密炼机液压系统设计说明
液压系统的设计范文
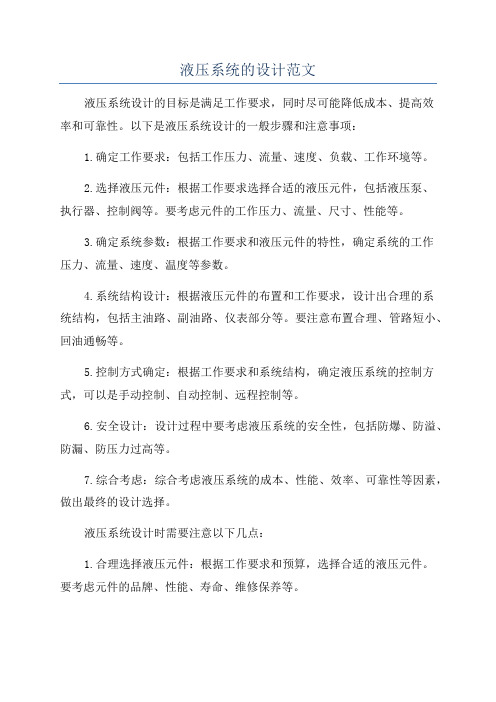
液压系统的设计范文液压系统设计的目标是满足工作要求,同时尽可能降低成本、提高效率和可靠性。
以下是液压系统设计的一般步骤和注意事项:1.确定工作要求:包括工作压力、流量、速度、负载、工作环境等。
2.选择液压元件:根据工作要求选择合适的液压元件,包括液压泵、执行器、控制阀等。
要考虑元件的工作压力、流量、尺寸、性能等。
3.确定系统参数:根据工作要求和液压元件的特性,确定系统的工作压力、流量、速度、温度等参数。
4.系统结构设计:根据液压元件的布置和工作要求,设计出合理的系统结构,包括主油路、副油路、仪表部分等。
要注意布置合理、管路短小、回油通畅等。
5.控制方式确定:根据工作要求和系统结构,确定液压系统的控制方式,可以是手动控制、自动控制、远程控制等。
6.安全设计:设计过程中要考虑液压系统的安全性,包括防爆、防溢、防漏、防压力过高等。
7.综合考虑:综合考虑液压系统的成本、性能、效率、可靠性等因素,做出最终的设计选择。
液压系统设计时需要注意以下几点:1.合理选择液压元件:根据工作要求和预算,选择合适的液压元件。
要考虑元件的品牌、性能、寿命、维修保养等。
2.确保系统的工作可靠性和安全性:要考虑系统在工作过程中的安全性,包括防爆、防溢、防漏、防压力过高等。
3.考虑系统的能效:要尽可能减少能源消耗,提高液压系统的效率。
可以采用变量泵、液压油气蓄能器等技术来提高系统的能效。
4.预留扩展余地:在设计时要留有一定的扩展余地,以便后期可以根据需要进行系统的扩展和升级。
综上所述,液压系统的设计是一个综合考虑工作要求、元件选择、系统参数确定、系统结构设计、控制方式选择等多方面因素的过程。
通过合理的设计,可以满足工作要求,提高系统的效率和可靠性,降低成本。
同时,设计过程中要注意系统的安全性和能效,预留扩展余地。
液压系统设计需要深入理解液压原理和液压元件特性,并结合实际情况做出合理选择。
完整的液压系统设计毕业设计

完整的液压系统设计毕业设计1. 引言液压系统在工程领域中具有广泛的应用,特别是在机械制造、航空航天、汽车制造等领域中。
本文档旨在设计一个完整的液压系统作为毕业设计,并提供系统设计的详细说明。
2. 设计目标本设计的目标是创建一个可靠、高效的液压系统,满足以下需求:•传递大量的力和动力;•控制和调节工作负载;•提供良好的工作稳定性;•实现节能和环保。
3. 系统设计3.1 系统结构我们的液压系统将包含以下主要组件:1.液压泵:负责将液体加压并输送到液压马达或液压缸;2.液压马达或液压缸:负责将液压能转化为机械能,实现力的传递及工作载荷控制;3.液体储存装置:用于储存液体并平衡系统压力;4.液压阀门:用于控制液体流动和压力,实现系统工作的调节和控制;5.传感器和仪表:用于监测和测量液压系统的压力、流量、温度等参数。
3.2 液体选择在设计液压系统时,我们需要选择合适的液体作为工作介质。
一般情况下,液压系统常采用液体油作为工作介质,因为它具有良好的润滑性、稳定性和耐高温性能。
对于不同的应用场景,需要考虑液体的黏度、温度范围、氧化稳定性以及环境友好程度等因素。
3.3 液压元件选型为了实现液压系统的设计目标,我们需要对液压元件进行合理的选型。
液压泵、液压马达或液压缸、液压阀门等元件都有不同的类型和规格可供选择。
在选型过程中,需要考虑力的传递要求、流量和压力范围、工作稳定性以及适应特定工况的能力等因素。
3.4 系统控制在液压系统设计中,系统的控制是十分重要的。
通过合理的控制方法和策略,可以实现对液体流动、压力和工作负载的准确控制。
常用的液压系统控制方法有手动控制、自动控制和比例控制等。
根据具体需求,选择适合的控制方式可以提高系统的稳定性和性能。
4. 系统优化为了提高液压系统的工作效率和节能性,我们可以进行进一步的优化。
以下是一些常见的系统优化方法:•使用高效节能的液压泵和液压马达;•优化液体流动路径,减小能量损失;•采用高效的液压阀门和控制系统,减小能量损耗;•合理设计系统布局和管路,减小摩擦损失;•控制液压系统的工作温度,在适当的范围内减小能量损失。
液压系统的设计步骤与设计要求
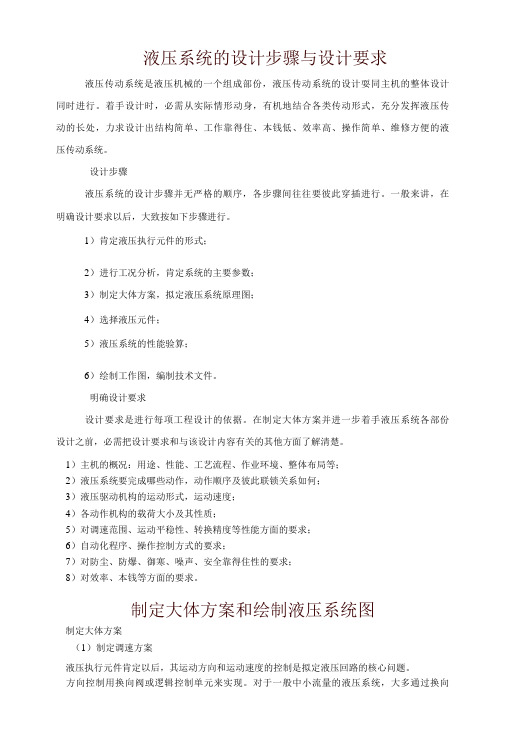
液压系统的设计步骤与设计要求液压传动系统是液压机械的一个组成部份,液压传动系统的设计耍同主机的整体设计同时进行。
着手设计时,必需从实际情形动身,有机地结合各类传动形式,充分发挥液压传动的长处,力求设计出结构简单、工作靠得住、本钱低、效率高、操作简单、维修方便的液压传动系统。
设计步骤液压系统的设计步骤并无严格的顺序,各步骤间往往要彼此穿插进行。
一般来讲,在明确设计要求以后,大致按如下步骤进行。
1)肯定液压执行元件的形式;2)进行工况分析,肯定系统的主要参数;3)制定大体方案,拟定液压系统原理图;4)选择液压元件;5)液压系统的性能验算;6)绘制工作图,编制技术文件。
明确设计要求设计要求是进行每项工程设计的依据。
在制定大体方案并进一步着手液压系统各部份设计之前,必需把设计要求和与该设计内容有关的其他方面了解清楚。
1)主机的概况:用途、性能、工艺流程、作业环境、整体布局等;2)液压系统要完成哪些动作,动作顺序及彼此联锁关系如何;3)液压驱动机构的运动形式,运动速度;4)各动作机构的载荷大小及其性质;5)对调速范围、运动平稳性、转换精度等性能方面的要求;6)自动化程序、操作控制方式的要求;7)对防尘、防爆、御寒、噪声、安全靠得住性的要求;8)对效率、本钱等方面的要求。
制定大体方案和绘制液压系统图制定大体方案(1)制定调速方案液压执行元件肯定以后,其运动方向和运动速度的控制是拟定液压回路的核心问题。
方向控制用换向阀或逻辑控制单元来实现。
对于一般中小流量的液压系统,大多通过换向阀的有机组合实现所要求的动作。
对高压大流量的液压系统,现多采用插装阀与先导控制阀的逻辑组合来实现。
速度控制通过改变液压执行元件输入或输出的流量或利用密封空间的容积转变来实现。
相应的调整方式有节流调速、容积调速和二者的结合——容积节流调速。
节流调速一般采用定量泵供油,用流量控制阀改变输入或输出液压执行元件的流量来调节速度。
此种调速方式结构简单,由于这种系统必需用闪流阀,故效率低,发烧量大,多用于功率不大的场合。
全液压式实验密炼机加料、压料及传动部分的设计

前言炼混炼胶料存在质量差、效率低、劳动强度工作环境恶劣等一系列问题。
为了克服这一系列的问题密炼机慢慢出现。
随着高分子材料的飞速发展和科学技术的不断进步,密炼机的用途越来越广泛,主要用于橡胶的塑炼及混炼,还可以用于塑料、沥青等其它高分子材料的混合以及橡塑共混等,由于其独特的优越性,已经成为橡塑工业中最关键的混炼设备之一。
自密炼机产生以后,在混炼过程中显示了它一系列的优点:混炼时间短,生产效率高,操作容易,较好的克服粉尘飞扬,减少配合剂的损失,改善劳动条件,减轻劳动强度等。
随着科技的进步,人们对橡胶混炼的要求越来越高,迫切要求对原来的旧机台进行更新换代,对旧的密炼机技术进行提高和完善。
随着世界橡胶工业的全面复苏及轮胎工业的全面崛起,于是密炼机正向着密炼室容量大型化、主电机大功率,转子转速高速化,多级化或无级化的方向发展。
一种作为研制开发作用的小型实验密炼机的出现势在必行,其为各种密炼机的发展演示起着至关重要的作用。
X(S)M-1全液压式实验密炼机就是顺应密炼机发展,功能演示的一种高性能的密炼机。
其具有橡塑共混,同步高速转子转动,尺寸比较小结构比较紧凑,主要适用于实验室等良好的环境的场合下,尺寸结构简洁、经济、实用的众多优点。
本设计总结了X(S)M-1全液压式实验密炼机的设计过程,设计方法和设计理论依据,设计机台的优缺点。
