PCB生产涨缩管控.pptx
pcb制造过程中基材涨缩之形成机理及其控制

pcb制造过程中基材涨缩之形成机理及其控制下载提示:该文档是本店铺精心编制而成的,希望大家下载后,能够帮助大家解决实际问题。
文档下载后可定制修改,请根据实际需要进行调整和使用,谢谢!本店铺为大家提供各种类型的实用资料,如教育随笔、日记赏析、句子摘抄、古诗大全、经典美文、话题作文、工作总结、词语解析、文案摘录、其他资料等等,想了解不同资料格式和写法,敬请关注!Download tips: This document is carefully compiled by this editor. I hope that after you download it, it can help you solve practical problems. The document can be customized and modified after downloading, please adjust and use it according to actual needs, thank you! In addition, this shop provides you with various types of practical materials, such as educational essays, diary appreciation, sentence excerpts, ancient poems, classic articles, topic composition, work summary, word parsing, copy excerpts, other materials and so on, want to know different data formats and writing methods, please pay attention!PCB制造过程中基材涨缩之形成机理及其控制引言PCB(Printed Circuit Board,印刷电路板)在现代电子制造中扮演着至关重要的角色。
PCB基板涨缩的判定与测量[1]
![PCB基板涨缩的判定与测量[1]](https://img.taocdn.com/s3/m/10df319251e79b89680226b1.png)
5.2.3 涨缩与钻偏—X-Ray照孔确认
假设以上为4个PCS﹐以上孔偏方向如红箭头所示﹐孔偏方向为 离心式扩张偏移﹐可以判定此板有整板内缩现象﹔另有单PCS 或部分PCS的孔偏呈现出扩张式﹐也可判定为涨缩异常。
2020年3月7日星期六
12
钻孔所有孔均向一个方向偏移﹐如果压合钻靶未偏移﹐即可断定为钻 孔整体移位。当然﹐钻孔钻偏大多数是BGA密集区部分孔偏移﹐判定 人须根据具体情况做判断﹐不可和涨缩引起的钻偏混淆。
底片放置的 时间和条件
人
底片制作时是否按 抓好的补偿进行预
放或预缩
基板的厚 度以及铜
厚
压合参数设 置是否合理
P/P的物性与
基板底片的 尺寸安定性
料
基板的匹配性 内层补偿值
是否抓准
法
内层板棕化 后放置条件
压合冷压设置 的冰水温度
为 何 涨 缩
板层多少及 板厚是否一致
残铜率及工 程迭构设计
钻靶前是否 冷却至室温
因為4層板只有一張內層板﹐壓合前測量靶距﹐壓合后MARK中心鑽靶
后再測靶距﹐即是其絕對漲縮數據﹐至于層偏的影響一般可以不予考
慮。
1.2 6層板測量
6層板共有兩張內層板﹐基本上為對稱疊構﹐因此壓合后兩面漲縮差異
可以不考慮﹐測量方式與4層板類似。
1.3 8層以上板測量
8層以上板因為層次排列不同﹐內外層次壓合中會產生較大差異﹐因此
需要建立標靶進行監控﹐如下頁圖注。
2020年3月7日星期六
20
2020年3月7日星期六
21
2.相對漲縮的測量﹕ 測量工程設定值數據與壓合后數據對比。 2.1 壓合后漲縮測量 壓合后產品可以選擇用X-Ray鑽靶機測量靶距或標靶距離來判定漲縮﹐ 也可以將靶孔用MARK方式鑽破后使用2D測量其數據。 2.2 鑽孔首件后漲縮測量 壓合鑽靶選用中央基准補償式鑽靶﹐當產品到鑽孔后靶孔已無法作為漲 縮測量的參考依據﹐此時可以選擇待鑽板用鑽靶機MARK方式鑽破外圍 孔﹐用X-Ray或2D測量孔距判定漲縮尺寸﹐8層以上有標靶的可以同壓 合測量方式。 2.3 中測漲縮的判定與測量 中測板因為加上外層線路﹐對漲縮的判定有一定遮蔽性。一般漲縮為批 量性異常﹐但也會有鑽孔首件等個別漲縮異常板流入﹐此時需要對異常 板蝕刻后造X-Ray﹐判定方式同鑽孔﹐中測板已無可供測量的孔﹐尺寸 漲縮 值不能測量。
PCB基板涨缩的判定与测量[1]33450
![PCB基板涨缩的判定与测量[1]33450](https://img.taocdn.com/s3/m/697cefa3770bf78a652954b4.png)
异常受影响的因素过多﹐生产中有任意参数变更都会引起涨异常的发 生。
04.08.2020
整理ppt
5
3.引起涨缩异常的要因分析﹔
机
压机热盘温度 均匀性是否达标
内层底片检测是否 按标准进行
钻靶机钻 靶精度是 否达标
环
压机升温速 率是否均匀
内短的原因判定还需要找点﹐切片及数据分析﹐涨缩引起的内短只能计算其贡献 度﹐单独的涨缩不会引起内短﹐还需要加上钻偏﹑层偏导致。如下图﹕
铜面 线路
04.08.2020
介质层
导通孔
整理ppt
线路
如果孔与线最小距离为 8mil﹐层间偏移2mil﹐涨 缩3mil﹐钻孔偏3mil(以上皆偏 上限或下限)﹐导通孔就会连接 到线路﹐造成层间短路。
涨缩
同心圆 4﹑5层 同时延X 方向向 外或向 内可判 定为X向
涨缩 整理ppt
同心圆 4﹑5层 同时向 4个拐 角偏移 可以确 定为整 板涨缩
9
层次铆偏以8层板为例﹕
同心圆 某一层 次同时 向一个 方向偏
移
同心圆 某一层 延一个 圆心朝 不同的 方向偏
移
同心圆 一边正 常﹐另 一边同 时往一 个方向
偏移
以上归纳的为较为常见的几种涨缩与铆偏容易混淆的异常区分办法﹐而 实际生产中会出现更多更复杂的现象﹐那样就需要我们凭借经验去做层 别﹐判定异常的真实归属。
04.08.2020
整理ppt
10
5.2.2 涨缩与内短—同心圆判定(查看是否存在层间偏移)。
内层短路一般由底片漏光或吸气不良﹑显影不洁等造成﹐压合及基板的铜粉铜屑 和压合的铆钉屑也会引起内短。而涨缩引起的内短则是因层间涨缩差异造成﹐只 会存在于8层以上板﹐因此只需要观察同心圆是否有涨缩即可判ppt
PCB生产涨缩管控

内容
涨缩制程管控方法 涨缩异常处理
2
1.尺寸涨缩概述
什么是尺寸涨缩?
