机械加工时机械振动原因及对策分析(新编版)
机械加工过程中机械振动的原因及对策研究

机械加工过程中机械振动的原因及对策研究机械振动是机械加工过程中的一个重要问题,它对机械加工精度和工作效率有很大的影响。
本文将探讨机械加工过程中机械振动的原因和对策。
一、机械振动的原因1.机床结构刚性不足机床的结构刚性是影响机床运行的重要因素之一。
如果机床结构刚性不足,在机械加工过程中就会引起机床振动。
此时,需要采取相应的措施来提高机床结构的刚度,如增加机床重量、加强机床和刀架床身之间的连接、改善刀具和加工件的支持等。
2.工件不平衡在机械加工过程中,如果工件存在不平衡现象,特别是在高速旋转时,不平衡力会引起机床振动,严重影响机械加工精度和表面质量。
因此,要控制工件的平衡质量,在机械加工之前对工件进行平衡处理。
3.刀具不良刀具的质量和磨损情况也是影响机床振动的重要因素。
如果刀具质量差或者磨损过度,就会引起机床振动。
此时需要及时更换刀具或进行刀具磨损检测,并根据实际情况对刀具进行调整和优化。
4.切削参数不合理切削参数的设定对机床振动的影响非常大。
如果切削参数不合理,过大的进给速度或切削深度等会引起机床振动。
因此,需要对切削参数进行合理的配置和调整,在机械加工过程中保持稳定的切削状态。
5.材料热变形材料的热变形也是影响机床振动的原因之一。
在高温状态下进行机械加工,由于材料的热膨胀和热变形,会导致机床振动,从而影响机械加工精度和表面质量。
为此,需要采取合理的温度控制措施和降低机床转速等措施来减少机床振动。
为保证机械加工的精度和表面质量,需要加强机床结构刚性。
可以采用的方式包括增加机床重量、加强机床和刀架床身之间的连接、增加装载切削力的部件的支撑等。
工件不平衡是引起机床振动的主要原因之一,因此需要在机械加工之前对工件进行平衡处理。
如果已经存在不平衡现象,则需要采取相应的措施进行平衡处理,如采用自动平衡设备等。
3.改善刀具和加工件的支持为了减少机械振动,需要改善刀具和加工件的支持情况。
可以采用的措施包括增加刀具直径、改变加工方向、增加承载工件的支撑板的面积等。
机械加工过程中机械振动的原因及对策分析
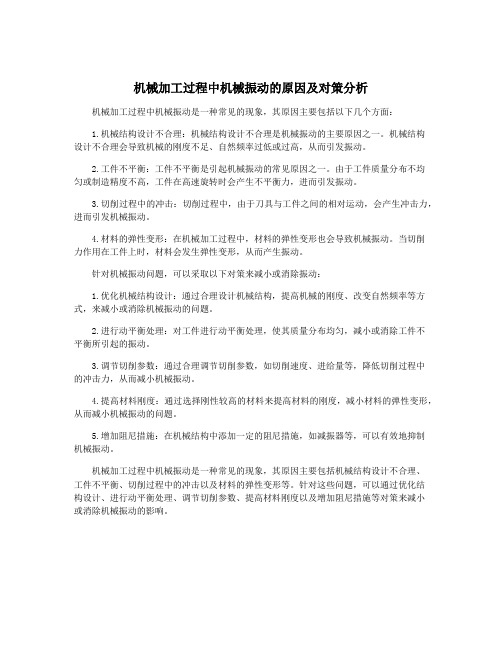
机械加工过程中机械振动的原因及对策分析机械加工过程中机械振动是一种常见的现象,其原因主要包括以下几个方面:1.机械结构设计不合理:机械结构设计不合理是机械振动的主要原因之一。
机械结构设计不合理会导致机械的刚度不足、自然频率过低或过高,从而引发振动。
2.工件不平衡:工件不平衡是引起机械振动的常见原因之一。
由于工件质量分布不均匀或制造精度不高,工件在高速旋转时会产生不平衡力,进而引发振动。
3.切削过程中的冲击:切削过程中,由于刀具与工件之间的相对运动,会产生冲击力,进而引发机械振动。
4.材料的弹性变形:在机械加工过程中,材料的弹性变形也会导致机械振动。
当切削力作用在工件上时,材料会发生弹性变形,从而产生振动。
针对机械振动问题,可以采取以下对策来减小或消除振动:1.优化机械结构设计:通过合理设计机械结构,提高机械的刚度、改变自然频率等方式,来减小或消除机械振动的问题。
2.进行动平衡处理:对工件进行动平衡处理,使其质量分布均匀,减小或消除工件不平衡所引起的振动。
3.调节切削参数:通过合理调节切削参数,如切削速度、进给量等,降低切削过程中的冲击力,从而减小机械振动。
4.提高材料刚度:通过选择刚性较高的材料来提高材料的刚度,减小材料的弹性变形,从而减小机械振动的问题。
5.增加阻尼措施:在机械结构中添加一定的阻尼措施,如减振器等,可以有效地抑制机械振动。
机械加工过程中机械振动是一种常见的现象,其原因主要包括机械结构设计不合理、工件不平衡、切削过程中的冲击以及材料的弹性变形等。
针对这些问题,可以通过优化结构设计、进行动平衡处理、调节切削参数、提高材料刚度以及增加阻尼措施等对策来减小或消除机械振动的影响。
机械加工过程中机械振动的原因及对策分析
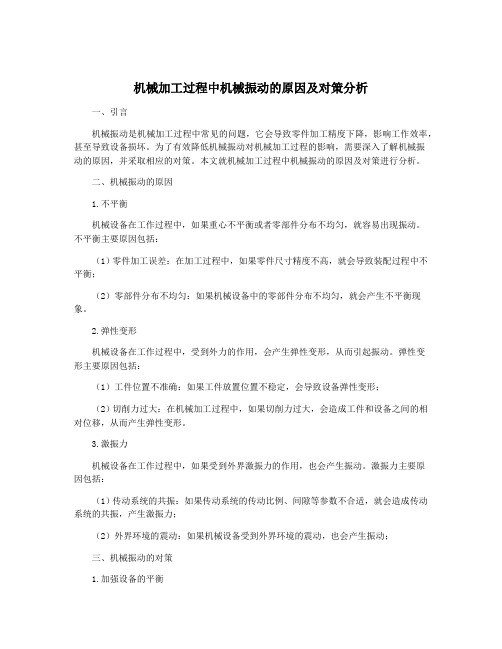
机械加工过程中机械振动的原因及对策分析一、引言机械振动是机械加工过程中常见的问题,它会导致零件加工精度下降,影响工作效率,甚至导致设备损坏。
为了有效降低机械振动对机械加工过程的影响,需要深入了解机械振动的原因,并采取相应的对策。
本文就机械加工过程中机械振动的原因及对策进行分析。
二、机械振动的原因1.不平衡机械设备在工作过程中,如果重心不平衡或者零部件分布不均匀,就容易出现振动。
不平衡主要原因包括:(1)零件加工误差:在加工过程中,如果零件尺寸精度不高,就会导致装配过程中不平衡;(2)零部件分布不均匀:如果机械设备中的零部件分布不均匀,就会产生不平衡现象。
2.弹性变形机械设备在工作过程中,受到外力的作用,会产生弹性变形,从而引起振动。
弹性变形主要原因包括:(1)工件位置不准确:如果工件放置位置不稳定,会导致设备弹性变形;(2)切削力过大:在机械加工过程中,如果切削力过大,会造成工件和设备之间的相对位移,从而产生弹性变形。
