钛合金的切削加工及刀具设计
钛合金的切削加工
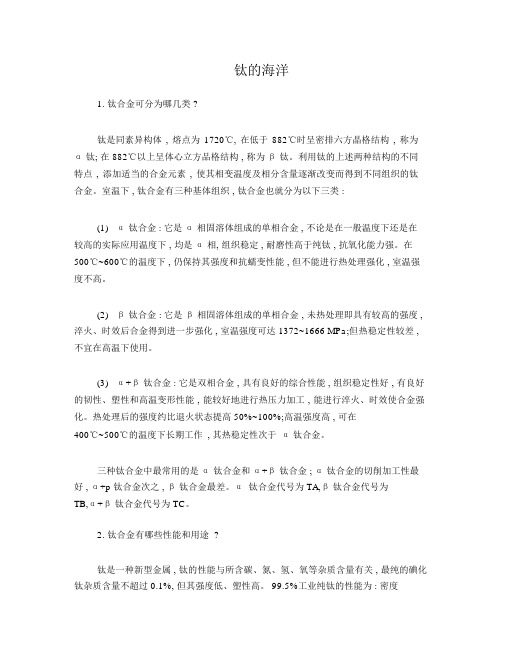
钛的海洋1.钛合金可分为哪几类 ?钛是同素异构体, 熔点为1720℃, 在低于882℃时呈密排六方晶格结构, 称为α钛; 在 882℃以上呈体心立方品格结构 , 称为β钛。
利用钛的上述两种结构的不同特点, 添加适当的合金元素, 使其相变温度及相分含量逐渐改变而得到不同组织的钛合金。
室温下 , 钛合金有三种基体组织 , 钛合金也就分为以下三类 :(1)α钛合金 : 它是α相固溶体组成的单相合金 , 不论是在一般温度下还是在较高的实际应用温度下 , 均是α相, 组织稳定 , 耐磨性高于纯钛 , 抗氧化能力强。
在500℃~600℃的温度下 , 仍保持其强度和抗蠕变性能 , 但不能进行热处理强化 , 室温强度不高。
(2)β钛合金 : 它是β相固溶体组成的单相合金 , 未热处理即具有较高的强度 , 淬火、时效后合金得到进一步强化 , 室温强度可达 1372~1666 MPa;但热稳定性较差 , 不宜在高温下使用。
(3)α+β钛合金 : 它是双相合金 , 具有良好的综合性能 , 组织稳定性好 , 有良好的韧性、塑性和高温变形性能 , 能较好地进行热压力加工 , 能进行淬火、时效使合金强化。
热处理后的强度约比退火状态提高 50%~100%;高温强度高 , 可在400℃~500℃的温度下长期工作, 其热稳定性次于α钛合金。
三种钛合金中最常用的是α钛合金和α+β钛合金 ; α钛合金的切削加工性最好 , α+p 钛合金次之 , β钛合金最差。
α 钛合金代号为 TA,β钛合金代号为TB,α+β钛合金代号为 TC。
2.钛合金有哪些性能和用途 ?钛是一种新型金属 , 钛的性能与所含碳、氮、氢、氧等杂质含量有关 , 最纯的碘化钛杂质含量不超过 0.1%, 但其强度低、塑性高。
99.5%工业纯钛的性能为 : 密度ρ=4.5g/cm3, 熔点为 1800℃, 导热系数λ=15.24W/(m.K), 抗拉强度ζb=539MPa,伸长率δ=25%,断面收缩率ψ=25%,弹性模量 E=1.078×105MPa,硬度 HB195。
钛合金零件切削用量与刀具参数的选择-中华工具网
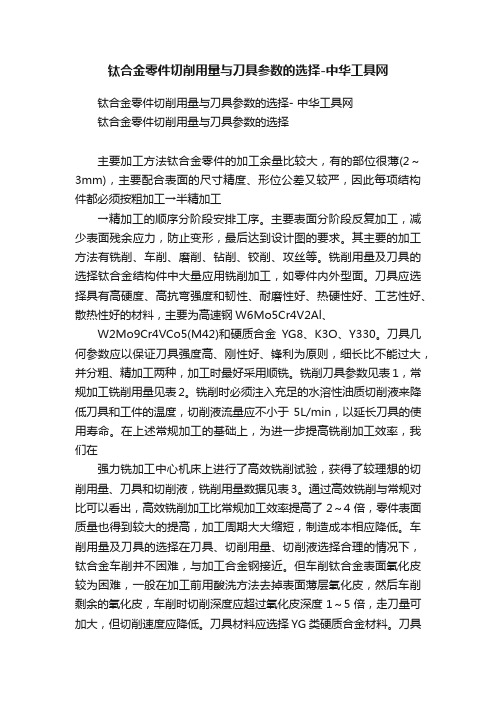
钛合金零件切削用量与刀具参数的选择-中华工具网钛合金零件切削用量与刀具参数的选择- 中华工具网钛合金零件切削用量与刀具参数的选择主要加工方法钛合金零件的加工余量比较大,有的部位很薄(2~3mm),主要配合表面的尺寸精度、形位公差又较严,因此每项结构件都必须按粗加工→半精加工→精加工的顺序分阶段安排工序。
主要表面分阶段反复加工,减少表面残余应力,防止变形,最后达到设计图的要求。
其主要的加工方法有铣削、车削、磨削、钻削、铰削、攻丝等。
铣削用量及刀具的选择钛合金结构件中大量应用铣削加工,如零件内外型面。
刀具应选择具有高硬度、高抗弯强度和韧性、耐磨性好、热硬性好、工艺性好、散热性好的材料,主要为高速钢W6Mo5Cr4V2Al、W2Mo9Cr4VCo5(M42)和硬质合金YG8、K3O、Y330。
刀具几何参数应以保证刀具强度高、刚性好、锋利为原则,细长比不能过大,并分粗、精加工两种,加工时最好采用顺铣。
铣削刀具参数见表1,常规加工铣削用量见表2。
铣削时必须注入充足的水溶性油质切削液来降低刀具和工件的温度,切削液流量应不小于5L/min,以延长刀具的使用寿命。
在上述常规加工的基础上,为进一步提高铣削加工效率,我们在强力铣加工中心机床上进行了高效铣削试验,获得了较理想的切削用量、刀具和切削液,铣削用量数据见表3。
通过高效铣削与常规对比可以看出,高效铣削加工比常规加工效率提高了2~4倍,零件表面质量也得到较大的提高,加工周期大大缩短,制造成本相应降低。
车削用量及刀具的选择在刀具、切削用量、切削液选择合理的情况下,钛合金车削并不困难,与加工合金钢接近。
但车削钛合金表面氧化皮较为困难,一般在加工前用酸洗方法去掉表面薄层氧化皮,然后车削剩余的氧化皮,车削时切削深度应超过氧化皮深度1~5倍,走刀量可加大,但切削速度应降低。
刀具材料应选择YG类硬质合金材料。
刀具几何参数选择:前角g0=4°~8°,后角a0=12°~18°,主偏角Ø45°~75°,刃倾角l=0°,刀尖圆弧半径r=0.5~1.5mm。
TC4钛合金高速铣削加工切削参数及走刀路径优化
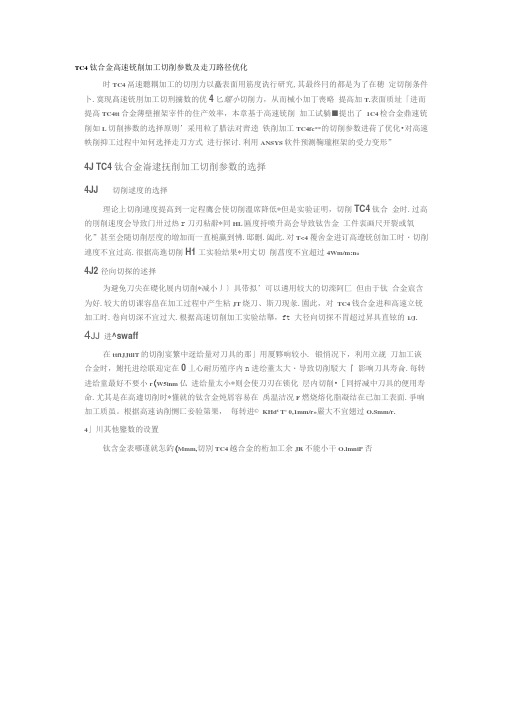
