图像识别技术在棒材计数中的应用
手持PDA:钢筋计数(棒材计数)-工业级OCR识别技术
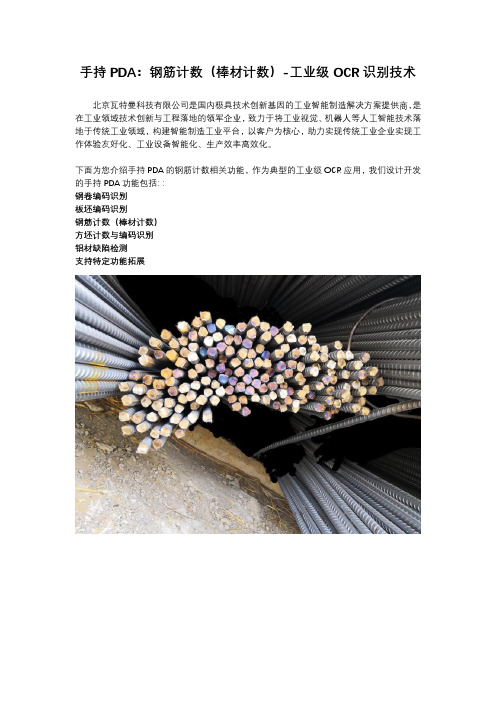
手持PDA:钢筋计数(棒材计数)-工业级OCR识别技术
北京瓦特曼科技有限公司是国内极具技术创新基因的工业智能制造解决方案提供商,是在工业领域技术创新与工程落地的领军企业,致力于将工业视觉、机器人等人工智能技术落地于传统工业领域,构建智能制造工业平台,以客户为核心,助力实现传统工业企业实现工作体验友好化、工业设备智能化、生产效率高效化。
下面为您介绍手持PDA的钢筋计数相关功能,作为典型的工业级OCR应用,我们设计开发的手持PDA功能包括::
钢卷编码识别
板坯编码识别
钢筋计数(棒材计数)
方坯计数与编码识别
铝材缺陷检测
支持特定功能拓展
高性能识别算法:
通过现场采集真实数据,训练神经网络模型。
支持捆扎摆放不均匀、截面长短不一致情况计数需求。
产品功能:
实时检测与计数:实时检测,结果展示直观,极低使用成本
排班管理:对接集成MES排班;支持排班调度管理,便于现场作业
报警机制:检测异常,声光,图形化报警,及时发现问题
多维报表:从多个维度汇聚系统检测结果,便于管理决策
产品优势:
- 定制化核心算法:针对客户场景,优化模型,性能更优。
- 简单易用:产品操作简单,工人学习成本低。
- 系统稳定:工业级软、硬件标准,7*24稳定工作
- 手持式:轻巧便携、灵活方便、可视化操作
- 计数准确率高:准确率高达99.9%
- 计数时间快:棒材(钢筋等)截面拍摄后秒级结果输出
- 应用场景:仓库、车间等
- 支持不同直径、不同大小棒材(钢筋)的计数需求。
- 适应反光、腐蚀、锈化等多种复杂钢筋截面变化影响。
图像识别技术在冶金行业中的应用研究
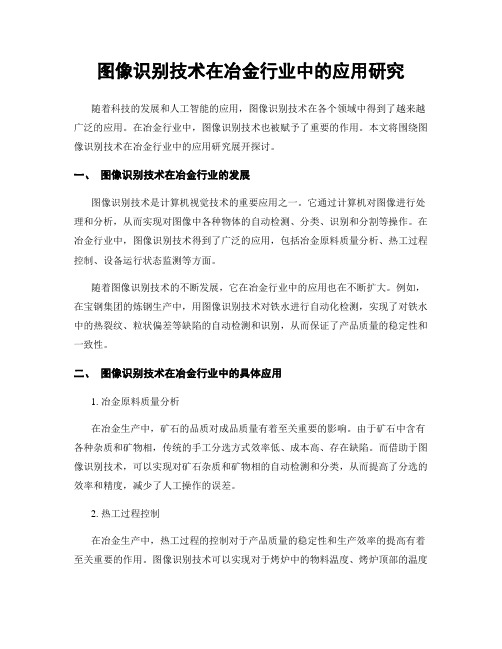
图像识别技术在冶金行业中的应用研究随着科技的发展和人工智能的应用,图像识别技术在各个领域中得到了越来越广泛的应用。
在冶金行业中,图像识别技术也被赋予了重要的作用。
本文将围绕图像识别技术在冶金行业中的应用研究展开探讨。
一、图像识别技术在冶金行业的发展图像识别技术是计算机视觉技术的重要应用之一。
它通过计算机对图像进行处理和分析,从而实现对图像中各种物体的自动检测、分类、识别和分割等操作。
在冶金行业中,图像识别技术得到了广泛的应用,包括冶金原料质量分析、热工过程控制、设备运行状态监测等方面。
随着图像识别技术的不断发展,它在冶金行业中的应用也在不断扩大。
例如,在宝钢集团的炼钢生产中,用图像识别技术对铁水进行自动化检测,实现了对铁水中的热裂纹、粒状偏差等缺陷的自动检测和识别,从而保证了产品质量的稳定性和一致性。
二、图像识别技术在冶金行业中的具体应用1. 冶金原料质量分析在冶金生产中,矿石的品质对成品质量有着至关重要的影响。
由于矿石中含有各种杂质和矿物相,传统的手工分选方式效率低、成本高、存在缺陷。
而借助于图像识别技术,可以实现对矿石杂质和矿物相的自动检测和分类,从而提高了分选的效率和精度,减少了人工操作的误差。
2. 热工过程控制在冶金生产中,热工过程的控制对于产品质量的稳定性和生产效率的提高有着至关重要的作用。
图像识别技术可以实现对于烤炉中的物料温度、烤炉顶部的温度分布、加热炉温度等参数的自动检测和监测,从而提高了生产过程中的控制精度和效率。
3. 设备运行状态监测在冶金生产中,设备的运行状态对于生产效率和安全运行有着至关重要的作用。
利用图像识别技术,可以实现对于各种设备的运行状态监测和故障诊断,例如对于钢材表面的缺陷、轧制机辊的损伤和烧孔等问题进行自动检测和报警。
三、图像识别技术在冶金行业中存在的问题虽然图像识别技术在冶金行业中的应用前景广阔,但是在实际应用过程中也存在不少问题。
其中比较明显的问题包括:1. 数据质量问题:由于冶金设备和生产环境的复杂性,图像获取中可能会受到光照不佳、噪声、遮挡、模糊等因素影响,从而影响了图像识别算法的精度和效果。
基于数字图像处理的棒线材计数方法

基于数字图像处理的棒线材计数方法
韩庆大;辛颖
【期刊名称】《中国图象图形学报》
【年(卷),期】2007(012)007
【摘要】棒线材自动计数是一个一直没有得到很好解决的问题,为解决此问题,提出了一种基于距离变换技术的图像识别方案.该方法先利用CCD摄像机采集棒线材的端面图像;然后采用中值滤波法、二值化分割、腐蚀及膨胀运算实现棒线材图像的预处理;最后根据距离变换的思想,采用距离变换图中搜索种子点的方法实现棒线材的计数.通过对现场采集到的图像进行的试验结果表明,该方法不仅不受棒线材种类及端面形态影响,而且对端头不齐、捆扎散乱的棒线材也有较好识别效果,具有一定的推广和应用价值.