3.激振力机械设备在工作过程中,如果受到外界激振力的作用,也会产生振动。
激振力主要原因包括:(1)传动系统的共振:如果传动系统的传动比例、间隙等参数不合适,就会造成传动系统的共振,产生激振力;(2)外界环境的震动:如果机械设备受到外界环境的震动,也会产生振动;三、机械振动的对策1.加强设备的平衡对于不平衡造成的振动,可以采取以下对策:(1)提高零件加工精度:在零件加工过程中,应严格控制尺寸精度,避免误差导致的不平衡;(2)调整零部件分布:改变零部件的位置,使得机械设备的重心分布更加均匀。
2.增加刚度对于弹性变形引起的振动,可以采取以下对策:(1)稳定工件位置:通过改进夹具结构,提高工件的抓紧力,稳定工件的位置,减少弹性变形;(2)优化切削参数:通过调整切削速度、切削深度等参数,降低切削力,减少工件和设备之间的相对位移,减小弹性变形。
3.减少激振力对于激振力引起的振动,可以采取以下对策:(1)改善传动系统的设计:优化传动系统的传动比例、间隙等参数,避免传动系统的共振;(2)加强设备的隔振措施:通过在机械设备底部安装隔振装置,降低设备受外界环境震动的影响。
机械加工中机械振动的原因解析与应对

机械加工中机械振动的原因解析与应对随着工业技术的不断发展,机械加工已成为现代生产中不可或缺的重要环节。
然而在机械加工过程中,经常会遇到机械振动的问题,这不仅会影响加工质量,还有可能引发安全事故。
了解机械振动的原因和有效应对是非常重要的。
一、机械振动的原因解析1.不稳定的加工条件在机械加工过程中,如果加工条件不稳定,比如切削速度、切削深度、进给速度等参数没有得到合理控制,就会引起机床工作状态的不稳定,从而产生振动。
2.机床结构设计不合理机床是机械加工的主要设备,如果机床的结构设计不合理,会导致刚性不足、固定件松动等问题,使得在加工过程中产生振动。
3.切削刀具磨损切削刀具是机械加工中常用的工具,如果刀具磨损严重或者安装不良,就会引起加工过程中的振动。
4.工件材料变形在加工过程中,由于工件材料自身性能的变化,也有可能引起机械振动。
5.进给系统问题进给系统的性能不稳定、传动链条出现松动等问题,会导致机床在工作时的振动。
刀具在加工时,间歇切削会引起刀具的振动,影响加工质量。
二、机械振动的应对措施1.合理选择切削工艺参数在机床的结构设计上,要注重刚性的设计和加强工装的固定,确保机床在加工过程中稳定性。
加强机床的维护保养工作,及时发现并解决机床结构问题。
3.切削刀具的选择和维护合理选择切削刀具,并确保刀具的安装正确、刃磨合适,定期进行刀具的维护和更换工作。
选择质量稳定的工件材料,对材料性能进行精密测试和处理,以减少因材料变形引起的机械振动。
对进给系统进行定期的检查和维护工作,确保传动链条、导轨等部件的稳定性和耐磨性。
6.刀具间歇切削的解决方法对于刀具间歇切削引起的问题,可以采用提高刀具速度、增加刀具的刚度等方法来减少刀具的振动。
三、结语在机械加工中,机械振动是一个常见问题,如果不能得到及时合理的处理,会对加工质量和安全性造成很大影响。
加强对机械振动原因的分析和应对措施的研究非常重要。
通过合理选择加工条件、加强机床结构设计和维护、切削刀具的选择和维护、工件材料处理、进给系统的维护以及解决刀具间歇切削等措施,可以有效减少机械振动的发生,提高机械加工的质量和效率。
机械加工中机械振动的原因解析与应对

机械加工中机械振动的原因解析与应对
机械加工中的机械振动指的是机器在运行过程中的震动和共振现象。
机械振动不仅会影响产品的加工精度和质量,还会对机器本身造成损伤,因此必须引起足够的重视。
以下是机械振动的原因解析与应对措施。
一、机械振动的原因
1.不平衡:机械零件中存在不平衡现象时,发动机转动时会由于离心力产生横向或纵向的振动。
2.共振:当机器设备的固有频率与强制振动频率接近或相等时,就会出现共振现象,引起机器的强烈振动。
3.摩擦和磨损:机械零件的摩擦和磨损会导致运动不平稳,引起机器的振动。
4.不稳定结构:机器结构不够稳定,机械零件的振动会自我放大。
5.加工精度:由于零件加工误差、装配不良等原因,会导致机械零件在运行时振动加剧。
二、机械振动的应对措施
1.动平衡处理:对于不平衡现象严重的零件,应采取动平衡处理,通过在转子上安装调节重量来消除不平衡,降低振动的影响。
2.增加阻尼:在机械设备中增加阻尼器,可以有效地减小机械振动的幅度和频率。
3.改变固有频率:对于因共振引起的振动,可以通过改变机器的结构和材料,改变固有频率,避免共振的出现。
4.加强润滑:保持机器设备的良好润滑状态,减少磨损和摩擦,可以降低机械振动的程度。
5.改善加工质量:严格控制零件加工误差,加强装配质量,提高机器的运行精度,从而减轻机械振动的影响。
综上所述,机械振动是机械加工中必须面对的一个问题。
只有全方位的应对措施,才能保证机器的正常运行,同时也能保证产品加工的质量和精度。
