加工中心刀具卡
加工中心硬质合金刀具切削参数表经典

0.06 -0.025--0.047 高速推荐侧刃切削
1500 -0.025--0.047 高速推荐侧刃切削
13000 -0.025--0.047 高速推荐侧刃切削
60 -0.025--0.047 高速推荐侧刃切削
0.81 -0.025--0.047 高速推荐侧刃切削
刀具直径
E6 E6 E6 E6 E6 E6 E8 E8 E8 E8 E8 E8 刀具直径
0.06 -0.025--0.047 高速推荐侧刃切削
1500 -0.025--0.047 高速推荐侧刃切削
13000 -0.025--0.047 高速推荐侧刃切削
60 -0.025--0.047 高速推荐侧刃切削
0.81 -0.025--0.047 高速推荐侧刃切削
高速切削 刀具精度
侧刃切削
15 -0.025--0.047 高速推荐侧刃切削
侧刃切削
0.2-0.3 4
1200 2950 50 0.783 0.2-0.3
6 1300 2800 50 0.783 侧刃切削
0.25-0.5 8
1500 1750 60 1.087 0.25-0.5 10 1500 2000 60
高速切削 刀具精度
侧刃切削
9
-0.025--0.047 高速推荐侧刃切削
0.06 -0.025--0.047 高速推荐侧刃切削
1500 -0.025--0.047 高速推荐侧刃切削
13000 -0.025--0.047 高速推荐侧刃切削
60 -0.025--0.047 高速推荐侧刃切削
0.81 -0.025--0.047 高速推荐侧刃切削
9
-0.025--0.047 高速推荐侧刃切削
盘类零件加工工艺

附表1 机械加工工艺过程卡片1附表2 机械加工工艺过程卡片23附表3 机械加工工艺过程卡片4附表4 数控加工工序卡5附表5 数控加工工序卡6附表6 数控加工工序卡7附表7 数控加工工序卡8附表8 数控加工刀具卡片9附表9 数控加工刀具卡片10附表10 数控加工刀具卡片11附表11 数控加工进给路线图廓12附表12 数控加工进给路线图廓13附表13 数控加工进给路线图廓14附表14 数控加工进给路线图03 钻Φ32孔数控机床ck6140O0002 3爪卡盘乳化液数控加工15附表15 数控加工进给路线图04 钻铰所有孔立式加工中心XH714O0003 专用夹具乳化液数控加工16附表16 数控加工进给路线图05 钻铰Φ11孔立式加工中心XH714O0004 专用夹具乳化液数控加工17附录17 数控加工程序O0001:N0010 G40 G17 G90 G70N0020 G91 G28 Z0.0N0030 T00 M06N0040 G0 G90 X-.7181 Y.4098 S0 M03 N0050 G43 Z.6693 H00N0060 G83 Z-.9055 R.6693 F9.8 Q0.0 N0070 X.7139 Y.417N0080 X.0042 Y-.8268N0090 G80N0100 M02O0002:N0010 G40 G17 G90 G70N0020 G91 G28 Z0.0 N0030 T00 M06N0040 G0 G90 X-.6988 Y1.2104 S0 M03N0050 G43 Z.1969 H00N0060 G83 Z-1.7717 R.1969 F9.8 Q0.0N0070 X-1.3976 Y0.0N0080 X-.6988 Y-1.2104N0090 X.6988N0100 X1.3976 Y0.0N0110 X.6988 Y1.2104N0120 G80N0130 M02O0003:N0010 G40 G17 G90 G70N0020 G91 G28 Z0.0N0030 T00 M06N0040 G0 G90 X-2.3828 Y-1.3846 S0 M03N0050 G43 Z-1.1849 H00N0060 G83 X-.9508 Y-.5578 R-1.1849 F9.8Q0.0N0070 G80N0080 M02O0004:N0010 G40 G17 G90 G70N0020 G91 G28 Z0.0N0030 T00 M06N0040 G0 G90 X.0042 Y-.8268 S0 M03N0050 G43 Z.6693 H00N0060 G83 Z-.9055 R.6693 F9.8 Q0.018N0070 X-.7181 Y.4098N0080 X.7139 Y.417N0090 G80N0100 M02O0005:N0010 G40 G17 G90 G70N0020 G91 G28 Z0.0N0030 T00 M06N0040 G0 G90 X-.6988 Y-1.2104 S0 M03 N0050 G43 Z1.1811 H00N0060 G83 Z-1.5748 R1.1811 F9.8 Q0.0 N0070 X-1.3976 