【总页数】4页(P1276-1279)
【作者】韩庆大;辛颖
【作者单位】东北大学设备诊断工程中心,沈阳,110004;东北林业大学,哈尔
滨,150040
【正文语种】中文
【中图分类】TP391.41
【相关文献】
1.基于数字图像处理课程内容的创新实践项目实施——以"基于数字图像处理的作物颗粒计数"为例 [J], 马慧敏; 黄金日; 焦俊; 乔焰; 沈春山
2.一种基于多尺度融合卷积神经网络的人群计数方法 [J], 蒋俊;龙波;高明亮;邹国锋
3.基于多尺度增强网络的人群计数方法 [J], 徐涛;段仪浓;杜佳浩;刘才华
4.基于跨列特征融合的人群计数方法 [J], 李佳倩;严华
5.基于图像识别的干涉条纹计数方法研究 [J], 曲阳;曹显莹;孙纪勃
因版权原因,仅展示原文概要,查看原文内容请购买。
扎捆棒材的图像识别计数算法

扎捆棒材的图像识别计数算法侯维岩;侯兆阳【摘要】为了快速获得扎捆棒材的数量,在大量观测和实验的基础上,提出一种动态获取棒材形态学直径的方法;根据扎捆棒材的形态学分布,提出“米”字形搜索算法( RSS算法)和一种覆盖原则。
先对棒材截面图像进行灰度化处理,然后根据灰度图片的灰度直方图两峰一谷的特点得到图片的全局阈值,将灰度棒材图片二值化;再对二值图片进行膨胀、腐蚀操作削弱粘连;最后基于二值图片,利用RSS算法进行计数。
现场采集扎捆棒材的计数实验验证了该算法的有效性、可靠性和准确性。
在加入人工矫正环节后,棒材计数准确度达到100%。
试验结果表明,在计数对象满足两个分布特征的情况下,该算法都可以实现高准确度的计数。
%In order to quickly obtain the number of the lash bar,the method of dynamically obtaining the morphology diameter of the lash bar is put forward on the basis of a large number of observations and experiments. According to the morphological distribution of the lash bar,the rice shape searching(RSS) algorithm and coverage principle is proposed.Firstly,gradation processing is conducted for section image of rod,then, according to the global threshold of the image is obtained in accordance with the two peaks one valley characteristics of the gray histogram of the gray scale image to get the binarization image,and then the adhesions is weakened by operations of expansion and corrosion,finally based on binarized image the RSS algorithm is used for counting. The experimentson site prove the validity,reliability and accuracy of this algorithm. The accuracy of bar counting is up to 100% when manual correction is added.The result of test shows that the conclusion is highly accurate counting can be implemented if the objects satisfy the two distribution features mentioned.【期刊名称】《自动化仪表》【年(卷),期】2016(037)005【总页数】5页(P27-31)【关键词】扎捆棒材;形态学;“米”字形搜索( RSS);智能分割;人工矫正;图像处理;图像识别【作者】侯维岩;侯兆阳【作者单位】郑州大学信息工程学院,河南郑州450001;郑州大学信息工程学院,河南郑州 450001【正文语种】中文【中图分类】TH74;TP29;TP313在扎捆棒材的流通过程中,传统称重方法人力消耗大,且不容易操作,人工计数往往效率低下。
实时高速棒材图像的识别与跟踪
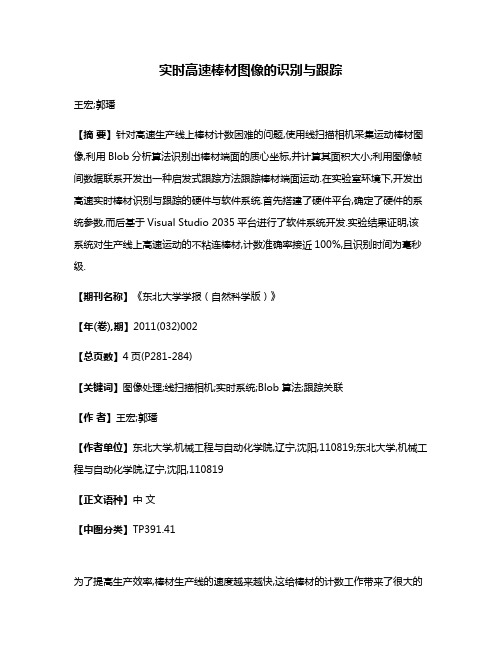
实时高速棒材图像的识别与跟踪王宏;郭璠【摘要】针对高速生产线上棒材计数困难的问题,使用线扫描相机采集运动棒材图像,利用Blob分析算法识别出棒材端面的质心坐标,并计算其面积大小;利用图像帧间数据联系开发出一种启发式跟踪方法跟踪棒材端面运动.在实验室环境下,开发出高速实时棒材识别与跟踪的硬件与软件系统.首先搭建了硬件平台,确定了硬件的系统参数,而后基于Visual Studio 2035平台进行了软件系统开发.实验结果证明,该系统对生产线上高速运动的不粘连棒材,计数准确率接近100%,且识别时间为毫秒级.【期刊名称】《东北大学学报(自然科学版)》【年(卷),期】2011(032)002【总页数】4页(P281-284)【关键词】图像处理;线扫描相机;实时系统;Blob算法;跟踪关联【作者】王宏;郭璠【作者单位】东北大学,机械工程与自动化学院,辽宁,沈阳,110819;东北大学,机械工程与自动化学院,辽宁,沈阳,110819【正文语种】中文【中图分类】TP391.41为了提高生产效率,棒材生产线的速度越来越快,这给棒材的计数工作带来了很大的困难,传统的人工计数已不能适用·近几年国内外不少科技工作者使用图像采集、图像处理的方法解决棒材自动计数问题·例如,利用距离变换进行棒材端面识别[1],主要采用Chamfering倒角法,图像经两次扫描实现距离变换,而后得出各区域的中心,完成棒材识别计数;通过预测棒材运动位置与速度来进行跟踪[2-3],主要利用Kalman 滤波器对棒材位置进行无偏最优预测·但上述方法有以下不足:现阶段的研究主要使用面阵相机采集图像,如果棒材运动速度过快,图像会模糊不清,如果利用距离变换等方法需要首先进行图像复原;而Kalman滤波虽然适合计算机编程,但同时跟踪多个目标时计算量仍然很大,耗时较长,造成系统实时性不佳或难以满足实时处理要求·本文提出一种新的思路:利用高速线扫描相机搭建机器视觉检测系统·首先给出硬件系统的相关参数,指出该硬件系统的固有特性;接着利用Blob(团块)识别算法识别出棒材端面Blob,获得Blob相关参数,并开发出一种启发式跟踪方法,实现了对生产线上高速运动的棒材进行实时图像采集、统计棒材数并在图像上标记棒材序号的功能·实验证明,统计准确率接近100%,且系统实时性也较好·1 系统架构1.1 硬件组成本系统是在实验室条件下的模拟系统,硬件组成如图1所示,主要由线扫描相机、编码器、光源、传送带和计算机[4-5]组成·各部分说明如下·图1 硬件系统组成Fig.1 Configuration of hardware system1)相机:线扫描相机采用线形传感器成像,必须利用运动速度才能取得面积影像,因此对连续运动物体的成像敏感,可进行高分辨率成像,而对静止物体无法清晰成像[6]·使用线扫描相机采集高速运动棒材图像,不仅对棒材目标成像清晰,而且大幅减少了背景干扰,降低了图像预处理及棒材识别与跟踪的难度·本文使用加拿大Dalsa公司Spyder3线扫描相机SG-10-02K80,线分辨率2 048,最高扫描线频率36 kHz·该相机使用网口传输数据,无需图像采集卡;配合千兆网卡可实现1Gbit/s的传输速度,传输距离可达50m,适合远距离系统搭建·2)编码器:相对式编码器,安装于驱动传送带的电机轴上·相对式编码器在轴旋转时产生A,B两个相位差为90°的方波信号·本文只使用A信号作为相机的线扫描触发信号,使相机的线触发频率与传送带速度同步·3)光源:条形白色光源,对棒材采用前向反射照明,光源从上方偏向下方照射,相机从下方偏向上方采集图像,以增大棒材端面与背景的灰度差·为排除背景干扰,使用遮光板遮挡背景·4)传送带:传送带为链传动,装有直流调速电机,用于模拟真实生产线上的棒材运动环境·5)计算机:对图像进行预处理,Blob分析,目标跟踪及结果显示·1.2 系统主要参数相机的像素尺寸PS=14 μ m;镜头焦距F=24 