生产线平衡 PPT
合集下载
《生产线平衡》课件

优化路径规划
对生产线上的作业要素进行路径规划,减少重复行走和等待时间,降低能耗和生 产成本。
提高作业要素的效率
培训与技能提升
对生产线上的作业人员进行培训和技能提升,提高其操作熟 练度和工作效率。
引入激励机制
建立有效的激励机制,激发作业人员的工作积极性和创造力 ,提高生产效率。
引入自动化设备
自动化设备的应用
。
谢谢聆听
引入先进的自动化设备,如机器人、 自动化流水线等,提高生产线的自动 化水平,降低人工成本和出错率。
技术升级与改造
对现有生产线进行技术升级与改造, 实现数字化、智能化生产,提高生产 效率和产品质量。
04 生产线平衡的实践案例
案例一:某汽车制造企业的生产线平衡优化
要点一
总结词
要点二
详细描述
通过生产线平衡优化,提高生产效率,降低生产成本。
计算方法
生产线平衡率 = (最短作业要素时间 / 平 均作业要素时间)× 100%。
B
C
影响因素
生产线平衡率受到作业要素周期时间、作业 要素负荷率等多种因素的影响。
优化方法
通过调整作业要素的分配、改进作业方法等 措施,可以提高生产线平衡率,降低生产成 本。
D
作业要素周期时间
作业要素周期时间
指完成一个作业要素所需的时间。它 是生产线平衡评估的重要指标之一。
计算方法
作业要素周期时间 = (作业要素时 间 / 总作业要素数)× 100%。
影响因素
作业要素周期时间受到设备性能、作 业方法、作业环境等多种因素的影响 。
优化方法
通过改进设备、优化作业方法、提高 作业效率等措施,可以缩短作业要素 周期时间,提高生产效率。
对生产线上的作业要素进行路径规划,减少重复行走和等待时间,降低能耗和生 产成本。
提高作业要素的效率
培训与技能提升
对生产线上的作业人员进行培训和技能提升,提高其操作熟 练度和工作效率。
引入激励机制
建立有效的激励机制,激发作业人员的工作积极性和创造力 ,提高生产效率。
引入自动化设备
自动化设备的应用
。
谢谢聆听
引入先进的自动化设备,如机器人、 自动化流水线等,提高生产线的自动 化水平,降低人工成本和出错率。
技术升级与改造
对现有生产线进行技术升级与改造, 实现数字化、智能化生产,提高生产 效率和产品质量。
04 生产线平衡的实践案例
案例一:某汽车制造企业的生产线平衡优化
要点一
总结词
要点二
详细描述
通过生产线平衡优化,提高生产效率,降低生产成本。
计算方法
生产线平衡率 = (最短作业要素时间 / 平 均作业要素时间)× 100%。
B
C
影响因素
生产线平衡率受到作业要素周期时间、作业 要素负荷率等多种因素的影响。
优化方法
通过调整作业要素的分配、改进作业方法等 措施,可以提高生产线平衡率,降低生产成 本。
D
作业要素周期时间
作业要素周期时间
指完成一个作业要素所需的时间。它 是生产线平衡评估的重要指标之一。
计算方法
作业要素周期时间 = (作业要素时 间 / 总作业要素数)× 100%。
影响因素
作业要素周期时间受到设备性能、作 业方法、作业环境等多种因素的影响 。
优化方法
通过改进设备、优化作业方法、提高 作业效率等措施,可以缩短作业要素 周期时间,提高生产效率。
生产线平衡分析课件
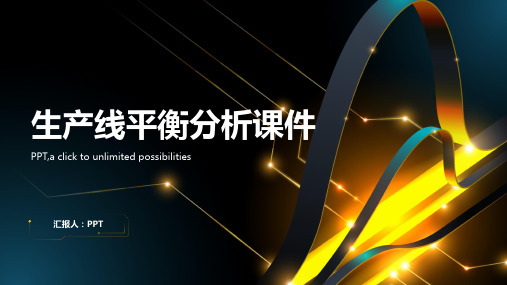
生产线平衡分析课件
PPT,a click to unlimited possibilities
汇报人:PPT
目录
01 添 加 目 录 项 标 题 03 生 产 线 平 衡 分 析 方 法 05 生 产 线 平 衡 优 化 策 略 07 生 产 线 平 衡 案 例 分 析
