《切断与切槽》数控车床编程格式与编程方法(DOC)
数控车床编程与操作(广数系统)教学课件ppt作者崔兆华主编_第六章切槽与切断
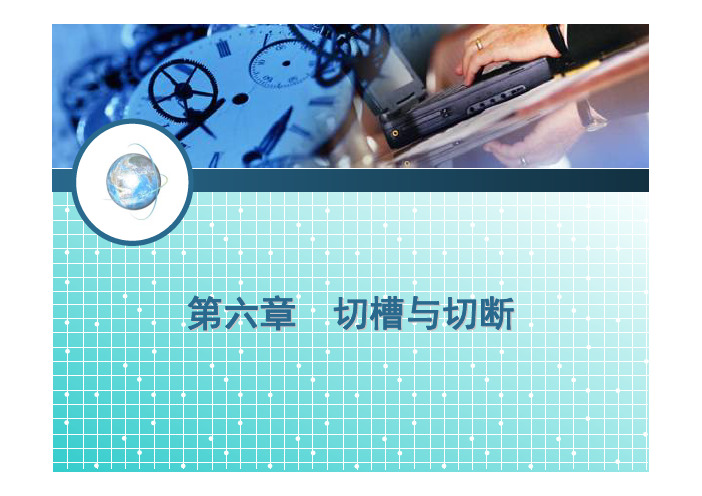
第六章切槽与切断
多次切入。
宽槽的加工
第一节单槽加工
第二节多槽加工
第三节异型槽的加工第四节切断
第一节单槽加工
2. 简单凹槽的加工
简单凹槽加工示意图
精密凹槽加工示例
G75 指令运动轨迹
根据G75 指令切削循环的特点, G75 指令常用于深槽、宽槽、等距多槽的加工, 但不用于高精度槽
1. 零件加工中, 槽的定位是非常重要的, 编程时要引起重视。
2. 切槽刀通常有三个刀位点, 编程时可根据基准
材料为45 钢。
槽加工实训零件图
mm
第六章 切槽与切断
第二节多槽加工
利用G75 指令循环加工后, 刀具回循环的起点位置。
切槽刀要区分是左刀尖还是右刀尖对刀, 防止编程出错。
切断与切槽数控车床编程花式与编程方法

25m/min;
(3)用硬质合金切槽刀车钢料时:进给量 f=0.1——0.2mm/r;切削速度 v=80——
120m/min;
(4)用硬质合金切槽刀车铸铁时:进给量 f=0.15——0.25mm/r;切削速度 v=60—
100m/min;
二、编程指令与格式 1、外经/内径切槽复合循环(G75)
该指令可用于回转体类零件的内/外沟槽或切断的循环加工。 编程格式: G75 R(e);
第 9 讲 切断与切槽
·学习目的和要求
1、掌握在数控车床上切断工件与切沟槽的基本方法 2、掌握切断刀的安装、调整以及对刀操作 3、掌握切槽切断指令的编程格式与编程方法 4、掌握内切槽、外切槽、典型槽的加工方法 5、掌握切断与沟槽加工的加工工艺
·重点内容
1、数控车床上切断工件与切沟槽的基本方法 2、切断刀的安装、调整以及对刀操作 3、切槽切断循环指令的编程格式 4、内切槽、外切槽、典型槽的加工方法 5、掌握切断与沟槽加工的加工工艺
一、切槽/切断方法 1、槽的类型
在工件表面上车沟槽的方法叫切槽,槽的形状有外槽、内槽和端面槽。 2、切槽的方法 (1)加工外槽时用外切槽刀,且沿着工件中心方向切削;加工内槽时用内切槽刀,且沿着 工件大径方向切削;加工端面槽时可用外切槽刀、内切槽刀或自磨刀具。 (2)车削精度不高的和宽度较窄的矩形沟槽:可以用刀宽(主切削刃宽度)等于槽宽的切 槽刀,直接采用 G01 直进法横向走刀一次将槽切出。 (3)车削精度要求较高的和宽度较宽的沟槽:主切削刃宽度小于槽宽,分几次直进法横向 走刀,并在槽的两侧、槽底留一定的精车余量。切出槽宽后,然后根据槽深、槽宽,最后 一刀纵向走刀精车至槽底尺寸。当切削到槽底时一般应暂停一段时间以光顺槽底。 (4)加工宽槽和多槽时:可用移位法、调用子程序、宏程序或 G75 切槽复合循环指令编程。
切槽与切断G75

切槽复合循环指令切削轨迹图
G75循环指令切削轨迹图
编制加工程序
程序 O0001; N10 M03 S500 G99 T0202; 程序号 选用2号外切槽刀(4mm),左刀 尖对刀,2号刀具补偿,启动主轴 快速定位, 槽侧面留余量0.2mm , 切削液开 回退量 说明
槽 加 工 程 序
N20 G00 X70.0 Z-29.2 M08; N30 G75 R1.0;
课题
切槽与切断
一、复习
以下分别是几种槽的加工方式。
简单槽加工: 简单槽加工:
直接切入,一次成形 直接切入 一次成形
深槽加工: 深槽加工:
分次切入,多次成形 分次切入 多次成形
宽槽加工: 宽槽加工:
排刀粗切,沿槽精切 排刀粗切 沿槽精切
任务分析
1
该零件上有哪些加 工特征? 工特征?