本说明书主要介绍了X(S)M-1全液压式实验密炼机的加料压料装置、传动装置设计计算,还有有关的技术说明。
本设计力求使机台性能达到同类机台的先进水平。
希望所设计的机台既能准确完成既定的工艺生产要求,又能使机台强度、刚度、耐磨性、寿命等可靠。
并注意汲取先前的经验,注意创新改进,使机台结构简单,外形美观,且能提高生产率和降低能耗,另外,还要考虑加工成本和维修方便等。
1.绪论1.1 密炼机的发展与我国密炼机现状1.1.1密炼机的发展概述1.1.2 我国内密炼机现状国内在20世纪80年代以前,混炼胶加工机械的发展与工业化国家生产的机型、数量、结构形式、自动化程度、可靠性和联动化的水平等都存在很大的差距。
密炼机说明书

2电控设备的操作2.1 直流主电动机的启动和停止直流主电动机的启动和停止是由直流传动柜和操作台来完成的。
2.1.1 直流主电机的启动首先将直流传动柜中的所有断路器及熔断器合上,直流传动柜的本控/遥控开关旋至本控位置,则直流电动机的启动由直流传动柜本身来完成,按合闸按钮,按主机启动,点击启动后,按升降速按钮调整主机速度,但需要注意的是此时电机的转动与机器附属设备没有联锁,因此只可为临时调试中使用;如旋至遥控位置,先要在直流传动柜上把主开关合上,既按合闸按钮,ME开关合闸,此时倒操作台来启动主电机,在启动主电机前,附属设备首先要运转正常,没有故障报警,按操作台上的63SH14装置主回路合闸,同时电机风机启动,这时才可以按操作台上的63SH06启动主电机,根据工艺要求电机的速度可以通过按升速按钮63S12或按降速按钮63S13在4-40r/min连续可调。
2.1.2 直流主电动机的停止1)当要停止直流主电动机时,按降速按钮63S13,电机转速降为低速时,按动操作台上的63SH07或直流柜上的主机停止按钮,主电机将进入停止状态。
如果长时间不启动电机,应到控制室将装置主回路断开,即使ME开关断开。
2)当机器有下列情况发生,产生声光报警,压砣抬起,卸料门打开,延时10秒主机停止。
(a)主机过载。
(b)主电机绕组超温(100度)。
(c)高压泵故障。
3)当机器有下列情况发生,产生社声光报警并延时150秒停机,压砣抬起,卸料门打开。
(a)干油泵停。
(b)减速机润滑油堵塞。
(c)干油泵低油位。
(d)密封圈、电机、减速机轴承超温。
(e)电机冷却水停。
(f)液压站停止。
(g)液压站滤油堵塞。
(h)密炼温度超过炼胶温度(根据工艺要求)。
2.2 控制电源当外部电源已接至操作柜内,此时合上6Q01断路器,用万能表测量三相电压为AC380V 后,合上6Q02断路器。
按动控制电源开(按钮6SH01),控制电源开指示灯亮(灯钮6SH01),说明控制电源正常通电。
GK系列密炼机新型液压密封动环结构的设计

作者简介:秦恩臣(1993-),男,工学学士,毕业于青岛科技大学,主要从事炼胶设备密炼机等的设计。
收稿日期:2020-08-05目前混炼胶的生产主要是采用密炼机来进行的。
混炼胶是由橡胶、炭黑、促进剂、油料等混合加工而成。
这些油料和细粉状的物料是通过密炼机的转子轴端密封装置来控制以避免泄露。
因此密炼机密封效果成为决定炼胶设备品质优良的重要因素,密封效果好,就可以减少物料的泄露,这样既能保证工艺配方的稳定和胶料的品质,又能减少污染,改善工作环境。
所以密封问题一直是橡胶行业重点关注的问题。
1 密炼机液压密封装置目前转子端面密封形式多种多样,但应用最多的为端面接触式密封,而自动化程度最高操作更便捷的液压密封方式更被广大厂家所青睐。
液压密封是通过油缸实现对静环的加压,使静环与动环之间产生压力,从而达到密封的效果,其主要有拨叉式液压密封(图1)和油缸直压式液压密封(图2)两种。
1-油缸;2-弹簧;3-拨叉;4-支杆;5-静环;6-动环图1 拨叉式液压密封示意图1.1 拨叉式液压密封拨叉式液压密封是由动环、静环、支杆、弹簧、GK 系列密炼机新型液压密封动环结构的设计秦恩臣,王志飞,陈兴忠,康鹏志(益阳橡胶塑料机械集团有限公司,湖南 益阳 413000)摘要:文章主要论述对密炼机转子轴端液压密封装置中动环结构的改进,通过改变动环的安装方式,将动环改为新式的剖分结构,达到既能保证密封效果,又方便维修拆装的目的。
关键词:GK 系列密炼机;液压密封;动环;剖分式结构中图分类号:TQ336.42文章编号:1009-797X(2020)21-0031-05文献标识码:BDOI:10.13520/ki.rpte.2020.21.007 拔叉及油缸等组成。
其主要是通过杠杆原理,通过油缸注油使活塞杆伸长,带动拔叉以中间支杆固定点为支点,把外力传递到拔的另一端,使静环紧贴于动环的工作端面起到密封作用。
1.2 油缸直压式液压密封油缸直压式液压密封主要由动环、静环、油缸及油缸固定板等组成。
液压系统设计说明书

液压系统设计说明书⽬录第⼀章组合机床⼯况分析 (2)1.1.⼯作负载分析 (3)1.2.惯性负载分析 (3)1.3.阻⼒负载分析 (3)1.4.⼯进速度选择 (3)1.5.运动时间 (3)1.6.运动分析 (4)1.7.根据上述数据绘液压缸F-s与v-s图 (5)第⼆章液压缸主要参数确定 (6)2.1 初选液压缸⼯作压⼒ (6)2.2 计算液压缸主要尺⼨ (6)2.3 活塞杆标准⾏程的确定 (7)2.4 活塞杆稳定性校核 (7)2.5 计算液压缸流量、压⼒和功率 (7)2.6 绘制⼯况图 (9)2.7 液压缸结构设计 (9)2.8 液压缸设计需注意的事项 (10)2.9 液压缸主要零件的材料和技术要求 (10)第三章拟定液压系统图 (11)3.1 动作要求分析 (11)3.2 选⽤执⾏元件 (11)3.3 确定供油⽅式 (11)3.4 调速⽅式选择 (11)3.5 速度换接选择 (12)3.6 换向⽅式选择 (12)3.7 选择调压和卸荷回路 (12)3.8 拟定液压系统原理图 (12)3.9 液压系统⼯作原理 (13)第四章拟定液压系统图 (14)4.1确定液压泵 (14)4.2 计算总流量 (15)4.3 电动机的选择 (15)4.4 阀类元件和辅助元件的选择 (16)4.6 隔板尺⼨的确定 (17)4.7 油管选择 (17)第五章液压系统性能验算 (19)5.1验算系统压⼒损失并确定压⼒阀的调整值 (19)5.2油液温升验算 (21)第六章设计⼼得 (22)附录:参考⽂献 (23)第⼀章组合机床⼯况分析明确设计要求:组合机床动⼒滑台的⼯作要求液压系统在组合机床上主要是⽤于实现⼯作台的直线和回转运动,多数动⼒滑台采⽤液压驱动,以便实现⾃动⼯作循环。
本实验设计⼀台卧式单⾯多轴钻镗两⽤组合机床液压系统,要求液压系统实现快进——⼯进——死挡铁停留——快退——停⽌的动作循环,切削⼒为18000N,动⼒滑台采⽤平导轨,⼯进速度要求⽆级调速。
7、密炼机加压、卸料装置及液压系统的设计

参考专利
1.主要设计参数
密炼机容积1L
采用四棱啮合式结构
采用哈克结构
联接方式:采用万向联轴节
轴向振动频率500次/分,采用超声驱动
下定栓采用液压翻转机构
上顶栓采用液压翻转结构
主要任务
(1)对整台橡胶混炼装置的各个部分组成、工作原理及主要结构等要有较全面的了解。
(2)熟练掌握并应用一种二维CAD设计软件。
(3)在掌握和理解整台机器工作原理、用途和结构基础上,提出所承担部分的密炼机加料、卸料装置及液压系统的设计方案,并进行比较,选用一种最为理想的
能代表本人能力的方案,作为本次设计方案。
(4)重点掌握的结构,完成以下几个部分设计
1)密炼机加料装置的设计
2)卸料结构的设计
3)液压系统的设计。
(5) 完成所规定的总(部)、零件图的设计,总工作量要在3张零号图纸以上。
(6)设计说明书一份,不低于10000字(阐述清楚、计算正确)。