02 生 产 线 平 衡 概 述 04 生 产 线 平 衡 评 价 指 标 06 生 产 线 平 衡 实 施 步 骤
平衡率指标
定义:平衡率指标是指生产线各工 序时间与瓶颈工序时间的比值
意义:平衡率指标用于衡量生产线 平衡程度,即生产线各工序时间分 布的均匀程度
添加标题
添加标题
添加标题
添加标题
计算方法:平衡率 = (各工序时间 总和 / 瓶颈工序时间) × 100%
改善方向:通过调整生产线各工序 的作业时间,降低瓶颈工序时间, 提高平衡率指标,以实现生产效率 的提升
确定需要收集的数 据和信息类型
确定数据和信息来 源
制定收集计划和时 间表
确保数据和信息的 准确性和完整性
进行分析和评估
确定生产线的瓶颈工序 分析生产线的平衡状况 制定平衡改善方案 实施平衡改善方案并进行评估
制定改进措施并实施
根据分析结果,制定针对性的改进措施 确定改进措施的优先级和实施顺序 制定详细的实施计划和时间表 确保改进措施得到有效执行和监控
明确分析目标:确定生产 线平衡的目标和范围
收集数据:收集生产线上 的相关数据,包括设备、 人员、时间等
流程图绘制:根据收集的 数据绘制流程图,展示生 产线的运行过程
平衡点确定:根据流程图 确定生产线上的平衡点, 即瓶颈工序
平衡方法选择:根据平衡 点选择合适的平衡方法, 如调整设备、优化流程等
PPT,a click to unlimited possibilities
汇报人:PPT
目录
01 添 加 目 录 项 标 题 03 生 产 线 平 衡 分 析 方 法 05 生 产 线 平 衡 优 化 策 略 07 生 产 线 平 衡 案 例 分 析
02 生 产 线 平 衡 概 述 04 生 产 线 平 衡 评 价 指 标 06 生 产 线 平 衡 实 施 步 骤
平衡率指标
定义:平衡率指标是指生产线各工 序时间与瓶颈工序时间的比值
意义:平衡率指标用于衡量生产线 平衡程度,即生产线各工序时间分 布的均匀程度
添加标题
添加标题
添加标题
添加标题
计算方法:平衡率 = (各工序时间 总和 / 瓶颈工序时间) × 100%
改善方向:通过调整生产线各工序 的作业时间,降低瓶颈工序时间, 提高平衡率指标,以实现生产效率 的提升
确定需要收集的数 据和信息类型
确定数据和信息来 源
制定收集计划和时 间表
确保数据和信息的 准确性和完整性
进行分析和评估
确定生产线的瓶颈工序 分析生产线的平衡状况 制定平衡改善方案 实施平衡改善方案并进行评估
制定改进措施并实施
根据分析结果,制定针对性的改进措施 确定改进措施的优先级和实施顺序 制定详细的实施计划和时间表 确保改进措施得到有效执行和监控
明确分析目标:确定生产 线平衡的目标和范围
收集数据:收集生产线上 的相关数据,包括设备、 人员、时间等
流程图绘制:根据收集的 数据绘制流程图,展示生 产线的运行过程
平衡点确定:根据流程图 确定生产线上的平衡点, 即瓶颈工序
平衡方法选择:根据平衡 点选择合适的平衡方法, 如调整设备、优化流程等
生产线平衡分析与改善PPT课件
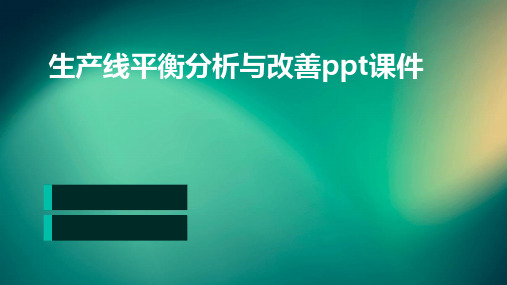
详细描述
某汽车企业在生产过程中面临工艺复杂、生产流程长等问题,通过改进生产工 艺和引入智能制造技术,实现了生产线平衡的持续改进,提高了生产效率和产 品质量。
06 结论与展望
生产线平衡对企业的影响
提高生产效率
生产线平衡能够优化资源配置,减少生 产过程中的空闲时间,提高设备利用率,
从而提高生产效率。
持续改进与优化
定期检查
定期对生产线进行检查,发现潜在问题并及时解 决。
员工培训
加强员工培训,提高操作技能和生产意识,促进 持续改进。
ABCD
数据跟踪
建立数据跟踪机制,对生产线相关数据进行实时 监测和分析,以便及时调整和优化。
