冷轧工艺教材武钢2
冷轧工艺教材-武钢2
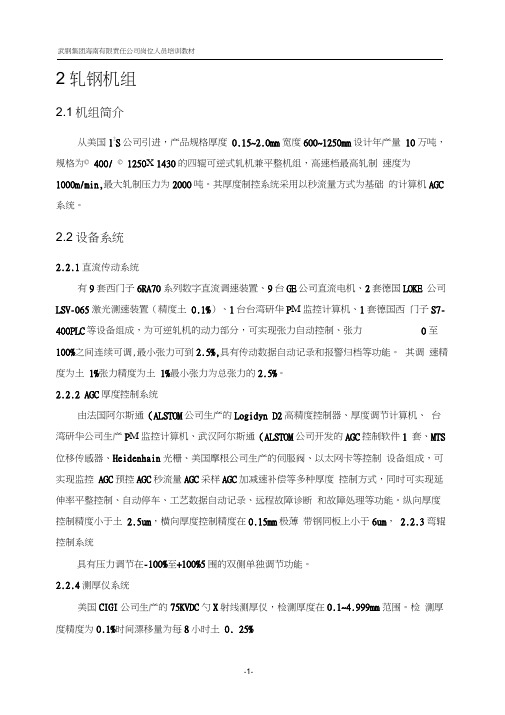
2轧钢机组2.1机组简介从美国l2S公司引进,产品规格厚度0.15~2.0mm宽度600~1250mm设计年产量10万吨,规格为© 400/ © 1250X 1430的四辊可逆式轧机兼平整机组,高速档最高轧制速度为1000m/min,最大轧制压力为2000吨。
其厚度制控系统采用以秒流量方式为基础的计算机AGC 系统。
2.2设备系统2.2.1直流传动系统有9套西门子6RA70系列数字直流调速装置、9台GE公司直流电机、2套德国LOKE 公司LSV-065激光测速装置(精度土0.1%)、1台台湾研华P M监控计算机、1套德国西门子S7-400PLC等设备组成,为可逆轧机的动力部分,可实现张力自动控制、张力0至100%之间连续可调,最小张力可到2.5%,具有传动数据自动记录和报警归档等功能。
其调速精度为土1%张力精度为土1%最小张力为总张力的2.5%。
2.2.2 AGC厚度控制系统由法国阿尔斯通(ALSTOM公司生产的Logidyn D2高精度控制器、厚度调节计算机、台湾研华公司生产P M监控计算机、武汉阿尔斯通(ALSTOM公司开发的AGC控制软件1 套、MTS 位移传感器、Heidenhain光栅、美国摩根公司生产的伺服阀、以太网卡等控制设备组成,可实现监控AGC预控AGC秒流量AGC采样AGC加减速补偿等多种厚度控制方式,同时可实现延伸率平整控制、自动停车、工艺数据自动记录、远程故障诊断和故障处理等功能。
纵向厚度控制精度小于土 2.5um,横向厚度控制精度在0.15mm极薄带钢同板上小于6um,2.2.3弯辊控制系统具有压力调节在-100%至+100%5围的双侧单独调节功能。
2.2.4测厚仪系统美国CIGI公司生产的75KVDC勺X射线测厚仪,检测厚度在0.1~4.999mm范围。
检测厚度精度为0.1%时间漂移量为每8小时土0. 25%2.2.5乳化液控制系统由美国公司生产的10个电子乳化液调节阀,实现工作辊和支撑辊的分段喷射冷却,可实现良好的板形控制;美国公司生产的磁过滤系统,过滤乳化液中的铁份,保证乳化液的灰份和清洁;由武钢科技公司最新引进的磁净化装置,可达控制铁离子范围小于50pmm226辅助控制系统由美国公司开发的触摸屏操作系统,可很好的实现无操作台操作,轧机的全部操作均可在计算机上完成。
武钢冷轧板表面_黑线_缺陷分析

表 1 缺陷处夹杂物成分及其化合物质量分数
Table 1 Compositions of defects
元素 Al Si Ca Ti Mn Fe O
wB/ % 7. 91 1. 28 0. 58 14. 33 4. 33 40. 43 31. 14
xB/ % 8. 62 1. 34 0. 42 8. 79 2. 32 21. 28 57. 22
第1期
彭其春等 :武钢冷轧板表面“黑线”缺陷分析
23
2. 2 “黑线”的微观形貌与成分 在“黑线”缺陷处取样 ,经打磨、抛光后在电镜下观
察(放大倍数为 500 倍) ,缺陷中间和缺陷边缘形貌如图 5 所示 ,缺陷中间夹杂物的呈明暗两种颜色 ,亮色形状 不规则 ,成岛状分布 ,被暗色包裹于其中。缺陷边缘有 大量的颗粒状残留物 ,主要是“亮色”和“暗色”两种颗 粒 ,亮色成星罗棋布状镶嵌于暗色夹杂物中间。
采用优质耐火材料和性能相适应的保护渣降低耐火材料被钢水冲刷的程度进一步增加保护渣对夹杂物的吸附强度在轧制过程中减少热轧板表面feo铁皮也是去除黑线缺陷的一个重要途径改善高温除鳞设备的除鳞效果选择合适的喷嘴和高压水的入射角采用合适的压力提高除鳞效果控制二次除鳞水的温度保持合适的水温al2o3tio2夹杂在热轧板上破碎后留在表面形成划痕或斑痕在轧制过程中热轧板上的氧化铁皮压入其中形成减少钢中al2o3tio2夹杂是减少冷轧板黑线缺陷最根本的方法
(a) 缺陷中间夹杂物颗粒 SEM 照片 ; (b) 能谱图 。 图 6 缺陷中间夹杂物 SEM 照片及能谱图 Fig. 6 SEM micrograph and EDS of defects
缺陷边缘处“亮色”颗粒尺寸在 5~25μm ,主要 是 含 Al2 O3 ( 491 28 %) 、MnO ( 211 07 %) 和 FeO (261 02 %) 的颗粒 ,见图 7 和表 2 。
冷轧工艺介绍
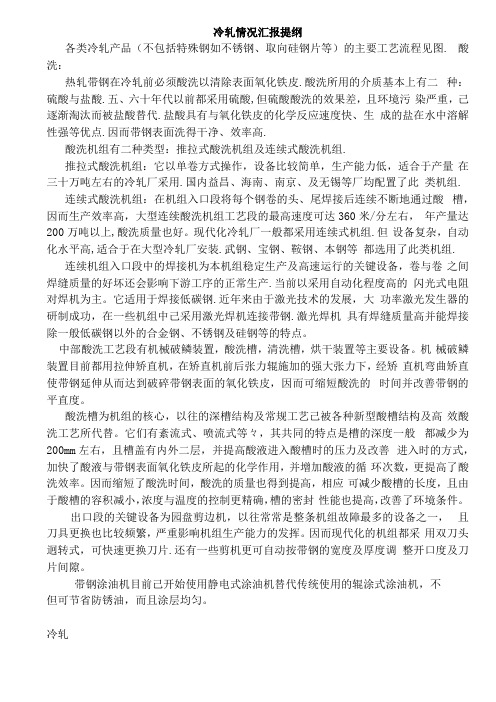
冷轧情况汇报提纲各类冷轧产品(不包括特殊钢如不锈钢、取向硅钢片等)的主要工艺流程见图. 酸洗:热轧带钢在冷轧前必须酸洗以清除表面氧化铁皮.酸洗所用的介质基本上有二种:硫酸与盐酸.五、六十年代以前都采用硫酸,但硫酸酸洗的效果差,且环境污染严重,己逐渐淘汰而被盐酸替代.盐酸具有与氧化铁皮的化学反应速度快、生成的盐在水中溶解性强等优点.因而带钢表面洗得干净、效率高.酸洗机组有二种类型:推拉式酸洗机组及连续式酸洗机组.推拉式酸洗机组:它以单卷方式操作,设备比较简单,生产能力低,适合于产量在三十万吨左右的冷轧厂采用.国内益昌、海南、南京、及无锡等厂均配置了此类机组.连续式酸洗机组:在机组入口段将每个钢卷的头、尾焊接后连续不断地通过酸槽,因而生产效率高,大型连续酸洗机组工艺段的最高速度可达360米/分左右,年产量达200万吨以上,酸洗质量也好。