3. 目标:
在指导教师指导下,通过查阅资料、实习参观,完成所承担的密炼机加料、卸料装置及液压系统的设计,设计内容应准确无误。
通过本学期毕业设计,要达到能综合运用大学期间所学各种知识,逐渐养成一种能独立发现问题、分析问题和解决问题能力思维意识。
串联式密炼机卸料门液压驱动系统设计与仿真
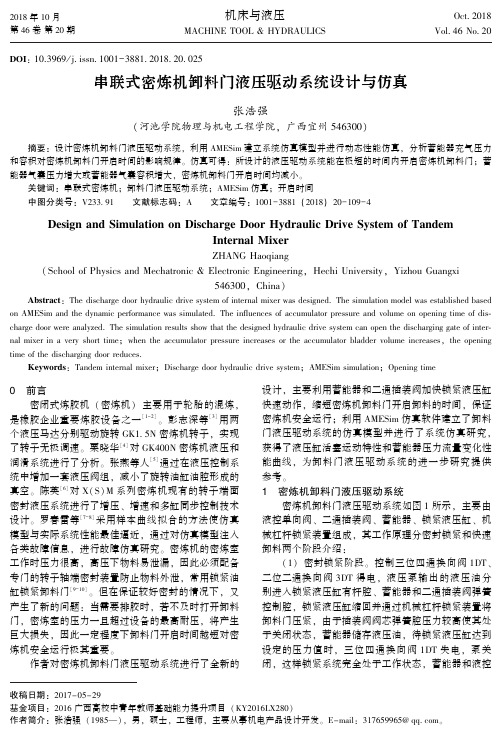
2018年10月第46卷第20期机床与液压MACHINETOOL&HYDRAULICSOct 2018Vol 46No 20DOI:10.3969/j issn 1001-3881 2018 20 025收稿日期:2017-05-29基金项目:2016广西高校中青年教师基础能力提升项目(KY2016LX280)作者简介:张浩强(1985 ),男,硕士,工程师,主要从事机电产品设计开发㊂E-mail:317659965@qq com㊂串联式密炼机卸料门液压驱动系统设计与仿真张浩强(河池学院物理与机电工程学院,广西宜州546300)摘要:设计密炼机卸料门液压驱动系统,利用AMESim建立系统仿真模型并进行动态性能仿真,分析蓄能器充气压力和容积对密炼机卸料门开启时间的影响规律㊂仿真可得:所设计的液压驱动系统能在极短的时间内开启密炼机卸料门;蓄能器气囊压力增大或蓄能器气囊容积增大,密炼机卸料门开启时间均减小㊂关键词:串联式密炼机;卸料门液压驱动系统;AMESim仿真;开启时间中图分类号:V233 91㊀㊀文献标志码:A㊀㊀文章编号:1001-3881(2018)20-109-4DesignandSimulationonDischargeDoorHydraulicDriveSystemofTandemInternalMixerZHANGHaoqiang(SchoolofPhysicsandMechatronic&ElectronicEngineering,HechiUniversity,YizhouGuangxi546300,China)Abstract:Thedischargedoorhydraulicdrivesystemofinternalmixerwasdesigned.ThesimulationmodelwasestablishedbasedonAMESimandthedynamicperformancewassimulated.Theinfluencesofaccumulatorpressureandvolumeonopeningtimeofdis⁃chargedoorwereanalyzed.Thesimulationresultsshowthatthedesignedhydraulicdrivesystemcanopenthedischarginggateofinter⁃nalmixerinaveryshorttime;whentheaccumulatorpressureincreasesortheaccumulatorbladdervolumeincreases,theopeningtimeofthedischargingdoorreduces.Keywords:Tandeminternalmixer;Dischargedoorhydraulicdrivesystem;AMESimsimulation;Openingtime0㊀前言密闭式炼胶机(密炼机)主要用于轮胎的混炼,是橡胶企业重要炼胶设备之一[1-2]㊂彭志深等[3]用两个液压马达分别驱动旋转GK1 5N密炼机转子,实现了转子无极调速㊂栗晓华[4]对GK400N密炼机液压和润滑系统进行了分析㊂张燕等人[5]通过在液压控制系统中增加一套液压阀组,减小了旋转油缸油腔形成的真空㊂陈英[6]对X(S)M系列密炼机现有的转子端面密封液压系统进行了增压㊁增速和多缸同步控制技术设计㊂罗春雷等[7-8]采用样本曲线拟合的方法使仿真模型与实际系统性能最佳逼近,通过对仿真模型注入各类故障信息,进行故障仿真研究㊂密炼机的密炼室工作时压力很高,高压下物料易泄漏,因此必须配备专门的转子轴端密封装置防止物料外泄,常用锁紧油缸锁紧卸料门[9-10]㊂但在保证较好密封的情况下,又产生了新的问题:当需要排胶时,若不及时打开卸料门,密炼室的压力一旦超过设备的最高耐压,将产生巨大损失,因此一定程度下卸料门开启时间越短对密炼机安全运行极其重要㊂作者对密炼机卸料门液压驱动系统进行了全新的设计,主要利用蓄能器和二通插装阀加快锁紧液压缸快速动作,缩短密炼机卸料门开启卸料的时间,保证密炼机安全运行;利用AMESim仿真软件建立了卸料门液压驱动系统的仿真模型并进行了系统仿真研究,获得了液压缸活塞运动特性和蓄能器压力流量变化性能曲线,为卸料门液压驱动系统的进一步研究提供参考㊂1㊀密炼机卸料门液压驱动系统密炼机卸料门液压驱动系统如图1所示,主要由液控单向阀㊁二通插装阀㊁蓄能器㊁锁紧液压缸㊁机械杠杆锁紧装置组成,其工作原理分密封锁紧和快速卸料两个阶段介绍:(1)密封锁紧阶段㊂控制三位四通换向阀1DT㊁二位二通换向阀3DT得电,液压泵输出的液压油分别进入锁紧液压缸有杆腔㊁蓄能器和二通插装阀弹簧控制腔,锁紧液压缸缩回并通过机械杠杆锁紧装置将卸料门压紧,由于插装阀阀芯弹簧腔压力较高使其处于关闭状态,蓄能器储存液压油,待锁紧液压缸达到设定的压力值时,三位四通换向阀1DT失电,泵关闭,这样锁紧系统完全处于工作状态,蓄能器和液控单向阀为锁紧液压缸保压㊂(2)快速卸料㊂控制三位四通换向阀2DT,切断了蓄能器与插装阀弹簧腔的连通,插装阀弹簧腔与油箱连通泄压,二通插装阀开启,蓄能器经二通插装阀为锁紧液压缸无杆腔供液,此时锁紧液压缸处于差动连接,有杆腔的油液快速为无杆腔补液,这样锁紧液压杆快速伸出,通过机械杠杆锁紧装置使卸料门快速开启排胶㊂快速卸料阶段不需要控制泵的启动,也不需要控制三位四通换向阀工作,提高系统利用效率,节约了能源㊂图1㊀密炼机卸料门液压驱动系统而传统密炼机卸料门液压驱动系统中无二位四通换向阀㊁蓄能器和插装阀元件的,如图2所示,通过控制泵启停和三位四通换向阀换向实现卸料门的开启与关闭㊂图2㊀传统密炼机卸料门液压驱动系统2 仿真分析2 1㊀密炼机卸料门液压驱动系统仿真模型根据密炼机卸料门液压驱动系统原理,搭建系统AMESim仿真模型,如图3所示㊂图3㊀密炼机卸料门液压驱动系统仿真模型2 2㊀仿真参数设置参数设置如表1所示㊂表1㊀系统仿真初始参数模块标号参数名称参数值油缸质量块质量/kg30锁紧液压缸活塞直径/mm60活塞杆直径/mm35活塞行程/mm500安全阀开启压力/MPa30插装阀质量块质量/kg5.5位移/m0 0.03插装阀阀芯阀芯直径/mm35阀座通径/mm30插装阀弹簧腔直径/mm32弹簧刚度/(N㊃mm-1)10蓄能器气囊容积/L3充气压力/MPa7泵排量/(mL㊃r-1)200额定转速/(r㊃min-1)15002 3㊀系统仿真结果设置信号源一在0 45s为0(初始状态),45 50s为40(换向);设置信号源二在0 45s为-40(右位),45 50s为0(中位)进行仿真,得到图4和图5所示的锁紧液压缸活塞杆位移变化曲线以及图6所示的蓄能器气囊压力容积变化曲线㊂㊃011㊃机床与液压第46卷图4㊀锁紧液压缸活㊀㊀㊀㊀图5㊀锁紧液压缸活塞位移塞伸出位移图6㊀蓄能器压力容积曲线由图4 6可得锁紧液压缸活塞缩回耗时9 5s,蓄能器在0 40s处于储能阶段,40 45s处于保压阶段;45s时蓄能器开始为锁紧液压缸无杆腔提供油液,锁紧液压缸活塞迅速伸出,耗时约0 06s而传统密炼机卸料门开启完全依靠泵提供的液压油,活塞杆伸出时间t估算如下(q为泵排量mL/r,n为泵转速r/min):t=1000ˑπ4D2qn/60=1000ˑπ4ˑ0.0620.2ˑ1500/60=0.57s因此,该系统实现了密炼机的快速卸料排胶㊂(1)改变蓄能器充气压力进行仿真,得到充气压力对活塞位移的影响曲线和充气压力对气囊压力的影响,如图7 