2
加工该槽时需要 什么指令? 什么指令?
3
离合器 加工出现误差时 如何处理? 如何处理?
切槽复合循环指令
1.格式 .
G75 Re; G75 X(U)__ Z(W)__ P△i Q△k R△d Ff; △ △ △
ቤተ መጻሕፍቲ ባይዱ
2.说明 .
e:回退量,该值为模态值,可由参数5319号指定, 由程序指令修改。 X:最大切深点的X轴绝对坐标。 U:最大切深点的X轴增量坐标。 Z:最大切深点的Z轴绝对坐标。 W:最大切深点的Z轴增量坐标。 △i:X方向的进给量(不带符号)。 △k:Z方向的位移量(不带符号)。 △d:刀具在切削底部的退刀量,△d的符号总是正的。 f :进给量。
练习
切纸辊
1 2 3
简述常见深槽的进刀方式、切深的 分配方式是什么?
简述指令G75的加工工艺路线。
数控车床编程切槽加工

指令代码
指令代码是数控车床编程的基础, 包括准备功能指令(G指令)、 辅助功能指令(M指令)等。
坐标系设定与原点选择
01
02
03
坐标系设定
数控车床采用右手直角坐 标系,分别设定X、Y、Z 三个坐标轴。
原点选择
原点选择是建立工件坐标 系的关键步骤,通常选择 工件的某一固定点为原点, 建立工件坐标系。
需的槽深度和宽度。
圆弧槽编程方法
选择合适的切削刀具
与直线槽类似,根据圆弧槽的半径和深度选择合适的切削刀具。
编写圆弧插补程序
使用G02或G03指令编写圆弧插补程序,指定圆弧的起点、终点 和中心点坐标,以及切削速度和进给量等参数。
添加切削循环
同样使用切削循环指令实现多次切削,直到达到所需的圆弧槽深 度和宽度。
补偿原理
刀具补偿原理主要包括长度补偿和半径补偿两种。长度补偿通过测量刀具长度并输入数控 系统,实现刀具长度的自动调整;半径补偿则根据刀具半径和工件轮廓计算出刀具中心轨 迹,实现工件的精确加工。
02
切槽加工原理及工艺参数
切槽加工原理简介
切槽加工定义
切槽加工是数控车床上的一种常见加 工方式,通过切削工具在工件表面切 除一定深度和宽度的材料,形成所需 的槽形结构。
04
常见问题及解决方案
切削振动问题分析及处理措施
切削振动原因分析
切削振动可能由刀具刚性不足、 切削参数不合理、工件装夹不稳 等因素引起。
处理措施
提高刀具刚性,优化切削参数, 确பைடு நூலகம்工件装夹稳定,采用减振装 置等措施。
刀具磨损过快原因及优化策略
刀具磨损过快原因
刀具材料选择不当、切削用量过大、冷却不充分等。
数控车工教案车槽与车断加工程序的编制

课题车槽与车断加工程序的编制总课时 2 主备人课型新授备课时间研讨时间投放时间教学目标 初步掌握槽加工编程的方法。
能掌握车断时的注意事项。
懂得机床的保养和切削加工时的安全知识。
教学重难点切断的编程参数的设置教学准备切断刀教学设计教学内容师生活动复备栏一:相关的工艺知识在加工机械零件过程中,经常需要车断零件;在车削螺纹时为了退刀方便,并使零件装配有一个正确的轴向位置须加工退刀槽;在加工变径轴的过程中也常用排刀切削等加工零件,这些都需要进行车槽或车断,所以说车槽或车断是机械加工过程中不可缺少的一个环节。
1 车槽(车断)刀车槽(车断)刀是以横向进给为主,前端的切削刃为主切削刃,有两个刀尖,两侧为副切削刃,刀头窄而长,强度差;主切削刃太宽会引起振动,切断时浪费材料,太窄又消弱了刀头的强度。
主切削刃可以用以下经验公式计算α≈(0.5~0.6)d式中α————为主切削刃的宽度(mm) d————为待加工零件的表面直径(mm)刀头的长度可用如下经验公式计算:L=h+(2~3)式中 L————为刀头长度(mm)H————为切入深度(mm)2. 车槽工序安排教师运用图示法分析、讲解,并对学生进行提问,了解学生掌握程度。