创新与改进
鼓励员工提出创新和改进意见,激发团队活力和 创造力,实现持续改进与优化。
设备利用率是指生产线设备在一段时间内 的有效工作时间与总工作时间的比值,反 映了设备的利用情况。
生产效率
在制品库存
生产效率是指生产线在一定时间内完成的 产品数量与总工作时间的比值,反映了生 产线的生产能力。
在制品库存是指生产线在制品的数量和存 储时间,反映了生产线的库存状况。
生产线平衡的优化目标
01
随着工业4.0和智能制造的兴起,未来生产 线平衡将更加注重智能化技术的应用,如
物联网、大数据、人工智能等。
绿色生产线的推广
随着环保意识的提高,未来生产线平衡将 更加注重环保和可持续发展,推广绿色生
产技术和设备。
柔性生产线的构建
为了更好地适应市场需求的变化,未来生 产线平衡将更加注重生产线的柔性和可重 构性。
绘制工艺流程图,直观展示工艺流程, 便于发现瓶颈环节。
引入自动化和智能化设备,减少人工 干预,提高生产效率。
某汽车企业在生产过程中面临工艺复杂、生产流程长等问题,通过改进生产工 艺和引入智能制造技术,实现了生产线平衡的持续改进,提高了生产效率和产 品质量。
06 结论与展望
生产线平衡对企业的影响
提高生产效率
生产线平衡能够优化资源配置,减少生 产过程中的空闲时间,提高设备利用率,
从而提高生产效率。
持续改进与优化
定期检查
定期对生产线进行检查,发现潜在问题并及时解 决。
员工培训
加强员工培训,提高操作技能和生产意识,促进 持续改进。
ABCD
数据跟踪
建立数据跟踪机制,对生产线相关数据进行实时 监测和分析,以便及时调整和优化。
创新与改进
鼓励员工提出创新和改进意见,激发团队活力和 创造力,实现持续改进与优化。
设备利用率是指生产线设备在一段时间内 的有效工作时间与总工作时间的比值,反 映了设备的利用情况。
生产效率
在制品库存
生产效率是指生产线在一定时间内完成的 产品数量与总工作时间的比值,反映了生 产线的生产能力。
在制品库存是指生产线在制品的数量和存 储时间,反映了生产线的库存状况。
生产线平衡的优化目标
01
随着工业4.0和智能制造的兴起,未来生产 线平衡将更加注重智能化技术的应用,如
物联网、大数据、人工智能等。
绿色生产线的推广
随着环保意识的提高,未来生产线平衡将 更加注重环保和可持续发展,推广绿色生
产技术和设备。
柔性生产线的构建
为了更好地适应市场需求的变化,未来生 产线平衡将更加注重生产线的柔性和可重 构性。
绘制工艺流程图,直观展示工艺流程, 便于发现瓶颈环节。
引入自动化和智能化设备,减少人工 干预,提高生产效率。
生产线平衡方法.pptx

OEE所涵盖的其 他时间损失
传统效率衡量方 式只计算了部分
时间损失
总时间损失
六种重大OEE损失类型 OEE时间损失分为6大类
质量缺陷
计划外停 机
机器故障
速度下降
换线
损坏
OEE计算 – 模型
六种重大损失降低机器效能说明
设备时间
设备损失
设备最大可用工时
可使用总工时
时间稼动
SD损失
性能稼动 速度损失 价值稼动
• 14、Thank you very much for taking me with you on that splendid outing to London. It was the first time that I had seen the Tower or any of the other fam ous sights. If I'd gone alone, I couldn't have seen nearly as much, because I wouldn't have known my way about.