现代化冷轧厂一般都采用连续式机组.但设备复杂,自动化水平高,适合于在大型冷轧厂安装.武钢、宝钢、鞍钢、本钢等都选用了此类机组.连续机组入口段中的焊接机为本机组稳定生产及高速运行的关键设备,卷与卷之间焊缝质量的好坏还会影响下游工序的正常生产.当前以采用自动化程度高的闪光式电阻对焊机为主。
它适用于焊接低碳钢.近年来由于激光技术的发展,大功率激光发生器的研制成功,在一些机组中己采用激光焊机连接带钢.激光焊机具有焊缝质量高并能焊接除一般低碳钢以外的合金钢、不锈钢及硅钢等的特点。
中部酸洗工艺段有机械破鳞装置,酸洗槽,清洗槽,烘干装置等主要设备。
机械破鳞装置目前都用拉伸矫直机,在矫直机前后张力辊施加的强大张力下,经矫直机弯曲矫直使带钢延伸从而达到破碎带钢表面的氧化铁皮,因而可缩短酸洗的时间并改善带钢的平直度。
酸洗槽为机组的核心,以往的深槽结构及常规工艺己被各种新型酸槽结构及高效酸洗工艺所代替。
它们有紊流式、喷流式等々,其共同的特点是槽的深度一般都减少为200mm左右,且槽盖有内外二层,并提高酸液进入酸槽时的压力及改善进入时的方式,加快了酸液与带钢表面氧化铁皮所起的化学作用,并增加酸液的循环次数,更提高了酸洗效率。
冷轧工艺教材武钢2
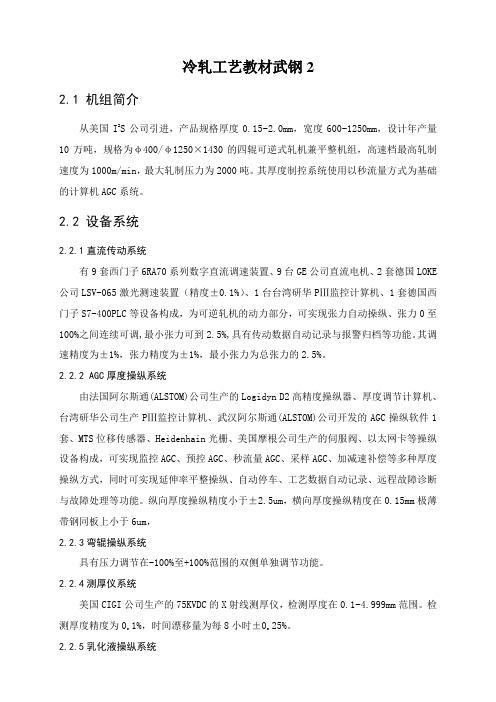
冷轧工艺教材武钢22.1 机组简介从美国I2S公司引进,产品规格厚度0.15~2.0mm,宽度600~1250mm,设计年产量10万吨,规格为φ400/φ1250×1430的四辊可逆式轧机兼平整机组,高速档最高轧制速度为1000m/min,最大轧制压力为2000吨。
其厚度制控系统使用以秒流量方式为基础的计算机AGC系统。
2.2 设备系统2.2.1直流传动系统有9套西门子6RA70系列数字直流调速装置、9台GE公司直流电机、2套德国LOKE 公司LSV-065激光测速装置(精度±0.1%)、1台台湾研华PⅢ监控计算机、1套德国西门子S7-400PLC等设备构成,为可逆轧机的动力部分,可实现张力自动操纵、张力0至100%之间连续可调,最小张力可到2.5%,具有传动数据自动记录与报警归档等功能。
其调速精度为±1%,张力精度为±1%,最小张力为总张力的2.5%。
2.2.2 AGC厚度操纵系统由法国阿尔斯通(ALSTOM)公司生产的Logidyn D2高精度操纵器、厚度调节计算机、台湾研华公司生产PⅢ监控计算机、武汉阿尔斯通(ALSTOM)公司开发的AGC操纵软件1套、MTS位移传感器、Heidenhain光栅、美国摩根公司生产的伺服阀、以太网卡等操纵设备构成,可实现监控AGC、预控AGC、秒流量AGC、采样AGC、加减速补偿等多种厚度操纵方式,同时可实现延伸率平整操纵、自动停车、工艺数据自动记录、远程故障诊断与故障处理等功能。
纵向厚度操纵精度小于±2.5um,横向厚度操纵精度在0.15mm极薄带钢同板上小于6um,2.2.3弯辊操纵系统具有压力调节在-100%至+100%范围的双侧单独调节功能。
2.2.4测厚仪系统美国CIGI公司生产的75KVDC的X射线测厚仪,检测厚度在0.1~4.999mm范围。
检测厚度精度为0.1%,时间漂移量为每8小时±0.25%。
轧钢热轧冷轧工艺介绍PPT学习教案课件
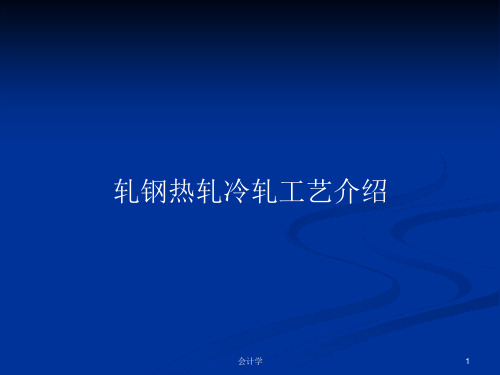
2)冷加工无缝钢管的生产方法 用冷加工方法生产无缝钢管主要有冷轧、冷拔和冷
旋压法。 3)焊管生产方法
焊管生产的实质是:将管坯(钢板或带钢)用不 同成型方法弯曲成所需要的钢管形状,然后用不同的 焊接方法将其焊接成钢管。
第39页/共41页
②电焊管生产 电焊管生产具有尺寸范围广、可以生产各种成分的钢管
连铸机
隧道式加热
结
炉
晶
器
摆动剪
精轧机
飞剪 除鳞箱 第33页/共41页
卷取机 层流冷却
② ISP工艺(Inline Strip Production )
ISP工艺,即在线热带生产工艺。 1992年1月在意大利的阿尔维迪 公司建成世界上第一条生产线,该类生产线是目前世界上最短的薄板坯 连铸连轧生产线。世界上已经建成5条。
宝钢5m轧机采用世界最先进工艺与设备,试 车成功。
第28页/共41页
(3)中厚板生产的工艺流程
原料
加热
除鳞
轧制
冷矫
冷床
热矫
层流冷却
冷床
剪切
喷印
包装
第29页/共41页
轧制
中厚板的轧制过程大致可分为粗轧和精轧。
(1)全纵轧法 当板坯宽度大于或等于钢板宽度时,即可不用展宽而直接纵轧成
成品。
(2)横轧-纵轧法或综合轧制法 先进行横轧将板坯展宽至所需宽度以后再转90°进行纵轧完成。
1)冷轧的含义 金属学说法:加工温度低于该钢种在特定变形条件下的再 结晶温度的压力加工称为“冷加工”;
工业上的习惯:坯料事先不经过再加热的常温轧制过
程。
2)冷轧的工艺特点 (1)冷轧中的加工硬化; (2)冷轧中的工艺冷却和润滑; (3)冷轧中的张力轧制。
冷轧热镀锌线立式活套控制分析
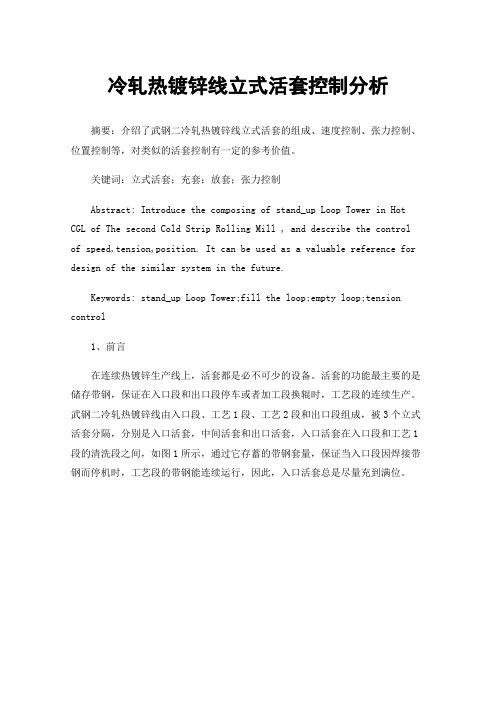
