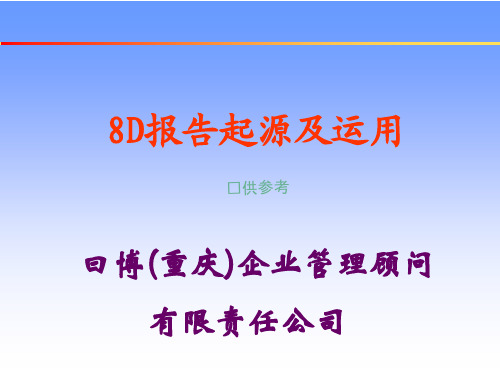
紧急反应计划可能很难用测量验证,因为它是以常 识为基础。例如,如果将受到影响的产品停止发运, 那么顾客就不会再经历症状。
1D现象描述和准备
紧急反应计划的执行和证实: 选择和验证并执行了紧急反应计划后,必须证 实紧急反应计划能够起作用。证实就是提供正 在进行中的证据证明紧急反应计划达到了目的 并且没有引起新的问供题参考。 到达顾客前的证实: 试验 检测 观察 关于产品和过程的检测 顾客证实包括顾客反馈。
6D 预防措施(管理、技术) 修改必需的系统包括政策、程序、图纸等 来防止同一或相似问题的再发生。
7D责任落实和表彰 供参考 落实相关供应商、内部责任人的责任,并 根据情况表彰小组和个人的贡献。
8D关闭确认和总结。 总结本次改进活动过程中的经验,找出遗 留问题。
1D需填写的内容
表头内容: 主题 产品型号/过程名称 状态:开发、样件供、参小考 批、批量等 重要度 公司或部门 小组或负责人 启用日期
3D 开发临时纠正措施
第三步:执行临时纠正措施 执行临时纠正措施的重要部分是计划怎样执行临时纠 正措施。
第四步:证实临时纠正措施 执行临时纠正措施后,需要进行证实。证实用来证明 临时纠正措施满足要求供并参且考没有产生新的问题。 证实有两种形式: 到达顾客前证实。在暴露给顾客前和成功验证之后, 证明行动在起作用的证实。包括试验、观测、和其 它质量检测。 顾客证实。来自于顾客的证明临时纠正措施正在起 作用的证实。
1D需填写的内容
1D: 现象(事实) 发生件数(故障件与总数的比例) 发生的状况(发生场所如山区平地海边、季
节、使用状况、是否新供的参产考品等) 应急反映计划 实施人/日期 确认及有效性检查 检查人/日期
1D现象描述和准备
为什么准确描述和准备8D过程
8D报告知识培训ppt课件
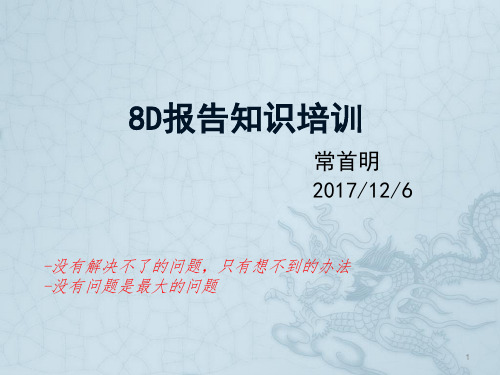
执行永久性的纠正措施,并监视其长期效果
11
8、 D7:预防再发生标准化
目的:修改现有的管理系统、操作系统、工作惯例、设计与规程以防 止这一问题与所有类似问题重复发生。 关键要点:选择预防措施;验证有效性;决策 ;组织、人员、设备、环境、 材料、文件重新确定
修正必要的系统,包括方针、运作方式、 程序,将永久对策标准 化,写入文件之中。以避免此问题及类似问题的再次发生。必要时, 要提出针对体系本身改善的建议。
FMEA
严重度(S)、频率(O)、侦测度(D)
5
2、 D1:小组成立
目的:成立一个小组,小组成员具备工艺/产品的知识,有配给的时间并授予 了权限,同时应具有所要求的能解决问题和实施纠正措施的技术素质。小组 必须有一个指导和小组长。
关键要点: 成员资格,具备工艺、产品的知识;目标 ;分工 ;程序 ;小组建设
8D报告知识培训
常首明 2017/12/6
-没有解决不了的问题,只有想不到的办法 -没有问题是最大的问题
1
➢ 8D分析手法 ➢ 8D工作方法 ➢ 适用范围 ➢ 案例分析 ➢ 解释:鱼骨图、5W1H 分析法
2
一、 8D分析手法
8D又称团队导向问题解决方法、8D问题求解法是福特公司处 理问题的一种方法,它提供了一套符合逻辑的解决问题的方法, 同时对于统计制程管制与实际的品质提升架起了一座桥梁。8D最 早是美国福特公司使用的经典质量问题分析手法。