Station 2: G:11.3-11.3=0 Total time=11.3
Station 5: N:11.3-10.7=0.6 Total time=10.7
Station 3: C:11.3-2.1=9.2 D:9.2-2.5=6.7 E:6.7-1.8=4.9 F:4.9-1.8=3.1 H:3.1-2.1=1 Total time=10.3
6. 设定产能 标准产能
实际产能
1:TT & CT
1.Tact time=Cycle time的计算:
B
①A
传统效率衡量方 式只计算了部分
时间损失
总时间损失
六种重大OEE损失类型 OEE时间损失分为6大类
质量缺陷
计划外停 机
机器故障
速度下降
换线
损坏
OEE计算 – 模型
六种重大损失降低机器效能说明
设备时间
设备损失
设备最大可用工时
可使用总工时
时间稼动
SD损失
性能稼动 速度损失 价值稼动
• 14、Thank you very much for taking me with you on that splendid outing to London. It was the first time that I had seen the Tower or any of the other fam ous sights. If I'd gone alone, I couldn't have seen nearly as much, because I wouldn't have known my way about.
Station 2: G:11.3-11.3=0 Total time=11.3
Station 5: N:11.3-10.7=0.6 Total time=10.7
Station 3: C:11.3-2.1=9.2 D:9.2-2.5=6.7 E:6.7-1.8=4.9 F:4.9-1.8=3.1 H:3.1-2.1=1 Total time=10.3
6. 设定产能 标准产能
实际产能
1:TT & CT
1.Tact time=Cycle time的计算:
B
①A
07生产线平衡-PPT精品文档

时间测试ห้องสมุดไป่ตู้
分解动作时间量测,一般每个动作测量5 次为宜; 量测人员应站在作业员斜后面1米以外, 以能看清楚全部操作动作为准则; 测试中不能打扰作业员的正常操作,和引 起作业员的紧张;
时间测量流程
作业内容
测试中判断作业员的速度水平,并作如 数据与信息记录 实记录,不可修改量测数据;
若有其它特殊情况,也应加以实录;
Steps 6:实施新的仿真流程 改善后时间测量 改善后山积表制作
平衡的步骤
Steps 7: 改善总结报告: 平衡率 设定产能﹑实际产能﹑人均产能(单机产能) 损失分析 质量分析 成本改善率
平衡率= ----------------------100% 瓶颈时间人数
相关的概念
时间
T2
瓶颈时间
T1
T3 T4 T5
S1 S2 S3 S4 S5 工站
单件标准时间 = T1+T2+T3+T4+T5 (流程中各工站所有动作标准时间之和)
相关的概念
概念2:可供工时
可供工时=可供时间*人数-借出工时 可供时间:上班时间内,为某产品生产而投入
工站
平衡的步骤
Steps 4:山积表平衡
联合操作的工站时间(S1-1≦S1-2)
时间
t4 t3 t2
S1标准时间为﹕t2+t3; S1工站时间为﹕t4
t1
当S1-1不需等 S1-2就能开始, S1工站时间为 ﹕ S1-2的时间
S1-1 S1-2 S1-1 S1-2 S1-1 S1-2 工站
T5 =等待时间之和
S1 S2 S3 S4 S5 工站
相关的概念
概念7:平衡率100%代表﹕ 1. 工站之间无等待,前后产能一致﹔
生产线平衡培训课程PPT课件

第13页/共48页
二. 生产线平衡分析方法
• 案例计算
第14页/共48页
二. 生产线平衡分析方法
• 案例
第15页/共48页
二. 生产线平衡分析方法
6. 生产线平衡分析方法
第16页/共48页
二. 生产线平衡分析方法
7. 改善瓶颈岗位
第17页/共48页
二. 生产线平衡分析方法
• 改善四大原则
• 较少动作次数
改善前生产线平衡率=(18+16+24+37+45+16)/(37*7)*100%=60.2%