Y0.0N0080 X-.6988 Y1.2104N0090 X.6988 N0100 X1.3976 Y0.0N0110 X.6988 Y-1.2104N0120 G80N0130 M02O0006:N0010 G40 G17 G90 G70N0020 G91 G28 Z0.0N0030 T00 M06N0040 G0 G90 X-.6988 Y-1.2104 S0 M03N0050 G43 Z1.1811 H00N0060 G83 Z-.9843 R1.1811 F9.8 Q0.0N0070 X-1.3976 Y0.0N0080 X-.6988 Y1.2104N0090 X.6988N0100 X1.3976 Y0.0N0110 X.6988 Y-1.2104N0120 G80N0130 M02O0007:N0010 G40 G17 G90 G70N0020 G91 G28 Z0.0N0030 T00 M06N0040 G0 G90 X-2.3828 Y-1.3846 S0 M03N0050 G43 Z-1.1849 H00N0060 G83 X-.9508 Y-.5578 R-1.1849 F9.8Q0.0N0070 G80N0080 M021920。
加工中心编程及操作
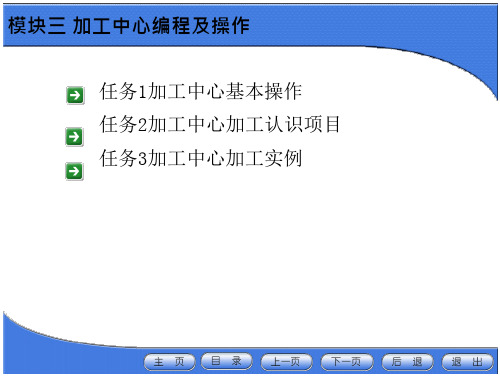
模块三 数控铣削、加工中心编程及操作
刀库移动—主轴升降式换刀过程
模块三 数控铣削、加工中心编程及操作
5 .加工中心的刀具系统
加工中心上使用的刀具由刃具部分和连接刀柄两部分组成。 刃具部分包括钻头、铣刀、镗刀、铰刀等等。连接刀柄部分基本 已规范化,制订了一系列标准。
刀具系统的种类
整体式数控刀具系统 应用广 模块式数控刀具系统
图1-1
模块三 数控铣削、加工中心编程及操作
2. 加工中心的分类及其加工范围
根据机床的主轴布置形式将其分为以下三种:
(1) 立式加工中心: 指主轴垂直布置的加工中心。 它具有操作方便、工件装夹和找正容易、占地面积小等
优点,故应用较广。但由于受立柱的高度和自动换刀装置 的限制,不能加工太高的零件。因此,主要适用于加工高 度尺寸小、加工面与主轴轴线垂直的板材类、壳体类零件, 也可用于模具加工 。
模块二 加工中心编程与加工操作
5.对刀
对刀的目的是通过刀具或对刀工具确定工件坐标系与 机床坐标系之间的空间位置关系,并将对刀数据输入到相 应的存储位置,是数控加工中最重要的操作内容,其准确 性将直接影响零件的加工精度。对刀可以采用铣刀接触工 件或通过塞尺接触工件对刀,但精度较低。加工中常用寻 边器和Z向设定器对刀,效率高,能保证对刀精度。
模块二 加工中心编程与加工操作
3.实训过程参照企业5S标准进行管理和实施。
1S整理:即——1)对自己的工作场所(范围)全面检查,包括看得 到和看不到的;2)将不要物品清除出工作场所;3)每日自我检查。
2S整顿:即1)需要的物品明确放置场所;2)摆放整齐、有条不 紊;3)地板划线定位 ;4)场所、物品标示
它是加工中心中种类最多、规格最全、应用范围最广的一 种。
加工中心常用刀具参数

加工中心常用刀具参数加工中心是一种用来进行金属材料的数控加工的机床,常用刀具参数是决定加工质量和效率的重要因素之一、以下是一些常用的加工中心刀具参数。
1.刀柄类型:加工中心常用的刀柄类型有普通刀柄、卡盘刀柄和棒料刀柄。
普通刀柄适用于一般的加工需求,卡盘刀柄适用于需要多次换刀的加工,棒料刀柄适用于棒料材料的加工。
2. 刀具直径:刀具直径是指刀具刃部的直径,常用的刀具直径有2mm、4mm、6mm等。
刀具直径的选择要根据加工件的尺寸、加工深度和加工材料的硬度等因素确定。
3.切削长度:切削长度是指刀具的刃部可以进入工件的深度。
切削长度的选择主要根据加工件的尺寸和形状来确定。
4.刀具材料:常用的刀具材料有硬质合金、高速钢和陶瓷等。
硬质合金的刀具具有较高的硬度和耐磨性,适用于加工硬度较高的材料;高速钢的刀具耐热性较好,适用于高速加工;陶瓷刀具具有良好的耐磨性和耐高温性,适用于高精度加工。
5.刀具涂层:刀具涂层可以提高刀具的耐磨性和切削性能。
常用的刀具涂层有涂层碳化物、涂层氮化物和涂层氧化物等。
不同的刀具涂层适用于不同的加工材料和加工工艺。
6.切削速度:切削速度是指刀具在切削过程中切削的线速度。
切削速度的选择要根据加工材料的硬度、刀具的材料和刀具的刃数等因素确定。
7.进给速度:进给速度是指刀具在切削过程中每分钟进给的长度。
进给速度的选择要根据加工材料的硬度、刀具的材料和加工质量要求等因素确定。
8.加工参数:加工参数是指切削深度、切削宽度和进给量等加工过程中的参数。
加工参数的选择要根据加工材料的硬度、刀具的材料和加工质量要求等因素确定。
常用刀具参数的选择要根据具体的加工要求和材料特性等因素来确定,可以通过试刀和实验等方式来确定最佳的刀具参数。
刀具参数的正确选择可以提高加工效率和加工质量,减少加工成本和损耗。