尺寸涨缩通常就是指PCB制作流程中,其基材吸湿而澎涨,脱湿而收 缩之尺寸变化的过程.愈高温愈易吸湿,因而愈高温高湿时,尺寸变化更 大.
尺寸涨缩对PCB的影响?
尺寸涨缩对各制程的作业有很大的影响,它将影响到钻孔与内层的
对准度,外层和防焊,文字的对准度,以及成品的尺寸公差.
富士DX L2 富士DX L3 富士DX L4 富士DX L5 富士DY L2 富士DY L3 富士DY L4 富士DY L5
2.0 1.5 1.0 0.5 0.0 -0.5 -1.0 -1.5 -2.0
發放值 4小時變化 8小時變化 16小時變化 16小時總變化
结果:
E162C6014DD内层底片:上机后十六小时与上机前对比DX最大变化缩1.5mil,DY最
玻 尺安測試值 TG點 布 經向(Warp) 緯向(Fill)
D F G G 138.14 138.14 136.12 136.23 136.12 137.6 135.23 137.91 136.23 138.9 138.9 138.9 138.1 138.1 138.1 138.1 138.1 -0.0087% -0.0011% -0.0439% -0.0439% -0.0206% -0.0152% -0.0396% -0.0055% -0.0396% -0.0050% -0.0013% -0.0114% -0.0069% -0.0026% -0.0103% -0.0026% -0.0035% -0.0079% -0.0121% -0.0449% -0.0449% -0.0165% -0.0033% -0.0440% -0.0058% -0.0440% -0.0090% -0.0181% -0.0039% -0.0142% -0.0070% -0.0095% -0.0070% -0.0111%
PCB基板涨缩的判定与测量[1]54787ppt课件
![PCB基板涨缩的判定与测量[1]54787ppt课件](https://img.taocdn.com/s3/m/8798c456de80d4d8d05a4f19.png)
異常受影響的因素過多﹐生產中有任意參數變更都會引起漲異常的發 生。
03.07.2020
.
5
3.引起漲縮異常的要因分析﹔
機
壓機熱盤溫度 均勻性是否達標
內層底片檢測是否 按標准進行
鑽靶機鑽 靶精度是 否達標
環
壓機升溫速 率是否均勻
季節﹑天氣 變化
11
5.2.3 漲縮與鑽偏—X-Ray照孔確認
假設以上為4個PCS﹐以上孔偏方向如紅箭頭所示﹐孔偏方向為 離心式擴張偏移﹐可以判定此板有整板內縮現象﹔另有單PCS 或部分PCS的孔偏呈現出擴張式﹐也可判定為漲縮異常。
03.07.2020
.
12
鑽孔所有孔均向一個方向偏移﹐如果壓合鑽靶未偏移﹐即可斷定為鑽 孔整體移位。當然﹐鑽孔鑽偏大多數是BGA密集區部分孔偏移﹐判定 人須根據具體情況做判斷﹐不可和漲縮引起的鑽偏混淆。
偏移
以上歸納的為較為常見的几種漲縮與鉚偏容易混淆的異常區分辦法﹐ 而實際生產中會出現更多更復雜的現象﹐那樣就需要我們憑借經驗去做 層別﹐判定異常的真實歸屬。
03.07.2020
.
10
5.2.2 漲縮與內短—同心圓判定(查看是否存在層間偏移)。
內層短路一般由底片漏光或吸氣不良﹑顯影不潔等造成﹐壓合及基板的銅粉 銅屑和壓合的鉚釘屑也會引起內短。而漲縮引起的內短則是因層間漲縮差異造成 ﹐只會存在于8層以上板﹐因此只需要觀察同心圓是否有漲縮即可判定漲縮對內短 有多大貢獻度。
﹖
03.07.2020
.