车槽一般安排在粗车和半精车之后,精车之前。
若零件的刚性好或精度要求不高时也可以在精车后再车槽。
二、槽加工编程的方法:一、单槽车削实例如图所示图7-2-1 槽类零件(一)刀具选择1、选用有断屑槽的90°正偏刀。
2、选择刀宽为4mm的车槽刀。
3、选择45°端面刀。
(二)工艺分析1、外圆粗精采用同一把车刀置于T01刀位。
车槽刀对刀时以左刀尖进行对刀,置于T02刀位。
2、用三爪自定心卡盘夹持毛坯左端伸出108左右,找正夹紧。
用45°端面刀手动车端面。
3、用T01偏刀粗精加工外圆。
4、调T02切槽刀加工槽。
(三)参考程序:O1234 ;%1234 ;G95 M43 ;M03 S500 ;T0101 ;G00 X55 Z2 ; 讲解编程实例,并板书运用CAXA软件进行G71 U1.5 R1 P10 Q20 X0.5 Z0.1 F0.2 ; (粗、精加工外圆)M03 S800 ;G00 X50 Z2 ;N10 G01 Z-100 F0.1 ;N20 X56 ;G00 X100 Z100 ;M03 S500 ;T0202 ; (调2号切槽刀)G00 X51 Z-80 ;G01 X47 F0.05 ; (切槽)G04 X2 ; (暂停2秒)G00 X100 ;Z100 ;T0200 ;T0100 ; (取消刀补,转回基准刀)M30 ; (程序结束)二、车断实例及注意事项实例:工件切断如图所示编程,模拟运行,让学生有更直观的了解。
(精品)任务二数控车床切槽循环指令编程及工件切断编程

4. 编程举例(9)
零件加工时选择三把刀 具: ●T0101:外圆端面粗加 工刀具,刀尖角55°; ●T0202:外圆端面精加 工刀具,刀尖角35°, 刀尖半径R0.8; ●T0303:切槽刀,刀宽 4㎜,切槽深度25㎜, 对刀时注意刀位点的选 择。
4. 编程举O例20(26(10已)调试)
T0101;(外圆表面粗加工) G98 M03 S300; G00 X41.0 Z2.0; G71 U2.0 R0.5; G71 P10 Q20 U0.5 W0.1 F80.0; N10 G00 G42 X19.975; G01 X25.975 Z-1.0 F40.0;
Z-20.0; X37.985; N20 Z-75.0; T0202 S500;(外圆表面精加工) G70 P10 Q20; G40 G00 X100.0 Z50.0; M05;
T0303;(切槽加工)
4. 编程举例MG00(03XS148001.00)Z-36.1;
G75 R0.5; G75 X26.5 Z-54.9 P2000 Q3800 F0.1; G00 Z-36.0; G01 X25.95 F40.0;
5.编程举例(3)
G03 X10.0 Z-13.0 R2.0; G01 Z-2.0; X6.0 Z0.0;
N20 X0.0; S800; G70 P10 Q20; G40 G00 X100.0 Z50.0; M05; M30;
3.编程举例
6 2 10 2 6 2 10 40
50
20 30
O0002; T0101; M03 S500; G00 X42.0 Z-29.0; G75 R0.3; G75 X32.0 Z-45.0 P1500 Q2000 F0.1 G00 X100.0 Z100.0; M30;
模块二项目10数控车床切槽钻孔循环指令编程及工件切断编程共55页文档
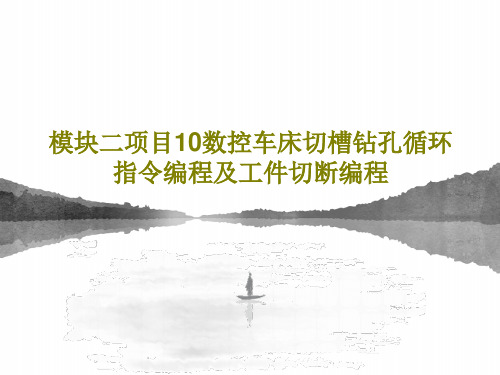
1、战鼓一响,法律无声。——英国 2、任何法律的根本;不,不成文法本 身就是 讲道理 ……法 律,也 ----即 明示道 理。— —爱·科 克