9所示㊂㊀㊀图7㊀充气压力对活塞㊀㊀㊀㊀㊀㊀㊀图8㊀充气压力对活塞位移的影响㊀㊀㊀㊀㊀㊀图9㊀充气压力对气囊压㊀位移的影响曲线局部放大力的影响㊀㊀由图7 9可得:随充气压力的增大,锁紧液压缸缩回的时间减小,伸出的时间减小,也即密炼机卸料门开启时间缩短㊂(2)改变气囊容积进行仿真分析,得到气囊容积对活塞位移的影响曲线和气囊容积对气囊压力的影响,如图9 11所示㊂㊀㊀图10㊀气囊容积对活塞㊀㊀㊀㊀㊀㊀㊀㊀图11㊀气囊容积对活塞位移的㊀㊀㊀㊀㊀㊀㊀图12㊀气囊容积对气囊㊀位移的影响影响曲线局部放大压力的影响㊀㊀由图10 12可得:随气囊容积的增大,锁紧液压缸缩回的时间延长,伸出的时间缩短,即密炼机卸料门开启时间减小㊂3㊀结论设计密炼机卸料门液压驱动系统,并阐述了系统原理;利用AMESim建立了系统仿真模型,并进行了系统动态仿真,研究了蓄能器充气压力和容积对卸料门液压驱动系统的影响㊂主要得到以下结论:㊀㊀(1)所设计的密炼机卸料门液压驱动系统能满足密炼机的快速卸料排胶要求㊂(2)蓄能器气囊压力增大或蓄能器气囊容积增大,密炼机卸料排胶时间均有所减小㊂参考文献:[1]李雄.GK型密炼机上顶栓液压系统性能仿真及控制策略研究[D].长沙:中南大学,2009.[2]宋宝玉.密炼机转子密封装置与故障排除实例[J].润滑㊃111㊃第20期张浩强:串联式密炼机卸料门液压驱动系统设计与仿真㊀㊀㊀与密封,2016,41(3):145-148.SONGBY.MixerRotorSealingDeviceandTroubleshootingExamples[J].LubricationEngineering,2016,41(3):145-148.[3]彭志深,林广.GK1.5N液压驱动式密炼机液压系统研究[J].橡塑技术与装备,2009,35(12):33-36.PENGZS,LING.StudyonHydraulicSystemforGK1.5NHydraulic⁃drivenInternalMixer[J].ChinaRubber/PlasticsTechnology&Equipment,2009,35(12):33-36.[4]栗晓华.GK400N密炼机液压和润滑系统分析[J].橡塑技术与装备,2007,33(6):43-52.LIXH.GK400NMixerHydraulicPressureandLubricationSystemAnalysis[J].ChinaRubber/PlasticsTechnology&Equipment,2007,33(6):43-52.[5]张燕,张祥.密炼机卸料门液压系统改造[J].橡胶工业,2009,56(10):620-622.ZHANGY,ZHANGX.ModificationoftheHydraulicSys⁃temofMixerDischargeDoor[J].ChinaRubberIndustry,2009,56(10):620-622.[6]陈英.密炼机转子端面密封装置增速及同步性能提升研究[J].机械研究与应用,2014,27(3):110-113.CHENY.ResearchontheSpeedIncreasingofMixerRotorFaceSealDeviceandSimultaneousPerformanceGrowth[J].MechanicalResearch&Application,2014,27(3):110-113.[7]罗春雷,邓强泉,李雄.密炼机上顶栓液压系统故障仿真研究[J].现代制造工程,2010(10):147-151.LUOCL,DENGQQ,LIX.FaultSimulationoftheRAM sHydraulicSystemofInterMixer[J].ModernManufacturingEngineering,2010(10):147-151.[8]罗春雷,李雄,邓强泉,等.利用AMEsim的密炼机上顶栓液压传动系统动态分析[J].现代制造工程,2010(9):135-139.LUOCL,LIX,DENGQQ,etal.TheFluidDrivingSys⁃tem sDynamicAnalysisofInterMixer sBasedonAMEsim[J].ModernManufacturingEngineering,2010(9):135-139.[9]孙庆伟,刘冰,崔浩森,等.GK密炼机油缸直接液压密封结构及关键件应力分析[J].橡塑技术与装备,2016(11):55-58.SUNQW,LIUB,CUIHS,etal.AnalysisofGKMixerHydraulicCylinderDirectsealStructureandKeyPartsofStress[J].ChinaRubber/PlasticsTechnologyandEquip⁃ment,2016(11):55-58.[10]朱志松,成亚云,刘静,等.密炼机上顶栓压力泵控系统研究[J].机床与液压,2017,45(4):142-145.ZHUZS,CHENGYY,LIUJ,etal.ResearchonPumpControlSystemforInternalmixerPistonPressureofMixer[J].MachineTool&Hydraulics,2017,45(4):142-145.(责任编辑:张艳君)(上接第124页)[11]CHOUXM,HOVLANDG.AdaptiveBacksteppingControlofNonlinearHydraulic⁃mechanicalSystemIncludingValveDynamics[J].Modeling,IdentificationandControl,2010,31(1):35.[12]CHOUXM,BLANKEM.FaultDiagnosisforNon⁃linearHydraulic-MechanicalDrillingPipeHandlingSystem[C]//ProceedingsofDecision&Control&EuropeanControlConference,2011:1620-1626.[13]CHOUXM,KARIMIHR,HOVLANDG,etal.RobustAdaptiveBacksteppingControlDesignforaNonlinearHydraulic⁃mechanicalSystem[C]//ProceedingsofIEEEConferenceonDecision&Control,2009:2460-2467.[14]SWAROOPD,HEDRICKJK,YIPPP,etal.DynamicSurfaceControlforaClassofNonlinearSystems[J].IEEETransactionsonAutomaticControl,2000,45(10):1893-1899.[15]JACKSONIRH.ConvergencePropertiesofRadialBasisFunctions[J].ConstructiveApproximation,1988,4(1):243-264.[16]CANUDAS-DE-WITC.Commentson ANewModelforControlofSystemswithFriction [J].IEEETransactionsonAutomaticControl,2002,43(8):1189-1190.