mm;相机工作距离 d=1 m;电机转速为 n;传送带速度为v;链轮直径D=0.05 m;编码器输出脉冲数P=2 000·1)相机单像素可视范围FOV(field of view):FOV为1个像素代表的真实物体的长度值·2)不失真线频率 f:其中K为频率转换系数·以频率 f触发相机,必须保证获取长宽比适中、不失真的图像·要保证采集图像不失真,则需满足综合式(2)与式(3),得频率转换系数由式(4)可知,系数K为系统的固有参数·将系统各参数代入,得此系统K=7.43·3)测速范围:设每帧图像需扫描480线(即图像分辨率为2 048×480),则每秒图像帧数满足系统传送带速度满足一般采集帧数范围为15至20帧,可算出本系统速度范围为v∈[4.19,5.59],若想改变系统测速范围,可改变 P,d或F·1.3 系统工作流程系统的工作流程如图2所示·图2 系统的工作流程Fig.2 Working process of the system传送带电机驱动旋转编码器工作;编码器信号触发相机电子快门采集图像,图像存放于相机缓存区;预先设定图像转移周期 t(ms),每隔t对相机缓存区进行锁存,读取缓存中的图像进入计算机内存,进行图像处理与分析,输出结果;对相机缓存区解除锁定,等待下一个转移周期 t的到来,重复上述过程·每秒帧数 NFr为 t的倒数·2 棒材图像的预处理图3为采集到的棒材图像·原始图像由于存在背景以及噪声的干扰,不能直接识别,需要进行预处理·图3 采集的标准棒材图像Fig.3 Standard bar images acquired by camera首先对采集到的棒材图像进行二值化处理[7],消除可能存在的背景影响·假设图像区域为f(x,y),选取合适的阈值 T,进行图像的二值化,得到二值图像(x,y)·由图3可知,由于光源照射使棒材端面与背景差异较明显,经实验,本文将 T设为整个图像的灰度平均值·图像二值化后存在一些噪声,利用中值滤波[8]即可消除噪声·本文运用3×3的掩模进行二值中值滤波·3 Blob分析Blob算法是在一幅图像内把出现灰度突变的连通区域标记出来,并确定其大小、面积及准确位置等几何参数的算法·本文利用Blob算法快速准确提取出了棒材图像的端面区域,并计算了每个Blob的长、宽、面积和质心坐标·预处理完成后,可能的目标区域已经成为一个个独立的连通域·本文通过八邻域Blob 分析,提取出每一帧图像中棒材的端面Blob,剔除其他Blob干扰,并且计算出各目标区域的质心,标记出其在当前帧上的序号·3.1 Blob识别预处理后的二值图像R(x,y)(简称R)可完全分割为s个子区域Ri(x,y),这 s个区域由m个Blob和一个背景组成[7]·在识别时,背景用零值像素表示,Blob则用非零值像素表示·3.2 剔除伪Blob目标用矩[8]来描述Blob区域的形状特性,对某一Blob图像 I(x,y),其(m,n)阶矩为式中(x,y)为Blob区域内点或边界点,对于二值图像,I(x,y)取值仅为1(Blob内)或0(Blob外)·特殊地,图像零阶矩式(8)即为Blob区域的面积,以像素个数为单位·设棒材端面大小在[a,b]内(本文取[7 000,12 000]),统计各Blob的 M0,0,剔除伪Blob区域·3.3 单帧Blob标记Blob区域的质心(¯x,¯y)可由式(9)求得:将每个Blob区域按从左到右,从上到下,依次赋予质心标记及序号标记值·图4为Blob图像分析结果,序号标记值为当前帧Blob的序号;表1为各Blob参数值·图4 棒材Blob分析结果Fig.4 Results of Blob analysis for bar specimens表1 各棒材Blob参数值(像素)Table 1 Blob parameters of bar specimens(in pixel)序号面积质心横坐标质心纵坐标0 11030 547.2 759.8 1 8 340 250.5 764.6 2 7 653 845.6 765.8实际对棒材图像进行Blob分析时,无需分析整个图像,而是设定感兴趣的区域,从而大幅减小Blob算法运算量·进行Blob处理时,处理时间在10 ms内,考虑锁存、解锁、数据转移的时间,亦能满足20帧/s的处理速度要求·4 利用启发式方法进行跟踪关联棒材图像进行Blob标记后,需要将各帧图像上同一Blob区域关联起来,完成棒材端面的跟踪·启发式跟踪方法不需要特定的跟踪目标函数,给定启发条件与起始点后,进行简单的逻辑判定即可完成跟踪·贪婪最近邻滤波器方法[9]对新的数据按一定顺序进行处理,并与先前的数据中最近的目标进行关联,从而在每次扫描后,选取单一的数据关联·本文改进了此方法,对高速采集的棒材图像数据进行关联,收到了良好的效果·由于相邻两帧的图像时间间隔Δt较小,可以认为相邻两帧中同一棒材走过的距离小于同一帧中棒材间隔Δx·位置变化可用一维坐标表示,以减少计算量·具体算法如下:①初始化NumBlob=0,作为棒材总数计数值;②利用已获得的Blob标记,找到 N,N+1帧中标记值blob-Index=0的Blob,获得其质心横坐标,分别赋予ycold与ycnew;③判断ycold-ycnew的差值符号:如果为正,则当前帧各棒材标号改为NumBlob-blob-Index;如果为负,则NumBlob+1,当前各帧棒材标号改为NumBlob-blob-Index;④N+1替换N,N+2替换N+1,重复②至③;⑤用户停止计数,输出棒材总数NumBlob·如图5所示,Blob左上角为当前帧的顺序标记值,右上角为实际顺序标记值·由算法求得的跟踪结果为实际顺序标记值·第 N帧出现5根棒材,按运动方向从右至左依次给予标记值1至5;第N+1帧没有新棒材目标进入处理区,故标记值不变;第 N+2帧中出现了新棒材目标,给予其标记值6·由图可知该算法结果与实际相符·图5 启发式跟踪方法示意图Fig.5 Schematic of heuristic tracking method5 实验结果本文基于Visual Studio 2005开发平台开发系统界面,使用Dalsa Sapera Processing 6.0开发包,对Dalsa驱动相机程序进行二次开发,植入图像采集模块、Blob处理及其参数设置模块、启发式跟踪功能模块·为实现长时间不间断识别跟踪,利用传送带上的链齿代替生产线上的运动棒材,对模拟生产线上的“棒材”进行识别跟踪测试·图6为启发式Blob跟踪某一时刻的结果,表2为识别时间·表2 处理时间Table 2 Processing time帧序号 10 20 100 200处理时间/ms 7.43 7.86 7.31 7.80图6 启发式Blob跟踪结果Fig.6 Result of heuristic tracking method6 结论该系统能成功识别“棒材”端面位置以及进行准确的跟踪,对高速生产线上的不粘连棒材识别率可达100%,并且较以往识别系统的实时性要好·参考文献:[1] 韩庆大,辛颖·基于数字图像处理的棒线材计数方法[J]·中国图象图形学报,2007,12(7):1276-1279·(Han Qing-da,Xin Ying.Counting method for wire bars and rods based on digital image processing[J].Journal of Image and Graphics,2007,12(7):1276-1279.)[2] Costntini G,Casali D,Perfetti R.Analogic CNN algorithm for estimating position and size ofmoving objects[J].International Journal of Circuit Theory and Applications,2004,32(5):509-522.[3] Kosaka A,Nakazawa G.Vision-based position tracking of rigid objects using prediction of uncertainties[C]∥IEEE International Conference on Robotics and Automation.New York:IEEE,1995:2637-2644.[4] Athana P,Abbott A.Real-time image processing on a custom computing platform[J].IEEE Transactions on Computers,1995,28(2):16-24.