精益生产七大浪费课程
精益生产之七大浪费

精益生产之七大浪费精益生产是一种以最小化浪费为目标,通过优化流程和提高效率来提高产品质量和客户满意度的管理方法。
在精益生产中,有七大浪费被认为是造成资源浪费和低效率的主要原因,它们是:过产、等待、运输、不合格、运动、库存和过程错误。
1. 过产(Overproduction):过产是指在没有实际需求的情况下进行生产活动,导致产品过度积压和资源浪费。
这不仅会给企业带来高成本,还会增加库存量和缩短产品寿命。
2. 等待(Waiting):等待是指生产过程中出现的不必要的停顿和延迟。
这可能是由于设备故障、物料不足、工人缺席等原因导致的。
等待会降低生产效率,增加生产周期,延迟产品交付。
3. 运输(Transportation):运输是指不必要的材料和产品的长距离运输。
这使得运输成为了一个独立的过程,需要额外的时间和资源。
这些额外的步骤可能会导致物料的损坏、遗失和延迟,进一步增加了生产成本。
4. 不合格(Defects):不合格是指生产中出现的错误、缺陷和质量问题。
不合格的产品需要进行修正、重新制造或报废,这增加了不必要的时间和资源。
这不仅会导致生产延误,还会降低产品质量和客户满意度。
5. 运动(Motion):运动是指工人在生产过程中进行不必要的移动和动作。
这可能是由于生产线布局不合理、工具和设备摆放不当等原因导致的。
这增加了工人的体力消耗,降低了生产效率,也增加了人为错误的可能性。
6. 库存(Inventory):库存是指未经加工的原材料和半成品的储存量。
过多的库存可能会导致资金占用、过期损失、储存空间浪费等问题。
此外,库存过多也会隐藏潜在的问题,如质量问题和需求变化的风险。
7. 过程错误(Processing):过程错误是指生产过程中出现的不必要的重复、增补和调整。
这可能是由于不合理的工艺流程、工具和设备的不良设计等原因导致的。
这会增加生产成本和时间,降低生产效率和产品质量。
有效管理和消除以上七大浪费是精益生产的关键。
精益生产中的七大浪费及改善方法
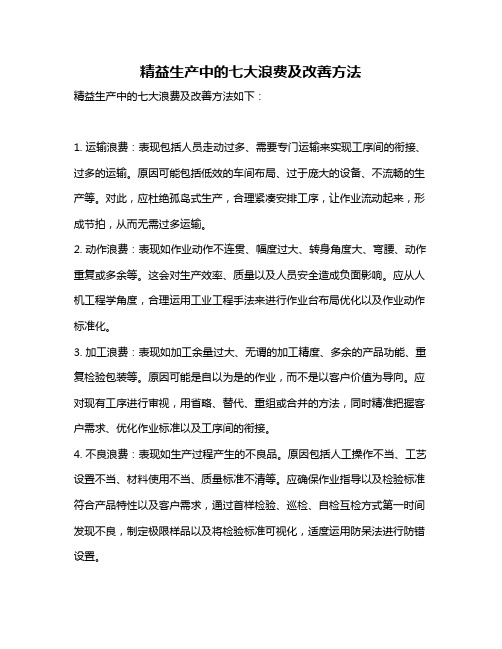
精益生产中的七大浪费及改善方法精益生产中的七大浪费及改善方法如下:1. 运输浪费:表现包括人员走动过多、需要专门运输来实现工序间的衔接、过多的运输。
原因可能包括低效的车间布局、过于庞大的设备、不流畅的生产等。
对此,应杜绝孤岛式生产,合理紧凑安排工序,让作业流动起来,形成节拍,从而无需过多运输。
2. 动作浪费:表现如作业动作不连贯、幅度过大、转身角度大、弯腰、动作重复或多余等。
这会对生产效率、质量以及人员安全造成负面影响。
应从人机工程学角度,合理运用工业工程手法来进行作业台布局优化以及作业动作标准化。
3. 加工浪费:表现如加工余量过大、无谓的加工精度、多余的产品功能、重复检验包装等。
原因可能是自以为是的作业,而不是以客户价值为导向。
应对现有工序进行审视,用省略、替代、重组或合并的方法,同时精准把握客户需求、优化作业标准以及工序间的衔接。
4. 不良浪费:表现如生产过程产生的不良品。
原因包括人工操作不当、工艺设置不当、材料使用不当、质量标准不清等。
应确保作业指导以及检验标准符合产品特性以及客户需求,通过首样检验、巡检、自检互检方式第一时间发现不良,制定极限样品以及将检验标准可视化,适度运用防呆法进行防错设置。
5. 等待浪费:表现如人员(以及设备)在等待,或者有时忙、有时闲的不均衡现象。
原因如生产线品种切换、工作量少、时常缺料、设备闲置等。
应实施生产均衡化,快速换模技术的运用,全员生产性防护,多技能工,消除不良浪费,提升供应商水准。
6. 过量生产:这是常被视为最大的浪费。
其结果导致库存、资金的占用以及潜在的报废风险。
应形成一个流、节拍化生产。
“一个流生产”是指从毛坯投入成品产出的整个制造加工过程,零件始终处于不停滞、不堆积、不超越的状态。
每道工序加工完一个制件后立即流到下一工序;工序间的在制品数量不超过前工序的装夹数量。
零件的运动不间断、不超越、不落地。
只有合格的产品才允许往下一道工序流。
节拍化生产要求是需求节拍与生产节拍平衡。
精益生产之七大浪费(PPT 36页)
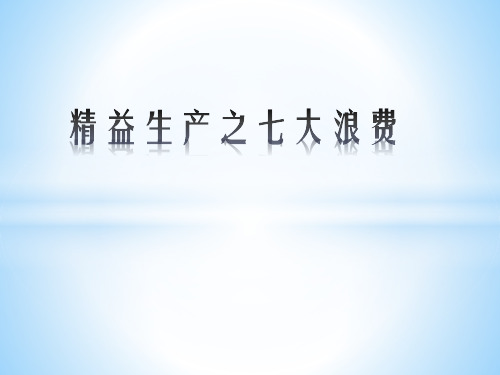
过量生产的危害:
直接造成 成本增加!