[17]YUY,LIY,LIJ.ParameterIdentificationandSensitivityAnalysisofanImprovedLuGreFrictionModelforMagne⁃torheologicalElastomerBaseIsolator[J].Meccanica,2015,50(11):2691-2707.[18]KUMARBV,REDDYGM,MOHANDAST.IdentificationofSuitableProcessParametersforFrictionSurfacingofMildSteelwithAA6063AluminiumAlloy[J].TheInter⁃nationalJournalofAdvancedManufacturingTechnology,2014,74(1-4):433-443.[19]LINFJ,SHENPH,HSUSP.AdaptiveBacksteppingSlidingModeControlforLinearInductionMotorDrive[J].IEEProceedingsofElectricPowerApplications,2002,149(3):184-194.[20]TANY.NonlinearObserver/ControllerDesignandItsAppli⁃cationtoFrictionCompensation[D].UniversityofCalifor⁃nia,LosAngeles,2000.[21]GUORJ,DUS,YINHM.Slide⁃modeVariableStructureAdaptiveControlofElectro⁃hydraulicServoSystemsBasedonLuGreFrictionModel[J].AppliedMechanicsandMate⁃rials,2014,687-691:371-374.(责任编辑:张艳君)㊃211㊃机床与液压第46卷。
12MN锻造液压机本体设计说明书
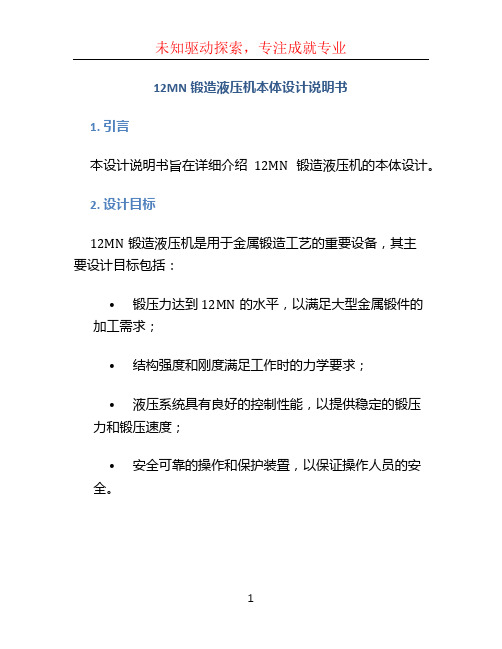
12MN锻造液压机本体设计说明书1. 引言本设计说明书旨在详细介绍12MN锻造液压机的本体设计。
2. 设计目标12MN锻造液压机是用于金属锻造工艺的重要设备,其主要设计目标包括:•锻压力达到12MN的水平,以满足大型金属锻件的加工需求;•结构强度和刚度满足工作时的力学要求;•液压系统具有良好的控制性能,以提供稳定的锻压力和锻压速度;•安全可靠的操作和保护装置,以保证操作人员的安全。
3. 设计方案3.1 结构设计12MN锻造液压机的本体采用框架结构,由上梁、下梁和立柱组成。
上下梁之间通过滑块连接,滑块上安装有锻模。
立柱采用矩形截面,以提供足够的强度和刚度。
3.2 液压系统设计液压系统是12MN锻造液压机的核心部件之一,其设计需满足以下要求:•锻压力的调节范围广,以满足不同锻件的加工要求;•快速响应的液压系统,以提供稳定的锻压力和锻压速度;•输油系统的过滤和冷却装置,以保证液压系统的可靠运行;•安全阀和溢流阀等安全保护装置,以防止超载和系统故障。
3.3 控制系统设计控制系统是12MN锻造液压机的核心之一,其设计需满足以下要求:•可编程控制器(PLC)作为控制核心,以实现自动化控制;•人机界面(HMI)提供直观的操作界面,以方便操作人员操作;•传感器用于采集锻压力、位移和温度等关键参数,以实时监测设备状态;•控制算法设计合理,以实现稳定的锻压力和锻压速度控制。
4. 实施方案本节将介绍12MN锻造液压机的具体实施方案。
4.1 结构实施根据设计方案,采用合适的材料和工艺对12MN锻造液压机进行结构实施。
首先制造上下梁和立柱,然后组装成框架结构。
最后进行加工和调整,以确保结构的强度和刚度。
4.2 液压系统实施根据设计方案,选择合适的液压元件和控制装置进行液压系统的实施。
对液压系统进行组装、连接和调试,以确保系统的正常运行。
4.3 控制系统实施根据设计方案,选择合适的控制器、传感器和人机界面进行控制系统的实施。
密炼机说明书
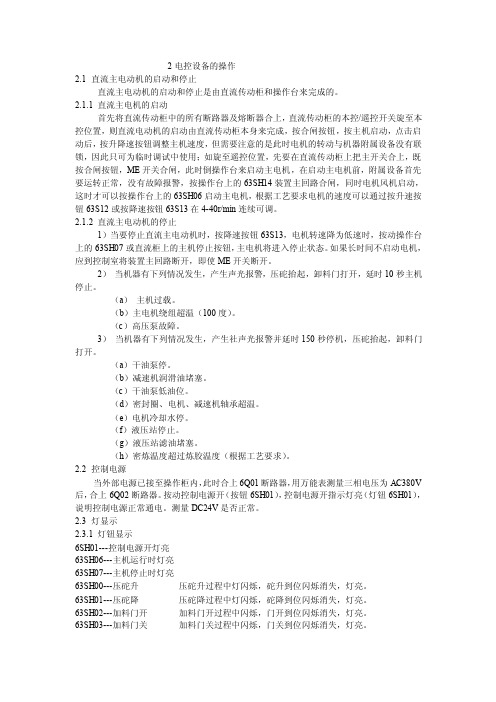
2电控设备的操作2.1 直流主电动机的启动和停止直流主电动机的启动和停止是由直流传动柜和操作台来完成的。
2.1.1 直流主电机的启动首先将直流传动柜中的所有断路器及熔断器合上,直流传动柜的本控/遥控开关旋至本控位置,则直流电动机的启动由直流传动柜本身来完成,按合闸按钮,按主机启动,点击启动后,按升降速按钮调整主机速度,但需要注意的是此时电机的转动与机器附属设备没有联锁,因此只可为临时调试中使用;如旋至遥控位置,先要在直流传动柜上把主开关合上,既按合闸按钮,ME开关合闸,此时倒操作台来启动主电机,在启动主电机前,附属设备首先要运转正常,没有故障报警,按操作台上的63SH14装置主回路合闸,同时电机风机启动,这时才可以按操作台上的63SH06启动主电机,根据工艺要求电机的速度可以通过按升速按钮63S12或按降速按钮63S13在4-40r/min连续可调。
2.1.2 直流主电动机的停止1)当要停止直流主电动机时,按降速按钮63S13,电机转速降为低速时,按动操作台上的63SH07或直流柜上的主机停止按钮,主电机将进入停止状态。
如果长时间不启动电机,应到控制室将装置主回路断开,即使ME开关断开。
2)当机器有下列情况发生,产生声光报警,压砣抬起,卸料门打开,延时10秒主机停止。
(a)主机过载。
(b)主电机绕组超温(100度)。
(c)高压泵故障。
3)当机器有下列情况发生,产生社声光报警并延时150秒停机,压砣抬起,卸料门打开。
(a)干油泵停。
(b)减速机润滑油堵塞。
(c)干油泵低油位。
(d)密封圈、电机、减速机轴承超温。
(e)电机冷却水停。
(f)液压站停止。
(g)液压站滤油堵塞。
(h)密炼温度超过炼胶温度(根据工艺要求)。
2.2 控制电源当外部电源已接至操作柜内,此时合上6Q01断路器,用万能表测量三相电压为AC380V 后,合上6Q02断路器。
按动控制电源开(按钮6SH01),控制电源开指示灯亮(灯钮6SH01),说明控制电源正常通电。
小型液压机:液压系统设计方案概述

小型液压机:液压系统设计方案概述1. 介绍本文件主要阐述了一款小型液压机的液压系统设计方案。
该方案旨在为小型液压机提供安全、稳定、高效的液压动力,以满足各种工业应用需求。
本文档将详细介绍液压系统的组成、工作原理、主要参数及应用范围。
2. 液压系统组成小型液压机的液压系统主要由以下几个部分组成:1. 液压泵:为整个液压系统提供动力来源,将液体从油箱吸入,然后高压输出至液压缸或液压马达。
2. 控制阀:控制液压系统的工作状态,包括方向、压力、流量等,确保系统按照预定的方式运行。
3. 液压缸/液压马达:将液压泵提供的压力能转化为机械能,完成各种工程任务。
4. 油箱:储存液压油,为液压系统提供充足的冷却和过滤。
5. 管路及连接件:连接液压系统的各个部分,确保液压油畅通无阻。
6. 传感器及监控系统:实时监测液压系统的运行状态,确保系统安全、稳定运行。
3. 工作原理小型液压机的液压系统工作原理如下:1. 启动液压泵,将液体从油箱吸入,经过过滤器过滤后,高压输出至控制阀。
2. 控制阀根据操作指令,调节液压系统的方向、压力、流量等参数,将液压油输送至液压缸或液压马达。
3. 液压缸或液压马达将液压油的压力能转化为机械能,完成各种工程任务。
4. 液压油回流至油箱,经过冷却和过滤,再次被液压泵吸入,形成循环。
5. 传感器及监控系统实时监测液压系统的运行状态,如压力、流量、温度等,确保系统安全、稳定运行。
4. 主要参数小型液压机液压系统的主要参数包括:1. 液压泵额定压力:根据液压机的工作需求,选择合适的液压泵额定压力。