冷轧热镀锌线立式活套控制分析摘要:介绍了武钢二冷轧热镀锌线立式活套的组成、速度控制、张力控制、位置控制等,对类似的活套控制有一定的参考价值。
关键词:立式活套;充套;放套;张力控制Abstract: Introduce the composing of stand_up Loop Tower in Hot CGL of The second Cold Strip Rolling Mill , and describe the control of speed,tension,position. It can be used as a valuable reference for design of the similar system in the future.Keywords: stand_up Loop Tower;fill the loop;empty loop;tension control1、前言在连续热镀锌生产线上,活套都是必不可少的设备。
活套的功能最主要的是储存带钢,保证在入口段和出口段停车或者加工段换辊时,工艺段的连续生产。
武钢二冷轧热镀锌线由入口段、工艺1段、工艺2段和出口段组成,被3个立式活套分隔,分别是入口活套,中间活套和出口活套,入口活套在入口段和工艺1段的清洗段之间,如图1所示,通过它存蓄的带钢套量,保证当入口段因焊接带钢而停机时,工艺段的带钢能连续运行,因此,入口活套总是尽量充到满位。
图12、组成活套塔:型钢结构,带有位于上方的活套车、钢绳卷扬提升系统、下固定转向辊和平衡重,总能力约508 米带钢,工作能力480 米带钢;活套车:全行程约25.4 米,工作行程24 米,带可调节的导向轮,用于安放可移动的转向辊;钢绳卷扬提升系统:1 台变频马达,带绝对值编码器和测速马盘,用于钢绳卷扬的传动,带可转向的卷筒,用于卷取或开卷活套车的两根钢绳;2 台变频马达,用于张力补偿,安装在底部转向辊上;2根卷扬钢绳,带钢绳导轮,用于卷扬系统提升和降低活套车;转向辊:空心管结构,带安装在轴承座中的减摩擦轴承,直径1 000毫米 X 长度2400 毫米,10 根可移动的上转向辊,8 根固定的下转向辊,钢辊壳,表面镀铬,每个传动的转向辊上都有清洁设备;4 个配重:带钢绳,钢绳导轮和导向装置,用于平衡活套车,配重等于辊系重量;过载保护装置:安装在底部转向辊上,当带钢张力超限时该转向辊框架会被提升,释放张力,以保护活套塔框架结构;润滑:齿轮单元带飞溅润滑,转向辊采用集中干油润滑;纠偏辊单元:共3套,分别安装在底部入口侧、中间和出口侧的转向辊上,双纠偏单元,带液压对中控制系统,纠偏带钢到机组的中心;测张仪:安装在出口侧纠偏转向辊上,有两个压力传感器,传动侧、操作侧各1个,可水平或垂直方向测量压力,然后根据包角换算成张力;极限:空套快停1个,空套急停操作侧和传动侧各1个,满套快停1个,满套急停操作侧和传动侧各1个,监控钢绳断裂极限2个,同步校正极限1个,过载保护极限2个。
武科大轧制原理(二)讲课内容及思考题(1--2章)

轧制原理及工艺(二)教材:金属塑性加工学--轧制理论与工艺(第2、3版)王廷溥,齐克敏主编,(2002、2012)主要参考书:【1】板带生产原理与工艺王廷溥主编, 冶金工业出版社,1995.11【2】板带轧制工艺学【美】V.B 金兹伯格马东清等译,冶金工业出版社,1998 【3】中国热轧宽带钢轧机及生产技术中国金属学会热轧板带学术委员会编,冶金工业出版社,2002 【4】中厚板生产与质量控制崔风平等编,冶金工业出版社,2008【5】中厚钢板生产孙本荣等编,冶金工业出版社,1993【6】冷轧薄钢板生产傅作宝,冶金工业出版社,2005阅读国内刊物《钢铁》、《轧钢》《金属学报》、《特殊钢》等国内核心刊物;阅读英文刊物《Iron and Steel Engineer》《ISIJ International》《The Iron and Steel Institute》等国外刊物第一章板、带钢生产工艺绪论章节教学重点、难点教学重点•板、带材生产工艺特点、技术要求•板、带材轧制技术的发展演变过程•当前国内外板带材轧制技术的现状、特点、发展趋势教学难点板、带材生产工艺特点、技术要求1.1板带材分类1.2 板带材主要技术要求1.3板带材生产特点1.4 板带轧制技术的发展1.4.1围绕着降低金属变形阻力的演变发展1.4.2围绕改变应力状态、降低外阻的演变发展1.4.3在减少和控制轧机变形方向的发展1.4.4近代发展主要趋势和特点(略)第1章思考题1,推动板、带材轧制方法与轧机型式演变的主要矛盾是什么?2,板带材是如何分类的?3,板、带材生产工艺有何特点?4,板带材技术要求主要包含那些内容?第二章中厚板生产章节教学重点、难点教学重点•中厚板轧机型式及布置;•中厚板生产工艺流程;•中厚板轧制中平面形状控制技术;教学难点•中厚板轧制方法特点;中厚板轧制中平面形状控制技术;2.1轧机的型式及布置2.1.1型式2.1.2 布置2.2 中厚板生产工艺2.2.1 原料选择2.2.2加热2.2.3 轧制2.2.4轧后冷却2.3中厚板轧制中平面形状控制轧制2.3.1调整纵、横轧制比控制方法2.3.2调节形状控制方法第2章思考题1,中厚板粗轧阶段有哪几种常用轧制方式?各有何特点?2,为提高成材率, 中厚板轧制中可采用哪些平面形状控制技术?。