6
4.鑽孔X-Ray照看方式﹕ 上
右 左
下
COMP面
03.07.2020
PCB涨缩不良现象及改善措施

PCB涨缩不良现象及改善措施PCB(Printed Circuit Board,印刷电路板)在电子设备制造中起着至关重要的作用。
然而,由于材料和环境的影响,PCB可能会出现涨缩不良的问题。
本文将探讨PCB涨缩不良的原因以及改善措施,以帮助读者更好地理解和解决相关问题。
一、PCB涨缩不良的原因1. 材料热膨胀系数不匹配PCB的主要材料包括导电层、外层热固性树脂、内层介质层等。
这些材料由于温度变化会存在不同程度的热膨胀,如果它们的热膨胀系数不匹配,就会导致PCB出现涨缩不良的问题。
2. 焊接温度不均匀在PCB制造过程中,焊接是一个关键步骤。
如果焊接温度不均匀,某些区域的PCB可能会受热不均,导致局部涨缩不良。
3. PCB设计不合理PCB设计中考虑到材料的热膨胀以及温度变化对电路板的影响是十分重要的。
如果在设计阶段没有充分考虑这些因素,也会导致PCB涨缩不良。
二、改善PCB涨缩不良的措施1. 优化材料选择选择热膨胀系数匹配的材料对于解决PCB涨缩问题至关重要。
在选材时,要仔细研究材料的热膨胀系数,并确保它们与其他材料相匹配。
2. 控制焊接温度在PCB焊接过程中,确保温度均匀分布是关键。
可以通过提高焊接设备的精度和稳定性,采用均热设计等方式来实现温度的均匀控制,减少PCB的局部涨缩不良。
3. 合理的PCB设计在PCB设计过程中,应充分考虑材料的热膨胀系数以及温度变化对电路板的影响。
可以采用增加焊盘面积、减小板厚度等设计技巧,以提高PCB的涨缩性能。
4. 精确的温度控制在实际使用中,对PCB的温度进行精确控制也能够有效改善涨缩不良的问题。
可以采用温度传感器和自动控温装置等技术手段,确保PCB始终处于适宜的工作温度范围内。
5. 定期检测和维护定期检测PCB的涨缩情况,及时发现并解决问题,对于维护PCB的稳定性和可靠性非常重要。
可借助扫描电镜等设备对PCB进行全面的检测,以了解其状况并制定相应的维护计划。
结论PCB涨缩不良是在电子设备制造中常见的问题,但通过选材、焊接温度控制、合理的PCB设计、精确的温度控制以及定期检测和维护等改善措施,可以降低PCB涨缩不良的发生率,提高PCB的稳定性和可靠性。
PCB基板涨缩的判定与测量[1]83508ppt课件
![PCB基板涨缩的判定与测量[1]83508ppt课件](https://img.taocdn.com/s3/m/dc6ebb415022aaea988f0f7e.png)
异常受影响的因素过多﹐生产中有任意参数变更都会引起涨异常的发 生。
28.06.2020
.
5
3.引起涨缩异常的要因分析﹔
机
压机热盘温度 均匀性是否达标
内层底片检测是否 按标准进行
钻靶机钻 靶精度是 否达标
环
压机升温速 率是否均匀
季节﹑天气 变化
内短的原因判定还需要找点﹐切片及数据分析﹐涨缩引起的内短只能计算其贡献 度﹐单独的涨缩不会引起内短﹐还需要加上钻偏﹑层偏导致。如下图﹕
铜面 线路
28.06.2020
介质层
导通孔
.
线路
如果孔与线最小距离为 8mil﹐层间偏移2mil﹐涨 缩3mil﹐钻孔偏3mil(以上皆偏 上限或下限)﹐导通孔就会连接 到线路﹐造成层间短路。
底片放置的 时间和条件
人
底片制作时是否按 抓好的补偿进行预
放或预缩
基板的厚 度以及铜
厚
压合参数设 置是否合理
P/P的物性与
基板底片的 尺寸安定性
料
基板的匹配性 内层补偿值
是否抓准
法
内层板棕化 后放置条件
压合冷压设置 的冰水温度
为 何 涨 板层多少及 缩
板厚是否一致
残铜率及工 程迭构设计
钻靶前是否 冷却至室温
第三步﹑如外围孔与靶孔表象不
符﹐测量靶距﹐检测压合是否有
钻靶. 异常。
7
5.角度判定與計算偏移值﹕
孔
隔
離
層
內層pad
28.06.2020
.
切破 90°
切破180 °
8
5.
5.1 涨缩异常表现的形式﹕
pcb制程基板尺寸涨缩
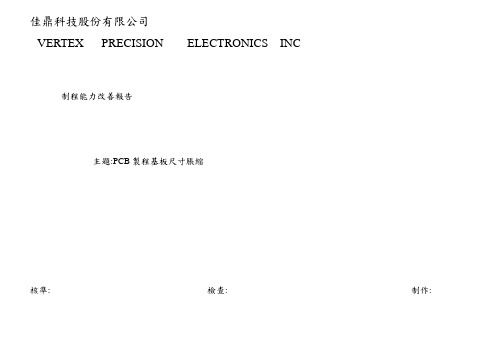