机械加工过程中机械振动的原因及对策分析
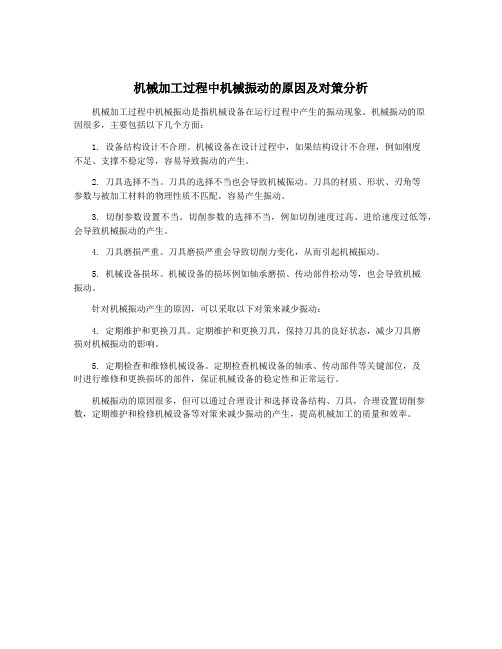
机械加工过程中机械振动的原因及对策分析
机械加工过程中机械振动是指机械设备在运行过程中产生的振动现象。
机械振动的原
因很多,主要包括以下几个方面:
1. 设备结构设计不合理。
机械设备在设计过程中,如果结构设计不合理,例如刚度
不足、支撑不稳定等,容易导致振动的产生。
2. 刀具选择不当。
刀具的选择不当也会导致机械振动。
刀具的材质、形状、刃角等
参数与被加工材料的物理性质不匹配,容易产生振动。
3. 切削参数设置不当。
切削参数的选择不当,例如切削速度过高、进给速度过低等,会导致机械振动的产生。
4. 刀具磨损严重。
刀具磨损严重会导致切削力变化,从而引起机械振动。
5. 机械设备损坏。
机械设备的损坏例如轴承磨损、传动部件松动等,也会导致机械
振动。
针对机械振动产生的原因,可以采取以下对策来减少振动:
4. 定期维护和更换刀具。
定期维护和更换刀具,保持刀具的良好状态,减少刀具磨
损对机械振动的影响。
5. 定期检查和维修机械设备。
定期检查机械设备的轴承、传动部件等关键部位,及
时进行维修和更换损坏的部件,保证机械设备的稳定性和正常运行。
机械振动的原因很多,但可以通过合理设计和选择设备结构、刀具,合理设置切削参数,定期维护和检修机械设备等对策来减少振动的产生,提高机械加工的质量和效率。
机械加工过程中机械振动的原因及对策分析
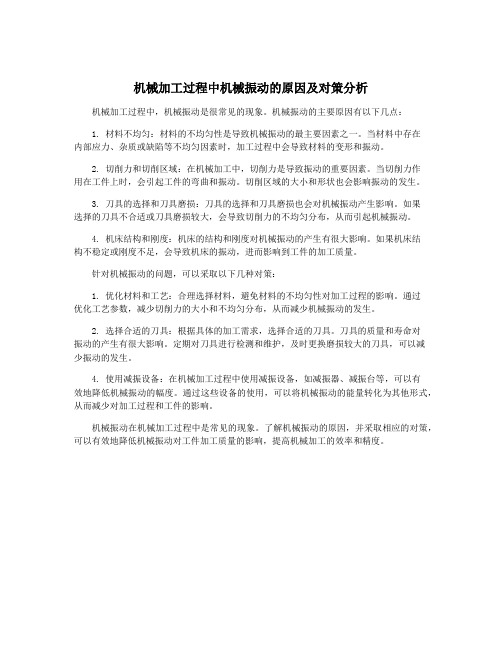
机械加工过程中机械振动的原因及对策分析机械加工过程中,机械振动是很常见的现象。
机械振动的主要原因有以下几点:1. 材料不均匀:材料的不均匀性是导致机械振动的最主要因素之一。
当材料中存在内部应力、杂质或缺陷等不均匀因素时,加工过程中会导致材料的变形和振动。
2. 切削力和切削区域:在机械加工中,切削力是导致振动的重要因素。
当切削力作用在工件上时,会引起工件的弯曲和振动。
切削区域的大小和形状也会影响振动的发生。
3. 刀具的选择和刀具磨损:刀具的选择和刀具磨损也会对机械振动产生影响。
如果选择的刀具不合适或刀具磨损较大,会导致切削力的不均匀分布,从而引起机械振动。
4. 机床结构和刚度:机床的结构和刚度对机械振动的产生有很大影响。
如果机床结构不稳定或刚度不足,会导致机床的振动,进而影响到工件的加工质量。
针对机械振动的问题,可以采取以下几种对策:1. 优化材料和工艺:合理选择材料,避免材料的不均匀性对加工过程的影响。
通过优化工艺参数,减少切削力的大小和不均匀分布,从而减少机械振动的发生。
2. 选择合适的刀具:根据具体的加工需求,选择合适的刀具。
刀具的质量和寿命对振动的产生有很大影响。
定期对刀具进行检测和维护,及时更换磨损较大的刀具,可以减少振动的发生。
4. 使用减振设备:在机械加工过程中使用减振设备,如减振器、减振台等,可以有效地降低机械振动的幅度。
通过这些设备的使用,可以将机械振动的能量转化为其他形式,从而减少对加工过程和工件的影响。
机械振动在机械加工过程中是常见的现象。
了解机械振动的原因,并采取相应的对策,可以有效地降低机械振动对工件加工质量的影响,提高机械加工的效率和精度。
机械加工中机械振动的原因解析与应对

机械加工中机械振动的原因解析与应对机械加工中,机械振动是一个非常常见的问题,它会对加工精度造成影响,同时也会影响加工效率、设备寿命甚至工人的健康。
了解机械振动的原因并采取有效的应对措施是非常重要的。
本文将就机械振动的原因进行解析,并提出相应的应对措施,希望能够对广大机械加工工作者有所帮助。
一、机械振动的原因解析1.加工切削力不平衡在机械加工过程中,切削力是造成机械振动的一大原因。
由于切削刀具的精度问题、工件的不平衡或者安装的不稳定等因素,都会造成切削力的不平衡,从而引起机械振动。
特别是在高速切削时,这种振动会更加显著。
2.机械结构刚度不足机械加工设备的结构刚度对于振动有着重要的影响。
如果机械结构刚度不足,就会导致在工作时产生振动。
特别是一些较为复杂的机械结构,由于其本身的几何形状和加工工艺的限制,往往无法保证其足够的刚度。
3.工件和夹具的不稳定工件和夹具在机械加工过程中,如果安装不稳定或者本身的质量问题,都会造成机械振动。
尤其是一些大型工件,在进行加工时如果夹具的设计和安装不当,容易产生振动。
4.刀具磨损刀具的磨损也是导致机械振动的一个非常重要的原因。
随着切削刀具的使用时间增加,刀具的磨损会导致切削力的不平衡,从而产生振动。
尤其是一些高速切削时,磨损对振动的影响更为显著。
5.传动系统故障机械加工设备的传动系统是保证机械稳定工作的关键组成部分,如果传动链条中出现故障,比如链条松动、皮带松动、齿轮磨损等,都会影响到设备的工作稳定性,从而引起振动。
6.工艺参数不合理在机械加工过程中,一些工艺参数的不合理也会导致机械振动。
比如进给速度过大、切削速度过快、切削深度过大等,都会导致加工时产生振动。
