棒料切割机的设计设计专业论文
棒料切割机的设计_毕业设计论文 精品
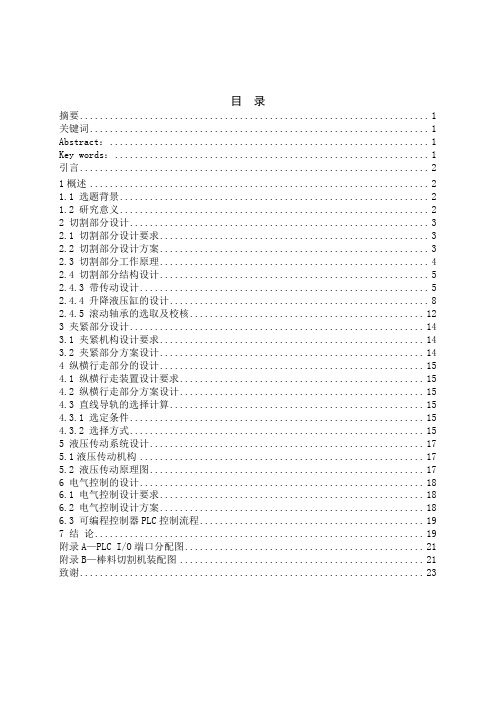
目录摘要 (1)关键词 (1)Abstract: (1)Key words: (1)引言 (2)1概述 (2)1.1 选题背景 (2)1.2 研究意义 (2)2 切割部分设计 (3)2.1 切割部分设计要求 (3)2.2 切割部分设计方案 (3)2.3 切割部分工作原理 (4)2.4 切割部分结构设计 (5)2.4.3 带传动设计 (5)2.4.4 升降液压缸的设计 (8)2.4.5 滚动轴承的选取及校核 (12)3 夹紧部分设计 (14)3.1 夹紧机构设计要求 (14)3.2 夹紧部分方案设计 (14)4 纵横行走部分的设计 (15)4.1 纵横行走装置设计要求 (15)4.2 纵横行走部分方案设计 (15)4.3 直线导轨的选择计算 (15)4.3.1 选定条件 (15)4.3.2 选择方式 (15)5 液压传动系统设计 (17)5.1液压传动机构 (17)5.2 液压传动原理图 (17)6 电气控制的设计 (18)6.1 电气控制设计要求 (18)6.2 电气控制设计方案 (18)6.3 可编程控制器PLC控制流程 (19)7 结论 (19)附录A—PLC I/O端口分配图 (21)附录B—棒料切割机装配图 (21)致谢 (23)棒料切割机的设计棒料切割机的设计机械电子专业学生韦忠爽指导教师闫冰洁摘要:通过对切割过程的观察和研究,本课题采用了机电一体化系统设计思想,对其整体造型、机械结构和控制系统进行设计,此棒料切割机电一体化系统主要由四个部分组成:机械本体、电子控制单元、执行器和动力源。
工作原理是电动机通过带传动带动切割片做高速旋转运动,电机与工作台之间采用铰支撑方式,升降液压缸可推动切割片进行上下移动带动刀片完成顺序切割动作。
切割机采用PLC控制各个液压换向阀的电磁铁,实现棒料的自动下料和切割以及检测工作。
随动工作台前进速度也可以通过夹紧机械手夹紧棒料使之与棒料速度同步。
横向切割时的切割速度可以通过液压缸来调节。
机械制造及自动化专业毕业论文--青玉米秸秆收割切碎机的设计1
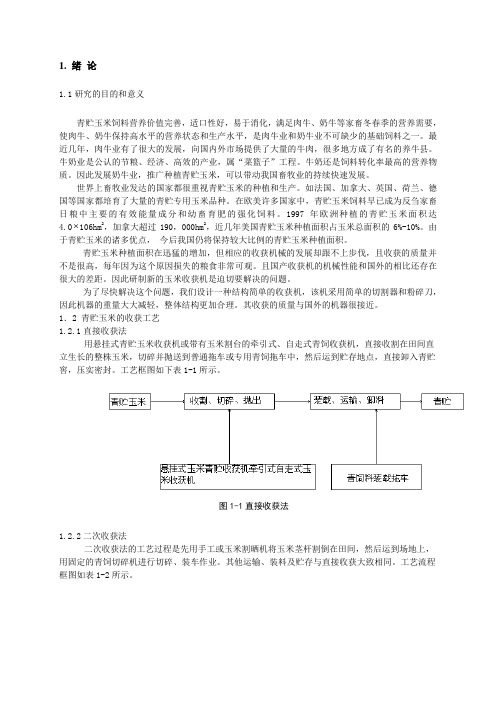
1. 绪论1.1研究的目的和意义青贮玉米饲料营养价值完善,适口性好,易于消化,满足肉牛、奶牛等家畜冬春季的营养需要,使肉牛、奶牛保持高水平的营养状态和生产水平,是肉牛业和奶牛业不可缺少的基础饲料之一。
最近几年,肉牛业有了很大的发展,向国内外市场提供了大量的牛肉,很多地方成了有名的养牛县。
牛奶业是公认的节粮、经济、高效的产业,属“菜篮子”工程。
牛奶还是饲料转化率最高的营养物质。
因此发展奶牛业,推广种植青贮玉米,可以带动我国畜牧业的持续快速发展。
世界上畜牧业发达的国家都很重视青贮玉米的种植和生产。
如法国、加拿大、英国、荷兰、德国等国家都培育了大量的青贮专用玉米品种。
在欧美许多国家中,青贮玉米饲料早已成为反刍家畜日粮中主要的有效能量成分和幼畜育肥的强化饲料。
1997年欧洲种植的青贮玉米面积达4.0 106hm2,加拿大超过190,000hm2,近几年美国青贮玉米种植面积占玉米总面积的6%-10%。
由于青贮玉米的诸多优点,今后我国仍将保持较大比例的青贮玉米种植面积。
青贮玉米种植面积在迅猛的增加,但相应的收获机械的发展却跟不上步伐,且收获的质量并不是很高,每年因为这个原因损失的粮食非常可观。
且国产收获机的机械性能和国外的相比还存在很大的差距。
因此研制新的玉米收获机是迫切要解决的问题。
为了尽快解决这个问题,我们设计一种结构简单的收获机,该机采用简单的切割器和粉碎刀,因此机器的重量大大减轻,整体结构更加合理。
其收获的质量与国外的机器很接近。
1.2 青贮玉米的收获工艺1.2.1直接收获法用悬挂式青贮玉米收获机或带有玉米割台的牵引式、自走式青饲收获机,直接收割在田间直立生长的整株玉米,切碎并抛送到普通拖车或专用青饲拖车中,然后运到贮存地点,直接卸入青贮窖,压实密封。
工艺框图如下表1-1所示。
图1-1直接收获法1.2.2二次收获法二次收获法的工艺过程是先用手工或玉米割晒机将玉米茎杆割倒在田间,然后运到场地上,用固定的青饲切碎机进行切碎、装车作业。
棒料切割机的设计_毕业设计
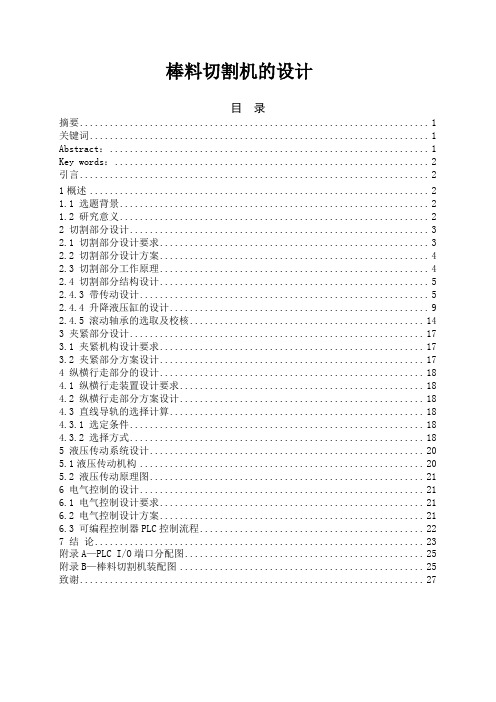
1.1 选题背景
机电一体化产品广泛应用各种加工业,切割技术也有了飞速的发展,手工切割已经适应不了现代工业发展的要求。如今已进入以通用机械时代。几十年来,切割技术的研究和发展一直比较活跃,设计在不断的修改,品种也在不断的增加,应用领域也在不断的扩大。而目前市面上有很多型号的棒料切割机结构复杂,调节,维修不方便,生产效率低,智能化低等不足。
Key words:Cutting machine;Mechanical and electrical integration;Hydraulic pressure; bar; PLC control
引言
当今时代正是中国发展的黄金时代,中国又是一个发展中国家,要想谋求更大的发展,行业的转型是一定的,所以轻工业的转型,重工业与机械制造的行业的重视是必然的。就这一点来看,让我们清晰看到机械行业的发展前景有着如此大的潜力。它与其他行业有着千丝万缕的联系,随着经济的发展和科技的进步,越来越多的产品智能化、自动化、网络化,单纯的机械已经不能适应行业发展的需要,渐渐地就出现了机电一体化。现代机械的机电一体化的目标是综合利用机、电、信息、控制等各方面的相关技术的优势[1],扬长避短以达到系统优化的效果,取得显著地社会效益和技术经济效益。
1.2 研究意义
本棒料切割机的切割机构属于机械技术领域,它解决了现有的自动切割机所存在的精度不高,操作复杂,智能化低等问题。本课题针对目前市场上的切割机设计的不足,对棒料切割机进行改造创新,增加智能化程度,设计出具有控制方便,性能稳定,结构简单,调节、维修方便,安全可靠,低能耗,在切割过程中能使棒料位置稳定、切割长度准确,生产率高,运行平稳,提高产品质量,提高生产效率等优点的具有广泛应用前景的方案。
棒料切割机的设计
棒料切割机的设计
【设计】机械毕业论文钢管切割机设计

【关键字】设计前言在毕业设计选定题目的社会调研中发现,生产中所需的钢管大都使用手工切断,采用手工操作劳动强度大,工作效率低,并存在极其危险的安全隐患,建议设计制造机械化的钢管切割机,当即受到企业欢迎,表示愿意使用设备,我们小组主动承接了此项设计任务。
一、钢管切割机的用途及设计要求1、用途钢管切割机主要是用来切割加工工程所需不同长度的管材,它可以自动适应各种管材横截面直径的大小,对不同材质的钢管均有较好的切割性能,切口平整圆滑为下道工序的顺利加工奠定了基础。
2、设计要求1)被切割管子直径范围为19.05mm(3/4")~101.6mm(4") 。
2)被切割管子壁厚范围为3~5mm。
3)中批量生产。
4)中型机械厂承制。
5)单人操作,每日两班制(每班断续工作,时间≤10小时)。
二、钢管切割机的总体方案设计1、工艺分析原工厂对金属管材的切割采用了弓锯切割及气割的方法。
弓锯的工艺质量因人而异,且工作效率低下,浪费人工工时,不适合批量加工。
气割的方法较弓锯切割工作效率高,节约人工工时,但切割处的金属内部分子结构发生转变,材质性能劣化,并且切口处的金属熔渣严重影响下道工序的加工。