确保 D4 问题不会再次发生的后续行动方案,如人员教育训练、改 善案例分享、作业标准化等
12
9、 D8:小组祝贺
目的:承认小组的集体努力,对小组工作进行总结并祝贺。 关键要点: 有选择的保留重要文档;流览小组工作,将心得形成文件;了 解小组对解决问题的集体力量,及对解决问题作出的贡献;必要的物质、 精神奖励
11
8、 D7:预防再发生标准化
目的:修改现有的管理系统、操作系统、工作惯例、设计与规程以防 止这一问题与所有类似问题重复发生。 关键要点:选择预防措施;验证有效性;决策 ;组织、人员、设备、环境、 材料、文件重新确定
修正必要的系统,包括方针、运作方式、 程序,将永久对策标准 化,写入文件之中。以避免此问题及类似问题的再次发生。必要时, 要提出针对体系本身改善的建议。
FMEA
严重度(S)、频率(O)、侦测度(D)
5
2、 D1:小组成立
目的:成立一个小组,小组成员具备工艺/产品的知识,有配给的时间并授予 了权限,同时应具有所要求的能解决问题和实施纠正措施的技术素质。小组 必须有一个指导和小组长。
关键要点: 成员资格,具备工艺、产品的知识;目标 ;分工 ;程序 ;小组建设
8D报告知识培训
常首明 2017/12/6
-没有解决不了的问题,只有想不到的办法 -没有问题是最大的问题
1
➢ 8D分析手法 ➢ 8D工作方法 ➢ 适用范围 ➢ 案例分析 ➢ 解释:鱼骨图、5W1H 分析法
2
一、 8D分析手法
8D又称团队导向问题解决方法、8D问题求解法是福特公司处 理问题的一种方法,它提供了一套符合逻辑的解决问题的方法, 同时对于统计制程管制与实际的品质提升架起了一座桥梁。8D最 早是美国福特公司使用的经典质量问题分析手法。
确保 D4 问题不会再次发生的后续行动方案,如人员教育训练、改 善案例分享、作业标准化等
12
9、 D8:小组祝贺
目的:承认小组的集体努力,对小组工作进行总结并祝贺。 关键要点: 有选择的保留重要文档;流览小组工作,将心得形成文件;了 解小组对解决问题的集体力量,及对解决问题作出的贡献;必要的物质、 精神奖励
8D报告-8d报告.ppt

• 临时措施一直要持续实施至后续的永久对策的执行有 效后,方可撤消。
• 临时措施实施中,应及时跟踪和验证其效果。
四. 8D步骤—D3临时对策
纠正(对策或临时措施)
为消除已发现的不合格而采取的措施。
纠正措施(对策)
为消除已发现的不合格或其它不期望情况的原因所采取 的措施。
预防措施(预防再发对策)
为消除潜在不合格或其它潜在不期望情况的原因所采取 的措施。
一.什么是8D
此方法以团队运作导 向以事实为基础,避 免个人主见之介入, 使问题之解决能更具 条理。
面对问题应群策群力, 互相帮助、相互提拔、 如此才能彻底解决问题。
3
二.为什么要推行8D
三. 何时采用8D
重复发生,一直没有解决的问题 比较重大的制程品质问题 客户要求回复的品质投诉
何时 采用 8D
四. 8D步骤-D7效果确认及标准化
验证预防再发对策并监控长期的效果。 水平展开,以防同一问题及类似问题再 度发生。将相关对策形成书面文件(管 理制度、程序文件、作业指导书、表单、 技术文件、工程图纸等)。
四. 8D步骤-D7效果确认及标准化
效果确认 实事求是,以事实和数据为依据,对数据用统计工具处 理后得出相应的结论,不应未做对比分析即判定效果。