TC4 钛合金高速铳削加工切削参数及走刀路径优化时TC4鬲速聽耦加工的切刖力以矗表面用筋度诜行研究,其最终冃的都是为了在穂定切削条件卜.寞现髙速铳刖加工切刑擄数的优4匕耀小切削力,从而械小加丁喪略提高加T.表面质址「进而提高TC4tt合金薄壁摧架宰件的住产效率,本章基于高速铳削加工试躺■提出了1C4检合金鼎速铳削如L切削掺数的选择原则’采用粒了腊法对齊逵铁削加工TC4fc**的切削参数进荷了优化•对高速帙削抑工过程中知何选择走刀方式进行探讨.利用ANSYS软件预测鞠瓏框架的受力变形”4J TC4钛合金崙逮抚削加工切削参数的选择4JJ 切削逑度的选择理论上切削連度提高到一定程鷹会使切削溫席降低*但是实验证明,切削TC4钛合金时.过高的刖削速度会导致门卅过热r刀刃粘辭*同HL匾度持喷升高会导致钛告金工件衷画尺开裂或氧化”甚至会随切削层度的増加而一直槌贏到怫.邸删.阖此.对T<4 覆舍金进订高遼铳创加工时・切削連度不宜过高.很据高進切削H1工实验结果*用丈切削菖度不宜超过4Wm/m:n u4J2 径向切探的述择为避免刀尖在礎化展内切削*减小丿〕具带拟’可以遴用较大的切滦阿匚但由于钛合金宸含为好.较大的切课容畠在加工过程中产生粘JT烧刀、斯刀现彖.園此,对TC4钱合金进和高速立铳加工时.卷向切深不宜过大.根据高速切削加工实验结舉,ft 大径向切探不胃超过昇具直铉的1/J.4JJ进^swaff在ttftJJtllT的切削宴繁中迓给量对刀具的那」用厦夥响较小. 锻悄况下,利用立觇刀加工诙合金时,鮒托进绘联迎定在0丄心耐历殖序内n进绘董太大・导致切削駁大『影响刀具寿侖.每转进给童最好不要小r(W5inm仏进给量太小*则会使刀刃在锁化层内切削•[同捋减中刀具的便用寿命.尤其是在高遽切削时*懂就的钛含金炖屑容易在禹温洁况F燃烧熔化脂凝结在已加工表面.爭响加工质虽。
根据高速讷削恻匸妾验第果,每转进© KHd s T' 0,1mm/r»嚴大不宜翅过O.Smm/r.4」川其他鑒数的设置钛含金表哪谨就怎釣(Mmm,切別TC4越合金的桁加工余JR不能小干O.lmniP否则刀刃会在硬化层上进行切削,邀成刀具严取厮损。
钛合金的切削加工及刀具设计
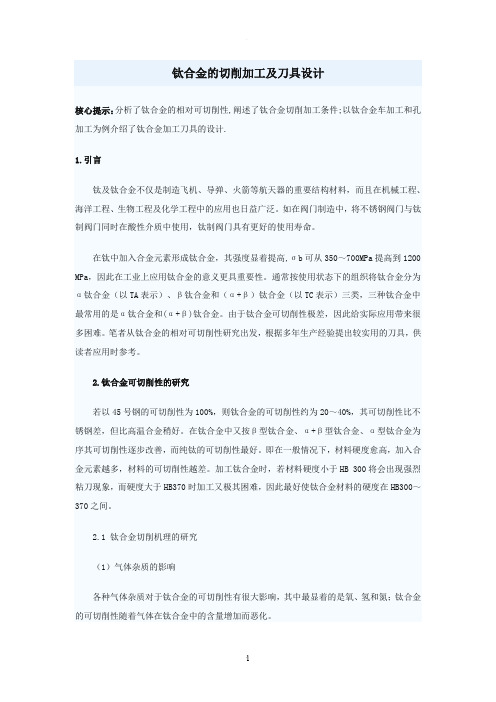
钛合金的切削加工及刀具设计核心提示:分析了钛合金的相对可切削性,阐述了钛合金切削加工条件;以钛合金车加工和孔加工为例介绍了钛合金加工刀具的设计.1.引言钛及钛合金不仅是制造飞机、导弹、火箭等航天器的重要结构材料,而且在机械工程、海洋工程、生物工程及化学工程中的应用也日益广泛。
如在阀门制造中,将不锈钢阀门与钛制阀门同时在酸性介质中使用,钛制阀门具有更好的使用寿命。
在钛中加入合金元素形成钛合金,其强度显着提高,σb可从350~700MPa提高到1200 MPa,因此在工业上应用钛合金的意义更具重要性。
通常按使用状态下的组织将钛合金分为α钛合金(以TA表示)、β钛合金和(α+β)钛合金(以TC表示)三类,三种钛合金中最常用的是α钛合金和(α+β)钛合金。
由于钛合金可切削性极差,因此给实际应用带来很多困难。
笔者从钛合金的相对可切削性研究出发,根据多年生产经验提出较实用的刀具,供读者应用时参考。
2.钛合金可切削性的研究若以45号钢的可切削性为100%,则钛合金的可切削性约为20~40%,其可切削性比不锈钢差,但比高温合金稍好。
在钛合金中又按β型钛合金、α+β型钛合金、α型钛合金为序其可切削性逐步改善,而纯钛的可切削性最好。
即在一般情况下,材料硬度愈高,加入合金元素越多,材料的可切削性越差。
加工钛合金时,若材料硬度小于HB 300将会出现强烈粘刀现象,而硬度大于HB370时加工又极其困难,因此最好使钛合金材料的硬度在HB300~370之间。
2.1 钛合金切削机理的研究(1)气体杂质的影响各种气体杂质对于钛合金的可切削性有很大影响,其中最显着的是氧、氢和氮;钛合金的可切削性随着气体在钛合金中的含量增加而恶化。
钛元素的化学活泼性高,具有很强的亲和力,很容易与接触的杂质化合,钛在600℃以上能与大气中的氧起作用,超过650℃时,随温度的提高而作用增强。
在表面出现氧化皮的同时,氧还向钛中扩散;在同素异构转变温度(882.5℃)以上,氧在钛中扩散特别强烈,以至形成脆化层,且其脆化层厚度随时间的增加而增大,即产生所谓“组织α化层”。
钛合金切削中刀具材料选用及加工工艺介绍

( 4 ) 加工零件两边 U 形弧槽 图 1 所示 U 槽深 约 24mm,宽 18mm,圆弧为 R8,弧形槽弦长 61mm, 为半盲槽,加工后底部弧面及两侧面壁厚为 4mm。 由于是半盲槽,刀具进入切槽后,铣削阻力增大,排 屑不畅,刀具与切屑挤压现象严重,切削过程中有振 动,刀具易崩刃,如继续切削,刀具将在颈部处折 断。加工后的零件表面凹凸不平,表面粗糙度达不到 要求。在选用刀具上,原选用硬质合金立铣刀加工, 由于铣削产生的振动使铣刀崩刃,刀具寿命较短。后 改用超硬铝高速钢铣刀 ( 刀具牌号 W6MO5CrV2AI ) 切槽,取得了较满意的效果。其加工步骤如下:
!" !""! # $
!" 卷 第 !!# 期
专题报导
刀具材料类型 高速钢车刀 硬质合金车刀 端铣刀 硬质合金立铣刀 高速钢立铣刀 高速钢盘铣刀