3、法律是最保险的头盔。——爱·科 克 4、一个国家如果纲纪不正,其国风一 定颓败 。—— 塞内加 5、法律不能使人人平等,但是在法律 面前人 人是平 等的。 ——波 洛克
6、最大的骄傲于最大的自卑都表示心灵的最软弱无力。——斯宾诺莎 7、自知之明是最难得的知识。——西班牙 8、勇气通往天堂,怯懦通往地狱。——塞内加 9、有时候读书是一种巧妙地避开思考的方法。——赫尔普斯 10、阅读一切好书如同和过去最杰出的人谈话。——笛卡儿
Thaபைடு நூலகம்k you
《切断与切槽》数控车床编程格式与编程方法(DOC)

《切断与切槽》数控车床编程格式与编程方法(DOC)第9讲切断与切槽学习目标和要求1、掌握在数控车床上切断工件与切沟槽的基本方法2、掌握切断刀的安装、调整以及对刀操作3、掌握切槽切断指令的编程格式与编程方法4、掌握内切槽、外切槽、典型槽的加工方法5、掌握切断与沟槽加工的加工工艺关键内容1、数控车床上切断工件与切沟槽的基本方法2、切断刀的安装、调整以及对刀操作3、切槽切断循环指令的编程格式4.内切槽、外切槽、典型槽的加工方法5。
掌握切割和坡口加工的加工技术难点内容1.工件切割和坡口的加工路线2。
切槽加工方法实训任务1.要求每组学生完成一个实践培训项目。
2.要求每位学生独立完成实习报告。
教学准备课时分配:4小时先讲解知识内容,再进行加工操作练习。
教学过程1、强调上课纪律,考勤记录。
2.解释本课的主题并简要总结内容。
3.讲解安全操作规程4。
备课5、教学分配(分组,工具配发)6、知识内容讲解7、本节课点评总结一、开槽/切割方法1。
沟槽类型在工件表面上车沟槽的方法叫切槽,槽的形状有外槽、内槽和端面槽。
2、切槽的方法(1)加工外槽时,使用外槽刀具沿工件中心方向切割;加工内槽时,使用内槽刀具沿工件大直径方向切割;加工端面坡口时,可使用外切槽刀、内切槽刀或自磨刀具。
(2)车削精度不高的和宽度较窄的矩形沟槽:可以用刀宽(主切削刃宽度)等于槽宽的切槽刀,直接采用g01直进法横向走刀一次将槽切出。
(3)对于车削精度高、宽度大的坡口:主切削刃宽度小于坡口宽度时,刀具应水平进行多次直线前进,坡口两侧和底部应留有一定的精加工余量。
切完槽宽后,根据槽深和槽宽,将最后一把刀纵向切至槽底尺寸。
切割至槽底时,一般暂停一段时间,使槽底光滑。
(4)加工宽槽和多槽时:可用移位法、调用子程序、宏程序或g75切槽复合循环指令编程。
(5)车削较小的圆弧形槽,一般用成形车刀车削,或改变主偏角与副偏角的角度。
(6)梯形槽和倒角槽的车削一般通过成形车刀、梯形刀具直行法或左右切削法完成。
槽类零件加工数控车床编程

钻中心孔时容易出现的问题以及产生原因
四、一夹一顶时顶尖使用的工艺要求
后顶尖有固定顶尖和回转顶尖两种。
1. 固定顶尖
特点:刚度好,定心准确;顶尖与工件中心孔的滑动摩擦, 容易产生过多热量,而将中心孔或顶尖“烧坏” 。
用途:只适用于低速加工、精度要求较高的工件。
普通固定顶尖
镶硬质合金固定顶尖
2. 回转顶尖
子程序——一组程序段在一个程序中多次出现,或者在几个程 序中都要使用它,这个典型的加工程序可以做成固定程序,并 单独命名。
特点:不独立的加工程序,只能通过调用,实现加工中的局 部动作; 子程序执行结束后,能自动返回到调用的程序中。
二、子程序的嵌套
子程序的嵌套——子程序调用另一个子程序的功能。 一级子程序:被主程序调用的子程序。 在FANUC 0i系统中,子程序可以嵌套4级。
地址P后面的四位数字为子程序序号,地址L后的数字表示重 复调用的次数,子程序号及调用次数前的0可省略不写。如果 只调用一次,则地址L及其后的数字可省略。
3. 编程实例
加工该零件中的两个直槽,用G00、G01、G04、M98、 M99等指令编写精加工程序。