加工中心常用刀具参数
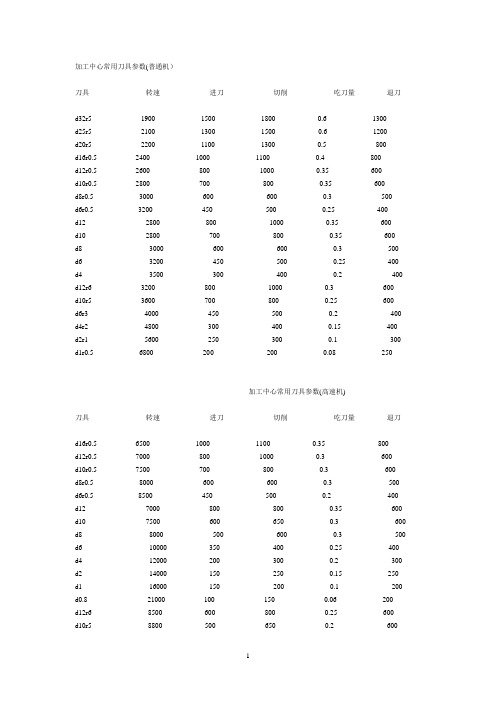
加工中心常用刀具参数(普通机)刀具转速进刀切削吃刀量退刀d32r5 1900 1500 1800 0.6 1300d25r5 2100 1300 1500 0.6 1200d20r5 2200 1100 1300 0.5 800d16r0.5 2400 1000 1100 0.4 800d12r0.5 2600 800 1000 0.35 600d10r0.5 2800 700 800 0.35 600d8r0.5 3000 600 600 0.3 500d6r0.5 3200 450 500 0.25 400d12 2800 800 1000 0.35 600d10 2800 700 800 0.35 600d8 3000 600 600 0.3 500 d6 3200 450 500 0.25 400 d4 3500 300 400 0.2 400 d12r6 3200 800 1000 0.3 600d10r5 3600 700 800 0.25 600d6r3 4000 450 500 0.2 400 d4r2 4800 300 400 0.15 400d2r1 5600 250 300 0.1 300 d1r0.5 6800 200 200 0.08 250加工中心常用刀具参数(高速机)刀具转速进刀切削吃刀量退刀d16r0.5 6500 1000 1100 0.35 800d12r0.5 7000 800 1000 0.3 600d10r0.5 7500 700 800 0.3 600d8r0.5 8000 600 600 0.3 500 d6r0.5 8500 450 500 0.2 400d12 7000 800 800 0.35 600 d10 7500 600 650 0.3 600 d8 8000 500 600 0.3 500 d6 10000 350 400 0.25 400 d4 12000 200 300 0.2 300 d2 14000 150 250 0.15 250 d1 16000 150 200 0.1 200 d0.8 21000 100 150 0.06 200d12r6 8500 600 800 0.25 600d10r5 8800 500 650 0.2 6001d6r3 11000 450 400 0.25 400 d4r2 14000 350 250 0.2 300 d2r1 17000 250 200 0.15 250 d1r0.5 19000 200 150 0.1 200常用G代码G00快速定位G01直线G02顺圆G03逆圆G04暂停G08加速G09 试建G17xy平面G18xz平面G19yx平面G20英制G21公制G28返回机床参考点G33螺纹切削G40刀补取消G41左补偿G42右补偿G43刀正偏G44刀负偏G80固定循取消G81固定循环G90绝对坐标G91增量坐标G92工件原点G96--G97恒线速控制G98没分进给G99每转进给常用M代码M00程式停M01选折停M03主轴顺转M04主轴反转M05主轴停M06换刀M07冷却液开(液态)M09------------(雾状)M10卡盘加紧M30程式结束M98调用子程式M99子程式并反回主程式文件(F)-新建(N)... Ctrl+N文件(F)-打开(O)... Ctrl+O文件(F)-保存(S) Ctrl+S文件(F)-另存为(A)... Ctrl+Shift+A 文件(F)-绘图(L)... Ctrl+P文件(F)-导出(E)-部件(P) 0文件(F)-执行(T)-图形交互编程(G)... Ctrl+G文件(F)-执行(T)-Grip 调试(D)... Ctrl+Shift+G 文件(F)-执行(T)-NX Open(N)... Ctrl+U编辑(E)-撤消列表(U)-1 进入“建模”Ctrl+Z编辑(E)-修剪(T) Ctrl+X编辑(E)-粘贴(P) Ctrl+V编辑(E)-删除(D)... Ctrl+D Delete 编辑(E)-选择(L)-最高选择优先级- 特征(F) F编辑(E)-隐藏(B)-隐藏(B)... Ctrl+B2编辑(E)-隐藏(B)-反向隐藏全部(R) Ctrl+Shift+B编辑(E)-隐藏(B)-取消隐藏所选的(S)... Ctrl+Shift+K编辑(E)-隐藏(B)-显示部件中所有的(A) Ctrl+Shift+U编辑(E)-变换(N)... Ctrl+T编辑(E)-对象显示(J)... Ctrl+J编辑(E)-特征(F)-移除参数(V)... Y视图(V)-刷新(R) F5视图(V)-操作(O)-缩放(Z)... Ctrl+Shift+Z视图(V)-操作(O)-旋转(R)... Ctrl+R视图(V)-操作(O)-剖面(C)... Ctrl+H视图(V)