佳鼎科技股份有限公司VERTEX PRECISION ELECTRONICS INC制程能力改善報告主題:PCB製程基板尺寸脹縮核準: 檢查: 制作:主題:PCB製程基板尺寸脹縮動機:12月份中,因基板尺寸脹縮,以而使制程工具重新設計的比例過高,外層底片,防焊底片的影響甚巨.這增加重工機率,降低工作效率.為了有效降低重工率,提升產能效率,於11月份組織品質改善小組,推動基板脹縮研究,期望在學習過程中可以找出一個規範,以利日后工程設計與制造流程中,有一定的方法可遵循.定義:1.物質有一定的物理特性-----熱脹冷縮2.務物質有膨脹系數不同,銅,樹脂,玻璃纖維皆不同,造成基板內部應力不同,而影響尺寸安定性.3.圖為基尺寸脹縮后,對制程品質影響示意圖.基板發生熱脹冷縮后,板了的尺寸不臺預期之尺寸,所以在制程未修正時,會產生孔對位偏移現象,為左右,上下對稱.4.本次研究主題,在目前制程條件下,材料物理性對產品品質的影響.目的:1.減低重工率2.提升工程設計能力及制程能力現況分析工程部基板脹縮設計各制程孔偏容許誤差值:1.內層板與鑽孔程式-----------±10mil2.外層底片與鑽孔底片程式---±2mil3.S/M底片與外層底片---------±2mil內層基板尺寸數據結論:內層板之脹縮值於壓合制程后,可含蓋其制程上之誤差(鑽孔對內層有10mil的誤差容許範圍)壓合課脹縮料號統計表結論:1.標準化制程參數下,不同料號會產生不同和脹縮比例.同一料號尺寸差異並不會太大.2.基板在經過壓合后,由於會產生很大的障脹比例,所以在工程設計要加以考慮.各制程脹縮分析結論: 1.鑽孔后之制程以鑽孔程式為基準,孔位對準度以鑽孔后為標準.2.引表內所述的制程與CAM值差異小,不會影響孔位對準度品質.3.鑽孔修改程式值,后制程之制造工具(底片等)也應修正.工作計劃進度表制程能力數據收集Array目的:收集目前5制程參數下,基板尺寸脹縮數據內容:1.料號---A2621013D2.壓板材料銅箔0.5oz*1Prepreg 7630*1(聯茂)Lam 1.0mm0.5/0.5 oz(南亞)Prepreg 7630*1(聯茂)銅箔0.5 oz*1各制程脹縮數據追蹤記錄結論: 1.各制程對基板脹縮的貢獻,在誤差容許範圍內.2.外層刷磨后基板脹縮影響品質.結論: 1.FR-4基板之底片脹縮值X=1.2/10000、Y=1.5/10000.2.刷磨方向性並不影響基板脹縮.改善工程部基板脹縮設計結論: 1.根據所收集的各制程數據作工程設計的修正.2.為應付特殊狀況,設計基板脹縮流程,並適時反應資料與工程部.基板漲縮流程圖壓合課與鑽孔課外層課與濕膜課結論:1.三個月來重工率已降低2.目前的工作只是一個開始,日后須更深入研究.制程工具用量表。
PCB生产涨缩管控
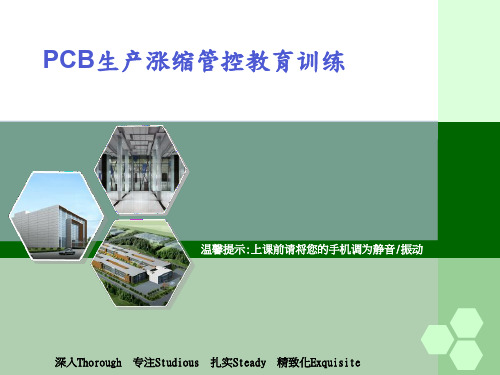
宏仁 1.2mm 1/1oz 09月05日 09月08日 9905N3C2M2 D 138.1 -0.0026% -0.0070% 9905N3C2U1-D 9905N3C2I2-D
宏仁 1.2mm 1/1oz 09月01日 09月08日 9901N3B1D2 D 138.1 -0.0035% -0.0111% 9901N3B1U2-D 9901N3B1M2-D
宏仁 1.3mm 1/1oz 08月28日 09月05日 9828N6A1U D 137.91 -0.0055% -0.0058% 9829N3C2M1-D 9826N3A2M1-D
宏仁 0.08mm 1/1oz 09月04日 09月05日 9904N1A1U G 136.23 -0.0396% -0.0440% 9904N1A1D-G 9903N1C2D-G
250
100
200
80
150
60
100
40
50
20
0 板层数 异常料号数
百分比
累积 %
4L 166
64.8 64.8
6L 78
30.5 95.3
0 其他
12
4.7
100.0
200
150
100
50
0 層別 不良數 百分比 累积 %
09/04~09/09月四层板异常统计表
層別 的 Pareto 图
6L 96
14
2.尺寸涨缩流程分解
进料
开料
内层
压合
钻孔
基板尺寸安定性 检测
经纬向区分
厂商:±300PPM 建议厂内管控: R值≦300PPM
无尘室温湿度 管控
P.P裁切经 纬向区分
PCB基板涨缩的判定与测量[1]38578说课讲解
![PCB基板涨缩的判定与测量[1]38578说课讲解](https://img.taocdn.com/s3/m/866550d4d4d8d15abe234ebe.png)
2020/7/4
12
5.2.4 外偏與漲縮—看孔環與孔偏移 外偏導致原因一般有二﹐其一﹕外層底片對位失准﹔其二﹕底片漲縮。 由于外層曝光為單面曝光﹐底片對位為兩面分開﹐如果有一面對位不准 即會造成單面曝偏﹐如有兩面整體向一個方向偏移即可判定為漲縮。這 種判定是帶有一些隨機性﹐但應該可以COVER95%以上異常。