对小组的效益进行沟通和文件化
四. 8D步骤
注意事项 上述各项步骤,不一定必须完全依序进行,各步骤之顺 序可因个别问题而异。
五.8D改善案例
D0:发生时间线
(Time-Line)
12/08 8:25 动力运行金晓 栋从5#动力栋 赶至2#1F现场
12/08 8:31
12/08 8:32
动力运行金晓栋 金晓栋与曹健东手
临时措施(对策)
• 临时措施实施中,应及时跟踪和验证其效果。
四. 8D步骤—D3临时对策
纠正(对策或临时措施)
为消除已发现的不合格而采取的措施。
纠正措施(对策)
为消除已发现的不合格或其它不期望情况的原因所采取 的措施。
预防措施(预防再发对策)
为消除潜在不合格或其它潜在不期望情况的原因所采取 的措施。
一.什么是8D
此方法以团队运作导 向以事实为基础,避 免个人主见之介入, 使问题之解决能更具 条理。
面对问题应群策群力, 互相帮助、相互提拔、 如此才能彻底解决问题。
3
二.为什么要推行8D
三. 何时采用8D
重复发生,一直没有解决的问题 比较重大的制程品质问题 客户要求回复的品质投诉
何时 采用 8D
四. 8D步骤-D7效果确认及标准化
验证预防再发对策并监控长期的效果。 水平展开,以防同一问题及类似问题再 度发生。将相关对策形成书面文件(管 理制度、程序文件、作业指导书、表单、 技术文件、工程图纸等)。
四. 8D步骤-D7效果确认及标准化
效果确认 实事求是,以事实和数据为依据,对数据用统计工具处 理后得出相应的结论,不应未做对比分析即判定效果。
对小组的效益进行沟通和文件化
四. 8D步骤
注意事项 上述各项步骤,不一定必须完全依序进行,各步骤之顺 序可因个别问题而异。
五.8D改善案例
D0:发生时间线
(Time-Line)
12/08 8:25 动力运行金晓 栋从5#动力栋 赶至2#1F现场
12/08 8:31
12/08 8:32
动力运行金晓栋 金晓栋与曹健东手
临时措施(对策)
8D推行管理知识.ppt (报告篇)
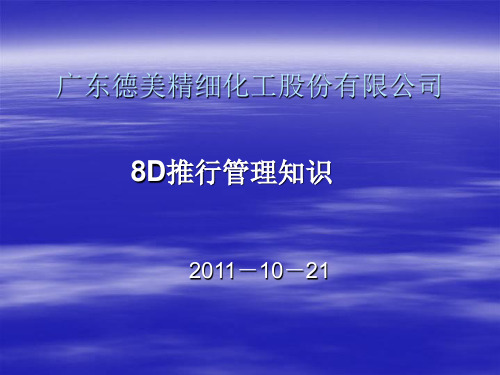
8D推行具体步骤 8D推行具体步骤 D4-第四步骤: 找出问题真正原因 D4-第四步骤:
1)从问题描述中寻找最有可能的一些原因,若有可能,做一些测试帮助 1)从问题描述中寻找最有可能的一些原因,若有可能, 寻找原因. 寻找原因. 2)检查所有考虑到的可能原因, 将它们会带来的结果与观察到的结果 2)检查所有考虑到的可能原因, 比较, 原因/结果矩阵图可帮助选择优先考虑哪个原因. 比较, 原因/结果矩阵图可帮助选择优先考虑哪个原因. 3)识别问题的种类.(设计,程序,制程,材料,人员技巧 3)识别问题的种类.(设计,程序,制程,材料, 4)探寻可能的解决方案,列出可行性,效果,实施时间等. 4)探寻可能的解决方案,列出可行性,效果,实施时间等. 5)建立将要实施的那些措施的检验标准. 5)建立将要实施的那些措施的检验标准. 6)尽量利用各种图表 6)尽量利用各种图表 找问题真正原因时,最好不要盲目地动手改变目前的生产状态,先动 动脑。您第一件事是要先观察、分析、比较。列出您所知道的所有生 产条件(即鱼骨图) 产条件(即鱼骨图),逐一观察,看看是否有些条件走样,还是最近有 些什么异动?换了夹具吗?