-布局(L)-新建(N)... Ctrl+Shift+N视图(V)-布局(L)-打开(O)... Ctrl+Shift+O视图(V)-布局(L)-充满所有视图(F) Ctrl+Shift+F视图(V)-可视化(V)-高质量图像(H)... Ctrl+Shift+H视图(V)-重设方位(E) Ctrl+F8插入(S)-草图(S)... S插入(S)-基准/点(D)-点(P)... P插入(S)-曲线(C)-基本曲线(B)... L插入(S)-设计特征(E)-拉伸(E) (X)插入(S)-设计特征(E)-回转(R)... R插入(S)-联合体(B)-求差(S)... C插入(S)-联合体(B)-求交(I)... Ctrl+C插入(S)-裁剪(T)-修剪的片体(R)... T插入(S)-细节特征(L)-边倒圆(E)... B插入(S)-扫掠(W)-变化的扫掠(V) (V)插入(S)-直接建模(I)-偏置区域(O)... O格式(R)-图层的设置(S)... Ctrl+L格式(R)-视图中的可见层(V)... Ctrl+Shift+V格式(R)-移动至图层(M)... Shift+Z格式(R)-复制至图层(O)... Shift+X格式(R)-WCS-显示(P) W工具(T)-日记(J)-播放(P)... Alt+F8工具(T)-日记(J)-编辑(E) Alt+F11工具(T)-宏(R)-开始记录(R)... Ctrl+Shift+R工具(T)-宏(R)-回放(P)... Ctrl+Shift+P工具(T)-宏(R)-步进(S)... Ctrl+Shift+S工具(T)-特定于工艺(O)-注塑模向导(M)-模具工具(T)-分割实体(O) (4)信息(I)-对象(O)... Ctrl+I分析(L)-距离(D).. K分析(L)-角度(A)... G分析(L)-曲线(C)-刷新曲率图表(R) Ctrl+Shift+C首选项(P)-对象(O)... Ctrl+Shift+J首选项(P)-选择(E)... Ctrl+Shift+T应用(N)-建模(M)... Ctrl+M3M应用(N)-外观造型设计(T)... Ctrl+Alt+S 应用(N)-制图(D)... Ctrl+Shift+DD应用(N)-加工(N)... Ctrl+Alt+MN应用(N)-钣金(H)-NX 钣金(H)... Ctrl+Alt+N 应用(N)-船舶设计(S)... Ctrl+E应用(N)-装配(L) A应用(N)-基本环境(G)... Ctrl+W帮助(H)-根据关联(C)... F1适合窗口(F) Ctrl+F缩放(Z) F6Z旋转(O) F7定向视图(R)-正二测视图(T) HomeF4定向视图(R)-正等测视图(I) End定向视图(R)-俯视图(O) Ctrl+Alt+T 定向视图(R)-前视图(F) Ctrl+Alt+F 定向视图(R)-右(R) Ctrl+Alt+R 定向视图(R)-左(L) Ctrl+Alt+L 捕捉视图(N) F8常用材质缩水none 1.000nylon 1.016abs 1.005ppo 1.010ps 1.006pc+abs 1.0045abs+pc 1.0055pc 1.0045pmma 1.002pa+60%gf 1.001pc+10%gf 1.00354。
加工中心卡刀原因及处理方法

加工中心卡刀原因及处理方法加工中心是一种高精度、高效率的机床设备,广泛应用于各种机械加工领域。
在加工中心中,卡刀是一个重要的零部件,它直接影响到加工质量和效率。
然而,由于各种原因,卡刀可能会发生问题,需要及时处理。
一、卡刀原因及处理方法1. 刀具磨损严重:在长时间使用后,刀具会因为磨损而失去原有的锋利度,导致加工质量下降。
处理方法是定期更换刀具,避免过度磨损。
2. 切削力过大:切削力过大会导致卡刀变形或断裂,严重影响加工效果。
处理方法是优化刀具和切削参数,减小切削力的作用。
3. 加工中心稳定性差:如果加工中心本身稳定性差,容易引起卡刀问题。
处理方法是检查和调整加工中心的各个部件,确保其稳定性。
4. 加工中心刀座松动:如果加工中心的刀座松动,会导致卡刀的位置不准确,影响加工精度。
处理方法是定期检查和紧固刀座,确保其稳定性。
5. 刀具装夹不正确:如果刀具装夹不正确,会导致刀具不稳定,容易发生卡刀问题。
处理方法是正确选择和安装刀具,并确保装夹牢固。
6. 刀具选择不当:如果选择的刀具不适合具体的加工任务,容易出现卡刀问题。
处理方法是根据加工要求选择合适的刀具,并根据实际情况进行调整。
7. 切削液不合适:切削液的选择和使用对卡刀也有一定影响。
处理方法是选择合适的切削液,并按照要求进行使用和更换。
8. 环境温度变化大:加工环境的温度变化也会对卡刀产生影响。
处理方法是控制加工环境温度,避免温度变化过大。
9. 切削参数设置不当:切削参数的设置不当会导致切削力过大,从而引起卡刀问题。