零件图
(下一页续表)
续表
一、一夹一顶装夹
一、G75指令功能
G75指令可使程序执行到出现该指令的程序段时暂停。如车槽 加工时,为使槽底圆整光滑,可采用该指令。
轴向(Z轴)进刀循环复合径向断续切削循环,……;切削到
切削终点后,返回起点(G75起点和终点相同),径向车槽复 合循环完成。
G75的轴向进刀和径向进刀方向由切削终点X(U)Z(W)与 起点的相对位置决定。此指令用于加工径向环形槽或圆柱面, 径向断续切削起到断屑、及时排屑的作用。
(职业教育)《数控编程与加工》课件=任务七 切槽和切断

9
用径向切槽多重循环指令G75完成项目任务
一、G75指令格式
G75 R(e); G75X(U)Z(W)P(Δi)Q(Δk)R(Δd)F
目FA录NU页C Oi 任务七
;
P(Δi) :径向(X 轴)进刀时,X 轴断续进刀的进刀量,取值 范围 0<Δi≤ 9999999(单位:0.001mm,直径值)。
12
用径向切槽多重循环指令G75完成项目任务
二、G75指令运动轨迹
目FA录NU页C Oi 任务七
⑥ 轴向(Z 轴)快速移动进刀,进刀方向与④退刀方向相反。 如果 Z 轴进刀(△d+△k)后,进刀终点仍在 A 点与 Af 点(最后一 次径向切削循环起点)之间,Z 轴快速移动进刀(△d+△k),即: Dn→An+1,然后执行①(开始下一次径向切削循环);如果 Z 轴 进 刀(△d+△k)后,进刀终点到达 Af 点或不在 Dn 与 Af 点之间,Z 轴快速移动至 Af 点,然后执行①,开始最后一次径向切削循环;
17
项目任务零件的切断
三、刀具磨损补偿的应用举例
据、状态,延时给定的时间后,再执行下一个程序段。
格式:G04P
;或G04X
;或G04U
;
其中:G04延时时间由代码字P__、X__或U__指定;P值
取范围为1~9999999 ,单位为毫秒(ms)。X、U代码
范围为0~99999.999,单位为秒(s)。
二、用G01指令完成项目任务参考程序
5
目录
用G01指令完成 项目任务
8
用径向切槽多重循环指令G75完成项目任务
一、G75指令格式
G75 R(e); G75X(U)Z(W)P(Δi)Q(Δk)R(Δd)F
数控 车床 编程 切槽加工[新版]
![数控 车床 编程 切槽加工[新版]](https://img.taocdn.com/s3/m/74d59f3ff8c75fbfc67db29e.png)
• 切槽切削用量选择:
• 切削速度: • • 通常取外圆切削速度的60%—70%;
• 进给量: • • 一般取0.05---0.3mm/r;
3、编写图3-44零件的加工程序 4、切槽质量分析 5、任务评价 6、综合练习
加工如图3-51所示工件。
• 小结:
一、径向切槽循环G75 指令格式 G75 R(e)
• 1)切槽刀具:
•
包括外圆、内孔、端面切槽刀具
• 2)切槽刀几何参数 (如图3-50):
• 3)切槽加工方法 • ◆一般要求切槽刀刀尖与工件轴线 • 等高,而且刀头与工件轴线垂直. • ◆精度要求较高的沟槽,一般采用 • 二次进给车成.
• ◆车较宽的沟槽,可以采用多次直进法切割, • 并在槽壁及底面留精加工余量,最后一刀 • 精车至尺寸较小的梯形槽一般用成形刀车 • 削完成. 较大的梯形槽,通常先车直槽,然 • 后用梯形刀直进法或左右切削法完成.
• ◆ Δk为刀具完成一次径向切削后,在Z方向的偏移量,用不带符号的值表;
• ◆ Δd为刀具在切削底部的Z向退刀量,无要求时可省略;
• 2)指令说明 G75循环轨迹如(图3-45)所示。
• 注意:
• 程序段中的Δi、Δk值,在FANUC系 • 统中,不能输入小数点,而直接输入最小 • 编程单位.
