炼钢连铸技术发展和年展望
连铸新技术
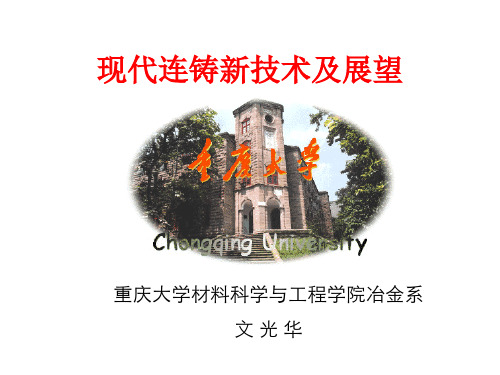
,
,
16
,
2.3
连续铸钢的生产现状
• 近几年,在我国钢铁工业大力发展的同时,连 铸生产也得到高速的增长。2002年全国连铸比 就上升到94%,粗钢产量为1.8亿吨。 2005年
估计钢产量将达 3.5 亿吨左右,占世界钢产量
,
,
、 20
3.1 高效连铸的应用
化国 最外 高方 拉坯 速铸 :机 高 效
21
3.1 高效连铸的应用
国内状况
可以说,采用高效连铸技术后,使我国钢铁工 业仅用10年时间完成了行业总体流程和生产水平的 历史性技术改造任务,步入了中后期工业国家的先 进行列。
22
3.2 高效连铸关键技术
当连铸机作业率超过了80%以上, 再要提 高连铸机产量就必须从提高拉速着手。而拉速 的提高决定于: —出结晶器均匀的坯壳厚度; —液相穴的长度; —铸坯的冷却强度。
用,低碳钢拉速达3.5m/min. ,中碳钢达2.8m/min.,高
碳钢达2.6m/min.。生产效率提高了50%,铸坯表面质量 改善,中心偏析减少。
29
板坯结晶器高效化技术
• 结晶器自动调宽技术; • 结晶器冷却优化技术(水缝、水速等); • 奥钢联最近开发的CLEVER的新型高效箱式结晶 器。该结晶器具有以下特点:箱式设计可快速更换铜板;
27
新型方坯高拉速结晶器
3 、奥地利VAI公司的钻石结晶器(DIAMOLD) 该结晶器在设计上有如下三个特点:①将结晶器长 度延长至1000mm,以延长铸坯在结晶器内的停留时间, 增加出结晶器的坯壳厚度;②采用比传统结晶器锥度大 的抛物线锥度,以保证坯壳均匀成长;③从结晶器顶部 往下300~400mm处开始,角部取消锥度以减小摩擦力, 而中部仍旧保持抛物线锥度。按照此方法设计出的结晶 器,从顶部看其内壁形状象钻石,故称作 DIAMOLD 。 数值模拟表明,该结晶器内坯壳生长稳定均匀,坯壳与 模壁间的摩擦力也小。在奥地利、美国、法国、德国及 意大利等国投入使用后,拉速大幅度提高,最高超过 5.0m/min. ,生产效率提高 20% ~ 50% ,铸坯质量明显 改善,而且铜管寿命也有所提高。 28
连铸技术国内外现状及发展趋势

连铸技术国内外现状及发展趋势
连铸技术是钢铁工业中的重要技术之一,它可以实现高效连续生产,提高生产效率,降低成本。
目前,国内外的连铸技术都在不断发展和完善中。
在国内,连铸技术已经实现了从单流到双流、三流、四流等多流程的升级。
同时,还出现了带分段式结晶器、上下扫描式结晶器等新型结晶器,提高了连铸成材率和质量。
此外,国内的连铸技术还在不断推广智能化生产、绿色环保等方面的应用。
在国外,美国、日本等发达国家在连铸技术方面也有很多创新。
例如,美国的Hazelett连铸技术可以实现高品质的铝合金连铸,日本的CCS连铸技术则可以实现高浓度的钢水连铸。
此外,欧洲的一些连铸厂还在探索使用第三方能源进行加热,以实现更高的能源利用效率。
未来,随着新材料、新工艺、新技术的不断涌现,连铸技术将继续发展和创新。
同时,环保、智能化、自动化等方面也将成为连铸技术发展的重要方向。
- 1 -。
武钢转炉炼钢与连铸生产技术进展与展望

2003中国钢铁年会论文集画
2.1第一炼钢厂
一炼钢采用100t铁水罐喷吹式脱硫工艺,原 采用20%金属Mg与80%CaO的混合脱硫剂。
好的脱硫效果,根据钢种需要,采用深浅两种脱硫 工艺,深脱硫后[s]≤0.005%,最好时可达 [S]≤0.001%,浅脱硫后[S]≤o.010%。铁水 脱硫效率通常可达90%左右。
2000年年均吨铁铁水脱硫剂消耗为1.93kg。2001 年引进了中乌(乌克兰)合资戴斯玛克有限公司的
3转炉炼钢
金属纯镁铁水脱硫技术。试生产时吨铁脱硫剂单耗 为0.34kg,平均温降9.83℃,平均后硫为 0.0089%,喷吹时间缩短约3min,吨铁脱硫铁损 降低4.32kg,脱硫剂单耗成本降低2.35元,综合 效益达8.03元,喷吹终点目标硫±0.002%,合格 率达86%。从总体上看,该工艺从技术上是先进
4 55 273 97 313.70 87 34
3 1l
2002年
550 9B 717 85 76 75 9l 85 】65 99 55 33
/0 24 16I 3f 205 1l 78 65
4 57 297 80 346 75 85 88
3、15
— — — — — — —一— — — — — — — — — —一— .286.