2. 液压泵额定流量:确保液压泵在规定时间内提供足够的液压油。
3. 液压缸/液压马达额定功率:根据工程任务需求,选择合适的液压缸/液压马达额定功率。
4. 管路直径及长度:根据液压系统的压力损失和流量要求,合理设计管路直径及长度。
5. 控制阀规格:根据液压系统的需求,选择合适的控制阀规格,确保系统稳定运行。
X(S)M-1全液压式实验密炼机加料、压料及传动部分的设计

前言在19世纪初期开始,胶料的塑炼和混炼主要靠开炼机来实现.由于开炼机塑炼混炼胶料存在质量差、效率低、劳动强度工作环境恶劣等一系列问题。
为了克服这一系列的问题密炼机慢慢出现。
随着高分子材料的飞速发展和科学技术的不断进步,密炼机的用途越来越广泛,主要用于橡胶的塑炼及混炼,还可以用于塑料、沥青等其它高分子材料的混合以及橡塑共混等,由于其独特的优越性,已经成为橡塑工业中最关键的混炼设备之一。
自密炼机产生以后,在混炼过程中显示了它一系列的优点:混炼时间短,生产效率高,操作容易,较好的克服粉尘飞扬,减少配合剂的损失,改善劳动条件,减轻劳动强度等。
随着科技的进步,人们对橡胶混炼的要求越来越高,迫切要求对原来的旧机台进行更新换代,对旧的密炼机技术进行提高和完善。
随着世界橡胶工业的全面复苏及轮胎工业的全面崛起,于是密炼机正向着密炼室容量大型化、主电机大功率,转子转速高速化,多级化或无级化的方向发展。
一种作为研制开发作用的小型实验密炼机的出现势在必行,其为各种密炼机的发展演示起着至关重要的作用。
X(S)M-1全液压式实验密炼机就是顺应密炼机发展,功能演示的一种高性能的密炼机。
其具有橡塑共混,同步高速转子转动,尺寸比较小结构比较紧凑,主要适用于实验室等良好的环境的场合下,尺寸结构简洁、经济、实用的众多优点。
本设计总结了X(S)M-1全液压式实验密炼机的设计过程,设计方法和设计理论依据,设计机台的优缺点。
本说明书主要介绍了X(S)M-1全液压式实验密炼机的加料压料装置、传动装置设计计算,还有有关的技术说明。
本设计力求使机台性能达到同类机台的先进水平。
希望所设计的机台既能准确完成既定的工艺生产要求,又能使机台强度、刚度、耐磨性、寿命等可靠。
并注意汲取先前的经验,注意创新改进,使机台结构简单,外形美观,且能提高生产率和降低能耗,另外,还要考虑加工成本和维修方便等。
机械设计的一般过程:1)明确设计任务,制定设计任务书。
2)提供方案并进行评价。
液压系统设计说明书
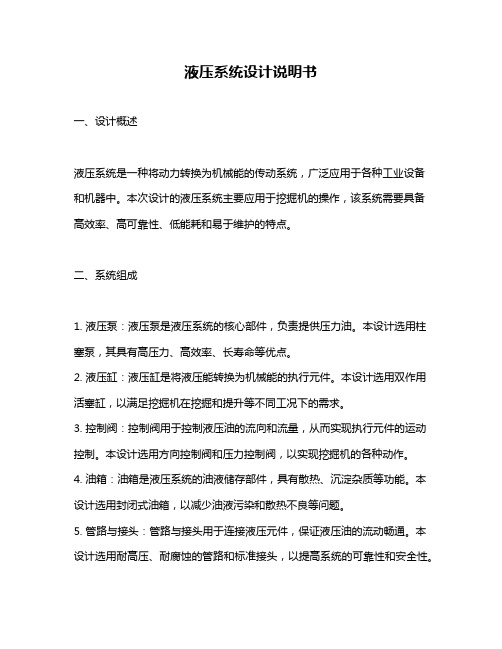
液压系统设计说明书一、设计概述液压系统是一种将动力转换为机械能的传动系统,广泛应用于各种工业设备和机器中。
本次设计的液压系统主要应用于挖掘机的操作,该系统需要具备高效率、高可靠性、低能耗和易于维护的特点。
二、系统组成1. 液压泵:液压泵是液压系统的核心部件,负责提供压力油。
本设计选用柱塞泵,其具有高压力、高效率、长寿命等优点。
2. 液压缸:液压缸是将液压能转换为机械能的执行元件。
本设计选用双作用活塞缸,以满足挖掘机在挖掘和提升等不同工况下的需求。
3. 控制阀:控制阀用于控制液压油的流向和流量,从而实现执行元件的运动控制。
本设计选用方向控制阀和压力控制阀,以实现挖掘机的各种动作。
4. 油箱:油箱是液压系统的油液储存部件,具有散热、沉淀杂质等功能。
本设计选用封闭式油箱,以减少油液污染和散热不良等问题。
5. 管路与接头:管路与接头用于连接液压元件,保证液压油的流动畅通。
本设计选用耐高压、耐腐蚀的管路和标准接头,以提高系统的可靠性和安全性。
三、系统特点1. 高效率:本设计采用高效率的柱塞泵,可有效降低能量损失,提高系统效率。
2. 高可靠性:选用高质量的液压元件和管路,采用标准化的连接方式,提高了系统的可靠性和稳定性。
3. 低能耗:通过优化液压元件的参数和系统布局,降低能耗,符合绿色环保要求。
4. 易于维护:采用模块化设计,便于拆卸和维修;同时,选用易于购买的标准件,降低了维护成本。
四、系统控制本设计的液压系统采用手动控制和自动控制相结合的方式。
手动控制主要用于初次的设备调试和应急情况下的操作;自动控制则根据预设的程序,自动完成挖掘机的各种动作。
在自动控制中,还引入了传感器和电液比例阀等智能控制元件,以提高控制的精度和响应速度。
五、系统安全为确保系统的安全运行,采取了以下措施:1. 设置溢流阀和减压阀等安全保护装置,防止过载和压力过高对系统造成损坏;2. 在油箱中设置液位计和温度计,实时监测油液的液位和温度,防止油液不足或温度过高对系统造成影响;3. 在管路中设置过滤器,防止杂质进入系统对元件造成损坏;4. 设置报警装置,当系统出现异常情况时,及时发出报警信号并切断电源,确保设备和人员的安全。
GK400型密炼机液压系统的分析与改进

GK400型密炼机液压系统的分析与改进文章以GK400密炼机为研究对象,对密炼机的液压系统进行具体分析,设计分析完成的液压系统具有以下特点:先进液压系统、方便维护、备件易于采购、利于生产,努力使文章对密炼机的液压系统选型和生产有所帮助。
希望通过对本课题的设计和研究,为以后在社会生产实践中打下坚实的理论和实践基础。
标签:密炼机;液压系统;主泵组1 引言密炼机是在开炼机的基础上发展起来的一种高强度间隙性的混炼设备,主要用于塑料的混炼及其它物料的混合等。
密炼机的技术进步主要表现在下述三个方面:(1)向大功率、大容量和高转速发展功率从几十千瓦到1000KW、2000KW甚至更高,同时也从一个电机驱动发展到两个电机驱动。
容量从几L、几十L,发展到了270L、320L、400L甚至更高,转子速度从原来的20r/min、40r/min、60r/min,到目前已发展到80r/min,甚至80r/min以上,同时有的密炼机由直流电机驱动,可任意调节其转速与速比。
(2)系列化、联动化和自动化(3)完善、提高和创新匹配了取料比较准确、工作比较可靠的上辅机;下辅机由螺杆连续补充混炼压片设备取代了开炼机,并由双螺杆的下辅机逐步取代单螺杆的下辅机;各种构型的转子及其相对应的密炼机不断涌现,如销钉转子密炼机、同步转子密炼机以及可调距转子密炼机等等;由液压驱动上顶栓取代了风压驱动上顶栓;由计算机的全自动监控操作取代了手动和半自动操作。
2 GK400型密炼机液压系统分析2.1 GK400型密炼机液压系统工作原理分析上顶栓部分:主要用来做压砣的升降控制和炼胶时压胶力的平稳性控制。
油源部分:主要用来给系统供压力油。
加料门部分:控制加料口开关,给密炼腔加如胶料。
卸料门部分:控制卸料口的开关,以达到卸料的目的。
锁紧块部分:控制锁紧快的伸出和缩回,以达到锁紧和松开卸料门的目的。
2.2 原液压系统在实际使用中存在问题蓄能器容量和压力等级不匹配,工作极不稳定,胶囊易损坏,不能稳定保持系统压力,造成磁组电接点压力表及先导溢流阀长时间处于工作状态,缩短其寿命。
密炼机液压系统设计说明

目录内容提要 (3)ABSTRACT (4)1引言 (5)1.1 课题提出的背景和意义 (5)1.2国内外研究开发水平和发展趋势 (6)1.3课题研究目标 (9)2液压系统的要求 (10)3液压原理和主要技术参数 (11)4 液压系统方案的设计 (12)4.1确定工作压力 (12)4.2拟定液压系统原理图 (12)5 液压缸的设计计算 (15)5.1销锁油缸和旋转油缸的设计计算说明 (15)5.2加料门油缸和转子密封油缸设计说明 (17)6液压元件的选择和专用件的设计 (21)6.1液压泵的选择和泵的参数的计算 (21)6.2电动机的选择 (22)6.3液压控制阀的选择..... (22)6.4其他液压元件的选择 (24)6.5蓄能器的设计计算 (25)6.6确定油箱的有效容积 (26)6.7管道尺寸的确定 (26)7液压系统性能验算 (28)7.1验算回路中的压力损失 (28)7.2液压系统的发热温升的计算 (29)8设计液压装置 (34)8.1液压装置总体布局 (34)8.2液压阀的配置形式 (34)8.3集成块的设计 (34)8.4绘制正式工作图 (35)9密炼机液压系统使用、维护说明书 (36)9.1液压系统组成和控制方式 (36)9.2液压系统安装及调试 (39)9.3液压系统的维护及注意事项 (40)9.4日常维护要求 (41)9.5常见液压故障处理办法 (42)9.6主要元件 (44)9.7易损件 (46)结论 (47)致谢 (48)参考文献 (49)附录: 1 英文原著2 英文翻译3 设计图纸内容提要本文主要讲述了密炼机液压系统的设计,其中包括系统参数的设计、油缸的计算、系统的性能验算以及系统的使用说明。