为此,根据加工现场的工艺情况和要求,设计研制了这台钢管切割机,它采用了碾压的方法切割金属管材,对管材的切口加工精度高,并且适合连续切削,节约了人工工时,提高了生产效率。
2、对执行机构的运动要求2.1 计算总传动比和分配传动比总传动比计算初步确定滚筒转速:n =70r/min则总传动比:i总=—==20各级传动机构的传动比分配如下:带传动:i0=1.67蜗杆传动:i1=25齿轮传动: i2=2 i3=5/21实际总传动比等于:i总'=i0i1i2i3=1.67×25×2×=19.882.2 各传动轴传动功率及机械效率的计算带传动: η1=0.96 蜗杆传动:η2=0.7齿轮传动: η3=0.94 滚动轴承:η4=0.99各传动轴传动特性,见表13 切管工艺方案及传动方案设计和选型3.1 切管工艺方案选择,见表23.2传动方案选择如下图1所示图1如上图1所示,提供的切管机的三种传动系统方案.若仅满足总传动比要求,可以采用单级蜗杆传动.但综合考虑结构,操作及调整布局等方面的要求,宜采用图中传动系统方案3。
棒料切割机结构创新设计
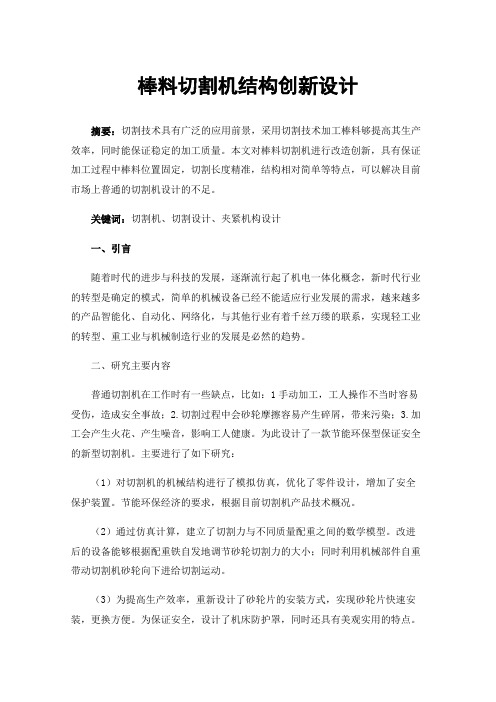
棒料切割机结构创新设计摘要:切割技术具有广泛的应用前景,采用切割技术加工棒料够提高其生产效率,同时能保证稳定的加工质量。
本文对棒料切割机进行改造创新,具有保证加工过程中棒料位置固定,切割长度精准,结构相对简单等特点,可以解决目前市场上普通的切割机设计的不足。
关键词:切割机、切割设计、夹紧机构设计一、引言随着时代的进步与科技的发展,逐渐流行起了机电一体化概念,新时代行业的转型是确定的模式,简单的机械设备已经不能适应行业发展的需求,越来越多的产品智能化、自动化、网络化,与其他行业有着千丝万缕的联系,实现轻工业的转型、重工业与机械制造行业的发展是必然的趋势。
二、研究主要内容普通切割机在工作时有一些缺点,比如:1手动加工,工人操作不当时容易受伤,造成安全事故;2.切割过程中会砂轮摩擦容易产生碎屑,带来污染;3.加工会产生火花、产生噪音,影响工人健康。
为此设计了一款节能环保型保证安全的新型切割机。
主要进行了如下研究:(1)对切割机的机械结构进行了模拟仿真,优化了零件设计,增加了安全保护装置。
节能环保经济的要求,根据目前切割机产品技术概况。
(2)通过仿真计算,建立了切割力与不同质量配重之间的数学模型。
改进后的设备能够根据配重铁自发地调节砂轮切割力的大小;同时利用机械部件自重带动切割机砂轮向下进给切割运动。
(3)为提高生产效率,重新设计了砂轮片的安装方式,实现砂轮片快速安装,更换方便。
为保证安全,设计了机床防护罩,同时还具有美观实用的特点。
三、工作原理由PLC控制电机和液压缸的动作完成预定切割加工动作,横向进给液压缸用来控制工作台横向移动;纵向进给液压缸可以带动工作台纵向进给;垂直液压缸可控制砂轮进行上下运动,电动机用铰链连接在工作台之上,由电机通过带传动使得砂轮高速转动从而完成切割加工。
机构设计方案如图1 所示。
1-大带轮;2-传送带;3-电动机;4-砂轮;5-垂直液压缸;6-进料口;7-横向进给板;8-夹具;9-棒料;10-横向进给缸;11-纵向进给板;12-纵向进给缸图1 机构设计棒料切割机系统由主要包括动力源、传动装置、执行部件和控制系统四个部分组成。
毕业设计 棒材飞剪机的设计
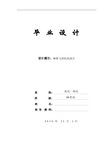
毕 业 设 计设计题目:棒材飞剪机的设计系 别:_________________________班 级:_________________________姓 名:_________________________指 导 教 师:_________________________2010年11月 1 日08机电 机电一体化棒材飞剪机的设计摘要棒材飞剪机是现代轧钢生产线上的咽喉设备,它负责钢材的切头切尾及定尺剪切。
在高速轧线上,确保飞剪的定尺剪切精度,对提高轧钢厂的成材率具有十分重要的意义。
本课题从机械设计和气动控制等各个方面找出影响剪切精度的因素,从而设计出启停特性好的飞剪机,并对飞剪的控制进行一定的分析研究以确保飞剪的定尺精度。
本课题的研究具有较高的应用价值,同时对飞剪的设计制造具有一定的指导意义,并可为企业提高成材率,进而创造经济效益。
而且,由于本课题综合运用了机电气的相关知识,通过对飞剪机的精度控制分析,提出了一些响应的改进方法,值得在实际的设计制造中借鉴,提出了几种飞剪机设计的新思路,可供参考。
相关词:飞剪机棒材精度控制剪切精度Strong material fly to cut machineAbstractStrong material fly to cut machine is the throat equipment on the modern production line of steel rolling, it responsible steel material cut head cut end and scale cut. On rolling line with high speed ensure to fly the scale that cuts cut precision, for rising steel rolling mill become useful to lead have very important meaning. This program is from mechanical design and is pneumatic to find out influence with every aspects such as electrical control to cut the factor of precision, so devise to start stop property good fly to cut machine, and as flying , the control that cut carries out certain analysis research so as ensure to fly the scale precision that cut.The research of this program has higher application value, at the same time as flying , the design production that cut has certain guidance meaning, and can become useful for enterprise raising to lead , and then create economic benefits. , since this program is synthesized with the related knowledge of Electromechanical air, pass for fly to cut machine precision control analysis, have put forward some improvement methods of responding , deserve to refer to in actual design production, have put forward some kinds of fly to cut the new train of thought of machine design, for