表4武钢3个钢厂近三年的吨钢钢铁料消耗统计
Tab.4
The metal cortsumptlon of three steelmaking
plants WISCO in recent three years
厂别
2000每/kg
2001正/kg
2002证/kg
折合量 实物量 折合量 实物量 折合量 实物量
铁水脱硫
连铸技术在钢铁冶炼中的应用

连铸技术在钢铁冶炼中的应用现代钢铁冶炼中的一项关键技术是连铸技术。
连铸技术是将液态钢浇注到连续铸机冷却结构上,形成连续的厚板、薄板、管材、工字钢等钢材产品,从而取代了以往钢液在浇铸过程中结晶、凝固而产生的不纯物及疵点,提高了钢材的质量。
连铸技术应用于钢铁冶炼中,提升钢材质量、生产率和经济效益,逐步普及和发展,成为钢铁行业的发展趋势。
一、连铸技术简介连铸是指将钢液在连续铸造机上,通过机械力使钢液流动的同时,紧靠着冷固结构快速凝固并形成的成品钢材。
同时,连铸设备和工艺连续化,无须在冶炼配料和成品钢材之间的中间过程转化步骤,从而提高了钢材质量,减少了能源消耗。
连铸技术的主要优点是:1. 避免了钢液在浇注过程中,由于结晶、凝固而产生的不纯物和疵点,提高了钢材的质量。
2. 减少了钢材制造过程中的能源消耗,同时提高了生产效率。
3. 减少了外观质量的不良因素,提高了铸造钢材的质量。
二、连铸工艺流程连续铸造过程中,首先将液态钢从钢包中送往浇注站,然后将钢液引入下垂式浇注管中,通过支撑装置的各种动作使钢液保持稳定的流动,进入连续铸造机,与冷却结构接触而凝固。
连续铸造过程中,一般采用感应加热方式加热钢水。
加热后的钢水通过调节水冷却器的水流,以达到理想的冷却速度,从而产生所需要的微观组织。
连续铸造机的工作原理是,将钢水通过下垂管输入机器,快速冷却成铜片,然后通过机器的牵引链条拖动,继续冷却、成型、切割制成成品钢材,整个过程实现了连续化生产,极大提升了生产力。
三、连铸技术应用案例1. 小排钢坯连铸小排钢坯连铸技术是近年来发展起来的一种先进的钢铁连铸生产工艺。
它的工艺流程与传统的结构光从钢水到钢坯形成的连铸工艺相同,但采用了先进的成杯技术,将定径后的小排钢坯成杯装载上车架,经热处理后直接送往轧机生产线,大大缩短了连铸生产过程,同时也减少了钢坯形变和凝固的不正常现象,大大提高了钢坯的质量。
2. 大直径碳素钢连铸大直径碳素钢连铸是在特别条件下,通过添加稳定剂、合理调整冷却条件来控制晶粒尺寸,使连铸坯疏松度降低,提高了连铸物质的牢度和成品合格率,在保证钢质量同时,也增加了生产量。
钢铁工业连铸自动化的现状与展望
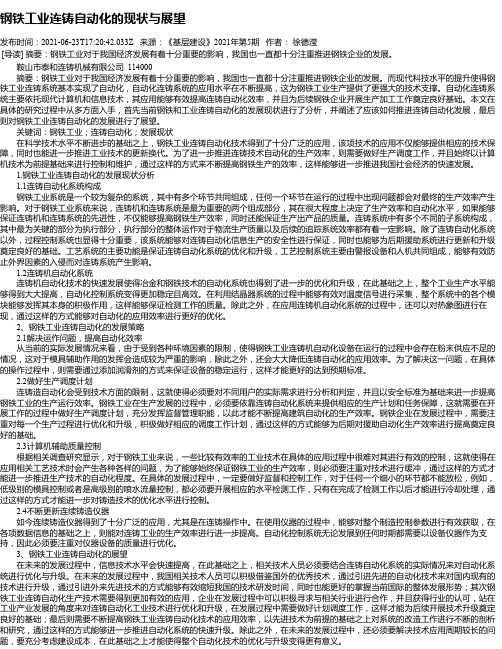
钢铁工业连铸自动化的现状与展望发布时间:2021-06-23T17:20:42.033Z 来源:《基层建设》2021年第5期作者:徐德滢[导读] 摘要:钢铁工业对于我国经济发展有着十分重要的影响,我国也一直都十分注重推进钢铁企业的发展。
鞍山市泰和连铸机械有限公司 114000摘要:钢铁工业对于我国经济发展有着十分重要的影响,我国也一直都十分注重推进钢铁企业的发展。
而现代科技水平的提升使得钢铁工业连铸系统基本实现了自动化,自动化连铸系统的应用水平在不断提高,这为钢铁工业生产提供了更强大的技术支撑。
自动化连铸系统主要依托现代计算机和信息技术,其应用能够有效提高连铸自动化效率,并且为后续钢铁企业开展生产加工工作奠定良好基础。
本文在具体的研究过程中从多方面入手,首先当前钢铁和工业连铸自动化的发展现状进行了分析,并阐述了应该如何推进连铸自动化发展,最后则对钢铁工业连铸自动化的发展进行了展望。
关键词:钢铁工业;连铸自动化;发展现状在科学技术水平不断进步的基础之上,钢铁工业连铸自动化技术得到了十分广泛的应用,该项技术的应用不仅能够提供相应的技术保障,同时也能进一步推进工业技术的更新换代。
为了进一步推进连铸技术自动化的生产效率,则需要做好生产调度工作,并且始终以计算机技术为前提基础来进行控制和维护,通过这样的方式来不断提高钢铁生产的效率,这样能够进一步推进我国社会经济的快速发展。
1.钢铁工业连铸自动化的发展现状分析1.1连铸自动化系统构成钢铁工业系统是一个较为复杂的系统,其中有多个环节共同组成,任何一个环节在运行的过程中出现问题都会对最终的生产效率产生影响。
对于钢铁工业系统来说,连铸机和连铸系统是最为重要的两个组成部分,其在很大程度上决定了生产效率和自动化水平,如果能够保证连铸机和连铸系统的先进性,不仅能够提高钢铁生产效率,同时还能保证生产出产品的质量。
连铸系统中有多个不同的子系统构成,其中最为关键的部分为执行部分,执行部分的整体运作对于物流生产质量以及后续的追踪系统效率都有着一定影响。
炼钢厂连铸年初工作计划

炼钢厂连铸年初工作计划一、工作总体目标1. 提高连铸工艺水平,确保炼钢厂连铸生产稳定运行。
2. 提高产品质量,降低废品率,提高利润。
3. 加强安全生产管理,保障员工安全。
二、主要工作内容1. 连铸设备维护和改进- 定期进行设备巡检和保养,确保设备能够正常运行。
- 加强设备改进,提高连铸过程的稳定性和效率。
- 更新设备操作规程,提高操作人员的技能水平。
2. 连铸工艺优化- 分析连铸生产过程中的问题,寻找并改进存在的瓶颈。
- 加强连铸操作监控,及时发现并处理潜在问题。
- 与冶金部门密切合作,提高炼钢和连铸之间的工艺协调性。
3. 产品质量管理- 加强原料质量检验,确保原料的合格率。
- 加强产品质量监测,及时发现质量问题并采取纠正措施。
- 强化质量意识培训,提高员工的质量意识和技能。
4. 废品率降低- 分析废品产生的原因,制定相应的改进计划。
- 加强废品处理和回收利用,减少资源浪费。
- 持续改进生产工艺,优化工艺参数,降低废品率。
5. 安全生产管理- 开展安全教育培训,提高员工的安全意识和技能。
- 加强设备安全管理,确保设备运行的安全可靠。
- 健全应急预案,提高应对突发事件的能力。
三、工作安排1. 第一季度:- 完成设备巡检和保养计划。
- 制定连铸工艺改进方案。
- 开展质量培训并提高废品处理能力。
2. 第二季度:- 实施连铸设备改进计划。