1)提前消耗了人工费和管理费等费用。
2)把“等待的浪费”隐性化,在等待的时间做了“多 余的”工作。
3)造成产品的积压,使生产周期变长,质量衰减
4)迫使作业空间变大,造成搬运和走动的浪费,并带 来安全隐患。
5)积压大量的资金,企业因此多付利息
6)导致信息传递不畅,导致管理者无法判断生产线正 常或异常的状态。
• 13、无论才能知识多么卓著,如果缺乏热情,则无异 纸上画饼充饥,无补于事。Sunday, October 18, 202018-
Oct-2020.10.18
• 14、我只是自己不放过自己而已,现在我不会再逼自 己眷恋了。20.10.1803:42:5618 October 202003:42
2020 3:42:56 AM03:42:562020/10/18
• 11、自己要先看得起自己,别人才会看得起你。10/18/
谢 谢 大 家 2020 3:42 AM10/18/2020 3:42 AM20.10.1820.10.18
• 12、这一秒不放弃,下一秒就会有希望。18-Oct-2018 October 202020.10.18
定义: 人员以及设备等资源的空闲。
例如: 人等机、人等料、机等人、以及换生产线引起的等待
产生原因: 1、生产线的品种切换 2、工作量不均衡 3、时常缺料,设备闲置 4、上工序延误,下游无 事可做 5、设备发生故障 6、生产线工序不平衡 7、制造通知或设计图未 送达
据统计: 制造费用的25-40%用于搬运 生产制造时间40%以上用于搬运和滞留 安全事故50%在搬运过程中发生 搬运使不良增加了20%
•
6、意志坚强的人能把世界放在手中像 泥块一 样任意 揉捏。 2020年 10月18 日星期 日上午 3时42 分56秒0 3:42:56 20.10.1 8
消除生产现场七大浪费PPT课件

02
利用工业互联网技术实现设备联网、数据采集和分析,优化生
产过程和决策。
学习并借鉴先进企业的经验和技术
03
关注行业发展趋势,学习并借鉴国内外先进企业的经验和技术,
持续改进和优化生产过程。
建立有效的质量管理体系
1 2
制定严格的质量标准和检验流程
确保产品符合客户要求和行业标准,降低不良品 率和返工率。
消除生产现场七大浪费ppt课 件
• 引言 • 生产现场七大浪费 • 消除浪费的方法与策略 • 案例分析 • 结论
01
引言
浪费的定义与影响
浪费定义
在生产现场中,任何超出生产产 品所必需的、不能创造价值的活 动或因素。
浪费影响
降低生产效率、增加成本、降低 产品质量和竞争力。
生产现场浪费的普遍性
普遍存在于各种规模 和类型的企业中。
建立员工建议和改进机制, 鼓励员工提出改进意见, 提高员工的积极性和参与 度。
建立奖励制度
对在消除浪费和改进生产 过程中表现优秀的员工给 予奖励,激发员工的积极 性。
引入先进的生产技术
采用自动化和智能制造技术
01
通过引入自动化设备和智能制造系统,降低人工操作和错误率,
提高生产效率和质量。
应用工业互联网技术
加强质量意识培训
提高员工对质量的认识和重视程度,培养员工自 主质量管理的能力。
3
建立质量信息反馈机制
及时收集和分析质量信息,针对问题采取改进措 施,持续优化产品质量。
04
案例分析
企业A的精益生产实践
总结词:成功实施
详细描述:企业A通过实施精益生产,成功地减少了生产现场的浪费,提高了生 产效率和产品质量。他们在改进生产流程、优化生产线布局和加强员工培训方面 取得了显著成果。
列举精益生产中的七大浪费
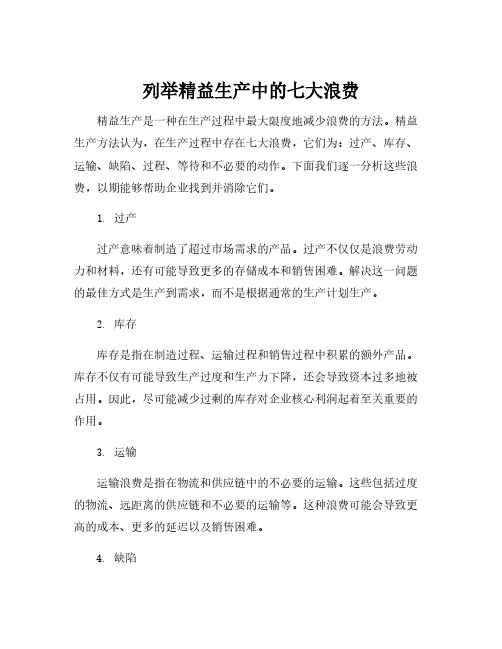
列举精益生产中的七大浪费精益生产是一种在生产过程中最大限度地减少浪费的方法。
精益生产方法认为,在生产过程中存在七大浪费,它们为:过产、库存、运输、缺陷、过程、等待和不必要的动作。