《冷轧专业培训》PPT课件

(2)提高机组和轧机的速度。以五机架轧机为例,20 世纪50 年代大都在20m/s 左 右,60 年代以来已逐步提高到30m/s 左右,最高轧制速度达37.5m/s。六机架冷连 轧机的最高轧制速度已超过了40m/s。但是,轧制速度的进一步提高会受到工艺润滑 材料与方式的限制。其他作业线(如单机架平整机组、双机架平整机组、各剪切机组 、连续热镀锌机组、酸洗机组、电镀锡机组等)的机组速度也都相应提高。
冷轧厂生产工艺
前言
针对冷轧生产的工艺流程及设备特点,为使新 入企人员及岗位调动人员在短时间内了解冷轧生产 的基本原理、熟悉冷轧工艺的生产流程、掌握上岗 必备基础知识,特编写了本教材。
目录
• 第一章 冷轧厂简介 • 第二章 冷轧厂工艺概况 • 第三章 酸洗工艺简介 • 第四章 轧制工艺简介 • 第五章 纵剪工艺简介 • 第六章 退火工艺简介 • 第七章 平整工艺简介
带钢基体 富氏体FeO 磁性体Fe3O4 氧化铁Fe2O
• 仔细观察带钢表面颜色会发现,往往带钢边部较宽度中间 部分颜色深些。这一现象是由于氧化铁皮的厚度不同而引 起光线的反射及干涉所致。随着氧化铁皮厚度的增大,颜 色逐渐由橙变成黄、绿、青、蓝、紫等。因此,由带钢表 面颜色及氧化铁皮的形状,大体可以判断出氧化铁皮的厚 度和均匀程度。
。四辊冷轧机按其轧辊运转方向可分为可逆式和不可逆式。 • 采用不可逆式四辊轧机进行单片生产时,轧制操作是由人工逐张将钢板
喂入轧机,全垛钢板轧完一道次后,用吊车将板垛吊送到轧机前,进行 下一道次的轧制,如此循环进行,直到轧成规定的成品尺寸时为止。
• 采用可逆式轧机时,则轧制操作有两种,一种是每一张钢板在轧机上往返轧 制,直到轧制成最终的成品尺寸,然后再进行第二张钢板的轧制。这种操作 方法虽然压下调整操作频繁,但产品表面不易划伤,故实际生产中应用较多 ,特别是轧制单重和尺寸较大的钢板,均采用此法。另一种是每张钢板逐张 送入轧机,待全垛钢板轧完一道次后,再逐张返回轧制第二道次。此种操作 方法使轧制产品尺寸较均一,而且省去了轧辊反转和压下的调整时间,从而 冷轧机产量较高,但板面之间有时可能造成划伤。
冷轧酸轧线培训教材

冷轧酸轧线培训教材酸洗-轧机联合⽣产线职⼯培训教材(⼯艺部分)编制:审核:⽬录第⼀章冷轧薄板⽣产的发展历史和前景⼀、冷轧薄板⽣产的发展历史 3⼆、我国冷轧薄板的现状 6三、我国冷轧薄板⽣产的发展⽅向 7第⼆章板带材分类及其轧制技术的原理⼀、带材分类 8⼆、轧制技术的原理 9第三章热轧薄板对冷轧钢板的影响⼀、钢的化学成分对成品性能的影响 12⼆、热轧带钢对冷轧钢板性能和组织的影响 13三、原料的⼏何尺⼨对冷轧成品的影响 15 第四章酸洗技术的发展及应⽤⼀、酸洗技术的发展 16⼆、酸洗机组的分类及特点 17三、酸洗机组主要单体设备 18四、盐酸酸洗⼯艺制度的制定 31 第五章冷轧板带轧制技术的特点与发展⼀、连轧过程的特点 32⼆、冷轧板带材⽣产的⼯艺特点 34三、轧制技术的发展 39四、轧机机组的主要单体设备 45五、轧制⼯艺制度 58 第六章板带材的⾼精度轧制和板形控制⼀、轧制缺陷 63⼆、板带轧制中的厚度控制 64三、横向厚差与板形控制技术 70第七章产品⼤纲、产品结构及主要设计技术经济指标⼀、产品⼤纲 77⼆、酸洗冷连轧区域主要设计技术经济指标 81三、原料 81四、主要⼯艺技术参数 83 第⼋章酸洗冷连轧⼯艺流程及过程叙述⼀、酸洗冷连轧⼯艺流程 88⼆、酸洗冷连轧⼯艺过程叙述 88第⼀章冷轧薄板⽣产的发展历史和前景⼀、冷轧薄板⽣产的发展历史钢的冷轧是在19世纪中叶始于德国,当时只能⽣产宽度20~25mm的冷轧带钢。
美国1859年建⽴了25mm冷轧机,1887年⽣产出宽度为150mm的低碳钢带。
1880年以后冷轧钢带⽣产在美国、德国发展很快,产品宽度不断扩⼤,并逐渐建⽴了附属设备,如剪切、矫直、平整和热处理设备等,产品质量也有了提⾼。
宽的冷轧薄板(钢带)是在热轧成卷带钢的基础上发展起来的。
⾸先是美国早在1920年第⼀次成功地轧制出宽带钢,并很快由单机架不可逆轧制⽽跨⼊单机架可逆式轧制。
1926年阿姆柯公司巴特勒⼯⼚建成四机架冷连轧机。
钢铁冷轧工艺概论课件

精整设备与操作
精整设备
包括矫直机、剪切机、表面处理设备等。
操作要点
通过矫直和剪切操作,去除钢材的弯曲和不平整部 分,并进行表面处理以满足客户需求。
注意事 项
精整过程中应关注设备运行状况,防止过度矫直和 剪切对钢材性能的影响。
04
冷轧产品的质量与性能
冷轧产品的质量标准与检测方法
质量标准
冷轧产品的质量标准主要包括厚度精度、表面质量、机械性能等方面。厚度精度要求严格,需控制在一定范围内; 表面质量要求无划痕、无锈蚀、无麻点等缺陷;机械性能要求抗拉强度、屈服强度、延伸率等符合标准要求。
检测方法
为确保冷轧产品质量,需采用多种检测方法进行检测。常用的检测方法包括厚度测量、表面检测、拉伸试验等。 厚度测量采用测厚仪进行测量,确保厚度精度符合要求;表面检测采用目视、金相显微镜等方法进行表面质量检 查;拉伸试验采用拉伸试验机进行机械性能测试。