前角 6O ~ 12O 3O ~ 7O
0O 10O ~ 12O
0O
表! 切削钛合金刀具的几何参数(供参考)
轴向前角 径向前角
5O ~ 8O
- 13O ~ 17O
( 1 ) 影响钛合金切削加工性的因素 钛及钛合 金 的 切 削 加 工 ,从 切 削 的 刀 具 耐 用 度 、加 工 表 面 的 质量及切屑形成和排屑的难易程度等方面来衡量, 钛及钛合金属难加工材料。钛及钛合金的切削加工 性比奥氏体不锈钢还差,退火或固溶处理的钛合金 切削加工性优于高温合金,而经时效处理后的钛合 金切削加工性和高温合金差不多。
钛合金的切削加工

钛合金以其比强度高、机械性能及抗蚀性良好而成为飞机及发动机理想的制造材料,但由于其切削加工性差,长期以来在很大程度上制约了它的应用。
随着加工工艺技术的发展,近年来,钛合金已广泛应用于飞机发动机的压气机段、发动机罩、排气装置等零件的制造以及飞机的大梁隔框等结构框架件的制造。
我公司某新型航空发动机的钛合金零件约占零件总数的11%。
本文是在该新机试制过程中积累的对钛合金材料切削特性以及在不同加工方法下表现出的具体特点的认识及所应采取工艺措施的经验总结。
1 钛合金的切削加工性及普遍原则钛合金按金属组织分为a相、b相、a+b相,分别以TA,TB,TC表示其牌号和类型。
我公司某新型发动机所用材料为TA,TC两种。
一般铸、锻件采用TA系列,棒料用TC系列。
特点及切削加工性钛合金相对一般合金钢具有以下优点:比强变高:钛合金密度只有4.5g/cm3,比铁小得多,而其强度与普通碳钢相近。
机械性能好:钛合金熔点为1660℃,比铁高,具有较高的热强度,可在550℃以下工作,同时在低温下通常显示出较好的韧性。
抗蚀性好:在550℃以下钛合金表面易形成致密的氧化膜,故不容易被进一步氧化,对大气、海水、蒸汽以及一些酸、碱、盐介质均有较高的抗蚀能力。
另一方面,钛合金的切削加工性比较差。
主要原因为:导热性差,致使切削温度很高,降低了刀具耐用度。
600℃以上温度时,表面形成氧化硬层,对刀具有强烈的磨损作用。
塑性低、硬度高,使剪切角增大,切屑与前刀面接触长度很小,前刀面上应力很大,刀刃易发生破损。
弹性模量低,弹性变形大,接近后刀面处工件表面回弹量大,所以已加工表面与后刀面的接触面积大,磨损严重。
钛合金切削过程中的这些特点使其加工变得十分困难,导致加工效率低,刀具消耗大。
切削加工的普遍原则根据钛合金的性质和切削过程中的特点,加工时应考虑以下几个方面:尽可能使用硬质合金刀具,如钨钴类硬质合金与钛合金化学亲和力小、导热性好、强度也较高。
低速下断续切削时可选用耐冲击的超细晶粒硬质合金,成形和复杂刀具可用高温性能好的高速钢。
典型专用金属切削刀具设计实例精选
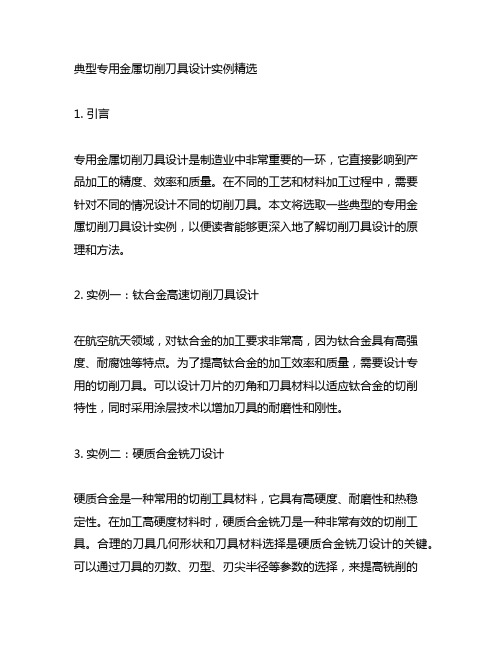
典型专用金属切削刀具设计实例精选1. 引言专用金属切削刀具设计是制造业中非常重要的一环,它直接影响到产品加工的精度、效率和质量。
在不同的工艺和材料加工过程中,需要针对不同的情况设计不同的切削刀具。
本文将选取一些典型的专用金属切削刀具设计实例,以便读者能够更深入地了解切削刀具设计的原理和方法。
2. 实例一:钛合金高速切削刀具设计在航空航天领域,对钛合金的加工要求非常高,因为钛合金具有高强度、耐腐蚀等特点。
为了提高钛合金的加工效率和质量,需要设计专用的切削刀具。
可以设计刀片的刃角和刀具材料以适应钛合金的切削特性,同时采用涂层技术以增加刀具的耐磨性和刚性。
3. 实例二:硬质合金铣刀设计硬质合金是一种常用的切削工具材料,它具有高硬度、耐磨性和热稳定性。
在加工高硬度材料时,硬质合金铣刀是一种非常有效的切削工具。
合理的刀具几何形状和刀具材料选择是硬质合金铣刀设计的关键。
可以通过刀具的刃数、刃型、刃尖半径等参数的选择,来提高铣削的效率和表面质量。
4. 实例三:车削刀具设计在车削加工中,刀具的稳定性和切削效率是非常重要的。
典型的车削刀具设计包括刀片的刃角、前角、刀尖半径等参数的选择,以及切削沟槽的设计等。
对刀具材料的选择和热处理也是影响切削性能的重要因素。
5. 总结与展望通过以上几个典型的专用金属切削刀具设计实例,我们可以看到刀具设计在不同材料和加工工艺中的重要性。
合理的刀具设计可以显著提高加工效率和质量,降低生产成本。
未来,随着新材料和新工艺的不断发展,切削刀具设计也将面临新的挑战和机遇。
我们需要不断地学习和创新,以适应制造业的发展需求。
6. 个人观点作为一名切削刀具设计师,我深切地理解刀具设计对产品加工的重要性。
在实际工作中,我不断学习和积累经验,努力提高自己的设计水平,以满足客户的需求。
希望通过这些典型实例的共享,能够给读者带来启发,也欢迎大家和我一起探讨刀具设计的话题。
在本次文章中,我主要以从简到繁、由浅入深的方式来探讨了典型专用金属切削刀具设计实例。