下面我们逐一分析这些浪费,以期能够帮助企业找到并消除它们。
1. 过产过产意味着制造了超过市场需求的产品。
过产不仅仅是浪费劳动力和材料,还有可能导致更多的存储成本和销售困难。
解决这一问题的最佳方式是生产到需求,而不是根据通常的生产计划生产。
2. 库存库存是指在制造过程、运输过程和销售过程中积累的额外产品。
库存不仅有可能导致生产过度和生产力下降,还会导致资本过多地被占用。
因此,尽可能减少过剩的库存对企业核心利润起着至关重要的作用。
3. 运输运输浪费是指在物流和供应链中的不必要的运输。
这些包括过度的物流、远距离的供应链和不必要的运输等。
这种浪费可能会导致更高的成本、更多的延迟以及销售困难。
4. 缺陷产品缺陷可能导致废品产生、产品延迟、客户不满、额外成本等问题。
这个问题通常涉及到的是特定生产过程或质量管控方面的基础问题。
企业应该尽可能及时发现和纠正这些错误以减少缺陷的出现。
5. 过程过程的重要作用是提高生产效率和生产效益。
如果过程中不断出现障碍,那么生产效率将大打折扣。
因此,企业应该通过样本分析、流程再造、员工培训等一系列措施来发现和解决过程中的问题。
6. 等待等待浪费通常是由周期时间差异、部件等待、人员速度不匹配等原因导致的。
这些问题可能导致工作环境不畅、效率低下。
因此,企业应该加强工作人员的培训、改进生产流程并确保供应链更稳定。
7. 不必要的动作不必要的动作可能是生产过程中一些不必要的或重复的动作。
这些问题通常是由于工人培训不足、生产流程和设备不完善,以及管理不到位等多种原因造成的。
因此,企业应该加强流程管理和员工培训以加强工作流程。
同时,确保员工有必要的设备和工具,尽可能自动化流程,降低人工干预。
总之,寻找和消除七大浪费是精益生产法的核心理念之一。
精益生产管理基础消除七大浪费
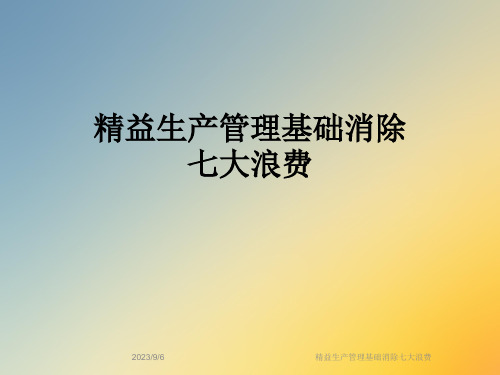
2.浪费的种类
浪费的种类
1.制造过多的浪费 2.等待的浪费 3.搬运的浪费 4.加工的浪费 5.库存的浪费 6.动作的浪费 7.制作不良的浪费
精益生产管理基础消除七大浪费
3.“七大浪费”之详 介
无其它好处
•会把等待的浪费隐藏起来,掩盖稼动不够的问题
•会使制程间积压在制品,制程时间变长,现场工作
空间变大 •会产生搬运、堆积的浪费 •使先进先出的工作产生困难 •会造成库存空间的浪费
?
精益生产管理基础消除七大浪费
对策:
1.制造过多的浪费 •顾客为中心的弹性生产系统
•单件流动—一个流生产线
•看板管理的贯彻
•快速换线换模
•少人化的作业方式
原因:
•人员过剩 •设备稼动过剩 •生产浪费大 •业务订单预测有误 •生产计划与统计错误
•均衡化生产
注意:
•生产速度快并不代表效率高 •设备余力并非一定是埋没成本 •生产能力过剩时,应尽量先考虑减 少作业人员,但并非辞退人员,而 是更合理、更有效率地应用人员
精益生产管理基础消除七大浪费
对策:
•采用均衡化生产 •制品别配置—一个流生产 •防误措施 •自动化及设备保养加强 •实施目视管理 •加强进料控制
注意:
•自动化不要闲置人员 •供需及时化 •作管理点数削减
精益生产管理基础消除七大浪费
3.搬运的浪费
不必要的移动及把东西暂放在一旁
不必要的搬运、工作的移动、预置、改装以及长距离的搬 运流程和活性度差等
1.制造过多的浪费 案例
生产的调配方案: •窗框班每班借出5人至硬包边班, 由13人生产窗框,标时30pcs/hr •前桥线抽调两人至滑道线,12hr 生产
JIT精益生产—七大浪费PPT课件

15
七大浪费之 6:过度加工 OVER PROCESSING
超出必要范围 画蛇添足 不必要的检验 太多审批 太多花样
16
Over Processing 过度加工
如何拼写?