- 优化连铸工艺参数并加强工艺监控。
- 继续加强产品质量管理和废品率降低。
3. 第三季度:- 持续改进连铸设备性能和稳定性。
- 分析产品质量问题并制定改进措施。
- 继续加强安全生产管理。
4. 第四季度:- 总结全年工作经验,制定下一年度工作计划。
- 开展员工培训和能力提升计划。
- 提交年度工作总结报告。
四、工作预期成果1. 连铸设备运行稳定,故障率降低,生产效率提高。
2. 产品质量得到有效控制,合格率提升,废品率明显降低。
3. 安全生产状况良好,未发生重大安全事故。
4. 员工安全意识和技能提高,员工参与积极性提高。
金属冶炼过程中的连铸技术

中大型钢厂由于规模较大,连铸技术 主要用于生产大型钢材和特殊钢材, 如大型矩形坯、板坯、方坯等。
中大型钢厂的连铸技术应用中,通常 采用先进的连铸工艺流程,如电磁搅 拌、结晶器振动、动态二冷等,以提 高产品质量和降低能耗。
中大型钢厂的连铸机通常采用多流形 式,以提高生产效率和降低成本。
不锈钢冶炼的连铸技术应用
06
连铸技术的应用实例
小型钢厂的连铸技术应用
小型钢厂由于规模较小,连铸技 术主要用于生产小型钢坯和钢材 ,如小型圆钢、小型矩形坯等。
由于设备规模较小,连铸机通常 采用单流或双流形式,便于维护
和操作。
小型钢厂的连铸技术应用中,通 常采用传统的连铸工艺流程,如 钢水注入、结晶器冷却、二次冷
却等。
中大型钢厂的连铸技术应用
板坯连铸技术主要用于生产薄板和钢板,广泛应用于汽车、船舶、建筑、家电等 领域。
板坯连铸技术的优点包括高精度、高质量、高效率等,是现代金属板材制造的重 要技术之一。
圆坯连铸技术
圆坯连铸技术主要用于生产圆形的钢坯,主要应用于石油、 化工、电力等领域。
圆坯连铸技术的优点包括高效率、低成本、节能环保等,是 现代圆形结构件制造的重要技术之一。
智能化与自动化
智能化
随着人工智能和大数据技术的应用,连铸技术正朝着智能化方向发展。通过建立智能化监控系统,实 时监测生产过程,对异常情况自动预警和处理,提高生产安全性和稳定性。
自动化
自动化是提高连铸生产效率和产品质量的重要手段。通过自动化设备、机器人和自动化控制系统,实 现连铸生产过程的自动化操作,减少人工干预,提高生产效率。
05
连铸技术的发展趋势
高效化与节能化
高效化
随着技术的不断进步,连铸技术正朝着提高生产效率和降低能耗的方向发展。 通过优化工艺参数、改进设备结构和采用先进的控制技术,实现连铸生产的高 效化,提高铸坯质量和产量。
高效连铸技术发展现状及进展

高效连铸技术发展现状及进展摘要:中国经济的快速发展使连铸技术艺得到了快速发展,连铸技术是炼钢生产的核心技术,它在炼钢厂的发展中发挥着举足轻重的作用,能有效地提高炼钢的生产率和产量,因此,对连铸技术的发展进行了论述,并以此为依据,对高效连铸技术艺进行了分析,以期对我国钢铁行业的可持续发展有所借鉴。
关键词:连铸技术;高效连铸;发展趋势;引言在冶金行业,连铸技术因其能耗低、环境污染小、投资规模小等优点,已逐渐取代传统的铸型铸造技术,自20世纪50年代第一台连铸机投入使用以来,无论是机器型号、生产工艺还是设备自动化水平都得到了极大的提高,所生产的钢材质量也不断提高,随着信息技术的广泛应用,连铸技术的发展得到了进一步的推动,在生产效率方面,连铸技术已经从单炉发展到多炉;在生产技术上,它已经从冷铸造转向直接轧制、直接装料和热输送,未来将向无头轧制发展。
1.连铸技术的发展状况我国的连铸技术起步较晚,改革开放前,我国连铸技术主要依靠外国引进,自身创新水平较低,随着我国经济的发展,特别是21世纪以来,我国的连铸技术发展迅速,钢铁产品的产量不断提高,生产技术和装备技术取得重大突破,现阶段,我国的连铸技术不仅可以生产各种特殊钢,而且在连铸设备生产上也可以实现国产化。
自1995年以来,我国开始着手解决高效连铸技术的关键问题,在确保高铸造速度的同时,在提高钢铁生产效率、改善机器与炉的匹配、降低生产成本等多方面取得了技术进步,从而推动我国连铸水平的全面发展,在第四次全国连铸工作会议上,提出以连铸为研究方向,实现我国钢铁精炼,尽管我国连铸技术取得了巨大突破,但与西方发达国家相比仍有一定差距,特别是在板坯连铸速度上,我国大型板坯连铸速度还在1.8m/min的范围,大多数薄板坯连铸速度企业只能保持在5m/min以内,近年来,随着我国重点行业的发展,对钢的强度和韧性提出了更高的要求,这也推动了我国特种钢的生产,如微合金钢产量已超过1亿吨,然而,微合金钢在连铸过程中经常出现局部裂纹,这降低了钢生产的合格率,纵观我国钢铁企业,微合金钢连铸过程中表面裂纹的发生率较高,部分企业可达10%。
连铸技术国内外现状及发展趋势

连铸技术国内外现状及发展趋势
随着钢铁工业的不断发展,连铸技术作为钢铁生产中的重要工艺技术,也在不断发展和改进。
本文旨在探讨连铸技术的国内外现状和发展趋势。
一、连铸技术国内外现状
1. 国内现状
目前我国连铸技术已经成为钢铁生产中的主要工艺技术之一,国内的连铸设备和技术水平也不断提高。
目前,我国铸造模具、连铸机、冷却系统等连铸设备已经实现国产化,并且在连铸技术的研究和应用方面也取得了不少成果。
然而,与国外相比,我国的连铸技术仍然存在一定的差距。
2. 国外现状
国外的连铸技术相对较为成熟,特别是在技术水平和设备精度方面已经达到了相当高的水平。
目前,欧美等发达国家的连铸技术已经开始向高端化、多功能化方向发展,能够适应更加复杂的钢铁材料生产需求。
二、连铸技术的发展趋势
1. 高端化
随着我国钢铁产业的不断发展,钢铁材料的品质和精度要求也越来越高。
因此,连铸技术也需要不断提升,向高端化方向发展。
2. 多功能化
在连铸技术的应用过程中,还需要考虑人工智能、大数据、机器
视觉等技术的应用。
未来,连铸技术将朝着多功能化的方向发展。
3. 绿色化
连铸技术的发展也需要考虑环保和资源节约。
因此,在设备制造和生产过程中,需要更多地考虑环保和资源节约问题,实现连铸技术的绿色化。
综上所述,连铸技术作为钢铁生产中的重要工艺技术,其国内外现状和发展趋势也在不断变化。
随着技术的不断提升和应用范围的扩大,连铸技术有望在未来实现更加高端化、多功能化和绿色化的发展。