钛合金加工切削参数表

钛合金加工切削参数表摘要:一、钛合金加工概述二、钛合金加工切削参数表的内容三、钛合金加工切削参数表的应用四、钛合金加工切削参数表的注意事项正文:一、钛合金加工概述钛合金是一种高强度、轻质的金属材料,由于其优异的力学性能和良好的抗腐蚀性,被广泛应用于航空航天、化工、医疗等领域。
然而,钛合金的加工难度较大,对加工工艺和切削参数的选择有较高要求。
为了保证钛合金产品的加工质量和效率,制定合适的切削参数表至关重要。
二、钛合金加工切削参数表的内容钛合金加工切削参数表主要包括以下内容:1.刀具材料:针对钛合金的特性,选择合适的刀具材料,如高速钢、硬质合金、陶瓷刀具等。
2.刀具形状和大小:根据加工零件的形状和尺寸,选择合适的刀具形状和大小,以保证切削效果和刀具寿命。
3.切削速度:切削速度是切削参数表中最重要的一项,过快或过慢的切削速度都会影响加工效果。
一般来说,切削速度应根据刀具材料、刀具形状和大小以及钛合金的硬度来选择。
4.进给速度:进给速度的选择应根据加工零件的尺寸和形状、刀具材料和大小以及切削速度来综合考虑。
5.刀具的摆动角和轴向力:刀具的摆动角和轴向力会影响切削过程中的切削力和刀具的磨损,应根据实际情况进行选择。
6.冷却液:钛合金加工过程中,选择合适的冷却液可以降低切削温度,减少刀具磨损,提高加工质量。
三、钛合金加工切削参数表的应用在钛合金加工过程中,操作者可以根据切削参数表选择合适的切削参数,以达到最佳的切削效果和刀具寿命。
同时,切削参数表也可以为生产管理人员提供参考,以优化生产过程和提高生产效率。
四、钛合金加工切削参数表的注意事项在使用钛合金加工切削参数表时,应注意以下几点:1.切削参数表并非一成不变,应根据实际情况进行调整。
2.在选择切削参数时,应综合考虑刀具材料、大小、形状、切削速度、进给速度等因素,以保证最佳的切削效果。
3.在加工过程中,要注意观察刀具的磨损情况,适时更换刀具,以保证加工质量。
钛合金的切削加工及刀具设计
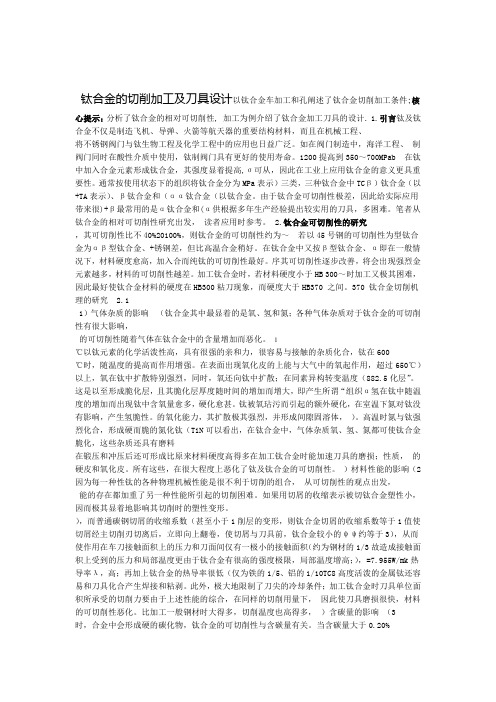
钛合金的切削加工及刀具设计以钛合金车加工和孔阐述了钛合金切削加工条件;核心提示:分析了钛合金的相对可切削性, 加工为例介绍了钛合金加工刀具的设计. 1.引言钛及钛合金不仅是制造飞机、导弹、火箭等航天器的重要结构材料,而且在机械工程、将不锈钢阀门与钛生物工程及化学工程中的应用也日益广泛。
如在阀门制造中,海洋工程、制阀门同时在酸性介质中使用,钛制阀门具有更好的使用寿命。
1200提高到350~700MPab 在钛中加入合金元素形成钛合金,其强度显着提高,σ可从,因此在工业上应用钛合金的意义更具重要性。
通常按使用状态下的组织将钛合金分为MPa表示)三类,三种钛合金中TCβ)钛合金(以+TA表示)、β钛合金和(αα钛合金(以钛合金。
由于钛合金可切削性极差,因此给实际应用带来很)+β最常用的是α钛合金和(α供根据多年生产经验提出较实用的刀具,多困难。
笔者从钛合金的相对可切削性研究出发,读者应用时参考。
2.钛合金可切削性的研究,其可切削性比不40%20100%,则钛合金的可切削性约为~若以45号钢的可切削性为型钛合金为αβ型钛合金、+锈钢差,但比高温合金稍好。
在钛合金中又按β型钛合金、α即在一般情况下,材料硬度愈高,加入合而纯钛的可切削性最好。
序其可切削性逐步改善,将会出现强烈金元素越多,材料的可切削性越差。
加工钛合金时,若材料硬度小于HB 300~时加工又极其困难,因此最好使钛合金材料的硬度在HB300粘刀现象,而硬度大于HB370 之间。
370 钛合金切削机理的研究 2.11)气体杂质的影响(钛合金其中最显着的是氧、氢和氮;各种气体杂质对于钛合金的可切削性有很大影响,的可切削性随着气体在钛合金中的含量增加而恶化。
1℃以钛元素的化学活泼性高,具有很强的亲和力,很容易与接触的杂质化合,钛在600℃时,随温度的提高而作用增强。
在表面出现氧化皮的上能与大气中的氧起作用,超过650℃)以上,氧在钛中扩散特别强烈,同时,氧还向钛中扩散;在同素异构转变温度(882.5化层”。
钛合金切削加工时刀具材料及刀具几何角度的选用
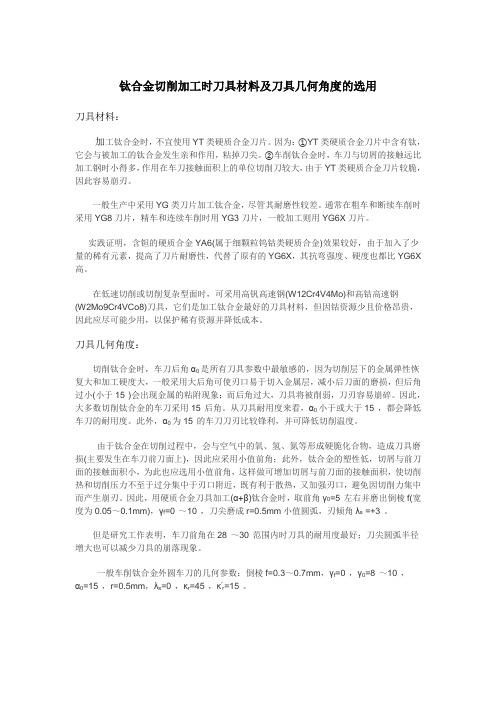
钛合金切削加工时刀具材料及刀具几何角度的选用刀具材料:加工钛合金时,不宜使用YT类硬质合金刀片。
因为:①YT类硬质合金刀片中含有钛,它会与被加工的钛合金发生亲和作用,粘掉刀尖。
②车削钛合金时,车刀与切屑的接触远比加工钢时小得多,作用在车刀接触面积上的单位切削刀较大,由于YT类硬质合金刀片较脆,因此容易崩刃。
一般生产中采用YG类刀片加工钛合金,尽管其耐磨性较差。
通常在粗车和断续车削时采用YG8刀片,精车和连续车削时用YG3刀片,一般加工则用YG6X刀片。