How do you spell that?
17
七大浪费之 7 :次品 DEFECTS
物品 设备 信息 服务 …… 凡是不符合客户要求的
37
发现浪费方法之 3
1. VSM 价值流 2. Gemba 去现场 3. 5S 整理整顿 4. Visual Control 可视化管理 5. Layout 布局 6. Standard Work 标准作业
38
5S
Sort-----------Seiri -------分类 Set in order--Seiton------定位 Shine---------Seiso -------擦亮 Standardize--Seiketsu--- 标准化 Sustain-------Shitsuke ---保持(素养)
便区分。
目的:排除寻找的浪费。 “三定”原则:
定位置:多思考易于“归位”的方法; 定数量:没有数量管制,位置将无法确定; 定标识:让任何人能一看就明白。
44
44
5S---SHINE 擦亮
每天清理作业区域 如有必要增加频率 边擦拭边检查物品是否有短少,破损,裂痕,
跑冒滴漏 想些办法防止物品变脏
45
3-S:清扫
有事时去现场
发生问题时应该先去现场,不要在办公室里听汇 报。
到现场后立即检查,只问事件过程,不急着下结 论。
采取临时措施处置。 用QAS方法检查流程控制点,更新流程。 一个月后回顾新流程的有效性。
精益管理七大浪费

03
激励机制:设立持续 改进的激励机制,鼓 励员工参与
04
持续沟通:建立持续 改进的沟通渠道,及 时反馈问题和建议
05
持续改进计划:制定 持续改进的计划,明 确目标和方法
06
持续改进成果展示: 展示持续改进的成果, 激发员工积极性
持续改进的方法和工具
持续改进的方法:PDCA循环、六西格玛、 精益生产、持续改进计划
05
跟踪评估:对实施计划进行 跟踪和评估,确保消除浪费 的效果得到持续改善
02
制定目标:设定消除浪费的 目标和期限
04
实施计划:按照制定的方案, 分阶段、分步骤实施消除浪 费的计划
实施消除浪费的措施
01
识别浪费: 识别并记录 生产过程中 的浪费现象
02
制定计划: 制定消除浪 费的具体计
划和措施
03
培训员工: 对员工进行 消除浪费的 培训和教育
04
持续改进: 持续改进生 跟踪评估消 除浪费的效 果,并进行 调整和优化
评估消除浪费的效果
设定明确的目标:明确消除 浪费的目标和预期效果
01
收集数据:收集与消除浪费
相关的数据,如时间、成本、 03
质量等
持续改进:根据分析结果,
生产过剩:生产过多或过早, 导致库存积压
等待浪费:等待材料、设备 或人员,导致时间浪费
运输浪费:不必要的运输, 导致时间和成本的浪费
过度加工:不必要的加工, 导致时间和成本的浪费
库存浪费:过多的库存,导 致时间和空间的浪费
动作浪费:不规范的操作, 导致时间和效率的浪费
管理浪费:不合理的管理制 度,导致时间和资源的浪费
浪费的负面影响
增加成本:浪费导致 生产成本上升,降低
精益生产中的七大浪费..课件

07
七大浪费之六:等待
定义与现象
等待浪费是指生产过程中,由于各种原因导致机器、员工、物料等处于停滞状态,无法继续进行生产 的情况。
常见现象包括:设备故障、物料短缺、人员休息等。
产生原因
生产计划不准确
计划与实际需求不匹配,导致 物料短缺或过多。
设备维护不当
设备故障频繁,维修时间长, 影响生产进度。
产生原因
过量加工浪费的产生 主要有以下几个原因
1. 缺乏有效的生产计 划和调度系统,导致 生产安排不合理,出 现了过多的加工任务 。
2. 缺乏对客户需求和 市场变化的了解,生 产出的产品超过了实 际需要。
3. 过于追求生产效率 ,忽略了产品质量和 资源利用效率。
4. 缺乏有效的质量控 制体系,导致部分产 品需要返工或重新加 工。
09
案例分析与实践建议
企业实践案例
某制造型企业通过识别七大浪费 ,成功减少了生产成本并提高了
生产效率。
某零售企业通过对员工进行七大 浪费的培训,成功提高了客户满
意度和销售额。
某医疗保健机构通过消除七大浪 费,提高了医疗服务的质量和效
率。
个人实践建议