[5] 沙毅,曹英禹,王经武,等·基于图像处理计数的工件长度在线测量[J]·东北大学学报:自然科学版,2005,26(10):957-959·(Sha Yi,CaoYing-yu,WangJing-wu,et al.Online measurement of workpiece length based on image processing techniques[J].Journal of Northeastern University:Natural Science,2005,26(10):957-959.)[6] Cash G L,Hatamian M.Optical character recognition by the method of moments[J].Computer Vision,Graphics,and Image Processing,1987,39:291-310.[7] William K P.Digital image processing[M].[S.l.]:Wiley-Interscience,2001:551-560.[8] Sonka M,Hlavac V,Boyle R.Image processing,analysis,and machine vision[M].New York:Thomson,2007:159-161.[9] Rangarajan K,Shah M.Establishing motioncorrespondence[J].CVGEP:Image Understanding,1991,54(1):56-73.。
一种基于图像处理的棒材计数测量系统的设计与实现

的棒材计数测量系统。给出了系统 的硬件平 台结构 , 对电源 电路 , 摄像头 , 人机交互 , 复位 电路 , U S B接 口, U A R T接 口做了简单
描述 , 其 中的图像采集接 口数据传输过程使用了 D M A方式 且以 R G B 8 8 8格式存储数据。之后 分别介绍 了计数测量算 法的 4个
w a r e h o u s e b a r c o u n t i n g , t h i s p a p e r d e s i g n s a n d i mp l e me n t s a b a r c o u n t me a s u r e me n t s y s t e m b a s e d o n i mp r o v e d i ma g e
中 图分 类号 : T P 2 9 T P 3 1 9 文献标识码 : A 国家 标 准 学 科 分 类 代 码 : 5 1 0 . 4 0 5 0
De s i g n a n d i mp l e me nt a t i o n o f b a r c o u nt me a s ur e me nt s y s t e m ba s e d o n i ma g e pr o c e s s i n t a ng
一Leabharlann 种基 于图像处理的棒材计数测量 系统 的设计与实现
侯 维岩 ,张利 伟 ,党 蟒 , 段 政伟 ,宋
( 1 . 郑州大学信息工程学院 郑州
杨 ,王海 宽
上海 2 0 0 0 7 2 )
4 5 0 0 0 1 ; 2 . 上海大学机电工程 与 自动化学院
摘
要: 针对钢铁物流企业在棒材统计入库工作中遇到的实际问题 , 设计并 实现 了一种基 于改进 的多模板 匹配图像处理 算法
基于数字图像处理的棒线材计数方法

2 棒线材图像的预处理
由于受棒线材图像在采集、 传输及接收过程中 的多种因素影响, 棒线材图像中必然包含多种噪声, 所以在从图像中提取各种特征之前 , 有必要除去噪
图 2 图像二值化 F ig . 2 T he i m age o f b inary transfor m
为了解决 中值滤波处理对图像细节产生的影 响 , 可采用加权的方法把窗口内各像素加权, 某一像 素加权值 m, 即窗口像素灰度排队时 , 该像素重复 m 个。如 1 维 1 3 窗口可使中间像素的权 m = 3 ,两 边像素的权各为 m = 2 , 加权中值变为 m edian { x i - 1, x i - 1, x i, x i, x i, x i + 1, x i + 1 }, 再按灰度值排序 , 这样就 可以有效保护图像的细节 ( 如图 1 所示 )。 图像和背景不能完全准确地用黑白两色表示。为了 去除干扰 , 可采用腐蚀运算和膨胀运算实现。利用 多次腐蚀运算 , 可将棒线材内部部分空洞和干扰背 景去除, 而再采用相应次数的膨胀运算 , 即可将去除 空洞的棒线材恢复到原始大小, 这就为下一步的识 别做好准备, 图像多次腐蚀结果和多次膨胀结果分 别如图 3 、 图 4 所示。
( 东北林业大学 , 哈尔滨
150040)
摘
要
棒线材自动计 数是一个一直没有得到很好解决 的问题 , 为解 决此问 题 , 提 出了一 种基于距 离变换 技术的
图像识别方案。该方法先利用 CCD 摄像机采集棒线材的端面 图像 ; 然后采用中值滤波法、 二值化分割、 腐蚀及膨胀 运算实现棒线材图像的 预处理 ; 最后根据距离变换的思 想 , 采 用距离 变换图 中搜索 种子点 的方法实 现棒线 材的计 数。通过对现场采集到的图像进 行的试验结果表明 , 该 方法不 仅不受棒 线材种 类及端 面形态 影响 , 而且对 端头不 齐、 捆扎散乱的棒线材也有较好识别效果 , 具有一定的推广和应用价值。 关键词 预处理 距离 变换 种子点 倒角法 文章编号 : 1006 8961( 2007) 07 1276 04 中图法分类号 : TP391. 41 文献标识码 : A
图像识别技术在棒材计数中的应用
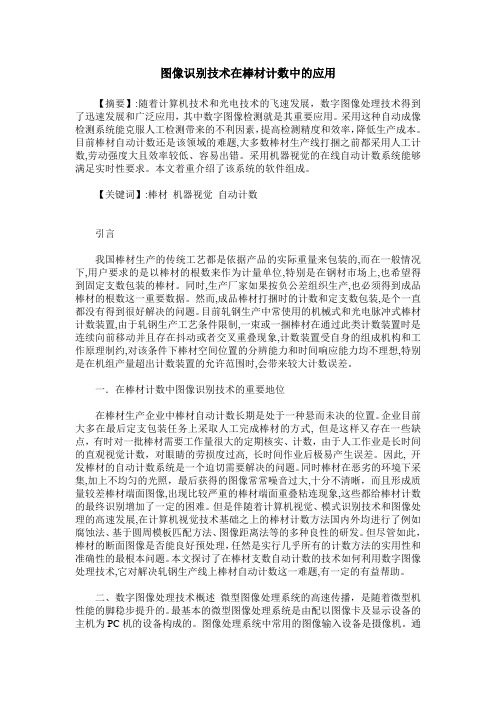
图像识别技术在棒材计数中的应用【摘要】:随着计算机技术和光电技术的飞速发展,数字图像处理技术得到了迅速发展和广泛应用,其中数字图像检测就是其重要应用。
采用这种自动成像检测系统能克服人工检测带来的不利因素,提高检测精度和效率,降低生产成本。
目前棒材自动计数还是该领域的难题,大多数棒材生产线打捆之前都采用人工计数,劳动强度大且效率较低、容易出错。
采用机器视觉的在线自动计数系统能够满足实时性要求。
本文着重介绍了该系统的软件组成。
【关键词】:棒材机器视觉自动计数引言我国棒材生产的传统工艺都是依据产品的实际重量来包装的,而在一般情况下,用户要求的是以棒材的根数来作为计量单位,特别是在钢材市场上,也希望得到固定支数包装的棒材。
同时,生产厂家如果按负公差组织生产,也必须得到成品棒材的根数这一重要数据。
然而,成品棒材打捆时的计数和定支数包装,是个一直都没有得到很好解决的问题。
目前轧钢生产中常使用的机械式和光电脉冲式棒材计数装置,由于轧钢生产工艺条件限制,一束或一捆棒材在通过此类计数装置时是连续向前移动并且存在抖动或者交叉重叠现象,计数装置受自身的组成机构和工作原理制约,对该条件下棒材空间位置的分辨能力和时间响应能力均不理想,特别是在机组产量超出计数装置的允许范围时,会带来较大计数误差。
一.在棒材计数中图像识别技术的重要地位在棒材生产企业中棒材自动计数长期是处于一种悬而未决的位置。
企业目前大多在最后定支包装任务上采取人工完成棒材的方式, 但是这样又存在一些缺点,有时对一批棒材需要工作量很大的定期核实、计数,由于人工作业是长时间的直观视觉计数,对眼睛的劳损度过高, 长时间作业后极易产生误差。
因此, 开发棒材的自动计数系统是一个迫切需要解决的问题。
同时棒材在恶劣的环境下采集,加上不均匀的光照,最后获得的图像常常噪音过大,十分不清晰,而且形成质量较差棒材端面图像,出现比较严重的棒材端面重叠粘连现象,这些都给棒材计数的最终识别增加了一定的困难。
探讨图像识别技术在机械零件质量检测中的运用

探讨图像识别技术在机械零件质量检测中的运用图像识别技术在机械零件质量检测中的运用已经成为一种非常有效的方法。
随着工业自动化的发展,传统的人工检测已经难以满足大批量和高效率的要求,而图像识别技术正好可以填补这个空白。
图像识别技术可以快速准确地识别出机械零件的质量问题。
传统的质量检测方法需要人工检查每个零件,费时费力,并且存在主观判断的问题。
而图像识别技术可以通过大规模数据的训练,准确识别出零件上的瑕疵、裂纹、变形等问题,快速确定是否合格。
图像识别技术具有高度的鲁棒性和稳定性。
相比于人工检测,图像识别技术不受外界环境的影响,可以在不同光照、角度、背景等条件下准确判断零件的质量,并且能够自动调整参数以适应不同的场景,大大提高了检测的准确率和稳定性。
图像识别技术还可以进行大规模数据的分析和统计。