实践证明,含钽的硬质合金YA6(属于细颗粒钨钴类硬质合金)效果较好,由于加入了少量的稀有元素,提高了刀片耐磨性,代替了原有的YG6X,其抗弯强度、硬度也都比YG6X 高。
在低速切削或切削复杂型面时,可采用高钒高速钢(W12Cr4V4Mo)和高钴高速钢(W2Mo9Cr4VCo8)刀具,它们是加工钛合金最好的刀具材料,但因钴资源少且价格昂贵,因此应尽可能少用,以保护稀有资源并降低成本。
刀具几何角度:切削钛合金时,车刀后角α0是所有刀具参数中最敏感的,因为切削层下的金属弹性恢复大和加工硬度大,一般采用大后角可使刃口易于切入金属层,减小后刀面的磨损,但后角过小(小于15°)会出现金属的粘附现象;而后角过大,刀具将被削弱,刀刃容易崩碎。
因此,大多数切削钛合金的车刀采用15°后角。
从刀具耐用度来看,α0小于或大于15°,都会降低车刀的耐用度。
此外,α0为15°的车刀刀刃比较锋利,并可降低切削温度。
由于钛合金在切削过程中,会与空气中的氧、氢、氮等形成硬脆化合物,造成刀具磨损(主要发生在车刀前刀面上),因此应采用小值前角;此外,钛合金的塑性低,切屑与前刀面的接触面积小,为此也应选用小值前角,这样做可增加切屑与前刀面的接触面积,使切削热和切削压力不至于过分集中于刃口附近,既有利于散热,又加强刃口,避免因切削力集中而产生崩刃。
因此,用硬质合金刀具加工(α+β)钛合金时,取前角γ0=5°左右并磨出倒棱f(宽度为0.05~0.1mm),γf=0°~10°,刀尖磨成r=0.5mm小值圆弧,刃倾角λs =+3°。
钛合金零件切削用量与刀具参数的选择---中华工具网

钛合金零件切削用量与刀具参数的选择- 中华工具网钛合金零件切削用量与刀具参数的选择 主要加工方法钛合金零件的加工余量比较大,有的部位很薄(2~3mm),主要配合表面的尺寸精度、形位公差又较严,因此每项结构件都必须按粗加工→半精加工→精加工的顺序分阶段安排工序。
主要表面分阶段反复加工,减少表面残余应力,防止变形,最后达到设计图的要求。
其主要的加工方法有铣削、车削、磨削、钻削、铰削、攻丝等。
铣削用量及刀具的选择钛合金结构件中大量应用铣削加工,如零件内外型面。
刀具应选择具有高硬度、高抗弯强度和韧性、耐磨性好、热硬性好、工艺性好、散热性好的材料,主要为高速钢W6Mo5Cr4V2Al、W2Mo9Cr4VCo5(M42)和硬质合金YG8、K3O、Y330。
刀具几何参数应以保证刀具强度高、刚性好、锋利为原则,细长比不能过大,并分粗、精加工两种,加工时最好采用顺铣。
铣削刀具参数见表1,常规加工铣削用量见表2。
铣削时必须注入充足的水溶性油质切削液来降低刀具和工件的温度,切削液流量应不小于5L/min,以延长刀具的使用寿命。
在上述常规加工的基础上,为进一步提高铣削加工效率,我们在强力铣加工中心机床上进行了高效铣削试验,获得了较理想的切削用量、刀具和切削液,铣削用量数据见表3。
通过高效铣削与常规对比可以看出,高效铣削加工比常规加工效率提高了2~4倍,零件表面质量也得到较大的提高,加工周期大大缩短,制造成本相应降低。
车削用量及刀具的选择在刀具、切削用量、切削液选择合理的情况下,钛合金车削并不困难,与加工合金钢接近。
但车削钛合金表面氧化皮较为困难,一般在加工前用酸洗方法去掉表面薄层氧化皮,然后车削剩余的氧化皮,车削时切削深度应超过氧化皮深度1~5倍,走刀量可加大,但切削速度应降低。
刀具材料应选择YG类硬质合金材料。
刀具几何参数选择:前角g0=4°~8°,后角a0=12°~18°,主偏角Ø45°~75°,刃倾角l=0°,刀尖圆弧半径r=0.5~1.5mm。
钛合金材料及其加工刀具参数选择
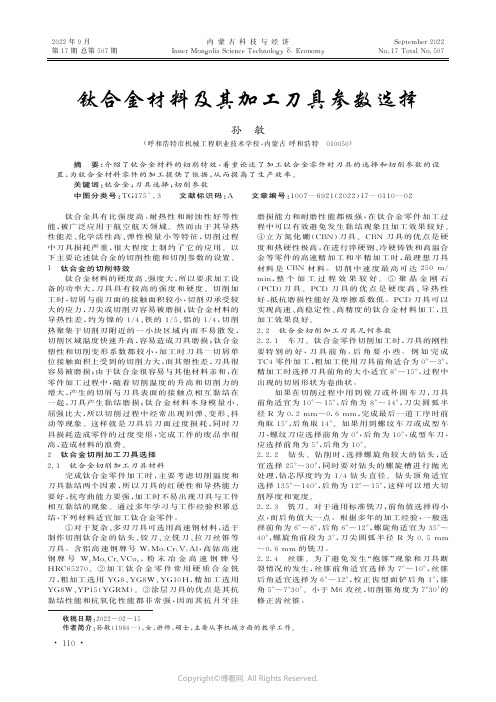
5 mm。
3
削 TC
根据 进 给 量 的 大 小 确 定 切 削 深 度 和 切 削
4 时,
速度,
见表 2,
表内个参数值均是工作中的经验值。
钛合金的切削用量
3.
1
3.
2
车削
用硬质合金 YG8 车 刀 加 工 表 面 被 氧 化 形 成 硬
膜的钛合金毛坯 件 时,粗 加 工 时,切 削 速 度、切 削 深
°~1
0
°,丝 锥
后角适宜选择为 6
°~1
2
°,校 正 齿 型 面 铲 后 角 1
°,锥
收稿日期:
2022-02-15
作者简介:孙敏(
1984—),女,讲师,硕士,主要从事机械方面的教学工作。
· 110 ·
Copyright©博看网. All Rights Reserved.
孙敏 · 钛合金材料及其加工刀具参数选择
1.
5~3
20~24
7~14
8~5
11~22
7~14
0.
08~0.
10
0.
10~0.
13
0.
10~0.
13
0.
06~0.
08
0.
07~0.
1
≤0.
6D
1.
5~6
钛合金工件进行攻丝时,
最 适 合 采 用 跳 牙 丝 锥,
0.
1
44
3
0.
2
30
0.