了解七大浪费的概念 和识别方法,提高对 精益生产的认识。
制定设备维护计划,定期检查、保养设备, 提高设备使用寿命和稳定性。
优化生产流程
对生产流程进行优化,减少生产瓶颈和物料 流通障碍,提高生产效率。
08
七大浪费之七:过量加工
定义与现象
• 过量加工浪费是指企业对于产品或服务进行了超过 实际需要的加工,或者对于产品进行了超过客户要 求的加工。这种现象通常会导致生产效率降低,生 产成本增加,甚至可能影响产品质量。
增强市场竞争力
精益生产之七大浪费培训资料

影响:增加成本、降低生产效率、影响产 品质量 单击此处输入你的正文,请阐述观点
案例分析:某企业精益生产实践案例 单击此处输入你的正文,请阐述观点
影响:增加运输成本、降低生产效率、影 响产品质量 精益生产之七大浪费培训资
培训效果评估:通过问卷调查、考试等方 式对培训效果进行评估 单击此处输入你的正文,请阐述观点
影响:增加生产成本,降低生产效率,影 响产品质量 精益生产之七大浪费培训资
料 精益生产之七大浪费培训资料
产生原因及影响:针对每种浪费进行深入 分析,提出改进措施
单击此处输入你的正文,请阐述观点
案例分析:分享成功案例,总结经验教 训
单击此处输入你的正文,请阐述观点
生产计划安排不合理
生产设备故障或维护 不当
生产流程不顺畅或瓶 颈问题
员工技能不足或操作 不当
物料供应不及时或短 缺
质量检查不合格或返 工返修
运输距离过长或运输 方式不当
产生原因:生产流程设计不合理、生产计 划安排不当、物料摆放不规范等 单击此处输入你的正文,请阐述观点
过量生产浪费产生原因及影响
影响:增加库存成本、降低设备利用率、增加搬 运和运输成本等 过量生产浪费产生原因及影响
过量生产浪费产生原因及影响
影响:增加库存成本、降低设备利用率、增加搬 运和运输成本等 过量生产浪费产生原因及影响
过量生产浪费产生原因及影响
影响:增加库存成本、降低设备利用率、增加搬 运和运输成本等
• 七大浪费产生原因及影响:不良品浪费产生原因及影响、过量的生产浪费产生原因及影响、 过多的库存浪费产生原因及影响、不必要的运输浪费产生原因及影响、不必要的人员浪费产 生原因及影响、等待时间的浪费产生原因及影响、过度加工的浪费产生原因及影响
消除七大浪费培训资料

消除七大浪费培训资料在企业的生产与运营过程中,往往存在着各种形式的浪费,这些浪费不仅增加了成本,降低了效率,还影响了产品质量和企业的竞争力。
为了实现精益生产,提高企业的效益,我们有必要深入了解并消除“七大浪费”。
一、什么是七大浪费1、过量生产的浪费过量生产是指生产出比需求更多的产品,导致库存积压。
这不仅占用了资金和空间,还增加了管理成本和质量风险。
例如,某工厂为了提高设备利用率,不顾市场需求,大量生产某种产品,结果造成库存积压,产品滞销。
2、等待的浪费等待的浪费包括人员等待、设备等待、物料等待等。
比如,在生产线上,前一道工序未完成,导致后一道工序的工人和设备处于等待状态;或者设备故障维修时,整个生产线停滞。
3、运输的浪费运输的浪费是指不必要的物料搬运和产品运输。
例如,工厂布局不合理,导致物料在车间内频繁搬运;或者为了将产品从一个仓库转移到另一个仓库,进行了不必要的运输。
4、过度加工的浪费过度加工是指对产品进行超出客户需求或标准的加工,增加了生产成本但并未带来价值的提升。
比如,为产品增加一些不必要的装饰或功能,导致加工时间和成本增加。
5、库存的浪费库存不仅包括成品库存,还包括原材料库存、在制品库存等。
大量库存会掩盖生产过程中的问题,如质量缺陷、设备故障等,同时也增加了资金占用和库存管理成本。
6、动作的浪费动作的浪费是指员工在工作中不必要的动作,如弯腰、转身、寻找工具等。
这些动作不仅浪费时间和体力,还可能导致疲劳和错误。
7、不良品的浪费不良品的产生意味着原材料、人工和设备等资源的浪费。
而且,不良品还可能需要返工或报废,进一步增加了成本。
二、七大浪费产生的原因1、生产计划不合理不准确的市场预测、不合理的生产排程,导致过量生产或生产不足。
2、流程不完善生产流程存在缺陷,工序之间不协调,容易出现等待和运输的浪费。