• 改善前生产线各工位平衡图
第42页/共48页
四. 线平衡经典案例分享
2. 改善前分析
第43页/共48页
四. 线平衡经典案例分享
பைடு நூலகம்3. 改善前后对比
第44页/共48页
四. 线平衡经典案例分享
3. 改善前后对比
B值得最优值为“1”
第29页/共48页
三. B值、F值的定义和计算
2. 一个流成产 One world、One dream One piece、One flow
• One piece flow是指单件进行生产,即人工每次只加工一件产品或部件,理想状态下,任何操作工位 间和工作内的多余的WIP为零。
• 例1:缩短生产节拍 • 提升生产速度,维持人手不变。
第20页/共48页
二. 生产线平衡分析方法
• 例2:减少人手(1) • 减少人员,维持生产速度不变
第21页/共48页
二. 生产线平衡分析方法
• 例3:减少人手(2) • 降低线体速度,减少生产产量
第22页/共48页
二. 生产线平衡分析方法
二. 生产线平衡分析方法
• 案例计算
第14页/共48页
二. 生产线平衡分析方法
• 案例
第15页/共48页
二. 生产线平衡分析方法
6. 生产线平衡分析方法
第16页/共48页
二. 生产线平衡分析方法
7. 改善瓶颈岗位
第17页/共48页
二. 生产线平衡分析方法
• 改善四大原则
• 较少动作次数
改善前生产线平衡率=(18+16+24+37+45+16)/(37*7)*100%=60.2%
• 改善前生产线各工位平衡图
第42页/共48页
四. 线平衡经典案例分享
2. 改善前分析
第43页/共48页
四. 线平衡经典案例分享
பைடு நூலகம்3. 改善前后对比
第44页/共48页
四. 线平衡经典案例分享
3. 改善前后对比
B值得最优值为“1”
第29页/共48页
三. B值、F值的定义和计算
2. 一个流成产 One world、One dream One piece、One flow
• One piece flow是指单件进行生产,即人工每次只加工一件产品或部件,理想状态下,任何操作工位 间和工作内的多余的WIP为零。
• 例1:缩短生产节拍 • 提升生产速度,维持人手不变。
第20页/共48页
二. 生产线平衡分析方法
• 例2:减少人手(1) • 减少人员,维持生产速度不变
第21页/共48页
二. 生产线平衡分析方法
• 例3:减少人手(2) • 降低线体速度,减少生产产量
第22页/共48页
二. 生产线平衡分析方法
生产线平衡 ppt课件
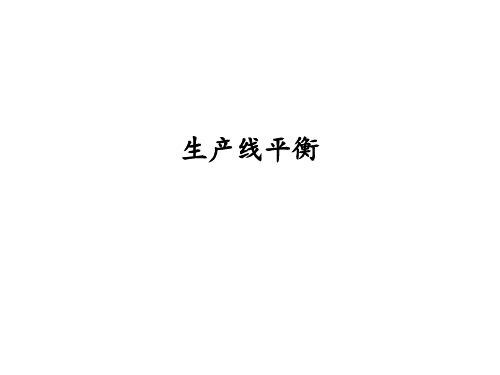
时间 t4 t3 t2
S1标准时间为﹕t2+t3;S1 工站时间为﹕t4
t1
S1-1 S1-2 S1-1 S1-2 S1-1 S1-2
当S1-1不需等S1-2就 能开始,S1工站时间 为﹕S1-2的时间
工站
25
Steps4:山积表平衡
(6) 联合操作的工站时间(S1-1>S1-2)
时间 t4 t3 t2
S1标准时间為 ﹕t2+t3;S1工站时间 为﹕t4
t1 S1-1 S1-2 S1-1 S1-2
工站
26
Steps4:山积表平衡
S1工站时间=?
(6) 联合操作的工站时间(S1-1>S1-2)
?
时间 t4 t3 t2
t1
S1-1 S1-2 S1-1 S1-2
工站
27
Steps 5:建立新的流程
新的FLOW CHART/ SOP
出料
入料
定义:生产线平衡即是对生产的全部工序进行平均化,调整作业负
荷,以使各作业时间尽可能相近的技术手段与方法。目的是消除作
业间不平衡的效率损失以及生产过剩。
瓶颈工序决定
最大产能
生产中的瓶颈(bottleneck)是指那些限制工作流整体水平(包括工作 流完成时间,工作流的质量等)的单个因素或少数几个因素。
作 业 时 间
工序 1 2 3 4 5 分担转移
作 业 时 间
工序 1 2 3 4 5 合并重排
工序 1 2 3 4 5 减人(分解消除)
作 业 时 间
工序 1 2 3 4 5 6 加 人(作业分解)
作 业 时 间
工序 1 2 3 4 5 减人(作业改善压缩)
生产线平衡(实例版)PPT课件
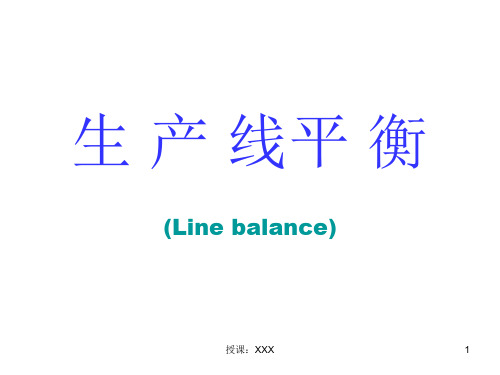
产能力﹑生产速度和效率.