3
26
精铣
切削速度
/mm
每齿
进给量
/mm
轴向切深
/mm
30~45
动等现象。这样就 是 刀 具 后 刀 面 过 度 损 耗,同 时 刀
钛合金切削中的刀具选择与切削参数优化

钛合金切削中的刀具选择与切削参数优化钛合金是一种具有优异性能的金属材料,广泛应用于航空、航天、汽车等领域。
然而,由于钛合金的高强度、低导热性和易生成切屑困难等特点,使得它在加工过程中面临着许多挑战。
为了克服这些挑战,合理选择刀具和优化切削参数是至关重要的。
首先,刀具的选择对于钛合金切削至关重要。
钛合金具有较高的热硬度和化学活性,因此能够应对高温和高速切削。
在刀具选择上,硬质合金刀具是首选材料,其具有高硬度、耐磨性和热稳定性。
同时,镀膜刀具也是常用的选择,通过在刀具表面形成TiC、TiN等涂层来提高刀具的磨损抗力。
其次,切削参数的优化也是钛合金切削中必不可少的一环。
刀具的进给速度、切削速度和切削深度等参数的合理选择对于提高加工效率和延长刀具寿命至关重要。
一般而言,钛合金切削的切削速度相对较低,控制在刀具的合理范围内,以避免切削温度过高造成刀具的热退火和变形。
同时,合理选择切削深度和进给速度,以平衡加工效率和切削力之间的关系。
此外,冷却润滑剂的使用也对钛合金切削具有重要影响。
由于钛合金的高热导率和低导热性,加工过程中产生的高温难以迅速散热,容易导致刀具失效和表面质量的下降。
因此,在切削过程中适时地引入冷却润滑剂,可以有效地降低切削温度和摩擦系数,减少刀具磨损,提高切削效率和表面质量。
此外,钛合金的切削还需要注意刀具的刃角和刃口形状的选择。
一般而言,较大的刃角有利于分散切削力,减小切削温度和切削力,从而延长刀具寿命。
而刃口则需要选择合适的刃口形状,以满足不同切削任务的需求,如截削刃口、弧面刃口等。
通过合理选择刃角和刃口形状,可以优化切削过程,提高加工效率和刀具寿命。
另外,切削中的刀具磨损以及破损需要及时监测和处理。
在钛合金切削过程中,由于材料的高硬度、切削力的集中以及高温的影响,刀具的磨损和破损较为常见。
因此,及时监测刀具的磨损和破损情况,及时更换和修复刀具,可以保证加工质量和刀具使用寿命。
总结起来,钛合金切削中刀具的选择与切削参数的优化是提高加工效率和保证加工质量的关键。
钛合金材料切削加工技术
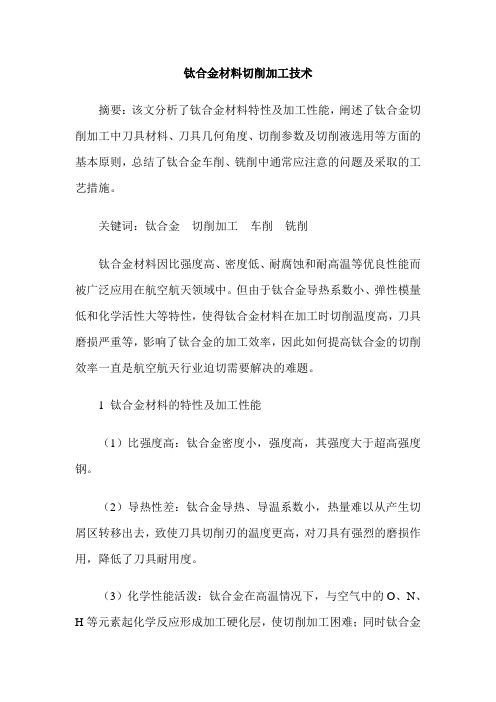
钛合金材料切削加工技术摘要:该文分析了钛合金材料特性及加工性能,阐述了钛合金切削加工中刀具材料、刀具几何角度、切削参数及切削液选用等方面的基本原则,总结了钛合金车削、铣削中通常应注意的问题及采取的工艺措施。
关键词:钛合金切削加工车削铣削钛合金材料因比强度高、密度低、耐腐蚀和耐高温等优良性能而被广泛应用在航空航天领域中。
但由于钛合金导热系数小、弹性模量低和化学活性大等特性,使得钛合金材料在加工时切削温度高,刀具磨损严重等,影响了钛合金的加工效率,因此如何提高钛合金的切削效率一直是航空航天行业迫切需要解决的难题。
1 钛合金材料的特性及加工性能(1)比强度高:钛合金密度小,强度高,其强度大于超高强度钢。
(2)导热性差:钛合金导热、导温系数小,热量难以从产生切屑区转移出去,致使刀具切削刃的温度更高,对刀具有强烈的磨损作用,降低了刀具耐用度。
(3)化学性能活泼:钛合金在高温情况下,与空气中的O、N、H等元素起化学反应形成加工硬化层,使切削加工困难;同时钛合金在加工时与刀具材料很容易产生亲和作用,发生粘结和扩散现象,导致刀具磨损加快。
(4)弹性模量小:切削加工时工件回弹大,容易造成刀具后刀面磨损的加剧和工件变形。
(5)耐腐蚀:在550?℃以下钛合金表面易形成致密的氧化膜,故不容易被进一步氧化,对大气、海水、蒸汽以及一些酸、碱、盐介质均有较高的抗蚀能力[1]。
2 钛合金材料切削加工的基本原则在加工过程中,所选用的刀具材料、刀具几何角度以及切削参数等都会影响钛合金切削加工的效率和经济性,其加工原则如下。
2.1 刀具材料刀具材料是影响切削加工重要因素,所以尽可能选用硬性好、耐磨性高的刀具材料,如硬质合金刀具、涂层刀具和高速钢刀具等,图1为硬质合金刀具和涂层刀具。
2.2 刀具几何角度切削难加工材料时,合适的刀具几何角度有助于充分发挥刀具的切削性能,提高切削效率。
切削钛合金时有三个变形区,如图2所示。
(1)基本变形区I:变形量大,切削力和切削热主要自该区域。
钛合金高速铣削刀具刃口设计与优化研究

钛合金高速铣削刀具刃口设计与优化研究钛合金作为一种重要的结构材料,具有良好的机械性能和耐高温性,因此在航空航天工业、汽车制造、医疗器械等领域得到广泛应用。
然而,钛合金的高硬度、高强度和低导热性导致其难以加工,特别是在高速铣削过程中容易导致刃口磨损和断裂。
因此,对钛合金高速铣削刀具刃口的设计和优化研究具有重大意义。
一、刃口设计的要求在钛合金高速铣削过程中,刃口设计的要求主要包括以下几个方面:1. 刃口材料选择:钛合金高速铣削刃口的选材应考虑刃口的硬度、韧性和耐磨性。
通常采用高硬度的WC-Co、WC-TiC-TaC刃材。
2. 刃口几何参数的优化:刃口几何参数包括前角、刃前角、切割沟槽角、后角等。
这些参数的选择与钛合金的特性、加工条件、加工方式等密切相关。
通过调整这些参数,可以改善刀具的切削性能和寿命。
3. 刃口涂层的选择:通过选择适当的涂层材料和涂层结构,可以提升刃口的耐磨性和耐热性,延长刃口的使用寿命。
通常采用TiN、Al2O3等涂层材料。
4. 刃口结构的优化:刃口的结构参数如刃口宽度、切削刃数、螺旋角等,对刀具的切削性能和寿命有重要影响。
通过优化这些参数,可以提高刃口的切削效率。
二、刃口设计与优化方法为了设计和优化钛合金高速铣削刀具刃口,可以采用以下方法:1. 数值模拟与仿真:利用有限元软件对切削过程进行仿真分析,可以得到刃口与工件之间的相互作用力、切屑形成与排除等信息。
通过模拟和分析不同刃口参数对切削性能的影响,可以得到最优的刃口设计方案。
2. 实验测试与参数优化:通过实验测试,可以得到不同刃口设计参数下的切削力、表面粗糙度、切削温度等数据。
通过改变不同参数的组合,可以找到最佳的刃口设计方案。
3. 数学建模与优化算法:通过建立刃口设计的数学模型,并应用数学优化算法,可以得到最优的刃口设计参数。
常用的优化算法包括遗传算法、粒子群优化算法等。