通过对检测结果进行记录和分析,可以得出零件质量的趋势和变化规律,提前预警可能出现的质量问题,及时采取相应措施,从而保证产品的质量和可靠性。
图像识别技术在机械零件质量检测中也存在一些挑战和限制。
首先是数据的准备和标注工作。
图像识别技术需要大量的标注数据来进行训练,而这些数据的准确性和标注方式将直接影响识别的准确率和稳定性。
其次是对不同类型的零件进行分类和识别的问题。
由于不同类型的零件在形状、尺寸、材料等方面存在差异,需要针对不同的零件进行优化和调整。
在复杂的生产环境中,可能存在遮挡、光照不均匀等问题,影响识别的准确性。
图像识别技术在机械零件质量检测中有着广泛的应用前景。
通过准确识别零件的质量问题,可以提高生产效率和产品质量,减少人为错误和资源浪费,提高企业的竞争力。
随着技术的进一步发展和改进,相信图像识别技术在机械零件质量检测中的应用将变得越来越广泛和成熟。
数字图像处理技术在棒材计数中的应用

s oh p o e sn , n o spo n n y p a e rc sig ,a d ga e e ma e i t n fre no bn r mo t r c sig a d g a i rmie tb e k d p o e sn l n y lv li g s r serd it iay r a
维普资讯
20 0 6年第 3期 ( 第 16期 ) 总 7
农 业 装备 与 车辆 工程
AG I U T R LE U P N RC L U A Q IME T&V H C EE G N E I G E IL N IE是 一个 迫切 需要 解决 的 问题 。
的困难 。本文结合实际 , 以圆钢端面图像处理为例 , 详 细介 绍 了棒 材识别 计数 前 图像 预处理 的流程 和有 效方法 ,为后续棒材相关特征的快速提取和识别计
(oa y16 T tl 7 ) l
数字图像处理技术在棒材计数中的应用
李邦 明 刘 中合 王瑞 雪 马长 青 刘 贤喜
(. 1 山东农 业大学 机械与 电子_ 程学院 , 1 2 山东 泰安 ,7 0 8 2山东科技大学信息 科学与工程学 院 , 2 11 ; . 山东 泰安 ,7 0 0 2 10 )
Ab t a t T e e d i g fb r se li c p u e y n me a a e a a d t r u h f r tt n fr s g a a i n s r c : h n ma e o a te s a t r d b u r c m , n h o g o ma r so l r a m , rd t o
棒材在线计数系统的研究与应用

2 计 数 系 统 理 论 基 础
L W 1 0 0 0 自动 计 数 系统 , 以 国际 先 进 的 计算 机 视觉 技术 为 原理 , 而 棒 材 端 面 的识 别 技 术 才 是 这项 技术 的核 心 。其 参 考 以往 出 现 的 K级 容 错 计 数 方 法、 不规 则 圆形 目标模 式识 别方 法 、 多模板 覆盖 的 图
1 设计方 案
采用 济南 火 炬开发 有 限公 司开 发 的 L Wi 0 0 0自
动计 数 系统 , 它从 移 钢 机 的一 侧 采 集 运 动 棒 材 断 面 图像 , 经 图像检 测 、 识别 、 目标跟踪 后 实现 实时 计数 ,
更快 、 识别率更高的螺纹钢识别算法。 物体轮廓降维 配算法的基本思想是 : 对于一 个 具有 明显 外 围轮廓 的 目标 , 以参 考 点 ( X Y ) 为 起
论重量 与 实 际 重 量 的 差 是 相 当 可观 的 , l 2 m m 螺
跟踪 计数 模块 。输 出控制 子系 统包括 链床 控制 模块 和结 果 示模 块 。链 床控制 模块 根据 当前 计数 值 和 每搁 螺纹 钢 的根数 控 制 链 床 的运 行 ; 结 果 示 模 块 实时 显示 计数 结果 。视 觉螺 纹钢 识别 位置 安装 位置
目标 外 围轮 廓形 状 的角度 一距 离一 维 曲线 。这样 就 把原 来 二维模 板 配 的 问题 , 转 化 为一 维 曲线 配
的问题。虽然较二维模板匹配算法中时间的复杂度 减少很多 , 但该算法需要对角度距离 曲线进行规则
1 7
于光学 。 等: 棒 材在 线计数 系统 的研 究与应 用 化 。原理如 图 2所 示 。
莱钢 科 技
2 0 1 4年 2月
基于图像处理的钢棒自动打包计数系统的研究

1将模 板在 图像 中漫游 ,并将 模板 中心与 图 中 ) 某个 像素 位置 重合 ; 2读取模 板 下各对 应 像素 的灰度 值 ; ) 3将 这些 像 素 的灰 度值 进行 升序 排列 ; )
4 找 出队列 中 的中 间值 ; )
互有 遮挡 ,还有棒 材 隐匿 于落 下 的棒 材 中 ,也增加 了准 确识 别棒 材数 量 的难度 .
程 中会发 生翘 起或 撞击 ,导致 端面 不齐 ,有 时边缘
低 通 滤波在 消 除噪 声的 同时 ,也会 将 图像 中的
一
些 细节 模 糊掉 .为 了达 到 既去 除 噪声 又保 持 图像
中值 滤波 ,其 工作 原理 如下 :
细节 的 目的 ,我们采 用 了一 种非 线性 滤波 方法 ,即
复杂 ,如何 构建 系 统及准 确提 取有 用 目标 ,是 决定
系统 成败 的 关键 .本文 介 绍 了 已成 功 应用 在湘 潭 钢
铁公 司棒材 厂 的棒材 计数 系 统 的硬 件 设计 、软件 技 术及 系统 在实 际生 产 中的应 用情 况.
图像 的增强 ,即在 图像 的某个变 换 域 内,对 图像进 行 操作 ,修 改变 换后 的系 数 ,再进 行反变 换得 到处
摘 要 : 究 了一种基 于图像 处理 的钢棒在 线 自动打 包计数 研
系统.为 该 系统设 计 了一种可从 复 杂背景 图像 中提取 圆形
获 得清 晰 的棒 材 堆放 垂直 截面 图.截面 图 由采集 卡
输 入下位 计算 机 , 下位 机对 采集 到 的图像进 行分 析 、 处 理与 模式 识别 ,得 到该捆 棒材 的钢 棒数 量 ,识别 结果连 同生产线 相关信 息 被送 入服 务器 数据 库进一 步 处理 ,并 生成 各种 现场 生 产信 息统 计 报 告.同时
基于物体轮廓检测和特征提取的木材图像计数模型

基于物体轮廓检测和特征提取的木材图像计数模型某些领域需要对大量的木材进行计数和分类,例如木材加工厂和仓储中心。
在过去,这一过程通常需要大量的人力和时间,以及可能存在的误差和不一致性。
近年来,随着计算机视觉和人工智能技术的发展,基于物体轮廓检测和特征提取的木材图像计数模型已经成为了一个可以解决这一问题的有效工具。
在本文中,我们将介绍基于物体轮廓检测和特征提取的木材图像计数模型的原理和应用,以及该模型的优势和局限性。
1. 模型原理基于物体轮廓检测和特征提取的木材图像计数模型主要依靠计算机视觉和图像处理技术进行,其原理可以简单总结为以下几个步骤:1.1 图像采集:需要使用摄像头或其他图像采集设备对木材进行拍摄或录像,以获取木材的图像数据。
这一步骤需要保证图像采集设备的清晰度和稳定性,以便后续的图像处理和分析。
1.2 物体检测:接下来,需要使用物体检测算法对图像中的木材进行识别和定位。
常用的物体检测算法包括基于深度学习的目标检测算法,例如YOLO(You Only Look Once)和Faster R-CNN(Region-based Convolutional Neural Networks)等。
这些算法可以自动识别图像中的木材,并生成其轮廓信息。
1.3 特征提取:一旦木材的轮廓信息被获取,就可以利用特征提取算法对其进行分析和处理。
常用的特征提取算法包括HOG(Histogram of Oriented Gradients)和SIFT (Scale-Invariant Feature Transform)等。
这些算法可以从木材的轮廓中提取出其形状、纹理和颜色等特征信息。
1.4 计数和分类:利用机器学习和模式识别技术,可以基于木材的特征信息对其进行计数和分类。
可以使用支持向量机(SVM)或卷积神经网络(CNN)等算法进行训练和预测,以实现对木材的自动计数和分类。
2. 应用案例基于物体轮廓检测和特征提取的木材图像计数模型已经在实际应用中取得了一些成功的案例。
浅谈钢厂棒材自动计数系统
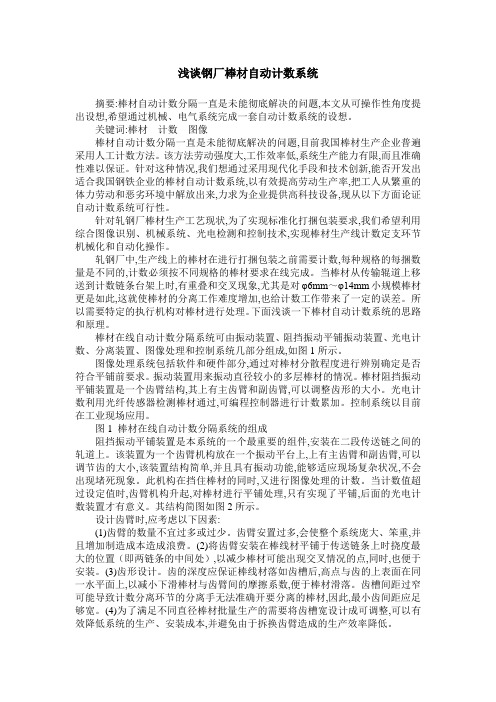
浅谈钢厂棒材自动计数系统摘要:棒材自动计数分隔一直是未能彻底解决的问题,本文从可操作性角度提出设想,希望通过机械、电气系统完成一套自动计数系统的设想。
关键词:棒材计数图像棒材自动计数分隔一直是未能彻底解决的问题,目前我国棒材生产企业普遍采用人工计数方法。