內短的原因判定還需要找點﹐切片及數據分析﹐漲縮引起的內短只能計算其 貢獻度﹐單獨的漲縮不會引起內短﹐還需要加上鑽偏﹑層偏導致。如下圖﹕
銅面 線路
2020/7/4
介質層
導通孔
線路
如果孔與線最小距離為 8mil﹐層間偏移2mil﹐漲 縮3mil﹐鑽孔偏3mil(以上皆偏 上限或下限)﹐導通孔就會連接 到線路﹐造成層間短路。
8
層次鉚偏以8層板為例﹕
同心圓 某一層 次同時 向一個 方向偏
移
同心圓 某一層 延一個 圓心朝 不同的 方向偏
移
同心圓 一邊正 常﹐另 一邊同 時往一 個方向
偏移
以上歸納的為較為常見的几種漲縮與鉚偏容易混淆的異常區分辦法﹐ 而實際生產中會出現更多更復雜的現象﹐那樣就需要我們憑借經驗去做 層別﹐判定異常的真實歸屬。
第二步﹑判定原因﹔如整pnl或部 分step有發生異常以上現象﹐查 看靶孔與外圍孔狀況﹐8層以上板 首先確定同心圓狀況。
第三步﹑如外圍孔與靶孔表象不
符﹐測量靶距﹐檢測壓合是否有
鑽靶異常。
6
5.角度判定與計算偏移值﹕
隔 離 層
2020/7/4
孔 內層pad
切破90° 切破180 °
7
5.漲縮異常的判定﹔
壓合中央基准補償鑽靶﹐發生3個靶孔同時延Y軸向內偏或外偏現象﹐為漲 縮補償鑽偏﹐其偏移標准看鑽靶的補償值﹐壓合鑽靶補償≦6mil為我司目前 管控標准﹐其對靶偏的尺寸影響計算方法如下﹕
PCB尺寸涨缩管控

开Fail单
开Pass单
曝光板退洗
接Pass单蚀刻
五、尺寸监控-生产监控
基材
PCB生产流程
PCB成品
内压钻电外防化文成电目 层合孔镀层焊金字型测检
过程首件管理 量测位置:上中下三点 量测频率:每60量测1片 判定标准:依照首件管理
量测位置:pcs量测 量测频率:每DC:25pcs 判定标准:依照工单
五、尺寸监控-PCB成品趋势监控
1. 成品板出货前按周期进行尺寸验证量测,数据记录并作出趋势图 2. 量测后根据客户规范要求判定是否可以出货
厂内预警线 a.平均值偏离中心规格20um b.max 距离上限20um c.min 距离下限10um
板厂一般建议客户端在打完件后一周内使用(Bonding)。
二、PCB尺寸变化试验-不同湿度
取PCB过炉后存放在恒温恒湿箱内与常温环境下比较PCB尺寸回涨变化 材料厚度39mil
1.湿度越高,回涨越快Fra bibliotek三、PCB尺寸设计-补偿设计
Q4季???表
1.补偿设计时考量基板厚度及叠构 2.补偿表由统计验证汇总经验数据得来 3.补偿表每年修正2次(Q2/Q4) 4.根据各家客户尺寸要求设计
三、设计-规格公差
公差为喇叭口设计 小大
客户公差的50%
+60um -60um
+30um -90um
+70um -70um
1.PCB生产时,外层光学点公差为客户公差的50% 2.基板材料水准批次生产收缩差异80ppm
四、生产管控-烘烤管理
基材
PCB生产流程
PCB成品
内压钻电外防化文成电目 层合孔镀层焊金字型测检
Key
生产前烘烤 条件:150度 4 Hr
PCB生产涨缩管控
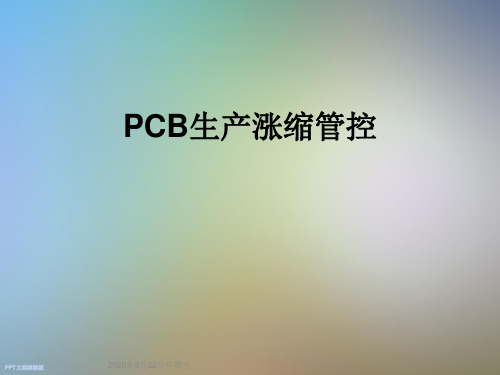
1.尺寸涨缩概述
基板尺寸涨缩的原因: (4)多层板在层压前,因基板有吸湿性,使薄基板或半固化片吸湿,造 成尺寸稳定性差,基板中树脂未完全固化,导致尺寸变化.
基材尺寸涨缩的控制方法: (4)基材必须进行烘烤以除去湿气.并将处理好的基板存放在真空干燥 箱内,以免再次吸湿, 烘烤还可以确保树脂固化,减少由于冷热的影响,导 致基板尺寸的变形.
尺寸涨缩对各制程的作业有很大的影响,它将影响到钻孔与内层的 对准度,外层和防焊,文字的对准度,以及成品的尺寸公差.
1.尺寸涨缩概述
通常我们所说的尺寸涨缩主要分为:基板涨缩与底片涨缩.
基板
底片
1.尺寸涨缩概述
基板尺寸涨缩的原因: (1)经纬方向差异造成基板尺寸变化;由于剪切时,未注意纤维方向
,造成剪切应力残留在基板内,一旦释放,直接影响基板尺寸的收缩.
孔位檢查
底片上机前 后变化
底片单张差异 底片每套间差异 底片使用次数
后烤前后变 化
3.尺寸涨缩管制方法
IQC进料对基板的玻布厂牌、进料尺寸安定性状况进行记录.
3.尺寸涨缩管制方法
开料对1.0mm以下基板进行烘烤150℃4H,使基板在制程中的涨缩更稳定. 追踪0.08mm板各站尺寸变化, 烘烤基板变化小于未烘烤基板,基板烘烤后更稳定.各站测试如下 :
基材尺寸涨缩的控制方法: (2)在设计电路时应尽量使整个板面分布均匀.如果不可能也要必须在 空间留下过渡段(不影响电路位置为主).这由于板材采用玻璃布结构中经纬 纱密度的差异而导致板材经纬向强度的差异.