reference.Key words:Fly to cut machine Strong material Precision is controled Cutprecision目录引言 (1)1 任务的提出 (2)1.1飞剪机的工业作用和分类 (2)1.2飞剪机应满足的设计要求 (2)1.3飞剪机设计任务书 (2)2 飞剪机机构的选型 (3)2.1剪切机构的结构选型 (3)2.2飞剪机工作方式的选择 (3)3 飞剪机机械系统的设计 (6)3.1飞剪机系统设计总的要求 (6)3.2飞剪机基本参数的确定与选择 (6)3.2.1基本参数的确定 (7)3.2.2力能参数的计算 (9)3.2.3电动机功率选择 (11)3.2.4飞轮力矩的确定 (12)3.3齿轮的确定和齿轮间隙的清除 (14)3.3.1传动齿轮参数的确定 (14)3.3.2齿侧间隙的消除的方法和调整 (14)3.4剪切机构剪刃动点轨迹的运动分析与优化 (15)3.4.1曲柄式剪切机构剪刃动点轨迹计算式 (16)3.4.2剪切机构动点轨迹分析 (19)4 飞剪机气动系统的设计 (20)4.1飞剪机的启动对离合器性能的要求 (20)4.2飞剪机的制动特性对制动器的要求 (20)4.3飞剪机对气动系统的气压高低和稳定的要求 (20)谢辞 (23)参考文献 (24)引言飞剪机是在轧件运动中对轧件实施剪切工艺的一种设备,是连续式轧钢生产线上不可缺少的,非常关键的设备之一。
液压带锯式切断机毕业设计
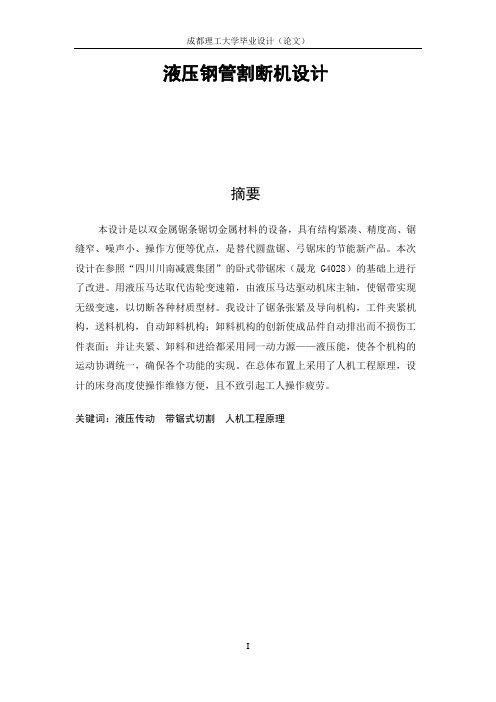
液压钢管割断机设计摘要本设计是以双金属锯条锯切金属材料的设备,具有结构紧凑、精度高、锯缝窄、噪声小、操作方便等优点,是替代圆盘锯、弓锯床的节能新产品。
本次设计在参照“四川川南减震集团”的卧式带锯床(晟龙G4028)的基础上进行了改进。
用液压马达取代齿轮变速箱,由液压马达驱动机床主轴,使锯带实现无级变速,以切断各种材质型材。
我设计了锯条张紧及导向机构,工件夹紧机构,送料机构,自动卸料机构;卸料机构的创新使成品件自动排出而不损伤工件表面;并让夹紧、卸料和进给都采用同一动力源——液压能,使各个机构的运动协调统一,确保各个功能的实现。
在总体布置上采用了人机工程原理,设计的床身高度使操作维修方便,且不致引起工人操作疲劳。
关键词:液压传动带锯式切割人机工程原理The design of Hydraulic steel pipecutting machineAbstractThe design is based on dual metal saw blade metal sawing equipment, has a compact, high precision, saw narrow slit, little noise, the advantages of easy operation, is a replacement disk sawing, bow sawing machine of new energy-saving products. The design to be according to ―Sichuan Chuanna n Absorber Group Limited‖ of the foundation of the lie type band saw bed (the Chenglong G4028) up carried on an improvement. Hydraulic motors to replace the gearbox, the motor-driven hydraulic machine spindle, Saw Band CVT, to cut off all material profile. We design and the influence of tension-oriented institutions, workpiece clamping, feed, automatic discharge; Discharge of innovative products enable automatic discharge without injury workpiece surface; and for clamping, Discharging and feed have the same power source -- Hydraulic can make all the campaign harmonization, ensure all functions. In general layout adopted the principle of human engineering, design height of the bed so that the operation and maintenance convenience and workers to operate without causing fatigue.Keywords:Hydraulic drive, E-store, Bandsaw-cutting, The man-machine engineering principle目录摘要 (I)ABSTRACT........................................................... I I 目录.............................................................. I II 第1章前言. (1)第2章方案设计 (1)2.1 初步方案选择 (2)2.1.1 问题的提出 (2)2.1.2 方案比较 (2)2.1.3 方案拟定 (3)2.2 切削力、切削功率的计算 (4)2.2.1初定锯带和锯带轮外形尺寸 (4)2.2.2 计算切削力、切削功率 (5)2.3 马达的选择 (6)第3章总体布局设计 (8)3.1 锯床设计方案简介 (8)3.2机床机构简图 (9)第4章锯梁的结构设计 (10)4.1 轴的设计 (10)4.1.1 强度设计 (10)4.1.2 结构设计 (12)4.1.3 轴承校核 (14)4.2 锯带轮的设计 (16)4.2.1 主动轮的结构设计 (17)4.2.2 从动轮的结构设计 (17)4.3 张紧装置的结构设计 (17)4.3.1 张紧原理 (17)4.3.2 张紧装置的结构设计 (18)4.4 导向装置的结构设计 (19)4.4.1 导向原理 (19)4.4.2 轴承选用 (19)第5章工件夹紧机构的设计 (20)5.1 夹紧原理 (20)5.2 结构设计 (20)5.3 液压缸的选择 (21)第6章送料装置的结构设计 (23)6.1 轨道的设计 (23)6.2 送料四轮小车的结构设计 (23)6.3 托料装置的设计 (24)6.4 其它附件设计 (24)第7章定尺装置和卸料装置的设计 (25)7.1 定尺装置的设计 (25)7.2 卸料装置的设计 (25)第8章进刀机构原理 (27)8.1 进刀原理示意图 (27)8.2 连接支座的设计 (27)8.3 液压缸的选择 (28)第9章床身和工作台的设计 (29)第10章液压控制系统的设计 (30)10.1 液压控制系统的要求及特点 (30)10.2 液压系统设计技术参数 (30)10.3 制定系统控制方案 (31)10.3.1 进刀机构快速回路方案 (31)10.3.2 顺序动作回路方案 (32)10.3.3 夹紧油缸的同步回路 (34)10.4液压系统的综合设计原理图 (36)10.5液压元件的选择 (38)10.5.1液压泵的选择 (38)10.5.2液压阀件的选择 (39)10.5.3 辅助元件微型液压站的选择 (40)第11章冷却系统的设计 (42)第12章附件设计 (44)12.1马达安装架的设计 (44)12.2 锯轮盖、箱门的设计 (44)12.3油盘和定尺挡块的设计 (44)结论 (45)致谢 (45)参考文献 (46)第1章前言在现代机器设备的结构中,为降低成本,大量采用型材,如圆钢、型钢、角钢、槽钢等。