处理方法是根据具体情况调整切削参数,以保证加工效果。
10. 定期保养和维护:定期保养和维护加工中心和刀具,可以有效预防卡刀问题的发生。
处理方法是按照设备和刀具的使用说明进行保养和维护工作。
二、结语卡刀是加工中心中一个重要的零部件,其质量和使用状态直接影响到加工质量和效率。
通过对卡刀原因及处理方法的了解,我们可以更好地预防和处理卡刀问题,确保加工中心的正常运行和加工质量。
(完整版)加工中心新刀具常用切削参数参照表1
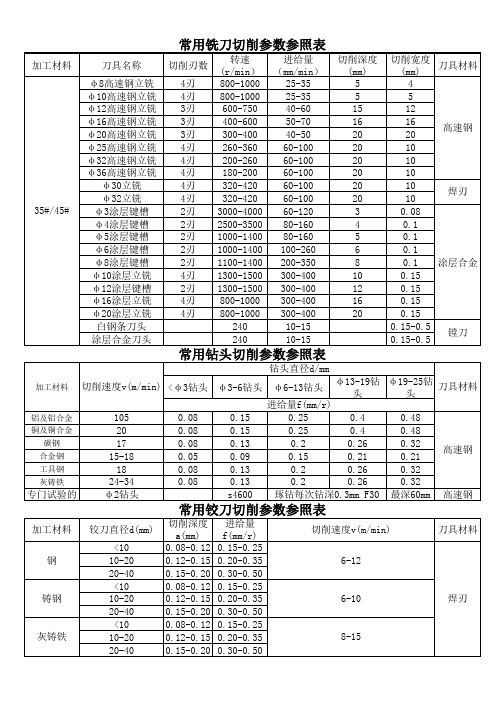
常用圆鼻刀切削参数参照表
加工材料 ZG275-485H
35#/45#
刀具名称
φ16圆鼻刀 φ20圆鼻刀 φ25圆鼻刀 φ25圆鼻刀 φ40圆鼻刀 φ40圆鼻刀 φ63圆鼻刀 φ63圆鼻刀 φ25圆鼻刀 φ32圆鼻刀 φ40圆鼻刀
用途
精加工 精加工 粗加工 精加工 粗加工 精加工 粗加工 精加工 粗加工 粗加工 粗加工
专门试验的
φ2钻头
s4600 琢钻每次钻深0.3mm F30 最深60mm 高速钢
常用铰刀切削参数参照表
加工材料 钢
铰刀直径d(mm)
<10 10-20
切削深度 进给量 a(mm) f(mm/r)
0.08-0.12 0.15-0.25 0.12-0.15 0.20-0.35
切削速度v(m/min) 6-12
2刃 1100-1400 200-350
8
0.1 0.1 涂层合金
φ10涂层立铣
4刃 1300-1500 300-400
10
0.15
φ12涂层键槽
2刃 1300-1500 300-400
12
0.15
φ16涂层立铣
4刃 800-1000 300-400
16
0.15
φ20涂层立铣
4刃 800-1000 300-400
800
60
800
20
700
50
400
60
400
80
120
40-50
120
40-50
用途
钻孔 扩孔 钻孔 钻孔 扩孔 精铰孔 精铰孔
切削宽度 (mm)
刀具材料
高速钢 合金 高速钢 高速钢 高速钢 合金 焊刃
加工中心卡刀原因及处理方法
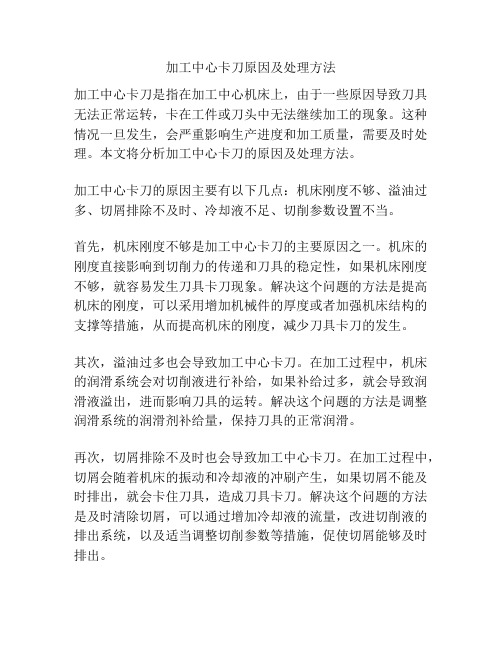
加工中心卡刀原因及处理方法加工中心卡刀是指在加工中心机床上,由于一些原因导致刀具无法正常运转,卡在工件或刀头中无法继续加工的现象。
这种情况一旦发生,会严重影响生产进度和加工质量,需要及时处理。
本文将分析加工中心卡刀的原因及处理方法。
加工中心卡刀的原因主要有以下几点:机床刚度不够、溢油过多、切屑排除不及时、冷却液不足、切削参数设置不当。
首先,机床刚度不够是加工中心卡刀的主要原因之一。
机床的刚度直接影响到切削力的传递和刀具的稳定性,如果机床刚度不够,就容易发生刀具卡刀现象。
解决这个问题的方法是提高机床的刚度,可以采用增加机械件的厚度或者加强机床结构的支撑等措施,从而提高机床的刚度,减少刀具卡刀的发生。
其次,溢油过多也会导致加工中心卡刀。
在加工过程中,机床的润滑系统会对切削液进行补给,如果补给过多,就会导致润滑液溢出,进而影响刀具的运转。
解决这个问题的方法是调整润滑系统的润滑剂补给量,保持刀具的正常润滑。
再次,切屑排除不及时也会导致加工中心卡刀。
在加工过程中,切屑会随着机床的振动和冷却液的冲刷产生,如果切屑不能及时排出,就会卡住刀具,造成刀具卡刀。
解决这个问题的方法是及时清除切屑,可以通过增加冷却液的流量,改进切削液的排出系统,以及适当调整切削参数等措施,促使切屑能够及时排出。
此外,冷却液不足也是加工中心卡刀的原因之一。
冷却液在加工过程中起到润滑和冷却的作用,如果冷却液不足,就会导致刀具过热,引发卡刀现象。
解决这个问题的方法是及时添加足够的冷却液,保持切削区域的正常冷却。
最后,切削参数设置不当也会导致加工中心卡刀。
切削参数包括切削速度、进给速度和切削深度等,如果切削参数设置不当,就会影响切削力的传递和刀具的运转,导致卡刀现象的发生。
解决这个问题的方法是根据材料的硬度和刀具的性能选择合适的切削参数,并进行适时的调整和优化。
综上所述,加工中心卡刀的原因有很多,但都可以通过合理的处理方法来解决。
处理时要根据具体情况进行针对性的措施,保证机床的刚度,调整溢油量,及时清除切屑,保持足够的冷却液供应,并合理设置切削参数等。
加工中心刀具补偿

刀具补偿
1、刀具长度补偿:G43刀具正补偿,G44刀具负补偿,G49刀具长度取消。
G43在Z轴第一次
走刀时用,即下到Z10安全平面的时候使用,如:G43 G00 Z10 H01。
当该把刀程序执行完全结束后用G49G00Z100取消长度补偿。
2、刀具半径补偿:G41刀具左补偿,外轮廓加工:顺时针走刀,顺铣时沿刀具进刀方向看,刀具与工件左侧铣削。
内轮廓加工:逆时针走刀,G41G01X-25F200D01。
G42刀具右补偿(一般不使用)。
3、G40刀具半径补偿取消。
1、加工尺寸不正确时,修改G41半径补偿的方法:
如:要求加工100×100mm的凸台,实测为102×102mm。
参数OFFET/SETTING→刀偏(补正)→形状D→-1→+输入。
如:要求加工100×100mm的凸台,实测为98×98mm。
参数OFFET/SETTING→刀偏(补正)→形状D→1→+输入。
分享加工中心维修几个案例

本文结合加工中心机械系统故障实例,对加工中心机械系统常见故障进行归纳和阐述,全面分析了故障产生的原因,系统介绍了检修的具体步骤,提出了相应的维修、保养措施。
一、主轴系统常见故障1.主轴发热,旋转精度下降某立式加工中心镗孔精度下降,圆柱度超差,主轴发热,噪声大,但用手拨动主轴转动阻力较小。
(1)故障分析。
主轴部件解体检查,发现故障原因如下:①主轴轴承润滑脂内混有粉尘和水分,这是因为该加工中心用的压缩空气无精滤和干燥装置,故气动吹屑时少量粉尘和水气窜入主轴轴承润滑脂内,造成润滑不良,导致发热且有噪声;主轴内锥孔定位表面有少许碰伤,锥孔与刀柄锥面配合不良,有微量偏心;②前轴承预紧力下降,轴承游隙变大;③主轴自动夹紧机构内部分碟形弹簧疲劳失效,刀具未被完全拉紧,有少许窜动。
(2)故障处理。
更换前轴承及润滑脂,调整轴承游隙,轴向游隙0.003mm,径向游隙士0.002mm;自制简易研具,手工研磨主轴内锥孔定位面,用涂色法检查,保证刀柄与主轴定心锥孔的接触面积大于85%;更换碟形弹簧。
将修好的主轴装回主轴箱,用千分表检查径向跳动,近端小于0.006mm,远端150mm处小于0.010mm。
试加工,主轴温升和噪声正常,加工精度满足加工工艺要求,故障排除。
(3)改进措施:①增加压缩空气精滤和干燥装置,过滤器要定期排水,定期清洗或更换滤芯;②随时检查主轴锥孔、刀柄的清洁和配合状况,检查空气干燥器工作是否正常;③合理安排加工工艺,避免材料切除率陡变;④严禁超负荷运行,有故障应及时报修,不得带病运行。
2.主轴部件的拉杆钢球损坏(1)故障现象。
某立式加工中心主轴内刀具自动夹紧机构的拉杆钢球和刀柄拉紧螺钉尾部锥面经常损坏。
(2)故障分析。
检查发现,主轴松刀动作与机械手拔刀动作不协调。
这是因为限位开关挡铁装在气液增压缸的气缸尾部,虽然气缸活塞动作到位,增压缸活塞动作却没有到位,致使机械手在刀柄还没有完全松开的情况下强行拔刀,损坏拉杆钢球及拉紧螺钉:(3)故障处理。
数控加工中心常见刀具系统故障诊断与排除方案

数控 7工中心 是 当代 高新技 术集 机 、电 、光 、气 、液 、汁算 J u 机 ,信息处理 等为—体 的结 晶,机械结构和 电路 电气复杂 .管路 交 叉林立 ,故障现 象也是 千奇百怪 ,各不相 同 。如何 能迅速 找出故 障 ,隐患特别是在我们实爿教学 中遇到的常见刀具 系现实 , 直接 最 的问题 本文所叙述的加工中心刀具 系统的 故障均 是以我院学生实 习用的 台湾友嘉精 ̄V 0 L M4立式 加工中心为例 ,其 配置的数控 系统 为F N C0 MA.其 自带一刀套编 码选刀方式的 自动刀库和机械 A U — i
信息解除 ,此时表示故障排除 ( 若机械手在6 。的位置且未 b) 0 松刀 ,转 ̄MD模式输入 M7 , J I I 3 待松 刀完成 后可 直接按 “f F ”键 , ) 此时机械手则以寸动的方式往l 。的位 置转动 ,等到确实在 10 ∞ 8。 的位置时 ,按键无效 , 下来转到MD 模式输入M7夹刀 ,待夹 刀 接 I 5 完成后继续按 “I F ”键 ,直到机械手转到0 l 。的 位置时 ,按键无效 且报警信息解除 ,此时表示故障排除。 ( ) c 若机械 手在10 8 。的位 置且未夹刀 ,此时按 “f F ”键无效 ,必须先执行M7后按健才 可继 ) 5 续以 寸动的 方式将机械 手转到0 o的位置 ,待机 械手到0 。的位 置 时 ,按键 无效 且报管信息解 除 .此时表示故障 排除 。 r ) 若机械 d 手在 10 8 。直接按 “ J R ”键 ,以寸 动的 方式将机 械手转 到0 。的位 置 。待 械 手到I 、 ) 。的位 置时 , 按键 无效且报警信 息解 除 ,此时 表 示故障指 除 。 f 、 若机械手 在6。 以前 r e o 不含6 。 ) o 的位置且 未 松刀 ,直轻按 “r F ”键 ,此时机械手则以寸动的方式往6。的位置 ) o 转动 ,等 ,确实在∞。的位置时 ,按键无效 ,输入M7松刀 ,完成 斟 3 后可继续投 “ ”键 ,直到机械手到达 10 Rl 8。的 位置时按键无效 , 继续输入M7夹 刀,待夹刀完成后继续按 “【 5 Fl ,直到机械手转 ”键 到【 l 位置时 ,按键无效 且报 警信息解除 ,此 时表示故障排 除 。的 ⑤ 当故障排除完成后 ,请检查主轴刀及预备刀是否正确 ,若有错误 清 自行更换刀具 。
加工中心卡刀原因及处理方法
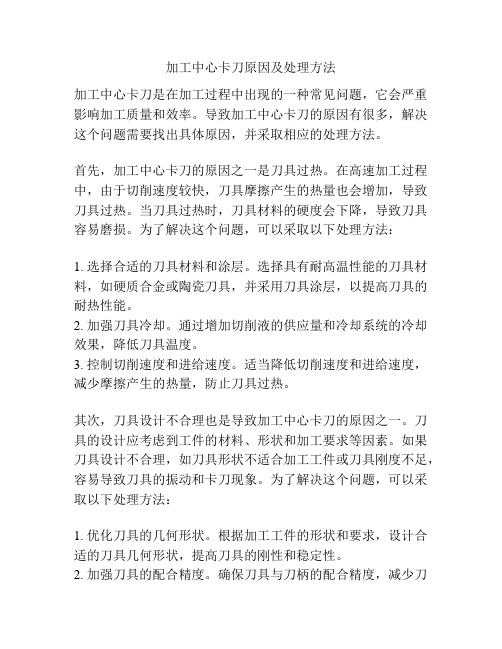
