覆膜中的一些问题与解决方案
模切问题点【范本模板】

一、模切机常见问题与解决方案输纸部分1. 走纸不稳,需经常调节该故障主要是针对国产模切机而言的,由于国产模切机多数没有采用带吸气的传送带,容易导致走纸不稳,纸张定位精度不高,输纸导轮、输纸带、压纸毛轮、前规挡块.侧规挡块等容易磨损.在走纸之前对纸张进行敲纸、打边并在走纸过程中加以调节可有效解决此问题。
2。
输纸不顺畅引起输纸不顺畅的原因有多种,主要为纸张变形、印刷品表面过于光滑或由其他机械故障引起。
(1)由纸张变形引起的输纸不顺畅由于模切加工是整个印刷加工最末端的一道工序,纸张经过若干工序加工后容易产生变形,特别是经过高温、高压的上光.覆膜后的纸张变形更加严重,这时飞达往往不能 J 顷利地送纸。
(2)由印刷品表面过于光滑引起的输纸不顺畅上光覆膜后的产品由于其表面过于光滑,也会给输纸造成一定的困难.对于以上两种情况,有经验的操作人员会在上纸之前做好前期准备工作,比如:装纸时,在纸张中加入一些木楔子或纸卷使纸张保持平整,在上纸时预先进行打边、敲纸工作或把模切机的速度适当降低,一般可以避免此问题的发生。
(3)机械故障引起的输纸困难飞达吸嘴吸力不够、距离纸堆上平面的位置不合适、规矩的定位不准确等机械原因会造成输纸过程中出现斜张,双张、空张等故障。
只要平时做好模切机保养工作和机械部位的调节就会避免由于机械故障产生的输纸困难二、模切机模切部分常见问题与解决方案。
A。
压力不均匀模切压痕过程中压力不均匀,一般有两种情况:1。
如果压力有轻微的不均匀,可能是由于模切刀、线(钢刀、钢线)分布不均,造成动平台在模切时受力歪斜所致,此时应在模切版上加装平衡刀线,使平台受力均匀。
2. 如果平台前后成四角处出现比较严重的压力不均匀现象,则主要是支撑动平台的四个连杆摆杆高度不一致造成的,此时应打开模切底座的护罩,检查摆杆是否磨损,如磨损严重则需更换,否则需要调整四个压力调整斜铁,直到压力一致为止.B。
模切精度不高模切的精度是衡量模切质量最为重要的标准之一,是生产出合格产品的重要保证,在实际生产过程中,常常出现模切精度达不到设计要求的情况。
热转印工艺的13 种常见质量故障

Technology网印工业Screen Printing Industry2021.0528工艺技术满版出现花版现象:满版部分出现斑点、花纹。
原因:油墨黏度太低,刮刀角度不当,油墨干燥温度不足,静电等。
排除:提高黏度,调整刮刀角度,提高烘箱温度,薄膜背面预涂静电剂。
拉毛现象:在图案的一侧会出现类似彗星的线,经常出现在白墨上和图案边缘部分。
原因:油墨颜料颗粒较大,油墨不干净,黏度高,静电等。
排除:过滤油墨,降低油墨浓度,白墨中可以预先磨刀,对薄膜静电处理,用削尖的筷子在刮刀和版间刮尽,或加静电剂。
套色不良,露底现象:几个颜色叠加时出现组色偏离,特别表现在底色上。
主要原因:机器本身精度不良,有波动;制版不良;底色扩缩不当。
排除:利用频闪灯人工套准;重新制版;在不影响图案视觉效果下扩大扩缩或在小部分图案上不衬白。
油墨刮不清现象:在印刷膜上出现蒙状。
原因:刮刀固定架松弛;版面不干净。
排除:重新调节好刮刀,并固定好刀架;清洗印版,必要时用去污粉清洗;在版面与刮刀之间安装反面送风。
热转印工艺的13种常见质量故障热转印工艺,化妆品包材表面处理中常见的一种工艺,是指以涂有颜料或染料的转印纸为媒介,通过加热、加压等方式,将媒介上油墨层的花纹图案转移到承印物上的一种印刷方式。
其基本原理是将涂有油墨的媒介与承印物直接接触,通过热印刷头和压印滚筒的加热、加压作用,媒介上的油墨就会熔解并转移到承印物上,得到所要的印刷品的过程。
因为印刷方便,且色彩、图样可以自定义设计,所以也是受到品牌商较喜欢的一种工艺,但热转印工艺也经常遇到相关的质量问题,本文将列举一些常见的质量问题与解决方案,供朋友们参考。
Technology 网印工业Screen Printing Industry2021.0529工艺技术印刷颜色掉块现象:在相对较大的图案的局部部分出现颜色剥落现象,特别是在印刷玻璃、不锈钢的预处理膜上最易出现此现象。
原因:颜色层在已处理的薄膜上印刷本身比较容易剥落;静电;颜色墨层较厚,干燥不充分。
tpu覆膜布的熔接

tpu覆膜布的熔接TPU覆膜布是一种以热熔技术将TPU薄膜与布料紧密结合的新型复合材料。
它拥有许多优良的特性,如防水、透气、耐磨等,广泛应用于户外服装、鞋类、包装材料等领域。
TPU覆膜布的熔接工艺是确保其性能和质量的重要环节。
1. 熔接设备与工艺在TPU覆膜布的熔接过程中,需要使用专门的热熔设备。
常见的熔接设备包括热熔机、高频熔接机等。
热熔机主要通过加热和压力将TPU薄膜与布料熔接在一起,而高频熔接机则是利用高频电场的作用将两者熔接在一起。
具体的熔接工艺会根据材料的类型和要求而有所不同。
2. 熔接温度和时间控制熔接温度和时间是影响熔接效果的重要因素。
一般来说,TPU薄膜的熔点较低,通常在100°C左右,而布料的熔点则较高,一般在150°C以上。
因此,在熔接过程中,需要控制好温度和时间,以保证TPU薄膜和布料能够充分熔接在一起,同时不会造成材料破损或变形等质量问题。
3. 熔接压力控制熔接压力是保证TPU薄膜和布料能够牢固粘结的关键因素之一。
过低的熔接压力可能导致熔接不牢固,而过高的熔接压力则可能造成材料破损。
因此,在熔接过程中,需要选择合适的压力,并通过调节熔接设备的参数来进行控制。
4. 熔接面积和形状熔接面积和形状也会直接影响TPU覆膜布的熔接效果。
通常情况下,熔接面积越大,熔接效果越好,但同时也会增加成本和制造难度。