二、机械振动的应对措施1.提高刀具的加工精度首先要提高刀具的加工精度,保证切削刀具的平衡性和稳定性。
在加工时要按照刀具的使用规范,定期进行刀具的检查和维护,及时更换磨损严重的刀具。
加强机械结构刚度是解决机械振动问题的有效方法。
机械加工过程中机械振动的原因及对策分析
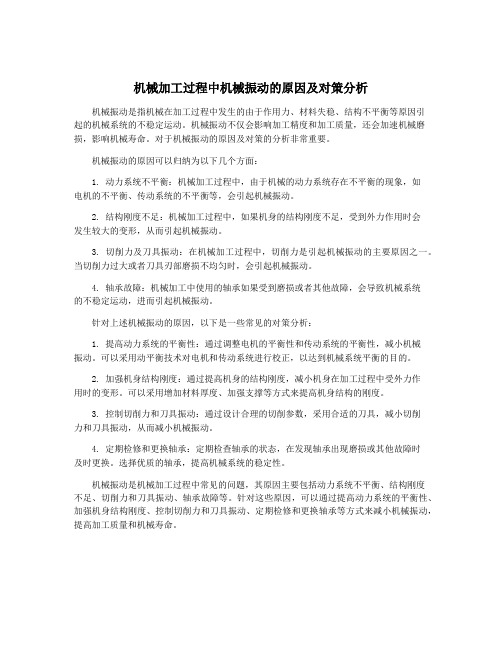
机械加工过程中机械振动的原因及对策分析机械振动是指机械在加工过程中发生的由于作用力、材料失稳、结构不平衡等原因引起的机械系统的不稳定运动。
机械振动不仅会影响加工精度和加工质量,还会加速机械磨损,影响机械寿命。
对于机械振动的原因及对策的分析非常重要。
机械振动的原因可以归纳为以下几个方面:1. 动力系统不平衡:机械加工过程中,由于机械的动力系统存在不平衡的现象,如电机的不平衡、传动系统的不平衡等,会引起机械振动。
2. 结构刚度不足:机械加工过程中,如果机身的结构刚度不足,受到外力作用时会发生较大的变形,从而引起机械振动。
3. 切削力及刀具振动:在机械加工过程中,切削力是引起机械振动的主要原因之一。
当切削力过大或者刀具刃部磨损不均匀时,会引起机械振动。
4. 轴承故障:机械加工中使用的轴承如果受到磨损或者其他故障,会导致机械系统的不稳定运动,进而引起机械振动。
针对上述机械振动的原因,以下是一些常见的对策分析:1. 提高动力系统的平衡性:通过调整电机的平衡性和传动系统的平衡性,减小机械振动。
可以采用动平衡技术对电机和传动系统进行校正,以达到机械系统平衡的目的。
2. 加强机身结构刚度:通过提高机身的结构刚度,减小机身在加工过程中受外力作用时的变形。
可以采用增加材料厚度、加强支撑等方式来提高机身结构的刚度。
3. 控制切削力和刀具振动:通过设计合理的切削参数,采用合适的刀具,减小切削力和刀具振动,从而减小机械振动。
4. 定期检修和更换轴承:定期检查轴承的状态,在发现轴承出现磨损或其他故障时及时更换。
选择优质的轴承,提高机械系统的稳定性。
机械振动是机械加工过程中常见的问题,其原因主要包括动力系统不平衡、结构刚度不足、切削力和刀具振动、轴承故障等。
针对这些原因,可以通过提高动力系统的平衡性、加强机身结构刚度、控制切削力和刀具振动、定期检修和更换轴承等方式来减小机械振动,提高加工质量和机械寿命。
机械加工中机械振动的原因解析与应对
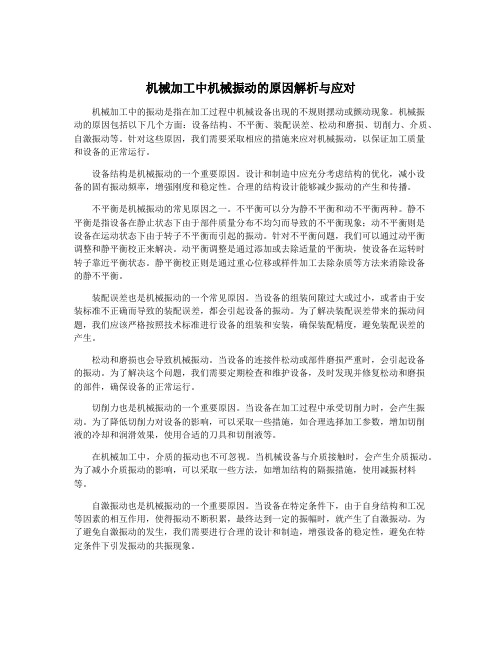
机械加工中机械振动的原因解析与应对机械加工中的振动是指在加工过程中机械设备出现的不规则摆动或颤动现象。
机械振动的原因包括以下几个方面:设备结构、不平衡、装配误差、松动和磨损、切削力、介质、自激振动等。
针对这些原因,我们需要采取相应的措施来应对机械振动,以保证加工质量和设备的正常运行。
设备结构是机械振动的一个重要原因。
设计和制造中应充分考虑结构的优化,减小设备的固有振动频率,增强刚度和稳定性。
合理的结构设计能够减少振动的产生和传播。
不平衡是机械振动的常见原因之一。
不平衡可以分为静不平衡和动不平衡两种。
静不平衡是指设备在静止状态下由于部件质量分布不均匀而导致的不平衡现象;动不平衡则是设备在运动状态下由于转子不平衡而引起的振动。
针对不平衡问题,我们可以通过动平衡调整和静平衡校正来解决。
动平衡调整是通过添加或去除适量的平衡块,使设备在运转时转子靠近平衡状态。
静平衡校正则是通过重心位移或样件加工去除杂质等方法来消除设备的静不平衡。
装配误差也是机械振动的一个常见原因。
当设备的组装间隙过大或过小,或者由于安装标准不正确而导致的装配误差,都会引起设备的振动。
为了解决装配误差带来的振动问题,我们应该严格按照技术标准进行设备的组装和安装,确保装配精度,避免装配误差的产生。
松动和磨损也会导致机械振动。
当设备的连接件松动或部件磨损严重时,会引起设备的振动。
为了解决这个问题,我们需要定期检查和维护设备,及时发现并修复松动和磨损的部件,确保设备的正常运行。
切削力也是机械振动的一个重要原因。
当设备在加工过程中承受切削力时,会产生振动。
为了降低切削力对设备的影响,可以采取一些措施,如合理选择加工参数,增加切削液的冷却和润滑效果,使用合适的刀具和切削液等。
在机械加工中,介质的振动也不可忽视。
当机械设备与介质接触时,会产生介质振动。
为了减小介质振动的影响,可以采取一些方法,如增加结构的隔振措施,使用减振材料等。
自激振动也是机械振动的一个重要原因。
机械加工过程中机械振动的原因及对策分析
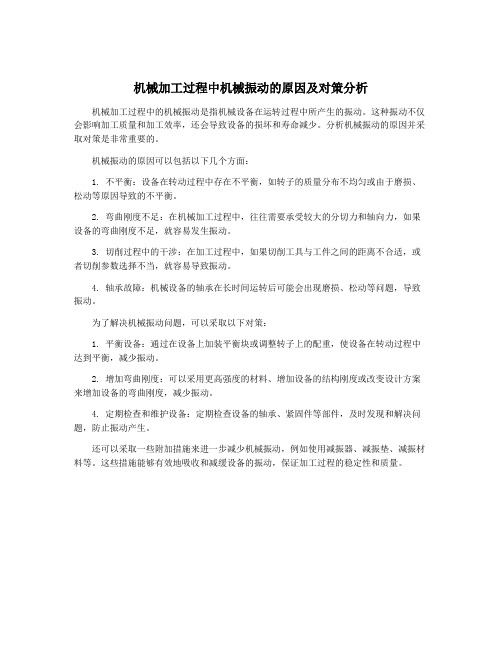
机械加工过程中机械振动的原因及对策分析
机械加工过程中的机械振动是指机械设备在运转过程中所产生的振动。
这种振动不仅会影响加工质量和加工效率,还会导致设备的损坏和寿命减少。
分析机械振动的原因并采取对策是非常重要的。
机械振动的原因可以包括以下几个方面:
1. 不平衡:设备在转动过程中存在不平衡,如转子的质量分布不均匀或由于磨损、松动等原因导致的不平衡。
2. 弯曲刚度不足:在机械加工过程中,往往需要承受较大的分切力和轴向力,如果设备的弯曲刚度不足,就容易发生振动。
3. 切削过程中的干涉:在加工过程中,如果切削工具与工件之间的距离不合适,或者切削参数选择不当,就容易导致振动。
4. 轴承故障:机械设备的轴承在长时间运转后可能会出现磨损、松动等问题,导致振动。
为了解决机械振动问题,可以采取以下对策:
1. 平衡设备:通过在设备上加装平衡块或调整转子上的配重,使设备在转动过程中达到平衡,减少振动。
2. 增加弯曲刚度:可以采用更高强度的材料、增加设备的结构刚度或改变设计方案来增加设备的弯曲刚度,减少振动。
4. 定期检查和维护设备:定期检查设备的轴承、紧固件等部件,及时发现和解决问题,防止振动产生。
还可以采取一些附加措施来进一步减少机械振动,例如使用减振器、减振垫、减振材料等。
这些措施能够有效地吸收和减缓设备的振动,保证加工过程的稳定性和质量。
机械加工过程中机械振动的原因及对策分析

机械加工过程中机械振动的原因及对策分析机械加工过程中出现机械振动的原因较多,主要包括以下几个方面:1.切削力的不平衡:机械加工过程中,切削力的大小和方向会不断变化,如果切削力不平衡,就会引发机械振动。
这主要是由于工件材料的异质性、表面瑕疵等原因导致的切削力不均匀分布。
2.进给速度过大:如果在机械加工过程中进给速度过大,刀具与工件之间会发生剧烈的冲击,从而产生振动。
进给速度过大还会引起切屑的断裂不良、刀具严重磨损等问题。
3.机床刚度不足:机床的刚度不足也是引起机械振动的重要原因。
刚度不足会导致机械系统的固有频率过低,与工件切削频率接近,从而引起共振现象。
4.切削液不当:切削液在机械加工过程中起到冷却润滑的作用,如果切削液的流量、温度、质量不合适,则会导致切削液无法有效冷却刀具和工件,增加切削力并引起振动。
针对上述问题,可以采取以下对策来降低机械振动:1.切削力平衡:选择合适的刀具和进给方式,确保切削力均匀分布。
在加工过程中可以采用动态平衡的方法动态调整刀具和工件的重心位置,提高切削力的平衡性。
2.控制进给速度:根据加工材料的性质和切削条件,合理控制进给速度,避免过大的进给速度引起振动。
如果需要加工高硬度材料,可以采用高速切削技术来提高加工效率,减少机械振动。
3.提高机床刚度:加强机床的刚度和稳定性可以有效抑制机械振动。
可以采用增加机床结构重量、增大导轨尺寸、优化机械系统刚度等措施来提高机床刚度。
4.优化切削液:选择合适的切削液,并设置合理的流量、温度和质量控制,确保切削液能够有效冷却刀具和工件,降低切削力。
还可以通过合理的刀具设计、提高工件材料的均匀性、改善切削过程中的冷却条件等方法来减少机械振动的发生,提高加工质量和效率。
对于特殊要求的加工任务,可以采用振动缓冲系统、动态平衡系统等技术手段来抑制机械振动,实现稳定加工。
机械加工过程中机械振动的原因及对策分析

机械加工过程中机械振动的原因及对策分析机械加工过程中,机械振动是一个普遍存在的问题,因为它不仅会导致精度降低,还会加速机器零件的磨损,甚至损坏设备。
因此,对于机械振动问题的解决非常关键。
本文就对机械振动的原因及对策进行分析。
一、机械振动的原因1、切削过程产生的振动切削过程中弯刀和工件之间的相互作用会产生振动。
机械加工时,刀具切削力的幅度和方向会发生变化,从而在机床或工件上形成振动。
2、结构共振机床和工件都是复杂的机械结构,当机床和工件的自然频率与加工中形成的激振频率相同时,就会产生结构共振现象。
3、加工质量问题如果切削刀具使用时间过长,切削的表面质量不佳,磨损过大等问题,就会导致加工过程中的振动。
4、材料变形在对某些材料进行加工时,因材料本身特性的影响,能量的传递不完善,自然会产生振动。
1、切削后处理切削后,工件表面存在不平整现象,如果直接进行下一步加工,就会产生新一轮的振动。
因此,在切削后应采取必要的光洁磨削或光洁加工处理,以减轻振动产生的影响。
2、提高刀具和夹具的刚性和刚度刀具和夹具的刚性和刚度直接影响到机械加工的质量和效率。
因此,加强刀具和夹具的刚度、抵抗自由度,可以减少振动的产生,并提高精度。
3、控制机床的机械系统误差机床的机械系统误差对机械振动产生了很大的影响。
因此,通过对机床的检修和调整,及时发现和排除机械系统误差,可以降低机械振动产生的风险。
4、选择适当的加工策略不同工件的加工策略会对机械振动产生不同的影响。
正确选择加工策略,调整加工参数,减少工件变形现象,避免产生振动。
三、总结在机械加工过程中,振动是一种常见的问题。
要想避免机械振动,就要在生产过程中采取正确的措施,改进机床、刀具等设备的刚性和刚度,控制机械系统误差,选择适当的加工策略等。
这样,就能高效地完成加工,保证加工精度和效率,进而提高生产效益。
机械加工过程中机械振动的原因及对策分析

机械加工过程中机械振动的原因及对策分析
机械加工过程中的机械振动是指在机床或工件上产生的机械振动现象。