冷轧产品的性能特点与应用领域
性能特点
冷轧产品具有高强度、良好的塑性和韧性、耐腐蚀等特点,广泛应用于汽车、 建筑、家电、航空航天等领域。
冷轧工艺的可持续发展路径与前景
节能减排
推广节能技术、优化工 艺流程,降低钢铁冷轧 过程中的能耗和污染物
排放。
循环经济
实现废钢、废铁等固体 废弃物的循环利用,减 少资源浪费和环境污染。
技术创新
加强科技创新,研发更 加环保、高效的钢铁冷
轧工艺技术和设备。
政策支持
政府应制定相关政策, 鼓励和支持钢铁冷轧企 业采取环保措施,推动
退火后的钢材应具有良好的塑 性和韧性,为后续加工提供良 好的材料基础。
精整
精整是冷轧工艺中的一道重要工序, 主要目的是进一步改善钢材的表面质 量和几何形状。
冷轧带钢生产的工艺流程ppt课件
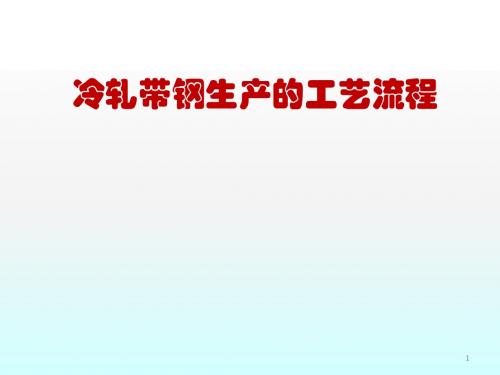
1-酸洗
2-冷轧
4-退火
6-检查
3-清洗
5-平整
17
再见
改造后 2 3
235 91 13.4
15
冷轧带钢生产的工艺流程
联合式全连续轧机
简介
全连轧机与前面的酸洗机组联合,即为酸洗联 合式全连轧机。
将单一全连轧 机再与其他生产工 序的机组联合,称 为联合式全连轧机 。
全连轧机与后面的连续退火机组联合,即为退 火联合式全连轧机;
16
冷轧带钢生产的工艺流程
全联合式全连续轧机
酸洗
→ 待轧 → 多机架连轧或单机架可逆式冷轧 → 罩式或连续式退火 ↓
入库 ← 包装 ← 横切分类或成卷 ← 平整
基本特点: 浅槽酸洗,多机架冷轧或单机架 可逆式轧制,热处理分罩式和连续式, 可单张包装,也可成卷包装。
11
冷轧带钢生产的工艺流程
⑷ 现代冷轧生产方法
酸洗 → 待轧 → 双卷双拆冷连轧机冷轧 → 罩式或连续式退火 → 平整
深冲板及热轧酸洗带卷生产工艺流程
涂镀层薄板生产工艺流程
4
冷轧带钢生产的工艺流程 不同产品冷轧薄钢板生产工艺流程
电工硅钢板生产工艺流程
不锈钢板生产工艺流程
5
冷轧带钢生产的工艺流程 二、冷轧带钢生产工艺的发展 1、冷轧车间工艺平面布置 2、冷轧钢板生产工艺的发展
6
冷轧带钢生产的工艺流程 1、冷轧带钢车间工艺平面布置
简介
全连轧机与前面 酸洗机组和后面连续 退火机组 (包括清洗 、退火、冷却、平整 、检查工序)全部联合 起来,即为全联合式 全连轧机。
பைடு நூலகம்
全联合式全连续轧机标志着冷轧板带设计、研究、生产、 控制及计算机技术已进入一个新的时代。为使整个机组能够 同步顺利生产,采用了先进的自动控制系统,板厚精度可以 控制在±1%以内。过去冷轧板带从投料到产出成品需12天, 而采用全联合式全连轧机只要20分钟。
冷轧新技术讲座PPT课件

2003.7
第11页/共103页
2. 钢板冷轧过程的特点
(4) 工序多,工艺复杂,综合性强
主要工序:焊接-酸洗-轧制-脱脂-退火
- 平整-剪切-矫直-镀层
技术综合:冶金、机械、控制、计算机
学科综合:力 学(轧制力、张力、应力分析)
化 学(酸洗、脱脂、涂层)
数 学(模型、公式、算法)
金属学(退火、织构、组织性能)
2003.7
第3页/共103页
1 我国冷轧钢板生产技术发展概况
我国代表性冷连轧机组的类型
年代 1978 1989 1990 1996 2001
厂家 武钢 宝钢 益昌 攀钢 宝钢
宽度/机架数 1700五机架 2030五机架 1220五机架 1220四机架 1550五机架
类型 4-h CVC PC HC UC
轧制力偏差
辊缝差(弹跳方程)
辊缝调节量 设定辊缝值 第29页/共103页
消除厚差
冷连轧机组的多AGC系统-功能
(2) 辊缝前馈AGC(GFF AGC)
第1机架采用辊缝前馈AGC。它是根据入口测厚仪测 得的入口带钢厚度偏差,通过控制液压压上调整辊缝 来消除带钢厚度偏差。
设定来料厚度
实测来料厚度
2003.7
卷
轧制-剪切-卷取
2003.7
板
退火-平整-分卷-包装-冷轧
退火-平整-横切-包装-冷轧板 退火-焊接-镀锌-剪切-镀锌
第15页/共103页
3. 冷连轧工艺及5.其冷新轧进产展品开发
2003.7
第16页/共103页
3. 冷连轧工艺及其新进展
带钢冷轧发展的 3 个阶段:
- 单机可逆轧制
- 连续式轧制(通常3-6个机架)
二次冷轧的特点及工艺要求
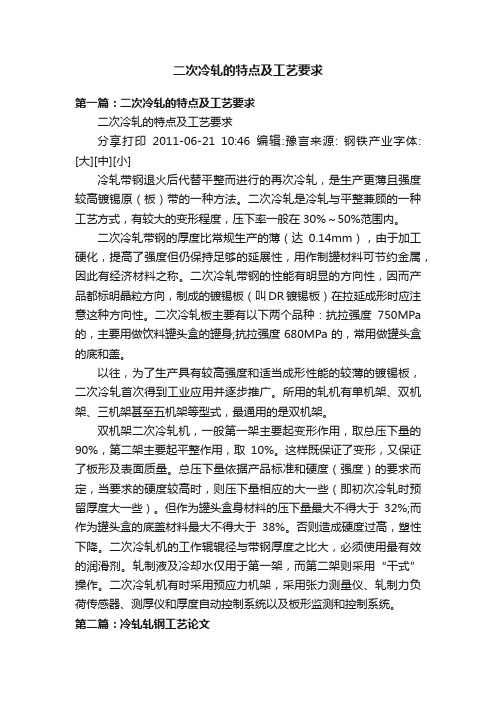
二次冷轧的特点及工艺要求第一篇:二次冷轧的特点及工艺要求二次冷轧的特点及工艺要求分享打印2011-06-21 10:46编辑:豫言来源: 钢铁产业字体: [大][中][小]冷轧带钢退火后代替平整而进行的再次冷轧,是生产更薄且强度较高镀锡原(板)带的一种方法。
二次冷轧是冷轧与平整兼顾的一种工艺方式,有较大的变形程度,压下率一般在30%~50%范围内。
二次冷轧带钢的厚度比常规生产的薄(达0.14mm),由于加工硬化,提高了强度但仍保持足够的延展性,用作制罐材料可节约金属,因此有经济材料之称。
二次冷轧带钢的性能有明显的方向性,因而产品都标明晶粒方向,制成的镀锡板(叫DR镀锡板)在拉延成形时应注意这种方向性。
二次冷轧板主要有以下两个品种:抗拉强度750MPa 的,主要用做饮料罐头盒的罐身;抗拉强度680MPa的,常用做罐头盒的底和盖。