该方法劳动强度大,工作效率低,系统生产能力有限,而且准确性难以保证。
针对这种情况,我们想通过采用现代化手段和技术创新,能否开发出适合我国钢铁企业的棒材自动计数系统,以有效提高劳动生产率,把工人从繁重的体力劳动和恶劣环境中解放出来,力求为企业提供高科技设备,现从以下方面论证自动计数系统可行性。
针对轧钢厂棒材生产工艺现状,为了实现标准化打捆包装要求,我们希望利用综合图像识别、机械系统、光电检测和控制技术,实现棒材生产线计数定支环节机械化和自动化操作。
轧钢厂中,生产线上的棒材在进行打捆包装之前需要计数,每种规格的每捆数量是不同的,计数必须按不同规格的棒材要求在线完成。
当棒材从传输辊道上移送到计数链条台架上时,有重叠和交叉现象,尤其是对φ6mm~φ14mm小规模棒材更是如此,这就使棒材的分离工作难度增加,也给计数工作带来了一定的误差。
所以需要特定的执行机构对棒材进行处理。
下面浅谈一下棒材自动计数系统的思路和原理。
棒材在线自动计数分隔系统可由振动装置、阻挡振动平铺振动装置、光电计数、分离装置、图像处理和控制系统几部分组成,如图1所示。
图像处理系统包括软件和硬件部分,通过对棒材分散程度进行辨别确定是否符合平铺前要求。
振动装置用来振动直径较小的多层棒材的情况。
棒材阻挡振动平铺装置是一个齿臂结构,其上有主齿臂和副齿臂,可以调整齿形的大小。
光电计数利用光纤传感器检测棒材通过,可编程控制器进行计数累加。
控制系统以目前在工业现场应用。
图1 棒材在线自动计数分隔系统的组成阻挡振动平铺装置是本系统的一个最重要的组件,安装在二段传送链之间的轧道上。
该装置为一个齿臂机构放在一个振动平台上,上有主齿臂和副齿臂,可以调节齿的大小,该装置结构简单,并且具有振动功能,能够适应现场复杂状况,不会出现堵死现象。
基于图像处理技术的棒材自动计数方法

像素灰度值相差 比较大 的像素改取近 似于周 围像素灰度 值 的值 , 因此可 以达 到消 除噪声的 目的。中值 滤波方法 的具 体 操作是 : 用一个含有奇数 像素点 的滑动窗 口, 滑动窗 口覆 用 盖子 图中各点灰度值 的中间值 来代替 窗 口中心 点像 素 的灰
度值 。平滑处理后的图像 如图 2所示 。
中 图分 类 号 : P 9 、 T 3 l4 文献标识码 : A
0 引言
棒材 自动计数一直是钢 材生 产企 业没有解决好 的难题 。 目前企业 主要靠人工来完成钢材 的最 后定 支包装任 务 , 但人 工长时间的 目测计数 , 会引起眼睛疲劳 , 生较 大的误 差 ; 产 有 时对 一批钢材需要定期计数 、 核实 , 工作量很 大 , 因此开发棒 材 自动计数系统具有实 际意义 。近年来 , 国内外对基于计算 机视觉技术的棒材计数方法也进行 了一些有益 的探索 , 其方
理过 程 。
因受到光线 等因素 的干 扰而 含有噪声 , 噪声使 图像 质量 变 差, 使得 图像模糊 , 甚至消失了横截 面的部分特征 , 给后续的
图像分 割和计数带来 了困难。本文选择 采用 中值滤波 的方
法, 此法不但 可以克服邻域平均法滤波所带来的图像模糊 现 象, 同时又能很好地保 护图像 的边 缘 , 由于 中值滤 波不 是通 过对邻域 内的所有像素求平均值来 消除噪声 , 而是让 与周 围
图
—
操作 , 因此就需要把腐蚀操 作和膨胀 操作级 连起来使 用 ; 若 粘连情况不能得 到很好 的解决 , 为后 来的处理带来更大 的 将 麻烦 , 甚至于最终不能得到准确的计数结果 。 在数学形态学中使 用 同一个结 构元素对 图像先 进行腐 蚀运算后再进行 膨胀 运算称为开启 , 开启运算是使 目标轮廓 光滑 , 并去掉 了毛刺 , 孤立点和锐化角 ; 相对应 的如果先进行 膨胀然后腐蚀 的运算 称为 闭合 , 闭合 运算则填 平小沟 , 弥合 孔洞和裂缝 。根据这 两种运算 的特点 , 本文选 择开启 运算 , 并经过反复 比较 圆形 元素 、 方形 元素和 椭 圆元素 等结 构元 素, 发现椭 圆元素更适合在 此处使用 , 因是 椭 圆元 素更有 原 利于获得 目标的大小 、 形状 、 通性和方 向等信 息。最后决 连 定采用椭圆结构 元素 , 可以很 好 的处 理棒 材 间的粘 连 问 它 题 。形态学开启运算 后得 到的棒材横截面图像如图 3 所示 。
基于机器视觉技术的棒材自动计数系统的研究与应用

22 边 缘 检 测 -
聚类 问题 。效检 测 , 噪能 其 抗 力 强 。然而 由于其 运算 时间 复杂 度太 高 无 法应 用 于在 线 计数 系 统
一
类 的实 时系 统 。 纹 钢计 数 系统 研 制期 间 , 对螺 纹 钢识 别方 面 螺 针
部 分 图像 存在 灰 度 变化 较 缓 慢 的 边 缘 ,经 过 处 理 后 输 出 图 像 中 的边 缘 轮 廓线 较 宽 , 常 不 利 于 轮 廓 线 检 测 。 以利 用 边 缘 非 可
处 存 在 的 灰度 极 大 值 点 和灰 度 的梯 度 方 向 进 行 细 化 ,保 留极 大 值 点 可 以使 轮 廓线 成 为宽 度 较 小 的 细线 。 在 获 得 灰 度 变 化 最 大
图3
I
/ 。 1^
棒 材 图像 的参 数 调 试
鸵 I 一 升 攒 皇 构 动 … 钢{ 机
21目标 的定 位 . 为 了加 快 图 像 处 理 的 速度 , 足 实 时 性 的 要 求 , 少 无 意 义 满 减 区域 的处 理 工 作 量 ,系 统 通 过 设 置 一 个 足 以 扶 得 棒 材 运 动 图 像
转 换 并 获 取数 字 图像 。 图像 传 输 至 上 位 机 后 , 图像 识 别 、 经 目标 跟 踪 后 , 处 理 结 果 转换 成棒 材根 数传 输 给 显示 器 实 时 显 示 , 将 当 数 值 达 到 设定 值 后 , 屏 幕 上 显示 分 钢 线 , 送 链 停 止 。 图形 工 在 传 作 站 发 出 信 号 至伺 服驱 动 器 ,进 而 驱 动 伺 服 电机 使 端 分 机 左 右 移动 , 当端 分 机 分 钢 楔 位 置 与 显 示 屏 幕 上 的 分 钢 线 重 合 时 , 缸 气
基于图像识别的管材计数系统方案研究-大学本科毕业设计

基于图像识别的管材计数系统方案研究-大学本科毕业设计基于图像识别的管材计数系统方案研究专业:测控技术与仪器专业摘要:目前国内对于管材的计数主要采用人工计数的方法,为减轻人工劳动强度和提高管材计数精度,论文基于图像识别对管材的计数系统进行了研究,通过识别管材的截面特征实现管材计数。
软件部分主要包括图像的预处理、图像分割和目标计数部分。
具体的研究内容包括:若管材截面图像内容较多,先截取对于图像中感兴趣的区域,再经过格式转换、图像增强、去噪等预处理得到边缘平滑的灰度图像,采用大津法自动获取阈值,将目标圆或椭圆与背景分离出来,由于管材之间存在一定空隙,可采用数学形态学中的闭运算以消除部分噪声和狭小间隙,之后通过对目标圆或椭圆的边缘进行计数,因为可能存在较大噪声在闭运算过程中并未消除,因此可通过设置边缘的最小外接圆的面积和边缘本身的面积的比率进行条件限制,以去除部分噪声。
若结果存在明显误差,可通过人工修改计数结果以提高精度,系统可保存计数结果和源图像以供日后查证;最后设计软件实现管材计数系统。
关键词:图像识别,管材,计数,图像分割Pipe Counting System Scheme Studies Based onImage RecognitionMajor:Measure and Control Technology and InstrumentAbstract:In China,the method for pipes counting mainly used manual counting. To alleviate the labor intensity and improve the accuracy,the paper makes a research on pipes counting based on image recognition. The system counts pipes through recognising the feature of the pipes cross-section. The software part mainly include the image preprocessing,the image segmentation and pipes counting. And the paper mainly includes the following content:If the pipe cross-section image include too much