该系统主要用于密炼机的液力装置,控制各工作点油缸动作,由于该系统配置有电接点温度计(WSSX)、压力继电器(HED10A20)、电磁阀、溢流阀、安全阀等,因此可对系统的油液温度、系统压力等实现远程监控,其结构设计紧凑、操作方便、性能可靠、节约能源是密炼机液力装置的理想配套液压设备。
液压系统的课程设计说明书
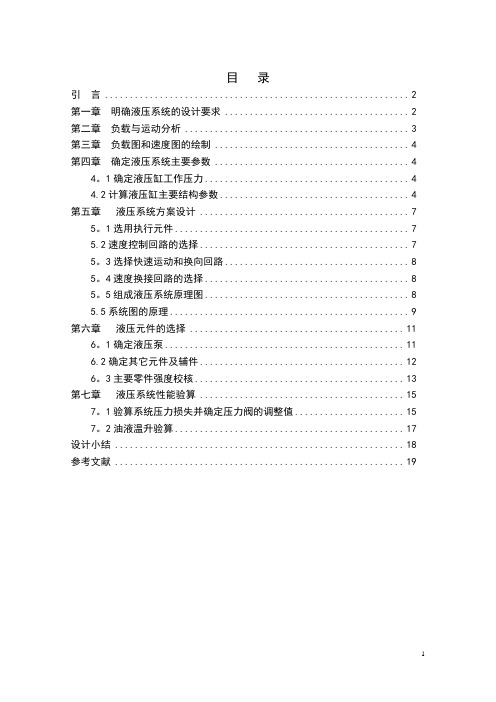
目录引言 (2)第一章明确液压系统的设计要求 (2)第二章负载与运动分析 (3)第三章负载图和速度图的绘制 (4)第四章确定液压系统主要参数 (4)4。
1确定液压缸工作压力 (4)4.2计算液压缸主要结构参数 (4)第五章液压系统方案设计 (7)5。
1选用执行元件 (7)5.2速度控制回路的选择 (7)5。
3选择快速运动和换向回路 (8)5。
4速度换接回路的选择 (8)5。
5组成液压系统原理图 (8)5.5系统图的原理 (9)第六章液压元件的选择 (11)6。
1确定液压泵 (11)6.2确定其它元件及辅件 (12)6。
3主要零件强度校核 (13)第七章液压系统性能验算 (15)7。
1验算系统压力损失并确定压力阀的调整值 (15)7。
2油液温升验算 (17)设计小结 (18)参考文献 (19)引言液压系统已经在各个部门得到越来越广泛的应用,而且越先进的设备,其应用液压系统的部门就越多.液压传动是用液体作为来传递能量的,液压传动有以下优点:易于获得较大的力或力矩,功率重量比大,易于实现往复运动,易于实现较大范围的无级变速,传递运动平稳,可实现快速而且无冲击,与机械传动相比易于布局和操纵,易于防止过载事故,自动润滑、元件寿命较长,易于实现标准化、系列化。
液压传动的基本目的就是用液压介质来传递能量,而液压介质的能量是由其所具有的压力及力流量来表现的。
而所有的基本回路的作用就是控制液压介质的压力和流量,因此液压基本回路的作用就是三个方面:控制压力、控制流量的大小、控制流动的方向。
所以基本回路可以按照这三方面的作用而分成三大类:压力控制回路、流量控制回路、方向控制回路。
第一章明确液压系统的设计要求要求设计一台卧式单面多轴钻孔组合机床动力滑台的液压系统.要求实现的动作顺序为:启动→快进→工进→快退→停止。
液压系统的主要参数与性能要求如下:轴向切削力Ft =20000N,移动部件总质量G=10000N;快进行程l1=100mm,工进行程l2=50mm。
一种密炼机液压站上顶栓控制装置的制作方法
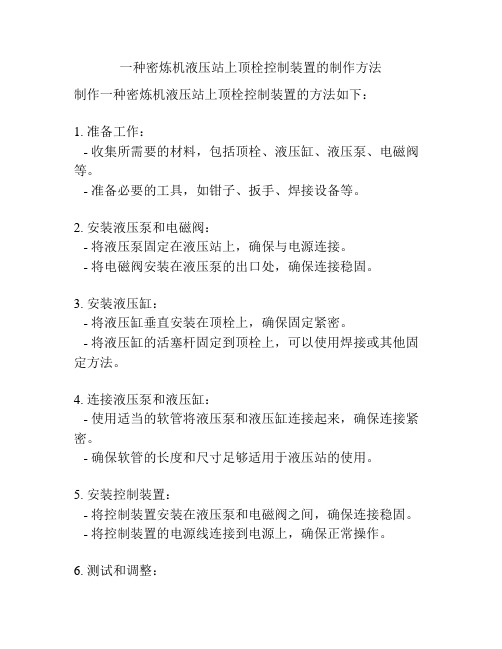
一种密炼机液压站上顶栓控制装置的制作方法
制作一种密炼机液压站上顶栓控制装置的方法如下:
1. 准备工作:
- 收集所需要的材料,包括顶栓、液压缸、液压泵、电磁阀等。
- 准备必要的工具,如钳子、扳手、焊接设备等。
2. 安装液压泵和电磁阀:
- 将液压泵固定在液压站上,确保与电源连接。
- 将电磁阀安装在液压泵的出口处,确保连接稳固。
3. 安装液压缸:
- 将液压缸垂直安装在顶栓上,确保固定紧密。
- 将液压缸的活塞杆固定到顶栓上,可以使用焊接或其他固定方法。
4. 连接液压泵和液压缸:
- 使用适当的软管将液压泵和液压缸连接起来,确保连接紧密。
- 确保软管的长度和尺寸足够适用于液压站的使用。
5. 安装控制装置:
- 将控制装置安装在液压泵和电磁阀之间,确保连接稳固。
- 将控制装置的电源线连接到电源上,确保正常操作。
6. 测试和调整:
- 打开液压泵和控制装置的电源,进行测试和调整。
- 检查液压缸能否顺利地控制顶栓的运动,需要确保操作稳定和灵活性。
以上就是制作一种密炼机液压站上顶栓控制装置的方法。
需要注意安全操作,并根据实际情况调整步骤。
如若不懂,建议咨询专业技术人员或相关技术支持。
- 1、下载文档前请自行甄别文档内容的完整性,平台不提供额外的编辑、内容补充、找答案等附加服务。
- 2、"仅部分预览"的文档,不可在线预览部分如存在完整性等问题,可反馈申请退款(可完整预览的文档不适用该条件!)。
- 3、如文档侵犯您的权益,请联系客服反馈,我们会尽快为您处理(人工客服工作时间:9:00-18:30)。
目录内容提要 (3)ABSTRACT (4)1引言 (5)1.1 课题提出的背景和意义 (5)1.2国内外研究开发水平和发展趋势 (6)1.3课题研究目标 (9)2液压系统的要求 (10)3液压原理和主要技术参数 (11)4 液压系统方案的设计 (12)4.1确定工作压力 (12)4.2拟定液压系统原理图 (12)5 液压缸的设计计算 (15)5.1销锁油缸和旋转油缸的设计计算说明 (15)5.2加料门油缸和转子密封油缸设计说明 (17)6液压元件的选择和专用件的设计 (21)6.1液压泵的选择和泵的参数的计算 (21)6.2电动机的选择 (22)6.3液压控制阀的选择..... (22)6.4其他液压元件的选择 (24)6.5蓄能器的设计计算 (25)6.6确定油箱的有效容积 (26)6.7管道尺寸的确定 (26)7液压系统性能验算 (28)7.1验算回路中的压力损失 (28)7.2液压系统的发热温升的计算 (29)8设计液压装置 (34)8.1液压装置总体布局 (34)8.2液压阀的配置形式 (34)8.3集成块的设计 (34)8.4绘制正式工作图 (35)9密炼机液压系统使用、维护说明书 (36)9.1液压系统组成和控制方式 (36)9.2液压系统安装及调试 (39)9.3液压系统的维护及注意事项 (40)9.4日常维护要求 (41)9.5常见液压故障处理办法 (42)9.6主要元件 (44)9.7易损件 (46)结论 (47)致谢 (48)参考文献 (49)附录: 1 英文原著2 英文翻译3 设计图纸内容提要本文主要讲述了密炼机液压系统的设计,其中包括系统参数的设计、油缸的计算、系统的性能验算以及系统的使用说明。
该系统主要用于密炼机的液力装置,控制各工作点油缸动作,由于该系统配置有电接点温度计(WSSX)、压力继电器(HED10A20)、电磁阀、溢流阀、安全阀等,因此可对系统的油液温度、系统压力等实现远程监控,其结构设计紧凑、操作方便、性能可靠、节约能源是密炼机液力装置的理想配套液压设备。
其主要特点是:当主机超载时,本系统可自动进入浮动状态;该系统采用多种措施来实现加料门开、关动作的缓冲,以减少对液压系统和机械设备的冲击。