• 如:P1500表示径向每次切深量为1.5mm
• 三、相关理论
• 1、径向切槽循环G75
(应用场合:G75指令用于内、外径切槽)
• 1)指令格式
• G75 R(e)
• G75 )
• ◆ e 为退刀量,其值为模态值;
• ◆ X() Z()为切模终点处的坐标;
• ◆ Δi为X方向的每次切深量,用不带符号的半径量表示;
模块二项目10__数控车床切槽(钻孔)循环指令编程及工件切断编程PPT文档56页

•
46、寓形宇内复几时,曷不委心任去 留。
•
ቤተ መጻሕፍቲ ባይዱ
47、采菊东篱下,悠然见南山。
•
48、啸傲东轩下,聊复得此生。
•
49、勤学如春起之苗,不见其增,日 有所长 。
•
50、环堵萧然,不蔽风日;短褐穿结 ,箪瓢 屡空, 晏如也 。
6、最大的骄傲于最大的自卑都表示心灵的最软弱无力。——斯宾诺莎 7、自知之明是最难得的知识。——西班牙 8、勇气通往天堂,怯懦通往地狱。——塞内加 9、有时候读书是一种巧妙地避开思考的方法。——赫尔普斯 10、阅读一切好书如同和过去最杰出的人谈话。——笛卡儿
Thank you
- 1、下载文档前请自行甄别文档内容的完整性,平台不提供额外的编辑、内容补充、找答案等附加服务。
- 2、"仅部分预览"的文档,不可在线预览部分如存在完整性等问题,可反馈申请退款(可完整预览的文档不适用该条件!)。
- 3、如文档侵犯您的权益,请联系客服反馈,我们会尽快为您处理(人工客服工作时间:9:00-18:30)。
第9讲切断与切槽·学习目的和要求1、掌握在数控车床上切断工件与切沟槽的基本方法2、掌握切断刀的安装、调整以及对刀操作3、掌握切槽切断指令的编程格式与编程方法4、掌握内切槽、外切槽、典型槽的加工方法5、掌握切断与沟槽加工的加工工艺·重点内容1、数控车床上切断工件与切沟槽的基本方法2、切断刀的安装、调整以及对刀操作3、切槽切断循环指令的编程格式4、内切槽、外切槽、典型槽的加工方法5、掌握切断与沟槽加工的加工工艺·难点内容1、工件切断与沟槽的加工工艺路线2、切断与沟槽的加工方法·实训任务1、要求每组学生必须完成一个实训项目。
2、要求每个学生必须独立完成实习报告。
·教学准备·课时分配:4H·教学方法先讲解知识内容,再进行加工操作练习。
·教学过程1、强调上课纪律,考勤记录。
2、讲解本节课主题,内容简要概括。
3、讲解安全操作规程4、上课准备5、教学分配(分组,工具配发)6、知识内容讲解7、本节课点评总结一、切槽/切断方法1、槽的类型在工件表面上车沟槽的方法叫切槽,槽的形状有外槽、内槽和端面槽。
2、切槽的方法(1)加工外槽时用外切槽刀,且沿着工件中心方向切削;加工内槽时用内切槽刀,且沿着工件大径方向切削;加工端面槽时可用外切槽刀、内切槽刀或自磨刀具。
(2)车削精度不高的和宽度较窄的矩形沟槽:可以用刀宽(主切削刃宽度)等于槽宽的切槽刀,直接采用G01直进法横向走刀一次将槽切出。
(3)车削精度要求较高的和宽度较宽的沟槽:主切削刃宽度小于槽宽,分几次直进法横向走刀,并在槽的两侧、槽底留一定的精车余量。
切出槽宽后,然后根据槽深、槽宽,最后一刀纵向走刀精车至槽底尺寸。
当切削到槽底时一般应暂停一段时间以光顺槽底。
(4)加工宽槽和多槽时:可用移位法、调用子程序、宏程序或G75切槽复合循环指令编程。
(5)车削较小的圆弧形槽,一般用成形车刀车削,或改变主偏角与副偏角的角度。
(6)车削梯形槽和倒角槽,一般用成形车刀、梯形刀直进法或左右切削法完成。
或者先加工出与槽底等宽的直槽,再沿着相应梯形角度或倒角角度,移动车刀车削出梯形槽和倒角槽。
(a)车外槽(b)车内槽(c)车端面槽图2-57 常用切槽的方法3、切断切断要用切断刀,切断刀的形状与切槽刀相似。
常用的切断方法有直进法和左右借刀法两种。
直进法常用于切断铸铁等脆性材料;左右借刀法常用于切断钢等塑性材料。