机械振动的原
因可以分为以下几个方面:
1. 刀具与工件的不平衡:刀具与工件的不平衡是引起机械振动的主要原因之一。
刀
具在高速旋转时不平衡会导致振动产生。
3. 刀具与刀架的松动:刀具安装不牢固、刀具松动也会引起机械振动。
刀具松动会
导致刀具与工件之间的相对运动不稳定,从而引起振动。
4. 机床刚度不足:机床刚度不足是引起机械振动的另一常见原因。
机床刚度不足会
导致加工过程中机床产生弯曲变形,使刀具与工件之间的相对位置发生变化,引起振动。
对于机械振动问题,以下是一些常见的对策分析:
1. 动平衡:对刀具、刀架等旋转部件进行动平衡处理,将不平衡量降至最低,减小
机械振动。
2. 调整刀具参数:根据实际情况调整刀具的切削参数,使刀具与工件之间的力平衡,减小机械振动。
3. 固定刀具、刀架:确保刀具、刀架等部件的安装牢固,防止松动引起的振动。
4. 提高机床刚度:通过增加机床的刚度来减小机械振动。
可以通过选用更加稳定的
机床、加强机床的结构设计等方式来提高机床刚度。
5. 使用减振装置:在机床或工件上安装减振装置,减小机械振动。
在机械加工过程中,机械振动是一个常见的问题,会影响加工质量和工作效率。
针对
机械振动问题,可以采取不同的对策,从而减小振动幅度,提高加工精度和稳定性。
机械加工过程中机械振动的原因及对策分析
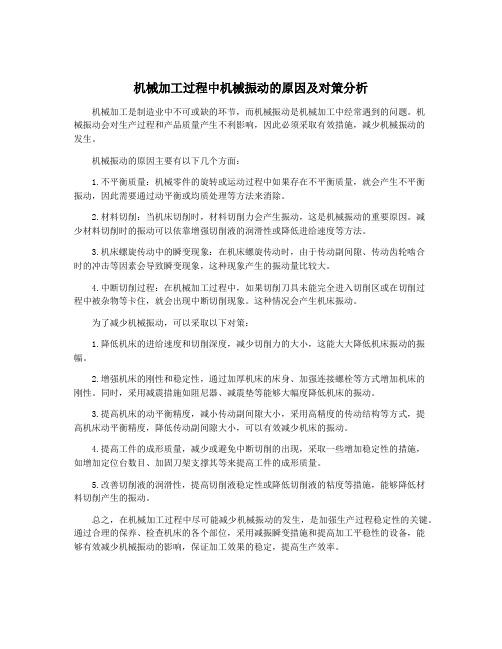
机械加工过程中机械振动的原因及对策分析机械加工是制造业中不可或缺的环节,而机械振动是机械加工中经常遇到的问题。
机械振动会对生产过程和产品质量产生不利影响,因此必须采取有效措施,减少机械振动的发生。
机械振动的原因主要有以下几个方面:1.不平衡质量:机械零件的旋转或运动过程中如果存在不平衡质量,就会产生不平衡振动,因此需要通过动平衡或均质处理等方法来消除。
2.材料切削:当机床切削时,材料切削力会产生振动,这是机械振动的重要原因。
减少材料切削时的振动可以依靠增强切削液的润滑性或降低进给速度等方法。
3.机床螺旋传动中的瞬变现象:在机床螺旋传动时,由于传动副间隙、传动齿轮啮合时的冲击等因素会导致瞬变现象,这种现象产生的振动量比较大。
4.中断切削过程:在机械加工过程中,如果切削刀具未能完全进入切削区或在切削过程中被杂物等卡住,就会出现中断切削现象。
这种情况会产生机床振动。
为了减少机械振动,可以采取以下对策:1.降低机床的进给速度和切削深度,减少切削力的大小,这能大大降低机床振动的振幅。
2.增强机床的刚性和稳定性,通过加厚机床的床身、加强连接螺栓等方式增加机床的刚性。
同时,采用减震措施如阻尼器、减震垫等能够大幅度降低机床的振动。
3.提高机床的动平衡精度,减小传动副间隙大小,采用高精度的传动结构等方式,提高机床动平衡精度,降低传动副间隙大小,可以有效减少机床的振动。
4.提高工件的成形质量,减少或避免中断切削的出现,采取一些增加稳定性的措施,如增加定位台数目、加固刀架支撑其等来提高工件的成形质量。
5.改善切削液的润滑性,提高切削液稳定性或降低切削液的粘度等措施,能够降低材料切削产生的振动。
总之,在机械加工过程中尽可能减少机械振动的发生,是加强生产过程稳定性的关键。
通过合理的保养、检查机床的各个部位,采用减振瞬变措施和提高加工平稳性的设备,能够有效减少机械振动的影响,保证加工效果的稳定,提高生产效率。
机械加工中机械振动的原因解析与应对
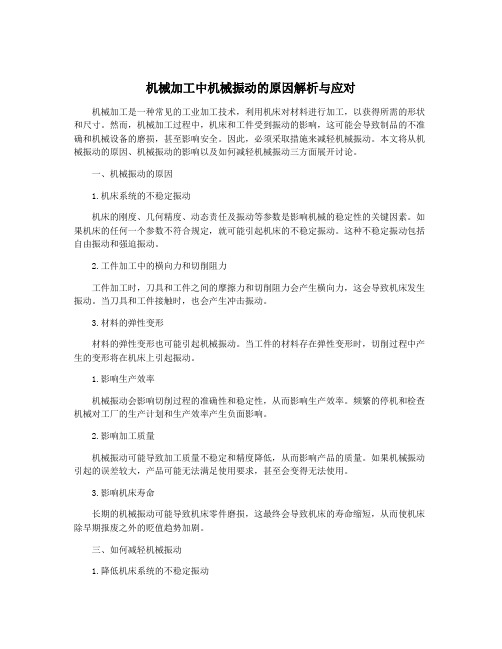
机械加工中机械振动的原因解析与应对机械加工是一种常见的工业加工技术,利用机床对材料进行加工,以获得所需的形状和尺寸。
然而,机械加工过程中,机床和工件受到振动的影响,这可能会导致制品的不准确和机械设备的磨损,甚至影响安全。
因此,必须采取措施来减轻机械振动。
本文将从机械振动的原因、机械振动的影响以及如何减轻机械振动三方面展开讨论。
一、机械振动的原因1.机床系统的不稳定振动机床的刚度、几何精度、动态责任及振动等参数是影响机械的稳定性的关键因素。
如果机床的任何一个参数不符合规定,就可能引起机床的不稳定振动。
这种不稳定振动包括自由振动和强迫振动。
2.工件加工中的横向力和切削阻力工件加工时,刀具和工件之间的摩擦力和切削阻力会产生横向力,这会导致机床发生振动。
当刀具和工件接触时,也会产生冲击振动。
3.材料的弹性变形材料的弹性变形也可能引起机械振动。
当工件的材料存在弹性变形时,切削过程中产生的变形将在机床上引起振动。
1.影响生产效率机械振动会影响切削过程的准确性和稳定性,从而影响生产效率。
频繁的停机和检查机械对工厂的生产计划和生产效率产生负面影响。
2.影响加工质量机械振动可能导致加工质量不稳定和精度降低,从而影响产品的质量。
如果机械振动引起的误差较大,产品可能无法满足使用要求,甚至会变得无法使用。
3.影响机床寿命长期的机械振动可能导致机床零件磨损,这最终会导致机床的寿命缩短,从而使机床除早期报废之外的贬值趋势加剧。