另外,熔接形状也需要考虑功能和美观性的需求,例如直线熔接、曲线熔接或者特殊图案熔接等。
5. 熔接检测和质量控制在熔接过程结束后,需要对熔接质量进行检测和控制。
常见的检测方法包括目测检查、拉力测试、水压试验等。
目测检查主要是通过外观来判断熔接效果,而拉力测试和水压试验则可以评估熔接强度和防水性能等。
通过合理的质量控制,可以确保TPU覆膜布的熔接质量达到设计要求。
TPU覆膜布的熔接工艺是一项综合技术,需要对材料、设备和工艺参数等进行合理的选择和控制。
只有在科学的熔接工艺指导下,才能生产出具有优良性能和可靠质量的TPU覆膜布产品。
绿化关键施工技术重点难点和解决方案

绿化关键施工技术重点难点和解决方案首先是选材方面。
绿化工程中的选材主要涉及到植物的选择和苗木的质量。
植物的选择要考虑到其适应性、生长习性、观赏价值等因素,而苗木的质量则涉及到苗圃的管理和育苗技术。
在选择植物时,可以根据当地的气候条件、土壤情况和绿化要求等因素进行合理选择,并进行综合评估。
在苗木的选取方面,可以依据苗木的生长情况、枝干的均匀度和根系的健康程度等指标进行判断,并通过与专业苗农的合作来获取优质的苗木。
其次是保水方面。
保水是绿化工程中一个非常关键的环节,尤其是在干旱地区。
保水的难点在于如何保持土壤的湿度,并避免水分的蒸发。
为了解决这个问题,可以采取以下措施:1.选择适合的土壤改良材料,改善土壤结构,增加土壤的贮水性能。
2.铺设覆盖材料,如草皮、覆土、覆膜等,可以有效减少土壤水分的蒸发。
3.合理设置灌溉系统,利用喷灌、滴灌等技术,精确控制水量和灌溉时间,减少浪费。
最后是养护方面。
绿化工程的养护是保证植物健康生长的重要保障,但同时也是施工中的难点之一、养护涉及到病虫害防治、修剪管理、施肥补充等方面。
解决养护难点的关键在于科学养护和定期维护。
1.病虫害防治:定期巡查绿化区域,发现病虫害及时采取相应的防治措施,如喷洒药剂、人工捕捉等。
2.修剪管理:根据植物的生长特点,采取针对性的修剪措施,促进植物的分枝和生长。
3.施肥补充:定期施加有机肥料和微量元素,补充植物生长所需的养分。
综上所述,绿化关键施工技术的重点难点包括选材、保水和养护等方面。
对于选材方面,可以根据实际情况进行合理选择,并与专业苗农合作获取优质苗木。
对于保水方面,可以采取改良土壤、覆盖材料和合理灌溉等措施来保持土壤湿度。
对于养护方面,需要科学养护和定期维护,包括病虫害防治、修剪管理和施肥补充等措施。
通过合理运用这些解决方案,可以有效解决绿化施工中的重点难点,保障绿化工程的顺利进行。
车衣裳汽车改色贴膜注意事项疑难解答百科大全详解
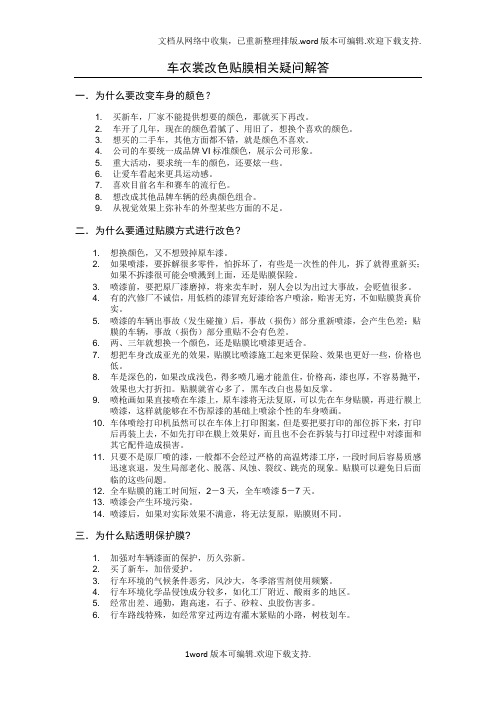
车衣裳改色贴膜相关疑问解答一.为什么要改变车身的颜色?1. 买新车,厂家不能提供想要的颜色,那就买下再改。
2. 车开了几年,现在的颜色看膩了、用旧了,想换个喜欢的颜色。
3. 想买的二手车,其他方面都不错,就是颜色不喜欢。
4. 公司的车要统一成品牌VI标准颜色,展示公司形象。
5. 重大活动,要求统一车的颜色,还要炫一些。
6. 让爱车看起来更具运动感。
7. 喜欢目前名车和赛车的流行色。
8. 想改成其他品牌车辆的经典颜色组合。
9. 从视觉效果上弥补车的外型某些方面的不足。
二.为什么要通过贴膜方式进行改色?1. 想换颜色,又不想毁掉原车漆。
2. 如果喷漆,要拆解很多零件,怕拆坏了,有些是一次性的件儿,拆了就得重新买;如果不拆漆很可能会喷溅到上面,还是贴膜保险。
3. 喷漆前,要把原厂漆磨掉,将来卖车时,别人会以为出过大事故,会贬值很多。
4. 有的汽修厂不诚信,用低档的漆冒充好漆给客户喷涂,贻害无穷,不如贴膜货真价实。
5. 喷漆的车辆出事故(发生碰撞)后,事故(损伤)部分重新喷漆,会产生色差;贴膜的车辆,事故(损伤)部分重贴不会有色差。
6. 两、三年就想换一个颜色,还是贴膜比喷漆更适合。
7. 想把车身改成亚光的效果,贴膜比喷漆施工起来更保险、效果也更好一些,价格也低。
8. 车是深色的,如果改成浅色,得多喷几遍才能盖住,价格高,漆也厚,不容易抛平,效果也大打折扣。
贴膜就省心多了,黑车改白也易如反掌。
9. 喷枪画如果直接喷在车漆上,原车漆将无法复原,可以先在车身贴膜,再进行膜上喷漆,这样就能够在不伤原漆的基础上喷涂个性的车身喷画。
10. 车体喷绘打印机虽然可以在车体上打印图案,但是要把要打印的部位拆下来,打印后再装上去,不如先打印在膜上效果好,而且也不会在拆装与打印过程中对漆面和其它配件造成损害。
11. 只要不是原厂喷的漆,一般都不会经过严格的高温烤漆工序,一段时间后容易质感迅速哀退,发生局部老化、脱落、风蚀、裂纹、跳壳的现象。
十大方案解决瓦楞纸箱防水防潮问题

CHINA PACKAGING|PACKAGING&PRINTING十大方案解决瓦楞纸箱防水防潮问题近年来冰鲜肉、果蔬、医药等冷链包装市场规模越来越大,瓦楞纸箱受防水防潮性能不佳原因所困,受到一定的局限。
可以说,行业急需从根本上解决纸箱包装受潮后易塌箱的问题。
以下十大方案,对瓦楞纸箱防水防潮方案有行业借鉴之处。
1.重度施胶箱板纸在箱板纸的造纸工艺中,对箱板纸表面进行重度施胶,可保证水滴在表面5分钟以内无渗透。
通常是在淀粉糊液中加入大量耐水助剂,如腺醛树脂、三聚氧胺甲醛树脂、聚乙烯醇缩丁醛等。
但该耐水剂成本较高,而且在瓦楞纸板生产过程中易造成瓦楞纸板开胶等问题。
2.淋膜纸淋膜纸就是将塑料粒子通过流延机涂覆在纸张表面的复合材料,主要特点是可以防油、防水(相对的)、可以热合。
但由于成本较高,不利于在包装行业广泛推广使用。