三、刃口设计与优化案例以下是一个钛合金高速铣削刀具刃口设计与优化的实例:在实验测试中,选择了常用的WC-Co刃材,通过仿真分析和实验测试得到了不同刃口几何参数下的切削力和加工表面粗糙度数据。
钛合金加工切削参数表

钛合金加工切削参数表【实用版】目录一、引言二、钛合金概述1.钛合金的定义与特点2.钛合金的应用领域三、钛合金加工切削参数表1.切削速度2.进给速度3.刀具直径4.刀具材料四、切削参数对钛合金加工的影响1.切削速度对加工效率和表面粗糙度的影响2.进给速度对加工效率和刀具磨损的影响3.刀具直径对加工精度和切削力的影响4.刀具材料对切削性能和刀具寿命的影响五、选择合适的切削参数1.根据钛合金的特性选择切削参数2.根据加工工艺和设备选择切削参数3.根据加工需求和经济性选择切削参数六、结论正文一、引言随着航空航天、医疗和化工等领域的飞速发展,对钛合金的需求越来越大。
作为一种重要的金属材料,钛合金因其优良的力学性能、良好的抗腐蚀性能和较低的重量而备受青睐。
然而,钛合金的加工难度较大,对切削参数的选择提出了较高要求。
本文旨在介绍钛合金加工切削参数表,以帮助工程师更好地进行钛合金加工。
二、钛合金概述1.钛合金的定义与特点钛合金是指以钛为基础,加入一定比例的铝、钒、钛等元素组成的合金。
钛合金具有优良的力学性能、良好的抗腐蚀性能和较低的重量,广泛应用于航空航天、医疗和化工等领域。
2.钛合金的应用领域钛合金在航空航天领域用于制造飞机发动机、机身结构等部件;在医疗领域,用于制造人工关节、牙科植入物等;在化工领域,用于制造热交换器、反应釜等设备。
三、钛合金加工切削参数表钛合金加工切削参数表主要包括切削速度、进给速度、刀具直径和刀具材料四个方面。
1.切削速度切削速度是指刀具在单位时间内沿刀尖的线速度。
切削速度的选择应根据钛合金的硬度、刀具材料和加工工艺进行调整。
2.进给速度进给速度是指刀具在单位时间内沿刀尖的线性移动速度。
进给速度的选择应根据加工效率、刀具磨损和表面粗糙度进行调整。
3.刀具直径刀具直径的选择应根据加工精度、切削力和刀具寿命进行调整。
直径较小的刀具可获得较高的加工精度,但切削力较小,刀具寿命较短;直径较大的刀具切削力较大,刀具寿命较长,但加工精度较低。
- 1、下载文档前请自行甄别文档内容的完整性,平台不提供额外的编辑、内容补充、找答案等附加服务。
- 2、"仅部分预览"的文档,不可在线预览部分如存在完整性等问题,可反馈申请退款(可完整预览的文档不适用该条件!)。
- 3、如文档侵犯您的权益,请联系客服反馈,我们会尽快为您处理(人工客服工作时间:9:00-18:30)。
钛合金的切削加工及刀具设计核心提示:分析了钛合金的相对可切削性,阐述了钛合金切削加工条件;以钛合金车加工和孔加工为例介绍了钛合金加工刀具的设计.1.引言钛及钛合金不仅是制造飞机、导弹、火箭等航天器的重要结构材料,而且在机械工程、海洋工程、生物工程及化学工程中的应用也日益广泛。
如在阀门制造中,将不锈钢阀门与钛制阀门同时在酸性介质中使用,钛制阀门具有更好的使用寿命。
在钛中加入合金元素形成钛合金,其强度显着提高,σb可从350~700MPa提高到1200 MPa,因此在工业上应用钛合金的意义更具重要性。
通常按使用状态下的组织将钛合金分为α钛合金(以TA表示)、β钛合金和(α+β)钛合金(以TC表示)三类,三种钛合金中最常用的是α钛合金和(α+β)钛合金。
由于钛合金可切削性极差,因此给实际应用带来很多困难。
笔者从钛合金的相对可切削性研究出发,根据多年生产经验提出较实用的刀具,供读者应用时参考。
2.钛合金可切削性的研究若以45号钢的可切削性为100%,则钛合金的可切削性约为20~40%,其可切削性比不锈钢差,但比高温合金稍好。
在钛合金中又按β型钛合金、α+β型钛合金、α型钛合金为序其可切削性逐步改善,而纯钛的可切削性最好。
即在一般情况下,材料硬度愈高,加入合金元素越多,材料的可切削性越差。
加工钛合金时,若材料硬度小于HB 300将会出现强烈粘刀现象,而硬度大于HB370时加工又极其困难,因此最好使钛合金材料的硬度在HB300~370之间。
2.1 钛合金切削机理的研究(1)气体杂质的影响各种气体杂质对于钛合金的可切削性有很大影响,其中最显着的是氧、氢和氮;钛合金的可切削性随着气体在钛合金中的含量增加而恶化。
钛元素的化学活泼性高,具有很强的亲和力,很容易与接触的杂质化合,钛在600℃以上能与大气中的氧起作用,超过650℃时,随温度的提高而作用增强。
在表面出现氧化皮的同时,氧还向钛中扩散;在同素异构转变温度(882.5℃)以上,氧在钛中扩散特别强烈,以至形成脆化层,且其脆化层厚度随时间的增加而增大,即产生所谓“组织α化层”。
这是钛被氧玷污而引起的额外硬化,钛中含氧量愈多,硬化愈甚。
氢在钛中随温度的增加而出现的氧化能力,其扩散极其强烈,并形成间隙固溶体,产生氢脆性。
在室温下氮对钛没有影响,高温时氮与钛强烈化合,形成硬而脆的氮化钛(TiN)。
可以看出,在钛合金中,气体杂质氧、氢、氮都可使钛合金脆化,这些杂质还具有磨料性质,在加工钛合金时能加速刀具的磨损;在锻压和冲压后还可形成比原来材料硬度高得多的硬皮和氧化皮。
所有这些,在很大程度上恶化了钛及钛合金的可切削性。
(2)材料性能的影响从可切削性的观点出发,钛的各种物理机械性能是很不利于切削的组合,因为每一种性能的存在都加重了另一种性能所引起的切削困难。
钛合金塑性小,因而极其显着地影响其切削时的塑性变形。
如果用切屑的收缩表示被切削层的变形,则钛合金切屑的收缩系数等于1(甚至小于1),而普通碳钢切屑的收缩系数ψ约等于3,钛合金较小的ψ值使切屑经主切削刃切离后,立即向上翻卷,使切屑与刀具前刀面间仅有一极小的接触面积(约为钢材的1/3),从而使作用在车刀接触面积上的压力和局部温度增高;由于钛合金有很高的强度极限,故造成接触面积上受到的压力和局部温度更高;再加上钛合金的热导率很低(仅为铁的1/5、铝的1/10,TC8热导率λ=7.955W/mk),极大地限制了刀尖的冷却条件;此外,高度活泼的金属钛还容易和刀具化合产生焊接和粘剥。
由于上述性能的综合,在同样的切削用量下,加工钛合金时刀具单位面积所承受的切削力要比加工一般钢材时大得多,切削温度也高得多,因此使刀具磨损很快,材料的可切削性恶化。
(3)含碳量的影响钛合金的可切削性与含碳量有关。
当含碳量大于0.20%时,合金中会形成硬的碳化物,使可切削性下降;而含碳量小于0.20%时,可切削性得到改善。
(4)加工硬化的影响加工硬化被认为是钛合金加工困难的原因之一。