加工中心卡刀原因及处理方法加工中心卡刀是在加工过程中出现的一种常见问题,它会严重影响加工质量和效率。
导致加工中心卡刀的原因有很多,解决这个问题需要找出具体原因,并采取相应的处理方法。
首先,加工中心卡刀的原因之一是刀具过热。
在高速加工过程中,由于切削速度较快,刀具摩擦产生的热量也会增加,导致刀具过热。
当刀具过热时,刀具材料的硬度会下降,导致刀具容易磨损。
为了解决这个问题,可以采取以下处理方法:1. 选择合适的刀具材料和涂层。
选择具有耐高温性能的刀具材料,如硬质合金或陶瓷刀具,并采用刀具涂层,以提高刀具的耐热性能。
2. 加强刀具冷却。
通过增加切削液的供应量和冷却系统的冷却效果,降低刀具温度。
3. 控制切削速度和进给速度。
适当降低切削速度和进给速度,减少摩擦产生的热量,防止刀具过热。
其次,刀具设计不合理也是导致加工中心卡刀的原因之一。
刀具的设计应考虑到工件的材料、形状和加工要求等因素。
如果刀具设计不合理,如刀具形状不适合加工工件或刀具刚度不足,容易导致刀具的振动和卡刀现象。
为了解决这个问题,可以采取以下处理方法:1. 优化刀具的几何形状。
根据加工工件的形状和要求,设计合适的刀具几何形状,提高刀具的刚性和稳定性。
2. 加强刀具的配合精度。
确保刀具与刀柄的配合精度,减少刀具在切削过程中的振动和位移。
3. 选择适当的刀柄材料和结构。
选择具有良好刚性和稳定性的刀柄,提高刀具系统的整体刚性。
此外,加工中心卡刀还可能是由切削力过大引起的。
切削力过大会导致刀具的振动和刀具系统的松动,进而引起卡刀现象。
为了解决这个问题,可以采取以下处理方法:1. 优化加工参数。
合理选择切削速度、进给速度和切削深度等加工参数,避免切削力过大。
2. 采用合适的刀具路径。
设计合理的刀具路径,避免出现过大的切削力集中区域,减少刀具的振动。
3. 加强刀具系统的刚性。
采用更精确的装夹方式和加强刀具系统的刚性,减少刀具系统松动带来的卡刀问题。
综上所述,加工中心卡刀的原因有很多,例如刀具过热、刀具设计不合理和切削力过大等。
加工中心新刀具常用切削参数参照表

8-15
20-40
0.15-0.20 0.30-0.50
加工材料/ 工件
A105(相当 于25Mn) /MQL导环
加工特殊材料及工件切削参数参照表
刀具名称
切削刃数
转速 (r/min)
进给量 (mm/min)
用途
切削宽度 (mm)
刀具材料
φ5钻头 φ5.8钻头 φ10.3钻头 φ13.5钻头 φ14.5钻头 φ6铰刀 φ15铰刀
35#/45#
刀具名称
0圆鼻刀 φ40圆鼻刀 φ63圆鼻刀 φ63圆鼻刀 φ25圆鼻刀 φ32圆鼻刀 φ40圆鼻刀
用途
精加工 精加工 粗加工 精加工 粗加工 精加工 粗加工 精加工 粗加工 粗加工 粗加工
转速 (r/min)
3300 3300 1800 3000 1500 3000 1300 2500 2000 3300 1800
12
φ16高速钢立铣 3刃
400-600
50-70
16
16
高速钢
φ20高速钢立铣 3刃
300-400
40-50
20
20
φ25高速钢立铣 4刃
260-360
60-100
20
10
φ32高速钢立铣 4刃
200-260
60-100
20
10
φ36高速钢立铣 4刃
180-200
60-100
20
10
φ30立铣
4刃
刀具材料
20-40
0.15-0.20 0.30-0.50
铸钢
<10 10-20 20-40
0.08-0.12 0.15-0.25 0.12-0.15 0.20-0.35 0.15-0.20 0.30-0.50
加工中心、数控铣床、刀具名称、转速、进给、下刀量(45#)
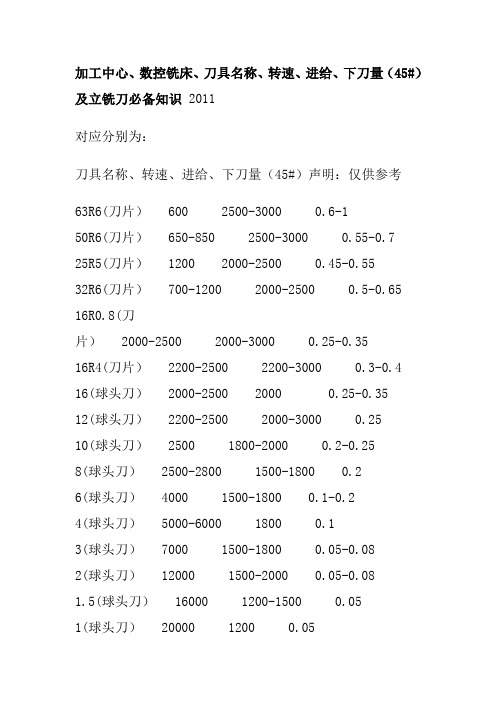
加工中心、数控铣床、刀具名称、转速、进给、下刀量(45#)及立铣刀必备知识2011对应分别为:刀具名称、转速、进给、下刀量(45#)声明:仅供参考63R6(刀片) 600 2500-3000 0.6-150R6(刀片) 650-850 2500-3000 0.55-0.725R5(刀片) 1200 2000-2500 0.45-0.5532R6(刀片) 700-1200 2000-2500 0.5-0.6516R0.8(刀片) 2000-2500 2000-3000 0.25-0.3516R4(刀片) 2200-2500 2200-3000 0.3-0.416(球头刀) 2000-2500 2000 0.25-0.3512(球头刀) 2200-2500 2000-3000 0.2510(球头刀) 2500 1800-2000 0.2-0.258(球头刀) 2500-2800 1500-1800 0.26(球头刀) 4000 1500-1800 0.1-0.24(球头刀) 5000-6000 1800 0.13(球头刀) 7000 1500-1800 0.05-0.082(球头刀) 12000 1500-2000 