3、设备维护不当设备故障频繁,维修时间长,影响生产效率,造成等待浪费。
4、员工培训不足员工技能水平低,操作不熟练,容易出现动作浪费和不良品浪费。
精益生产中的七大浪费

精益生产中的七大浪费一、库存浪费◆精益生产认为:“库存是万恶之源”,所有改善行动会直接或间接地和消除库存;①产生不必要的搬运、堆积、放置、防护处理、寻找等浪费②使先进先出的作业困难③损失利息及管理费用④物品的价值会减低,变成呆滞品⑤占用厂房空间、造成多余工场、仓库建设等⑥设备能力及人员需求的误判◆因库存造成无形损失,绝不亚于上述有形损失,精益生产者认为库存会隐藏问题,而“问题”在精益生产者被认为是宝藏,问题如果能不断地被发现解决,则利益便会不断地产生1、没有管理的紧张感,阻碍改进:2、库存量一多,因机械故障、不良产品所带来的不利后果不能马上显现出来,因而也不会产生对策;3、由于有了充足的库存,出现问题时可以用库存先顶上,问题就可以慢慢解决甚至不用解决,最起码是被掩盖住了,不急迫了,不会被上级追究了,于是本部门的工作成绩就出来了;二、过渡生产制造过多或过早浪费◆TPS强调的是“适时生产”;◆多做能提高效率,提早做好能减少产能损失不做白不做,机器还不是一样停着1、提早用掉了材料费、人工费而已,并不能得到什么好处;2、把“等待浪费”隐藏,使管理人员漠视等待的发生和存在;3、积压在制品,使生产周期L/T变长无形的,而且会使现场工作空间变大,不知不觉中吞蚀我们的利润;4、产生搬运、堆积浪费,先进先出变得困难;三、品质缺陷不良品浪费◆任何的不良品产生,皆造成材料、机器、人工等的浪费;◆及早发现不良品,容易确定不良来源,进而减少不良品的产生;◆关键是第一次要把事情做对,“零缺陷”四、运输搬运浪费◆大部分人皆认同搬运是一种无效的动作,也有人认为搬运是必须的;◆用“输送带”的方式来克服,行吗1、取放浪费;2、等待浪费;3、在制品过多浪费;4、空间浪费;◆搬运浪费又包含放置、堆积、移动、整理等动作的浪费;五、处理加工浪费◆定义:指的是与工程进度及加工精度无关的不必要的加工◆有一些加工程序是可以省略、替代、重组或合并;◆很多时候会习惯并认为现在的做法较好六、动作浪费◆12种动作浪费:◇两手空闲◇单手空闲◇不连贯停顿◇幅度太大◇左右手交换◇步行多◇转身角度大◇移动中变换状态◇不明技巧◇伸背动作◇弯腰动作◇重复不必要动作七、等待浪费◇生产线的品种切换◇工作量少时,便无所事事◇时常缺料,设备闲置◇上工序延误,下游无事可做◇设备发生故障◇生产线工序不平衡◇有劳逸不均的现象◇制造通知或设计图未送达。
精益生产七大浪费基础讲义PPT课件

结束语
当你尽了自己的最大努力时,失败也是伟大的, 所以不要放弃,坚持就是正确的。
When You Do Your Best, Failure Is Great, So Don'T Give Up, Stick To The End 演讲人:XXXXXX 时 间:XX年XX月XX日
2. 过量生产浪费
1. 超出下一操作的需求量 2. 提前生产下一操作的需求 3. 设备速度过快
3. 过分加工浪费
1. 超出/低于产品特定需求的精度 2. 多余的作业项目
质量成本概念
4. 搬运浪费
• 也就是说“每个工位都从手工操作开始”.
-- 找到、拿起、移动,用手放,然后
-- 从手推车移到货板
2.关于操作场所布置:
(9)工具物料应放于固定处。 (10)工具物料及装置应布置于工作者之前面近处。 (11)零件物料之供给,应利用其重量堕至工作者手边。 (12)[堕送]方法应尽可能利用之。 (13)工具物料应依照最佳之工作顺序排列。 (14)应有适当之照明设备,使视觉满意舒适。 (15)工作台及椅之高度,应使工作者坐立适宜。 (16)工作椅式样及高度,应可使工作者保持良好的姿势。
• 一种浪费通常能够导致另外一种浪费
发现浪费和认识浪费的能力很重要
隐性浪费/显性浪费
• 显性浪费
– 定义为可见的浪费 – 这些浪费很容易签别
如:
– 在流程中引起不良品的错误 – 等待时间浪費
• 隐性浪费
– 定义为看不见的浪費 – 这些浪費不易被签别 – 这些工作看起来非常有价值
直到使用新的策略发现其中 很大的浪费.