3.疏水瓦楞纸板又称拨水瓦楞纸板,是指在纸板面纸表面涂布如聚乳酸(PLA)、聚烯炷、聚碳酸酯、聚酰胺、聚酯、熔融石蜡等低表面能的物质,改变材料表面的粗糙度和表面形态的工艺。
22中国包装I包装印刷疏水瓦楞纸板在遭受水淋时,形成一种水滴在荷叶上的状态,水变成水滴滑落,而不会渗入纸板内部。
疏水瓦楞纸板成本非常低廉,适合于包装干燥粉状物品,尤其是吸水后容易结块的粉料,也适合于包装经常进出冷库的商品,从冷库中取出后容易在箱壁凝结。
经疏水加工后的纸板在露珠蒸发前不会显著降低耐压强度,能有效地保护商品。
4.防(遮)水瓦楞纸板又称防水或挡水瓦楞纸板,其表面长时间地与水接触几乎不透水,但不能浸入水中,否则失去防水性能。
遮水瓦楞纸板常用幕帘式涂布法,将熔融的合成树脂或石蜡混合物涂布在瓦楞纸板表面,形成一层树脂膜或蜡膜。
如有必要,也可进行双面涂布。
遮水瓦楞纸板多用来包装盐腌制品、冷冻食品和果蔬类产品,由于瓦楞纸板表面有柔软的石蜡层,故也适于包装易擦伤的高光洁度家具、钢琴、保险柜和精密机器等。
5.耐水瓦楞纸板长时间在水中浸泡后强度不明显降低的瓦楞板纸称为耐水瓦楞纸板。
印刷后工序 常见异常分析及改善
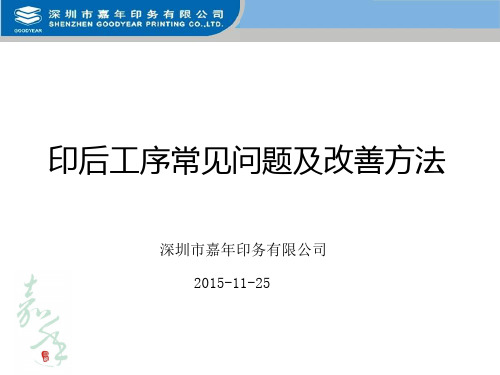
5、常见异常的分析和改善 5.4 ELP
1.镭射压印转移图案光泽度差 原因分析: (1)当UV光油黏度太低时,UV光油中固有的光敏寡聚物树脂的含量也较 低,这样UV光油固化后的成膜厚度就会变薄,从而导致镭射压印转移图案 光泽度变差。 (2)UV光油黏度太低还会降低UV光油在网纹辊表面的转移量,导致承印 物表面UV光油的涂层太薄,从而使得UV光油固化后,承印物表面形成的镭 射压印转移图案光泽度较差。 (3)当在UV光油中加入过量乙醇时,乙醇中所含的水分不能完全挥发, 在UV光油固化时容易产生水雾,并残留在光油膜层中,从而影响UV光油固 化成膜后的光泽度,甚至导致UV光油固化不彻底,使得镭射压印转移图案 产生雾化现象或失去应有的光泽。 为此,我们可以通过选择黏度较高的UV光油或在UV光油中加入适量的UV增 稠剂来提高其黏度,以及选用纯度稍高的乙醇且在使用过程中尽可能控制 乙醇的加入量等方法,来提高镭射压印转移图案的光泽度。
主要生产控制参数: 1、网目数 2、灯管电流
5、常见异常的分析和改善 5.3 全自动丝印/手工丝印
套位不准 产生原因: 1、纸张歪斜(切纸切歪) 2、纸张表面处理后变形(伸长/收缩) 3、针位不一致 4、拉规、前规等设备异常 5、网版张力太小 改善对策: 1、分针位生产 2、根据整体变形/走位状况,调节网版位置套
5、常见异常的分析和改善 5.0 常见问题
①、混料: 产生原因: 1、未按流程作业:未看工序要求、品标卡、未清场 2、不细心导致 3、其它偶发因素:无关人员放混、前工序混 改善对策: 1、按《 GY.TD014 产品混料防范管理规程》作业 2、机灵一点,不要只埋头做事,多思考。 3、细心、有责任感:对于其它人员的问题,不要抱着无所
1.3 UV上光:
UV上光即紫外线上光,它是以UV专用的特殊涂剂精 密、均匀地涂于印刷品的表现或局部区域后,经紫外线 照射,在极快的速度下干燥硬化而成,一般干燥时间 0.1~0.3S
覆膜机使用说明书

覆膜机使用说明书
1. 产品概述
1.1 简介:本文档为覆膜机的详细使用说明书,旨在帮助用户正确操作和维护该设备。
1.2 功能特点:列出该设备的主要功能及其优势。
2. 安全须知
在正式开始操作之前,请务必阅读并遵守以下安全须知:
2.1 设备环境与条件限制;
2.2 操作人员需具备的技能和经验;
- 所需技能或培训内容。
3.准备工作
步骤一:检查包装是否完好无损,并核对配件清单。
- 描述如何进行检查以确保所有零部件都存在且没有破损。
步骤二: 就地选择合适位置摊放器材、调整水平度等基础性设置;
- 提供关于就地选址、布置场地和校减水平度方面建议。
4.组装步骤(可按实际情况增加)
根据提供图纸/示意图完成各个模块间连接拼接工作,
a) A模块到B模块;
b) B模块到C模板;
5.启动与操作
5.1 设备启动前的准备工作;
- 列出需要进行的检查和调整。
5.2 启动设备步骤及注意事项;
a) 打开电源;
b) 调节温度、速度等参数。
6.常见故障与排除方法
在使用过程中,可能会遇到一些常见问题,请参考以下解决方案:
- 故障现象描述:具体故障情况;
解决方法:提供相应的排除措施或联系售后服务部门。
7.维护保养
提供关于日常维护保养以延长设备寿命和确保其正常运行所需知识,
如清洁、润滑剂更换等。
8.附件(本文档涉及)
- 列出所有相关附件,并注明文件名称或编号。
9.法律名词及注释(本文所涉及)
- 根据实际情况添加该章节内容,包括法律名词定义并给予简要说明。
浅谈模切生产工艺中存在的问题及其解决方案

浅谈模切生产工艺中存在的问题及其解决方案模切技术在印刷、标签等行业中技术已较成熟,但是在其工艺生产中还是存在一定的问题。
如在产品的检验中,常常发现许多模切制造的产品爆线或者切边起毛等质量问题,这些问题常常都是因为模切制造过程中的一些环节未能准确把握的原因。
针对模切生产过程中存在的一些问题,本文进行了总结并分析。
爆线现象及其对策模切工艺生产中,爆线问题是最常见的问题之一,也是非常值得引人关注的问题。
引发爆线问题的因素也非常多,主要有工作较长时间后有可能模切版上的压痕钢线发生松动、有异物与压槽中、模切压力太大和压痕钢线太高等原因。