ABSTRACTThis document talks about the hydraulic system design of the Close Rubber Extrusion Machine, it include the system parameter design、the calculation of the cylinder、the check of the system property and the using application of the system. This system is mainly used for control the cylinder motion at any working point in the hydraulic equipment of the close rubber extrusion machine, for it equipped with the electric connect thermometer (WSSX)、pressure relay (HED10A20)、solenoid valve、relief valve、safety valve and so on, it can far away control the oil temperature、system pressure, and it also has the priority of good structure、convenient operation、reliable property、less energy consuming and so on. The main characteristics is : it can automatic go into the floating state when it over loading; the system employs many measures in order to buffer feed door’s impact.1引言1.1 课题提出的背景和意义我国液压工业发展历程,大致可分为三个阶段,即:20世纪50年代初到60年代初为起步阶段;60~70年代为专业化生产体系成长阶段;80~90年代为快速发展阶段。
其中,液压工业于50年代初从机床行业生产仿苏的磨床、拉床、仿形车床等液压传动起步,液压元件由机床厂的液压车间生产,自产自用。
进入60年代后,液压技术的应用从机床逐渐推广到农业机械和工程机械等领域,原来附属于主机厂的液压车间有的独立出来,成为液压件专业生产厂。
到了60年代末、70年代初,随着生产机械化的发展,特别是在为第二汽车制造厂等提供高效、自动化设备的带动下,液压元件制造业出现了迅速发展的局面,一批中小企业也成为液压件专业制造厂。
1968年中国液压元件年产量已接近20万件;1973年在机床、农机、工程机械等行业,生产液压件的专业厂已发展到100余家,年产量超过100万件,一个独立的液压件制造业已初步形成。
这时,液压件产品已从仿苏产品发展为引进技术与自行设计相结合的产品,压力向中、高压发展,并开发了电液伺服阀及系统,液压应用领域进一步扩大。
进入80年代,在国家改革开放的方针指引下,随着机械工业的发展,基础件滞后于主机的矛盾日益突出,并引起各有关部门的重视。
为此,原一机部于1982年组建了通用基础件工业局,将原有分散在机床、农业机械、工程机械等行业归口的液压专业厂,统一划归通用基础件局管理,从而使该行业在规划、投资、引进技术和科研开发等方面得到基础件局的指导和支持。
从此进入了快速发展期,先后引进了60余项国外先进技术,其中液压40余项,经消化吸收和技术改造,现均已批量生产,并成为行业的主导产品。
近年来,行业加大了技术改造力度,1991~1998年国家、地方和企业自筹资金总投入共约20多亿元,其中液压16亿多元。
经过技术改造和技术攻关,一批主要企业技术水平进一步提高,工艺装备得到很大改善,为形成高起点、专业化、批量生产打下了良好基础。
近几年,在国家多种所有制共同发展的方针指引下,不同所有制的中小企业迅猛崛起,呈现出勃勃生机。
随着国家进一步开放,三资企业迅速发展,对提高行业水平和扩大出口起着重要作用。
目前我国已和美国、日本、德国等国著名厂商合资或由外国厂商独资建立了柱塞泵/马达、行星减速机、转向器、液压控制阀、液压系统、静液压传动装置、液压件铸造、机械密封、橡塑密封等类产品生产企业50多家,引进外资2亿多美元。
1.2国内外研究开发水平和发展趋势1.2.1国内外开发水平(1) 基本概况经过40多年的努力,我国液压行业已形成了一个门类比较齐全,有一定生产能力和技术水平的工业体系。
据1995年全国第三次工业普查统计,我国液压工业乡及乡以上年销售收入在100万元以上的国营、村办、私营、合作经营、个体、“三资”等企业约有700余家,其中液压700家。
按1996年国际同行业统计,我国液压行业总产值23.48亿元,占世界第6位。
(2) 当前供需概况通过技术引进,自主开发和技术改造,高压柱塞泵、齿轮泵、叶片泵、通用液压阀门、油缸和各类密封件第一大批产品的技术水平有了明显的提高,并可稳定的批量生产,为各类主机提高产品水平提供了保证。
另外,在液压元件和系统的CAD、污染控制、比例伺服技术等方面也取得一定成果,并已用于生产。
目前,液压产品总计约有1200个品种、10000多个规格。
已基本能适应各类主机产品的一般需要,为重大成套装备的品种配套率也可达60%以上,并开始有少量出口。
1998年国产液压件产量480万件,销售额约28亿元;密封件产量约8亿件,销售额约10亿元。
据中国液压气动密封件工业协会1998年年报统计,液压产品产销率为97 .5%,密封为98.7%。
这充分反映了产销基本衔接。
我国液压业虽取得了很大的进步,但与主机发展需求,以及和世界先进水平相比,还存在不少差距,主要反映在产品品种、性能和可靠性等方面。
以液压产品为例,产品品种只有国外的1/3,寿命为国外的1/2。
为了满足重点主机、进口主机以及重大技术装备的需要,每年都有大量的液压、气动和密封产品进口。
据海关统计及有关资料分析,1998年液压、气动和密封件产品的进口额约2亿美元,其中液压约1.4亿美元,气动近0.3亿美元,密封约0.3亿美元,比1997年稍有下降。
按金额计,目前进口产品的国内市场占有率约为30%。
1998年国内市场液压件需求总量约600万件,销售总额近40亿元;气动件需求总量约500万件,销售总额7亿多元;密封件需求总量约11亿件,销售总额约13亿元。
由于液压传动具有体积小、操作灵活、输出功率大等优点;也可用简单的管路连接代替复杂的机械传动,因而在收割机和插秧机中得到了广泛关注和大量应用。
随着农业机械化的推广与普及,农机研究部门、主机生产厂家和农户对液压系统的认识程度也在不断的提高,他们不仅要求产品有低廉的价格,更要求有较高的品质、可靠的使用性能;作为农业机械推广重点之一的联合收割机、插秧机,其液压系统的配置通过液压件生产厂家近几年的探索与努力,在功能、可靠性、合理性等方面已取得了较大的突破。
集成、复合、大通径、多功能。
已成为新一代农机液压件的开发热点。
结构上的集成化便于安装布置;性能上的复合为用户提供了很大方便;通道的大而畅更有利于减少发热与能耗;产品的多功能与农业机械的发展与开创紧密相连。
作为液压件,曾经困扰着农业机械的应用与发展,劣质液压元件、配置不合理的液压系统曾一度充斥着农机市场。
由此这也成为了液压件生产厂家的一个攻关课题。
通过多年的探索与研究,农机液压件的整体配套水平已取得了一个飞跃,并逐步接近了发达国家水平。
比如说,带有复合功能的手控、电控的操纵系统替代了功能单一的分配阀,而且性能、功效在不断升级;此外,行走系统采用了静液压无级变速器(HST),大大提高了操纵性能与工作效率。
因此,我们必须按照客观规律去办事,不能守旧,一定要有创新,要有突破,相信,液压技术在农机上的应用将更普及一定会达到发达国家水平。
液压系统结构紧凑、重量轻、体积小、压力高、自吸性能好。
在液压系统的设计中,不但要实现其拖动与调节功能,还要尽可能地利用能量,达到高效、可靠运行的目的。
液压系统的功率损失会使系统的总效率下降、油温升高、油液变质,导致液压设备发生故障。
因此,设计液压系统时必须多途径地考虑降低系统的功率损失。