以往,为了生产具有较高强度和适当成形性能的较薄的镀锡板,二次冷轧首次得到工业应用并逐步推广。
所用的轧机有单机架、双机架、三机架甚至五机架等型式,最通用的是双机架。
双机架二次冷轧机,一般第一架主要起变形作用,取总压下量的90%,第二架主要起平整作用,取10%。
这样既保证了变形,又保证了板形及表面质量。
总压下量依据产品标准和硬度(强度)的要求而定,当要求的硬度较高时,则压下量相应的大一些(即初次冷轧时预留厚度大一些)。
但作为罐头盒身材料的压下量最大不得大于32%;而作为罐头盒的底盖材料最大不得大于38%。
否则造成硬度过高,塑性下降。
二次冷轧机的工作辊辊径与带钢厚度之比大,必须使用最有效的润滑剂。
轧制液及冷却水仅用于第一架,而第二架则采用“干式”操作。
二次冷轧机有时采用预应力机架,采用张力测量仪、轧制力负荷传感器、测厚仪和厚度自动控制系统以及板形监测和控制系统。
第二篇:冷轧轧钢工艺论文冷轧轧钢工艺论文在轧钢(主要是冷轧)过程中,为了减小轧辊与轧材之间的磨擦力,降低轧制力和功率消耗,使轧材易于延伸,控制轧制温度,提高轧制产品质量,必须在轧辊和轧材接触面间加入润滑冷却液,这一过程就称为轧钢工艺润滑。
舞钢二炼钢炼钢系统基础学习知识资料
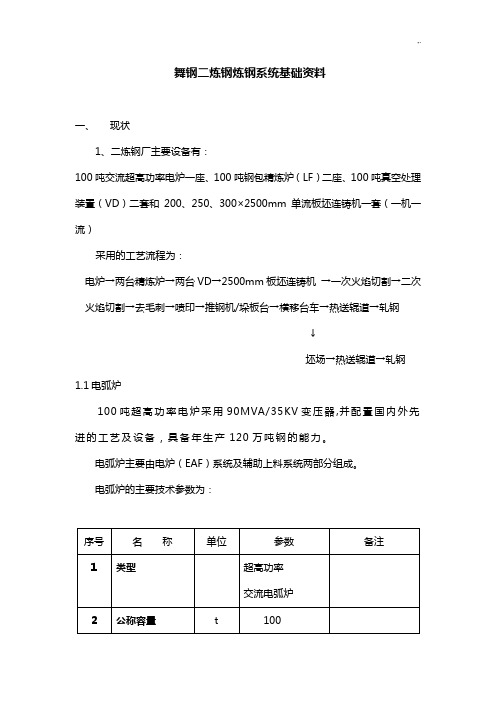
舞钢二炼钢炼钢系统基础资料一、现状1、二炼钢厂主要设备有:100吨交流超高功率电炉一座、100吨钢包精炼炉(LF)二座、100吨真空处理装置(VD)二套和200、250、300×2500mm单流板坯连铸机一套(一机一流)采用的工艺流程为:电炉→两台精炼炉→两台VD→2500mm板坯连铸机→一次火焰切割→二次火焰切割→去毛刺→喷印→推钢机/垛板台→横移台车→热送辊道→轧钢↓坯场→热送辊道→轧钢1.1电弧炉100吨超高功率电炉采用90MVA/35KV变压器,并配置国内外先进的工艺及设备,具备年生产120万吨钢的能力。
电弧炉主要由电炉(EAF)系统及辅助上料系统两部分组成。
电弧炉的主要技术参数为:1.2精炼炉精炼炉有2台,采用的是单盖双车的形式。
精炼炉主要分为三部分:机械组成部分、电气及自动化设备、辅助部分。
其主要技术参数为:1.3真空脱气装置(VD)真空脱气装置主要包括两部分:机械部分和电气部分。
真空脱气装置机械设备按功能(或所在工艺位置)划分为以下几个部分:VD处理站、真空泵系统(含冷却除尘;汽、水分配器)、机器冷却水系统、仪表氮气系统、氩气系统、液压系统等设备。
其核心设备(VD处理站和真空泵系统)的技术参数为:1.3.1 VD处理站VD处理站主要指钢液处理位置的设备。
它包括真空罐、真空罐盖、真空罐盖台车、罐盖升降液压系统、合金加料系统。
1.3.1.1 真空罐主要技术参数真空罐直径~Φ5800mm真空罐总高6850mm罐壁钢板厚度26mm罐底钢板厚度35mm密封圈材料硅橡胶或丁腈橡胶密封圈直径Φ50mm总重(不包括耐材)~68t(1套真空罐)1.3.1.2真空罐盖主要技术参数,.罐盖密封法兰外径Ф6150 mm盖高1730 mm防溅盖外径Φ3650 mm盖高1210 mm重量(不包括耐材)~4.0 t1.3.1.3罐盖台车主要技术参数轨道中心距7100mm轮距6000mm车轮直径Φ630mm台车走行距离16m台车走行速度2~12m/min(VVVF)定位精度±10mm油缸直径Φ200mm油缸行程1140mm罐盖提升速度~1m/min(可调)电缆拖链长度~12m宽度~1.0m弯曲半径~1.0m台车电机功率2×2.5 KW(带制动器)重量~28 t(1套罐盖台车)1.3.2 真空泵系统,.真空泵系统由抽气主管、移动弯头小车、气体冷却除尘器和真空泵及冷凝器等。
武钢二冷轧工程全面进入实施阶段

武钢二冷轧工程全面进入实施阶段
佚名
【期刊名称】《武钢技术》
【年(卷),期】2004(42)4
【总页数】1页(P27-27)
【关键词】武汉钢铁集团公司;工程建设;冷轧;轧钢
【正文语种】中文
【中图分类】TG33
【相关文献】
1.国网北京城区公司配网建设工程全面进入工程实施阶段 [J], ;
2.二冷轧建设进入工程实施阶段 [J],
3.通钢四平冷轧带钢项目进入全面实施阶段 [J],
4.安徽分行数据上收工程特别报道(二)已取得丰硕的阶段性成果进入全面攻坚阶段 [J],
5.深中通道全线桥梁桩基工程开钻桥梁工程建设进入全面实施阶段 [J], 林楚忠;因版权原因,仅展示原文概要,查看原文内容请购买。
- 1、下载文档前请自行甄别文档内容的完整性,平台不提供额外的编辑、内容补充、找答案等附加服务。
- 2、"仅部分预览"的文档,不可在线预览部分如存在完整性等问题,可反馈申请退款(可完整预览的文档不适用该条件!)。
- 3、如文档侵犯您的权益,请联系客服反馈,我们会尽快为您处理(人工客服工作时间:9:00-18:30)。
冷轧工艺教材武钢22.1 机组简介从美国I2S公司引进,产品规格厚度0.15~2.0mm,宽度600~1250mm,设计年产量10万吨,规格为φ400/φ1250×1430的四辊可逆式轧机兼平坦机组,高速档最高轧制速度为1000m/min,最大轧制压力为2000吨。