详细分析爆线问题的原因后,我们得出以下几种解决方案:1.1.调节模切压力、底模、压痕钢线模切工艺生产中,模切压力、底模、压痕钢线能够较大的影响印品的质量,在使用过程中需调节准确,否则很容易引起爆线。
1.1.1.调节压痕钢线高度时需充分考虑纸张定量因素。
如果纸张定量较低,相应的压痕钢线高度也设置的高一点;也就是说,如果纸张定量较高则相应的压痕钢线高度也降低一些。
在实际模切工艺生产中,如果在同一批的模切原件中含有不同的纸张定量原件,则最好进行分开操作并根据不同的纸张定量原件调节压痕高度,否则十分容易导致爆线问题。
1.1.2.底模痕槽与压痕钢线这两者的高度应该相匹配,这样可以很大程度的降低爆线发生概率,从而得到良好的压痕效果。
1.1.3.长时间工作后,模切版上的压痕钢线常常会有松动现象,容易引起套准偏差、压痕槽和底模错位、压痕线发生偏斜等质量问题。
这样会引发大量的爆线现象,且爆线现象大多数都位于压痕线边缘。
一旦出现此类问题,就需要底模换新或者重新安装模切版上的压痕钢线。
1.1.4.在产品模切工艺生产过程中,为有效防止爆线的产生,需明确并有效协调模切的局部和全局压力。
调节局部压力可通过增加垫纸的方法来实现,全局压力则直接调节模切设备有关参数即可。
1.2.根据产品工艺的不同进行调节模切工艺实施之前,因不同的产品具有特有的性能需求,有时候需要添加一些印后工序,比如UV上光、覆膜等等,这些印后工序对最终的产品模切质量影响较大。
三防漆涂覆工艺不良解决方案
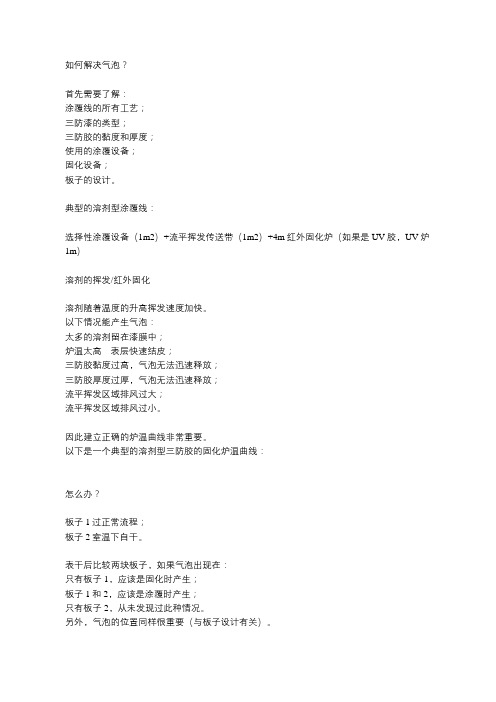
如何解决气泡?首先需要了解:涂覆线的所有工艺;三防漆的类型;三防胶的黏度和厚度;使用的涂覆设备;固化设备;板子的设计。
典型的溶剂型涂覆线:选择性涂覆设备(1m2)+流平挥发传送带(1m2)+4m 红外固化炉(如果是UV胶,UV炉1m)溶剂的挥发/红外固化溶剂随着温度的升高挥发速度加快。
以下情况能产生气泡:太多的溶剂留在漆膜中;炉温太高---表层快速结皮;三防胶黏度过高,气泡无法迅速释放;三防胶厚度过厚,气泡无法迅速释放;流平挥发区域排风过大;流平挥发区域排风过小。
因此建立正确的炉温曲线非常重要。
以下是一个典型的溶剂型三防胶的固化炉温曲线:怎么办?板子1过正常流程;板子2室温下自干。
表干后比较两块板子,如果气泡出现在:只有板子1,应该是固化时产生;板子1和2,应该是涂覆时产生;只有板子2,从未发现过此种情况。
另外,气泡的位置同样很重要(与板子设计有关)。
解决:大气泡=溶剂沸腾优化炉温曲线,降低炉温曲线爬坡坡度;增加固化前流平溶剂挥发量;涂覆时减小胶量,如减少重叠涂覆区域。
小气泡=压缩空气式漆罐涂覆方式降低漆罐的气压;降低固化炉温;增加固化前流平溶剂挥发量;更换稀释剂类型。
三防胶的气泡三防胶常见工艺问题分析之裂纹因为膜厚过厚引起的裂纹因为助焊剂残留造成的裂纹如何解决裂纹?优化炉温曲线,炉温不能过高;确认涂层已经完全固化,以达到最佳的性能;减小膜厚;清洗板子,尤其是焊点周围。
三防胶常见工艺问题分析之起皮元器件上的分层阻焊层上的分层阻焊层与三防胶涂层的兼容性阻焊剂的成分里含有添加剂,用来改善表面质量(如美化修饰、增加耐磨性、增加润湿性等等)这些添加剂可能会对三防胶涂层产生兼容性影响。
阻焊层修饰明亮的修饰=阻焊层没有被正确处理=表面质量不一致表面能量:达因笔使用方法:把达因笔装满墨水,测试范围32-44达因/cm建议最小能量:38达因/cm,以获得较好的润湿效果和附着力42达因/cm:失败38达因/cm:成功因保护造成的分层移除保护时造成分层,漆层附着力较差建议涂层达到指触干燥时(涂层仍柔软)去除保护如何消除分层减小膜厚减小炉温升温速度三防胶常见工艺问题分析之污染污染有两种:离子型和非离子型脱模剂污染:助焊剂残留:指印:因污染造成的缺陷:涂层剥离、涂层溶解或开裂、焊点腐蚀慢性反润湿原因:大面积污染;阻焊层的表面活性剂含硅;粘合剂含硅;清洗槽污染;HASL(热风整平)造成的污染。
塑料薄膜在UV包装印刷中需考虑的问题
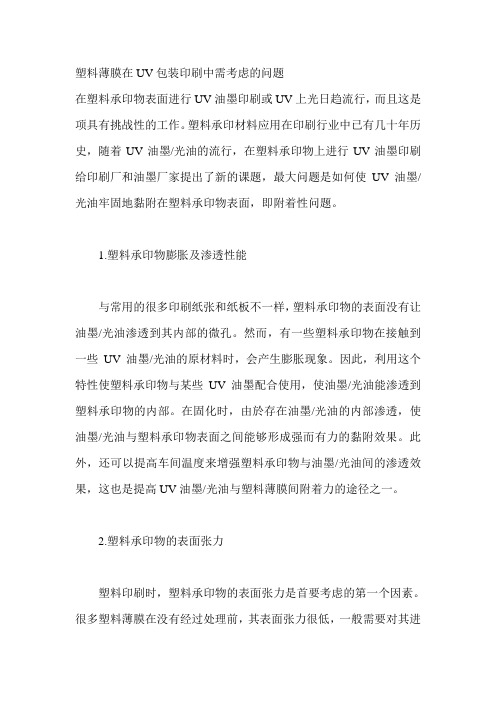
塑料薄膜在UV包装印刷中需考虑的问题在塑料承印物表面进行UV油墨印刷或UV上光日趋流行,而且这是项具有挑战性的工作。
塑料承印材料应用在印刷行业中已有几十年历史,随着UV油墨/光油的流行,在塑料承印物上进行UV油墨印刷给印刷厂和油墨厂家提出了新的课题,最大问题是如何使UV油墨/光油牢固地黏附在塑料承印物表面,即附着性问题。
1.塑料承印物膨胀及渗透性能与常用的很多印刷纸张和纸板不一样,塑料承印物的表面没有让油墨/光油渗透到其内部的微孔。
然而,有一些塑料承印物在接触到一些UV油墨/光油的原材料时,会产生膨胀现象。
因此,利用这个特性使塑料承印物与某些UV油墨配合使用,使油墨/光油能渗透到塑料承印物的内部。
在固化时,由於存在油墨/光油的内部渗透,使油墨/光油与塑料承印物表面之间能够形成强而有力的黏附效果。
此外,还可以提高车间温度来增强塑料承印物与油墨/光油间的渗透效果,这也是提高UV油墨/光油与塑料薄膜间附着力的途径之一。
2.塑料承印物的表面张力塑料印刷时,塑料承印物的表面张力是首要考虑的第一个因素。
很多塑料薄膜在没有经过处理前,其表面张力很低,一般需要对其进行表面处理,以提高塑料承印物的表面张力,处理后一般要达到40达因/cm甚至更高一些。
通常,塑料承印物供应厂家对塑料进行了表面处理,但是处理效果很快会丧失。
对印刷厂而言,连线处理是最佳的解决方案,以保证印刷时塑料承印物的表面张力还维持在可接受范围。
电晕放电(氧化作用)处理是最常见的处理方法,它被应用在各种塑料薄膜的表面处理中,而且不会损坏那些对温度敏感的塑料承印物。