连铸年度总结范文
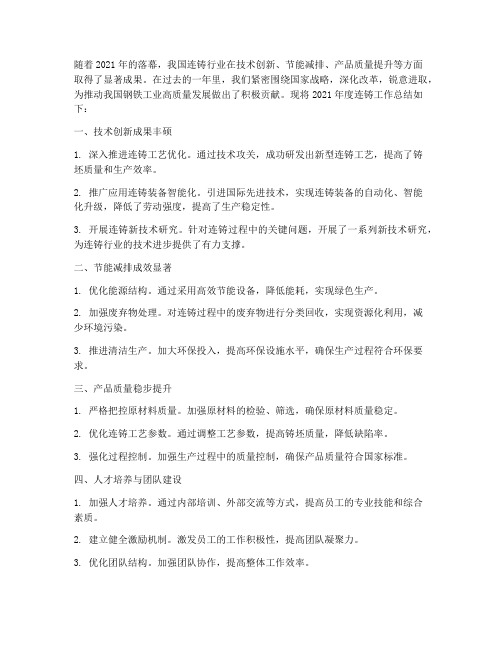
随着2021年的落幕,我国连铸行业在技术创新、节能减排、产品质量提升等方面取得了显著成果。
在过去的一年里,我们紧密围绕国家战略,深化改革,锐意进取,为推动我国钢铁工业高质量发展做出了积极贡献。
现将2021年度连铸工作总结如下:一、技术创新成果丰硕1. 深入推进连铸工艺优化。
通过技术攻关,成功研发出新型连铸工艺,提高了铸坯质量和生产效率。
2. 推广应用连铸装备智能化。
引进国际先进技术,实现连铸装备的自动化、智能化升级,降低了劳动强度,提高了生产稳定性。
3. 开展连铸新技术研究。
针对连铸过程中的关键问题,开展了一系列新技术研究,为连铸行业的技术进步提供了有力支撑。
二、节能减排成效显著1. 优化能源结构。
通过采用高效节能设备,降低能耗,实现绿色生产。
2. 加强废弃物处理。
对连铸过程中的废弃物进行分类回收,实现资源化利用,减少环境污染。
3. 推进清洁生产。
加大环保投入,提高环保设施水平,确保生产过程符合环保要求。
三、产品质量稳步提升1. 严格把控原材料质量。
加强原材料的检验、筛选,确保原材料质量稳定。
2. 优化连铸工艺参数。
通过调整工艺参数,提高铸坯质量,降低缺陷率。
3. 强化过程控制。
加强生产过程中的质量控制,确保产品质量符合国家标准。
四、人才培养与团队建设1. 加强人才培养。
通过内部培训、外部交流等方式,提高员工的专业技能和综合素质。
2. 建立健全激励机制。
激发员工的工作积极性,提高团队凝聚力。
3. 优化团队结构。
加强团队协作,提高整体工作效率。
五、展望未来2022年,我们将继续深化改革,创新发展,努力实现以下目标:1. 深化连铸工艺优化,提高铸坯质量和生产效率。
2. 加大节能减排力度,实现绿色生产。
3. 提升产品质量,满足市场需求。
4. 加强人才培养,打造高素质团队。
总之,2021年是我国连铸行业取得丰硕成果的一年。
在新的一年里,我们将继续努力,为实现我国钢铁工业高质量发展贡献力量。
冶金连铸技术总结汇报
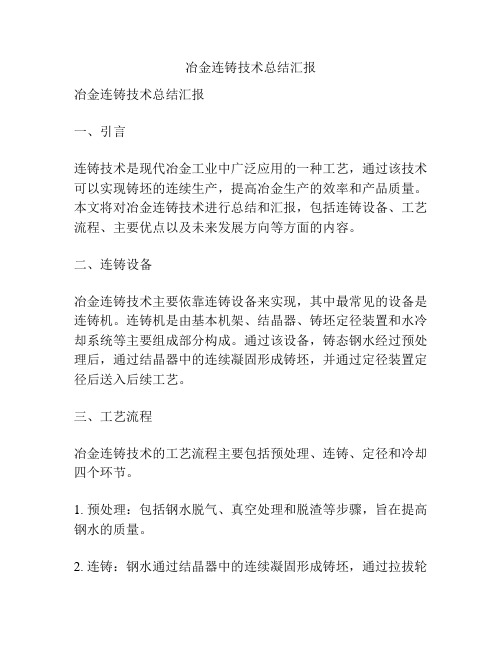
冶金连铸技术总结汇报冶金连铸技术总结汇报一、引言连铸技术是现代冶金工业中广泛应用的一种工艺,通过该技术可以实现铸坯的连续生产,提高冶金生产的效率和产品质量。
本文将对冶金连铸技术进行总结和汇报,包括连铸设备、工艺流程、主要优点以及未来发展方向等方面的内容。
二、连铸设备冶金连铸技术主要依靠连铸设备来实现,其中最常见的设备是连铸机。
连铸机是由基本机架、结晶器、铸坯定径装置和水冷却系统等主要组成部分构成。
通过该设备,铸态钢水经过预处理后,通过结晶器中的连续凝固形成铸坯,并通过定径装置定径后送入后续工艺。
三、工艺流程冶金连铸技术的工艺流程主要包括预处理、连铸、定径和冷却四个环节。
1. 预处理:包括钢水脱气、真空处理和脱渣等步骤,旨在提高钢水的质量。
2. 连铸:钢水通过结晶器中的连续凝固形成铸坯,通过拉拔轮和导板等辅助装置保持连续生产。
3. 定径:通过定径装置使铸坯达到所需直径,保证坯料的一致性。
4. 冷却:通过水冷却系统对铸坯进行冷却,使其达到适合下一道工序的温度。
四、主要优点冶金连铸技术相较于传统的浇铸工艺具有以下主要优点:1. 提高了生产效率:连铸技术采用连续生产方式,无需等待铸坯冷却,从而大大提高了冶金生产的效率。
2. 降低了生产成本:连铸技术减少了工序和人工操作,降低了生产成本。
3. 提高了产品质量:连铸技术减少了铸坯内部和表面缺陷的产生,提高了产品质量。
4. 减少了环境污染:连铸技术减少了铁水的飞溅和废水废气的排放,对环境污染更少。
五、未来发展冶金连铸技术在未来的发展中还有以下几个方向:1. 自动化程度提高:通过引入自动化设备和智能控制系统,提高连铸工艺的自动化程度,减少人工操作。
2. 连铸材料的拓展:研究开发新型连铸材料,拓展连铸技术的适用范围。
3. 资源和能源的可持续利用:通过提高资源利用率和能源利用效率,实现冶金连铸技术的可持续发展。
六、结论冶金连铸技术是一种高效、优质的冶金工艺,在现代冶金工业中得到广泛应用。
高级钢连铸技术进步和展望

高级钢连铸技术进步和展望1 连铸技术的进步1.1 中间包技术进步1.1.1 中间包钢水温度控制钢包中的钢水注入中间包后,通过塞棒或滑板机构从水口流入结晶器。
中间包内的钢水温度控制对作业稳定性、提高成坯率和铸坯质量具有很大影响。
为此,开发出等离子加热和感应加热的中间包钢水温度控制方法。
此外还有结合双枪式等离子加热法,对中间包堰的形状进行优化设计。
双枪式等离子加热不需要浸入式电极,可适应高生产效率的要求。
1.1.2 去除夹杂物提高洁净度中间包钢水氧化污染的主要原因是钢水被空气氧化。
其他原因包括:钢包钢渣的流入、钢水与中间包耐火材料内衬发生反应等。
为减少中间包钢水的氧化程度,推进了与钢水不发生反应的中间包保护渣和吸收氧化铝保护渣的使用,并采取Ar气保护以及使用钢包浸入式长水口稳定钢水和中间包大型化等措施。
为实现节能、降低耐火材料消耗并提高钢水洁净度,实施了中间包热循环使用操作法。
在浇注结束后将中间包立起,把包内的熔渣和残铁全部倒掉,然后不用预热继续使用(见图1)。
有报告报导采用该方法中间包可连续浇注560炉钢水。
在用燃气对中间包进行加热时,为防止罐内残铁氧化,采用了H2和N2混合气体的还原性气体加热方法。
图1 中间包热态循环使用示意图和降低熔渣氧化度的效果中间包的结构设计取得了很大进步,利用热流体计算和水模型解析,对中间包形状、挡墙数量、位置进行了优化设计,提高了去除夹杂物的能力。
此外,还开发了对钢包流入中间包的钢水实施电磁搅拌,利用电磁力使夹杂物聚集上浮排除从而降低夹杂物含量的方法。
高碳轴承钢等洁净度要求高的钢种,经LF-RH冶炼、用带有Ar气保护和电磁搅拌的中间包进行浇注,防止二次氧化,使钢的总氧量小于5ppm,并可批量生产。
LF 炉冶炼的高Al TRIP钢,采用带有Ar气保护和电磁搅拌的中间包,可使总氧量保持在5ppm的水平下进行浇注。