三、如何减轻机械振动1.降低机床系统的不稳定振动为了降低机床的不稳定振动,可以采取以下措施:优化机床的结构和几何精度,加强机床刚度,减少或消除机床的机械间隙,改造机床动态助力系统等。
2.减少横向力和切削阻力可以通过控制工件加工过程中的摩擦力和切削阻力来减少机械振动。
采用合适的刀具和润滑油的选择,对工件进行适当的冷却可以减少摩擦力和切削阻力。
3.提高机床刚度机床刚度是影响机床稳定性的重要因素。
为了提高机床的刚度,可以调整机床的结构设计,选用高质量的材料,以及保障机床及其零部件的充分刚性等。
机械加工中机械振动的原因解析与应对
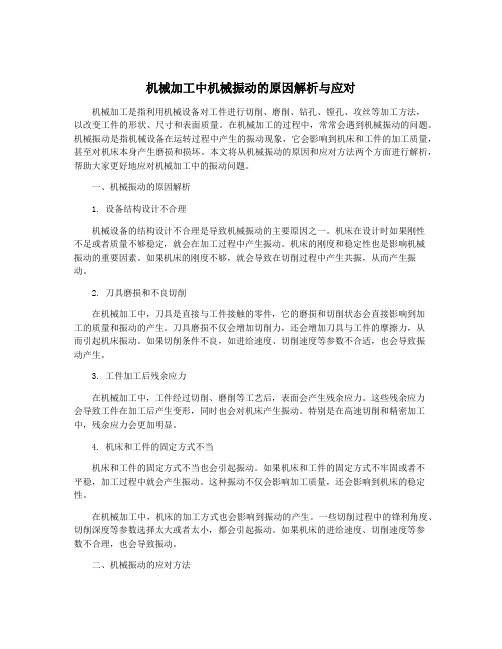
机械加工中机械振动的原因解析与应对机械加工是指利用机械设备对工件进行切削、磨削、钻孔、镗孔、攻丝等加工方法,以改变工件的形状、尺寸和表面质量。
在机械加工的过程中,常常会遇到机械振动的问题。
机械振动是指机械设备在运转过程中产生的振动现象,它会影响到机床和工件的加工质量,甚至对机床本身产生磨损和损坏。
本文将从机械振动的原因和应对方法两个方面进行解析,帮助大家更好地应对机械加工中的振动问题。
一、机械振动的原因解析1. 设备结构设计不合理机械设备的结构设计不合理是导致机械振动的主要原因之一。
机床在设计时如果刚性不足或者质量不够稳定,就会在加工过程中产生振动。
机床的刚度和稳定性也是影响机械振动的重要因素。
如果机床的刚度不够,就会导致在切削过程中产生共振,从而产生振动。
2. 刀具磨损和不良切削在机械加工中,刀具是直接与工件接触的零件,它的磨损和切削状态会直接影响到加工的质量和振动的产生。
刀具磨损不仅会增加切削力,还会增加刀具与工件的摩擦力,从而引起机床振动。
如果切削条件不良,如进给速度、切削速度等参数不合适,也会导致振动产生。
3. 工件加工后残余应力在机械加工中,工件经过切削、磨削等工艺后,表面会产生残余应力。
这些残余应力会导致工件在加工后产生变形,同时也会对机床产生振动。
特别是在高速切削和精密加工中,残余应力会更加明显。
4. 机床和工件的固定方式不当机床和工件的固定方式不当也会引起振动。
如果机床和工件的固定方式不牢固或者不平稳,加工过程中就会产生振动。
这种振动不仅会影响加工质量,还会影响到机床的稳定性。
在机械加工中,机床的加工方式也会影响到振动的产生。
一些切削过程中的锋利角度、切削深度等参数选择太大或者太小,都会引起振动。
如果机床的进给速度、切削速度等参数不合理,也会导致振动。
二、机械振动的应对方法为了降低机械振动,首先要从设备结构设计方面入手,加强机械设备的刚度和稳定性,提高机床的机械传动效率,改进机床结构,减少共振现象,使机床的设计更加合理化。
机械加工中机械振动的原因解析与应对

机械加工中机械振动的原因解析与应对
机械加工中的机械振动是指在机械加工过程中产生的机械系统的非均匀运动现象。
机械振动的产生原因很多,主要包括以下几个方面:
1.切削力引起的振动:切削力在机床和工件之间传递,当切削力不平衡时,就会引起机床和工件的振动。
2.零件不平衡引起的振动:在机械加工过程中,如果工件本身不平衡,或者夹具装夹不平衡,都会导致机床的振动。
3.切削过程中的共振现象:机械系统有自然振动频率,当切削过程中的振动频率与机械系统的自然频率相近时,就会发生共振现象,从而引起振动。
4.机床刚度不足引起的振动:机床的刚度直接影响着机床的稳定性和阻尼效果,如果机床刚度不足,就会导致振动加剧。
为了应对机械振动,可以采取以下几种措施:
1.提高机械系统的刚度:通过加强机床的结构设计和制造工艺,增加机床的刚度,从而减少机械振动的发生。
2.使用平衡装置:对工件和夹具进行平衡处理,减小零件的不平衡量,从而减少振动。
3.优化切削参数:合理选择切削速度、进给速度和切削深度等切削参数,避免过大或过小的切削力。
4.选用合适的切削工具:选择合适的切削工具,如刀具的刚度、刀具的几何形状等,从而减小切削力和振动。
5.加强润滑和冷却:合理使用润滑剂和冷却剂,保持切削过程中工件和切削工具的表面温度,减少摩擦和热变形,从而减小振动。
机械振动在机械加工中是一个普遍存在的问题,但通过合理的措施可以减少和控制振动,提高机械加工的质量和效率。
- 1、下载文档前请自行甄别文档内容的完整性,平台不提供额外的编辑、内容补充、找答案等附加服务。
- 2、"仅部分预览"的文档,不可在线预览部分如存在完整性等问题,可反馈申请退款(可完整预览的文档不适用该条件!)。
- 3、如文档侵犯您的权益,请联系客服反馈,我们会尽快为您处理(人工客服工作时间:9:00-18:30)。
When the lives of employees or national property are endangered, production activities are stopped to rectify and eliminate dangerous factors.