电晕放电采用高频高压或中频高压放电,对塑料表面进行处理,使其表面活化,呈多孔性,以提高塑料薄膜表面对油墨的黏附力,改善薄膜的印刷适性。
例如;常用的PE(聚乙烯)薄膜经过电晕放电处理后,在PE分子链上生成了羧基、羰基等不饱和键。
表面经过氧化后,使PE分子转化为极性分子,增加了表面能。
通常,PE的表面张力处理后从31达因/cm提高到39-40达因/cm,这样就增加了PE薄膜对UV油墨/光油的润湿性和黏附性,从而提高了印迹的牢固程度。
覆膜工艺及其问题解决方案

粘合剂的涂布对覆膜的影响
涂布过程是将粘合剂涂布到塑料薄膜(BOPP)上,涂布量 的大小取决于印刷品的纸张和油墨层的厚度,纸张平滑度高(如 铜版纸)涂布量就应该少一些。粘合剂的涂布量一般为每平方米 5——10克左右,胶层厚度为8——10微米左右。 涂布量的大小还与 涂布机的速度以及涂布辊和刮胶辊之间的 平行间隙有关,涂布机转速高涂布量就大,在操作过程中主机速 度与涂布机速度之比应为1:1· 5为好,涂布辊和刮胶辊之间的平 行间隙调整范围应控制在5——6微米之间。 涂布剂涂布量过小,涂布层厚度太薄,易影响粘结强度,由 于粘合力不足则覆膜度不牢,塑料薄膜极易与纸张分离脱落。涂 布量过大,涂布层过厚其影响更为严重,会造成粘合剂中溶剂挥 发减慢,产品放置后发生起泡起皱等现象。
覆膜场地环境湿度对覆膜的影 响
在相对湿度高的工作环境中,覆膜 的印刷品的平衡水份值会发生改变,从 空气中吸收大量的水份,在覆膜过程中 释放出来会在粘合界面上形成非粘合现 象,而且纸张印刷品边缘也会形成波浪 形,覆合时不能与塑料薄膜很好地粘合。 因此应保持场地环境的湿度相对稳定, 场地环境的相对湿度应严格控制在45— —50%之间。
覆膜工艺操作的控制要点
纸塑覆合是热压合物理作用的综合结 果,覆膜温度、覆膜压力、覆膜速度则 是实现这种物理综合的基本条件。正确 处理好覆膜温度、覆膜压力、覆膜速度 是保证覆膜质量以及为下工序带来良好 操作界面的至关重要。
覆膜的温度控制
即涂覆膜烘道的温度不可过高或过低,一般控制在50——60度 左右。温度过低,粘合剂中的溶剂不能充分发挥,将会影响覆膜 的牢度,极易产生气泡出现脱落现象。烘道温度过高,覆膜后表 面会产生许多皱褶。 在热压下覆合的粘合剂层处于熔融状态,分子加剧参加成键 的分子数量增多,使塑料薄膜、印刷品、粘合剂层界面间达到最 大粘合力。覆膜温度的提高有助于粘合强度的增加,但必须控制 在合理的范围内。即涂膜覆膜温度一般控制在80——90度左右, 预涂膜覆膜温度一般控制在80——100度左右。过高的温度,覆 合时会使塑料薄膜收缩变形,导致覆膜后产品皱褶、卷曲及局部 起泡。 正确的温度控制,才能使塑料薄膜上的粘合剂胶层彻底熔融, 成为粘流 状态,具备合适的流动性,以实现印刷品表面的润湿粘 结,同时保证覆合面即时固化,使覆膜产品外观平整光亮,胶层 熔融程度好,无折痕,并将油墨剥离。覆膜过程的温度控制还影 响和决定着热熔胶受耐热时的变化以及对后工序(如烫金)操作 中,将会承受的新热力的抗衡力度。因此,覆膜温度必须严格的 控制。
细数糊盒质量问题及解决方案

细数糊盒质量问题及解决方案在糊盒过程中,大家碰到了形形色色的问题,与此同时,也出现了多种多样的解决方案。
1、黏结牢度不高,纸盒脱胶。
脱胶是指粘口由于黏结牢度不够而开裂,主要原因归纳如下:(1) 胶黏剂的黏度不够或涂胶量不足。
(2) 胶黏剂和纸盒材料不匹配。
(3) 纸盒的粘口部分经过覆膜、上光等表面加工,胶黏剂难以透过表层,渗入纸张,纸盒难以粘牢。
(4) 折叠涂胶后压力不足,加压时间不够长,不利于粘贴结实。
对于以上由胶黏剂引起的糊盒不牢问题,应选择与纸盒材料相适应的胶黏剂,而胶黏剂的选择和使用也是很有讲究的。
首先,不能错误地认为胶黏剂的黏度越高,糊盒效果越好。
黏度高,胶黏剂强度也变高,起皱率也会随之升高。
在全自动糊盒机的涂胶辊以每分钟112转的高速运转的情况下,胶黏剂的推荐黏度是500~1000cps。
其次,胶黏剂的黏结力要强。
因为自动糊盒机成型部的瞬间压力不是很大,而且在每分钟生产30—40个纸盒的高速作业过程中,受压时间也不长,本身黏结力强的胶黏剂,即使轻轻施压,也可以将纸盒黏结牢固。
另外,糊盒车间的环境温度也会对胶黏剂产生一定的影响。
如果糊盒车间温度太低,胶黏剂会马上凝固,影响黏结牢度,即使涂胶量再多也不起作用。
当然,涂胶量越少,对室温越敏感,所以到冬天,糊盒车间的温度应保持在20℃以上,有条件的可以装上空调进行调节。
在糊盒车间里,还要安装大型易见的温度计,以便随时检查、控制作业环境。
对于糊好的产品,应在常温下干燥后再出厂,冬季切忌未干燥就急着送货。
对于经过覆膜、上光处理的纸盒,解决糊盒不牢的方法有4种:其一,模切时在粘口处放置针线刀,将粘口的表层扎破,以利于胶黏剂的渗入。
其二,用自动糊盒机附带的磨边装置将粘口的表层磨破,以利于胶黏剂的渗入。
其三,将热熔胶喷射到粘口部分,利用高温熔化粘口表面的物质,提高糊盒牢度。
其四,在印前进行盒型设计时,可预先在要覆膜和上光的盒片边缘留出涂胶部位。
对于由于压力不足产生的糊盒不牢现象,可以增加糊盒机压着部的压力,延长压着时间,或者更换黏结力强的胶黏剂。
覆膜常见缺点分析及改进方案

覆膜常见缺点分析及改进方案1. 背景介绍覆膜技术是一种常用的表面加工方法,可以提供薄膜保护和增强材料的外观。
然而,尽管覆膜有很多优点,但也存在一些常见缺点。
本文将分析并提出改进方案,以解决这些问题。
2. 常见缺点分析2.1. 易产生气泡覆膜过程中,常常会产生气泡,这会对制成品的外观和质量造成负面影响。