0.05-0.081.5(球头刀) 16000 1200-1500 0.051(球头刀) 20000 1200 0.050.5(球头刀) 20000 500 0.023.175(球头刀) 7000 1500 0.0830R5(平底立铣) 720-1000 2000-3000 0.3-0.540(平底立铣) 300-600 2000-2500 1.0-2.020(平底立铣) 600-1000 2000-2500 1.0-2.016(平底立铣) 1600 2000-2500 0.3-0.412(平底立铣) 2000-2200 2000-2500 0.25-0.3510(平底立铣) 2200-2500 2000-2500 0.25-0.38(平底立铣) 2500 1500-2000 0.2-0.36(平底立铣) 3000 1500-2000 0.15-0.24(平底立铣) 3500-4000 1500-2000 0.13(平底立铣) 6000 1500-1800 0.08-0.12(平底立铣) 9000 1500 0.05-0.081.5(平底立铣) 12000 1200-1500 0.05-0.081(平底立铣) 18000 1000-1500 0.03-0.05铣刀大体上分为:1.平头铣刀,进行粗铣,去除大量毛坯,小面积水平平面或者轮廓精铣;2.球头铣刀,进行曲面半精铣和精铣;小刀可以精铣陡峭面/直壁的小倒角。
加工中心刀臂掉刀的原因

加工中心刀臂掉刀的原因
1. 刀具装夹不牢,这就好比你手里拿个东西没握紧,能不掉吗?比如说在加工的时候,刀具没卡紧,那刀臂在换刀时不就容易掉刀啦!
2. 刀臂本身有故障呀,这就像人身体不舒服会影响工作一样!比如刀臂的某个零件松动了,它还怎么正常工作,不掉刀才怪呢!
3. 换刀程序出错了,这跟人走错路不是一个道理嘛!就像设定的程序有问题,刀臂能准确执行才怪呢,不掉刀都难呀!
4. 气压不稳定也会导致掉刀啊,这就好像你呼吸不顺畅还能好好干活吗?比如气压时高时低,刀臂能稳定工作吗,肯定容易掉刀呀!
5. 刀具太重了,刀臂承受不住呀,这不就跟让小孩背大人一样嘛!像那种特别重的刀具,刀臂怎么可能一直撑得住,不掉刀才怪呢!
6. 刀臂的润滑不够,这就好比机器没油了还怎么运转呀!比如长时间没保养,润滑不好,刀臂能不掉刀吗?
7. 加工中心的控制系统出问题了,这跟人的大脑混乱了一样啊!要是控制系统不正常,刀臂怎么能不掉刀呢!
8. 操作人员操作不当,这就像不会开车的人乱开车一样!比如错误地操作机器,刀臂不掉刀才怪呢!
9. 刀臂的设计有缺陷,这就跟盖房子设计不好会出问题一样呀!要是刀臂本身设计就有问题,那不掉刀能说得过去吗?
10. 周边环境太恶劣了,这就好像人在很差的环境里会不舒服一样!比如灰尘太多等,刀臂能正常工作才怪,不掉刀也难呀!
我觉得加工中心刀臂掉刀的原因有很多,得仔细排查,找到问题所在才能解决呀!。
数控加工中心编程的特点

8.7.1 加工中心的主要功能及加工对象 1.数控加工中心的主要功能 加工中心是一种集铣床、钻床和镗床3种机床功能于一体,由计算机控 制的高效、高度自动化的机床,其特点是数控系统能控制机床自动更换 刀具,零件经一次装夹后能连续地对各加工表面自动进行铣、镗、钻、 扩、铰、攻螺纹等多种工序的加工。 2.数控加工中心的主要加工对象 加工中心适用于加工形状复杂、工序多、精度要求较高、需用多种类 型的普通机床和众多刀具、夹具,且经多次装夹和调整才能完成加工的 零件,下面介绍适合加工中心加工零件的种类。 (1) 箱体类零件。箱体类零件一般是指具有孔系和平面,内有一定型腔 ,在长、宽、高方向尺寸比例相差不大的零件,如汽车的发动机缸体、 变速器箱体、机床主轴箱、齿轮泵壳体等。箱体类零件一般都需要进行 多工位孔系及平面加工,精度要求较高,特别是形状精度和位置精度要 求严格,通常要经过铣、钻、扩、镗、铰、锪、攻螺纹等工序加工,
8.7 数 控 加 工 中心 编程的 特点
对于刀具长度补偿(G43、G44、G49)的详细介绍见第8章。 例8-20 图8-39(a)为零件图,图8-39(b)为加工毛坯,编制加工程序。 工艺过程为,先用中心钻、钻头、锪刀进行孔加工,再对中间凸台盘 部分进行粗、精加工,精加工余量为0.5mm,其中4段R39mm圆弧可 用镜像编程,4个缺口可用子程序加工。需要进行数值计算的是4段 R39mm圆弧的圆心,因图形对称,故仅计算处于第一象限的圆弧的圆 心即可。 程序编制步骤: (1) 数值计算: 工件坐标系原点设在零件上表面对称中心处,由图8-39(a)可知,R39 圆弧的圆心距工件坐标系原点为80,位于X轴、Y轴夹角的平分线上。 设圆心坐标为(XR,YR),则 XR=YR=80cos45°=56.569 (2) 加工工序: ① 用中心钻按零件图8-39 (a)所示的5个孔中心位置钻5个定位孔,深 1mm。 ② 用Φ14mm的钻头在5个定位孔的基础上钻5个通孔。