机械专业切管机毕业设计论文

第一章绪论在机械制造、工程施工和建筑安装工作中, 钢管的传统切割方法主要是依靠手工锯割、锯床锯割、滚轮挤压、砂轮切割和气焊切割等。
这些钢管切割方法在不同程度上都存在着切割效率低、工人劳动强度大、工作环境差的缺点。
而且, 有的方法还存在着锥形切口(如滚轮挤压)、切口粗糙、凹凸不平(如气焊切割)、切削噪声大(如砂轮切割)、不易在现场施工作业等缺陷。
针对上述问题, 近年工厂来广泛采用高效自动切割机,她效率高、操作简便, 有的还能实现自动化,能够对不同管径、壁厚和材质的钢管进行切割的钢管切割机。
包钢的高效自动切管机是由武汉重型机床厂生产的一种专用钢管切断机床,广泛的应用于工业领域。
它是一种专用的切断机床,适用于大批量、自动或半自动的切断无缝钢管的头部和尾部,紧接着对切断后的两端进行倒角,机床的刚度大,功率大,自动化程度高,生产效率也高,是无缝钢管厂的必要设备,在生产无缝钢管的工艺中起着精整地作用。
其年钢管切头量为40万吨,切断后管子断面可自动倒内角外角或切大坡口。
装上镗孔辅件后也可以镗0、3、5、7、11、14、五种角度及各种规格管径的锥空口。
机床有切头自动定长检测装置,可以完成经冷锯切断后的管端平端面。
倒内角的工作分为手动、半自动、全自动。
该切管机通过机—电—液一体化的设计与综合,能够实现自动化控制,而且在其生产过程中效率高,操作方便、快捷,该设备广泛应用于无缝钢管的生产领域,因此对该设备的性能和生产工艺过程的掌握显得无比重要。
该设备是在原有的半自动切管机的基础上改造而成。
经改造后的切管机的执行元件由液压站提供动力源。
在工作现场除了清理切削铁屑的工人,整个过程可在电气,液压的控制下实现自动切割钢管的动作。
操作方便,快捷,大大提高了生产效率。
如加工直径为102mm的钢管,每小时可达130根;加工直径245mm的钢管,每小时为68根。
该切割机的特点是:该机床的执行元件全部采用液压传动。
由油缸顺序动作来完成切割过程。
切割机的设计范文
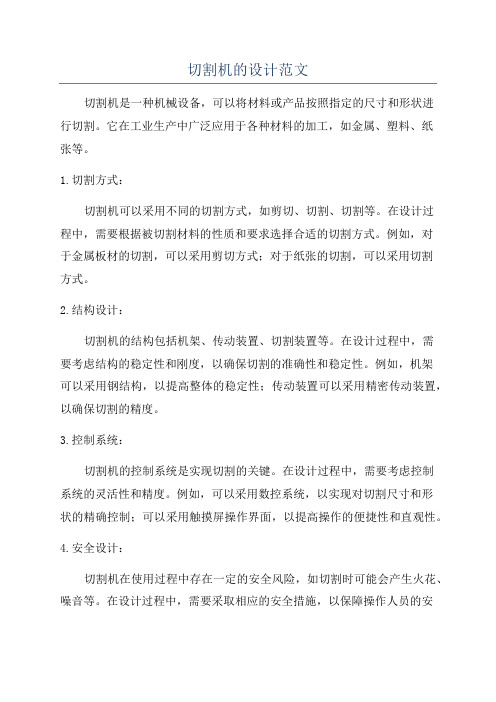
切割机的设计范文切割机是一种机械设备,可以将材料或产品按照指定的尺寸和形状进行切割。
它在工业生产中广泛应用于各种材料的加工,如金属、塑料、纸张等。
1.切割方式:切割机可以采用不同的切割方式,如剪切、切割、切割等。
在设计过程中,需要根据被切割材料的性质和要求选择合适的切割方式。
例如,对于金属板材的切割,可以采用剪切方式;对于纸张的切割,可以采用切割方式。
2.结构设计:切割机的结构包括机架、传动装置、切割装置等。
在设计过程中,需要考虑结构的稳定性和刚度,以确保切割的准确性和稳定性。
例如,机架可以采用钢结构,以提高整体的稳定性;传动装置可以采用精密传动装置,以确保切割的精度。
3.控制系统:切割机的控制系统是实现切割的关键。
在设计过程中,需要考虑控制系统的灵活性和精度。
例如,可以采用数控系统,以实现对切割尺寸和形状的精确控制;可以采用触摸屏操作界面,以提高操作的便捷性和直观性。
4.安全设计:切割机在使用过程中存在一定的安全风险,如切割时可能会产生火花、噪音等。
在设计过程中,需要采取相应的安全措施,以保障操作人员的安全。
例如,可以采用防护装置,将切割区域与操作人员隔离;可以采用减震装置,以减少噪音的传播。
5.维护和保养:切割机在长时间运行后,可能会出现一些故障和损坏。
在设计过程中,需要考虑设备的易维护性和易保养性。
例如,可以设计可拆卸的切割装置,以方便更换和维修;可以提供操作手册和维护手册,以指导操作和维护。
总之,切割机的设计需要综合考虑切割方式、结构设计、控制系统、安全设计和维护保养等方面的因素。
只有在满足切割要求的同时,保证设备的稳定性、安全性和可维护性,才能设计出一台性能卓越的切割机。
新型管材自动切割机的设计

新型管材自动切割机的设计【摘要】管材在各行业被大量的使用,其切割的人工操作普遍存在效率低、精度差,影响着相关产业的发展与生产能力。
新型管材切割机主要针对送料装置、夹紧装置、切割装置、控制系统,以及整机结构进行了设计。
送料、夹紧、切割等动作均通过编程自动控制,改善了中小型企业一直以来手动送料切割的难题。
对提升管件切割效率、提高切割精度、保证切割安全和实现管材切割的自动化有重要的促进作用。
【关键词】管材;切割;自动0 引言管材在各行业被大量使用,而下料工序是管材后续加工工序的基础,下料工序精度、效率的高低直接影响到产品质量的好坏及成本的高低。
管子定长切割加工,主要是将管子切割成要求的长度。
目前的管件切割方式如果还处在手工送料、手工取件的方式,将远远满足不了当今高速发展的机械、造船、军工、石油化工、能源、车辆制造、航空航天等工业需要。
因此,实现切割送料自动化显的十分重要。
通过机械传动或电气控制,按一定的规律自行完成人们所要求一系列动作,既可改善劳动条件、减轻工人劳动强度,确保生产安全,提高生产效率和产品质量,而且还能降低原材料消耗,节省设备投资,降低生产成本。
实现管件切割的自动化,是提升管件切割效率、提高切割精度和保证切割安全的根本途径和措施。
1 设计要求1.1 总体布置设计要求工作过程连续和流程;切割效率高;切割精读高,稳定性强;适用于多种不同尺寸、外形的管件切割;结构紧凑,层次分明;操作、维修、调整方便;寿命长,外形美观。
1.2 总体主要参数的确定被切割管件的原长不大于12m;圆管直径范围15~50mm;矩形管高≤200mm,宽≤35mm;管件最大切割长度为2m;工作台主轴离地面高度为0.8m。
2 总体设计及各部分工作原理2.1 总体设计1.滚轴;2.滚轴固定座;3.步进电机;4.联轴器;5.轴承透盖;6.轴承座;7.导轨;8.丝杆;9.移动气动夹具;10.夹具活塞;11.夹具滚轴;12.砂轮防护罩;13.砂轮;14.砂轮导轨;15.定位板;16.两个固定气动夹具总体结构简图如图1所示。
液压冲击式棒料快速切割机设计

应 的电液伺服阀 的特性 最好 。 ( 2 ) 由于 电液 伺服 阀 的固定节 流孔 结构 尺 寸本 来就较小 ,因此在加工过程中很 容易造成误差 ,即使 是 细微 的误差都将对伺服 阀的特性造成影响 。建议 提 高加工精度。 ( 3 )通 过 试验 验 证 了流 场 数值 模 拟 的正 确 性 , 得 出了不 同组合情况下 的流量系数 ,为伺服 阀节流孔 设计 提供 了理论依据 。
缓 冲由缓 冲油缸 3和 可调节缓 冲垫 4组 成。 图 4
送料 系统工作过程如下 :首先调整送料油缸指定 行程 ,装入棒料后 ,动夹抓夹紧棒料前进到指定切割
长度 ,然后 静夹抓 夹 紧固定住 棒料 ,进 而切 割棒料 ,
切割完成后 动夹抓 松开返 回,再次夹 紧送料 ,往复循
环 送 料 、切 割 。
场分析 及 结 构 优 化 [ J ] . 机床与液压, 2 0 1 1 , 3 9( 1 3) :
1 28 一 】 3 0.