2.2. 容易损坏和脱落覆膜层很容易损坏和脱落,因而无法持久保护材料表面。
2.3. 剥离困难覆膜在剥离时可能会很困难,需要特殊工具和技巧。
2.4. 限制可视性和传导性某些覆膜材料可能会限制材料的可视性和传导性,对于需要透明性和导电性的应用而言,这是一个明显的缺点。
3. 改进方案3.1. 优化覆膜过程通过优化覆膜过程,可以减少气泡的产生。
例如,控制覆膜液体的流速和温度,使用专业的覆膜设备和工具,以及对覆膜作业人员进行培训,都可以有效降低气泡问题的发生。
3.2. 使用耐用覆膜材料选择耐用的覆膜材料可以解决覆膜层易损坏和脱落的问题。
例如,使用耐磨、耐撞击的高品质材料,可以延长覆膜的寿命,提高产品的使用寿命。
3.3. 开发容易剥离的覆膜材料研发容易剥离的覆膜材料可以解决剥离困难的问题。
这样一来,无需特殊工具和技巧,覆膜层可以轻松地剥离,从而减少生产过程中的时间和劳动成本。
3.4. 提供不同特性的覆膜材料开发不同特性的覆膜材料可以满足不同的应用需求。
例如,针对需要透明性和导电性的产品,推出可透明和导电性能的覆膜材料,以满足相关行业对于可视性和传导性的要求。
4. 总结覆膜技术在提供外观保护和增强材料外观方面具有重要作用。
然而,我们也不可忽视它的一些常见缺点。
通过优化覆膜过程,使用耐用和易剥离的覆膜材料,以及提供不同特性的材料,我们可以改进覆膜技术,提高其效果和应用范围。
(字数:823字)。
包衣常见问题及解决方法
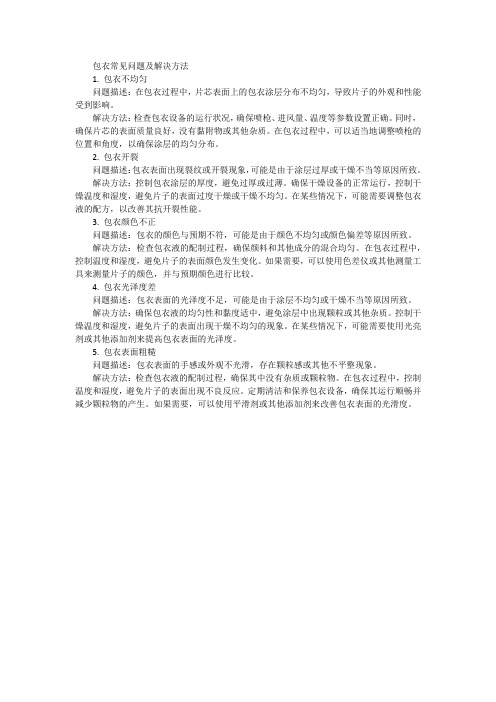
包衣常见问题及解决方法1. 包衣不均匀问题描述:在包衣过程中,片芯表面上的包衣涂层分布不均匀,导致片子的外观和性能受到影响。
解决方法:检查包衣设备的运行状况,确保喷枪、进风量、温度等参数设置正确。
同时,确保片芯的表面质量良好,没有黏附物或其他杂质。
在包衣过程中,可以适当地调整喷枪的位置和角度,以确保涂层的均匀分布。
2. 包衣开裂问题描述:包衣表面出现裂纹或开裂现象,可能是由于涂层过厚或干燥不当等原因所致。
解决方法:控制包衣涂层的厚度,避免过厚或过薄。
确保干燥设备的正常运行,控制干燥温度和湿度,避免片子的表面过度干燥或干燥不均匀。
在某些情况下,可能需要调整包衣液的配方,以改善其抗开裂性能。
3. 包衣颜色不正问题描述:包衣的颜色与预期不符,可能是由于颜色不均匀或颜色偏差等原因所致。
解决方法:检查包衣液的配制过程,确保颜料和其他成分的混合均匀。
在包衣过程中,控制温度和湿度,避免片子的表面颜色发生变化。
如果需要,可以使用色差仪或其他测量工具来测量片子的颜色,并与预期颜色进行比较。
4. 包衣光泽度差问题描述:包衣表面的光泽度不足,可能是由于涂层不均匀或干燥不当等原因所致。
解决方法:确保包衣液的均匀性和黏度适中,避免涂层中出现颗粒或其他杂质。
控制干燥温度和湿度,避免片子的表面出现干燥不均匀的现象。
在某些情况下,可能需要使用光亮剂或其他添加剂来提高包衣表面的光泽度。
5. 包衣表面粗糙问题描述:包衣表面的手感或外观不光滑,存在颗粒感或其他不平整现象。
解决方法:检查包衣液的配制过程,确保其中没有杂质或颗粒物。
在包衣过程中,控制温度和湿度,避免片子的表面出现不良反应。
定期清洁和保养包衣设备,确保其运行顺畅并减少颗粒物的产生。
如果需要,可以使用平滑剂或其他添加剂来改善包衣表面的光滑度。
聚乙烯膜落标不合格
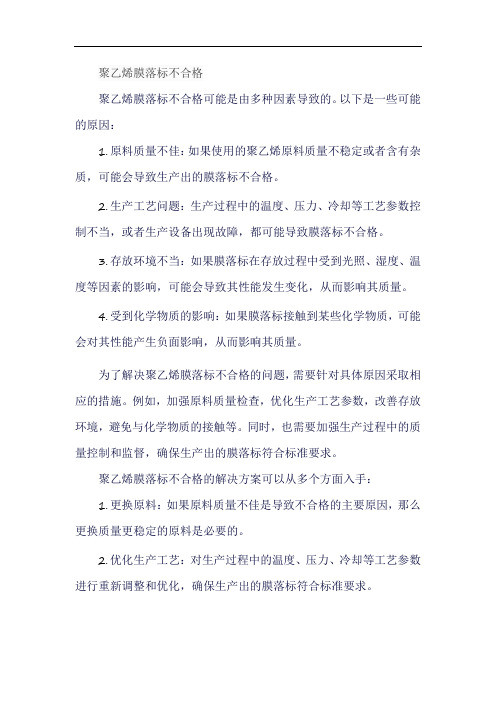
聚乙烯膜落标不合格聚乙烯膜落标不合格可能是由多种因素导致的。
以下是一些可能的原因:1.原料质量不佳:如果使用的聚乙烯原料质量不稳定或者含有杂质,可能会导致生产出的膜落标不合格。
2.生产工艺问题:生产过程中的温度、压力、冷却等工艺参数控制不当,或者生产设备出现故障,都可能导致膜落标不合格。
3.存放环境不当:如果膜落标在存放过程中受到光照、湿度、温度等因素的影响,可能会导致其性能发生变化,从而影响其质量。
4.受到化学物质的影响:如果膜落标接触到某些化学物质,可能会对其性能产生负面影响,从而影响其质量。
为了解决聚乙烯膜落标不合格的问题,需要针对具体原因采取相应的措施。
例如,加强原料质量检查,优化生产工艺参数,改善存放环境,避免与化学物质的接触等。
同时,也需要加强生产过程中的质量控制和监督,确保生产出的膜落标符合标准要求。
聚乙烯膜落标不合格的解决方案可以从多个方面入手:1.更换原料:如果原料质量不佳是导致不合格的主要原因,那么更换质量更稳定的原料是必要的。
2.优化生产工艺:对生产过程中的温度、压力、冷却等工艺参数进行重新调整和优化,确保生产出的膜落标符合标准要求。
3.维护和检修设备:检查生产设备是否存在故障,并进行必要的维修和保养,以确保设备的正常运行。
4.改善存放环境:控制好膜落标的存放环境,避免光照、湿度、温度等因素对其性能产生负面影响。
5.避免化学物质接触:确保膜落标在存放和使用过程中不与任何有害化学物质接触。
6.加强质量控制:在生产过程中加强质量控制和监督,及时发现和纠正问题,确保生产出的膜落标符合标准要求。
7.培训员工:对员工进行必要的培训,提高他们的技能和意识,确保他们能够按照标准要求进行操作和管理。
这些解决方案需要根据具体情况进行选择和实施,同时需要持续监测和改进,以确保聚乙烯膜落标的生产质量得到不断提高。
覆膜机改善措施方案

覆膜机改善措施方案
背景
覆膜机主要用于农业生产和加工业,在农作物覆膜和生产过程中发挥重要作用。
覆膜机主要由控制系统、转动装置、框架和薄膜滚轴组成。