换了作业员?换了供应商?换了运输商? 些什么异动?换了夹具吗?换了作业员?换了供应商?换了运输商?修过 电源供应器?流程改过? 电源供应器?流程改过? 或比较良品与不良品的检查结果,看看那个 数据有很大的差?,尺寸?重量?电压值?CPK?耐电压? 数据有很大的差?,尺寸?重量?电压值?CPK?耐电压?等等不良的发 生,总是有原因,资料分析常常可以看出蛛丝马迹。这样的分析,可 以帮助您缩小范围,越来越接近问题核心。当分析完成,列出您认为 最有可能的几项,再逐一动手作些调整改变,并且观察那一些改变可 使品质回复正常及影响变异的程度,进而找到问题真正的原因。这就 是著名田口式方法最简单而实际的运用。
- 1、下载文档前请自行甄别文档内容的完整性,平台不提供额外的编辑、内容补充、找答案等附加服务。
- 2、"仅部分预览"的文档,不可在线预览部分如存在完整性等问题,可反馈申请退款(可完整预览的文档不适用该条件!)。
- 3、如文档侵犯您的权益,请联系客服反馈,我们会尽快为您处理(人工客服工作时间:9:00-18:30)。
按需要调整 团队成员
四. 8D步骤—D2问题描述
以客户的角度和观点详细描述其所感受到的问题现象, 将所遭遇的问题,以量化的方式,明确出所涉及的人, 事,时,地,为何,如何,多少。
什么是问题???
问期题望
期望 目标
现实
四. 8D步骤—D2问题描述
问题描述方法:5W/2H
WHO
WHAT
WHEN WHERE WHY HOW
5W2H 谁
什么
何时 何地 为什么 怎么样
解释 识别那一个客户(内/外部)在抱怨 问题的症状,无法用文字描述清楚的,借助 于数字或图片将问题表达清楚
记入问题发生的日期 记入问题发生的场所 识别已知的解释 在什么的模式或状态这问题会发生
HOW MUCH
什么程度 问题发生的程度、量
13
四. 8D步骤—D3临时对策
四. 8D步骤—D3临时对策
临时措施与长期措施的区别
临时措施
消除问题及后果
只能治标 (可能再发)
长期措施
消除问题原因
可以治本 (不会再发)
四. 8D步骤—D4原因分析
用统计工具列出可以用来解释问题起因的所 有潜在原因,再分别针对每一可能原因予以 测试,最终确定产生问题的根本原因。
需要考虑的问题:
8D报告培训教材(经典)
Possible 2016.11.09
课堂纪律
1. 手机请关机或调成静音。 2. 请保持课堂安静,请勿交头接耳或大声讲话。 3. 如有问题请会后交流 。
一.什么是8D 二.为什么要推行8D 三.何时采用8D 四.8D步骤 五. 8D改善案例 六.八D报告经典案例
目录
一.什么是8D
1.列可能 原因时要 周全。
2. 原因和结 果要有论证, 说得通。
3.原因一定是根本 原因,而非表面 原因。
四. 8D步骤—D4原因分析
深入明 确问题
团队协 作: 列出所 有可能 的疑点
进一步明确问题 (不良解析)
从流程分析 (流程图)
质量问题5M1E分析 (鱼翅图分析)
各个可疑原因排查
对现场人机料环法
三. 何时采用8D
重复发生,一直没有解决的问题 比较重大的制程品质问题 客户要求回复的品质投诉
何时
采用 8D
0 问题初步了解
四. 8D步骤
原因分析
4
确定可能原因
5
长期对策
1
建立小组
2
问题描述
3
临时对策
选择最可能原因
NO
最有
可能的原因
是否是根本
原因?