参 考 文献 :
【 1 】 苏东海 , 任 大林 , 杨京兰. 电液 比例 阀与 电液伺服 阀性能 比较及前景展望 [ J ] . 液压气动与密封 , 2 0 0 8 ( 4 ) : 1 — 4 . 【 2 】 方群 , 黄增 . 电液伺服 阀的发展历史 、 研究现状及发展趋
H R C 5 4~ 5 6 ,具 有较好 的韧性和抗 冲击 性能 。如 图 3
送料系统 由送料油缸 、动夹抓 、静 夹抓 、位移传
感器 S 1 和s 2 、电磁换 向阀 v 2 ,V 3 ,v 7 ,V 9和手动
所示 ,锤 头 1的行程手 动调节装置用来调节锤头活塞 杆的行程 ,以控制活塞杆 的剪切动能 。当需要切 割直 径较小棒料时 ,行程调小 ;切割大直径棒料 ,行程调
棒料切割机设计

毕业设计(论文)设计(论文)题目:棒料切割机系别:机械工程系专业:机械制造/计算机班级:学号:姓名:引言机电一体化产品广泛应用各种加工业,切割技术也有了飞速的发展,手工切割已经适应不了现代工业发展的要求。
同时,切割机的夹紧机构也有了迅速的发展,一些简单的机械手已经得到广泛的应用。
简单的机械手经过几十年的发展,如今已进入以通用机械手为标志的时代。
几十年来,这项技术的研究和发展一直1比较活跃,设计在不断的修改,品种也在不断的增加,应用领域也在不断的扩大。
简单的机械手是一种仿人操作、自动控制、的机电一体化自动化生产设备。
特别适合于多品种、变批量的柔性生产。
它对稳定、提高产品质量,提高生产效率,改善劳动条件和产品的快速更新换代起着十分重要的作用。
我们设计的铸棒线切割机结构简单,性能安全可靠,操作方便可行,很好的实现了其预定功能。
铸棒线切割机主要由三个大的部分组成,即切割部分、夹紧部分和纵横行走部分。
切割部分是由电极带动砂轮旋转,由气缸控制砂轮上下移动完成切割。
夹紧部分主要采用了一个气动夹紧机械手,电磁阀控制气缸活塞的伸缩来实现夹紧和放松。
纵横行走部分是由气缸控制纵向、横向行走板,使之沿直线导轨前进或返回。
整个机器由PLC控制各个气动换向阀的电磁铁,由气缸驱动完成顺序切割动作过程。
而随动工作台的随动前进速度也可以通过夹紧机械手夹紧铸棒使之与铸棒速度同步。
横向切割时的切割速度可以通过气缸来调节。
与一般的切割机相比,这种切割机有以下优点:一、实现了机械工程和自动控制的有效结合,机械部分采用机械优化设计,整个设计过程中都进行了综合技术比较与经济评价,实现了预定的功能。
二、整个运动过程都采用了气压传动控制,与液压传动相比,气压传动有无介质费用、处理方便、无泄露污染、无介质变质等优点。
三、在设计过程中,纵横行走装置采用了直线导轨,既提高了运动系统的运动精度,又很大程度的减小了摩擦力,达到了节能的效果。
四、整个切割过程都由PCL控制,以其结构简单合理、设备性能良好、使用寿命长、安全系数高等因素,满足了自动化大批量的生产要求。
自动钢管无屑切割机的研究与设计

摘要本文在详细分析钢管无屑切断特点的基础上,基于金属塑性加工原理,开发了一种钢管无屑切割机,主要进行了无屑滚切原理分析、无屑切割机总体方案以及机械结构设计和计算,无屑切割机虚拟样机设计。
提出了一种创新的无屑切割机构,选择了新型的直线电机传动方法并设计了整机的自动控制系统,最佳地满足了钢管定尺度的无屑切割工艺要求。
钢管切割的传统机械生产加工工艺大多应用切削加工方法来制造有精确的尺寸和形状要求的零件,生产过程中坯料的30%以上成为切屑,这不仅浪费大量的材料和能源,而且占用大量的机床设备和人力。
采用无屑滚切的工艺,工件不需要或只需要少量切削加工即可,大大节约了材料、设备和人力。
在结构设计上,使用Pro/E软件建立了切管机机械系统的三维实体模型和力学模型,分析和评估了系统的性能,从而为物理样机的设计和制造提供了参考依据。
通过利用虚拟样机技术,从设计的初始阶段——概念设计阶段就对整体系统进行了完整的分析,观察并试验了各组成部件的相互运动情况,使用系统仿真插件在各种虚拟环境中真实地模拟系统的运动,直接在计算机上修改设计缺陷,仿真试验不同的设计方案,对整个系统不断的改进,最后获得最优化的设计方案。
本文在研究了钢管无屑切割机结构特点的基础上依托Pro/E软件为平台,实现了无屑切管机的可视化、自动化和参数化设计。
系统地提高了设计、三维造型的效率和准确性。
实现了设计计算、数据修正、三维造型与绘制工程图纸的有机结合,同时也为同类产品的设计提供了有益参考。
在动力、传动、控制方面,根据直线电机的结构特点、性能优势和控制特性配合PLC控制,设计出结构紧凑、动态响应快、精度高、振动和噪声小、节能、高效的切管机系统。
本文通过选用两台直线电机成功地解决了切管机系统中定位、卸料和进给的直线运动问题。
关键词:切管机;无屑滚切;系统设计;PLC控制;虚拟样机IAbstractOn the basis of the characteristic analysis of steel pipe chip-less cutting, the paper develops a steel pipe chip-less cutting machine, basing on the principium of plastic working of metals. Mainly on the analysis of the principle of chip-less of hobbing, chip-less cutting machine general planning and mechanical structure design and calculation, virtual prototype design of chip-less cutting machine, put forward an innovative cutting Chip-less agencies, Select a new type of linear motor drive method and design the machine's automatic control system, meet the requirements of chip-less cutting of set-scale steel pipe at best.The traditional mechanical processing technology of steel cutting mainly is the method of cutting to The manufacture precise size and shape parts as required, more than 30% of the billet quality turns into chip in this production process. This is not only a waste of a large number of materials and energy and use up a lot of machine and human. If chip-free cutting process was used, work piece will became mechanical parts with only a little cutting or none, which greatly saving materials, equipment and human.In structural design, we have established a pipe cutting machine mechanical system of three-dimensional solid model and the mechanical model, analysis and assessment of the performance of the system with Pro/E software, so as to provide a reference to physical prototype design and manufacturing. Through the use of virtual prototyping technology, from the initial stages of design - conceptual design phase of the overall system on a complete analysis of observation and test the various components of the mutual movement of components, plug-ins using the system simulation environment in a variety of virtual real simulate the movement system directly on the computer modify the design defects, simulation experiment with different design, the entire system of continuous improvement, and finally obtain the optimal design, for the manufacture of the physical prototype of the fully prepared to do. This paper realize the visualization, automation and parameters in chip-less pipe cutting machine design based on Pro/E software after studied the structural characteristics of chip-less steel pipe cutting machine. Improved the efficiency and accuracy systematically in design, three-dimensional modeling. Achieved a seamless integration between design, calculation, data amendment, three-dimensional modeling and engineer drawing, as well as provided a useful reference to the design of similar products at the same time.About power, transmission, control, design a fast, dynamic response and high precision, according to the structure of linear motor characteristics, performance characteristics and control with the advantages of PLC control, which is small vibration and