此外,中间包钢水夹杂物含量直接测定技术也有了提高。
1.2 结晶器技术进步1.2.1结晶器浸入式水口夹杂物堵塞防止技术钢水中的氧化铝夹杂物附着在结晶器浸入式水口,使水口堵塞。
炼钢连铸年度总结(3篇)

第1篇一、前言随着我国经济的快速发展,钢铁行业作为国民经济的重要支柱产业,其地位和作用日益凸显。
炼钢连铸作为钢铁生产的关键环节,其技术水平的高低直接影响着钢铁企业的生产效率和产品质量。
本年度,我单位在炼钢连铸领域取得了显著成绩,现将年度总结如下:二、工作回顾1. 技术创新与改进(1)设备升级:本年度,我单位对炼钢连铸设备进行了全面升级,引进了国际先进的炼钢连铸生产线,提高了生产效率和产品质量。
(2)工艺优化:针对生产过程中存在的问题,我们不断优化炼钢连铸工艺,降低能耗,提高金属收得率,确保产品质量稳定。
(3)技术创新:我单位积极开展技术创新,成功研发了多项新技术、新工艺,为炼钢连铸生产提供了有力保障。
2. 安全生产(1)加强安全管理:我们始终把安全生产放在首位,严格执行安全生产责任制,确保生产过程安全稳定。
(2)隐患排查治理:定期开展安全隐患排查,及时发现并消除安全隐患,降低事故发生率。
(3)员工安全培训:加强员工安全教育培训,提高员工安全意识和操作技能。
3. 降本增效(1)优化生产流程:通过优化生产流程,提高生产效率,降低生产成本。
(2)节能降耗:加大节能降耗工作力度,降低能源消耗,提高资源利用率。
(3)技术创新:通过技术创新,降低原材料消耗,提高产品附加值。
4. 市场拓展(1)开拓新市场:积极拓展国内外市场,提高产品市场占有率。
(2)加强客户关系维护:与客户保持良好沟通,提高客户满意度。
(3)提升品牌形象:通过优质的产品和服务,提升企业品牌形象。
三、工作亮点1. 生产指标完成情况(1)产量:本年度,炼钢连铸产量同比增长10%,超额完成年度生产任务。
(2)质量:产品质量稳定,合格率高达99.8%,顾客满意度不断提高。
(3)能耗:通过节能降耗措施,能耗同比下降5%,为企业节约了大量成本。
2. 技术创新成果(1)成功研发了新型炼钢连铸工艺,提高了生产效率和产品质量。
(2)引进了国际先进的炼钢连铸生产线,提升了企业核心竞争力。
我国炼钢-连铸技术发展和xxxx 年展望.doc

1我国炼钢-连铸技术发展和2010 年展望殷瑞钰钢铁研究总院北京10081摘要:本文系统总结了2000 年以来国内炼钢-连铸技术的发展和主要的技术成果,分析了目前炼钢-连铸生产技术的主要问题,并对2010 年我国炼钢-连铸的技术发展方向进行了系统阐述。
为了进一步提高国内炼钢-连铸的生产技术水平,必须确立21 世纪新一代钢铁厂的新理念和新目标,通过对炼钢-连铸生产过程的系统优化、解析与集成,建立起高效、低成本洁净钢生产平台。
讨论了洁净钢生产平台建设面临的主要技术问题、解决方法和具体措施。
关键词:炼钢、连铸、炉外精炼、洁净钢、流程工程前言进入新世纪以来,我国钢铁生产持续发展,钢产量增加,许多企业的技术装备达到了国际水平,钢材品种与质量已接近或达到国际先进水平,上述事实说明我国钢铁工业的发展已经进入一个新的时代。
今后几年,我国钢铁工业不但应在规模和质量等方面达到国际先进水平,而且在钢铁生产、工程设计、工艺与装备、节能减排、环保等方面的研究开发、生产运行都应走向国际前沿。
为实现上述战略目标,必须认真回顾总结新世纪以来我国钢铁工业特别是炼钢-连铸生产技术发展的成就,分析存在的问题,研究今后炼钢-连铸技术的发展趋势和方向,不断创新,为完善和发展新一代炼钢工艺流程做出贡献。
1.炼钢-连铸生产和技术的发展2000 年以来,国内炼钢-连铸生产和技术取得明显的进步,主要表现在以下几个方面:1.1 钢产量高速增长图1 给出2000 年以来国内钢铁产量增长趋势,粗钢产量从2000 年1.285 亿吨增长到2007年4.892 亿吨,平均年增长率为18.2%。
转炉是目前中国最主要的炼钢方法,转炉钢产量从20001080902000 2001 2002 2003 2004 2005 2006 20071000020000300004000050000比例 (%)产量(万吨)年份粗钢转炉钢电炉钢转炉钢比例电炉钢比例图1 2000 年以来国内粗钢产量增长与生产结构的变化2年的1.058 亿吨增长到2007 年的4.4 亿吨,平均年增长率为19.5%,高于国内粗钢产量增长速度。
2023年连铸坯行业市场发展现状
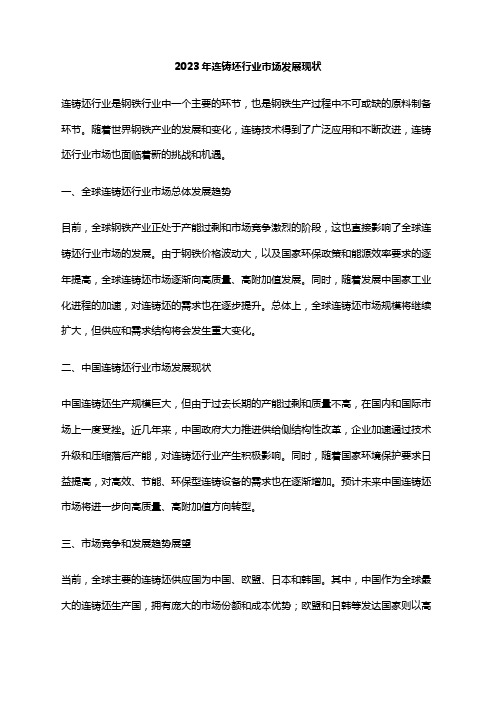
2023年连铸坯行业市场发展现状连铸坯行业是钢铁行业中一个主要的环节,也是钢铁生产过程中不可或缺的原料制备环节。
随着世界钢铁产业的发展和变化,连铸技术得到了广泛应用和不断改进,连铸坯行业市场也面临着新的挑战和机遇。
一、全球连铸坯行业市场总体发展趋势目前,全球钢铁产业正处于产能过剩和市场竞争激烈的阶段,这也直接影响了全球连铸坯行业市场的发展。
由于钢铁价格波动大,以及国家环保政策和能源效率要求的逐年提高,全球连铸坯市场逐渐向高质量、高附加值发展。
同时,随着发展中国家工业化进程的加速,对连铸坯的需求也在逐步提升。
总体上,全球连铸坯市场规模将继续扩大,但供应和需求结构将会发生重大变化。
二、中国连铸坯行业市场发展现状中国连铸坯生产规模巨大,但由于过去长期的产能过剩和质量不高,在国内和国际市场上一度受挫。
近几年来,中国政府大力推进供给侧结构性改革,企业加速通过技术升级和压缩落后产能,对连铸坯行业产生积极影响。
同时,随着国家环境保护要求日益提高,对高效、节能、环保型连铸设备的需求也在逐渐增加。
预计未来中国连铸坯市场将进一步向高质量、高附加值方向转型。
三、市场竞争和发展趋势展望当前,全球主要的连铸坯供应国为中国、欧盟、日本和韩国。
其中,中国作为全球最大的连铸坯生产国,拥有庞大的市场份额和成本优势;欧盟和日韩等发达国家则以高品质、高附加值连铸坯为主战场。
市场上,不同规模和类型的企业共存,市场竞争激烈。
同时,新技术、新材料不断涌现,将会对连铸坯市场产生重要影响。
总之,连铸坯行业市场将继续扩大,但需求和供应结构将发生较大变化,未来市场竞争将更加激烈。