其计算公式:
计划期内有效工作时间
节拍r= 计划期内计划产量
[时间/件]
授课:XXX
11
1﹑生产线平衡的相关概念
例﹕节拍计算
某制品流水线计划年销售量为500000件﹐另 需生产备件10000件﹐良率98%﹐两班制工作 ﹐每班8小时﹐每周6天工作时间﹐时间有效 利用系数95%﹐求流水线的节拍。
按A 键 按 B 键归零
23
2﹑生产线平衡的实施
2.1.3时间记录表
授课:XXX
9.23
24
2﹑生产线平衡的实施
2.1.4工时测量的作用
➢ 获取各工站的实际操作时间﹐为山积表 制作﹐时间平衡作准备﹔
➢ 通过时间观测﹐分析作业价值﹐发现问 题和改善空间﹔
➢ 形成标准﹐比较实际差异﹐找出问题.
授课:XXX
时间
瓶颈时间
T1 T2
T5
T3 T4
S1 S2 S3 S4 工站
S1 S2 S3 S4 S5 工站
授课:XXX
29
2﹑生产线平衡的实施
2.3.3提高作业者技能
--或调换高技能作业者
1.优化工站物料﹐
时
工具摆放
间
2.改善操作员的
操作方法
3.提高操作员动作
效率
授课:XXX
山积表 重合简取排并化消
工 站
时间
T2
T1
T3 T4 T5
工站 S1 S2 S3 S4 S5
单件标准时间= T1+T2+T3+T4+T5
(流程中各工站所有动作标准时间之和)
授课:XXX
13
1﹑生产线平衡的相关概念
其计算公式:
计划期内有效工作时间
节拍r= 计划期内计划产量
[时间/件]
授课:XXX
11
1﹑生产线平衡的相关概念
例﹕节拍计算
某制品流水线计划年销售量为500000件﹐另 需生产备件10000件﹐良率98%﹐两班制工作 ﹐每班8小时﹐每周6天工作时间﹐时间有效 利用系数95%﹐求流水线的节拍。
按A 键 按 B 键归零
23
2﹑生产线平衡的实施
2.1.3时间记录表
授课:XXX
9.23
24
2﹑生产线平衡的实施
2.1.4工时测量的作用
➢ 获取各工站的实际操作时间﹐为山积表 制作﹐时间平衡作准备﹔
➢ 通过时间观测﹐分析作业价值﹐发现问 题和改善空间﹔
➢ 形成标准﹐比较实际差异﹐找出问题.