noise, energy saving, efficient system of pipe cutting machine. In this paper, by using two linear motors have successfully IIresolved the pipe cutting machine positioning system, and discharge into the problem to the linear motion.Key words: Pipe cutting machine; Chip-less cutting; System design; PLC control; Virtual prototypeIII目录摘要 (I)Abstract ................................................................... II 目录 (IV)第一章绪论 (1)1.1 课题提出背景及研究的目的和意义 (1)1.1.1 选题背景 (1)1.1.2 研究目的和意义 (1)1.2 切管工艺与设备技术发展综述 (2)1.2.1 切管机的种类 (3)1.2.2 国内外切管机及技术的发展概况 (3)1.3 课题研究的主要内容 (5)第二章无屑滚切的原理 (7)2.1 无屑滚切的工艺过程 (7)2.2 无屑滚切的工艺特点 (8)2.3 工艺参数分析计算 (9)2.4 切削功率的理论计算 (12)2.4.1 理论假设 (12)2.4.2 正压力的理论计算 (12)2.4.3 摩擦面积的理论计算 (13)2.4.4 切削功率的理论计算 (13)第三章系统方案设计 (15)3.1 功能要求 (15)3.2 功能分析 (16)3.3 功能方案综合 (16)3.3.1 柔性进给 (16)3.3.2 刚性进给 (18)第四章结构设计与计算 (20)4.1 刀架组合的设计计算 (21)4.1.1 刀轴 (21)4.1.1.1 刀轴的材料 (21)4.1.1.2 刀轴的强度、刚度校核计算 (22)4.1.1.3 刀轴的振动稳定性校核计算 (23)4.1.2 刀片的设计计算 ................................................ 25 IV4.2 进刀与退刀机构的设计计算 (28)4.2.1 径向进给导轨的设计计算 (29)4.2.2 轴向运动转化为径向运动的结构设计 (31)4.2.3 轴向运动与径向运动的组合设计 (33)4.3 定位与卸料装置的设计 (34)第五章传动系统设计 (36)5.1 主切削运动的传动 (37)5.2 进给运动的传动 (42)5.3 定位与卸料运动的传动 (46)第六章电气自动控制系统设计 (49)6.1 系统控制功能分析 (49)6.2 PLC介绍 (51)6.3 PLC的选型 (52)6.4 I/O地址分配及控制流程图 (53)第七章总结与展望 (56)参考文献 ................................................................... 57 VVI第一章绪论在钢材生产以及机械制造过程中,对管材按定尺长度要求进行切割是必不可少的加工工序。
棒料切割机的设计说明书

棒料切割机的设计说明书本文介绍了一种铸棒线切割机的设计,该机器采用了机械优化设计和气压传动控制,具有结构简单、控制方便、性能稳定、调节修改方便、生产率高等优点。
该切割机主要由切割部分、夹紧部分和纵横行走部分组成,整个切割过程都由PLC 控制。
与一般的切割机相比,该切割机的优点在于实现了机械工程和自动控制的有效结合,采用了直线导轨提高了运动系统的运动精度,同时也减小了摩擦力,达到了节能的效果。
该切割机具有广阔的应用前景。
连续铸造是一种先进的铸造方法,它的工作原理是将熔融的金属不断浇入结晶器中,然后从结晶器的另一端连续拉出铸件。
这种方法已经在国内外得到广泛应用,如连续铸锭和连续铸管等。
相比传统的铸造方法,连续铸造有以下优点:金属冷却迅速,结晶致密,组织均匀,机械性能较好;铸件上没有浇注系统的冒口,节约了金属,提高了收得率;简化了工序,减轻了劳动强度,所需生产面积也大为减少;易于实现机械化和自动化,提高了生产效率。
铸棒线割机是一种用于连续铸造的自动控制切割机,由PLC控制电磁阀,使气缸驱动切割部件对铸棒进行准确定长切割,并自动返回初始位置。
这种切割机具有控制方便、性能稳定、结构简单、调节和维修方便、生产率高等优点,具有广泛的应用前景。
本科毕业设计(论文)的目录包括引言、摘要、切割部分设计、夹紧部分设计、纵横行走部分设计和PLC概述等章节。
在切割部分设计中,需要考虑设计要求、方案设计和结构设计;在夹紧部分设计中,需要考虑设计要求和方案设计;在纵横行走部分设计中,需要考虑设计要求、方案设计和直线导轨的选择计算。
在PLC概述中,需要详细介绍PLC控制技术的应用。
在本科毕业设计中,我们选择了功率为3.0KW,满载时的转速为2870r/min,额定电流6.39A,功率因数0.87,效率82%,额定转矩2.3N m2的系列三相异步电动机。
这款电机的功率等级和安装尺寸与国外同类型的先进产品相当,因此具有很好的互换性,可以供配套出口或引进设备替换。
鹿文晓棒料切割机设计说明书3.22(1)(1)
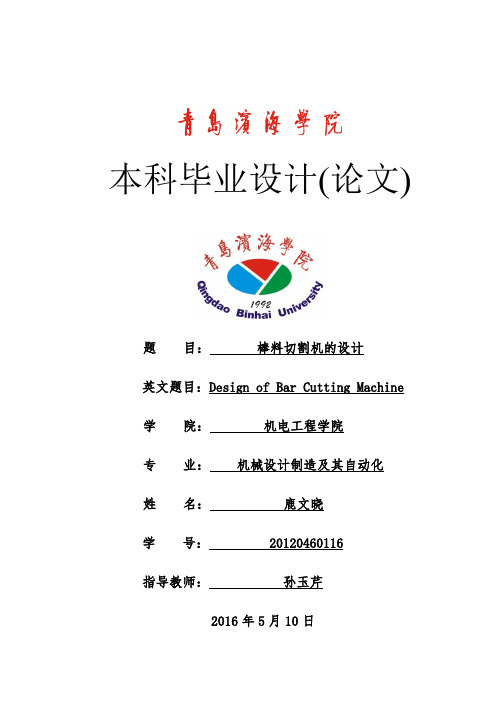
本科毕业设计(论文)题目:棒料切割机的设计英文题目:Design of Bar Cutting Machine学院:机电工程学院专业:机械设计制造及其自动化姓名:鹿文晓学号: ***********指导教师:***2016年5月10日毕业设计(论文)独创性声明该毕业设计(论文)是我个人在导师指导下进行的研究工作及取得的研究成果。
文中除了特别加以标注和致谢的地方外,不包含其他人或其他机构已经发表或撰写过的研究成果。
其他同志对本研究的启发和所做的贡献均已在论文中作了明确的声明并表示了谢意。
作者签名:日期:年月日毕业设计(论文)使用授权声明本人完全了解青岛滨海学院有关保留、使用毕业设计(论文)的规定,即:学校有权保留送交毕业设计(论文)的复印件,允许被查阅和借阅;学校可以公布全部或部分内容,可以采用影印、缩印或其他复制手段保存该毕业设计(论文)。
保密的毕业设计(论文)在解密后遵守此规定。
作者签名:导师签名:日期:年月日摘要:机械工业是一个国家的重要产业,机械工业的发展无时不刻都在影响着国家经济的发展,人类的进步离不开机械工业的发展。
在全球经济发展的大环境下,中国各个行业被其他国家的先进技术影响的同时,越来越多的外国企业和品牌传播到中国已经成为现实。
在新的市场需求的推动下,对棒料切割机进行改良和优化是当务之急。
生产棒料切割机的企业,必须充分考虑到在棒料切割机运行中可能出现的问题,尽量使棒料切割机的自动化程度越高越好,从而减少人工搬运工具的时间,国内棒料切割机的研发及制造要与全球号召的高效经济、安全稳定主题保持一致。
棒料切割机的发展与人类社会的进步和科学技术的水平密切相关。
设计的题目是棒料切割机的设计,目前,国内棒料切割机的研发也在向朝着运行高速化、功能复合化、控制智能化的方向发展,廉价、简单、方便成了工作台发展的主题。
关键词:机械产品棒料切割机智能化Abstract:This graduation design is the optimization design of driving roller conveyor, first on the driving roller type conveyer is summarized; then analyzed the selection principle and calculating method of driving roller conveyor; then calculated based on these design criteria and abase is designed; then checked on the main parts selected conveyor. Is the drive roller conveyor consists of four main parts: driving device, tension device, middle rack, and the moving part. Finally, a simple description of the installation and maintenance of transport. At present, the drive roller conveyor is moving towards long distance, high speed, low friction direction, air cushion conveyor in recent years is one of the. the motion trajectory when the diagonal curve is slanting line do the walking motion, robot. The miniature walking robot is mainly driven by DC servo motor, so as to drive the leg action driven synchronous belt wheel by a crank and rocker mechanism.In the design, driving roller type conveyer manufacture and application, at present our country compared with foreign advanced level there are still large gaps, domestic in the design and manufacture of driving .This design is the optimization design of driving roller conveyor.Keywords:Driving roller Crankshaft Processing intelligent目录1 前言 (1)1.1课题的来源与研究的目的和意义 (1)1.2本课题研究的内容 (3)1.3研究的意义 (4)2 棒料切割机总体结构的设计 (5)2.1切割部分设计方案的选择 (6)2.2切割部分的工作原理 (6)2.3 摆动杆的结构设计 (7)3 机械传动部分的设计计算 (8)3.1切割电机的选型计算 (8)3.2带传动的设计计算 (9)3.3直线导轨的设计计算 (11)3.4水平移动气缸在选型计算 (14)4 棒料切割机中主要零件的三维建模 (15)4.1切割锯片的三维建模 (15)4.2 V带轮的三维建模 (15)4.3气缸的三维建模 (16)4.4棒料切割机的三维建模 (16)5 棒料切割机中主要零件的强度分析与校核 (17)5.1滚动轴承强度的校核计算 (17)结论 (18)参考文献 (19)致谢 (20)1 前言1.1 课题的来源与研究的目的和意义我国生产的棒料切割机结构简陋,切割效率始终不高,虽然经过几十年的发展,近期产品的质量较早期有所提高。
棒料切割机