其厚度制控系统采纳以秒流量方式为基础的运算机AGC系统。
2.2 设备系统2.2.1直流传动系统有9套西门子6RA70系列数字直流调速装置、9台GE公司直流电机、2套德国LOKE 公司LSV-065激光测速装置(精度±0.1%)、1台台湾研华PⅢ监控运算机、1套德国西门子S7-400PLC等设备组成,为可逆轧机的动力部分,可实现张力自动操纵、张力0至100%之间连续可调,最小张力可到2.5%,具有传动数据自动记录和报警归档等功能。
其调速精度为±1%,张力精度为±1%,最小张力为总张力的2.5%。
2.2.2 AGC厚度操纵系统由法国阿尔斯通(ALSTOM)公司生产的Logidyn D2高精度操纵器、厚度调剂运算机、台湾研华公司生产PⅢ监控运算机、武汉阿尔斯通(ALSTOM)公司开发的AGC操纵软件1套、MTS位移传感器、Heidenhain光栅、美国摩根公司生产的伺服阀、以太网卡等操纵设备组成,可实现监控AGC、预控AGC、秒流量AGC、采样AGC、加减速补偿等多种厚度操纵方式,同时可实现延伸率平坦操纵、自动停车、工艺数据自动记录、远程故障诊断和故障处理等功能。
纵向厚度操纵精度小于±2.5um,横向厚度操纵精度在0.15mm极薄带钢同板上小于6um,2.2.3弯辊操纵系统具有压力调剂在-100%至+100%范畴的双侧单独调剂功能。
2.2.4测厚仪系统美国CIGI公司生产的75KVDC的X射线测厚仪,检测厚度在0.1~4.999mm范畴。
检测厚度精度为0.1%,时刻漂移量为每8小时±0.25%。
2.2.5乳化液操纵系统由美国公司生产的10个电子乳化液调剂阀,实现工作辊和支撑辊的分段喷射冷却,可实现良好的板形操纵;美国公司生产的磁过滤系统,过滤乳化液中的铁份,保证乳化液的灰份和清洁;由武钢科技公司最新引进的磁净化装置,可达操纵铁离子范畴小于50pmm。
2.2.6辅助操纵系统由美国公司开发的触摸屏操作系统,可专门好的实现无操作台操作,轧机的全部操作均可在运算机上完成。
2.3 差不多概念2.3.1冷轧是指金属在再结晶温度下进行轧制变形的一种金属加工方法,一样指带钢不经加热在室温下直截了当进行轧制加工。
2.3.2板形是板材平直度的简称,是指板带材横向是否产生波浪、折皱,它决定于板带材沿宽度方向延伸是否相等。
2.3.3加工硬化带钢在冷轧后,由于晶粒被压扁、拉长、晶格歪扭、畸变、晶粒破裂,使金属的塑性降低、硬度增加这种现象称为加工硬化。
2.3.4横向厚差是指板带材沿宽度方向的厚度偏差,它决定于板材的横截面形状。
2.3.5液压弯辊是用液压缸对工作辊或支承辊施加附加弯曲力,使轧辊产生附加挠度,补偿轧辊原始辊型凸度,以保证带钢板形良好。
2.3.6辊型轧辊辊身表面的轮廓形状称为辊型,一样用辊身中部和端部的直径差△D来表示。
2.3.7变形抗力是指金属抗击塑性变形的能力。
2.3.8塑性是指金属在外力作用下,能确定地发生永久变形而不破坏其完整性的能力。
2.3.9前滑轧制过程中,轧件出口速度大于轧辊在该处的线速度,这种现象叫做前滑。
2.3.10后滑轧件进入轧辊的速度,小于轧辊在该处线速度的水平重量的现象叫后滑。
2.3.11轧机刚度轧机底座抗击纵向弹性变形的能力大小称为轧机纵向刚度,简称轧机刚度。
2.3.12抗拉强度材料抗击拉力破坏作用的最大能力,即材料在断裂前能承担的最大载荷除以原横截表示。
面积得到的应力,叫做抗拉强度,用σb2.3.13屈服强度材料(试样)在受外力作用,载荷增大到某一数值时,试样发生连续伸长现象,叫表示。
做屈服现象,这时材料抗击外力的能力,叫做屈服强度,用σs2.3.14延伸率材料受拉力作用而断裂时,伸长的长度与原有长度的百分比,叫做延伸率,用δ%表示。
2.3.15轧制压力是指金属轧制变形时所需的总压力。
2.4 常见工艺咨询题解答2.4.1如何样利用调剂乳化液来排除两边浪、中间浪?在轧制过程中,带钢显现两边浪,除带钢两边轧制压力大以外,轧辊两边产生的热膨胀过大也是一个缘故,这时适当加大带钢两侧的乳化液流量来排除轧辊的热膨胀,从而排除带钢的两边浪。
同样,若带钢显现中间浪,则采纳加大中间流量或减小两边乳化液流量来排除。
2.4.2冷轧带钢生产中张力的作用是什么?在冷轧带钢生产中张力起着重要作用,第一,张力能够降低轧制力;其次,张力在冷轧过程中自动调剂带钢的横向延伸,使之平均化,从而保证带钢板形平直,提高表面质量;另外,带张力卷取可使钢卷紧密整齐,在连轧生产中还可起到自动调剂连轧关系的作用。
2.4.3冷轧工艺的特点是什么?冷轧工艺的特点要紧有:1)加工温度低,在轧制中将产生不同程度的加工硬化。
2)冷轧中要采纳工艺冷却和润滑。
3)冷轧中要采纳张力轧制。
2.4.4轧制过程中,轧机产生振动的缘故有哪些?应如何处理?轧机振动一样发生在高速轧制极薄带钢时,由于振动,使带钢厚度波动,同时易产生断带。
另外,厚度波动带钢经镀锡后产生“斑马纹”使镀锡板降级,甚至产生废品。
产生振动的缘故要紧有以下几个方面:1)轧制速度太高,成品规格薄。
2)道次轧制工艺参数不合理,如轧制压力低,变形量小,带钢前张力较大。
3)润滑条件不佳,如乳化液浓度太高或太低。
4)轧辊损坏,未及时更换。