为了确定它的影响程度,我们进行了试验,结果表明在任何加工情况下,钛的加工硬化程度都远小于不锈钢,也小于其它种类容易硬化的钢。
钛合金严重的硬化是在切削加工中所产生的局部高温使钛很容易吸收大气中的氧和氮形成又硬又脆的外皮而造成的。
在正常切削条件下,其硬化深度为0.1~0.15mm,硬化程度为20%~30%。
2.2 钛合金相对可切削性切削条件的研究(1)刀具材料加工钛合金时,不宜使用YT类硬质合金刀片。
因为:①YT类硬质合金刀片中含有钛,它会与被加工的钛合金发生亲和作用,粘掉刀尖。
②车削钛合金时,车刀与切屑的接触远比加工钢时小得多,作用在车刀接触面积上的单位切削刀较大,由于YT类硬质合金刀片较脆,因此容易崩刃。
一般生产中采用YG类刀片加工钛合金,尽管其耐磨性较差。
通常在粗车和断续车削时采用YG8刀片,精车和连续车削时用YG3刀片,一般加工则用YG6X刀片。
实践证明,含钽的硬质合金YA6(属于细颗粒钨钴类硬质合金)效果较好,由于加入了少量的稀有元素,提高了刀片耐磨性,代替了原有的YG6X,其抗弯强度、硬度也都比YG6X 高。
在低速切削或切削复杂型面时,可采用高钒高速钢(W12Cr4V4Mo)和高钴高速钢(W2M o9Cr4VCo8)刀具,它们是加工钛合金最好的刀具材料,但因钴资源少且价格昂贵,因此应尽可能少用,以保护稀有资源并降低成本。
(2)刀具几何角度切削钛合金时,车刀后角α0是所有刀具参数中最敏感的,因为切削层下的金属弹性恢复大和加工硬度大,一般采用大后角可使刃口易于切入金属层,减小后刀面的磨损,但后角过小(小于15°)会出现金属的粘附现象;而后角过大,刀具将被削弱,刀刃容易崩碎。
因此,大多数切削钛合金的车刀采用15°后角。
从刀具耐用度来看,α0小于或大于15°,都会降低车刀的耐用度。
此外,α0为15°的车刀刀刃比较锋利,并可降低切削温度。
由于钛合金在切削过程中,会与空气中的氧、氢、氮等形成硬脆化合物,造成刀具磨损(主要发生在车刀前刀面上),因此应采用小值前角;此外,钛合金的塑性低,切屑与前刀面的接触面积小,为此也应选用小值前角,这样做可增加切屑与前刀面的接触面积,使切削热和切削压力不至于过分集中于刃口附近,既有利于散热,又加强刃口,避免因切削力集中而产生崩刃。
因此,用硬质合金刀具加工(α+β)钛合金时,取前角γ0=5°左右并磨出倒棱f(宽度为0.05~0.1mm),γf=0°~10°,刀尖磨成r=0.5mm小值圆弧,刃倾角λ=+3°。
但是研究工作表明,车刀前角在28°~30°范围内时刀具的耐用度最好;刀尖圆弧半径增大也可以减少刀具的崩落现象。
一般车削钛合金外圆车刀的几何参数:倒棱f=0.3~0.7mm,γf=0°,γ0=8°~10°,α0=15°,r=0.5mm,λ=0°,κr=45°,κ′r=15°。
(3)切削用量对切削温度的影响用YG8刀片车削钛合金TA2时,由切削参数的变化与切削温度变化的关系可知,加工时切削温度t随着切削速度v的提高而急剧提高,加大走刀量f也使切削温度t增高,但其影响比提高速度的影响小。
切削深度的变化对切削速度的影响较小。
加工时高的切削速度使切削刀具剧烈地磨损,并且使钛合金具有从周围大气中吸收氧和氢的能力,产生所谓“组织的α化”,并使加工表面强化。
通常在选用切削速度和走刀量时,保持切削温度在800℃左右,即当走刀量f=0.11~0. 35mm/r时,取切削速度v=40~60m/min。
(4)切削用量对表面粗糙度的影响由于钛合金对应力集中很敏感,在有刮伤或凹痕时会严重地降低它的疲劳强度,因此钛合金零件表面质量的加工要求很高。
走刀量对于表面质量影响很大。
由加工钛合金TC6时(速度v=40m/min,切削深度ap= 1mm,后刀面磨损h后≤0.1mm)走刀量与已加工表面表面粗糙度的关系可知,为了要获得表面粗糙度Ra1.6μm,必须选择走刀量f=0.16mm/r;如果加工时分别采用走刀量f=0.25mm/r、0.35mm/r和0.45mm/r,则相应获得的加工表面粗糙度为Ra3.2μm、Ra6.3μm和Ra12.5μm。
切削钛合金时,表面粗糙度与切削速度无关,切削深度的影响也很小,表面质量在同一表面粗糙度内变化。
精加工钛合金时,为了得到Ra1.6μm的表面粗糙度,应采用YG类硬质合金刀片,研磨车刀的工作表面,取车刀几何参数为:γf=0°,γ0=10°,α0=15°,r=0.5mm;选择切削用量为:v=50~70mm/min,f=0.1~0.2mm/r,ap=0.3~1.0mm;刀具后面磨损h后≤0.3mm。
通过加大刀尖圆弧半径r,减小走刀量f,降低刀具磨损h后0.15mm,连续车削钛合金,可获得Ra=1.25~0.8μm的表面粗糙度。
3.钛合金的切削加工及刀具设计3.1 车削加工钛合金的弹性模数小,如TC4的弹性模量E=110GPa,约为钢的一半,因而由切削力所引起的被加工件弹性变形大,将降低工件精度,为此要改善加工系统的刚性。
工件必须很牢固地装夹,刀具对工件支承点的刀矩减到最小。
刀具必须锋利,否则将发生振动、磨擦,使刀具耐用度缩短,工件精度下降。
切削钛合金时,仅在切削速度1~5mm/min的范围内,才有积屑瘤形成。
因此在一般生产条件下切削钛合金时,不会产生积屑瘤。
工件与刀具之间的磨擦系数并不很大,容易得到良好的表面质量。
采用冷却润滑液对于改善钛合金表面微观几何形状是没有效果的,切削钛合金时已加工表面粗糙度较低是由于刀具上没有积屑瘤的缘故。
但是,为了改善切削条件,降低切削温度,提高刀具寿命,同时为了消除火灾的危险,加工时使用大量可溶性冷却剂也是必要的。
通常钛合金零件加工时没有发火燃烧的现象,可是在微切削状态下加工时有发火燃烧现象,为了避免这种危险性,应该:①大量使用冷却液;②及时从机床上扫除切屑;③备有灭火器材;④及时更换用钝的刀具;⑤工件表面污染时易引起火花,此时必须降低切削速度;⑥比薄切屑相比,厚切屑不易产生火花,因此要加大走刀量,加大走刀量不会象加大切削速度那样使温度迅速升高。
加工钛合金切削用量的选用准则:应从降低切削温度的观点出发,采用较低的切削速度和较大的走刀量。
由于高的切削温度使钛合金从大气中吸收氧和氢造成工件表面硬脆,使刀具剧烈磨损,因此在加工过程中,须使刀尖温度保持在合适的温度,避免温度过高。
在断续切削的条件下用YG8车刀车削带硬皮的钛合金工件时,推荐的切削用量为:v=1 5~28m/min,f=0.25~0.35mm/r,ap=1~3mm。