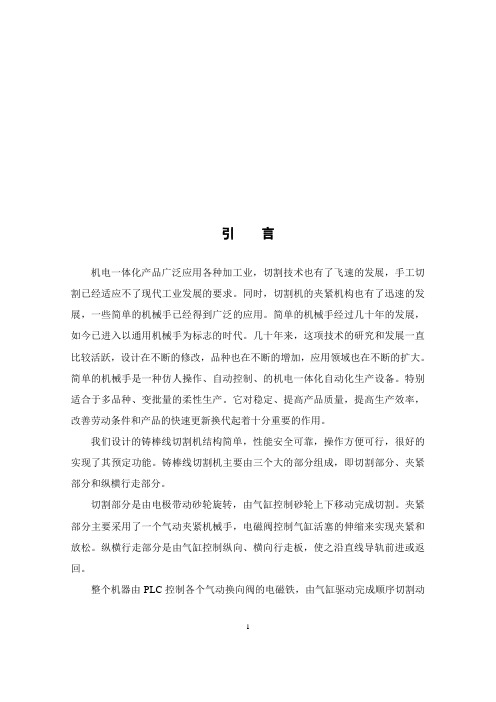
引言机电一体化产品广泛应用各种加工业,切割技术也有了飞速的发展,手工切割已经适应不了现代工业发展的要求。
同时,切割机的夹紧机构也有了迅速的发展,一些简单的机械手已经得到广泛的应用。
简单的机械手经过几十年的发展,如今已进入以通用机械手为标志的时代。
几十年来,这项技术的研究和发展一直比较活跃,设计在不断的修改,品种也在不断的增加,应用领域也在不断的扩大。
简单的机械手是一种仿人操作、自动控制、的机电一体化自动化生产设备。
特别适合于多品种、变批量的柔性生产。
它对稳定、提高产品质量,提高生产效率,改善劳动条件和产品的快速更新换代起着十分重要的作用。
我们设计的铸棒线切割机结构简单,性能安全可靠,操作方便可行,很好的实现了其预定功能。
铸棒线切割机主要由三个大的部分组成,即切割部分、夹紧部分和纵横行走部分。
切割部分是由电极带动砂轮旋转,由气缸控制砂轮上下移动完成切割。
夹紧部分主要采用了一个气动夹紧机械手,电磁阀控制气缸活塞的伸缩来实现夹紧和放松。
纵横行走部分是由气缸控制纵向、横向行走板,使之沿直线导轨前进或返回。
整个机器由PLC控制各个气动换向阀的电磁铁,由气缸驱动完成顺序切割动1作过程。
而随动工作台的随动前进速度也可以通过夹紧机械手夹紧铸棒使之与铸棒速度同步。
横向切割时的切割速度可以通过气缸来调节。
与一般的切割机相比,这种切割机有以下优点:一、实现了机械工程和自动控制的有效结合,机械部分采用机械优化设计,整个设计过程中都进行了综合技术比较与经济评价,实现了预定的功能。
二、整个运动过程都采用了气压传动控制,与液压传动相比,气压传动有无介质费用、处理方便、无泄露污染、无介质变质等优点。
三、在设计过程中,纵横行走装置采用了直线导轨,既提高了运动系统的运动精度,又很大程度的减小了摩擦力,达到了节能的效果。
四、整个切割过程都由PCL控制,以其结构简单合理、设备性能良好、使用寿命长、安全系数高等因素,满足了自动化大批量的生产要求。
棒料切割机设计毕业设计机械设计开题报告毕业论
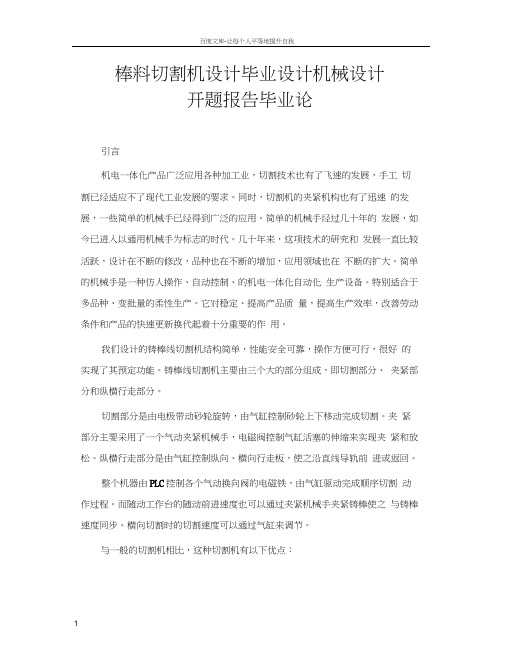
棒料切割机设计毕业设计机械设计开题报告毕业论引言机电一体化产品广泛应用各种加工业,切割技术也有了飞速的发展,手工切割已经适应不了现代工业发展的要求。
同时,切割机的夹紧机构也有了迅速的发展,一些简单的机械手已经得到广泛的应用。
简单的机械手经过几十年的发展,如今已进入以通用机械手为标志的时代。
几十年来,这项技术的研究和发展一直比较活跃,设计在不断的修改,品种也在不断的增加,应用领域也在不断的扩大。
简单的机械手是一种仿人操作、自动控制、的机电一体化自动化生产设备。
特别适合于多品种、变批量的柔性生产。
它对稳定、提高产品质量,提高生产效率,改善劳动条件和产品的快速更新换代起着十分重要的作用。
我们设计的铸棒线切割机结构简单,性能安全可靠,操作方便可行,很好的实现了其预定功能。
铸棒线切割机主要由三个大的部分组成,即切割部分、夹紧部分和纵横行走部分。
切割部分是由电极带动砂轮旋转,由气缸控制砂轮上下移动完成切割。
夹紧部分主要采用了一个气动夹紧机械手,电磁阀控制气缸活塞的伸缩来实现夹紧和放松。
纵横行走部分是由气缸控制纵向、横向行走板,使之沿直线导轨前进或返回。
整个机器由PLC控制各个气动换向阀的电磁铁,由气缸驱动完成顺序切割动作过程。
而随动工作台的随动前进速度也可以通过夹紧机械手夹紧铸棒使之与铸棒速度同步。
横向切割时的切割速度可以通过气缸来调节。
与一般的切割机相比,这种切割机有以下优点:一、实现了机械工程和自动控制的有效结合,机械部分采用机械优化设计,整个设计过程中都进行了综合技术比较与经济评价,实现了预定的功能。
二、整个运动过程都采用了气压传动控制,与液压传动相比,气压传动有无介质费用、处理方便、无泄露污染、无介质变质等优点。
三、在设计过程中,纵横行走装置采用了直线导轨,既提高了运动系统的运动精度,又很大程度的减小了摩擦力,达到了节能的效果。
四、整个切割过程都由PCL控制,以其结构简单合理、设备性能良好、使用寿命长、安全系数高等因素,满足了自动化大批量的生产要求。
DJ-01棒料切割机设计

DJ-01棒料切割机设计摘要本次设计主要做出了DJ-01棒料切割机切割部分、夹紧部分、纵横行走部分等机械部分,切割机的电气控制线路和PLC自动控制等控制部分,切割机的气压系统等传动部分的设计。
为了降低生产成本,提高生产效率要求切割机必须能够实现较高精度的定长切割,必须有较快的运动速度及运动精度,在这样的要求下我及我公司多位同仁的共同努力下,经过多次的实验改进终于做出了DJ-01这台较优秀的金属棒料切割机,它的工作是由PLC控制电磁阀,使电磁阀控制气缸,并由气缸驱动与其连接的部件,实现对棒料的准确定长切割,切割后自动返回初始位置。
一个切割机分别切割两条钨棒,其切口深度为35mm,然后由压断机进行压断。
从我们的实际使用情况来看这台机器操作简便,运行稳定、维护方便等优点,大大的提高了生产效率。
该产品性能良好,不但能切钨棒,还可以切割其他的金属棒料并且功耗小可以广泛应用。
关键词:自动控制,切割,PLCDJ-01 BAR CUTTING MACHINE DESIGNABSTRACTThis design made the DJ-01 main bar cutting machine to cut parts, clamping parts, mechanical parts such as vertical and horizontal moving parts, cutting machines electrical control circuits and PLC automatic control, control parts, cutting machine pneumatic systems, transmission parts design. In order to reduce production costs, improve production efficiency requirements cutting machine must be able to achieve higher precision fixed-length cutting, there must be a faster movement speed and movement precision, such a request in for me and my company the joint efforts of many colleagues, After several experiments to improve the DJ-01 has finally made this station a more excellent cutting machine metal sticks, which is handled by the PLC control solenoid valve, solenoid valve to control the cylinder by cylinder drive connected components, to achieve the accuracy of the bar fixed-length cutting, cutting back to initial position automatically. A cutting machine cutting two tungsten rods, respectively, the incision depth of 35mm, then the pressure off machine pressure off. From our perspective the actual use of the machine easy to operate, stable running, easy maintenance and so greatly improved the production efficiency. Good performance of the product, not only can cut tungsten rod, you can also cut the other Metal Rod and power consumption can be widely used.KEY WORDS: Automatic Control, cut, PLC目录前言 (1)第1章切割机的整体结构 (2)第2章切割部分设计 (3)2.1设计要求 (3)2.2 方案设计 (3)2.3 结构设计 (4)2.3.1 砂轮片的选取 (4)2.3.2 电机的选取 (4)2.3.3 带传动设计 (4)2.3.4 升降气缸的选择 (8)2.3.5滚动轴承的选取及校核 (10)第3章夹紧部分设计 (14)3.1设计要求 (14)3.2方案设计 (14)第4章纵横行走部分的设计 (16)4.1 4.1 设计要求 (16)4.2方案设计 (16)4.3 直线导轨的选择计算 (16)4.3.1 选定条件: (16)4.3.2 选择方式 (17)第5章控制部分的设计 (19)5.1 电气控制线路的设计 (19)5.2 气动原理图设计 (19)5.3 PLC自动控制电路设计 (21)5.3.1PLC的组成 (21)5.3.2 可编程控制器的特点 (22)结论 (24)谢辞 (26)参考文献 (27)附录 (28)外文资料翻译 ................................................... 错误!未定义书签。
棒料切割机的设计

目录摘要 (1)关键词 (1)Abstract: (1)Key words: (1)引言 (2)1概述 (2)1.1 选题背景 (2)1.2 研究意义 (2)2 切割部分设计 (3)2.1 切割部分设计要求 (3)2.2 切割部分设计方案 (3)2.3 切割部分工作原理 (4)2.4 切割部分结构设计 (5)2.4.3 带传动设计 (5)2.4.4 升降液压缸的设计 (8)2.4.5 滚动轴承的选取及校核 (12)3 夹紧部分设计 (14)3.1 夹紧机构设计要求 (14)3.2 夹紧部分方案设计 (14)4 纵横行走部分的设计 (15)4.1 纵横行走装置设计要求 (15)4.2 纵横行走部分方案设计 (15)4.3 直线导轨的选择计算 (15)4.3.1 选定条件 (15)4.3.2 选择方式 (15)5 液压传动系统设计 (17)5.1液压传动机构 (17)5.2 液压传动原理图 (17)6 电气控制的设计 (18)6.1 电气控制设计要求 (18)6.2 电气控制设计方案 (18)6.3 可编程控制器PLC控制流程 (19)7 结论 (19)附录A—PLC I/O端口分配图 (21)附录B—棒料切割机装配图 (21)致谢 (23)棒料切割机的设计棒料切割机的设计机械电子专业学生韦忠爽指导教师闫冰洁摘要:通过对切割过程的观察和研究,本课题采用了机电一体化系统设计思想,对其整体造型、机械结构和控制系统进行设计,此棒料切割机电一体化系统主要由四个部分组成:机械本体、电子控制单元、执行器和动力源。