企业需要不断加强技术创新,提升产品质量和附加值,逐步向高端市场发展,谋求市场竞争优势。
国内外现代连铸技术的应用现状与发展前景
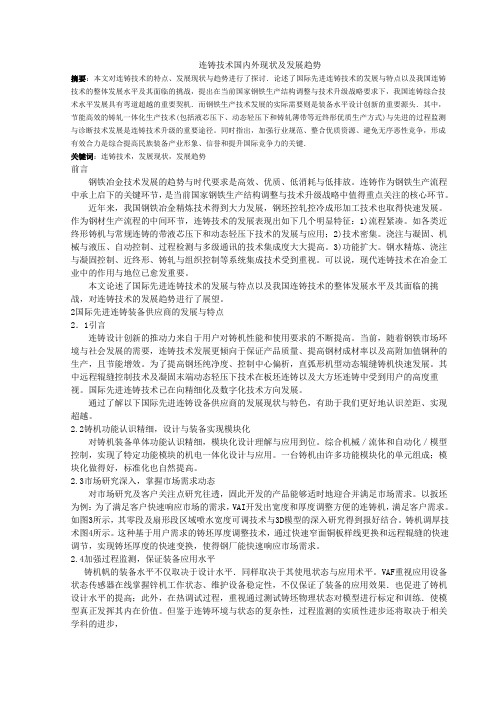
连铸技术国内外现状及发展趋势摘要:本文对连铸技术的特点、发展现状与趋势进行了探讨.论述了国际先进连铸技术的发展与特点以及我国连铸技术的整体发展水平及其面临的挑战,提出在当前国家钢铁生产结构调整与技术升级战略要求下,我国连铸综合技术水平发展具有弯道超越的重要契机.而钢铁生产技术发展的实际需要则是装备水平设计创新的重要源头.其中,节能高效的铸轧一体化生产技术(包括液芯压下、动态轻压下和铸轧薄带等近终彤优质生产方式)与先进的过程监测与诊断技术发展是连铸技术升级的重要途径。
同时指出,加强行业规范、整合优质资源、避免无序恶性竞争,形成有效合力是综合提高民族装备产业形象、信誉和提升国际竞争力的关键.关键词:连铸技术,发展现状,发展趋势前言钢铁冶金技术发展的趋势与时代要求是高效、优质、低消耗与低排放。
连铸作为钢铁生产流程中承上启下的关键环节,是当前国家钢铁生产结构调整与技术升级战略中值得重点关注的核心环节。
近年来,我国钢铁冶金精炼技术得到大力发展,钢坯控轧控冷成形加工技术也取得快速发展。
作为钢材生产流程的中间环节,连铸技术的发展表现出如下几个明显特征:1)流程紧凑。
如各类近终形铸机与常规连铸的带液芯压下和动态轻压下技术的发展与应用;2)技术密集。
浇注与凝固、机械与液压、自动控制、过程检测与多级通讯的技术集成度大大提高。
3)功能扩大。
钢水精炼、浇注与凝固控制、近终形、铸轧与组织控制等系统集成技术受到重视。
可以说,现代连铸技术在冶金工业中的作用与地位已愈发重要。
本文论述了国际先进连铸技术的发展与特点以及我国连铸技术的整体发展水平及其面临的挑战,对连铸技术的发展趋势进行了展望。
2国际先进连铸装备供应商的发展与特点2.1引言连铸设计创新的推动力来自于用户对铸机性能和使用要求的不断提高。
当前,随着钢铁市场环境与社会发展的需要,连铸技术发展更倾向于保证产品质量、提高钢材成材率以及高附加值钢种的生产,且节能增效。
为了提高钢坯纯净度、控制中心偏析,直弧形机型动态辊缝铸机快速发展。
连铸技术国内外现状及发展趋势

连铸技术国内外现状及发展趋势
连铸技术是一种现代化的钢铁生产工艺,旨在提高钢铁生产效率与质量。
自上世纪80年代起,连铸技术在全球范围内得到广泛应用,并不断发展。
当前,连铸技术已成为钢铁工业中的主流生产工艺之一。
国内,随着钢铁行业的不断发展,连铸技术也发展壮大。
目前,国内的连铸机数量和产量均居世界前列。
同时,国内企业也在不断引进新的技术和设备,以提高生产效率和质量。
此外,国内的连铸技术也在不断创新,如微量元素控制技术、智能化控制技术等,为生产提供更多的选择。
国外,欧美、日本等工业发达国家一直处于连铸技术的领先地位。
他们在研究和应用连铸技术方面投入巨大,不断创新。
如今,一些新的连铸技术已经应用于生产中,比如脱氧合金化技术、超细化技术等。
同时,在连铸技术的数字化、智能化方面,国外也取得了一定的进展和成果。
这些技术的应用,使得钢铁生产效率和质量得到了进一步提高。
总的来说,连铸技术已经成为了钢铁生产的主流工艺之一,国内外的企业都在不断发展和创新。
未来,随着科技的不断进步和工业的不断发展,连铸技术将会更加完善和智能化,为钢铁生产带来更多的发展机遇。
- 1 -。
连铸技术的现状及发展趋势

连铸技术的现状及发展趋势摘要:随着科学技术的发展,连铸技术的发展也越来越趋向于成熟。
本文主要介绍了连铸技术在国内外的发展现状和趋势,用到电磁冶金、终形连铸、中间包的加热、结晶器液压振动、在线调宽、摩擦力监控和中间包连续测温等技术,在介绍技术的同时,又联系现实的生产状况,分析了它的发展状况。
关键词:连铸技术;现状;发展;趋势一、近终形连铸技术的介绍近终形连铸技术就是一种集连铸、轧制和热处理为一体的可以生产特殊新材料的一种技术,它最大的特点就是快速凝固,这样可以生产出传统轧制工艺无法生产的材料。
连铸技术分为多种,下面介绍薄板坯连铸和薄带连铸技术。
对于薄板坯连铸技术,薄板坯连铸技术早在1989年就开始投产,在美国最先兴起,结合了德国当时最先进的生产技术。
随着时代的发展,薄板坯连铸技术也日渐成熟,早先只有国外公司拥有这种生产技术,现在,中国已经成为薄板坯连铸产能最大、生产线最多的国家。
对于薄带连铸技术,它相对于其它连铸技术更为先进,它属于冶金领域中一项前沿技术。
它又分为前期传统的技术和现代薄带连铸技术,区别于以前它最大的特点就是薄带连铸技术更加综合,它集连铸、轧制和热处理技术为一体,生产的薄带坯更加精细,并且可以一次成型。
现在的连铸技术中最受关注还有就是双辊薄带连铸技术,它广受关注的原因就是此种高效的生产工艺可以提高生产效率,增加高额的经济效益[1]。
双辊薄带连铸这种工艺非常复杂,所以至今没有完全掌握,虽然近些年有些突破性进展,但是,想要达到商业化量产阶段是不可能的,还是需要大量的研究和探索工作。
其中有几大问题,第一就是生产中的裂纹,这是制约此项技术发展的重大原因之一。
第二就是厚度不均匀的问题,现在能实现的厚度就是在小范围内波动,但还是不利于冷轧过程的进行。
第三就是连铸的速度,上面也提到,现在的技术不足,生产成品的速率低下,不能满足商业化需求。
第四就是薄带的宽度小,并且侧封还不理想。
剩下的还有铸辊的材质问题、钢液的氧化问题、二次冷却问题等等。
连铸过程控制系统的发展及展望

连铸过程控制系统的发展及展望随着现代工业的快速发展,钢铁行业作为支撑工业发展的重要组成部分,也面临着不断提高生产效率和产品质量的挑战。
在连铸工艺中,连铸过程控制系统的发展起着至关重要的作用。
本文将探讨连铸过程控制系统的发展历程,并对其未来发展进行展望。
1. 连铸过程控制系统的发展历程连铸过程控制系统起源于20世纪80年代,当时的连铸工艺主要依赖于人工操作和经验判断。
然而,这种传统的生产方式存在着质量不稳定、效率低下和安全隐患等问题。
为了应对这些挑战,不断有研究人员和工程师投身于连铸过程控制系统的研究与开发。