5)轧辊轴承和轴承座之间存在间隙。
轧制过程中产生轧机振动,应判定分析产生的缘故,并采取相应措施进行处理。
如一时复杂难以下结论,可适当降低轧制速度,排除和降低振动程度,等到机组检修时再进行处理。
2.4.5平坦的要紧作用是什么?平坦实质上是一种小压下率(1-5%)的二次冷轧,其要紧作用是:1)供冲压用的板带钢事先通过小压下率的平坦,就能够在冲压时不显现“滑移线”,以一定的压下率进行平坦后,钢的应力应变曲线即可不显现“屈服台阶”。
2)冷轧板带材在退火后再经平坦,能够使板材的平直度(板形)与板面光洁度有所改善。
3)改变平坦的压下率,能够使钢板的机械性能在一定的幅度内变化,能够适应不同用途对硬度和塑性要求。
2.4.6在轧制过程中,带钢显现跑偏的缘故是什么?如何处理?在轧制过程中,造成带钢跑偏的缘故要紧有以下几个方面:2)操作缘故,由于操作者双摆调剂不合理,造成带钢跑偏。
3)电气缘故,由于在轧制过程中卷取机张力突然减小或消逝造成带钢跑偏断带。
4)轧辊,由于轧辊磨削有严峻的锥度,使得压下校不了,在轧制过程中给操作者双摆调剂增加了难度,轻者会产生严峻一边浪造成板形缺陷,重者造成带钢跑偏、断带。
带钢轻微跑偏可通过调剂双摆及时排除,严峻跑偏发觉后应赶忙停车,将带钢剪断重新穿带,如轧辊损坏应及时换辊。
2.4.7轧制过程中产生的轧辊缺陷有哪些?产生的缘故如何?轧制过程中产生的轧辊缺陷要紧有热划伤、粘辊、勒辊、裂纹等。
其中热划伤要紧是由于带钢和轧辊之间产生相对摩擦,也确实是润滑状况不佳(润滑不足或过好)造成。
粘辊的缘故是局部压下量过大,断带碎片重叠和破边等造成。
勒辊要紧是由于压下量过大而使带钢产生重波或轻微折叠和带钢跑偏产生重波造成的。
裂纹的产生要紧由于轧辊局部压力过大和轧辊急冷急热引起的,轧机上,若乳化喷嘴堵塞,造成轧辊局部冷却条件不佳,就会产生裂纹。
2.4.8造成带钢断带的缘故有哪些?断带后如何处理?在轧制过程中造成断带有以下几方面缘故:1)来料缘故。
来料有严峻板型缺陷和质量缺陷,如废边压入,严峻溢出边及严峻欠酸洗或过酸洗,厚度严峻不均,板形边浪或中间浪,都会导致断带。
2)设备故障。
电气操纵系统故障或液压系统故障,常见的有张力波动,张力消逝,液压系统停车等。
3)操作故障造成的断带较为常见。
如发觉带钢跑偏缺陷处未及时降速或停车;道次打算选用不合理,道次变形量太大,造成轧制压力大,板形难操纵,道次前后张力太大,将带钢拉断;前道次带钢某处厚度波动(减薄或超厚),后道次未及时减速或将张力操纵切断,造成断带。
4)工作辊的爆裂造成断带。
断带后,应赶忙停车,将机架内带钢拉出,并将工作辊换出。
支承辊轻微粘辊可用油石将表面磨平,严峻损坏应更换支承辊。
2.4.9轧制力的波动是阻碍板带轧制厚度的要紧因素,那么阻碍轧制力变化的因素有哪些?阻碍轧制力变化的因素有:轧件成分和组织性能不均;原料原始厚度不均;张力的变化;轧制速度的变化。
2.5 轧制时的弹塑性曲线轧机在轧制过程中,由于处在轧制力的作用下,使轧机整个机座产生弹性变形,轧件产生塑性变形。
2.5.1轧机的弹性曲线图1 轧制时轧机产生的弹性变形如图1所示,由于整个机架产生了弹性变形,使轧辊原先的辊缝S增大为h,即h=S+∆S,式中∆S--机座弹性变形值,它符合虎克定律,故∆S=P/KP--轧制压力;K--轧机刚性系数;S--轧辊辊缝。
机座的弹性变形值∆S,包含了机架、轧辊、轴承以及压下系统等所组成的机架各部件的变形总和。
刚性系数K的物理意义,是指机座产生单位弹性变形值时的压力(K=P/∆S)。
K值越大,讲明轧机的刚性越好,反映到辊缝中的弹跳值就越小。
如图2所示,∆S1<∆S2<∆S3,它讲明了K1>K2>K3。
图2 理想状态下的K值曲线理论弹性曲线与实际弹性曲线是有差不的,实际弹性曲线的开始时期不是直线段,这是由于机座各部件在加工及装配过程中产生了一定的间隙。
在轧制时,如把辊缝S考虑到里面去,那么曲线将不是由零开始,如图3所示。
由此可知轧件厚度:h=S实+∆S实或 h= S理+∆S理。
在A点(P1轧制力)轧制时,不论是理论弹性曲线,依旧实际曲线,轧件轧出的厚度h是相同的。
但组成厚度h的辊缝S值和弹跳值∆S是不相同的。
实际辊缝值S实较理论辊缝值S理小,而实际弹跳值∆S实较理论弹跳值∆S理大。
在实际生产中,轧辊的真正零位是找不到的(不管是B点或C点)。
因此,通常人为的假设某点(一样在弹性曲线的直线上)作为轧辊辊缝的零点。
图3 机座的弹性曲线及轧件尺寸在弹性曲线上的表示2.5.2轧件的塑性曲线表示轧制力与轧制厚度关系的图示叫塑性曲线,如图4所示。
图4 轧件的塑性曲线1)金属性质的阻碍:金属变形抗力大(硬金属)的塑性曲线比金属变形抗力小(软金属)的塑性曲线陡。
假如轧件的原始厚度为H1时,若采纳相同的压下量,即得到相同的h1,明显轧制硬金属的轧制压力P2比轧制软金属的P1大。
因此,在相同的轧制压力(P2力)下轧制时,轧件轧出的厚度是不同的,即软金属的h2厚度较硬金属的h1小。
如图5。
图5 金属性质的阻碍轧制过程中工艺因素的波动,如轧制温度的变化,张力大小的变化,摩擦条件的改变以及金属化学成分的不平均性等因素的波动,都对轧件的塑性曲线有阻碍,同时曲线的变化形式与图5类似。