1.尺寸涨缩概述
基板尺寸涨缩的原因: (3)刷板时由于采用压力过大,致使产生压拉应力导致基板变形.
制程涨缩管控制度

制程涨缩管控制度、目的:有效的管控板材涨缩变化,降低因板料涨缩变化造成的内短、层偏、菲林偏位等品质不良,同时减少菲林、钻带更改次数,方便锣板,满足客户要求。
二、适用范围:2.1所有普通多层板;2.2所有HDI板(包括次外层)。
三、各工序管控措施:1、开料1.1、开料要区分板料的经纬方向,对于同型号中有两种方向的板件,在开好料后做好经纬方向的标识转序;1.2、开料后板厚w 0.8mm 要烤板,烤板参数为板料TG值(非高TG材料一般设定150 C) 土 5 °C温度下烤板4〜6小时;例如:(1).查MI或LOR卡上注明了板厚(0.3mm )、TG值(150 C)(2).双手戴棉手套持板将板子整齐平放在烤箱台面上,移动支架时需注意滑板,PC板上下面需用牛皮纸隔开。
(3).每叠板高度25PNL以下,设定150 C温度烤板4小时。
1.3、同一批板原则上使用同一家供应商的板料,如有不同供应商的板料,需要进行相应的标识区264、生产内层批量生产过程中IPQA抽测到不合格时,IPQA需追溯到前几批首板,从后往前一做复检,一直到0K板为止并分开不良板。
由生产将此料号之菲林退回工程做复测,复测动作同2.6.1 ;265、不良板的处理由生产以书面特采单的形式报请QAE和工艺系数组会签,裁决权归工艺系数组;同意特采此不良板,分开lot卡,由生产在短边右上角钻直径为 3.175mm 孔一个,工艺跟进此批板压合并最终制定处理意见。
3、层压3.1 钻靶标定位孔:3.1.1、每次在钻靶位孔(含换不同的型号)前进行校准,使用全新钻咀,钻咀使用寿命控制在 1000孔次以下;3.1.2、每50pnl生产自检一次孔形(含披锋),不允许有残铜、披锋。
3.2、普通多层及以上高层板、手机通孔板、HDI板次外层、镭射板涨缩区间的划分与标识;3.2.1、普通多层及以上高层板涨缩区间的划分伐U分工序:压合)3.2.2、手机通孔板涨缩区间的划分(划分工序:压合)323、 HDI板次外层涨缩区间的划分(划分工序:压合)附件1为压合靶距数据记录单:3.3、压合X-RAY打靶机需二次元校正,打靶偏差与二次元测量偏差之差值w± 1mil ,校正频率:1次/班,并做好校正记录,打靶时板面温度需冷却至室温,具体操作由QA监控;3.3.1、压合打靶时,所有普通多层板及 HDI板次外层、HDI板外层,打靶方式选择抓靶孔中心打孔,即中心打靶方式作业。
pcb涨缩机理
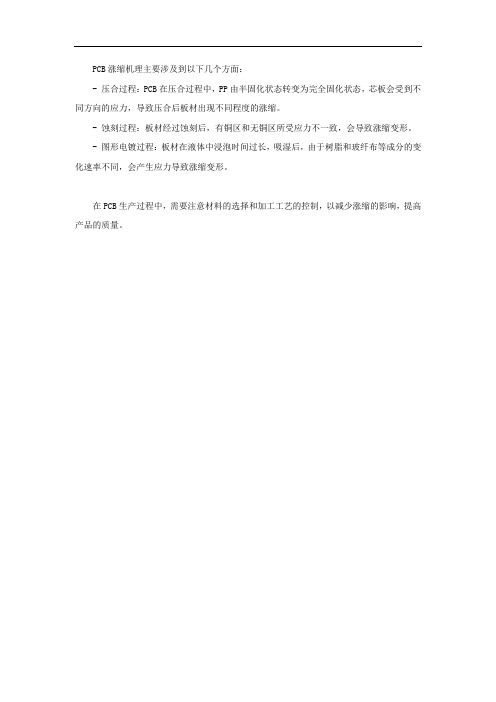
PCB涨缩机理主要涉及到以下几个方面:
- 压合过程:PCB在压合过程中,PP由半固化状态转变为完全固化状态,芯板会受到不同方向的应力,导致压合后板材出现不同程度的涨缩。
- 蚀刻过程:板材经过蚀刻后,有铜区和无铜区所受应力不一致,会导致涨缩变形。
- 图形电镀过程:板材在液体中浸泡时间过长,吸湿后,由于树脂和玻纤布等成分的变化速率不同,会产生应力导致涨缩变形。
在PCB生产过程中,需要注意材料的选择和加工工艺的控制,以减少涨缩的影响,提高产品的质量。
PCB生产涨缩管控[1]
![PCB生产涨缩管控[1]](https://img.taocdn.com/s3/m/e75d2d4bf90f76c660371a45.png)
PTH/ICU
PTH前处理 前后差异
PTH/Icu 前后差异
外层
IICu
无尘室温湿 度管控
IICu前后 差异
温度22±2℃,湿度 55±5%
外层前处理 前后差异
蚀刻后尺 寸变化
压膜前 后差异
曝光机內部温 湿度变化
底片上机前 后变化
底片单张差异 底片每套间差异 底片使用次数
防焊
文字
二钻
无尘室温湿 度管控
行钻带修改.
PCB生产涨缩管控[1]
4.异常处理
4.3.异常当站改善方法. 4.3.1通过X-RAY拍光用图片与图标记录偏孔方向.
X-RAY拍光照片 通过图标确定修改钻带时修改原点位置.