随着计算机技术的迅猛发展,连铸过程控制系统也得到了巨大的改进。
首先,人工操作逐渐被自动控制所取代,使得生产过程更加稳定和可靠。
其次,引入了物联网和大数据技术,实现了对连铸设备的远程监控和故障诊断,大大提高了生产效率和设备利用率。
同时,随着传感器技术和数据采集技术的不断革新,连铸过程控制系统的数据获取能力不断提高。
温度、速度、尺寸等关键参数可以实时监测,实现对连铸过程的精细控制。
这不仅提高了产品的质量稳定性,还降低了生产能耗和生产成本。
2. 连铸过程控制系统的展望随着人工智能技术的迅速发展,连铸过程控制系统将进入一个全新的时代。
在未来,我们可以期待以下几个方面的发展:2.1 智能优化控制:利用人工智能的算法和模型,连铸过程控制系统可以自动优化参数设定和控制策略,最大限度地提高连铸工艺的效率和产品质量。
2.2 联网与云平台应用:通过将连铸过程控制系统与云平台相连接,实现设备之间的数据共享和远程控制。
这将加强设备之间的协同作业,提高整体生产效益。
2.3 预测分析与预警系统:借助大数据和机器学习技术,连铸过程控制系统可以对连铸设备的运行状态进行实时监测和预测分析,提前发现潜在的设备故障,并及时采取措施,避免生产事故的发生。
2.4 绿色制造与可持续发展:连铸过程控制系统将更加注重节能减排和资源利用的可持续性。
- 1、下载文档前请自行甄别文档内容的完整性,平台不提供额外的编辑、内容补充、找答案等附加服务。
- 2、"仅部分预览"的文档,不可在线预览部分如存在完整性等问题,可反馈申请退款(可完整预览的文档不适用该条件!)。
- 3、如文档侵犯您的权益,请联系客服反馈,我们会尽快为您处理(人工客服工作时间:9:00-18:30)。
炼钢连铸技术发展和年展望Modified by JEEP on December 26th, 2020.1我国炼钢-连铸技术发展和2010 年展望殷瑞钰钢铁研究总院北京10081摘要:本文系统总结了2000 年以来国内炼钢-连铸技术的发展和主要的技术成果,分析了目前炼钢-连铸生产技术的主要问题,并对2010 年我国炼钢-连铸的技术发展方向进行了系统阐述。
为了进一步提高国内炼钢-连铸的生产技术水平,必须确立21 世纪新一代钢铁厂的新理念和新目标,通过对炼钢-连铸生产过程的系统优化、解析与集成,建立起高效、低成本洁净钢生产平台。
讨论了洁净钢生产平台建设面临的主要技术问题、解决方法和具体措施。
关键词:炼钢、连铸、炉外精炼、洁净钢、流程工程前言进入新世纪以来,我国钢铁生产持续发展,钢产量增加,许多企业的技术装备达到了国际水平,钢材品种与质量已接近或达到国际先进水平,上述事实说明我国钢铁工业的发展已经进入一个新的时代。
今后几年,我国钢铁工业不但应在规模和质量等方面达到国际先进水平,而且在钢铁生产、工程设计、工艺与装备、节能减排、环保等方面的研究开发、生产运行都应走向国际前沿。
为实现上述战略目标,必须认真回顾总结新世纪以来我国钢铁工业特别是炼钢-连铸生产技术发展的成就,分析存在的问题,研究今后炼钢-连铸技术的发展趋势和方向,不断创新,为完善和发展新一代炼钢工艺流程做出贡献。
1.炼钢-连铸生产和技术的发展2000 年以来,国内炼钢-连铸生产和技术取得明显的进步,主要表现在以下几个方面:钢产量高速增长图1 给出2000 年以来国内钢铁产量增长趋势,粗钢产量从2000 年亿吨增长到2007年亿吨,平均年增长率为%。
转炉是目前中国最主要的炼钢方法,转炉钢产量从200010802000 2001 2002 2003 2004 2005 2006 20071000020000300004000050000比例 (%)产量(万吨)年份粗钢转炉钢电炉钢转炉钢比例电炉钢比例图1 2000 年以来国内粗钢产量增长与生产结构的变化2年的亿吨增长到2007 年的亿吨,平均年增长率为%,高于国内粗钢产量增长速度。
转炉钢比例相应从2000 年的%增长到90%左右。
电炉也是目前国内主要炼钢方法,随着中国钢产量迅速增长,电炉钢比例2003 年以前缓慢增长,最高达%;2004 年以后,由于转炉钢的快速增长,电炉钢比例逐年降低,但电炉钢产量持续增长,和2000 年相比电炉钢产量翻了一番。
在国内钢产量迅速发展的同时,连铸比也不断增长。
如图2 所示,2000年全国连铸坯产量为亿吨,连铸比%;2007 年全国连铸坯产量为亿吨,连铸比%。
随着连铸比的提高,成材率也相应提高,平均达到了%,说明连铸技术的进步为我国钢铁工业增产增效、节能减排做出了重要贡献。
技术经济指标不断优化国内炼钢-连铸生产技术的进步主要体现在各项技术经济指标不断优化。
表1给出2003 至2007 年国内转炉、电炉和连铸的主要技术经济指标变化情况。
表1 2003 年以来国内大、中型钢铁企业炼钢-连铸技术经济平均指标变化2003 2004 2005 2006 2007钢铁料消耗,kg/t 1085日历作业率,%转炉平均炉龄,炉4630 5218 5785 6823 7921电耗,kWh/t 422 328电极消耗,kg/t电炉冶炼周期,min连铸比,%日历作业率,%连铸连浇炉数,炉/ /国内转炉炼钢技术进步主要体现在:完善溅渣护炉工艺,提高转炉炉龄;推广强化供氧技术,提高转炉作业率;推广长寿复吹工艺,进一步降低钢铁料消耗并提高以终点控制为核心的转炉自动化控制水平。
20 年来电炉生产技术发生重大变化:采用大型高功率和超高功率电炉淘汰607075808590951002000 2001 2002 2003 2004 2005 2006 20071000020000300004000050000连铸比,成材率 /%产量/万吨年连铸坯产量连铸比成材率图2 2000 年后连铸坯产量、连铸比、成材率的变化大批30 吨以下小型电炉;建设电炉-精炼-连铸-连轧现代化短流程生产线,采用优化配料与供电制度,强化供氧提高化学能输入量和部分电炉采用热装铁水等新工艺技术,达到降低冶炼电耗,缩短冶炼周期,实现多炉连浇。
在此基础上,实现电炉生产多元化,形成电炉-普钢长材、电炉-特殊钢长材、电炉-无缝钢管、电炉-中厚板和电炉-薄板坯连铸连轧等多种生产线,完善了电炉钢产品结构,扩大了生产品种。