工作原理是电动机通过带传动带动切割片做高速旋转运动,电机与工作台之间采用铰支撑方式,升降液压缸可推动切割片进行上下移动带动刀片完成顺序切割动作。
切割机采用PLC控制各个液压换向阀的电磁铁,实现棒料的自动下料和切割以及检测工作。
随动工作台前进速度也可以通过夹紧机械手夹紧棒料使之与棒料速度同步。
横向切割时的切割速度可以通过液压缸来调节。
- 1、下载文档前请自行甄别文档内容的完整性,平台不提供额外的编辑、内容补充、找答案等附加服务。
- 2、"仅部分预览"的文档,不可在线预览部分如存在完整性等问题,可反馈申请退款(可完整预览的文档不适用该条件!)。
- 3、如文档侵犯您的权益,请联系客服反馈,我们会尽快为您处理(人工客服工作时间:9:00-18:30)。
棒料切割机的设计设计专业论文目录摘要 0关键词 0Abstract: 0Key words: (1)引言 (1)1概述 (1)1.1 选题背景 (1)1.2 研究意义 (2)2 切割部分设计 (2)2.1 切割部分设计要求 (2)2.2 切割部分设计方案 (3)2.3 切割部分工作原理 (4)2.4 切割部分结构设计 (4)2.4.3 带传动设计 (4)2.4.4 升降液压缸的设计 (8)2.4.5 滚动轴承的选取及校核 (11)3 夹紧部分设计 (13)3.1 夹紧机构设计要求 (13)3.2 夹紧部分方案设计 (13)4 纵横行走部分的设计 (14)4.1 纵横行走装置设计要求 (14)4.2 纵横行走部分方案设计 (14)4.3 直线导轨的选择计算 (15)4.3.1 选定条件 (15)4.3.2 选择方式 (15)5 液压传动系统设计 (16)5.1液压传动机构 (16)5.2 液压传动原理图 (17)6 电气控制的设计 (17)6.1 电气控制设计要求 (17)6.2 电气控制设计方案 (18)6.3 可编程控制器PLC控制流程 (18)7 结论 (19)附录A—PLC I/O端口分配图 (21)附录B—棒料切割机装配图 (21)致谢 (23)棒料切割机的设计机械电子专业学生韦忠爽指导教师闫冰洁摘要:通过对切割过程的观察和研究,本课题采用了机电一体化系统设计思想,对其整体造型、机械结构和控制系统进行设计,此棒料切割机电一体化系统主要由四个部分组成:机械本体、电子控制单元、执行器和动力源。
工作原理是电动机通过带传动带动切割片做高速旋转运动,电机与工作台之间采用铰支撑方式,升降液压缸可推动切割片进行上下移动带动刀片完成顺序切割动作。
切割机采用PLC控制各个液压换向阀的电磁铁,实现棒料的自动下料和切割以及检测工作。
随动工作台前进速度也可以通过夹紧机械手夹紧棒料使之与棒料速度同步。
横向切割时的切割速度可以通过液压缸来调节。
现场运行情况表明,此切割机具有动作快、运动平稳以及与计算机联机方便等优点,能够降低工人的劳动强度,实现自动控制,提高劳动生产率。
关键词:切割机;机电一体化;液压;棒料;PLC控制Design of Bar Cutting MachineStudent majoring in mechanical and electronic engineering Name WeiZhongshuangTutor Yan BingjieAbstract:Based on the research of the cutting process, this subject adopts mechanical and electrical integration of system design idea, the overall modeling, mechanical structure and control system design, bar stock cutting the mechanical andelectrical integration system is mainly composed of four parts: the basic machine, electronic control unit, actuators, and power supply. Working principle is the motor drives the cutting piece of high-speed movement, motor and adopts the hinged support method between the workbench, a falling cylinder can be driven to move up and down push cutting disc blade cutting action completed order, each hydraulic cutting machine adopts PLC control reversing valve electromagnet, implement automatic cutting and blanking bar work and tests. And servo table speed can also be through the clamping manipulator clamping bar to that of the bar speed synchronization. Transverse cutting when the cutting speed can be adjust by hydraulic cylinder. Field operation shows that, the design of the cutting machine is fast, smooth movement, and convenient with computer on line, it can improve the labor intensity of workers, to achieve automatic control, improve labor productivity.Key words:Cutting machine; Mechanical and electrical integration; Hydraulic pressure; bar; PLC control引言当今时代正是中国发展的黄金时代,中国又是一个发展中国家,要想谋求更大的发展,行业的转型是一定的,所以轻工业的转型,重工业与机械制造的行业的重视是必然的。
就这一点来看,让我们清晰看到机械行业的发展前景有着如此大的潜力。
它与其他行业有着千丝万缕的联系,随着经济的发展和科技的进步,越来越多的产品智能化、自动化、网络化,单纯的机械已经不能适应行业发展的需要,渐渐地就出现了机电一体化。
现代机械的机电一体化的目标是综合利用机、电、信息、控制等各方面的相关技术的优势[1],扬长避短以达到系统优化的效果,取得显著地社会效益和技术经济效益。
1概述1.1 选题背景机电一体化产品广泛应用各种加工业,切割技术也有了飞速的发展,手工切割已经适应不了现代工业发展的要求。
如今已进入以通用机械时代。
几十年来,切割技术的研究和发展一直比较活跃,设计在不断的修改,品种也在不断的增加,应用领域也在不断的扩大。
而目前市面上有很多型号的棒料切割机结构复杂,调节,维修不方便,生产效率低,智能化低等不足。
1.2 研究意义本棒料切割机的切割机构属于机械技术领域,它解决了现有的自动切割机所存在的精度不高,操作复杂,智能化低等问题。
本课题针对目前市场上的切割机设计的不足,对棒料切割机进行改造创新,增加智能化程度,设计出具有控制方便,性能稳定,结构简单,调节、维修方便,安全可靠,低能耗,在切割过程中能使棒料位置稳定、切割长度准确,生产率高,运行平稳,提高产品质量,提高生产效率等优点的具有广泛应用前景的方案。
与一般现在市面上的切割机相比,本次设计的这种切割机有以下优点:1)实现了机械工程和自动控制的有效结合,机械部分采用机械优化设计,整个设计过程中都进行了综合技术比较与经济评价,实现了预定的功能。
2)整个运动过程都采用了液压传动控制,与气压传动相比,液压传动有可在大范围内实现无级调速;液压传递运动均匀、平稳;易于实现过载保护等优点。
3)在设计过程中,纵横行走装置采用了直线导轨,既提高了运动系统的运动精度,又很大程度的减小了摩擦力,达到了节能的效果。
4)整个切割过程都由PCL 控制,以其结构简单合理、设备性能良好、生产率高、安全系数高等因素,满足了自动化大批量的生产要求。
所设计的棒料切割机,融合了液压自动控制、机器人技术和PLC 控制技术。
PLC 控制各个液压换向阀的电磁铁,由液压缸驱动机械手完成顺序切割过程,实现了机械设计、电器控制和液压传动控制的有效结合。
此棒料切割机是一种既能有效的提高生产率,又在价格和使用方面能被广大用户所接受的一种新型的自动控制切割机。
2 切割部分设计2.1 切割部分设计要求为了保证棒料的剪断,剪应力应超过材料的许应剪应力][τ,即切断棒料的条件为: []Q Aττ=≤ (2-1) 查资料可知棒料的许用剪应力为:[]MPa 285~128=τ,取最大值MPa 285。
由于本切断机切断的最大棒料粗度为:mm d 35max =。
则本机器的最小切断力Q 由(2-1)得:[]274063N43514.3285422m ax >⨯⨯=⨯>Q d Q πτ取切割机的N Q 280000=项目设计采用机电一体化设计思想,要求棒料切割机采用PLC 对棒料的切割过程及检测进行自动控制,并能根据PLC 定长信号分别切割两条连续的棒料,完成了系统的硬件和软件设计后可以实现对棒料的准确定长切割,切割后自动返回初始位置。
原始棒料尺寸范围在角钢:10100100⨯⨯ 圆钢:50φ≤ 槽钢:120x53 钢管:6135⨯φ,切割成m l ~0.1之间的棒料,其切口深度为35mm ~ 5,再用压断机进行压断处理。
2.2 切割部分设计方案切割部分主要有砂轮切片、电动机和传动机构组成。
现在设计的在切割部分有两种方案可行:第一,电动机通过带传动带动切割片转动。
第二,电动机通过圆锥齿轮传动方式带动切割片转动。
但考虑到切割过程中电动机带动切割片进行高速旋转运动,所以优先选取第一种方案,原因是圆锥齿轮传动不宜应用在转速太高的场合,并且在运用齿轮进行传动时,还应考虑怎样消除震动和用什么方法润滑齿轮,这样就会使设计成本增加,而带传动则具有结构简单,传动平稳、价格低廉和缓冲吸振等优点。
切割部分结构如图2-1所示。
图2-1 切割部分结构图1-电动机;2-升降液压缸;3-砂轮片;4-支撑板;5-传送带2.3 切割部分工作原理切割部分的原理如图2-2所示,电动机带动割切片高速旋转运动,电机与工作台之间采用铰链支撑方式,升降液压缸可推动切割片进行上下移动,完成切割运动。
横向行走液压缸可推动工作台横向移动,控制切割的长度。
纵向行走液压缸可使工作台纵向移动,使切割片能切割两根棒料。
其中电动机和液压缸电磁阀都需要通过由PLC 机控制,实现其按照顺序完成动作。
图2-2 切割部分原理简图1-带轮;2-传送带;3-电机;4-砂轮;5-升降液压缸;6-进料道;7-横向行走板;8-夹具;9-待加工棒料;10-横向行走液压缸;11-纵向行走板;12-纵向行走液压缸2.4 切割部分结构设计2.4.1 切割片的选取 设计任务所需电机的最小功率为KW P 2.2min =,主轴转速:2800r.p.m 条件下,轮片的最大线速度为s m /40。