偏孔方向记录
PCB生产涨缩管控[1]
4.异常处理
4.3.2涨缩常见状况: 异常状况一
原点处 不良类型一:此异常需加大钻带比例修改(如:原X=Y=1.0000改为X=Y=1.0001).
层别
月份
0904月 0905月 0906月 0907月 0908月 0909月
4L 6L 8L 合计
13
23
8
13
10
15
19
11
12
20
10
24
4
1
0
1
3
3
36
35
20
34
23
42
PCB生产涨缩管控[1]
3.尺寸涨缩管制方法
09年04月~09年09月异常总表分析模块(四层板)
厂版
基板
pp组合
偏涨(件)
PCB生产涨缩管控
2020/11/3
PCB生产涨缩管控[1]
FPC涨缩系统管理讲解ppt课件
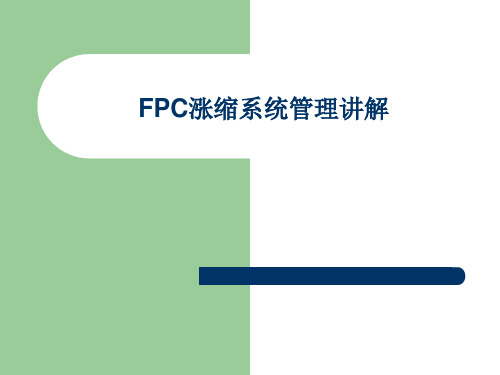
0.96 0
MD ‰ 9
5.83 5.19
0.5 -2
典型FPC涨缩比例一览表
D005C009
线路菲林 防焊菲林 文字菲林
D0013C006
线路菲林 防焊菲林 文字菲林
D0018F022
线路菲林 防焊菲林 文字 文字菲林
TD 1.000126
合时胶填充不足导致产品变形,胶的厚度及是否分布均 匀,是FPC材料涨缩的罪魁祸首。
工艺设计方面:覆盖膜尽量覆盖所有铜箔部分,不建议
条贴覆盖膜,避免压制时受力不均,5MIL以上的PI补强 贴合面胶不宜过大,如无法避免则需将覆盖膜压合烘烤 完成后再进行PI补强的贴合压制。
二、材料储存方面
需严格按照材料供应商提供的条件存放 。 供应商的制造条件,运输过程的条件,我司的加
1.0002
TD 1.000153
1.000095
TD 0.999088
0.998988
TD 1.000153 1.000096
1
MD 1.00045 0.9999
MD 1.000583
1.00005
MD 1.000075
0.999975
MD 1.000583 1.00005
0.9998
工环境上的不同造成的材料,工具的整个系统的 涨缩。 重点加强材料和工具到我司后的储存和涨缩的严 格管理。
2.1 菲林的管理
菲林在菲林室的储存条件与工作场所的温度,湿 度的差异。
菲林回厂后的测量涨缩,黑片翻出后黑片的涨缩 的系统测量,统计记录。
各个工段的对菲林涨缩的极限是万分之几?
2.2 材料的管理
不同的材料,相同的环境下其涨缩比例也是不同 我们的文件涨缩比例应根据基材的不同而不同。
- 1、下载文档前请自行甄别文档内容的完整性,平台不提供额外的编辑、内容补充、找答案等附加服务。
- 2、"仅部分预览"的文档,不可在线预览部分如存在完整性等问题,可反馈申请退款(可完整预览的文档不适用该条件!)。
- 3、如文档侵犯您的权益,请联系客服反馈,我们会尽快为您处理(人工客服工作时间:9:00-18:30)。
1.尺寸涨缩概述
基板尺寸涨缩的原因: (5)多层板经压合时,过度流胶造成玻璃布形,从而导致尺寸.
基材尺寸涨缩的控制ቤተ መጻሕፍቲ ባይዱ法: (5)需进行工艺试压,调整工艺参数然后进行压制.同时还可以根据 半固化的特性,选择合适的流胶量.
9
1.尺寸涨缩概述
底片尺寸涨缩的原因: (1)底片从真空包装拆包后静置时间不足;
底片单张差异 底片每套间差异 底片使用次数
DES后尺寸变化
15
2.尺寸涨缩流程分解
PTH/ICU
PTH前处理 前后差异
PTH/Icu 前后差异
外层
IICu
无尘室温湿 度管控
IICu前后 差异
温度22±2℃,湿度 55±5%
外层前处理 前后差异
蚀刻后尺 寸变化
压膜前 后差异
曝光机內部温 湿度变化
底片上机前 后变化
宏仁 0.9mm 1/1oz 08月29日 09月02日 9829N6C2M F 138.14 -0.0011% -0.0121% 9829N6C2U-F 9829N6C2D-F
孔位檢查
底片上机前 后变化
底片单张差异 底片每套间差异 底片使用次数
后烤前后变 化
16
3.尺寸涨缩管制方法
IQC进料对基板的玻布厂牌、进料尺寸安定性状况进行记录.
廠牌
板厚
銅厚 生產日期 進料日期 進料批號
玻 布
TG點
尺安測試值 經向(Warp緯) 向(Fill)
备注
宏仁 1.0mm 2/2oz 08月17日 09月02日 917N3A1D1 D 138.14 -0.0087% -0.0079% 917N3A1D1-D
30sht/叠,150度4小时 烤箱温度均勻性监控 烘烤后冷却时间监控
先进先出管 理
暂存要求
内层涂布前 后差异
有效期点检: 基板: P.P:
曝光机內部温湿 度变化
铆合与热熔
同心圆对准 度检测 压合程式 热压/冷压 钻靶
上PIN作业
Run Out值 检测
X-Ray偏孔 檢查
底片上机前后变 化
钻靶精度 尺寸涨缩检测
3
1.尺寸涨缩概述
通常我们所说的尺寸涨缩主要分为:基板涨缩与底片涨缩.