20 世纪90 年代,国内连铸基本以小方坯连铸为主,至2007 年已建成板坯连铸机(宽度700mm 以上)175 台,237 流;薄(中)板坯连铸机17 台,18 流;方坯和矩形坯连铸机(>)437 台,1323 流;小方坯连铸机305 台,1027 流;圆坯连铸机48 台,173 流。
全国总计连铸机996 台,2806 流,年生产能力达到亿吨。
应该看到新世纪以来,我国连铸呈继续快速发展的态势,而且自主开发的能力进一步提高。
随着国内炼钢-连铸技术的进步和技术经济指标的优化,获得明显经济效益:据2007 年国内93 家大中型企业的统计,年利润达亿元,比上年同期增长%。
建立现代化炼钢生产流程2000 年以后国内钢铁企业重点开展钢铁生产流程与工艺结构的优化,基本建立起现代化炼钢生产工艺流程:转炉流程:铁水脱硫预处理→转炉复合吹炼→二次精炼→全连铸;电炉流程:大型超高功率电炉(兑铁水)冶炼→二次精炼→全连铸。
近几年铁水脱硫预处理技术在国内广泛应用,主要采用KR 法石灰脱硫和喷吹法脱硫(包括CaO、CaC2 喷吹,纯Mg 喷吹和Mg+CaO 喷吹)等方法。
铁水预处理的装备能力逐年提高,至2007 年铁水脱硫比已接近50%,宝钢、武钢、鞍钢等大型钢铁公司已基本实现100%铁水预处理。
表2 给出目前国内常用的几种铁水脱硫工艺技术的比较,说明国内铁水脱硫预处理工艺已经积累了比较丰富的经验,为钢厂合理选择铁水脱硫预处理工艺提供了广泛的空间。
表2 各种脱硫方法的技术比较脱硫工艺石灰、CaC2 脱硫Mg 脱硫脱硫方法KR 脱硫喷粉脱硫纯Mg 混合脱硫剂CaO 粉CaO+CaC2 Mg Mg+CaO4终点[S](%) ~ ~ ~ ~处理时间(min) 8~15 23~28 10~15 10~15处理温降(℃) 25~30 30~35 8~12 10~15脱硫剂消耗(kg/t) 6~8 4(CaC2)~12(CaO) ~ ~综合处理成本(元/t)[1] (CaC2)为提高转炉生产效率和扩大洁净钢生产比例,国内大多数转炉炼钢厂综合采用铁水预处理、复合吹炼、强化供氧、终点动态控制和溅渣护炉等成套先进工艺技术,较大幅度提高转炉的生产效率,降低生产成本,提高钢水的洁净度。
2000 年以前国内电炉技术进步的重点是采用大型超高功率电炉淘汰小型电炉,如2000 年我国电炉座数已从1600 多座减少到179 座,其中50 吨以上的大、中型电炉占全国电炉钢产量61%。
2000 年以后国内电炉厂综合采用铁水热装、废钢预热、优化配料供电和供氧等先进技术,获得明显的效果。
如表 3 所示,电炉采用铁水热装工艺冶炼电耗平均降低约67kwh/t 钢,减少电极消耗35%,缩短冶炼周期10min。
国内已有16 座60~150 吨电炉采用铁水热装工艺,其单吨的生产率超过了8000 吨/吨·年。
表3 国内大型电炉全废钢与兑铁水冶炼工艺的技术经济指标比较统计工厂数/个吨位/MVA 生产工艺铁水比%电耗kwh/t氧耗M3/t电极消耗kg/t冶炼周期min4 50~120全废钢+预热10 50~150 废钢+铁水20-30钢材洁净度与品种质量的进步表4 2007 年国内二次精炼设备能力总汇(不包括吹Ar)为了满足市场对洁净钢生产的需求,国内钢厂普遍重视二次精炼工艺,完善二次精炼设施。
国内大、中型骨干企业钢水二次精炼的比例从2000 年不足20%迅速增长到2007 年64%。
表4 给出2007 年国内各种二次精炼设备的台数和公称吨位总计(不包括吹Ar 在内)。
随着精炼设备的增长,二次精炼工艺技术也取得明显的进步,形成了以挡渣精炼种类台数/台总公称吨位/吨RH 61 9040AOD 43 1712VOD 27 1475LF 295 23440VD 32 2510CAS-OB 16 2190合计474 403675出钢、合成渣洗、炉渣改质、白渣精炼和喂线与钢中夹杂物形态控制、钢水温度、成分精确控制以及真空脱碳、脱气、夹杂物上浮分离等核心技术为基础的二次精炼工艺技术,能满足不同类型产品的批量生产,达到超低氧、超低碳和超低硫等高品质洁净钢的质量要求。
二次精炼技术的发展使国内钢材的洁净度得到显着的提高:15 年前国内绝大多数转炉厂生产的钢水洁净度(.(S+P+T. O+N+H))波动在300~,目前国内多数钢厂已可以大批量生产钢水洁净度≤的洁净钢,宝钢、武钢、鞍钢和首钢等大型钢铁企业生产的部分钢种洁净度可以达到≤。
从表5 可以看出,国内生产的典型高附加值产品的洁净度已达到国际先进水平。
表5 国内某些高质量要求洁净钢达到的水平(.10-6)钢种[C] [N] [S] [P] T[O] [H] 夹杂物其它IF 钢<20 <20 <30 <100 <20 <2 d<高强度汽车板<50 <50 <100 <30 <2 d<管线钢(X80) <50 <10 <80 <20 <1轴承钢(GCr15) <50 <100 <10 < d< [Ti]≤30帘线钢<40 <30 <100 <30 <2 d< 无Al2O3 夹杂高速铁路钢轨<40 <30 <100 <15 < d< [Al]<40电工钢(35W230) <24 <20 <10 <100 <15 <2 d<不锈钢(409L) <50 <70 <10 <150 <30 <2 d<钢材洁净度的大幅度提高导致我国钢铁工业产品结构发生了重大改变。
如表6 所示,近几年国内典型高品质钢种的生产比例迅速增长,不仅给钢铁企业带来更大的经济效益,而且有力的支持了国家经济建设。
表6 2000~2006 年典型高品质钢种增长率钢种铁道用钢大型型钢特厚板中厚板冷轧薄板镀层板冷轧电工钢板无缝管2000 年产量/万吨158 360 76 1668 495 328 64 4152006 年产量/万吨334 917 328 8214 2605 1625 330 1484增长率/%节能环保技术的发展年份综合能耗转炉电炉2000 9202001 8762002 8152003 780表7 国内炼钢工序能耗变化(kgce/t 钢)6近年来,国内钢铁企业高度重视节能减排工作,研究开发和应用各种先进的节能环保技术。