动作经济原则
7. 不平衡浪费
1. 人员工作分配不合理 2. 计划对人员需求不均匀 3. 设备产能搭配不合理 4. 设备故障 5. 物料短缺 6. 信息流与物流不同步
精益生产之七种浪费培训

精益生产之七种浪费培训精益生产是一种管理方法,旨在通过减少浪费来提高生产效率和质量。
在精益生产中,有七种被认为是浪费的元素,被称为七种浪费。
这些浪费分别是:1. 运输浪费:指产品或材料在生产过程中的不必要的运输。
这种浪费会消耗时间和资源,并增加出错的可能性。
例如,将原材料从一个生产线运输到另一个生产线,或者将成品从一个仓库运输到另一个仓库。
2. 库存浪费:指过多的库存,不仅占用了宝贵的空间,还需要额外的成本来维护和管理。
过多的库存也意味着产品无法及时交付给客户,增加了交货延迟和过度备货的风险。
3. 过程浪费:指不必要的生产步骤、繁琐的操作和不必要的等待时间。
这些浪费会增加生产周期,并使生产过程变得低效。
4. 超生产浪费:指生产出了超过需求的产品数量。
这种浪费会导致产品堆积在仓库中,没有销售出去,并占用宝贵的资源和资金。
5. 劳动力浪费:指员工的不必要的等待、无效的运动和重复的工作。
这些浪费会降低员工的效率,同时也会对员工的士气和工作满意度产生负面影响。
6. 缺陷浪费:指产品在生产过程中出现的缺陷或错误。
缺陷会导致产品返工或废品产生,增加了成本和生产周期。
7. 不必要的处理浪费:指在生产过程中进行的不必要的操作和处理。
这些操作可能是由于过度设计、不正确的工艺或无效的工作方法引起的,会增加生产成本和工作时间。
通过了解和识别这七种浪费,企业可以采取相应的措施来降低或消除浪费,提高生产效率和质量。
这可能包括改善生产流程、优化库存管理、培训员工以提高技能和意识,以及推动持续改进的文化和实践。
精益生产的目标是实现高效率、高质量、高价值的生产,从而提高企业的竞争力和持续发展能力。
通过消除浪费,企业能够更好地满足客户需求,提供更好的产品和服务,同时也能够降低成本、提高利润和创造更可持续的发展。
在精益生产中,减少浪费是一项重要的任务。
通过减少浪费,企业可以提高生产效率、降低成本,并提供更优质的产品和服务。
下面我们来详细介绍如何应对这七种浪费。
精益生产七大浪费课程讲义

库存水平 例子: 过多的设备维修备品库存
人手不够 设备故障
物料未到
质量不良 技能不足 订单变更
第三节 搬运的浪费
定义:搬移零组件产品,过程仅属一种临时需要的搬运活动。 结果:搬运的动作会直接造成时间、空间、容器、载具、人力等浪费,并
间接造成库存、管理上的浪费,更严重的是,搬运过程还经常发生物 品的损伤,也会造成许多质量性和不可预测性的连锁浪费。
1、车间开工后,生产管理者根据员工忙闲情况见缝插针、机动派工, 员工亦不管后续工序消化能力全力赶工,做完就立即往下道工序传递,遇 到阻塞就在一旁等待或再次见缝插针;
2、当质量、急件等问题出现时,只能停产、换型并重新安排生产; 3、等待拉长了生产周期,换型增加了搬运浪费,提高了管理者生产压 力,增加了库存,占用了生产空间,导致了寻找、误用、脏污、碰伤等问 题。
• 良率过低导致投料增加
• 产能高于需求
• 由于生産方法或设备难以改变而预先生産出大 批量的零组件
• 过量的影印、附件、存档等 • 型录宣传品过量印刷 • 简报超过时间未能精简扼要
• 在顾客从来不会看到的内部零组件上涂刷油漆 • 与工作无关的多余的资料收集、文件制作、报告等作业 • 流程中须签核的作业过多,未标准化
反之,违反这个原则就会产生:多余的库存、多余的搬运、多余ห้องสมุดไป่ตู้等 待…等等各种浪费。
物资浪费(Material)
- 1、下载文档前请自行甄别文档内容的完整性,平台不提供额外的编辑、内容补充、找答案等附加服务。
- 2、"仅部分预览"的文档,不可在线预览部分如存在完整性等问题,可反馈申请退款(可完整预览的文档不适用该条件!)。
- 3、如文档侵犯您的权益,请联系客服反馈,我们会尽快为您处理(人工客服工作时间:9:00-18:30)。
物资浪费(Material)
➢没有的浪费 ➢库存的浪费 ➢搬运的浪费 ➢拿、放的浪费 ➢等待的浪费 ➢困难工序的浪费
作业方法浪费(Method)
➢Lot的浪费 ➢库存的浪费 ➢搬运的浪费 ➢拿、放的浪费 ➢困难工序的浪费
无附加价值的 时间与工作
必须的 时间与 工作
产生附加价值的行为
不产生附加价值的行为
第一次 浪费 (能即时消除)
• 等待 • 寻找 • 保管 • 重新整理 • 打开包装
常见的无价值作业!