content,clipping the region of interest in the image. Then preprocess the image,including converting the image format,the image enhancement,removing noise and so on,and then there will be a grayscale image with smooth edges. Next,use Otsu method to obtain threshold automatically,and get the image isolated target circle or ellipse and background. Since there are some gaps between the pipes,use closed operation of morphology mathematical to remove part of the noise and small gaps. Then count the edge of the circle or ellipse.Because there may be some large area noise that has not been eliminated in the process of closed operation,set the ratio of the area of the minimum circumscribed circle to the edge and its area to remove part of noise.If the result has obvious errors,it can be manually modified in order to improve the accuracy.The source image and the result can be saved for verification in the future.Finally design software to complete the pipes counting system.Keywords:Image recognition;Pipes;Counting;Image segmentation目录第一章绪论 (1)1.1 研究目的 (1)1.2 选题背景及意义 (1)1.2.1 选题背景 (1)1.2.2 选题意义 (1)1.3 国内外研究现状 (2)1.3.1 国外研究现状 (2)1.3.2 国内研究现状 (2)1.4 主要研究内容 (3)第二章图像处理相关技术 (4)2.1 图像预处理 (4)2.1.1 灰度转换 (4)2.1.2 图像滤波 (5)2.2 图像分割 (9)2.2.1 阈值分割法 (10)2.2.2 基于边缘的分割方法 (11)2.2.3 基于特定理论工具的分割方法 (12)第三章方案设计 (15)3.1 简单背景图片的处理 (15)3.1.1 灰度处理 (16)3.1.2 滤波处理 (16)3.1.3 图像分割 (17)3.1.4 消除噪声 (17)3.2 繁杂背景图片的处理 (18)3.2.1 截取管材区域 (18)3.2.2 图片处理 (19)第四章目标计数 (20)4.1 计数方法的比较和选取 (20)4.2 计数结果和精度分析 (20)第五章计数系统的设计与实现 (22)5.1 硬件部分 (22)5.2 软件开发环境 (22)5.3 软件设计流程 (23)5.3.1 图像输入部分 (24)5.3.2 图像处理部分 (25)5.3.3 结果显示部分 (26)第六章总结与展望 (26)6.1 总结 (26)6.2 展望 (26)致谢 (27)参考文献 (28)第一章绪论1.1 研究目的本设计通过识别管材的截面图像实现管材的计数,并结合硬件和软件的设计实现系统的开发。
图像采集识别技术在计量器具检验中的应用

图像采集识别技术在计量器具检验中的应用研究社会发展非常迅速,而且智能化技术开始在各行各业普及。
电能计量器具的质量以及准确性开始受到了社会各界的关注,因此将电能计量器具放置在权威的机构完成更加全面的检验,确保整个电能计量装置的准确性是非常必要的。
在现阶段,电能表等计量器具的种类是非常多的,而且样品的数量也非常大,整个试验的过程是比较复杂的。
一、人工智能以及计算机视觉的发展现状在20世纪50年代,主要的计算机图像识别在于光学字符的识别以及显微图片和航空图片的分析上面。
60年代的MIT能够通过计算机图像当中提取出立方体或者是棱柱体等多种三维模型,并且对物体的形状进行描述,Roberts的研究工作开创了三维场景的研究,Roberts对于积木世界的创造性给予了人们很多的启示,70年代正式出现了视觉应用系统。
70年代的中期,麻省理工学院的人工智能实验室展开了相关的课程研究,并且吸引了许多知名学者参与研究,对于该项技术的研究热潮,从20世纪80年代开始一直到中期,计算机视觉得到了非常好的发展,有一些新的理论以及现在概念开始不断地涌现出来,计算机视觉领域在研究的过程当中一直呈现着两个非常明显的特点,分别为多样性和不完善性,针对于计算机视觉的研究其实可以追溯到更早的时候。
但是一直到20世纪70年代后期,计算机的性能有效地提升了之后才得到真正的关注,而且这些发展是源自于其他不同的领域的需求的,对于计算机视觉问题始终没有得到一个真正的定义尽管如此,但是人们仍旧对计算机视觉的研究任务非常的憧憬,并且将这些方法应用在了某些大规模系统的问题的解决上面。
比如工业当中的质量控制和医学当中的图像处理。
人工智能在研究过程当中的一个最为主要的问题就是如何让系统设备能够具有计划跟决策的能力,从而完成一个特定的动作。
这和计算机的视觉问题发展是有着很大的联系,对于人工智能来说,计算机的视觉相当于它的一个智能的感应器,可以有效地提供更多的数据信息。
图像识别技术在棒材计数中的应用
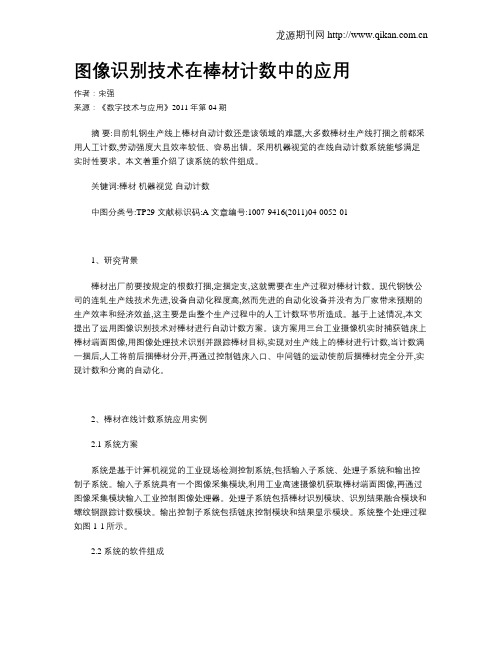
图像识别技术在棒材计数中的应用作者:宋强来源:《数字技术与应用》2011年第04期摘要:目前轧钢生产线上棒材自动计数还是该领域的难题,大多数棒材生产线打捆之前都采用人工计数,劳动强度大且效率较低、容易出错。
采用机器视觉的在线自动计数系统能够满足实时性要求。
本文着重介绍了该系统的软件组成。
关键词:棒材机器视觉自动计数中图分类号:TP29 文献标识码:A 文章编号:1007-9416(2011)04-0052-011、研究背景棒材出厂前要按规定的根数打捆,定捆定支,这就需要在生产过程对棒材计数。
现代钢铁公司的连轧生产线技术先进,设备自动化程度高,然而先进的自动化设备并没有为厂家带来预期的生产效率和经济效益,这主要是由整个生产过程中的人工计数环节所造成。
基于上述情况,本文提出了运用图像识别技术对棒材进行自动计数方案。
该方案用三台工业摄像机实时捕获链床上棒材端面图像,用图像处理技术识别并跟踪棒材目标,实现对生产线上的棒材进行计数,当计数满一捆后,人工将前后捆棒材分开,再通过控制链床入口、中间链的运动使前后捆棒材完全分开,实现计数和分离的自动化。
2、棒材在线计数系统应用实例2.1 系统方案系统是基于计算机视觉的工业现场检测控制系统,包括输入子系统、处理子系统和输出控制子系统。
输入子系统具有一个图像采集模块,利用工业高速摄像机获取棒材端面图像,再通过图像采集模块输入工业控制图像处理器。
处理子系统包括棒材识别模块、识别结果融合模块和螺纹钢跟踪计数模块。
输出控制子系统包括链床控制模块和结果显示模块。
系统整个处理过程如图1-1所示。
2.2 系统的软件组成棒材计数系统软件部分可以大致分为如下五个模块:图像采集模块、图像预处理和棒材识别模块、棒材跟踪和计数模块、链床控制模块和结果显示模块。
(1)图像采集模块;视频图像采集模块的主要软件功能是采集位置合适、清晰、实时的现场图像,供图像预处理和棒材识别模块进行后续处理。
利用图像采集卡,采集由摄像头拍摄的现场图像,并通过采集卡输入工控机,为以后的图像处理做好准备。
基于物体轮廓检测和特征提取的木材图像计数模型

基于物体轮廓检测和特征提取的木材图像计数模型
木材图像计数是一个重要的问题,它在木材加工和管理中起着关键作用。
由于木材的复杂形状和数量,传统的计数方法往往不够准确和高效。
基于物体轮廓检测和特征提取的木材图像计数模型应运而生。
我们需要使用计算机视觉中的图像处理技术来提取木材的轮廓。
常用的方法包括边缘检测和分割算法。
边缘检测算法可以通过检测图像中的边缘线条来获取木材的轮廓信息,常用的边缘检测算法包括Canny算法和Sobel算法。