(安全管理)
单位:___________________
姓名:___________________
日期:___________________
机械加工时机械振动原因及对策
分析(新编版)
机械加工时机械振动原因及对策分析(新编
版)
导语:生产有了安全保障,才能持续、稳定发展。
生产活动中事故层出不穷,生产势必陷于混乱、甚至瘫痪状态。
当生产与安全发生矛盾、危及职工生命或国家财产时,生产活动停下来整治、消除危险因素以后,生产形势会变得更好。
"安全第一"
的提法,决非把安全摆到生产之上;忽视安全自然是一种错误。
随着科学技术的飞速发展和人们生活水平得不断提高,当前人们逐渐对机械加工行业的发展重视起来。
众所周知,我们在进行具体加工操作的过程中应该注重机械振动对机械加工流程所造成的相关影响,因为只有对机械加工时机械振动具体原因进行分析并加以解决才能在一定程度上保证生产质量和加工效率。
本文针对我国当前机械加工现状,对机械振动产生原因进行详细分析和阐述并总结出合理对策,希望为我国机械加工行业的发展贡献出一份力量。
广义而言,在实际生产生活中应用到振动原理进行正常工作运行的项目有很多种类,其中包括中标和打桩机等,同时在进行水泥浇筑的过程中也会运用到振动机。
但是过多振动会带来一定负面影响,并且也会危害身心健康,过大机械振动会造成机床加工精度降低和机床仪表测精度降低以及机床控制系统失灵等状况发生。
机械加工时机械振动原因探究
1.1.机械加工时机械振动原因经验推断
在进行对相应更换轴承进行安装之前我们要对其进行较为严格的挑选,要确保手感框量和滚珠表面质量以及相关空负噪音等无误,并且轴承内圈加精度和轴承外圈加工精度二者中不存在任何质量问题。
而在实施轴承配合过程中,其与轴承箱之间的精度误差应控制在规定合理范围之内,且确保轴承外圈并无一定转动状况产生。
轴承箱中添油量一定要适中且必须要对机体地脚螺栓加以紧固,在紧固的基础上施加隔震橡胶。
电机安装统轴度要求与风机轴安装同轴度要求都相对较高,应该在满足机械加工使用需求的状态下才能予以安装。
在进行试车的过程中,车辆轴承箱振动效果明显,此时不排除风机叶轮产生动平衡状况的可能性。
基于电机拖动且高速运转时,对应叶轮轴会暴露在风机壳和相关轴承箱二者之间,我们在用肉眼看时其是一条模糊曲线,但当电机低俗运转时,通过千分表进行测量之后会发现其按周期性进行跳动。
弓状回转现状是由同一轴承滚珠直径间差异所造成,另外一种情况就是由风机轴弯曲所造成的。
C630车床是当前我国进行机械加工生产中较为常用的一种车床,通过对C630轴承和对C630风机轴实施测试实践我们会发现,相关风机轴正常做回转运动时会出现一定的径向跳动状况且风机轴局部最大跳动量为±0.32mm,此时排除
珠体直径差异的可能性。
综上所述,当我们在进行新轴更换且风机能够正常平稳运行时,风机叶轮便不会出现动平衡等有关问题。
图为风机叶轮矫正示意:
图一风机叶轮矫正示意图
1.2.机械加工时机械振动力学动因分析
风机轴在固定径向跳动量状态下运转时所产生振动的原因是我们严密切关注的问题之一。
一般而言,风机轴和电机轴二者之间的联接是以相关弹性联轴器作为主要联接手段的,假设此时联轴器端是较为自由的运行状态且忽略风机轴自重情况,之后在此基础上进行通轴简化。
当轴角速度呈逐渐递增趋势时,其分母会减小,此时挠度会随着角速度的增大而增大,若没有收到阻尼影响其挠度值会不断加大,上述状况说明了回转体会遭到一定变形且会被破坏。
当风机转速与轴临界转速二者已处避开状态时便不会产生破坏性振动效应。
机械加工时防机械振动策略探究
2.1.合理控制切削用量和选择刀具几何参数
当机械出现自动状况且要考虑提高相应机械加工生产效率时应该采用高速切削方法最为适宜,选取较大进给量切削深度和较小进给量
切削深度才能在一定程度上减小机械加工机械振动机率。
需要强调,影响参数的主要原因大体分为主偏角和前角两种,当几何参数为90时振幅为最小,切削力在前脚方向上最小且也最大,但是传统机械加工工艺中其刚度方向与前脚方向相比较为优越,所以此时不会出现机械振动状况。
2.2.提高机械加工时加工工艺抗振性能
正确的做法是,我们应在提高机械加工工艺接触刚度的基础上对相应接触面进行刮研,之后通过减小轴承间隙对机械滚动轴承实施预紧力施加以至提高顶尖孔研磨品质。
在对细长轴进行加工的过程中,细长轴工件刚性相对较差且极易发生弯曲和变形,当出现机械振动状态时,我们应该用辅助支承来进行机械设备抗振性能提高。
与此同时,应该适当减小刀具的运行延伸长度,采用切向刚度性能较好的刀杆可以有效避免相应弯曲高频振动。
2.3.调整刚度比以及合理运用减振装置
振型刚度比和振型组合都会在机械加工造成一定振动影响,产生此种状况的主要原因是因为受到振型耦合原理影响,应该科学有效的对二者之间关系进行细节调整,之后在此基础上提高机械加工运行系统的抗振性以至防止自激状况产生。
安装减振装置时上述方法不可行
时才予以运用,消振装置和减振装置是防止和制约机械振动状况产生的优良方案之一,减振装置应安装在机械加工工艺系统流程之中,同时其也会对防止机械设备自激振动起到良好效果。
综上所述,只有对机械加工时机械振动具体原因进行分析并加以解决才能在一定程度上保证生产质量和加工效率。
本文针对机械加工时机械振动原因进行分析,从相关振动产生经验和动力学原因两个方面进行阐述,之后提出了控制切削用量和选择刀具几何参数、提高机械加工时加工工艺抗振性能和调整刚度比以及合理运用减振装置等有效防振措施,希望为我国机械加工行业领域的发展那提供合理化建议。
XX设计有限公司
Your Name Design Co., Ltd.。