作
业
无附加价值的作业
第二次 浪费 (作业本身)
第三次 浪费 (设备的浪费)
• 复位作业 • 调整作业 • 去除毛刺 • 修正作业 • 喷 除锈剂
在以上原理的基础上,丰田公司进一步将浪费定义为:“凡是超过生 产产品所绝对必要的最少量的设备、材料、零件和工作时间的部分,都是 浪费”。
由此提出JIT (Just in time) 准时生产观念,即:只有在顾客需要的 时候,才生产顾客所需质量和数量的产品。
JIT的三要素:正确的时间(顾客需要的)、正确的数量(顾客需要的)、 正确的产品(顾客需要的)。
挤占工艺
强
的生产计划
挤占物料整 整备时间
的
半成品库存
备时间
生
前后进度难实
产
时衔接
管
理
一大堆
等来等去拉长生 产周期时间
只好靠提前 投产来保证
交期
部
只好先去
为了搬运效率只好 大批量搬运
从图中可以看到,离岛式车间布局“加工地点分散各地”的特点在一连串
的连锁反应后,最终会引发制造型企业“生产计划难以控制”的严重问题,这
• 油空压 空回转 • 切削机 空转 • 监视作业 • 拧紧 螺丝
精密作业
“非成本主义”的观点认为,商品的售价是市场决定的,企业的利润 必须以市场认可的价格为基点,减去企业实际发生的产品成本后产生。
丰田公司正是以这种理念出发,把凡是会造成成本增加的所有一切非 增值作业称之为浪费,把企业经营的着眼点放在了千方百计降低产品的成 本上,即发现和减少浪费的精益生产管理核心所在。
机器位置 固定不变
乱流生产
质量责任 难追溯
扯皮容易 蒙混过关
派活时由现场主管视各 岗位忙闲情况见缝插针
每一批次的加工路线 (经手人)都不一样
花金钱时间精力 去追查或控制
问题被隐藏
注定要 搬来搬去
拉长生 产周期 时间
陷入事后管 理的漩涡
同样问题 一再重复发生
救火/ 善后 变成家常便饭
第三节 事后管理
事后管理是传统制造型企业中管理人员所养成的一种习惯,在这种习惯 的驱使下他们只会在问题发生之后再采取相应的反映措施:
1、车间开工后,生产管理者根据员工忙闲情况见缝插针、机动派工, 员工亦不管后续工序消化能力全力赶工,做完就立即往下道工序传递,遇到 阻塞就在一旁等待或再次见缝插针;
2、当质量、急件等问题出现时,只能停产、换型并重新安排生产; 3、等待拉长了生产周期,换型增加了搬运浪费,提高了管理者生产压 力,增加了库存,占用了生产空间,导致了寻找、误用、脏污、碰伤等问题 。
竞争力提升
品质提升 合理化成本降低 形象提升
标准化 改善
消除浪费 现场5S
动作标准化、作业流程标准化、操作流程 标准化、包装运输标准化等
动作改善、作业流程改善、物流改善、设 备模夹治具改善、品质改善、管理改善等
七大浪费
整理、整顿、清扫、清洁、素养等
第一章 制造业常见的管理误区
为了能够运用一些精益的手法排除企业车间现场的七大浪 费,首先需要对传统制造企业中长期存在的一些布局特点有所 认识,从而了解它们可能对企业整个生产效益产生的影响。
玉柴金创 讲师
精益生产 七大浪费课程
2014年
编制:李振兴 Copyright © 2014 jingchuang
前言
浪费普遍存在于企业生产经营的全部过程,是造成成本增 加的主要原因,应该被彻底消除,是企业生产经营效益提升的 万恶之源。
金创公司由于技术和管理水平仍然处于较低水平,资源利 用率不如国内外优秀企业,甚至不如玉柴集团的其他子公司, 在此基础下,发现浪费和消除浪费是金创公司全体员工为实现 精益生产又一重要里程碑,具有巨大的现实意义。
陷入事后管理的漩涡……
事后管理就是等事情 发生之后再处理
习惯先 追究责任
挤在一起发生 只好忙于救火
怕后遗症扩大 只好采取围堵措施
没空/不愿追查 发生的原因
同样问题 一再重复发生
惩罚扣款 多于奖励
关闭心门 消极抵抗
救火/ 善后 变成家常便饭
垃圾流程丛生 只治标不治本
经常产生一人错误 百人忙的连锁反应
第一节 离岛式的车间布局
离岛式的车间布局是指通常在制造型企业里将相同功能的 加工设备集中摆放在同一个车间或者区域的整体布局方式。这 种方式一般适用于大批量生产的生产组织方式,具有集中生产 、集中搬运、减少搬运次数等特点,但同时会导致在制品搬运 浪费大、生产周期长、空间占用大以及“混乱”等缺陷。
(A车间:铸造)
因此造成了七大浪费!
第二章 识别七大浪费
传统的概念中,浪费指材料丢失、产品受损等。 现代的浪费指企业各项经营环节中所存在的非增值环节。 对应的增值环节,指的是能够直接给企业带来利润的环节,在加工制 造环节则指企业通过有形的物理变化或化学变化,将原材料转变为具有使 用价值商品的过程,那些无法给企业带来创效的环节则是非增值环节。 说明:非增值环节虽然不能够直接给企业创收,但并不意味着它没有 存在的必要,相反要采取措施,使增值环节强化,非增值环节优化。
个问题也就是企业通常所描述的“计划永远跟不上变化”的情况。
第二节 机器位置固定不动
在传统的制造型企业中,一般在设备安装完毕后,其位置 就基本不会发生变化,这已经成为一种普遍观念,如此会导致 企业生产出现如下问题:
1、生产工序跳跃前进和等待; 2、生产型号混乱生产; 3、企业总体效率降低。
机器位置固定不动所引发的问题…
离岛式车间布局
(B车间:打磨)
(C车间:加工)
(D车间:清洗)
投
单
生
3
产
2
7 8 13 14 6 9 12 15
产
品
18
交
付
17
5
11
1
4
10
16
19 20
离岛式车间所引发的问题…
协 调
加工地点分 散各地
因批量返工而变 更生产计划
质量事故频生
能 力
计划难
经常停工待料 愈急愈草率
很
A车间不知B车间
以控制