而分割算法则可以将图像中的木材区域与背景区域进行分离,常用的分割算法包括阈值分割和基于区域的分割算法。
接下来,我们需要对提取到的木材轮廓进行特征提取。
特征提取的目的是从木材的轮廓中提取出能够区分不同木材的特征。
常用的特征包括周长、面积、形状因子等。
其中周长可以用来表征木材的长度,面积可以用来表征木材的大小,而形状因子可以用来表征木材的形状。
然后,我们可以使用机器学习的方法来建立木材图像计数模型。
常用的机器学习算法包括支持向量机(SVM)、K近邻(KNN)、决策树等。
这些算法可以通过学习已知数量的木材图像来预测未知数量的木材图像,以达到准确计数的目的。
我们需要对木材图像计数模型进行评估和优化。
评估的方法可以使用混淆矩阵、精确率、召回率等指标来衡量模型的准确性和性能。
而优化的方法可以使用参数调整、数据增强等技术来提高模型的性能和鲁棒性。
- 1、下载文档前请自行甄别文档内容的完整性,平台不提供额外的编辑、内容补充、找答案等附加服务。
- 2、"仅部分预览"的文档,不可在线预览部分如存在完整性等问题,可反馈申请退款(可完整预览的文档不适用该条件!)。
- 3、如文档侵犯您的权益,请联系客服反馈,我们会尽快为您处理(人工客服工作时间:9:00-18:30)。
图像识别技术在棒材计数中的应用
【摘要】:随着计算机技术和光电技术的飞速发展,数字图像处理技术得到了迅速发展和广泛应用,其中数字图像检测就是其重要应用。
采用这种自动成像检测系统能克服人工检测带来的不利因素,提高检测精度和效率,降低生产成本。
目前棒材自动计数还是该领域的难题,大多数棒材生产线打捆之前都采用人工计数,劳动强度大且效率较低、容易出错。
采用机器视觉的在线自动计数系统能够满足实时性要求。
本文着重介绍了该系统的软件组成。
【关键词】:棒材机器视觉自动计数
引言
我国棒材生产的传统工艺都是依据产品的实际重量来包装的,而在一般情况下,用户要求的是以棒材的根数来作为计量单位,特别是在钢材市场上,也希望得到固定支数包装的棒材。
同时,生产厂家如果按负公差组织生产,也必须得到成品棒材的根数这一重要数据。
然而,成品棒材打捆时的计数和定支数包装,是个一直都没有得到很好解决的问题。
目前轧钢生产中常使用的机械式和光电脉冲式棒材计数装置,由于轧钢生产工艺条件限制,一束或一捆棒材在通过此类计数装置时是连续向前移动并且存在抖动或者交叉重叠现象,计数装置受自身的组成机构和工作原理制约,对该条件下棒材空间位置的分辨能力和时间响应能力均不理想,特别是在机组产量超出计数装置的允许范围时,会带来较大计数误差。
一.在棒材计数中图像识别技术的重要地位
在棒材生产企业中棒材自动计数长期是处于一种悬而未决的位置。
企业目前大多在最后定支包装任务上采取人工完成棒材的方式, 但是这样又存在一些缺点,有时对一批棒材需要工作量很大的定期核实、计数,由于人工作业是长时间的直观视觉计数,对眼睛的劳损度过高, 长时间作业后极易产生误差。
因此, 开发棒材的自动计数系统是一个迫切需要解决的问题。
同时棒材在恶劣的环境下采集,加上不均匀的光照,最后获得的图像常常噪音过大,十分不清晰,而且形成质量较差棒材端面图像,出现比较严重的棒材端面重叠粘连现象,这些都给棒材计数的最终识别增加了一定的困难。
但是伴随着计算机视觉、模式识别技术和图像处理的高速发展,在计算机视觉技术基础之上的棒材计数方法国内外均进行了例如腐蚀法、基于圆周模板匹配方法、图像距离法等的多种良性的研发。
但尽管如此,棒材的断面图像是否能良好预处理,任然是实行几乎所有的计数方法的实用性和准确性的最根本问题。
本文探讨了在棒材支数自动计数的技术如何利用数字图像处理技术,它对解决轧钢生产线上棒材自动计数这一难题,有一定的有益帮助。
二、数字图像处理技术概述微型图像处理系统的高速传播,是随着微型机性能的脚稳步提升的。
最基本的微型图像处理系统是由配以图像卡及显示设备的主机为PC机的设备构成的。
图像处理系统中常用的图像输入设备是摄像机。
通
常图像采集卡安装于计算机主板扩展槽中,主要包括图像存储器单元、显示查找表单元、摄像头接口、监视器接口和PC机总线接口单元。
图像处理系统的输出设备可采用很多形式, 最常用的设备打印机和监视器。
“Digital Image Processing”是数字图像处理的英文名称。
Computer Image Processing,即通常所说的数字图像处理,为计算机图像处理指用计算机进行的处理。
利用其他数字硬件或者数字计算机为数字图像处理,为了提高图像的使用性,而通过某些数学运算对从图像信息转换而得的电信号进行处理。
这样做的好处是:1) 方便简洁,精度高。
2) 图像大小能用度高。
3) 良好的再现性。
三.传统点扩散算法
点扩散法具有阈值抖动和误差扩散的优点。
它使用一个参数矩阵C(设该矩阵的大小I×J是,元素的值从1—I×J,I、J是正整数常量)来决定处理像素的顺序。
其具体步骤如下:
1.对于一个连续调图像,设(n1,n2)是其中的像素点,将所有像素点按照(n1modI,n2modJ)的方法分成I×J个等级。
2.设X(n1,n2)是对连续调图像像素进行的阈值操作,取阈值为0.5,k为像素点的等级,当k=1时,对所有等级为1的像素点进行处理:X(n1,n2)∈[0,1](1)
对于一个固定的等级k,让所有等级为k的像素点通过公式进行半色调处理:
3.考虑此点的8个邻域点,定义误差e(n1,n2)=X(n1,n2)-h(n1,n2),对八邻域点内等级高于当前点而且未被半色调处理的点按下面的规则进行像素值调整:如果此邻域点垂直于当前点(处于当前点的上下位置或水平位置)则调整为X(i,j)+2e(n1,n2)/ω,如果此邻域点处于对角线位置则调整为X(i,j)+e(n1,n2)/ω,其中ω为误差的
累加(对垂直邻域点和对角线邻域点的不同处理是根据人眼对垂直点的像素变化更敏感的原理)。
4.继续按相同方法处理下一个等级,即k=2的像素点(此时原图像的某些点的像素值已经被调整,但因为是基于前面的误差进行的调整,所以对最后输出图像的效果没有负面影响),依次处理完图像所有的点,最后获得原始图像的半色调图像。
四.在线计数系统中的棒材应用实例
1. 工业现场检测控制系统
包括输入子系统、处理子系统和输出控制子系统的系统是在计算机视觉基础之上的工业现场检测控制系统。
它们三者又是一下部分构成,图像采集模块、工业高速摄像机、图像采集模块和工业控制图像处理器构成输入子系统,它们之前相关联运作。
螺纹钢跟踪计数模块、识别结果融合模块和棒材识别模块构成处理子系统。
结果显示模块和链床控制模块构成输出控制子系统包括。
2工业现场检测控制系统的软件组成
棒材计数系统软件可大致以以下五个模块来划分:图像采集模块、计数模块和棒材跟踪、棒材识别模块和图像预处理、结果显示模块和链床控制模块。
视频图像采集模块; 图像的采集模块的主要软件功能是现场采集清晰、实时、位置合适的图像,便于棒材识别模块和图像预处理进行后面的处理工作。
棒材识别模块和图像预处理;利用图像采集卡,手机现场的由摄像头拍摄的在线情景,再交由采集卡输入工控机,方便以后的图片处理工作。
棒材识别模块和图像预处理主要功能分别是最终识别出棒材及其中心位置和分割出要识别的棒材目标。
计数模块和棒材跟踪; 对位跟踪相邻帧图像中识别的棒材是计数模块和棒材跟踪的主要功能,并在合适的时候对棒材进行计数。
进一步跟踪棒材之前,需要识别得到棒材中心坐标点,然后再计算出经过当前视窗范围的棒材数目,从而达到最终的目的,棒材计数。
链床控制模块;它是根据当前的设定和计数值和对每捆棒材根数控制中间链床运动和入口链床。
当计数值达到额定值,为了快速准确的完成端头分钢,需要等待停止中间链运动, 一定时间后,分钢窗口左边分钢停止,; 当计数值未满一捆值时,协调中间链运动、控制入口链,从而使棒材堆叠情况减少。
结果显示模块;当前帧图像中已计数螺纹钢、当前计数值、已识别但未确认的棒材构成计数状态。
它用于实时显示系统运行时计数状态。
结语
综上所述,研究复杂工况条件下的基于机器视觉在线棒材自动计数具有非常巨大的技术研究价值和实际应用价值。
在技术研究方面,本课题虽是针对棒材计数而提出的,但其原理和方法却能适应其他场合,有广阔的应用价值。
参考文献
[1]宋强, 等.基于图像处理的棒材自动计数技术[J].钢铁.2004;39( 5) ,
[2]章霄,董艳雪,赵文娟,等,数字图像处理技术[J],北京,冶金工业出版社.2005
[3]李红俊,韩冀皖,数字图像处理技术及其应用[J],计算机测量与控制,2002,10(9)
[4]刘中合,王瑞雪,王锋德,等,数字图像处理技术现状与展望[J],计算机时代,2005。