4、切削用量的选择:(1)用高速钢切槽刀车钢料时:进给量f=0.05——0.1mm/r;切削速度v=30——40m/min;(2)用高速钢切槽刀车铸铁时:进给量f=0.1——0.2mm/r;切削速度v=15——25m/min;(3)用硬质合金切槽刀车钢料时:进给量f=0.1——0.2mm/r;切削速度v=80——120m/min;(4)用硬质合金切槽刀车铸铁时:进给量f=0.15——0.25mm/r;切削速度v=60—100m/min;二、编程指令与格式1、外经/内径切槽复合循环(G75)该指令可用于回转体类零件的内/外沟槽或切断的循环加工。
编程格式: G75 R(e);G75 X(U) __ Z(W) __ P(△i) Q(△k) R(△d) F(f);注解: e——退刀量(半径指定,单位mm)X——槽深;(绝对值方式下,槽的终点B的X坐标值,单位mm)U——增量值方式下,循环起点A到槽的终点B在X坐标的增量值Z——绝对值方式下,槽的终点D(B)的Z坐标值W——增量值方式下,循环起点A到槽的终点C在Z坐标的增量值△i——X轴方向间断切削长度(每次循环切削量,不带小数点,无正负,半径值,单位um ) △k ——Z 轴方向间断切削长度(每次循环切削量,不带小数点,无正负,增量值,单位um ) △d ——为切削至终点的退刀量(半径值),△d 的符号为正,但如果Z(W)和Q(△k)省略,可用正、负符号指定退刀方向。
退刀方向与Z 向进给方向相反,通常情况下,因加工槽时,刀两侧无间隙,无退让距离,所以一般△d 取零或省略。
工进切削快速退刀图2-58 外经/内径切槽复合循环走刀路线说明:(1)执行G75循环加工指令时,应指定循环起点的位置。
即该指令程序段前的X 、Z 坐标就是加工起始位置,也是G74循环加工结束后刀具返回的终点位置。
(2)X 向和Z 向间断切削时,如最后余量小于指定长度值,就按余量值进行间断切削加工。
2、外径切槽切断循环(G75)该指令是上述格式的简化,适合于在外圆面上切削沟槽或切断加工。
编程格式:G75 R(e);G75 X(U) __ P(△i) F(f);项目一 车沟槽练习 一、实训内容:如下图2-59所示,要求采用G75切槽加工指令车沟槽,以及切断加工。
图2-59二、实训准备:设备:FANUC 0i-TC(1台)毛坯:Ф30×70塑胶棒(1件)刀具:900外圆车刀、切断刀(4mm)量具:游标卡尺(1把)工具:卡盘扳手,刀架扳手三、实训步骤:(一)工艺分析1、图纸分析该零件外形规则,主要为一沟槽的切削加工和切断加工2、工艺处理该零件为一回转体轴类零件,加工内容主要为切槽切断加工,选择在数控车床上加工比较合理。
选择毛坯尺寸为Ф30×70,用一道工序即可加工完成,采用三爪自定心卡盘装夹。
该零件外形规则,轮廓简单,工件表面对加工精度没有严格的要求,只需要选用一把900外圆车刀,一把切断刀即可完成切削加工。
切削加工时先加工外圆及端面,再加工沟槽,最后进行切断加工。
选择工件右端面与轴线的交点处作为编程原点。
●工序一:加工沟槽(1)加工方法:选择在数控车床上加工(2)工艺安排与走刀路线的确定:①车外圆及端面,选择900外圆车刀。
②车沟槽,选择4mm切断刀。
③自动切断,选择4mm切断刀。
(3)夹具选择:三爪自定心卡盘(4)装夹方案确定与定位基准的选择:夹住工件左端10~20mm,三爪夹紧。
(5)刀具及切削参数选择(二)编程1、建立编程坐标系,确定编程原点。
以工件右端面与主轴轴线位置作为编程原点。
2、数学计算(1)计算各节点坐标值。
(略)(2)确定走刀方向,计算相对位移量。
(略)3、编写数控程序。
(参考程序如附件)(三)机床调试与加工操作1、开机,返回机床参考点。
2、输入零件程序将零件的数控加工程序输入到数控机床系统。
3、程序校验在自动运行方式下,选择“机床锁住”、“空运行”键,按“循环启动”运行零件加工程序。
通过图形模拟功能进行程序校验,检查轮廓程序及输入是否正确,观测刀具相对于工件的运动轨迹是否正确。
若程序中有格式、语法错误,则应修改程序,之后才能进行程序校验。