随着使用时间的增加,覆膜机的部件容易出现问题,导致工作效率降低,甚至导致设备报废。
问题与挑战
1.覆膜机受环境影响大,容易出现故障。
2.容易产生浪费和损失情况。
3.覆膜的质量受控制能力、机器运动速度和表面状况等多方面因素的影响,需要进行改进。
改善措施
针对上述问题,提出以下改善方案:
1.设备保养
设备保养是延长覆膜机使用寿命和提高工作效率的重要措施。
保养主要包括:
•每季度进行设备检测和维护,及时发现并解决问题;
•将覆膜机置于干燥、通风、不受阳光直射的地方;
•定期更换磨损的零件;
•手动操作时,保证人员技能和安全意识。
2.日常管理
日常管理是规范覆膜机操作和维护的手段,包括:
•对操作员进行相关培训,提高操作的标准化和统一性;•确定操作和维护规范,防止误操作引起的损坏和详细记。
- 1、下载文档前请自行甄别文档内容的完整性,平台不提供额外的编辑、内容补充、找答案等附加服务。
- 2、"仅部分预览"的文档,不可在线预览部分如存在完整性等问题,可反馈申请退款(可完整预览的文档不适用该条件!)。
- 3、如文档侵犯您的权益,请联系客服反馈,我们会尽快为您处理(人工客服工作时间:9:00-18:30)。
D.检查薄膜电晕处理是否达到36-40达因。
E.搭边处粘接不实。这主要表现在厚纸。收卷时纸张会产生一定的卷曲变形。且收卷直径越小越明显。刚出施压辊还未干燥的覆膜品往往就会在搭边处被卷曲的纸张顶开,造成此处粘接不实。为提高成品率,此时应尽量减小搭边宽度,以保证粘接不实的宽度在模切咬口范围内。
4.烘干。其目的是去除粘合剂中的溶剂,保留粘合剂的固体含量。烘道温度应掌握在40~60℃之间,主要由过塑粘合剂中溶剂的挥发性快慢来确定。胶层的干燥度一般控制在90~95%,此时粘结力大,纸塑复合最牢。涂层不平或过干,会使粘结力下降,造成覆膜起泡、脱层。
5.调整热压温度和辊间压力。热压温度根据印刷品墨层厚度、纸质好坏、气候变化等情况来调整,一般应控制在60~80℃。温度过高会超过薄膜承受范围,薄膜等受高热而变形,极易使产品曲卷、起泡、皱褶等,且橡胶辊表面易烫损变形;温度过低,覆膜不牢,易脱层。般铜版纸的热压温度较低,胶版纸、白板纸及墨层厚的印刷品的热压温度偏高。
覆膜中的一些问题与解决方案
一、前言
在印后加工中覆膜是一项重要的印刷工艺,工艺虽然不很复杂,但是在覆膜的操作和工艺设计中,往往会由于对覆膜本身以及印刷缺乏充分的了解,而经常出现这样或那样的问题。在本文中将对覆膜中经常遇到的一些问题进行分析,并提出一些解决方案。覆膜是一项综合性的技术,它涉及许多因素,如塑料薄膜、粘合剂、溶剂、印刷品表面墨层状况、机械控制以及环境条件等。要获得高质量的覆膜产品,就必须在工艺过程中控制上述诸因素的变化,并协调好它们之间的关系。
二、加工工艺
覆膜的工艺流程为:工艺准备→安装塑料薄膜滚筒→涂布粘合剂→烘干→设定工艺参数(烘道温度和热压温度、压力、速度)→试覆膜→抽样检测→正式覆膜→复卷或定型分割。
1.工艺准备工作。准备工作是否充分,对保证覆膜生产的正常进行,提高生产效率和产品质量有很大影响。覆膜生产的准备工作一般应包括:待覆印刷品的检查、塑料薄膜的选用以及粘合剂的配制等。
4.喷粉的加放。为适应多色高速印刷,胶印中常采用喷粉工艺来解决背面蹭脏之弊。喷粉大都是谷类淀粉及天然的悬浮型物质组成,喷粉的防粘作用主要是在油墨层表面形成一层不可逆的垫子,从而减少粘连。因颗粒较粗,若印刷过程中喷粉过多,这些颗粒浮在印刷品表面,覆膜时粘合剂不是每处都与墨层粘合,而是与这层喷粉粘合,从而造成假粘现象,严重影响了覆膜质量。因此,若印后产品需进行覆膜加工,则印刷时应尽量控制喷粉用量。
溶剂型粘合剂应用较广泛,常用的溶剂有醋类(如醋酸乙酯)、醇类、苯类(如甲苯)。溶剂型粘合剂有单组分和双组分之分。单组分粘合剂使用方便,成本较低,虽粘结强度略低于双组分粘合剂,但可以采取其它工艺措施加以弥补,使用较普遍。双组分粘合剂虽粘结强度较高,但成本高,使用较麻烦。
各种粘合剂应符合以下要求:色泽浅、透明度高;无沉淀杂质;使用时分散性能好,易流动,干燥性好;溶剂无毒性或毒性小;粘附性能持久良好,对油墨、纸张、塑料薄膜均有良好的亲附性;覆膜产品长期放置不泛黄、不起皱、不起泡和不脱层;并要求粘合剂具有耐高温,抗低温、耐酸碱以及操作简便,价格便宜等特点。
B.若是印刷品表面状况不善如有喷粉、墨层太厚、墨迹未干或未干彻底等而造成粘合不良,则可用干布轻轻地擦去喷粉,或增加粘合剂涂布量、增大压力,以及采用先热压一遍再上胶,或改用固体含量高的粘合剂,或增加粘合剂涂布厚度,或增加烘干道温度等办法解决;
C.若是因粘合剂被印刷油墨及纸张吸收,而造成涂覆量不足,可考虑重新设定配方和涂覆量。
6.机速的控制。机速越快,热压时间也就越短,因此温度可调高些,压力可加大些,粘合剂的粘度应大些;反之亦然。机速一般控制在6~10m/min为宜,机速过快或过慢都会影响覆膜质量。
Байду номын сангаас
7.试样检测。试覆膜后抽出样张,按照产品标准,对抽样产品进行关键性能检测,要求达到表面光亮、平滑,以及无褶皱、气泡、脱层等。
1.印刷品墨层厚度。墨层厚实的实地印刷品,往往很难与塑料薄膜粘合,不久便会脱层、起泡。这是因为,厚实的墨层改变了纸张多孔隙的表面特性,使纸张纤维毛细孔封闭,严重阻碍了粘合剂的渗透和扩散。粘合剂在一定程度内的渗透,对覆膜粘合是有利的。
另外,印刷品表面墨层及墨层面积不同,则粘合润湿性能也不同。实验证明,随着墨层厚度的增加或图文面积的增大,表面张力值明显降低。故不论是单色印刷还是叠色印刷,都应力求控制墨层在较薄的程度上。