授课:XXX
时间
瓶颈时间
T1 T2
T5
T3 T4
S1 S2 S3 S4 工站
S1 S2 S3 S4 S5 工站
授课:XXX
29
2﹑生产线平衡的实施
2.3.3提高作业者技能
--或调换高技能作业者
1.优化工站物料﹐
时
工具摆放
间
2.改善操作员的
操作方法
3.提高操作员动作
效率
授课:XXX
山积表 重合简取排并化消
工 站
时间
T2
T1
T3 T4 T5
工站 S1 S2 S3 S4 S5
单件标准时间= T1+T2+T3+T4+T5
(流程中各工站所有动作标准时间之和)
授课:XXX
13
1﹑生产线平衡的相关概念
《生产线平衡》课件

瓶颈工序
生产节拍
生产线上的瓶颈工序是指生产能力不足的 工作站,应通过优化生产流程和调整工作 量来消除瓶颈。
生产节拍是指生产线上的一个工作站完成 一个产品所需的时间,应保持生产节拍的 一致性以提高生产效率。
02
生产线平衡的优化方法
工艺流程分析
总结词
通过对生产工艺流程的详细分析,识别流程中的瓶颈和浪费,为后续优化提供基 础。
工作研究
总结词
通过系统的方法对工作过程进行研究 ,以提高工作效率和工作质量。
详细描述
工作研究是对整个工作过程进行系统 化研究的学科,通过工作研究可以发 现工作中存在的问题和瓶颈,提出改 进方案,提高工作效率和工作质量。
动作分析
总结词
对操作过程中的动作进行分解、分析和 优化,以提高工作效率和减轻工人负担 。
优化工艺流程
总结词
通过优化工艺流程,可以减少生产瓶颈,提高生产线的平衡率。
详细描述
对工艺流程进行分析,找出瓶颈环节,通过改进工艺、调整设备参数等方式,提高各环节的生产能力 ,使整个生产线更加平衡。
提高设备利用率
总结词
通过提高设备利用率,可以降低生产成本, 提高产能。
详细描述
合理安排生产计划,确保设备得到充分利用 。同时,加强设备维护保养,延长设备使用 寿命,降低故障率,进一步提高设备利用率 。
生产线平衡的目标与原则
目标
实现工作站间的平衡,提高生产效率,降低生产成本。
原则
合理分配工作量、保持生产线的连续性和稳定性、优化生产流程。
生产线平衡的评估指标
平衡率
空闲时间
衡量生产线平衡程度的指标,计算公式为 (各工作站所需时间总和)/(最长工作站 所需时间)×100%。
- 1、下载文档前请自行甄别文档内容的完整性,平台不提供额外的编辑、内容补充、找答案等附加服务。
- 2、"仅部分预览"的文档,不可在线预览部分如存在完整性等问题,可反馈申请退款(可完整预览的文档不适用该条件!)。
- 3、如文档侵犯您的权益,请联系客服反馈,我们会尽快为您处理(人工客服工作时间:9:00-18:30)。
计划期内有效工作时间 节拍r=
计划期内计划产量
[时间/件]
例:某制品流水线计划年销售量为500000件﹐另需生 产备件10000件﹐良率98%﹐两班制工作﹐每班8小时 ﹐每周6天工作时间﹐时间有效利用系数95%﹐求流水 线的节拍。
T有效=365/7*6*8*2*60*0.95=285325分钟
Q=(500000+10000)/0.98=520408件
工站:一个或多个作业员在一个工作地共同完成产品加 工工艺中某一特定作业的操作组合.
周期时间:完成某工站内所有工作所需时间.
时间
T2
T1
T3 T4 T5
工站 S1 S2 S3 S4 S5 CycleTime﹕每工站中1个循环的作业所需的标准工 时(如图中所示﹕T1,T2,T3,T4,T5)
4
时间
T2
可以互相讨论下,但要小声点
1.3 木桶定律
1.木桶定律 一个木桶盛水多少,并不取决于桶壁上最高的那块木板, 而恰恰取决于桶壁上最短的那块木板,这一规律我们称 之为“木桶定律”。 2.木桶定律的三个推论 A.只有桶壁上所有木板都足够高,木桶才能盛满水。 B.所有木板高出最低木板的部分是没有意义的,而且高出 越多,浪费就越大。 C.提高木桶容量最有效的办法就是设法加高最低木板的 高度。
r=T/Q=285325/520408=0.55分钟/件=33秒/件
7
单件标准时间:完成一个产品所有加工作业 所需的时间(单位:小时人)
时间
T2
T1
T3 T4 T5
工站 S1 S2 S3 S4 S5
单件标准时间= T1+T2+T3+T4+T5
(流程中各工站所有动作标准时间之和)
8
大家有疑问的,可以询问和交流
T1
T3 T4 T5
工站 S1 S2 S3 S4 S5
瓶颈工时﹕生产线作业工时最长的工站的 标准工时称之为瓶颈工时
5
时间
T2
瓶颈时间
T1
T3 T4 T5
Tack Time
工站 S1 S2 S3 S4 S5 Tack Time﹕产线各工站单循环最大充许作业时间(Tack time>=瓶颈工时)
6
TackTime即节拍,它决定了生产线的生产能力﹑生产速度 和效率.