4、刀具、工件的装夹与校准清理机床台面卫生,安装夹具,校验并修正夹具,再装夹工件。
然后安装所需要的刀具。
5、对刀及参数设置以工件右端面与主轴轴线位置作为工件原点。
将此时的机床坐标值抄数到相应的刀补中。
6、首件试切与切削加工首件试切用于检查对刀操作及参数输入是否正确,检验零件轮廓、尺寸精度、形位公差、表面粗糙度等技术要求是否符合图纸要求,否则需要重新调试机床、设置参数或编制修改程序。
在加工操作过程中,要始终观察加工过程,严禁负责操作的学生离开操作区域或干其它工作,若出现撞击等其它异常情况,应立即按下“急停”按钮。
操作期间,严禁非本次操作的其它学生按动机床操作面板上的按键。
7、零件测量检验正确使用量具,检验零件轮廓、尺寸精度、形位公差、表面粗糙度等技术要求是否符合图纸要求,检查零件外观是否合格。
(四)操作完毕1、机床维护与卫生清洁清扫实习场地,整理好刀具、工具、量具等,保养机床。
2、关机3、填写实习报告4、实验总结与点评四、注意事项:1、学生的实训必须在实训老师的指导下,严格按照数控机床安全操作规程有步骤地进行。
2、合理地确定编程坐标系,使数学计算简单方便及对刀操作。
数学计算时要细心,并检查节点坐标是否计算正确。
编程时,要严格按照机床指令代码与编程格式进行,输入程序后要反复检查,以确保程序输入正确。
3、工件、刀具装夹要牢固可靠。
4、机床在试运行前必须进行图形模拟加工,避免程序错误、刀具干涉等事项。
5、快速进刀和退刀时,一定要注意不能碰到工件和夹具。
6、加工零件过程中一定要提高警惕,将手放在“急停”按钮上,如遇到紧急情况,迅速按下此按钮,防止意外事故发生。
7、要按照操作步骤逐一进行相关训练,实习中对未涉及的问题及不明白之处要询问指导教师,切忌盲目加工。
8、操作中出现工件跳动、异常声音等情况时,必须立即停车处理。
五、评分标准:参考程序:O2034N1 T0101; //换1号外圆车刀G97 G99 M03 S600;G00 X100. Z100. M08;G00 X-1. Z2.;G01 Z0. F0.25G01 X30.; //车端面Z-45.; //车外圆G00 X32.;X32. Z2.;G00 X100. Z100.; //退刀M09;M05;M01;N2 T0202 G00 X100. Z100.; //换2号外切槽刀,槽刀宽4mmM03 S400;G00 X40. Z2. M08;X32. Z-14.; //定位到切槽循环起点位置G75 R1.; //切槽退刀量单边为1mmG75 X16.4 Z-30. P2000 Q3000 R0 F0.08;//X轴双边预留0.4mm的精车余量,X轴间断切削长度为单边2mm,Z轴间断切削长度为3mm。
G00 X32. Z-14;G01 X16. F0.1; //精车槽底G04 X0.5; //槽底暂停0.5sZ-30.;G04 X0.5; //槽底暂停0.5sG00 X32.;Z-44.; //定位到切断位置处G01 X0. F0.08; //切断G00 X40.;G00 X100. Z100.;M09;M01;M30;项目二车沟槽练习一、实训内容:如下图2-60所示,要求采用G75切槽加工指令车沟槽,以及切断加工。
图2-60二、实训准备:设备:FANUC 0i-TC(1台)毛坯:Ф30×75塑胶棒(1件)刀具:900外圆车刀、切断刀(3mm)量具:游标卡尺(1把)工具:卡盘扳手,刀架扳手三、实训步骤:(一)工艺分析1、图纸分析该零件外形规则,主要为一沟槽的切削加工和切断加工2、工艺处理该零件为一回转体轴类零件,加工内容主要为切槽切断加工,选择在数控车床上加工比较合理。
选择毛坯尺寸为Ф30×75,用一道工序即可加工完成,采用三爪自定心卡盘装夹。
该零件外形规则,轮廓简单,工件表面对加工精度没有严格的要求,只需要选用一把900外圆车刀,一把切断刀即可完成切削加工。
切削加工时先加工外圆及端面,再加工沟槽,最后进行切断加工。