基板
底片
4
1.尺寸涨缩概述
基板尺寸涨缩的原因: (1)经纬方向差异造成基板尺寸变化;由于剪切时,未注意纤维方向,
造成剪切应力残留在基板内,一旦释放,直接影响基板尺寸的收缩.
基材尺寸涨缩的控制方法:
(1)确定经纬方向的变化规律按照收缩率在底片上进行补偿(光绘前进
湿度的影响 : 在相对温度下,菲林的尺寸随着湿度的上升而涨大,相对湿度的降低而 缩小,湿涨变形系数在10ppm/%RH右,也就是说当湿度度发生 1℃的变化 时,50cm长的菲林会发生5um的变化(或20寸中的0.20mil).
13
1.尺寸涨缩概述
底片尺寸涨缩的原因: (4)曝光机温升过高.
底片尺寸涨缩的控制方法: (4)采用冷光源或有冷却装置的曝光机及不断更换备份底片.
行此项工作).同时剪切时按纤维方向加工,或按生产厂商在基板上提供的字
符标志进行加工.(一般是字符的竖方向为基板的纵方向)
5
1.尺寸涨缩概述
基板尺寸涨缩的原因: (2)基板表面铜箔部份被蚀刻掉对基板的变化限制,当应力消除时产生 尺寸变化.
基材尺寸涨缩的控制方法:
(2)在设计电路时应尽量使整个板面分布均匀.如果不可能也要必须在
Palwonn Electronics (Suzhou) Co., Ltd.
PCB生产涨昱缩鑫科管技控(教苏育州)训有练限公司
温馨提示:上课前请将您的手机调为静音/振动 深入Thorough 专注Studious 扎实Steady 精致化Exquisite
课程纲要
序号
内容
1 尺寸涨缩概述
2 涨缩流程分解
底片尺寸涨缩的控制方法: (1)黑片从真空包装中拆封后需静置24小时,棕片需静置8小时;
10
1.尺寸涨缩概述
底片尺寸涨缩的原因: (2)底片绘制完成后静置时间不足直接用于生产;
底片尺寸涨缩的控制方法: (2)底片绘制完成后静置时间必须大于2小时才可用于生产;
11
1.尺寸涨缩概述
底片尺寸涨缩的原因: (3)温湿度控制失灵;
3 涨缩制程管控方法
4 涨缩异常处理
2
1.尺寸涨缩概述
什么是尺寸涨缩?
尺寸涨缩通常就是指PCB制作流程中,其基材吸湿而澎涨,脱湿而收 缩之尺寸变化的过程.愈高温愈易吸湿,因而愈高温高湿时,尺寸变化更 大.
尺寸涨缩对PCB的影响?
尺寸涨缩对各制程的作业有很大的影响,它将影响到钻孔与内层的 对准度,外层和防焊,文字的对准度,以及成品的尺寸公差.
7
1.尺寸涨缩概述
基板尺寸涨缩的原因: (4)多层板在层压前,因基板有吸湿性,使薄基板或半固化片吸湿,造 成尺寸稳定性差,基板中树脂未完全固化,导致尺寸变化.
基材尺寸涨缩的控制方法: (4)基材必须进行烘烤以除去湿气.并将处理好的基板存放在真空干燥 箱内,以免再次吸湿, 烘烤还可以确保树脂固化,减少由于冷热的影响,导 致基板尺寸的变形.
14
2.尺寸涨缩流程分解
进料
开料
内层
压合
钻孔
基板尺寸安定性 检测
经纬向区分
厂商:±300PPM 建议厂内管控: R值≦300PPM
无尘室温湿度 管控
P.P裁切经 纬向区分
温度22±2℃,湿度 55±5%
储存条件
压烤前后尺 寸变化
内层前处理 前后差异
温湿度管控: 温度22±2℃湿度5±5% PP须放在室内6~12HR以上
底片单张差异 底片每套间差异 底片使用次数
防焊
文字
二钻
无尘室温湿 度管控
印刷前尺 寸变化
温度22±2℃,湿度 55±5%
防焊前处理 前后差异
印刷对准 度
防焊预烤前 后差异
制版底片涨缩 网版张力 网版涨缩 网版使用次数
后烤后尺寸 变化
二钻前尺 寸变化
上PIN
Run Out 值检测
曝光机內部温 度湿度变化
空间留下过渡段(不影响电路位置为主).这由于板材采用玻璃布结构中经纬
纱密度的差异而导致板材经纬向强度的差异.
6
1.尺寸涨缩概述
基板尺寸涨缩的原因: (3)刷板时由于采用压力过大,致使产生压拉应力导致基板变形.
基材尺寸涨缩的控制方法: (3)应采用试刷,使工艺参数处在最佳状态,然后进行刷板.对薄型基材, 清洁处理时应采用化学处理或喷砂处理.
底片尺寸涨缩的控制方法: (3)温度控制在22+2℃,湿度在55%+5%RH;
12
1.尺寸涨缩概述
温度的影响 : 在相对湿度下,菲林的尺寸随着温度的上升而涨大,温度下降
而缩小,其热涨变形系数在18ppm/℃左右,也就是说当温度发生1℃的 变化时,50cm长的菲林会发生9um的变化(或20寸中的0.36mil).