YES
确定根本原因
6 预防再发对策
7 效果确认及标准化
定义、验证和执行临时控制行动,保证在永 久纠正措施实施前,将问题与内外部顾客隔 离。
需要考虑的问题:
1.防止继续产生不 良品(减少不良品产 生)。
2.减小产生的不良和 后续可能产生不良对 客户的影响。
四. 8D步骤—D3临时对策
• 确定并执行应先采取的临时措施,以遏制外界/内部 客户问题的扩大。
• 临时措施的确定应考虑从供应商零件库存---供应商零 件在途品--内部零件/材料—生产制程—仓库储存—交 付在途品—客户端减少和降低(消除)后果的产生。
一.什么是8D
此方法以团队运作导 向以事实为基础,避 免个人主见之介入, 使问题之解决能更具 条理。
面对问题应群策群力, 互相帮助、相互提拔、 如此才能彻底解决问题。
5
二.为什么要推行8D
通过建立小组训练内部合作的 技巧。
提供问题有效解决的方法。
防止相同或类似问题的再发生。
提高顾客满意度,增强其对供 方的产品和过程的信心 。
建立小组需要考虑的要素:
小组的领导: 小组的资源: 小组的成员: 人员的数量:
谁来推动? 谁工D步作团骤队—D1建立小组 选择小组成员的准则
小组成员的 人数控制在4到 10个之间
选择具有相 应技能、知识、 资源、权力等 的人作为团队 成员
各类成员之 间职责、任务 合理搭配
测进行观察测量,
有历史数据的对数据
疑
进行初步分析
点
验
关键原因确认
证
统计分析
DOE验证
机理分析
关键原因-是否为根本原因 5-WHY分析
四. 8D步骤—D4原因分析
鱼骨图分析
机
手工喷涂
员工品质意识淡薄
人
标准执行 力差
人员变动大
杜邦油漆性能 不良
素材表面
输送链台车
要打磨
漆渣太厚
喷涂房
环境差
未对半成品
环
进行检验
法
料
复押半成品 表面粒点
车 顶 饰 条 附 着 力 不 良
四. 8D步骤—D4原因分析
人--人员相关信息是否有变更 机--设备维修保养记录,
5M1E 分析
料--物料更改记录(主料、辅料)
环--温湿度记录 法--工艺更改记录,生产原始记录, 测--检测条件方法人员
常用方法
1.对操作员现场询问 2.现场观察 3.模拟试验
8
恭贺小组
四. 8D步骤—D0问题初步了解
问题初步了解(立项和准备工作)
– 鉴定是否有进行8D 的必要; – 立项和确定主题; – 收集资料。
此过程尽量获取内部 和外部的问题信息、 数据、进行初步的分
析和方案策划。
四. 8D步骤—D1建立小组
建立一个小组来解决问题和执行纠正计划, 小组成员应具有过程和/或产品知识、分配的 时间、权威和需要的技能。
8D 的原名叫做 8 Disciplines,又称团队导向问 题解决方法。是由福特公司始创,全球化品质管 制及改善的特殊必备方法,之后已成为QS9000/ ISO TS16949、福特公司的特殊要求。凡是做福 特的零件,必需采用 8D 作为品质改善的工具, 目前有些企业并非福特的供应商或汽车业的合作 伙伴,也很喜欢用这个方便而有效的方法解决品 质问题,成为一个固定而有共识的标准化问题解 决步骤。
• 临时措施一直要持续实施至后续的永久对策的执行有 效后,方可撤消。
• 临时措施实施中,应及时跟踪和验证其效果。
四. 8D步骤—D3临时对策
纠正措施(对策)
为消除已发现的不合格或其它不期望情况的原因所采取 的措施。
预防措施(预防再发对策)
为消除潜在不合格或其它潜在不期望情况的原因所采取 的措施。
预防措施与纠正措施的区别
采取纠正措施是为了防止发生,而采取预防措施是为了防 止再发生。
四. 8D步骤—D3临时对策
临时措施(对策)
为了不让问题不再扩大而采取的措施,相当于纠正。 常采取的动作如:隔离、全检、换货、报废、降级,员 工培训。
长期措施(对策)
为了问题不再发生所采取的措施。 一般必须进行根本原因分析才可以采取长期措施。 常见如:防错、更换原材料、设计变更等。