工站
21
Steps4:山积表平衡
(4) 若T严重小于CT:将CT设为上限,重排 错误的做法是:消除瓶颈
时间
CT 平均时间T
S1 S2 S3 S4 S5
工站
22
Steps4:山积表平衡
(5) 若有动作作了改善,应更新后再平衡
时间
S1 S1’ S2 S2’
工站
23
Steps4:山积表平衡
(6) 联合操作的工站时间(S1-1≦S1-2)
出料
入料
定义:生产线平衡即是对生产的全部工序进行平均化,调整作业负
荷作
业间不平衡的效率损失以及生产过剩。
瓶颈工序决定
最大产能
生产中的瓶颈(bottleneck)是指那些限制工作流整体水平(包括工作 流完成时间,工作流的质量等)的单个因素或少数几个因素。
生产线平衡
目录
3 1 生产线平衡的定义 3 2 生产线平衡的作用 3 3 生产线平衡的方法 3 4 生产线平衡案例分析
1 生产线平衡的定义
1.1 流水线
基本特征 固定生产一种或少数几种产 品 工作中心专业化程度高 按节拍生产 生产能力保持平衡 1) 工艺过程是封闭的
1.2 工站及周期时间
ECRS
5W1H
PDCA
16
Steps1:改善工作准备 1 选择产品﹐了解流程 2 时间测量﹕时间记录表,测时工具 3 掌握现况﹕ (1)设定产能 实际产能 人均产能(单机台产能)
(2)操作效率OPE (3)损失分析 质量分析 (4)改善前山积表 ......
17
Steps2:消除生产浪费 1 八大浪费消除 [不良品浪费/动作浪费/过程浪费/过量浪費/ 库存浪费/移动浪费/不平衡浪费/管理浪费] 2制作浪费改善前/后比较图,报告中经验分享
增加可供 时间
(1) 算出需求产出周期时间[CT=可供时间*OPE/需求量]
(2) 若T≥CT:将CT设为上限,重排
时间
? 还有什
么方法
平均时间T
CT
S1
S2
S3
S4
S5
工站
20
Steps4:山积表平衡 (3) 若T略小于CT:将CT设为上限,消除瓶颈
时间
CT 平均时间T
S1 S2 S3 S4 S5
作业岗位工时测定
B
①
A
A通过①,B前端到达①所需时间
13
2 生产线平衡的作用
• 通过平衡生产线可以综合应用到程序分析、动作分析、layout分析, 搬动分析、时间分析等全部IE手法,提高全员综合素质
• 在平衡的生产线基础上实现单元生产,提高生产应变能力 • 减少单件产品的工时消耗,降低成本(等同于提高人均产量) • 减少工序的在制品,真正实现“一个流”或“单片流” • 提升整体生产线效率和降低生产现场的各种浪费 • 消除人员等待现象,提升员工士气 • 减少工序间的在制品, 减少现场场地的占用 • 可以稳定和提升产品品质
1.4 生产线平衡的定义
生产线平衡与木桶定律的关系
1.“生产线平衡”与“木桶定律”非常相似:生产线的最大产能不是取 决于作业速度最快的工位,而恰恰取决于作业速度最慢的工位,最快与 最慢的差距越大,产能损失就越大。
2.企业现场管理的整体水平并不取决于最优秀的车间单位而是取决于最 差的车间单位,同理,对一条生产线来言,其产量、效率高低也是如此。
18
Steps3:方法研究改善
(1) 程序分析 [四大原则(ECRS)/五大内容(工艺流程分析、搬运
分析、检验分析、存储分析、等待分析)/六大步骤(选择、 记录、分析、建立、实施、维持)] (2) 操作分析
[人机操作/联合操作/双手操作] (3) 动作分析
[动素分析/动作经济原则]
19
Steps 4:山积表平衡
3 生产线平衡的方法
参数计算
节拍-生产周期:最长工序时间(瓶颈岗位时间)决定了整个生产 线的作业时间,即等于节拍。
∑(各工序的作业时间) 平衡率=
瓶颈岗位时间*人数
* 100%
产品标准工时= 每个工位所用时间的总和
生产线平衡损失 =1 - 平衡率
一般要求生产线平衡率达到85%以上
生产线平衡流程
1、改善准备工作 2、消除生产线浪费 3、方法研究改善 4、山积表平衡 5、构建新的产线流程 6、改善后流程现场实践 7、改善报告总结 8、标准化