(1)待覆印刷品的检查。对待覆膜印刷品的检查,有别于对普通印刷品的质量检查。主要应针对覆膜影响较大的项目,如表面是否有喷粉、墨迹是否充分干燥、印刷品是否平整等,一旦发现问题,应及时采取处理措施。
(2)塑料薄膜的选用。塑料薄膜的选用包括塑料薄膜的选定及质量检查和分切卷料。覆膜材料是否恰当是关系产品质量的一个重要因素。
印刷墨层的厚度还与印刷方式有直接关系,印刷方式不同,其墨层厚度也不同。如平印产品的墨层厚度约为1~2μm,凸印时约为2~5μm,凹印时可达10μm。从覆膜的角度看,平印的印刷品是理想的,其墨层很薄。
2.印刷油墨的种类。需覆膜的印刷品应采用快固着亮光胶印油墨,该油墨的连结料是由合成树脂、干性植物油、高沸点煤油及少量胶质构成。合成树脂分子中含有极性基团,极性基团易于同粘合剂分子中的极性基团相互扩散和渗透,并产生交联,形成物理化学结合力,从而有利于覆膜;快固着亮光胶印油墨还具有印刷后墨层快速干燥结膜的优势,对覆膜也十分有利。但使用时不宜过多加放催干剂,否则,墨层表面会产生晶化,反而影响覆膜效果。
四、常见故障及解决方案
影响覆膜质量的因素较多,除纸张、墨层、薄膜、粘合剂等客观因素外,还受温度、压力速度、胶量等主观因素影响。这些因素处理不善,就会产生各种覆膜质量问题。
1.粘合不良。
A.因粘合剂选用不当、涂胶量设定不当、配比计量有误而引起的覆膜粘合不良故障,应重选粘合剂牌号和涂覆量,并准确配比;
维利油是氢氧化铝和干性植物油连结料分散轧制而成的浆状透明体,可用以增加印刷品表面的光泽,印刷性能优良。但氢氧化铝质轻,印刷后会浮在墨层表面,覆膜时使粘合剂与墨层之间形成不易察觉的隔离层,导致粘合不上或起泡。其本身干燥慢,还具有抑制油墨干燥的特性,这一点也难以适应覆膜。
亮光油是一种从内到外快速干燥型冲淡剂,是由树脂、干性植物油、催干剂等混合炼制而成的胶状透明物质,质地细腻:结膜光亮,具有良好的亲和作用,能将聚丙烯薄膜牢固地吸附于油墨层表面。同时,亮光油可以使印迹富有光泽和干燥速度加快,印刷性能良好。因此,它是理想的油墨冲淡剂。
5.印刷品表面墨层干燥状况。印刷品墨层干燥不良对覆膜质量危害极大。影响墨层干燥的因素,除了有油墨的种类、印刷过程中催干剂的用量与类型及印刷、存放间的环境温湿度外,纸张本身的结构也相当重要。如铜版纸与胶版纸其结构不同,则墨层的干燥状况亦有区别。
无论是铜版纸还是胶版纸,在墨迹未完全彻底干燥时覆膜,对覆膜质量的影响均是不利的。油墨中所含的高沸点溶剂极易使塑料薄膜膨胀和伸长,而塑料薄膜膨胀和伸长是覆膜后产品起泡、脱层的最主要原因。
2.起泡。
A.其原因若是印刷墨层未干透,则应先热压一遍再上胶,也可以推迟覆膜日期,使之干燥彻底;
B.施压辊压力太小
整个印刷品表面均有气泡是因为压力太小,可适当加大施压辊压力。B.若是印刷墨层太厚,则可适当增加粘合剂涂布量,增大压力及复合温度;
C.若是复合辊表面温度过高,则应采取风冷、关闭电热丝等散热措施,尽快降低复合辊温度;
单组分的粘合剂可直接使用。双组分或多组分粘合剂,一经混合后即进行反应,而且粘合剂的粘合力随贮存时间的增加会因表面老化而下降,所以,配制好的粘合剂不宜长时间贮存,应当天用完。覆膜质量的好坏与粘合剂的配制质量优劣有很大关系,配制时要细心谨慎。
2.安装塑料薄膜卷筒。将选定的薄膜按印刷品的幅面切割成适当宽度后,安装在覆膜机的出卷装置上,并将塑料薄膜穿至涂布机构上。要求薄膜平整无皱,张力均匀适中。如覆膜印刷品要做成纸盒,则须考虑留出接口空隙,否则粘接不牢。
3.油墨冲淡剂的使用。油墨冲淡剂是能使油墨颜色变淡的一类物质,常用的油墨冲淡剂有白墨、维利油和亮光油等。
白墨属油墨类,由白墨颜料、连结料及辅料构成,常用于浅色实地印刷、专色印刷及商标图案印刷。劣质白墨有明显的粉质颗粒,与连结料结合不紧,印刷后连结料会很快渗入纸张,而颜料则浮于纸面对粘合形成阻碍,这就是某些淡色实地印刷品常常不易覆膜的原因。印刷前应慎重选择白墨,尽量选用均匀细腻、无明显颗粒的白墨作为冲淡剂。
塑料薄膜的质量检查方法,除上述膜面表面处理等几项外,大都可以用手感或目测来解决。宽筒薄膜卷料还须按所要求的宽度分切成窄筒卷料才能用于覆膜,分切后的窄筒卷料要求边缘平齐、两端平齐、卷曲张力一致。
(3)粘合剂的配制。国内使用的粘合剂的品种较多,主要有聚氨酯类、橡胶类以及热塑高分子树脂等。其中以热塑性高分子类胶粘剂使用效果最好。
辊间压力应视不同纸质及纸张厚度正确调整。压力过大,纸面稍有不平整或薄膜张力不完全一致时,会产生压皱或条纹的现象;压力长期过大,会导致橡胶辊变形,辊的轴承也会因受力过大而磨损。压力过高或不均匀,则会造成覆膜不牢、脱层现象。一般覆膜表面光滑、平整、结实的印刷品,压力为 19~20mPa;覆膜粗糙松软的印刷品,压力为22~23mPa。
3.涂布粘合剂。首先,粘合剂的粘稠度应视纸质好坏、墨层厚薄、烘道温度及烘道长短、机器转动速度等因素而定。当墨层厚、烘道温度低、烘道短、机速快时,粘合剂的粘度应适当增大,反之则相反。其次应掌握涂布胶层的厚度,使之达到均匀一致。涂层厚度应视纸质好坏及油墨层厚薄而定:表面平滑的铜版纸,涂布量一般为3~5g/m(厚约5μm);表面粗糙、吸墨量大的胶版纸、白板纸,涂布量为7~8g/m(厚约8μm)。当然,墨层厚,涂布量应稍大,反之则相反。但涂层过厚,易起泡、起皱,反之则覆膜不牢。
常用塑料薄膜有:聚氯乙烯(PVC)、聚丙烯(BOPP)和聚酯(PET)薄膜等。其中BOPP薄膜(15~20μm)柔韧、无毒性,而且平整度好、透明度高、光亮度好,并具有耐磨、耐水、耐热、耐化学腐蚀等性能,此外,它的价格便宜,是覆膜工艺中较理想的复合材料。